火炮身管及加工工艺
浅谈火炮身管加工工艺

( 2 ) 替代炮管 电镀铬的衬管技术。 美 国陆军为淘 5 m m 自紧处理中施加压力 的方法包括 : 水压法 、 棒压 汰含 六价 铬 的炮管 电镀铬 工艺 ,已验证 了 2 法及气压法。利用超高水压机 , 可以制成耐一万个标 M2 4 2 “ 丛 林 之 王” 中 口径火 炮 采 用 T a 一 1 0 W 衬 管 的可 准大气压的超高压身管。经过 自紧处理 的身管 , 其内 行性。在尤马试验场进行的试验 已证实 , 与炮管镀铬 外径 再 受 到机 械 加 工 时 , 一部 分 应 力 被 消除 , 随之 产 相 比, 抗烧蚀寿命至少可提高三倍。 生膨胀 、 收缩 。因此 , 在加工工序和加工方法上要下
身 管加 工 工 艺 , 并 对 国外 最新 进 展 进 行 了分 析 , 以期
对 国内相关行业的生产发展起到一定 的促进作用 。
2 O 世纪 6 0 年代后 , 身管 自紧技术成熟并真正受 到重视。英 国 L 7 式1 0 5 毫米坦克炮率先采用了身管
自紧技 术 。 之后 , 德国“ 豹” I 坦克 、 美 国 M6 0 坦 克 的 主
1 身管材料
对锻造身的钻头和钻孑 L 刀具。为 了确保钻 出的孔
的尺寸精度 和表面光 洁度 ,研 削等精细加工是不可 高膛 压火炮 对 内膛 的强度 和韧 性有 极 高的 要 缺少 的, 所 以要有适合各种类型炮管的研削工具。用 求, 身管加工的第一个难题是材料的选择和冶炼。早 于深孔加工 的机床都是很复杂的专用机床 ,加工炮 期 的火炮主要是 由青铜或铁 等金属材料铸造而 成 , 管膛孔能达到很高的精度 , 是火炮加工的利器。 随着 l 9 世纪后半期转炉炼钢法的发 明 , 火炮开始采 2 . 2 自紧 工艺 用 大型铸钢制造炮身 , 不久之后 , 又研制 出高强度合 高膛压火炮大多采用 自紧身管。 自紧工艺是在 金 钢用 于炮 身 的制作 。 镗孑 L 直径基本达到要求 ,即在 内膛半精加工 的过程 电渣重熔是为 了满足炮身合金 钢精炼要求而诞 中进行 。 自紧是在普通单筒身管 内通过特殊工艺使 生 的一 种 工 艺 , 精炼 过 的特 种 钢 , 再 经 过 电渣 重 熔 工 炮管 由内向外产生一定的塑性变形 ,这样身管外层 艺可 以去掉残留的少量硫 、磷等对 火炮强度和韧性 使 身管的承压能力增 有害 的元 素 , 使钢 的纯度更高 , 以满 足身管的要求 。 对 内层产生压力 ,在射击时 , 可以有效减小身管厚度 , 进而降低火炮全重。由 现代火炮身 管材料都采用合金钢 ,常以中碳镍 铬铂 大 , 系合 金 钢 为 主 , 也 有增 加 少量 的 钒做 改性 钢 。本 文 针 于 自紧 ,内层 的压 缩 预应 力 可 以阻 止疲 劳 裂 缝 的 扩 增 大 了疲 劳寿 命 。 对火炮身管加工工艺 的发展现状 ,介绍 了传统典 型 大 ,
火炮工艺技术
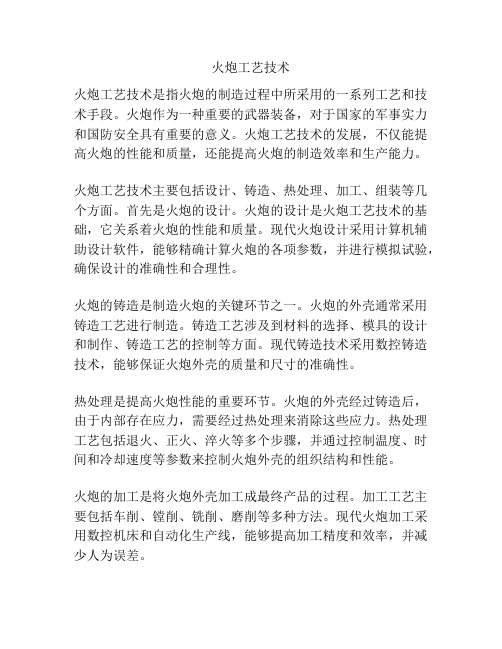
火炮工艺技术火炮工艺技术是指火炮的制造过程中所采用的一系列工艺和技术手段。
火炮作为一种重要的武器装备,对于国家的军事实力和国防安全具有重要的意义。
火炮工艺技术的发展,不仅能提高火炮的性能和质量,还能提高火炮的制造效率和生产能力。
火炮工艺技术主要包括设计、铸造、热处理、加工、组装等几个方面。
首先是火炮的设计。
火炮的设计是火炮工艺技术的基础,它关系着火炮的性能和质量。
现代火炮设计采用计算机辅助设计软件,能够精确计算火炮的各项参数,并进行模拟试验,确保设计的准确性和合理性。
火炮的铸造是制造火炮的关键环节之一。
火炮的外壳通常采用铸造工艺进行制造。
铸造工艺涉及到材料的选择、模具的设计和制作、铸造工艺的控制等方面。
现代铸造技术采用数控铸造技术,能够保证火炮外壳的质量和尺寸的准确性。
热处理是提高火炮性能的重要环节。
火炮的外壳经过铸造后,由于内部存在应力,需要经过热处理来消除这些应力。
热处理工艺包括退火、正火、淬火等多个步骤,并通过控制温度、时间和冷却速度等参数来控制火炮外壳的组织结构和性能。
火炮的加工是将火炮外壳加工成最终产品的过程。
加工工艺主要包括车削、镗削、铣削、磨削等多种方法。
现代火炮加工采用数控机床和自动化生产线,能够提高加工精度和效率,并减少人为误差。
火炮的组装是将各个部件组合在一起,形成完整的火炮系统的过程。
组装工艺包括零部件的配对、拼装和调试等多个环节。
现代火炮组装采用装配线作业和机器人自动化装配技术,能够提高组装速度和质量,并减少人为操作错误。
火炮工艺技术的发展,不仅提高了火炮的性能和质量,还提高了火炮的制造效率和生产能力。
现代火炮制造所采用的工艺技术,既保证了火炮的可靠性和耐久性,也提高了火炮的作战效能和使用寿命。
总之,火炮工艺技术是现代军事工业的重要组成部分。
通过火炮工艺技术的不断发展和创新,能够提高火炮的性能和质量,促进国家的军事实力和国防安全。
火炮身管标准

火炮身管标准火炮是一种重要的军用武器,其身管是其最为关键的部件之一。
火炮身管标准是为了确保火炮的性能和稳定性而制定的一系列规范和要求。
1. 材料选择:火炮身管标准要求使用高强度、耐热、耐腐蚀的材料,以承受高温、高压和化学腐蚀等极端条件。
常见的材料包括高强度合金钢、不锈钢以及钨合金。
材料的选择要根据火炮的使用环境和任务需求进行。
2. 尺寸精度:火炮身管标准要求身管的尺寸精度高,以确保火炮的射击精度和稳定性。
尺寸精度包括内径、外径、长度和直线度等方面的要求。
一般来说,内径要求直径公差小、内表面光洁度高,以保证弹丸顺利通过;外径和长度要求尺寸一致,以便与火炮其他部件的组装配合;直线度要求身管的轴线与火炮的中心轴线重合,以确保火炮的射击精度。
3. 表面处理:火炮身管标准要求对身管表面进行特殊处理,以提高其耐磨性和抗腐蚀性。
常见的表面处理方法有镀铬、热处理和抛光等。
镀铬可以提高身管的硬度和耐磨性,减少磨损;热处理可以改善材料的结构和性能;抛光可以提高内表面光洁度,减少摩擦阻力。
4. 强度和耐久性测试:火炮身管标准要求对身管进行强度和耐久性测试,以评估其在使用过程中的性能。
