制冷管路设计规范
制冷5匹压缩机管路设计规范

制冷5匹压缩机管路设计规范一、研究背景随着制冷工业市场的扩大,氨制冷、丙烯制冷、LNG冷剂压缩机的应用变得越来越广泛。
因此其设备布置与管道布置方案就变得日益重要。
本文分析制冷压缩机设备布置、管路布置的方案形成过程及其中可能遇到的问题,对制冷压缩机组的设备布置方案、管路布置方案提供有价值的参考。
二、制冷压缩机及制冷系统的组成及工作原理制冷压缩机主要由进口分离器、压缩机组、气体冷却器、出口冷却器、冷凝器、储罐、过冷器、空气分离器等设备组成,它们之间用管路依次连接起来,形成封闭系统。
制冷剂在系统中不断循环流动,发生状态变化,与外界实现热交换。
其工作过程是:液态冷剂吸收被冷却物的热量后,汽化为低压、低温的气态冷剂,被压缩机吸入,压缩成高压、高温的气态冷剂排入冷凝器,在冷凝器中降热冷凝为高压液态冷剂,经节流阀节流为低压低温的液态冷剂,再进入蒸发器吸热汽化,达到循环制冷的目的。
这样,冷剂在系统中经过蒸发、压缩、冷凝、节流四个基本过程完成一个制冷循环。
该流程可参见附图1。
三、设备布置、管路布置方案制冷压缩机组设备多,且冷剂介质均在一定的危害性,所以设备布置需要充分考虑各设备特点、流程特点,并兼顾管道的安全性,需要将所有因素有机的结合到一起,不能单一考虑每台设备的布置,忽略其完整性。
设备布置方案首先,压缩机组、驱动机形成统一的土建基础,方便吊装、操作与检修,并将该装置与段间气体冷却器、润滑油站、高位油箱放置于厂房内,这样设计是基于以下几点考虑:1、保证核心机组设备相对独立,布置简洁、美观;2、可以减小二层钢平台的承重柱设计,便于设计检修空间和维修通道;3、方便动、静设备基础分开,避免振动;4、便于主管道设计。
制冷系统的管道设计⑴⑵

制冷系统的管道设计⑴⑵制冷系统管道设计包括管径的确定、管道和设备的防腐、保温以及管道的布置问题。
管道设计的好坏,关系到制冷装置运行的安全性、经济性和安装操作的简单方便程度。
通过本章的学习,掌握公式法和图表法确定系统管径以及管材、阀件的正确选用、管道安装布置时需注意的问题。
第一节氨制冷系统管道设计要求(一)对管道、阀件及连接件的一般要求1、管道氨制冷系统的管道应采用无缝钢管。
2、阀门制冷管道系统应采用氨专用阀门,氨系统所用阀类不允许有铜和铜合金的零部件。
阀体应是灰铸铁、可锻铸铁或铸钢的。
其公称压力不应小于2.5Mpa(表压),应有倒关阀座,当阀开足后能在运行中更换材料。
3、连接件氨系统管道一律采用焊接,一般管壁厚度小于4mm者宜用气焊,管壁厚度4mm以上者可用电焊。
(1)弯头一律采用煨弯。
(2)法兰用A3镇静钢制作,应带凸凹口。
(3)两根管子做T形连接时,应作顺流向的弯头。
若两根管子管径相同,则应在结合部位加一段较大的管子,如图7-1 (4)小口径阀门用丝扣连接时,连接管车削螺纹后剩余厚度不小于2.5~3.0mm,应先用一短管与阀门连接后,再与系统管道焊接,丝扣连接时不得使用白油麻丝,应采用纯甘油与黄粉(氧化铅)调和的填料。
(5)支管与集管的连接,支管管头应开弧形叉口与集管平接,不应插入集管内。
一、管道内允许的流速和压降在工程设计中,一般是采用限定管段流动阻力损失来确定对应管径的大小,氨制冷系统的吸气管道的压力损失不宜超过相当蒸发温度降低0.5℃,排气管道的压力损失不宜超过相当冷凝温度升高0.5℃。
二、氨管道布置原则氨与润滑油几乎是不互溶的,因此,在氨制冷系统中,设置氨油分离器,并在可能集油的设备底部装设放油阀,制冷系统中应有放油装置。
(1)吸气管为防止氨液滴进入压缩机,氨压缩机的吸气管应有不小于0.5%的坡度,坡向蒸发器。
(2)排气管为防止润滑油和冷凝液氨回流至压缩机,压缩机的排气管道应有不小于0.01的坡度,坡向油分离器。
汽车空调制冷管路设计要求

绩效评估过程与面谈技巧绩效评估是企业管理中一个非常重要的环节,它可以对员工的工作表现进行系统化的评价。
在评估员工表现时,需要通过特定的流程并运用一定的面谈技巧,确保评估能够精确、公正地进行。
本文将为您介绍绩效评估的过程和面谈技巧,以帮助企业有效评估员工表现。
一、绩效评估的过程1. 设定绩效标准在考核员工时,需要明确的是评估的标准。
因此,企业需要制定明确的绩效标准,以评估员工在各项工作职责和目标上的表现。
这些绩效标准应该是可以量化的,能够反映出真实的工作表现。
2. 收集评估数据在开始评估之前,需要搜集评估数据以了解员工的表现。
这可以通过直接观察、询问同事、参考工作报告和项目成果等方式进行。
这些数据将有助于评估员工在实现公司目标和标准方面的表现状况。
3. 绩效评估当数据搜集完毕之后,需要将数据反映到员工绩效表现中。
在评估过程中,需要认真考察员工是否达到和超越了制定的绩效标准。
如果员工的表现不能满足标准,则需要制定处理方案,并向员工明确未来需要改进的方向。
4. 推动绩效改进绩效评估的主要目的是为了確保员工持续改进工作。
根据评估的结果,需要确定无效措施以及支持员工发展的计划。
推进改进需要依据员工的优势和弱点制订可行的计划以迎接未来的挑战。
