常减压装置新技术的应用
先进控制技术在常减压装置的应用
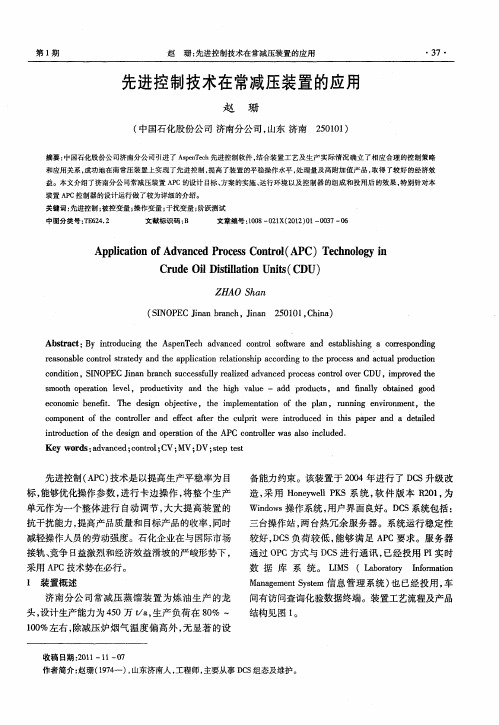
采用 A C技术势在必行。 P
l 装置概 述
数 据 库 系 统 。 LM (Lbr o I o ao IS ao t y n r tn ar fm i M ngm n Ss m信息 管理系统 ) 已经投用 , aae et y e t 也 车 间有访问查询化验数据终端。装置工艺流程及产品
c mp n n f t e c n o lr a d e e t atr t e c l r e e i t d c d i h s p p r a d a d ti d o o e t o o t l n f c fe u p i w r n r u e n t i a e n e al h r e h t o e i t d cin o e d s n p r t n o e AP o t l rwa l n l d d n o u t f e i a d o e a o ft C c nr l sa s i cu e . r o h t n g i h oe o Ke r s a v n e c n r l CV; y wo d : d a c d; o t ; o MV; V ;t p t s D s e t e
s ot prtn l e,pouti ad tehg a e— ad pout,ad f a otnd go m o oeao e l rdcv h i v i  ̄ n h ih vl u d rdc s n nl ba e od i  ̄ i
eoo i b nf .T e d s n ojc v ,te i pe n t n o h ln u nn n i n n ,te cn m c e e t h ei bet e h m l i g i met i fte pa ,rn ig e v omet h ao r
常减压装置新技术的应用
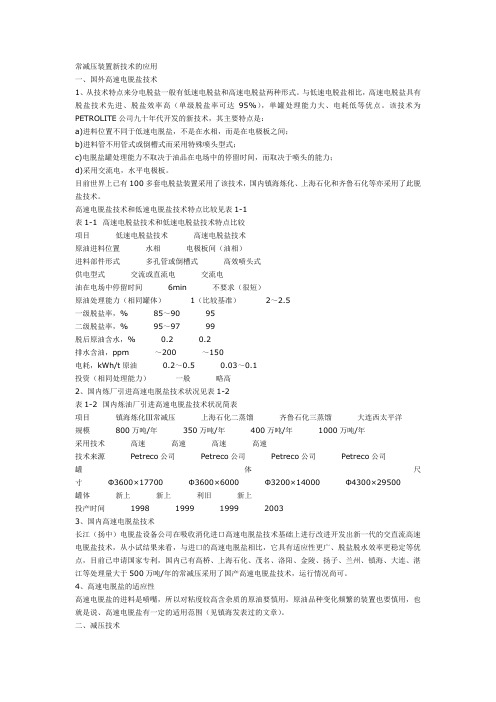
常减压装置新技术的应用一、国外高速电脱盐技术1、从技术特点来分电脱盐一般有低速电脱盐和高速电脱盐两种形式。
与低速电脱盐相比,高速电脱盐具有脱盐技术先进、脱盐效率高(单级脱盐率可达95%),单罐处理能力大、电耗低等优点。
该技术为PETROLITE公司九十年代开发的新技术,其主要特点是:a)进料位置不同于低速电脱盐,不是在水相,而是在电极板之间;b)进料管不用管式或倒槽式而采用特殊喷头型式;c)电脱盐罐处理能力不取决于油品在电场中的停留时间,而取决于喷头的能力;d)采用交流电,水平电极板。
目前世界上已有100多套电脱盐装置采用了该技术,国内镇海炼化、上海石化和齐鲁石化等亦采用了此脱盐技术。
高速电脱盐技术和低速电脱盐技术特点比较见表1-1表1-1 高速电脱盐技术和低速电脱盐技术特点比较项目低速电脱盐技术高速电脱盐技术原油进料位置水相电极板间(油相)进料部件形式多孔管或倒槽式高效喷头式供电型式交流或直流电交流电油在电场中停留时间6min 不要求(很短)原油处理能力(相同罐体)1(比较基准)2~2.5一级脱盐率,% 85~90 95二级脱盐率,% 95~97 99脱后原油含水,% 0.2 0.2排水含油,ppm ~200 ~150电耗,kWh/t原油0.2~0.5 0.03~0.1投资(相同处理能力)一般略高2、国内炼厂引进高速电脱盐技术状况见表1-2表1-2 国内炼油厂引进高速电脱盐技术状况简表项目镇海炼化Ⅲ常减压上海石化二蒸馏齐鲁石化三蒸馏大连西太平洋规模800万吨/年350万吨/年400万吨/年1000万吨/年采用技术高速高速高速高速技术来源Petreco公司Petreco公司Petreco公司Petreco公司罐体尺寸Φ3600×17700Φ3600×6000Φ3200×14000Φ4300×29500罐体新上新上利旧新上投产时间1998 1999 1999 20033、国内高速电脱盐技术长江(扬中)电脱盐设备公司在吸收消化进口高速电脱盐技术基础上进行改进开发出新一代的交直流高速电脱盐技术,从小试结果来看,与进口的高速电脱盐相比,它具有适应性更广、脱盐脱水效率更稳定等优点,目前已申请国家专利,国内已有高桥、上海石化、茂名、洛阳、金陵、扬子、兰州、镇海、大连、湛江等处理量大于500万吨/年的常减压采用了国产高速电脱盐技术,运行情况尚可。
新型计量泵在常减压装置的应用
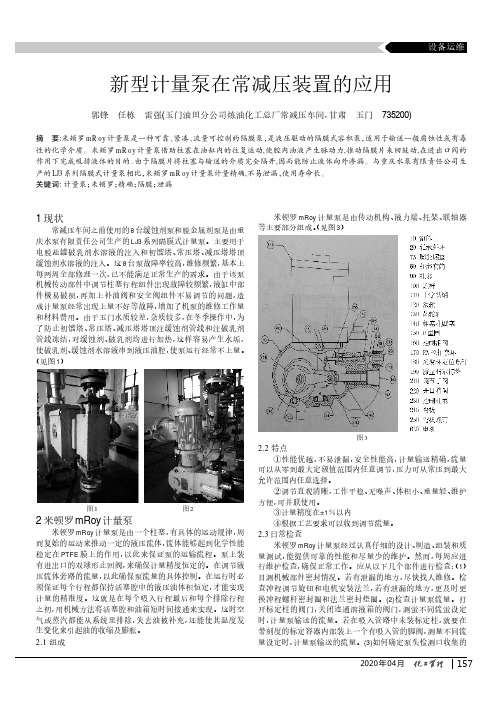
2020年04月新型计量泵在常减压装置的应用郭锋任栋雷强(玉门油田分公司炼油化工总厂常减压车间,甘肃玉门735200)摘要:米顿罗mRoy 计量泵是一种可靠、紧凑、流量可控制的隔膜泵,是液压驱动的隔膜式容积泵,适用于输送一般腐蚀性或有毒性的化学介质。
米顿罗mRoy 计量泵借助柱塞在油缸内的往复运动,使腔内油液产生脉动力,推动隔膜片来回鼓动,在进出口阀的作用下完成吸排液体的目的.由于隔膜片将柱塞与输送的介质完全隔开,因而能防止液体向外渗漏。
与重庆水泵有限责任公司生产的LJ3系列隔膜式计量泵相比,米顿罗mRoy 计量泵计量精确,不易泄漏,使用寿命长。
关键词:计量泵;米顿罗;精确;隔膜;泄漏1现状常减压车间之前使用的8台缓蚀剂泵和脱金属剂泵是由重庆水泵有限责任公司生产的LJ3系列隔膜式计量泵。
主要用于电脱盐罐破乳剂水溶液的注入和初馏塔、常压塔、减压塔塔顶缓蚀剂水溶液的注入。
