模具母体结构强度分析及优化方法
模具改善分析方案

模具改善分析方案模具是制造业中一种非常重要的工艺品,它的好坏直接影响到产品质量和生产效率。
随着制造业的不断发展和技术的不断进步,对模具质量和效率的要求也在不断提高,模具的改善和升级也成为了现代制造业最迫切的需求之一。
本文将从模具改善的角度出发,提出一些可行的分析方案,帮助制造业提高模具的质量和效率。
模具设计的分析和改善模具设计是影响模具质量和效率的关键因素之一,因此在模具设计方面的分析和改善是非常重要的。
模具设计的分析和改善主要从以下几个方面进行:1. 模具结构的分析和改善模具结构的设计和布局对于模具的质量和效率影响很大。
如果模具结构设计合理,不仅可以提高模具的使用寿命,而且可以提高生产效率,减少因模具结构不合理而导致的废品率和生产成本。
因此,在模具的设计阶段要对模具结构进行分析,提出可行的改善方案,不断提高模具的质量和效率。
2. 模具制造材料的分析和改善模具制造材料的选用也是影响模具质量和效率的重要因素之一。
合理的材料选用可以提高模具使用寿命,提高生产效率,减少废品率和生产成本。
因此,在模具制造材料方面要进行分析,选用合适的材料制造模具。
3. 模具表面处理的分析和改善模具表面处理是影响模具质量和效率的重要因素之一。
好的表面处理可以防止模具生锈、腐蚀,可以减少因模具表面处理不良而导致的废品率和生产成本。
因此,在模具表面处理方面要进行分析,选择合适的表面处理方式,提高模具质量和效率。
生产流程的分析和改善生产流程是影响模具质量和效率的另一个重要因素。
在生产流程的分析和改善中,要注重以下几个方面:1. 模具加工技术的改进模具加工技术的改进可以提高模具的精度和质量,减少生产成本。
因此,在模具加工技术方面要进行分析,提出可行的改进方案,提高模具的质量和效率。
2. 模具加工设备的改善模具加工设备的改善对于提高生产效率和减少生产成本也非常重要。
好的模具加工设备可以提高生产效率,减少废品率和生产成本。
因此,在模具加工设备方面要进行分析,选用现代化的设备,提高模具加工效率。
模具设计中的模具结构与强度分析
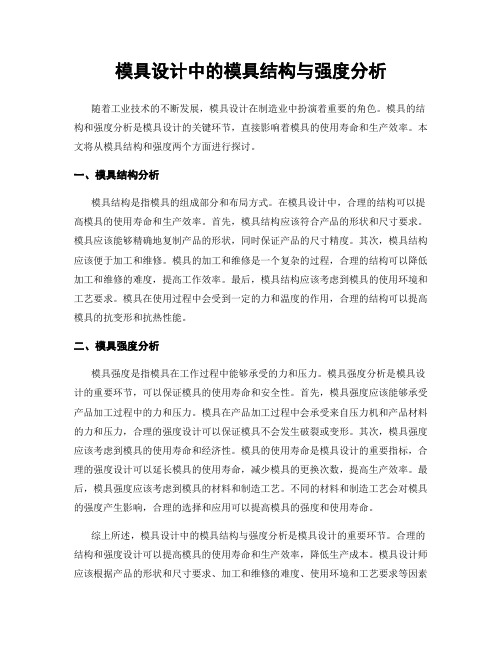
模具设计中的模具结构与强度分析随着工业技术的不断发展,模具设计在制造业中扮演着重要的角色。
模具的结构和强度分析是模具设计的关键环节,直接影响着模具的使用寿命和生产效率。
本文将从模具结构和强度两个方面进行探讨。
一、模具结构分析模具结构是指模具的组成部分和布局方式。
在模具设计中,合理的结构可以提高模具的使用寿命和生产效率。
首先,模具结构应该符合产品的形状和尺寸要求。
模具应该能够精确地复制产品的形状,同时保证产品的尺寸精度。
其次,模具结构应该便于加工和维修。
模具的加工和维修是一个复杂的过程,合理的结构可以降低加工和维修的难度,提高工作效率。
最后,模具结构应该考虑到模具的使用环境和工艺要求。
模具在使用过程中会受到一定的力和温度的作用,合理的结构可以提高模具的抗变形和抗热性能。
二、模具强度分析模具强度是指模具在工作过程中能够承受的力和压力。
模具强度分析是模具设计的重要环节,可以保证模具的使用寿命和安全性。
首先,模具强度应该能够承受产品加工过程中的力和压力。
模具在产品加工过程中会承受来自压力机和产品材料的力和压力,合理的强度设计可以保证模具不会发生破裂或变形。
其次,模具强度应该考虑到模具的使用寿命和经济性。
模具的使用寿命是模具设计的重要指标,合理的强度设计可以延长模具的使用寿命,减少模具的更换次数,提高生产效率。
最后,模具强度应该考虑到模具的材料和制造工艺。
不同的材料和制造工艺会对模具的强度产生影响,合理的选择和应用可以提高模具的强度和使用寿命。
综上所述,模具设计中的模具结构与强度分析是模具设计的重要环节。
合理的结构和强度设计可以提高模具的使用寿命和生产效率,降低生产成本。
模具设计师应该根据产品的形状和尺寸要求、加工和维修的难度、使用环境和工艺要求等因素进行综合考虑,制定合理的设计方案。
同时,模具设计师应该了解模具材料和制造工艺的特点,选择合适的材料和制造工艺,提高模具的强度和使用寿命。
只有在模具结构和强度分析上下功夫,才能设计出高质量的模具,推动制造业的发展。
模具设计中的结构优化与性能提升
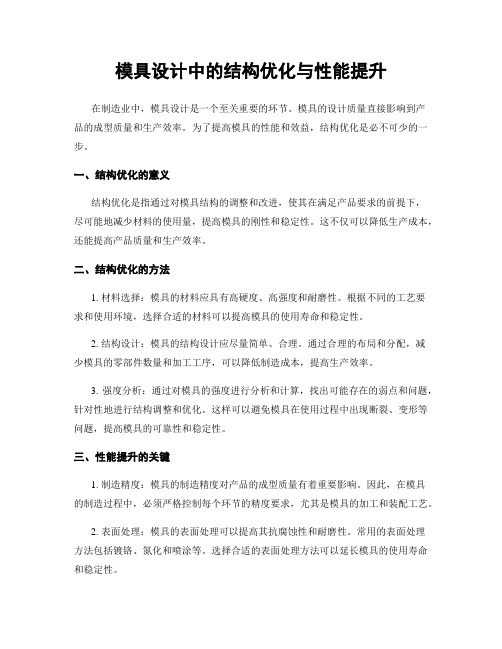
模具设计中的结构优化与性能提升在制造业中,模具设计是一个至关重要的环节。
模具的设计质量直接影响到产品的成型质量和生产效率。
为了提高模具的性能和效益,结构优化是必不可少的一步。
一、结构优化的意义结构优化是指通过对模具结构的调整和改进,使其在满足产品要求的前提下,尽可能地减少材料的使用量,提高模具的刚性和稳定性。
这不仅可以降低生产成本,还能提高产品质量和生产效率。
二、结构优化的方法1. 材料选择:模具的材料应具有高硬度、高强度和耐磨性。
根据不同的工艺要求和使用环境,选择合适的材料可以提高模具的使用寿命和稳定性。
2. 结构设计:模具的结构设计应尽量简单、合理。
通过合理的布局和分配,减少模具的零部件数量和加工工序,可以降低制造成本,提高生产效率。
3. 强度分析:通过对模具的强度进行分析和计算,找出可能存在的弱点和问题,针对性地进行结构调整和优化。
这样可以避免模具在使用过程中出现断裂、变形等问题,提高模具的可靠性和稳定性。
三、性能提升的关键1. 制造精度:模具的制造精度对产品的成型质量有着重要影响。
因此,在模具的制造过程中,必须严格控制每个环节的精度要求,尤其是模具的加工和装配工艺。
