管壳式换热器的设计及计算
管壳式换热器设计要领

管壳式换热器设计要领1.结构设计:管壳式换热器由壳体、管束、管板、管头盖板等部分组成。
在设计中,需考虑到换热器的耐压性能、换热面积、流体分布等因素。
换热器的结构应具有良好的刚性和密封性能,以确保设备的可靠运行。
2.材料选择:换热器的材料选择直接影响其性能和使用寿命。
一般来说,壳体、管束等部分可选用碳钢、不锈钢、铜合金等材料,而密封件宜选择耐高温、耐腐蚀的材料。
在实际应用中,还需要根据工艺要求和介质特性选择合适的材料。
3.传热计算:换热器的传热计算是设计的重要环节之一、传热计算需要确定换热器的传热系数、摩擦阻力、压降等参数。
传热系数的计算可采用经验公式或传热实验数据进行估算。
同时,需考虑换热介质的性质、流体状态和流速等因素。
4.流动特性:换热器的流动特性对传热效果和设备性能有重要影响。
合理设计的管束结构和流体分布能有效提高传热效果。
同时,应考虑流体在管束间和壳内的流动方式,如单相流、两相流、多相流等。
对于热敏介质,还需注意避免结垢、热点等问题。
5.安全性和维修性:管壳式换热器在使用过程中要保证安全性和维修性。
在设计中要考虑到设备的容易维修、更换部件的便利性,以及防止泄漏、爆炸等安全事故的发生。
合理的结构设计和材料选择可以提高设备的可靠性和安全性。
6.经济性:在设计过程中要全面考虑成本和效益,追求经济性指标。
应根据具体的工艺要求和使用情况,合理选择换热器的型号、大小和材料。
在满足工艺条件的前提下,尽量降低投资成本和运行成本,提高设备的经济效益。
综上所述,管壳式换热器的设计要领主要包括结构设计、材料选择、传热计算、流动特性、安全性和维修性、经济性等方面。
合理的设计能够保证设备的正常运行和高效换热,同时提高设备的安全性和经济性。
在具体的设计中应根据实际情况进行优化和改进,以满足特定工艺要求和使用要求。
管壳式换热器的设计
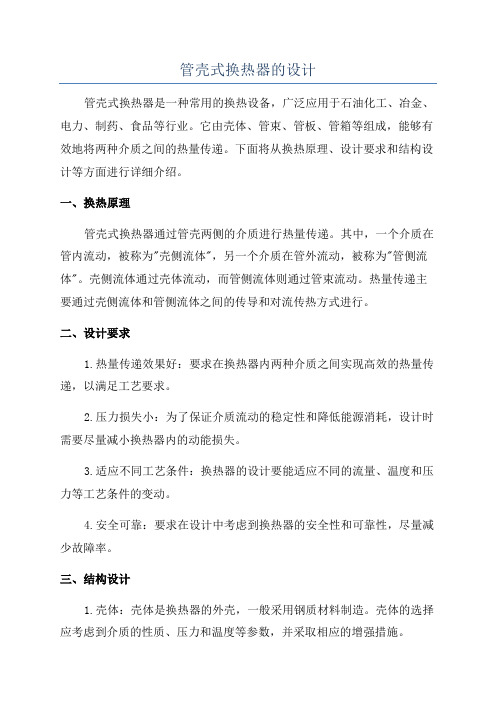
管壳式换热器的设计管壳式换热器是一种常用的换热设备,广泛应用于石油化工、冶金、电力、制药、食品等行业。
它由壳体、管束、管板、管箱等组成,能够有效地将两种介质之间的热量传递。
下面将从换热原理、设计要求和结构设计等方面进行详细介绍。
一、换热原理管壳式换热器通过管壳两侧的介质进行热量传递。
其中,一个介质在管内流动,被称为"壳侧流体",另一个介质在管外流动,被称为"管侧流体"。
壳侧流体通过壳体流动,而管侧流体则通过管束流动。
热量传递主要通过壳侧流体和管侧流体之间的传导和对流传热方式进行。
二、设计要求1.热量传递效果好:要求在换热器内两种介质之间实现高效的热量传递,以满足工艺要求。
2.压力损失小:为了保证介质流动的稳定性和降低能源消耗,设计时需要尽量减小换热器内的动能损失。
3.适应不同工艺条件:换热器的设计要能适应不同的流量、温度和压力等工艺条件的变动。
4.安全可靠:要求在设计中考虑到换热器的安全性和可靠性,尽量减少故障率。
三、结构设计1.壳体:壳体是换热器的外壳,一般采用钢质材料制造。
壳体的选择应考虑到介质的性质、压力和温度等参数,并采取相应的增强措施。
2.管束:管束是由多根管子组成的,一般采用金属材料或塑料制造。
管束的设计要考虑到介质对管材的腐蚀性、温度和压力等参数,同时也要考虑到换热面积的要求。
3.管板:管板位于管束两端,起到支撑和固定管束的作用,一般采用钢质材料制造。
管板的设计要考虑到壳侧和管侧流体的流动特性,并采用合适的孔洞布置,以保证流体的均匀流动。
4.管箱:管箱是安装在管板上的设施,主要用于集流壳侧流体并将其引导出换热器。
管箱的设计应考虑到壳侧流体的流动特性和流量等参数,以实现流体的顺畅流动。
在设计过程中,需要进行换热器的热力计算和结构力学计算,以确定壳体、管束和管板等部件的尺寸和选材。
同时,还需要根据不同工艺和使用条件的要求,进行热交换面积的计算和确定。
管壳式换热器的设计及计算
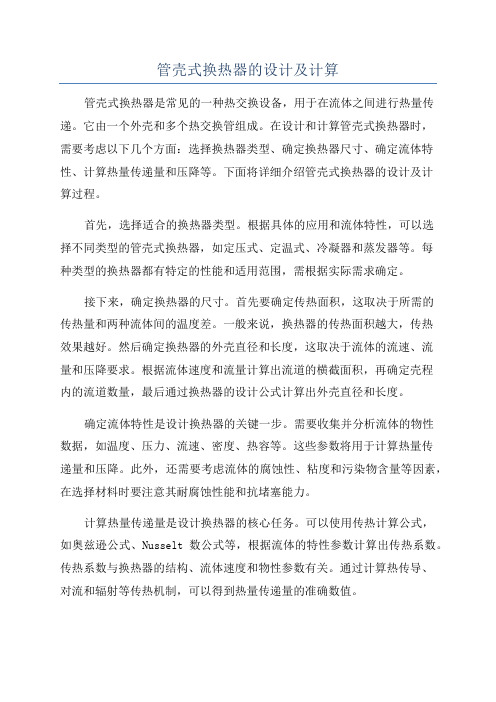
管壳式换热器的设计及计算管壳式换热器是常见的一种热交换设备,用于在流体之间进行热量传递。
它由一个外壳和多个热交换管组成。
在设计和计算管壳式换热器时,需要考虑以下几个方面:选择换热器类型、确定换热器尺寸、确定流体特性、计算热量传递量和压降等。
下面将详细介绍管壳式换热器的设计及计算过程。
首先,选择适合的换热器类型。
根据具体的应用和流体特性,可以选择不同类型的管壳式换热器,如定压式、定温式、冷凝器和蒸发器等。
每种类型的换热器都有特定的性能和适用范围,需根据实际需求确定。
接下来,确定换热器的尺寸。
首先要确定传热面积,这取决于所需的传热量和两种流体间的温度差。
一般来说,换热器的传热面积越大,传热效果越好。
然后确定换热器的外壳直径和长度,这取决于流体的流速、流量和压降要求。
根据流体速度和流量计算出流道的横截面积,再确定壳程内的流道数量,最后通过换热器的设计公式计算出外壳直径和长度。
确定流体特性是设计换热器的关键一步。
需要收集并分析流体的物性数据,如温度、压力、流速、密度、热容等。
这些参数将用于计算热量传递量和压降。
此外,还需要考虑流体的腐蚀性、粘度和污染物含量等因素,在选择材料时要注意其耐腐蚀性能和抗堵塞能力。
计算热量传递量是设计换热器的核心任务。
可以使用传热计算公式,如奥兹逊公式、Nusselt数公式等,根据流体的特性参数计算出传热系数。
传热系数与换热器的结构、流体速度和物性参数有关。
通过计算热传导、对流和辐射等传热机制,可以得到热量传递量的准确数值。
最后,要计算管壳式换热器的压降。
