2019年最新-热喷涂技术研究进展-精选文档
热喷涂技术研究进展-PPT课件

1、热喷涂技术概论
原理 热喷涂技术是一种将涂层材料(粉末或丝材) 送入某种热源(电弧、燃烧火焰、等离子体等)中 熔化, 并利用高速气流将其喷射到基体材料表面 形成涂层的工艺 。 涂层结构特点
特点
a. 能赋予基体以多种功能的表面; b. 设备轻便,可现场施工; c. 除喷焊外,对基材加热温度较低,工件 变形小,金相组织及性能变化也较小。 d. 喷涂操作的程序较少,施工时间较短,效率 高,比较经济。
微等离子喷涂
微等离子喷涂是20世纪90年代由乌克兰巴顿焊 接研究所开发的, 它的特点是具有层流等离子 射流、发射角只有2°~ 6°(普通的等离子枪的 发射角达10°~ 18°)、功率低( 1~ 3 kW )、基 体受热低、噪声小( 30~ 50 dB) , 可在极薄的基 体(如0.5mm厚的不锈钢薄板或1.0 mm 厚的锰 片)上进行喷涂。这种喷涂方法的功率虽低, 但 能量集中, 其束斑直径小于5 mm, 所以仍可喷 涂各种材料, 特别适宜制备小零件及薄壁件的 精密涂层, 且该设备重量轻, 适合于现场的维修 工作。
悬浮式等离子喷涂示意图
反应等离子喷涂
反应等离子喷涂是对真空等离子喷涂进一步改进的结果, 该方法在真空等离子喷涂过程中,在喷嘴出口处的等离子射 流中加入反应气体(如N2),反应气体与加热中的喷涂颗粒相 互作用,进而得到新的生成物。 例如,用这种方法可以获得TiN涂层,它是靠喷涂钛粉和注入 N2反应后得到的,其工作原理如图所示。TiN具有高熔点、 高硬度、耐磨、耐蚀等特点,并且还具有优良的导电性和超 导性。 反应等离子喷涂制备 TiN涂层克服了传统的物理或者化 学气相沉积(PVD及CVD)工艺 制备TiN 涂层,存在沉积速 率低、涂层厚度过薄的缺点,可制备纳米晶TiN涂层, 涂层厚度可达500µ m。
热喷涂技术论文(2)

热喷涂技术论文(2)热喷涂技术论文篇二热喷涂技术的研究现状与发展趋势【摘要】热喷涂技术拥有着巨大的发展优势,且被广泛应用在工程领域方面。
综述了热喷涂技术的研究现状以及未来的发展趋势,主要介绍了超音速火焰喷涂技术、火焰喷涂技术、电弧喷涂技术、等离子喷涂技术、冷喷涂技术与超音速电弧喷涂技术等,并简洁了这些技术的研究发展趋势与实际应用。
【关键词】热喷涂技术;研究现状;发展趋势热喷涂技术是利用某种热源使得喷涂材料受热呈现熔融或者是半熔融状态,再将其喷射到需要涂敷的基体表面,从而可以形成一层比原基体材料涂层性能优异的涂层,使得工件的表面性能更加优异,或是使得工件形成一种或多种原基体材料不具备的表面性能膜状组织结构。
热喷涂涂层具有耐磨损、隔热以及耐高温等性能,并且能够实现对出现磨损、被腐蚀的零件以及因加工出现误差的零件进行必要的有效修复。
热喷涂技术是表面工程的重要组成部分,在工业与科学技术快速发展的今天,喷涂技术在航空航天、石油化工以及机械制造等众多的领域中应用广泛。
本文主要介绍了超音速火焰喷涂技术、火焰喷涂技术、电弧喷涂技术、等离子喷涂技术、冷喷涂技术与超音速电弧喷涂技术等,并简洁了这些技术的研究发展趋势与实际应用。
1 超音速火焰喷涂技术1.1 超音速火焰喷涂的发展超音速火焰喷涂(HVOF)是在上个世纪80年代初期由普通的火焰喷涂技术发展而来的一种新型的喷涂技术。
该项技术主要是以氢、丙烯、乙炔以及煤等作为燃料,以氧气作为助燃剂,在特殊的喷嘴中进行燃烧或者是在专门的燃烧室进行燃烧,形成温度高达2000℃-3000℃,速度快至2100m/s的超音速火焰,与此同时将各类粉末送进火焰中,使得粉末粒子呈现熔化或是半熔化状态,并高速运转撞击至基体表面从而在基体表面形成涂层,此类涂层比普通火焰喷涂的涂层更加结实紧密。
1982年在美国出现了第一代超音速火焰喷涂装置,随后超音速火焰喷涂技术得到了长足的发展。
1.2 超音速火焰喷涂原理超音速火焰喷涂以氢、丙烯、乙炔以及煤等作为燃料,利用氧气作为助燃剂,在特殊的喷嘴中进行燃烧或者是在专门的燃烧室进行燃烧产生的高温高速的火焰。
热喷涂技术应用与发展调研分析
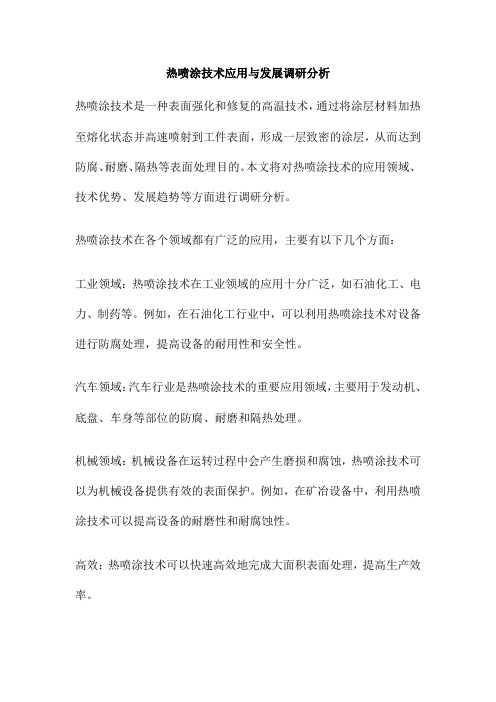
热喷涂技术应用与发展调研分析热喷涂技术是一种表面强化和修复的高温技术,通过将涂层材料加热至熔化状态并高速喷射到工件表面,形成一层致密的涂层,从而达到防腐、耐磨、隔热等表面处理目的。
本文将对热喷涂技术的应用领域、技术优势、发展趋势等方面进行调研分析。
热喷涂技术在各个领域都有广泛的应用,主要有以下几个方面:工业领域:热喷涂技术在工业领域的应用十分广泛,如石油化工、电力、制药等。
例如,在石油化工行业中,可以利用热喷涂技术对设备进行防腐处理,提高设备的耐用性和安全性。
汽车领域:汽车行业是热喷涂技术的重要应用领域,主要用于发动机、底盘、车身等部位的防腐、耐磨和隔热处理。
机械领域:机械设备在运转过程中会产生磨损和腐蚀,热喷涂技术可以为机械设备提供有效的表面保护。
例如,在矿冶设备中,利用热喷涂技术可以提高设备的耐磨性和耐腐蚀性。
高效:热喷涂技术可以快速高效地完成大面积表面处理,提高生产效率。
耐磨:热喷涂材料具有高硬度、高耐磨性等特点,可以延长设备的使用寿命。
防腐:热喷涂技术可以形成致密的涂层,有效防止腐蚀,提高设备的耐久性和安全性。
隔热:热喷涂技术可以形成一层隔热材料,有效降低设备表面的温度,提高设备的使用安全性。
经济:热喷涂技术成本较低,可以降低生产成本,提高经济效益。
随着科学技术的不断进步,热喷涂技术也在不断发展创新。
未来,热喷涂技术的发展趋势主要体现在以下几个方面:新材料的应用:随着新材料的不断涌现,热喷涂技术的材料选择范围也越来越广,未来将会有更多新型、高性能的材料应用于热喷涂技术中。
高能束技术的应用:高能束流技术如激光、等离子等在热喷涂技术中的应用将更加广泛。
这些技术的应用可以提高热喷涂层的结合强度和致密性,进一步提高表面处理的质量和效率。
智能化技术的应用:智能化技术在热喷涂技术中的应用将成为未来的发展趋势。
通过引入机器人和自动化技术,可以实现热喷涂过程的自动化和智能化控制,提高生产效率和产品质量。
(整理)热喷涂技术

摘要:介绍了热喷涂技术的特点以及分类,较为详细地介绍和分析了火焰喷涂、电弧喷涂、等离子喷涂等几种喷涂技术的特点及其应用,并对其进行了比较,最后对热喷涂技术的发展前景进行了展望。
关键词:热喷涂技术,火焰喷涂,电弧喷涂,等离子喷涂Abstract:The characteristics and classification of thermal spray technology were described. Thecharacteristics and applications of the flame spraying, arc spraying and plasma spraying were alsointroduced and analyzed in detail as well as making a comparison between them. Finally, thermalspray technology was predicted.Keywords: thermal spray technology, flame spraying, arc spraying, plasma spraying1前言高新技术的飞速发展对提高金属材料的性能、延长仪器设备中零部件的使用寿命提出了越来越高的要求。
