4.7脱模机构解析
第10讲 脱模机构设计
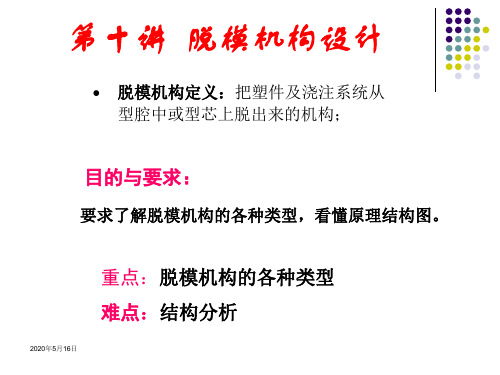
二级推出机构产生的原因
由于特殊形状或自动化生产的需要, 在一次脱模动作完成后,仍难于从 型腔中取出或不能自动脱落。
有时为避免一次脱模塑件受力过大,也采用二次脱模推出, 以保证塑件质量。
2013年7月14日
1.弹簧式二级推出机构
这种方法结构简单,装 配后所占面积小,缺点 是动作不可靠,弹簧容 易失效,需要及时更换。
2013年7月14日
2.斜楔滑块式二次推出机构
8-14斜楔滑块式二次推出机构 1- 动模座板 2-推板 3-弹簧 4-滑块 5-销钉 6-斜楔; 7-推件板 8-推杆 9-型芯 10-中心推杆 11-复位杆
2013年7月14日
3.三角滑块式二级推出机构
图8-15 三角滑块式二次推出机构 1- 一次推板 2- 三角滑块 3- 二次推板 4-推杆固定板 5-斜楔杆 6-推杆 7-动模型腔板 8-型芯 9-推杆
2013年7月14日
1.推杆推出机构
(1)推出机构组成: 推杆、拉料杆、复位杆、推杆固定板、推杆垫板、
推杆导柱、推杆导套、限位钉。
2013年7月14日
(2)推杆的设计
• • 适用范围:脱模阻力小的简单塑件 特点:简单、灵活,但与塑件接触面积小,易将 塑件顶变形或损坏。
推杆的形状及尺寸 推杆的固定及装配 推杆推出位置的选择
(四)螺纹塑件推出机构
手动脱螺纹机构
模内手动脱螺纹机构 齿轮齿条脱螺纹机构 直角式注射机脱螺纹机构 推杆轴承旋转式脱出机构
2013年7月14日
1.手动脱螺纹机构
2013年7月14日
手动脱螺纹机构
2013年7月14日
手动脱螺ቤተ መጻሕፍቲ ባይዱ机构
2013年7月14日
2.模内手动脱螺纹机构
模具的脱模机构

模具的脱模机构胶件脱模是注射成型过程中最后一个环节,脱模质量好坏将最后决定胶件的质量;当模具打开时,胶件须留在具有脱模机构的半模(常在动模)上,利用脱模机构脱出胶件。
脱模设计原则:(1)为使胶件不致因脱模产生变形,推力布置尽量均匀,并尽量靠近胶料收缩包紧的型芯,或者难于脱模的部位,如胶件细长柱位,采用司筒脱模。
(2)推力点应作用在胶件刚性和强度最大的部位,避免作用在薄胶位,作用面也应尽可能大一些,如突缘、(筋)骨位、壳体壁缘等位置,筒形胶件多采用推板脱模。
(3)避免脱模痕迹影响胶件外观,脱模位置应设在胶件隐蔽面(内部)或非外观表明;对透明胶件尤其须注意脱模顶出位置及脱模形式的选择。
(4)避免因真空吸附而使胶件产生顶白、变形,可采用复合脱模或用透气钢排气,如顶杆与推板或顶杆与顶块脱模,顶杆适当加大配合间隙排气,必要时还可设置进气阀。
(5)脱模机构应运作可靠、灵活,且具有足够强度和耐磨性,如摆杆、斜顶脱模,应提高滑碰面强度、耐磨性,滑动面开设润滑槽;也可渗氮处理提高表面硬度及耐磨性。
(6)模具回针长度应在合模后,与前模板接触或低于0.1mm,如图8.1.1所示。
(7)弹簧复位常用于顶针板回位;由于弹簧复位不可靠,不可用作可靠的先复位。
1 顶针、扁顶针脱模胶件脱模常用方式有顶针、司筒、扁顶针、推板脱模;由于司筒、扁顶价格较高(比顶针贵8~9倍),推板脱模多用在筒型薄壳胶件,因此,脱模使用最多的是顶针。
当胶件周围无法布置顶针,如周围多为深骨位,骨深/15mm时,可采用扁顶针脱模。
顶针、扁顶针表面硬度在HRC55以上,表面粗糙度Ra1.6以下。
顶针、扁顶针脱模机构如图8.1.1所示,设置要点如下:(1)顶针直径 d£Ø2.5mm时,选用有托顶针,提高顶针强度。
(2)扁顶针、有托顶针 K/H。
(3)顶位面是斜面,顶针固定端须加定位销;为防止顶出滑动,斜面可加工多个R小槽,如图8.1.2所示。
第七节脱模机构1
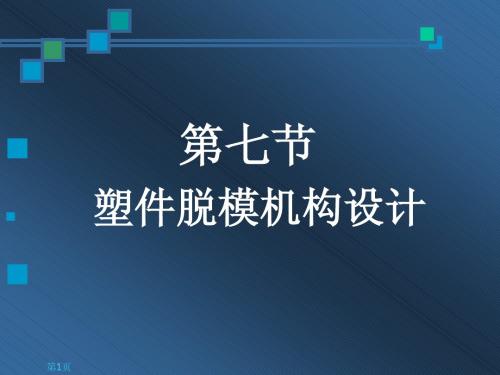
第34页
应用: ①一次脱模难以顶出制品或不 能自动脱 落的情况。 ②一次顶出,制品受力较大, 易变形或损坏的情况。
第35页
二级脱模机构可分为三大类: (一)气动二级脱模机构 (二)单顶出板二级脱模机构
(三)双顶出板二级脱模机构
第36页
第37页
第38页
第39页
第10页
第11页
2、顶出
形状与尺 寸
第12页
3、顶杆与顶出固定板的连接形式
第13页
(二)顶管脱模机构
特点: 塑件受力均匀,推出时平稳可靠, 塑件不易损坏,不会留下明显接触痕 迹。 应用场合: 环形、圆筒形、中间带孔的制品.