这8台泵故障率较高,维修频繁,基本上每两周全部修理一次,已不能满足正常生产的需求。
由于该泵机械传动部件中调节柱塞行程组件出现故障较频繁,液缸中部件极易破损,再加上补油阀和安全阀组件不易调节的问题,造成计量泵经常出现上量不好等故障,增加了机泵的维修工作量和材料费用。
由于玉门水质较差,杂质较多,在冬季操作中,为了防止初馏塔、常压塔、减压塔塔顶注缓蚀剂管线和注破乳剂管线冻结,对缓蚀剂、破乳剂均进行加热,这样容易产生水垢,使破乳剂、缓蚀剂水溶液串到液压油腔,使泵运行经常不上量。
(见图1)图1图22米顿罗mRoy 计量泵米顿罗mRoy 计量泵是由一个柱塞,有具体的运动规律,周而复始的运动来推动一定的液压流体,流体能够起到化学性能稳定在PTFE 膜上的作用,以此来保证泵的运输流程。
泵上装有进出口的双球形止回阀,来确保计量精度恒定的。
在调节液压流体旁路的流量,以此确保泵流量的具体控制。
在运行时必须保证每个行程都保持活塞腔中的液压油体积恒定,才能实现计量的精准度。
炼油常减压装置特点及节能新技术

炼油常减压装置特点及节能新技术摘要:常减压装置能够回收余热、降低过剩空气系数,本文对如何控制常减压装置的能耗展开研究,分析常减压装置的特性,然后分析当前可以采取的技术措施。
通过研究帮助工厂解决常减压装置的运行能耗问题,提升综合效益。
关键词:常减压装置;特点;技术;应用引言:现代炼油厂为了保证工作的顺利进行,会使用常减压装置开展工作。
但是常减压装置同样有耗能较大的问题,为了保证生产的顺利进行,需要使用有效的技术,控制常减压装置的能耗。
1炼油常减压装置特性分析1.1加强烟气余热回收使用常减压装置能够回收炼油厂的烟气余热,常减压装置的余热回收系统会包括高温段空气预热器、低温段空气预热器两种装置,在高温段使用了高效的导热元件是,低温段使用双向板翅预热器[1]。
通过使用这些装置,常减压装置能够有效控制烟气余热所导致的露点腐蚀问题,控制烟气温度在130℃的安全范围以内。
通过使用常减压装置,其中的余热回收系统可以有效利用炼油系统的余热,解决温度浪费问题,并降低炼油系统的能耗临。
目前一般使用冷凝技术进行烟气的低温余热回收,可以有效提升热炉的热反应效率。
1.2减少过剩空气炼油厂工作中,如果剩余的空气系数比较小,加热炉内部的燃烧就会缺少足够的空气,很难满足加热炼油的要求,不仅会造成工作效率降低,还会释放出比较多的废物,对环境造成比较严重的损害。
但是如果盲目提升空气系数,过剩的空气就会将炉内多余的热量带走,同样会导致炼油设备热强度不能达标的问题,还会严重影响系统的热传递效率,也会缩短锅炉的使用寿命,以及造成空气污染。
为了解决上述问题,在目前的炼油工作中会使用常减压设备将空气系数控制在合理的范围内。
工作人员在点燃火嘴含氧量会比较高,常减压设备也会同时对气压进行调节,让设备的火焰能始终处于燃烧的状态下,并保证锅炉温度保持正常,工作人员通过随时控制常减压设备可以进行工作方式的调节,让炉内的空气系数保持最佳的运行状态。
1.3能源消耗大在目前的炼油厂生产中,常减压设备的装置会占据比较大的能源消耗,普遍超过了30%,在很多炼油厂重,常减压设备已经成为了最为主要的生产成本要素。
浅谈绕管换热器在常减压装置创新应用

设备运维减速器异常如漏油、磨损甚至停止运转;机械密封失效;罐体掉瓷。
减少、消除减速器故障的最有效办法就是做好润滑工作。
定点、定时、定量、定质、定人进行润滑仍然是最常见最有效的润滑管理模式。
对于机械密封,保持密封油盒洁净、油面稳定是延长机械密封寿命的最简单有效的方式。
目前也出现了无油润滑的干磨式机械密封。
更换反应釜机械密封是一个危险而工作量又大的维修活动,因此,在建立装置时就要重视维修设计,不用拆卸减速器及搅拌轴、人员不进入反应釜内即可更换机械密封。
搪瓷反应釜一旦掉瓷,尤其是反应釜下封头及罐体掉瓷,反应釜将无法继续使用。
引起掉瓷的原因除制造缺陷外,大多数情况下是异物撞击瓷面及冷热交替冲击;如给反应釜内投料时固体物料中混有石头、铁块等坚硬的异物击打瓷面;在给反应釜内升温或者降温时急冷或者快速升温。
因此避免物料中混入大块坚硬异物,精细操作,反应釜缓慢降温或者缓慢升温均是避免反应釜掉瓷的有效办法。
4.2离心分离设备的维修技术离心机是化工新行业使用广泛而价值较高的设备,其主要故障为主轴承轴封系统失效,机组振动超过允许值,安全联锁装置失效。
离心泵是化工行业最常见的机械设备之一,离心泵运行过程中常见的故障主要有设备抽空、泵不打量、轴承温度过高、泵体振动大、密封泄漏。
主要的处理方法为调节润滑油量、更换合适间隙的轴承、更换清洁的润滑油,去除机械杂质;泵体振动过大可能的原因为电动机与泵轴不同心、泵抽空、基础不牢、泵轴弯曲、轴承损坏或间隙过大。
主要的解决方法为对联轴器重新进行找正、加固基础、校正或更换泵轴、更换轴承、调整轴承间隙等;密封泄漏过大主要原因有填料磨损严重、轴或轴套磨损、动静环划伤或间隙不合适、弹簧压缩量不合适。
主要处理的方法有修复或更换动静环、调整弹簧压缩量等。
4.3静止设备的维修技术静止设备主要包括反应器、塔、换热器、储罐等。
静止设备的故障主要包括跑、冒、滴、漏以及设备腐蚀、压力容器的失效等情况。
静止设备主要通过日常巡检、定期检测缺陷、设备壁厚定期测量等方法进行维修保养。
先进控制技术在常减压装置上的开发与应用

夕 ) C (一 ) ∑c u —) ( ( = A p+ A B( f 5 k )
i =1
根据 输 出预测 值 再计 算 多变 量 预 测控 制 系统 的最 优控 制律 。
23 1 先 进 过 程 控 制软 件 应 用 介 绍 。.
