表面粗糙度 基础
表面粗糙度的基本术语

表面粗糙度的基本术语表面粗糙度是指物体表面的不平整程度,通常用于描述工程制品的加工质量。
表面粗糙度是一个重要的质量指标,对于一些机械零件的连接、密封和摩擦等方面都有很大的影响。
因此,表面粗糙度也成为了机械加工行业中的一个重要概念。
在描述表面粗糙度时,我们需要了解一些基本术语。
1. 粗糙度粗糙度是指表面上的微小起伏,包括高峰和低谷。
这些起伏的尺寸通常由表面的平均高度和深度确定。
粗糙度是表面不规则程度的一个量化指标,通常用Ra值表示。
2. Ra值Ra值是表面粗糙度的一个重要参数。
它表示整个表面的平均高度偏差,通常以微米为单位。
Ra值越小,表面越光滑。
3. Rz值Rz值是表面粗糙度的另一个重要参数。
它表示表面上最大峰和最大谷之间的距离。
Rz值越小,表面越光滑。
4. Rt值Rt值是表面粗糙度中的一个参数。
它表示表面上最高和最低点之间的距离。
Rt值越小,表面越光滑。
5. Rq值Rq值是表面粗糙度的另一个参数。
它表示表面上所有高度偏差的平方和的平方根。
Rq值越小,表面越光滑。
6. Rmax值Rmax值是表面粗糙度的一个参数。
它表示表面上最大峰和最大谷之间的距离。
Rmax值越小,表面越光滑。
7. Rmr值Rmr值是表面粗糙度的另一个参数。
它表示表面上所有高度偏差的平方和的平方根。
Rmr值越小,表面越光滑。
8. Rk值Rk值是表面粗糙度的一个参数。
它表示表面上最大谷的深度。
Rk 值越小,表面越光滑。
9. Rpk值和Rvk值Rpk值和Rvk值分别表示表面上最高峰和最低谷的高度。
Rpk值和Rvk值越小,表面越光滑。
表面粗糙度是一个非常重要的概念,对于机械制造和加工行业有着重要的意义。
掌握表面粗糙度的基本术语,可以更好地评估加工品质,并提高加工品质的控制能力。
表面粗糙度基础知识
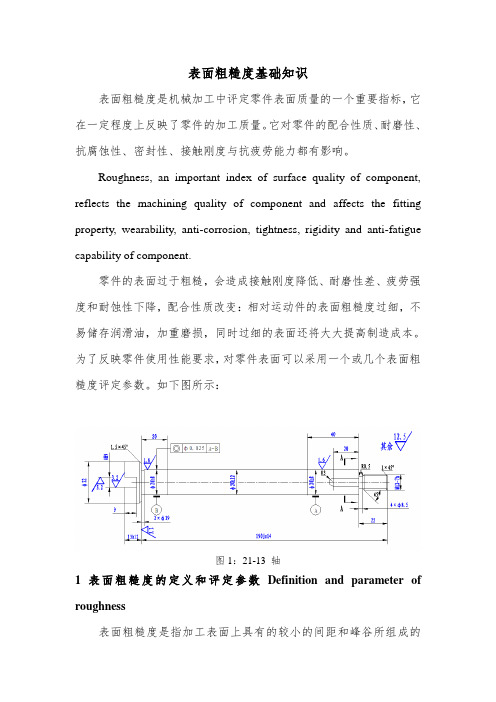
表面粗糙度基础知识表面粗糙度是机械加工中评定零件表面质量的一个重要指标,它在一定程度上反映了零件的加工质量。
它对零件的配合性质、耐磨性、抗腐蚀性、密封性、接触刚度与抗疲劳能力都有影响。
Roughness, an important index of surface quality of component, reflects the machining quality of component and affects the fitting property, wearability, anti-corrosion, tightness, rigidity and anti-fatigue capability of component.零件的表面过于粗糙,会造成接触刚度降低、耐磨性差、疲劳强度和耐蚀性下降,配合性质改变:相对运动件的表面粗糙度过细,不易储存润滑油,加重磨损,同时过细的表面还将大大提高制造成本。
为了反映零件使用性能要求,对零件表面可以采用一个或几个表面粗糙度评定参数。
如下图所示:图1:21-13 轴1 表面粗糙度的定义和评定参数Definition and parameter of roughness表面粗糙度是指加工表面上具有的较小的间距和峰谷所组成的微观几何特性。
一般由所采用的加工方法和其他因素形成。
Caused by machining and other factors.表面粗糙度的评定参数:轮廓算数平均偏差Ra,微观不平度十点高度Rz,轮廓最大高度Ry。
表1:术语与定义Table 1: terms and definitionTerm Definition Diagram Remarks轮廓算数平均偏差Ra 在取样长度内轮廓绝对值的算术平均值Ra=微观不平度十点高度Rz 在取样长度内5个最大的轮廓峰值与5个最小的轮廓谷深的平均值之和Rz=+轮廓最大高度Ry 在取样长度轮廓峰顶线和轮廓谷底线之间的距离2 表面粗糙度的基本符号与含义2.1基本符号basic sign表示表面可用任何方法获得,当不加注粗糙度数值或有关说明(如表面处理、局部热处理)时,仅适用简化代号标注。
形状测量·粗糙度测量教程
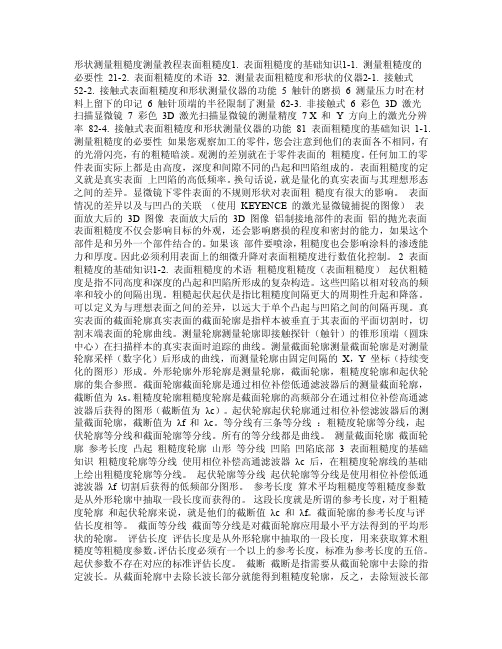
形状测量粗糙度测量教程表面粗糙度1. 表面粗糙度的基础知识1-1. 测量粗糙度的必要性21-2. 表面粗糙度的术语32. 测量表面粗糙度和形状的仪器2-1. 接触式52-2. 接触式表面粗糙度和形状测量仪器的功能5 触针的磨损6 测量压力时在材料上留下的印记6 触针顶端的半径限制了测量62-3. 非接触式6 彩色3D 激光扫描显微镜7 彩色3D 激光扫描显微镜的测量精度7 X 和Y 方向上的激光分辨率82-4. 接触式表面粗糙度和形状测量仪器的功能81 表面粗糙度的基础知识1-1. 测量粗糙度的必要性如果您观察加工的零件,您会注意到他们的表面各不相同,有的光滑闪亮,有的粗糙暗淡。
