‘壳盖’薄壁铝合金件加工工艺
铝合金薄壁零件加工技术
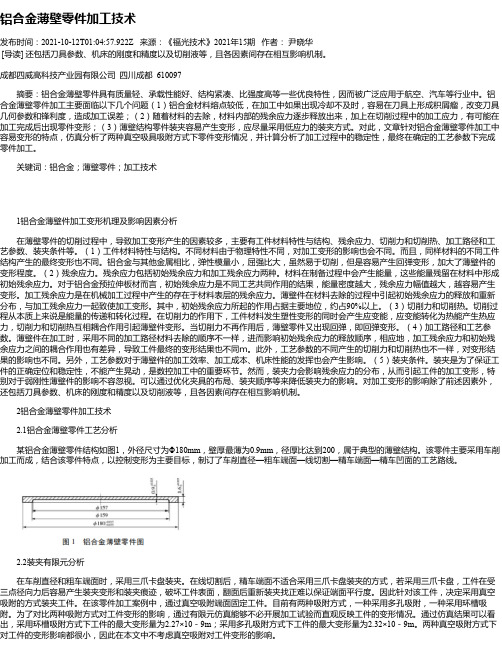
铝合金薄壁零件加工技术发布时间:2021-10-12T01:04:57.922Z 来源:《福光技术》2021年15期作者:尹晓华[导读] 还包括刀具参数、机床的刚度和精度以及切削液等,且各因素间存在相互影响机制。
成都四威高科技产业园有限公司四川成都 610097摘要:铝合金薄壁零件具有质量轻、承载性能好、结构紧凑、比强度高等一些优良特性,因而被广泛应用于航空、汽车等行业中。
铝合金薄壁零件加工主要面临以下几个问题(1)铝合金材料熔点较低,在加工中如果出现冷却不及时,容易在刀具上形成积屑瘤,改变刀具几何参数和锋利度,造成加工误差;(2)随着材料的去除,材料内部的残余应力逐步释放出来,加上在切削过程中的加工应力,有可能在加工完成后出现零件变形;(3)薄壁结构零件装夹容易产生变形,应尽量采用低应力的装夹方式。
对此,文章针对铝合金薄壁零件加工中容易变形的特点,仿真分析了两种真空吸具吸附方式下零件变形情况,并计算分析了加工过程中的稳定性,最终在确定的工艺参数下完成零件加工。
关键词:铝合金;薄壁零件;加工技术1铝合金薄壁件加工变形机理及影响因素分析在薄壁零件的切削过程中,导致加工变形产生的因素较多,主要有工件材料特性与结构、残余应力、切削力和切削热、加工路径和工艺参数、装夹条件等。
(1)工件材料特性与结构。
不同材料由于物理特性不同,对加工变形的影响也会不同。
而且,同样材料的不同工件结构产生的最终变形也不同。
铝合金与其他金属相比,弹性模量小,屈强比大,虽然易于切削,但是容易产生回弹变形,加大了薄壁件的变形程度。
(2)残余应力。
残余应力包括初始残余应力和加工残余应力两种。
材料在制备过程中会产生能量,这些能量残留在材料中形成初始残余应力。
对于铝合金预拉伸板材而言,初始残余应力是不同工艺共同作用的结果,能量密度越大,残余应力幅值越大,越容易产生变形。
加工残余应力是在机械加工过程中产生的存在于材料表层的残余应力。
薄壁件在材料去除的过程中引起初始残余应力的释放和重新分布,与加工残余应力一起致使加工变形。
铝合金薄壁零件的加工工艺及变形控制探讨
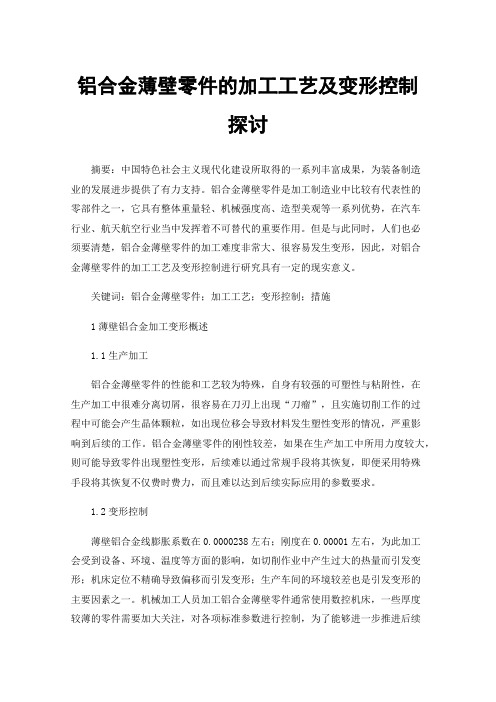
铝合金薄壁零件的加工工艺及变形控制探讨摘要:中国特色社会主义现代化建设所取得的一系列丰富成果,为装备制造业的发展进步提供了有力支持。
铝合金薄壁零件是加工制造业中比较有代表性的零部件之一,它具有整体重量轻、机械强度高、造型美观等一系列优势,在汽车行业、航天航空行业当中发挥着不可替代的重要作用。
但是与此同时,人们也必须要清楚,铝合金薄壁零件的加工难度非常大、很容易发生变形,因此,对铝合金薄壁零件的加工工艺及变形控制进行研究具有一定的现实意义。
关键词:铝合金薄壁零件;加工工艺;变形控制;措施1薄壁铝合金加工变形概述1.1生产加工铝合金薄壁零件的性能和工艺较为特殊,自身有较强的可塑性与粘附性,在生产加工中很难分离切屑,很容易在刀刃上出现“刀瘤”,且实施切削工作的过程中可能会产生晶体颗粒,如出现位移会导致材料发生塑性变形的情况,严重影响到后续的工作。
铝合金薄壁零件的刚性较差,如果在生产加工中所用力度较大,则可能导致零件出现塑性变形,后续难以通过常规手段将其恢复,即便采用特殊手段将其恢复不仅费时费力,而且难以达到后续实际应用的参数要求。
1.2变形控制薄壁铝合金线膨胀系数在0.0000238左右;刚度在0.00001左右,为此加工会受到设备、环境、温度等方面的影响,如切削作业中产生过大的热量而引发变形;机床定位不精确导致偏移而引发变形;生产车间的环境较差也是引发变形的主要因素之一。
机械加工人员加工铝合金薄壁零件通常使用数控机床,一些厚度较薄的零件需要加大关注,对各项标准参数进行控制,为了能够进一步推进后续行业的持续健康发展,需要着重考虑到设备、环境、温度等与金属材料的差异化特点,保证参数精确度符合预期的生产要求,从而有效解决加工伴有的质量问题。
2铝合金薄壁零件的加工工艺随着科技发展,中国的零部件加工技术越来越成熟,对于薄壁零部件的加工能力也在不断提升,铝合金薄壁零件是其中比较有代表性的零部件之一。
铝合金材质决定了该零部件具有比重指数小、比强度指数大的特点,而薄壁结构则导致该零部件的刚性不佳、容易变形,这给铝合金薄壁零件加工带来了一定挑战。
薄壁铝合金件的加工工艺