S el h l 多变 量 优 化控 制器 (MOC 是 壳牌 全 球解 决 S p )
2 3 多变 量模 型预 测 控 制 .
上世 纪 8 0年 代以来 , S系统得 到了广泛应 用 , D 但
灰 箱 模 型 将 过 程 与 模 型 之 间 的 失 配 包 含 在 内 , 高 了控 提
制 器 的 鲁棒性 。在 控制 器 中引入 状 态变 量 来改 善对 大
《 动 技 与应 21 年 0 第5 自 化 术 用 0 1 第3 卷 期
工 业 控 制I 应 用 与
n s r on r l d Ap ia i n du ty C to an pl to s c
时 滞 过 程 的 预 测 精 度 。 例 如 , 常 压 塔 的 产 品 组 成 的 改 在 变 往 往 会 滞 后 于 塔 顶 灵 敏 板 的 温 度 。 使 用 灵 敏 板 温 度
流量的 影响耦 合严 重 , 常 波动较 大 。 通
x k+l =Ax k 4Bu k ( 、 ()- () ) 足 =C ( ) , ) x k (
其 中 : ∈ , e , ET, e y U I'A , e B , e C
() 1
,
不失一般性 , 假设矩 阵 是列满秩 的 , rn B m; 即 a k = 矩阵
2 1 工 艺 特 点
本装置 主要 由电脱盐 系统 、初 馏和常压 系统 、航煤
减压深拔技术在常减压蒸馏装置上的应用

减压深拔技术在常减压蒸馏装置上的应用
减压深拔技术是指在常减压蒸馏装置中,通过在蒸馏过程中采取一系列的措施,减少
或排除对组分塔底部的推动力,以达到减小深拔浸出塔对底部塔板气液分布状态影响的目的。
常减压蒸馏装置是一种在一定条件下进行分馏的设备,它可根据不同组分的沸点差异,将混合物中的各个组分分离出来。
在常减压蒸馏装置中,底部塔板的气液分布状态会受到
深拔浸出塔的推动力的影响,造成气液分布不均匀,严重时可能导致组分的“垫底”现象,即轻组分在塔底集聚,重组分在塔顶集聚,使得分馏效果下降,生产成本增加。
为了解决这个问题,减压深拔技术应运而生。
减压深拔技术主要包括以下方面的应
用:
1. 更换深拔浸出塔结构:采用新型的深拔浸出塔结构,如配置高效的减压深拔浸出
塔板或板栅等,在一定程度上减小对底部塔板气液分布状态的影响,提高分馏的效果。
2. 优化操作条件:通过控制塔底回流液量、塔顶蒸汽流量等操作参数,使得塔底塔
顶的液相质量更均匀,减小分馏过程中组分的集聚现象。
3. 引入额外的混合物进料点:在常减压蒸馏装置中,引入额外的混合物进料点,将
一部分混合物在塔底而非塔顶注入,调节塔内的气液分布,改善深拔浸出塔对底部塔板的
推动力,提高分馏效果。
减压深拔技术的应用可以有效地改善常减压蒸馏装置的分馏效果,降低生产成本。
它
不仅适用于石油化工行业,还可以应用于化工领域的其他分馏装置,如煤化工、精细化工等。
未来,减压深拔技术还有很大的发展空间,可以通过改进装置结构、调节操作参数等
方式,进一步提高分馏的效果,降低能耗,实现更加可持续发展的目标。
2024年炼油常减压装置中减压塔技术优化

2024年炼油常减压装置中减压塔技术优化减压塔是炼油常用的一种设备,用于降低石油产品中的压力和温度,将过热蒸汽或气体转化为液体。
随着炼油工艺的不断发展和炼油设备的不断升级,减压塔的技术也需要不断优化,以提高效率、降低能耗和减少对环境的影响。
2024年炼油常减压装置中减压塔技术优化主要包括以下几个方面:材料选择、结构设计、流动动力学分析、操作参数优化、节能降耗与环保措施等。
一、材料选择减压塔材料的选择直接影响到其使用寿命和安全性能。
2024年,炼油常减压装置中的减压塔可以采用更先进的高强度、高温抗腐蚀材料,如高温合金、镍基合金等。
这些材料具有良好的抗腐蚀性能和高温稳定性,可以有效延长减压塔的使用寿命,并提高设备的安全性。
二、结构设计减压塔的结构设计要考虑到流体动力学和传热性能等因素。
优化的设计可以提高减压塔的传质传热效率,并降低能耗。
结构设计需要考虑到流体的流动状态、流速和压降等参数,通过合理的结构设计可以减小流体的阻力和压降,提高减压塔的流动动力学性能。
三、流动动力学分析流动动力学分析是减压塔优化设计的关键环节。
减压塔内流体的流动状态对传质传热效率和能耗有着直接影响。
可以通过数值模拟等方法,研究减压塔内流体的流动规律,优化设计减压塔的内部结构和分布组件等,改善流体的分布和流动状态,提高传热效率,降低能耗。
四、操作参数优化优化减压塔的操作参数,可以提高减压塔的工艺效率和能源利用率。
操作参数优化主要包括进料压力、温度、流速等参数的优化。
合理的操作参数可以提高减压塔的转化率和产品质量,降低能耗和生产成本。
通过优化操作参数,可以实现能耗和产量的双重优化。
五、节能降耗与环保措施炼油常减压装置中减压塔的技术优化还需要考虑到节能降耗和环保问题。
可以采用一些节能措施,如余热回收、换热器优化设计等,降低能耗。
同时,还可以采用一些环保措施,如废气处理、废水处理等,减少对环境的影响。
技术优化的目标是在提高效率的同时,降低能耗和对环境的影响。
常减压蒸馏装置的节能分析
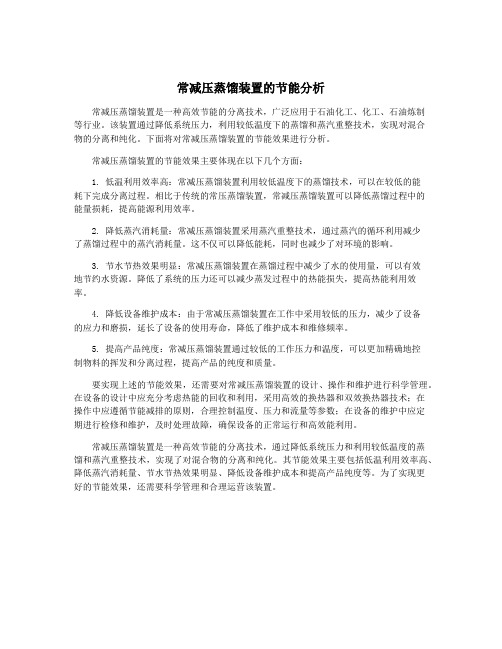
常减压蒸馏装置的节能分析常减压蒸馏装置是一种高效节能的分离技术,广泛应用于石油化工、化工、石油炼制等行业。
该装置通过降低系统压力,利用较低温度下的蒸馏和蒸汽重整技术,实现对混合物的分离和纯化。
下面将对常减压蒸馏装置的节能效果进行分析。
常减压蒸馏装置的节能效果主要体现在以下几个方面:1. 低温利用效率高:常减压蒸馏装置利用较低温度下的蒸馏技术,可以在较低的能耗下完成分离过程。
相比于传统的常压蒸馏装置,常减压蒸馏装置可以降低蒸馏过程中的能量损耗,提高能源利用效率。
