报废汽车催化剂中铑的提取与富集
失效汽车尾气催化剂中铂族金属回收的研究进展

失效汽车尾气催化剂中铂族金属回收的研究进展
李明钢;高元兴;郭学益
【期刊名称】《贵金属》
【年(卷),期】2024(45)1
【摘要】失效汽车尾气催化剂是回收铂族金属(铂、钯、铑)的重要二次资源。
本文介绍了失效汽车尾气催化剂中铂族金属的回收工艺流程,包括失效催化剂预处理、铂族金属富集、分离与精炼三部分;详细介绍了两种高效预处理技术、两种富集方法以及四种分离与精炼工艺,总结了各种方法的原理、工艺流程、优缺点及改进方向。
回收企业应根据回收规模和环保政策采用合适的回收工艺,以实现不同回收工艺之间的优势互补,未来需重点研发回收率高且环境友好的清洁回收工艺。
【总页数】12页(P78-89)
【作者】李明钢;高元兴;郭学益
【作者单位】中南大学冶金与环境学院
【正文语种】中文
【中图分类】TF83;X705
【相关文献】
1."从失效汽车尾气净化催化剂中回收铂族金属"项目通过验收
2.从失效汽车尾气净化催化剂中回收铂族金属
3.从失效汽车尾气净化催化剂中回收铂族金属--亚砜萃取工艺研究
4.失效汽车尾气净化催化剂中铂族金属回收技术
5.从失效汽车尾气催化剂中回收铂族金属研究进展
因版权原因,仅展示原文概要,查看原文内容请购买。
汽车催化剂提炼

汽车催化剂提炼一、引言汽车催化剂是一种能够将有害气体转化为无害气体的装置,是现代汽车尾气净化的核心技术之一。
其中最重要的组成部分是催化剂,其主要成分为铂、钯和铑等贵金属。
本文将详细介绍汽车催化剂提炼的过程和相关知识。
二、汽车催化剂提炼的原理汽车催化剂中含有大量贵金属元素,如何从中提取这些贵金属成为了工业界关注的问题。
汽车催化剂提炼主要基于两个原理:物理分离和化学还原。
1. 物理分离物理分离是指利用物料在不同条件下的物理性质进行分离。
对于汽车催化剂来说,主要采用高温焙烧法将有机物和无机材料进行分解,进而得到含有贵金属元素的粉末。
2. 化学还原化学还原是指利用还原剂将贵金属离子还原成自由状态下的贵金属。
对于汽车催化剂来说,常用的还原剂包括氢气、硝酸亚铁等。
其中氢气还原法最为常用,其原理是将汽车催化剂中的贵金属离子还原成金属颗粒。
三、汽车催化剂提炼的过程汽车催化剂提炼的过程主要包括前处理、焙烧和还原三个步骤。
1. 前处理前处理是指对汽车催化剂进行预处理,以便更好地进行后续的焙烧和还原。
主要包括以下几个步骤:(1)去除杂质:将汽车催化剂中的杂质去除,以保证后续操作的纯度。
(2)打碎:将汽车催化剂打碎成小颗粒,以便于后续操作。
(3)洗涤:用稀硝酸或盐酸洗涤汽车催化剂,以去除表面附着物和残留物。
2. 焙烧焙烧是指将经过前处理的汽车催化剂在高温下分解,并得到含有贵金属元素的粉末。
主要包括以下几个步骤:(1)加热:将经过前处理的汽车催化剂放入高温炉中加热,通常温度在500℃以上。
(2)分解:汽车催化剂经过高温加热后,有机物和无机材料会分解成气体和固体两部分。
其中固体部分就是含有贵金属元素的粉末。
(3)冷却:将焙烧后的汽车催化剂取出,放置在通风处自然冷却。
3. 还原还原是指将焙烧后得到的贵金属离子还原成自由状态下的贵金属。
主要包括以下几个步骤:(1)氢气还原:将焙烧得到的汽车催化剂粉末放入还原器中,通过通入氢气来进行还原。
铑的回收与提炼技巧

铑的回收与提炼技巧铑是一种稀有而贵重的金属,在许多工业领域都有广泛的应用。
它是铂族元素中的一员,具有良好的耐腐蚀性和催化活性。
由于其稀有性和高价值,铑的回收和提炼技巧变得尤为重要。
在本文中,我们将深入探讨铑的回收与提炼技巧,并分享我们对这一主题的观点和理解。
一、铑的回收:1. 知识储备:进行铑的回收,我们需要了解铑的特性和应用领域。
了解它的性质和使用情况,将有助于我们更好地设计回收工艺,并选择合适的回收方法。
2. 废物分类:铑通常存在于废弃物和催化剂中。
废物分类和处理非常关键。
正确识别和分离废物中的铑,可以避免资源的浪费,并确保回收过程的高效性。
3. 物理方法:铑的回收可以使用物理方法,如沉淀法、溶剂萃取和吸附等。
这些方法可以通过改变物理条件来分离和回收铑,例如温度、压力、pH值等。
4. 化学方法:另一种常用的回收方法是化学方法,如还原、溶解和析出等。
通过与其他物质的反应,可以将铑从废物中分离出来,并进一步提炼。
5. 回收工艺:根据废物的类型和含量,选择合适的回收工艺非常重要。
这可能涉及多个步骤和工艺条件的调整,以确保高效、可持续的铑回收。
二、铑的提炼技巧:1. 原料选择:铑通常存在于铂矿石中,选择适合提炼铑的铂矿石是关键。
高品质的铂矿石含有更高的铑含量,这将有助于提高提炼效率。
2. 矿石处理:在提炼铑之前,需要对铂矿石进行预处理。
这包括破碎、磨矿和浮选等步骤,以提高铑的浓度,并减少杂质的含量。
3. 浸出与萃取:在浸出过程中,将铂矿石与浸出剂接触,以将铑从矿石中溶解出来。
使用相应的萃取剂来提取溶液中的铑,并将其分离出来。