观测的差别就在于零件表面的粗糙度。
任何加工的零件表面实际上都是由高度,深度和间隙不同的凸起和凹陷组成的。
表面粗糙度的定义就是真实表面上凹陷的高低频率。
换句话说,就是量化的真实表面与其理想形态之间的差异。
显微镜下零件表面的不规则形状对表面粗糙度有很大的影响。
表面情况的差异以及与凹凸的关联(使用KEYENCE 的激光显微镜捕捉的图像)表面放大后的3D 图像表面放大后的3D 图像铝制接地部件的表面铝的抛光表面表面粗糙度不仅会影响目标的外观,还会影响磨损的程度和密封的能力,如果这个部件是和另外一个部件结合的。
如果该部件要喷涂,粗糙度也会影响涂料的渗透能力和厚度。
因此必须利用表面上的细微升降对表面粗糙度进行数值化控制。
2 表面粗糙度的基础知识1-2. 表面粗糙度的术语粗糙度粗糙度(表面粗糙度)起伏粗糙度是指不同高度和深度的凸起和凹陷所形成的复杂构造。
这些凹陷以相对较高的频率和较小的间隔出现。
粗糙起伏起伏是指比粗糙度间隔更大的周期性升起和降落。
可以定义为与理想表面之间的差异,以远大于单个凸起与凹陷之间的间隔再现。
真实表面的截面轮廓真实表面的截面轮廓是指样本被垂直于其表面的平面切割时,切割末端表面的轮廓曲线。
测量轮廓测量轮廓即接触探针(触针)的锥形顶端(圆珠中心)在扫描样本的真实表面时追踪的曲线。
精度设计与质量控制基础--第3章--表面粗糙度课件(1)
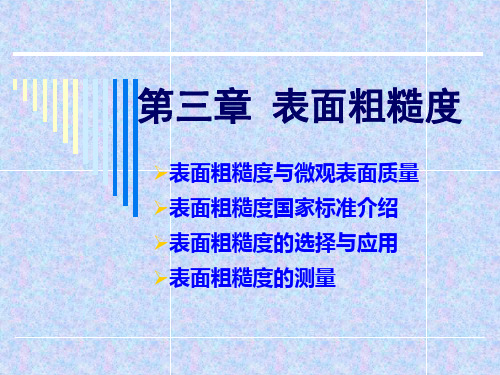
GB 131-93规定: ➢当允许在表面粗糙度参数的所有实测值中,超过规定值的个 数少于总数的16%时,应在图中标注表面粗糙度参数的上限值 或下限值; ➢当要求在表面粗糙度参数所有实测值不允许超过规定值时, 应在图样上标注表面粗糙度参数的最大值或最小值。
2、表面粗糙度代号及标注(6)
表面粗糙度标注方法示例
yi
2、微观不平度十点高度Rz
定义 在取样长度内,5个最大的轮廓峰高ypi平均值与5个最大轮廓 谷深yvi平均值之和。即:
5
5
ypi yvi
Rz i1
i1
5
3、轮廓最大高度Ry
定义: 在取样长度内,轮廓的峰顶线和谷底线之间 的距离。 Ry =︱ypmax︱+︱yvmax︱
Ry
4、轮廓微观不平度平均间距Sm
GB6061-85 轮廓法测量表面粗糙度的仪器-术语;
GB6062-85 轮廓法触针式表面粗糙度测量仪—轮廓记录仪及中级制轮廓计;
GB10610—89 触针式仪器测量表面粗糙度的规则和方法;
GB/T12472—2003 木制件表面粗糙度参数及其数值
§3.2 表面粗糙度GB介绍
一、主要术语及定义
1.取样长度l
二、参数值的确定方法(2)
③ 承受交变载荷的表面及容易引起应力集中的部分,粗糙 度要求高些;
④ 对配合性质有稳定可靠性要求的表面,粗糙度要求应高 些;
⑤ 配合性质相同时,小尺寸比大尺寸、轴比孔的表面粗糙 度要求要高些;
⑥ 对特殊用途的零件,表面粗糙度参数值的选择应按照特 殊要求考虑。
二、参数值的确定方法(3)
Ra μm ≥0.008~0.02 >0.02~0.1 >0.1~2.0 >2.0~10.0 >10.0~80.0
表面粗糙度
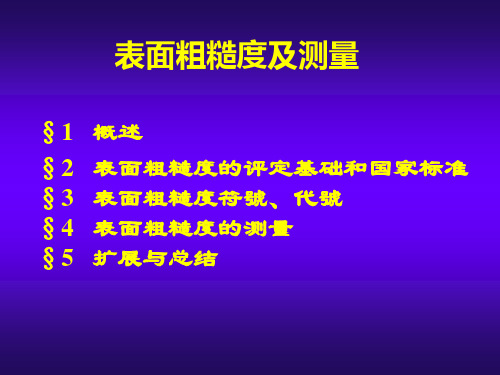
3. 评定长度 ln: 包含一个或数个取样长度的总长度称为 评定长度 GB规定:ln=5*l
輪廓中線
α
l
l
l
l
ln
x
4.取樣長度 l 和
評定長度
ln
图4-2-9 TR200型手持式粗糙度仪
图4-2-10 2210型电动轮廓仪
五.印模法
1.原理: 利用某些塑性材料将被测表面印模下来,然后对印摸表面 进行测量.常用的印模材料有川蜡、石蜡和低熔点合金等, 2.特点: 印模材料的强度和硬度都不高,固一般不用针描法测量它. 由于印模材料不可能填满谷底,且取下印模材料时往往使 印模波峰削平,所以测得印模的Rz值比实际略有缩小,一 般可以根据实验进行修整.印模法适用于大尺寸的内表 面.测量范围为Rz=0.8~330 µ m
图4-2-8触针法测量原理图
2.触针法测量的特点: 所用仪器为电动轮廓仪或粗糙度仪,与前两种仪器相比 该测量方法显示更直观、操作更方便、效率更高、测量范 围更大(0.02~50 µ m)更广,即适用适用于规则表 面又适用于不规则表面;不要求被测表面具有反射能力; 更重要的是可以测量参数Ra值.所以现今使用最多的就 是这种方法.但它属于接触测量,不适用于强度硬度较低 的表面.