2. 降低蒸汽消耗量:常减压蒸馏装置采用蒸汽重整技术,通过蒸汽的循环利用减少了蒸馏过程中的蒸汽消耗量。
这不仅可以降低能耗,同时也减少了对环境的影响。
3. 节水节热效果明显:常减压蒸馏装置在蒸馏过程中减少了水的使用量,可以有效地节约水资源。
降低了系统的压力还可以减少蒸发过程中的热能损失,提高热能利用效率。
4. 降低设备维护成本:由于常减压蒸馏装置在工作中采用较低的压力,减少了设备的应力和磨损,延长了设备的使用寿命,降低了维护成本和维修频率。
5. 提高产品纯度:常减压蒸馏装置通过较低的工作压力和温度,可以更加精确地控制物料的挥发和分离过程,提高产品的纯度和质量。
要实现上述的节能效果,还需要对常减压蒸馏装置的设计、操作和维护进行科学管理。
在设备的设计中应充分考虑热能的回收和利用,采用高效的换热器和双效换热器技术;在操作中应遵循节能减排的原则,合理控制温度、压力和流量等参数;在设备的维护中应定期进行检修和维护,及时处理故障,确保设备的正常运行和高效能利用。
常减压蒸馏装置是一种高效节能的分离技术,通过降低系统压力和利用较低温度的蒸馏和蒸汽重整技术,实现了对混合物的分离和纯化。
其节能效果主要包括低温利用效率高、降低蒸汽消耗量、节水节热效果明显、降低设备维护成本和提高产品纯度等。
为了实现更好的节能效果,还需要科学管理和合理运营该装置。
常减压蒸馏新技术

四、减压深拔技术
• 提高常压拔出率,促进减压深拔 • 采用新型填料,减少压降,提高闪蒸段真空度 • 减压炉炉管多次扩径和低速转油线 • 加入活性添加剂,提高减压拔出率 • 控制减压塔底温度,减少裂解气生成 • 改善减压塔闪蒸段分离效果,减少雾沫夹带 图 • 一段净洗和低液量分配,改善深拔蜡油的质量 图 • 减压塔深拔生产重交沥青 切换
环形填料
拉西环 勒辛环
十字环
内螺旋环
开孔环形填料
鲍尔环
共轭环
阶梯环型填料
鞍形填料的发展
弧鞍填料
矩鞍填料
环矩鞍型填料
球形填料的发展
多面球形填料
TRI球形填料
海尔环
麦勒环
返回
波纹板填料
金属板波纹填料
SK型薄壁陶瓷波纹填料
陶瓷规整
格栅型填料组装图
液体分布器
• 液体初始分布对填料塔性能的影响最大, 故液体分配器是最重要的塔内件;
三、低温位热的回收利用
问题的提出: • 低温位热源来自两个方面:
– 高温位热源经过多次换热,最终变成低温位 热源
– 直接来自温度不高的塔内馏出的轻质油
• 轻质原油轻组分多,低温位热源过多, 高温位热源明显不足
三、低温位热的回收利用
• 采取措施: • 原油分多段换热,充分利用低温位热源 • 采用“窄点”技术,优化换热网络 • 采用高效换热器,提高换热效率,如:
压塔回收其中的柴油; • 提高减压塔顶部的分离精度,直接出柴
油。
二、轻烃回收
• 采用初馏塔提压操作来实现回收轻烃
– 可免去气体压缩机,节省投资 – 降低能耗 – 不影响催化裂化• 采用增压机增压的方法回收轻烃
炼油常减压装置特点及节能新技术
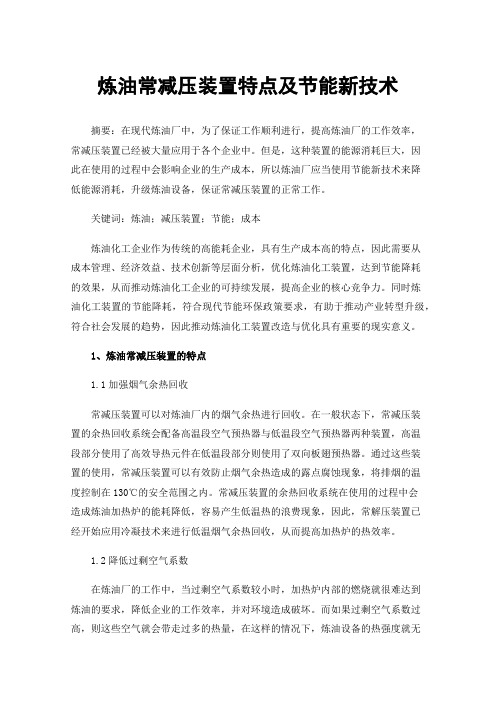
炼油常减压装置特点及节能新技术摘要:在现代炼油厂中,为了保证工作顺利进行,提高炼油厂的工作效率,常减压装置已经被大量应用于各个企业中。
但是,这种装置的能源消耗巨大,因此在使用的过程中会影响企业的生产成本,所以炼油厂应当使用节能新技术来降低能源消耗,升级炼油设备,保证常减压装置的正常工作。
关键词:炼油;减压装置;节能;成本炼油化工企业作为传统的高能耗企业,具有生产成本高的特点,因此需要从成本管理、经济效益、技术创新等层面分析,优化炼油化工装置,达到节能降耗的效果,从而推动炼油化工企业的可持续发展,提高企业的核心竞争力。
同时炼油化工装置的节能降耗,符合现代节能环保政策要求,有助于推动产业转型升级,符合社会发展的趋势,因此推动炼油化工装置改造与优化具有重要的现实意义。
1、炼油常减压装置的特点1.1加强烟气余热回收常减压装置可以对炼油厂内的烟气余热进行回收。
在一般状态下,常减压装置的余热回收系统会配备高温段空气预热器与低温段空气预热器两种装置,高温段部分使用了高效导热元件在低温段部分则使用了双向板翅预热器。
通过这些装置的使用,常减压装置可以有效防止烟气余热造成的露点腐蚀现象,将排烟的温度控制在130℃的安全范围之内。
常减压装置的余热回收系统在使用的过程中会造成炼油加热炉的能耗降低,容易产生低温热的浪费现象,因此,常解压装置已经开始应用冷凝技术来进行低温烟气余热回收,从而提高加热炉的热效率。
1.2降低过剩空气系数在炼油厂的工作中,当过剩空气系数较小时,加热炉内部的燃烧就很难达到炼油的要求,降低企业的工作效率,并对环境造成破坏。
而如果过剩空气系数过高,则这些空气就会带走过多的热量,在这样的情况下,炼油设备的热强度就无法达标,影响传热效率,并且容易缩短炉管的使用寿命,并污染空气。
在炼油厂的实际工作中,常减压设备的使用可以降低过剩空气系数,使空气系数控制在规定范围之内。
工作人员在点燃火嘴时含氧量会提高,而常减压设备则会进行适当调节气压,使设备中的火焰即保持在始终燃烧的状态,又能保证炉温的正常,工作人员通过随时操控常减压设备进行调节工作,可以使空气系数始终保持在最佳状态。
炼油厂常减压装置节能新技术措施分析

炼油厂常减压装置节能新技术措施分析炼油厂常减压装置是炼油过程中重要的装置之一,它主要用于将高温高压的油气降压并冷却,以保证炼油过程的安全性和稳定性。
常减压装置的运行消耗大量的能源,造成能源浪费和环境污染,因此需要采取节能措施来降低能源消耗。
1. 优化常减压装置的结构:通过改变常减压装置的结构设计,减少局部压降,提高设备的能效。
可以采用多级联合减压的形式,将原来的单级减压改为多级减压,减少单级减压过程中的能量损失。
