塑件脱模机构设计PPT演示课件
合集下载
第10讲 脱模机构设计
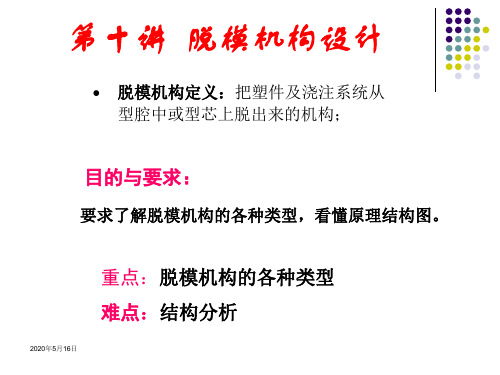
二级推出机构产生的原因
由于特殊形状或自动化生产的需要, 在一次脱模动作完成后,仍难于从 型腔中取出或不能自动脱落。
有时为避免一次脱模塑件受力过大,也采用二次脱模推出, 以保证塑件质量。
2013年7月14日
1.弹簧式二级推出机构
这种方法结构简单,装 配后所占面积小,缺点 是动作不可靠,弹簧容 易失效,需要及时更换。
2013年7月14日
2.斜楔滑块式二次推出机构
8-14斜楔滑块式二次推出机构 1- 动模座板 2-推板 3-弹簧 4-滑块 5-销钉 6-斜楔; 7-推件板 8-推杆 9-型芯 10-中心推杆 11-复位杆
2013年7月14日
3.三角滑块式二级推出机构
图8-15 三角滑块式二次推出机构 1- 一次推板 2- 三角滑块 3- 二次推板 4-推杆固定板 5-斜楔杆 6-推杆 7-动模型腔板 8-型芯 9-推杆
2013年7月14日
1.推杆推出机构
(1)推出机构组成: 推杆、拉料杆、复位杆、推杆固定板、推杆垫板、
推杆导柱、推杆导套、限位钉。
2013年7月14日
(2)推杆的设计
• • 适用范围:脱模阻力小的简单塑件 特点:简单、灵活,但与塑件接触面积小,易将 塑件顶变形或损坏。
推杆的形状及尺寸 推杆的固定及装配 推杆推出位置的选择
(四)螺纹塑件推出机构
手动脱螺纹机构
模内手动脱螺纹机构 齿轮齿条脱螺纹机构 直角式注射机脱螺纹机构 推杆轴承旋转式脱出机构
2013年7月14日
1.手动脱螺纹机构
2013年7月14日
手动脱螺纹机构
2013年7月14日
手动脱螺ቤተ መጻሕፍቲ ባይዱ机构
2013年7月14日
2.模内手动脱螺纹机构
塑料模具课件-脱摸机构图
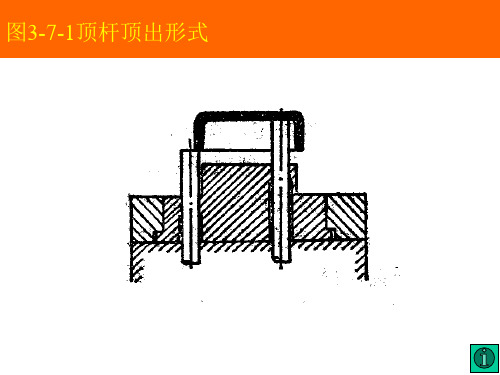
图3-7-55大升角螺杆结构
图3-7-56气(液)动形式
图3-7-57电动机驱动形式
脱摸力计算图
脱摸力计算图
脱摸力计算图
脱摸力计算图
导柱的安装
导柱
导柱的安装
导柱的安装固定形式
导套
盲孔导套的侧壁开孔
导套与孔的固定
直导套的固定
导柱与导套的配合形式
导柱的布置形式
锥面定位
1-圆柱销 2-弹簧 3-摆杆 4-U形限制架 5-注射机顶杆 6-转动
图3-7-23 U形限制架式
图3-7-23 U形限制架式
图3-7-24滑块式二次脱模机构
1-型芯 2-顶出干 3-推板 4-顶杆 5-斜导柱 6-滑块
图3-7-24滑块式二次脱模机构
图3-7-24滑块式二次脱模机构
3-7-25滑块式二次脱模机构
锥面定位
顶杆的形状
顶管顶出机构
1 顶出板 2 顶管 3方销 4 型芯 5 塑件
顶管顶出机构
顶管顶出机构
推板脱模机构
推板脱模机构
带周边间隙的脱模板
进气装置
1 推板 2 顶杆 3弹簧
利用活动镶件脱出塑件
利用型腔的脱模结构
多元件综合脱模机构
讨论题目
请画出这两种顶杆的固定方式
讨论L和H的公差,并说明原因
图3-7-11双脱摸机构
1、型芯 2、型腔
图3-7-12气动双脱模机构
1、4-密封圈 2、3-空气阀门
图3-7-13弹簧顺序脱模机构
图3-7-14拉钩顺序脱模机构
1、压块 2-挡块 3-拉钩 4-拉板 5-弹簧 6-滚轮 7-定模
