塑料模具设计实战
ug注塑模具设计实例

ug注塑模具设计实例以下是一个简单的注塑模具设计实例,模具设计的基本概念和步骤。
设计案例:一个简单的塑料瓶盖模具1. 确定产品尺寸和形状产品是一个简单的塑料瓶盖,直径为20mm,高度为3mm。
瓶盖表面有纹理,以增加摩擦力,方便开启。
2. 确定模具结构模具采用典型的双板模结构,由动模板和定模板组成。
动模板上设有型腔,定模板上设有浇口和流道。
3. 确定型腔布局由于瓶盖尺寸较小,可以采用一模一腔的布局。
型腔布置在动模板上,浇口和流道布置在定模板上。
4. 设计浇口和流道浇口和流道的设计需要考虑塑料的填充和流动。
本例中,采用点浇口,浇口直径为1mm,流道直径为4mm。
5. 设计推出机构推出机构用于将成型后的产品从模具中推出。
本例中,采用推杆推出,推杆直径为8mm,数量为4个。
推杆安装在动模板上,推出时推动瓶盖脱离型腔。
6. 设计冷却系统冷却系统用于将成型过程中的热量从模具中带走,防止产品变形和开裂。
本例中,采用水管冷却,水管直径为4mm,布置在动模板和定模板上。
7. 设计排气系统排气系统用于将成型过程中的气体从模具中排出,防止气体的积聚和压力的升高。
本例中,采用排气槽,排气槽直径为2mm,数量为4个。
排气槽布置在定模板上。
8. 设计模具零件加工工艺性模具零件的加工需要考虑其工艺性。
本例中,采用数控加工中心进行加工,材料选择不锈钢。
9. 设计模具装配工艺性模具装配需要考虑其工艺性。
本例中,采用螺钉连接动模板和定模板,并使用定位销进行定位。
以上是一个简单的注塑模具设计实例,希望能帮助您更好地理解模具设计的基本概念和步骤。
塑料注射模设计实例

第10页/共27页
二、模具结构方案设计
4、成型零件结构设计
(2)型芯:整体式?整体+局部镶入式?
➢型芯整体式
▪优点:曲面过渡圆滑;拼接痕迹少;冷却 系统易开设; ▪缺点:结构复杂、制造难度大,电火花加 工量大,加工时间长。
➢整体型芯+局部镶入式
▪既具有整体式的优点,又改善了局部制造 工艺(如圆形小型芯);但冷却系统开设 受一定限制。
➢薄壁深腔罩形件——推件板推出; ➢内部筋多、管形凸台多——推杆、推管推出;
➢螺纹部分——哈夫分型脱模;
➢综合考虑:推件板推出为主,高管形凸台采 用推管推出辅助。 ➢结论:推件板+推管联合推出
第13页/共27页
二、模具结构方案设计 6、侧向分型抽芯结构设计
➢开口端部外螺纹——矩形螺牙,螺距和牙尺寸较大,成型容易; ➢自动脱螺纹:螺纹成型精度高,但机构复杂,模具造价高 ➢斜滑块分型:导滑与推出机构设计难度较大,斜滑块冷却系统难以设置;推出 机构应改为推块推出才行。
▪注射容量:811cm3 锁模行程:1145mm
▪注射压力:150MPa 模板尺寸:840×840
▪注射行程:230
导柱间距:560×560
▪喷嘴半径:10mm
最小容模厚度:200mm
▪喷嘴孔径:3.5mm
最大容模厚度:640mm
▪定位圈直径:120mm 顶出力:73kN
Байду номын сангаас
▪锁模力:2500kN
顶出行程:125mm
第5页/共27页
细小 深槽
二、模具结构方案设计 1、分型面选择
➢选在塑件最大轮廓面上——可选A-A、B-B或C-C; ➢避免侧抽芯及长抽芯距——可选A-A或C-C; ➢便于充模排气——可选A-A或C-C ➢便于脱模——可选A-A;螺纹部分选B-B为好 ;
塑料模具设计实例
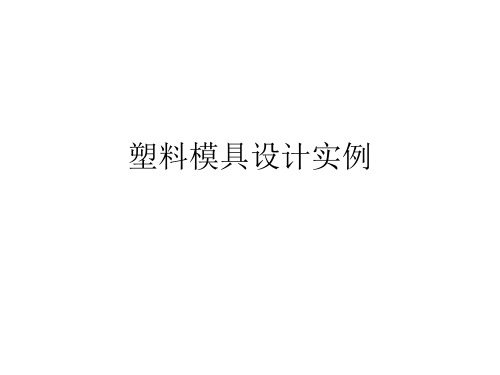
塑料件结构图
模具图
模具图-卸ቤተ መጻሕፍቲ ባይዱ图
模具设计特点
• 制品为薄壁件,内腔相对较深且有一定的精度要求。该模具采 用点浇口,并设计了点浇口自动切断脱落机构;采用摆块式二 级机构,确保了制品不发生推出变形。模具结构紧凑,工作安 全、可靠。 • 工作原理:开模时,在弹簧20的作用下I-I面首先分型,拉料杆 13拉断点浇口,流道凝料脱出流道板14,保留在拉料杆上。流 道板14运行至定距拉杆17端部时受定距拉杆17的阻挡而停止。 接着Π-Π面分型。当Ι-Ι面分型之后,脱浇板11在弹簧15的作用下, 将流道凝料推离拉料杆13,继而弹簧8推动拉料杆9,使流道凝 料脱离浇口套10和脱浇板11而掉落。定距螺钉5限定脱浇板11的 推出高度。当Π-Π面分型到一定距离时,机床开始推动推板37, 安装在推板两侧的顶板26推动顶块25向上转动(以轴钉29为转 轴),从而推动推件板23和凹模板22上行,由于凸模21不动, 故制品与凸模脱松,完成第一级推出动作。继续推出,顶板26 失去对顶块25的作用,故推件板和凹模板不在上行,而推杆36 继续上行将制品推出凹模,完成第二级推出动作。
再例如-零件图
模具结构
模具结构
花盆及模具设计
花盆结构图
模具结构——一次注塑两件
模具结构——一次注塑两件
花盆模具特点
• 特点:制品为深腔圆桶形状。该模具设计了2个型腔; 采用流道浇注系统,使用塑料能够较好地充模并节约原 料;型腔、型芯设计均设计了螺旋式冷却水路,使冷却 和冷却效率提高;定、动模合模时除了导柱导身装置外, 增加了圆锥定位面,确保了制品壁厚的均匀性;镶块31 的装配面要留有适当间隙(必要时开设气道),避免制 品与型芯之间产生真空状态。推件采用推件板,同气吹 结合的方式。 • 工作原理:开模后,制品脱离型腔镶件7留在型芯10上。 推出时,连接推杆36和环形推件板9在推板13的作用下, 将制品上推出一小段高度,然后高压空气经过进气管接 头11进入制品与型芯脱松的空隙中,制品即补吹起,最 后由人工取出制品。连接推杆36上套有弹簧37可使推件 板9复位。
[整理]InventorMold塑料模具设计实战.