第14页
第1ቤተ መጻሕፍቲ ባይዱ页
(三)推板脱模机构 特点: 顶出力均匀,运动 平稳,顶出力大。 不需设回程杆。
应用场合: 薄壁容器, 壳体形制品, 以及不能在 表面留有顶 出痕迹的制 品。
第16页
第17页
(四)活动镶件脱模机构 应用场合: 结构特殊的制品,如有螺纹、内 凹的制品。
第18页
第19页
(五)多元件综合脱模机构 应用场合: 大型深腔壳体、薄壁、有局部凸 台、有金属镶件的复杂制品。
第20页
第21页
第4页
④定模拔模斜度大于动模。 ⑤用拉料杆拉住凝料产品,使其 留于动模上。 ⑥定模温度低于动模,使制品与 定模接触的部分收缩率大,粘 附性小。
第5页
2、产品不变形不损坏
具体方法: ①顶出力作用点尽可能靠近 型芯 ②顶出力作用于产品刚度和 强度较大的部位 ③作用面积尽可能大
第6页
3、良好的产品外观 顶出产品的位置应尽量设在 制品内部,以免影响制品外观。 4、结构可靠 脱模机构要工作可靠,运动 灵活,制造方便,配换容易。
说明推管脱模机构的基本结构与工作原理

轻松掌握推管脱模机构的基本结构与工作原
理
推管脱模机构是一种常用于塑料、橡胶、玻璃等领域的设备,主要用于将模具内的成型件推出或取出,从而完成整个成型过程。
以下是推管脱模机构的基本结构与工作原理:
一、基本结构
1.主体部分:由机架、滑块、导柱等组成,支撑并引导推板和脱模板的运动。
2.推板:安装在主体上方,提供顶出力,将成型件顶出模具。
3.脱模板:安装在主体下方,用于接受成型件。
4.传动机构:通过电动机、减速器、连杆等传动装置,驱动推板和脱模板运动。
二、工作原理
当模具内的成型件形成后,推板开始向上移动,提供顶出力,将成型件顶出模具。
同时,脱模板开始向上移动,接受并保持成型件,完成脱模工作。
整个推板和脱模板的运动由传动机构驱动,使推板和脱模板可以快速且精确地完成推出和取出的过程。
需要注意的是,推管脱模机构在工作时,需根据成型件的大小、重量、材质等条件,合理地选择推出力和脱模速度,以确保成型件顺
利地推出或取出。
此外,还需根据实际情况进行维护和保养,以保证设备的长期稳定运行。
以上就是推管脱模机构的基本结构与工作原理的介绍。
掌握了这些知识,我们便能更加深入地了解该设备,为其选择、使用和维护提供指导。
4.7脱模机构解析
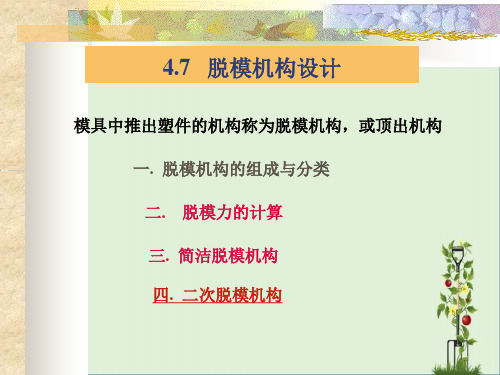
模具中推出塑件的机构称为脱模机构,或顶出机构 一. 脱模机构的组成与分类 二. 脱模力的计算 三. 简洁脱模机构 四. 二次脱模机构
一. 脱模机构的组成与分类
组成
脱模机构一般由三局部组成:推出部件,导向部件,复位部件 推出部件:推杆、拉料杆、推杆固定板,推板等
导向部件:导柱、导套 复位部件:复位杆
3〕直径和数量
保证足够的刚度。可设计成阶梯形
数量应保证顺当脱模且不损伤塑件表观
4〕推杆材料及热处理要求
材料常用T8A,T10A或65Mn,碳素工具钢热处理要求硬度HRC50~54,
弹簧钢热处理硬度要求HRC50~54。
5〕推杆固定形式
推杆
推杆
推杆
推杆
推杆
推杆
(a)
(b)
(c)
(d)
(e)
(f)
图4-79 推杆的固定形式
3〕气动脱模: 利用压缩空气将塑件吹出。
2、按模具构造分
一次推出脱模〔简洁脱模〕、二次推出脱模、动定模双向推出脱模、 挨次脱模、带螺纹塑件脱模塑件不变形损坏 机构推出中心与脱模力中心相重合,推出力分布均匀,
作用点尽可能靠近型芯防止塑件脱模后变形;推出力施于 塑件刚性和强度最大的地方〔如凸缘、加强筋等〕。
留有0.2~025mm的间隙 锥面 协作
推件板常用材料为45钢,热处理要求28~32HRC
四. 二次脱模机构
作用:由于塑件的特殊外形或生产自动化的需要;为避 开一次脱模塑件受力过大。
单推板
摆块拉板式二级脱模机构
双推板
三角滑块式双推板二次脱模机构
螺纹的脱模
强制脱出:弹性较好或较松软的塑件,用于精 度不高和小批量生产的塑件 模外脱出:活动螺纹镶块
说明推管脱模机构的基本结构与工作原理

说明推管脱模机构的基本结构与工作原理推管脱模机构是一种用于混凝土管道生产中的关键设备,其作用是在混凝土管道浇筑完成后帮助将管道从模具中取出并进行后续处理。
