关于感应淬火机床的结构与性能的介绍
感应淬火设备原理

感应淬火设备原理
感应淬火设备原理是利用感应电流通过工件表面和电磁感应涡流的产生,使得工件表
面产生无序磁化,从而达到材料表面淬火的一种方法。
该设备主要由感应装置、冷却装置、电源、控制系统等组成。
感应装置主要是由感应线圈和感应电源组成。
感应线圈是为产生交变磁场而设的。
通
过感应电源的交流电信号,驱动感应线圈发生交变磁场。
该磁场垂直于工件表面,从而通
过感应电流的作用,使工件表面局部加热,形成一定的淬火组织。
冷却装置主要是通过水或其他液体形成强制冷却,以达到快速淬火的效果。
冷却系统
通过管道和喷孔形成所需淬火区域,水流和工件的热交换作用导致工件的快速冷却,避免
因过度加热引起的变形、裂纹及其他问题出现。
电源是保证感应线圈正常运行的实体装置,其主要功能是加工操作和功率控制。
直流
电源通常被用来获得一个恒定的感应电流,而改变其施加时间则可以调整效应相关参数,
如表面深度、淬火组织等。
控制系统是将感应装置、冷却装置、电源等系统进行联动控制、交互控制的设备。
该
系统可根据需求完成多组工件、多条工况的淬火加工操作。
通常,控制系统具有灵活的参
数调整功能和预设程序,可适应不同的行业需求。
感应淬火设备原理
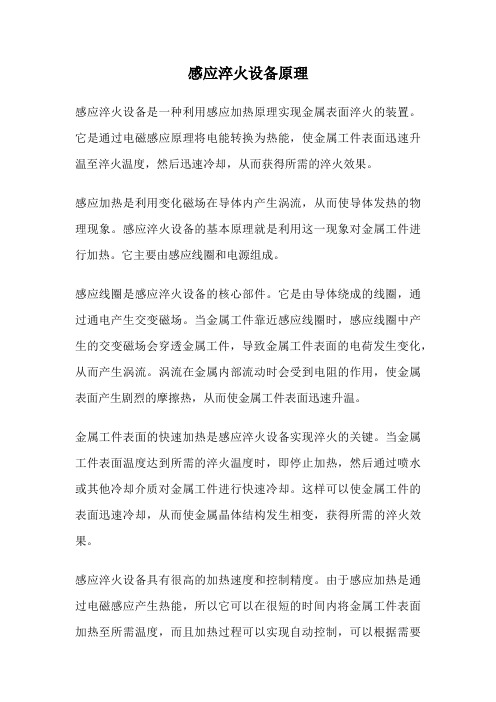
感应淬火设备原理感应淬火设备是一种利用感应加热原理实现金属表面淬火的装置。
它是通过电磁感应原理将电能转换为热能,使金属工件表面迅速升温至淬火温度,然后迅速冷却,从而获得所需的淬火效果。
感应加热是利用变化磁场在导体内产生涡流,从而使导体发热的物理现象。
感应淬火设备的基本原理就是利用这一现象对金属工件进行加热。
它主要由感应线圈和电源组成。
感应线圈是感应淬火设备的核心部件。
它是由导体绕成的线圈,通过通电产生交变磁场。
当金属工件靠近感应线圈时,感应线圈中产生的交变磁场会穿透金属工件,导致金属工件表面的电荷发生变化,从而产生涡流。
涡流在金属内部流动时会受到电阻的作用,使金属表面产生剧烈的摩擦热,从而使金属工件表面迅速升温。
金属工件表面的快速加热是感应淬火设备实现淬火的关键。
当金属工件表面温度达到所需的淬火温度时,即停止加热,然后通过喷水或其他冷却介质对金属工件进行快速冷却。
这样可以使金属工件的表面迅速冷却,从而使金属晶体结构发生相变,获得所需的淬火效果。
感应淬火设备具有很高的加热速度和控制精度。
由于感应加热是通过电磁感应产生热能,所以它可以在很短的时间内将金属工件表面加热至所需温度,而且加热过程可以实现自动控制,可以根据需要对加热时间和温度进行精确控制。
这使得感应淬火设备在工业生产中得到广泛应用。
感应淬火设备在金属加工行业有着重要的应用价值。
它可以提高金属零件的硬度和耐磨性,改善其力学性能和表面质量,延长使用寿命。
特别是对于大型和复杂形状的工件,感应淬火设备具有独特的优势,可以实现对工件表面的局部加热,避免了整体加热带来的变形和损坏。
感应淬火设备利用感应加热原理实现金属表面淬火,通过电磁感应产生的交变磁场使金属工件表面迅速加热至淬火温度,然后通过快速冷却获得所需的淬火效果。
它具有加热速度快、控制精度高等优点,在金属加工行业得到广泛应用。
表面淬火设备介绍

5)晶闸管中频电源装置在运行中,能根据负载变化自动调整频率 系统的输出功率一直保持在额定值
器结构示意图及说明。
表4-11 高频感应器结构
表4-11 中频感应器结构
三、感应器基本尺寸的确定
1.感应器与工件之间的间隙确定 表4-13为推荐采用的感应器与零件表面之间间隙的经验
数据。 2.感应器尺寸的确定
(1)感应器直径的确定 加热外圆表面时,感应器的内径 可由下式计算:
加热圆孔表面时,感应器的外径可由下 式计算:
3.前进法:火焰喷嘴和冷却装置沿淬火零件表面作平行移动,一边加 热,一边冷却,淬火零件可缓慢移动和不动。这种方法可以使很长 的工件进行表面淬火(如长轴、机床床身、导轨等),也适用于大模 数齿轮进行逐齿的淬火。
4.联合法:是指淬火零件绕其轴线作迅速旋转,而喷嘴及喷水装置同时沿 零件轴线平行移动。该法加热比较均匀,可作冷轧辊的表面淬火用。
二、感应器的分类及结构
1 分类 (1)加热方法 同时加热感应器和连续加热感应器
(2)零件加热部位形状 外表面加热感应器 内表面加热感应器 平面加热感应器 特殊形状加热感应器
(3)电源频率 高频 中频
2 结构
(1).制造感应器用纯铜厚度
纯铜厚度应稍大于感应电流冷态透入深度。
• 高频电流较小,不需要很高的机械强度,可用薄壁纯铜管绕制而 成,也可用薄铜片焊接而成。
如采用多匝时,则匝间距不超过零件与感应器之间的间隙, 以提高效率,一般匝间距为3~6mm。
数控淬火机床说明书【指南】

淬火机床一般指使用感应加热电源进行淬火工艺的特殊机床设备。
它具有精度高、可靠性好、省时省力等优点。
淬火机床的种类有很多,根据不同分类可立式的、卧式的淬火机床,数控淬火机床。