图 4-2-2测量 原理图
光带影像 观察方向
光束投射方向
图4-2-3 光束与 表面截图
2.光切发的特点:
所用仪器 为光切显微镜(双管 显微镜),适用与规则表面(如:车、 铣、刨等去除材料的加工表 面),且表面有一定的反射能力。 可以测量Rz、Ry、S参数,测 量范围:(0.8~80µ m).测量方 法属于非接触测量
第一节表面粗糙度的评定参数

❖ 1.L 2 表面粗糙度测量的基本原则
❖
(1)测量方向
❖ 按现行标准所定义的各种粗糙度评定参数,是基于轮廓法确定数值,是在被测表面的法向截面上的 实际轮廓上进行测量的结果。由于垂直于被测表面的法向截面存在各种不同的测量方向.所以规定在垂 直于加工纹理力向的d向截面(参R图g”8)测得的结果,称作横向轮廊的表面粗糙度数值(d);在平行于加 工纹理方向的5向截面上所作的测量,称为纵向轮廓的粗糙度数值(6)。试验表明,大多数的切削加工表
2.表面粗糙度:是一种微观几何形状误差又称微观不平度。 3.表面粗糙度的产生原因:在加工过程中,刀具和零件表面
间产生磨擦、高频振动及切削时在工作表面上留下的微观 痕迹。
二.表面粗糙度的影响
❖ 表面粗糙度对机器零件的使用性能有着重要的影响,主要表 现在:
1.对摩擦和磨损的影响 2.对配合性的影响 3.对接触刚度的影响 4.对疲劳强度的影响 5.对抗腐蚀性的影响 6.对结合密封性的影响 ❖ 此外表面粗糙度还影响检验零件时的测量不确定度、零件外
1、轮廓算术平均偏差Ra
在取样长度L内,轮廓偏转距绝对值的算术平均值。
用公式表示为:
1l
Ra L 0 y(x) dx
Ra
1 n
n i 1
yi
Rz
图4-3 表面粗糙度的高度参数
2.微观不平度十点高度
❖ 在取样长度内五个最大的轮廓峰高的平均值与五个最大的轮
廓谷深的平均值之和,如图4-3所示。用公式表示为:
§4-1 表面粗糙度的评定参数
主要内容:
1、主要术语及定义 取样长度L 评定长度L
n
轮廓中线m 2、6个评定参数
3个基本、3个附加 3、一般规定
重点: 3个基本评定参数
表面粗糙度测量入门 线条粗糙度篇

线条粗糙度篇非常感谢您阅读“形状测量入门(线条粗糙度篇)”。
本资料汇总了表面粗糙度及形状测量的相关基础知识以及有关测量的注意事项。
希望您阅读以后,能通过本书的内容解决工作上遇到的问题,我们将不胜荣幸。
表面放大3D图像表面放大3D图像1-2表面粗糙度的术语粗糙度(surface roughness)“粗糙度(表面粗糙度)”是指高度、深度、间隔各异的峰、谷呈连续复杂形状,并且还呈现出周期较短、间隔比深度小的连续起伏的表面状态。
波度(waviness)“波度”是指由大于粗糙度的间隔所引起的表面周期性起伏,可以定义为由比深度大得多的间隔不断重复所引起的与理想表面的偏差。
实际表面的横截面曲线“实际表面的横截面曲线”是指以指定的垂直平面切割样品实际表面后,呈现于该切口上的曲线。
测量曲线(traced profile)“测量曲线”是指通过 VK-X 系列测量的结果、计算得出的样品表面形状。
测量横截面曲线(total profile)“测量横截面曲线”是在由纵轴和横轴构成的坐标(连续变化的图表)上,对测量曲线按一定间隔取样(数字化)所获得的曲线。
轮廓曲线(profile)“轮廓曲线”是测量横截面曲线、横截面曲线、粗糙度曲线、波度曲线等曲线的总称。
横截面曲线(primary profile)“横截面曲线”是指将截止值λs的相位补偿型低通滤波器应用于测量横截面曲线所获得的曲线。
粗糙度曲线(roughness profile)“粗糙度曲线”是指通过位相补偿型高通滤波器(截止值λc)、仅记录横截面曲线高频成分的曲线。
波度曲线(waviness profile)“波度曲线”是指将截止值λs 和λc 的相位补偿型滤波器应用于横截面曲线所获得的曲线。
平均线(average line)“平均线”分为“粗糙度曲线用的平均线”、“波度曲线用的平均线”、“横截面曲线用的平均线”共3种平均线,均为曲线。
粗糙度波度横截面曲线平均线平均线粗糙度曲线峰顶谷峰谷底基准长度粗糙度曲线用的平均线(average line for roughness profile )“粗糙度曲线用的平均线”是指利用相位补偿型高通滤波器λc (高通滤波器)进行剪切、记录了低频成分的曲线。
机械制造基础第四章表面粗糙度

※给出Rmr(c)参数时,必须同时给出轮廓水平截距c值。
(2)轮廓的实体材料长度Ml(c)
▲定义:评定长度内,一平行于X轴的直线从峰顶线向下 移一水平截距c时,与轮廓相截所得各段截线长度之和。
n
Ml(c) b1 b2 bi bn bi i 1