2. 提高常减压装置的传热效率:常减压装置中的传热过程是能源消耗的重要环节。
可以采用增加传热面积的方法,如增加传热管束数量或采用表面增强传热技术,提高传热效率,减少能源消耗。
3. 优化常减压装置的操作方式:通过优化常减压装置的操作方式,减少能源的消耗。
可以采用变压降操作策略,根据炼油过程中油气的压力变化,调整减压装置的压降,以最低的能量消耗实现安全的减压。
4. 应用先进的控制技术:采用现代化的控制系统和自动化技术,实现常减压装置的精细化控制和优化操作。
通过精确控制常减压装置的压力、温度等参数,提高设备的运行效率,减少能源浪费。
5. 温度回收利用技术:常减压装置中的冷凝器常常需要大量的冷却水,造成能源的浪费。
可以采用温度回收利用技术,将冷凝器排出的高温水回收利用,用于其他工艺环节或生活热水供应,减少能源消耗。
6. 应用节能设备和材料:选择高效节能的设备和材料,如高效换热器、高效节能电机等,减少能源的消耗,提高设备的能效。
在炼油厂常减压装置的节能措施分析中,可以从结构优化、传热效率提高、操作方式优化、控制技术应用、温度回收利用技术以及应用节能设备和材料等多个方面入手,共同促进常减压装置的节能改造,降低能源消耗,提高炼油过程的能效。
某炼化公司常减压装置工艺技术和设备简介
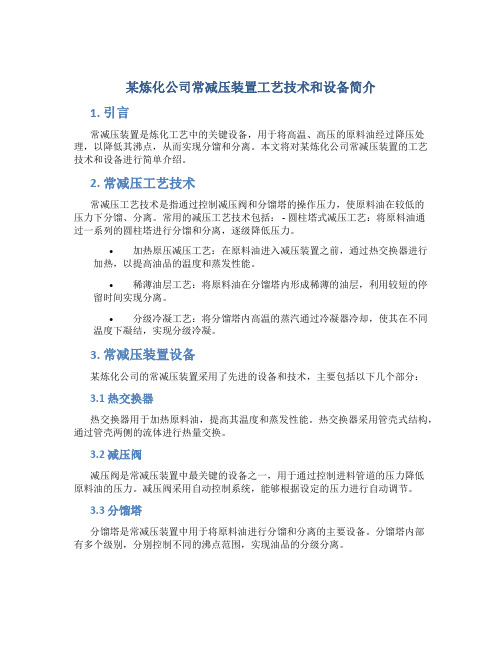
某炼化公司常减压装置工艺技术和设备简介1. 引言常减压装置是炼化工艺中的关键设备,用于将高温、高压的原料油经过降压处理,以降低其沸点,从而实现分馏和分离。
本文将对某炼化公司常减压装置的工艺技术和设备进行简单介绍。
2. 常减压工艺技术常减压工艺技术是指通过控制减压阀和分馏塔的操作压力,使原料油在较低的压力下分馏、分离。
常用的减压工艺技术包括: - 圆柱塔式减压工艺:将原料油通过一系列的圆柱塔进行分馏和分离,逐级降低压力。
•加热原压减压工艺:在原料油进入减压装置之前,通过热交换器进行加热,以提高油品的温度和蒸发性能。
•稀薄油层工艺:将原料油在分馏塔内形成稀薄的油层,利用较短的停留时间实现分离。
•分级冷凝工艺:将分馏塔内高温的蒸汽通过冷凝器冷却,使其在不同温度下凝结,实现分级冷凝。
3. 常减压装置设备某炼化公司的常减压装置采用了先进的设备和技术,主要包括以下几个部分:3.1 热交换器热交换器用于加热原料油,提高其温度和蒸发性能。
热交换器采用管壳式结构,通过管壳两侧的流体进行热量交换。
3.2 减压阀减压阀是常减压装置中最关键的设备之一,用于通过控制进料管道的压力降低原料油的压力。
减压阀采用自动控制系统,能够根据设定的压力进行自动调节。
3.3 分馏塔分馏塔是常减压装置中用于将原料油进行分馏和分离的主要设备。
分馏塔内部有多个级别,分别控制不同的沸点范围,实现油品的分级分离。
3.4 冷凝器冷凝器用于冷却分馏塔内的高温蒸汽,使其凝结成液体,实现分级冷凝。
冷凝器采用板式热交换器结构,通过冷却介质与蒸汽之间的热量交换,实现蒸汽的冷凝。
3.5 废气处理系统常减压装置在分馏过程中会产生大量废气,包含了有害的气体和油气。
废气处理系统主要包括净化塔和废气焚烧炉,用于对废气进行净化和燃烧处理,以降低环境污染。
4. 总结某炼化公司的常减压装置采用先进的工艺技术和设备,能够有效地降低原料油的沸点,实现分馏和分离。
通过控制减压阀和分馏塔的操作压力,使原料油在较低的压力下进行分馏,得到不同沸点范围的油品。
常减压装置新技术介绍

1.7 塔内件
近年来常减压蒸馏系统的主要进步在于新 型或改进塔内部的开发。其发展方向是首先实现 汽液混合(操作条件甚至远在液泛点以上)然后 用辅助设施实现汽液相分离。这样可以大大提高 处理量,脱除以前不能超过液泛点的制约。采用 这一理念,各塔器内部构件供应商相继推出了一 系列专利新产品,据称新型塔板可以提高能力 30%~50%或更多。
常减压装置新技术介绍
主要内容
1、国外蒸馏装置技术现状及发展趋势 2、国内蒸馏装置技术现状
1. 国外蒸馏装置技术现状及发展趋势
1.1 单套蒸馏装置的能力
随着炼厂规模的扩大,单套蒸馏装置的加工规 模也日益大型化。美国ExxonMobil公司贝汤炼油厂 的一套蒸馏装置规模为1300x104t/a常压塔直径9.75 米。
1.3减压渣油的切割点温度和总拔出率
对于不同的原油,减压拔出率的要求和意义是 完全不同的。对于低硫低金属石蜡基原油的燃料型 常减压装置,由于其减压渣油可以全部进入重油催 化裂化装置加工,因此不必追求减压拔出率,甚至 可以不需要减压蒸馏,全部常压渣油都可以直接进 入重油催化裂化装置。对于生产润滑油的常减压装 置,减压拔出率应根据对润滑油的粘度要求和丙烷 脱沥青装置的情况来决定减压拔出率。对于生产道 路沥青的常减压装置,减压拔出率应根据沥青的生 产要求而定。
近几年来,国外蒸馏装置工艺又有了新的 进展。法国的ELF和Technip公司共同开发了一 种次分馏技术,主要将汽,煤,柴油等各种产 品逐渐进行分离,从而降低工艺总用能,可以 降低能耗30%左右。
壳牌石油公司提出的整体蒸馏装置(Shell Bulk Distillation Unit),将原油蒸馏装置,加氢脱硫装置, 高真空减压蒸馏装置和减粘装置作为一个整体加以 优化。整体分馏装置将原油分为:常压渣油,含蜡 馏分油,中间馏分油和石脑油组分。常压部分分出 常压渣油,中间馏分和石脑油以下的馏分。中间馏 分在加氢分馏脱硫塔中分离为煤油,轻,重柴油, 常压渣油进入高真空减压蒸馏,分馏出的蜡油作为 催化裂化装置和加氢裂化装置的原料。整体整流装 置可以节省投资的30%左右。
石油炼制中常减压装置的节能分析

石油炼制中常减压装置的节能分析石油炼制过程中,炼油塔通常会采用常减压装置。
该装置能够实现有效的蒸汽排放和溶剂回收,在生产过程中具有非常重要的作用。