强度测试包括拉伸和冲击试验,以确定身管的最大承载能力和抗冲击性能。
耐久性测试要模拟实际使用条件,进行多次射击测试,以检验身管的使用寿命和稳定性。
5. 管膛生产工艺:火炮身管标准要求具备先进的管膛生产工艺,以确保身管的质量和稳定性。
常见的管膛生产工艺包括冷挤压、冷拉伸和热锻等。
这些工艺可以提高身管的材料性能和结构稳定性,减少内部缺陷,提高射击精度和使用寿命。
在制定和执行火炮身管标准时,需要考虑到火炮的使用环境、任务需求和制造技术的发展。
火炮身管标准的实施可以保证火炮的性能、稳定性和安全性,提高其在战场上的作战效能。
同时,合理的身管标准还可以推动火炮制造技术的创新和改进,提高火炮的质量和可靠性。
总之,火炮身管标准是确保火炮性能和稳定性的重要规范和要求。
炮管制作工艺-概述说明以及解释
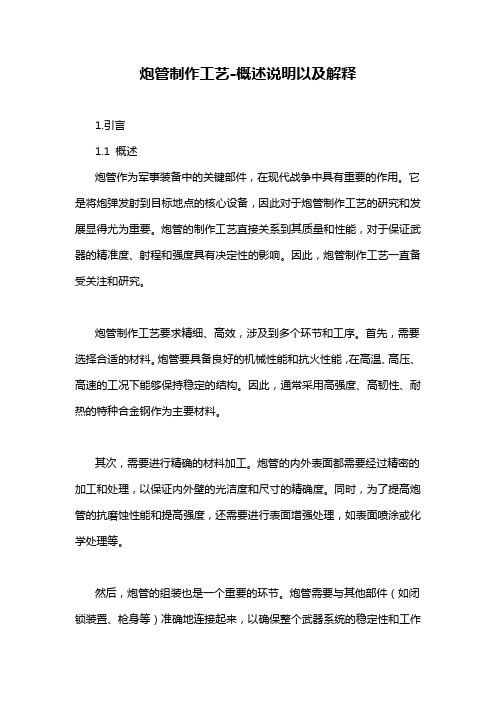
炮管制作工艺-概述说明以及解释1.引言1.1 概述炮管作为军事装备中的关键部件,在现代战争中具有重要的作用。
它是将炮弹发射到目标地点的核心设备,因此对于炮管制作工艺的研究和发展显得尤为重要。
炮管的制作工艺直接关系到其质量和性能,对于保证武器的精准度、射程和强度具有决定性的影响。
因此,炮管制作工艺一直备受关注和研究。
炮管制作工艺要求精细、高效,涉及到多个环节和工序。
首先,需要选择合适的材料。
炮管要具备良好的机械性能和抗火性能,在高温、高压、高速的工况下能够保持稳定的结构。
因此,通常采用高强度、高韧性、耐热的特种合金钢作为主要材料。
其次,需要进行精确的材料加工。
炮管的内外表面都需要经过精密的加工和处理,以保证内外壁的光洁度和尺寸的精确度。
同时,为了提高炮管的抗磨蚀性能和提高强度,还需要进行表面增强处理,如表面喷涂或化学处理等。
然后,炮管的组装也是一个重要的环节。
炮管需要与其他部件(如闭锁装置、枪身等)准确地连接起来,以确保整个武器系统的稳定性和工作效果。
组装过程中需要对连接部位进行严格的检测和调整,以保证其安全性和可靠性。
最后,炮管的测试是制作工艺的最后一道关口。
通过对炮管进行压力测试、温度测试和射击测试等,来验证其性能和可靠性。
同时,还需要进行炮管的疲劳强度测试和寿命测试,以确保其可以长时间稳定地工作。
总之,炮管制作工艺是一项综合性、复杂性很高的工程。
它要求在材料选择、加工工艺、组装和测试等方面都具备高水平的技术和专业知识。
只有通过不断的研究和改进,不断提高炮管制作工艺的质量和效率,才能生产出更加优良的炮管产品,为军事装备的发展和提高提供坚实的支撑。
1.2文章结构1.2 文章结构本文将围绕"炮管制作工艺"这一主题展开讨论。
文章分为引言、正文和结论三个部分。
在引言部分,我们将对炮管制作工艺进行概述,介绍其在军事和工业领域的重要性和应用。
同时,我们将介绍本文的结构和目的,以便读者对整篇文章有一个清晰的了解。
炮管制作工艺

炮管制作工艺炮管制作是一门古老而复杂的工艺,它需要经过精细的设计和精湛的技术才能完成。
炮管是火炮的核心部件,它直接影响着火炮的威力和性能。
下面将为大家详细介绍炮管制作的工艺和过程。
炮管的材料是炮制的基础。
常见的炮管材料有钢和铜。
钢是最常用的材料,因为它具有良好的强度和耐磨性。
而铜则常用于特殊要求的火炮,因为它导热性能好,能够更好地散热。
选择合适的炮管材料是确保火炮性能的关键。
在炮管的制作过程中,首先需要进行炮管的设计。
设计师会根据火炮的用途和性能要求来确定炮管的内外形状、长度和直径等参数。
设计的关键是要保证炮管内部的燃气能够顺利地推动炮弹,并且尽量减少燃气的泄漏,以提高火炮的射程和精度。
接下来是炮管的加工。
首先,需要将选定的材料切割成适当的长度,并进行精确的加工。
加工过程中,需要使用各种工具和设备,如车床、钻床和砂轮等。
设计师和工匠们需要精确地操作这些工具,以确保炮管的尺寸和形状达到设计要求。
在加工完成后,还需要对炮管进行热处理。
热处理可以改善炮管的硬度和强度,提高其耐磨性和抗拉伸性能。
常见的热处理方法包括淬火和回火。
这些处理过程需要精确地控制温度和时间,以确保炮管的性能得到最佳的提升。
是炮管的表面处理。
表面处理可以提高炮管的耐腐蚀性能和外观质量。
常见的表面处理方法有镀铬、氮化和喷涂等。
这些方法可以有效地保护炮管免受氧化和腐蚀的侵害,延长其使用寿命。
总的来说,炮管制作是一门精密而复杂的工艺。
它需要设计师和工匠们精湛的技术和严谨的态度。
只有通过精心的设计和精细的加工,才能制作出性能优良的炮管,为火炮的威力和精度提供坚实的保障。
炮管制作工艺的发展也正是人类智慧和技术的结晶,为战争和和平的进程做出了巨大的贡献。
火炮身管标准

火炮身管标准火炮身管是火炮系统中的重要组成部分,直接影响到火炮的质量、性能和使用寿命。
身管的设计、制造和质检一直以来都是火炮研发的重点和难点之一。
本文将详细介绍火炮身管的标准,并探讨其对火炮性能的影响。
一、火炮身管标准的背景火炮作为一种重要的军事装备,其功能主要是发射炮弹,对目标进行攻击。
而炮弹的速度、精度和射程等方面的性能,直接依赖于火炮身管的质量。
良好的身管设计和制造标准,能够保证火炮的射击精度和可靠性,提高其作战效能。
二、火炮身管的设计标准1.材料选择火炮身管的材料应具备高强度、高韧性、良好的耐热性和抗疲劳性能。
典型的材料有合金钢、不锈钢和钛合金等。
在选择材料时,还应考虑到生产工艺、成本以及对环境的适应性。
2.结构设计火炮身管一般采用钢管形式,内外壁贴有保护层。
内壁防止腐蚀和磨损,外壁防止高温烧蚀。
身管结构设计应符合火炮的使用要求和弹药装填方式。
同时,还需兼顾重量、均衡性和抗震能力等方面的考虑。
3.内部表面处理为了提高火炮身管的耐热性和抗磨损性能,一般会对内部表面进行处理。
常见的方法有镀铬、熔渗和光洁处理等。
这些处理方式能够有效地降低身管内部的摩擦阻力,提高炮弹的发射速度和射击精度。
三、火炮身管的制造标准1.制造工艺火炮身管的制造工艺包括炼钢、热处理、挤压和加工等多个环节。
炼钢过程中需要控制钢的成分和纯度,以保证身管的质量。