这种机构的基本结构和工作原理对于混凝土管道生产的效率和质量具有重要影响。
一般来说,推管脱模机构主要由推杆、升降装置、支撑架、固定块、导向架等部件组成。
推杆是推动混凝土管道脱模的关键部件,其长度和直径需根据具体的管道尺寸而定。
升降装置用于控制推杆的上下运动,以便将管道顺利地脱出模具。
支撑架和固定块则用于固定模具和管道,保证在脱模过程中不发生位移或倾斜。
导向架则用于引导管道在脱模过程中保持正确的位置和方向。
推管脱模机构的工作原理主要是通过推杆的推动和升降装置的控制来完成的。
在脱模前,首先需要将混凝土管道浇筑完成,待混凝土充分硬化后,启动机构将推杆插入管道的一端,并通过升降装置将推杆顶起,逐步推动管道从模具中取出。
在脱模过程中,支撑架和固定块起到了固定管道和模具的作用,保证脱模过程的稳定性。
导向架则通过引导管道的运动,确保管道脱模时保持正确的位置和方向,避免管道变形或损坏。
推管脱模机构的设计和使用对于混凝土管道生产具有重要意义。
合理的结构设计和稳定的工作原理可以提高生产效率,减少生产成本,同时也可以保证混凝土管道的质量和准确度。
因此,在混凝土管道生产中,推管脱模机构是一种不可或缺的设备。
推管脱模机构作为混凝土管道生产中的关键设备,其基本结构和工作原理对于生产效率和产品质量具有重要影响。
通过合理的设计和稳定的工作原理,推管脱模机构可以帮助生产厂家提高生产效率,降低生产成本,保证产品质量,是混凝土管道生产中不可或缺的设备之一。
脱模机构
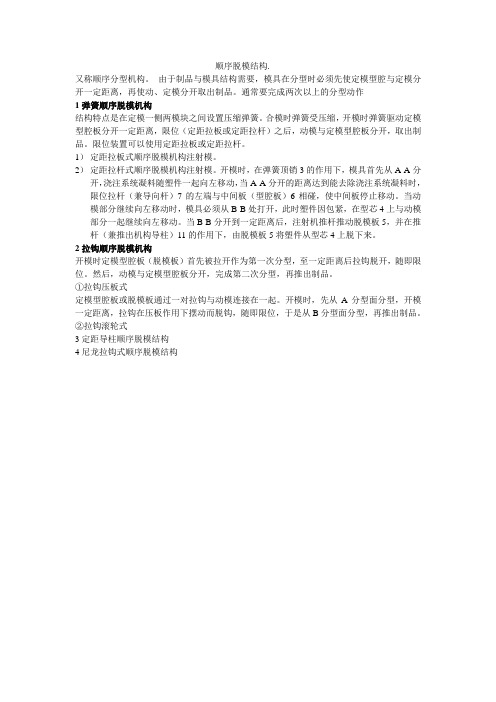
顺序脱模结构.
又称顺序分型机构。
由于制品与模具结构需要,模具在分型时必须先使定模型腔与定模分开一定距离,再使动、定模分开取出制品。
通常要完成两次以上的分型动作
1弹簧顺序脱模机构
结构特点是在定模一侧两模块之间设置压缩弹簧。
合模时弹簧受压缩,开模时弹簧驱动定模型腔板分开一定距离,限位(定距拉板或定距拉杆)之后,动模与定模型腔板分开,取出制品。
限位装置可以使用定距拉板或定距拉杆。
1)定距拉板式顺序脱模机构注射模。
2)定距拉杆式顺序脱模机构注射模。
开模时,在弹簧顶销3的作用下,模具首先从A-A分开,浇注系统凝料随塑件一起向左移动,当A-A分开的距离达到能去除浇注系统凝料时,限位拉杆(兼导向杆)7的左端与中间板(型腔板)6相碰,使中间板停止移动。
当动模部分继续向左移动时,模具必须从B-B处打开,此时塑件因包紧,在型芯4上与动模部分一起继续向左移动。
当B-B分开到一定距离后,注射机推杆推动脱模板5,并在推杆(兼推出机构导柱)11的作用下,由脱模板5将塑件从型芯4上脱下来。
2拉钩顺序脱模机构
开模时定模型腔板(脱模板)首先被拉开作为第一次分型,至一定距离后拉钩脱开,随即限位。
然后,动模与定模型腔板分开,完成第二次分型,再推出制品。
①拉钩压板式
定模型腔板或脱模板通过一对拉钩与动模连接在一起。
开模时,先从A分型面分型,开模一定距离,拉钩在压板作用下摆动而脱钩,随即限位,于是从B分型面分型,再推出制品。
②拉钩滚轮式
3定距导柱顺序脱模结构
4尼龙拉钩式顺序脱模结构。
塑料模具课件_脱模机构
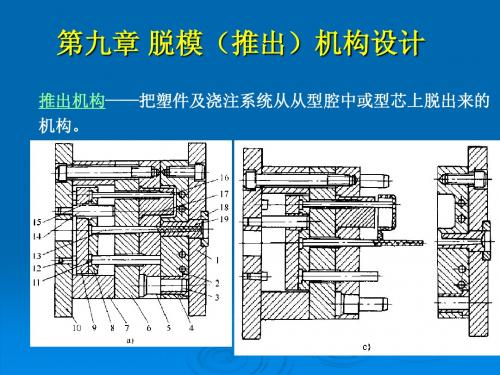
3.模内旋转的脱模方式
(1)螺纹塑件的止转形式
模具设自动脱螺纹机构时塑件外形有止转结构,通常为花纹。
常用模内旋转脱螺纹机构主要有手动脱螺纹和机动脱螺 纹两种。
(2) 手动脱螺纹机构
(3) 机动脱螺纹机构
原理:利用开模时的直线运动,通过齿轮齿条的运动,使 螺纹型芯作回转运动而脱离塑件。 图为,锥齿轮脱螺纹型 芯结构,它用于侧浇口多 型腔模,螺纹型芯只要作 回转运动就可脱出塑件。
p—因塑件收缩对型芯产生的单位正压力(12~20MPa) A—塑件包紧型芯的侧面积(mm2)
F脱= pA(f·cosα-sinα)
总脱模力等于F总=F脱+F大气(大气压力影响:引气、不引气) 以上对脱模力的计算是一种比较粗略的方法。 计算脱模力是为了校核设备的顶出力是否足够,以及校核推出 元件的刚度强度及可靠性。
为减少脱模过程中推件板与型芯之间的摩擦,两者之间留有0.2~ 0.25mm的间隙,并采用锥面配合,以防止推件板 偏斜溢料,锥面 的斜度约取3~5˚左右,图 (b)。
