真空自耗
真空自耗炉事故应急预案

一、预案背景真空自耗炉是一种高温熔炼设备,广泛应用于冶金、材料加工等领域。
由于真空自耗炉操作过程中存在高温、高压、易燃易爆等风险,一旦发生事故,可能造成人员伤亡和财产损失。
为提高应急处置能力,降低事故危害,特制定本预案。
二、预案目标1. 最大限度地减少事故造成的伤亡和财产损失;2. 确保事故现场人员安全撤离;3. 及时、有效地控制事故发展,恢复正常生产秩序。
三、预案适用范围本预案适用于真空自耗炉在操作过程中发生的各类事故,包括但不限于火灾、爆炸、中毒、窒息等。
四、事故分类及应对措施1. 火灾事故(1)发现火情,立即切断电源,关闭炉体阀门,停止真空泵运行。
(2)使用灭火器、灭火器材等对初期火灾进行扑救。
(3)组织人员撤离事故现场,确保人员安全。
(4)报告上级领导,启动应急预案。
2. 爆炸事故(1)发现爆炸迹象,立即切断电源,关闭炉体阀门,停止真空泵运行。
(2)组织人员迅速撤离事故现场,确保人员安全。
(3)使用防爆器材、工具进行事故现场处理。
(4)报告上级领导,启动应急预案。
3. 中毒、窒息事故(1)发现中毒、窒息人员,立即将其移至空气新鲜处。
(2)对中毒、窒息人员实施急救,如需,立即送往医院。
(3)对事故现场进行通风,降低有害气体浓度。
(4)报告上级领导,启动应急预案。
五、应急组织机构及职责1. 应急指挥部(1)负责组织、指挥、协调事故应急处置工作;(2)负责制定事故现场处置方案;(3)负责向上级领导报告事故情况。
2. 现场处置组(1)负责现场事故处置;(2)负责组织人员疏散;(3)负责对事故现场进行封锁、警戒。
3. 医疗救护组(1)负责事故现场受伤人员的急救;(2)负责将受伤人员送往医院。
4. 通讯联络组(1)负责事故信息的收集、汇总、上报;(2)负责与上级领导、相关部门的沟通协调。
六、应急演练1. 定期组织应急演练,提高应急处置能力;2. 对演练中发现的问题进行总结,完善应急预案;3. 加强应急队伍的培训,提高应急人员的业务水平。
真空自耗电弧炉var

真空自耗电弧炉var摘要:1.真空自耗电弧炉的概念与原理2.真空自耗电弧炉的组成结构3.真空自耗电弧炉的应用领域4.真空自耗电弧炉的优势与局限性正文:一、真空自耗电弧炉的概念与原理真空自耗电弧炉,简称真空电弧炉,是一种在真空环境下进行金属熔化和精炼的设备。
它是通过利用电弧产生的热量将金属加热至一定的温度,使其熔化并进行精炼的一种电热设备。
真空自耗电弧炉在工作过程中,金属在真空环境下熔化,有助于去除金属中的杂质,提高金属的纯度。
二、真空自耗电弧炉的组成结构真空自耗电弧炉主要由以下几个部分组成:1.炉体:炉体是真空自耗电弧炉的主要部分,用于容纳金属和进行熔化过程。
2.电极:电极是真空自耗电弧炉的关键部件,负责产生电弧并加热金属。
3.真空系统:真空系统负责维持炉内的真空度,确保金属在真空环境下进行熔化。
4.控制系统:控制系统用于监控和调节真空自耗电弧炉的运行参数,保证设备正常运行。
三、真空自耗电弧炉的应用领域真空自耗电弧炉广泛应用于以下领域:1.金属熔化:真空自耗电弧炉可用于熔化各种金属,如铜、铝、钛等。
2.金属精炼:真空自耗电弧炉可在真空环境下进行金属精炼,有效去除金属中的杂质。
3.金属铸造:真空自耗电弧炉可用于铸造各种金属制品,如铸件、锻件等。
4.科研领域:真空自耗电弧炉在科研领域也有广泛应用,如材料研究、冶金研究等。
四、真空自耗电弧炉的优势与局限性真空自耗电弧炉具有以下优势:1.熔化效率高:真空自耗电弧炉利用电弧产生的热量进行金属熔化,熔化效率较高。
2.金属纯度高:真空环境下进行熔化,有助于去除金属中的杂质,提高金属纯度。
3.设备运行稳定:真空自耗电弧炉采用控制系统对设备运行进行监控和调节,保证设备运行稳定。
然而,真空自耗电弧炉也存在一定的局限性:1.设备投资成本较高:真空自耗电弧炉设备本身价格较高,且需要配套真空系统等设备,投资成本相对较大。
2.运行成本较高:真空自耗电弧炉在运行过程中需要维持真空度,以及消耗大量的电能,导致运行成本较高。
var真空自耗熔炼

var真空自耗熔炼
技术简介
Var真空自耗熔炼技术,是一种高级的单晶生长技术,主要用于生长高品质、高纯度的单晶材料。
这种技术在国内外得到了广泛应用,被应用于晶体管、太阳能电池、LED等电子器件和无机纤维等领域。
Var真空自耗熔炼技术的主要原理是,通过将一定数量的材料放入真空熔炉中,在恒定的温度下,通过熔炼和控制熔体的温度、组成等条件,实现高质量单晶材料的生长。
技术优势
Var真空自耗熔炼技术具有以下优势:
1. 高纯度:能够控制熔体组成,保证高品质、高纯度的单晶材料的生长;
2. 高匀性:熔体在容器内进行对流混合,能够使得生长的单晶材料具有更好的匀性;
3. 低缺陷:通过控制材料熔化的速度和温度梯度,能够使得单晶材料中的缺陷数量降低。
应用领域
Var真空自耗熔炼技术被广泛应用于以下领域:
1. 电子材料:高质量晶体管、太阳能电池、LED等电子器件材料的生长;
2. 化学材料:高纯度的有机化合物晶体的生长;
3. 无机材料:生长陶瓷材料、多晶硅等材料。
总结
Var真空自耗熔炼技术是一种高级的单晶生长技术,具有高纯度、高匀性、低缺陷等优点。
在电子器件、化学材料、无机材料等领域都有广泛应用。
随着技术的不断发展,Var真空自耗熔炼技术在未来的发展前景十分广泛。
真空自耗电弧炉操作规程
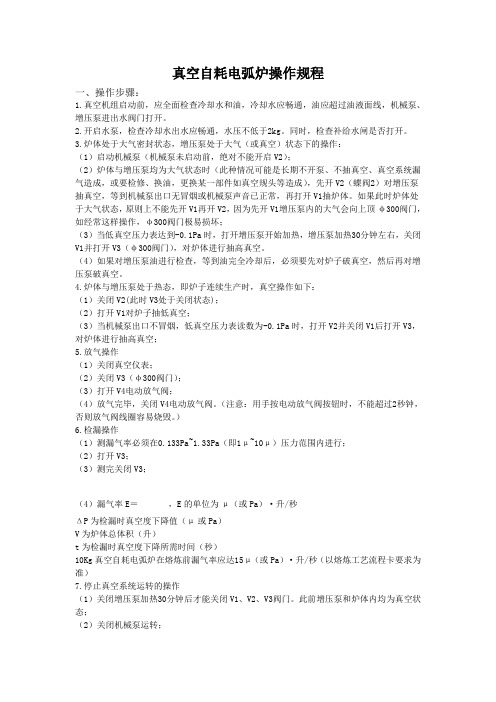
真空自耗电弧炉操作规程一、操作步骤:1.真空机组启动前,应全面检查冷却水和油,冷却水应畅通,油应超过油液面线,机械泵、增压泵进出水阀门打开。
2.开启水泵,检查冷却水出水应畅通,水压不低于2kg。