2. 表面处理:模具的表面处理可以提高其抗腐蚀性和耐磨性。
常用的表面处理方法包括镀铬、氮化和喷涂等。
选择合适的表面处理方法可以延长模具的使用寿命和稳定性。
3. 冷却系统:模具的冷却系统对于产品的成型速度和质量有着重要的影响。
通过合理设计冷却系统,可以提高模具的冷却效果,缩短生产周期,减少产品变形和缺陷。
四、结构优化案例分析以注塑模具为例,通过结构优化可以有效提升模具的性能和效益。
首先,通过对模具的结构进行优化,减少材料的使用量和加工工序,降低制造成本。
其次,通过强度分析,找出可能存在的弱点和问题,进行结构调整和优化,提高模具的可靠性和稳定性。
最后,通过制造精度的控制、表面处理和冷却系统的设计,提高模具的使用寿命和生产效率。
五、结论在模具设计中,结构优化是提高模具性能和效益的关键步骤。
机械设计中的结构优化与强度分析
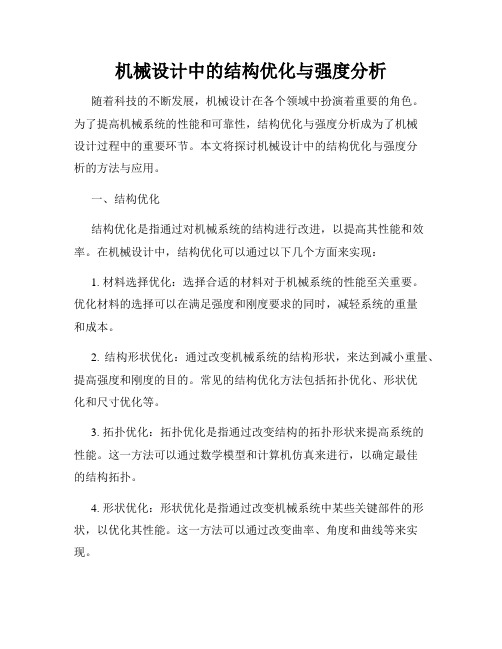
机械设计中的结构优化与强度分析随着科技的不断发展,机械设计在各个领域中扮演着重要的角色。
为了提高机械系统的性能和可靠性,结构优化与强度分析成为了机械设计过程中的重要环节。
本文将探讨机械设计中的结构优化与强度分析的方法与应用。
一、结构优化结构优化是指通过对机械系统的结构进行改进,以提高其性能和效率。
在机械设计中,结构优化可以通过以下几个方面来实现:1. 材料选择优化:选择合适的材料对于机械系统的性能至关重要。
优化材料的选择可以在满足强度和刚度要求的同时,减轻系统的重量和成本。
2. 结构形状优化:通过改变机械系统的结构形状,来达到减小重量、提高强度和刚度的目的。
常见的结构优化方法包括拓扑优化、形状优化和尺寸优化等。
3. 拓扑优化:拓扑优化是指通过改变结构的拓扑形状来提高系统的性能。
这一方法可以通过数学模型和计算机仿真来进行,以确定最佳的结构拓扑。
4. 形状优化:形状优化是指通过改变机械系统中某些关键部件的形状,以优化其性能。
这一方法可以通过改变曲率、角度和曲线等来实现。
5. 尺寸优化:尺寸优化是指通过改变机械系统中各个部件的尺寸,以提高其性能。
这一方法可以通过分析和计算来确定最佳的尺寸。
二、强度分析强度分析是机械设计中不可或缺的一步,它用于评估机械系统在工作条件下的强度和可靠性。
强度分析主要包括以下几个方面:1. 应力分析:应力分析是指对机械系统中各个部件的应力状态进行评估。
应力分析可以通过有限元分析等数值方法来进行,以确定机械系统在受力情况下的强度。
2. 刚度分析:刚度分析是指对机械系统的刚度进行评估。
刚度分析可以通过有限元分析等方法来进行,以确定机械系统的刚度是否满足设计要求。
3. 疲劳分析:疲劳分析是指对机械系统在长期使用情况下的疲劳寿命进行评估。
这一分析主要通过应力循环和材料疲劳性能等因素来确定机械系统的疲劳强度。
4. 可靠性分析:可靠性分析是指对机械系统在不确定条件下的可靠性进行评估。
这一分析可以通过概率统计方法和可靠性工程等方法来进行,以确定机械系统的可靠性。
注塑模具结构分析与优化方法研究

以某款汽车零部件的注塑模具为例,该模具在生产过程中出现了产品表面质 量较低、成型困难等问题。通过结构分析,发现浇口设计不合理,导致熔体填充 速度慢、剪切力过大。针对这一问题,采取了以下优化措施:
1、调整浇口大小和位置:将浇口从原来的点浇口改为扇形浇口,增大浇口 面积,降低熔体填充速度,减小剪切力。同时,将浇口位置调整至产品厚度的中 心位置,以减小填充过程中的阻力。
(2)材料优化:选用高强度、轻质、耐磨的模具材料,提高模具的使用寿 命。如采用粉末冶金模具材料等。
(3)工艺优化:通过调整制造工艺参数,提高模具的制造精度和表面质量。 如采用高速切削、超精加工等先进工艺。
四、基于ProE的注塑模具优化设 计实践
利用ProE软件进行注塑模具优化设计实践,主要包括以下步骤: 1、建立三维模型:利用ProE软件的建模功能,建立注塑模具的三维模型。
在今后的研究中,我们将进一步探讨基于ProE的注塑模具优化设计理论和方 法,以推动注塑模具设计水平的不断提升,为塑料制品行业的发展做出更大的贡 献。
感谢观看
2、模拟分析:利用ProE软件的模拟分析功能,对注塑模具进行模拟分析, 如充填模拟、冷却模拟等。
3、优化设计:根据模拟分析结果,对注塑模具进行优化设计,如调整浇口 位置、改变冷却水路等。
4、模拟验证:对优化后的注塑模具进行模拟验证,确保优化效果符合预期。
ห้องสมุดไป่ตู้
五、结论
本次演示基于ProE软件,对注塑模具的优化设计进行了研究。通过改变模具 结构、选用优质模具材料和调整制造工艺参数等方法,可实现注塑模具的优化设 计。实践表明,利用ProE软件进行注塑模具优化设计,可有效提高生产效率、降 低制造成本、提高模具可靠性。
3、温度控制系统:注塑模具的温度控制系统主要包括加热和冷却系统。加 热系统用于提高模具温度,使其高于塑料熔点的温度,以保证塑料熔体在注入型 腔时能够迅速填充。冷却系统则用于在塑料制品成型后将模具温度降至一定范围 内,以防止由于模具温度过高而造成塑料制品收缩过大或者变形。
冲压磨具结构的模拟与优化
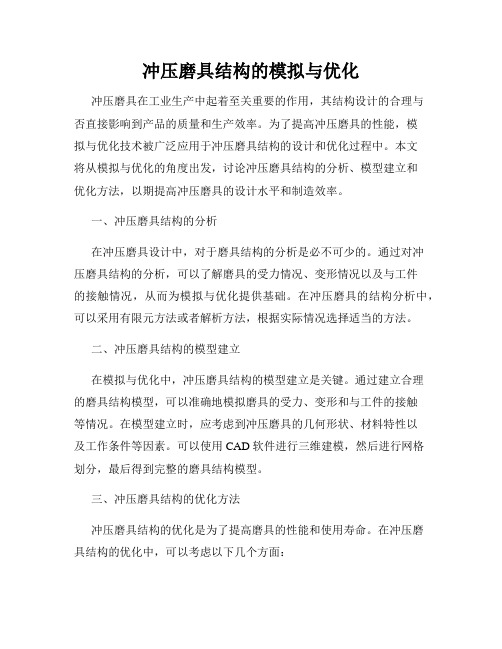
冲压磨具结构的模拟与优化冲压磨具在工业生产中起着至关重要的作用,其结构设计的合理与否直接影响到产品的质量和生产效率。
为了提高冲压磨具的性能,模拟与优化技术被广泛应用于冲压磨具结构的设计和优化过程中。
本文将从模拟与优化的角度出发,讨论冲压磨具结构的分析、模型建立和优化方法,以期提高冲压磨具的设计水平和制造效率。