而这两个方面的要求又面临高性能结构材料成本逐年上升的问题。
近年来,表面工程发展很快,尤其是热喷涂技术获得了巨大进展,为解决上述问题提供了一种新的方法。
热喷涂技术是利用热源将喷涂材料加热至熔化或半熔化状态,并以一定的速度喷射沉积到经过预处理的基体表面形成涂层的方法。
热喷涂技术在普通材料的表面上,制造一个特殊的工作表面,使其达到:防腐、耐磨、抗高温、抗氧化、隔热、绝缘、导电、防微波辐射等一系多种功能,使其达到节约材料,节约能源的目的,我们把特殊的工作表面叫涂层,把制造涂层的工作方法叫热喷涂[1]热喷涂技术的基本特点是具有真正的叠加效应,即多种成分及变量在同时作用和正在应用时产生的效果,远远比这些成分或变量在单独情况下产生的效果要大[2]。
热喷涂技术的发展和应用
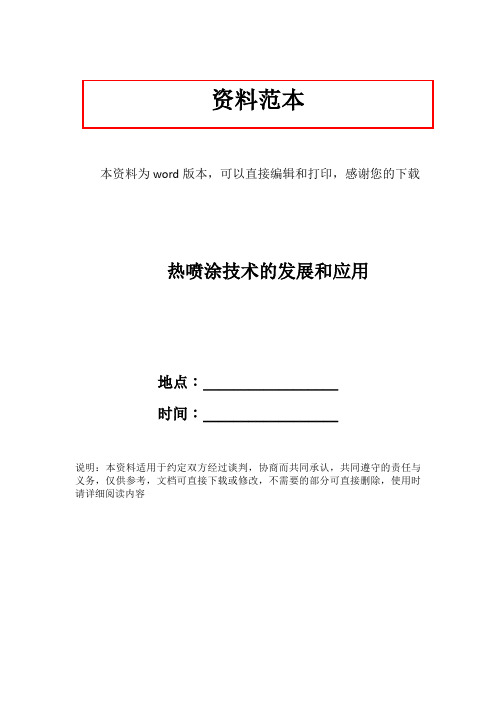
资料范本本资料为word版本,可以直接编辑和打印,感谢您的下载热喷涂技术的发展和应用地点:__________________时间:__________________说明:本资料适用于约定双方经过谈判,协商而共同承认,共同遵守的责任与义务,仅供参考,文档可直接下载或修改,不需要的部分可直接删除,使用时请详细阅读内容表面工程学(论文)班级:材科101学生姓名:宋俊伟学号:201001524125指导教师:汤峰热喷涂技术的发展和应用【摘要】主要介绍了热喷涂的基本方法、设备、材料和涂层特性;以及当前的发展动态和应用情况;并简要介绍了应用研究的前景。
【关键词】热喷涂加工技术、加工原理、应用现状、发展前景。
引言热喷涂是一种迅速发展的表面强化新工艺新技术。
它采用专用设备,利用各种热源将金属或非金属材料加热到熔化或半熔化状态,用高速气流将其吹成微小微粒并喷射到机件表面,形成覆盖涂层,以提高机件耐磨、耐蚀、耐热等性能。
热喷涂技术最早出现在上世纪早期的瑞士,随后在苏联、德国、日本、美困等圉得到了不断的发展,各种热喷涂设备的研制,新的热喷涂材料的开发,新技术的不断应用,使热喷涂涂层质量得到了不断的提高,并不断开拓新的应用领域。
目前,以火焰喷涂、超音速喷涂、电爆喷涂、电容放电喷涂、等离子喷涂为代表的热喷涂技术与设备,以及一系列喷涂喷焊粉末新材料,各种热喷涂技术趋于成熟,喷涂装置日益完善,不仅能喷金属、合金、陶瓷,还能喷涂塑料和复合材料。
近几年来电子计算机在等离子喷涂系统中的应用,使热喷涂技术达到了相当完善的地步,不仅使应用范嗣大为扩展,而且使涂层质量有了质的飞跃。
热喷涂技术不仅涉及到材料学、表面物理化学、流体力学、传热学、等离子物理等,还涉及到机械,计算机和新材料等学科,是一门交叉边缘学科。
热喷涂技术简介热喷涂技术是通过某种热源将某些材料表面加热至熔融或半熔融状态,然后喷射到涂敷的基体表面,形成一层性能优于原来基体的涂层,从而使原工件具有更加优异的表面性能,或者是使工件获得一种或几种原来基体材料不具备的表面性能膜状组织。
热喷涂技术应用及研究进展与挑战
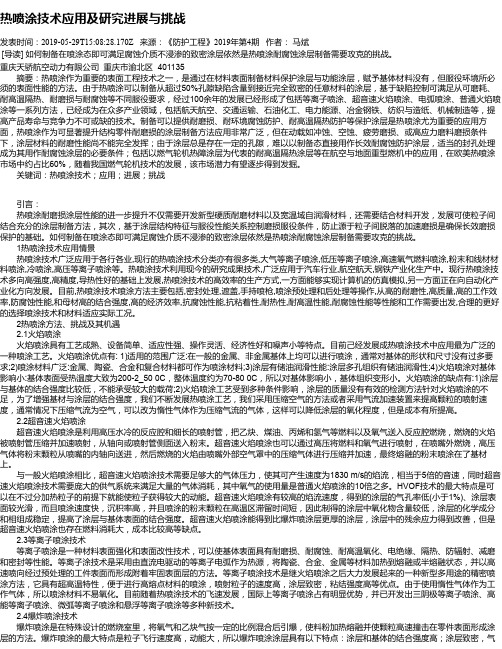
热喷涂技术应用及研究进展与挑战发表时间:2019-05-29T15:08:28.170Z 来源:《防护工程》2019年第4期作者:马斌[导读] 如何制备在喷涂态即可满足腐蚀介质不浸渗的致密涂层依然是热喷涂耐腐蚀涂层制备需要攻克的挑战。
重庆天骄航空动力有限公司重庆市渝北区 401135摘要:热喷涂作为重要的表面工程技术之一,是通过在材料表面制备材料保护涂层与功能涂层,赋予基体材料没有,但服役环境所必须的表面性能的方法。
由于热喷涂可以制备从超过50%孔隙缺陷含量到接近完全致密的任意材料的涂层,基于缺陷控制可满足从可磨耗、耐高温隔热、耐磨损与耐腐蚀等不同服役要求,经过100余年的发展已经形成了包括等离子喷涂、超音速火焰喷涂、电弧喷涂、普通火焰喷涂等一系列方法,已经成为在众多产业领域,包括航天航空、交通运输、石油化工、电力能源、冶金钢铁、纺织与造纸、机械制造等,提高产品寿命与竞争力不可或缺的技术。
制备可以提供耐磨损、耐环境腐蚀防护、耐高温隔热防护等保护涂层是热喷涂尤为重要的应用方面,热喷涂作为可显著提升结构零件耐磨损的涂层制备方法应用非常广泛,但在动载如冲蚀、空蚀、疲劳磨损、或高应力磨料磨损条件下,涂层材料的耐磨性能尚不能完全发挥;由于涂层总是存在一定的孔隙,难以以制备态直接用作长效耐腐蚀防护涂层,适当的封孔处理成为其用作耐腐蚀涂层的必要条件;包括以燃气轮机热障涂层为代表的耐高温隔热涂层等在航空与地面重型燃机中的应用,在欧美热喷涂市场中约占比60%,随着我国燃气轮机技术的发展,该市场潜力有望逐步得到发掘。
关键词:热喷涂技术;应用;进展;挑战引言:热喷涂耐磨损涂层性能的进一步提升不仅需要开发新型硬质耐磨材料以及宽温域自润滑材料,还需要结合材料开发,发展可使粒子间结合充分的涂层制备方法,其次,基于涂层结构特征与服役性能关系控制磨损服役条件,防止源于粒子间脱落的加速磨损是确保长效磨损保护的基础。
如何制备在喷涂态即可满足腐蚀介质不浸渗的致密涂层依然是热喷涂耐腐蚀涂层制备需要攻克的挑战。
04热喷涂技术

机电工程学院 赵占西
3
第4章 热喷涂技术
一、热喷涂技术原理与特点
4.1 热喷涂技术
1.热喷涂原理(分类:根据热源的不同)
2019/11/2
机电工程学院 赵占西
4
第4章 热喷涂技术
一、热喷涂技术原理与特点
4.1 热喷涂技术
2.热喷涂技术的特点(优点)
(1)各种基体___各种涂层:金属、陶瓷、工程塑料 等既可用作热喷涂材料又都可以作为热喷涂的基材。
②延长铝和锌防护涂层的寿命;
③在某些机械部件中防止液体和压力的密封泄露;
④防止污染或研磨碎屑碎片进入涂层;
⑤保持陶瓷涂层的绝缘强度。
2019/11/2
机电工程学院 赵占西
16
第4章 热喷涂技术
一、热喷涂技术原理与特点
4.1 热喷涂技术
7.热喷涂工艺流程(常用封孔剂)
类型
封孔剂
非干燥型 石蜡、油脂、油
一、热喷涂技术原理与特点 7.热喷涂工艺流程(粗化要求)
4.1 热喷涂技术
2019/11/2
机电工程学院 赵占西
13
第4章 热喷涂技术
一、热喷涂技术原理与特点
7.热喷涂工艺流程 (粘结底层)
4.1 热喷涂技术
2019/11/2
机电工程学院 赵占西
14
第4章 热喷涂技术
一、热喷涂技术原理与特点 7.热喷涂工艺流程(影响因素)
一、热喷涂技术原理与特点
2.热喷涂技术的特点(缺点) 热效率低; 材料利用率低; 涂层与基材结合强度较低。
4.1 热喷涂技术
2019/11/2
机电工程学院 赵占西
6
第4章 热喷涂技术
一、热喷涂技术原理与特点
热喷涂材料的研究和开发

热喷涂材料的研究和开发随着人们生活水平的不断提高,高性能材料逐渐成为了各个领域的研究重点。
其中,热喷涂技术(HVOF)作为一种新型的涂覆材料技术,日益得到大家的重视。
它不仅可以为材料表面提供良好的保护性能,还可以改善材料的强度、耐磨性和附着力等物理性能。
本文将探究热喷涂材料的研究和开发,以期为相关领域的研究人员提供一些有价值的参考。
