微细切削加工技术研究进展
微铣加工关键技术研究现状与发展
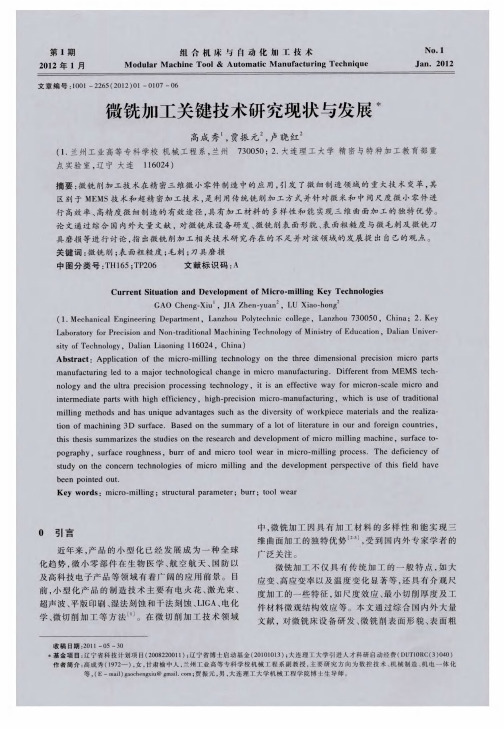
参 数对 表面 粗 糙 度 的影 响 , 立 了 表 面 粗糙 度 数 学 建 模 型 。Bs co等 建 立 了 微 铣 理 论 生 成 表 面 模 iac s 型 。K a — igL 等 用 硬质 合 金刀 具 干铣 削 热作 u nM n i
大影 响 , 当 进 给 量 小 到 一 定 程 度后 表 面 粗糙 度 反 且
而会增加 , 因此 存 在 一 个 最 优 的 进 给量 。Le等 e
通 过实 验研 究 了微 细 铣 削铝 和 铜 时产 生 的 5 进 行 了 黄 铜 微 铣 削 实 n
微量 进 给 。
齿 进 给量为 0 5 . m 时才 会 出 现几 毫 米 长 的 毛刺 , 大 多 数 情 况 下 毛 刺 的 高 度 在 5 ~6 1 0 m。G oLa q x w .in C en 等研 究 了微铣 加工 件表 面 毛刺 的形 成 过程 。 hr
V g r 采用 刃 口半 径 5 ol e m 和 2x 的 两 种 铣 刀在 l m 同样 的进 给量范 围 内进 行微 端 铣 实验 研 究微 细 切 削 的表 面形成 机 理 , 现 刃 口半 径 对 表 面 粗 糙 度 有 很 发
大连 理工 大学研 发 的微铣 床 ( 6 整 体 尺寸 图 ) 14 m ×14 m × 0 m 工作 空 间为 5 rm×5 mm 9m 9m 4 0 m, 0 a 0 ×12 m, 0 m 定位 精 度 1 m, 复 定 位 精 度 0 2x 主 I 重 x .1 m,
轴最 高 转 速 10 0 rmi, 以 实 现精 度 为 2 n 的 4 0 0/ n 可 0m
至关重 要 。 国 内外 学 者 针 对 微 铣 削 表 面 形 貌 、 面 表
南京 航空航 天 大学 机 电学 院 和北 京 航 空精 密 机
微细加工技术概述及其应用

2011 年春季学期研究生课程考核(读书报告、研究报告)考核科目:微细超精密机械加工技术原理及系统设计学生所在院(系):机电工程学院学生所在学科:机械设计及理论学生姓名:杨嘉学号:10S008214学生类别:学术型考核结果阅卷人微细加工技术概述及其应用摘要微细加工原指加工尺度约在微米级范围的加工方法,现代微细加工技术已经不仅仅局限于纯机械加工方面,电、磁、声等多种手段已经被广泛应用于微细加工,从微细加工的发展来看,美国和德国在世界处于领先的地位,日本发展最快,中国有很大差距。
本文从用电火花加工方法加工微凹坑和用微铣削方法加工微小零件两方面描述了微细加工技术的实际应用。
关键词:微细加工;电火花;微铣削1微细加工技术简介及国内外研究成果1.1微细加工技术的概念微细加工原指加工尺度约在微米级范围的加工方法。
在微机械研究领域中,从尺寸角度,微机械可分为1mm~10mm的微小机械,1μm~1mm的微机械,1nm~1μm的纳米机械,微细加工则是微米级精细加工、亚微米级微细加工、纳米级微细加工的通称。
广义上的微细加工,其方式十分丰富,几乎涉及现代特种加工、微型精密切削加工等多种方式,微机械制造过程又往往是多种加工方法的组合。
从基本加工类型看,微细加工可大致分为四类:分离加工——将材料的某一部分分离出去的加工方式,如分解、蒸发、溅射、切削、破碎等;接合加工——同种或不同材料的附和加工或相互结合加工方式,如蒸镀、淀积、生长等;变形加工——使材料形状发生改变的加工方式,如塑性变形加工、流体变形加工等;材料处理或改性和热处理或表面改性等。
微细加工技术曾广泛用于大规模集成电路的加工制作,正是借助于微细加工技术才使得众多的微电子器件及相关技术和产业蓬勃兴起。
目前,微细加工技术已逐渐被赋予更广泛的内容和更高的要求,已在特种新型器件、电子零件和电子装置、机械零件和装置、表面分析、材料改性等方面发挥日益重要的作用,特别是微机械研究和制作方面,微细加工技术已成为必不可少的基本环节。
现代机械设计制造工艺和精密加工技术研究

现代机械设计制造工艺和精密加工技术研究摘要:工业4.0战略背景下,机械制造产业产品质量,与制造工艺和精密加工有密切联系。
科技作为发展第一生产力,优化机械设计工艺和技术,为产业发展注入活力。
夯实机械制造实力的同时,满足市场提出的特殊要求,助力机械制造产业发展。
针对机械制造发展方向、工艺、技术等深入探索,对现代机械设计发展前景展望,对于现代化机械领域发展有重要的现实意义。
关键词:现代机械设计;制造工艺;精密加工技术引言:市场经济飞速发展过程中,对现代化工艺生产提出更高要求。
现代化生产制造,不仅要保证产品质量,还应在原有基础上设计优化,保证产品美观度。
因此,基于机械设计质量和产量等要求,机械制造领域中,精密加工技术得以发展,通过对产品精密设计,提高制造工艺水准,满足机械制造产业实力,促进机械设计领域稳定发展。
一、机械制造工艺与精密加工技术概述(一)机械制造工艺机械制造工艺是现代化机械领域的重要内容,以高标准施行制造工艺。