![[整理]InventorMold塑料模具设计实战.](https://img.taocdn.com/s3/m/2fad0014482fb4daa48d4b2a.png)
Inventor Mold塑料模具设计实战默认分类2010-05-28 00:36:30 阅读16 评论0 字号:大中小订阅本文旨在与读者分享Inventor Mold的设计思路。
其特点是在一款三维设计软件中完成所有的设计,并且集成模流分享软件Mold Flow功能,满足塑料模具设计的整体解决方案。
随着塑料模具行业的快速发展、塑料模具制造精度的提高以及模具行业的激烈竞争,使得消费者对塑料模具设计的要求越来越高,必须同时考虑设计精度和设计周期的影响。
目前,大部分塑料模具设计都是在三维软件中进行分模设计,在二维中进行排位的设计。
这种方式,由于三维软件和二维软件分别独立,缺乏关联,存在着一些弊病,很容易出现设计的错误。
另外三维与二维的“拼凑式”设计,也严重影响了塑料模具设计的精度。
下面以一个实例,来介绍Inventor Mold的设计流程。
塑料产品如图1所示。
该产品的特点是需要修补孔,要做抽芯机构。
1.新建模具设计打开Inventor Mold后,新建一塑料模具设计,进入到Inventor Mold塑料模具设计的环境下,在未导入塑料产品之前,其中很多的指令都处于不可用状态,如图2所示。
2.导入塑胶产品执行“塑料零件”指令,选择塑件产品,将塑件产品导入到塑料模具设计环境中,如图3所示。
此时可看到菜单都已经被激活,如图4所示。
3.调整出模方向此步骤是用来调整塑件产品的出模方向,当塑件导入模具设计环境后,会有一个默认的方向,但是默认的方向有可能不是正确的模具出模方向,所以必须进行调整。
如图5所示,这里调整出模方向非常重要,因为Inventor Mold自动补孔(自动修补破孔)方式会根据出模的方向来定。
4.选择材料材料库是Inventor Mold的一大特色,Inventor Mold基本上含有模具行业常用的材料,共有七千多种塑料材料,且每种材料都有其属性,包括厂商以及牌号,当然还包括收缩率。
之所以Inventor Mold含有如此丰富的材料库,那是因为Inventor Mold中含有Mold Flow 的功能,在进行模流分析时,必须先定义具体的材料,才可以进行工艺的设定和模流的分析。
注塑模设计案例

2024年10月10日
三、注射模旳构造设计
3.浇注系统旳设计
⑶浇口设计 浇口形式旳选择
因为该塑件外观质量要求较高,浇口旳位置和大小应以不 影响塑件旳外观质量为前提。同步,也应尽量使模具构造 更简朴。
潜伏式浇口 浇口位置在塑件内表面,不影响其外 观质量。 但采用这种浇口形式增长了模具构造 旳复杂程度。
2024年10月10日
二、拟定成型设备选择与模塑工艺规程编制
2.拟定成型工艺参数
⑴塑件模塑成型工艺参数旳拟定 查附表9得出工艺参数见下表,试模时可根据实际 情况作适当调整。
聚碳酸脂
预热和干燥 料筒温度t/0C
喷嘴温度t/0C
温度t/0C110~120 时间τ/h8~12 后段 210~240 中段 230~280 前段 240~285
⑵塑件型腔较大,有尺寸不等旳孔,如Ф12、4-Ф10、4Ф4.5、4-Ф5它们均符合最小孔径要求。
⑶在塑件内壁有4个高2.2,长11旳内凸台。所以,塑件不 易取出。需要考虑侧抽装置。
结论:综上所述,该塑件可采用注射成型加工。
2024年10月10日
二、拟定成型设备选择与模塑工艺规程编制
1.计算塑件旳体积和重量
查有关手册得PC旳收缩率为Q=0.5%~0.7%,故平 均收缩率为:Scp=(0.5+0.7)%/2=0.6%=0.006,根 据塑件尺寸公差要求,模具旳制造公差取Z=Δ/3。
已知条件:平均收缩率SCP =0.006mm;模具旳制 造公差取Z=Δ/3。
类 零件 别 图号
模具 零件 名称
塑件尺寸
计算公式
塑料模设计及制造实例
二、拟定模具构造方案
1.拟定型腔数量及布局形式 2.选择分型面 3.拟定浇注系统与排气系统 4.选择推出方式 5.拟定侧凹部分旳处理方式 6.模具加热与冷却方式 7.拟定成型零件旳构造形式
注塑模具设计实例

注塑模具设计实例注塑模具是注塑成型过程中的重要工具,它决定了产品的形状、尺寸和质量。
下面将介绍一个注塑模具设计实例。
该注塑模具用于生产一个塑料小零件,产品尺寸为25mm × 10mm × 5mm。
根据客户要求,模具设计师需要考虑以下几个方面:1.产品结构设计:根据产品尺寸和功能要求,模具设计师需要确定模具中的产品结构。
在这个实例中,小零件是一个封闭的长方体,底部有一个孔。
设计师结合注塑工艺和产品功能要求,选择了一种单腔模具结构。
这个结构能够满足产品形状和尺寸的要求,同时保证注塑成型的稳定性。
2.模具材料选择:模具的材料选择直接影响着模具的使用寿命和成本。
根据产品的使用环境和注塑工艺要求,设计师选择了优质的冷作模具钢作为模具材料。
这种钢材具有良好的切削性能和耐磨性,可以满足长时间连续生产的需求。
3.注塑工艺参数:注塑模具的设计需要考虑注塑工艺的各个参数,如注塑温度、保压时间、保压压力等。
在这个实例中,设计师根据塑料材料的熔体温度和流动性选择了适当的注塑温度和保压时间。
同时,根据产品的厚度和尺寸,设计师设定了合适的保压压力,以确保产品的成型质量。
4.模具结构设计:模具结构的设计需要考虑产品的成型要求和模具的制造工艺。
在这个实例中,设计师在模具上设置了合适的冷却水道和顶针机构,以确保注塑成型过程中的温度控制和产品的尺寸稳定。
同时,设计师在模具上设置了合适的排气装置,以避免产品出现气泡和缺陷。
5.模具制造和组装:根据设计图纸,模具制造师使用数控机床进行模具加工。
首先进行粗加工,然后进行精细加工和装配。
在模具加工和组装过程中,需要进行严格的尺寸和工艺控制,以确保模具的精度和质量。
综上所述,注塑模具设计需要综合考虑产品结构、模具材料、注塑工艺、模具结构以及模具制造和组装等方面的因素。
通过合理设计和制造,注塑模具可以满足产品的形状、尺寸和质量要求,提高注塑成型的效率和稳定性。
UG12.0塑料塑胶模具设计教程NX10.0实战