一、热喷涂技术的原理热喷涂技术是一种通过高温气流将粉末状材料喷射到被涂覆物表面的工艺。
它主要由热喷涂设备和喷涂材料两部分组成。
喷涂材料包括金属涂料、陶瓷涂料、聚合物涂料和生物涂料等。
其中,金属涂料和陶瓷涂料是应用最为广泛的两种材料。
在喷涂过程中,热喷涂设备将粉末状的金属或陶瓷材料喷射到被涂覆物的表面,产生高速热流和热冲击。
荷载作用下材料表面的块状粒子会在接触面产生相互作用产生挤压变形和塑性变形,这部分形变随后就会转化为应变能,并通过产生的各种塑性流动来向整体变形传递,从而产生整体的形变。
在热喷涂技术的使用过程中,使用曲线光谱重点关注于热喷涂后的材料表面和形态。
通过对材料表面和形态的分析,我们可以推断出材料的物理性能、化学性质和微观结构等方面的信息。
二、热喷涂材料的研究与开发随着热喷涂技术的发展,近年来对热喷涂材料的研究与开发也得到了迅速发展。
热喷涂材料的研究领域广泛,包括化学、物理、机械、材料科学等不同领域。
其主要目标是优化材料的物理性能,以满足不同领域的需求。
其中,以下几点是热喷涂材料研究方向的集中:1. 金属涂料:金属涂料是热喷涂材料研究的重点。
其主要功能包括提供高耐磨性、耐磨性、防腐性和化学稳定性等。
目前,大多数金属涂料是由铝、锌、铜、钛、镍等单一或合金材料组成。
相比于其他材料,金属涂料更可靠、更精准,并且能够在各种温度和环境中工作。
2. 陶瓷涂料:陶瓷涂料在热喷涂技术中的应用也很广泛。
其应用不仅可以提高原材料的防磨损和防腐蚀性能,还可以增加材料的粘附性和抗剥离性能。
热喷涂技术的最新研究应用现状
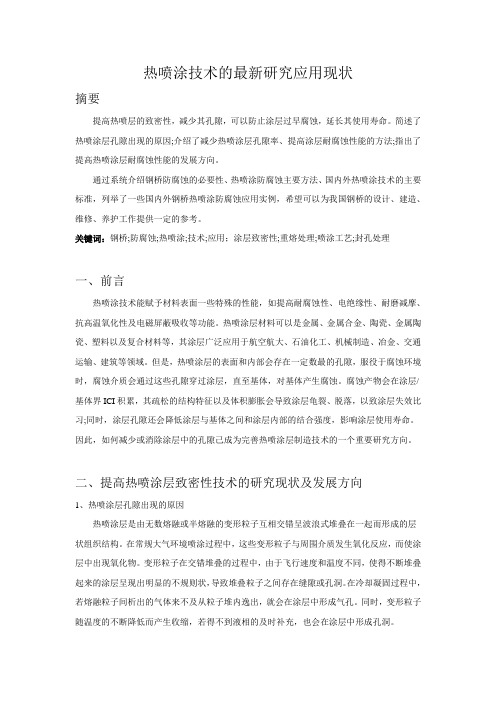
热喷涂技术的最新研究应用现状摘要提高热喷层的致密性,减少其孔隙,可以防止涂层过早腐蚀,延长其使用寿命。
简述了热喷涂层孔隙出现的原因;介绍了减少热喷涂层孔隙率、提高涂层耐腐蚀性能的方法;指出了提高热喷涂层耐腐蚀性能的发展方向。
通过系统介绍钢桥防腐蚀的必要性、热喷涂防腐蚀主要方法、国内外热喷涂技术的主要标准,列举了一些国内外钢桥热喷涂防腐蚀应用实例,希望可以为我国钢桥的设计、建造、维修、养护工作提供一定的参考。
关键词:钢桥;防腐蚀;热喷涂;技术;应用;涂层致密性;重熔处理;喷涂工艺;封孔处理一、前言热喷涂技术能赋予材料表面一些特殊的性能,如提高耐腐蚀性、电绝缘性、耐磨减摩、抗高温氧化性及电磁屏蔽吸收等功能。
热喷涂层材料可以是金属、金属合金、陶瓷、金属陶瓷、塑料以及复合材料等,其涂层广泛应用于航空航大、石油化工、机械制造、冶金、交通运输、建筑等领域。
但是,热喷涂层的表面和内部会存在一定数最的孔隙,服役于腐蚀环境时,腐蚀介质会通过这些孔隙穿过涂层,直至基体,对基体产生腐蚀。
腐蚀产物会在涂层/基体界ICI积累,其疏松的结构特征以及体积膨胀会导致涂层龟裂、脱落,以致涂层失效比习;同时,涂层孔隙还会降低涂层与基体之间和涂层内部的结合强度,影响涂层使用寿命。
因此,如何减少或消除涂层中的孔隙己成为完善热喷涂层制造技术的一个重要研究方向。
二、提高热喷涂层致密性技术的研究现状及发展方向1、热喷涂层孔隙出现的原因热喷涂层是由无数熔融或半熔融的变形粒子互相交错呈波浪式堆叠在一起而形成的层状组织结构。
在常规大气环境喷涂过程中,这些变形粒子与周围介质发生氧化反应,而使涂层中出现氧化物。
变形粒子在交错堆叠的过程中,由于飞行速度和温度不同,使得不断堆叠起来的涂层呈现出明显的不规则状,导致堆叠粒子之间存在缝隙或孔洞。
在冷却凝固过程中,若熔融粒子间析出的气体来不及从粒子堆内逸出,就会在涂层中形成气孔。
同时,变形粒子随温度的不断降低而产生收缩,若得不到液相的及时补充,也会在涂层中形成孔洞。
纳米热喷涂技术和涂层研究的进展
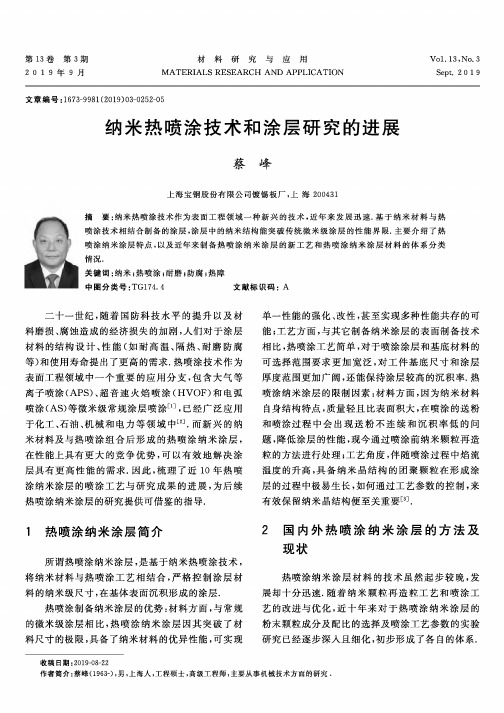
第13卷第3期2 0 19年9月材料研究与应用MATERIALS RESEARCH AND APPLICATIONVol. 13,No. 3Sept. 2 0 19文章编号:1673-9981(2019)03-0252-05纳米热喷涂技术和涂层研究的进展蔡峰上海宝钢股份有限公司镀锡板厂,上海200431摘要:纳米热喷涂技术作为表面工程领域一种新兴的技术,近年来发展迅速.基于纳米材料与热 喷涂技术相结合制备的涂层,涂层中的纳米结构能突破传统微米级涂层的性能界限.主要介绍了热 喷涂纳米涂层特点,以及近年来制备热喷涂纳米涂层的新工艺和热喷涂纳米涂层材料的体系分类 情况.关键词:纳米;热喷涂;耐磨;防腐;热障中图分类号:TG174.4文献标识码:A二十一世纪,随着国防科技水平的提升以及材 料磨损、腐蚀造成的经济损失的加剧,人们对于涂层材料的结构设计、性能(如耐高温、隔热、耐磨防腐 等)和使用寿命提出了更高的需求•热喷涂技术作为 表面工程领域中一个重要的应用分支,包含大气等 离子喷涂(APS)、超音速火焰喷涂(HVOF)和电弧 喷涂(AS)等微米级常规涂层喷涂丙,已经广泛应用 于化工、石油、机械和电力等领域中⑵•而新兴的纳米材料及与热喷涂组合后形成的热喷涂纳米涂层,在性能上具有更大的竞争优势,可以有效地解决涂 层具有更高性能的需求.因此,梳理了近10年热喷涂纳米涂层的喷涂工艺与研究成果的进展,为后续 热喷涂纳米涂层的研究提供可借鉴的指导.1热喷涂纳米涂层简介所谓热喷涂纳米涂层,是基于纳米热喷涂技术,将纳米材料与热喷涂工艺相结合,严格控制涂层材 料的纳米级尺寸,在基体表面沉积形成的涂层.热喷涂制备纳米涂层的优势:材料方面,与常规 的微米级涂层相比,热喷涂纳米涂层因其突破了材料尺寸的极限,具备了纳米材料的优异性能,可实现单一性能的强化、改性,甚至实现多种性能共存的可 能;工艺方面,与其它制备纳米涂层的表面制备技术相比,热喷涂工艺简单,对于喷涂涂层和基底材料的可选择范围要求更加宽泛,对工件基底尺寸和涂层 厚度范围更加广阔,还能保持涂层较高的沉积率•热喷涂纳米涂层的限制因素:材料方面,因为纳米材料 自身结构特点,质量轻且比表面积大,在喷涂的送粉和喷涂过程中会出现送粉不连续和沉积率低的问 题,降低涂层的性能,现今通过喷涂前纳米颗粒再造 粒的方法进行处理;工艺角度,伴随喷涂过程中焰流温度的升高,具备纳米晶结构的团聚颗粒在形成涂 层的过程中极易生长,如何通过工艺参数的控制,来有效保留纳米晶结构便至关重要闪.2国内外热喷涂纳米涂层的方法及现状热喷涂纳米涂层材料的技术虽然起步较晚,发展却十分迅速•随着纳米颗粒再造粒工艺和喷涂工艺的改进与优化,近十年来对于热喷涂纳米涂层的 粉末颗粒成分及配比的选择及喷涂工艺参数的实验研究已经逐步深入且细化,初步形成了各自的体系.收稿日期:2019-08-22作者简介:蔡峰(1963-),男,上海人,工程硕士,高级工程师,主要从事机械技术方面的研究.第13卷第3期蔡峰:纳米热喷涂技术和涂层研究的进展2532.1热喷涂纳米涂层的喷涂工艺为了保证涂层材料纳米结构的完整性,保证喷涂后的涂层具有纳米材料的优异性能,在常规喷涂工艺的基础上,三个新兴的方法分为为悬浮液等离子喷涂(SPS),高速火焰喷涂(HVOF)与冷动力喷涂(CGDS).2.1.1悬浮液等离子喷涂(SPS)悬浮液等离子喷涂(SPS),喷涂的原料粉末为纳米陶瓷粉末的悬浮液,通过等离子喷涂方式进行喷涂、沉积,最终得到含有纳米结构的微纳级涂层.