同时,检查补给水闸是否打开。
3.炉体处于大气密封状态,增压泵处于大气(或真空)状态下的操作:(1)启动机械泵(机械泵未启动前,绝对不能开启V2);(2)炉体与增压泵均为大气状态时(此种情况可能是长期不开泵、不抽真空、真空系统漏气造成,或要检修、换油,更换某一部件如真空规头等造成),先开V2(蝶阀2)对增压泵抽真空,等到机械泵出口无冒烟或机械泵声音已正常,再打开V1抽炉体。
如果此时炉体处于大气状态,原则上不能先开V1再开V2,因为先开V1增压泵内的大气会向上顶φ300阀门,如经常这样操作,φ300阀门极易损坏;(3)当低真空压力表达到-0.1Pa时,打开增压泵开始加热,增压泵加热30分钟左右,关闭V1并打开V3(φ300阀门),对炉体进行抽高真空。
(4)如果对增压泵油进行检查,等到油完全冷却后,必须要先对炉子破真空,然后再对增压泵破真空。
4.炉体与增压泵处于热态,即炉子连续生产时,真空操作如下:(1)关闭V2(此时V3处于关闭状态);(2)打开V1对炉子抽低真空;(3)当机械泵出口不冒烟,低真空压力表读数为-0.1Pa时,打开V2并关闭V1后打开V3,对炉体进行抽高真空;5.放气操作(1)关闭真空仪表;(2)关闭V3(φ300阀门);(3)打开V4电动放气阀;(4)放气完毕,关闭V4电动放气阀。
(注意:用手按电动放气阀按钮时,不能超过2秒钟,否则放气阀线圈容易烧毁。
)6.检漏操作(1)测漏气率必须在0.133Pa~1.33Pa(即1μ~10μ)压力范围内进行;(2)打开V3;(3)测完关闭V3;(4)漏气率E=,E的单位为μ(或Pa)·升/秒ΔP为检漏时真空度下降值(μ或Pa)V为炉体总体积(升)t为检漏时真空度下降所需时间(秒)10Kg真空自耗电弧炉在熔炼前漏气率应达15μ(或Pa)·升/秒(以熔炼工艺流程卡要求为准)7.停止真空系统运转的操作(1)关闭增压泵加热30分钟后才能关闭V1、V2、V3阀门。
真空自耗炉工作原理

真空自耗炉工作原理真空自耗炉是一种利用真空环境和电磁辐射加热的设备,广泛应用于材料的热处理和实验室研究中。
它的工作原理是通过将待处理的材料放置在真空环境中,并通过电磁辐射加热产生高温,从而实现材料的处理和实验目的。
真空自耗炉的主要组成部分包括真空室、加热元件、温度控制系统和真空泵等。
真空室是炉内的密封容器,通过真空泵将炉内空气抽取出来,形成高真空环境。
加热元件通常采用电阻丝或电磁线圈,通过电流通入加热元件,产生的电磁辐射能量将材料加热至所需温度。
温度控制系统可以监测和控制炉内温度,保证材料的处理和实验过程达到预期效果。
真空自耗炉的工作原理可以简单分为两个步骤:真空环境的形成和材料的加热。
首先,通过真空泵将炉内空气抽取出来,形成高真空环境。
真空环境的形成可以有效降低材料表面的氧化速率,保护材料的性能和质量。
其次,通过加热元件产生的电磁辐射能量将材料加热至所需温度。
电磁辐射能量可以迅速传递到材料表面,实现快速加热和均匀加热。
同时,由于真空环境下的热传导和对流受到限制,材料的热损失较少,能量利用效率较高。
真空自耗炉的工作原理具有以下特点:首先,真空环境的形成可以避免材料表面的氧化和污染,保证材料的处理和实验的准确性和可靠性。
其次,电磁辐射加热可以实现快速加热和均匀加热,提高处理和实验的效率。
此外,真空环境下的热传导和对流受到限制,能量损失较少,能量利用效率较高。
最后,真空自耗炉还可以通过控制真空度和加热功率等参数,实现对材料的不同处理和实验要求。
在实际应用中,真空自耗炉被广泛应用于金属材料的热处理、半导体材料的生长、光学薄膜的制备等领域。
例如,金属材料的热处理可以通过真空环境的形成,避免氧化和污染,从而提高材料的性能和质量。
半导体材料的生长可以通过加热元件产生的电磁辐射能量,实现材料的快速生长和均匀生长。
光学薄膜的制备可以通过控制真空度和加热功率等参数,实现对薄膜的厚度和光学性能的控制。
真空自耗炉是一种利用真空环境和电磁辐射加热的设备,通过真空环境的形成和材料的加热,实现对材料的处理和实验目的。
《真空自耗电弧炉》课件
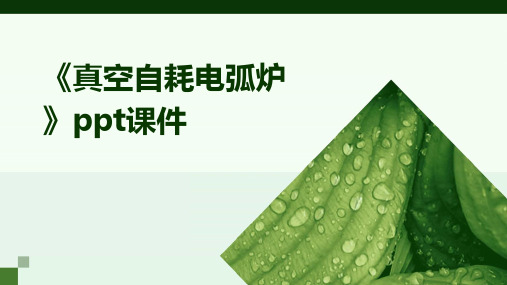
量。
节能环保
采用电弧加热,相比传 统火焰熔炼方式更加节
能环保。
操作简便
设备自动化程度高,操 作简便,减少人工干预
。
缺点
设备成本高
真空自耗电弧炉设备成本较高 ,投资较大。
维护成本高
由于设备复杂,需要专业人员 进行维护和保养,维护成本较 高。
真空自耗电弧炉的定义
解释真空自耗电弧炉 的基本概念和原理。
强调真空自耗电弧炉 在熔炼、合金制备等 领域的重要作用。
说明真空自耗电弧炉 的主要构成部件和工 作流程。
02
真空自耗电弧炉的工作原 理
电弧产生与熔炼过程
电弧产生
在真空环境中,通过高压电源在 电极和坩埚之间产生电弧,提供 熔炼所需的热量。
THANK YOU
感谢观看
熔炼过程
电极熔化后,金属液滴通过电弧 作用被吸入坩埚中,实现金属的 熔炼。
金属熔体的处理与凝固
金属熔体处理
在熔炼过程中,通过控制温度和搅拌,确保金属熔体的均匀性和纯净度。
金属凝固
金属熔体冷却后,在坩埚内壁逐渐凝固成金属锭。
真空系统与炉体结构
真空系统
真空系统用于维持炉内的真空状态, 确保电弧的稳定燃烧和金属的顺利熔 炼。
低碳排放
研究和应用低碳排放技术,降低熔炼过程中的温 室气体排放。
市场前景与竞争格局
市场需求增长
随着制造业的发展和金属 材料需求的增加,真空自 耗电弧炉市场前景广阔。
技术竞争
各厂商在技术研发、产品 性能和成本方面展开激烈 竞争,不断提升自身竞争 力。
产业链合作
加强产业链上下游企业合 作,共同推动真空自耗电 弧炉技术的进步和应用。
真空自耗电弧炉var

真空自耗电弧炉var