数控淬火机床具有手动操作及全自动操作功能,适用于单件及批量零件生产,广泛应用于拖拉机、汽车、工程机械、机床行业的感应热处理领域。
结构合理、功能齐全、安装调试方便。
一.机床操作说明1、性能特点立式数控淬火机床采用框架式焊接床身结构,双层精密工作台,上工作台移动,该机床上工作台移动采用滚珠丝杠传动,步进电机驱动,移动速度无级可调,零件旋转采用变频调速控制,速度无级可调。
零件夹持长度可电动调整,以适应淬火零件长度的变化,便于调整。
采用数控系统实现自动控制,可存储二十多种零件工艺程序。
该机床具有手动操作及全自动操作功能,适用于单件及批量零件生产,广泛应用于拖拉机、汽车、工程机械、机床行业的感应热处理领域。
结构合理、功能齐全、安装调试方便。
该机床具有连续淬火、同时淬火、分段连续淬火、分段同时淬火、等功能,主要用于半轴、传动轴、凸轮轴等各种轴类零件表面淬火,齿轮类、环类及平面类零件的感应淬火。
2、结构特点该机床主机由床身、双层精密工作台、上顶尖座调整滑动机构、上顶尖总成、工作台移动及传动系统、主轴旋转及传动系统、零件旋转与上顶尖调整机构,配种平衡,罩框、电气数控部分等组成。
1、床身部分:机床采用焊接床身结构,整体进行去应力退火。
主要外露件表面经特殊处理,具有良好的防锈抗蚀性能。
2、上顶尖调整机构:上顶尖调整采用电动调整,可实现不同长度工件的装夹。
3、工作台系统:采用步进电机通过变速机构驱动滚珠丝杠实现上工作台的升降运动,移动速度无级可调,传动轻快,导向精度高,定位准确。
4、主轴旋转系统:由异步电机通过变速机构和传动轴驱动主轴旋转。
采用变频调速实现零件转速无级调节。
5、罩框:罩框用厚钢板制成。
制作精良,外观美观,色泽大方。
罩框上部设有玻璃窗及推拉门,既可防止冷却水外溅,又便于装卸零件及监控淬火过程。
感应加热淬火机床性能特点__感应加热淬火机床应用
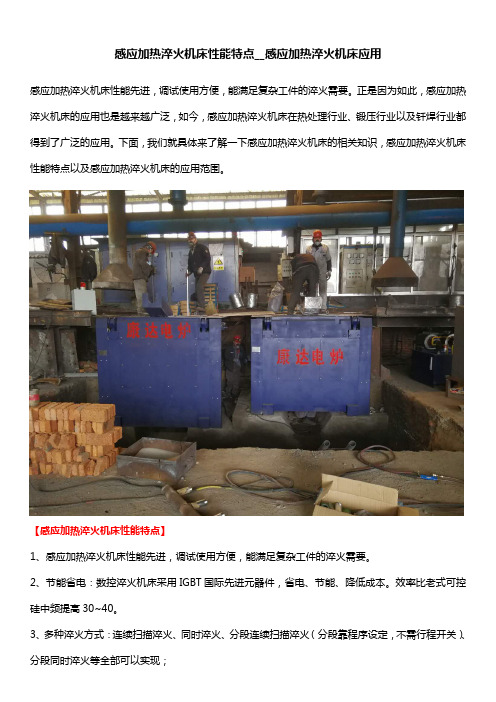
感应加热淬火机床性能特点__感应加热淬火机床应用感应加热淬火机床性能先进,调试使用方便,能满足复杂工件的淬火需要。
正是因为如此,感应加热淬火机床的应用也是越来越广泛,如今,感应加热淬火机床在热处理行业、锻压行业以及钎焊行业都得到了广泛的应用。
下面,我们就具体来了解一下感应加热淬火机床的相关知识,感应加热淬火机床性能特点以及感应加热淬火机床的应用范围。
【感应加热淬火机床性能特点】1、感应加热淬火机床性能先进,调试使用方便,能满足复杂工件的淬火需要。
2、节能省电:数控淬火机床采用IGBT国际先进元器件,省电、节能、降低成本。
效率比老式可控硅中频提高30~40。
3、多种淬火方式:连续扫描淬火、同时淬火、分段连续扫描淬火(分段靠程序设定,不需行程开关)、分段同时淬火等全部可以实现;4、适应性强:数控淬火机床为自行式,特别适用于较大较重较长的导轨:如龙门铣、龙门刨、大型车床等,同时也适用各种机床床面等机床附件的淬火处理。
能加热各种各样的工件。
5、数控淬火机床的床身校正一致,不需换头;6、环保:没有污染、噪声和粉尘;7、感应加热淬火机床保护措施齐全,故障率低,性能稳定,无后顾之忧;8、控制柜与变压器柜一体,组成整体设计的成套系统一齐行走,减少电源线和水管带来的托拽,使车间布置整洁有序。
而工件是固定不动的,安装方便,站台操作方便,移动灵活。
9、配置冷却系统:一体化淬火液循环冷却系统的冷却液为轿车冷却液,这样就解决了建水池时间长、不方便及冬天结冻等现象。
全封闭式循环冷却,避免杂物引起的管路堵塞;无水垢生成引起的电源,感应线圈等过热损坏。
10、三维的运动方向:机器可做包括:水平运动、垂直运动、上下运动等自行运动。
克服了在使用时要带动机床本身的运动,解决了客户做工装难、不方便、时间长等隐患。
11、高精度高质量率的淬火工艺:A.淬火精度高:量身设计制作的感应器与导轨面之间的间隙控制采用可调节的导轮定位,避免感应器与床面之间接触打火,间隙始终固定一致,温度及加热时间可得到控制,移动平稳,温度均匀;B.淬火质量高:无氧化层,变形小,淬硬层深度及硬度在2~4MM 左右,也可按照厂家工艺要求而定。
淬火感应器简介概述

淬火感应器简介概述淬火感应器是利用感应加热原理对淬火工件进行加热的终端设备。
根据加热频率的不同,分为中频淬火感应器,和高频淬火感应器。
一个标准的淬火感应器由以下几部分组成:1、接触板:也称汇流排,它的前端与淬火变压器的二次线圈联接,后端与有效圈焊在一起。
接触板共有对称的两块,使电流构成回路,两接触板之间有多用云母板制造的绝缘板。
2、冷却水盒:每块接触板各焊一只冷却水盒,以冷却接触板。
3、接触板紧固螺栓:两接触板及其间的绝缘板需用两个螺栓紧固,螺栓一般用黄铜棒制造,使用时要加上胶木垫圈和胶木套管,使螺栓与接触板绝缘。
如果接触板工作时温升不高,紧固螺栓可用尼龙制造。
4、定位环压板:使用夹布胶木制造,用于夹紧定位环,使之与感应器本体绝缘。
5、定位环:用于淬火零件的轴向定位和径向限位,工作时零件上端的六方帽压在定位环上,以保证零件淬火区的轴向分布准确。