其独特的工作原理为通过送粉器将喷涂前的悬浮液送至等离子喷嘴内部,悬浮液在高压下发生分散或者雾化后进入到等离子的焰流中,在高温高速的焰流中发生蒸发和部分烧结,并在焰流喷出的过程中发生剪切变形,进一步缩小悬浮液液滴的尺寸,同时悬浮液在飞行过程中蒸发吸热,可以保留部分氧化物纳米粉末的结构,最终形成具有纳米结构的氧化物或氧化物复合材料的涂层.由于等离子喷涂焰流温度足够高,因此适用于氧化物或碳化铸纳米粉末材料,如WC,ZrO2,A12O3-Y2O3等.2.1.2超音速火焰喷涂(HVOF)超音速火焰喷涂(HVOF),是以氧气和煤油为燃烧介质,纳米粉末材料在高压高速的焰流中分散,纳米粉末材料以半融化状态撞击基体表面形成纳米结构涂层.工作原理是通过送粉系统将纳米喷涂粉末材料送至喷枪筒,氧气和煤油在燃烧室中点火,连续燃烧喷出的高速焰流流经喷枪筒,通过径向送粉的方式,将纳米粉末材料送入高温(3000K)高速(700m/s)的焰流中,纳米粉末材料在飞行过程中融化、分散,最终撞击基体表面,形成纳米涂层•因为超音速火焰喷涂的温度在3000K附近,不适合易氧化的单一金属材料,常用于含有碳化物的金属或合金复合纳米材料,如WC-Co,MCrAlY, Al2O3-SiC等.2.1.3冷动力喷涂(CGDS)冷动力喷涂,顾名思义,利用空气动力学规律,纳米粉末材料通过轴向送粉,送入到低温(600°C)、高压高速(300-1200m/s)的焰流中充分混合,在完全固态的状态下直接撞击基体表面,形成具有较大塑性形变的纳米涂层.其工作原理为将纳米粉末材料通过送粉系统送至通有高速压缩气体的德拉瓦尔喷嘴处,因被加热的喷嘴温度仅为600°C左右,远低于纳米粉末材料的熔点,所以纳米粉末材料在低温和高速的焰流中被加热和加速,最终以固态撞击基体,形成塑性形变较大的纳米涂层.正因为喷枪的加速温度较低,且纳米粉末在焰流中飞行时间短,因此其纳米结构得以保留,形成含有纳米结构的涂层•因为冷动力喷涂具有低温高速的特点,因此需纳米粒子必须具有较好的塑性形变能力,该法更适合单一金属或合金的纳米粉末材料,包括Al,Zn,Cu,Ag,W,Mo,Ti等⑷.2.2喷涂纳米功能性涂层近十年来,人们对于热喷涂功能性纳米涂层的研究已经逐渐深入,比较成体系的研究主要集中在纳米结构耐磨涂层,纳米结构防腐涂层和纳米结构热障涂层.2.2.1热喷涂纳米结构耐磨涂层C.R.C.Lima囚等人采用超音速火焰喷涂和电弧喷涂,在相同的喷涂参数条件下,成功制备了纳米WC-10Co4Cr和WC-12CO复合涂层,涂层厚度分别为500pm和450pm,并进行摩擦磨损性能的对比,其磨损损失量如图1所示•结果表明,超音速火焰喷涂制备的纳米涂层的耐磨损性能更好,其中以纳米WC-10Co4Cr的复合涂层性能最好,比超音速火焰喷涂制备的WC-12Co复合涂层的耐磨性高5倍,即图1基材、纳米WC-12CO和WC-10Co4Cr复合涂层磨损体积损失量对比Fig.1Comparison of wear volume loss of substrate, nano WC-12Co and WC-10Co4Cr compositecoatings254材料研究与应用2019李万青⑷等人采用超音速等离子喷涂方法,在0Crl3Ni5Mo马氏体不锈钢基底上,在相同的喷涂工艺参数下,分别喷涂厚度均为(300+15)M m的WC-17Co纳米和微米级涂层,并对二种涂层的常规性能如孔隙率、结合强度和耐磨性进行了检测:从孔隙率角度,纳米级涂层和微米级涂层的平均孔隙率分别为0.64%和0.93%,即纳米涂层的孔隙率仅为微米级涂层孔隙率的2/3;结合强度方面,纳米级涂层和微米级涂层的平均结合强度分别为69.2MPa 和56MPa,即纳米级涂层的结合强度性能比微米级提升了23.5%;最后,耐磨性能分析,二者涂层均属于轻微的磨粒磨损形式,如图2所示,测试表明二者的磨损量分别为基体磨损量的10.9%和14.9%,纳米涂层的磨损量仅为微米涂层的73.15%.图2纳米涂层(a)、微米涂层(b)和基体(c)的摩擦磨损形貌图Fig.2Friction and wear profile of nano-coating(a),micro-coating(b)and matrixs(c)石绪忠囚等人采用大气等离子喷涂方法,在相同的工艺参数条件下,以钢为基体进行了纳米Al2O3/TiO2复合纳米涂层和微米涂层的制备,并针对二种涂层的常规性能进行测试.结果表明,纳米级Al2O3/TiO2的在大载荷球盘模式下的摩擦磨损性能优异,4h试验时间内,涂层的磨损率为3.68X IO-?g/h(过程失重与时间的关系如图3所示),且摩擦系数的稳定值在0.37-0.40,表明纳米A12O3/ TiO2复合涂层比常规的微米级复合涂层具有更加优异的耐磨性能.Time/h图3纳米Al2O3/TiO2复合涂层磨损量与时间的对应关系Fig.3Corresponding relationship between wear amountment and time of nano-Al2O3/TiO2composite coatingJianhui Yan闪等人利用空气等离子喷涂,在镰基合金上制备以纳米ZrOz为添加剂的二硅化钳(MoSi2)基复合涂层.通过SEM和XRD的测试证明:ZrO2-MoSi2复合涂层中确实存在纳米ZrO2结构,并在T-MoSi2和H-MoSi2相之间相互转化;针对复合涂层的高温摩擦磨损性能,将该复合涂层与1100°C下的纯MoSi2涂层进行比较,ZrO2-MoSi2复合涂层的耐磨性最佳.结果表明,纳米ZrOz的加入可明显提高MoSi2涂层的耐磨性.上海英佛曼纳米科技股份有限公司采用100 nm以下的WC-12CO粉末用超音速火焰喷涂制备的纳米结构的涂层,涂层厚度为200~250p.m,涂层结合力为100MPa,其耐磨损性能从微米涂层的100万转磨损至坏提高到1000万转无损坏,使得攀钢输送辐道的过钢量从9万吨提高到了280万吨,使用寿命提高了30多倍.2.2.2热喷涂纳米结构防腐涂层刘晓明⑷等人采用超音速火焰喷涂方法,在20G钢表面成功制备出纳米Fe-Al/Cr3C2复合涂层,为了突出涂层抗高温腐蚀的性能,分别测试了为微米、纳米级的Fe-Al/Cr3C2复合涂层的参数,并对腐蚀动力学曲线进行拟合,测算出二者腐蚀速率的差距(图4).结果表明,在经140h的中性盐雾试验后,纳米级的Fe-Al/Cr3C2复合涂层的腐蚀速率仅第13卷第3期蔡峰:纳米热喷涂技术和涂层研究的进展255为微米级的29.5%,这意味着在同样的腐蚀环境中纳米级Fe-Al/Cr3C2复合涂层的寿命是微米级涂层寿命的3倍.图4Fe-Al/Cr3C2复合涂层动力学曲线的拟合腐蚀速率Fig.4Fitting corrosion rate of kinetic curve of Fe-Al/ Cr3C2composite coating李威霆匚诃等人利用悬浮液热喷涂方法,成功制备出纳米Al/TiO2复合梯度涂层•通过SEM表征涂层结构发现,微米级的团聚体中依然存在10〜20 nm的TiO2纳米级结构,因此确保了实验的成功.