二、面谈技巧1. 保持专业态度在面谈中,企业需要保持专业态度,以确保面谈的准确性和公正性。
面谈时,应保持冷静,避免冲动和主观性。
对于任何评估结果和所得出的结论,需要用清晰的语言详细地解释,以便员工能够理解收到的反馈意见。
2. 聆听员工意见在面谈中,需要倾听员工的反馈,以了解员工对自己的看法。
问题是评估过程中最主要的环节之一。
员工可以表达对自己的态度和对领导的看法,以便他们获得针对性的评估。
3. 维持氛围和确保员工信任优秀面谈技巧不仅仅是思想,还涉及管理技巧。
对员工的评估可以增强他们的自我效能感,同时也能让他们对企业更加信任。
因此,面谈时,需要加强员工与公司之间的互动,以维护和谐氛围。
制冷管路设计规范

制冷管路设计规范1.材料选择:制冷管路应选用耐腐蚀、耐高温的材料,如不锈钢、铜、铝等。
材料选择应符合相关国家标准,并考虑到运行环境中可能存在的腐蚀介质。
2.管路布局:制冷管路布局应尽量简短、直接,并且避免过多的弯头和管道连接,以减小压力损失和能量消耗。
同时,管路应合理安装,避免产生应力和振动,以提高制冷系统的运行效率和稳定性。
3.管径选择:管路的直径应根据系统的制冷量、流体压降和流速来确定。
管径过小会增加压力损失,管径过大则会增加制冷剂的填充量和系统的成本。
因此,管径的选择应在满足流体流动要求的前提下尽可能小。
4.管道绝热:制冷管路应进行绝热处理,以减小热量的传递和能量的损失。
常见的绝热材料有聚氨酯泡沫和橡胶泡沫等,应选择合适的厚度和材质来达到预期的绝热效果。
5.清洗和检漏:在制冷管路安装之前,应进行必要的清洗和检漏工作,以确保管路内部的洁净度和密封性。
清洗可以采用化学清洗剂或高压氮气进行,检漏则可使用气态或液态检漏剂进行。
6.安全和环保:在管路设计过程中,需要考虑到系统的安全性和环境保护。
合理设置安全装置,如压力开关、温度传感器等,以保护系统在异常情况下的安全运行。
并注意选用环保的制冷剂和相应的管路材料,以符合相关的环保标准。
7.施工和维护:制冷管路的施工和维护应按照相关的规范和标准进行,确保工作的质量和安全。
施工过程中要注意管道的泄漏和材料的防护,维护则包括定期检查、清洗、更换密封件等,以延长管路的使用寿命和维持系统的性能。
综上所述,制冷管路设计规范是确保制冷系统正常运行和长期稳定性能的重要准则。
通过合适的材料选择、管路布局、管径选择、绝热处理、清洗检漏、安全环保、施工维护等措施,可以提高系统的效率、减少能量消耗,并确保系统的安全运行和环境保护。
制冷机组管路设计
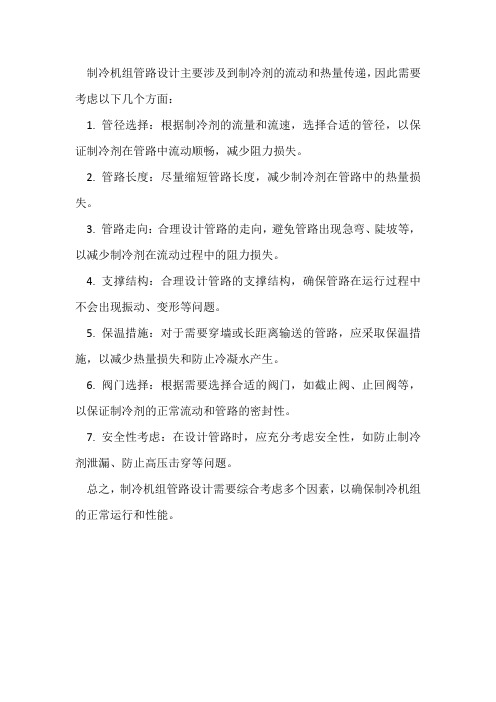
制冷机组管路设计主要涉及到制冷剂的流动和热量传递,因此需要考虑以下几个方面:
1. 管径选择:根据制冷剂的流量和流速,选择合适的管径,以保证制冷剂在管路中流动顺畅,减少阻力损失。
2. 管路长度:尽量缩短管路长度,减少制冷剂在管路中的热量损失。
3. 管路走向:合理设计管路的走向,避免管路出现急弯、陡坡等,以减少制冷剂在流动过程中的阻力损失。
4. 支撑结构:合理设计管路的支撑结构,确保管路在运行过程中不会出现振动、变形等问题。
5. 保温措施:对于需要穿墙或长距离输送的管路,应采取保温措施,以减少热量损失和防止冷凝水产生。
6. 阀门选择:根据需要选择合适的阀门,如截止阀、止回阀等,以保证制冷剂的正常流动和管路的密封性。
7. 安全性考虑:在设计管路时,应充分考虑安全性,如防止制冷剂泄漏、防止高压击穿等问题。
总之,制冷机组管路设计需要综合考虑多个因素,以确保制冷机组的正常运行和性能。
制冷系统中制冷管道的布置要求
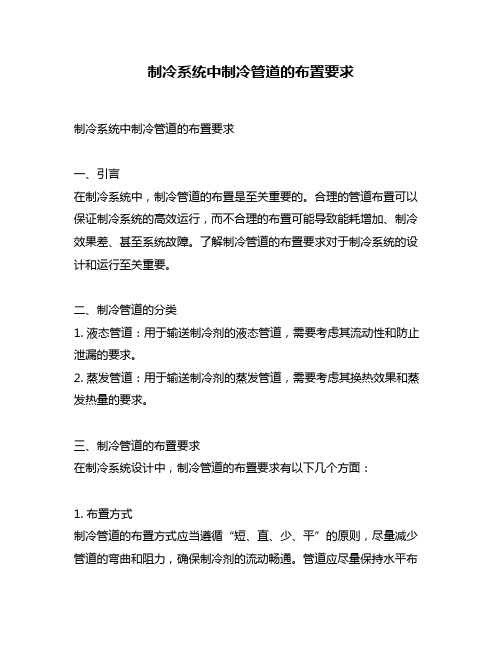
制冷系统中制冷管道的布置要求制冷系统中制冷管道的布置要求一、引言在制冷系统中,制冷管道的布置是至关重要的。
合理的管道布置可以保证制冷系统的高效运行,而不合理的布置可能导致能耗增加、制冷效果差、甚至系统故障。
了解制冷管道的布置要求对于制冷系统的设计和运行至关重要。
二、制冷管道的分类1. 液态管道:用于输送制冷剂的液态管道,需要考虑其流动性和防止泄漏的要求。
2. 蒸发管道:用于输送制冷剂的蒸发管道,需要考虑其换热效果和蒸发热量的要求。
三、制冷管道的布置要求在制冷系统设计中,制冷管道的布置要求有以下几个方面:1. 布置方式制冷管道的布置方式应当遵循“短、直、少、平”的原则,尽量减少管道的弯曲和阻力,确保制冷剂的流动畅通。
管道应尽量保持水平布置,以减少垂直高度对流动的影响。
2. 绝缘材料由于制冷管道中的制冷剂通常为低温液体或气体,因此在设计中需要考虑绝缘材料的选择,以防止制冷管道受到外界环境的影响而出现冻结或结露。
常见的绝缘材料包括聚乙烯、聚丙烯等。
3. 安全防护制冷管道的布置还需要考虑安全防护的要求,保证在系统运行时不会受到外部损害或人员误操作而造成泄漏或故障。
制冷管道应当悬挂在固定的支架上,并且设置好防护罩。
4. 布置的连续性和可维护性为了便于日常维护和检修,制冷管道的布置应当考虑其连续性和可维护性。