2019年 第11期冷加工57CUTTING TOOLS刀 具薄壁铝合金件的加工工艺■■宜宾普什联动科技有限公司 (四川宜宾 644000) 何清贤 彭永辉摘要:在机械加工工艺设计过程中碰到薄壁零件一直是让人头疼的问题,特别是铝合金材料,无法使用传统的夹具或磁性吸附方式固定零件来完成零件的成形加工。
本文通过对某典型薄壁框形零件结构特点的分析,制定了该零件的加工工艺路线,并对专用工装进行了探讨。
我公司是一家综合型机械制造企业,笔者所在的机加事业部专门对外承接机加工订单,车间内拥有各型数控加工中心、立加、卧加及数控镗铣床。
最近公司开发的新产品中,需要加工一批图1所示铝合金薄壁零件压板。
图1 压板零件1.工艺分析该压板件为框形零件,长650m m ,宽480m m ,总厚度14 -0-0.018mm ,最薄处厚度仅5mm ,属于薄壁零件。
内腔沉台及大面上各有一圆孔,长边靠近中线位置有4处半圆形缺口,如图2所示。
该压板设计为铝合金材质, 整体框形。
同时零件与关键重要部件镜片直接接触,表面粗糙度要求较高,对零件的加工工艺提出非常高的要求,不允许表面有任何的划痕、印记等。
关键控制点是厚度尺寸公差0.018mm 和平面度≤0.12mm 。
该压板是薄壁框形零件,考虑到批量较小及不适合开模等问题,最终确定选用厚度为20m m 的铝板直接下料。
该压板零件在加工过程中材料去除率达90%以上,所产生的加工应力会引起非常大的形变。
为保证成品的平面度≤0.12mm 和厚度14 -0-0.018mm ,工艺路线的制定必须考虑到零件的加工变形,需在粗加工后进行人工时效,去除加工应力。
由于铝合金不能采用磨的方式进行加工,为达到图样需要的表面粗糙度值R a =1.6μm 、平面度0.12mm 及厚度公差0.018mm ,可以考虑选用小直径铝合金专用刀具,采用小的吃刀量分多刀进行精铣,同时半精铣留余量,先检测平面度及厚度合格再进行精铣到位。
“壳盖”薄壁铝合金件加工工艺
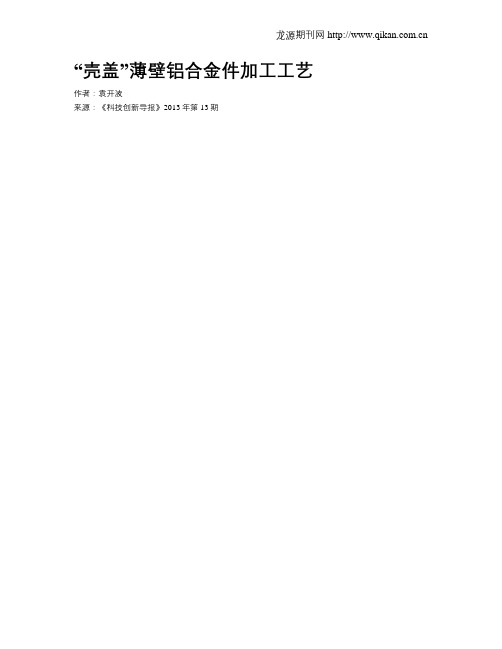
“壳盖”薄壁铝合金件加工工艺作者:袁开波来源:《科技创新导报》2013年第13期摘要:零件的主要特点就是壁薄,由于是铝合金件,其强度差,加工时容易变形,要高效率加工合格的零件,加工过程中编制好工艺路线,做好准确的装夹与定位,就至关重要。
关键词:“壳盖”零件铝合金工艺中图分类号:TG506 文献标识码:A 文章编号:1674-098X(2013)05(a)-0032-01“壳盖”零件是一个薄壁的铝合金零件,其形状及尺寸如图1所示。
1 工艺分析考虑到此零件的内、外形均为圆环形状,其主要的加工方法为数车工序完成,数车工序为分别加工内、外形2个步骤。
这里就要考虑加工完第一工序后,在进行第二工序加工时的装夹与定位问题。
既要能准确装夹与定位,又要使第二工序的加工操作方便。
在经过多次的工艺路线分析及相配合的夹具结构设计之后,确定了先加工内形面,并在其端面上制出装夹定位的位置,然后进行外形面的加工。
2 工艺路线在加工零件的内形面之后,“壳盖”需要安装在一种辅助夹具上,才能进行第二工序的加工,如图2所示。
2.1 第一工序的加工“壳盖”在第一工序中要完成如图2(a)所示的加工内容,注意保持各个孔与M64×0.75螺孔的同轴度。
由于“壳盖”壁薄,偏心更易使“壳盖”产生变形。
2.2 第二工序的加工如图2(b)所示,型腔口部的M64×0.75螺纹段位为装夹部分,用M64X0.75螺纹与辅助夹具进行定位与连接。
其夹具的设计,如图2(b)所示。
从图中可以看出,辅助夹具的设计,其型面尺寸与零件的内形面是一致的,零件扣在夹具上,并通过M64X0.75螺纹拧紧,以保证零件内形面与夹具相贴合,这样,在加工外形面时,零件不会产生变形。
3 安装在辅助夹具上“壳盖”切削时加紧状况的分析零件在装夹后,车刀切削时,零件的状态是否会松动,可通过图3做一个装夹及切削的状况分析。
从图3(a)中,显示零件在装夹到夹具上时,是顺时针方向旋紧。
铝合金薄壁零件的机械加工工艺分析

铝合金薄壁零件的机械加工工艺分析[摘要]铝合金薄壁零件应用领域较为广泛,但其自身性能较为特殊,在加工过程中需要注意工艺与方法。
基于此,本文分析了铝合金薄壁零件性能与特点,并提出提高铝合金薄壁零件机械加工质量的有效对策。
[关键词]铝合金薄壁零件;机械加工;工艺特点与其他零件相比,铝合金薄壁零件结构复杂,并且在尺寸方面要求较高,因此,在加工过程中难度较大。
为了加工出符合工艺标准的机械设备零件,需要不断提高相关加工人员的工作能力与操作水平。
一、铝合金薄壁零件的性能及工艺特点第一,铝合金材料本身具有较强的可塑性与韧性,并且其粘附性较大,容易出现切屑粘连的情况,加工人员在进行切削操作时,切屑容易粘附在刀刃上,对切削刀日后使用会造成影响。