热处理过程中,通过控制加热温度和冷却速度,使得身管的组织达到理想的状态。
挤压和加工过程需要保证身管的几何尺寸和表面质量。
2.检测方法火炮身管的制造过程需要进行严格的质检,以保证其达到设计标准。
常用的检测方法有金相分析、磁粉探伤、超声波检测和压力试验等。
这些方法能够有效地检测身管的材料和结构的缺陷,如裂纹、气孔和夹杂等。
四、火炮身管标准对火炮性能的影响火炮身管的质量和性能直接影响到火炮的精度、射程和可靠性。
良好的身管设计和制造标准能够降低火炮的射击误差,提高其打击精度。
同时,通过精确的尺寸控制和表面处理,能够提高炮弹的速度和穿透能力。
火炮配件加工的工艺与技术
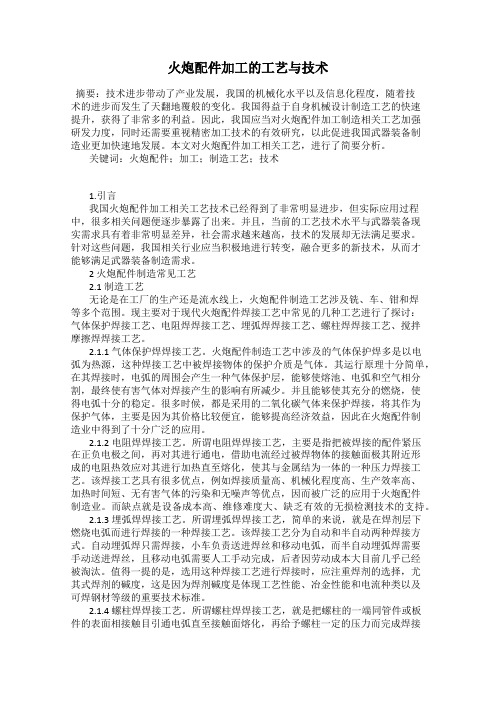
火炮配件加工的工艺与技术摘要:技术进步带动了产业发展,我国的机械化水平以及信息化程度,随着技术的进步而发生了天翻地覆般的变化。
我国得益于自身机械设计制造工艺的快速提升,获得了非常多的利益。
因此,我国应当对火炮配件加工制造相关工艺加强研发力度,同时还需要重视精密加工技术的有效研究,以此促进我国武器装备制造业更加快速地发展。
本文对火炮配件加工相关工艺,进行了简要分析。
关键词:火炮配件;加工;制造工艺;技术1.引言我国火炮配件加工相关工艺技术已经得到了非常明显进步,但实际应用过程中,很多相关问题便逐步暴露了出来。
并且,当前的工艺技术水平与武器装备现实需求具有着非常明显差异,社会需求越来越高,技术的发展却无法满足要求。
针对这些问题,我国相关行业应当积极地进行转变,融合更多的新技术,从而才能够满足武器装备制造需求。
2 火炮配件制造常见工艺2.1 制造工艺无论是在工厂的生产还是流水线上,火炮配件制造工艺涉及铣、车、钳和焊等多个范围。
现主要对于现代火炮配件焊接工艺中常见的几种工艺进行了探讨:气体保护焊接工艺、电阻焊焊接工艺、埋弧焊焊接工艺、螺柱焊焊接工艺、搅拌摩擦焊焊接工艺。
2.1.1 气体保护焊焊接工艺。
火炮配件制造工艺中涉及的气体保护焊多是以电弧为热源,这种焊接工艺中被焊接物体的保护介质是气体。
其运行原理十分简单,在其焊接时,电弧的周围会产生一种气体保护层,能够使熔池、电弧和空气相分割,最终使有害气体对焊接产生的影响有所减少。
并且能够使其充分的燃烧,使得电弧十分的稳定。
很多时候,都是采用的二氧化碳气体来保护焊接,将其作为保护气体,主要是因为其价格比较便宜,能够提高经济效益,因此在火炮配件制造业中得到了十分广泛的应用。
2.1.2 电阻焊焊接工艺。
所谓电阻焊焊接工艺,主要是指把被焊接的配件紧压在正负电极之间,再对其进行通电,借助电流经过被焊物体的接触面极其附近形成的电阻热效应对其进行加热直至熔化,使其与金属结为一体的一种压力焊接工艺。
火炮设计理论(炮身设计)
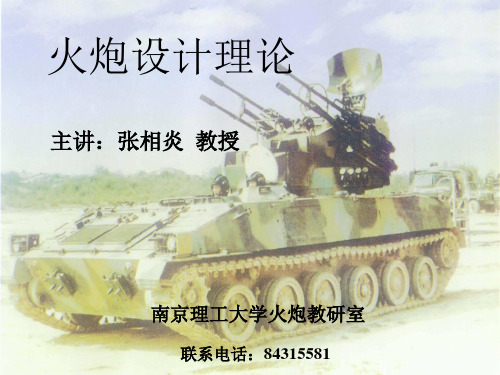
§2.1 概述
药筒分装式药室: 适用于药筒分装式炮弹的药室,先装弹丸,再装药筒及 发射药。 药室结构形状由药筒的外形结构形状确定。
药筒分装式药筒有两种结构形式: 一种与定装式药筒相同,仅药筒口部较短; 另一种药筒仅有药筒主体。 对应第一种药筒,药室也与定装式药室相同,仅园柱部 较短; 对应第二种药筒,药室仅由药室主体(基本锥体)和园 柱部组成。
§2.1 概述
4 身管寿命
4.1 身管寿命 火炮在按规定射击条件射击,身管在丧失要求的功能、 安全性或毁坏之前,所发射的当量全装药炮弹数。 4.2 身管主要失效现象 炸膛; 胀膛; 膛线剥落; 炮膛挂铜。
§2.1 概述
4.3 身管寿命分类
烧蚀寿命 烧蚀寿命终止标准: ①初速下降百分数超过规定值(5%~10%)。一般可以通 过测量药室增长量来评定烧蚀寿命等级。 ②射击密集度超过规定范围(如散布面积超过8倍)。
§2.1 概述
2 炮身的结构设计 2.1 内膛结构
药室部 坡膛
导向部
§2.1 概述
2 炮身的结构设计 2.1 内膛结构
2.2.1 药室: 发射前容纳/承装发射药(及药筒);击发后提供火药正 常燃烧空间的炮膛部分。 药室容积由内弹道设计确定,药室结构形状取决于炮弹 结构及装填方式等。 药室分为药筒定装式药室、药筒分装式药室、药包分装 式药室。
主讲:张相炎 教授
南京理工大学火炮教研室
联系电话:84315581
第二章 炮身设计
§2.1 概述
1 炮身 1.1 炮身 1.2 炮身的作用 1.3 炮身的组成 完成炮弹的装填和发射,并赋予弹丸 初速和方向的火炮主要部件。 承受火药气体压力,引导 弹丸运动。 炮尾
身管
炮闩
现代炮管生产工艺
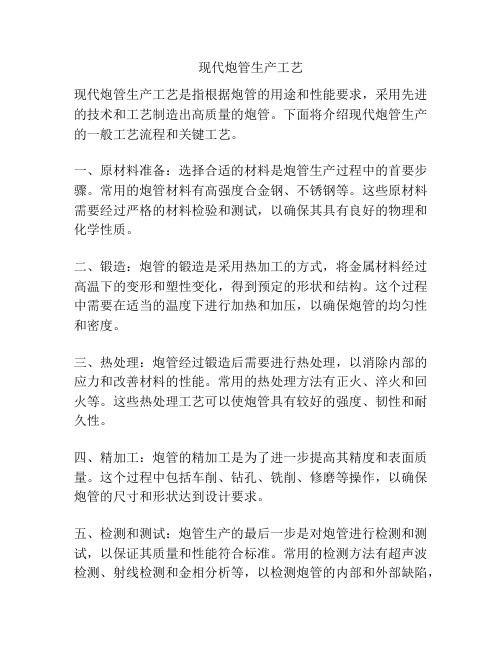
现代炮管生产工艺
现代炮管生产工艺是指根据炮管的用途和性能要求,采用先进的技术和工艺制造出高质量的炮管。
下面将介绍现代炮管生产的一般工艺流程和关键工艺。
一、原材料准备:选择合适的材料是炮管生产过程中的首要步骤。
常用的炮管材料有高强度合金钢、不锈钢等。
这些原材料需要经过严格的材料检验和测试,以确保其具有良好的物理和化学性质。
二、锻造:炮管的锻造是采用热加工的方式,将金属材料经过高温下的变形和塑性变化,得到预定的形状和结构。
这个过程中需要在适当的温度下进行加热和加压,以确保炮管的均匀性和密度。
三、热处理:炮管经过锻造后需要进行热处理,以消除内部的应力和改善材料的性能。
常用的热处理方法有正火、淬火和回火等。
这些热处理工艺可以使炮管具有较好的强度、韧性和耐久性。
四、精加工:炮管的精加工是为了进一步提高其精度和表面质量。
这个过程中包括车削、钻孔、铣削、修磨等操作,以确保炮管的尺寸和形状达到设计要求。
五、检测和测试:炮管生产的最后一步是对炮管进行检测和测试,以保证其质量和性能符合标准。
常用的检测方法有超声波检测、射线检测和金相分析等,以检测炮管的内部和外部缺陷,
并确定其性能参数。
通过上述工艺流程和关键工艺,现代炮管能够在保证强度和耐用性的同时,保持较高的精度和效率。
随着科技的进步和工艺技术的不断创新,炮管生产工艺也在不断发展和改进,以满足不同领域和需求的炮管应用。
现代火炮的炮管是怎样制造出来的?