先进的制造工艺,能够提高材料使用效率,提高产品精密性。
实际发展中,能够发现机械制造工艺还存在一定不足,导致技术有待完善,难以满足现阶段的机械生产需求。
还需要根据工艺体系进行升级,促使整体制造工艺水平提升。
(二)精密加工技术精密加工技术是实现机械产品精细化生产的重要内容,对于整个制造业发展有促进性作用。
具备先进的精密加工技术,能够显著提高机械制造工艺,保障行业长效发展。
精密加工技术包含了切削技术、研磨技术、纳米技术等,能够通过精密加工提高产品制造质量,满足高精度零件、产品加工需求,为制造行业发展提供良好支撑。
二、现代机械设计制造工艺和精密加工技术概述(一)特点1.关联性现代机械设计制造与精密加工均有一定难度,其复杂性体现在产品设计、生产等多个环节中。
两者在产品生产研发过程中,有关联性。
也就是说,任何一个环节出现问题,都会影响后续工作开展,导致工艺和加工技术效果差强人意。
2.系统化生产角度来看,现代机械制造工艺和精密加工技术是共同体的存在。
电化学微细加工技术的研究进展

电化学微细加工技术的研究进展李凤云【摘要】介绍了微细电化学加工的原理及其特点,系统地阐述了微细电化学加工在几个方面的研究情况和工艺特点,例如EFAB工艺、3D电化学加工、约束刻蚀剂层技术等.微细电化学加工必将在未来的微纳加工中起着举足轻重的作用.【期刊名称】《江西化工》【年(卷),期】2016(000)001【总页数】3页(P1-3)【关键词】微细加工EFAB工艺;3D电化学加工;复杂三维结构【作者】李凤云【作者单位】南昌航空大学,江西南昌330063【正文语种】中文随着微机电系统(Mcro elecro mechanical system:MEMS)和微电子(microelectronics)技术的日趋发展,在微纳米尺度上的、具有三维加工能力的、能处理性能优异的金属材料(特别是一些极限作业环境下所要求的高强度、高韧性、高耐磨、耐高温、耐冲击、抗疲劳等性能的合金材料)的微细加工方法,正受到国内外科技界的广泛关注。
电化学加工(Elecrochemical Machining:ECM)一般没有宏观的切削力作用,且复制精度、重复精度、表面质量、加工效率、加工过程稳定性等方面都比较优良,因此在加工行业中有着不可替代的优越性。
从机理上讲,由于ECM是通过金属离子的还原或金属的氧化对材料进行加工,材料的增加或去除都是以离子的形态进行的;因此,从理论上分析,只要控制好加工条件,选择适当的加工参数,可实现以离子数量级进行材料加工。
实践也证明了用电化学的方法进行微细加工是可行的。
EFAB(Electrochemical Fabrication)技术是由基于SFF(Solid freeform fabric-ation)中的分层制造原理[1]而提出的一种采用电化学方法制作三维多层微结构的技术[2]。
它的基本原理:首先利用3D CAD软件将所需加工的图形分解成为多数单个的适合制作成光刻模板的二维图形,然后将其加工成一种由金属阳极和绝缘材料构成的一组模具,通过电沉积方法将金属以及牺牲层金属按照光刻模板上的图形分别沉积出来,直至牺牲层金属溶解完全,就得到了所需的三维立体图形。
精密微细铣削工艺——机加工前沿技术
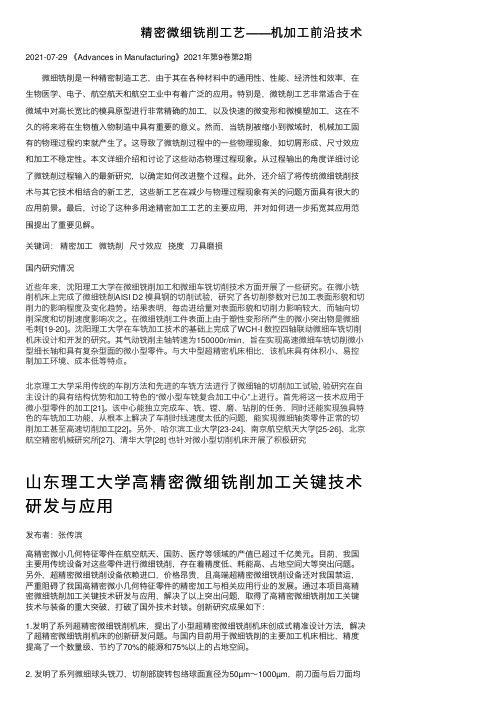
精密微细铣削⼯艺——机加⼯前沿技术2021-07-29 《Advances in Manufacturing》2021年第9卷第2期微细铣削是⼀种精密制造⼯艺,由于其在各种材料中的通⽤性、性能、经济性和效率,在⽣物医学、电⼦、航空航天和航空⼯业中有着⼴泛的应⽤。
特别是,微铣削⼯艺⾮常适合于在微域中对⾼长宽⽐的模具原型进⾏⾮常精确的加⼯,以及快速的微变形和微模塑加⼯,这在不久的将来将在⽣物植⼊物制造中具有重要的意义。
然⽽,当铣削被缩⼩到微域时,机械加⼯固有的物理过程约束就产⽣了。
这导致了微铣削过程中的⼀些物理现象,如切屑形成、尺⼨效应和加⼯不稳定性。
本⽂详细介绍和讨论了这些动态物理过程现象。
从过程输出的⾓度详细讨论了微铣削过程输⼊的最新研究,以确定如何改进整个过程。
此外,还介绍了将传统微细铣削技术与其它技术相结合的新⼯艺,这些新⼯艺在减少与物理过程现象有关的问题⽅⾯具有很⼤的应⽤前景。
最后,讨论了这种多⽤途精密加⼯⼯艺的主要应⽤,并对如何进⼀步拓宽其应⽤范围提出了重要见解。
关键词:精密加⼯微铣削尺⼨效应挠度⼑具磨损国内研究情况近些年来,沈阳理⼯⼤学在微细铣削加⼯和微细车铣切削技术⽅⾯开展了⼀些研究。
在微⼩铣削机床上完成了微细铣削AISI D2 模具钢的切削试验,研究了各切削参数对已加⼯表⾯形貌和切削⼒的影响程度及变化趋势。
结果表明,每齿进给量对表⾯形貌和切削⼒影响较⼤,⽽轴向切削深度和切削速度影响次之。
在微细铣削⼯件表⾯上由于塑性变形所产⽣的微⼩突出物是微细⽑刺[19-20]。
沈阳理⼯⼤学在车铣加⼯技术的基础上完成了WCH-I 数控四轴联动微细车铣切削机床设计和开发的研究。