图3-7-15拉钩顺序脱模机构
1-定模板 2-定模型腔 3-动模板 4-凸块 5-转轴 6-拉钩 7圆销 8- 定伸弹簧 9-定距拉板
第10讲 脱模机构设计 PPT

第10讲 脱模机构设计
10.1 脱模机构概述 10.2 脱模力的计算 10.3 推出零件尺寸的确定 10.4 简单脱模机构 10.5 定模脱模机构 10.6 双脱模机构 10.7 顺序脱模机构 10.8 二次脱模机构 10.9 转动脱模机构 10.10 流道凝料的脱模机构
10.1 脱模机构概述
10.1.1 脱模机构的组成
10.2.1 影响脱模力的因素
F摩 ( F正F脱 si ) n
Fk 0 F摩 c o s F 脱 F正 s i n 0
F脱F正 1(ccooss ssii nn)
F 脱 F 正 ( c o s s i ) A n ( c p o s s i )
10.2.1 影响脱模力的因素
F 脱 F 正 ( c o s s i ) A n ( c p o s s i )
a. 推杆应设置在制品的内侧。 b. 如果必须设在其外表面时,可在推杆工作 端面加工一些装饰性标志。
大的地方。
推杆的位置 1-推杆(兼复位杆)2-塑件 3-推杆 4-型芯 5-盘形推杆
10.4.1 常见脱模机构的类型
1.推杆脱模机构
2)应设在塑件强度刚度 较大处。
推杆不宜设在塑件的薄壁
处,应尽可能设在塑件厚壁、
凸缘处及筋与筋或壁与筋的交点上,以免使塑件变形损坏。来自如必须设在薄壁处时,应
增大推杆截面积,以降低单位
10.1.3 推出机构的设计原则
2)塑件应滞留于动模。以便利用注射机推杆驱 动动模一侧的推出机构完成脱模动作。
3)保证良好的塑件外观。塑件的推出位置应尽 量设在塑件内部或对外观影响不大的部位。
4)脱模机构应动作灵活可靠、制造维修更换方 便。
对于生产批量不大的制品,应尽量选择简单的 脱模机构,以降低模具的制造成本。
10.1 脱模机构概述 10.2 脱模力的计算 10.3 推出零件尺寸的确定 10.4 简单脱模机构 10.5 定模脱模机构 10.6 双脱模机构 10.7 顺序脱模机构 10.8 二次脱模机构 10.9 转动脱模机构 10.10 流道凝料的脱模机构
10.1 脱模机构概述
10.1.1 脱模机构的组成
10.2.1 影响脱模力的因素
F摩 ( F正F脱 si ) n
Fk 0 F摩 c o s F 脱 F正 s i n 0
F脱F正 1(ccooss ssii nn)
F 脱 F 正 ( c o s s i ) A n ( c p o s s i )
10.2.1 影响脱模力的因素
F 脱 F 正 ( c o s s i ) A n ( c p o s s i )
a. 推杆应设置在制品的内侧。 b. 如果必须设在其外表面时,可在推杆工作 端面加工一些装饰性标志。
大的地方。
推杆的位置 1-推杆(兼复位杆)2-塑件 3-推杆 4-型芯 5-盘形推杆
10.4.1 常见脱模机构的类型
1.推杆脱模机构
2)应设在塑件强度刚度 较大处。
推杆不宜设在塑件的薄壁
处,应尽可能设在塑件厚壁、
凸缘处及筋与筋或壁与筋的交点上,以免使塑件变形损坏。来自如必须设在薄壁处时,应
增大推杆截面积,以降低单位
10.1.3 推出机构的设计原则
2)塑件应滞留于动模。以便利用注射机推杆驱 动动模一侧的推出机构完成脱模动作。