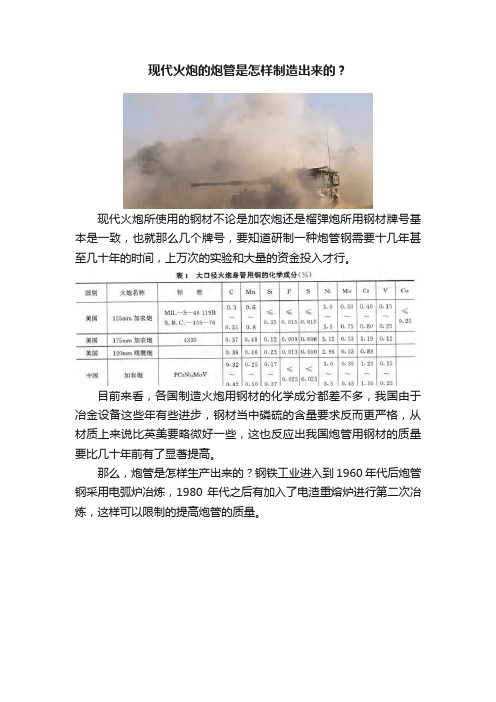
现代火炮的炮管是怎样制造出来的?现代火炮所使用的钢材不论是加农炮还是榴弹炮所用钢材牌号基本是一致,也就那么几个牌号,要知道研制一种炮管钢需要十几年甚至几十年的时间,上万次的实验和大量的资金投入才行。
目前来看,各国制造火炮用钢材的化学成分都差不多,我国由于冶金设备这些年有些进步,钢材当中磷硫的含量要求反而更严格,从材质上来说比英美要略微好一些,这也反应出我国炮管用钢材的质量要比几十年前有了显著提高。
那么,炮管是怎样生产出来的?钢铁工业进入到1960年代后炮管钢采用电弧炉冶炼,1980年代之后有加入了电渣重熔炉进行第二次冶炼,这样可以限制的提高炮管的质量。
电弧炉是目前钢铁工业必备的冶金设备,大部分高档钢材都有它来进行冶炼,由于电能是“二次能源”,不存在有害物质的带入,所以它冶炼出来的钢水会更加纯净。
图片里就是电弧炉冶炼钢水到出钢的生产流程3D模拟图,右侧是电弧炉、中间是盛钢桶、左面是电弧炉冶炼完毕后出钢。
电弧炉冶炼完成的钢液,要浇铸成图片里的这种棒材,如果想要进一步提高质量也可以浇铸成钢锭,再由“初轧机”开坯成圆钢坯,这样的棒材表面光滑和内部致密,更适合电渣重熔炉使用。
那么为啥要制成圆钢棒材?电渣重熔炉的原理就和我们日常所看到的电焊是一样的,这根圆钢棒材就相当于“电焊条”,只不过粗一些罢了,电渣重熔炉根据二次冶炼钢锭的大小的需要,使用几十或者几百根这样的圆钢棒材。
电渣重熔炉外观就是这个样子,有三到四个电加热臂,臂的前端有卡头将圆钢棒材夹住→将圆钢棒材垂直插入电渣重熔炉中→通电开始加热、熔化→熔化的钢液一点点累积,最后形成一个大型电渣重熔钢锭。
由于需要后续的锻造工序,电渣重熔钢锭是多棱型的,这样才能便于锻造。
通常情况下大口径炮管钢锭在30吨以上,只有这样大的钢锭才能经过多次锻打使内部更加致密,也只有致密的钢材制造出来的炮管,才能经受发射药的高温高压和炮弹弹丸高速摩擦。
大型锻造钢锭要经过万吨级别(至少三万吨)的锻造机进行锻压,将钢锭锻造出炮管粗坯,万吨级别锻造机是重要的工业设备,世界上只有少数几个国家可以将它制造出来,它不仅仅是锻造炮管,大型钢铁结构件、承重件、飞机主梁、大型发电机转子…都需要采用万吨级别锻造机锻造,才能精确成型。
战列舰大口径炮管是如何锻造的?