一、冲压磨具结构的分析在冲压磨具设计中,对于磨具结构的分析是必不可少的。
通过对冲压磨具结构的分析,可以了解磨具的受力情况、变形情况以及与工件的接触情况,从而为模拟与优化提供基础。
在冲压磨具的结构分析中,可以采用有限元方法或者解析方法,根据实际情况选择适当的方法。
二、冲压磨具结构的模型建立在模拟与优化中,冲压磨具结构的模型建立是关键。
通过建立合理的磨具结构模型,可以准确地模拟磨具的受力、变形和与工件的接触等情况。
在模型建立时,应考虑到冲压磨具的几何形状、材料特性以及工作条件等因素。
可以使用CAD软件进行三维建模,然后进行网格划分,最后得到完整的磨具结构模型。
三、冲压磨具结构的优化方法冲压磨具结构的优化是为了提高磨具的性能和使用寿命。
在冲压磨具结构的优化中,可以考虑以下几个方面:1. 材料选择优化:选择合适的材料可以提高冲压磨具的强度和硬度,延长磨具的使用寿命。
可以通过优化材料的力学性能和热处理工艺等方法,提高磨具的耐磨性和抗变形性能。
2. 结构形状优化:通过对磨具的结构形状进行优化,可以减小磨具的重量、降低磨具与工件的摩擦、改善磨具的刚度和刚性等。
在结构形状优化中,可以使用CAD软件进行参数化建模,通过改变参数的取值范围,得到不同结构形状的磨具。
3. 热处理工艺优化:热处理工艺对冲压磨具的性能有着重要的影响。
通过优化热处理工艺,可以提高冲压磨具的硬度、韧性和抗疲劳能力。
可以根据不同材料的特性和磨具的使用条件,选择合适的热处理工艺参数,以达到最佳的磨具性能。
四、冲压磨具模拟与优化的案例研究通过一个具体的案例研究,可以更好地理解冲压磨具的模拟与优化过程。
模具设计中的构造优化与强度分析

模具设计中的构造优化与强度分析在制造业中,模具设计起着至关重要的作用。
模具是用于制造各种产品的工具,其设计质量直接影响产品的质量和生产效率。
在模具设计中,构造优化和强度分析是两个重要的方面,它们能够提高模具的性能和寿命。
构造优化是指通过对模具结构进行合理的调整和改进,以提高模具的性能和效率。
在模具设计中,构造优化可以从多个方面进行考虑。
首先,要考虑模具的材料选择和结构设计。
不同的材料具有不同的物理性质和机械性能,选择合适的材料可以提高模具的强度和耐用性。
其次,要考虑模具的结构设计。
合理的结构设计可以减少模具的重量和材料消耗,提高模具的制造和使用效率。
此外,还可以通过优化模具的冷却系统和排气系统,提高模具的冷却效果和产品质量。
强度分析是指通过对模具进行力学分析,评估模具的强度和稳定性。
在模具设计中,强度分析可以通过有限元分析等方法进行。
有限元分析是一种常用的数值分析方法,可以模拟模具在实际工作条件下的受力情况,评估模具的强度和变形情况。
通过强度分析,可以确定模具的受力部位和受力情况,进而进行针对性的结构优化和改进。
强度分析还可以帮助设计师预测模具的寿命和故障情况,提前采取相应的措施,延长模具的使用寿命。
在模具设计中,构造优化和强度分析是相互关联的。
构造优化可以提高模具的性能和效率,而强度分析可以验证和评估构造优化的效果。
通过结合构造优化和强度分析,可以设计出更加优化和高效的模具。
除了构造优化和强度分析,模具设计中还有其他一些重要的考虑因素。
例如,模具的制造工艺和装配要求。
模具的制造工艺直接影响模具的制造成本和周期,因此需要在设计过程中考虑到制造的可行性和效率。
此外,模具的装配要求也需要在设计中进行充分考虑,以确保模具的装配精度和稳定性。
总之,模具设计中的构造优化和强度分析是两个重要的方面。
通过合理的构造优化和强度分析,可以提高模具的性能和效率,延长模具的使用寿命。
在模具设计中,还需要考虑其他一些因素,如制造工艺和装配要求。
模具结构强度分析方法
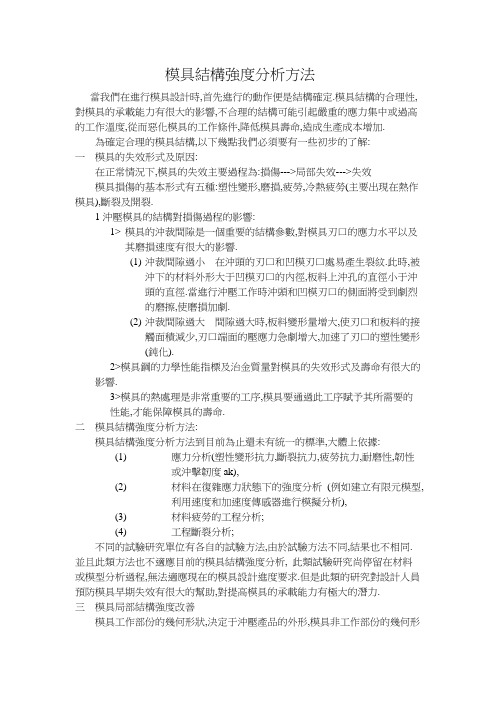
模具結構強度分析方法當我們在進行模具設計時,首先進行的動作便是結構確定.模具結構的合理性,對模具的承載能力有很大的影響,不合理的結構可能引起嚴重的應力集中或過高的工作溫度,從而惡化模具的工作條件,降低模具壽命,造成生產成本增加.為確定合理的模具結構,以下幾點我們必須要有一些初步的了解:一模具的失效形式及原因:在正常情況下,模具的失效主要過程為:損傷--->局部失效--->失效模具損傷的基本形式有五種:塑性變形,磨損,疲勞,冷熱疲勞(主要出現在熱作模具),斷裂及開裂.1沖壓模具的結構對損傷過程的影響:1>模具的沖裁間隙是一個重要的結構參數,對模具刃口的應力水平以及其磨損速度有很大的影響.(1)沖裁間隙過小在沖頭的刃口和凹模刃口處易產生裂紋.此時,被沖下的材料外形大于凹模刃口的內徑,板料上沖孔的直徑小于沖頭的直徑.當進行沖壓工作時沖頭和凹模刃口的側面將受到劇烈的磨擦,使磨損加劇.(2)沖裁間隙過大間隙過大時,板料變形量增大,使刃口和板料的接觸面積減少,刃口端面的壓應力急劇增大,加速了刃口的塑性變形(鈍化).2>模具鋼的力學性能指標及治金質量對模具的失效形式及壽命有很大的影響.3>模具的熱處理是非常重要的工序,模具要通過此工序賦予其所需要的性能,才能保障模具的壽命.二模具結構強度分析方法:模具結構強度分析方法到目前為止還未有統一的標準,大體上依據:(1)應力分析(塑性變形抗力,斷裂抗力,疲勞抗力,耐磨性,韌性或沖擊韌度ak),(2)材料在復雜應力狀態下的強度分析(例如建立有限元模型,利用速度和加速度傳感器進行模擬分析),(3)材料疲勞的工程分析;(4)工程斷裂分析;不同的試驗研究單位有各自的試驗方法,由於試驗方法不同,結果也不相同.