引气装置: 对于大型深腔薄壁容器,推板脱模时 塑件部易形成真空, 使脱模困难,甚至还会使塑件变形或损坏,应在凸模上附设引 气装置,如图(推件板引气)。(推件板不引气)
加粗,增加刚性。
顶盘式推杆:锥面推杆,推出面积较大,适合于深筒形塑件 推出。
b)
c)
d)
2.推杆的固定及配合
(1)推杆的固定
2.推杆的配合
推杆固定板上的孔为d+1mm;推杆台阶部分的直径为
d+5mm;推杆固定板上的台阶孔为d+6mm。推杆与固定 板配合长度为S(一般采用H8/f8配合)
S 可取12~15mm;当d>5mm时, S=(2~3)d (d为推杆直径),配合部分表面Ra=0.8μm。 推杆与塑料接触并与孔经常摩擦,因此多采用热处理后硬度 高的材料制作。推杆材料常用T8A、T10A等碳素工具钢 (50 ~ 54HRC自制推杆)或65Mn (46 ~ 50HRC市场上的 推杆标准件)
1.4.7 顶出(脱模)机构设计[共5页]
![1.4.7 顶出(脱模)机构设计[共5页]](https://img.taocdn.com/s3/m/b6353f20ba0d4a7303763ab4.png)
46与︱缺点:侧向抽拔力较小。
行位回位时,大部分行位需由斜导柱启动,斜导柱受力状况不好。
特别注意:当驱动行位的斜导柱或斜滑板开始工作前,前、后模必须由导柱导向。
1.4.7 顶出(脱模)机构设计胶件脱模是注射成型过程中最后一个环节,脱模质量好坏将决定最后胶件的质量;当模具打开时,胶件须留在具有脱模机构的半模(常在动模)上,利用脱模机构脱出胶件。
脱模设计原则如下。
①为使胶件不致因脱模产生变形,推力布置应尽量均匀,并尽量靠近胶料收缩包紧的型芯,或者难于脱模的部位,如胶件细长柱位采用司筒脱模。
②推力点应作用在胶件刚性和强度最大的部位,避免作用在薄胶位,作用面也应尽可能大一些,如突缘、(筋)骨位、壳体壁缘等位置。
筒形胶件多采用推板脱模。
③避免脱模痕迹影响胶件外观,脱模位置应设在胶件隐蔽面(内部)或非外观表面;对透明胶件尤其需注意脱模顶出位置及脱模形式的选择。
④避免因真空吸附而使胶件产生顶白、变形,可采用复合脱模或用透气钢排气,如顶杆与推板或顶杆与顶块脱模,顶杆适当加大配合间隙排气,必要时还可设置进气阀。
⑤脱模机构应运作可靠、灵活,且具有足够强度和耐磨性,如摆杆、斜顶脱模,应提高滑碰面强度、耐磨性,滑动面开设润滑槽;也可采用渗氮处理,提高表面硬度及耐磨性。
⑥模具回针长度应在合模后,与前模板接触或低于0.1mm,如图1-106所示。
图1-106 顶出(脱模)机构⑦弹簧复位常用于顶针板回位;由于弹簧复位不可靠,不可用作可靠的先复位。
1.顶针、扁顶针脱模胶件脱模常用方式有顶针、司筒、扁顶针、推板脱模;由于司筒、扁顶针价格较高(比顶针价格贵8~9倍),推板脱模多用在筒型薄壳胶件中,因此,脱模使用最多的是顶针。
当胶件周围无法布置顶针,如周围多为深骨位,骨深大于或等于15mm时,可采用扁顶针脱模。
顶针、扁顶针表面硬度在HRC55以上,表面粗糙度R a在1.6以下。
顶针、扁顶针脱模机构如图1-107所示,设置要点如下。
①顶针直径d≤φ2.5mm时,选用有托顶针,提高顶针强度。
第10讲-脱模机构设计-PPT
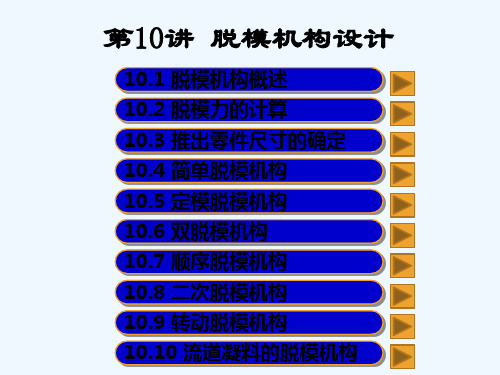
推杆的位置 1-推杆(兼复位杆)2-塑件 3-推杆 4-型芯 5-盘形推杆
10.4.1 常见脱模机构的类型
1.推杆脱模机构
2)应设在塑件强度刚度 较大处。
推杆不宜设在塑件的薄壁
处,应尽可能设在塑件厚壁、
凸缘处及筋与筋或壁与筋的交
点上,以免使塑件变形损坏。
如必须设在薄壁处时,应
增大推杆截面积,以降低单位
大家有疑问的,可以询问和交流
可以互相讨论下,但要小声点
10.2 脱模力的计算
概念
(1)定义:指将塑件从型芯上脱出时所需克服的阻力。 包括:
成型收缩的包紧力; 不带通孔的壳体类塑件的大气压力; 机构运动的摩擦力; 塑件对模具的粘附力;
10.2.1 影响脱模力的因素
(2)影响脱模力的因素
型芯成型部分的表面积及其形状. 收缩率及摩擦系数. 塑件壁厚和包紧型芯的数量. 型芯表面粗糙度. 成型工艺:P注、t冷.
