焙烧启动电解槽技术
科技成果——电解槽新型节能焙烧启动技术及自控装置

科技成果——电解槽新型节能焙烧启动技术及自控装置技术开发单位郑州经纬科技实业有限公司适用范围适用于电解铝行业,作为电解铝进入正常生产管理期之前的电解槽焙烧启动。
使用时需电解铝厂有天然气接入,有天然气专用管道。
成果简介该项目创新研制了新型焙烧技术和焙烧装置,以天然气为燃料,将燃烧后的高温烟气通入电解槽进行焙烧,与传统焦粒通电焙烧技术相比:(1)清洁环保,节能降耗:以焙烧启动一台300kA电解槽为例,可平均节电7万kW•h,折合节约标煤约22t,减排CO257t;(2)解决了焙烧不均匀、温差大、阴阳极氧化几率高、电解槽使用寿命短的技术难题;(3)操作简便、自动化程度高,不需铺焦粒、捞碳渣、焊拆分流片等大量繁琐的人工工作,降低了焙烧成本。
技术效果与目前通用的焦粒通电焙烧技术对比,以铝厂应用较多的300kA 电解槽为例,经河南省冶金研究所有限责任公司(具有能源监测资质)现场监测,启动单台槽的平均监测结果对比如下:(1)该技术:平均消耗5700Nm3天然气,折标煤约7t;(2)焦粒通电:平均消耗8.7万kW•h电能及1.6t焦粒,折标煤约29t;(3)节能效果:可节约标煤约22t,减少CO2排放57t。
(注:折标系数:1万Nm3天然气=12.143t标煤,1万kW•h电=3.13t标煤,1t焦粒=0.9714t标煤,1t标煤约排放2.6tCO2)应用情况目前已在25家铝企应用,重复采购整套设备或配件次数达44次,无论是新建槽还是大修槽或事故槽,全部实现100%的焙烧启动成功率,且均运行良好。
4家示范工程:(1)2016年8月,焦作万方铝业500台280kA大修槽重启,节电3250万kW•h,折合CO2减排2.6万t。
(2)2016年7月,山东茌平信源300台660kA新槽启动,节电4620万kW•h,折合CO2减排3.7万t。
(3)2015年3月,辽宁营口忠旺220台500kA新槽启动,节电2574万kW•h,折合CO2减排2万t。
曲面阴极槽焙烧启动方案
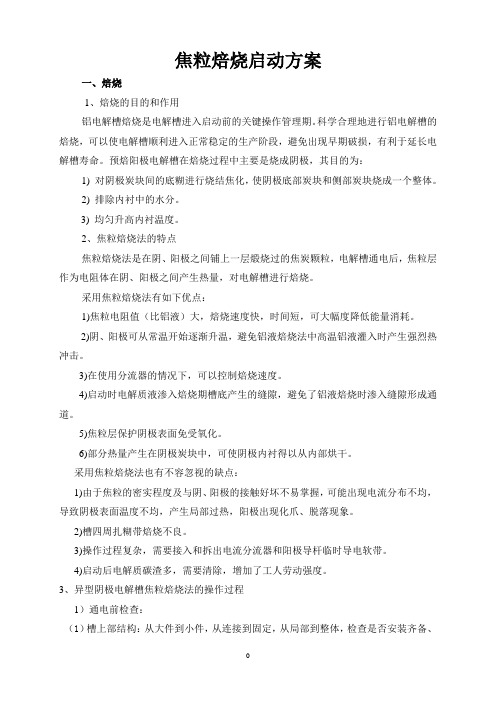
焦粒焙烧启动方案一、焙烧1、焙烧的目的和作用铝电解槽焙烧是电解槽进入启动前的关键操作管理期。
科学合理地进行铝电解槽的焙烧,可以使电解槽顺利进入正常稳定的生产阶段,避免出现早期破损,有利于延长电解槽寿命。
预焙阳极电解槽在焙烧过程中主要是烧成阴极,其目的为:1) 对阴极炭块间的底糊进行烧结焦化,使阴极底部炭块和侧部炭块烧成一个整体。
2) 排除内衬中的水分。
3) 均匀升高内衬温度。
2、焦粒焙烧法的特点焦粒焙烧法是在阴、阳极之间铺上一层煅烧过的焦炭颗粒,电解槽通电后,焦粒层作为电阻体在阴、阳极之间产生热量,对电解槽进行焙烧。
采用焦粒焙烧法有如下优点:1)焦粒电阻值(比铝液)大,焙烧速度快,时间短,可大幅度降低能量消耗。
2)阴、阳极可从常温开始逐渐升温,避免铝液焙烧法中高温铝液灌入时产生强烈热冲击。
3)在使用分流器的情况下,可以控制焙烧速度。
4)启动时电解质液渗入焙烧期槽底产生的缝隙,避免了铝液焙烧时渗入缝隙形成通道。
5)焦粒层保护阴极表面免受氧化。
6)部分热量产生在阴极炭块中,可使阴极内衬得以从内部烘干。
采用焦粒焙烧法也有不容忽视的缺点:1)由于焦粒的密实程度及与阴、阳极的接触好坏不易掌握,可能出现电流分布不均,导致阴极表面温度不均,产生局部过热,阳极出现化爪、脱落现象。
2)槽四周扎糊带焙烧不良。
3)操作过程复杂,需要接入和拆出电流分流器和阳极导杆临时导电软带。
4)启动后电解质碳渣多,需要清除,增加了工人劳动强度。
3、异型阴极电解槽焦粒焙烧法的操作过程1)通电前检查:(1)槽上部结构:从大件到小件,从连接到固定,从局部到整体,检查是否安装齐备、连接是否坚固、到位、有无缺损零部件等,同时检查各运转机构是否灵活、运转是否到位。
(2)槽控机:检查槽控机各控制板、件及附属电气设备是否安装齐全、上、下联机是否通路、控制盘上各种控制按钮是否灵便、制动项目是否有效、显示装置是否清楚无误。
(3)打壳下料系统:检查供风系统是否通畅、有无漏风之处、氧化铝输送系统有无堵塞、跑、冒现象、下料阀安装是否正确、氧化铝下料量是否准确。
400KA电解槽焙烧启动实用技术