UG12.0塑料塑胶模具设计教程NX10.0实战UG12.0塑料塑胶模具设计教程NX10.0实战观看地址:https:///course/384820 手机电脑平板永久在线观看1.1塑料塑胶模具简介.avi1.2产品的初始化.avi1.3模具坐标系设定.avi1.4收缩率设定.avi1.5调入模芯.avi1.6区域设定.avi1.7生成分型面.avi1.8分模.avi1.vwt2.10产品投影面积分析1.avi2.11矩形型腔布局1.avi2.12圆形型腔布局1.avi2.1曲面补片面命令1.avi2.2曲面补片遍历命令1.avi2.3设计裙边分型面命令1.avi2.4手动设计分型面1.avi2.5拆分面设计分型面1.avi2.6拆分面设计分型面21.avi2.7调整零件位置1.avi2.8产品拔模分析1.avi2.9产品厚度分析1.avi3.10侧抽芯带镶件分模实例(创建分型面及分模).avi3.11侧抽芯带镶件分模实例2(创建侧抽和镶件).avi3.12侧抽芯带镶件分模实例2(创建分型面及分模).avi3.13侧抽芯带镶件分模实例3(侧抽芯及镶件拆分).avi3.14侧抽芯带镶件分模实例3(创建分型面及分模).avi3.15复杂产品手动分型面设计实例(产品分析区域划分).avi 3.16复杂产品手动分型面设计实例(修补内孔).avi3.17复杂产品手动分型面设计实例(设计裙边曲面).avi3.18复杂产品手动分型面设计实例(产品分模).avi3.1分摸实例异形孔件分摸(产品分析).avi3.2分摸实例异形孔件分模(产品检查区域划分).avi3.3分摸实例异形孔件分模(分型面创建及分模).avi3.4分摸实例手机前面板分模.avi3.5分摸实例显示器外壳带侧抽分模(产品检查区域划分).avi 3.6分摸实例显示器外壳带侧抽分模(分型面创建及分模).avi 3.7分摸实例显示器外壳带侧抽分模(侧抽芯拆分).avi3.8分模实例水杯哈弗模.avi3.9侧抽芯带镶件分模实例(产品分析及区域划分).avi4.10等斜度曲线分模.avi4.11等斜度曲线分模.avi4.12斜顶分模.avi4.13斜顶分模.avi4.14斜顶分模实例2.avi4.15斜顶分模实例2.avi4.16斜顶分模实例2.avi4.17斜顶分模实例3.avi4.18体积块分模法.avi4.1手动分模介绍及快捷键设定.avi4.2手动分模一般步骤.avi4.3有异型孔的分模实例(补面).avi4.4多个异形孔复杂产品分模.avi4.5多个异形孔复杂产品分模(巧用颜色选面).avi4.6多型腔模具布局(产品分模).avi4.7多型腔模具布局(型腔布局).avi4.8出不同产品型腔(产品相对位置调整).avi4.9出不同产品型腔(产品同步分模).avi5.10添加水路密封圈.avi5.11添加水路水堵.avi5.12添加水嘴.avi5.13添加侧抽芯系统.avi5.14侧抽芯系统机构细化.avi5.15调取斜顶结构.avi5.16斜顶结构细化.avi5.1模具典型结构演示.avi5.2ug模架库调取模架一般过程.avi5.3腔体切除.avi5.4调取定位圈和浇口套.avi5.5调取顶杆.avi5.6调取弹簧.avi5.7调取拉料杆.avi5.8创建浇注系统.avi5.9创建水路.avi6.10全流程设计实例(曲面分型面).avi6.11全流程设计实例(曲面分型面).avi6.12全流程设计实例(曲面分型面).avi6.13全流程设计实例(曲面分型面).avi6.14全流程设计实例(曲面分型面).avi6.15全流程设计实例(曲面分型面).avi6.1全流程设计实例一电话机上盖模具.avi 6.2全流程设计实例一电话机上盖模具.avi 6.3全流程设计实例一电话机上盖模具.avi 6.4全流程设计实例一电话机上盖模具.avi 6.5全流程设计实例一电话机上盖模具.avi 6.6全流程设计实例一电话机上盖模具.avi6.7全流程设计实例一电话机上盖模具.avi 6.9全流程设计实例(曲面分型面).avi。
塑料模具设计实例.
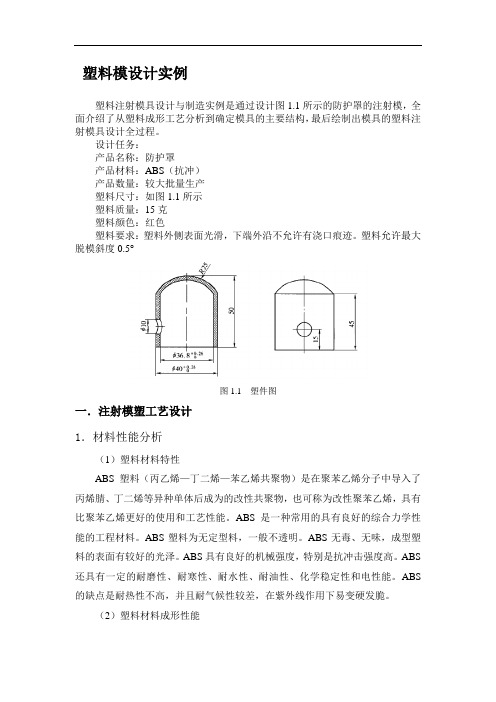
塑料模设计实例塑料注射模具设计与制造实例是通过设计图1.1所示的防护罩的注射模,全面介绍了从塑料成形工艺分析到确定模具的主要结构,最后绘制出模具的塑料注射模具设计全过程。
设计任务:产品名称:防护罩产品材料:ABS(抗冲)产品数量:较大批量生产塑料尺寸:如图1.1所示塑料质量:15克塑料颜色:红色塑料要求:塑料外侧表面光滑,下端外沿不允许有浇口痕迹。
塑料允许最大脱模斜度0.5°图1.1 塑件图一.注射模塑工艺设计1.材料性能分析(1)塑料材料特性ABS塑料(丙乙烯—丁二烯—苯乙烯共聚物)是在聚苯乙烯分子中导入了丙烯腈、丁二烯等异种单体后成为的改性共聚物,也可称为改性聚苯乙烯,具有比聚苯乙烯更好的使用和工艺性能。
ABS是一种常用的具有良好的综合力学性能的工程材料。
ABS塑料为无定型料,一般不透明。
ABS无毒、无味,成型塑料的表面有较好的光泽。
ABS具有良好的机械强度,特别是抗冲击强度高。
ABS还具有一定的耐磨性、耐寒性、耐水性、耐油性、化学稳定性和电性能。
ABS的缺点是耐热性不高,并且耐气候性较差,在紫外线作用下易变硬发脆。
(2)塑料材料成形性能使用ABS 注射成形塑料制品时,由于其熔体黏度较高,所需的注射成形压力较高,因此塑料对型芯的包紧力较大,故塑料应采用较大的脱模斜度。
另外熔体黏度较高,使ABS 制品易产生熔接痕,所以模具设计时应注意减少浇注系统对料流的阻力。
ABS 易吸水,成形加工前应进行干燥处理。
在正常的成形条件下,ABS 制品的尺寸稳定性较好。
(3)塑料的成形工艺参数确定查有关手册得到ABS (抗冲)塑料的成形工艺参数: 密 度 1.01~1.04克/mm³ 收 缩 率 0.3%~0.8%预热温度 80°c~85°c ,预热时间2~3h料筒温度 后段150°c~170°c ,中段165°C~180°c ,前段180°c~200°c 喷嘴温度 170°c~180°c 模具温度 50°c~80°c 注射压力 60~100MPa注射时间 注射时间20~90s ,保压时间0~5s ,冷却时间20~150s.2.塑件的结构工艺性分析(1)塑件的尺寸精度分析该塑件上未注精度要求的均按照SJ1372中8级精度公差值选取,则其主要尺寸公差标注如下(单位均为mm ):外形尺寸:26.0040+φ、 1.2050+、12.0045+、94.0025+R 内形尺寸:26.008.36+φ 孔 尺 寸:52.0010+φ孔心距尺寸:34.015± (2)塑件表面质量分析该塑件要求外形美观,外表面表面光滑,没有斑点及熔接痕,粗糙度可取Ra0.4μm ,下端外沿不允许有浇口痕迹,允许最大脱模斜度0.5°,而塑件内部没有较高的表面粗糙度要求。
塑料模具课程设计实例