其⽓动铣削主轴转速为150000r/min,旨在实现⾼速微细车铣切削微⼩型细长轴和具有复杂型⾯的微⼩型零件。
与⼤中型超精密机床相⽐,该机床具有体积⼩、易控制加⼯环境、成本低等特点。
北京理⼯⼤学采⽤传统的车削⽅法和先进的车铣⽅法进⾏了微细轴的切削加⼯试验, 验研究在⾃主设计的具有结构优势和加⼯特⾊的“微⼩型车铣复合加⼯中⼼”上进⾏。
微小零件加工的微细切削技术
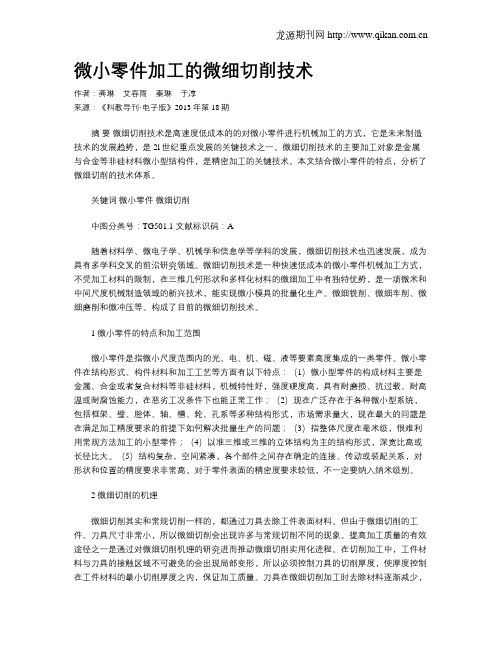
微小零件加工的微细切削技术作者:龚琳艾春雨秦琳于淳来源:《科教导刊·电子版》2013年第18期摘要微细切削技术是高速度低成本的的对微小零件进行机械加工的方式,它是未来制造技术的发展趋势,是2l世纪重点发展的关键技术之一。
微细切削技术的主要加工对象是金属与合金等非硅材料微小型结构件,是精密加工的关键技术。
本文结合微小零件的特点,分析了微细切削的技术体系。
关键词微小零件微细切削中图分类号:TG501.1 文献标识码:A随着材料学、微电子学、机械学和信息学等学科的发展,微细切削技术也迅速发展,成为具有多学科交叉的前沿研究领域。
微细切削技术是一种快速低成本的微小零件机械加工方式,不受加工材料的限制,在三维几何形状和多样化材料的微细加工中有独特优势,是一项微米和中间尺度机械制造领域的新兴技术,能实现微小模具的批量化生产。
微细铣削、微细车削、微细磨削和微冲压等。
构成了目前的微细切削技术。
1 微小零件的特点和加工范围微小零件是指微小尺度范围内的光、电、机、磁、液等要素高度集成的一类零件。
微小零件在结构形式、构件材料和加工工艺等方面有以下特点:(1)微小型零件的构成材料主要是金属、合金或者复合材料等非硅材料,机械特性好,强度硬度高,具有耐磨损、抗过载、耐高温或耐腐蚀能力,在恶劣工况条件下也能正常工作;(2)现在广泛存在于各种微小型系统,包括框架、壁、腔体、轴、槽、轮、孔系等多种结构形式,市场需求量大,现在最大的问题是在满足加工精度要求的前提下如何解决批量生产的问题;(3)指整体尺度在毫米级,很难利用常规方法加工的小型零件;(4)以准三维或三维的立体结构为主的结构形式,深宽比高或长径比大。
(5)结构复杂,空间紧凑,各个部件之间存在确定的连接、传动或装配关系,对形状和位置的精度要求非常高。
对于零件表面的精密度要求较低,不一定要纳入纳米级别。
2 微细切削的机理微细切削其实和常规切削一样的,都通过刀具去除工件表面材料。
微细加工技术及其应用
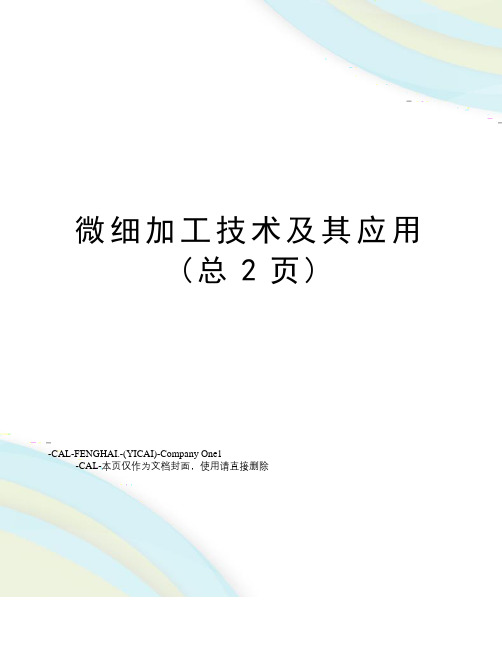
微细加工技术及其应用(总2页)-CAL-FENGHAI.-(YICAI)-Company One1-CAL-本页仅作为文档封面,使用请直接删除微细加工技术及其应用微细加工技术是由瑞士BinC公司发明的一种新型加工工艺,在2004年法国巴黎举办的国际表面处理展览会(SITS)和2004年在法国里昂举办的ALLIANCE展览会上荣获2项发明奖。
微细加工工艺和设备拥有国际专利保护。
微细加工技术结合了超精增亮和超精抛光两项革新技术,能够有选择性地保留表面的微观结构,以提高表面的摩擦和滑动性能(表面技术),以机械化和自动化取代传统的手工抛光,提高表面的美学功能。
这种微细加工技术应用于切削刀具、冲压和锻造工具,航空、汽车、医疗器械、塑料注射模具等机械零件的表面处理,能够极大地改善零件表面的性能。
微细加工原理微细加工技术采用全自动方式对金属零件表面进行超精加工,通过一种机械化学作用来清除金属零件表面上1~40μm的材料,实现被加工表面粗糙度达到或者好于ISO标准的N1级的表面质量。
微细加工技术主要应用于超精抛光和超精增亮这两个领域。
超精抛光使传统的手工抛光工艺自动化;而超精增亮则生成新的表面拓扑结构。
微细加工技术的一个突出优点是能够赋予零件表面新的微观结构。
这些微观结构能提高零件表面对特定应用功能的适应性。
如减小摩擦和机械差异、提高抗磨损性能、改善涂镀前后表面的沉积性能等。
总的说来,超精增亮可去除次级微观粗糙表面,次级粗糙表面的厚度在0~20μm之间,位于零件表面初级微观粗糙面的峰尖之间。
而超精抛光则部分或整体去除初级微观粗糙表面,其值在10~40μm之间,当然这取决于零件材料表面的初始状态。
微细加工技术迄今能够加工的材料有退火及淬火钢、铜及铜合金、铸铁、Inconel镍合金(镍基合金)、钛金属、表面硬涂层处理前后的预处理(PVD、CVD、电镀)。
技术专利微细加工技术是一种有选择性地精修被加工对象表面微观粗糙度和拓扑结构的创新性微观加工工艺。
面向微小零件加工的微细切削技术

面向微小零件加工的微细切削技术摘要:微细切削技术是高速度低成本的的对微小零件进行机械加工的方式,它是未来制造技术的发展趋势,是2l世纪重点发展的关键技术之一。
微细切削技术的主要加工对象是金属与合金等非硅材料微小型结构件,是精密加工的关键技术。
本文结合微小零件的特点,分析了微细切削的技术体系。