4. 精炼与纯化:提取的铑可能仍然含有杂质,因此需要进行精炼和纯化。
这可以通过电解、溶剂萃取和化学反应等方法来实现,以确保最终产品的纯度和质量。
5. 质量控制:在整个提炼过程中,质量控制非常重要。
使用适当的分析技术和设备,确保提取和纯化过程的准确性和一致性,以满足不同应用领域对铑质量的要求。
失效汽车催化剂中铂钯铑富集方法探讨
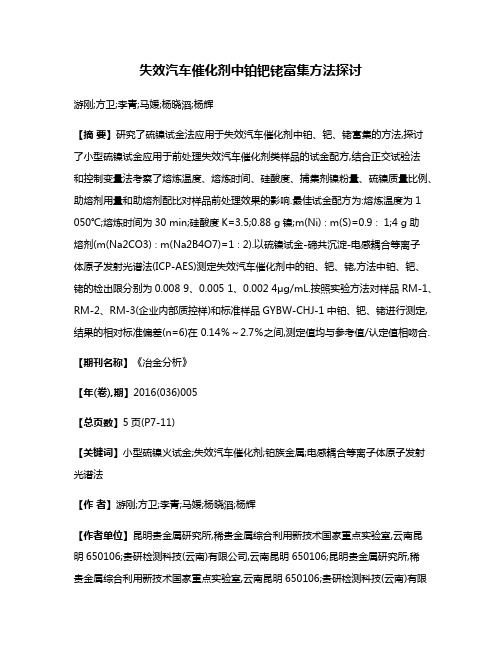
失效汽车催化剂中铂钯铑富集方法探讨游刚;方卫;李青;马媛;杨晓滔;杨辉【摘要】研究了硫镍试金法应用于失效汽车催化剂中铂、钯、铑富集的方法,探讨了小型硫镍试金应用于前处理失效汽车催化剂类样品的试金配方,结合正交试验法和控制变量法考察了熔炼温度、熔炼时间、硅酸度、捕集剂镍粉量、硫镍质量比例、助熔剂用量和助熔剂配比对样品前处理效果的影响.最佳试金配方为:熔炼温度为1 050℃;熔炼时间为30 min;硅酸度K=3.5;0.88 g镍;m(Ni)∶m(S)=0.9∶ 1;4 g助熔剂(m(Na2CO3)∶m(Na2B4O7)=1∶2).以硫镍试金-碲共沉淀-电感耦合等离子体原子发射光谱法(ICP-AES)测定失效汽车催化剂中的铂、钯、铑,方法中铂、钯、铑的检出限分别为0.008 9、0.005 1、0.002 4μg/mL.按照实验方法对样品RM-1、RM-2、RM-3(企业内部质控样)和标准样品GYBW-CHJ-1中铂、钯、铑进行测定,结果的相对标准偏差(n=6)在0.14%~2.7%之间,测定值均与参考值/认定值相吻合.【期刊名称】《冶金分析》【年(卷),期】2016(036)005【总页数】5页(P7-11)【关键词】小型硫镍火试金;失效汽车催化剂;铂族金属;电感耦合等离子体原子发射光谱法【作者】游刚;方卫;李青;马媛;杨晓滔;杨辉【作者单位】昆明贵金属研究所,稀贵金属综合利用新技术国家重点实验室,云南昆明650106;贵研检测科技(云南)有限公司,云南昆明650106;昆明贵金属研究所,稀贵金属综合利用新技术国家重点实验室,云南昆明650106;贵研检测科技(云南)有限公司,云南昆明650106;昆明贵金属研究所,稀贵金属综合利用新技术国家重点实验室,云南昆明650106;贵研检测科技(云南)有限公司,云南昆明650106;昆明贵金属研究所,稀贵金属综合利用新技术国家重点实验室,云南昆明650106;贵研检测科技(云南)有限公司,云南昆明650106;昆明贵金属研究所,稀贵金属综合利用新技术国家重点实验室,云南昆明650106;贵研检测科技(云南)有限公司,云南昆明650106;昆明贵金属研究所,稀贵金属综合利用新技术国家重点实验室,云南昆明650106;贵研检测科技(云南)有限公司,云南昆明650106【正文语种】中文伴随着我国汽车保有量的激增,汽车尾气排放污染已成为我国雾霾成因的来源之一[1]。
从废石油催化剂中提炼稀有金属的工艺
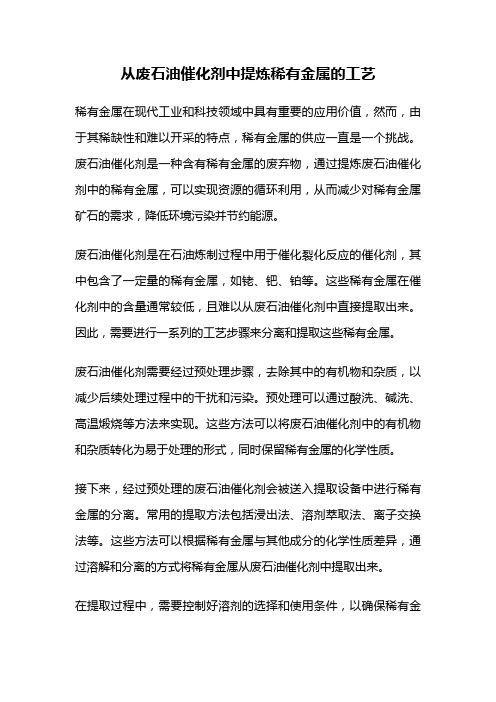
从废石油催化剂中提炼稀有金属的工艺稀有金属在现代工业和科技领域中具有重要的应用价值,然而,由于其稀缺性和难以开采的特点,稀有金属的供应一直是一个挑战。
废石油催化剂是一种含有稀有金属的废弃物,通过提炼废石油催化剂中的稀有金属,可以实现资源的循环利用,从而减少对稀有金属矿石的需求,降低环境污染并节约能源。
废石油催化剂是在石油炼制过程中用于催化裂化反应的催化剂,其中包含了一定量的稀有金属,如铑、钯、铂等。
这些稀有金属在催化剂中的含量通常较低,且难以从废石油催化剂中直接提取出来。
因此,需要进行一系列的工艺步骤来分离和提取这些稀有金属。
废石油催化剂需要经过预处理步骤,去除其中的有机物和杂质,以减少后续处理过程中的干扰和污染。
预处理可以通过酸洗、碱洗、高温煅烧等方法来实现。
这些方法可以将废石油催化剂中的有机物和杂质转化为易于处理的形式,同时保留稀有金属的化学性质。
接下来,经过预处理的废石油催化剂会被送入提取设备中进行稀有金属的分离。
常用的提取方法包括浸出法、溶剂萃取法、离子交换法等。
这些方法可以根据稀有金属与其他成分的化学性质差异,通过溶解和分离的方式将稀有金属从废石油催化剂中提取出来。
在提取过程中,需要控制好溶剂的选择和使用条件,以确保稀有金属的高效提取和纯度的保持。
此外,提取设备的设计和操作也对提取效果有着重要的影响。
合理选择提取剂、控制温度和压力等参数,可以提高稀有金属的回收率和纯度,降低生产成本。
提取出稀有金属后,还需要进行后续的处理和精炼步骤,以获得高纯度的稀有金属产品。
这些步骤可以包括溶剂萃取、离子交换、电解精炼等方法。
通过这些方法,可以去除残留的杂质和其他金属,使得稀有金属的纯度达到工业标准要求。
提炼出的稀有金属可以通过冶炼、合金化等方式进一步加工和利用。
稀有金属在航空航天、电子、医疗器械等领域具有广泛的应用,其高温耐蚀、导电导热等特性使其成为不可替代的材料。