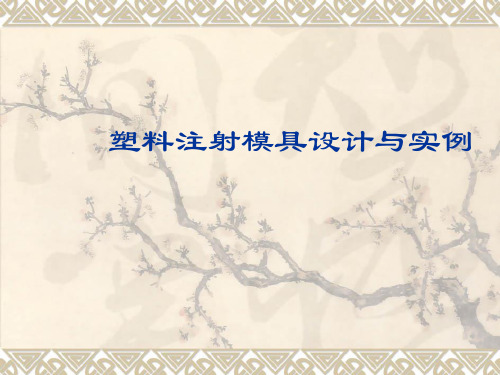
塑料注射模具设计与实例
本章基本内容
(2)模具钢
3Cr2Mo(P20)钢:可预硬化的塑料模具钢,预硬化后
硬度为36~38 HRC,适用于制作塑料注射模具型腔,其 加工性能和表面抛光性较好。 10Ni3CuAIVS(PMS)钢:析出硬化钢。预硬化后时效 硬化,硬度可达40~45 HRC。热变形极小,可做镜面抛 光,特别适合于腐蚀精细花纹。可用于制作尺寸精度高, 生产批量大的塑料注射模具。 6Ni7Ti2Cr钢:马氏体时效钢。在未加工前为固熔体 状态,易于加工。精加工后以480℃~520℃进行时效, 硬度可达50-57 HRC。适用于制造要求尺寸精度高的小 型塑料注射模具,可做镜面抛光。 8CrMnWMoVS(8CrMn)钢:为易切预硬化钢,可做镜面 抛光。其抗拉强度高,常用于大型注射模具。调质后硬 度为33-35 HRC,淬火时可空冷,硬度可达42-60 HRC。 25CrNi3MoAI钢:适用于型腔腐蚀花纹,属于时效硬 化钢。调质后硬度23 25 HRC,可用普通高速钢刀具加 工。时效后硬度38~42 HRC。可以做氮化处理,氮化处 理后表层硬度可达1100 HV。 Crl6Ni4Cu3Nb(PCR)钢:耐腐蚀钢。可以空冷淬火,
塑料注射模具制造特点 塑料注射模具零件常用加工方法和材料 塑料注射模具装配 塑料注射模具设计与制造实例
重点、难点
塑料注射模具制造特点 塑料注射模具零件常用加工方法和材料 塑料注射模具设计
ug注塑模具设计实例
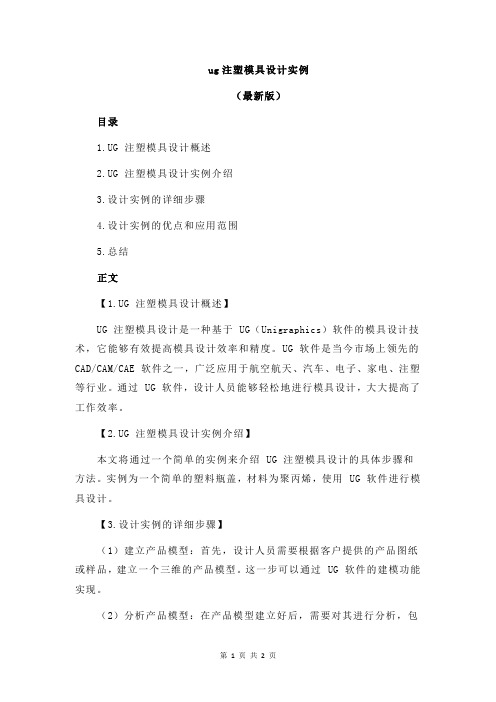
ug注塑模具设计实例(最新版)目录1.UG 注塑模具设计概述2.UG 注塑模具设计实例介绍3.设计实例的详细步骤4.设计实例的优点和应用范围5.总结正文【1.UG 注塑模具设计概述】UG 注塑模具设计是一种基于 UG(Unigraphics)软件的模具设计技术,它能够有效提高模具设计效率和精度。
UG 软件是当今市场上领先的CAD/CAM/CAE 软件之一,广泛应用于航空航天、汽车、电子、家电、注塑等行业。
通过 UG 软件,设计人员能够轻松地进行模具设计,大大提高了工作效率。
【2.UG 注塑模具设计实例介绍】本文将通过一个简单的实例来介绍 UG 注塑模具设计的具体步骤和方法。
实例为一个简单的塑料瓶盖,材料为聚丙烯,使用 UG 软件进行模具设计。
【3.设计实例的详细步骤】(1)建立产品模型:首先,设计人员需要根据客户提供的产品图纸或样品,建立一个三维的产品模型。
这一步可以通过 UG 软件的建模功能实现。
(2)分析产品模型:在产品模型建立好后,需要对其进行分析,包括分析产品的结构、材料、尺寸公差等,以便在模具设计中充分考虑这些因素。
(3)模具设计:在分析好产品模型后,就可以开始进行模具设计了。
这一步包括确定模具的类型、设计模具的结构、确定模具的尺寸等。
(4)模具制造:在模具设计好后,需要根据设计图纸制造模具。
这一步通常由专门的模具制造厂完成。
(5)模具试模:模具制造好后,需要进行试模。
通过试模,可以检查模具的设计和制造是否存在问题,如果存在问题,需要及时进行修正。
【4.设计实例的优点和应用范围】UG 注塑模具设计具有许多优点,包括设计精度高、效率高、操作简单等。
这使得它广泛应用于各种注塑产品的生产中。
无论是简单的日用品,还是复杂的机械零件,都可以通过 UG 注塑模具设计进行生产。
注塑模具设计实例

二、注塑模具设计实例实例 1——电流线圈架的模具设计及制造塑料制品如图 3—219 所示,大量量生产,试进行塑件的成型工艺和模具设计,并选择模具的主要加工方法与工艺。
图 3— 219电流线圈架部件图(一)成型工艺规程的编制1.塑件的工艺性剖析(1)塑件的原资料剖析(2)塑件的构造和尺寸精度表面质量剖析1)构造剖析。
从部件图上剖析,该部件整体形状为长方形,在宽度方向的一侧有两个高度为8.5mm ,R5mm 的两个凸耳,在两个高度为 12mm 、长、宽分别为 17mm 和 13.5mm 的凸台上,一个带有的凹槽 (对称散布 ),另一个带有 4.lmmXl .2 mm 的凸台对称散布。
所以,模具设计时一定设置侧向分型抽芯机构,该部件属于中等复杂程度。
2)尺寸精度剖析。
该部件重要尺寸如:12.100 .12 mm 、12.100..0402 mm 、15.1 00..1402 mm 、15.100.12 mm 等精度为 3 级(Sj1372—78),次重要尺寸如:13.5±0.11、1700.2 mm、10.5±0.1mm 、1400 .2 mm 等的尺寸精度为4~5 级(Sj 1372—78)。
由以上剖析可见,该部件的尺寸精度中等偏上,对应的模具有关部件的尺寸加工能够保证。
从塑件的壁厚上来看,壁厚最大处为1.3mm ,最小处为 0.95mm ,壁厚差为 0.35mm ,较均匀,有益于部件的成型。
3)表面质量剖析。
该部件的表面除要求没出缺点、毛刺,内部不得有导电杂质外,没有特其他表面质量要求,故比较简单实现。
综上剖析能够看出,注射时在工艺参数控制得较好的状况下,零件的成型要求能够获得保证。
(3)计算塑件的体积和质量计算塑件的质量是为了采纳注射机及确立型腔数。
经计算塑件的体积为 V=4087mm 3;计算塑件的质量:依据设计手册可查得加强聚丙烯的密度为ρ=1.04g/cm3。
故塑件的质量为W=Vρ=4.25g采纳一模两件的模具构造,考虑其外形尺寸、注射时所需压力和工厂现有设施等状况,初步采纳注射机为XS—Z—60 型。
塑料模具设计步骤与实例精解
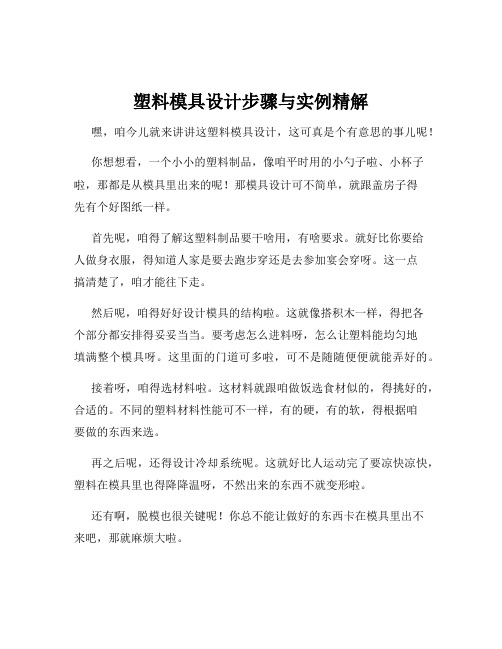
塑料模具设计步骤与实例精解嘿,咱今儿就来讲讲这塑料模具设计,这可真是个有意思的事儿呢!你想想看,一个小小的塑料制品,像咱平时用的小勺子啦、小杯子啦,那都是从模具里出来的呢!那模具设计可不简单,就跟盖房子得先有个好图纸一样。
首先呢,咱得了解这塑料制品要干啥用,有啥要求。
就好比你要给人做身衣服,得知道人家是要去跑步穿还是去参加宴会穿呀。
这一点搞清楚了,咱才能往下走。
然后呢,咱得好好设计模具的结构啦。
这就像搭积木一样,得把各个部分都安排得妥妥当当。
要考虑怎么进料呀,怎么让塑料能均匀地填满整个模具呀。
这里面的门道可多啦,可不是随随便便就能弄好的。
接着呀,咱得选材料啦。
这材料就跟咱做饭选食材似的,得挑好的,合适的。
不同的塑料材料性能可不一样,有的硬,有的软,得根据咱要做的东西来选。
再之后呢,还得设计冷却系统呢。