第二,铝合金薄壁零件刚性较弱,在进行加工过程中,需要把握好对铝合金薄壁力的大小,如果加工人员用力过大,极易导致铝合金薄壁零件形状发生变化,从而达不到质量要求。
第三,线膨胀系数大,通常情况下,铝的线膨胀系数要远超于钢的线膨胀系数,因此加工人员在进行切削作业时会使温度上升,造成零件变形。
第四,铝合金材料硬度较差,在进行加工时,加工面容易出现划伤的现象。
因此,在进行铝合金薄壁零件加工时,要达到设备对零件表面粗糙度的要求,加工人员需要熟练掌握加工设备,保证操作水平。
第五,通常情况下,加工人员会应用数控机床对铝合金薄壁零件进行加工操作,但是由于有些零件厚度较薄,在操作时,要注意切削作业会产生切削力,加之薄板本身存在弹性,因此容易出现切削面震动的现象,零件的厚度尺寸是控制不了的,并且表面的粗糙程度也会有所增加。
二、薄壁零件机械加工过程及主要工艺(一)选择合适的切削刀在进行加工时,要选择合适的刀具,充分考虑刀具的形状、切削用量等特点,规划好加工任务,注意加工过程中的镜像切削力,对薄壁零件的变形情况加以重视。
切削刀具的前角要综合刀具的形状及切削变形等特点决定,如果切削前角过大,则在切削过程中摩擦力会变小,可见,在确定刀具前角大小时需要综合各项影响因素。
薄壁壳体类铝件的数控加工

第1期薄壁壳体类铝件型腔复杂,内部和四侧均需加工,其四侧和底面最薄处为1mm左右的薄壁,所用材料为锻铝,受力后易变形。
加工这种复杂薄壁类零件,工艺上首先要解决的是装夹引起的加工干涉及变形问题。
采用真空吸盘吸住工件的底部进行加工,可有效解决上述问题。
具体方法是将工件放在吸盘上,并用配套的特种密封条将其底部与外界隔开,接着将底部抽真空,当压力表显示真空度达到指示值时,工件相当于加有一定的压力。
为防止加工内腔时外壁的变形,可在工件的四侧各加上1~2个支撑。
另外,还要注意走刀路径的优化选择,使走刀路径尽量短,避免加工时切削力引起的薄壁变形。
本文以手机测试板外壳为例讨论该类零件的快速制造方法。
1加工工艺手机测试板外壳的数学模型见图1和图2。
加工工序如表1所示。
2刀路生成2.1刀路生成流程首先用Mastercam软件对薄壁壳体类铝件进行数学建模。
数学建模完成后,就可用Mastercam软件对其进行刀路生成了。
Mastercam生成刀路的一般过程为:首先打开需要加工的零件图形,检查零件表面的光顺性。
如果零件有通孔,就必须用实体或曲面进行补孔,防止加工过程中出现“掉刀”现象(刀具沿孔径突然往下沉,可能造成断刀或铣坏工作台);然后,创建刀具路径(Toolpath)。
具体流程为:(1)选择加工方法:轮廓加工(Contour)、挖槽加工(Pocket)和钻孔类点位加工(Drill)等。
(2)选择加工部位。
(3)设置相关工艺参数:切削参数、刀具参数、薄壁壳体类铝件的数控加工施勇成(南通纺织职业技术学院机电系,江苏南通226007)摘要:从图样分析、加工工艺、数学建模、工艺参数设置、刀路生成、加工程序的模拟仿真以及后置处理等几方面详细分析薄壁壳体类铝件数控加工的实例,提出采用真空吸盘装夹零件的新工艺。
为解决薄壁壳体类铝件难装夹及加工时易变形的问题,提供了一套较为完整的数控加工方法。
关键词:薄壁;壳体;数控加工;真空吸盘;Mastercam中图分类号:TG659文献标识码:A文章编号:1008-5327(2006)01-0073-03收稿日期:2005-08-30作者简介:施勇成(1965-),男,江苏南通人,高级工程师,研究方向:数控技术,CAD/CAM.Vol.20No.1Mar.2006第20卷第1期2006年3月!!!!!!!!!!!!!!!!!!!!!!!!!!!!!!!!!!!!!!!!!!!!!!!!!!!!!!!!!!南通职业大学学报JOURNALOFNANTONGVOCATIONALCOLLEGE732006南通职业大学学报年序号工序内容操作名刀具名1毛坯上料,上、下表面铣平盘铣刀2校正后,用真空吸盘吸住底面3粗铣外轮廓,轮廓铣,留余量0.2mmContour-1Φ18端面铣4精铣外轮廓,轮廓铣,留余量0mmContour-2Φ10端面铣5粗铣壳体型腔,型腔铣,留余量2mmPocket-1Φ18端面铣6半精铣壳体型腔,型腔铣,留余量0.8mmPocket-2Φ8球头刀7铣削未铣到的沟槽,使得精加工时各处的余量相同,减少刀具振动,两次清根,清根铣,留余量0.8mmFlowcut-singleΦ8球头刀R3平底刀8精铣壳体型腔,型腔铣,留余量0mmPocket-3Φ6球头刀9铣清未铣到的沟槽,三次清根,清根铣,留余量0mmFlowcut-singleΦ6球头刀Φ4球头刀Φ2球头刀10中心钻钻孔,孔深3mmDrill-1Φ3中心钻11钻孔,孔深18mmDrill-2Φ6.8钻头12攻Φ8螺纹孔,深12mmTape-1Φ8丝锥走刀路径、加工余量、进退刀方式以及加工精度等。