压降是流体通过换热器时产生的能量损失。
为了保证流体的正常流动和换热效果,需要控制良好的压降。
可以通过实验或计算公式,如达西公式和克尔文公式,预测换热器内的压降情况。
根据流体的流速、流量和物性参数,计算出壳程和管程内的压降,并进行整体的能量平衡计算。
综上所述,管壳式换热器的设计和计算包括选择换热器类型、确定尺寸、确定流体特性、计算热量传递量和压降等步骤。
管壳式换热器设计 课程设计
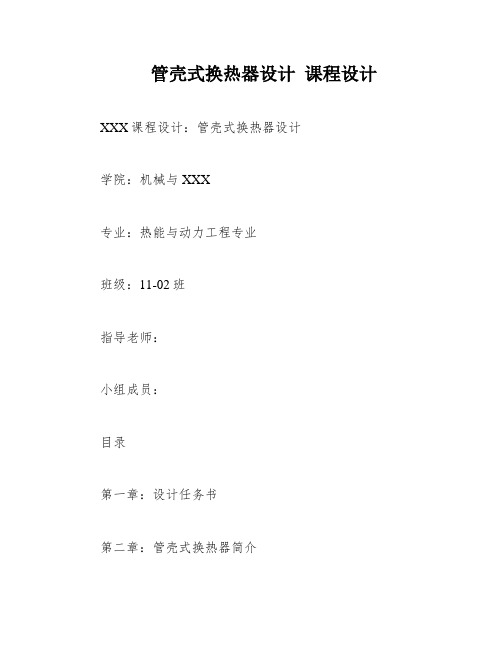
管壳式换热器设计课程设计XXX课程设计:管壳式换热器设计学院:机械与XXX专业:热能与动力工程专业班级:11-02班指导老师:小组成员:目录第一章:设计任务书第二章:管壳式换热器简介第三章:设计方法及设计步骤第四章:工艺计算4.1 物性参数的确定4.2 核算换热器传热面积4.2.1 传热量及平均温差4.2.2 估算传热面积第五章:管壳式换热器结构计算管壳式换热器是常用的热交换设备,广泛应用于化工、石油、制药、食品等行业。
本次课程设计旨在设计一台管壳式换热器,以满足特定工艺条件下的换热需求。
在设计之前,需要了解管壳式换热器的基本结构和工作原理。
管壳式换热器由外壳、管束、管板、管箱、管夹等部分组成。
热量通过内置于管束中的流体在管内传递,再通过管壳间的流体传递到外壳中,从而实现热交换。
设计过程中,需要确定流体的物性参数,包括密度、比热、导热系数等。
同时,还需要核算换热器传热面积,以满足特定的传热需求。
传热量和平均温差是计算传热面积的重要参数,而估算传热面积则需要考虑流体的流动状态、管束的排布方式等因素。
最终,我们将根据设计要求进行管壳式换热器的结构计算,确定外壳、管束等部分的尺寸和数量,以满足特定工艺条件下的换热需求。
第一章设计任务书本项目旨在设计一台管壳式换热器,用于将煤油由140℃冷却至40℃。
处理能力为10t/h,压强降不得超过100kPa。
具体操作条件为:煤油的入口温度为140℃,出口温度为40℃,冷却水的入口温度为26℃,出口温度为40℃。
2.第二章管壳式换热器简介管壳式换热器是石油化工行业中应用最广泛的换热器。
尽管各种板式换热器的竞争力不断上升,但管壳式换热器仍然占据着换热器市场的主导地位。
目前,各国为提高这类换热器性能进行的研究主要集中在强化传热、提高对苛刻工艺条件的适应性以及开发适用于各类腐蚀介质的材料。
此外,结构改进也是向着高温、高压、大型化方向发展的必然趋势。
5.1 换热管计算及排布方式在设计管壳式换热器时,需要计算并确定换热管的数量、直径和排布方式。
PPT-7-管壳式换热器设计计算实例
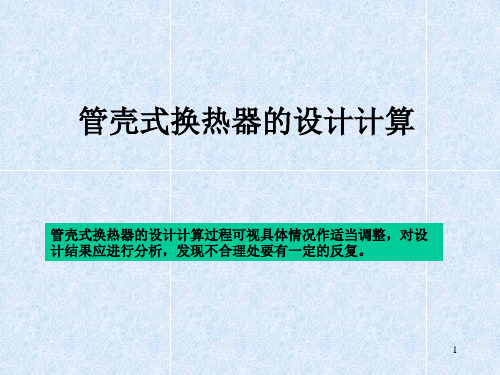
t fi t f 0
所以,只要 o 1 就可以起到强化换热的效果。 由于β值常常远大于1,而使η0β的值总是远大于1,这就
使肋化侧的热阻显著减小,从而增大传热系数的值。
32
ln( d o d i ) 2 l
28
上面三式相加
l t fi t fo
do 1 1 1 ln hi d i 2 d i ho d o
对外侧面积而言得传热系数的定义式由下式表示:
k ko 1 do d d 1 o ln o hi di 2 di ho
10
1 构造和工作原理
翅片管热交换器可以仅由一根或若干根翅片管组成,如室内取 暖用翅片管散热器;也可再配以外壳、风机等组成空冷器型式 的热交换器。
11
主要换热元件是翅片管,由基管和翅片组成。
翅片管的类型和选择
对翅片管的要求:良好的传 热性能、耐温性能、耐热冲 击能力(如介质热负荷不稳 定)及耐腐蚀能力,易于清 除尘垢,压降较低。
13
常见的翅片管形式
•
14
翅片管因制造方法不同而使其在传热性能、机械性能等方面有一定的 差异。按制造方法分有整体翅片、焊接翅片、高频焊翅片和机械连接 翅片。
整体翅片:由铸造、机械加工或轧制而成,翅片与管子一体,无接触 热阻,强度高,但要求翅片与管子同种材料。如低压锅炉的省煤器就 是采用整体翅片。 焊接翅片:用钎焊或氩弧焊等工艺制造,可使用与管子不一样的材料。 由于它制造简单、经济且具有较好的传热和机械性能,故已广泛应用, 主要问题是焊接工艺的质量。 高频焊翅片:利用高频发生器产生的高频电感应,使管子表面与翅片 接触处产生高温而部分熔化,同通过加压翅片与管子连成一体而成。 这种连接方法无焊剂、焊料,制造简单,性能优良。
管壳式换热器的设计及计算
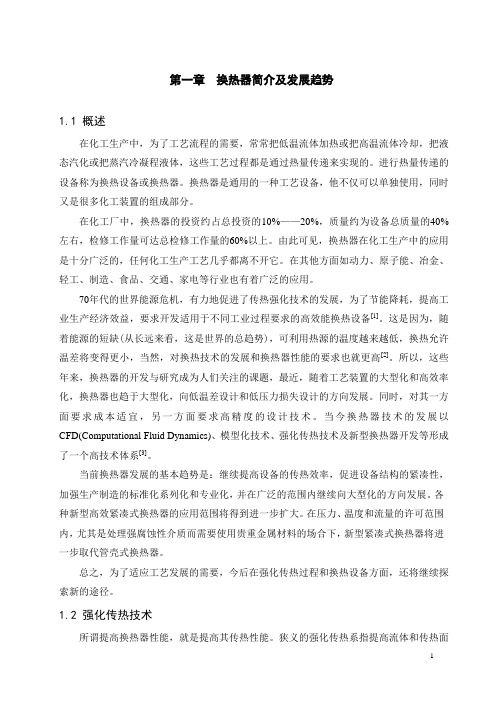
第一章换热器简介及发展趋势1.1 概述在化工生产中,为了工艺流程的需要,常常把低温流体加热或把高温流体冷却,把液态汽化或把蒸汽冷凝程液体,这些工艺过程都是通过热量传递来实现的。
进行热量传递的设备称为换热设备或换热器。
换热器是通用的一种工艺设备,他不仅可以单独使用,同时又是很多化工装置的组成部分。
在化工厂中,换热器的投资约占总投资的10%——20%,质量约为设备总质量的40%左右,检修工作量可达总检修工作量的60%以上。
由此可见,换热器在化工生产中的应用是十分广泛的,任何化工生产工艺几乎都离不开它。
在其他方面如动力、原子能、冶金、轻工、制造、食品、交通、家电等行业也有着广泛的应用。
70年代的世界能源危机,有力地促进了传热强化技术的发展,为了节能降耗,提高工业生产经济效益,要求开发适用于不同工业过程要求的高效能换热设备[1]。
这是因为,随着能源的短缺(从长远来看,这是世界的总趋势),可利用热源的温度越来越低,换热允许温差将变得更小,当然,对换热技术的发展和换热器性能的要求也就更高[2]。