对于防腐蚀性能的测试,经过120h的中性盐雾试验发现,带有Al/TiO2的纳米梯度涂层几乎没有显著缺陷,整体状况良好,具有更长的使用寿命.2.2.3热喷涂纳米结构热障涂层R.S.Lima[11]等人利用大气等离子喷涂,制备纳米ZrO2-7wt.%¥203复合涂层•在空气中、在1400°C下将涂层进行热处理1,5和20h后,针对其导热性能进行了测试.结果发现,与密集区域相比,多孔纳米带表现出优异的烧结驱动力,使得纳米区以比密度更大的基质区域收缩速度加剧,从而形成了重要的网络涂层微观结构,其导热率和弹性模量值大约仅为传统涂层的一半,具有极好的隔热性能.梁波[切等人通过大气等离子喷涂,成功制备了ZrO2-3wt.%Y2O3的纳米复合涂层.通过SEM观察发现:涂层中存在大量微小气孔,并且能够观察到纳米结构的存在;对于其导热性能检测得知,导热系数仅为0.63〜0.80W/m•K,表明ZrO2-3wt.% Y2O3的纳米复合涂层适合作为热障涂层.3结语面对高端设备和零件对涂层的耐磨、防腐和热障等性能的新需求,纳米热喷涂技术提供了一种解决问题的新思路口叫研究表明,纳米热喷涂涂层突破了材料的尺寸限制,为涂层带来了纳米材料具有的独特性能,无论是涂层的孔隙率、强度、硬度和韧性,都较常规微米级涂层有很大的进步.同时,纳米结构对于涂层耐磨损、防腐蚀和热障性能与微米级涂层相比也有了质的飞跃,使用寿命寿命可延长3〜5倍.同时,采用热喷涂的方式来沉积纳米涂层,对于环境污染小,粉体材料和基材的可调节范围大,操作简单方便.目前,纳米热喷涂技术已逐渐走向工业应用,相信在不久的将来,其必将在工业领域中的表面工程技术方向面大放异彩.参考文献:[1]PAWLOWSKI L.热喷涂科学与工程[M].李辉,贺宝勇,译.2版.北京:机械工业出版社,2011.[2]倪立勇,孙宏飞,毕继鑫,等.离子喷涂纳米陶瓷涂层的研究进展口].材料保护,2008,41(4):44-46.[3]王铀,杨勇.热喷涂纳米结构涂层的研究进展及在外军舰艇上的应用[J].中国表面工程,2008(1):6-15.李长久.热喷涂技术应用及研究进展与挑战m.热喷涂技术,2018,10(04):8-29.[5]LIMA C R C,LIBARDI R,CAMARGO F,et al.Assessment of abrasive wear of nanostructured WC-Co and Fe-based coatings applied by HP-HVOF,flame and wire arc spray[J].Journal of Thermal Spray Technology,2014,23(7):1097-1104.[6]李万青.等离子喷涂WC-17Co纳米涂层的工艺及组织性能研究[D].哈尔滨:哈尔滨工业大学,2014.[7]石绪忠,许康威,武笑宇.等离子喷涂纳米氧化铝钛涂层机械性能研究[J].表面技术,2018(4):96-101.[8]YAN J,ZHANG Z,LIU L,et al.Effect of nano-ZrO2onthe microstructure and high temperature tribological properties of MoSi2coating[J].Journal of Thermal Spray Technology,2013,22(6):873-881.[9]刘晓明,杨月红,韩吉伟,等.纳米F^Al/Cr3C2复合涂层及其抗高温腐蚀性能[J].光学精密工程,2018,26(9):119-126.口0]李威霆,段晨风,张泽龙,等.热喷涂制备纳米结构TiO2涂层及其自清洁性能研究[J].热加工工艺,2017(2):137-140.256材料研究与应用2019口1]LIMA R S,MARPLE B R.Toward highly sinteringresistant nanostructured ZrO2-7wt.%Y2O3coatings for TBC applications by employing differential sintering [J]・Journal of Thermal Spray Technology,2008, 17(5-6):846-852・口2]梁波,蔡岸,陈煌,等.纳米造粒料等离子喷涂氧化错涂层的热物性研究[J1无机材料学报,2010,25(7):695-699.[13]徐群飞,陈利斌,吴彩霞.热喷涂纳米涂层研究进展[J].浙江冶金,2019(2):1-4.Progress in nano-thermal spraying technology and coatingsCAI FengTinplate Plant of Shanghai Baosteel Co.9Ltd.,Shanghai200431Abstract:As an emergant technology in the field of surface engineering,nano-thermal spraying technology has developed rapidly in recent years・Based on nano-material re-granulation and combined with thermal spray technology,nanostructures in the coating can break the limits of performance of traditional micron-scale coatings.This paper mainly introduced the thermal spraying nano-coatings?the new process o£thermal spraying nano-coatings and the classifications of the material system of thermal spraying nanocoatings.Key words:nano;thermal spray;wear-resisting;anti-corrosion;thermal barrier(上接第251页)Research progress of PS-PVD rare earth high temperature functional coatingsDENG Chunming1,XIAO Juan2,CAO Jiaxu1'3,ZHANG Xiaofeng1,NIU Shaopeng1,MAO Jie1,DENG Ziqian1,SONG chen11・Guangdong Institute of Nexv Materials,National Engineering Laboratory for Modern Materials Surface Engineering Technology,The Key Lab of Guangdong for Modem Surface Engineering Technology,Guangzhou 510650,C加?la;2.Nanfang Industrial Co.Ltd.of Aero Engine Corporation of China, Zhuzhou412002,China;3.College of