对于生产批量很大的制品,为提高生产率,可 采用结构比较复杂、自动化程度比较高的脱模机构。
10.1.3 推出机构的设计原则
5)推出零件应有足够的强度、刚度和硬度。 6)合模时应正确复位。并保证不与其他模具零 件相干涉。 7)脱模行程应恰当。应保证推出零件运动的初 始位置和终止位置恰当合理,以保证制品可靠脱模。
由上面的式子可以看影响因素脱模力的大小主要有以下几点:
(l)主要与塑件包络型芯侧面积的大小有关。型芯的侧面积越大,所需的脱 模力也越大。 (2)与型芯的脱模斜度有关。脱模斜度越大,所需的脱模力越小。 (3)与型芯的表面粗糙度有关。表面粗糙度值越低,型芯表面越光洁,所需 的脱模力就越小。 (4)与塑件的结构有关。塑件厚度越大、形状越复杂,冷却凝固时所引起的 包紧力和收缩应力越大,则所需的脱模力越大。 (5)与注射工艺有关。 注射压力越大,则包紧型芯的力越大,所需脱模力越大; 脱模时模具温度越高,所需的脱模力越小; 塑件在模内停留时间越长,所需的脱模力越大。 (6)与成型塑件的塑料品种有关。不同的塑料品种,由于分子的结构不一样, 因而它们的脱模力也不一样。
说明推管脱模机构的基本结构与工作原理

说明推管脱模机构的基本结构与工作原理推管脱模机构是一种常用于管材生产中的设备,其主要作用是将成型的管材从模具中推出,以便进行下一步的加工和处理。
本文将从基本结构和工作原理两个方面来介绍推管脱模机构。
一、基本结构
推管脱模机构主要由以下几个部分组成:
1. 推杆:推杆是推管脱模机构的核心部件,其作用是将成型的管材从模具中推出。
推杆通常由高强度合金钢制成,具有较高的耐磨性和耐腐蚀性。
2. 推杆导向机构:推杆导向机构是用来保证推杆在运动过程中的稳定性和精度的。
通常采用滑动轴承或滚动轴承来实现。
3. 推杆传动机构:推杆传动机构是用来驱动推杆运动的。
通常采用液压缸或气缸来实现。
4. 推杆保护机构:推杆保护机构是用来保护推杆不受外界损伤的。
通常采用防护罩或防护网来实现。
5. 推杆调节机构:推杆调节机构是用来调节推杆的行程和速度的。
通常采用液压阀或气控阀来实现。
二、工作原理
推管脱模机构的工作原理比较简单,其基本流程如下:
1. 开始推杆运动:当管材成型完成后,推杆传动机构开始工作,驱动推杆向模具内部运动。
2. 推杆推出管材:推杆运动到一定位置后,开始推出成型的管材。
此时,管材被推出模具,进入下一步的加工和处理。
3. 推杆返回原位:当管材被推出后,推杆开始返回原位。
此时,推杆传动机构停止工作,推杆导向机构和推杆调节机构开始工作,保证推杆的稳定性和精度。
推管脱模机构是一种非常重要的设备,其基本结构和工作原理都比较简单,但是在管材生产中起着至关重要的作用。
塑胶件的脱模机构

P cos(f tg)
Q1
P=c·h ·q
1 f sin cos
Q1 P
上式中 α——设计斜度 f——可查表 已知条件
经验公式 P=c·h·q 式中 c——型芯成型部分断面形状的周长
h——型芯成型部分的高度 q—— 塑料的收缩流利(一般取80~120kg/m2)
正压力P的理论计算公式
薄壁件: P 2Etl 1
点浇口自动切断机构
顶管和推板联合推出机构
二.脱模力的计算
对型芯进行受力分析
包紧力P——塑件冷却收缩将型芯或凸模包紧
脱模力Q1——初始脱模力
摩擦力F——塑料与钢材之间的粘附力 F f (P Q1sin )(1)
(1)代入(2)
∑Fx=0
F cos Q1 Psin (2)
f (P Q1 sin ) cos Q P sin
(3) 推板的几种种固定方式
套在型芯上 与顶杆用过盈配合固定在一起、顶杆头部带螺纹 限制推板的脱落
4. 脱模系统的辅助零件
(1) 导向零件:导套、导柱 (2) 回程装置
回程杆回程 顶杆(顶管)兼回程杆回程 弹簧复位
弹簧复位
杠杆复位
摆杆复位
连杆复位
1
气动抽芯、液压抽芯
5.其他一些脱模机构
(2)设计顶杆脱模机构应注意的几点 顶杆直径:一般在2.5~12 顶杆位置 顶杆装配位置: 顶杆与模具装配间隙 材料 顶杆形状
①顶杆直径:一般在2.5~12mm
注意刚度和强度 直径不应过细,应有足够的刚度承受顶出力 当直径在3以下时可设计成阶梯形等形状
②顶杆位置
设置在脱模阻力大的地方 如图
局部有细而深的凸台或筋,应在其底部加设顶杆 如图
浇注系统凝料推出机构

塑料制品成型及模具设计•教学内容4.7.8浇注系统凝料的脱出机构4.7.9 带螺纹塑件的脱模机构•教学目的掌握点浇口式浇注系统凝料的脱出机构和带螺纹塑件的脱模机构的特点、结构、运动原理,了解旋转脱螺纹所需扭矩与功率的计算。
•重点点浇口式浇注系统凝料的脱出机构和带螺纹塑件的脱模机构的特点、结构、运动原理•难点点浇口式浇注系统凝料的脱出机构和带螺纹塑件的脱模机构的特点、结构、运动原理课时:24.7 脱模机构设计4.7.8浇注系统凝料的脱出机构一般来说,普通浇注系统多数是单分型面的二板模具,而点浇口、潜伏式浇口多是双分型面的三板模具。