关键词:微小零件;微细切削;技术Abstract: the subtle cutting technology is high speed of low cost to tiny mechanical parts of the process, it is the future the development trend of manufacturing technology, is 2 l century focus on the development of the key technical one. Subtle cutting technology is the main processing objects such as metals and alloys of silicon micro small parts, is the key technology of precision processing. Based on the characteristics of small parts, and analyzes the technological system of fine cutting.Keywords: small parts; Subtle cutting; technology随着材料学、微电子学、机械学和信息学等学科的发展,微细切削技术也迅速发展,成为具有多学科交叉的前沿研究领域。
微细切削技术是一种快速低成本的微小零件机械加工方式,不受加工材料的限制,在三维几何形状和多样化材料的微细加工中有独特优势,是一项微米和中间尺度机械制造领域的新兴技术,能实现微小模具的批量化生产。
脉冲激光微细加工金刚石机理的研究进展

脉冲激光微细加工金刚石机理的研究进展陈梦;张凤林;欧阳承达;毛俊波;李盼来【摘要】Diamond is an ultimate material in terms of hardness,thermal conductivity and chemical resistance,and widely used in the cutting tools,abrasives,thermal devices and optical windows.The application of pulsed or ultrashort pulsed lasers in micromachining of diamond materials can promote the utilization of diamond materials in various fields.In this paper,the advance of research on the mechanism of machining of diamond materials by pulsed laser was generalized.The pulsed laser induced diamond graphitization and la-ser ablation in the machining of diamond materials were summarized.%金刚石具有极高的硬度、导热率及优异的化学稳定性,广泛应用于切削刀具、磨具、导热器件、光学窗口等领域。
脉冲激光尤其是超短脉冲激光可以对金刚石材料进行各种微细加工,是扩展金刚石材料在工业领域运用的一个重要手段,文章综述了国内外激光微细加工金刚石机理的研究进展,总结了脉冲激光在微细加工金刚石材料过程中的石墨化和材料蚀除机理。
【期刊名称】《超硬材料工程》【年(卷),期】2014(000)001【总页数】6页(P15-20)【关键词】激光技术;微细加工;金刚石;石墨化;蚀除【作者】陈梦;张凤林;欧阳承达;毛俊波;李盼来【作者单位】广东工业大学机电工程学院,广州 510006;广东工业大学机电工程学院,广州 510006;广东工业大学机电工程学院,广州 510006;广东工业大学机电工程学院,广州 510006;广东工业大学机电工程学院,广州 510006【正文语种】中文金刚石晶体属于立方晶系,具有面心立方晶胞结构,每个碳原子都以sp3杂化轨道与另外四个碳原子形成共价键,这样的特殊结构使其具备极高的硬度、导热率和优异的化学稳定性,被广泛应用于切削刀具、磨具、导热器件、光学窗口等领域[1-3]。
6061铝合金微细刨削的表面粗糙度试验研究