这就好比人运动完了要凉快凉快,塑料在模具里也得降降温呀,不然出来的东西不就变形啦。
还有啊,脱模也很关键呢!你总不能让做好的东西卡在模具里出不来吧,那就麻烦大啦。
咱来举个例子哈,就说做个简单的塑料碗。
咱得先想好这碗多大呀,多深呀,形状得好看吧。
然后设计模具,让塑料能顺利地流进去,填满每个角落。
材料得选那种结实又安全的,可不能有害物质超标呀。
冷却系统得保证碗能快速冷却成型,脱模的时候得轻轻松松就能把碗拿出来。
你说这塑料模具设计神奇不神奇?这可都是技术活呀!要是没设计好,那做出来的东西不是有瑕疵就是用不了,多浪费呀。
所以啊,这模具设计师可得有真本事,得细心,还得有创意。
咱平时用的那些塑料制品,可都是经过模具设计师精心设计出来的呢。
他们就像魔法师一样,能把一堆塑料变成各种各样有用的东西。
所以呀,可别小看了这塑料模具设计,这里面的学问大着呢!咱得尊重这些设计师的劳动成果,好好珍惜咱用的每一个塑料制品呀。
怎么样,现在是不是对塑料模具设计有了更深的了解啦?嘿嘿!。
注塑模课程设计实训报告

注塑模课程设计实训报告一、前言注塑模具设计是机械工程领域的一个重要分支,它涉及到塑料成型工艺、模具结构设计、CAD/CAM技术等多个方面。
为了提高我们的实践能力,加深对注塑模具设计的理解,我们参加了注塑模具课程设计实训。
以下是本次实训的报告。
二、实训目的1. 熟悉注塑模具设计的基本流程和方法。
2. 掌握注塑模具的结构设计要点。
3. 培养运用CAD/CAM技术进行模具设计的能力。
4. 提高团队协作和沟通能力。
三、实训内容1. 塑件分析本次实训选取的塑件为某电子产品中的塑料衬套。
首先,我们对塑件进行详细分析,包括尺寸、形状、材质、表面粗糙度等。
通过对塑件的分析,为后续模具设计提供依据。
2. 成型工艺分析根据塑件分析结果,我们确定了成型工艺参数,包括注射压力、温度、冷却时间等。
同时,对塑件成型过程中的收缩率、翘曲变形等进行了预测和评估。
3. 模具结构设计(1)模具总体结构设计根据塑件形状和尺寸,我们确定采用单腔模具结构。
模具主要由定模、动模、浇注系统、导向机构、脱模机构等部分组成。
(2)浇注系统设计浇注系统是注塑模具的重要组成部分,其设计直接影响塑件的成型质量和生产效率。
我们采用主流道、分流道、冷却水道等结构,确保塑料熔体顺利流入模具型腔。
(3)导向机构设计导向机构的作用是保证模具在成型过程中各部件的相对位置准确。
我们设计了导向柱、导向套等结构,确保模具在成型过程中的稳定性。
(4)脱模机构设计脱模机构的作用是使塑件在成型后顺利从模具中取出。
我们采用斜导柱、弹簧等结构,实现塑件的顺利脱模。
4. CAD/CAM技术应用利用CAD/CAM软件进行模具设计,可以提高设计效率,降低设计成本。
我们采用SolidWorks软件进行模具设计,并生成CAD图纸和CAM加工文件。
四、实训成果1. 完成了一套塑料衬套注塑模具的设计,包括模具结构、CAD图纸和CAM加工文件。
2. 通过实训,我们掌握了注塑模具设计的基本流程和方法,提高了设计能力。
塑料模具设计(内含实训小结)

目录第一章 (2)一、塑件是的工艺分析 (2)PP塑料概念 (3)比重: (3)二、塑件的材料分析 (3)成型收缩率: 1.0-2.5% (4)成型温度:160-220℃ (4)干燥条件: (4)物料性能密度小,强度刚度,硬度耐热性均优于低压聚乙烯,可在100度左右使用.具有良好的电性能和高频绝缘性不受湿度影响,但低温时变脆,不耐磨易老化. 适于制作一般机械零件,耐腐蚀零件和绝缘零件。
(4)成型性能 (4)三、塑件的工艺尺寸 (5)第二章 (5)一、模具的结构设计 (5)二、注射机选择及校核 (6)三、确定浇注系统 (7)四、分型面的设计 (9)第三章 (10)一、模具成型零件工作尺寸的计算 (10)模具型腔的尺寸计算 (10)型芯布置 (11)参考文献 (14)奔驰车标塑料模具设计第一章一、塑件是的工艺分析塑件如图1 所示,材料为聚丙烯(PP)。
该塑件尺寸小,精度高。
此塑件为奔驰车标外有圆环,外环为ø60、内环为ø50。
中间为奔驰的三角。
名称:奔驰车标材料:聚丙烯(PP)中文名:(聚丙烯)英文名称:Polypropylene PP塑料概念比重:0.9-0.91克/立方厘米二、塑件的材料分析关于PP材料的介绍成型收缩率: 1.0-2.5%成型温度:160-220℃干燥条件:物料性能密度小,强度刚度,硬度耐热性均优于低压聚乙烯,可在100度左右使用.具有良好的电性能和高频绝缘性不受湿度影响,但低温时变脆,不耐磨易老化. 适于制作一般机械零件,耐腐蚀零件和绝缘零件。
成型性能1.结晶料,吸湿性小,易发生融体破裂,长期与热金属接触易分解.2.流动性好,但收缩范围及收缩值大,易发生缩孔.凹痕,变形.3.冷却速度快,浇注系统及冷却系统应缓慢散热,并注意控制成型温度.料温低方向方向性明显.低温高压时尤其明显,模具温度低于50度时,塑件不光滑,易产生熔接不良,留痕,90度以上易发生翘曲变形4.塑料壁厚须均匀,避免缺胶,尖角,以防应力集中.特定条件下容易分解常见制品:盆、桶、家具、薄膜、编织袋、瓶盖、汽车保险杠等。
注塑模具设计模拟实训报告

一、实训背景随着我国塑料工业的快速发展,注塑模具设计在塑料成型领域中扮演着至关重要的角色。
为了提高注塑模具设计的专业水平,培养学生的实际操作能力,我们开展了注塑模具设计模拟实训。
本次实训采用先进的注塑模具设计软件,通过模拟实验,使学生深入了解注塑模具设计流程,掌握模具设计的基本原理和方法。
二、实训目的1. 熟悉注塑模具设计的基本流程和原理;2. 掌握注塑模具设计软件的操作技能;3. 培养学生的实际操作能力和团队协作精神;4. 提高学生对注塑模具设计的认识,为今后的工作奠定基础。
三、实训内容1. 注塑模具设计软件学习实训过程中,我们学习了Moldex3D、UG等注塑模具设计软件。
通过软件操作,掌握了模具设计的基本步骤,如:创建模型、设置浇注系统、设计冷却系统、设置脱模机构等。
2. 注塑模具设计模拟实验(1)实验一:模具结构设计以一个简单的塑料杯为例,通过Moldex3D软件进行模具结构设计。
首先创建模型,然后设置浇注系统、冷却系统、脱模机构等。
通过模拟实验,分析模具结构设计的合理性和优缺点。
(2)实验二:模具加工工艺分析针对实验一中设计的模具,分析模具加工工艺。
包括模具材料选择、加工方法、加工顺序等。
通过模拟实验,验证模具加工工艺的可行性。
(3)实验三:模具性能分析通过Moldex3D软件对实验一、二中的模具进行性能分析,包括熔体填充、冷却、脱模等过程。