3)保证良好的塑件外观。塑件的推出位置应尽 量设在塑件内部或对外观影响不大的部位。
4)脱模机构应动作灵活可靠、制造维修更换方 便。
对于生产批量不大的制品,应尽量选择简单的 脱模机构,以降低模具的制造成本。
塑料模具课件_脱模机构
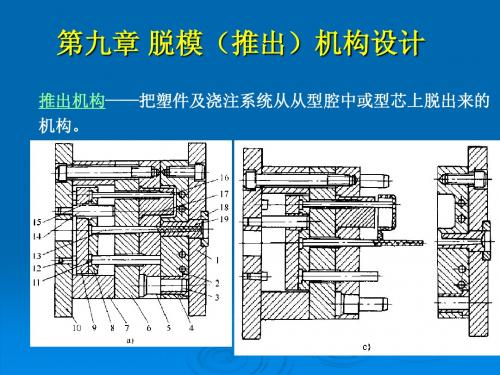
3.模内旋转的脱模方式
(1)螺纹塑件的止转形式
模具设自动脱螺纹机构时塑件外形有止转结构,通常为花纹。
常用模内旋转脱螺纹机构主要有手动脱螺纹和机动脱螺 纹两种。
(2) 手动脱螺纹机构
(3) 机动脱螺纹机构
原理:利用开模时的直线运动,通过齿轮齿条的运动,使 螺纹型芯作回转运动而脱离塑件。 图为,锥齿轮脱螺纹型 芯结构,它用于侧浇口多 型腔模,螺纹型芯只要作 回转运动就可脱出塑件。
p—因塑件收缩对型芯产生的单位正压力(12~20MPa) A—塑件包紧型芯的侧面积(mm2)
F脱= pA(f·cosα-sinα)
总脱模力等于F总=F脱+F大气(大气压力影响:引气、不引气) 以上对脱模力的计算是一种比较粗略的方法。 计算脱模力是为了校核设备的顶出力是否足够,以及校核推出 元件的刚度强度及可靠性。
为减少脱模过程中推件板与型芯之间的摩擦,两者之间留有0.2~ 0.25mm的间隙,并采用锥面配合,以防止推件板 偏斜溢料,锥面 的斜度约取3~5˚左右,图 (b)。
引气装置: 对于大型深腔薄壁容器,推板脱模时 塑件部易形成真空, 使脱模困难,甚至还会使塑件变形或损坏,应在凸模上附设引 气装置,如图(推件板引气)。(推件板不引气)
加粗,增加刚性。
顶盘式推杆:锥面推杆,推出面积较大,适合于深筒形塑件 推出。
b)
c)
d)
2.推杆的固定及配合
(1)推杆的固定
2.推杆的配合
推杆固定板上的孔为d+1mm;推杆台阶部分的直径为
d+5mm;推杆固定板上的台阶孔为d+6mm。推杆与固定 板配合长度为S(一般采用H8/f8配合)
S 可取12~15mm;当d>5mm时, S=(2~3)d (d为推杆直径),配合部分表面Ra=0.8μm。 推杆与塑料接触并与孔经常摩擦,因此多采用热处理后硬度 高的材料制作。推杆材料常用T8A、T10A等碳素工具钢 (50 ~ 54HRC自制推杆)或65Mn (46 ~ 50HRC市场上的 推杆标准件)
第10讲-脱模机构设计-PPT
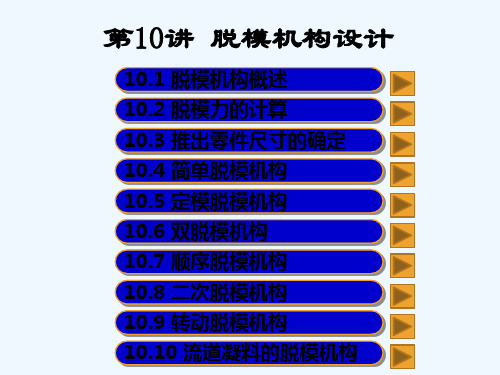
大的地方。
推杆的位置 1-推杆(兼复位杆)2-塑件 3-推杆 4-型芯 5-盘形推杆
10.4.1 常见脱模机构的类型
1.推杆脱模机构
2)应设在塑件强度刚度 较大处。
推杆不宜设在塑件的薄壁
处,应尽可能设在塑件厚壁、
凸缘处及筋与筋或壁与筋的交
点上,以免使塑件变形损坏。
如必须设在薄壁处时,应
增大推杆截面积,以降低单位
大家有疑问的,可以询问和交流
可以互相讨论下,但要小声点
10.2 脱模力的计算
概念
(1)定义:指将塑件从型芯上脱出时所需克服的阻力。 包括:
成型收缩的包紧力; 不带通孔的壳体类塑件的大气压力; 机构运动的摩擦力; 塑件对模具的粘附力;
10.2.1 影响脱模力的因素
(2)影响脱模力的因素
型芯成型部分的表面积及其形状. 收缩率及摩擦系数. 塑件壁厚和包紧型芯的数量. 型芯表面粗糙度. 成型工艺:P注、t冷.