典型薄壁铝件的数控加工工艺

文索引号:119
图15 数控编程的一次合格率时间统计
机床仿真时间
图17 查看机床仿真时间
五、总结
当今的市场经济环境下,安全是企业生存的基础,质量
是企业的生命,工作效率是企业发展的源泉,将仿真技术与工
艺、生产管理全方位结合,形成系统化的仿真应用规范,提升
了工厂的整体实力。
希望通过本文的介绍,能够为大家拓展视
野,拓宽思路,使数控加工仿真能更好的为技术服务,为生产
管理服务。
图16 数控机床干涉碰撞柏拉图
CAD/CAM与制造业信息化·2010年第5期
文索引号:120
d8r4-5.nc
加工简图:
工件名称:薄壁铝件X
机 床: CNC Y
文件地址:2015Z=0
审核xu会签
的环节之一,其在实现设计加工自动化、提高加工精度和
加工质量、缩短产品研制周期等方面发挥着重要作用。
采用
CIMATRON、Pro/ENGINEER或NX等先进软件进行三维建模,然后
根据零件的结构特点,生成零件的工程图、加工工艺图。
根据
图1 薄壁件图。
铝合金薄壁件的点焊及表面处理工艺研究

铝合金薄壁件的点焊及表面处理工艺研究随着铝合金薄壁件在汽车、航空、军事等行业的应用越来越普及,制作薄壁件的点焊及表面处理工艺的研究也受到了广泛关注。
首先,铝合金薄壁件的点焊工艺涉及到两个主要部分:热和电。
在热方面,如果要进行制作,需要使用高焊接速度的电焊设备,以及夹具、滑块来定位加工件,并针对焊接所用的钎料类型、参数选择电焊机的功率、输出电流等。
在电方面,电焊必须使用稳定性好、反应时间短、抗干扰能力强的电源,以保证薄壁件的焊接质量和稳定性。
接下来,就是薄壁件的表面处理工艺。
通常情况下,表面处理往往是采用电镀法来处理表面,一般情况下,电镀可分为软镀层和硬镀层。
对于铝合金薄壁件来说,软镀层比较常用,可以提升产品的耐腐蚀性和抗蚀性、抗氧化性,并且具有良好的美观性。
此外,除了采用电镀外,还可以采用化学处理的方法来处理表面,化学处理主要是用化学腐蚀剂将材料表面的氧化膜等物质腐蚀掉,从而提高表面的质量和光洁度。
总之,铝合金薄壁件的点焊和表面处理工艺都是非常精密的,需要仔细考虑多种因素,才能保证最终产品的质量和性能。
因此,在实际应用时,应根据产品的实际需要综合考虑,采用最合适的方法。
- 1 -。
铝合金加工工艺流程
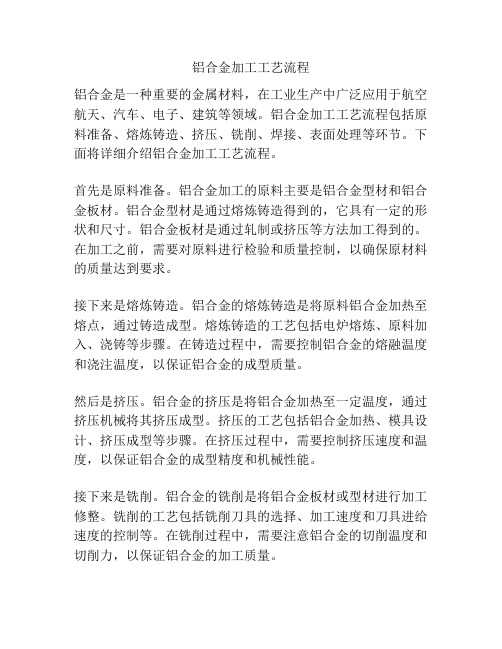
铝合金加工工艺流程铝合金是一种重要的金属材料,在工业生产中广泛应用于航空航天、汽车、电子、建筑等领域。
铝合金加工工艺流程包括原料准备、熔炼铸造、挤压、铣削、焊接、表面处理等环节。
下面将详细介绍铝合金加工工艺流程。
首先是原料准备。
铝合金加工的原料主要是铝合金型材和铝合金板材。
铝合金型材是通过熔炼铸造得到的,它具有一定的形状和尺寸。
铝合金板材是通过轧制或挤压等方法加工得到的。
在加工之前,需要对原料进行检验和质量控制,以确保原材料的质量达到要求。
接下来是熔炼铸造。
铝合金的熔炼铸造是将原料铝合金加热至熔点,通过铸造成型。
熔炼铸造的工艺包括电炉熔炼、原料加入、浇铸等步骤。
在铸造过程中,需要控制铝合金的熔融温度和浇注温度,以保证铝合金的成型质量。
然后是挤压。
铝合金的挤压是将铝合金加热至一定温度,通过挤压机械将其挤压成型。
挤压的工艺包括铝合金加热、模具设计、挤压成型等步骤。
在挤压过程中,需要控制挤压速度和温度,以保证铝合金的成型精度和机械性能。
接下来是铣削。
铝合金的铣削是将铝合金板材或型材进行加工修整。
铣削的工艺包括铣削刀具的选择、加工速度和刀具进给速度的控制等。
在铣削过程中,需要注意铝合金的切削温度和切削力,以保证铝合金的加工质量。
然后是焊接。
铝合金的焊接是将两个或多个铝合金部件通过热熔或压力焊接在一起。
焊接的工艺包括焊接方法的选择、焊接电流和焊接速度的控制等。
在焊接过程中,需要控制焊接温度和焊接压力,以保证焊接接头的强度和密封性。
最后是表面处理。
铝合金的表面处理是为了改善铝合金的耐腐蚀性和装饰性。
表面处理的方法有阳极氧化、电泳涂装、喷涂等。
在表面处理过程中,需要控制处理液的温度和浓度,以保证表面处理的效果。