並且此類方法也不適應目前的模具結構強度分析, 此類試驗研究尚停留在材料或模型分析過程,無法適應現在的模具設計進度要求.但是此類的研究對設計人員預防模具早期失效有很大的幫助,對提高模具的承載能力有極大的潛力.三模具局部結構強度改善模具工作部份的幾何形狀,決定于沖壓產品的外形,模具非工作部份的幾何形狀決定於壓力機的結構.因此,設計模具時,其工作部份及非工作部份的幾何形狀,很難隨意改變,但是改變模具的局部結構來提高模具的承載能力方面,還是可以挖掘出巨大的潛力.下面我們就一些模具設計中的實例給大家作一些講解:1>鑲套結構:在模具設計過程中,為在局部獲得高的抗壓強度或高的耐磨性,要求<圖示3-1>圖3-3-1中沖頭兩段尺寸相差較大,屬於突變式尺寸過渡,極易在尺寸突變處引起較嚴重的應力集中而導致早期疲勞斷裂或一次性折斷.如采用圖3-3-2或圖3-3-3形式,將突變式尺寸過渡改為漸變式尺寸過渡,可明顯延長沖頭壽命.。
模具结构设计中的优化研究
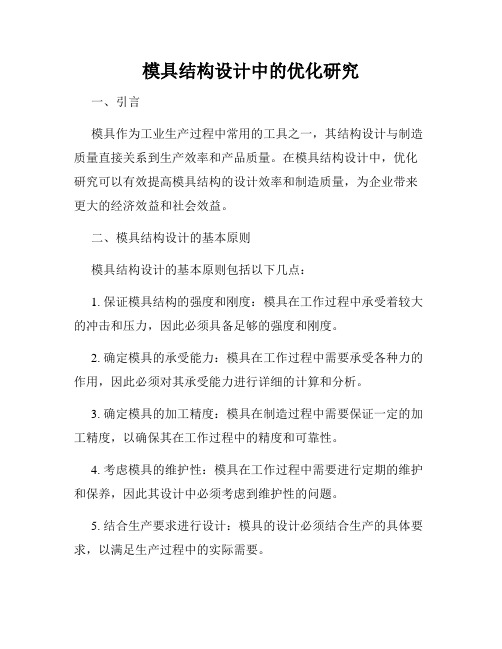
模具结构设计中的优化研究一、引言模具作为工业生产过程中常用的工具之一,其结构设计与制造质量直接关系到生产效率和产品质量。
在模具结构设计中,优化研究可以有效提高模具结构的设计效率和制造质量,为企业带来更大的经济效益和社会效益。
二、模具结构设计的基本原则模具结构设计的基本原则包括以下几点:1. 保证模具结构的强度和刚度:模具在工作过程中承受着较大的冲击和压力,因此必须具备足够的强度和刚度。
2. 确定模具的承受能力:模具在工作过程中需要承受各种力的作用,因此必须对其承受能力进行详细的计算和分析。
3. 确定模具的加工精度:模具在制造过程中需要保证一定的加工精度,以确保其在工作过程中的精度和可靠性。
4. 考虑模具的维护性:模具在工作过程中需要进行定期的维护和保养,因此其设计中必须考虑到维护性的问题。
5. 结合生产要求进行设计:模具的设计必须结合生产的具体要求,以满足生产过程中的实际需要。
三、模具结构优化的方法模具结构优化的方法包括以下几种:1. 优化模具结构:通过对模具结构进行分析和计算,优化模具的结构,以提高其强度和刚度。
2. 优化模具材料:选择合适的材料,并进行热处理和表面处理,以提高其硬度和耐磨性。
3. 优化模具加工工艺:通过选择合适的加工工艺和设备,提高模具的加工精度和生产效率。
4. 优化模具的表面处理:通过表面涂层、气体渗入等方式,提高模具的表面硬度和耐腐蚀性。
五、模具结构优化的实践应用在模具结构设计中,优化研究是一个极其重要的课题。
优化研究可以帮助企业提高产品的制造质量和生产效率,减少生产成本,从而提高企业的经济效益。
因此,在模具结构设计中,应当积极开展优化研究工作,并结合实际需要,加以实践。
结论综上所述,模具结构设计中的优化研究是一个十分重要的工作,其影响着企业的生产效率和产品质量。
在模具结构设计中,需要遵循一定的基本原则,并通过优化了模具结构、材料、加工工艺等方面的设计,来提高模具的强度、刚度、加工精度等性能指标。
模具产品的优化方案

模具产品的优化方案概述模具是工业生产中常用的一种工具,用于制造各种产品的形状和结构。
模具产品的质量和性能直接影响着产品的生产效率和成本。
为了提高模具产品的质量和性能,需要进行优化方案的研究和实施。
本文将从以下几个方面介绍模具产品的优化方案:1.材料选择2.结构设计3.表面处理4.工艺控制5.模具维护材料选择材料选择是模具产品优化的关键步骤。
合适的材料能够提供良好的机械性能和耐磨性,能够有效延长模具的使用寿命并提高产品质量。
常用的模具材料包括钢、铝、塑料等。
选材时需要考虑以下几个因素:•强度和刚度要求:根据产品的使用环境和工作条件选择合适的材料强度和刚度。
•耐磨性要求:对于需要经常与产品接触的模具,应选择具有良好耐磨性的材料。
•腐蚀和氧化抗性:对于可能接触腐蚀性物质或需要抵抗氧化的模具,选择具有良好抗腐蚀和抗氧化性能的材料。
结构设计模具产品的结构设计对产品的质量和性能影响很大。
合理的结构设计可以提高产品的准确度、稳定性和生产效率。
以下是一些常见的结构设计优化方案:1.减少零件数量:通过合理的设计,尽量减少模具产品的零件数量,减少制造成本和装配工序。
2.提高刚度:增加模具产品的刚度,能够有效减少形变和振动,提高加工精度和产品的表面质量。
3.增加冷却系统:合理设计冷却系统,能够有效降低模具温度,提高成型周期和产品质量。
4.考虑易于维护性:在结构设计中考虑模具的易于维护性,包括易于拆卸、更换零件和清洁等。
表面处理模具产品的表面处理对产品的质量和外观有很大影响。
合适的表面处理能够提高产品的光洁度、耐磨性和耐腐蚀性。
常见的表面处理方法包括:1.镀铬:镀铬能提高模具的硬度和抗氧化性能,使得模具能够更好地抵抗磨损和腐蚀。
2.氮化:氮化处理能提高模具的硬度和耐磨性,对于需要经常与产品接触的模具特别有效。
3.表面喷涂:通过喷涂一层特殊涂料或涂层,能够提高模具的耐磨性和耐腐蚀性。
4.抛光:抛光能够提高模具的表面光洁度和减少摩擦阻力,使得产品表面更加光滑。
模具改善分析方案
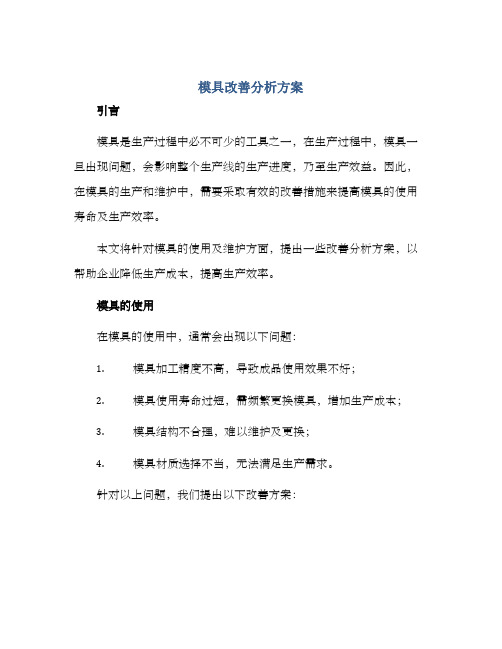
模具改善分析方案引言模具是生产过程中必不可少的工具之一,在生产过程中,模具一旦出现问题,会影响整个生产线的生产进度,乃至生产效益。
因此,在模具的生产和维护中,需要采取有效的改善措施来提高模具的使用寿命及生产效率。
本文将针对模具的使用及维护方面,提出一些改善分析方案,以帮助企业降低生产成本,提高生产效率。