■轮廓的水平截距c大小可用微米或用它占轮廓制了长波轮廓成分相 对应的中线,即具有几何轮廓形状并划分轮廓的 基准线,用来评定表面粗糙度参数值的给定线。
轮
轮廓的最小二乘中线
廓
中
线
轮廓的算术平均中线
△以中线为基准线评定轮廓的计算制称为中线制
(1)轮廓的最小二乘中线
▲定义:在取样长度内,使轮廓线上各点轮廓偏距zi的
6、配合性质高的表面、小间隙配合表面、受重载的过 盈配合表面Ra和Rz值要小; 7、配合性质相同,零件尺寸越小,Ra和Rz值越小;同 一精度等级,小尺寸比大尺寸、轴比孔的Ra和Rz参数值 要小; 8、抗腐蚀性、密封性、外观性要求高的表面的Ra和Rz 参数值要小; 9、标准规定的按规定的参数值选用; 10、尺寸公差值和形状公差值小,其Ra和Rz参数值相应 要小,一般情况下,可取Ra为形状公差值的20-25%。
■轮廓支承长度率(Rmr(c))随着轮廓的水平截距c 大小而变化。其关系曲线称为支承长度率曲线。
■支承长度率曲线对于 反映零件表面耐磨性有 着显著的功效。
Rmr(c) % 支承长度率曲线
c%
■ 轮廓峰顶线:在取样长度内,平行于基准线并通过 轮廓最高点的线。
■ 轮廓谷底线:在取样长度内,平行于基准线并通过 轮廓最低点的线。
规定取样长度是为了限制减弱宏观几何误差,尤其是表面波 纹度对测量结果的影响,表面越粗糙,取样长度就应越大,它 至少应包含5个以上的轮廓峰和轮廓谷,
表面粗糙度的基本概念汇总

表面粗糙度的基本概念表面粗糙度的基本概念表面粗糙度的定义(本站相关粗糙度仪的产品介绍:粗糙度仪)表面粗糙度(Surface roughness)是指加工表面上具有的较小间距和峰谷所组成的微观几何形状特性性它是一种微观几何形状误差,也称为微观不平度。
表面粗糙度应与形状误差(宏观几何形状误差)和表面波度区别开。
通常,波距小于 1mm 的属于表面粗糙度,波距在 1~10mm 的属于表面波度,波距大于 10mm 的属于形状误差。
表面粗糙度对机械零件使用性能的影响表面粗糙度的大小对零件的使用性能和使用寿命有很大影响。
1. 影响零件的耐磨性表面越粗糙,摩擦系数就越大,相对运动的表面磨损得越快。
然而,表面过于光滑,由于润滑油被挤出或分子间的吸附作用等原因,也会使摩擦阻力增大和加速磨损。
2. 影响配合性质的稳定性零件表面的粗糙度对各类配合均有较大的影响。
对于间隙配合,两个表面粗糙的零件在相对运动时会迅速磨损,造成间隙增大,影响配合性质;对于过盈配合,在装配时表面上微观凸峰极易被挤平,产生塑性变形,使装配后的实际有效过盈减小,降低联接强度;对于过渡配合,因多用压力及锤敲装配,表面粗糙度也会使配合变松。
3. 影响疲劳强度承受交变载荷作用的零件的失效多数是由于表面产生疲劳裂纹造成的。
疲劳裂纹主要是由于表面微观峰谷的波谷所造成的应力集中引起的。
零件表面越粗糙,波谷越深,应力集中就越严重。
因此,表面粗糙度影响零件的抗疲劳强度。
4. 影响抗腐蚀性粗糙表面的微观凹谷处易存积腐蚀性物质,久而久之,这些腐蚀性物质就会渗入到金属内层,造成表面锈蚀。
此外,表面粗糙度对接触刚度、密封性、产品外观、表面光学性能、导电导热性能以及表面结合的胶合强度等都有很大影响。
所以,在设计零件的几何参数精度时,必须对其提出合理的表面粗糙度要求,以保证机械零件的使用性能。
公差等级与粗糙度的关系表面粗糙度是反映零件表面微观几何形状误差的一个重要技术指标,是验证零件表面质量的主要依据;它选择的合理与否,直接关系到产品的质量,使用寿命和生产成本。
机械制造基础ch12表面粗糙度

幅度参数
1、轮廓算术平均偏差Ra [旧国标:Ra] (the arithmetical mean of the departures)
在取样长度内,被测轮廓上各点至轮廓中线偏距绝对值
的算术平均值。 Ra值能客观反映被测表面的微观几何特
性。——普遍采用
Ra
1 l
l 0
y
x
dx 1 n
止波长至长波截止波长这两个极限值之间的波长 范围称为传输带。三种滤波器的截止波长不同, 具体数值见GB/T 6062-2009。
为了评价实际表面轮廓上的某一几何形状误
差,可以通过轮廓滤波器来呈现这一几何形状误 差,过滤掉其他的几何形状误差。
对表面轮廓采用轮廓滤波器λs抑制短波后得 到的总的轮廓,称为原始轮廓。
评定长度内在给定水平截面高度c上轮廓的实体材料长度 Ml(c)与评定长度的比率。Rmr(c)能直观反映实际接 触面积的大小,是反映零件表面耐磨性能的指标。
第二节 表面粗糙度的选择
一、评定参数的选择(Basic Nomenclature)