对于生产批量很大的制品,为提高生产率,可 采用结构比较复杂、自动化程度比较高的脱模机构。
10.1.3 推出机构的设计原则
5)推出零件应有足够的强度、刚度和硬度。 6)合模时应正确复位。并保证不与其他模具零 件相干涉。 7)脱模行程应恰当。应保证推出零件运动的初 始位置和终止位置恰当合理,以保证制品可靠脱模。
由上面的式子可以看影响因素脱模力的大小主要有以下几点:
(l)主要与塑件包络型芯侧面积的大小有关。型芯的侧面积越大,所需的脱 模力也越大。 (2)与型芯的脱模斜度有关。脱模斜度越大,所需的脱模力越小。 (3)与型芯的表面粗糙度有关。表面粗糙度值越低,型芯表面越光洁,所需 的脱模力就越小。 (4)与塑件的结构有关。塑件厚度越大、形状越复杂,冷却凝固时所引起的 包紧力和收缩应力越大,则所需的脱模力越大。 (5)与注射工艺有关。 注射压力越大,则包紧型芯的力越大,所需脱模力越大; 脱模时模具温度越高,所需的脱模力越小; 塑件在模内停留时间越长,所需的脱模力越大。 (6)与成型塑件的塑料品种有关。不同的塑料品种,由于分子的结构不一样, 因而它们的脱模力也不一样。
推杆的位置 1-推杆(兼复位杆)2-塑件 3-推杆 4-型芯 5-盘形推杆
10.4.1 常见脱模机构的类型
1.推杆脱模机构
2)应设在塑件强度刚度 较大处。
推杆不宜设在塑件的薄壁
处,应尽可能设在塑件厚壁、
凸缘处及筋与筋或壁与筋的交
点上,以免使塑件变形损坏。
如必须设在薄壁处时,应
增大推杆截面积,以降低单位
大家有疑问的,可以询问和交流
可以互相讨论下,但要小声点
10.2 脱模力的计算
概念
(1)定义:指将塑件从型芯上脱出时所需克服的阻力。 包括:
成型收缩的包紧力; 不带通孔的壳体类塑件的大气压力; 机构运动的摩擦力; 塑件对模具的粘附力;
10.2.1 影响脱模力的因素
(2)影响脱模力的因素
型芯成型部分的表面积及其形状. 收缩率及摩擦系数. 塑件壁厚和包紧型芯的数量. 型芯表面粗糙度. 成型工艺:P注、t冷.
对于生产批量很大的制品,为提高生产率,可 采用结构比较复杂、自动化程度比较高的脱模机构。
10.1.3 推出机构的设计原则
5)推出零件应有足够的强度、刚度和硬度。 6)合模时应正确复位。并保证不与其他模具零 件相干涉。 7)脱模行程应恰当。应保证推出零件运动的初 始位置和终止位置恰当合理,以保证制品可靠脱模。
由上面的式子可以看影响因素脱模力的大小主要有以下几点:
(l)主要与塑件包络型芯侧面积的大小有关。型芯的侧面积越大,所需的脱 模力也越大。 (2)与型芯的脱模斜度有关。脱模斜度越大,所需的脱模力越小。 (3)与型芯的表面粗糙度有关。表面粗糙度值越低,型芯表面越光洁,所需 的脱模力就越小。 (4)与塑件的结构有关。塑件厚度越大、形状越复杂,冷却凝固时所引起的 包紧力和收缩应力越大,则所需的脱模力越大。 (5)与注射工艺有关。 注射压力越大,则包紧型芯的力越大,所需脱模力越大; 脱模时模具温度越高,所需的脱模力越小; 塑件在模内停留时间越长,所需的脱模力越大。 (6)与成型塑件的塑料品种有关。不同的塑料品种,由于分子的结构不一样, 因而它们的脱模力也不一样。
塑胶件的脱模机构

P cos(f tg)
Q1
P=c·h ·q
1 f sin cos
Q1 P
上式中 α——设计斜度 f——可查表 已知条件
经验公式 P=c·h·q 式中 c——型芯成型部分断面形状的周长
h——型芯成型部分的高度 q—— 塑料的收缩流利(一般取80~120kg/m2)
正压力P的理论计算公式
薄壁件: P 2Etl 1
点浇口自动切断机构
顶管和推板联合推出机构
二.脱模力的计算
对型芯进行受力分析
包紧力P——塑件冷却收缩将型芯或凸模包紧
脱模力Q1——初始脱模力