从废石油催化剂中提炼稀有金属的工艺是一项复杂而重要的过程。
废催化剂中铂、钯、铑的萃取分离及精炼
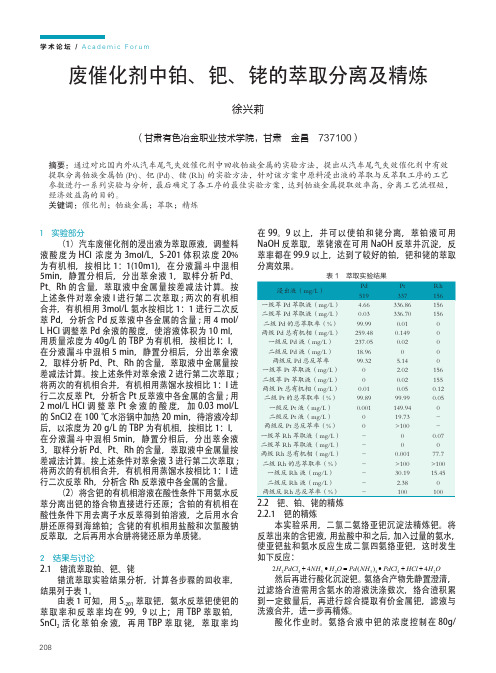
学术论坛 / A c a d e m i c F o r u m2081 实验部分(1)汽车废催化剂的浸出液为萃取原液,调整料液酸度为HCl 浓度为3mol/L,S-201体积浓度20%为有机相,按相比1:1(10m1),在分液漏斗中混相5min,静置分相后,分出萃余液1,取样分析Pd、Pt、Rh 的含量,萃取液中金属量按差减法计算。
按上述条件对萃余液l 进行第二次萃取;两次的有机相合并,有机相用3mol/L 氨水按相比1:1进行二次反萃Pd,分析含Pd 反萃液中各金属的含量;用4 mol/L HCl 调整萃Pd 余液的酸度,使溶液体积为10 ml,用质量浓度为40g/L 的TBP 为有机相,按相比l:l,在分液漏斗中混相5 min,静置分相后,分出萃余液2,取样分析Pd、Pt、Rh 的含量,萃取液中金属量按差减法计算。
按上述条件对萃余液2进行第二次萃取;将两次的有机相合并,有机相用蒸馏水按相比1:l 进行二次反萃Pt,分析含Pt 反萃液中各金属的含量;用2 mol/L HCl 调整萃Pt 余液的酸度,加0.03 mol/L 的SnCl2在100 ℃水浴锅中加热20 min,待溶液冷却后,以浓度为20 g/L 的TBP 为有机相,按相比1:l,在分液漏斗中混相5min,静置分相后,分出萃余液3,取样分析Pd、Pt、Rh 的含量,萃取液中金属量按差减法计算。
按上述条件对萃余液3进行第二次萃取;将两次的有机相合并,有机相用蒸馏水按相比1:l 进行二次反萃Rh,分析含Rh 反萃液中各金属的含量。
(2)将含钯的有机相溶液在酸性条件下用氨水反萃分离出钯的络合物直接进行还原;含铂的有机相在酸性条件下用去离子水反萃得到铂溶液,之后用水合肼还原得到海绵铂;含铑的有机相用盐酸和次氯酸钠反萃取,之后再用水合肼将铑还原为单质铑。
2 结果与讨论2.1 错流萃取铂、钯、铑错流萃取实验结果分析,计算各步骤的回收率,结果列于表1。
贵金属铑的提炼方法

贵金属铑的提炼方法铑是一种贵重的稀有金属,具有耐腐蚀、高熔点和良好的催化性能。
由于其稀有性和昂贵成本,提炼铑的过程非常重要。
本文将介绍几种主要的提炼方法。
1.溶剂萃取法溶剂萃取法是最常用的提炼铑的方法之一、该过程使用有机溶剂与铑溶液接触,通过液液萃取的原理将铑从其他杂质分离出来。
常用的有机溶剂有丁基酮(MIBK)和二辛基硫脲(D2EHPA)。
首先,将铑溶液与有机溶剂混合,在适当的条件下,使铑与有机溶剂中的配体形成配合物。
然后,通过调节pH值或温度,使配合物发生相反的反应,将铑从有机溶剂中分离出来。
2.水热法水热法是另一种提炼铑的常见方法。
该方法利用高温高压水环境下的化学反应来分离铑。
首先,将铑溶液与氢气一起封装在高压反应器中,然后加热至高温(通常在200-250摄氏度)并加压。
在这些条件下,铑可以与水反应生成一种可溶性金属络合物,而杂质不会被溶解。
之后,通过降低温度或减压,可使金属络合物分解,从而得到纯铑。
3.粉末冶金法粉末冶金法是另一种提炼铑的常见方法。
该方法涉及将铑粉末与其他金属粉末混合,制成高度精炼的合金,然后通过热处理来分离铑。
首先,将铑粉末与其他金属粉末按一定比例混合,并且通常使用一些添加剂来增强反应。
然后,将混合粉末置于高温熔融炉中,通常在1500摄氏度左右,使金属粉末熔融。
在这个过程中,铑会与其他杂质金属发生合金化反应,形成合金。
然后,通过冷却和固化,可以获得纯铑。
4.电解法电解法是提炼铑的常见方法之一,尤其适用于高纯度铑的提炼。
该过程涉及使用电解槽将铑溶液作为电解液,然后通过外加电流来分离铑。
通过调节电流密度和电解时间,可以控制铑的析出速率。
由于铑在氯化铑溶液中的电化学活性较高,因此使用氯化铑作为电解液是一种常见的选择。
通过这种方法可以获得高纯度的铑。
总结起来,目前常用的提炼铑的方法主要包括溶剂萃取法、水热法、粉末冶金法和电解法。
这些方法各有优缺点,但都能有效地分离铑并实现高纯度的提取。
铑回收提炼方法

铑回收提炼方法一、铑的概述二、铑的应用三、铑回收提炼方法1.化学法1.1 溶剂萃取法1.2 离子交换法1.3 氧化还原法2.冶金法2.1 熔融盐电解法2.2 氢气还原法四、铑回收提炼的优势和局限性一、铑的概述铑是一种稀有贵金属,其化学符号为Rh,原子序数为45,具有高度稳定性和耐腐蚀性。
它是一种白色有光泽的金属,在自然界中很少出现。
它通常与其他贵金属如钯、铂和镍等共存。
二、铑的应用由于其高度稳定性和耐腐蚀性,铑在许多工业领域中得到广泛应用。
其中最主要的应用是在汽车排放控制系统中作为催化剂。
此外,它还被用作电阻器元件中的电极材料、合成有机化合物催化剂以及制造玻璃陶瓷等。
三、铑回收提炼方法铑的回收和提炼方法主要包括化学法和冶金法两种。