标准规定,幅度参数是首选参数,是必须标 注的参数,如零件无特殊要求,一般仅选用幅度 参数。只有对于少数零件的重要表面有特殊使用 要求时才选用附加参数。
原因
表面粗糙度对机械零件使用性能的影响
1 配合性质 2 摩擦、磨损 3 接触刚度下降 4 疲劳强度下降 5 耐腐蚀性降低 6 密封性降低
第一节
第一节 表面粗糙度的评定
一、基本术语(Basic Nomenclature) 1、 表面轮廓(Surface Profile)
平面与实际表面相交所得的轮廓,称为表面轮廓。
评定表面粗糙度数值的基准线,其方向应与被 测轮廓的方向一致 。
粗糙度培训课件

原子力显微镜(AFM)
总结词
通过检测探针与样品表面间的微弱作用力来表征表面形貌。
详细描述
原子力显微镜(AFM)是一种高分辨率的表面形貌测量设备,其工作原理是通过 检测探针与样品表面间的微弱作用力来表征表面形貌。AFM可以在纳米尺度上对 样品表面进行无损、无污染的测量,广泛应用于材料科学、生物学等领域。
触针式仪器的针头磨损问题
触针式仪器针头磨损是常见的仪器问题,它会影响测量结果 的准确性和可靠性。
由于长时间使用或频繁接触粗糙表面,触针式仪器的针头容 易磨损。磨损的针头会导致测量结果失真,因此需要定期检 查和更换针头。为减少针头磨损,可以调整触针的施加压力 、选择更耐磨的针头材料或优化触针的结构设计。
人工智能与机器学习在粗糙度检测中的应用
01
02
03
深度学习算法
利用深度学习算法对粗糙 度图像进行自动识别和分 类,提高检测精度和效率 。
数据驱动模型
基于大量数据建立粗糙度 检测模型,通过机器学习 算法实现自适应调整和优 化。
智能传感器技术
将人工智能技术与传感器 技术相结合,实现实时、 在线、自动的粗糙度检测 。
用环境,保持清洁并稳定环境条件。
数据处理与分析中的误差来源
数据处理与分析过程中可能引入多种误差,如信号噪声、数据处理算法的误差等。
在获取表面粗糙度数据后,需要进行数据处理与分析以提取表面特征。在此过程中,数据采集的噪声、算法的不完善或人为 操作失误都可能导致误差的产生。为减小误差,可以采用数字滤波技术去除噪声、优化数据处理算法并提高操作人员的技能 水平。此外,对同一表面进行多次测量并取平均值也是一种减小误差的方法。
光干涉式仪器对环境的要求问题
光干涉式仪器对环境的要求较高,温度、湿 度和尘埃等因素都可能影响其测量精度。
公差配合基础知识培训(1)可修改文字

-0.025
轴 -0.041
二、尺寸公差基础知识
例1 已知轴
mm,孔 60 0.01 0.03
60
0.03 0
mm,求孔、轴的极限尺寸和公差。
公差基础知识培训
公差基础知识培训
一、公差与测量概述
二、尺寸公差基础知识
目
三、形位公差基础知识
录
四、表面粗糙度基础知识
五、测量技术基础知识
一、公差与测量概述
(一)互换性概述
1、什么叫互换性? (1)定义:
互换性是指同一规格的零件或部件,不需要任何挑选、 调整或附加修配(如钳工修配),就能直接装配,并能保证产 品使用要求的一种特性。
标准的含义:为在一定的范围内获得最佳秩序,对活动或结果规定的 共同的和重复使用的规则、导则或特性文件。它是实现互换性的基础。
2 . 标准化:现代化生产的特点是品种多、 规模大、 分工细、 协作多, 为使社会生产有序地进行,必须通过标准化使产品规格简化,使分散的、
局部的生产环节相互协调和统一。
标准化的含义:制定、颁布、实施标准的全部活动过程。
检验:是确定零件的几何参数是否在规定的极限范围内, 并作出合格性判断,而不必得出被测量的具体数值。
测量:是将被测量与作为计量单位的标准量进行比较,以 确定被测量的具体数值的过程。
意义:检测不仅用来评定产品质量,而且用于分析产生不 合格品的原因,及时调整生产,监督工艺过程,预防废品产生 。检测是机械制造的“眼睛”。产品质量的提高,除设计和加 工精度的提高外,往往更有赖于检测精度的提高。所以,合理 地确定公差与正确进行检测,是保证产品质量、实现互换性生 产的两个必不可少的条件和手段。
二、尺寸公差基础知识
(一) 尺寸的基本术语
表面粗糙度 基础2
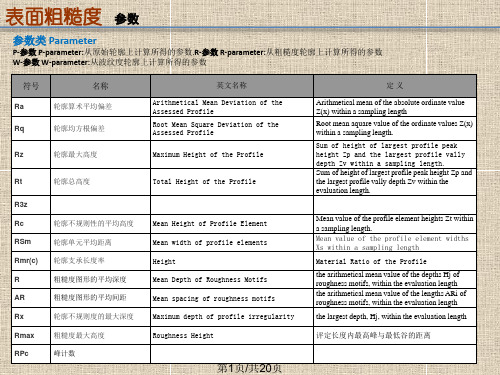
表面粗糙度 Motif
Motif概念
轮廓单峰 Local peak of profile 两相邻轮廓最低点之间的轮廓部分。
轮廓单谷 Local vally of profile 两相邻轮廓最高点之间的轮廓部分。
Motif 图形 不一定相邻的单峰之间的原始轮廓部分。 表征Motif的参量 1)长度Ari 2)两个深度Hi和Hi+1 3)T型特征:两个深度中最小的一个。
在一个取样长度内纵坐标值Z(x) 的均方根值