综上所述,铝合金加工工艺流程包括原料准备、熔炼铸造、挤压、铣削、焊接、表面处理等环节。
这些环节相互配合,共同完成了铝合金的制造过程。
合理控制加工工艺流程,可以保证铝合金产品的质量和性能,提高生产效率。
铝合金加工将在未来的发展中得到更广泛的应用。
薄壁铝合金封头冲压成形的加工工艺

薄壁铝合金封头冲压成形的加工工艺铝合金封头是石油化工,原子能,食品制药等诸多行业压力容器设备中不可缺少的重要部件,是压力容器上的端盖是压力容器的一个主要承压部件。
铝合金封头的质量直接关系到压力容器的长期可靠安全运行。
文章主要对客户来料加工制作的薄壁铝合金封头,浅谈薄壁铝合金封头的冲压加工工艺过程。
标签:铝合金封头;冲压;垫板现我公司按客户要求来料制作铝合金封头EHA2000mm、数量2个、材质5052、投料板厚5mm、成形后最小板厚4.3mm、直边高度25mm、外周长6315(-3~+6)mm、成形后消应力退火、制造标准GB/T25198-2010[2]。
1 铝合金封头的加工方法冲压:适应大批量生产,需制作相应模具,但成形质量好,材料减薄少,实际成形形状和理论要求形状误差较少,尤其适用封头容器内部需安装其他部件的加工工艺。
2 铝合金封头的加工设备(1)加热设备:电炉,铝合金封头的加热多采用电炉,加热电炉要求保温性能良好,升温降温可控,炉膛内气氛呈弱氧化性,炉膛内各部位温度均匀,而且电炉应定期校核,保证炉膛内各部位实测温差在设计范围内,加热电炉应配置自动控温测温装置和温度记录仪。
(2)压机:双向油压机,按客户要求铝合金封头EHA2000*5(4.3)=2 H=25材质5052由于封头直径大,壁薄,成形时极易产生鼓包和减薄,为保证封头形状和成形后封头最小板厚制作此封头是必须采用垫板,垫板厚度10mm。
如图1所示。
5052材料化学成分和机械性能,如表1所示。
3 加工工艺铝板整形、焊缝打磨、PT[6]+清洗、铝板热处理+垫板抛光、加垫板予冲+成形+清洗、热处理+坡口、研磨坡口+清洗+检验、入库。
根据制作工艺要求此规格铝合金封头要求圆片下料直径2380,通常下料的板材标准宽度只有1500,由于宽度不够,需要下2块料,最后进行拼接(客户焊接)。
在板料焊接后,若铝合金圆片不平整就进行压制,压制时会出现很多不稳定因素,尤其在焊缝角变形位置容易产生材料失稳产生鼓包,所以铝合金圆片有焊接角变形需先把铝合金圆片修整水平。
铝合金薄壁零件的车削工艺要点分析
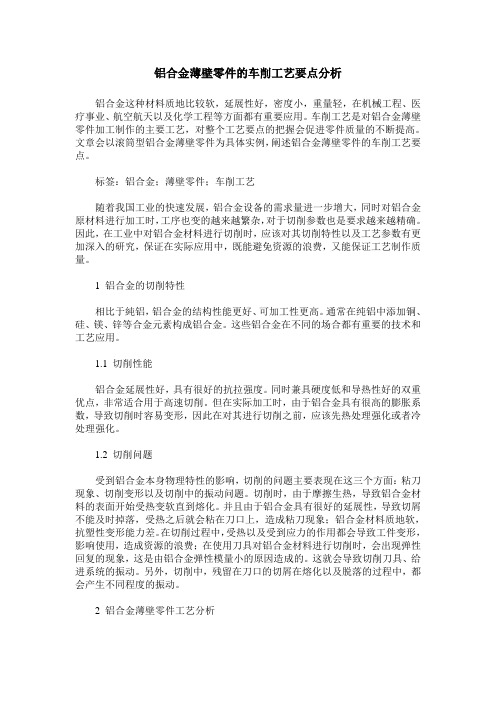
铝合金薄壁零件的车削工艺要点分析铝合金这种材料质地比较软,延展性好,密度小,重量轻,在机械工程、医疗事业、航空航天以及化学工程等方面都有重要应用。
车削工艺是对铝合金薄壁零件加工制作的主要工艺,对整个工艺要点的把握会促进零件质量的不断提高。
文章会以滚筒型铝合金薄壁零件为具体实例,阐述铝合金薄壁零件的车削工艺要点。
标签:铝合金;薄壁零件;车削工艺随着我国工业的快速发展,铝合金设备的需求量进一步增大,同时对铝合金原材料进行加工时,工序也变的越来越繁杂,对于切削参数也是要求越来越精确。
因此,在工业中对铝合金材料进行切削时,应该对其切削特性以及工艺参数有更加深入的研究,保证在实际应用中,既能避免资源的浪费,又能保证工艺制作质量。
1 铝合金的切削特性相比于純铝,铝合金的结构性能更好、可加工性更高。
通常在纯铝中添加铜、硅、镁、锌等合金元素构成铝合金。
这些铝合金在不同的场合都有重要的技术和工艺应用。
1.1 切削性能铝合金延展性好,具有很好的抗拉强度。
同时兼具硬度低和导热性好的双重优点,非常适合用于高速切削。
但在实际加工时,由于铝合金具有很高的膨胀系数,导致切削时容易变形,因此在对其进行切削之前,应该先热处理强化或者冷处理强化。
1.2 切削问题受到铝合金本身物理特性的影响,切削的问题主要表现在这三个方面:粘刀现象、切削变形以及切削中的振动问题。
切削时,由于摩擦生热,导致铝合金材料的表面开始受热变软直到熔化。
并且由于铝合金具有很好的延展性,导致切屑不能及时掉落,受热之后就会粘在刀口上,造成粘刀现象;铝合金材料质地软,抗塑性变形能力差。
在切削过程中,受热以及受到应力的作用都会导致工件变形,影响使用,造成资源的浪费;在使用刀具对铝合金材料进行切削时,会出现弹性回复的现象,这是由铝合金弹性模量小的原因造成的。
这就会导致切削刀具、给进系统的振动。
另外,切削中,残留在刀口的切屑在熔化以及脱落的过程中,都会产生不同程度的振动。
外形复杂的高精度铝合金薄壁件加工工艺

1.序言铝合金薄框结构件具有质轻、抗压和耐蚀等特点,被广泛应用于航空航天零备件[1-3],以达到降低机型整体质量、提高飞行力等目的。