分析模具性能对产品品质的影响,并提出改进措施。
3. 模具设计团队协作在实训过程中,我们分成小组进行模具设计。
每个小组负责模具设计的一部分,如:模具结构设计、浇注系统设计、冷却系统设计等。
通过团队协作,提高了学生的沟通能力和团队协作精神。
四、实训成果1. 学员们掌握了注塑模具设计的基本流程和原理;2. 学员们熟练掌握了注塑模具设计软件的操作技能;3. 学员们的实际操作能力得到显著提高;4. 学员们的团队协作精神得到加强。
五、实训总结本次注塑模具设计模拟实训取得了圆满成功。
塑料模具设计实例(word文档良心出品)

塑料模设计实例塑料注射模具设计与制造实例是通过设计图1.1所示的防护罩的注射模,全面介绍了从塑料成形工艺分析到确定模具的主要结构,最后绘制出模具的塑料注射模具设计全过程。
设计任务:产品名称:防护罩产品材料:ABS(抗冲)产品数量:较大批量生产塑料尺寸:如图1.1所示塑料质量:15克塑料颜色:红色塑料要求:塑料外侧表面光滑,下端外沿不允许有浇口痕迹。
塑料允许最大脱模斜度0.5°图1.1 塑件图一.注射模塑工艺设计1.材料性能分析(1)塑料材料特性ABS塑料(丙乙烯—丁二烯—苯乙烯共聚物)是在聚苯乙烯分子中导入了丙烯腈、丁二烯等异种单体后成为的改性共聚物,也可称为改性聚苯乙烯,具有比聚苯乙烯更好的使用和工艺性能。
ABS是一种常用的具有良好的综合力学性能的工程材料。
ABS塑料为无定型料,一般不透明。
ABS无毒、无味,成型塑料的表面有较好的光泽。
ABS具有良好的机械强度,特别是抗冲击强度高。
ABS还具有一定的耐磨性、耐寒性、耐水性、耐油性、化学稳定性和电性能。
ABS的缺点是耐热性不高,并且耐气候性较差,在紫外线作用下易变硬发脆。
(2)塑料材料成形性能使用ABS 注射成形塑料制品时,由于其熔体黏度较高,所需的注射成形压力较高,因此塑料对型芯的包紧力较大,故塑料应采用较大的脱模斜度。
另外熔体黏度较高,使ABS 制品易产生熔接痕,所以模具设计时应注意减少浇注系统对料流的阻力。
ABS 易吸水,成形加工前应进行干燥处理。
在正常的成形条件下,ABS 制品的尺寸稳定性较好。
(3)塑料的成形工艺参数确定查有关手册得到ABS (抗冲)塑料的成形工艺参数: 密 度 1.01~1.04克/mm³ 收 缩 率 0.3%~0.8%预热温度 80°c~85°c ,预热时间2~3h料筒温度 后段150°c~170°c ,中段165°C~180°c ,前段180°c~200°c 喷嘴温度 170°c~180°c 模具温度 50°c~80°c 注射压力 60~100MPa注射时间 注射时间20~90s ,保压时间0~5s ,冷却时间20~150s.2.塑件的结构工艺性分析(1)塑件的尺寸精度分析该塑件上未注精度要求的均按照SJ1372中8级精度公差值选取,则其主要尺寸公差标注如下(单位均为mm ):外形尺寸:26.0040+φ、 1.2050+、12.0045+、94.0025+R 内形尺寸:26.008.36+φ 孔 尺 寸:52.0010+φ孔心距尺寸:34.015± (2)塑件表面质量分析该塑件要求外形美观,外表面表面光滑,没有斑点及熔接痕,粗糙度可取Ra0.4μm ,下端外沿不允许有浇口痕迹,允许最大脱模斜度0.5°,而塑件内部没有较高的表面粗糙度要求。
塑料模课程设计实训报告
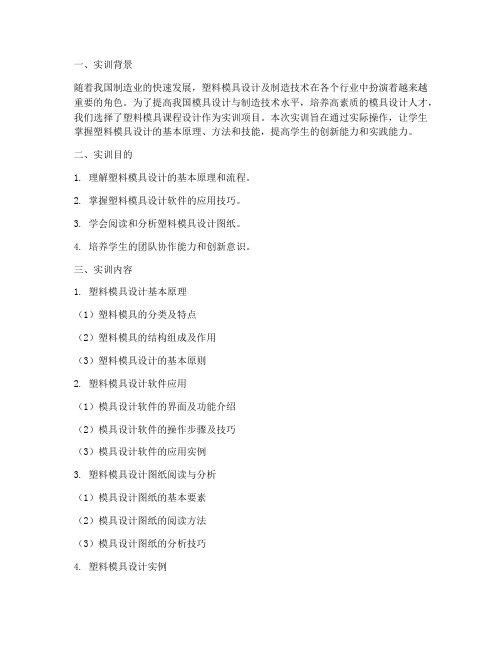
随着我国制造业的快速发展,塑料模具设计及制造技术在各个行业中扮演着越来越重要的角色。
为了提高我国模具设计与制造技术水平,培养高素质的模具设计人才,我们选择了塑料模具课程设计作为实训项目。
本次实训旨在通过实际操作,让学生掌握塑料模具设计的基本原理、方法和技能,提高学生的创新能力和实践能力。
二、实训目的1. 理解塑料模具设计的基本原理和流程。
2. 掌握塑料模具设计软件的应用技巧。
3. 学会阅读和分析塑料模具设计图纸。
4. 培养学生的团队协作能力和创新意识。
三、实训内容1. 塑料模具设计基本原理(1)塑料模具的分类及特点(2)塑料模具的结构组成及作用(3)塑料模具设计的基本原则2. 塑料模具设计软件应用(1)模具设计软件的界面及功能介绍(2)模具设计软件的操作步骤及技巧(3)模具设计软件的应用实例3. 塑料模具设计图纸阅读与分析(1)模具设计图纸的基本要素(2)模具设计图纸的阅读方法(3)模具设计图纸的分析技巧4. 塑料模具设计实例(2)塑料模具设计实例的分析与设计(3)塑料模具设计实例的优化与改进四、实训过程1. 理论学习在实训前,我们通过查阅资料、课堂讲解等方式,对塑料模具设计的基本原理、方法和技能进行了系统学习,为实训打下了坚实的理论基础。
2. 软件操作在实训过程中,我们使用模具设计软件进行实际操作,熟悉软件界面、功能及操作步骤。
通过不断练习,掌握了模具设计软件的应用技巧。
3. 图纸阅读与分析我们阅读了多个塑料模具设计图纸,学会了如何分析图纸中的要素,了解模具的结构、尺寸、公差等信息。
4. 设计实例我们选择了多个塑料模具设计实例,通过分析、设计、优化和改进,提高了自己的实践能力。
五、实训成果1. 完成了多个塑料模具设计实例,掌握了塑料模具设计的基本原理和技能。
2. 学会了使用模具设计软件进行实际操作,提高了自己的计算机应用能力。
3. 提升了阅读和分析模具设计图纸的能力,为今后的工作打下了基础。
4. 培养了团队协作能力和创新意识,为今后的职业发展奠定了基础。
注塑模模具设计实训报告

一、实训目的通过本次实训,我了解了注塑模具设计的基本原理和流程,掌握了模具设计软件的使用方法,提高了自己的动手实践能力,为今后从事注塑模具设计工作打下了坚实的基础。
二、实训内容1. 塑件设计分析(1)塑件模型建立:利用CAD软件进行塑件的三维建模,确保塑件的形状、尺寸、精度等符合设计要求。
(2)塑件参数设计:分析塑件的材料、收缩率、壁厚、拔模斜度等参数,为模具设计提供依据。
(3)塑件表面质量要求:根据塑件的用途,确定表面粗糙度、光泽度等质量要求。
2. 注塑机和模架选择(1)注塑机选择:根据塑件的材料、重量、尺寸等因素,选择合适的注塑机型号。
(2)模架选择:根据塑件的尺寸、形状、生产批量等因素,选择合适的模架结构。
3. 模具结构设计(1)分型面设计:确定分型面位置,使塑件在模具中能够顺利脱模。
(2)型腔布局:根据塑件的形状、尺寸、生产批量等因素,确定型腔数量和排列方式。
(3)浇注系统设计:包括主流道、分流道、浇口等的设计,确保熔体在模具中均匀流动。