所以,这些年来,换热器的开发与研究成为人们关注的课题,最近,随着工艺装置的大型化和高效率化,换热器也趋于大型化,向低温差设计和低压力损失设计的方向发展。
同时,对其一方面要求成本适宜,另一方面要求高精度的设计技术。
当今换热器技术的发展以CFD(Computational Fluid Dynamics)、模型化技术、强化传热技术及新型换热器开发等形成了一个高技术体系[3]。
当前换热器发展的基本趋势是:继续提高设备的传热效率,促进设备结构的紧凑性,加强生产制造的标准化系列化和专业化,并在广泛的范围内继续向大型化的方向发展。
各种新型高效紧凑式换热器的应用范围将得到进一步扩大。
在压力、温度和流量的许可范围内,尤其是处理强腐蚀性介质而需要使用贵重金属材料的场合下,新型紧凑式换热器将进一步取代管壳式换热器。
总之,为了适应工艺发展的需要,今后在强化传热过程和换热设备方面,还将继续探索新的途径。
管壳式换热器直径计算公式

管壳式换热器直径计算公式管壳式换热器是一种常用的换热设备,广泛应用于化工、石油、电力等工业领域。
它以管道中的流体与壳体中的流体进行换热,从而实现能量的传递。
在设计管壳式换热器时,确定合适的直径是非常重要的,因为直径的大小直接影响着换热器的性能和成本。
因此,掌握管壳式换热器直径计算公式是非常必要的。
管壳式换热器的直径计算公式可以通过以下步骤来推导:首先,我们需要确定管壳式换热器的传热面积。
传热面积是换热器的关键参数,它直接影响着换热效率。
传热面积可以通过以下公式来计算:A = π D L。
其中,A表示传热面积,π表示圆周率,D表示管壳式换热器的直径,L表示管道的长度。
通过这个公式,我们可以看出传热面积与直径和长度成正比,这也说明了直径对换热器性能的重要影响。
其次,我们需要确定管壳式换热器的传热系数。
传热系数是描述换热器传热性能的重要参数,它与流体的性质、流速、管道壁面情况等因素有关。
传热系数可以通过实验测定或理论计算得到。
最后,我们可以通过传热面积和传热系数来确定管壳式换热器的换热功率。
换热功率可以通过以下公式来计算:Q = U A ΔT。
其中,Q表示换热功率,U表示传热系数,ΔT表示流体的温度差。
通过这个公式,我们可以看出换热功率与传热系数、传热面积和温度差成正比,这也说明了直径对换热器性能的重要影响。
综上所述,我们可以得出管壳式换热器直径计算公式:D = (4 Q) / (π U ΔT)。
通过这个公式,我们可以根据需要的换热功率、传热系数和温度差来确定管壳式换热器的合适直径。
这个公式为工程师提供了一个简便而有效的工具,可以帮助他们在设计管壳式换热器时更加准确地确定直径,从而提高换热器的性能和经济性。
在实际工程中,除了上述公式外,还需要考虑一些其他因素,比如流体的性质、压力损失、材料成本等。
因此,在使用管壳式换热器直径计算公式时,工程师还需要综合考虑各种因素,进行合理的优化设计。
总之,管壳式换热器直径计算公式是设计管壳式换热器的重要工具,它可以帮助工程师确定合适的直径,从而提高换热器的性能和经济性。
管壳式换热器的设计和选用的计算步骤
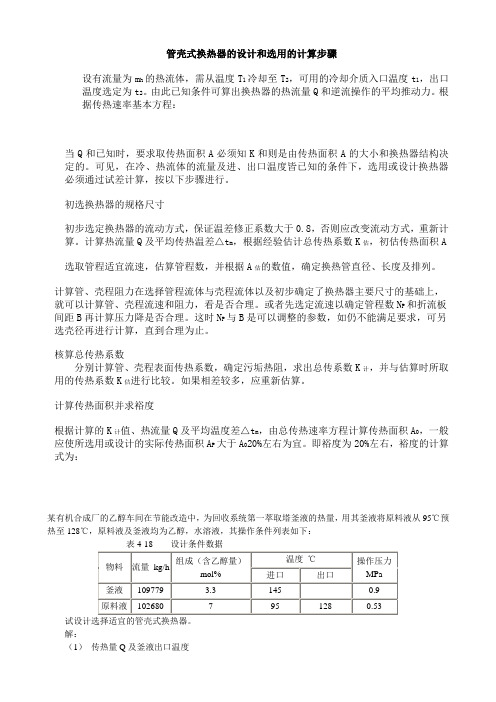
管壳式换热器的设计和选用的计算步骤设有流量为m h的热流体,需从温度T1冷却至T2,可用的冷却介质入口温度t1,出口温度选定为t2。
由此已知条件可算出换热器的热流量Q和逆流操作的平均推动力。
根据传热速率基本方程:当Q和已知时,要求取传热面积A必须知K和则是由传热面积A的大小和换热器结构决定的。
可见,在冷、热流体的流量及进、出口温度皆已知的条件下,选用或设计换热器必须通过试差计算,按以下步骤进行。
初选换热器的规格尺寸初步选定换热器的流动方式,保证温差修正系数大于0.8,否则应改变流动方式,重新计算。
计算热流量Q及平均传热温差△t m,根据经验估计总传热系数K估,初估传热面积A选取管程适宜流速,估算管程数,并根据A估的数值,确定换热管直径、长度及排列。
计算管、壳程阻力在选择管程流体与壳程流体以及初步确定了换热器主要尺寸的基础上,就可以计算管、壳程流速和阻力,看是否合理。
或者先选定流速以确定管程数N P和折流板间距B再计算压力降是否合理。
这时N P与B是可以调整的参数,如仍不能满足要求,可另选壳径再进行计算,直到合理为止。
核算总传热系数分别计算管、壳程表面传热系数,确定污垢热阻,求出总传系数K计,并与估算时所取用的传热系数K估进行比较。
如果相差较多,应重新估算。
计算传热面积并求裕度根据计算的K计值、热流量Q及平均温度差△t m,由总传热速率方程计算传热面积A0,一般应使所选用或设计的实际传热面积A P大于A020%左右为宜。
即裕度为20%左右,裕度的计算式为:某有机合成厂的乙醇车间在节能改造中,为回收系统第一萃取塔釜液的热量,用其釜液将原料液从95℃预热至128℃,原料液及釜液均为乙醇,水溶液,其操作条件列表如下:表4-18设计条件数据试设计选择适宜的管壳式换热器。
解:a. 传热量Q以原料液为基准亦计入5%的热损失,按以下步骤求得传热量Q。
平均温度℃以上表中混合物的各物性分别由下式求得:混合物:Cp混合物热导率:W/(m℃)混合物密度:kg/m3混合物比热容:kJ/(kg℃)式中为组成为i的摩尔分率,为组分i的质量分率。
管壳式换热器的设计
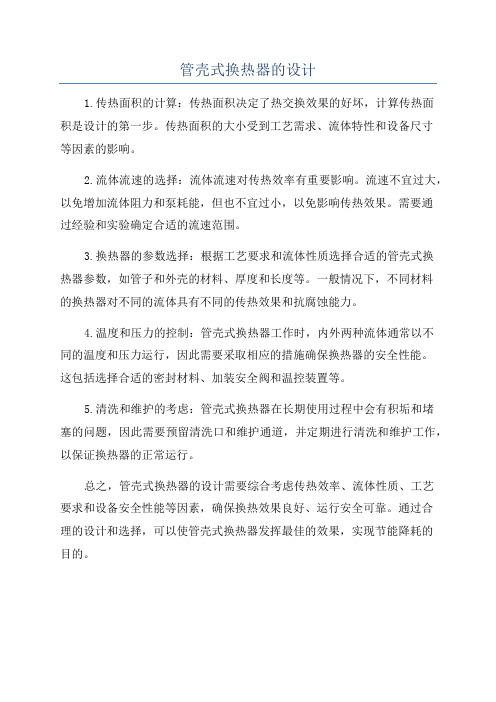
管壳式换热器的设计
1.传热面积的计算:传热面积决定了热交换效果的好坏,计算传热面
积是设计的第一步。
传热面积的大小受到工艺需求、流体特性和设备尺寸
等因素的影响。
2.流体流速的选择:流体流速对传热效率有重要影响。