模具的使用在模具的使用中,通常会出现以下问题:1.模具加工精度不高,导致成品使用效果不好;2.模具使用寿命过短,需频繁更换模具,增加生产成本;3.模具结构不合理,难以维护及更换;4.模具材质选择不当,无法满足生产需求。
针对以上问题,我们提出以下改善方案:加强模具加工工艺加工精度是影响模具使用效果的关键因素之一。
针对加工精度不高的问题,可以通过采用更先进的数控加工技术,来提高模具加工精度。
优化模具材质选择合适的模具材质,可以有效地提高模具使用寿命并降低更换模具的频率。
其中,可以采用高强度、耐腐蚀、高温度的材质,以满足生产需求。
设计合理的模具结构模具结构的设计是影响模具维护及更换的重要因素之一。
针对难以维护及更换的问题,可以在模具设计时,考虑到易拆装、易清洗的要求,以方便维修及更换。
模具的维护在模具的使用过程中,维护工作同样重要。
通常会出现以下问题:1.模具零件损坏或缺失,导致模具无法使用;2.模具表面易受损,需要定期涂层;3.模具维护工作不及时或不专业,导致模具寿命缩短。
针对以上问题,我们提出以下改善方案:建立模具维护规范建立模具维护规范,对模具进行定期检查和维护,可有效地延长模具使用寿命,并降低更换模具的频率。
模具表面涂层技术的推广定期进行模具表面涂层,能够有效地保护模具表面,同时降低模具维护工作量,并延长模具使用寿命。
建立专业维护团队建立专业的模具维护团队,能够有效地避免维护工作不及时或不专业的问题,同时提高模具维护的效率。
结论综上所述,模具改善分析方案对于降低生产成本,提高生产效率具有重要意义。
冲压磨具结构优化提升产品质量与效能
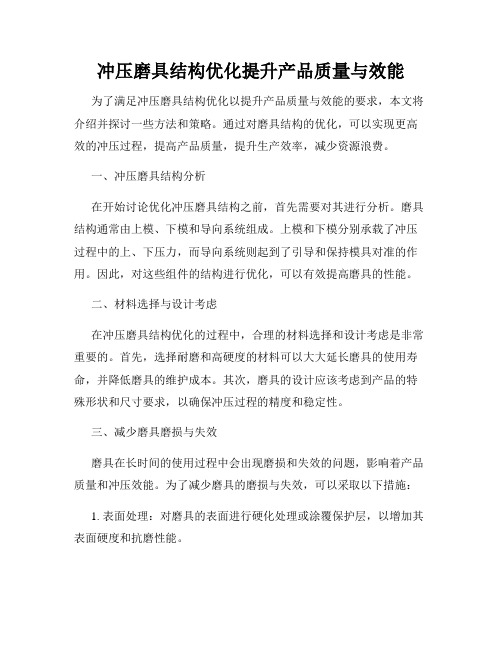
冲压磨具结构优化提升产品质量与效能为了满足冲压磨具结构优化以提升产品质量与效能的要求,本文将介绍并探讨一些方法和策略。
通过对磨具结构的优化,可以实现更高效的冲压过程,提高产品质量,提升生产效率,减少资源浪费。
一、冲压磨具结构分析在开始讨论优化冲压磨具结构之前,首先需要对其进行分析。
磨具结构通常由上模、下模和导向系统组成。
上模和下模分别承载了冲压过程中的上、下压力,而导向系统则起到了引导和保持模具对准的作用。
因此,对这些组件的结构进行优化,可以有效提高磨具的性能。
二、材料选择与设计考虑在冲压磨具结构优化的过程中,合理的材料选择和设计考虑是非常重要的。
首先,选择耐磨和高硬度的材料可以大大延长磨具的使用寿命,并降低磨具的维护成本。
其次,磨具的设计应该考虑到产品的特殊形状和尺寸要求,以确保冲压过程的精度和稳定性。
三、减少磨具磨损与失效磨具在长时间的使用过程中会出现磨损和失效的问题,影响着产品质量和冲压效能。
为了减少磨具的磨损与失效,可以采取以下措施:1. 表面处理:对磨具的表面进行硬化处理或涂覆保护层,以增加其表面硬度和抗磨性能。
2. 冷却系统:在磨具结构中设置冷却系统,通过降低温度来减少磨具的热变形和磨损。
3. 润滑措施:在冲压过程中使用适当的润滑剂,减少磨具与工件之间的摩擦,从而降低磨损。
四、优化冲压参数除了磨具结构的优化外,还应重视冲压参数的调整和优化。
合理的冲压参数可以提高产品的尺寸精度和表面质量,减少因冲压过程引起的变形和缺陷。
1. 压力控制:通过控制上下模的压力大小和分布,可以减少冲压过程中的变形和拉伸。
2. 速度控制:控制上下模的运动速度,可以影响冲压过程中的应变率和冷却速度,进而影响产品的性能。
3. 模具间隙控制:合理的模具间隙设置可以减小工件的变形和提高表面质量。
五、采用先进技术与设备通过引入先进的冲压技术和设备,可以进一步提升产品质量和效能。
1. CAD/CAM技术:采用计算机辅助设计和制造技术,可以提高磨具结构的设计精度和效率。
模具结构与优化方案

模具结构与优化方案
模具是工业产品的重要辅助品,其结构设计和优化是提高模具质量和效率的关键。
模具结构与优化方案主要包括以下几个方面:材料选择、结构设计、加工工艺和热处理。
首先,材料选择对模具的使用寿命和耐磨性有着重要影响。
常用模具材料有高速钢、硬质合金、塑料模和粉末冶金材料等。
根据具体的使用环境和工艺要求,选择适合的材料可以提高模具的耐磨性和抗变形能力。
其次,结构设计是模具性能优化的关键。
合理的结构设计可以提高模具的强度和刚度,降低变形和磨损。
在设计过程中,需要考虑多个因素,如受力情况、热胀冷缩、工艺要求等,选择合适的结构形式和参数。
再次,加工工艺是模具结构优化的重要环节。
采用先进的数控加工技术和高精度设备,可以保证模具的精度和表面质量。
此外,采用先进的装配工艺和检测手段,可以提高模具的装配精度和质量稳定性。
最后,热处理是模具结构优化中的关键一环。
通过合适的热处理工艺,可以改善模具的硬度和耐磨性。
常用的热处理方法包括淬火、回火、表面处理等,根据模具材料和使用要求选择适宜的热处理工艺,可以提高模具的使用寿命和性能稳定性。
综上所述,模具结构与优化方案需要综合考虑材料选择、结构设计、加工工艺和热处理等多个方面。
只有在这些方面的综合
优化下,模具才能具有更好的性能和使用寿命,从而提高工业产品的质量和效率。
注塑模具设计中的结构优化与安全性能提升
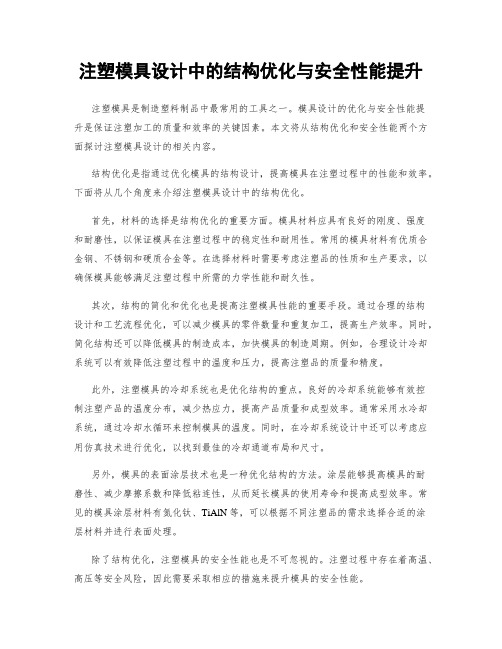
注塑模具设计中的结构优化与安全性能提升注塑模具是制造塑料制品中最常用的工具之一。
模具设计的优化与安全性能提升是保证注塑加工的质量和效率的关键因素。
本文将从结构优化和安全性能两个方面探讨注塑模具设计的相关内容。
结构优化是指通过优化模具的结构设计,提高模具在注塑过程中的性能和效率。