(4)冷却系统设计:根据塑件的材料、形状、尺寸等因素,设计冷却水道,保证塑件冷却均匀。
(5)脱模机构设计:包括顶杆、推杆等的设计,确保塑件在模具中顺利脱模。
(6)导向机构设计:确保模具各部件在注塑过程中的相对位置准确。
4. 模具零件设计(1)模具零件的尺寸计算:根据塑件的尺寸、精度要求,计算模具零件的尺寸。
(2)模具零件的材料选择:根据模具零件的受力情况、工作环境等因素,选择合适的材料。
(3)模具零件的加工方法:根据模具零件的材料、形状、尺寸等因素,确定加工方法。
三、实训成果1. 完成了一款注塑模具的设计,包括塑件设计、模具结构设计、模具零件设计等。
2. 掌握了模具设计软件的使用方法,提高了自己的动手实践能力。
3. 加深了对注塑模具设计原理和流程的理解。
四、实训心得1. 注塑模具设计是一个复杂的过程,需要综合考虑塑件、材料、设备、工艺等多个因素。
2. 模具设计软件在模具设计中起到了重要的作用,熟练掌握软件的使用方法可以提高设计效率。
塑料模具设计实训报告

一、实训背景随着我国制造业的快速发展,塑料模具在工业生产中的应用越来越广泛。
为了提高我国塑料模具设计水平,培养具备实际操作能力的专业人才,本实训课程旨在通过实际操作,使学生掌握塑料模具设计的基本原理、方法和技巧,提高学生的实践能力。
二、实训目的1. 熟悉塑料模具设计的基本流程和工艺;2. 掌握塑料模具设计软件的使用方法;3. 学会塑料模具结构设计、零件加工、装配和调试;4. 培养学生的团队协作精神和创新意识。
三、实训内容1. 塑料模具设计基本原理(1)塑料模具的定义、分类及特点(2)塑料模具设计的基本流程(3)塑料模具设计的基本要求2. 塑料模具设计软件(1)Pro/E软件的使用(2)UG软件的使用3. 塑料模具结构设计(1)模具结构组成及作用(2)模具零件设计(3)模具装配图绘制4. 塑料模具零件加工(1)模具零件的加工方法(2)模具零件的加工工艺5. 塑料模具装配与调试(1)模具装配方法(2)模具调试方法四、实训过程1. 塑料模具设计基本原理学习(1)通过课堂讲解、实验演示等方式,使学生掌握塑料模具设计的基本原理。
(2)布置课后作业,要求学生独立完成塑料模具设计的基本流程。
2. 塑料模具设计软件学习(1)教师讲解Pro/E和UG软件的基本操作,学生跟随操作。
(2)布置课后作业,要求学生独立完成塑料模具结构设计。
3. 塑料模具结构设计(1)学生分组,每组完成一个塑料模具结构设计。
(2)教师指导,解决学生在设计过程中遇到的问题。
4. 塑料模具零件加工(1)教师讲解模具零件的加工方法,学生跟随操作。
(2)布置课后作业,要求学生独立完成模具零件加工。
5. 塑料模具装配与调试(1)学生分组,每组完成一个塑料模具的装配与调试。
(2)教师指导,解决学生在装配与调试过程中遇到的问题。
五、实训成果1. 学生掌握了塑料模具设计的基本原理、方法和技巧。
2. 学生熟练掌握了Pro/E和UG软件的使用。
3. 学生完成了塑料模具结构设计、零件加工、装配和调试。
塑料模具设计实例

塑料模具设计实例塑料模具是指用于生产塑料制品的模具,它是由模具设计师根据产品要求和工艺流程进行设计和制造的。
以下是一个关于塑料模具设计的实例。
该塑料模具设计实例是用于生产手机外壳的模具。
手机外壳采用塑料注塑工艺进行生产,因此需要设计一个适用于塑料注塑的模具,以实现手机外壳的批量生产。
首先,模具设计师需要了解手机外壳的尺寸要求和工艺流程。
根据客户提供的手机外壳样品和CAD图纸,模具设计师对手机外壳的尺寸、形状和结构进行分析和测量。
然后,根据手机外壳的要求,设计师开始制定模具的设计方案。
在设计模具时,模具设计师首先需要确定手机外壳的形状和结构,包括外壳的外观、边缘、按键等。
然后,根据这些要求,设计师开始绘制模具的三维模型。
在绘制三维模型时,设计师需要考虑到如何使模具具有良好的冷却效果和顺畅的塑料流动效果。
在设计模具的过程中,设计师需要考虑到模具的分型面、冷却系统、定位销、导向柱等重要部分。
分型面的设计要使得塑料制品能够顺利脱模,避免出现卡模现象。
冷却系统的设计需要保证模具能够迅速冷却,提高生产效率。
定位销和导向柱的设计要确保模具在生产过程中能够保持稳定的位置,避免出现偏移和变形。
模具设计师还需要考虑到模具的制造工艺和材料选择。
在制造工艺方面,设计师需要考虑到模具的加工工艺、加工设备和加工顺序。
材料选择方面,设计师需要选择适合模具制造的材料,如钢材或铝材,以保证模具具有足够的强度和耐磨性。
最后,模具设计师需要对设计方案进行评估和优化。
评估和优化包括模具结构的优化、模具制造工艺的优化和模具性能的优化。
通过评估和优化,模具设计师可以确保设计方案的合理性和可行性。
总之,塑料模具设计是一个综合性的工程,需要模具设计师具备丰富的经验和专业知识。
通过合理的设计和优化,可以提高模具的生产效率和产品质量,从而满足客户的需求。
- 1、下载文档前请自行甄别文档内容的完整性,平台不提供额外的编辑、内容补充、找答案等附加服务。
- 2、"仅部分预览"的文档,不可在线预览部分如存在完整性等问题,可反馈申请退款(可完整预览的文档不适用该条件!)。
- 3、如文档侵犯您的权益,请联系客服反馈,我们会尽快为您处理(人工客服工作时间:9:00-18:30)。
Inventor Mold塑料模具设计实战
默认分类2010-05-28 00:36:30 阅读16 评论0 字号:大中小订阅
本文旨在与读者分享Inventor Mold的设计思路。
其特点是在一款三维设计软件中完成所有的设计,并且集成模流分享软件Mold Flow
功能,满足塑料模具设计的整体解决方案。
随着塑料模具行业的快速发展、塑料模具制造精度的提高以及模具行业的激烈竞争,使得消费者对塑料模具设计的要求越来越高,必须同时考虑设计精度和设计周期的影响。
目前,大部分塑料模具设计都是在三维软件中进行分模设计,在二维中进行排位的设计。
这种方式,由于三维软件和二维软件分别独立,缺乏关联,存在着一些弊病,很容易出现设计的错误。
另外三维与二维的“拼凑式”设计,也
严重影响了塑料模具设计的精度。
下面以一个实例,来介绍Inventor Mold的设计流程。
塑料产品如图1所示。
该产品的特点是需要修补孔,要做抽芯机构。
1.新建模具设计
打开Inventor Mold后,新建一塑料模具设计,进入到Inventor Mold塑料模具设计的环境下,在未导入塑料产品之前,其中很多的
指令都处于不可用状态,如图2所示。