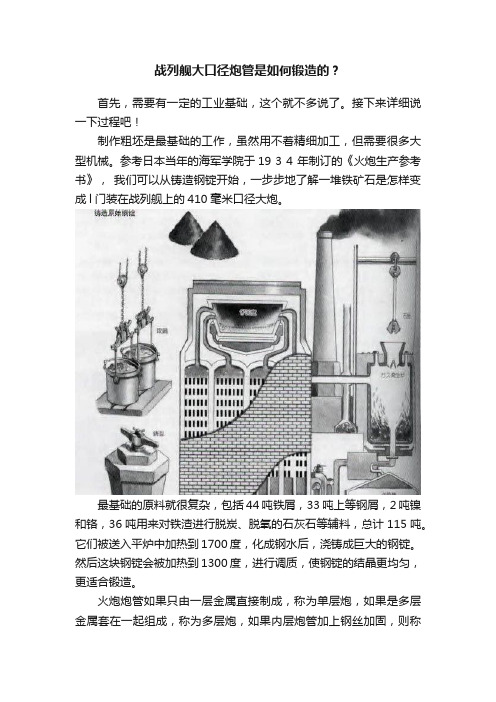
战列舰大口径炮管是如何锻造的?首先,需要有一定的工业基础,这个就不多说了。
接下来详细说一下过程吧!制作粗坯是最基础的工作,虽然用不着精细加工,但需要很多大型机械。
参考日本当年的海军学院于19 3 4 年制订的《火炮生产参考书》,我们可以从铸造钢锭开始,一步步地了解一堆铁矿石是怎样变成l门装在战列舰上的410毫米口径大炮。
最基础的原料就很复杂,包括44吨铁屑,33吨上等钢屑,2吨镍和铬,36吨用来对铁渣进行脱炭、脱氧的石灰石等辅料,总计115吨。
它们被送入平炉中加热到1700度,化成钢水后,浇铸成巨大的钢锭。
然后这块钢锭会被加热到1300度,进行调质,使钢锭的结晶更均匀,更适合锻造。
火炮炮管如果只由一层金属直接制成,称为单层炮,如果是多层金属套在一起组成,称为多层炮,如果内层炮管加上钢丝加固,则称为钢丝套炮。
长门级的4 10 毫米主炮就是由内外两层炮管组成,其中还加入了钢丝进行加固,以抵抗射击时巨大的膛压。
每根炮管需要浇铸4块钢锭,以后要分别制成炮口套管、炮尾套管、外层炮管和内层炮管。
经过调质后的钢锭送上锻压机进行初步成型,把它锻制成圆柱体后,再进行一次退火,以消除冷却时产生的内部应力。
由于在铸造过程中,钢锭底部最容易出现问题,需要用大型锯片切割机将底部切去,切断的部分约占钢锭总体积的5%。
同时,容易出现问题的顶部也要切去,这里切得更多,约为20%.也就是说,用115 吨原料铸造出来的钢锭,有近l/4是无用的废料。
此外,钢锭中心也是铸造中容易发生问题的部件,所以在锻压成型前,要用大型钻孔机的超长钻头把钢锭中心钻掉。
钻好孔的空心圆柱被送入加热炉内,加热到1600度。
为了保证它受热均匀,加热炉采用一氧化碳为燃料。
直到钢柱被烧得通红,温度均匀后,才被拉到大型水压机上,锻压成炮管的形状,成为最基础的粗坯。
在制作粗坯的过程中,每进行一道工序,都要对其进行非常细致的检查,尤其是内层炮管,必须确保没有任何裂纹。
特种材料之火炮
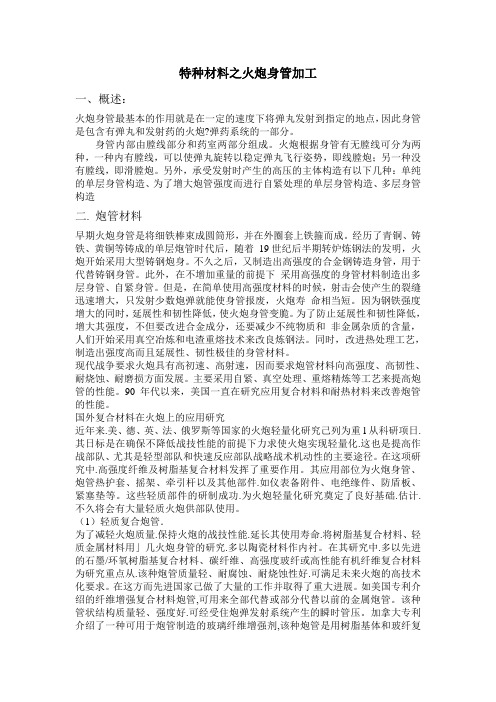
特种材料之火炮身管加工一、概述:火炮身管最基本的作用就是在一定的速度下将弹丸发射到指定的地点,因此身管是包含有弹丸和发射药的火炮?弹药系统的一部分。
身管内部由膛线部分和药室两部分组成。
火炮根据身管有无膛线可分为两种,一种内有膛线,可以使弹丸旋转以稳定弹丸飞行姿势,即线膛炮;另一种没有膛线,即滑膛炮。
另外,承受发射时产生的高压的主体构造有以下几种:单纯的单层身管构造、为了增大炮管强度而进行自紧处理的单层身管构造、多层身管构造二. 炮管材料早期火炮身管是将细铁棒束成圆筒形,并在外圈套上铁箍而成。
经历了青铜、铸铁、黄铜等铸成的单层炮管时代后,随着19世纪后半期转炉炼钢法的发明,火炮开始采用大型铸钢炮身。
不久之后,又制造出高强度的合金钢铸造身管,用于代替铸钢身管。
此外,在不增加重量的前提下采用高强度的身管材料制造出多层身管、自紧身管。
但是,在简单使用高强度材料的时候,射击会使产生的裂缝迅速增大,只发射少数炮弹就能使身管报废,火炮寿命相当短。
因为钢铁强度增大的同时,延展性和韧性降低,使火炮身管变脆。
为了防止延展性和韧性降低,增大其强度,不但要改进合金成分,还要减少不纯物质和非金属杂质的含量,人们开始采用真空冶炼和电渣重熔技术来改良炼钢法。
同时,改进热处理工艺,制造出强度高而且延展性、韧性极佳的身管材料。
现代战争要求火炮具有高初速、高射速,因而要求炮管材料向高强度、高韧性、耐烧蚀、耐磨损方面发展。
主要采用自紧、真空处理、重熔精炼等工艺来提高炮管的性能。
90年代以来,美国一直在研究应用复合材料和耐热材料来改善炮管的性能。
国外复合材料在火炮上的应用研究近年来.美、德、英、法、俄罗斯等国家的火炮轻量化研究己列为重l从科研项日.其日标是在确保不降低战技性能的前提下力求使火炮实现轻量化.这也是提高作战部队、尤其是轻型部队和快速反应部队战略战术机动性的主要途径。
在这项研究中.高强度纤维及树脂基复合材料发挥了重要作用。
其应用部位为火炮身管、炮管热护套、摇架、牵引杆以及其他部件.如仪表备附件、电绝缘件、防盾板、紧塞垫等。
火炮制造工艺
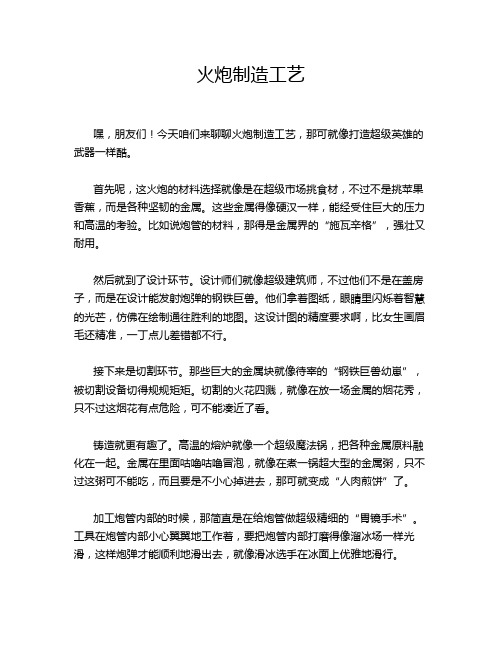
火炮制造工艺嘿,朋友们!今天咱们来聊聊火炮制造工艺,那可就像打造超级英雄的武器一样酷。
首先呢,这火炮的材料选择就像是在超级市场挑食材,不过不是挑苹果香蕉,而是各种坚韧的金属。
这些金属得像硬汉一样,能经受住巨大的压力和高温的考验。
比如说炮管的材料,那得是金属界的“施瓦辛格”,强壮又耐用。
然后就到了设计环节。
设计师们就像超级建筑师,不过他们不是在盖房子,而是在设计能发射炮弹的钢铁巨兽。
他们拿着图纸,眼睛里闪烁着智慧的光芒,仿佛在绘制通往胜利的地图。
这设计图的精度要求啊,比女生画眉毛还精准,一丁点儿差错都不行。
接下来是切割环节。
那些巨大的金属块就像待宰的“钢铁巨兽幼崽”,被切割设备切得规规矩矩。
切割的火花四溅,就像在放一场金属的烟花秀,只不过这烟花有点危险,可不能凑近了看。
铸造就更有趣了。
高温的熔炉就像一个超级魔法锅,把各种金属原料融化在一起。
金属在里面咕噜咕噜冒泡,就像在煮一锅超大型的金属粥,只不过这粥可不能吃,而且要是不小心掉进去,那可就变成“人肉煎饼”了。
加工炮管内部的时候,那简直是在给炮管做超级精细的“胃镜手术”。
工具在炮管内部小心翼翼地工作着,要把炮管内部打磨得像溜冰场一样光滑,这样炮弹才能顺利地滑出去,就像滑冰选手在冰面上优雅地滑行。
组装环节呢,就像是拼一个巨大的金属乐高。
各个部件得严丝合缝,就像牙齿咬得紧紧的,要是有个小缝隙,那火炮在发射的时候可能就会像个打喷嚏打一半的人,憋得难受,还发挥不出威力。
表面处理就像是给火炮化妆。
要把它打扮得既能抵御风雨侵蚀,又看起来威风凛凛。
这涂层就像是火炮的时尚外衣,让它在战场上成为最靓的仔。
测试环节那可是惊心动魄。
火炮发射的瞬间,那声音就像雷神在怒吼,整个大地都在颤抖。
要是成功了,就像运动员打破世界纪录一样值得欢呼;要是失败了,那可就像小丑表演时摔了个大跟头,得赶紧检查问题重新来过。
火炮制造工艺啊,就是这样一个充满神奇和挑战的过程,就像一场钢铁与智慧的狂欢派对,最后诞生出那些令人敬畏的战争利器。
火炮设计理论.