管道之间的连接应合理,便于拆卸和更换,以及便于管道的清洗和检修。
四、结论制冷系统中制冷管道的合理布置是确保系统高效运行的关键之一。
在设计和施工中,应当严格遵循布置要求,确保管道的短、直、少、平,选用合适的绝缘材料,设置好安全防护,并考虑布置的连续性和可维护性。
只有这样,制冷系统才能稳定、高效地运行,为人们的生活和工作提供舒适的环境。
个人观点:制冷管道的合理布置对于制冷系统的运行至关重要,尤其在工业和商业领域,更需要严格遵循布置要求,以保证系统的安全性和高效性。
希望随着技术的发展,能够出现更先进、更节能的制冷管道布置技术,为人们的生活和生产带来更多便利和高效。
制冷管路设计规范

制冷管路设计规范
首先,在制冷管路的选择上,应根据制冷工质的性质和工作条件来选
择合适的管材和管径。
对于常见的工质如氨气、氟利昂等,一般使用无缝
钢管或铜管。
对于高温、高压的工况,应选择耐压、耐高温的材料,如不
锈钢管或钛合金管。
其次,在管路的布置上,应尽量减少回弯和弯头的数量,使管路呈直
线或近似直线,并避免锐角。
管路布置应考虑到维修和检修的便利性,确
保操作人员能够方便地接触到各个管道,避免因管路布置不合理而导致维
修困难或操作不便。
在管路连接方面,应采用可靠的连接方式,如焊接、承插连接或夹紧
连接等。
焊接连接应符合相关的焊接标准,确保焊缝的强度和密封性。
承
插连接和夹紧连接应使用高强度的连接件,并进行严格的密封性检测,以
防止漏气现象的发生。
在绝热方面,制冷管路应进行良好的绝热处理,以减少能量损失和提
高系统效率。
常见的绝热材料有聚氨酯泡沫塑料、挤塑聚苯乙烯等,应选
择密度适中、导热系数较低的材料,确保管路的绝热效果。
绝热层应紧密
贴合管道表面,防止冷却剂渗入绝热层,造成绝热效果下降。
此外,制冷管路设计还应符合相关的安全标准和法规要求。
对于高压
管路,应采取必要的安全措施,如设置安全阀等,以确保系统的安全运行。
对于易燃、易爆的工质,应采取相应的防爆措施,如选择适当的管材和使
用防爆电器设备。
综上所述,制冷管路设计规范包括管路的选择、布置、连接、绝热以及符合相关的安全标准和法规要求。
通过合理的设计规范,可以确保制冷系统的正常运行和高效性能。
制冷系统中制冷管道的布置要求

制冷系统中制冷管道的布置要求1.管道长度和直线段:合理控制制冷管道的长度和直线段的数量,可以减少对制冷剂流动的阻力,降低能源损耗。
长的弯头和曲线会增加制冷剂流动的阻力,因此尽量避免使用或减少使用这些结构。
2.管道走向:管道应尽可能直线走向,避免出现大的弯曲和复杂的走向。
这样可以减少流体的阻力,提高制冷效率。
同时,管道也应尽量避免与其他管道和设备的交叉和重叠,以方便维护和清洁。
3.管道直径:根据制冷系统的需求和设计参数,选择合适的管道直径。
如果管道直径过小,会增加流体的阻力,导致制冷效率降低,同时也会增加系统故障的风险。
而管道直径过大,则会增加系统的成本和维护难度。
4.管道支撑和固定:制冷管道应该有足够的支撑和固定,以保证管道的稳定性和安全性。
支撑和固定的位置应该考虑管道的固定点和连接点,避免过度应力和振动。
同时,在管道的弯头、接头和连接处,应使用适当的材料和技术进行加固和密封,以防止管道泄漏和破裂。
5.管道绝缘:制冷管道应进行良好的绝缘处理,以防止制冷剂的温度损失、流体泄漏和系统能量的浪费。
绝缘材料的选择和使用要符合相关标准,并且应具有良好的耐腐蚀性和耐高温性能。
6.管道安全阀和排气阀:制冷管道中应设置相应的安全阀和排气阀,以确保系统的安全运行和维护。
安全阀用于在系统压力过高时释放压力,避免系统爆炸和损坏;排气阀用于排除管道中的空气和非凝汽体,保持制冷系统的正常运行。
7.管道与室外环境的距离:制冷管道在室外布置时,应与周围环境保持一定的距离,以避免受到外部环境的影响。
管道应避免与高温设备、电线、管道和高压部位相邻,以防止因接触而产生热量传导或电导,导致系统故障和安全隐患。
综上所述,制冷系统中制冷管道的布置要求包括管道长度和直线段、管道走向、管道直径、管道支撑和固定、管道绝缘、管道安全阀和排气阀等方面。
通过合理的管道布置,可以提高制冷系统的能效和安全性,延长系统的使用寿命,并降低维护和运行成本。
因此,在制冷系统设计和施工中,要注重管道布置的合理性和科学性,以确保系统的正常运行和高效工作。
制冷管路设计规范
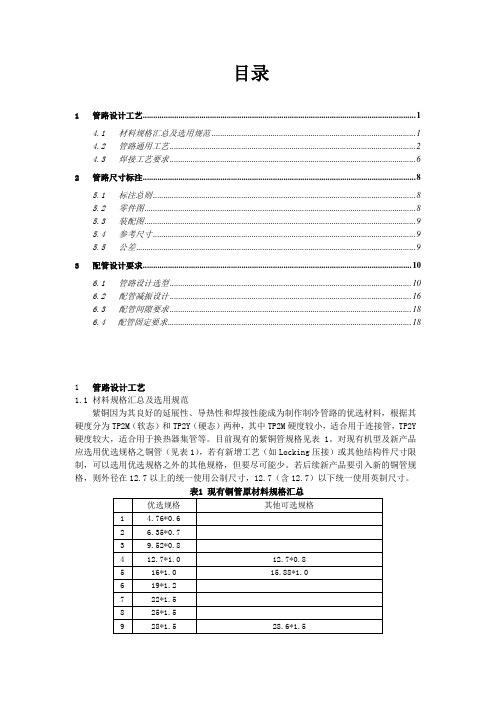
目录1管路设计工艺 (1)4.1材料规格汇总及选用规范 (1)4.2管路通用工艺 (2)4.3焊接工艺要求 (6)2管路尺寸标注 (8)5.1标注总则 (8)5.2零件图 (8)5.3装配图 (9)5.4参考尺寸 (9)5.5公差 (9)3配管设计要求 (10)6.1管路设计选型 (10)6.2配管减振设计 (16)6.3配管间隙要求 (18)6.4 配管固定要求 (18)1管路设计工艺1.1材料规格汇总及选用规范紫铜因为其良好的延展性、导热性和焊接性能成为制作制冷管路的优选材料,根据其硬度分为TP2M(软态)和TP2Y(硬态)两种,其中TP2M硬度较小,适合用于连接管,TP2Y 硬度较大,适合用于换热器集管等。