摩擦力F——塑料与钢材之间的粘附力 F f (P Q1sin )(1)
(1)代入(2)
∑Fx=0
F cos Q1 Psin (2)
f (P Q1 sin ) cos Q P sin
(3) 推板的几种种固定方式
套在型芯上 与顶杆用过盈配合固定在一起、顶杆头部带螺纹 限制推板的脱落
4. 脱模系统的辅助零件
(1) 导向零件:导套、导柱 (2) 回程装置
回程杆回程 顶杆(顶管)兼回程杆回程 弹簧复位
弹簧复位
杠杆复位
摆杆复位
连杆复位
1
气动抽芯、液压抽芯
5.其他一些脱模机构
(2)设计顶杆脱模机构应注意的几点 顶杆直径:一般在2.5~12 顶杆位置 顶杆装配位置: 顶杆与模具装配间隙 材料 顶杆形状
①顶杆直径:一般在2.5~12mm
注意刚度和强度 直径不应过细,应有足够的刚度承受顶出力 当直径在3以下时可设计成阶梯形等形状
②顶杆位置
设置在脱模阻力大的地方 如图
局部有细而深的凸台或筋,应在其底部加设顶杆 如图
注塑模推出机构详解 PPT课件
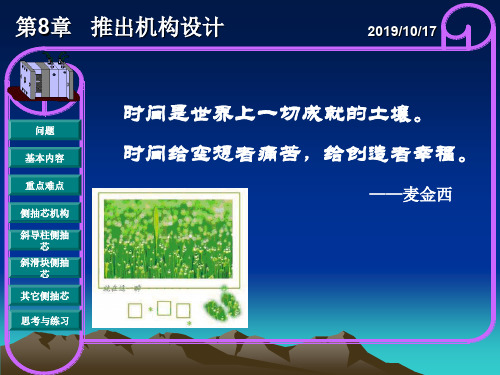
其它侧抽芯
思考与练习
L l1 l2 l4 l5 D tan ha S抽 (5 ~ 10)mm
2
cos sin
第8章 推出机构设计
2019/10/17
§9.2 机动侧向分型与抽芯机构
一、斜导柱侧向分型与抽芯机构
问题 基本内容 重点难点
1. 斜导柱设计 (4) 斜导柱直径计算
2019/10/17
§9.2 机动侧向分型与抽芯机构
一、斜导柱侧向分型与抽芯机构 斜导柱侧抽芯机构的工作过程与各零件功能
问题
基本内容
重点难点
侧抽芯机构
斜导柱侧抽 芯
斜滑块侧抽 芯
其它侧抽芯
思考与练习
第8章 推出机构设计
§9.2 机动侧向分型与抽芯机构
一、斜导柱侧向分型与抽芯机构
问题 基本内容
1. 斜导柱设计 (1) 斜导柱的形状及技术要求
芯 斜滑块侧抽
芯 其它侧抽芯
思考与练习
抽拔力:与脱模力相同 抽芯距(S抽):S抽= h+(2~3)mm
特殊情况 圆形线圈骨架的抽芯距 S抽= S1+(2~3)mm
R2 r2 (2 ~ 3)mm
S1:抽芯极限尺寸 R:塑件大圆盘半径 r:塑件腰部外圆半径
第8章 推出机构设计
2019/10/17
b)斜导柱固定在动模、侧滑块安装在定模 斜导柱在动模 -1.swf
斜导柱在动模侧 型芯滑块在定模 的结构.swf
斜导柱在动模 -2.swf
第8章 推出机构设计
2019/10/17
§9.2 机动侧向分型与抽芯机构
一、斜导柱侧向分型与抽芯机构
问题 基本内容
6.斜导柱侧向分型与抽芯机构的应用形式 c)斜导柱与侧滑块同时安装在动模
思考与练习
L l1 l2 l4 l5 D tan ha S抽 (5 ~ 10)mm
2
cos sin
第8章 推出机构设计
2019/10/17
§9.2 机动侧向分型与抽芯机构
一、斜导柱侧向分型与抽芯机构
问题 基本内容 重点难点
1. 斜导柱设计 (4) 斜导柱直径计算
2019/10/17
§9.2 机动侧向分型与抽芯机构
一、斜导柱侧向分型与抽芯机构 斜导柱侧抽芯机构的工作过程与各零件功能
问题
基本内容
重点难点
侧抽芯机构
斜导柱侧抽 芯
斜滑块侧抽 芯
其它侧抽芯
思考与练习
第8章 推出机构设计
§9.2 机动侧向分型与抽芯机构
一、斜导柱侧向分型与抽芯机构
问题 基本内容
1. 斜导柱设计 (1) 斜导柱的形状及技术要求
芯 斜滑块侧抽
芯 其它侧抽芯
思考与练习
抽拔力:与脱模力相同 抽芯距(S抽):S抽= h+(2~3)mm
特殊情况 圆形线圈骨架的抽芯距 S抽= S1+(2~3)mm
R2 r2 (2 ~ 3)mm
S1:抽芯极限尺寸 R:塑件大圆盘半径 r:塑件腰部外圆半径
第8章 推出机构设计
2019/10/17