第3页/共20页
表面粗糙度 参数
幅度参数 3)轮廓最大高度(Rz,Rt)
在一个取样长度内最大轮廓峰 高和最大轮廓谷深之和的高度
Rz =︱Zpmax︱+︱Zvmax︱ Rt =︱Zpmax︱+︱Zvmax︱
4)R3z(Daimler Benz Standard 31007-1983) R3zi的定义为,粗糙度轮廓上一个取样长 度lr内第3高的轮廓峰和第3深的轮廓谷之间 的垂直距离,如图 参数R3z示意图
the arithmetical mean value of the depths Hj of roughness motifs, within the evaluation length the arithmetical mean value of the lengths ARi of roughness motifs, within the evaluation length
形状特廓的 实体材料长度Ml(c)与评定长度 ln的比率。
第6页/共20页
表面粗糙度 参数
DIN参数 7)最大粗糙度(Rmax)
评定长度内最高峰与最低谷的 距离。
8)(RPc) (prEN 10049)
表面粗糙度应用
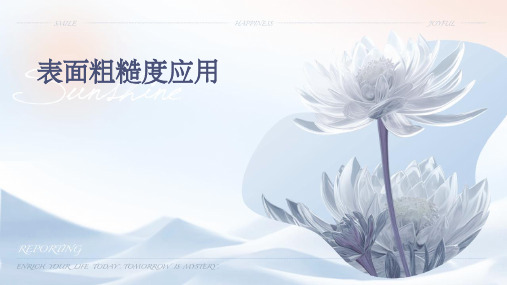
表面粗糙度影响接触刚度和稳定性,从而影响耐磨性。粗糙 度值较高的表面可能导致接触刚度降低和稳定性变差,加剧 磨损。
03
表面粗糙度在航空航天领 域的应用
表面粗糙度对飞机发动机性能的影响
表面粗糙度对飞机发动机的性能具有显著影响。粗糙的表面 会导致气流在发动机内部产生湍流,增加摩擦和热量,降低 发动机效率。因此,需要控制表面粗糙度,以保持发动机的 性能和稳定性。
表面粗糙度应用
目录 CONTENT
• 表面粗糙度基础 • 表面粗糙度在机械工程中的应用 • 表面粗糙度在航空航天领域的应
用 • 表面粗糙度在汽车工业中的应用 • 表面粗糙度在其他领域的应用
01
表面粗糙度基础
定义与测量
定义
表面粗糙度是指物体表面微观不平度 的程度,通常是指在加工过程中由于 刀痕、切削、砂轮磨削等产生的表面 粗糙不平的微观表现。
测量
表面粗糙度的测量通常采用触针式表 面粗糙度测量仪,通过触针在试样表 面滑行来测量表面的微观不平度。
表面粗糙度的影响因素
加工方法
不同的加工方法会对表面粗糙度产生影响,如 车削、铣削、磨削等。
刀具或砂轮的粒度
刀具或砂轮的粒度越小,加工后的表面粗糙度 值越小。
进给量与切削深度
进给量与切削深度的大小也会影响表面粗糙度。
表面粗糙度决定了车漆表面的微观结 构,从而影响车漆表面的光泽度和质 感。
表面粗糙度在汽车涂装工艺中的应用
在汽车涂装工艺中,表面粗糙度 可以影响涂层的附着力和装饰性。
适当的表面粗糙度可以提高涂层 与基材之间的附着力,增强涂层
的耐久性和装饰性。
在涂装前处理过程中,表面粗糙 化处理可以提高涂层的附着力和
表面粗糙度基础知识
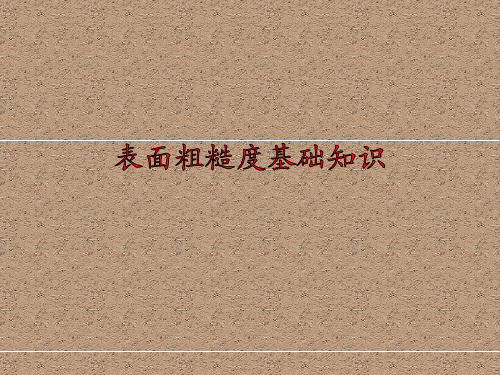
10.什么称为轮廓算术平均中线?
答:轮廓的算术平均中线是在取样长度内, 划分实际轮廓为上、下两部分,且使上、 下面积相等的线。
11.基本评定参数为哪些?
答:三项高度参数为基本评定参数,即轮 廓算术平均偏差(Ra)、微观不平度十点 高度(Rz)和轮廓最大高度(Ry);另三 项为附加评定参数,即轮廓微观不平度的 平均间距(Sm)、轮廓单峰平均间距(S)
5. 什么称为实际轮廓?
答:是平面与实际表面相交所得的轮廓线。 按照相截方向的不同,它又可分为横向实 际轮廓和纵向实际轮廓。在评定和测量表 面粗糙度时,除特殊指明,通常均按横向 实际轮廓,即与加工纹理方向垂直的截面 上的轮廓。
6. 什么称为取样长度?
答:用于判别具有表面粗糙度特征的一段 基准线长度。表面越粗糙,取样长度就应
38.用类比法确定表面粗糙度时,对高度 参数一般按哪些原则选择?
答:同一零件上,工作表面的表面粗糙度 值应小于非工作表面。摩擦表面的表面粗 糙度值应小于非摩擦表面;滚动摩擦表面 的表面粗糙度值应小于滑动摩擦表面;运 动速度高、单位压力大的表面粗糙度值应
小。受循环载荷的表面及易引起应力集中 的部位(如圆角、沟槽)表面粗糙度值应 选得小些。配合性质要求高的结合表面, 配合间隙小的配合表面以及要求连接可靠, 受重载的过盈配合表面等都应取较小的表 面粗糙度值。配合性质相同,零件尺寸越 小,其表面粗糙度值应越小。同一精度等 级,小尺寸比大尺寸、轴比孔的表面粗糙 度值要小。对于配合表面,其尺寸公差、 形状公差、表面粗糙度应当协凋,一般情 况下有一定的对应关系。
1. 什么称为表面粗糙度?