目前现有的紫铜管规格见表1。
对现有机型及新产品应选用优选规格之铜管(见表1),若有新增工艺(如Locking压接)或其他结构件尺寸限制,可以选用优选规格之外的其他规格,但要尽可能少。
若后续新产品要引入新的铜管规格,则外径在12.7以上的统一使用公制尺寸,12.7(含12.7)以下统一使用英制尺寸。
表1 现有铜管原材料规格汇总1.2管路通用工艺1.2.1折弯管4.2.1.1同一根管的折弯半径应一致,以避免频繁换模。
4.2.1.2原则上可以一次折弯成型的管尽量避免拆成两根管(除非装配需要)。
4.2.1.3折弯设计必须满足折弯端部留有足够的管口直线段长度;各规格的最短直线段长度(不包括弯位的等效长度)不小于其弯管半径。
(见图1)4.2.1.4各种规格的弯管半径见表2,其优选弯曲半径是常用折弯半径,其它弯曲半径工段也可以加工。
4.2.1.5管径在φ45以上(含φ45)的铜管只能加工弯位数不超过2个的平面折弯(即半自动)。
*L为最短直线段长度图11.2.2管端成型4.2.2.1管端成型包括扩口、缩口、打定位点、墩口、锥口、管端封口和管端切弧等(见图2),其中管端封口和切弧为冷冻水大管径的制造工艺。
空调制冷系统管路设计 更新
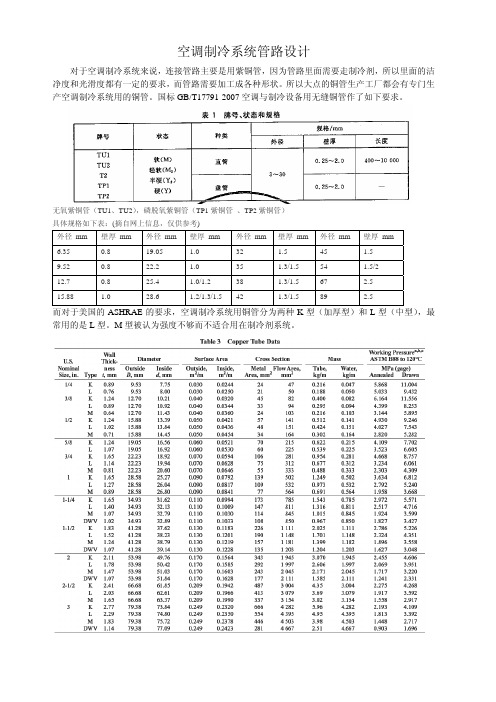
空调制冷系统管路设计对于空调制冷系统来说,连接管路主要是用紫铜管,因为管路里面需要走制冷剂,所以里面的洁净度和光滑度都有一定的要求,而管路需要加工成各种形状。
所以大点的铜管生产工厂都会有专门生产空调制冷系统用的铜管。
国标GB/T17791-2007空调与制冷设备用无缝铜管作了如下要求。
无氧紫铜管(TU1、TU2),磷脱氧紫铜管(TP1紫铜管、TP2紫铜管)具体规格如下表:(摘自网上信息,仅供参考)外径 mm 壁厚 mm 外径 mm 壁厚 mm 外径 mm壁厚 mm外径 mm 壁厚 mm6.35 0.8 19.05 1.0 32 1.5 45 1.59.52 0.8 22.2 1.0 35 1.3/1.5 54 1.5/212.7 0.8 25.4 1.0/1.2 38 1.3/1.5 67 2.515.88 1.0 28.6 1.2/1.3/1.5 42 1.3/1.5 89 2.5而对于美国的ASHRAE的要求,空调制冷系统用铜管分为两种K型(加厚型)和L型(中型),最常用的是L型。
M型被认为强度不够而不适合用在制冷剂系统。
管路设计的基本原则:1.保证供应蒸发器所需的的制冷剂液体,从而保证制冷能力;2.保证制冷剂以最小的压降在系统中流动,以避免产生额外的功率损失;3.保证冷冻油和制冷剂尽量回到压缩机而不会在管路中积存,从而保证压缩机的正常运行;4.防止制冷剂液体和冷冻油不会对压缩机造成冲击;5.管路和制冷剂的合理成本。
管径的选择选择管径时对于不同用途的制冷系统会用不同的考虑,对于舒适性空调,每天的使用时间约为8-18小时,所以比较在意初投资,如果想为了减小压降而过份增大管径,那么无论是管路还是制冷剂充注量的成本都会增加,所以可以在保证回油的及合理的压降的条件下选择成本比较低的方案。
而工业用空调,特别是机房空调,是全年无休运行,所以比较在意运行费用,这时可以考虑在保证回油时制冷效率比较高的方案。
制冷剂管路设计_2

15
压力降要求 3 、从冷凝器至贮液器的液管 , 靠重力 , 流速应小于 0.5m/s 4 、从贮液器至膨胀阀的压力损失 , 压力降也不应过大, 以免引起液态制冷剂管内发生气化 , 造成膨胀阀供液不 足 , 降低系统的制冷能力。
16
(二) 、 回油要求 (1) 回油要求: 向下的吸气管或者水平的 吸气管 , 润滑油靠重力回压缩机 , 上升的立 管的最低回油速度如图:
17
18Βιβλιοθήκη 2 、对于变负荷工作的氟利昂制冷系 统, 为了保证最低负荷时 , 润滑油也能从 蒸发器顺利返回压缩机 , 可采用双上 升吸气立管。
19
三、制冷剂管径计算 1 、损失: 直管的摩擦阻力和管件的局部阻 力 为了方便计算 , 常把各管件的局部阻力系 数折合成当量管长度Ld
20
管道压损计算
fm: 摩擦阻力系数 di; 管道内径 MR: 质量流量 ,Kg/s VR: 制冷剂的比容 ,m3/Kg
12
二、管径的确定 考虑因素: 经济 、压力降 、 回油
13
(一 )、管道的压力降 危害: 压缩机吸气管路和排气管路的 压力损失 , 将引起制冷能力降低和单 位制冷量耗电量增加 , R12为例 , 如表:
14
压力降要求 1、氨系统: 吸气管路和排气管路的压力损失希望 不超过相当于蒸发温度降低0.5度和 冷凝温 度升高 0.5度 2.氟利昂系统: 吸气管路和排气管路的压力损失希望 不超过 相当 于蒸发温度降低1度和冷凝温度升高 1度
4