6、压板紧固螺栓:用于压板与感应器上法兰盘之间的紧固,保证定位环的位置准确。
7、法兰盘:用紫铜板制造,与有效圈及水套焊接,以便形成淬火水腔,并能附代上下定位夹具。
8、有效圈:能形成磁场,而该磁场直接用于加热工件的导体称为有效圈或有效导体,如果有效导体是一段铜管也可称为有效导线。
它与接触板牢固地焊接在一起。
9、淬火水管:其全称应是淬火水导入管,淬火水通过它进入淬火水腔,淬火水管与水套焊接在一起。
10、淬火水孔:当零件加热到淬火温度后,淬火水经淬火水管进入淬火水腔,再从淬火水孔喷射而出,使零件淬火。
11、感应器定位孔:钻在接触板端面上,当感应器安装时,淬火变压器二级线圈的固定螺栓从固定孔伸出来,拧紧螺母,保证接触板与变压器二级线圈接触板良好。
12、冷却水管:焊接在冷却水盒上,一进一出。
13、限位板:对零件下端进行径向限位。
根据淬火感应器所加工零件的不同,淬火感应器又分为以下几类:一.圆柱形零件表面淬火感应器1.轴类零件表面连续淬火感应器2.长轴类零件表面淬火感应器3.汽车半轴零件连续淬火感应器4.镗杆零件连续淬火感应器5.钻杆及岩芯管零件高频连续淬火感应器6.长轴类零件整体表面淬火感应器7.半圈式连续淬火感应器二.齿轮淬火感应器1.全齿加热淬火感应器2.齿轮轴连续淬火感应器3.单齿表面淬火感应器4.大模数齿轮单齿连续淬火感应器5.沿齿沟淬火感应器6.中、高频沿齿沟连续淬火感应器三.曲轴淬火感应器1.分合式曲轴淬火感应器2.半圈式曲轴淬火感应器四.凸轮轴及凸轮类零件表面淬火感应器1.凸轮轴表面淬火感应器2.汽车减震器凸轮淬火感应器3.刹车凸轮淬火感应器五.球面零件淬火感应器1.汽车转向节球头支承中频淬火感应器2.汽车转向拉杆球头销淬火感应器3.小型球头销淬火感应器4.大型球头销淬火感应器5.连接球头淬火感应器六.平面及平面类零件淬火感应器1.高频平面连续加热淬火感应器2.中频平面连续加热感应器3.机床导轨高频淬火感应器4.机床导轨中频淬火感应器5.钢轨和道岔尖轨中频淬火感应器6.平面齿盘同时加热感应器7.平台表面淬火感应器七.端头和端面淬火感应器1.气门调整螺栓顶部淬火感应器2.进排气阀端头淬火感应器3.油嘴端头淬火感应器4.支承圈侧端面淬火感应器八.套类零件内表面淬火感应器1.直径大于75mm的深内孔淬火感应器2.直径25mm ~75mm的深内孔淬火感应器3.直径20mm ~30mm的内孔淬火感应器4.直径小于20mm的内孔淬火感应器5.肓孔淬火感应器6.液压马达内曲线导轨中频淬火感应器7.主轴内锥孔中频淬火感应器8.液压缸孔高频淬火感应器九.槽口淬火感应器1.刹车齿轮槽口淬火感应器2.爪式联轴器槽口淬火感应器3.变速箱导块槽口淬火感应器4.V型槽口淬火感应器以上本文由河北恒远电炉()提供。
感应淬火 (2)
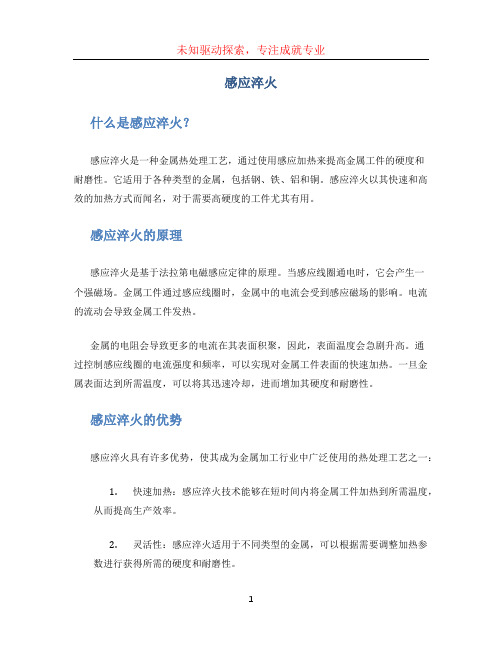
感应淬火什么是感应淬火?感应淬火是一种金属热处理工艺,通过使用感应加热来提高金属工件的硬度和耐磨性。
它适用于各种类型的金属,包括钢、铁、铝和铜。
感应淬火以其快速和高效的加热方式而闻名,对于需要高硬度的工件尤其有用。
感应淬火的原理感应淬火是基于法拉第电磁感应定律的原理。
当感应线圈通电时,它会产生一个强磁场。
金属工件通过感应线圈时,金属中的电流会受到感应磁场的影响。
电流的流动会导致金属工件发热。
金属的电阻会导致更多的电流在其表面积聚,因此,表面温度会急剧升高。
通过控制感应线圈的电流强度和频率,可以实现对金属工件表面的快速加热。
一旦金属表面达到所需温度,可以将其迅速冷却,进而增加其硬度和耐磨性。
感应淬火的优势感应淬火具有许多优势,使其成为金属加工行业中广泛使用的热处理工艺之一:1.快速加热:感应淬火技术能够在短时间内将金属工件加热到所需温度,从而提高生产效率。
2.灵活性:感应淬火适用于不同类型的金属,可以根据需要调整加热参数进行获得所需的硬度和耐磨性。
3.均匀加热:感应淬火能够实现金属表面的均匀加热,可以避免局部热应力和变形。
4.环保:相比传统的加热方式,感应淬火减少了能源消耗和排放,对环境更友好。
感应淬火的应用感应淬火广泛应用于各个行业,包括汽车、机械、航空航天等。
以下是几个常见的应用领域:1.汽车零部件:感应淬火可用于加工发动机气门、凸轮轴和传动轴等零部件,使其具有更高的硬度和耐磨性。
2.钢铁加工:对于一些需要高硬度和耐磨性的钢材,如轴承钢和切割工具钢,感应淬火可以提供更好的性能。
3.电力行业:感应淬火可用于制造电机转子和发电机组件等关键元件,提高其耐用性和效率。
4.金属模具:通过感应淬火处理,金属模具可以获得更高的硬度和表面耐磨性,延长使用寿命。
感应淬火的挑战尽管感应淬火具有许多优势,但也存在一些挑战需要考虑:1.设备成本:感应加热设备的价格相对较高,这可能对小型企业和初创公司构成一定的挑战。
2.参数控制:感应淬火需要准确控制加热参数,包括电流强度、频率和加热时间等。
高频感应淬火设备原理和用途-河南高频淬火机
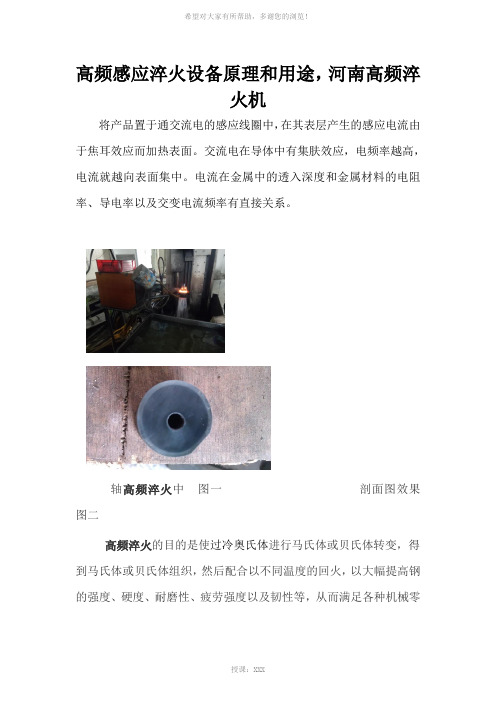