一、真空自耗电弧炉的概述
真空自耗电弧炉(Vacuum Self-Consuming Arc Furnace)是一种先进的熔炼设备,主要用于金属材料的熔化、净化和熔炼。
它采用真空技术,能够在较低的温度下实现金属的熔化,具有节能、环保、高效等特点。
二、真空自耗电弧炉的工作原理
真空自耗电弧炉的工作原理主要是利用高频直流电源将金属材料加热至熔化状态,并通过真空泵将熔融金属中的气体抽出,实现金属的净化和熔炼。
在熔炼过程中,自耗电极不断熔化,补充炉内熔融金属的消耗,从而实现连续熔炼。
三、真空自耗电弧炉的优点
1.节能:真空自耗电弧炉在较低的温度下实现金属熔化,能耗较低,有利于降低生产成本。
2.环保:真空环境下,金属熔炼过程中产生的有害气体得到有效控制,减轻了对环境的污染。
3.高效:真空自耗电弧炉具有较高的熔炼速度,生产效率高。
4.质量稳定:真空环境下,金属熔炼过程中的氧化物、氮化物等夹杂物得到有效去除,提高了产品的质量。
四、真空自耗电弧炉的应用领域
真空自耗电弧炉广泛应用于钢铁、有色金属、稀土等行业,主要用于熔炼、精炼、合金制备等领域。
五、真空自耗电弧炉的维护与保养
1.定期检查真空泵的运行状态,确保真空泵的正常工作。
2.定期清理炉膛内的杂质,防止炉膛结垢。
3.定期检查高频电源的运行状态,确保电源的稳定输出。
4.熔炼过程中,注意观察熔池的稳定性,如有异常应及时处理。
5.熔炼结束后,及时关闭电源和真空泵,进行设备保养。
通过以上介绍,我们可以了解到真空自耗电弧炉的特点、工作原理、优点及应用领域,并为设备的维护和保养提供了一定的指导。
真空自耗电弧炉var

真空自耗电弧炉var摘要:I.真空自耗电弧炉简介A.真空自耗电弧炉的定义B.真空自耗电弧炉的工作原理II.真空自耗电弧炉的类型和应用A.真空自耗电弧炉的类型1.高频真空自耗电弧炉2.直流真空自耗电弧炉3.真空自耗电弧炉的其他类型B.真空自耗电弧炉的应用领域1.航空航天领域2.军事领域3.核工业领域4.其他领域III.真空自耗电弧炉的特点和优势A.真空自耗电弧炉的特点1.高真空环境2.快速熔炼3.低氧化程度4.节能环保B.真空自耗电弧炉的优势1.高品质的熔炼产品2.高效率的生产过程3.适应性强IV.真空自耗电弧炉的发展趋势和前景A.技术发展趋势1.高功率密度2.自动化控制3.材料研究B.行业前景1.国家政策支持2.市场需求增长3.国际竞争优势正文:真空自耗电弧炉是一种在真空条件下,通过电弧放电产生的高温来熔炼金属的设备。
它具有高真空环境、快速熔炼、低氧化程度和节能环保等特点,广泛应用于航空航天、军事、核工业等领域。
随着我国政策支持和市场需求的增长,真空自耗电弧炉行业前景看好,技术发展趋势将朝着高功率密度、自动化控制和材料研究等方面发展。
真空自耗电弧炉的工作原理是在高真空环境中,利用电弧放电产生的高温将金属原料熔化。
根据不同的应用需求,真空自耗电弧炉有高频真空自耗电弧炉、直流真空自耗电弧炉等多种类型。
其中,高频真空自耗电弧炉具有熔炼速度快、熔融率高、氧化程度低等优点;直流真空自耗电弧炉具有熔炼过程中成分均匀、熔融温度高、设备占地面积小等特点。
真空自耗电弧炉在各个领域有着广泛的应用。
在航空航天领域,它可用于制造高性能的航空发动机、导弹等部件;在军事领域,可用于生产高精度武器、装甲等;在核工业领域,可用于核燃料熔炼、核反应堆部件制造等。
此外,真空自耗电弧炉还在其他领域发挥着重要作用。
随着科技的进步和市场需求的提高,真空自耗电弧炉行业将不断发展和创新。
未来,真空自耗电弧炉将朝着高功率密度、自动化控制和材料研究等方面发展,以满足各个领域对高品质熔炼产品的需求。
简述真空自耗电弧熔炼的工艺过程

真空自耗电弧熔炼的工艺过程简介真空自耗电弧熔炼是一种常用的金属熔炼方法,通过利用电弧的高温和真空环境,在各种金属熔炼和提纯过程中具有广泛应用。
本文将详细介绍真空自耗电弧熔炼的工艺过程。
工艺概述真空自耗电弧熔炼是指在真空环境下,通过自耗电极钢筋和炉料之间的电弧熔化金属炉料,以实现金属的熔炼和提纯。
此方法因其具有高温、高效、低污染等优点,被广泛应用于钢铁、有色金属等行业。
工艺步骤真空自耗电弧熔炼主要包括以下几个步骤:1. 准备工作在进行真空自耗电弧熔炼前,需要进行一系列准备工作,包括选材、设计熔炼工艺和准备炉料等。
2. 入炉装料将待熔炼的金属炉料按照一定比例装入真空自耗电弧熔炼炉中。
炉料通常由金属块、废料或合金组成。
3. 真空抽取将熔炼炉密封后,通过真空泵对炉腔进行抽取,以降低炉内气体压力。
通常需要达到一定真空度,以提供良好的熔炼环境。
4. 熔化炉料通过电源引导电弧产生,并在电极与炉料之间击穿形成电弧。
电弧的高温将金属炉料熔化,形成熔池。
在真空环境中,电弧本身也会将气体分解,提供一定的能量。
5. 渣液分离在熔炼过程中,金属炉料中的杂质和氧化物会形成熔渣。
利用熔渣的比重差异,通过重力或离心力的作用将熔渣与金属分离。
6. 金属提纯通过在真空中进行熔炼,能够使金属炉料中的气体和杂质得到一定程度的去除。
此外,可以通过添加化学剂或采用特殊的炼铁工艺,使金属达到所需的纯度。
7. 出炉倾包待金属炉料熔化后,根据需要,可以将熔池倾入铸型中,进行铸造、凝固等后续工艺。
同时,可以根据需要按照特定的工艺要求,对金属进行调温和锻造等处理。
工艺特点和优点真空自耗电弧熔炼具有如下特点和优点:1. 高温环境真空自耗电弧熔炼利用电弧高温熔化金属,使得金属能够达到极高的温度,从而有利于熔炼和提纯。
2. 高效和节能相比传统的金属熔炼方法,真空自耗电弧熔炼省去了预热过程,同时熔化和提纯效率更高,因而具有较高的能源利用效率。
3. 低污染真空自耗电弧熔炼在真空环境中进行,减少了气体和杂质的污染。
真空自耗炉工作原理