1. 化学法化学法是通过化学反应将铑从废料中分离出来,常用的方法包括溶剂萃取法、离子交换法和氧化还原法。
1.1 溶剂萃取法溶剂萃取是通过将含铑废料与有机溶剂混合,在一定条件下使铑转移到有机相中,再用酸或碱水解有机相中的铑盐得到纯铑。
这种方法适用于含有低浓度的铑废料。
1.2 离子交换法离子交换是利用具有特殊功能的树脂或吸附剂将含有铑的废液中的金属离子与树脂上固定的功能基团进行交换,从而实现分离纯化。
这种方法适用于含有高浓度的铑废液。
1.3 氧化还原法氧化还原是通过氧化或还原反应将铑从废料中提取出来,常采用硫酸亚铁或亚硝酸钠还原含有铑的废液,并用盐酸沉淀得到纯铑。
这种方法适用于含有高浓度的铑废液。
2. 冶金法冶金法是通过高温熔融或氢气还原等方法将铑从废料中分离出来,常用的方法包括熔融盐电解法和氢气还原法。
2.1 熔融盐电解法熔融盐电解是将含有铑的废料与一定比例的碳酸钠和碳酸钙混合,并在高温下进行电解,使铑转移到阴极上。
这种方法适用于含有高浓度的铑废料。
2.2 氢气还原法氢气还原是利用高温下的氢气将含有铑的废料还原成金属铑,再用酸或碱水解得到纯铑。
这种方法适用于含有低浓度的铑废液。
铝碎法回收铑均相催化剂废液中的铑

铝碎法回收铑均相催化剂废液中的铑作者:杜继山来源:《中国化工贸易·下旬刊》2017年第06期摘要:以铑均相废催化剂用后的含铑废液为原料,采用焚烧富集、铝碎、除铝、浸出,并考察了亚硝酸钠络合后加入氯化铵进行提纯工艺操作,由于回收成铑粉后续使用时仍以三氯化铑为基础原料,而铑粉至三氯化铑工艺困难,故本研究最终以回收的RhCl3为成品。
Rh的回收率可以达到98%以上。
关键词:铑;铝碎;亚硝酸钠络合;回收率铑是第五周期IX族铂系元素的成员,是由1803年英国化学家武拉斯顿发现并分离的。
铂、铑等贵金属元素因具有优异的耐酸碱、抗氧化等物理化学性质,被广泛地应用于高新技术、国防工业、航天航海、新能源开发、石油化工、医药合成、电子信息、环境治理等领域。
因其优异的性能和应用的范围广泛,而被誉为“现代工业的维他命”和“第一高新技术金属”,是我国国民经济建设中必不可少和不可替代的关键性战略资源。
铑在地壳中储量非常稀少。
矿物品味低,共生成分复杂,分离和加工及其困难,所以将使用失效的二次贵金属资源再次回收就成了世界各国的工作重点。
铑在化学中主要做催化剂;除了制造合金外,铑可用作其他金属的光亮而坚硬的镀膜,用于照相机零件和制作高效反射镜面、首饰等。
铑均相催化剂主要用于医药化工催化反应过程中,使用完后变性失活,需要更换,其铑的催化剂成为回收铑的二次资源,催化剂因失活变性,催化剂效率降低,对铑的回收造成不利影响,催化剂中的有机物含量高达95%,回收困难,且铑在通常情况下不溶于王水等强酸,因此,本研究采用活性炭吸附铑,铝碎化后浸出铑的实验方案。
1 实验1.1 实验原料本研究所用废铑液主要为医药化工反应失活的催化剂废液,其中含有铑元素为1.2%、铜为0.15%、铁为0.31%、镍为0.18%、锰为0.11%,有机物为97.6%,其他无机盐为0.45%,催化剂中铑的含量为12Kg/t,具有很高的回收价值,但物料成分复杂,除含有较多的铜、铁、镍、锰等贱金属,还有大量的有机物,造成了铑的回收困难。
铑的提炼方法

铑的提炼方法
嘿,你知道铑是啥不?那可是超级厉害的贵金属呢!咱先说说铑的提炼方法吧。
可以从含铑的废料中提炼,就像从一堆沙子里找金子一样。
先把废料溶解,这就好比把一个大拼图打散。
然后通过各种化学方法,把铑给分离出来。
哇塞,这过程可得小心,要是不小心弄错一步,那可就糟糕啦!就像走钢丝一样,得小心翼翼。
说到过程中的安全性和稳定性,那可太重要啦!这就像开车得系安全带一样。
如果不注意安全,那可不得了。
在提炼过程中,得严格遵守操作规程,不然随时可能出危险。
稳定性也不能忽视,要是过程不稳定,那结果肯定不靠谱。
铑的应用场景那可多了去啦!在汽车尾气净化、化工、电子等领域都有大用。
为啥呢?因为铑超级稳定,性能超棒。
这就好比一个万能工具,啥都能搞定。
它的优势也很明显,耐腐蚀、耐高温,简直无敌啦!
给你举个实际案例吧。
有个工厂用铑来净化汽车尾气,效果那叫一个好。
以前尾气污染严重,现在干净多了。
这就像给汽车戴上了一个超级口罩。
总之,铑的提炼虽然不容易,但价值巨大。
只要小心操作,就能发挥它的大作用。
三元催化器提取铂钯铑的流程

三元催化器提取铂钯铑的流程下载温馨提示:该文档是我店铺精心编制而成,希望大家下载以后,能够帮助大家解决实际的问题。