6061铝合金微细刨削的表面粗糙度试验研究陈子乾;杨光【摘要】试验研究了6061铝合金的微细刨削性能.在定制的精密雕铣床上,使用金刚石刀具在不同的切削条件下,对6061铝合金进行切削深度(0.005~0.1)mm的微细刨削,观察切削参数对工件表面粗糙度的影响.使用激光共聚焦显微镜对金刚石刀具以及各种切削条件下的加工表面进行分析.试验结果表明:切削速度和切削深度对铝合金工件刨削表面粗糙度影响很小,进给量是影响微细刨削铝合金表面粗糙度的主要原因.一般情况下,越小的进给量获得表面粗糙度值越小,但是进给量小到一定程度时,表面粗糙度趋于稳定.此时,工件表面的微裂痕,坑洞、划痕和材料本身的杂质是影响其表面粗糙度的主要因素.另外,单晶金刚石刀具的刃磨质量要优于聚晶金刚石刀具,因此可以获得更小的表面粗糙度值.结论表明,使用单晶金刚石刀具对6061铝合金进行切削速度v=2000mm/min、切削深度ap=10μ.m、进给量f=-10μm的微细刨削可以获得Ra37.3nm的表面.【期刊名称】《机械设计与制造》【年(卷),期】2016(000)005【总页数】4页(P115-117,121)【关键词】6061铝合金;微细刨削;表面粗糙度【作者】陈子乾;杨光【作者单位】集美大学机械与能源工程学院,福建厦门361021;集美大学机械与能源工程学院,福建厦门361021【正文语种】中文【中图分类】TH16;TG552.2;TH161.1微细加工技术是研究特征尺度在(0.01~1)mm范围并具有特定功能的器件与系统的设计与制造的综合交叉科学,是制造高性能设备和产品的关键技术之一。
其应用范围广,在高技术产业如微电子、国防、汽车、新能源、生物医学工程、环境与安全检测中应用广泛[1-2]。
微细加工技术主要包括有光刻技术、薄膜技术、离子注入加工技术、特种电加工技术以及微细切削技术等。
随着对产品功能要求的提高,微细切削技术凭借着效率高、成本低、适用材料广以及三维加工能力强的优势,在近年来得到迅速发展,并成为微细加工技术的主要手段,在微/纳制造领域发挥了越来越重要的作用,已经成为衡量一个国家制造业水平的重要标志[3-5]。
微细钻削铣削关键技术及应用基础研究

3、质量研究:通过控制原材料质量、优化加工参数等方式,提高加工质量。 在微细钻削铣削中,加工质量受到原材料性能、切削条件、刀具质量等多种因 素的影响。研究这些因素对加工质量的影响规律,有助于实现高质量加工。
参考内容
一、引言
随着科技的发展,制造业对零件的精度和性能要求越来越高,微细加工技术在 此领域中扮演着越来越重要的角色。微细铣削工艺,作为一种典型的微细加工 技术,被广泛应用于各种材料和零件的制造过程中。本次演示将探讨微细铣削 工艺的基础知识和实验研究。
微细钻削铣削关键技术及应用 基础研究
目录
01 引言
03
微细钻削铣削关键技 术
02
微细钻削铣削技术概 述
04 参考内容
引言
微细钻削铣削技术是一种先进的制造工艺,适用于精密零件的加工。随着科技 的不断进步,微细钻削铣削技术在航空、汽车、医疗等领域得到了广泛的应用。 本次演示将围绕微细钻削铣削关键技术及应用基础研究展开讨论,旨在深入探 讨微细钻削铣削技术的优势、关键技术、应用基础研究等方面,为相关领域的 研究和实践提供有益的参考。
2、刀具状态监测
刀具状态监测是微细钻削铣削技术的另一个关键技术。在加工过程中,刀具会 受到磨损、温度、应力等多种因素的影响,这些因素可能影响加工精度和表面 质量。因此,需要对刀具状态进行实时监测,以便在刀具磨损或破损时及时更 换刀具,从而确保加工过程的稳定性和精度。常用的刀具状态监测方法包括直 接监测法和间接监测法两种。
我们也需要加强跨学科合作,借鉴其他领域的最新技术和理论,推动微细加工 技术的发展和应用。
谢谢观看
四、结论与展望
本次演示通过对微细铣削工艺基础和实验研究的探讨,揭示了微细铣削过程中 的主要影响因素和不同材料的加工特性。然而,微细铣削工艺在实际应用中仍 存在许多问题需要解决,如刀具磨损、加工表面粗糙度等。未来,我们需要在 深入研究微细铣削工艺的基础上,通过不断改进和创新,提高微细铣削的加工 效率和精度,以满足制造业对零件精度和性能的更高要求。
微细切削加工技术
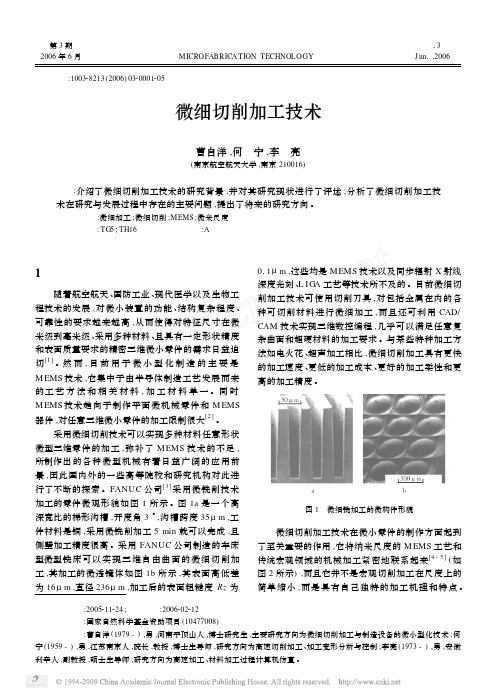
图 4 切削力与切屑变形
在传统加工过程中 ,切屑沿剪切面发生剪切变 形 ,然而在微细切削中 ,在切削刃周围的剪切应力却 显著的增加 ,通过正交微切削力分析模型还可以看 出 ,沿着刀具后刀面有弹性回复现象[28 - 29 ] 。由于刀 具刃口圆弧半径的存在 ,使得切削变形明显增大 ,切 削深度很小时 ,刀具刃口圆弧半径造成的附加变形 (犁切效应) 占总切削变形的比例很大 。微细切削加 工的切削力特征为 :切削力微小 ,单位切削力大 ,在 切削深度很小时切削力会急剧增大 ,这就是微细切 削的尺寸效应 。 215 微细切削加工的尺寸效应
2
微细加工技术
2006 年
由于对微细切削加工机床 、刀具 、磨损 、过程监控等 方面的研究还不够深入 ,限制了微细切削加工技术 进一步的发展[6 ] 。本文对微细切削加工技术目前面 临的主要问题进行了深入的探讨 。
图 2 微切削的加工尺度
2 关键问题的分析和讨论
211 微细切削加工机床 为了制造出高精度的微型零件 ,机床的尺寸必
在微细切削过程中由于切削层厚度已经十分薄其尺寸与微观尺度相近尺寸效应对加工精度的影响就变得十分明显传统的图3最小切屑厚度对切屑形成的影响在微细切削加工前需确定最小切屑厚度因为切屑变形依赖于最小切屑厚度而最小切屑厚度又依赖于刀具刃口的圆弧半径和工件材?的物??学4微细加工技术2006?制造精度?论和分析方法将?再适用