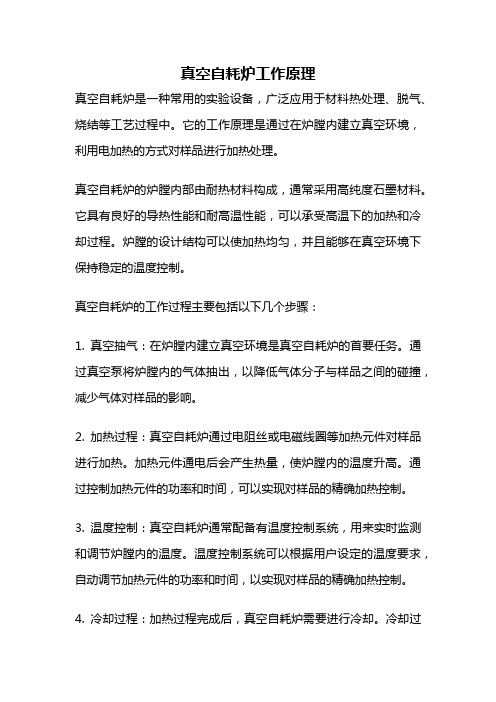
真空自耗炉工作原理真空自耗炉是一种常用的实验设备,广泛应用于材料热处理、脱气、烧结等工艺过程中。
它的工作原理是通过在炉膛内建立真空环境,利用电加热的方式对样品进行加热处理。
真空自耗炉的炉膛内部由耐热材料构成,通常采用高纯度石墨材料。
它具有良好的导热性能和耐高温性能,可以承受高温下的加热和冷却过程。
炉膛的设计结构可以使加热均匀,并且能够在真空环境下保持稳定的温度控制。
真空自耗炉的工作过程主要包括以下几个步骤:1. 真空抽气:在炉膛内建立真空环境是真空自耗炉的首要任务。
通过真空泵将炉膛内的气体抽出,以降低气体分子与样品之间的碰撞,减少气体对样品的影响。
2. 加热过程:真空自耗炉通过电阻丝或电磁线圈等加热元件对样品进行加热。
加热元件通电后会产生热量,使炉膛内的温度升高。
通过控制加热元件的功率和时间,可以实现对样品的精确加热控制。
3. 温度控制:真空自耗炉通常配备有温度控制系统,用来实时监测和调节炉膛内的温度。
温度控制系统可以根据用户设定的温度要求,自动调节加热元件的功率和时间,以实现对样品的精确加热控制。
4. 冷却过程:加热过程完成后,真空自耗炉需要进行冷却。
冷却过程可以通过关闭加热元件的电源,或者将样品从炉膛中取出,并放置在冷却装置中进行快速冷却。
真空自耗炉的工作原理可以总结为以下几个关键点:1. 真空环境:真空自耗炉通过抽气装置将炉膛内的气体抽出,建立稳定的真空环境。
真空环境可以减少气体对样品的影响,避免氧化、腐蚀等问题。
2. 加热控制:真空自耗炉通过加热元件对样品进行加热。
加热元件的功率和时间可以通过温度控制系统进行调节,以实现对样品的精确加热控制。
3. 温度控制:真空自耗炉通常配备有温度控制系统,用来实时监测和调节炉膛内的温度。
温度控制系统可以根据用户设定的温度要求,自动调节加热元件的功率和时间,以实现对样品的精确加热控制。
4. 冷却装置:真空自耗炉在加热完成后需要进行冷却。
冷却可以通过关闭加热元件的电源,或者将样品从炉膛中取出,并放置在冷却装置中进行快速冷却。
真空自耗电弧炉(VAR)的工作原理与特点

书山有路勤为径,学海无涯苦作舟
真空自耗电弧炉(VAR)的工作原理与特点
世界上第一台真空自耗电弧炉是于1950 年在美国诞生的。
真空自耗电弧炉是在真空室中利用电弧的能量来熔炼金属的一种电炉。
真空自耗电弧炉主要用来熔炼钛、锆、钼等活泼金属和难熔金属,也用来熔炼耐热钢、不锈钢、工具钢、轴承钢。
上个世纪五十年代初,用来重熔高温合金,显示出极好的优越性,真空技术网(chvacuum/)认为成为高温合金和特殊钢重熔的重要手段之一。
1、真空自耗电弧炉的工作原理
真空自耗电弧炉结构示意首先,在自耗电极下端部同结晶器之间燃起电弧,自耗电极下端部同熔池之间形成电弧等离子区,该区具有极高的温度,能使自耗电极端部首先在这里被熔化掉。
随着自耗电极中一些非金属夹杂物,如氧化物、氮化物,在真空和高温条件下,发生离解或被碳还原而被去除掉,达到进一步提纯的目的。
由于真空自耗电弧炉工艺能去除气体和非金属夹杂物,以及去除某些低熔点的有害杂质,从而使冷、热加工性能、塑性和力学性能、物理性能得到明显改善。
特别是改善了纵向和横向性能的差异,这对保证材料性能的稳定性、一致性和可靠性有着极其重要的意义。
为了获得高质量锭子,熔炼过程中要求熔炼功率稳定,对供电电源要求具有
恒流特性的直流电流。
真空自耗电弧炉用的硅整流电源主回路示于上述硅整流装置的参数为:
(1)在20-40V 工作电压范围内具有恒流特性,空载电压在70V 左右。
(2)电流调节范围为1:10。
(3)当各整流臂中有10%硅元件损坏时,系统会发出信号,但能在额定电流下继续运行。
tc4真空自耗成分不均匀的原因

tc4真空自耗成分不均匀的原因《tc4真空自耗成分不均匀的原因及相关分析》引言你有没有遇到过这样的情况,使用某种产品的时候,发现它的效果忽好忽坏,就像开盲盒一样?我有个朋友就跟我抱怨过,他使用一款含有tc4成分的产品,有时候感觉效果超棒,可有时候又觉得不尽如人意。
这背后可能就和tc4真空自耗成分不均匀有关。
对产品成分进行分析其实就像是一场探秘之旅,它能让我们了解为什么产品会有这样那样的表现,从而帮助我们更好地选择适合自己的产品。
成分分析首先来说说tc4中的钛(Ti)元素。
钛在自然界中广泛存在,它可是个很厉害的家伙。
它的来源有很多,像矿石中就含有大量的钛。
钛在产品中的作用可不小,它就像一个坚强的护盾。
从使用体验来说,钛的存在让产品更加耐用,具有良好的抗腐蚀性。
我记得有一次,我使用的一个小物件,含有钛成分,即使在比较恶劣的环境下,它也没有轻易损坏。
它的优点很明显,非常稳定,而且对大多数人来说,几乎不会引起过敏反应,就像一个温和的伙伴。
不过呢,它也有个小缺点,就是可能会让产品的成本相对较高,毕竟它的提炼过程还是比较复杂的。
然后是铝(Al)元素。
铝也是一种常见的元素,来源丰富,比如铝土矿。
铝在tc4中的作用像是一个活力小助手。
它能提高产品的强度,让产品更有韧性。
就好比我们吃的饼干,如果没有足够的韧性,一捏就碎了。
在使用产品时,含有铝元素的产品在承受一定压力或者外力的时候,不容易变形。
铝对皮肤的友好度一般,有些人可能会觉得如果长期接触含铝量高的产品,皮肤会有轻微的不适,但这也是因人而异的。
而且,过量的铝摄入可能对健康存在一定潜在风险,这也是我们需要关注的。
还有钒(V)元素。
钒相对来说比较特殊,它的来源不像钛和铝那么常见。
钒在tc4中的作用像是一个神秘的调味料。
它能改善产品的微观结构,让产品的性能更加优良。
在使用感受上,它可能不会被我们直接察觉到,但它却默默地在背后发挥着作用。