流速不宜过大,以免增加流体阻力和泵耗能,但也不宜过小,以免影响传热效果。
需要通
过经验和实验确定合适的流速范围。
3.换热器的参数选择:根据工艺要求和流体性质选择合适的管壳式换
热器参数,如管子和外壳的材料、厚度和长度等。
一般情况下,不同材料
的换热器对不同的流体具有不同的传热效果和抗腐蚀能力。
4.温度和压力的控制:管壳式换热器工作时,内外两种流体通常以不
同的温度和压力运行,因此需要采取相应的措施确保换热器的安全性能。
这包括选择合适的密封材料、加装安全阀和温控装置等。
5.清洗和维护的考虑:管壳式换热器在长期使用过程中会有积垢和堵
塞的问题,因此需要预留清洗口和维护通道,并定期进行清洗和维护工作,以保证换热器的正常运行。
总之,管壳式换热器的设计需要综合考虑传热效率、流体性质、工艺
要求和设备安全性能等因素,确保换热效果良好、运行安全可靠。
通过合
理的设计和选择,可以使管壳式换热器发挥最佳的效果,实现节能降耗的
目的。
管壳式换热器传热计算示例终 用于合并
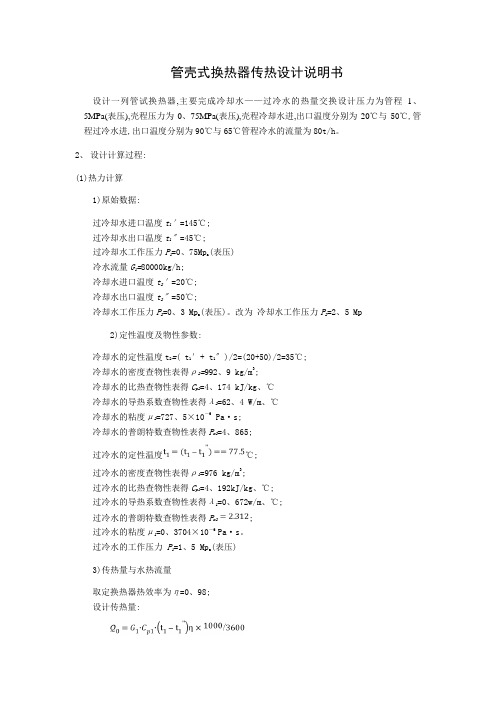
Pa;
取导流板阻力系数:
;
导流板压降:
壳程结垢修正系数: 壳程压降:
Pa ;(表 3-12)
管程允许压降:[△P2]=35000 Pa;(见表 3-10) 壳程允许压降:[△P1]=35000 Pa;
△P2<[△P2] △P1<[△P1] 即压降符合要求。
Pa;
(2)结构设计(以下数据根据 BG150-2011)
m2; 选用φ25×2、5 无缝钢管作换热管; 管子外径 d0=0、025 m; 管子内径 di=0、025-2×0、0025=0、02 m; 管子长度取为 l=3 m; 管子总数:
管程流通截面积:
取 720 根 m2
管程流速: 管程雷诺数: 管程传热系数:(式 3-33c)
m/s 湍流
6)结构初步设计: 布管方式见图所示: 管间距 s=0、032m(按 GB151,取 1、25d0); 管束中心排管的管数按 4、3、1、1 所给的公式确定:
结构设计的任务就是根据热力计算所决定的初步结构数据,进一步设计全部结构尺寸, 选定材料并进行强度校核。最后绘成图纸,现简要综述如下:
1) 换热器流程设计 采用壳方单程,管方两程的 1-4 型换热器。由于换热器尺寸不太大,可以用一台,未考虑 采用多台组合使用,管程分程隔板采取上图中的丁字型结构,其主要优点就是布管紧密。 2)管子与传热面积 采用 25×2、5 的无缝钢管,材质 20 号钢,长 3m,管长与管径都就是换热器的标准管子 尺寸。 管子总数为 352 根,其传热面积为:
3)传热量与水热流量
取定换热器热效率为η=0、98; 设计传热量:
过冷却水流量:
; 4)有效平均温差 逆流平均温差:
根据式(3-20)计算参数 p、R: 参数 P:
管壳式换热器传热计算示例(终)
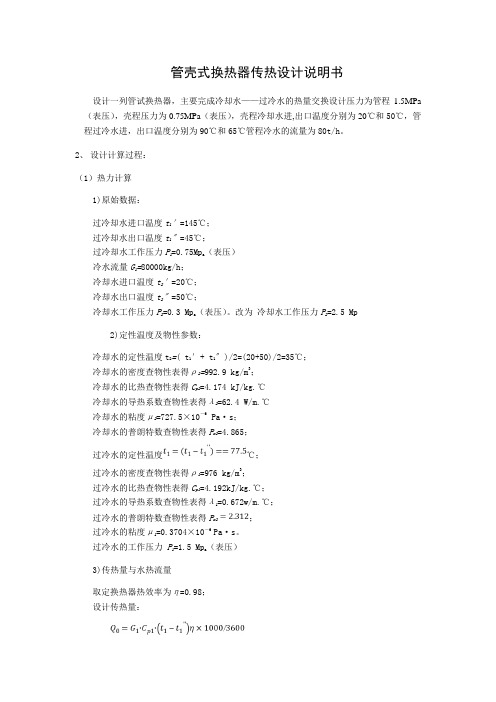
管壳式换热器传热设计说明书设计一列管试换热器,主要完成冷却水——过冷水的热量交换设计压力为管程1.5MPa (表压),壳程压力为0.75MPa(表压),壳程冷却水进,出口温度分别为20℃和50℃,管程过冷水进,出口温度分别为90℃和65℃管程冷水的流量为80t/h。
2、设计计算过程:(1)热力计算1)原始数据:过冷却水进口温度t1′=145℃;过冷却水出口温度t1〞=45℃;过冷却水工作压力P1=0.75Mp a(表压)冷水流量G1=80000kg/h;冷却水进口温度t2′=20℃;冷却水出口温度t2〞=50℃;冷却水工作压力P2=0.3 Mp a(表压)。
改为冷却水工作压力P2=2.5 Mp2)定性温度及物性参数:冷却水的定性温度t2=( t1′+ t1〞)/2=(20+50)/2=35℃;冷却水的密度查物性表得ρ2=992.9 kg/m3;冷却水的比热查物性表得C p2=4.174 kJ/kg.℃冷却水的导热系数查物性表得λ2=62.4 W/m.℃冷却水的粘度μ2=727.5×10-6 Pa·s;冷却水的普朗特数查物性表得P r2=4.865;过冷水的定性温度℃;过冷水的密度查物性表得ρ1=976 kg/m3;过冷水的比热查物性表得C p1=4.192kJ/kg.℃;过冷水的导热系数查物性表得λ1=0.672w/m.℃;过冷水的普朗特数查物性表得P r2;过冷水的粘度μ1=0.3704×10-6 Pa·s。
过冷水的工作压力P1=1.5 Mp a(表压)3)传热量与水热流量取定换热器热效率为η=0.98;设计传热量:过冷却水流量:;4)有效平均温差逆流平均温差:根据式(3-20)计算参数p、R:参数P:参数R:换热器按单壳程2管程设计,查图3—8得温差校正系数Ψ=0.83;有效平均温差:5)管程换热系数计算:附录10,初定传热系数K0=400 W/m.℃;初选传热面积:m2;选用φ25×2.5无缝钢管作换热管;管子外径d0=0.025 m;管子径d i=0.025-2×0.0025=0.02 m;管子长度取为l=3 m;管子总数:取720根管程流通截面积:m2管程流速:m/s管程雷诺数:湍流管程传热系数:(式3-33c)6)结构初步设计:布管方式见图所示:管间距s=0.032m(按GB151,取1.25d0);管束中心排管的管数按4.3.1.1所给的公式确定:取20根;壳体径:m 取Di=0.7m;长径比:布管示意图l/D i=3/0.9=3.3 ,合理选定弓形折流板弓形折流板弓高:折流板间距:m折流板数量:折流板上管孔直径由GB151-2014可确定为 0.0254mm折流板直径由GB151-2014可确定为 0.6955m 7)壳程换热系数计算壳程流通面积:根据式(3-61)中流体横过管束时流道截面积046.0032.0025.016.0233.01o i c1=⎪⎪⎭⎫⎝⎛-⨯=⎪⎪⎭⎫ ⎝⎛-=s d BD A m 2壳程流速:m/s ;壳程质量流速:kg m 2/s ;壳程当量直径:m ;壳程雷诺数:; 切去弓形面积所占比例按 h/D i =0.2查图4-32得为0.145壳程传热因子查 图3-24得为j s =20 管外壁温度假定值 t w1′=45℃ 壁温过冷水粘度 Pa.s粘度修正系数:根据式(3-62)计算壳程换热系数:8)传热系数计算:水侧污垢热阻:r 2=0.000344m 2.