4.7.8.1 普通浇注系统凝料的脱出机构通常采用侧浇口、直接浇口及盘环形浇口类型的模具,其浇注系统凝料一般与塑件连在一起。
塑件脱出时,先用拉料杆拉住冷料穴,使浇注系统留在动模一侧,然后用推杆或拉料杆推出,靠其自重而脱落。
4.7.8.2 点浇口式浇注系统凝料的脱出机构(1)利用推杆拉断点浇口凝料:如图4-79所示,开模时模具首先沿A-A面分开,流道凝料被带出定模座板8,当限位钉1对推板2限位后,推杆4及推杆5共同将浇注系统凝料推出。
(2)利用侧凹拉断点浇口凝料:分流道末端钻一小斜孔,开模时确保模具先由A-A面分开,点浇口被拉断,流道凝料被中心拉料杆9蜡像型腔板一侧,当限位钉6其作用后,动模与定模型腔板5分开即B-B 分型,中心拉料杆随之失去作用,流道凝料便自动脱落,如图4-80所示。
图4-79 利用推杆拉断点浇口图4-80 利用推杆拉断点浇口图4-81为侧凹拉断点浇口的另一种形式,分流道末端做成斜面,开模时,由于弹簧6的作用,模具首先从A-A面分型,点浇口被拉断,同时拉料杆相对于型芯固定板1移动l距离,继续开模时,型芯固定板1碰到拉料杆2的台阶,拉料杆2则将主流道凝料脱出,随后型腔板(中间板)3将流道凝料从拉料杆2上推出并自动脱落。
图4-81 利用侧凹拉断点浇口的另一种形式(3)利用拉料杆拉断点浇口凝料:如图4-82所示,图4-82(a)为闭模状态,图4-82(b)为开模状态。
塑料模具成型第七章 脱模机构

2、制件不变形损坏3、良好制件的外观1、顶杆固定在顶出板固定板和顶出板,螺钉连接,注射机的顶出力作用在顶出板上。
2、导柱、导套为顶出平稳,顶出零件不致于弯区、卡死,长设顶出系统的导柱、导套。
3、回程杆为完成顶出板的回程,靠回程杆实现。
四、脱模机构结构组成4、勾料杆(拉料杆)5、挡销并不是所有的模具都必须由这些零件,主要由结构决定,有的还有挡销。
2个作用:(1)使顶出板与底板之间有间隙,以便清除废料及杂物(多用于压制模);(2)由调节挡销厚度来控制顶板的位置和顶出距离。
第二节简单脱模机构凡在动模一边施加一次顶出力,就可实现制件的脱模。
形式:推杆、顶管、推板、多元件综合脱模机构、气压脱模机构、活动镶件或型腔脱模机构。
一、顶杆脱模机构1、特点:(1)广泛应用,加工简单,易更换,效果好;(2)易引起应力集中,面积小,顶穿或变形)2、组成(1)推出部件:推杆、推杆固定板、推板;(2)导向部分:导柱、导套;平稳、不弯曲、不卡死(3)复位部件:复位杆、弹簧;(4)固定零件:螺钉、挡销。
设计要点:(1)应该设在脱模阻力大的地方;(2)应该足够的强度和刚度承受推出力;弯曲或折断直径=2.5-12mm 当直径﹤3mm 时,要做阶梯形(3)断面和型腔应同一平面或高出0.05-0.10mm (4)带侧抽芯的模具,要开设侧抽芯(5)有冷却水道的模具,避免推杆穿过冷却水道,防止漏水(6)对格子板状塑件,断面为矩形推杆(7)对于薄壁壳体塑件,用断面为D 形推杆(8)在模内排气困难处,设推杆(9)阻力大的部位,多设推杆(10)顶杆材料选用45#钢,顶头应该淬火处理(11)顶杆特殊形式A 型:用途广泛,最简单;D-d=4-6mm B型:阶梯型,用于顶杆直径小的情况;d 1=2d 提高强度C型:阶梯插入式,顶杆较细,与塑料接触的滑动部分,选用优质钢。
d 插入d 1,过渡配合M=(4-6)d E型:特殊断面插入式顶杆,为防止拔出,在顶杆两端铆接使之固定。
脱模机构设计优秀课件

1
按刚度计算:
H
k1FR 2
E
3
1
按强度计算:H
k2F
3
2)矩形或异环形截面塑件:
1
按刚度计算:H
0.54L
F
EB
3
4. 推块脱模
推管的一种特殊形式,用于推出非圆形的大面积塑件。 例如一些齿轮或带有凸缘的零件,用推杆容易变形,用脱 模板容易粘附在脱模板上,可以使用推块脱模
脱模机构设计
一、脱模机构的分类及设计原则
1.脱模机构的分类 按推出动作的动力源分类
手动脱模 机动脱模 液压与气动脱模
按推出动作特点分类
一次脱模 二次脱模 双脱模 顺序脱模 浇注系统凝料脱模 带螺纹塑件脱模
2. 脱模机构的设计原则
① 塑件滞留于动模。 ② 保证塑件不因推出而变形损坏:设计时应仔细分析塑件对
d
4F
n
注:推杆直径不宜过细,应有足够的强度、刚度承 受推出力。通常推杆直径取2.5~12㎜,对直径小于2 ㎜的细长推杆应作成下部加粗的阶梯形。
2)推杆的数量
在首先保证推出稳定、可靠的情况下,应尽可能地降低推 杆数。
3)推杆布置的一般原则
① 推杆必须布置在需要排气的区域,这些区域不依靠分型面 排气。
推管在轴向上开有连接槽或连接孔,可将销连接在推管上,大大缩短型 芯的长度,模具高度减小,结构更加紧凑,但因紧固力小,只适用于小尺 寸型芯。
推管的形式
推管的形状有直通式(I型)和阶梯形(II型),前者适 用于短推管,后者可增大推管的刚度,适用于长推管,为便 于制造,推管壁厚一般不小于1.5mm.