高频感应淬火设备原理和用途,河南高频淬火机将产品置于通交流电的感应线圈中,在其表层产生的感应电流由于焦耳效应而加热表面。
交流电在导体中有集肤效应,电频率越高,电流就越向表面集中。
电流在金属中的透入深度和金属材料的电阻率、导电率以及交变电流频率有直接关系。
轴高频淬火中图一剖面图效果图二高频淬火的目的是使过冷奥氏体进行马氏体或贝氏体转变,得到马氏体或贝氏体组织,然后配合以不同温度的回火,以大幅提高钢的强度、硬度、耐磨性、疲劳强度以及韧性等,从而满足各种机械零件和工具的不同使用要求。
也可以通过高频淬火满足某些特种钢材的的铁磁性、耐蚀性等特殊的物理、化学性能。
高频淬火设备多数用于工业金属零件表面淬火,是使工件表面产生一定的感应电流,迅速加热零件表面,然后迅速淬火的一种金属热处理方法。
高频淬火设备,即对工件进行感应加热,以进行表面淬火。
感应加热的原理:工件放到感应器内,感应器一般是输入中频或高频交流电 (1000-300000Hz或更高)的空心铜管。
产生交变磁场在工件中产生出同频率的感应电流,这种感应电流在工件的分布是不均匀的,在表面强,而在内部很弱,到心部接近于0,利用这个集肤效应,可使工件表面迅速加热,在几秒钟内表面温度上升到800-1000℃,而心部温度升高很小。
河南德胜高频淬火设备图三数控淬火机床图四一、节能型高频淬火设备广泛应用于:汽车半轴、球笼、球销、球座、转向节、拨叉轴、汽车摇臂、摩托车零部件的淬火处理等;机械零件的热处理;如各种齿轮、链轮、各种轴、销等的淬火处理;黄铜阀门、接头等制品的锻打或铸造;有色金属的熔炼等等领域。
具有节能环保,性能稳定,可靠,应用广泛,使用简单安全等特点。
该设备适用于: 1、直径适应盘类、轴类等工件的表面淬火;2、需匹配数控淬火机床能实现分段和连续工作;三、节能型DSGP-120超音频感应加热设备主要特点:>IGBT逆变技术和串联谐振电路;>锁相技术和软开技术确保高可靠性,实现频率自动跟踪;>功率因数不小于0.95;>100%负载持续率设计,可连续工作,可马上开机或者关机;>保护电路功能>环保、清洁、无污染,提高工人工作环境;>低能耗,变换效率高达97.5%以上,与可控硅中频感应加热设备相比节能10%--30%;>取代氧焕焰、焦炭炉、盐浴炉、煤气炉、油炉等传统加热方式;>操作简单安全。
高端数控感应淬火机床原理

高端数控感应淬火机床原理1.引言随着制造业的发展,数控机床在金属加工领域的应用日益广泛。
感应淬火机床作为一种高端数控机床,其原理与传统的淬火机床有所不同,具有更高的加工精度和效率。
本文将介绍高端数控感应淬火机床的原理及其工作过程。
2.感应淬火的基本原理感应淬火是一种利用电磁感应原理进行加热和淬火的方法。
在感应淬火机床中,通过电磁感应线圈产生高频交流电场,使工件表面产生感应加热,然后通过快速冷却来实现淬火过程。
感应淬火具有加热均匀、温度可控、淬火速度快等优点,因此在金属加工领域中得到了广泛的应用。
3.高端数控感应淬火机床的结构高端数控感应淬火机床由数控系统、感应装置、冷却系统、夹具等部分组成。
其中数控系统为感应淬火机床的核心,控制整个加工过程的参数和轨迹,具有高精度、高效率、高自动化程度等特点。
3.1数控系统数控系统是感应淬火机床的核心部件,其主要功能是控制电磁感应线圈的工作状态,调节加热功率和加热时间,实现对工件的精准加热和淬火。
数控系统通常采用PLC或CNC控制,能够实现多轴联动控制、自动化加工流程、参数设定和调整等功能。
3.2感应装置感应装置是感应淬火机床中的重要部件,通过高频交流电场对工件进行感应加热。
感应装置通常由电磁感应线圈、电源装置、冷却系统等部分组成。
电磁感应线圈根据工件的形状和尺寸设计成不同的形状和尺寸,有效地实现对工件的均匀加热。
3.3冷却系统冷却系统是感应淬火机床中的关键部件,其主要作用是对经过加热的工件进行快速冷却,实现淬火过程。
冷却系统通常采用循环水冷却或喷水冷却的方式,能够实现对工件的快速冷却和温度控制。
3.4夹具夹具是感应淬火机床中的辅助部件,用于固定和夹持工件,确保加工过程中工件的位置和姿态的稳定性。
夹具通常根据工件的形状和尺寸设计成不同的形状和尺寸,能够适应不同加工需求。
4.高端数控感应淬火机床的工作原理高端数控感应淬火机床的工作原理是将工件放置在感应装置中,通过数控系统对电磁感应线圈进行控制,实现对工件的精准加热和淬火。
恒远中频淬火感应器的典型结构
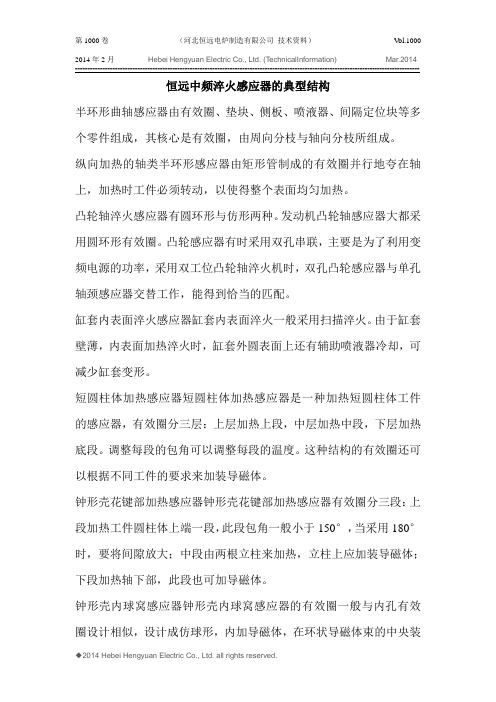
恒远中频淬火感应器的典型结构半环形曲轴感应器由有效圈、垫块、侧板、喷液器、间隔定位块等多个零件组成,其核心是有效圈,由周向分枝与轴向分枝所组成。
纵向加热的轴类半环形感应器由矩形管制成的有效圈并行地夸在轴上,加热时工件必须转动,以使得整个表面均匀加热。
凸轮轴淬火感应器有圆环形与仿形两种。
发动机凸轮轴感应器大都采用圆环形有效圈。
凸轮感应器有时采用双孔串联,主要是为了利用变频电源的功率,采用双工位凸轮轴淬火机时,双孔凸轮感应器与单孔轴颈感应器交替工作,能得到恰当的匹配。