3 、对不设油分离器的氟利昂压缩机 , 当冷凝器高 于压缩机2.5m以上时 , 在压缩机的排气管路上应该 设置分油环管 , 防止压缩机突然停止运转时 , 较多 的润滑油返回压缩机 , 造成冲缸事故。
制冷系统管路系统设计总原则1
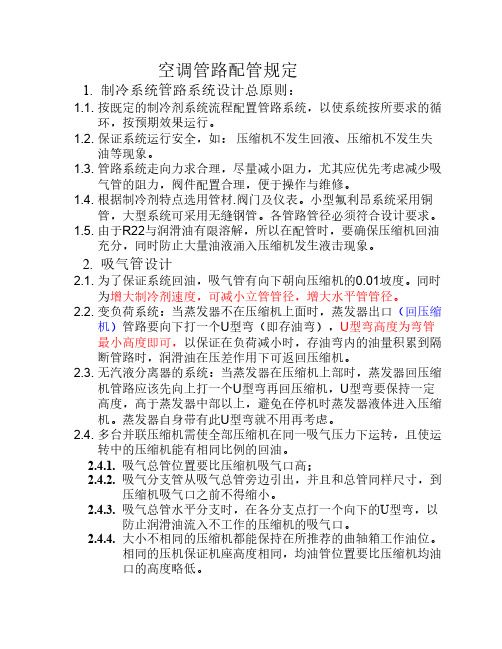
空调管路配管规定1. 制冷系统管路系统设计总原则:1.1. 按既定的制冷剂系统流程配置管路系统,以使系统按所要求的循环,按预期效果运行。
1.2. 保证系统运行安全,如:压缩机不发生回液、压缩机不发生失油等现象。
1.3. 管路系统走向力求合理,尽量减小阻力,尤其应优先考虑减少吸气管的阻力,阀件配置合理,便于操作与维修。
1.4. 根据制冷剂特点选用管材.阀门及仪表。
小型氟利昂系统采用铜管,大型系统可采用无缝钢管。
各管路管径必须符合设计要求。
1.5. 由于R22与润滑油有限溶解,所以在配管时,要确保压缩机回油充分,同时防止大量油液涌入压缩机发生液击现象。
2. 吸气管设计2.1. 为了保证系统回油,吸气管有向下朝向压缩机的0.01坡度。
同时为增大制冷剂速度,可减小立管管径,增大水平管管径。
2.2. 变负荷系统:当蒸发器不在压缩机上面时,蒸发器出口(回压缩机)管路要向下打一个U型弯(即存油弯),U型弯高度为弯管最小高度即可,以保证在负荷减小时,存油弯内的油量积累到隔断管路时,润滑油在压差作用下可返回压缩机。
2.3. 无汽液分离器的系统:当蒸发器在压缩机上部时,蒸发器回压缩机管路应该先向上打一个U型弯再回压缩机,U型弯要保持一定高度,高于蒸发器中部以上,避免在停机时蒸发器液体进入压缩机。
蒸发器自身带有此U型弯就不用再考虑。
2.4. 多台并联压缩机需使全部压缩机在同一吸气压力下运转,且使运转中的压缩机能有相同比例的回油。
2.4.1. 吸气总管位置要比压缩机吸气口高;2.4.2. 吸气分支管从吸气总管旁边引出,并且和总管同样尺寸,到压缩机吸气口之前不得缩小。
2.4.3. 吸气总管水平分支时,在各分支点打一个向下的U型弯,以防止润滑油流入不工作的压缩机的吸气口。
2.4.4. 大小不相同的压缩机都能保持在所推荐的曲轴箱工作油位。
相同的压机保证机座高度相同,均油管位置要比压缩机均油口的高度略低。
2.4.5. 当多台相同型号的压机并联时,吸气管的长度和折弯形式尽量保证一致。
制冷系统管路系统设计总原则1

制冷系统管路系统设计总原则1空调管路配管规定1. 制冷系统管路系统设计总原则:1.1. 按既定的制冷剂系统流程配置管路系统,以使系统按所要求的循环,按预期效果运行。
1.2. 保证系统运行安全,如:压缩机不发生回液、压缩机不发生失油等现象。
1.3. 管路系统走向力求合理,尽量减小阻力,尤其应优先考虑减少吸气管的阻力,阀件配置合理,便于操作与维修。
1.4. 根据制冷剂特点选用管材.阀门及仪表。
小型氟利昂系统采用铜管,大型系统可采用无缝钢管。
各管路管径必须符合设计要求。
1.5. 由于R22与润滑油有限溶解,所以在配管时,要确保压缩机回油充分,同时防止大量油液涌入压缩机发生液击现象。
2. 吸气管设计2.1. 为了保证系统回油,吸气管有向下朝向压缩机的0.01坡度。
同时为增大制冷剂速度,可减小立管管径,增大水平管管径。
2.2. 变负荷系统:当蒸发器不在压缩机上面时,蒸发器出口(回压缩机)管路要向下打一个U型弯(即存油弯),U型弯高度为弯管最小高度即可,以保证在负荷减小时,存油弯内的油量积累到隔断管路时,润滑油在压差作用下可返回压缩机。
2.3. 无汽液分离器的系统:当蒸发器在压缩机上部时,蒸发器回压缩机管路应该先向上打一个U型弯再回压缩机,U型弯要保持一定高度,高于蒸发器中部以上,避免在停机时蒸发器液体进入压缩机。
蒸发器自身带有此U型弯就不用再考虑。
2.4. 多台并联压缩机需使全部压缩机在同一吸气压力下运转,且使运转中的压缩机能有相同比例的回油。
2.4.1. 吸气总管位置要比压缩机吸气口高;2.4.2. 吸气分支管从吸气总管旁边引出,并且和总管同样尺寸,到压缩机吸气口之前不得缩小。
2.4.3. 吸气总管水平分支时,在各分支点打一个向下的U型弯,以防止润滑油流入不工作的压缩机的吸气口。
2.4.4. 大小不相同的压缩机都能保持在所推荐的曲轴箱工作油位。
相同的压机保证机座高度相同,均油管位置要比压缩机均油口的高度略低。
制冷管路设计规范

目录1管路设计工艺51.1材料规格汇总及选用规范 (5)1.2管路通用工艺 (6)1.3焊接工艺要求 (10)2管路尺寸标注122.1标注总则 (12)2.2零件图 (12)2.3装配图 (13)2.4参考尺寸 (13)2.5公差 (13)3配管设计要求143.1管路设计选型 (14)3.2配管减振设计 (22)3.3配管间隙要求 (23)3.4配管固定要求 (24)1 管路设计工艺1.1材料规格汇总及选用规范紫铜因为其良好的延展性、导热性和焊接性能成为制作制冷管路的优选材料,根据其硬度分为TP2M (软态)和TP2Y (硬态)两种,其中TP2M硬度较小,适合用于连接管,TP2Y硬度较大,适合用于换热器集管等。