它的优点是能让产品在细节上表现得更好,缺点就是如果含量控制不好,可能会影响整个产品的稳定性。
真空自耗电弧炉

A
10Байду номын сангаас
罗茨泵工作原理简图
A
11
罗茨泵工作原理动态图
A
12
油增压泵
油增压泵是蒸汽流泵的一 种,是利用室温下饱和蒸 汽压强低于5×10Pa的增 压泵油,加热到工作温度 后所产生的大量油蒸汽, 分别由各级喷嘴喷出而得 到的高速蒸汽射流作为介 质。被抽气体进入油蒸汽 射流内,含气体的油蒸气 射流到泵壁被冷却,油蒸 汽冷凝后返回油锅,而气 体逐级被压缩,最后被前 级泵抽走。
再现性:是指通过电控系统和重量传感器(电子称) 来控制熔炼过程中参数的稳定。
灵活性:是指一台炉子可生产多种锭型。
A
4
炉体结构
1.炉体固定,坩埚移动式。
此种炉型炉体被固定在金属结构物框架上不 动,而坩埚被设置在一个可以移动的小车上,装 炉时移动至炉体下方,提升坩埚以完成封炉操作。
优点:结构稳定,占地面积小。 缺点:生产效率不高。
08.熔化站
09铸锭
10.旋转立柱
11.闭锁阀
12. 大蝶阀
13. 油增压泵
14. 大罗茨泵
15. 小罗茨泵
16. 机械泵
A
3
构造特点
主要表现在〝同轴性〞 、〝再现性〞、 〝灵活性〞
的设计思想上。
同轴性:是指把阳极电缆靠近阴极电缆线并且都接在 炉子的上部,二者保持近距离平行,使得由于强大电流流 过导线,电极和炉体对所产生的感应磁场互相抵消,从而 减弱或消除了感应磁场对合金质量的不利影响并提高电效 率。
1.能保证带走熔炼过程中产生的大量热能。
2.电阻要小。
3.密封性好,坩埚筒体、止口密封面不能有凹坑 、裂纹等现象。
坩埚系统主要由筒体、地垫、底座和水套组成。
简述真空自耗电弧熔炼的工艺过程
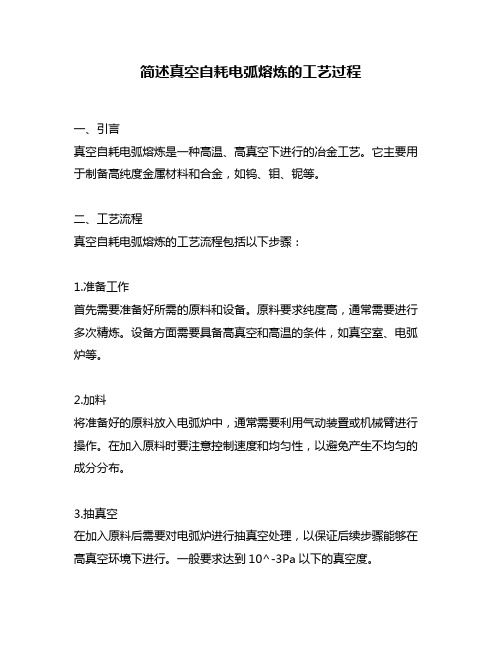
简述真空自耗电弧熔炼的工艺过程一、引言真空自耗电弧熔炼是一种高温、高真空下进行的冶金工艺。
它主要用于制备高纯度金属材料和合金,如钨、钼、铌等。
二、工艺流程真空自耗电弧熔炼的工艺流程包括以下步骤:1.准备工作首先需要准备好所需的原料和设备。
原料要求纯度高,通常需要进行多次精炼。
设备方面需要具备高真空和高温的条件,如真空室、电弧炉等。
2.加料将准备好的原料放入电弧炉中,通常需要利用气动装置或机械臂进行操作。
在加入原料时要注意控制速度和均匀性,以避免产生不均匀的成分分布。
3.抽真空在加入原料后需要对电弧炉进行抽真空处理,以保证后续步骤能够在高真空环境下进行。
一般要求达到10^-3Pa以下的真空度。
4.预加热将电弧炉加温至预定温度,以保证后续步骤能够顺利进行。
预定温度根据不同的材料和合金而有所不同。
5.自耗电弧熔炼在预定温度下,通电产生自耗电弧,使原料加热并熔化。
在高温、高真空下进行的反应可以消除大部分杂质,从而制备出高纯度的金属材料或合金。
6.冷却将熔融的金属或合金缓慢冷却至室温。
在冷却过程中需要控制速度和均匀性,以避免产生不均匀的组织结构。
7.取样检测将冷却后的样品进行取样检测,以确定其组织结构和成分分布是否符合要求。
如果需要进一步提高纯度,则需要进行多次精炼处理。
三、工艺特点真空自耗电弧熔炼具有以下特点:1.高纯度:由于在高温、高真空下进行反应,可以消除大部分杂质,从而制备出高纯度的金属材料或合金。
2.均匀性好:自耗电弧加热方式能够使原料均匀加热,并且能够保证成分分布均匀。
3.适用范围广:可以制备多种金属材料和合金,如钨、钼、铌等。
4.设备要求高:需要具备高真空和高温的条件,如真空室、电弧炉等。
四、应用领域真空自耗电弧熔炼主要应用于以下领域:1.航空航天领域:制备高强度、高温抗氧化性能的金属材料和合金。
2.半导体材料领域:制备高纯度的硅片和其他半导体材料。
3.化工领域:制备高纯度的催化剂和其他化工原料。
真空自耗电弧炉var
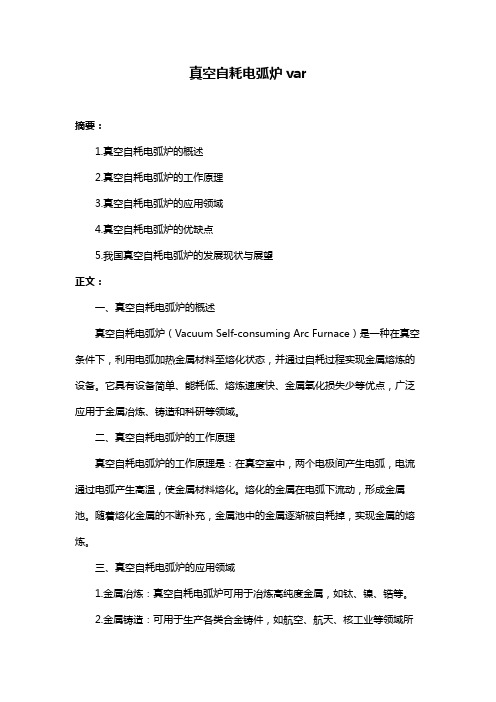
真空自耗电弧炉var摘要:1.真空自耗电弧炉的概述2.真空自耗电弧炉的工作原理3.真空自耗电弧炉的应用领域4.真空自耗电弧炉的优缺点5.我国真空自耗电弧炉的发展现状与展望正文:一、真空自耗电弧炉的概述真空自耗电弧炉(Vacuum Self-consuming Arc Furnace)是一种在真空条件下,利用电弧加热金属材料至熔化状态,并通过自耗过程实现金属熔炼的设备。
它具有设备简单、能耗低、熔炼速度快、金属氧化损失少等优点,广泛应用于金属冶炼、铸造和科研等领域。
二、真空自耗电弧炉的工作原理真空自耗电弧炉的工作原理是:在真空室中,两个电极间产生电弧,电流通过电弧产生高温,使金属材料熔化。
熔化的金属在电弧下流动,形成金属池。
随着熔化金属的不断补充,金属池中的金属逐渐被自耗掉,实现金属的熔炼。
三、真空自耗电弧炉的应用领域1.金属冶炼:真空自耗电弧炉可用于冶炼高纯度金属,如钛、镍、锆等。
2.金属铸造:可用于生产各类合金铸件,如航空、航天、核工业等领域所需的特种合金。
3.科研:用于科研领域的金属材料熔炼、制备和测试。
四、真空自耗电弧炉的优缺点优点:1.设备简单,投资较低。
2.能耗低,熔炼过程中能量损耗较少。
3.金属氧化损失少,有利于提高金属纯度。
4.熔炼速度快,生产效率高。
缺点:1.真空系统易损,维修成本较高。
2.对金属材料的导电性要求较高,部分金属不适合采用真空自耗电弧炉熔炼。
五、我国真空自耗电弧炉的发展现状与展望1.发展现状:我国真空自耗电弧炉技术已达到国际先进水平,设备种类齐全,应用于多个领域。
2.展望:随着科技的进步和产业需求的变化,真空自耗电弧炉将向更高温度、更大容量、更高纯度、更多功能等方向发展。
真空自耗炉