微细加工技术概述

微细加工技术概述XxxxxxxxxxXxxxxxxxxxxx摘要:微细加工原指加工尺度约在微米级范围的加工方法,现代微细加工技术已经不仅仅局限于纯机械加工方面,电、磁、声等多种手段已经被广泛应用于微细加工,从微细加工的发展来看,美国和德国在世界处于领先的地位,日本发展最快,中国有很大差距。
本文从用电火花加工方法加工微凹坑和用微铣削方法加工微小零件两方面描述了微细加工技术的实际应用。
关键词:微细加工,超细加工论文1.微细加工技术简介微细加工技术是精密加工技术的一个分支,面向微细加工的电加工技术,激光微孔加工、水射流微细切割技术等等在发展国民经济,振兴我国国防事业等发面都有非常重要的意义,这一领域的发展对未来的国民经济、科学技术等将产生巨大影响,先进国家纷纷将之列为未来关键技术之一并扩大投资和加强基础研究与开发。
所以我们有理由有必要加快这一领域的发展和开发进程。
微细加工技术应满足下列功能:1)为达到很小的单位去除率(UR),需要各轴能实现足够小的微量移动,对于微细的机械加工和电加工工艺,微量移动应可小至几十个纳米,电加工的UR最小极限取决于脉冲放电的能量。
2)高灵敏的伺服进给系统,它要求低摩擦的传动系统和导轨主承系统以及高精度跟踪性能的伺服系。
3)高平稳性的进给运动,尽量减少由于制造和装配误差引起的各轴的运动误差。
4)高的定位精度和重复定位精度。
5)低热变形结构设计。
6)刀具的稳固夹持和高的重复夹持精度。
7)高的主轴转速及极低的动不平衡。
8)稳固的床身构件并隔绝外界的振动干扰。
9)具有刀具破损和微型钻头折断的敏感的监控系统。
2.微细加工的特点微细加工技术是指加工微小尺寸零件的生产加工技术。
从广义的角度来讲,微细加工包括各种传统精密加工方法和与传统精密加工方法完全不同的方法,如切削技术,磨料加工技术,电火花加工,电解加工,化学加工,超声波加工,微波加工,等离子体加工,外延生产,激光加工,电子束加工,粒子束加工,光刻加工,电铸加工等。
微细铣削技术研究

题目:微细铣削技术研究
报告人:李光俊 任课老师:张弘弢 导师:贾振元 2011年04月23日
目录
一、研究背景及意义 二、微细制造技术简介 三、微细铣削加工机理 四、微细铣削刀具 五、微细铣削加工设备 六、微细铣削研究发展趋势
2
一、研究背景及意义
随着科学技术的不断发展,在航空航天、国防工业、汽车工 业、微电子工业、医疗器械、光学仪器等各个领域,对精密微 小零件的需求日益迫切。
从工艺方面对尺寸效应的研究
从模型方面对尺寸效应的研究
8
三、微细铣削加工机理
从力学方面对尺寸效应的研究
从力学方面对尺寸效应的研究涉及切削力、切削比能、 切削温度、刀具磨损、切屑形成、弹塑性变形等众多领域, 焦点集中在两个方面: 最小切削厚度的研究 由于最小切削厚度是探索切屑形成的最基本条件,从以金 刚石刀具为代表的超精密切削研究到当前的微铣削研究, 关于最小切削厚度的研究一直没有停止。 切削力的研究 由于微观尺度铣削加工的许多现象和变化难以观察和测量, 切削力作为一个受许多加工因素影响的函数,越来越受到 微切削研究领域的重视。
3
一、研究背景及意义
微小型化零件的尺寸范围为0.1~10mm,几何特征尺寸范围为 0.01~1mm,结构复杂且精度要求比较高。 如何实现适用于多种材料、结构复杂的小型化零件的高精度、 低成本加工成为微小型化制造技术的关键。
4
二、微细制造技术简介
微细制造技术是二十世纪七十年代开始才逐步发展起来 的前沿、交叉性新兴学科领域,是当前机械制造科学与技 术领域的前沿和热点,从美国的斯坦福大学开始,后续的 日本和欧洲各国均投入大量的人力进行探究。 微细机械加工技术以微小机械零件为加工对象,利用系 统化、集成化理论和技术,根据加工工件机构及要求实现 机床各部件的有机结合,在较小的空间内完成微小零件的 制造,实现在小空间内加工小零件的目的。 微细加工技术减小了整个制造系统以及零件的尺寸规模, 既可以节省能源又可以节省制造空间和资源,符合节能、 环保的生产模式,是绿色制造的发展方向之一,是衡量一 个国家制造技术水平的重要标志。
微细加工技术的发展及应用
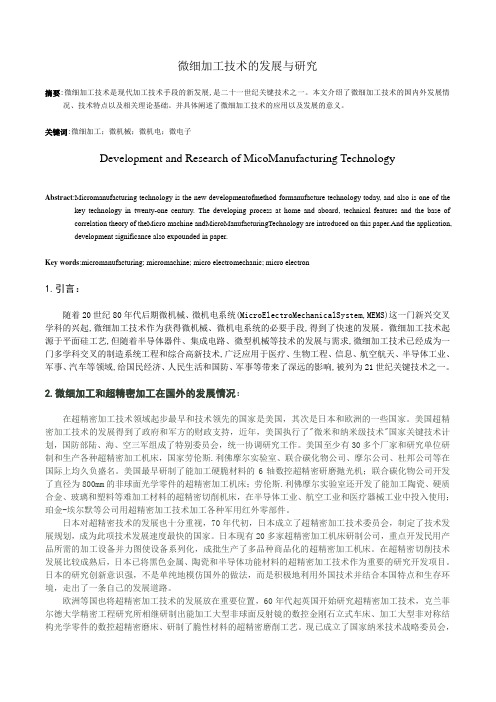
微细加工技术的发展与研究摘要:微细加工技术是现代加工技术手段的新发展,是二十一世纪关键技术之一。
本文介绍了微细加工技术的国内外发展情况、技术特点以及相关理论基础。
并具体阐述了微细加工技术的应用以及发展的意义。