但是由于结构件体型大,表面质量要求高,在机械加工中切削力与夹持力形成材料残余应力,会导致零件尺寸发生变化[4-7],难以满足产品特性要求。
目前现有的加工方法需要采用高端高精密设备,降低切削量进行多次走刀[8-10],加工效率低且生产成本高。
本文以某航空航天用外形复杂的高精度铝合金薄壁件为例,根据零件的尺寸大小,设计带有夹头的毛坯,采用合理的工艺路线,将冷加工、热处理和线切割等工序进行有效安排,避免薄壁件产生应力所导致的尺寸变化,对加工变形量进行控制。
2.加工难点薄壁件材质为2D14高强度硬质合金,整体体积相对较大且壁较薄,尺寸精度、几何公差等要求较高。
零件的铣削加工主要涉及型腔铣与轮廓铣,通过压板胎、组合夹具与机床工作台配合使用将零件进行固定,零件加工后由于压板等夹具夹持所引起的应力释放而导致尺寸超差。
最终加工的薄壁件尺寸发生变化,无法满足航空件高精度的特性要求。
3.工艺安排3.1 整体工艺路线根据零件外形特征及加工难点,对工艺顺序进行合理安排,其中涉及冷加工、电加工及热处理相关知识与设备的运用。
整体工艺安排如图1所示,零件外形结构如图2所示。
图1整体工艺安排图2 零件外形结构根据铝合金薄壁件的外形特征,下料时左右两端各留有夹头30~50mm,夹持固定两端夹头,采用两刃φ16~φ20mm硬质合金刀具对毛坯进行开粗,转速为6000~7000r/min,单边留有3~5mm余量。
粗加工后的零件进行第一次稳定化时效处理,然后采用三刃φ10~φ16mm硬质合金刀具对零件进行半精加工,夹持两端夹头,修正外形及内腔,单边留有0.5~1mm余量。
半精加工后的零件进行第二次稳定化时效处理,之后用压板夹持两端夹头,采用三刃φ6~φ8mm硬质合金刀具对零件进行精加工,零件的外形及内腔尺寸加工成形。
铝合金薄板零件的典型数控加工工艺方案
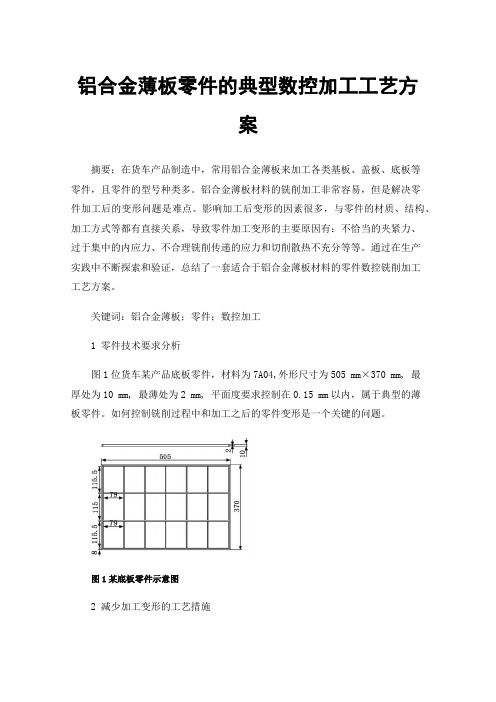
铝合金薄板零件的典型数控加工工艺方案摘要:在货车产品制造中,常用铝合金薄板来加工各类基板、盖板、底板等零件,且零件的型号种类多。
铝合金薄板材料的铣削加工非常容易,但是解决零件加工后的变形问题是难点。
影响加工后变形的因素很多,与零件的材质、结构、加工方式等都有直接关系,导致零件加工变形的主要原因有:不恰当的夹紧力、过于集中的内应力、不合理铣削传递的应力和切削散热不充分等等。
通过在生产实践中不断探索和验证,总结了一套适合于铝合金薄板材料的零件数控铣削加工工艺方案。
关键词:铝合金薄板;零件;数控加工1 零件技术要求分析图1位货车某产品底板零件,材料为7A04,外形尺寸为505 mm×370 mm, 最厚处为10 mm, 最薄处为2 mm, 平面度要求控制在0.15 mm以内,属于典型的薄板零件。
如何控制铣削过程中和加工之后的零件变形是一个关键的问题。
图1某底板零件示意图2 减少加工变形的工艺措施2.1 减少薄板毛坯变形的措施铝合金薄板材料一般是整张规格为1 220 mm×2 440 mm的铝板,下料时绝不能用剪板机裁剪下料,这样会使毛坯边缘产生弯曲变形,产生较大应力,给零件加工变形埋下了隐患。
可以使用激光切割机、线切割机或者大型数控铣床下料,能够避免毛坯产生较大的内应力和变形。
2.2 降低零件铣削内应力的措施铣削加工时为了尽可能减少铣削应力和热量的产生,选择直径Ф6以下铣刀加工,切削转速在8 000 r/min以上,切深在 0.1 mm~0.3 mm, 切宽为刀具直径的50%。
采用高速切削的方式,这样零件在加工中变形量会大幅度地降低。
根据材料切削原理,刀具铣削过程中会产生和传递应力。
对于较大毛坯,由于切削余量大,应先粗铣去掉毛坯多余部分,给零件各尺寸均匀留下2 mm以上余量。
零件粗铣完成后应进行时效去应力处理,可选用自然时效、热处理时效和振动时效三种方法进行时效处理。
采用自然时效时将零件水平放置48 h; 采用热处理时效时将零件加热到100 ℃后保持2 h; 采用振动时效时将零件振动8 h。
浅析铝合金薄壁零件机加工工艺
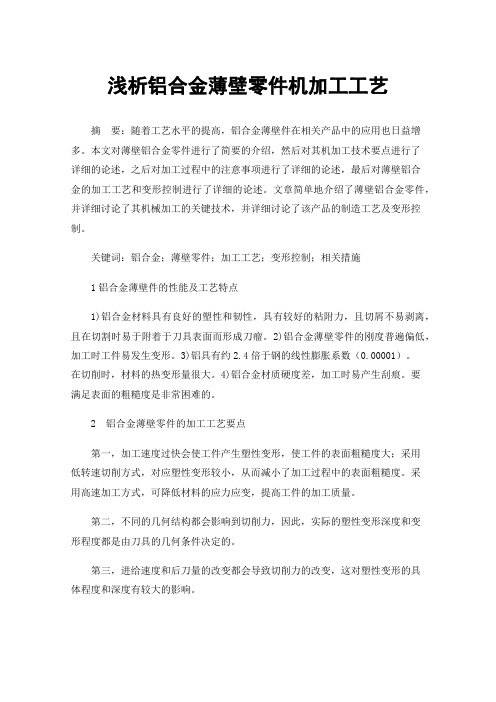
浅析铝合金薄壁零件机加工工艺摘要:随着工艺水平的提高,铝合金薄壁件在相关产品中的应用也日益增多。
本文对薄壁铝合金零件进行了简要的介绍,然后对其机加工技术要点进行了详细的论述,之后对加工过程中的注意事项进行了详细的论述,最后对薄壁铝合金的加工工艺和变形控制进行了详细的论述。
文章简单地介绍了薄壁铝合金零件,并详细讨论了其机械加工的关键技术,并详细讨论了该产品的制造工艺及变形控制。