Materials and Energy,Guangdong University of Technology^Guangzhou510006Abstract:Rare Earths,known as industrial"vitamins",are important strategic materials because they can irreplaceably enhance properties of materials significantly?especially for high temperature functional coatings.Plasma spray-physical vapor deposition(PS-PVD)technology can achieve functional coatings with remark different microstructures such as columnar TBC,highly dense thin electrolyte?governed by either vapor or liquid phase deposition through powder adjustment and process optimizatioTherefore the technology is a research hotspot in the current surface engineering・This paper summarizes the research progress of PS-PVD deposited TBC,EBC,mixed conductor oxygen permeable membrane and SOFC electrolyte at Guangdong institute of New Materials・It is pointed out that high temperature functional RE coating materials with high performance play important roles in advanced weapons,and should be fast and intensively developed and invested in china.Key words:rare earth high temperature functional coating;plasma spray-physical vapor deposition;thermal barrier coating;environmental barrier coating;mixed conductor oxygen permeable membrane;SOFC electrolyte。
热喷涂技术的发展和应用
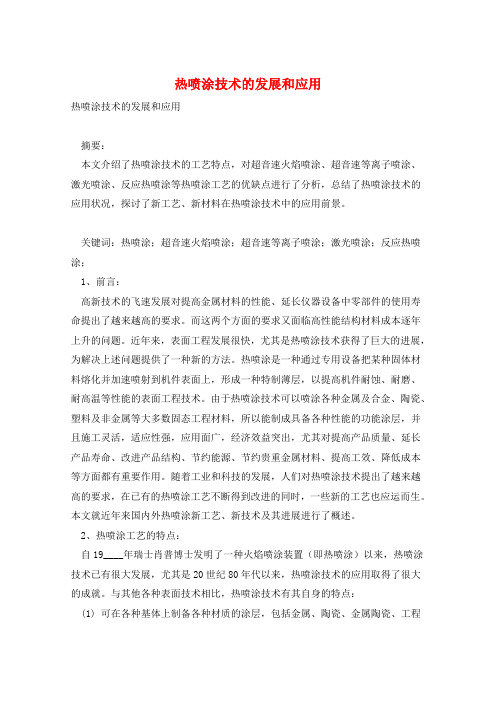
热喷涂技术的发展和应用热喷涂技术的发展和应用摘要:本文介绍了热喷涂技术的工艺特点,对超音速火焰喷涂、超音速等离子喷涂、激光喷涂、反应热喷涂等热喷涂工艺的优缺点进行了分析,总结了热喷涂技术的应用状况,探讨了新工艺、新材料在热喷涂技术中的应用前景。
关键词:热喷涂;超音速火焰喷涂;超音速等离子喷涂;激光喷涂;反应热喷涂;1、前言:高新技术的飞速发展对提高金属材料的性能、延长仪器设备中零部件的使用寿命提出了越来越高的要求。
而这两个方面的要求又面临高性能结构材料成本逐年上升的问题。
近年来,表面工程发展很快,尤其是热喷涂技术获得了巨大的进展,为解决上述问题提供了一种新的方法。
热喷涂是一种通过专用设备把某种固体材料熔化并加速喷射到机件表面上,形成一种特制薄层,以提高机件耐蚀、耐磨、耐高温等性能的表面工程技术。
由于热喷涂技术可以喷涂各种金属及合金、陶瓷、塑料及非金属等大多数固态工程材料,所以能制成具备各种性能的功能涂层,并且施工灵活,适应性强,应用面广,经济效益突出,尤其对提高产品质量、延长产品寿命、改进产品结构、节约能源、节约贵重金属材料、提高工效、降低成本等方面都有重要作用。
随着工业和科技的发展,人们对热喷涂技术提出了越来越高的要求,在已有的热喷涂工艺不断得到改进的同时,一些新的工艺也应运而生。
本文就近年来国内外热喷涂新工艺、新技术及其进展进行了概述。
2、热喷涂工艺的特点:自19____年瑞士肖普博士发明了一种火焰喷涂装置(即热喷涂)以来,热喷涂技术已有很大发展,尤其是20世纪80年代以来,热喷涂技术的应用取得了很大的成就。
与其他各种表面技术相比,热喷涂技术有其自身的特点:(1) 可在各种基体上制备各种材质的涂层,包括金属、陶瓷、金属陶瓷、工程塑料、玻璃、木材、布、纸等几乎所有的固体材料。
(2) 基体温度低。
基体温度一般在30-200__176;C 之间,变形小,热影响区浅。
(3) 操作灵活。
可喷涂各种规格和形状的物体,特别适合于大面积涂层,并可在野外作业。
热喷涂技术的原理及应用实验报告

热喷涂技术的原理及应用实验报告一、引言热喷涂技术是一种常用的表面涂覆技术,通过高速喷射热能将粉末或线状材料熔化,并在基材表面形成涂层。
本文将介绍热喷涂技术的原理以及在实验中的应用情况。
二、热喷涂技术的原理热喷涂技术基于热能喷射原理,通过将热能引入喷枪中,使喷口处的涂层材料达到熔化状态,然后以高速喷射到基材表面。
热喷涂技术主要包括燃烧喷涂和等离子喷涂两种方式。
2.1 燃烧喷涂原理燃烧喷涂是利用火焰的高温将涂层材料加热至熔化状态的技术。
其原理可以分为两个步骤:1.燃烧产生高温火焰:在喷涂枪中,燃烧剂和氧气混合燃烧产生高温火焰。
这种高温火焰可以使涂层材料达到熔化状态。
2.喷涂涂层:熔化状态的涂层材料通过高速喷射到基材表面,形成一层均匀的涂层。
涂层在快速冷却后变得致密,并具有良好的附着力。
2.2 等离子喷涂原理等离子喷涂是利用电弧放电将涂层材料加热至熔化状态的技术。
其原理可以分为三个步骤:1.弧电离气体:在喷涂枪中,高压电源产生电弧,将气体电离,形成等离子体。
等离子体产生的高温可以使涂层材料达到熔化状态。
2.喷涂涂层:熔化状态的涂层材料通过高速喷射到基材表面,形成一层均匀的涂层。
等离子体的高温状态有利于涂层材料的熔化和喷射。
3.冷却和固化:涂层在快速冷却后变得致密,并具有良好的附着力。
三、热喷涂技术的应用实验3.1 实验目的本实验旨在研究热喷涂技术在材料表面涂覆方面的应用情况,并对涂层性能进行评估。
3.2 实验材料和设备实验材料:使用钴基和铝基合金粉末作为涂层材料。
基材使用不锈钢板。
实验设备:燃烧喷涂设备和等离子喷涂设备。
3.3 实验步骤1.准备基材:将不锈钢板进行表面处理,保证其干净无杂质。
2.准备涂层材料:将钴基和铝基合金粉末进行筛选和混合。
3.燃烧喷涂实验:将喷涂枪调整到适当位置,控制喷涂距离和喷涂速度,进行燃烧喷涂实验。
4.等离子喷涂实验:将喷涂枪调整到适当位置,控制喷涂距离和喷涂速度,进行等离子喷涂实验。
热喷涂技术的应用与展望

热喷涂技术的应用与展望摘要:本文综述了热喷涂工艺的特点、分类以及在不同行业的应用和研究现状,并对热喷涂技术的发展趋势进行了展望。