关键词:微细加工;微机械;微机电;微电子Development and Research of MicoManufacturing TechnologyAbstract:Micromanufacturing technology is the new developmentofmethod formanufacture technology today, and also is one of the key technology in twenty-one century. The developing process at home and aboard, technical features and the base of correlation theory of theMicro machine andMicroManufacturingTechnology are introduced on this paper.And the application, development significance also expounded in paper.Key words:micromanufacturing; micromachine; micro electromechanic; micro electron1.引言:随着20世纪80年代后期微机械、微机电系统(MicroElectroMechanicalSystem,MEMS)这一门新兴交叉学科的兴起,微细加工技术作为获得微机械、微机电系统的必要手段,得到了快速的发展。
微细加工技术起源于平面硅工艺,但随着半导体器件、集成电路、微型机械等技术的发展与需求,微细加工技术已经成为一门多学科交叉的制造系统工程和综合高新技术,广泛应用于医疗、生物工程、信息、航空航天、半导体工业、军事、汽车等领域,给国民经济、人民生活和国防、军事等带来了深远的影响,被列为21世纪关键技术之一。
刀具表面微织构切削机理研究
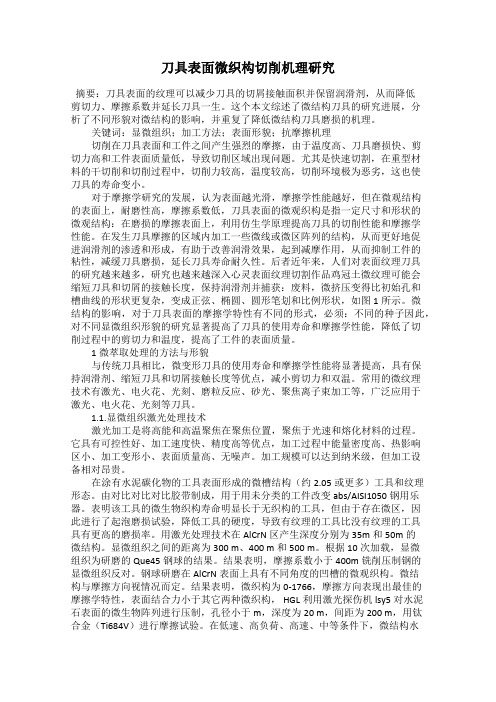
刀具表面微织构切削机理研究摘要:刀具表面的纹理可以减少刀具的切屑接触面积并保留润滑剂,从而降低剪切力、摩擦系数并延长刀具一生。
这个本文综述了微结构刀具的研究进展,分析了不同形貌对微结构的影响,并重复了降低微结构刀具磨损的机理。
关键词:显微组织;加工方法;表面形貌;抗摩擦机理切削在刀具表面和工件之间产生强烈的摩擦,由于温度高、刀具磨损快、剪切力高和工件表面质量低,导致切削区域出现问题。
尤其是快速切割,在重型材料的干切削和切削过程中,切削力较高,温度较高,切削环境极为恶劣,这也使刀具的寿命变小。
对于摩擦学研究的发展,认为表面越光滑,摩擦学性能越好,但在微观结构的表面上,耐磨性高,摩擦系数低,刀具表面的微观织构是指一定尺寸和形状的微观结构:在磨损的摩擦表面上,利用仿生学原理提高刀具的切削性能和摩擦学性能。
在发生刀具摩擦的区域内加工一些微线或微区阵列的结构,从而更好地促进润滑剂的渗透和形成,有助于改善润滑效果,起到减摩作用,从而抑制工件的粘性,减缓刀具磨损,延长刀具寿命耐久性。
后者近年来,人们对表面纹理刀具的研究越来越多,研究也越来越深入心灵表面纹理切割作品鸡冠土微纹理可能会缩短刀具和切屑的接触长度,保持润滑剂并捕获:废料,微挤压变得比初始孔和槽曲线的形状更复杂,变成正弦、椭圆、圆形笔划和比例形状,如图1所示。
微结构的影响,对于刀具表面的摩擦学特性有不同的形式,必须:不同的种子因此,对不同显微组织形貌的研究显著提高了刀具的使用寿命和摩擦学性能,降低了切削过程中的剪切力和温度,提高了工件的表面质量。
1微萃取处理的方法与形貌与传统刀具相比,微变形刀具的使用寿命和摩擦学性能将显著提高,具有保持润滑剂、缩短刀具和切屑接触长度等优点,减小剪切力和双温。
常用的微纹理技术有激光、电火花、光刻、磨粒反应、砂光、聚焦离子束加工等,广泛应用于激光、电火花、光刻等刀具。
1.1.显微组织激光处理技术激光加工是将高能和高温聚焦在聚焦位置,聚焦于光速和熔化材料的过程。
微铣削 微切削的概念及其研究意义

一、微铣削微切削的研究意义应用领域微型化是制造业未来发展面连的挑战和动力。
随着科学技术的发展对零件的加工提出了越来越高的要求,既要满足越来越高的加工效率、加工精度和表面质量,又要满足绿色生产的要求。
微制造加工在这方面有着巨大的发展潜力。
现代生活中,由于人们生存空间和移动方便的需要,各类产品的小型、微型化成为了全球的一个重要发展趋势,这使得微细产品的应用范围迅速扩大,微铣削和微切削作为微型制造加工技术的重要部分,正越来越多的被各国制造业热点研究发展。
众所周知,超精零件制造加工的能力是一个国家机械制造业水平的重要体现,它直接影响一个国家医疗、高科技电子产品及设备、现代军事国防、航空等重要先进领域的发展。
微型制造加工较普通加工能达到更高的精度要求,以微铣削和微切削为代表的超精密微制造加工技术越来越成为一个国家先进制造加工技术水平的衡量标准。
在现代制造技术领域中,微细加工技术占有极为重要的位置。
它不仅是制造高新技术产品的关键技术,而且也是取得国际竞争优势的重要技术之一。
微制造业的发展不仅对我国高新技术水平的提高有着重要战略意义,同时对节约能源,减少污染等方面也意义非凡。
因此,深入的了解和研究微铣削和微切削加工技术是发展制造业是十分重要也是必不可少的。