℃/w 管壁热阻r 忽略 总传热系数:传热系数比值,合理9)管壁温度计算:管外壁热流密度:W/m2.℃根据式(3-94a)计算管外壁温度:℃误差较核:℃,误差不大;10)管程压降计算:根据式(3-94b)计算管壁温度:℃;壁温下水的粘度:Pa·s;粘度修正系数:;查图3-30得管程摩擦系数:管程数:;管沿程压降计算依据式(3-112):Pa (W=w.ρ)回弯压降:Pa;取进出口管处质量流速:W N2=1750 ㎏/㎡·s; (依据ρw2<3300取 w=1.822m/s) 进出口管处压降(依据 3-113):;管程结垢校正系数:;管程压降:11)壳程压降计算:壳程当量直径:m;雷诺数:;查得壳程摩擦系数:λ1=0.08;(图 3-34)管束压降(公式3-129):Pa;取进出口质量流速: kg/m2·s;( ρw2<2200 取W N2=1000 ㎏/㎡·s) 进出口管压降:Pa;取导流板阻力系数:;导流板压降:Pa壳程结垢修正系数:;(表3-12)壳程压降:Pa;管程允许压降:[△P2]=35000 Pa;(见表3-10)壳程允许压降:[△P1]=35000 Pa;△P2<[△P2]△P1<[△P1]即压降符合要求。
管壳式换热器的设计计算

管壳式换热器的设计计算1.流体流径的选择哪一种流体流经换热器的管程,哪一种流体流经壳程,下列各点可供选择时参考(以固定管板式换热器为例)(1) 不洁净和易结垢的流体宜走管内,以便于清洗管子。
(2) 腐蚀性的流体宜走管内,以免壳体和管子同时受腐蚀,而且管子也便于清洗和检修。
(3) 压强高的流体宜走管内,以免壳体受压。
(4) 饱和蒸气宜走管间,以便于及时排除冷凝液,且蒸气较洁净,冷凝传热系数与流速关系不大。
(5) 被冷却的流体宜走管间,可利用外壳向外的散热作用,以增强冷却效果。
(6) 需要提高流速以增大其对流传热系数的流体宜走管内,因管程流通面积常小于壳程,且可采用多管程以增大流速。
(7) 粘度大的液体或流量较小的流体,宜走管间,因流体在有折流挡板的壳程流动时,由于流速和流向的不断改变,在低Re(Re>100)下即可达到湍流,以提高对流传热系数。
在选择流体流径时,上述各点常不能同时兼顾,应视具体情况抓住主要矛盾,例如首先考虑流体的压强、防腐蚀及清洗等要求,然后再校核对流传热系数和压强降,以便作出较恰当的选择。
2. 流体流速的选择增加流体在换热器中的流速,将加大对流传热系数,减少污垢在管子表面上沉积的可能性,即降低了污垢热阻,使总传热系数增大,从而可减小换热器的传热面积。
但是流速增加,又使流体阻力增大,动力消耗就增多。
所以适宜的流速要通过经济衡算才能定出。
此外,在选择流速时,还需考虑结构上的要求。
例如,选择高的流速,使管子的数目减少,对一定的传热面积,不得不采用较长的管子或增加程数。
管子太长不易清洗,且一般管长都有一定的标准;单程变为多程使平均温度差下降。
这些也是选择流速时应予考虑的问题。
3. 流体两端温度的确定若换热器中冷、热流体的温度都由工艺条件所规定,就不存在确定流体两端温度的问题。
若其中一个流体仅已知进口温度,则出口温度应由设计者来确定。
例如用冷水冷却某热流体,冷水的进口温度可以根据当地的气温条件作出估计,而换热器出口的冷水温度,便需要根据经济衡算来决定。
管壳式换热器设计
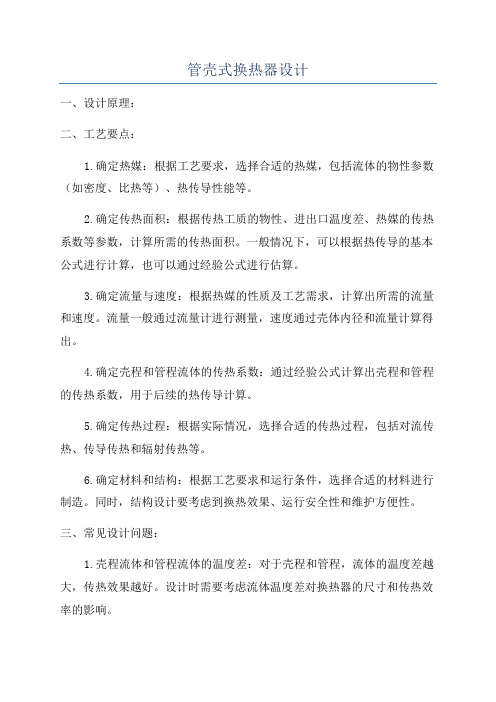
管壳式换热器设计一、设计原理:二、工艺要点:1.确定热媒:根据工艺要求,选择合适的热媒,包括流体的物性参数(如密度、比热等)、热传导性能等。
2.确定传热面积:根据传热工质的物性、进出口温度差、热媒的传热系数等参数,计算所需的传热面积。
一般情况下,可以根据热传导的基本公式进行计算,也可以通过经验公式进行估算。
3.确定流量与速度:根据热媒的性质及工艺需求,计算出所需的流量和速度。
流量一般通过流量计进行测量,速度通过壳体内径和流量计算得出。
4.确定壳程和管程流体的传热系数:通过经验公式计算出壳程和管程的传热系数,用于后续的热传导计算。
5.确定传热过程:根据实际情况,选择合适的传热过程,包括对流传热、传导传热和辐射传热等。
6.确定材料和结构:根据工艺要求和运行条件,选择合适的材料进行制造。
同时,结构设计要考虑到换热效果、运行安全性和维护方便性。
三、常见设计问题:1.壳程流体和管程流体的温度差:对于壳程和管程,流体的温度差越大,传热效果越好。
设计时需要考虑流体温度差对换热器的尺寸和传热效率的影响。
2.压降:壳程和管程的流体在换热过程中会产生压降。
设计时需要考虑压降对流体流速和传热系数的影响,并在设计中进行合理的折减和控制。
3.热媒的物性参数:热媒的物性参数对换热器的设计和运行有很大影响。
需要考虑热媒的密度、比热、热传导系数等参数,并在设计中进行合理的估算和计算。
4.材料选择:根据工艺要求和运行条件,选择合适的材料进行制造。
必须考虑材料的耐受性和耐腐蚀性,以及对流体和环境的影响。