真空自耗炉概述真空自耗炉是一种特殊的热处理设备,用于在真空环境下对材料进行加热处理。
它经过精密设计和优化,能够实现高温均匀加热,并具有低能耗和环保的特点。
本文将介绍真空自耗炉的工作原理、应用领域以及其优势。
工作原理真空自耗炉主要由炉体、加热系统、真空系统和控制系统四个部分组成。
炉体炉体是真空自耗炉的主要组成部分,通常由耐高温材料制成,如不锈钢。
炉体内部通常通过铸造或焊接形成密封的空腔,以确保真空环境的维持。
炉体表面通常涂有高温耐烧的涂层,以提高热辐射的效率。
加热系统加热系统是真空自耗炉的关键组成部分,通常采用电阻加热器。
电阻加热器由高温合金材料制成,通过电流通过产生热能,从而对物料进行加热。
加热系统通常采用多个加热区域,可以实现对物料的分段加热,以确保温度的均匀性。
真空系统用于将炉体内部抽成真空状态。
真空系统通常由真空泵和阀门组成,可以实现快速而稳定的抽真空过程。
抽取真空后,可以通过控制阀门来调节炉内的气体排放,以保持稳定的真空环境。
控制系统控制系统用于监测和控制真空自耗炉的运行。
它通常包括温度传感器、气压传感器和电子控制器。
温度传感器用于测量炉内的温度变化,气压传感器用于监测真空环境的稳定性,而电子控制器则用于根据传感器的反馈信号控制加热系统和真空系统的运行。
应用领域真空自耗炉在许多领域都有广泛的应用,以下列举几个典型的应用领域。
金属热处理真空自耗炉在金属热处理方面有着重要的应用。
金属材料在高温下的结构和性能往往受到氧化、腐蚀等因素的影响,而真空自耗炉可以在无氧环境中对金属材料进行加热处理,从而有效地消除这些不利因素,提高金属材料的性能和质量。
陶瓷烧结陶瓷材料的烧结是制作陶瓷制品的重要过程之一。
真空自耗炉可以在无氧环境中对陶瓷材料进行烧结,从而避免了氧化反应的发生,保证了陶瓷制品的质量和稳定性。
真空自耗炉在半导体制造过程中也有着广泛的应用。
半导体材料对温度和环境的要求非常严格,而真空自耗炉可以提供高温均匀的加热环境,并保持稳定的真空状态,满足半导体材料的加工需求。
真空自耗电弧炉介绍资料

真空自耗电弧熔炼炉简介技术支持啥是真空自耗电弧炉?真空自耗电弧炉就是一个巨型直流电焊机在那堆焊作业呢。
第一个不同的是焊把是电机减速机滚珠丝杠传动进给的,第二个不同就是堆焊环境是负压的,可以有效取出堆焊时焊条放出的气体,第三个不同是可以将焊条里面低熔点的金属和杂质在高温融化时气化的金属去除,提纯金属。
第四个不同为了得到品质好的堆焊圆柱体,我们选择在水冷铜坩埚里堆焊,这样还是不能得到合格的堆焊体我们就给水冷铜坩埚加了电磁感应稳弧线圈。
即可以稳定电弧压制电弧和搅拌熔池减少材料的偏析(偏析:合金中各组成元素在结晶时分布不均匀的现象称为偏析。
焊接熔池一次结晶过程中,由于冷却速度快,巳凝固的熔池金属中化学成分来不及扩散,造成分布不均,产生偏柝)第五个不同就是整个系统需要三个个可靠的循环系统,1是水循环系统,主要作用是冷却,2是液压循环系统,提供直线运动的动力,3是压缩空气系统,给各个阀门和执行器提供动力第六个不同就是这个巨型焊机的堆焊是按照参数自动堆焊的实现小电流起弧、自动堆焊、收弧补缩。
其他复杂造作基本实现一件操作。
第七个不同供电方式区间很大,380V、440V、960V、6000V、10000V都对它的胃口。
不过要提前说好供电环境。
前言真空自耗电弧炉是利用弧光放电产生的电弧热能熔炼金属材料的先进设备。
它是在真空状态下将自耗电极接负极,坩埚接正极,通电时两极间产生弧光放电产生5000K(约4700℃)高温使材料熔化。
熔炼时,液态金属以熔滴的形式滴落到坩埚熔池形成铸锭,熔炼金属的过程是精炼的过程,起到提纯作用,达到了净化金属,改善结晶结构;在电弧高温加热下的熔池受到电磁搅拌,一些易挥发杂质将加速扩散到熔池表面被真空去除,合金的化学成分经搅拌可达到充分均匀,提高性能的目的。
在电弧的作用下,自耗电极的不断熔化消耗,熔池不断上升,熔融金属被水冷坩埚逐渐冷凝。
这种炉子主要用于钛、锆、钼活泼金属,以及特铁金属的熔铸。
真空自耗冷却速率
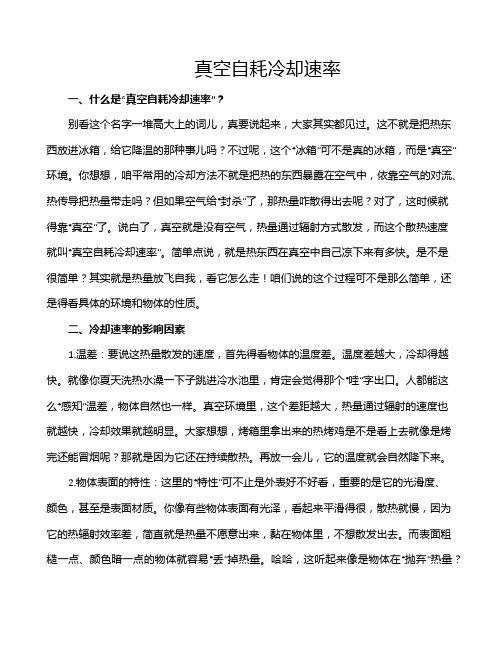
真空自耗冷却速率一、什么是“真空自耗冷却速率”?别看这个名字一堆高大上的词儿,真要说起来,大家其实都见过。
这不就是把热东西放进冰箱,给它降温的那种事儿吗?不过呢,这个“冰箱”可不是真的冰箱,而是“真空”环境。
你想想,咱平常用的冷却方法不就是把热的东西暴露在空气中,依靠空气的对流、热传导把热量带走吗?但如果空气给“封杀”了,那热量咋散得出去呢?对了,这时候就得靠“真空”了。
说白了,真空就是没有空气,热量通过辐射方式散发,而这个散热速度就叫“真空自耗冷却速率”。
简单点说,就是热东西在真空中自己凉下来有多快。
是不是很简单?其实就是热量放飞自我,看它怎么走!咱们说的这个过程可不是那么简单,还是得看具体的环境和物体的性质。
二、冷却速率的影响因素1.温差:要说这热量散发的速度,首先得看物体的温度差。
温度差越大,冷却得越快。
就像你夏天洗热水澡一下子跳进冷水池里,肯定会觉得那个“哇”字出口。
人都能这么“感知”温差,物体自然也一样。
真空环境里,这个差距越大,热量通过辐射的速度也就越快,冷却效果就越明显。
大家想想,烤箱里拿出来的热烤鸡是不是看上去就像是烤完还能冒烟呢?那就是因为它还在持续散热。
再放一会儿,它的温度就会自然降下来。
2.物体表面的特性:这里的“特性”可不止是外表好不好看,重要的是它的光滑度、颜色,甚至是表面材质。
你像有些物体表面有光泽,看起来平滑得很,散热就慢,因为它的热辐射效率差,简直就是热量不愿意出来,黏在物体里,不想散发出去。
而表面粗糙一点、颜色暗一点的物体就容易“丢”掉热量。
哈哈,这听起来像是物体在“抛弃”热量?其实也差不多。