目前现有的紫铜管规格见表1。
对现有机型及新产品应选用优选规格之铜管(见表1),若有新增工艺(如Locking压接)或其他结构件尺寸限制,可以选用优选规格之外的其他规格,但要尽可能少。
若后续新产品要引入新的铜管规格,则外径在12.7以上的统一使用公制尺寸,12.7(含12.7)以下统一使用英制尺寸。
1.2管路通用工艺1.2.1折弯管1.2.1.1同一根管的折弯半径应一致,以避免频繁换模。
1.2.1.2原则上可以一次折弯成型的管尽量避免拆成两根管(除非装配需要)。
1.2.1.3折弯设计必须满足折弯端部留有足够的管口直线段长度;各规格的最短直线段长度(不包括弯位的等效长度)不小于其弯管半径。
(见图1)1.2.1.4各种规格的弯管半径见表2,其优选弯曲半径是常用折弯半径,其它弯曲半径工段也可以加工。
1.2.1.5管径在e45以上(含@45)的铜管只能加工弯位数不超过2个的平面折弯(即半自动)。
表2各种规格弯管半径汇总图11.2.2管端成型1.2.2.1管端成型包括扩口、缩口、打定位点、墩口、锥口、管端封口和管端切弧等(见图2),其中管端封口和切弧为冷冻水大管径的制造工艺。
1.2.2.2管端成型的设计必须满足焊接的装配间隙和装配长度(参见4.3焊接工艺要求部分)。
制冷剂管路的设计原则

制冷剂管路的设计原则在制冷系统中,制冷剂管路的设计与整个系统的性能、安全性、可靠性以及维护性息息相关。
下面将详细介绍制冷剂管路设计的七个关键原则。
1. 安全性在制冷剂管路设计中,安全性应是最重要的考虑因素。
设计应确保在正常操作条件下,系统能安全运行,同时应考虑到可能的异常情况,如泄漏、压力过高或过低等。
为确保安全,设计时应采取适当的防护措施,如使用安全阀、压力传感器等。
2. 高效性制冷剂管路的设计应追求高效性,以最大限度地提高制冷效率。
设计时,应优化管路结构,减少制冷剂在管路中的流动阻力,降低热交换器的热阻,从而减少系统的能耗。
3. 可靠性制冷剂管路的设计应具有可靠性,确保系统的长期稳定运行。
为此,应选用高质量的管材和配件,并采取防震、防腐等措施,以增强系统的可靠性。
此外,设计时还应考虑到备份和冗余系统,以增强系统的容错能力。
4. 经济性在满足安全、高效和可靠性的前提下,制冷剂管路的设计应考虑经济性。
这可以通过选用性价比高的材料、降低系统的能耗以及优化维护成本等方式实现。
5. 可维护性制冷剂管路的设计应考虑可维护性,以便于系统的安装、调试和维修。
为提高可维护性,设计时应尽量减少管路连接点和附件数量,同时应设置必要的检修空间和通道。
6. 环保性随着人们对环境保护的重视,制冷剂管路的设计也应考虑环保性。
设计时应尽量减少对环境的影响,如选用环保型的制冷剂、减少制冷剂泄漏等。
此外,还应考虑设备的噪音和振动对环境的影响,并采取相应的减噪和减振措施。
7. 标准化制冷剂管路的设计应遵循标准化原则,以利于降低成本、提高生产效率和质量。
在设计过程中,应采用通用的设计规范和标准,以及标准的管材和配件,以实现设计的一致性和互换性。
此外,还应积极推动行业标准的制定和更新,以适应不断发展的制冷技术。
综上所述,制冷剂管路的设计原则包括安全性、高效性、可靠性、经济性、可维护性、环保性和标准化。
在设计过程中,应全面考虑这些因素,并对其进行权衡和优化,以实现一个安全、高效、可靠、经济、环保且具有良好可维护性的制冷系统。
制冷系统管道流速设计规范

油冷却器高压进液管(汇管、支管)
0.2~0.3
油冷却器回气管(汇管、支管)
2~3
开启螺杆压缩机(R717)油管(汇管、支管)
1~1.5
开启螺杆压缩机(R22)油管(汇管、支管)
1~2.5
半封压缩机油管(油量按输气量的0.8%计算)
≤1.0
液体过滤器(有效面积为管道的20倍)
350目
制冷系统管道流速设计Байду номын сангаас范
名称
流速(m/s)
压缩机排气管
≤15
压缩机排气汇管
≤15
冷凝器进气汇管
≤5
冷凝器进气管
≤10
冷凝器出液管
≤0.5
冷凝器出汇管
≤0.5
虹吸罐进、出液管
≤0.5
贮液器进液管
≤0.5
高压向低压输送液体管(汇管、支管)
≤1.0
压缩机排气管、汇管
≤15
蒸发器出气管
≤15
低压分离设备进出气管
- 1、下载文档前请自行甄别文档内容的完整性,平台不提供额外的编辑、内容补充、找答案等附加服务。
- 2、"仅部分预览"的文档,不可在线预览部分如存在完整性等问题,可反馈申请退款(可完整预览的文档不适用该条件!)。
- 3、如文档侵犯您的权益,请联系客服反馈,我们会尽快为您处理(人工客服工作时间:9:00-18:30)。
1目录管路设计工艺 (5)4.14.24.3材料规格汇总及选用规范 (5)管路通用工艺 (6)焊接工艺要求 (10)2管路尺寸标注 (12)5.1 5.2 5.3 5.4 5.5标注总则 (12)零件图 (12)装配图 (13)参考尺寸 (13)公差 (13)3配管设计要求 (14)6.1 6.2 6.3 6.4管路设计选型 (14)配管减振设计 (22)配管间隙要求 (23)配管固定要求 (24)1 管路设计工艺1.1 材料规格汇总及选用规范紫铜因为其良好的延展性、导热性和焊接性能成为制作制冷管路的优选材料,根据其硬度分为TP2M(软态)和TP2Y(硬态)两种,其中TP2M硬度较小,适合用于连接管,TP2Y硬度较大,适合用于换热器集管等。