答:表面粗糙度是指零件加工表面上具有 的由较小间距和峰谷所组成的微观几何形 状特征。它是一种微观几何形状误差。
机械基础(表面粗糙度)模板
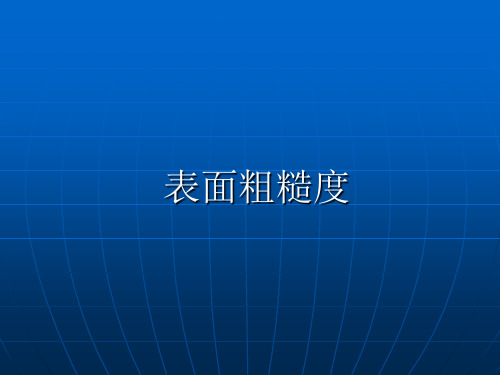
指向并接触表面。
必要时,表面结构符号也可用带箭头或黑点的指引线引出标注。
图4.9 符号从材料外指向并接触表面
(3)用指引线引出标注表面结构要求,如图4.10所示。
图4.10 引出标注表面结构
(4)表面结构要求标注在尺寸线上。
(5)表面结构要求标注在形位公差框格的上方。
(6)表面结构要求标注在圆柱特征的延长线上。
图4.1 加工误差示意图
2.表面粗糙度对互换性的影响 表面粗糙度直接影响产品的质量,对零件表面许多功 能都有影响。其主要影响: 1、配合性质的稳定性 2. 零件表面的耐磨性 3. 零件表面的耐腐蚀性 4. 疲劳强度 5、密封性 6、机器或仪器的工作精度 7、产品 外观 8、设备的震动、噪音及动力消耗。
(3)摩擦表面应比非摩擦表面的粗糙度参数值小,滚动轴承表面 应比滑动摩擦表面的粗糙度参数值小。
(4)运动速度越高,粗糙度参数值越小。
(5)配合性质要求越稳定,其配合面的粗糙度参数值越小。
(6)尺寸公差等级高,形状位置精度高,其表面粗糙度参数值越
小;同一公差等级,轴应比孔的粗糙度参数值小。
(7)腐蚀性、密封性要求越高,粗糙度参数值应越小。
(7规定了一些简化标注方法,使用时可查阅GB/T 131— 2006中的有关规定。
4.4 表面粗糙度的选择 表面粗糙度参数值选择应遵循既满足零件表面的功能要求,又考 虑经济性的原则,一般用类比法确定。 其选择原则如下。
(1)既要满足零件表面的功能要求,又要考虑尽量简化加工工 艺和降低加工成本,应尽量选择大的参数值。 (2)在同一零件上,工作表面的粗糙度数值一般小于非工作表面 的粗糙度数值。
度,即具有表面粗糙度特征的一段基准线长度。
X轴的方向与轮廓总的走向一致,一般应包括5个以
表面粗糙度的讲解(A类基础)

一个轮廓谷。当在若干个连续的取样长度上确定若干个轮廓单 元时,在每一个
取样长度的始端或末端评定的峰和谷仅在每个取样长度的始 端计人一次。
3.2.8 纵坐标值 Z(x) 被评定轮廓在任一位置距X轴的高度。 注:若纵坐标位于X轴下方,该高度被视作负值,反之则为正值。
a教类
20
Xp 3.2.9 局部斜率 Zp
4.2 幅度参数(纵坐标平均值)
4.2.1 评定轮廓的算术平均偏差 Pa、Ra、Wa
在一个取样长度内纵坐标值Z(x)绝对值的算术平均值。
Pa、Ra、Wa 1 l Z (x) dx
l
依据不同的情况,式中
l
0=
lp、lr、lw
。
4.2.2 评定轮廓的均方根偏差 Pq、Rq、 Wq
在一个取样长度内纵坐标值Z(J)的均方根值。
a教类
21
3.2.10 轮廓峰高 Z p 轮廓最高点距X轴线的距离(见图3)。
3.2.11 轮廓谷深 Z v X轴线与轮廓谷最低点之间的距离(见图3)
3.2.12 轮廓单元的高度 Z t 一个轮廓单元的峰高和谷深之和(见图3)。
3.2.13 轮廓单元的宽度 X s X轴线与轮廓单元相交线段的长度(见图3)。
Pq、Rq、Wq 1 l Z 2 ( x)dx l0
依据不同情况,式中 l = lp、lr、lw 。
a教类
25
4.2.3 评定轮廓的偏斜度 Psk、Rsk、Wsk
在一个取样长度内纵坐标值Z(x)三次方的平均值分别与Pq、Rq和
a教类
24
4.1.5 轮廓的总高度 Pt、Rt、Wt 在评定长度内最大轮廓峰高Zp和最大轮廓谷深Zv之和。 注:1 由于Pt、Rt、Wt 是根据评定长度而不是在取样长度上定义的,以 下关系对任何轮廓来讲都成立:
6.3表面粗糙度
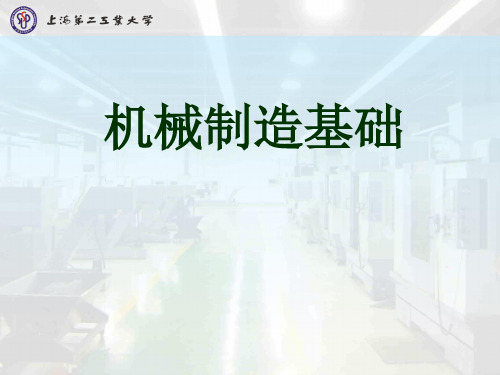
3.基本符号周围的有关标注
a —第一个表面粗糙度轮廓 (单一)要求(μm); b c — 第二个表面粗糙度轮廓要求 ; — 加工方法;
d— 表面纹理和纹理方向; e— 加工余量(mm)。
图6.3.9粗糙度要求的注写位置
4.标注示例见图6.3.10及图6.3.11
图6.3.11 粗糙度标注示例
表面粗糙度轮廓评定参数共 4个: Ra —轮廓算术平均偏差 基本参数 2个
附加参数 (辅助参数) 2 个
Rmr(c)是与轮廓曲线形状相关的评定参数,当c值一定时, Rmr(c)值愈大,则支承能力和耐磨性越好,如图6.3.8所示。 在评定零件的表面粗糙度时,轮廓间距小于0.01l的轮廓单峰 间距值不计入o
Zi
Ra
Ra 1 Z ( x) dx Ra 1 Zi n i1 lr 0
Z(x)
lr
n
算术平均 偏差Ra
X lr
图6.3.6
(2)轮廓的最大高度 Rz
峰顶线
Z(x)
Z P1
ZPmax
在lr内
Rz ZP max ZV min
中线
Rz
Z v1
lr
Z v2
X
Z vmax
最大高度Rz
一般按S分: 间距S
S<1mm 为表面粗糙度轮廓;
1≤S≤10mm为表面 波纹度轮廓;
S>10mm为 f形状.。 高低
Z
表面粗糙度轮廓的产生: (1) 切削后遗留 的刀痕;
(2) 切削过程中切屑分离时的塑性变形; (3) 以及机床等工装系统的振动等。
3.表面粗糙度轮廓对零件使用性能的影响 (1) 对摩擦和磨损的影响 表面不是越光越好。 (2)对配合性质的影响 (3)对抗疲劳强度的影响 (4) 对抗腐蚀性的影响
- 1、下载文档前请自行甄别文档内容的完整性,平台不提供额外的编辑、内容补充、找答案等附加服务。
- 2、"仅部分预览"的文档,不可在线预览部分如存在完整性等问题,可反馈申请退款(可完整预览的文档不适用该条件!)。
- 3、如文档侵犯您的权益,请联系客服反馈,我们会尽快为您处理(人工客服工作时间:9:00-18:30)。
在应用短波长滤波器λs之后的总的轮廓 * 原始轮廓是评定原始轮廓参数的基础