这就是为什么咱们看到一些物体表面总是刷上一层特殊的涂层,增加散热效率,就好比穿上了“隔热服”一样。
3.真空的压力:真空环境的“真空”程度,直接决定了冷却速率。
高压环境下的真空,热量传递会变慢;而低压的真空,热量传递更迅速。
听起来好像高压更厉害,对吧?但其实高压会限制热量的辐射,因为空气分子太多,它们反而挡住了热量的“逃跑”。
- 1、下载文档前请自行甄别文档内容的完整性,平台不提供额外的编辑、内容补充、找答案等附加服务。
- 2、"仅部分预览"的文档,不可在线预览部分如存在完整性等问题,可反馈申请退款(可完整预览的文档不适用该条件!)。
- 3、如文档侵犯您的权益,请联系客服反馈,我们会尽快为您处理(人工客服工作时间:9:00-18:30)。
真空自耗电弧炉1 VAR的结构组成及其特点VAR 炉由真空系统、电极驱动机械系统、铜坩埚及冷却循环系统、直流电源、自动和手动控制系统、稳弧搅拌系统、检测和自动记录系统等部分组成。
VAR 炉现已处于较为完善的阶段,在结构上具有同轴性、再现性和灵活性特征,正在向更大容量和远距离精确操作发展。
VAR炉采用先进的计算机自动电控和数据收集系统,能够对给定的合金和铸锭规格建立良好的熔炼模式,并分析熔炼过程中出现的问题,获得良好的铸锭表面质量和内在冶金质量,提高金属成品率。
2 真空自耗炉的工作原理真空自耗炉主要用于钛和钛合金的生产。
图1所示为真空自耗炉原理示意图。
该炉有一个结晶器,结晶器装入水冷的外套里,并与熔炼电源的正极相接。
电源的负极与活塞即“拉杆”连接,该拉杆通过滑动的真空密封进入炉内。
待熔炼的钢材(即电极)夹紧在控制活塞的机座上,并且在炉膛抽空以后,下降电极与在结晶器底部的同样材料的金属垫料触发电弧。
当电极由于输人功率而熔化时,就可通过液压控制系统下降活塞,以便保持电极同由此而形成的熔池之间的距离不变。
当熔炼继续进行时,在结晶器里就逐渐地形成了一支新的锭料。
3 VAR基本的工艺流程:工艺流程:混料一压制电极一电极和残料焊接成自耗电极一熔炼一铸锭处理一检验。
3.1 真空自耗原料由纯料、合金元素、返回料等组成。
3.2 电极制备经过混料后,添加或未添加残料的原料通过压制、焊接,制成自耗电极。
焊接方法为自耗电弧焊或等离子焊,焊接应进行充分的保护或在惰性气氛下的容器里进行,以避免污染和难熔氧化物或氮化物的形成。
应严禁使用钨极氩弧焊。
制备的自耗电极必须具备足够的机械稳定性,即使在熔炼过程中加热时也不会开裂.并确保电流畅通无阻地通过。
3.3 熔炼过程炉子采用真空系统,是为了避免空气污染,同时有效去除氢气和氯化物。
水冷铜坩埚给金属的熔炼提供了适宜的容器,只要冷却适当,熔融金属就在其表面形成一层“渣壳”.既保护坩埚,又不被坩埚污染。
生产中,应对重熔电极和炉室彻底清理,清除外来物和炉室中的冷凝物,诸如氧化物、氯化物等。
这些是造成氧、氮含量增加、引起铸锭冶金质量问题的潜在来源。
熔炼的初始电流设置应低一些,电压在30V~5OV 之间,主要取决于电极和炉室中的气体含量、电流大小、电弧间隙、电极的电阻及铸锭的尺寸。
形成熔池后,将熔炼功率增加到高于主熔炼期所预定的水平.以弥补坩埚底部的激冷效应。
熔炼期间,功率应保持不变,直到熔炼末期,这时按照预定热封顶工艺降低功率,以便把锭料头部缩孔和偏析减少到最小。
对于特定的合金和锭料直径.一旦确定了合适的熔炼条件,较大锭料所要求的电流通常可以简单地按比率推算。
因为锭料单位面积的功率维持不变.电流与面积保持正比关系。
表1为电流和电流密度值对比数据熔炼时,要保证电极与坩埚间隙为50mm--80mm或更大,一方面确保安全性,另一方面为气体排除提供良好的通道。
电弧长度(弧距)通常控制在25 mm~50 mm或更大,太短会造成频繁的短路,降低铸锭质量,太长会使电弧移动,击穿坩埚壁。
弧距不能超过电极和坩埚之间的最小距离。
在高的电流情况下,如果电弧集中在坩埚表面某一位置就会瞬间击穿坩埚而造成严重的爆炸事件。
为此应采取和安装有效的安全预防设施,包括炉子观测系统、自动断电元件、爆破口、防爆墙。
采用液态钠一钾作为冷却剂就不存这种危险性,相应不必采取防爆措施。
3.4 压力炉内压力和原料的气体含量影响电弧行为和产品质量。
当电弧区内残余压力增大到13 Pa~66 Pa时就达到辉光放电的临界压力范围,电弧燃烧不稳定.甚至导致电弧熄灭.严重时会产生边弧而击穿设备,依据实践经验,VAR 通常在0.13Pa --1.3 Pa压力下进行。
高的弧电压则产生长弧。
3.5 热封顶和冷却热封顶的目的是减少铸锭头部的缩孔、疏松和偏析区,减少铸锭的切头量.提高成品率。
最后一次熔炼,当电极消耗到9O%以上时,应逐级降低电流.使熔池凝固不形成有害的缺陷。
大规格铸锭的热封顶需要进行几个小时,同时应保证有足够的电极材料,尤其头部应是整个铸锭最后凝固的部分。
铸锭一般在真空或惰性气体保护下冷却至400 ℃以下出炉。
惰性气体保护会加速冷却,如果还需进一步的熔炼,应避免铸锭氧化。
有些对热裂纹较敏感的合金成品锭,应在热态时出炉.然后缓慢冷却。
3.6 磁场效应电弧是一种由流动的电子和离子化的粒子组成的电现象,必然受到磁场影响而发生偏转。
通常的做法是在水套上缠绕稳弧线圈,以此对电弧和熔池更好地控制。
稳弧线圈通常有两种形式,一种是永久固定在水套上,基本上覆盖整个坩埚;另一种则较短并可移动,只用来覆盖弧区及熔池的上部区域,随熔池的升高而不断升高,对于拉锭系统则保持在某一位置不动。
理论上,电磁搅拌或稳定的必要条件可根据以下三点确定:①熔池的有意搅拌和搅动;②防止熔池旋转;③熔池中热分布的影响。
为使合金的化学成分均匀,在初次熔炼时希望熔池旋转,旋转由平行于坩埚轴的固定磁场产生。