缸套内表面淬火感应器缸套内表面淬火一般采用扫描淬火。
由于缸套壁薄,内表面加热淬火时,缸套外圆表面上还有辅助喷液器冷却,可减少缸套变形。
短圆柱体加热感应器短圆柱体加热感应器是一种加热短圆柱体工件的感应器,有效圈分三层:上层加热上段,中层加热中段,下层加热底段。
调整每段的包角可以调整每段的温度。
这种结构的有效圈还可以根据不同工件的要求来加装导磁体。
钟形壳花键部加热感应器钟形壳花键部加热感应器有效圈分三段:上段加热工件圆柱体上端一段,此段包角一般小于150°,当采用180°时,要将间隙放大;中段由两根立柱来加热,立柱上应加装导磁体;下段加热轴下部,此段也可加导磁体。
钟形壳内球窝感应器钟形壳内球窝感应器的有效圈一般与内孔有效圈设计相似,设计成仿球形,内加导磁体,在环状导磁体束的中央装上了喷液管,喷液喷到球窝底再反射到需淬硬表面上。
三柱滑套内孔加热感应器三柱滑套内孔加热感应器有两种设计方法:扫描淬火法。
有效圈是三个加热圈串联,工件位于上端。
加热淬火开始,工件向下移动,位于有效圈下的喷液器开始喷液淬火;扫描到最后,位于喷液器中心的第二喷液器,将淬火液喷向工件闭端,补充冷却了有效圈扫描停止这一段加热区。
一次加热法。
优先权仍是串联三个圈,但喷液器不同。
半轴扫描淬火感应器半轴的加热部位一般为法兰端面、杆部与花键轴段。
半轴扫描淬火感应器有效圈一般加装导磁体,是电流能面向法兰面。
高端数控感应淬火机床原理
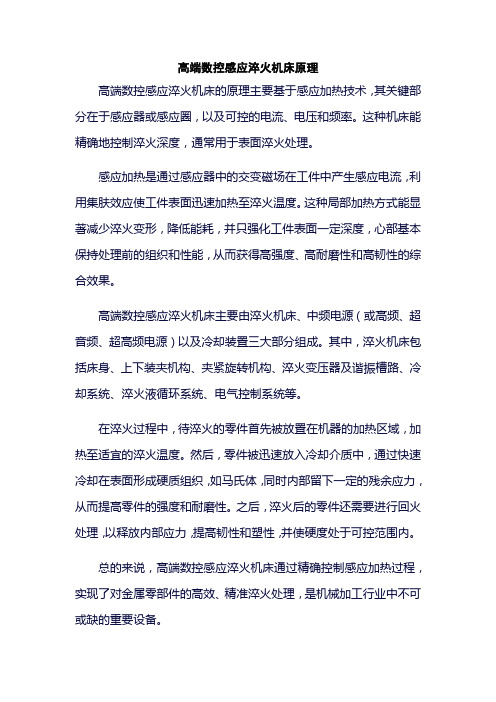
高端数控感应淬火机床原理
高端数控感应淬火机床的原理主要基于感应加热技术,其关键部分在于感应器或感应圈,以及可控的电流、电压和频率。
这种机床能精确地控制淬火深度,通常用于表面淬火处理。
感应加热是通过感应器中的交变磁场在工件中产生感应电流,利用集肤效应使工件表面迅速加热至淬火温度。
这种局部加热方式能显著减少淬火变形,降低能耗,并只强化工件表面一定深度,心部基本保持处理前的组织和性能,从而获得高强度、高耐磨性和高韧性的综合效果。
高端数控感应淬火机床主要由淬火机床、中频电源(或高频、超音频、超高频电源)以及冷却装置三大部分组成。
其中,淬火机床包括床身、上下装夹机构、夹紧旋转机构、淬火变压器及谐振槽路、冷却系统、淬火液循环系统、电气控制系统等。
在淬火过程中,待淬火的零件首先被放置在机器的加热区域,加热至适宜的淬火温度。
然后,零件被迅速放入冷却介质中,通过快速冷却在表面形成硬质组织,如马氏体,同时内部留下一定的残余应力,从而提高零件的强度和耐磨性。
之后,淬火后的零件还需要进行回火处理,以释放内部应力,提高韧性和塑性,并使硬度处于可控范围内。
总的来说,高端数控感应淬火机床通过精确控制感应加热过程,实现了对金属零部件的高效、精准淬火处理,是机械加工行业中不可或缺的重要设备。
感应加热淬火机床保养__感应加热淬火机床设备参数
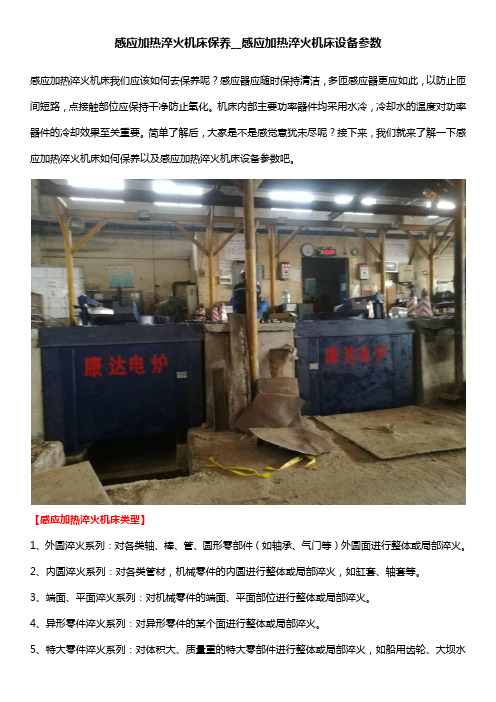
感应加热淬火机床保养__感应加热淬火机床设备参数感应加热淬火机床我们应该如何去保养呢?感应器应随时保持清洁,多匝感应器更应如此,以防止匝间短路,点接触部位应保持干净防止氧化。
机床内部主要功率器件均采用水冷,冷却水的温度对功率器件的冷却效果至关重要。
简单了解后,大家是不是感觉意犹未尽呢?接下来,我们就来了解一下感应加热淬火机床如何保养以及感应加热淬火机床设备参数吧。
【感应加热淬火机床类型】1、外圆淬火系列:对各类轴、棒、管、圆形零部件(如轴承、气门等)外圆面进行整体或局部淬火。
2、内圆淬火系列:对各类管材,机械零件的内圆进行整体或局部淬火,如缸套、轴套等。
3、端面、平面淬火系列:对机械零件的端面、平面部位进行整体或局部淬火。
4、异形零件淬火系列:对异形零件的某个面进行整体或局部淬火。
5、特大零件淬火系列:对体积大、质量重的特大零部件进行整体或局部淬火,如船用齿轮、大坝水闸道轨、大型输油管道等。
6、模具表面淬火系列:模具表面感应淬火机床是一种适用于大型汽车覆盖件模具和大型非圆空间曲面零件的热处理的数控工艺装备。
【感应加热淬火机床保养】1、冷却水应保证水质清洁无杂质,若水质太差,应在水入口处加过滤器,工作时严禁缺水。
2、使用中应防止感应器短路。
3、感应器应随时保持清洁,多匝感应器更应如此,以防止匝间短路,点接触部位应保持干净防止氧化。
4、机床内部主要功率器件均采用水冷,冷却水的温度对功率器件的冷却效果至关重要,在停止工作的间隙时间,请不要关冷却水,对于负载持续率为100的用户冷却水水温低于40℃,条件允许推荐使用软水。
5、使用普通水作冷却水的用户,应定期(以水质而定,一般为两个月为一个周期),对设备内的管路进行除垢处理,以防设备因散热不畅而损坏。
除垢剂选用普通汽车水箱除垢剂,按1∶40稀释后直接泵入设备管路进行清洗。
6、机内应保持清洁,应定期用毛刷和压缩空气清除电路板和其它部件上的灰尘。
7、随时保持风冷、水冷通道畅通无阻。