关键词:热喷涂;涂层;应用0引言热喷涂是一种采用专用设备利用热源将金属或非金属材料加热到熔化或熔融状态,借助焰流或外加的推力将熔滴雾化或推动熔粒成喷射的粒束以一定速度喷射到经过制备的基体表面形成某种功能的涂层,以提高机件耐蚀、耐磨、耐热等性能的新兴表面工程技术[1-2]。
热喷涂技术在航空航天、机械制造、石油化工、电力设备维修,造纸业等领域中得到了广泛的应用,并取得了良好的经济效益[3]。
热喷涂成为金属表面科学领域中一个十分活跃的学科。
1 热喷涂工艺特点热喷涂技术从上世纪初开始出现到现在已有几十年的历史了,热喷涂工艺、设备、喷涂材料以及施工都有了突飞猛进的发展,从早期制备一般装饰性和防护性表面,发展到制备各种功能的功能性涂层;由旧件的修复工艺发展成新产品的强化工艺;由单一涂层发展到多层的包括产品失效分析、涂层设计、工艺设计和施工以及质量检测和控制在内的系统工程,成为像铸、锻、焊、热处理一样的、独立的热加工工艺。
热喷涂技术与其他各种表面技术相比,有许多自身的特点[4]:(1)喷涂材料的选择范围广泛,它几乎包括所有的固体材料。
(2)选择合适的工艺方法几乎能在任何固体材料表面上进行喷涂,这是其它表面技术无法实现的。
(3)一般不受施工场所的限制,既可以在室内喷涂,又可以现场施工。
(4)一般不受工件尺寸及形状限制,既可对工件进行大面积喷涂,也可以对工件进行局部喷涂。
(5)涂层厚度可以在几十微米到几毫米范围内控制。
(6)除喷熔外,热喷涂工艺对基体材料热影响小,并且可以进行控制,它不会影响基体金属的金相组织和机械性能。
(7)能够使涂层具有不同功能,尤其是复合功能。
(8)热喷涂的生产率高.(9)与其他堆焊方法比较,火焰喷熔层和等离子喷熔层的冲淡率较低,而且表面成形平整、光滑、加工余量少。
涡轮机械工程中的热喷涂技术研究

涡轮机械工程中的热喷涂技术研究引言涡轮机械工程作为现代工程领域的重要组成部分,在能源、航空、航天等领域扮演着重要的角色。
然而,由于长时间高温高速运转,涡轮机械零部件容易受到磨损和腐蚀的影响,从而影响其性能和寿命。
为了解决这个问题,热喷涂技术应运而生,被广泛应用于涡轮机械工程中。
本文将探讨热喷涂技术在涡轮机械工程中的研究进展、应用以及未来的发展方向。
1. 热喷涂技术的基本原理1.1 热喷涂技术的发展历程热喷涂技术起源于20世纪初期的飞艇和火箭发动机的研究。
最初采用的是火焰喷射和电弧喷涂等简单粗糙的方法。
随着研究的深入和技术的进步,热喷涂技术逐渐发展成为一门独立的学科,并广泛应用于航空、航天、能源等领域。
1.2 热喷涂技术的基本原理热喷涂技术是利用喷涂设备将热源与喷涂材料进行混合,并通过喷嘴喷射到工件表面形成涂层。
这些喷涂材料可以是金属、陶瓷、塑料等材料,涂层的厚度可根据需要进行调整。
热喷涂过程中的常用热源包括等离子喷射、火焰喷射和高压渗硅等。
2. 热喷涂技术在涡轮机械工程中的应用2.1 涡轮叶片的保护涂层涡轮叶片是涡轮机械中的核心部件,承受着高温、高速和高压的作用。
为了保护涡轮叶片免受高温气流和腐蚀的侵害,热喷涂技术被广泛应用于涡轮叶片的保护涂层制备。
通常使用的涂层材料包括高温合金、陶瓷和金属陶瓷复合材料等。
这些涂层能够有效提高叶片的耐热性、耐磨性和抗腐蚀性。
2.2 涡轮内部组件的修复和增强由于涡轮内部组件长时间运行后容易出现磨损、腐蚀等问题,为了延长其寿命并节约维修成本,热喷涂技术被应用于涡轮内部组件的修复和增强。
通过在受损部位喷涂合适材料的涂层,可以修复和增强涡轮的性能。
这种修复和增强的方式比传统的更换零件的方法更加经济和可行。
2.3 涡轮静叶环的涂层制备涡轮静叶环作为涡轮机械中的重要部件,具有降低能量损失和提高热效率的作用。
热喷涂技术可以在静叶环表面喷涂耐高温和耐磨的涂层,从而提高涡轮的工作效率。
热喷涂技术研究报告

热喷涂技术研究报告热喷涂技术是一种将热能转化为动能并喷射到被涂物表面的喷涂技术,已经被广泛应用于各个领域,如航空、航天、汽车、电力等。
本文主要介绍热喷涂技术的原理、分类、应用及发展趋势,并探讨了热喷涂技术在未来的发展方向。
一、热喷涂技术的原理热喷涂技术是一种将热能转化为动能并喷射到被涂物表面的喷涂技术。
热喷涂技术可以将固态、液态、气态的物质喷涂到被涂物表面,形成一层保护层或者改性层。
热喷涂技术主要包括火焰喷涂、等离子喷涂、高速气流喷涂、爆炸喷涂等几种类型。
二、热喷涂技术的分类1.火焰喷涂火焰喷涂是最普及的喷涂技术,通过燃烧燃料和氧气产生高温火焰,将喷涂材料加热熔化,并通过氧化反应形成一层涂层。
火焰喷涂涂层具有优异的耐腐蚀性、耐磨性和抗氧化性。
2.等离子喷涂等离子喷涂是一种高温等离子体喷涂技术,通过电弧放电或者离子束轰击等方式将喷涂材料加热熔化,并通过化学反应形成一层涂层。
等离子喷涂涂层具有优异的耐高温、耐腐蚀等性能。
3.高速气流喷涂高速气流喷涂是一种将喷涂材料加热熔化后通过高速气流喷涂到被涂物表面的喷涂技术。
高速气流喷涂涂层具有优异的耐磨性、耐腐蚀性和抗氧化性。
4.爆炸喷涂爆炸喷涂是一种通过爆炸将喷涂材料加热熔化后喷涂到被涂物表面的喷涂技术。
爆炸喷涂涂层具有优异的耐磨性、耐腐蚀性和抗氧化性。
三、热喷涂技术的应用热喷涂技术已经被广泛应用于各个领域,如航空、航天、汽车、电力等。
以下是热喷涂技术的应用领域:1.航空航天热喷涂技术可以用于飞机发动机叶片、涡轮叶片、火箭发动机喷管等高温部件的保护和修复。
热喷涂技术可以提高这些部件的耐高温性能和耐腐蚀性能。
2.汽车制造热喷涂技术可以用于汽车发动机缸体、缸盖、曲轴、凸轮轴等零部件的修复和加固。
热喷涂技术可以提高这些部件的耐磨性能和耐腐蚀性能。
3.电力工业热喷涂技术可以用于涡轮机叶片、蒸汽涡轮机叶片、汽轮机叶片等高温部件的保护和修复。
热喷涂技术可以提高这些部件的耐高温性能和耐腐蚀性能。
热喷涂耐高温涂层研究现状及发展趋势
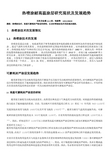
热喷涂耐高温涂层研究现状及发展趋势无机非金属12-2班,祝超锋1201130633摘要:热喷涂技术,高温可磨耗封严涂层的研制,以及对喷涂层技术的发展及展望。
1热喷涂技术的发展情况1.1热喷涂技术的发展热喷涂是通过火焰、电弧或等离子体等热源将某种线状或粉末状的材料加热至熔化或半熔化状态, 通过气流吹动使其雾化, 并高速喷射到经过预处理的基体表面, 以形成喷涂层的表面加工技术。
热喷涂技术的产生和应用已有近百年[ 3] , 最早的热喷涂技术始于1882年, 德国人用一种简单的装置将熔融态金属喷射成粉体。
真正的热喷涂技术则产生于1910年, 在瑞士被V.SCHOOP博士研究出来, 他发明了固定式坩埚熔融喷射装置。
20世纪后期, 热喷涂技术的基础研究越来越受到重视, 主要集中于喷涂过程中的粒子状态及其影响因素的研究。
在其应用研究中, 涂层与基体的结合技术是一个热点。
进入21世纪, 纳米技术的研究为热喷涂一个研究的热点, 其引入为改善涂层的性能开拓了新途径。
可磨耗封严涂层发展趋势随着新型航空发动机使用温度的不断提升以及航空发动机材料的更新换代,对可磨耗封严涂层的综合使用性能提出了越来越高的要求,因此亟需在国内现有可磨耗封严涂层研究的基础上,开发研制具有更高使用温度和适应更新一代发动机材料的新型可磨耗封严涂层。