然而,常减压装置的大量蒸汽排放不仅浪费了能源资源,同时还对环境造成了污染。
因此,为了提高石油炼制生产过程的能效,减少能源的消耗和环境污染,需要对常减压装置进行节能分析。
1、技术方面升级技术:在现有的萃取塔中安装冷凝回收装置,将从排气管道中引出的温度高达90°的热蒸汽冷凝回收,然后再送回原系统作为回收溶剂使用。
这样可有效地减少蒸汽排放,提高了石油炼制过程的能源利用效率。
改进操作流程:通过改进设备以及操作流程等措施,降低常减压过程中的能耗。
2、管理方面有组织程序的操作:建立和落实那么进行常减压操作的程序和标准化措施,从而保证操作过程的合理性和规范化程度,减少误操作带来的损失。
提高员工技能:通过生产技能培训和考核,加强员工的操作技能,提高工作效率和安全生产水平。
优化管理模式:强制执行科学合理的计划管理模式,定期对设备进行检测和维修保养,减少设备故障率。
3、设备方面优化设备结构:通过改进设备结构和工艺流程,减少热量损失,提高设备的能效。
定期维护保养:通过定期对设备进行维护保养,保证常减压装置的稳定运行和长期使用效果。
定时检测设备运行状态:建立和落实常减压设备的定时检测制度,对重要设备进行状态监测,及时发现问题并解决。
总之,采取有效的技术、企业管理和设备措施,对石油炼制生产过程中的常减压装置进行节能分析是非常必要的。
这不仅能够减少对能源的浪费,还能减少对环境的污染,提高生产效率,降低生产成本,实现可持续发展战略。
常减压装置超声波-电脱盐破乳技术应用

1 项目背景中石油华北石化公司500万吨/年常减压装置加工的原油包括:华北混合油、冀东原油。
电脱盐采用两串两并的方式,合计两级共4个电脱盐罐,采用传统的化学法-破乳剂破乳,脱前原油含盐18mg/L,含水0.3%以上,脱后原油含盐2.6 mg/L,含水0.23%,脱后排水COD、含油超标,对污水场造成极大冲击,不利于环保排放达标。
2 超声波破乳设备作用机理2.1 作用机理超声波在传播过程中产生的机械振动作用,带动原油乳状液的剧烈振动,降低了乳化液界面上的吸附量和乳化液滴的表面张力,削弱了保护膜,从而有利于液珠的聚结。
另一方面,超声波使乳化态的水粒子产生振动,乳化态的水粒子在波腹或波节的出现时间远远大于平衡态,宏观上表现为水粒子向波腹或波节的往复运动,大大增加了乳化液滴间的碰撞几率,促使生成更大直径的水滴,在重力和电场作用下进行沉降,达到油水分离的目的。
2.2 控制原理1)超声波作用区通过副线接入4个脱盐罐入口主线上,每个作用区由2个超声波发生器,共有4个超声波作用区8个超声波发生器,每个电脱盐罐的超声波发生器由该电脱盐罐的3路变压器初级电流平均值控制超声波功率输出。
2)每个发生器均设置手动和自动控制2部分控制,手—自动可切换操作,自动显示控制输出、功率指示,手动显示设定输出、功率指示。
3)对于性质相对稳定的原油,在脱盐罐中含盐含水量的变化可用导电性来表征,因此可用电脱盐罐内的电流变化来表征原油性质的变化。
每个发生器设置可变常数值和可变系数值的设定,其关系式是:输出功率P=常数-系数×电流平均值。
3 研究过程及改造内容3.1 研究过程2014年装置大检修过程中,常减压装置安装了超声波破乳设备,检修后12月运行部同厂家一起投用电脱盐超声波破乳设备,并停注破乳剂,脱后含盐、脱后含水、电脱盐切水含油等指标均达标。
但自2015年1月8日开始,四具电脱盐罐变压器电流开始出现超高跳闸情况,电脱盐切水颜色开始变差,从电脱盐罐检查口检查发现罐内有较多的乳化液,破乳效果不理想,与厂家联系共同调整电脱盐和超声波破乳设备的参数,但效果始终不理想。
石油炼制中常减压装置的节能分析

石油炼制中常减压装置的节能分析石油炼制过程中,常减压装置是一个关键的设备,用于降低原油的压力,使其能够在后续的处理过程中更好地分离和提炼。
常减压装置的操作虽然能够实现石油炼制的需要,但也存在能源浪费和环境污染的问题。
通过对常减压装置的节能分析,可以找到改善措施,减少能源消耗和环境影响。
常减压装置中的节能技术主要有以下几个方面:1. 循环利用能源:常减压装置中的流体经过减压后,产生大量的低温低压废热和废气。
通过对这些废热和废气进行有效利用,可以减少对额外能源的需求。
可以利用废热进行余热回收,用于加热或蒸汽生成。
通过合理设计废气收集和处理系统,减少有害气体的排放。
2. 引入先进技术:常减压装置的设计和运行中,可以采用一些先进的技术,提高能源利用效率。
采用节能型设备,改善设备的传热传质性能,提高设备的热力学效率。
在操作控制方面,可以采用先进的自动化控制系统,实现更加精确的控制,避免能源的浪费。
3. 优化工艺条件:通过优化常减压装置的工艺条件,可以减少能源的消耗。
合理选取工作压力和温度,减少能源的传输损失。
通过合理安排减压阶段,提高石油分馏的效率,减少副产物的形成。
对于不同类型的原油,采取不同的操作策略,以最大限度地保证能源的利用效果。
进行常减压装置的节能分析需要从技术、经济和环境等方面进行综合考虑。
在技术方面,需要综合考虑常减压装置的主要设备、工艺参数和运行条件等因素。
通过对各个环节的分析,确定存在的能源浪费问题,提出改进措施。
对于能源利用率低的设备,可以进行能效改造,提高设备的能源利用效率。
对于操作不当导致的能源浪费问题,可以加强培训和管理,确保操作人员正确使用设备。
在经济方面,需要进行能源消耗成本和改进措施成本的评估。
通过经济分析,确定节能改进措施的经济可行性,为节能技术的推广和应用提供依据。
还需要考虑节能措施对产品质量和生产效率的影响,确保节能措施的实施不会降低工艺效益。
在环境方面,需要评估常减压装置对环境的影响。
新技术在常减压装置中的应用—Agar电脱盐界位控制系统