b)斜导柱固定在动模、侧滑块安装在定模 斜导柱在动模 -1.swf
斜导柱在动模侧 型芯滑块在定模 的结构.swf
斜导柱在动模 -2.swf
第8章 推出机构设计
2019/10/17
§9.2 机动侧向分型与抽芯机构
一、斜导柱侧向分型与抽芯机构
问题 基本内容
6.斜导柱侧向分型与抽芯机构的应用形式 c)斜导柱与侧滑块同时安装在动模
脱模机构解析PPT课件
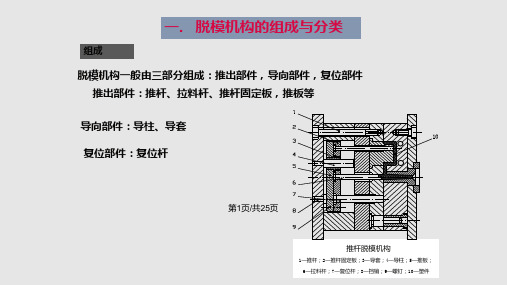
3)运动准确、可靠、灵活,有足够的刚度和强度来克服脱模力。
4)考虑合模时推出机构的复位。 第3页/共25页
二. 脱模力的计算
当塑件从包紧的型芯上脱出所需要克服的阻 力称为脱模力,主要是塑件收缩引起的塑件 与型芯的摩擦阻力。 塑件刚开始脱模时,所需的脱模力最大, 称为初始脱模力;其后,脱模力的作用仅 仅为了克服脱模机构移动的摩擦力,称为 相继脱模力。 脱模力一般指初始脱模力。
双推板
三角滑块式双推板二次脱模机构
第15页/共25页
螺纹的脱模
强制脱出:弹性较好或较柔软的塑件,用于精度不高和小批 量生产的塑件
模外脱出:活动螺纹镶块
第16页/共25页
对合螺纹型环成型时的脱出 齿轮齿条机动脱螺纹机构
第17页/共25页
第18页/共25页
第19页/共25页
第20页/共25页
3)直径和数量
保证足够的刚度。可设计成阶梯形 数量应保证顺利脱模且不损伤塑件表观
第6页/共25页
4)推杆材料及热处理要求
材料常用T8A,T10A或65Mn,碳素工具钢热处理要求硬度HRC50~54, 弹簧钢热处理硬度要求HRC50~54。
5)推杆固定形式
推杆
推杆
推杆
推杆
推杆
推杆
(a)
(b)
第7页/共25页
脱模机构的分类
1、按动力来源分:
1)机动脱模:注射机上设置机械或者液压顶出装置,通过该顶 出装置推动模具脱模机构顶出塑件。
2)手动脱模:开模后人工操纵脱模机构,多用于定模(定模部分 注射机未设脱模装置)
3)气动脱模: 利用压缩空气将塑件吹出。
2、按模具结构分
第2页/共25页
一次推出脱模(简单脱模)、二次推出脱模、动定模双向推出脱模、 顺序脱模、带螺纹塑件脱模等不同类型
4)考虑合模时推出机构的复位。 第3页/共25页
二. 脱模力的计算
当塑件从包紧的型芯上脱出所需要克服的阻 力称为脱模力,主要是塑件收缩引起的塑件 与型芯的摩擦阻力。 塑件刚开始脱模时,所需的脱模力最大, 称为初始脱模力;其后,脱模力的作用仅 仅为了克服脱模机构移动的摩擦力,称为 相继脱模力。 脱模力一般指初始脱模力。
双推板
三角滑块式双推板二次脱模机构
第15页/共25页
螺纹的脱模
强制脱出:弹性较好或较柔软的塑件,用于精度不高和小批 量生产的塑件
模外脱出:活动螺纹镶块
第16页/共25页
对合螺纹型环成型时的脱出 齿轮齿条机动脱螺纹机构
第17页/共25页
第18页/共25页
第19页/共25页
第20页/共25页
3)直径和数量
保证足够的刚度。可设计成阶梯形 数量应保证顺利脱模且不损伤塑件表观
第6页/共25页
4)推杆材料及热处理要求
材料常用T8A,T10A或65Mn,碳素工具钢热处理要求硬度HRC50~54, 弹簧钢热处理硬度要求HRC50~54。
5)推杆固定形式
推杆
推杆
推杆
推杆
推杆
推杆
(a)
(b)
第7页/共25页
脱模机构的分类
1、按动力来源分:
1)机动脱模:注射机上设置机械或者液压顶出装置,通过该顶 出装置推动模具脱模机构顶出塑件。
2)手动脱模:开模后人工操纵脱模机构,多用于定模(定模部分 注射机未设脱模装置)
3)气动脱模: 利用压缩空气将塑件吹出。
2、按模具结构分
第2页/共25页
一次推出脱模(简单脱模)、二次推出脱模、动定模双向推出脱模、 顺序脱模、带螺纹塑件脱模等不同类型