3.脱模板脱模机构
1)推杆的固定形式
a.常用形式 b.采用垫块或垫圈代
脱模机构

7 顶出的辅助机构
a. 导向机构 b. 回程机构
a导向机构
保证顶出连接板正常移动
b回程机构
确保顶出连接板准确回到顶出之前的位 置。
回程杆复位
顶杆弹簧复位机构
三、定模脱模机构
制品留在定模,需要在定模位置设置脱 模结构。
定模顶板脱模机构
1 支架 2 动模垫板 3 成型镶片 4 动模 5 定距拉钉 6 推板 7 定模板 8 定模底板 9 主流道 10 导柱
型芯与顶板的配合
b设计注意事项
多型腔的情况下,一般要在推板和 型腔相接触的部位,安装套筒,用 以防止偏心。 当推板后退至最后时,顶出板和安 装板之间应留有2-3mm的间隙,以利 于对模具的保护。 当以细长型芯成型通孔时,为了防 止其偏心及倾倒,要在型腔中设支 承。‘
c顶板顶出形式
有各种顶出形式
7 推板 8 主型芯
七、浇注系统的去除
对于自动化生产,浇注系统的去除,需 要特殊的装置,尤其是潜伏式浇口和点 浇口模具设计。
潜伏式浇口的脱除
顶板和顶杆分别切断潜伏式浇口
1 定模板 2 导柱
3 顶板
4 动模板 5 支架 6 中心顶杆 7 顶杆
利用斜面拉断点浇口
1 拉料杆
2 主型芯
3 定模 4 定模底板
二、简单脱模机构
1. 2. 3. 4. 5. 6. 7. 顶杆脱模机构 顶管脱模机构 顶板脱模机构 活动镶件或凹模推出的脱模机构 气压脱模机构 联合脱模机构 顶出的辅助机构
1 顶杆脱模机构
a. 顶杆顶出机构的工作原理 b. 设计注意事项 c. 顶杆与顶出板连接形式
b设计注意事项
1. 2. 3. 4. 5. 6. 7.
4.7脱模机构

推件板和型芯的配合
留有0.2~025mm的间隙 配合长度
配合锥度20°
二次脱模机构
作用:由于塑件的特殊形状或生产自动化的需要;为避 免一次脱模塑件受力过大。
摆杆拉钩二级脱模机构
三角滑块式双推板二次脱模机构
螺纹的脱模
强制脱出:弹性较好或较柔软的塑件,用于精 度不高和小批量生产的塑件 模外脱出:活动螺纹镶块
3)直径和数量
保证足够的刚度。可设计成阶梯形
数量应保证顺利脱模且不损伤塑件表观
4)推杆固定形式
推杆
推杆
推杆
推杆
推杆
推杆
(a)
(b)
(c)
(d)
(e)
(f)
图4-79 推杆的固定形式
2、复位机构 复位杆:2~4根 弹簧复位:先复位
3、导向机构 导柱、垫块、复位杆
二)推管脱模机构
又称为空心推杆,主要用于圆筒形塑件的脱模
对于盖、壳类塑件,因侧面脱模阻力较大,应在底面和侧面周边同时布 置脱模机构。
图4-77 盖类塑件的顶出位置
图4-78 加强筋部增设推杆结构
2)配合和装配
推杆和推杆孔配合取H8/f8间隙配合,配合段长度取推杆直径的2~3倍, 不小于10mm。非工作段与孔有0.5 ~1mm的间隙,以减少磨擦。 推杆端面应和型腔在同一平面或比型腔的平面高出0.05~0.1mm。一般 不允许推杆端面低于塑件表面。
顶出位置应设在塑件内部
4)结构可靠
工作可靠、运动灵活、制造方便、配换容易。
二、简单脱模机构
通过一次推出动作将塑件脱卸出模具的机构称为一次推出脱模机构, 或称为简单脱模机构。最常见的结构形式,包括推杆机构、推板机构、 推管机构等
脱模机构设计讲解
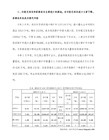
1、教学目的与要求
目的: 学习塑料注射模具脱模机构及设计要求。 要求: (1)掌握脱模机构的结构分类; (2)掌握脱模机构结构中的简单脱模机构设计; (3)熟悉脱模机构结构中的二次脱模机构及其 它结构的设计; (4)掌握相关的英文词汇。
制品包裹型芯的情况
顶杆(ejector pin )
(7)顶杆的强度计算 a 圆形顶杆 2 2 64 u L Q d 4 由欧拉公式: min 3 n E
设计时为保证可靠程度,d = 1.5 dmin。 u—考虑支撑条件的长度系数,u≈0.7; L—顶杆长度,cm; E—顶杆的抗拉弹性模量,N/ cm; n—顶杆件数; Q—脱模力,N;
Q一般情况下也可按下式计算: 对通孔型芯: Q = LHq(f· cos—sin) 对盲孔型芯: Q = LHq(f· cos—sin) + B 以上两式中: L—活动型芯中被塑件包紧的断面周长,cm; H—活动型芯成型部分的高度,cm; B—垂直于顶出方向的型芯投影面积,cm; q—包紧型芯的单位压力,一般取800~3400N/ cm; —塑料与钢的摩擦系数,一般取0.15~0.2。
2
二、脱模力的计算
如塑件孔为盲孔,上述计算式中还须加上塑件所 受的大气压力。
F = 10A
式中:F—克服真空增加的脱模阻力,N;
A—塑件盲孔的底面积, cm。
三、简单脱模机构 1、顶杆脱模机构
设计要点: (1)顶杆应设在塑件能承力较大或脱模阻力较大的 地方,尽量使顶出的塑件受力均匀,但不宜与型芯或 的镶件的距离过近,以免影响成型零件的强度; (2)顶杆直径必须有足够的强度,能承受顶出时 的冲击力。顶杆直径一般取2.5~12mm,对3 毫米以下的顶杆建议采用阶梯式结构,即顶杆下部 加粗以增加强度;