总结:管壳式换热器设计涉及多个方面的参数和工艺要求,包括热媒选择、传热面积计算、流量和速度确定、传热系数估算、传热过程选择、材料和结构设计等。
在实际设计中,需按照工艺要求和运行条件合理选择参数和材料,并通过模拟计算和经验公式进行设计。
同时,需要注意常见的设计问题,如温度差、压降、热媒物性参数和材料选择等。
通过合理的设计和选择,可以实现管壳式换热器的高效工作和长期稳定运行。
ggh换热器计算书

标题:ggh换热器计算书一、设备概述本设备为一款ggh(管壳式)换热器,用于在一定温度和压力条件下,对两种流体进行热交换。
设备的主要组成部分包括:壳体、管板、传热管、隔板、密封垫等。
二、设计参数1. 设备型号:GGH-250/400,表示为管壳式换热器,规格为250mm内径×400mm高。
2. 工作压力:设备的工作压力为15bar。
3. 工作温度:设备的工作温度范围为-5℃~+50℃,可根据实际需要调整。
4. 传热面积:设备总传热面积为6m2。
5. 流体物性:流体A为水,流体B为油,其物理性质分别如下:流体A密度为1kg/L,黏度为0.01Pa·s;流体B密度为0.8kg/L,黏度为0.3Pa·s。
三、计算过程1. 传热面积计算:根据设备规格和流体性质,选用适宜的传热面积。
本次设计选取总传热面积为6m2。
2. 传热系数计算:根据流体性质和设备规格,选择适宜的传热系数,以确保换热效果良好。
本次设计选取传热系数为6000W/(m2·℃)。
3. 确定传热系数后,根据传热公式(Q=KAΔT),可计算出所需的换热面积。
其中,Q为换热量,K为传热系数,A为传热面积,ΔT为冷热流体的温差。
4. 根据实际需要,对设备进行优化设计,包括隔板、密封垫等部件的选型和布局。
四、结果分析经过计算和优化,本次设计的ggh换热器满足工作条件和性能要求,能够实现良好的热交换效果。
预计设备的换热效率较高,使用寿命较长。
五、结论本次设计的ggh换热器满足设计参数和工作条件要求,具有良好的换热效果和稳定性。
建议在实际使用中注意维护保养,确保设备的正常运行。
如有任何疑问或建议,请及时联系我们。
换热机组换热面积

换热机组换热面积
换热面积的计算涉及到许多参数,包括传热介质的物性参数、传热系数、被传热介质的流量及物性参数、流体状态参数等。
具体来说,不同的换热设备有不同的计算方法。
1. 管壳式换热器:换热面积A可以通过公式A=Q/(U×ΔT)来计算,其中A为换热面积,Q为热量,U为传热系数,ΔT为传热介质的温度差。
2. 换热管式换热器:换热面积A可以通过公式A=(π×d×l×n)/(e×N)来计算,其中d为管子外径,l为管长,n为管数,e为管子壁厚度,N为管板孔数。
3. 板式换热器:换热面积A可以通过公式A=Q/(U×ΔT)来计算,其中Q为传热量,U为传热系数,ΔT为介质温差。
以上是几种常见的换热设备的换热面积计算方法,更多类型的换热设备的换热面积计算方法需要参照具体的专业资料和手册。
另外,在计算换热面积时,需要注意确定传热系数及被传热介质的物性参数、确定传热介质流量、采用比较简单的计算方法以及根据实际工艺数据进行检验和验证。
管壳式换热器换热面积-换热器设计手册(精品文档)
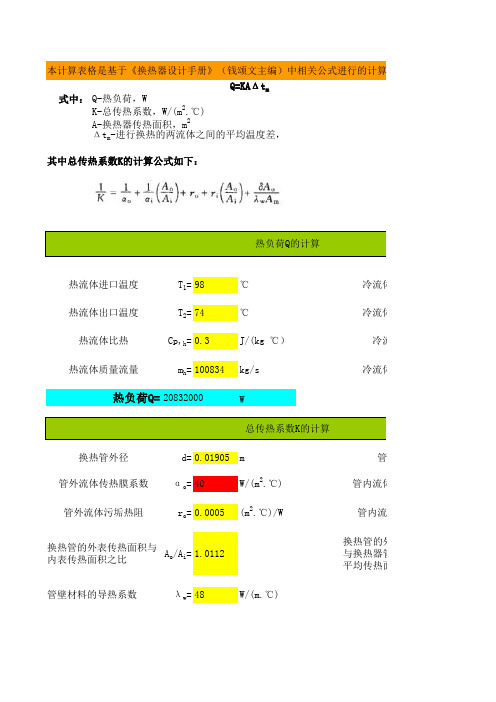
式中:T 1=98℃T 2=74℃Cp,h =0.3J/(kg ℃)m h =100834kg/sWd=0.01905m αo =40W/(m 2.℃)r o =0.0005(m 2.℃)/W A o /A i =1.0112λw =48W/(m .℃)本计算表格是基于《换热器设计手册》(钱颂文主编)中相关公式进行的计算Q=KAΔt mQ-热负荷,WK-总传热系数,W/(m 2.℃)热负荷Q的计算热流体进口温度冷流体进A-换热器传热面积,m 2Δt m -进行换热的两流体之间的平均温度差,其中总传热系数K的计算公式如下:热流体质量流量冷流体质热负荷Q=20832000热流体出口温度冷流体出热流体比热冷流体管外流体污垢热阻管内流体换热管的外表传热面积与内表传热面积之比换热管的外表与换热器管内和管外的平均传热面积之比总传热系数K的计算换热管外径管壁管外流体传热膜系数管内流体传管壁材料的导热系数17.05W/(m 2.℃)Δt 2=51℃Δt 1=47℃0.922Δt 2=71℃Δt 1=27℃0.38Δt m =49Δt m =49Δt m =48.97277702Δt m =45.5089394P=0.2816901411、当换热器冷热流体逆向流动时较大端温差较小端温差Δt 1/Δt 2=总传热系数K=3、确定平均温度差(1)当Δt 1/Δt 2 <2 时且逆向流动时(2)当Δt 1/Δt 2 <2 时且并向流动时(3)当Δt 1/Δt 2 >2 时且逆向流动时2、当换热器冷热流体并向流动时较大端温差较小端温差Δt 1/Δt 2=(4)当Δt 1/Δt 2 >2 时且并向流动时4、确定温度修正系数(1)对于单壳程、双管程或者2n管程的管壳式换热器R=1.20.9825462m 2温度修正系数换热面积A=5、根据P、R值查图,确定对应温度修正系物料摩尔比比热容t 1=27℃H2O 27.42.02H243.6114.2t 2=47℃CH40.253.72N215.51.12Cp,c =2100J/(kg ℃)Ar 0.2 1.2CO210.861.1m c =496kg/s CO 2.181.12混合气体7.075276δ=0.000211m αi =45W/(m 2.℃)r i =0.0005(m 2.℃)/W A o /A m =1.005569计算定性温度在292℃流体进口温度混合气体粘度、比热计算公式流体质量流量流体出口温度冷流体比热内流体污垢热阻的外表传热面积与换热器管内和管外的平均传热面积之比管壁厚度流体传热膜系数的计算292℃时的物性数据粘度密度导热系数0.01920.01420.08990.1630.01810.7170.030.0282 1.2510.02280.0363 1.7820.01730.0272 1.9760.01370.0278 1.250.02260.0225。