下面将从几个角度来介绍注塑模具设计中的结构优化。
首先,材料的选择是结构优化的重要方面。
模具材料应具有良好的刚度、强度和耐磨性,以保证模具在注塑过程中的稳定性和耐用性。
常用的模具材料有优质合金钢、不锈钢和硬质合金等。
在选择材料时需要考虑注塑品的性质和生产要求,以确保模具能够满足注塑过程中所需的力学性能和耐久性。
其次,结构的简化和优化也是提高注塑模具性能的重要手段。
通过合理的结构设计和工艺流程优化,可以减少模具的零件数量和重复加工,提高生产效率。
同时,简化结构还可以降低模具的制造成本,加快模具的制造周期。
例如,合理设计冷却系统可以有效降低注塑过程中的温度和压力,提高注塑品的质量和精度。
此外,注塑模具的冷却系统也是优化结构的重点。
良好的冷却系统能够有效控制注塑产品的温度分布,减少热应力,提高产品质量和成型效率。
通常采用水冷却系统,通过冷却水循环来控制模具的温度。
同时,在冷却系统设计中还可以考虑应用仿真技术进行优化,以找到最佳的冷却通道布局和尺寸。
另外,模具的表面涂层技术也是一种优化结构的方法。
涂层能够提高模具的耐磨性、减少摩擦系数和降低粘连性,从而延长模具的使用寿命和提高成型效率。
常见的模具涂层材料有氮化钛、TiAlN等,可以根据不同注塑品的需求选择合适的涂层材料并进行表面处理。
除了结构优化,注塑模具的安全性能也是不可忽视的。
注塑过程中存在着高温、高压等安全风险,因此需要采取相应的措施来提升模具的安全性能。
首先,模具的安装和调试过程需要严格按照操作规程进行,保证操作人员的安全。
模具安装时需要保证模具固定可靠,防止模具在注塑过程中的震动和松动。
模具改善分析方案

模具改善分析方案随着现代工业化的不断发展,模具已成为生产过程中不可或缺的一部分。
模具的质量和设计对于产品的成本和质量影响非常大,因此对模具进行改善分析是非常重要的工作。
本文将介绍针对模具改善所需要考虑的要素以及如何有效地进行模具改善分析的方案。
模具改善的要素要对模具进行改善分析,需要考虑以下要素:1. 模具的使用情况首先需要了解模具的使用情况,包括生产周期、使用次数、模具损耗情况等。
这些信息可以帮助我们更好地评估模具的使用寿命和维护情况,从而确定是否需要进行改善。
2. 模具的结构和材料对于模具的改善分析,需要考虑模具的结构和材料,评估模具的制造质量是否达标,确定模具的受力情况,避免设计或加工方面的缺陷对模具的影响。
3. 模具的设计和制造模具的设计和制造是影响模具质量的重要因素,需要考虑设计方案和加工工艺是否合理。
同时也需要考虑制造厂家的技术水平和经验,避免出现加工或质量方面的缺陷。
4. 模具的维护情况模具的维护情况对于模具的寿命和效率有着非常重要的影响。
因此需要对模具的维护情况进行全面的评估和分析,以确定是否需要进行更换或维修。
模具改善分析方案针对以上要素,可以制定一系列的模具改善分析方案:1. 模具使用情况分析对于模具的使用情况,可以通过生产录像、产品质检等手段进行全面的分析和评估,以确定模具的使用情况,进而确定是否需要进行改善。
2. 模具设计和制造分析模具的设计和制造是影响模具质量的重要因素。
可以通过对模具的CAD图纸进行评估,采用质量标准、制造规范等手段进行评估,进而确定模具的结构、材料和制造方式。
3. 模具维护情况分析模具的维护情况对于模具的效率、寿命和使用效果有着非常重要的影响。
可以通过保养记录、使用验证、检验报告等手段进行评估,进而确定模具的维护情况,判断是否需要进行更换或维修。
4. 模具改善方案制定根据以上分析和评估,可以制定一系列模具改善方案,包括模具的结构、材料、制造工艺、维护等方面的改善,以达到提高模具效率和质量的目的。
机械设计中的结构强度分析与优化
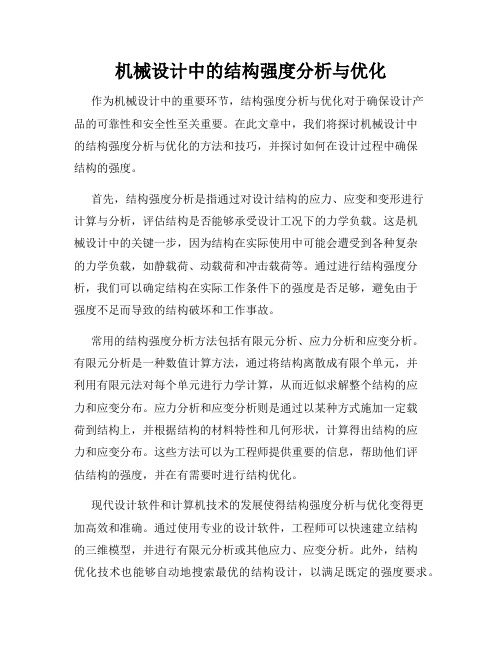
机械设计中的结构强度分析与优化作为机械设计中的重要环节,结构强度分析与优化对于确保设计产品的可靠性和安全性至关重要。
在此文章中,我们将探讨机械设计中的结构强度分析与优化的方法和技巧,并探讨如何在设计过程中确保结构的强度。
首先,结构强度分析是指通过对设计结构的应力、应变和变形进行计算与分析,评估结构是否能够承受设计工况下的力学负载。
这是机械设计中的关键一步,因为结构在实际使用中可能会遭受到各种复杂的力学负载,如静载荷、动载荷和冲击载荷等。
通过进行结构强度分析,我们可以确定结构在实际工作条件下的强度是否足够,避免由于强度不足而导致的结构破坏和工作事故。
常用的结构强度分析方法包括有限元分析、应力分析和应变分析。
有限元分析是一种数值计算方法,通过将结构离散成有限个单元,并利用有限元法对每个单元进行力学计算,从而近似求解整个结构的应力和应变分布。
应力分析和应变分析则是通过以某种方式施加一定载荷到结构上,并根据结构的材料特性和几何形状,计算得出结构的应力和应变分布。
这些方法可以为工程师提供重要的信息,帮助他们评估结构的强度,并在有需要时进行结构优化。
现代设计软件和计算机技术的发展使得结构强度分析与优化变得更加高效和准确。
通过使用专业的设计软件,工程师可以快速建立结构的三维模型,并进行有限元分析或其他应力、应变分析。
此外,结构优化技术也能够自动地搜索最优的结构设计,以满足既定的强度要求。
通过这些工具和技术的应用,设计师可以在较短的时间内得到满足结构强度要求的最优设计,提高产品的性能和可靠性。
然而,仅仅满足结构的强度要求并不是设计的唯一目标。
在实际设计中,我们还需要考虑其他因素,如重量、成本和可制造性等。
这就需要在结构强度分析的基础上进行结构优化,以满足更多的设计要求。