感应加热表面淬火的特点

感应加热表面淬火的特点感应加热表面淬火是一种通过感应加热将金属表面加热至淬火温度,然后迅速冷却以使金属表面硬化的热处理方法。
它具有以下几个特点。
感应加热表面淬火具有加热速度快的特点。
感应加热是利用变化磁场在导体内产生涡流热,将电能转化为热能。
感应加热具有高效率、高加热速度和良好的控制性能等优点,能够快速将金属表面加热至淬火温度,大大缩短了加热时间。
感应加热表面淬火具有淬火效果好的特点。
感应加热的加热速度快,能够迅速将金属表面加热至淬火温度,然后通过冷却剂迅速冷却,使金属表面形成马氏体组织,从而提高了金属表面的硬度和耐磨性。
感应加热表面淬火具有加热均匀的特点。
感应加热是通过变化磁场在导体内产生涡流热,涡流热的分布与导体的电阻率和磁导率有关。
在感应加热过程中,由于导体表面与磁场的交互作用,导致表层电流密度大于内部电流密度,从而实现了金属表面的加热均匀性。
感应加热表面淬火具有节能环保的特点。
感应加热能够将电能转化为热能,不需要加热介质,减少了能源的浪费。
同时,感应加热的加热速度快,加热时间短,减少了加热过程中的能量消耗。
此外,感应加热无污染,不会产生废气、废水和噪音等环境污染物,更加符合环保要求。
感应加热表面淬火具有操作简便、自动化程度高的特点。
感应加热过程中只需要将工件放置在感应加热器中,通过调节加热器的电源、工作频率和工作时间等参数,即可实现加热和冷却过程的控制。
同时,感应加热设备可以与传感器、控制器等自动化设备相连接,实现自动化生产过程,提高生产效率和产品质量。
感应加热表面淬火具有加热速度快、淬火效果好、加热均匀、节能环保和操作简便等特点。
在金属加工和热处理领域中,感应加热表面淬火已被广泛应用,为金属制品的性能提升和质量保障提供了有效的解决方案。
感应淬火

7.不仅用在表面淬火还可用在穿透加热与化学热处理等。载线、电容器、变压器、感应器、机床几部分组成。
感应淬火分类
感应淬火类型分为:工频、低频、中频、超音频、高频、超高频几种,根据淬硬深度需要来选择适用频率。淬硬层深度越大,所需频率越低,反之,则越高。
感应淬火英文名称:induction hardening定义:利用感应电流通过材料或工件所产生的热量,使材料或工件表层、局部或整体加热并快速冷却的淬火。
简介
感应淬火(induction hardening)
感应加热就是利用电磁感应在工件内产生涡流而将工件进行加热。感应加热表面淬火与普通淬火比具有如下优点:
1.热源在工件表层,加热速度快,热效率高
感应淬火设备
2.工件因不是整体加热,变形小
3.工件加热时间短,表面氧化脱碳量少
4.工件表面硬度高,缺口敏感性小,冲击韧性、疲劳强度以及耐磨性等均有很大提高。有利于发挥材料的潜力,节约材料消耗,提高零件使用寿命
5.设备紧凑,使用方便,劳动条件好
6.便于机械化和自动化
目前感应淬火以中频、超音频、高频、超高频为主。
中频一般为可控硅,目前国内有用IGBT感应电源做中频的,比可控硅节能,但是价格较可控硅的高。相对来说,IGBT是发展趋势,因其转换效率较高,而且性能稳定,内部实现软开关,不容易出故障。
超音频、高频则是IGBT感应电源。目前国内IGBT感应电源已经历三代。第一代为窄频率多主板为显著特征。第二代则是宽频率范围,单一主板为主要特征。第三代,则从技术结构上进行了革命性的改变,实现数字化控制,能传输和储存能量监控数据,便于实现标准化管理。
感应加热淬火设备-精选文档
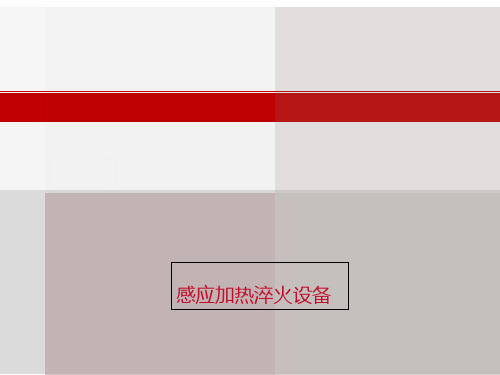
中频感应淬火设备的应用,具体如下: 1.各种五金工具、手工具。如钳子、扳手、锤子、斧头、 旋具、剪刀(园艺剪)等的淬火; 2.各种汽车、摩托车配件。如曲轴、连杆、活塞销、链轮、 铝轮、气门、摇臂轴、传动半轴、小轴、拔插等的淬火; 3.各种电动工具。如齿轮、轴心; 4.机床行业类。如机床床面、机床导轨等的淬火; 5.各种五金金属零件、机械加工零件。如轴类、齿轮、链 轮、凸轮、夹头、夹具等的淬火; 6.五金模具行业。如小型模具、磨具附件、模具内孔等的 淬火;
11
感应加热淬火设备自动化程度高,可实现全自动无人操作选用 自动上料和自动出料分检装置,再配上我公司的专用控制软件, 可实现全自动无人操作。 感应加热淬火设备的突出特点: 1、采用IGBT为主器件、全桥逆变。 2、100%负载持续率设计,可连续工作。 3、保护功能完善,可靠性高。 4、可远控和配接红外测温,实现温度的自动控制,提高加热 质量和简化工人操作。 5、取代氧炔焰、焦碳炉、盐浴炉、煤气炉、油炉等加热方式 。 6、采用频率自动跟踪及多路闭环控制7、安装简单,操作方便 。
6
特殊水冷系统降低了功耗,完善的保护措施保证设备在各 种情况下安全连续运行。同时,采用多丝扭绞电缆做感应 加热电源与感应加热器之间的电气连接线,降低了线路的 交流损耗。
感应加热装置的效率比火焰炉高60%以上,比电阻炉高 50%以上,比其他采用可控硅控制的感应加热装置高30% 以上,具有明显的节能效果,市场前景广阔。