文档下载后可定制随意修改,请根据实际需要进行相应的调整和使用,谢谢!并且,本店铺为大家提供各种各样类型的实用资料,如教育随笔、日记赏析、句子摘抄、古诗大全、经典美文、话题作文、工作总结、词语解析、文案摘录、其他资料等等,如想了解不同资料格式和写法,敬请关注!Download tips: This document is carefully compiled by theeditor. I hope that after you download them,they can help yousolve practical problems. The document can be customized andmodified after downloading,please adjust and use it according toactual needs, thank you!In addition, our shop provides you with various types ofpractical materials,such as educational essays, diaryappreciation,sentence excerpts,ancient poems,classic articles,topic composition,work summary,word parsing,copy excerpts,other materials and so on,want to know different data formats andwriting methods,please pay attention!三元催化器是一种用于减少汽车尾气排放的装置,其中含有铂、钯、铑等贵金属。
三元催化器提炼铑的方法

三元催化器提炼铑的方法1. 引言三元催化器是一种常用于汽车尾气处理的催化剂,其中的铑是关键成分之一。
铑在催化剂中具有良好的抗高温和耐腐蚀性能,能够有效地促进废气中有害物质的转化。
本文将介绍三元催化器提炼铑的方法,包括原料准备、催化剂制备、铑的分离和纯化等步骤。
2. 原料准备三元催化器通常由稀土氧化物(如氧化锆、氧化镧等)、贵金属(如铑、钯、铂等)和载体材料(如γ-Al2O3等)组成。
为了提炼铑,需要先将三元催化器进行分解,得到其中的贵金属部分。
原料准备包括以下步骤:•获得废弃或过期的三元催化器;•将三元催化器放入高温炉中进行热解,使其分解成贵金属颗粒;•将热解后得到的贵金属颗粒进行混合均匀,以便后续的催化剂制备。
3. 催化剂制备铑的提炼需要通过制备催化剂来进行。
催化剂的制备步骤如下:•将混合均匀的贵金属颗粒与适量的稀土氧化物和载体材料一同加入到球磨罐中;•在球磨罐中进行球磨操作,使得各种成分充分混合,并形成均匀的混合物;•将球磨后得到的混合物进行干燥,以去除其中的水分;•将干燥后的混合物放入高温炉中进行焙烧,使其形成结晶性较好、颗粒较大的催化剂。
4. 铑的分离经过上述步骤得到的催化剂中含有铑、钯和铂等贵金属。
为了提取纯度较高的铑,需要对催化剂进行分离。
铑的分离步骤如下:•将催化剂放入溶液中,添加适量盐酸或硝酸等强酸,使其发生溶解反应;•加入过量氯化亚铜溶液,使铑以[RhCl6]3-的形式沉淀下来;•将沉淀的铑用去离子水洗涤,去除杂质;•将洗涤后的铑沉淀用氨水溶解,得到铑的氨络合物;•通过加热或其他方法将氨络合物转化为铑金属。
5. 铑的纯化经过上述步骤得到的铑金属仍然可能含有少量杂质,需要进行纯化处理。
铑的纯化步骤如下:•将铑金属放入稀硝酸中进行溶解;•加入适量盐酸和过量亚硫酸钠溶液,使其中的杂质以沉淀形式被去除;•将溶液过滤,得到纯净的含有铑离子的溶液;•通过电解、水合物还原或其他方法将含有铑离子的溶液转化为纯净的金属铑。
失效三元催化剂中铂族金属提取回收方法

失效三元催化剂中铂族金属提取回收方法汽车尾气排放一直是环境治理的重点之一,近来年随着汽车工业的飞速发展,汽车尾气排放标准日益严苛。
铂、钯、铑三元催化剂具有高活性、高选择性、高热稳定性等良好性能,能有效去除汽车尾气中的CO、HC及NOx等污染物,是较为理想的汽车尾气净化催化剂,自20世纪90年代以来得到广泛应用。
三元催化剂中铂族金属的含量约为 1.5-2g/kg,而我国铂族金属自然资源贫瘠,铂族金属矿的平均品位仅为0.796 g/t,富矿品位2.33g/t,因此,从失效的催化剂中提取铂族金属作为再生资源回收利用意义重大。
标签:湿法溶解;火法冶金;其它方法;三元催化剂;铂族金属从失效三元催化剂中回收铂族金属的方法分为提取富集和精炼提纯两步。
第一步通常是采用湿法或火法提取得到铂族金属的富集物;第二步将富集物中的铂、钯、铑进一步分离提纯,目前分离提纯的工艺技术已经较为成熟,不再赘述。
以下着重探讨提取富集的一些工艺方法:湿法溶解、火法冶金、加压氰化法、氯化干馏法,以及湿-火法联用等。
1 湿法溶解1.1 载体溶解法此法可处理以γ-Al2O3为载体的粒状和压制的催化剂,原理是利用铂族金属与载体γ-Al2O3对浸出剂反应活性的差异,用酸将γ-Al2O3溶解,不溶的铂族金属留在滤渣中。
之后再对滤渣中的铂族金属进行化学法分离提纯。
载体溶解法的优点是成本低、回收率高,副产品硫酸铝可再利用。