结构优化主要分为两个方面:形状优化和材料优化。
形状优化是通过改变结构的几何形状,以达到最优设计的目的。
例如,通过改变零件的厚度或截面形状,可以减少结构的应力和应变分布,从而提高结构的强度。
冲压磨具结构分析技巧掌握核心优化路径

冲压磨具结构分析技巧掌握核心优化路径冲压磨具是现代制造业中常用的工具,在模具设计和制造过程中起着至关重要的作用。
为了提高冲压磨具的质量和效率,需要对其结构进行分析,并掌握相应的优化路径。
本文将介绍冲压磨具结构分析的技巧,并探讨核心的优化路径。
一、冲压磨具结构分析技巧1.1 切削力分析:在进行冲压加工时,切削力是一个重要的参数。
通过切削力分析可以了解材料在切削过程中的变形情况,从而对冲压磨具的结构进行优化。
切削力的分析方法包括经验公式法、有限元法等。
1.2 应力分析:应力分析是对冲压磨具结构进行评估的重要手段。
通过应力分析可以确定磨具在工作过程中受到的应力分布情况,从而针对性地进行结构强度的优化。
应力分析可以采用有限元分析方法。
1.3 前置工艺分析:在进行冲压加工之前,需要进行前置工艺分析。
前置工艺分析包括工件的材料分析、冲压工艺参数分析等,通过分析可以确定冲压磨具的合理结构和工艺参数,提高冲压磨具的制造效率和加工质量。
二、冲压磨具结构优化路径2.1 材料选择优化:冲压磨具的材料选择直接影响其性能和寿命。
优化材料选择可以考虑磨具的工作环境、所需机械性能等因素,选用合适的高强度和耐磨材料,提高冲压磨具的使用寿命。
2.2 结构设计优化:冲压磨具的结构设计需要考虑到切削力、应力分布等因素。
通过改变磨具的结构参数,如磨具的几何形状、尺寸等,可以达到减小切削力和应力集中的目的,提高冲压磨具的性能。
2.3 表面处理优化:冲压磨具工作时会受到磨损和疲劳的影响。
通过表面处理,如热处理、表面涂层等,可以提高冲压磨具的耐磨性和抗疲劳性,延长其使用寿命。
2.4 工艺调整优化:冲压磨具在制造过程中,需要配合相应的工艺流程。
通过优化工艺流程,如磨具的热处理工艺、加工工艺等,可以提高冲压磨具的制造效率和加工质量。
三、总结冲压磨具结构分析技巧的掌握以及核心优化路径的把握是提高冲压磨具质量和效率的重要手段。
通过切削力分析、应力分析和前置工艺分析,可以了解冲压磨具的工作状态,为优化提供参考。
冲压磨具结构的优化策略优化冲压磨具结构提高生产效率与质量的策略
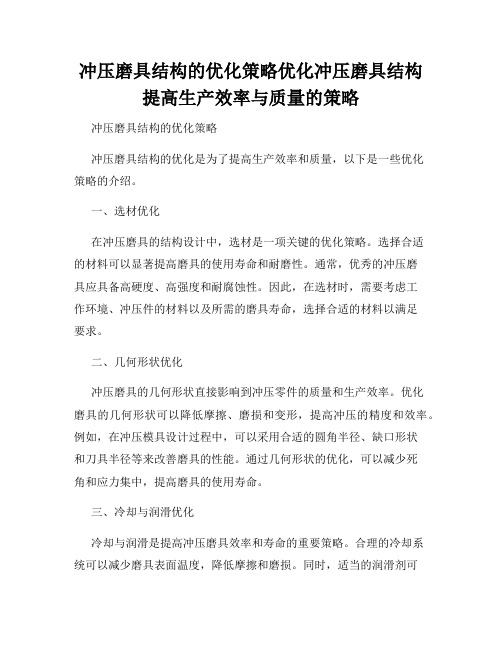
冲压磨具结构的优化策略优化冲压磨具结构提高生产效率与质量的策略冲压磨具结构的优化策略冲压磨具结构的优化是为了提高生产效率和质量,以下是一些优化策略的介绍。
一、选材优化在冲压磨具的结构设计中,选材是一项关键的优化策略。
选择合适的材料可以显著提高磨具的使用寿命和耐磨性。
通常,优秀的冲压磨具应具备高硬度、高强度和耐腐蚀性。
因此,在选材时,需要考虑工作环境、冲压件的材料以及所需的磨具寿命,选择合适的材料以满足要求。
二、几何形状优化冲压磨具的几何形状直接影响到冲压零件的质量和生产效率。
优化磨具的几何形状可以降低摩擦、磨损和变形,提高冲压的精度和效率。
例如,在冲压模具设计过程中,可以采用合适的圆角半径、缺口形状和刀具半径等来改善磨具的性能。
通过几何形状的优化,可以减少死角和应力集中,提高磨具的使用寿命。
三、冷却与润滑优化冷却与润滑是提高冲压磨具效率和寿命的重要策略。
合理的冷却系统可以减少磨具表面温度,降低摩擦和磨损。
同时,适当的润滑剂可以减少磨具与工件之间的摩擦,提高磨具的耐磨性能。
因此,在冲压磨具结构设计中,需要考虑冷却系统的布置和润滑剂的选择,以确保磨具的正常运行和长期稳定的性能。
四、模具加工工艺优化模具加工工艺优化是提高冲压磨具结构质量和生产效率的重要策略。
通过合理的刀具选择、切割参数和切削路径等,可以提高磨具加工的精度和效率。
同时,在模具加工过程中,需要注意避免热处理后的变形和残余应力的产生。
因此,进行适当的热处理和机加工工艺调整,可以优化冲压模具的结构和性能。
五、设计优化软件的应用在冲压磨具结构的优化过程中,设计优化软件的应用可以提高设计效率和设计准确性。
通过使用CAD、CAE和CAM等软件工具,可以对磨具的结构进行仿真分析和优化。
同时,采用计算机辅助设计技术,可以降低磨具的制造成本和加工周期,实现优化冲压磨具结构的目标。
总之,优化冲压磨具结构是提高生产效率和质量的重要策略。
通过选材优化、几何形状优化、冷却与润滑优化、模具加工工艺优化以及设计优化软件的应用,可以实现磨具结构的持续改进和优化,提高冲压生产的效率和质量。
模具结构改善分析报告
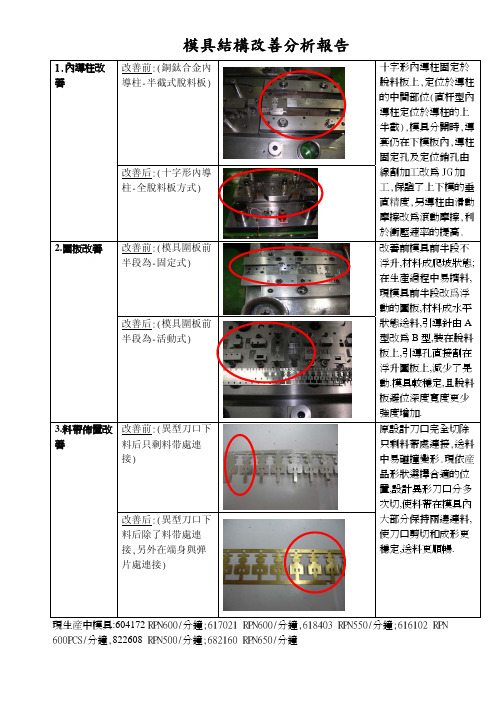
十字形內導柱固定於 脫料板上,定位於導柱 的中間部位(直杆型內 導柱定位於導柱的上 半截),模具分開時,導 套仍在下模板內,導柱 固定孔及定位銷孔由 線割加工改為 JG 加 工,保證了上下模的垂 直精度,另導柱由滑動 摩擦改為滾動摩擦,利 於衝壓速率的提高. 改善前模具前半段不 浮升,材料成爬坡狀態; 在生產過程中易擠料, 現模具前半段改爲浮 動的圍板,材料成水平 狀態送料,引導針由 A 型改為 B 型,裝在脫料 板上,引導孔直接割在 浮升圍板上,減少了晃 動.模具較穩定,且脫料 板避位深度寬度更少 強度增加. 原設計刀口完全切除 只剩料帶處連接,送料 中易碰撞變形.現依産 品形狀選擇合適的位 置,設計異形刀口分多 次切,使料帶在模具內 大部分保持兩邊連料, 使刀口剪切和成形更 穩定,送料更順暢.