- 1、下载文档前请自行甄别文档内容的完整性,平台不提供额外的编辑、内容补充、找答案等附加服务。
- 2、"仅部分预览"的文档,不可在线预览部分如存在完整性等问题,可反馈申请退款(可完整预览的文档不适用该条件!)。
- 3、如文档侵犯您的权益,请联系客服反馈,我们会尽快为您处理(人工客服工作时间:9:00-18:30)。
拉料杆头部 应淬火到
HRC50以上.
29
利用凝料推板脱出针点浇口凝料
塑料成型模具
顶销3的作用是 确保首先从A面 分型,把浇注系 统凝料从流道 中脱出.
限位杆6、7决 定第一、二次 分型的距离。
凝料推板与定 模板间用锥面 配合。
30
利用凝料推板脱出针点浇口凝料
塑料成型模具
开模前,注射机喷咀先后退,浇口衬套在压缩弹簧的作 用下移动并与浇注系统凝料分离。再从A面分型,凝料从 主流道中脱出。分型距离由决定于限位杆。然后从B面分 型,拉断浇口。
22
塑料成型模具
浇注系统凝料的脱出
浇注系统凝料的脱出、自动坠落和与制品的自 动分离是整个生产过程实现自动化的环节之一. 浇注系统凝料与制品的自动分离能提高效率缩 短后加工时间,减少人的体力劳动。 内容:
设计合理的浇口形式,比如:潜伏式浇口、针点浇 口等。 设计合理的浇口自动脱落方式。
23
普通浇注系统凝料 脱出和自动坠落
塑件脱模 机构设计
1
双脱模机构
塑料成型模具
有时由于制品形状的特殊性使制件会 留于定模一边,或者留于动、定模的 可能性都存在,这就必须在定模设计 脱模机构,或在两个半模都设顶出机 构即双脱模机构。
定模顶出机构
2
双脱模机构
塑料成型模具
下图在动定模都设有气动脱模机构。在开模时, 先开启定模进气阀,制品随型芯脱出,关闭定 模电磁阀;开模终止时,动模电磁阀开启,制 件从型芯脱出。
开模时,压块1通过 压棒推动滑块切断 主浇道中的细丝。
35
塑料成型模具
带螺纹塑料制品 脱模机构
36
带螺纹制品的脱落模
非旋转脱出螺纹
强制脱模 GIF 动画
用于制品螺纹的精度要 求不高的场合,且螺纹 的断面最好为圆弧形。 利用塑料(PP、PE等) 的弹性强制脱螺纹 强制脱螺纹时最好先让 出型芯或型腔,故多采用 顺序分型。 避免把圆弧形端面作为 顶出面,否则脱模困难。
塑料成型模具
针点浇口的优点是在制品上留下的痕迹小,对制 品的外观影响不大。此类浇口的浇注系统凝料在 模具中要与制品分离,故要增加一个分型面(模 板)用于分离制品和浇注系统凝料,这类模具又 叫三板式模具。
浇注系统凝料可由人工取出,也可设置相应的机 构让凝料自动脱落,后者能提高自动化的程度。
26
人工取出针点浇口凝料
塑料成型模具 37
带螺纹制品的脱模
塑料成型模具
利用硅橡胶螺纹型芯强制脱螺纹
开模时,在弹簧的作用下,先让出硅橡胶中的型芯以便于 桂橡胶螺纹型芯的向内收缩。为顺利地强制脱螺纹作好准 备。
硅橡胶螺纹型芯寿命低,用于小批量生产。
38
带螺纹制品的脱模
利用分瓣式可涨缩型芯脱螺纹
缺点是螺纹的内表面有拼合线痕迹。 也可成型其它的塑料件侧凹。
3
双脱模机构
塑料成型模具
成型无脱模斜度的轴套制品,制品 可能留在定模,开模的同时弹簧的 作用使制品从型腔脱出,留在型芯 上;开模完成后,再利用动模的推 板脱出制件。用于制品对型腔粘附 力不大,脱模距离不长的模具。注 意弹簧易失效。
在开模时,利用杠杆和滚轮使 制品留在动模。开模完成后
用动模的推板脱出制品。
塑料成型模具
27
利用斜孔(面)拉断针点浇口
塑料成型模具
此种结构最好用倒锥头或球头拉料杆,且分流道最好开 在定模板上,如开在动模板上则要用较长的中心顶杆。
Flash 动画
28
利用拉料杆拉断针点浇口
塑料成型模具
模具先从A面分型,距离由限位杆6确定;再从B面分型,距离由 (限位杆7减去限位杆6的限位距离)决定.最后完成主分型,再 顶出制品.