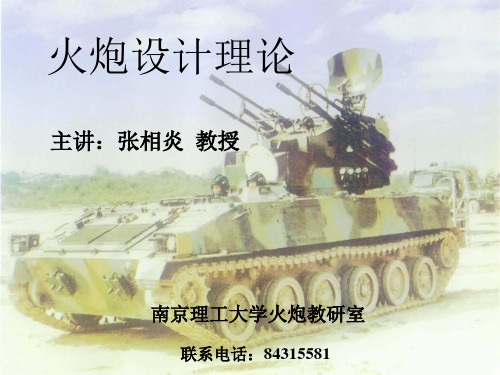
r
p
切向应力
r22 2 p s ln r 2r 2 2
r22 2 p s 2r22
2 r22 r 2
r2 2r22
r t s 1 ln r 2r22
2 2
2
r s ln 2r 2 r 2
→全弹状态
W2↑→Z↑→提高强度越明显
§2.4 自紧身管设计
2.3 残余应力(制造应力) 自紧时,在自紧压力P1作用下,身管从内表面开始出现塑性 变形,并且最终身管壁内形成塑性区和弹性区。并且身管壁内 存在径向应力(压力)p和切向应力σ t 。 卸去自紧压力P1时,由于身管内存在塑性变形,因此在卸载 过程中自紧身管内存在残余应力,也就是制造应力或预应力。 卸载过程是弹性卸载,相当于在一个内径为r1、外径为r2 ,的 弹性园筒上加一个-P1,而在身管内形成附加应力。附加应力 与自紧应力的迭加就形成残余应力。
1 2 1 2 1 2
2 m t p s
式中,2τm称为第三强度理论的相当应力。
§2.4 自紧身管设计
2.1 补充假设 (1)身管材料的拉伸和压缩特性一样; 这条假设就是为了略去鲍辛格效应的影响 (2)材料塑性变形后应力不增加; 这条假设就是为了忽略材料强化(硬化)现象的影响
半弹性状态
P1 K s ln
r2 r1
K 1.08
K 1.08 ~ 1.15
r22 2 P1 K s ln 2r 2 r1 2
§2.4 自紧身管设计
(5)说明 1)ρ 的影响
W22 W2 r22 2 ln ln W 2 s r1 2r2 2W22 P1
炮管的生产工艺
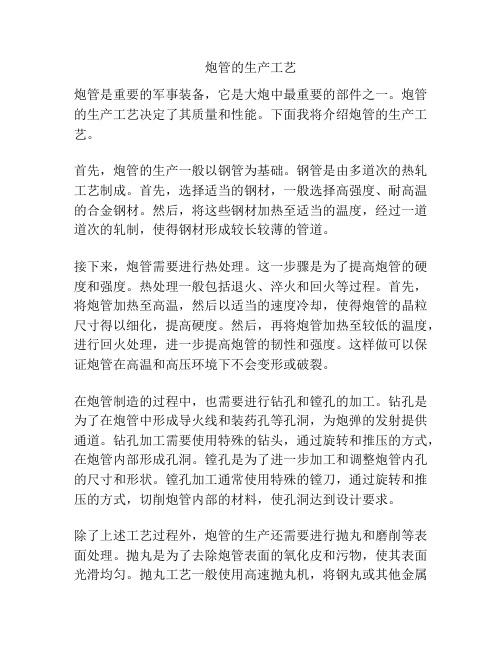
炮管的生产工艺炮管是重要的军事装备,它是大炮中最重要的部件之一。
炮管的生产工艺决定了其质量和性能。
下面我将介绍炮管的生产工艺。
首先,炮管的生产一般以钢管为基础。
钢管是由多道次的热轧工艺制成。
首先,选择适当的钢材,一般选择高强度、耐高温的合金钢材。
然后,将这些钢材加热至适当的温度,经过一道道次的轧制,使得钢材形成较长较薄的管道。
接下来,炮管需要进行热处理。
这一步骤是为了提高炮管的硬度和强度。
热处理一般包括退火、淬火和回火等过程。
首先,将炮管加热至高温,然后以适当的速度冷却,使得炮管的晶粒尺寸得以细化,提高硬度。
然后,再将炮管加热至较低的温度,进行回火处理,进一步提高炮管的韧性和强度。
这样做可以保证炮管在高温和高压环境下不会变形或破裂。
在炮管制造的过程中,也需要进行钻孔和镗孔的加工。
钻孔是为了在炮管中形成导火线和装药孔等孔洞,为炮弹的发射提供通道。
钻孔加工需要使用特殊的钻头,通过旋转和推压的方式,在炮管内部形成孔洞。
镗孔是为了进一步加工和调整炮管内孔的尺寸和形状。
镗孔加工通常使用特殊的镗刀,通过旋转和推压的方式,切削炮管内部的材料,使孔洞达到设计要求。
除了上述工艺过程外,炮管的生产还需要进行抛丸和磨削等表面处理。
抛丸是为了去除炮管表面的氧化皮和污物,使其表面光滑均匀。
抛丸工艺一般使用高速抛丸机,将钢丸或其他金属颗粒喷射到炮管表面,去除表面杂质。
磨削是为了进一步使炮管的尺寸和形状达到更高的精度要求。
磨削一般使用特殊的砂轮和磨削机械,将炮管表面进行高速旋转和磨削,使其表面更加光滑。
最后,炮管的生产还需要进行质量检测和测试。
这一步骤是为了确保炮管的质量和性能符合设计要求。
质量检测一般包括几何形状、尺寸精度、硬度、强度和耐腐蚀性等方面的测试。
测试一般使用光学仪器、机械设备和化学试剂等工具,对炮管进行各项指标的检测和测量。
炮管的生产工艺是一项复杂而精细的工作,需要采用多种专业设备和技术手段。
通过严格的生产工艺,可以生产出高质量、高性能的炮管,提高军队的作战能力。