目前现有的紫铜管规格见表1。
对现有机型及新产品应选用优选规格之铜管(见表1),若有新增工艺(如Locking压接)或其他结构件尺寸限制,可以选用优选规格之外的其他规格,但要尽可能少。
若后续新产品要引入新的铜管规格,则外径在12.7以上的统一使用公制尺寸,12.7(含12.7)以下统一使用英制尺寸。
9 28*1.5 28.6*1.51032*1.51135*1.51238*1.51342*1.51445*1.51554*2.016 76*2.01.2 管路通用工艺1.2.1 折弯管4.2.1.1 同一根管的折弯半径应一致,以避免频繁换模。
4.2.1.2 原则上可以一次折弯成型的管尽量避免拆成两根管(除非装配需要)。
4.2.1.3 折弯设计必须满足折弯端部留有足够的管口直线段长度;各规格的最短直线段长度(不包括弯位的等效长度)不小于其弯管半径。
(见图1)4.2.1.4 各种规格的弯管半径见表2,其优选弯曲半径是常用折弯半径,其它弯曲半径工段也可以加工。
4.2.1.5 管径在φ45以上(含φ45)的铜管只能加工弯位数不超过2个的平面折弯(即半自动)。
铜管规格优选弯曲半径其他弯曲半径备注1 4.76*0.6R10L10R15L20手动2 6.35*0.7R10L10R15L20手动39.52*0.8R15L15R20L20,R30L30数控412.7*1.0R20L20R25L30,R25L20数控516*1.0R30L30R20L30数控619*1.2R25L30R30L30数控722*1.5R30L30R30L25 数控825*1.5R40L40R40L30数控928*1.5R45L45R45L40 数控1032*1.5R50L50数控1135*1.5R50L80数控1238*1.5R60L80半自动1342*1.5R60L80R85L80半自动1445*1.5R70L80半自动1554*2.0R80L100半自动1676*2.0R120L120半自动*L为最短直线段长度图11.2.2 管端成型4.2.2.1 管端成型包括扩口、缩口、打定位点、墩口、锥口、管端封口和管端切弧等(见图2),其中管端封口和切弧为冷冻水大管径的制造工艺。
4.2.2.2 管端成型的设计必须满足焊接的装配间隙和装配长度(参见4.3焊接工艺要求部分)。
4.2.2.3 对于管端不需要扩口或缩口而两管口直接配合的情况,必须标注管口去毛刺后尺寸,以控制管端配合尺寸。
4.2.2.4 ;若设计上对该管口外径尺寸精度有高于通用文件的要求,则必须在图纸上标明尺寸公差。
4.2.2.5 一般情况下,管端扩缩口变径幅度不应超过30%(内径尺寸要折算为外径尺寸计算),如φ16扩19内径,变径幅度为(19+1*2-16)/16=31%,变径太大容易裂口;扩口尺寸一般要求内径尺寸,缩口尺寸一般要求外径尺寸,扩缩口尺寸及长度参考表3中的要求。
图2表3现有管端成型模具规格汇总铜管规格参考长度L扩(缩)口内径(ID)扩(缩)口外径(OD)管端切弧其他成型工艺1 4.76*0.65 6.35墩口*2 6.35*0.77 6.35墩口39.52*0.8104.76,9.52,12.710.6,12.7墩口、锥口412.7*1.01012.7,149.52,10.6,13.7,16锥口516*1.01516,19,2212.7,19,22锥口619*1.2151912.7,16,22722*1.5152219,25,28R15D3*825*1.5152528928*1.5202825,32R17.5D51032*1.5203222(旋压缩口)R18D5管端封口1135*1.52032,33,35,35.51238*1.52038R20D91342*1.520R20D9管端封口1445*1.53028(旋压缩口)管端封口1554*2.03032,38(旋压缩口)R27D15管端封口1676*2.03076R35管端封口*φ4.76墩口长度为4mm,φ6.35和φ9.52墩口长度为5mm*R15D3 表示切弧半径为15mm,切弧深度为3mm1.2.3 钻拔孔4.2.3.1 一般焊接注氟嘴(φ6.35)和平衡管(φ4.76)用的孔使用钻孔工艺,φ9.52以上孔径的为拔孔,拔孔翻边高度不小于2mm(φ35以上不小于5mm),(见图3),具体规格见表4。
4.2.3.2 钻(拔)孔位置须距离铜管弯位和管端(不包含管端成型长度)至少30mm,同时预留加工时的夹模直线段长度;开孔方向最好要与铜管的某条直线段成0°、90°或180°等特殊角度,应尽量避免非特殊角度,如131°。