- 1、下载文档前请自行甄别文档内容的完整性,平台不提供额外的编辑、内容补充、找答案等附加服务。
- 2、"仅部分预览"的文档,不可在线预览部分如存在完整性等问题,可反馈申请退款(可完整预览的文档不适用该条件!)。
- 3、如文档侵犯您的权益,请联系客服反馈,我们会尽快为您处理(人工客服工作时间:9:00-18:30)。
所谓提高换热器性能,就是提高其传热性能。狭义的强化传热系指提高流体和传热面之间的传热系数。其主要方法归结为下述两个原理,即使温度边界层减薄和调换传热面附近的流体,前者采用各种间断翅片结构,后者采用泡核沸腾传热[2]。最近还兴起一种EHD技术,即电气流体力学技术,又称为电场强化冷凝传热技术,进一步强化了对流、冷凝和沸腾传热,特别适用于强化冷凝传热,并适用于低传热性介质的冷凝,因而引起人们的普遍关注[3]。其原理是,对某些不导电液体的表面施以相垂直的电场,使液体表面变得很不稳定,借冷凝液表面的张力作用和在静电场下液膜的不稳定现象使液膜厚度减薄,从而强化冷凝传热。其所需电场耗用的电力很小。人们想尽各种办法实施强化传热,归结起来不外乎两条途径,即改变传热面的形状和在传热面上或传热流路径内设置各种形状的湍流增进器或插入物。
当前换热器发展的基本趋势是:继续提高设备的传热效率,促进设备结构的紧凑性,加强生产制造的标准化系列化和专业化,并在广泛的范围内继续向大型化的方向发展。各种新型高效紧凑式换热器的应用范围将得到进一步扩大。在压力、温度和流量的许可范围内,尤其是处理强腐蚀性介质而需要使用贵重金属材料的场合下,新型紧凑式换热器将进一步取代管壳式换热器。
第一章
在化工生产中,为了工艺流程的需要,常常把低温流体加热或把高温流体冷却,把液态汽化或把蒸汽冷凝程液体,这些工艺过程都是通过热量传递来实现的。进行热量传递的设备称为换热设备或换热器。换热器是通用的一种工艺设备,他不仅可以单独使用,同时又是很多化工装置的组成部分。
在化工厂中,换热器的投资约占总投资的10%——20%,质量约为设备总质量的40%左右,检修工作量可达总检修工作量的60%以上。由此可见,换热器在化工生产中的应用是十分广泛的,任何化工生产工艺几乎都离不开它。在其他方面如动力、原子能、冶金、轻工、制造、食品、交通、家电等行业也有着广泛的应用。
为了强化壳程传热,除上述改变管子外形或在管外加翅片外,另一途径就是改变壳程档板或管间支撑物。为了克服单弓形档板的缺点,先后开发了双档板(Double Segmental Baffles)、三档板(Triple Segmental Baffles)、折流计了一种“外导流筒(Shellside Flow Distri2bution)”结构,接着又出现了整圆槽孔折流栅板[11]。最近ABB Lummus公司又新推出了Helical Baffles折流板结构[12]。实践证明,这些改进都大大降低了流体在壳程中的阻Taborek曾指出,流体在壳程中作纵向流动是管壳式换热器中的最理想结构形式,如果壳程流体流量足以保证在湍流条件下作纵向流动,这种选择看来是有利的。为了强化壳程传热,目前,壳程设计也在向各种强化结构组合的方向发展。
第二章 换热器工艺尺寸的选择
在设计过程中可以选择HTFS或HTRI进行设计计算,有时需要使用ASPEN PLUS模拟工艺物料的物性数据。先进行设计性计算,输入基础数据,如换热器形式、流体走向、卧立式、流体温度、压力、流量及物性数据等,进行运算得出比较合适的换热器直径和换热管长,再进行校核型和模拟型计算,核算所选换热器是否满足设计要求。
改变传热面形状的方法有多种,其中用于无相变强化传热的有:横槽管、螺旋槽管(S管)和缩放管。新近又开发出偏置折边翅片管(一种间断翅片管)和螺旋扁管,后者也叫麻花管(Twisted Tube),这原是瑞士的Allares公司技术,后经布朗公司(Brown Fin tube,Ltd.)改进,是一种高效换热元件[4]。用于有相变强化传热的强化沸腾传热管有:烧结多孔表面管、机械加工的多孔表面管(如日本的Themoexcel2E管)、电腐蚀加工的多孔表面管[5]、T型翅片管、ECR40管和Tube2B型管。从所报导数据来看,在整体低肋管上切纵槽后再滚压成型的Tube2B型管似乎有较高的传热性能,它可能符合薄液膜面积较大,隧道与外界液体相通,因而有利于蒸汽流出和液体吸入等要求[6]。俄罗斯也开发出一种称之为“变形翅片管”[7]的传热管,可用于空分装置的冷凝2蒸发器[8]。用于强化冷凝传热的传热管有:纵槽管、低螺纹翅片管、锯齿形翅片管(ST管)和径向辐射肋管式翅片管(R管)等。近年来,Hamon2L ummus公司又新推出一种SRC翅片管(SRC Fin Tube)[3],用于冷凝传热。内翅片管与横槽管和螺旋槽管一样,不但可用于单相对流传热,也可有效地用于强化管内流动沸腾传热[9]。而横槽管和螺旋槽管不但能强化管内传热,同时杆(Rod Baffles)、窗口不排管(NTIW)和波网(Nest)等新壳程结构[10]。随后有人设还能强化管外传热。外翅片管可以利用液体表面张力减薄冷凝液膜厚度以强化传热,这一发现大大促进了新型翅片管的研究开发。