31
利用拉料块拉断针点浇口
塑料成型模具32利用源自杆撬断针点浇口塑料成型模具
33
利用顶出杆拉断针点浇口凝料
塑料成型模具
用于特殊场合,深腔 制品。
定模设顶出机构。
因开模行程较大,故 注意校核开模行程。
双导柱有何作用?
34
附设机构—对易拉丝塑料
塑料成型模具
对易拉丝塑料(如:PS),如果不切断拉丝,则 不易实现自动化。故要设置切断装置。
塑料成型模具
GIF 动画
39
带螺纹制品的脱模
塑料成型模具
旋转式脱出螺纹 GIF 动画
手动脱螺纹(活动螺纹型芯与型环)
4
顺序脱模机构
塑料成型模具
一般用于有两个分型面的情况,且这两 个分型面的分型有一个先后顺序。也叫 定距分型拉紧机构。
Flash 动画
5
弹 簧 顺 序 脱 模 机 构
Flash 动画
顺序脱模机构
塑料成型模具 6
顺序脱模机构 拉钩顺序分型机构
塑料成型模具
7
顺序脱模机构 其它形式的拉钩顺序脱模机构
Flash 动画
11
二级脱模-气动式
塑料成型模具
12
二级脱模-弹簧式
塑料成型模具
Flash 动画
13
二级脱模-凸轮推杆式
塑料成型模具
用于第一级脱模距离较短的情况。注意凸轮的旋转角度 不能太大,以免合模发生自锁,使凸轮不能压回。
14
二级脱模-拉勾推杆式
塑料成型模具
Flash 动画
15
二级脱模-滑块式
塑料成型模具
Flash 动画
16
二级脱模-杠杆式
塑料成型模具
17
二级脱模-拉钩式
塑料成型模具
Flash 动画1
18
二级脱模-八字形摆杆式
塑料成型模具
19
二级脱模-U形限制架式
塑料成型模具
20
二级脱模-套筒球槽式
塑料成型模具
21
两级脱模推杆标准件
塑料成型模具
尺寸小巧, 加工精度高, 热处理符合 规范,使用 寿命长,已 经标准化。
塑料成型模具
指凝料与制品连在一起的一类浇注系统.一般在 顶出后靠自重脱落,有时需要另设机构。
连杆掸落机构:利用注射机的开模运动使浇 注系统凝料脱落.
24
普通浇注系统凝料 脱出和自动坠落
塑料成型模具
机械手:开模时利用由液压驱动的机械手将塑料制品 或浇注系统凝料从模具中带出模外.
空气顶出和吹落
25
针点浇口凝料 脱出和自动坠落
塑料成型模具
8
顺序脱模机构
塑料成型模具
导
柱
顺
特点
序
结构简单,拉紧
脱
力小,用于塑料
模
粘附力小的模具
机
构
9
顺序脱模机构
塑料成型模具
滚 轮 顺 序 脱 模 机 构
还能很好地控制合模顺序, 国外此种机构已商品化。
10
二级脱模机构
塑料成型模具
一般模具的脱模机构(单一或多种形式 组合)是一级脱模机构,即脱模动作是 一次完成。有时由于制品的特殊形状, 在一次脱模动作完成后,制件还不能从 模具中脱落;或在脱模阻力很大时,为 避免一次脱模使制品受力过大而使制品 变形或损坏的情况下可采用二级(次) 脱模机构。