周俊等人对硫酸盐化焙烧-水浸出溶解法进行了研究,最优工艺条件下,Pt、Pd、Rh的回收率分别达到97%、99%和96%。
但是此法仅适用于γ-Al2O3为载体的催化剂,而目前应用的汽车尾气净化催化剂95%以上都是以堇青石为载体的催化剂,因此此法的局限性较大。
1.2 催化剂全溶解法此法也仅适用于处理以γ-Al2O3为载体的废催化剂。
原理是通过在溶解过程中提高浸出液的氧化气氛,将γ-Al2O3载体及活性成分全部溶解,得到含有贱金属和铂族金属的溶液,再通过离子交换树脂将溶液中的铂族金属富集回收,之后分离提纯得到Pt、Pd、Rh。
三元催化回收方案

三元催化回收方案一、背景介绍三元催化是指由铂、钯和铑组成的一种催化剂,其在汽车尾气处理中有着广泛的应用。
然而,这些贵重金属的回收利用率并不高,造成了资源浪费和环境污染问题。
二、三元催化回收方案1. 催化剂分离将废旧的三元催化剂进行分离,将其中含有贵重金属的部分进行回收。
这一步骤需要使用化学方法进行分离,如溶解、沉淀等。
2. 贵重金属提取将分离出来的含有贵重金属的部分进行提取。
可以使用电解法、还原法等方法对铂、钯和铑进行提取。
3. 二次利用将提取出来的贵重金属重新加入到新生产的三元催化剂中。
这样可以降低生产成本,并且减少对自然资源的消耗。
三、具体方案实施步骤1. 催化剂分离:将废旧催化剂加入到装有溶液(如盐酸)中,使其完全溶解。
然后加入沉淀剂(如氢氧化钠),待沉淀剂与盐酸反应后,将沉淀物过滤出来,即可得到含有贵重金属的部分。
2. 贵重金属提取:将分离出来的含有贵重金属的部分加入到电解槽中,加入一定量的电解液(如氯化铂酸钠),然后进行电解。
通过电解,铂、钯和铑会在阳极上析出,可以用化学方法进一步提纯。
3. 二次利用:将提取出来的贵重金属与新生产的三元催化剂进行混合,然后再进行成型。
这样可以降低生产成本,并且减少对自然资源的消耗。
四、方案优势1. 节约资源:通过回收三元催化剂中的贵重金属,可以减少对自然资源的消耗。
2. 降低成本:二次利用提取出来的贵重金属可以降低生产成本。
3. 减少污染:回收利用废旧催化剂中的贵重金属可以减少环境污染。
五、方案实施难点1. 催化剂分离:由于三元催化剂中还含有其他材料(如氧化铝、氧化钇等),因此分离过程需要一定的技术支持。
2. 贵重金属提取:提取贵重金属时,需要选择适当的电解液,并且需要进行多次提纯才能得到高纯度的铂、钯和铑。
3. 二次利用:将提取出来的贵重金属与新生产的三元催化剂进行混合,需要控制好比例,否则会影响催化剂性能。
六、结论通过对三元催化剂回收利用,可以减少对自然资源的消耗,降低生产成本,并且减少环境污染。
- 1、下载文档前请自行甄别文档内容的完整性,平台不提供额外的编辑、内容补充、找答案等附加服务。
- 2、"仅部分预览"的文档,不可在线预览部分如存在完整性等问题,可反馈申请退款(可完整预览的文档不适用该条件!)。
- 3、如文档侵犯您的权益,请联系客服反馈,我们会尽快为您处理(人工客服工作时间:9:00-18:30)。
报废汽车催化剂中铑的提取与富集三元催化器,是安装排气系统中最重要的机外净化装置,它可将汽车尾气排出的CO、HC和NOx等有害气体通过氧化和还原作用转变为无害的二氧化碳、水和氮气。
当高温的汽车尾气通过净化装置时,三元催化器中的净化剂将增强CO、HC和NOx三种气体的活性,促使其进行一定的氧化-还原化学反应,其中CO在高温下氧化成为无色、无毒的二氧化碳气体;HC化合物在高温下氧化成水(H20)和二氧化碳;NOx还原成氮气和氧气。
三种有害气体变成无害气体,使汽车尾气得以净化。
湿法回收用硫酸或于压力下用氢氧化钠在碱性介质内进行分解,使载体溶解。
溶解后贵金属留在残渣内,再用氯气和盐酸浸出,使铂族金属进入溶液。
在碱法中,所含SiO2不溶解全部留下来,从而妨碍了对贵金属的进一步加工处理。
用这类方法再生块状载体并不可取,因为在催化剂有效使用期间γ-Al2O3已转变为不溶的α- Al2O3。
而另一方面,各种溶解贵金属的方法及贵金属的回收率有较大的变化幅度,这些都是众所周知的,例如用盐酸和氯气、盐酸和硝酸或盐酸和过氧化氢等溶解方法。
所有这些方法的主要问题之一,就在于很难将铂族金属与有色金属在稀溶液实现分离。
这些方法的回收率,尤其是铑的回收率不能令人满意。
湿法冶金再生过程的负面效应可归纳如下:①废水数量过大;②浸出过的载体扔弃后有待堆放;③损失贵金属;④铝酸盐母液硫酸铝溶液不易利用。
它们的优点是:工作温度低;在贱金属含量低的情况下贵金属含量易于监控并且沉淀过程易于进行。
火法回收通常火法回收汽车尾气催化剂涉及陶瓷载体的熔炼同时与贵金属在金属捕收剂内的富集。
载体在不损失贵金属的情况下形成熔渣,对该过程至关重要。
氧化铝颗粒的熔点过于高(大约2000℃)是个大问题。
因此,对这类材料只能加入助熔剂或采取极高的熔融温度进行造渣。
一般考虑使用铜、镍、铅和铁作铂族金属的可能捕收剂。
选用的依据是加工过程及其后的湿法化学阶段的难易。