- 1、下载文档前请自行甄别文档内容的完整性,平台不提供额外的编辑、内容补充、找答案等附加服务。
- 2、"仅部分预览"的文档,不可在线预览部分如存在完整性等问题,可反馈申请退款(可完整预览的文档不适用该条件!)。
- 3、如文档侵犯您的权益,请联系客服反馈,我们会尽快为您处理(人工客服工作时间:9:00-18:30)。
脱模力一般公式:
其中:A—塑件包裹型芯的侧面积 p—塑件对型芯单位面积的包紧力,一般取8~12MPa μ—塑料对钢的摩擦系数,常取0.1 ~0.3,与塑料品种和型芯表 面粗糙度有关 α—脱模斜度
三. 简单脱模机构
通过一次推出动作将塑件脱卸出模具的机构称为一次推出脱模机构, 或称为简单脱模机构。最常见的结构形式,包括推杆机构、推板机构、 推管机构等。
对合螺纹型环成型时的脱出 齿轮齿条机动脱螺纹机构
2、按模具结构分
一次推出脱模(简单脱模)、二次推出脱模、动定模双向推出脱模、 顺序脱模、带螺纹塑件脱模等不同类型
对脱模机构的设计原则
1)塑件不变形损坏
机构推出中心与脱模力中心相重合,推出力分布均匀,作用点尽可 能靠近型芯防止塑件脱模后变形;推出力施于塑件刚性和强度最大的 地方(如凸缘、加强筋等)。
留有0.2~025mm的间隙 锥面 配合
推件板常用材料为45钢,热处理要求28~32HRC
四. 二次脱模机构
作用:由于塑件的特殊形状或生产自动化的需要;为避 免一次脱模塑件受力过大。
单推板 摆块拉板式二级脱模机构
双推板
三角滑块式双推板二次脱模机构
螺纹的脱模
强制脱出:弹性较好或较柔软的塑件,用于精 度不高和小批量生产的塑件 模外脱出:活动螺纹镶块
4.7 脱模机构设计
模具中推出塑件的机构称为脱模机构,或顶出机构 一. 脱模机构的组成与分类 二. 脱模力的计算 三. 简单脱模机构 四. 二次脱模机构
一. 脱模机构的组成与分类
组成
脱模机构一般由三部分组成:推出部件,导向部件,复位部件 推出部件:推杆、拉料杆、推杆固定板,推板等 导向部件:导柱、导套 复位部件:复位杆
2)良好的塑件外观
顶出位置应尽量设在塑件内部或对塑件外观影响不大的部位;与塑 件直接接触的脱模零件的配合间隙要保证不溢料,以避免在塑件上留 下飞边痕迹。
Hale Waihona Puke 3)运动准确、可靠、灵活,有足够的刚度和强度来克服脱模力。
4)考虑合模时推出机构的复位。
二.
脱模力的计算
当塑件从包紧的型芯上脱出所需要克服的阻 力称为脱模力,主要是塑件收缩引起的塑件 与型芯的摩擦阻力。 塑件刚开始脱模时,所需的脱模力最大, 称为初始脱模力;其后,脱模力的作用仅 仅为了克服脱模机构移动的摩擦力,称为 相继脱模力。 脱模力一般指初始脱模力。
推杆端面应和型腔在同一平面或比型腔的平面高出0.05~0.1mm。一般 不允许推杆端面低于塑件表面。
3)直径和数量
保证足够的刚度。可设计成阶梯形 数量应保证顺利脱模且不损伤塑件表观
4)推杆材料及热处理要求
材料常用T8A,T10A或65Mn,碳素工具钢热处理要求硬度HRC50~54, 弹簧钢热处理硬度要求HRC50~54。
三)推件板机构
用于薄壁容器、壳体形塑件以及不允许在塑件表面留有顶出痕迹的塑件。
特点:
顶出均匀、力量大,运动平稳,塑件不易变形,表面无顶出痕迹,结构简 单,勿需设置复位装置;但对于内腔不规则的塑件,其配合部分加工困难 推件板和推杆的连接 推件板和型芯配合采取H7/f7或H8/f7的间隙配合
推件板和型芯的配合的改进
推杆脱模机构
1—推杆;2—推杆固定板;3—导套;4—导柱;5—推板; 6—拉料杆;7—复位杆;8—挡销;9—螺钉;10—塑件
脱模机构的分类
1、按动力来源分:
1)机动脱模:注射机上设置机械或者液压顶出装置,通过该 顶出装置推动模具脱模机构顶出塑件。 2)手动脱模:开模后人工操纵脱模机构,多用于定模(定模部分 注射机未设脱模装置) 3)气动脱模: 利用压缩空气将塑件吹出。
5)推杆固定形式
推杆
推杆
推杆
推杆
推杆
推杆
(a)
(b)
(c)
(d) 图4-79 推杆的固定形式
(e)
(f)
2、复位机构
复位杆:2~4根 弹簧复位:先复位
3、导向机构
导柱、垫块
二. 推管脱模机构
又称为空心推杆,主要用于圆筒形塑件的脱模
三种形式
1)长型芯:推管固定在推杆固定板上,主型芯固定在动模座板上。 2)中长型芯:推管用推杆推拉,型芯固定在动模支承板上。推管在 型芯板(动模板)内滑动。 3)短型芯:型芯采用方销或键固定在动模支承板上,推管固定在推 杆固定板上。推管在轴向开槽 。
推杆脱模机构 1、推出部分 1)顶出位置:
应设置在脱模阻力大的地方;设置在非主要表面、较厚的部位 对于盖、壳类塑件,因侧面脱模阻力较大,应在底面和侧面周边同时布 置脱模机构。
图4-77 盖类塑件的顶出位置
图4-78 加强筋部增设推杆结构
2)配合和装配
推杆和推杆孔配合取H8/f8间隙配合,配合段长度取推杆直径的2~3倍, 不小于10mm。非工作段与孔有0.5 ~1mm的间隙,以减少磨擦。