实践证明,流过坩埚的电流不对称,供电线路、铁质结构及附近设备磁场的影响都会引起熔池的瞬时旋转,进一步影响铸锭的结晶凝固并降低冶金质量。
合理的稳弧线圈布置和参数给定能够使电弧围绕电极平稳缓慢地移动,防止集中在坩埚壁上击穿坩埚,使成品铸锭表面均匀。
这时,熔池也在缓慢轻微旋转。
若搅拌太快,会产生喷溅,形成较高的壳、差的表面及内部缺陷;旋转慢和不旋转造成铸锭表面质量发生变化然而.若要得到内外质量都好的成品锭,还必须满足其它的一些条件,包括最佳的电流值,电极和坩埚壁之间的间隙,电弧长度及较低的气体含量。
熔池的搅拌是获得良好的结晶组织以利于锻造加工的基础。
线圈的电流连续不断地沿着一个方向流动,凝固时,晶粒会在某一方向优先长大,对锻造不利。
实际中,可每隔几秒将直流电极性转换,补偿熔池固有的旋转。
这虽影响电弧,但对实际熔池影响很少。
这样就有可能控制电弧,使其移动到坩埚壁上的几率减小,同时熔池的涡流效应减轻,实际熔池变浅。
3.7 坩埚比也称填充比,是指电极与坩埚直径之比。
它是影响铸锭质量和安全生产的重要参数之一。
对于钛,坩埚比一般在0.625~0.88。
坩埚比大,铸锭表面质量好,致密度高,但易产生边弧。
3.8 铸锭熔化次数为了保证最终产品的均匀性.两次熔炼是必要的。
一次熔炼的铸锭作为二次熔炼的电极.一次熔炼使铸锭初步合金化、均匀化及去除挥发性物质和气体;二次熔炼获得成份分布均匀、表面质量好的铸锭。
而三次熔炼是为了获得更好的成份均匀性。
3.9 铸锭规格的确定铸锭尺寸不仅影响铸锭的质量,而且对生产率也有影响。
一般,铸锭尺寸依据半成品尺寸来确定。
大规格铸锭具有实用经济性优点,但增大铸锭的尺寸.偏析倾向就增高。
铸锭长度的确定必须考虑到炉子的生产率。
一定的电流下.随着铸锭长度的增加,生产率增加较小。
应当指出.长度的增加应合理,否则,会给生产带来困难,实际上起不到提高生产率的作用。
一般铸锭的合理长度可依下式确定:L =0.1 6II为熔化电流;0.16为系数,单位为mm/A。
4 VAR铸锭的质量问题至今,钛铸锭冶金技术上一直存在着冶金缺陷的难题。
缺陷的来源很多,类型现在已经得到认识。
4.1 I类缺陷:也称低密度夹杂、高间隙缺陷.指间隙元素N,O 稳定的α区,其硬度比邻近基体区高而塑性低。
缺陷区具有较高的β转变温度,经机械加工,会伴随产生孔洞,通常用超声波探伤可以发现。
图2是I类缺陷的典型金相照片。
最新的一些研究表明,在任何存在氧化反应的地方,都是产生这种缺陷的一个潜在原因,包括燃烧、炉子漏气、焊接时保护不好、外来杂质、低级残料及未混合均匀的TiO 添加剂等。
三次重熔是消除I类缺陷的一种手段,但对于大颗粒及难熔颗粒或者当熔炼本身就有问题时,三次重熔也并不是一个彻底的解决方法。
I类缺陷出现的位置往往是很小的、不连续的区域,这些区域会引起应力集中,因此是最有害的,绝对不允许存在的。
图2 Ti一6Al一4V 合金中典型的I类缺陷,100X4.2Ⅱ类缺陷也称软α偏析,是异常稳定的α区,可以延伸到部分β晶粒,是α稳定元素如A1,Sn偏析造成的。
缺陷区比邻近基体区的初生α比例和显微硬度高。
似乎此类缺陷只在钛合金中出现并在缩孔中形成,缩孔部位的低倍组织照片显示为或亮或暗的浸蚀线条(图3)。
这些线条是缩孔区由于A1,Sn或其它易挥发的组分气化和重新沉积而产生的贫化或富集区。
合理的补缩工艺可以避免这些缺馅的产生。
通常的检测方法不能查出这些缺陷,但当缺陷在表面上时,可以通过特殊浸蚀方法观测到。
4.3铸锭气孔(空洞)在成品或半成品钛合金锻件上发现存在气孔,呈椭圆形的空洞,虽经过大变形量加工也不能愈合,说明空洞内不是真空而是有一定气体存在其中。
空洞周围并不伴随有上述I类缺陷的特征。
除了缩孔外,重熔可基本上消除铸锭气孔。
研究表明,气孔的形成与海绵钛中所含的残余氯化物有关。
海绵钛中的盐类在固相金属中基本不溶解.但在液相中却形成蒸汽气泡。
真空熔炼中,氢含量很低,通常不足以形成气孔。
缩孔部位的气孔,是由于金属收缩和易挥发组分形成的,可以通过补缩工艺得以避免。
据报道,高熔化速率要比低熔化速率产生气孔的几率大。
熔炼速率低.有利于熔体脱气;熔池浅,可以减少凝固阶段形成的缩孔。
然而在低熔炼速率下及补缩过程中应避免压力过低造成一定量的铝损失。
4.4成分偏析成分偏析是在钛锭结晶中形成的各部分成分不均匀的现象。
偏析大体分为两类:一类是宏观偏析,经过酸腐蚀后用肉眼可见;另一类是微观偏析,只有在显微镜下才能观察到。
对合金元素偏析已进行了广泛的研究。
理论上讲,凝固过程都是在一定温度范围内完成的,由于固态物质扩散很慢,造成溶质在凝固过程中的重新分配,形成偏析。
偏析的大小与合金分配系数、凝固速率、液相的自然和受迫运动、扩散、晶粒尺寸及晶体形成的方式等有关,最为关键的是合金分配系数,其它因素则与具体操作工艺有关,可通过调整工艺来改进。
合金分配系数是指平衡时固液两相中溶质浓度比:K0=Cs/CL,CS为溶质在固相中的浓度,CL为溶质在液相中的浓度。
Ko> 1称为正偏析;K。
< 1称为负偏析。
N,Nb,Mo,C,O 等元素,其K。
>1,产生正偏析。
K。
<1的元素有:Mn,Sn.Cu,Si,Ni,Cr.Co,V,Fe,Zr5 铸锭质量铸锭质量好坏对加工材成品率及成本有重要影响。
影响铸锭质量的因素较多,主要与使用的原料、熔炼工艺参数有关。
自耗电极不洁净,气体含量过高,在熔炼过程中会产生过多的喷溅,从而附着在坩埚壁上,形成“壳”。
熔炼时选择适当的炉内压力,确保电弧稳定,不出现辉光放电现象,避免恶化铸锭质量。
重熔时.应对电极表面清洗.去除凝结的氯化物,并选择适当的电流和导电条件.保证电弧围绕电极端头平缓移动。
坩埚比过小.电弧的分布面积则小、辐射损失大,结晶器壁处的金属不能很好地熔融。