1.內導柱改 善
模具結構改善分析報告
改善前:(銅鈦合金內 導柱-半截式脫料板)
改善后:(十字形內導 柱-全脫料板方式)
2.圍板改善
改善前:(模Biblioteka 圍板前 半段為-固定式)改善后:(模具圍板前 半段為-活動式)
3.料帶佈置改 改善前:(異型刀口下
善
料后只剩料带處連
接)
改善后:(異型刀口下 料后除了料带處連 接,另外在端身與弹 片處連接)
現生産中模具:604172 RPN600/分鐘;617021 RPN600/分鐘,618403 RPN550/分鐘;616102 RPN 600PCS/分鐘,822608 RPN500/分鐘;682160 RPN650/分鐘
- 1、下载文档前请自行甄别文档内容的完整性,平台不提供额外的编辑、内容补充、找答案等附加服务。
- 2、"仅部分预览"的文档,不可在线预览部分如存在完整性等问题,可反馈申请退款(可完整预览的文档不适用该条件!)。
- 3、如文档侵犯您的权益,请联系客服反馈,我们会尽快为您处理(人工客服工作时间:9:00-18:30)。
二、模具母体结构强度分析及优化方法
模具强度分析及优化原则
1. 本分析只对HT300部分的模具母体材料进行,而其上的刀块和标准件 均按照刚体来计算,因此整形刀块结构及尺寸未进行优化和改进设计; 2. 分析时材料的抗拉强度许用值为300MPa,抗压强度取为900MPa; 3. 模具结构优化主要考虑强度、刚度和稳定性三个方面; 4. 由于稳定性分析到目前为止仍是一个世界性难题,本研究考虑上述模 具多种受力状态的复杂性,取强度的安全系数均不小于3. 即最大拉应力不 大于100MPa,最大压应力不大于300MPa。工作时的关键部位最大变形量 不超过允许的变形 0.5 mm,其他部位最大变形量不超过允许的变形 0.2mm 。
下模变形量云图
下模变形量云图
6
❖ 模具二受、力模情况具分母析体结构强度分析及优化方法
2. 起吊运输:自重、1g加速度、2g加速度(分别对应于不同工况的冲击力)
下模应力图 下模变形图
下模应力图 下模变形图
模具自重状况下在运输、起吊时
的吊耳上的最大拉应力为
7.67MPa,周边部分端头区域
最大应力为:4.15Mpa,加强筋
上模应力图
下模应力图
下模Z向变形量(刚度)
16
四、方案比较及分析
❖ 起吊分析:自重、1g加速度、2g加速度
下模拉应力图
下模压应力图
下模Z向变形图
下模Y向变形图
17
❖ 改进方案二:加四强、筋方板案结比构布较局及调分整析
1. 下模座(整体改进和标准件均保持 原貌,对主要三大件的 加强筋板进行重新设计。
汇报提纲
模具基本情况 模具母体结构强度分析及优化方法 强度分析和优. 化的工程验证 方案比较及分析 优化改进结果
1
一、模具基本情况:
2
❖ 强度二分、析模所考具虑母的体模结具构主强要受度力分析及优化方法
1. 冲压正压力:800T; 2. 冲压时的侧向压力(模具型面上倾斜区域传递的侧向力,随 模具型面的不同而不同); 3. 冲压时由非均匀分布承载导致的多种局部受力工况; 4. 调整或冲压时由于装配误差导致的导板上过大的侧向力; 5. 模具起吊时的重力和冲击力、运输时的冲击力; 6. 模具多层堆放时的受力;
8
❖ 模具二受力、情模况具分母析体结构强度分析及优化方法
4. 端头分析:分析导板受较大的侧向力时,端头部分的强度。
下模端头最大拉应力 上模端头最大拉应力
下模变形量图 上模变形量图
模具在X方向的两个导板上加载
10吨载荷,Y方向一侧导板上加
载20吨载荷。加载模具端头在
承受较大侧向力时,主要传力区
应力最大为:135.3Mpa,变形
上模应力图
下模应力图
return
13
❖ 实验测量三—、—强对度55分个不析同和位优置化点的进工行测程量验证
47个点的应力测试值与仿真计算一致,可以用于指导模具设计; 误差来源主要是模具实际整形冲压状态与仿真计算的理想状态存在差异;
8个点的应力值偏差较大,已经将其排除,原因为两个点数据线在测试过程中压断, 另外6个点测试过程中应变片接线端与模具接触,产生干扰信号。
39.6Mpa ,加强筋部分最大拉应力
为77.7Mpa,最大压应力为
171.3Mpa,模具拉应力安全系数为4,
模具压应力安全系数为5,有较大的
减重空间。
5
❖ 模具受力二情、况模分具析母体结构强度分析及优化方法
下模应力图
下模应力图
模具在工作状态时,根据分析 来看,下模主要承力部位(整 形区以内)的最大拉应力为 10Mpa,最大压应力为 118.5Mpa;周边部分端头区 域最大拉应力为50.7Mpa,最 大压应力为37.8Mpa,加强筋 部分最大拉应力为48.4Mpa, 最大压应力为101.8Mpa,模 具拉应力安全系数为6,模具 压应力安全系数为7,有较大 的减重空间。
❖ 验证流程
选择验证模具模型 仿真计算 实验验证
轮罩整形翻边模 有限元分析
现场应力应变测试
11
三、强度分析和优化的工程验证
❖ 轮罩整形翻边模
选取原则:基本尺寸与SSDT整形模接近;受力对称;整形力接近;
尺寸参数:1700×1400×650mm; 整形力: 600T;
return
12
❖ 仿真计算三、强度分析和优化的工程验证
从整体来看测试的应力分布规律与仿真计算应力分布规律一致,从而可以判
断仿真计算方法是有效的。
14
❖ 改进方案一:在四原、有方设案计比布局较的及基分础析上进行改进
通过进一步增加减轻 孔数量和增大尺寸达 到轻量化的目的
285×85 235×160 285×120
15
❖ 改进方案一的强四度、和方刚案度比分析较及分析
部分应力最大为:2.75Mpa,
安全系数为:39,仍有较大的
减重空间。
7
二、模具母体结构强度分析及优化方法
❖ 模具受力情况分析
3.模具堆放时的受力及强度分析:(50T)
下模应力图
下模变形量图
多层模具叠放情况,最大拉应力31.88Mpa,最大压应力59.9Mpa (出现在枕木部位),Z向最大变形量0.065mm,安全裕度为5,满足 强度要求。
根据形状扩大减轻孔
1) 主肋板形状沿整形 刀块上下主要传力位置布 局,厚度采用30mm;
2) 其上减轻孔,按照 强度分析结果,在受力较 小的部位增加了和加大减 轻孔。
18
❖ 改进方案二:加四强、筋方板案结比构布较局及调分整析
下模座局部放大图
减轻孔330×65改至: 增加减轻孔,尺寸
280×140
4
❖ 模具二受、力模情况具分母析体结构强度分析及优化方法
1. 正向冲压力:800T
上模应力图
上模应力图
上模变形量云图
上模变形量云图
模具在工作状态时,根据分析来看,
上模主要承力部位(整形区以内)的
最大拉应力为53.1Mpa,最大压应力
为133.2Mpa;周边部分端头区域最
大拉应力为25.6Mpa,最大压应力为
量:0.181mm,但变形区域位
于非关键部位,不影响模具的整
体精度,可以适当减重。
9
二、模具母体结构强度分析及优化方法
❖ 优化方法——拓扑优化
目标:根据模具工作状态的受力,对主 要受力区的支撑部分结构进行结构拓扑 优化,然后依据优化结果进行加强筋的 改进设计。
依据受力区域和边界 轮廓建立模型
10
三、强度分析和优化的工程验证