帕罗特线膛炮 制造 工艺
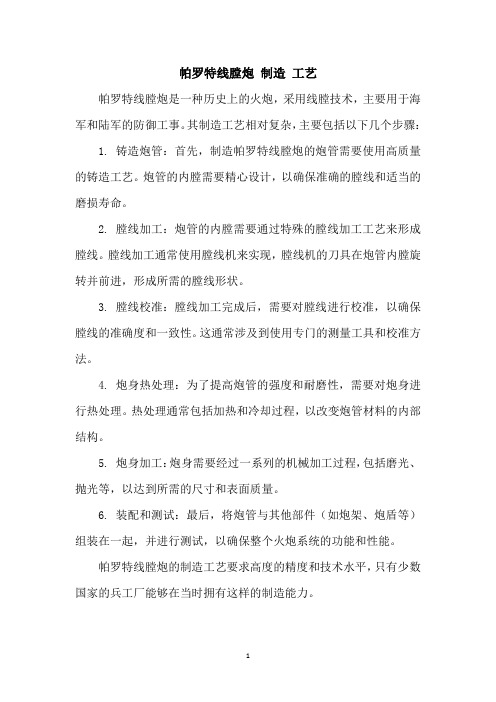
帕罗特线膛炮制造工艺
帕罗特线膛炮是一种历史上的火炮,采用线膛技术,主要用于海军和陆军的防御工事。
其制造工艺相对复杂,主要包括以下几个步骤:
1. 铸造炮管:首先,制造帕罗特线膛炮的炮管需要使用高质量的铸造工艺。
炮管的内膛需要精心设计,以确保准确的膛线和适当的磨损寿命。
2. 膛线加工:炮管的内膛需要通过特殊的膛线加工工艺来形成膛线。
膛线加工通常使用膛线机来实现,膛线机的刀具在炮管内膛旋转并前进,形成所需的膛线形状。
3. 膛线校准:膛线加工完成后,需要对膛线进行校准,以确保膛线的准确度和一致性。
这通常涉及到使用专门的测量工具和校准方法。
4. 炮身热处理:为了提高炮管的强度和耐磨性,需要对炮身进行热处理。
热处理通常包括加热和冷却过程,以改变炮管材料的内部结构。
5. 炮身加工:炮身需要经过一系列的机械加工过程,包括磨光、抛光等,以达到所需的尺寸和表面质量。
6. 装配和测试:最后,将炮管与其他部件(如炮架、炮盾等)组装在一起,并进行测试,以确保整个火炮系统的功能和性能。
帕罗特线膛炮的制造工艺要求高度的精度和技术水平,只有少数国家的兵工厂能够在当时拥有这样的制造能力。
1。
现代火炮的炮管是怎样制造出来的?看完你就知道了
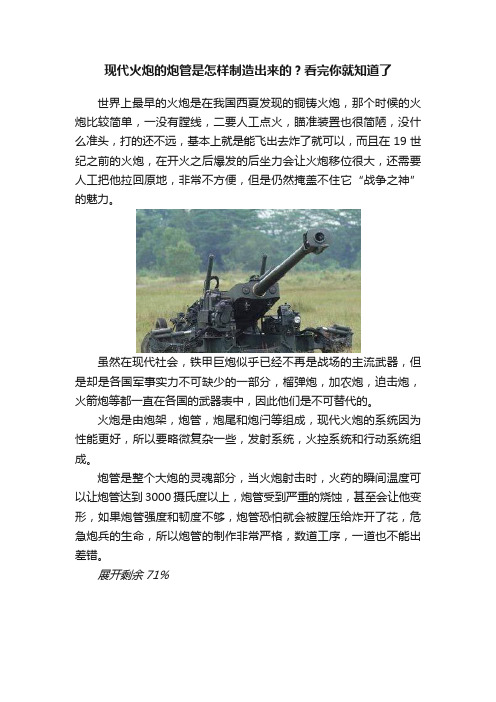
现代火炮的炮管是怎样制造出来的?看完你就知道了世界上最早的火炮是在我国西夏发现的铜铸火炮,那个时候的火炮比较简单,一没有膛线,二要人工点火,瞄准装置也很简陋,没什么准头,打的还不远,基本上就是能飞出去炸了就可以,而且在19世纪之前的火炮,在开火之后爆发的后坐力会让火炮移位很大,还需要人工把他拉回原地,非常不方便,但是仍然掩盖不住它“战争之神”的魅力。
虽然在现代社会,铁甲巨炮似乎已经不再是战场的主流武器,但是却是各国军事实力不可缺少的一部分,榴弹炮,加农炮,迫击炮,火箭炮等都一直在各国的武器表中,因此他们是不可替代的。
火炮是由炮架,炮管,炮尾和炮闩等组成,现代火炮的系统因为性能更好,所以要略微复杂一些,发射系统,火控系统和行动系统组成。
炮管是整个大炮的灵魂部分,当火炮射击时,火药的瞬间温度可以让炮管达到3000摄氏度以上,炮管受到严重的烧蚀,甚至会让他变形,如果炮管强度和韧度不够,炮管恐怕就会被膛压给炸开了花,危急炮兵的生命,所以炮管的制作非常严格,数道工序,一道也不能出差错。
展开剩余71%首先是在材料选择上,必须要使用特殊材料加工成的“炮钢”,因为火炮发射时的膛压可以达到500到700兆帕,一般的钢材根本憋不住那么大的压强,而且因为火炮发射温度高达3000摄氏度,所以材料必须要耐高温,但是外部温度却只有100多度,这就造成了内外温差大,炮管要在高温,高压和裂纹面前撑不了多久,所以它的韧度和强度也要一流,现代火炮的炮管一般都是用的碳镍铬铂系合金钢为主的改性钢。
给炮管增加厚度可以增加承压能力,但是大炮不能过重,所以就只能对大炮的炮管材料进行提纯和减轻重量,也就是电渣重熔和身管自紧。
在电渣重熔方面,即“炮钢”的提炼问题,他的目的就是为了让精钢中的一些硫,磷等物质被去除出去,使钢更纯,组织更加致密,达到火炮炮管的要求。
身管自紧就是用外部力量通过用机械等方法对炮管进内壁施压,使它塑性变形,但是外层确保留弹性,在弹药发射时产生的残余压应力可以将火药燃气的拉应力抵消,提高炮管的抗压能力。
一百多年前,国外工厂的炮管制造,用85000公斤钢水制造成品炮管!
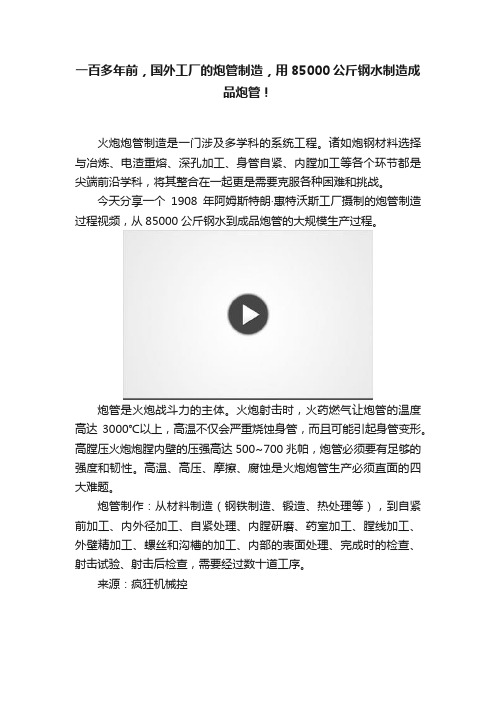
一百多年前,国外工厂的炮管制造,用85000公斤钢水制造成
品炮管!