(见图4)IDL拔孔图3图4表4各种规格铜管钻拔孔规格汇总铜管规格钻拔孔规格1 4.76*0.62 6.35*0.739.52*0.8 4.8,6.4 412.7*1.0 4.8,6.4516*1.0 4.8,6.4619*1.2 4.8,6.4,9.52 722*1.5 4.8,6.4,12.7,16 825*1.5 4.8,6.4928*1.5 4.8,6.4 1032*1.5 4.8,6.4,22,32 1135*1.5 4.8,6.4,22 1238*1.51342*1.5 4.8,6.4,28,42 1445*1.532,4215 54*2.0 32,38,42,541676*2.038*4.8,6.4为钻孔,其他为拔孔1.2.4 定位点1.2.4.1 工段目前可以对12.7(含)以下的铜管打定位点,具体加工能力见表5。
表5各种规格铜管打定位点规格汇总铜管规格钻拔孔规格1 4.76*0.6凸点L≦52 6.35*0.7凸点L≦739.52*0.8凹点、凸点L≦10412.7*1.0凹点、凸点L≦101.3 焊接工艺要求1.3.1 焊接间隙焊接设计间隙一般取0.05~0.15(单边),毛细管焊接间隙取0.1~0.20(单边)。
1.3.2 两管对接插入深度两管轴线同心对接的配合长度(图5)图5设计中两管轴线同心对接的配合长度应优先选用表3《现有管端成型模具规格汇总》中的参考长度L。
1.3.3 两管轴线垂直对接的插入深度(图6)两管轴线垂直对接的插入深度见表5.图6表5两管垂直对接插入深度单位:mm 支管外径Φ10以下Φ12Φ16主管外径Φ124Φ1645Φ19456Φ22456Φ25456Φ28567Φ32577Φ356771.3.4 两管对接限位结构设计两管件对接必须有限位结构设计,以控制插入深度。
可以根据使用情况的不同参考图7 选用,两管轴线垂直对接,除图6中B、C结构外,还可以选择对主管的孔翻边,支管打定位凸包。
图71.3.5 两焊点之间距离两焊点之间的距离过近会影响焊接质量,出现焊漏、焊堵等缺陷。
在设计时应注意区分以下类型结构的焊点,避免焊点距离过近,影响焊接质量。
图8注:图8中,焊点1、2、4、5可在同一工装上一次性配管焊接,L1-2>2A(A为支管直径);3与6需在先焊好焊点4和5之后,再焊3、6。
当A≤12时,L5-6≥40mm;当12<A≤25时,L5-6≥50mm;当25<A<40时,L5-6≥60mm。
1.3.6 结构设计应考虑工人区分零件的极限以下是两端尺寸相近的对称零件,肉眼难以区分,人工配管易出错。
改进1:将数值相近的尺寸通过调整其它尺寸,使其相等。
改进2:将数值相近的尺寸通过调整尺寸,使两尺寸区别放大到肉眼容易区分的范围。
1.3.7 焊料的选择。
根据生产经验,焊料与焊剂的选择如下:1.3.7.1 紫铜与紫铜的焊接,用B Cu88PAg钎料。
1.3.7.2 紫铜与黄铜、钢的焊接推荐使用B Ag45CuZn钎料,钎剂为U型糊状焊剂(硼酸、KF、硼酸盐等)。
1.3.8 焊接符号1.3.8.1 管路组(部)件图纸必须注明焊接符号(氧乙炔焊),如图9所示。
图91.3.9 倒焊1.3.9.1 进行管路设计时,因倒焊焊接容易出现气孔、沙眼、虚焊等质量隐患,要注意尽量避免出现倒焊焊点。
如果不可避免,需要在图纸中注明,要求车间焊接特别注意该点焊接质量。
2 管路尺寸标注2.1 标注总则2.1.1 管路图视图、标注尺寸、注释的格式应符合机械制图国家标准。
2.1.2 管路零部件图的视图和标注尺寸要能够清晰、正确、合理的反映出零部件的结构和功能。
2.1.3 尺寸标注的个数取决于零部件的复杂程度,以工艺上所必需的最少尺寸个数为佳。
2.1.4 除扩缩口尺寸,其余尺寸标注尽量取整数。
图纸上无特殊要求,一般默认的长度单位为“mm”,角度单位为“度”。
2.2 零件图2.2.1 标注应充分考虑设备的加工能力范围,详见以上各节管路加工工艺条件,当有疑问时可以提前和制造部门沟通。
2.2.2 标注应充分考虑管路加工工艺,管路零件标注最好能够直接标注折弯长度和折弯角度的真实尺寸,表达出“折弯长度+折弯角度+折弯长度(+折弯角度……+折弯长度)”的加工顺序。
2.2.3 对于无法直接标注折弯长度和折弯角度的,如蒸发器进出口管、毛细管等,可以使用投影尺寸标注。
2.2.4 垂直方向(指沿铜管轴线方向)的管口尺寸对装配精度影响较大,后续工序调管困难,应直接标注,以利于生产控制。
2.2.5 不适宜直接标注的,应通过同一基准面间接标注2.3 组件图2.3.1 组件图中应直接标注出反映各零件的安装情况、相对位置、配合要求等关键尺寸。
关键尺寸的直接标注,不但有利于生产检验,而且便于保证产品的装配精度。
2.3.2 不适宜直接标注的,应通过同一基准面间接标注。
2.3.3 组件图标注过程中,要选择合理的基准,基准可以是管口尺寸、装配定位尺寸等。
2.3.4 焊接组件中尽可能采用90度直角,无法采用90度时,直接标注焊接角度。
2.4 参考尺寸2.4.1 标注形成封闭尺寸链时,需要把某一不重要的尺寸作为参考尺寸,这样所有尺寸的误差将累计到这个开口环上,不会影响设计要求。