人们用不同金属制造不同形状的翅片管,其翅片形状有:三角肋三角槽、梯形肋三角槽、梯形肋梯形槽、三角肋梯形槽和Wolverine Tube2C管等。翅片密度在50~3000个翅片,与光管相比,给热系数可提高1~12倍[11]。俄罗斯还介绍了1种空冷器用的轧制翅片管,为双金属管,每隔1个翅片有切口,用以强化传热[12]。俄罗斯还有1种金属丝缠绕的绕丝翅片管[14]和气动喷涂翅片管[13]。内螺旋翅片管(NL管)是美国新开发的1种高效强化管内相变传热元件,根据翅片形状不同,可分为三角肋、梯形肋和矩形肋等,用于沸腾传热。内波纹螺纹管在湍流时可使对流传热系数增加1倍多。多头内螺纹管(ISF管)也是一种高效强化传热管,具有较好的强化管内沸腾传热的性能,传热膜系数为光管的116~212倍,在相同的传热面积下,能够完成相当于光管168%~200%的传热负荷。ISF管的强化传热作用主要是内表面和二次流的增加所致。可用于干式蒸发器,与目前制冷行业通用的星形内肋管蒸发器相比,质量可以减轻近50%。截面管也是近年来国外研究开发的强化传热元件,可分为蛋形管、豆状管和菱形管,统称为异形管。实验证明,此类管件与光圆管相比,具有显著的强化传热效果。
近年来,随着制造技术的进步,强化传热元件的开发,使得新型高效换热器的研究有了较大的发展,根据不同的工艺条件与换热工况设计制造了不同结构形式的新型换热器,并已在化工、炼油、石油化工、制冷、空分及制药各行业得到应用与推广,取得了较大的经济效益。国外推出的新型换热器有:ABB公司的螺旋折流板换热器(Helix changer TM)、Hamon Lummus公司的SRCTM空冷式冷凝器[3]、Packinox换热器[3]、NTIW列管式换热器[16]、英国Cal Gavin公司的丝状花内插物换热器(Hitran)[17]、日本的Hybrid混合式换热器[18],俄罗斯的变形翅片管换热器[8]、喷涂翅片管冷却器[19]、非钎焊金属丝缠绕翅片管换热器[14]和螺旋绕管式换热器[21]、美国Chemineer公司的Kenics换热器(KenicsHeat Exchanger)、日本的SM型换热器(内插静态混合器)、美国Brown Fin tube Ltd.的带扭带插入物的湍流增强式换热器(Ex2changerWith Turbulator)和麻花扁管换热器(TwistedTube Heat Exchanger)、美国Yuba公司的Hemilok○R换热器、澳大利亚Roach Heat Exchangers公司的柔性换热器(Flexible Heat Exchanger)等。此外,还有日本日阪制作所生产的世界单台最大处理能力为5000m3/h的UX2100型板式换热器、法国NordonCryogenie公司生产的6900mm×1525mm×1300mm(长×宽×高)换热面为1500m2的板翅式换热器、英国MichaelWebb Process EquipmentSupply公司的提箱式全焊板式换热器和其他各种紧凑式换热器(包括半焊式和全焊式板式换热器)、美国传热公司的F IV ER2ROD式防振结构换热器。更值一提的是在今年欧洲化工设备展览会上,法国Le Carbone公司还推出了1种称为新奇换热器(Exotic Heat Ex2changer),它是一种防腐的钽制换热器,光滑如玻璃,供制药工业,配有防污平管板,避免了任何污物在管接合处聚积。该换热器尺寸很大。此外,空冷器方向也有新进展。以上介绍的各式换热器的设计思想各有新颖之处,结构上各具特色。有的在于强化管内传热,有的着眼于壳程强化传热,有的改进了管箱设计,有的着重防止管板诱导振动,有的紧凑了设备结构,有的在于防腐防垢。其中最先进的要数PACK INOX、SRCTM、Helix2changerTMTwisted2tube Exchanger、H-2TRAN、Hybrid、Exotic Heat Exchanger几种换热器。PACK INOX换热器实际上是一种新型板式换热器,代替列管式换热器用作炼油厂催化重整装置混合料换热器,并且得到了迅速推广应用。SRCTM换热器,采用扁平翅片管(19mm×200mm),由于传热面造型特异,最适于强化传热,解决了偏流问题。其用于空冷式换热,传热特性高,压力损失低。He2liechangerTM换热器,采用了螺旋状折流板结构,设计原理是:将圆截面的特制板安装在拟螺旋状折流系统中。每块折流板占换热器壳程中横剖面的1/4,其倾角朝向换热器的轴线,即与换热器轴线保持一倾斜度。相邻折流板的周边相接,与外圆处成连续螺旋状,折流板轴向重叠。如欲减少支撑管子的跨度时,也可以采用双螺旋设计。独特的设计避免弓形折流板曲折的Z字形流道系统导致的死角和较高的返混。美国Brown公司最新推出了Twisted2tube Exchanger换热器,此换热器原本是瑞典Allares公司产品,Brown公司作了改进。其螺旋扁管制造过程包括“压扁”、“热扭”两个工序。由于管子结构独特,使管程与壳程同时处于螺旋流动,促进了湍流程度。该换热器总传热系数较常规换热器高40%,而压力降几乎相等。换热器组装时亦可采用螺旋扁管与光管混合方式。这种换热器在化工、石油化工行业中将具有广阔的应用前景[11]。HiTRAN换热器,采用丝状花内插物,可使流体在低速下产生径向位移和螺旋流相叠加的三维复杂流动,可提高诱发湍流和增强沿温度梯度方向上的流体扰动,能在不增加阻力的条件下大大提高传热系数[13]。Hy2brid换热器是日本近几年开发的一种新型换热器,它综合了板式换热器与管壳式换热器两者的优点,克服了板式换热器因密封问题而受到限制的弱点,很有发展前途[20]。