微小机械无论在国防、航空、航天和民用中国都有很大的市场,例如微小人造卫星、飞机、机床、汽轮发电机组、车辆、枪械等。
又如照相机、摄像机、手机等都是越做越小而功能却不断提高和完善。
而计量检测、生物医学、电子产品与计算机、仪器科学等多个领域也正朝着微型化发展,微型医用机器人、微型计算机、微型精密仪器等都是微型加工的直接应用。
因此,微型加工技术和理论的研究有着明显的广阔前景。
现状及发展趋势1959年,richardPFeynman就提出了微型机械的设想,之后随着研究工作的进行并取得一定的成果,显示出了微型机械加工在未来的明显的广阔前景。
微型机械在国外比较早的受到了政府部门、企业界、高等学校与研究机构的高度重视。
微细切削加工与测量共体技术、仪器及应用
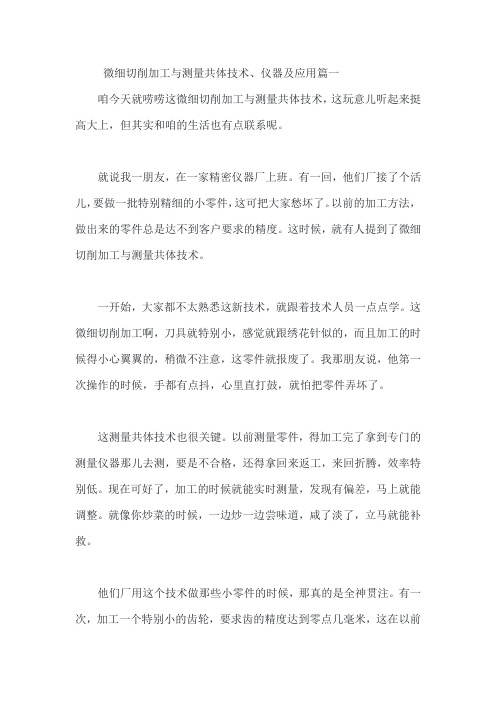
微细切削加工与测量共体技术、仪器及应用篇一咱今天就唠唠这微细切削加工与测量共体技术,这玩意儿听起来挺高大上,但其实和咱的生活也有点联系呢。
就说我一朋友,在一家精密仪器厂上班。
有一回,他们厂接了个活儿,要做一批特别精细的小零件,这可把大家愁坏了。
以前的加工方法,做出来的零件总是达不到客户要求的精度。
这时候,就有人提到了微细切削加工与测量共体技术。
一开始,大家都不太熟悉这新技术,就跟着技术人员一点点学。
这微细切削加工啊,刀具就特别小,感觉就跟绣花针似的,而且加工的时候得小心翼翼的,稍微不注意,这零件就报废了。
我那朋友说,他第一次操作的时候,手都有点抖,心里直打鼓,就怕把零件弄坏了。
这测量共体技术也很关键。
以前测量零件,得加工完了拿到专门的测量仪器那儿去测,要是不合格,还得拿回来返工,来回折腾,效率特别低。
现在可好了,加工的时候就能实时测量,发现有偏差,马上就能调整。
就像你炒菜的时候,一边炒一边尝味道,咸了淡了,立马就能补救。
他们厂用这个技术做那些小零件的时候,那真的是全神贯注。
有一次,加工一个特别小的齿轮,要求齿的精度达到零点几毫米,这在以前简直不敢想。
但是用了这新的共体技术,加工的时候,通过显微镜看着刀具一点一点地切削,测量仪器随时反馈数据,只要数据一不对,就赶紧调整刀具的进给量。
经过一番努力,这批零件终于做出来了,精度完全符合要求。
客户收到后特别满意,还追加了订单。
我朋友他们厂也因为掌握了这项技术,在行业里名声大噪。
从那以后,他们厂就越来越重视这微细切削加工与测量共体技术了,不断地改进工艺,还引进了更先进的仪器。
这技术的应用可不止在精密仪器厂,像做电子产品的那些小芯片,还有医疗设备里的微型零件,都得靠它。
它就像是一个神奇的魔法,能把那些微小的东西做得无比精准,让我们的生活变得更加便捷和美好。
以后啊,这技术肯定还会不断发展,说不定能创造出更多我们想不到的奇迹呢!微细切削加工与测量共体技术、仪器及应用篇二我记得有一次去参观一个机械加工的展览,看到了那些用微细切削加工与测量共体技术做出来的展品,真是让我大开眼界。
复杂曲面微细零件切削加工研究
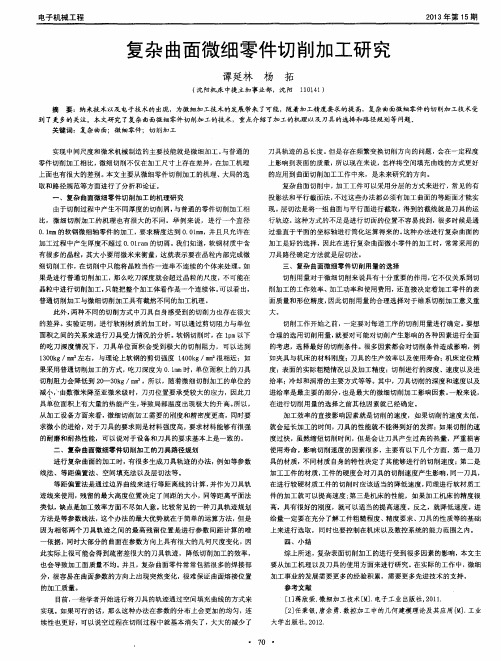
2 0 1 3 年第 1 5 期
复杂 曲面微细 零件切削加工研 究
谭延林 杨 拓
1 1 0 1 4 1 ) ( 沈阳机床 中捷立加事业部,沈阳
摘 要 :纳米技术以及 电子技术的 出现,为微细加工技 术的发展带来 了可能,随着加工精度要求的提 高,复杂 曲面微细零件 的切 削加工技术受 到 了更多的关注。本文研究 了复杂曲面微 细零件切削加工的技 术,重点介绍 了 加 工的机理 以及刀具的选择和路径规划等问题 。
大。
此外 , 两种不 同的切削方式 中刀具 自 身感受到的切 削力也存在很大
的差异。实验证 明,进行软刚材质 的加工 时,可 以通过剪切阻力与单位 面积之间的关系来进行刀具受力情况的分析。软钢切 削时, 在 l p m以下
切削工作开始之前,一定要对每道工序的切削用量进行确定 。 要想 合理的选用切削用量 , 就要对可能对切削产 生影响 的各种因素进行全面
现。 层切法是将一组曲面与平行面进行截取 , 得到 的截线就是刀具的运
行 轨 迹 。这 种 方 式 的不 足 是 进 行 切 面 的位 置不 容 易 找 到 ,很 多 时 候 是通
由于切削过程中产生不同厚度的切削屑, 与普通的零件切 削加工相 比,微 细切削加工的机理也有很大 的不同。举例来说,进行一个直径 0 . 1 m m的软钢微细轴零件的加工 ,要求精度达到 0 . 0 1 a r m ,并且只允许在 加工过程 中产生厚度不超过 0 . O l r a m的切屑 。 我们知道 , 软钢材质中含 有 很多的晶粒 , 其大小要用微米来衡量 ,这就表示要在晶粒内部完成微 细切削工作 , 在切削 中只能将晶粒当作一连 串不连续的个体来处理 。 如 果是进行 普通切 削加工 , 那么吃刀深度就会超过 晶粒 的尺度,不可能在 晶粒中进行切削加工 , 只能把整个加工体看 作是一个连续体。 可 以看出, 普通切削加工与微细切削加工具有截 然不同的加工机理。