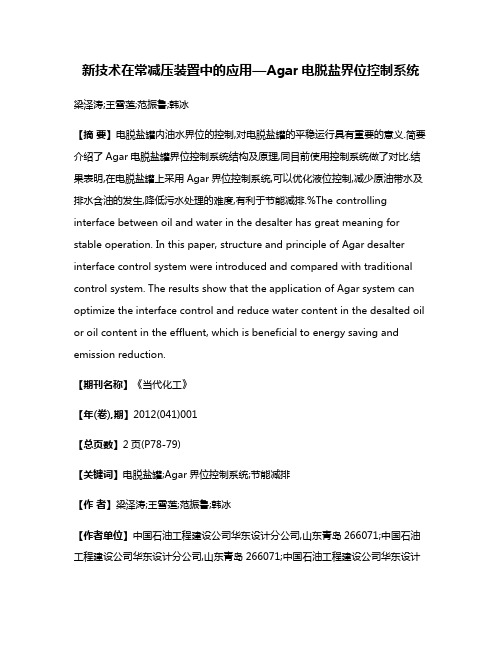
新技术在常减压装置中的应用—Agar电脱盐界位控制系统梁泽涛;王雪莲;范振鲁;韩冰【摘要】电脱盐罐内油水界位的控制,对电脱盐罐的平稳运行具有重要的意义.简要介绍了Agar电脱盐罐界位控制系统结构及原理,同目前使用控制系统做了对比.结果表明,在电脱盐罐上采用Agar界位控制系统,可以优化液位控制,减少原油带水及排水含油的发生,降低污水处理的难度,有利于节能减排.%The controlling interface between oil and water in the desalter has great meaning for stable operation. In this paper, structure and principle of Agar desalter interface control system were introduced and compared with traditional control system. The results show that the application of Agar system can optimize the interface control and reduce water content in the desalted oil or oil content in the effluent, which is beneficial to energy saving and emission reduction.【期刊名称】《当代化工》【年(卷),期】2012(041)001【总页数】2页(P78-79)【关键词】电脱盐罐;Agar界位控制系统;节能减排【作者】梁泽涛;王雪莲;范振鲁;韩冰【作者单位】中国石油工程建设公司华东设计分公司,山东青岛266071;中国石油工程建设公司华东设计分公司,山东青岛266071;中国石油工程建设公司华东设计分公司,山东青岛266071;中国石油工程建设公司华东设计分公司,山东青岛266071【正文语种】中文【中图分类】TE624.1常减压蒸馏装置中电脱盐系统的主要职能是去除原油中的无机氯和其他水溶性化合物。
HYSYSV10在常减压装置上的应用
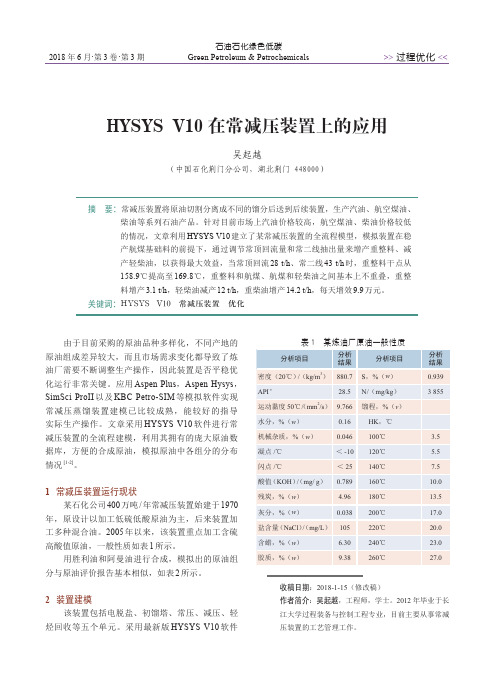
摘 要:常减压装置将原油切割分离成不同的馏分后送到后续装置,生产汽油、航空煤油、柴油等系列石油产品。
针对目前市场上汽油价格较高,航空煤油、柴油价格较低的情况,文章利用HYSYS V10建立了某常减压装置的全流程模型,模拟装置在稳产航煤基础料的前提下,通过调节常顶回流量和常二线抽出量来增产重整料、减产轻柴油,以获得最大效益,当常顶回流28 t/h 、常二线43 t/h 时,重整料干点从158.9℃提高至169.8℃,重整料和航煤、航煤和轻柴油之间基本上不重叠,重整料增产3.1 t/h ,轻柴油减产12 t/h ,重柴油增产14.2 t/h ,每天增效9.9万元。
关键词:HYSYS V10 常减压装置 优化HYSYS V10在常减压装置上的应用吴起越(中国石化荆门分公司,湖北荆门 448000)由于目前采购的原油品种多样化,不同产地的原油组成差异较大,而且市场需求变化都导致了炼油厂需要不断调整生产操作,因此装置是否平稳优化运行非常关键。
应用Aspen Plus ,Aspen Hysys ,SimSci ProII 以及KBC Petro-SIM 等模拟软件实现常减压蒸馏装置建模已比较成熟,能较好的指导 实际生产操作。
文章采用HYSYS V10软件进行常减压装置的全流程建模,利用其拥有的庞大原油数据库,方便的合成原油,模拟原油中各组分的分布 情况[1-2]。
1 常减压装置运行现状某石化公司400万吨/年常减压装置始建于1970年,原设计以加工低硫低酸原油为主,后来装置加工多种混合油。
2005年以来,该装置重点加工含硫高酸值原油,一般性质如表1所示。
用胜利油和阿曼油进行合成,模拟出的原油组分与原油评价报告基本相似,如表2所示。
2 装置建模该装置包括电脱盐、初馏塔、常压、减压、轻烃回收等五个单元。
采用最新版HYSYS V10软件收稿日期:2018-1-15(修改稿)作者简介:吴起越,工程师,学士。
2012年毕业于长江大学过程装备与控制工程专业,目前主要从事常减压装置的工艺管理工作。
100×10 4 t常减压装置节能降耗技改新技术应用

加 热炉 内壁涂 覆高 温红外 复合 液乳 料 , 结后 , 烧 黑度 增 大 , 辐射 热 量效 率 提 高 , 热 系 数小 , 导 可使 炉
外壳 温度 下降 十几度 或几 十度 , 而达到 节能效 果 。 从 1 3 常压炉 采 用两炉 并联 加热工 艺减 少投 资 . 加 热炉 的技 术改 造是关 系 到扩能 降耗 的关键 部
质 区域 由板 面液层 向立 体 空 间发 展 , 即充 分 利 用 两 层塔 板之 间 的空 间 ; 二是 同时 采取 喷射 型状态 操作 , 塔 板 在液相 为 分散 相 、 相 为 连续 相 状 态 下 进行 操 气
12 加 热炉 内壁 采 用涂 覆高 温 红 外 复合 液 乳 料 技 .
作 , 仅大 幅度 提高 了气液 两相 的接触 面积 , 不 而且使
液 滴 的表 面 不 断更 新 , 而 有 利 于 提 高 传 质 效 率 。 因
维普资讯
维普资讯
维普资讯
维普资讯
石 油
3 06
与 天 然 气 化
工
2 07 0
C H EM I L CA EN G I NEERI NG O F O I & G A置 节 能 降耗 技 改新 技 术应 用 0
杨 强 龙 杨 鸣
1 1 新建 加热 炉采 用水热 媒技术 回收余热 .