2.1 高温可磨耗封严涂层的研制随着航空涡轮发动机向高流量比、高推重比和高进口气体温度方向的发展,对高温部件的耐高温能力提出了越来越高的要求。
目前,发动机叶片的使用温度已经从20 世纪70 年代的960~1100℃发展到现在商用飞机的1500℃以及军用飞机的1700℃[24]。
随着压缩空气温度的逐级升高,可磨耗密封涂层的使用温度也从300℃提高到1100℃,目前其使用的最高温度已经达到1200℃以上[25]。
因此,研制适用于1100℃以上的新型高温可磨耗封严涂层材料已成为可磨耗封严涂层领域的重要研究方向之一。
- 1、下载文档前请自行甄别文档内容的完整性,平台不提供额外的编辑、内容补充、找答案等附加服务。
- 2、"仅部分预览"的文档,不可在线预览部分如存在完整性等问题,可反馈申请退款(可完整预览的文档不适用该条件!)。
- 3、如文档侵犯您的权益,请联系客服反馈,我们会尽快为您处理(人工客服工作时间:9:00-18:30)。
三阴极等离子喷涂示意图
100 HE
高能等离子喷涂
高能等离子喷涂是为满足陶瓷材料对涂层密度和结合强度以及喷
涂效率的更高需求而开发的一种高能、高速的等离子喷涂技术, 其特 点是在电弧电流与普通大气等离子喷涂相当的条件下, 利用较高的工 作电压(可达几百伏)提高功率, 并采用更大的气体流量来提高射流的 流速。
热喷涂技术的研究进展
1、热喷涂技术概论
原理 热喷涂技术是一种将涂层材料(粉末或丝材) 送入某种热源(电弧、燃烧火焰、等离子体等)中 熔化, 并利用高速气流将其喷射到基体材料表面 形成涂层的工艺 。
涂层结构特点
特点
a. 能赋予基体以多种功能的表面;
b. 设备轻便,可现场施工;
c. 除喷焊外,对基材加热温度较低,工件 变形小,金相组织及性能变化也较小。
电弧超音速喷涂示意图
电弧喷涂的特点
优点:
a. 涂层性能优异,与基体的结合力高; b. 经济、节能、效率高; c. 安全 电弧喷涂技术仅使用电和压缩空气,不用 氧气、乙炔等易燃气体助燃,安全性高 ; d.可制备伪合金涂层; 用金属, 而不能使用陶瓷,限制了电弧喷涂的应用范围。
等离子喷涂原理
等离子喷涂特点
1.超高温特性,便于进行高熔点材料的喷涂。 2.喷射粒子的速度高,涂层致密,粘结强度
高。 3.由于使用惰性气体作为工作气体,所以喷
涂材料不易氧化。
等离子喷涂研究进展
随着热喷涂技术的 飞速发展, 国际上等 离子喷涂占有明显 优势, 并已开发出三 阴极等离子喷涂、
PROTAL预处理工艺原理示意图
等离子喷涂后处理工艺
等离子喷涂后处理工艺的明显进步是采用激光重熔技术,利用等离子 喷涂形成陶瓷涂层后,随即就对热态的喷涂陶瓷层进行激光等离子加 热,其工作原理如图所示。由于等离子喷涂工艺特征决定了涂层呈层 状结构,涂层内存在较高的孔隙率和亚稳相,金属/陶瓷界面上存在较 大的残余应力且涂层结合强度不高,这些因素可能使涂层在使用过程 中容易失稳,引起脱落失效。陶瓷涂层经激光重熔后可减少孔隙率、 降低裂纹数、使陶瓷涂层中的亚稳相向稳定相转变,提高涂层的表面 硬度、耐磨性以及抗热震等性能。
d. 喷涂操作的程序较少,施工时间较短,效率 高,比较经济。
分类 (1)电弧喷涂(电弧为热源) (2)等离子喷涂(等离子体为热源) (3)火焰喷涂(燃烧火焰为热源)
2.电弧喷涂
电弧喷涂是以电弧为热源,将熔化的金属丝用高速气
流雾化,并以高速喷射到工件表面形成涂层的一种工 艺 。电弧喷涂过程可分为三个阶段:熔滴形成及雾化 阶段;熔滴飞行阶段;熔滴撞击基体,相互交错粘结形成 涂层阶段
应用: 1.重大件的修复:轴类零件修复;造纸烘
钢的修复;航天发动机的修复 2.严重腐蚀环境下的大面积防蚀涂层; 3.装饰涂层 4.填平和修补焊缝缺陷
等离子喷涂
等离子及等离子弧的产生 常规状态下原子是呈电中性的,气体在常温
状态下也是不导电的,但是如果外界通过改变条 件给予气体分子或原子分子以相当的能量时,就 会造成电子脱离原子成为自由电子而带正电荷, 这就是所谓的气体产生电离的现象,这也就是等 离子喷涂的等离子体和等离子弧的产生原理 。
悬浮式等离子喷涂示意图
反应等离子喷涂
反应等离子喷涂是对真空等离子喷涂进一步改进的结果, 该方法在真空等离子喷涂过程中,在喷嘴出口处的等离子射 流中加入反应气体(如N2),反应气体与加热中的喷涂颗粒相 互作用,进而得到新的生成物。 例如,用这种方法可以获得TiN涂层,它是靠喷涂钛粉和注入 N2反应后得到的,其工作原理如图所示。TiN具有高熔点、 高硬度、耐磨、耐蚀等特点,并且还具有优良的导电性和超 导性。 反应等离子喷涂制备 TiN涂层克服了传统的物理或者化 学气相沉积(PVD及CVD)工艺 制备TiN 涂层,存在沉积速 率低、涂层厚度过薄的缺点,可制备纳米晶TiN涂层, 涂层厚度可达500µm。
悬浮式送粉等离子喷涂
悬浮式送粉等离子喷涂是一种采用液料 送粉方式, 可直接喷涂纳米粉末且可以形 成超薄纳米涂层的新型喷涂技术传统的非 团聚喷涂粉末粒子半径必须大于10µm, 涂 层厚度一般大于125µm。悬浮等离子喷涂 采用液料为介质, 使用分散剂将粒子分散 在液料中(液料一般为酒精)行成悬浮液, 通 过液料送粉器将悬浮液送入到等离子弧中, 液料溶剂迅速蒸发, 溶剂中的粉末被等离 子弧加热熔化喷射到基体上形成涂层。这 种方式克服了喷涂粒子半径的限制, 不仅 实现了非团聚的纳米粉末直接进行喷涂, 而且可制备涂层厚度仅25µm 的超薄涂层 。
高能等离子喷涂、
微弧等离子喷涂和
悬浮等离子喷涂等 多种新技术
等离子 喷涂
三阴极 等离子 喷涂
高能 等离子 喷涂
微 等离子 喷涂
悬浮 等离子 喷涂
超音速 电弧 与火焰 喷涂
三阴极等离子喷涂
喷枪由3个阴极和由几个被绝缘的环体串联 组成的喷嘴组成, 只有离阴极相对远的最后 一个环体作为阳极工作。由于从3个阴极到 同一个阳极产生的3个独立电弧的长度稳定 不变, 3束等离子射流在汇流腔内汇聚成一 束主等离子流, 形成空心管状射流从喷嘴喷 出, 从而产生了稳定的等离子喷射。
高 能 等 离 子 喷 枪
喷涂WC-Co涂层的粒子平均速度可达527m/s; 同时还具有较高的喷涂效率 (可达200g/min)和沉积效率(可达95%)
微等离子喷涂
微等离子喷涂是20世纪90年代由乌克兰巴顿焊 接研究所开发的, 它的特点是具有层流等离子 射流、发射角只有2°~ 6°(普通的等离子枪的 发射角达10°~ 18°)、功率低( 1~ 3 kW )、基 体受热低、噪声小( 30~ 50 dB) , 可在极薄的基 体(如0.5mm厚的不锈钢薄板或1.0 mm 厚的锰 片)上进行喷涂。这种喷涂方法的功率虽低, 但 能量集中, 其束斑直径小于5 mm, 所以仍可喷 涂各种材料, 特别适宜制备小零件及薄壁件的 精密涂层, 且该设备重量轻, 适合于现场的维修 工作。
反应等离子喷涂示意图
PROTAL预处理工艺
在常规的热喷涂工艺中基体需要去油和主要用金钢砂喷砂处理。相反, PROTAL预处理工艺采用高能量激光束与基体表面相互作用,减少基体与 熔融粒子碰撞前的氧化层和其它污染,仅10ns的短暂脉冲的使用, 使基 体表面第一批原子层烧蚀而获得无污染的表面,其工作原理如图所示。 这种喷涂前预处理工艺可以在表面没有粗化处理的情况下,使涂层获得 相对好的附着力。