用硫酸浸出法将贵金属—铂、钯、铑与金属捕收剂分开。
如果选用铜作捕收剂,也可以用电解法使之分离。
与湿法冶金再生废汽车催化剂相比,火法的优点要大得多:①在金属相内富集的浓度高;②贵金属回收率高;③可在有色金属常用的炉型(鼓风炉、转炉)或专用装置(如电炉)内进行再生;④副产物或残渣的产出少。
熔炼过程铜、镍或铅工业所用炉子的温度通常大约1300℃,因此不十分适于熔化陶瓷基汽车尾气催化剂。
这种炉子用焦碳、煤气、燃油或富氧空气加热。
大的熔炼厂对额外处理这类材料,肯定不存在任何问题。
如果其进料量不足工厂总进料量的1%,则对熔炼过程不会产生任何影响。
故而一方面,在这样大的炉子内借众所周知的冶炼方法处理含贵金属材料的真正优点是冶炼和处理进料成本低,但另一方面又存在不能以有效的回收率和高的产率回收贵金属特别是铑。
铂族金属的稀释过分和造渣量过大。
这种情况表明,后续的铂族金属回收与精炼等富集过程将需要更高的成本。
获取纯金属是一个漫长而艰巨的过程。
故而该法已被许多厂家摒弃。
摘要:本文研究了催化剂预处理对酸性氯酸盐水氯化法提取报废汽车催化剂中铑的影响,并研究了氯化提取液中铑的锌粉置换。
结果表明,优化条件下,O2和H2预处理可以使铑的提取率由55.9%增加到82.7%。
锌粉置换过程研究了反应时间、锌粉用量对铑置换率的影响,结果表明,优化的锌粉用量和反应时间分别为20g/L和40分钟,在此条件下铑的置换率为85.6%。
全世界85% Rh用于汽车尾气净化催化剂的制造[1]。
自1999年以来,我国已销售了3000多万辆带有三元催化转化器的机动车,汽车催化剂中铑的总用量约在10t~20t之间。
因此,作为二次资源,从失效汽车尾气催化剂中回收利用Rh受到了极大重视[2]。
此工作研究了催化剂预处理对水氯化法提取铑的影响,水氯化法用酸性氯酸钠溶液做铑的提取剂,这个工作国内外未见报道。
同时本工作还研究了上述氯化提取液中铑的锌粉置换。
目前已报道了许多从提取液中回收铂族金属方法, 如还原沉淀法、溶剂萃取法、离子交换法、等离子熔炼法等[3-5]。
1 实验部分1.1仪器与主要试剂HH-S 数显恒温水浴箱, 温度误差±1℃,CJ-882A智能数显磁力搅拌器,UV765紫外可见分光光度计,DHG-9023A型电热鼓风干燥箱。
实验所用盐酸,硫酸,双氧水和锌粉均为分析纯,实验用水均为去离子水。
实验中的原料来自丰田报废汽车催化剂,经破碎、烘干、筛分的。
试验中所用原料粒度在200-250目。
原料的化学组成见表1。
表1 报废汽车催化剂组分Table 1 C hemical compositions of the auto-catalyst used inthis work成分Rh Pt Pd SiO2MgO Al2O3CeO2P2O5La2O3%(w/w)0.016 0.0370.06327.356.8439.157.9 4.33 3.621.2实验方法称取10 g粒度在200-250目数催化剂于特定气氛中进行预处理(先是氧气预处理:O2流量为200ml/min;后是氢气预处理:H2流量为200 ml/min)。
一个典型的氯化提取过程如下:将10g汽车催化剂放入250ml三口烧瓶中,加入100 ml混合液(3 mol/L盐酸和5mol/L 硫酸),加热至95℃后, 加入3mL 过氧化氢,磁力搅拌速率为230 r/min ,再将2mol/L 的NaClO 3溶液20ml 缓慢滴加入三口烧瓶中, 反应3小时后停止加热搅拌,静置冷却后过滤,通过0.4μm 孔径薄膜,得到氯化提取液约120mL 。
氯化提取实验积累了一大瓶大约14升这样的氯化提取液,提取液中铑的浓度为1.98 ppm 。
做置换沉淀实验时,每次取50ml 氯化提取液,放入一个250 mL 三口烧瓶中,烧瓶中也放入一个聚四氟搅拌子。
将烧瓶置于一个可控温的水浴锅中。
水浴锅置于一个32cm ×32cm 台面的磁力搅拌器上,搅拌速率可数显。
事先向溶液中通入氩气以排除溶解氧。
然后向浸取液中精确加入定量的锌粉,在一定温度和搅拌速率下反应,过滤,测量滤液体积和滤液中铑离子浓度。
1.3化学分析汽车催化剂中Rh 的溶解采用国标法[6],溶解溶液中Rh 测定用ICP-AES 。
催化剂中其它元素测定采用XRF 。
沉淀前后氯化液Rh 测定采用ICP-AES 。
Rh 的沉淀置换率按式1计算:)1(100V C V C V C (%)铑离子置换率112211 ⨯-=其中1C 和2C 分别为沉淀前后氯化液中某种铂族金属离子浓度;1V 和2V 分别为沉淀前后氯化液体积。