关键词:铝合金;薄壁零件;加工工艺;变形控制;相关措施1铝合金薄壁件的性能及工艺特点1)铝合金材料具有良好的塑性和韧性,具有较好的粘附力,且切屑不易剥离,且在切割时易于附着于刀具表面而形成刀瘤。
2)铝合金薄壁零件的刚度普遍偏低,加工时工件易发生变形。
3)铝具有约2.4倍于钢的线性膨胀系数(0.00001)。
在切削时,材料的热变形量很大。
4)铝合金材质硬度差,加工时易产生刮痕。
要满足表面的粗糙度是非常困难的。
2 铝合金薄壁零件的加工工艺要点第一,加工速度过快会使工件产生塑性变形,使工件的表面粗糙度大;采用低转速切削方式,对应塑性变形较小,从而减小了加工过程中的表面粗糙度。
采用高速加工方式,可降低材料的应力应变,提高工件的加工质量。
第二,不同的几何结构都会影响到切削力,因此,实际的塑性变形深度和变形程度都是由刀具的几何条件决定的。
第三,进给速度和后刀量的改变都会导致切削力的改变,这对塑性变形的具体程度和深度有较大的影响。
第四,不同的工艺指标和特定的加工方式对薄壁件的切削力有较大的影响,特别是对轴向切割深度的影响,同时,环型和斜插方式也是限制切削力的一个重要因素。
第五,由于夹持力、重力、惯性等因素的影响,加工过程中会发生系统的变形,而切削力的具体位置和加工余量的变化会导致工件的尺寸偏差。
在利用科学的切削量和刀具几何指标来控制切削力变化引起的变形时,必须保证加工余量的标准化配置,使加工变形得到最大程度的控制。
3 铝合金薄壁零件的加工工艺具体操作3.1 关注管理零件铣削变形在铣削铝合金薄壁件时,工件的铣削变形表现为夹持力、切削工件所涉及的切削力、工件刀具切削时的塑性形态、弹性模态、切削温度升高等。
控制薄壁壳体铝合金材料变形车削工艺
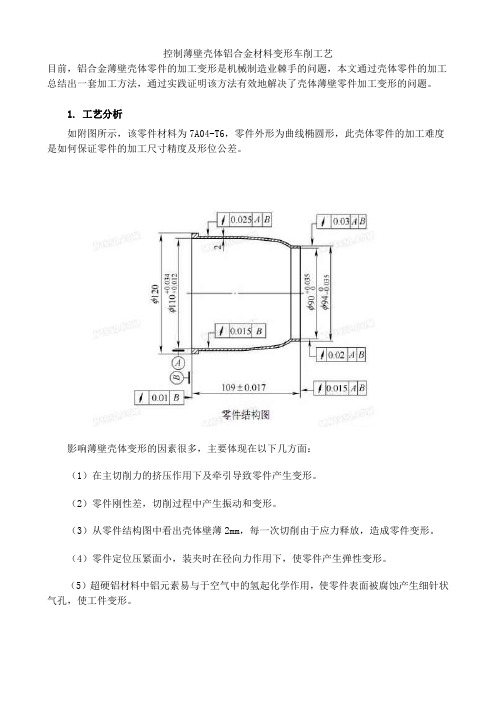
控制薄壁壳体铝合金材料变形车削工艺目前,铝合金薄壁壳体零件的加工变形是机械制造业棘手的问题,本文通过壳体零件的加工总结出一套加工方法,通过实践证明该方法有效地解决了壳体薄壁零件加工变形的问题。
1. 工艺分析如附图所示,该零件材料为7A04-T6,零件外形为曲线椭圆形,此壳体零件的加工难度是如何保证零件的加工尺寸精度及形位公差。
影响薄壁壳体变形的因素很多,主要体现在以下几方面:(1)在主切削力的挤压作用下及牵引导致零件产生变形。
(2)零件刚性差,切削过程中产生振动和变形。
(3)从零件结构图中看出壳体壁薄2mm,每一次切削由于应力释放,造成零件变形。
(4)零件定位压紧面小,装夹时在径向力作用下,使零件产生弹性变形。
(5)超硬铝材料中铝元素易与于空气中的氢起化学作用,使零件表面被腐蚀产生细针状气孔,使工件变形。
2. 解决方案通过以上分析,造成薄壁壳体零件加工变形的主要因素是切削振动、切削力、加工应力及夹紧力,因此通过以下方法有效地减小变形。
(1)合理的选择加工刀具控制变形。
刀钝会使零件主切削抗力加大,零件轴向压力加大,造成零件变形。
刀具切削刃太锋利,虽说有利于切削,但易加速刀具磨损,将零件拉向切削力的反方向,同样使零件变形。
经实践粗加工时:刀具选用R形断屑槽,前角γo=20°~25°,后角αo=6°~10°;主偏角κr=91°~93°;负偏角κ'r=6°~8°;主要是减小刀具摩擦及振动。
精加工时:前角γo=25°~30°,后角ao=10°~12°;主偏角κr=45°~90°,负偏角κ'r=10°~15°;主要是减小径向切削力,避免振动,并且加宽了主切削刃,从而减小了单位长度上的负荷,刀尖角大,散热快。
刃倾角λs=5°~10°,粗加工取小值,精加工取大值,用来弥补法向前角大而引起刀刃强度差的缺陷。
- 1、下载文档前请自行甄别文档内容的完整性,平台不提供额外的编辑、内容补充、找答案等附加服务。
- 2、"仅部分预览"的文档,不可在线预览部分如存在完整性等问题,可反馈申请退款(可完整预览的文档不适用该条件!)。
- 3、如文档侵犯您的权益,请联系客服反馈,我们会尽快为您处理(人工客服工作时间:9:00-18:30)。
'壳盖’薄壁铝合金件加工工艺
壳盖”薄壁铝合金件加工工艺分析中国航空工业集团公司航宇救生装备有限公司(湖北襄阳441002)袁开波
“壳盖”零件是一个薄壁的铝合金零件,其形状及尺寸如图1所示.零件的主
要特点就是壁薄,由于是铝合金件,其强度差,加工时容易变形,要高效率加工合格的零件,加工过程中编制好工艺路线,做好准确的装夹与定位,就至关重要,同时要控制由于切削对零件产生的变形。
图1冗盖
注:未注圆角,凸R1.8mm凹R1mm未注壁厚0.8mm.