4
感应加热时,工件截面上感应电流的分布状态与电流频率有 关。电流频率越高,集肤效应越强,感应电流集中的表层就 越薄,这样加热层深度与淬硬深度也就越薄。淬硬度根据客 户的要求,可通过调节电流频率来获得不同的淬硬层深度。
感应淬火的研究
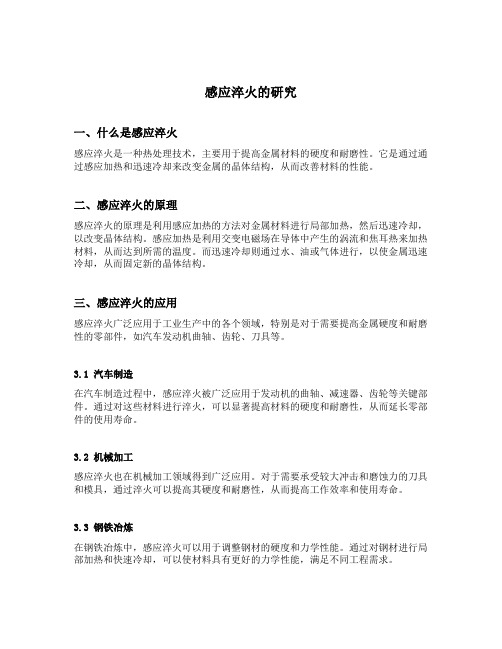
感应淬火的研究一、什么是感应淬火感应淬火是一种热处理技术,主要用于提高金属材料的硬度和耐磨性。
它是通过通过感应加热和迅速冷却来改变金属的晶体结构,从而改善材料的性能。
二、感应淬火的原理感应淬火的原理是利用感应加热的方法对金属材料进行局部加热,然后迅速冷却,以改变晶体结构。
感应加热是利用交变电磁场在导体中产生的涡流和焦耳热来加热材料,从而达到所需的温度。
而迅速冷却则通过水、油或气体进行,以使金属迅速冷却,从而固定新的晶体结构。
三、感应淬火的应用感应淬火广泛应用于工业生产中的各个领域,特别是对于需要提高金属硬度和耐磨性的零部件,如汽车发动机曲轴、齿轮、刀具等。
3.1 汽车制造在汽车制造过程中,感应淬火被广泛应用于发动机的曲轴、减速器、齿轮等关键部件。
通过对这些材料进行淬火,可以显著提高材料的硬度和耐磨性,从而延长零部件的使用寿命。
3.2 机械加工感应淬火也在机械加工领域得到广泛应用。
对于需要承受较大冲击和磨蚀力的刀具和模具,通过淬火可以提高其硬度和耐磨性,从而提高工作效率和使用寿命。
3.3 钢铁冶炼在钢铁冶炼中,感应淬火可以用于调整钢材的硬度和力学性能。
通过对钢材进行局部加热和快速冷却,可以使材料具有更好的力学性能,满足不同工程需求。
3.4 其他行业应用此外,感应淬火还可以用于其他行业的热处理需求,例如航空航天、船舶制造、电子设备等。
通过感应淬火技术,这些行业可以提高产品的质量和性能,提高工作效率。
四、感应淬火的优势感应淬火相对于传统的淬火方法具有一些明显的优势。
1.高效:感应加热可以实现局部加热,避免了整体加热的热能浪费,提高了能源利用率。
同时,感应淬火的加热速度快,可以缩短生产周期,提高生产效率。
2.均匀性好:感应加热可以实现局部加热,能够更好地控制材料的温度分布,避免了由于不均匀加热导致的变形和裂纹。
3.精确控制:感应加热设备可以实时监控和控制温度,可以精确控制加热温度和保持时间,以确保淬火的效果。
感应加热淬火设备

要获得良好的感应加热效果,需要制定正确的工艺。结果成 功与否,取决于电流频率、单位表面功率及输入功率、加热 温度、加热速度、加热方法、感应器结构及尺寸等工艺参数 的选择,缺一不可。
为提高感应加热的效率,减少漏磁损失,感应器与工件表面 的间隙要尽量减小,所以加厚机热处理和芯棒热处理等应用 会有不同规格感应炉的情况。对于维护过程中需要提醒的是 感应器除了要水冷外,需要有足够的机械强度和使用寿命, 因为中频电源感应器和工件之间有电磁力的作用,电流越大, 电磁力越大。例如,平面加热时,感应器与工件间会产生一 个推力,镶嵌导磁体后其之间将产生一个吸力,如感应器强 度不够,可能引起感应器变形或损坏。这种情况曾在HFW焊 管线中频线圈上得以体现,其部分导磁体会有脱落现象,有 时线圈会产生直度变形。
4
感应加热时,工件截面上感应电流的分布状态与电流频率有 关。电流频率越高,集肤效应越强,感应电流集中的表层就 越薄,这样加热层深度与淬硬深度也就越薄。淬硬度根据客 户的要求,可通过调节电流频率来获得不同的淬硬层深度。
中频淬火,就是将金属放在一个通有交流电而产生交变磁场 的感应线圈内,使金属件内感应出交流电,由于趋肤效应, 电流主要集中在金属表面,所以表面的温度最高,在感应线 圈下面紧跟着喷水冷却或其他冷却,由于感应加热及冷却主 要集中在金属件表面,所以表面改性很明显,而内部改性基 本没有,可以有很特殊的热处理效果。
15
用于普通工件的感应加热电源控制系统示意图
TA 656VAC
S300
高压桥
低压桥起动条件
低压桥
全控
来自S300
半控
来自S300
PROFIBUS
来自S300
逆变器 负载电路
IMF
S300
- 1、下载文档前请自行甄别文档内容的完整性,平台不提供额外的编辑、内容补充、找答案等附加服务。
- 2、"仅部分预览"的文档,不可在线预览部分如存在完整性等问题,可反馈申请退款(可完整预览的文档不适用该条件!)。
- 3、如文档侵犯您的权益,请联系客服反馈,我们会尽快为您处理(人工客服工作时间:9:00-18:30)。
关于感应淬火机床的结构与性能的介绍
一、感应淬火机床的类型:
感应淬火机床按所配电源设备区分,可分为高频淬火机床和中频淬火机床;按机床功能区分,可分为通用淬火机床和专用淬火机床。
最早的淬火机床是由金属切削机床改制而成的,淬火机床和金属切削机床所不同处有三点,即没有切削金属所产生的负载,有电磁场,有淬火冷却介质和电器以及感应器等的冷却水要求。
二、淬火机床常用的数控系统:
目前国内外数控系统品种繁多,用途不尽相同,适合淬火机床特点的数控系统有如下几种:(1)国产经济型数控系统:这种系统编程简单易学,操作方便,价格低廉,在中、抵挡数控通用淬火机床上应用。
但是,该系统应用在通用淬火机床上存在一些问题:一是系统输出、输入接口是按机加工机床功能要求设计的,特别是输入接口相对较少;二是相邻两条指令时,其间有0.4s间隔时间,不能做到加热结束后立即喷液(对小型工件一般要求加热后立即喷液);三是选用双坐标数控系统一个用于升降、一个用于旋转(分度)时,双坐标同时连续运动是会相互影响,所以将这种经济型数控系统用于通用淬火机床需进行必要的改造。
(2)国外经济型数控系统:国外的经济型数控系统有多种品牌,多种型号,其中以Siemense802系列常用。
这种系统具有功能完善、性能良好、稳定可靠、精度高、储存程序量大等特点,但价格偏高、维修成本高。
(3)工业控制计算机数控系统:工控机应用于淬火机床可以充分利用PC机的硬件(如586、Pentium III)与软件(如DOS、Windows、Win98/Me、WindowNT/2000)资源融合最新控制理论及网络技术,实现最为复杂的控制和更强的软件功能。
三、通用淬火机床的传动方式一般有几种?哪种比较稳定?
按主要传动型式可分为液压式和全机械式。
液压传动具有结构简单、驱动力大、移动速度快(可达150mm/S以上)等优点。
单存在移动速度不稳定、定位精度低等缺点,液压驱动感应淬火机床渐趋淘汰。
全机械式传动分为T型丝杠、滚珠丝杠、直线移动导轨等多种传动形式。
全机械式传动具有移动速度快、定位精准高、易实现变速移动等优点。
按移动部分机械结构形式可分为滑板式、导柱式两种。
滑板式是我国应用数量最多的二结构形式,其床身往往采用经过时效处理的铸造或焊接结构,承载量大,稳定性好,可以加工较大、较重的工件,适用范围最广,但该形式具有床身笨重,滑动不灵活,导轨加工复杂等缺点。
导柱式结构在欧美国家较常见,这种结构的主要优点是机床重量轻,运动灵便,便于实现与淬火液循环冷却系统的一体化设计,但不太适应大、重工件的加工,在行程大时稳定性稍差(如工件振动).
四、淬火工件扫描淬火时,应如何选取工件移动或变压器感应器组移动方式?
淬火机床一般有两种传动方式,一种是工件移动并传动,另一种是工件移动升降而变压器感应器组作升降移动。
两种传动方式的选定主要考虑以下因素:
1)从整个淬火机床高度(或长度)考虑,工件长度超过2m时,一般选用变压器感应器度移动。
因为这样设计,淬火机床的总高度(或长度)可以较低(短)。
扫描淬
火机床的总高度如采用工件移动,一般为工件扫描长度的1倍以上,两者相比。
优
越性可见。
因此,小型通用淬火机床、凸轮轴、半轴、转向齿条淬火机均采用此种
工件移动并转动的方式,而工件长度超过2m的立式淬火机军此阿勇变压器感应器
组移动方式。
2)从淬火工件的形状与重量考虑,如大齿轮单齿扫描机床,齿轮直径大6吗m,重量达20t,淬火变压器与感应器体积与重量均小,自然采用变压器感应器组的传动方
式移动比较方便。
3)特殊情况考虑,例如轧辊长而重,但由于变压器感应器组相对较重,工作时振动很大,此时仍采用工件移动方式,而变压器感应器固定不动。
4)近年来,德国一些感应加热公司对工件在750-1500mm的淬火机床亦采用变压器感应器组移动结构,是淬火机床的总高度下降,而Z轴快进速度大到24m/S(400mm/S) 五、淬火机床主顶尖的转速应如何选取?
淬火工件加热时转速的选取,从工件加热均匀性来说,转速越快,由于感应器与工件间隙不均产生的温度不均影响越小。
早期的淬机床对转速范围一般设定为60-300/min,有些机床是有级变速,有些机床则采用无级变速,用户可以任意选择。
然而有些机床因特定条件,转速特低。
如曲轴颈旋转淬火机,其主轴颈转速常用60r/min,而连杆颈转速则选用30r/min,这是由于连杆颈在淬火机床上通过摆动机构(四相连杆结构)产生转动,如转速太快,半环感应器不能稳定地跨到轴颈上随动,所以只能采用30r/min的低速旋转,此种转速对轴颈加热而言是不合适的,主轴颈采用60r/min是由于采用双速电机,设计上可简单的理由。
有一种论点,认为转速的选取,应该以工件加热周期来考虑,工件自一个加热周期中,旋转应不低于10次,就能保证工件圆周上温度均匀。
据此计算,一般工件感应加热时间常在5-10s之间,如果哦5s转10转,则为120r/min,10s转10转,则转速为60r/min。
随着感应加热速度的发展,对于同步双频加热齿轮,齿轮的加热周期已缩短到0.1-0.2s。
因此,其工件转速要求在不断增加,有些淬火机床主轴的最大转速已达到1600人/min。
目前,淬火机床的转速达到600r/min的已不多见。
另外,工件转速与冷却也有密切关系,对齿轮、花键轴而言,淬火冷却常采用喷液方式,工件转速太快,淬火液对齿的一侧冷却不足。
因此,淬火机床的转速还是以600r/min或300r/min作为上限。
另外,要研发加热结束后工件能及时降速的机械或电气部件,使工件既能快速旋转达到均匀加热目的,又能慢速旋转,以达到均匀冷却齿轮类工件的要求。