而后经过了3次修订成为GOCT2789-1973《表面粗糙度参数和特征》,该标准也采用中线制,并规定了包括 轮廓均方根偏差(即现在的Rq)在内的6个评定参数及其相应的参数值。
其它工业国家的标准大多是在50年代制定的,如联邦德国在1952年2月发布了DIN4760和DIN4762有关 表面粗糙度的评定参数和术语等方面的标准等。
表面粗糙度 概念与基础
基本概念
表面形态的三个层次:
形状误差
表面波纹度Leabharlann 表面粗糙度形状误差
表面波纹度
表面粗糙度
表面粗糙度 概念与基础
基本概念
表面形态的三个层次:
表面粗糙度 概念与基础
表面粗糙度对零件功用的影响 ●影响零件的耐磨性。
●影响配合性质的稳定性。 对于间隙配合,相对运动的表面因其粗糙不平而迅速磨损,致使间隙增大;对于过盈配合,表面轮廓峰顶 在装配时容易被挤平,使实际有效过盈量减小,致使联接强度降低。
确定粗糙度与波纹度成分之间相交界限的滤波器。
λf滤波器 λf profile filter
确定存在于表面上的波纹度与比 它更长的波的成分之间相交界限的 滤波器。
表面粗糙度 术语
表面粗糙度 术语
轮廓 profile
表面轮廓 Surface profile
平面与实际表面相交所得的轮廓,
* 实际上通常采用一条名义上与实际表面平行和在一个适当方向的法线来选择一个平面
表面粗糙度 术语
GB/T 3505《表面粗糙度术语表面及其参数》 ISO 4287 Geometrical Product Specifications (GPS) - Surface texture: Profile method - Terms, definitions and surface texture parameters
随着我国加入WTO 和与国际标准接轨,1993年又对GB/T131—1983进行了修订,主要对表面粗糙度参数 Ra、Rz、Ry的上(下)限值和最大(小)值加以区分,指出了在什么情况下用最大值,什么情况下用最小 值。GB/T131—1993《表面粗糙度符号、代号及其注法》沿用至今
各国的国家标准中都采用了中线制作为表面粗糙度参数的计算制,尽管具体参数千差万别,但其定义 的主要参数依然是Ra(或Rq),这也是国际间交流使用最广泛的一个参数。
表面粗糙度是不是越小越好?不一定:
当润滑非常重要时,表面上需有足够多的谷用于存储油 表面上足够的的峰用于吸附油漆和粘结剂 表面分布充足的谷可提高工件的可锻(塑)性 外观要求
流体阻力 光的反射
表面粗糙度 历史沿革
粗糙度研究的历史沿革
■ 表面粗糙度对机器零件表面性能的影响从1910s开始首先受到注意,在飞机和飞机发动机 设计中,由于要求用最少材料达到最大的强度,人们开始对加工表面的刀痕和刮痕对疲劳强 度的影响进行研究。但由于测量困难,当时没有定量数值上的评定要求,只是根据目测感觉 来确定。
●影响振动与噪音。
●影响零件的疲劳强度。 零件表面越粗糙,凹痕就越深,当零件承受交变荷载时,对应力集中更敏感。使疲劳强度降低,导致零件 表面产生裂纹而损坏。
●影响零件的抗腐蚀性。 表面越粗糙,越容易将腐蚀物质存于谷中,造成对工件表面的腐蚀。
●影响零件的密封性。 粗糙的表面结合时,两表面只在局部点上接触,中间有缝隙,影响密封性。因此,提高表面粗糙度,可提 高其密封性。
我国的表面粗糙度标准的制订工作是从五十年代初开始的。1951年颁布的中华人民标准620.040—13 《工程制图表面记号及处理说明》。1981年到1982年期间对GB/T131—1974进行了修订,经过修订后的标 准改为三个标准,即GB/T1031—1983《表面粗糙度 参数及其数值》、GB/T3505—1983《表面粗糙度 术语 表面及其参数》和GB/T131—1983《表面粗糙度 代号及其注法》。
■ 1920s~30s,世界上很多工业国家广泛采用三角符号(▽)的组合来表示不同精度的加工表 面。
■ 为定量研究表面粗糙度,1920s末到1930s,德、美、英等国专家设计制作了轮廓记录仪、 轮廓仪。同时也产生出了光切式显微镜和干涉显微镜等用光学方法的测量仪器,给从数值上 定量评定表面粗糙度创造了条件。
轮廓 Profile
轮廓滤波器 profile filter 把轮廓分成长波和短波成分的滤波器 *在测量粗糙度波纹度和原始轮廓的仪器中使用三种滤波器,它们的传输特性相同截止波长不同。
λs 滤波器 λs profile filter 确定存在于表面上的粗糙度与比它更短的波的成分之间相交界限的滤波器。
λc滤波器 λc profile filter
■ 1940年英国的Tylor-Hobson公司研制成功了粗糙度仪。
表面粗糙度 历史沿革
标准制定方面 美国在1940年发布了ASA B46.1国家标准,之后又经过几次修订,成为现行标准ANSI/ASME B46.1-1988
《表面结构表面粗糙度、表面波纹度和加工纹理》,该标准采用中线制,并将Ra作为主参数。 苏联在1945年发布了GOCT2789-1945《表面光洁度、表面微观几何形状、分级和表示法》国家标准,
■ 1930s起,已对表面粗糙度定量评定参数进行了研究,如美国的E.J.Abbott就提出了用距 表面轮廓峰顶的深度和支承长度率曲线来表征表面粗糙度,于1936年研制成功了可供现场测 量表面粗糙度的轮廓仪。
德国的G.Schmaltz从1929年开始对表面不平度的深度进行了定量测量,1936年出版了论 述表面粗糙度的专著,对表面粗糙度的评定参数和数值的标准化提出了建议。
●其他影响:对零件的外观、测量精度、表面光学性能、导电导热性能、流体动力学性能和胶合强度等。
表面粗糙度 概念与基础
表面粗糙度对零件功用的影响
舰舶的船体由粗糙度引起的磨擦阻力占总的流体阻力的80~90%。 使用中的船舶因船体油漆裂纹、腐蚀及污秽(fouling)最多可能增 加40%的动力消耗。
测量表面粗糙度用于: 1 生产过程控制 2 预测工件的表现 3 监控零件的性能