、工艺分析
考虑到此零件的内、外形均为圆环形状,其主要的加工方法为数车工序完成,数车工序为分别加工内、外形2个步骤。
这里就要考虑加工完第一工序后,在进行第二工序加工时的装夹与定位问题。
既要能准确装夹与定位,又要使第二工序的加工操作方便。
在经过多次的工艺路线分析及相配合的夹具结构设计之后,确定了先加工内形面,并在其端面上制出装夹定位的位置,然后进行外形面的加工。
、工艺路线
在加工零件的内形面之后,“壳盖”需要安装在一种辅助夹具上,才能进行第
工序的加工,如图
2所示
(a)第一工序图(b)第二工序简图
图2 “壳盖”工艺路线简图
1. 第一工序的加工
“壳盖”在第一工序中要完成如图2(a)所示的加工内容,注意保持各个孔与M64X 0.75螺孔的同轴度。
由于“壳盖”壁薄,偏心更易使“壳盖”产生变形。
2. 第二工序的加工
如图2(b)所示,型腔口部的M64X 0.75螺纹段位为装夹部分,用M64X0.75螺纹与辅助夹具进行定位与连接。
其夹具的设计,如图2(b)所示。
从图中可以看
出,辅助夹具的设计,其型面尺寸与零件的内形面是一致的,零件扣在夹具上,并通过M64X0.75螺纹拧紧,以保证零件内形面与夹具相贴合,这样,在加工外形面时,零件不会产生变形。
3. 安装在辅助夹具上“壳盖”切削时加紧状况的分析
零件在装夹后,车刀切削时,零件的状态是否会松动,可通过图3做一个装夹
及切削的状况分析
从图3(a)中,显示零件在装夹到夹具上时,是顺时针方向旋紧。
从图3(b)中
4
一
可以看出,当主轴旋转,车刀切削零件时。
车刀作用到零件上切削力的方向是与车床的旋转方向相反的方向。
即切削力也为顺时针方向,这就和零件装夹拧紧时力的方向一致。
所以,在车刀切削零件时,零件不会松动,而且会贴的越紧密。
(a) “壳盖”装夹的旋转方向(b)车床主轴的旋转方向图3 “壳盖”切削时的受力分析
通过上述零件加工的分析,若要保证零件加工后内、外形面的同轴度。
就要确
保零件在第二工序加工时,装夹后其轴线与车床旋转轴线保持一致。
从辅助夹具的制作,至V零件的装夹。
可以看出,只要夹具制作完后,就不能松动夹具,此时装夹的零件和车床主轴的中心线才是完全一致的。
也就是说,每加工一批次的零件,在零件加工到此工序时,就要配制一个夹具,这样才能保证零件加工后其内、外形面同轴度的要求。
三、控制加工参数来控制对零件产生的变形
1)合理的选择加工刀具控制变形。
刀钝会使零件主切削抗力加大,零件轴向压力加大,造成零件变形。
刀具切削刃太锋利,虽说有利于切削,但易加速刀具磨损,将零件拉向切削力的反方向,同样使零件变形。
经实践粗加工时:刀具选用R 形断屑槽,前角丫o,20?,25?,后角a o,6?,10?;主偏角K r,91?,93?;负偏角
K 'r,6? ,8?; 主要是减小刀具摩擦及振动。
精加工时:前角丫o,25?,30?,后角
ao,10?,12?;主偏角K r,45?,90?,负偏角K 'r,10?,15?; 主要是减小径向切削
力,避免振动,并且加宽了主切削刃,从而减小了单位长度上的负荷,刀尖角大,散热快。
刃倾角入s,5?,10?,粗加工取小值,精加工取大值,用来弥补法向前角大而引起刀刃强度差的缺陷。
刀具切削刃要求磨的锋利,刀面表面粗糙度值要小,提高零件表面加工质量。
加工时将刀具通过刀架使切削刃沿轴向装夹,通过薄壁壳体的加工此径向切削力最小,工件不易变形。
(2) 合理的选择切削参数控制变形。
粗加工时进给量为0.5,0.3mm/r; 切削深度
0.5,1mm;切削速度100m/mi n。
主要是去除壳体零件大的余量,加快零件的散热性,加速切削应力的释放。
精加工时进给量为:0.05,0.07mm/r ,切削深度0.05,0.075mm,切削速度65m/min。
主要是壳体零件加工时避开了与机床的共振,避免了切削时振动引起的变形。
高速度、小进给量,提高工件的表面加工质量,同时减小径向切削力,减小应力变形。
(3) 增加半精加工工序控制变形。
随着零件加工余量的逐渐去除,零件加工应力逐渐释放,为了保证零件加工尺寸精度及形位公差要求,增加一道半精加工工
序,加工余量控制在0.5,1mm左右,给精加工留余量0.3,0.5mm,主要是将壳体零件曲线椭圆形状在粗加工基础上,进行一次半精加工使加工应力进一步得到释放,为后续精加工打下基础。
(4) 在精加工前安排一道基准精加工,消除工件定位的椭圆度,保证定位尺寸的一致性及精度,使壳体零件与夹具定位间隙最小,达到保证形位公差要求的目的。
四、小结
应用上述的工艺方法,对一个批次为100 件的零件进行加工,其加工过程还很顺利的,零件尺寸及同轴度都能满足图纸要求。
超过100 件的零件,便会因辅助夹具定位面磨损而影响产品的质量,此时最好是要重制辅助夹具。
由此零件的加工可以看出,只要找到零件的加工规律, 再根据被加工零件的特点, 就可以选择必要的加工方法来保证其技术条件的要求。