2结果与讨论2.1 预处理的影响2.1.1 预处理温度的影响图1 预处理温度对铑提取率的影响Figure 1 Variation of extraction percentage of Rh with pretreatment temperature(O2预处理: 粒度=58-74μm, O2流速=200mL/min, O2时间=2h.H2预处理: 粒度=58-74 μm, O2流速=200mL/min, O2时间=2h. O2温度=300℃, H2流速=200mL/min, H2时间=3h)(O2-pretreatment: sample particle size = 58-74 μm, O2 flowrate = 200 mL/min, O2-pretreatment time = 2h.H2-pretreatment: sample particle size = 58-74 μm, O2 flowrate = 200 mL/min, O2-pretreatment temperature and timewere 300℃and 3h, respectively. H2flowrate = 200mL/min, H2-pretreatment time = 2h.)温度影响如图1所示,对于氢气预处理,25℃下Rh的提取率为56%。
在200-300℃,随着温度增加,Rh的提取率不断增大,在300℃达到最大值,此时铑的提取率为68.1%,温度在300-500℃,Rh提取率随温度增加而减少;之后进行氢气预处理,25℃下Rh的提取率为69.3%,在200-300℃,随着温度Rh的提取率随温度增加而增大,在300℃达到最大值,此时铑的提取率可以达到81.4%,温度在300-500℃,Rh提取率随温度增加而减少。
未经预处理的催化剂中铑的提取率为55.9%,经过O2-H2处理后,铑提取率可以达到81.4%,由此可见,O2-H2预处理可以显著提高铑的提取率。
表2 不同温度下氧化处理后汽车催化剂碳含量Table 2 The content of carbon of the auto-catalyst at different temperature after Oxidation treatment温度/℃0 300 400 500 600 碳含量/% 0.18 0.16 0.14 0.11 0.09我们推断可能是因为催化剂中含有一定量的碳和有机物,它们附着在Rh周围,通过氧气焙烧可以把它们除掉,由表2可知,原来的催化剂样品中的碳含量为0.18%(重量),随O2的热处理温度增加催化剂中的碳含量逐渐减少,使Rh充分的暴漏出来,以便于在水氯化过程中可以充分的与提取试剂接触,从而提高Rh的提取率。
Rh2O3与Cl2反应的△Gθ1/3Rh2O3(s)+Cl2(g)=2/3RhCl3(s)+1/2O2(g) (2)△Gθ与温度T的关系式为△Gθ= 0.0176T - 10.549 (kJ·mol-1) (3)2/3Rh(s)+Cl2(g)=2/3RhCl3(s) (4)△Gθ与温度T的关系式为△Gθ= 0.0386T - 33.123 (kJ·mol-1) (5)另一方面,在焙烧温度超过一定值,可能是因为Rh被部分氧化。
Robert R[7]等人的研究也表明,在温度大于200℃,Rh开始被氧化为Rh2O3。
从热力学计算(式3、式5)可知,单质铑相对于其氧化物更容易与氯气反应。
因此温度过高,铑易氧化,从而使铑提取率降低。
此外,温度过高也可导致催化剂粉末产生烧结现象,从而在水氯化过程使铑与提取液接触面减少,降低了铑的提取率。
2.1.2 预处理时间的影响图2 预处理时间对铑提取率的影响Figure 2 Variation of extraction percentage of Rh withpretreatment time(O2预处理:粒度=58-74μm, O2流速=200mL/min, O2温度=300℃. H2预处理:粒度=58-74μm, O2流速=200mL/min,O2温度=300℃, O2时间=3h, H2流速=200mL/min, H2温度=300℃.) (O2-pretreatment: sample particle size = 58-74 μm, O2 flowrate = 200 mL/min, O2-pretreatment temperature = 300℃.H2 pretreatment: sample particle size = 58-74 μm, O2 flowrate = 200 mL/min, O2-pretreatment temperature and time were 300℃and 3h, respectively. H2-pretreatment: H2 flowrate = 200 mL/min,H2-pretreatment temperature =300℃.)预处理时间的影响如图2所示,对氧气预处理:在0-3小时,铑提取率随时间的增加而逐渐增大,在3小时提取率达到最大值为69.3%,时间在3-4小时之间,铑提取率随时间的增加而不断减少;对于氢气预处理:在0-3小时之间,铑提取率随时间的增加而逐渐增大,在3小时提取率达到最大值为82.7%,时间在3-4小时之间,铑提取率趋于稳定。