火炮炮管制造是一门涉及多学科的系统工程。
诸如炮钢材料选择与冶炼、电渣重熔、深孔加工、身管自紧、内膛加工等各个环节都是尖端前沿学科,将其整合在一起更是需要克服各种困难和挑战。
今天分享一个1908年阿姆斯特朗·惠特沃斯工厂摄制的炮管制造过程视频,从85000公斤钢水到成品炮管的大规模生产过程。
炮管是火炮战斗力的主体。
火炮射击时,火药燃气让炮管的温度高达3000℃以上,高温不仅会严重烧蚀身管,而且可能引起身管变形。
高膛压火炮炮膛内壁的压强高达500~700兆帕,炮管必须要有足够的强度和韧性。
高温、高压、摩擦、腐蚀是火炮炮管生产必须直面的四大难题。
炮管制作:从材料制造(钢铁制造、锻造、热处理等),到自紧前加工、内外径加工、自紧处理、内膛研磨、药室加工、膛线加工、外壁精加工、螺丝和沟槽的加工、内部的表面处理、完成时的检查、射击试验、射击后检查,需要经过数十道工序。
来源:疯狂机械控。
二战各国BB炮加工工艺
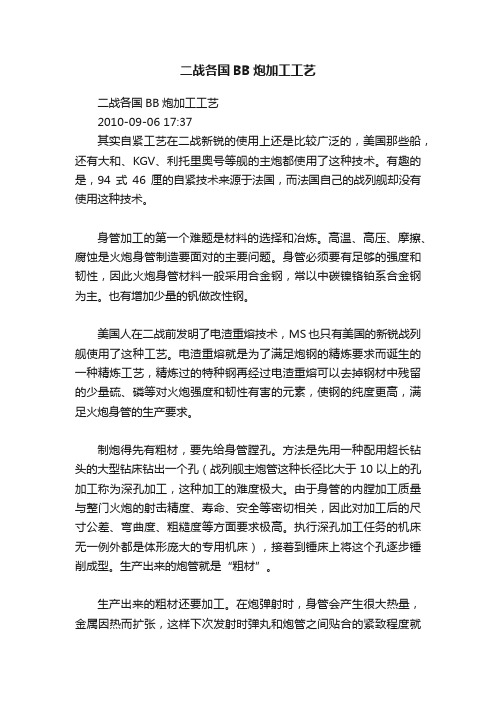
二战各国BB炮加工工艺二战各国BB炮加工工艺2010-09-06 17:37其实自紧工艺在二战新锐的使用上还是比较广泛的,美国那些船,还有大和、KGV、利托里奥号等舰的主炮都使用了这种技术。
有趣的是,94式46厘的自紧技术来源于法国,而法国自己的战列舰却没有使用这种技术。
身管加工的第一个难题是材料的选择和冶炼。
高温、高压、摩擦、腐蚀是火炮身管制造要面对的主要问题。
身管必须要有足够的强度和韧性,因此火炮身管材料一般采用合金钢,常以中碳镍铬铂系合金钢为主。
也有增加少量的钒做改性钢。
美国人在二战前发明了电渣重熔技术,MS也只有美国的新锐战列舰使用了这种工艺。
电渣重熔就是为了满足炮钢的精炼要求而诞生的一种精炼工艺,精炼过的特种钢再经过电渣重熔可以去掉钢材中残留的少量硫、磷等对火炮强度和韧性有害的元素,使钢的纯度更高,满足火炮身管的生产要求。
制炮得先有粗材,要先给身管膛孔。
方法是先用一种配用超长钻头的大型钻床钻出一个孔(战列舰主炮管这种长径比大于10以上的孔加工称为深孔加工,这种加工的难度极大。
由于身管的内膛加工质量与整门火炮的射击精度、寿命、安全等密切相关,因此对加工后的尺寸公差、弯曲度、粗糙度等方面要求极高。
执行深孔加工任务的机床无一例外都是体形庞大的专用机床),接着到锤床上将这个孔逐步锤削成型。
生产出来的炮管就是“粗材”。
生产出来的粗材还要加工。
在炮弹射时,身管会产生很大热量,金属因热而扩张,这样下次发射时弹丸和炮管之间贴合的紧致程度就会受到影响。
近现代战舰使用的是STGW44提到的“预应力炮管”,就是给炮管一个预应力,使炮管能够承受更大的压力。
缠丝工艺西洋解释了,套筒就根本不用说(傻子都能想明白怎么回事),当然还有自紧工艺。
自紧工艺在内膛半精加工的过程中就开始进行了,大概就是通过特殊工艺使炮管由内向外产生一定的塑性变形,这样身管外层对内层产生压力(就是预应力了),在射击时,这种压力就像在身管外又增加了无数层薄简,使身管的承压能力增大,可以有效减小身管厚度,还降低了火炮重量。
- 1、下载文档前请自行甄别文档内容的完整性,平台不提供额外的编辑、内容补充、找答案等附加服务。
- 2、"仅部分预览"的文档,不可在线预览部分如存在完整性等问题,可反馈申请退款(可完整预览的文档不适用该条件!)。
- 3、如文档侵犯您的权益,请联系客服反馈,我们会尽快为您处理(人工客服工作时间:9:00-18:30)。
对于火炮来说最重要的部分莫过于身管的制造,身管是符合弹道设计要求,用于抛射弹丸并能经受内部产生的压力的厚壁圆管。
其外形呈圆锥形(该圆锥形部分称炮前身),在炮口部分加厚形成喇叭管,使身管不致于爆炸,在喇叭管后面是身管最狭窄的部分,叫炮筒颈。
身管内表面称内膛(炮膛),分为药室、坡膛和线膛。
药室装发射药药包或药筒,这部分金属必须加厚些,以便能承受住初始发射弹药时产生的很高的气体压力。
线膛段由若干条具有一定宽度、深度和缠度以螺旋形沟槽作膛线,分为等齐、渐速和混合膛线三种。
其作用是在火药气体作用下使弹丸产生稳定飞行所需的旋转运动和导向,防止弹丸翻滚。
坡膛是药室与膛线部分的过渡区,保证炮弹的弹带能顺利地嵌入膛线中。
火炮射击时,炮弹在燃烧生成气体的加速推进之下,以越来越大的速率旋转,由于弹带和膛线的密切啮合,燃烧生成的气体总在炮弹的后面。
在设计身管时,应使其能经受内部产生的压力。
在制造过程中,应使身管壁获得人为的应力,以提高其强度,但制造工艺较复杂。
身管的加工包括深孔加工、膛线加工、药室加工,加工时必须注意要确保身管的垂直度对锻造身管毛坯件进行的深孔加工,需使用深孔钻等特殊的钻头和钻孔刀具。
使用钻孔刀具时可以一次性加工直径60mm以上的孔,然后再对剩余部分继续进行加工,这样可以加快钻孔速度。
无论是采用深孔钻还是采用钻孔刀具,都必须将身管表面进行仔细的切削,使身管壁表面光滑,如果加工不好的话,切削碎片会在加工表面形成划痕,炮管也会因此报废。
因此在切削条件的设置和切削油的选用上要十分注意。
为了确保钻出的孔的尺寸精度和表面光洁度,研削等精细加工是不可缺少的,所以要有适合各种类型炮管的研削工具。
膛线的加工是一种独特的加工方式所使用的是钻头和刀具。
要使用钻头反复加工数十次,才能达到所规定的膛线深度。
使用刀具时用机械调节刀具进刀量,进刀量每增加一次,就对膛线进行一次加工,直到达到所规定的膛线深度。
身管的自紧,即身管内表面受到超出材料屈服强度的压力,引起部分截面塑性变形,压力解除后,变形不能恢变原状。
此时身管内层有一个压缩预应力,而身管外层有一个拉伸预应力。
自紧处理中施加压力的方法包括:水压法、棒压法、气压法。
对于口径较大的炮管一般使用水压法。
利用超高利用超高利用超高利用超高水压机,甚至可以制成耐一万个标准大气压的超高压身管。
箱体的制造工艺包括毛坯铸造、人工时效热处理、涂漆、粗铣、半精铣、半精铣对中面、钻对中面孔、钻、攻顶盖四个螺纹孔、检查各处尺寸及精度。
而轴类零件的加工主要分为粗车、半精车、粗精磨各处外圆,各加工阶段一热处理为界。
轴类零件的定位基面,最常用的是两中心孔。
因为轴类零件各外圆表面、螺纹表面的同轴度及端面对轴线的垂直度是相互位置精度的主要项目,而这些表面的设计基准一般都是轴的中心线,采用两中心孔定位就能符合基准重合原则。
该轴需进行调质处理。
它应放在粗加工后,半精加工前进行。
如采用锻件毛坯,必须首先安排退火或正火处理。
该轴毛坯为热轧钢,可不必进行正火处理。