水 热 媒 空 气 预 热 器 系 统 主 要 由一 台烟 气 换 热
器 、 台空 气 预 热 器 、 台热 水循 环 泵 ( 开 一 备 ) 一 二 一 及 相应 的循 环水 管道 等组 成 , 用 锅 炉 给水 除 氧水 利
多 , 且 采用新 建加 热炉 采用 水热 媒余 热 回收技术 。 并
- 1、下载文档前请自行甄别文档内容的完整性,平台不提供额外的编辑、内容补充、找答案等附加服务。
- 2、"仅部分预览"的文档,不可在线预览部分如存在完整性等问题,可反馈申请退款(可完整预览的文档不适用该条件!)。
- 3、如文档侵犯您的权益,请联系客服反馈,我们会尽快为您处理(人工客服工作时间:9:00-18:30)。
常减压装置新技术的应用
一、国外高速电脱盐技术
1、从技术特点来分电脱盐一般有低速电脱盐和高速电脱盐两种形式。
与低速电脱盐相比,高速电脱盐具有脱盐技术先进、脱盐效率高(单级脱盐率可达95%),单罐处理能力大、电耗低等优点。
该技术为PETROLITE公司九十年代开发的新技术,其主要特点是:
a)进料位置不同于低速电脱盐,不是在水相,而是在电极板之间;
b)进料管不用管式或倒槽式而采用特殊喷头型式;
c)电脱盐罐处理能力不取决于油品在电场中的停留时间,而取决于喷头的能力;
d)采用交流电,水平电极板。
目前世界上已有100多套电脱盐装置采用了该技术,国内镇海炼化、上海石化和齐鲁石化等亦采用了此脱盐技术。
高速电脱盐技术和低速电脱盐技术特点比较见表1-1
表1-1 高速电脱盐技术和低速电脱盐技术特点比较
项目低速电脱盐技术高速电脱盐技术
原油进料位置水相电极板间(油相)
进料部件形式多孔管或倒槽式高效喷头式
供电型式交流或直流电交流电
油在电场中停留时间6min 不要求(很短)
原油处理能力(相同罐体)1(比较基准)2~2.5
一级脱盐率,% 85~90 95
二级脱盐率,% 95~97 99
脱后原油含水,% 0.2 0.2
排水含油,ppm ~200 ~150
电耗,kWh/t原油0.2~0.5 0.03~0.1
投资(相同处理能力)一般略高
2、国内炼厂引进高速电脱盐技术状况见表1-2
表1-2 国内炼油厂引进高速电脱盐技术状况简表
项目镇海炼化Ⅲ常减压上海石化二蒸馏齐鲁石化三蒸馏大连西太平洋
规模800万吨/年350万吨/年400万吨/年1000万吨/年
采用技术高速高速高速高速
技术来源Petreco公司Petreco公司Petreco公司Petreco公司
罐体尺寸Φ3600×17700Φ3600×6000Φ3200×14000Φ4300×29500
罐体新上新上利旧新上
投产时间1998 1999 1999 2003
3、国内高速电脱盐技术
长江(扬中)电脱盐设备公司在吸收消化进口高速电脱盐技术基础上进行改进开发出新一代的交直流高速电脱盐技术,从小试结果来看,与进口的高速电脱盐相比,它具有适应性更广、脱盐脱水效率更稳定等优点,目前已申请国家专利,国内已有高桥、上海石化、茂名、洛阳、金陵、扬子、兰州、镇海、大连、湛江等处理量大于500万吨/年的常减压采用了国产高速电脱盐技术,运行情况尚可。
4、高速电脱盐的适应性
高速电脱盐的进料是喷嘴,所以对粘度较高含杂质的原油要慎用,原油品种变化频繁的装置也要慎用,也就是说、高速电脱盐有一定的适用范围(见镇海发表过的文章)。
二、减压技术
1、全填料干式减压蒸馏
该工艺流程是国外七十年代逐渐发展起来的,其特点是在塔和炉内不注入水蒸汽,通过塔顶采用的三级抽空冷凝冷却系统,使减压塔的进料段和减压炉出口获得较高的真空度,在较低的操作温度下完成相同的减压拔出率。
减压塔内件采用了处理能力高、压力降小、传质传热效率高的新型、高效金属填料(如:规整填料)及相应的液体分布器,有利于提高减压馏分油的收率并降低了装置能耗。
2、大直径低速转油线及减压塔进料分布器
与全填料干式减压蒸馏相适应,发展了大直径低速转油线及新式结构的减压塔进料分布器。
采用大直径低速转油线的主要目的在于进一步降低减压炉出口压力,以获得较高的减压馏分油收率或较低的减压炉出口温度;采用新式结构的进料分布器的主要目的在于提高减压塔进料段的汽液分离效果,减少上升汽体的雾沫夹带量,同时有利于上升汽体的均匀分布提高填料的传热传质效果,改善产品质量。
3、加热炉及减压转油线
采用热管式空气预热器,尽量降低加热炉排烟温度,使加热炉热效率达92%以上。
采用大直径低速转油线及100%炉管吸收转油线热膨胀技术,使减压转油线温降控制在10℃以内。
4、减顶抽真空系统
影响减压拔出率的主要因素有减压塔蒸发层的温度、压力和汽提蒸汽量。
温度提高,减压拔出率提高,生产经验表明:进料段温度每提高10℃,总拔出率可提高2%~4%。
对于燃料型减压塔,由于炉出口的温度受油品热稳定性的限制,一般炉出口温度控制在不大于400~410℃。
进料段的压力降低,在相同的拔出率下,炉出口温度降低,炉负荷减少。
过低的塔顶压力会导致全塔压降的增加,使蒸发层压力的降低不明显,同时还将导致抽空系统能耗的增加。
大连1000万吨/年常减压装置为燃料型,减压的任务是为加氢裂化装置和渣油加氢脱硫装置提供原料,他们综合比较减压塔顶压力与减压炉出口温度和炉负荷的关系,选定减压塔顶压力为20mmHg。
表4-1 减压塔顶压力与抽空器耗量和减压炉负荷的比较
塔顶压力10mmHg 15mmHg 20mmHg 25mmHg 30mmHg
蒸汽耗量,kg/h 27763 22190 17813 16944 16537
蒸汽单耗,×104kcal/t 2.77 2.21 1.78 1.69 1.65
燃料单耗,×104kcal/t 6.35 6.51 6.59 6.67 6.74
总单耗,×104kcal/t 9.12 8.72 8.37 8.36 8.39
节能,×104kcal/t -0.73 -0.33 0.02 0.03 0
减压塔顶采用高效喷射式蒸汽抽真空加机械抽真空混合抽真空系统,在保证减顶真空度的前提下节约能量。
减压塔顶的操作压力设计值为12mmHg(绝)。
减顶抽真空系统目前一般采用水蒸汽抽真空系统,维护工作量小,可靠性高;但对于大型装置,机械抽真空系统愈显出其经济性的优点,节能降耗显著。
青岛1000万吨/年常减压装置减压塔顶采用高效喷射式蒸汽抽真空加机械抽真空混合抽真空系统,与采用全水蒸汽喷射式抽真空系统对比数据如下:混合抽真空方案全部水蒸汽抽真空方案
投资万元人民币+180 基准
水蒸汽耗量:吨/时基准+7.63
电 KW +160 基准
循环水:吨/时+100 基准
软化水:吨/时基准+3.0
折算能耗:千克标准/吨原油:-0.4413 基准
操作费用:万元人民币/年:-337.6632 基准
静态投资回收期:年0.533
由上表可见,采用混合抽真空系统比完全水蒸汽抽真空系统节能0.4413千克标油/吨原油,投资回收期只需0.533年。
5、减压深拔
减压深拔工艺技术目前在国内还未自主开发,少数几个新建的大型常减压装置的减压深拔技术均从国外Shell(壳牌)和KBC二个公司引进。
根据情报调研和技术交流,对这二个公司的减压深拔工艺技术初步了解如下:
壳牌公司的HVU减压蒸馏技术,是在传热段采用空塔喷淋传热技术,将减压塔全塔压降降低,达到更高的拔出率。
此项空塔喷淋传热技术目前也只有壳牌公司可以设计,但该公司对减压深拔后减压炉管内可能生焦,导致危及安全生产及缩短操作周期等工程问题的解决未做深入介绍,只是壳牌公司保证减压炉在430℃左右的出口温度下可连续操作4年以上。
KBC公司的减压深拔的技术核心是对减压炉管内介质流速、汽化点、油膜温度、炉管管壁温度、注汽量(包括炉管注汽和塔底吹汽)等的计算和选取,以防止炉管内结焦,保证四年以上的操作周期和安全生产。
并且该公司对减压塔及其内构件的选取无特殊要求。
通过最近的技术交流和谈判、二家公司的技术特点不同,工艺思路也不一样,技术服务的内容及报价差别更大,各有其适用性。