2.导入塑胶产品
执行“塑料零件”指令,选择塑件产品,将塑件产品导入到塑料模具设计环境中,如图3所示。
此时可看到菜单都已经被激活,如图4
所示。
3.调整出模方向
此步骤是用来调整塑件产品的出模方向,当塑件导入模具设计环境后,会有一个默认的方向,但是默认的方向有可能不是正确的模具出模方向,所以必须进行调整。
如图5所示,这里调整出模方向非常重要,因为Inventor Mold自动补孔(自动修补破孔)方式会根据出
模的方向来定。
4.选择材料
材料库是Inventor Mold的一大特色,Inventor Mold基本上含有模具行业常用的材料,共有七千多种塑料材料,且每种材料都有其属性,包括厂商以及牌号,当然还包括收缩率。
之所以Inventor Mold含有如此丰富的材料库,那是因为Inventor Mold中含有Mold Flow 的功能,在进行模流分析时,必须先定义具体的材料,才可以进行工艺的设定和模流的分析。
需要特别注意的是,如果没有选定材料,后面的模流分析将不能进行,收缩率也将没有参考值,如图6所示。
5.设置收缩率
此命令是用来设置塑料材料的收缩率,当上一步骤中选择好材料后,便有了一个范围值,也可输入具体的数值,如图7 所示。
6.定义毛坯工件
此步骤是用来定义毛坯的大小,即模芯的大小。
它的原理是根据塑件产品的最大轮廓尺寸加上塑件最大轮廓到毛坯边缘的距离值,自动计算得到一个尺寸,因此不用担心计算的尺寸会小于塑件产品的最大轮廓值,如图8所示。
7.补孔
修补产品上的破孔,这是分模设计必须的、且工作量较大的工作。
目前大部分的软件,都是通过创建曲面的方式去修补产品上的破孔。
所以,只要软件能提供更多方便的创建曲面方法,则能轻松完成补孔的操作。
这也是目前类似于Pro/ENGINEER和NX等软件的强
项。
通常创建曲面方式的工具都必须一个曲面接着一个曲面去做,如果软件能够自动去创建曲面,这将大大提高分模的效率。
在Inventor Mold中,一般都可以使用软件的自动补孔功能去补塑件产品的孔,对于在自动补孔操作中未能完成的,则可以通过其他方法进行。
所以,补孔这一工作在Inventor Mold中可以分成两种方式来进行。
以下是实际操作情况。
(1)自动补孔执行自动补孔命令后,软件会去识别塑件产品的孔并进行修补,但是并不是所有的孔都能正确识别和修补,需要后续手
动更改、添加,如图9所示。
(2)添加需要修补的孔软件未识别的孔,需要在对话框中单击添加,选择塑件产品破孔的边界,依次选择边界即可,如图10所示。
经过以上步骤,若还没有将塑件产品的孔完全修补好,则必须通过Inventor软件的创建曲面工具来修补了,操作就类似于其他软件修补曲
面的方法。
8.创建分型面
当塑件产品的破孔修补好后,接下来就是要创建出整个分型面。
通常做法,先找到塑件产品的分型线,然后根据分型线去创建曲面,
最后合并成一张完整的曲面。
在Inventor Mold的分型设计中,有个“创建分型面”的工具,只要创建了工件(工件是软件判定分型面大小的依据),则能自动产生分型面,如图11所示。
虽然自动创建分型面的功能不错,但是目前Inventor Mold并不能非常完美地创建分型面,必须进行一些更改,如删除、添加某边。
而且也可能出现自动创建分型面不能完成的时候,此时还必须通过创建曲面的方法去创建分型面。
9.分型面检测
当分型面创建好后,最值得期待的就是将前后模分开了。
但是在设计中,经常出现分不开的情况,也就是说分型面创建有问题。
此时需要去查找分型面的错误。
在Inventor Mold里提供了分型诊断的工具,可以检查其错误。
如图12所示,软件能模拟分型面的拉开状
态。
10.型芯/型腔
分型面创建好并且检测无误后,便可将毛坯进行分割。
这里仅仅是一个分割的执行,软件可以自动判断分型面、补孔面,如果补孔不全,或者分型面创建有误,这里的执行将出现失败,结果如图13所示。
11.加载标准模架
如果一直是从事二维软件模架设计的人员,可能看到Inventor Mold设计流程的加载模架,会有些惊讶,这是Inventor Mold中的一
大特色,它里面含有很多丰富的标准件库,如图14所示。
12.创建行位
Inventor Mold的行位设计,可以在分模前进行,也可以在分模后进行。
通过采用单独创建行位的方法,结果如图15所示。
13.放置滑块
创建完镶件后,调用标准的滑块机构,在Inventor Mold中,滑块机构有个标准件库,如图16所示。
将滑块机构与侧镶件连接在一
起就组成了行位的抽芯机构,如图17所示。
14.浇注系统设计
在进行浇注系统设计之前,先进行浇口位置的分析。
应用Inventor Mold集成的Mold Flow功能,分析结果采用云图的显示方式,同时,会有个流阻指示器,可查看塑件各个地方的阻力情况,如图18所示。
根据软件的分析结果,就可以设计浇注系统了,这包括浇注系统的主流道、分流道、冷料井和浇口等。
在Inventor Mold 中提供浇注系统各部分的设计工具,结果如图19所示。
同时,可加载浇注系统的标准件,如浇口套、定位环等,如图20所示。
15.顶出系统设计
放置顶针,通常是在二维排位设计的时候完成,这样不容易发现干涉问题,在Inventor Mold中可以利用其标准件库进行顶出系统的
设计,如图21所示。
16.模流分析
Inventor Mold的另一个特色便是能进行模流分析,它集成的Mold Flow功能,现在能做注塑工艺的分析、填充分析和浇口位置分析。
模具工艺分析,包括模具温度、熔体温度、注射压力、合模时间和注射时间。
填充分析,包括有塑料流体、填充状况、质量预测、气穴
和熔接痕等,如图22所示可以查看填充时间。
17.工程图样设计
当模具设计好后就必须进行工程图的设计了,这个步骤也就是出图工作。
Inventor Mold在进行模具设计的时候,会自动管理各部分组件,因此其出图可达到自动的效果,执行命令后便列出了所有的组件,如图23所示。
接下来就是不断完善图样,如添加尺寸和标准公
差等。
18.小结
Inventor Mold基本上是采取自动的方式来提高设计的效率,从自动补孔、自动分型面、载入三维模架等步骤都可以看出。
为了减少设计的错误,添加了很多标准件以满足在三维软件里完成所有设计,如顶针、滑块、浇口套等,特别是加入了工程师需要分析功能。
从流程上来看,这是符合塑料模具发展方向的。
不过,毕竟它是刚刚起步,也存在一些不足之处,如创建曲面的方式少等。
工程图出来后,在线型方面还是需要达到工程图的效果。
期待有更完善的工具来优化塑料模具设计。