抬置 7.0V, 当灌入 21 吨电解质后,电压抬置 8.0~9.0V。
Truck
Direction of bath cruces delivery for bath pouring
1 2
1
1
1
1
1
1
1
1
1
1
2
2
2
2
2
1
2
3
4
5
6
7
8
9
0
1
2
3
4
5
6
7
8
9
0
1
2
3
第 - 10 - 页 共 23 页
4 启动 4.1 启动原则
中部温度达到 900℃以上,边部温度不低于 600℃。 4.2 启动前的准备工作 4.2.1 启动前将所有测温套管、硅酸铝纤维毯全部取出。 4.2.2 将启动槽盒式卡具依次松开再紧一遍,在导杆上重新设线,
记录阳极窜动值。 4.2.3 准备启动所用的工器具、效应杆、槽门式立柱挡板、槽控箱
焦粒 石墨碎
冰晶 比冰晶
铝纸
钙钠组铝
铝
维毯
名称 质块
(吨) (吨)
石石
(m
(吨) (吨) (组) (吨)
(吨)
(m
(吨)
(吨) (吨)
2)
2)
装炉
6
2
1 24
用量
0.9 0.05
14 15 14
启动
3
32
用料
20 15 11
备注:表中液体铝为在产铝量。
主要原材料应满足以下要求: 3.1.1.高分子比冰晶石应符合 GB4291—1999 二级品以上要求。
500kA系列铝电解槽二次焙烧启动技术研究

500kA系列铝电解槽二次焙烧启动技术研究摘要:随着全国用能的紧张形势,国家进行宏观调控,导致部分电解铝企业产能受限停槽,其中一些新系列启动槽面临二次启动问题。
本文结合某企业500kA系列铝电解槽二次启动生产实践从保护性扣槽、补槽、安全平稳启动等进行全面综合论述,提高二次焙烧启动槽的成功率,延长电解槽寿命,降低大修费用,有效降低生产成本。
关键词:500kA;二次启动;焦粒焙烧;大修成本前言某电解铝企业自错峰用电及执行能耗双控政策要求以来,截止10月份共计停槽123台。
2022年年初开始复产,通过采取保护性扣槽、优化焙烧启动方式、严格工艺管控等措施,仅用不到一个月时间就将前59台电解槽全部启动完成,各项经济技术指标良好。
本文结合该企业500kA系列铝电解槽二次启动生产实践从合理地清槽、补槽和焙烧启动等进行全面综合论述,为同类型槽的二次启动起到很好的借鉴作用。
1清槽1.1回收物料(1)待电解槽阴极内衬温度基本降至常温后,开始操作天车开口错位拔极,导杆上标注好剩余周期天数,做好残极“结对子”使用工作。
(2)清理槽内疏松的电解质块、面壳块进行分类装袋并做好标注,要求直径大小不超过30cm。
1.2保护性扣槽(1)待疏松的物料清理完后,使用风镐、板锄、簸箕等工具对槽内物料进行逐层清理,清炉底至阴极表面,中缝及阴极沟槽内沉淀结壳应清出槽。
清理过程中注意不要破坏底部和侧部碳块及人造伸腿。
(2)清理槽底铝块时,从角落位置处“起头”抠出底铝,视铝块大小情况进行分割处理。
(3)清理完物料后,利用刨磨机打磨阴极炭块表面的碳化物,确保阴极表面干净达90%以上,最大限度提升阴极导电性能,降低电解槽冲击电压及启动后炉底压降。
1.3修补(1)用风管吹净,对各部位进行全面检查(有无裂纹、掉块、冲蚀坑等),建立完整的单槽档案,绘制炉底情况示意图,记录好炉底状况,并附图存档,为二次启动提供依据。
(2)阴极裂纹采用石墨碎配合液态碳焦泥进行修补,冲蚀坑及表面破损点用镁砂、氟化钙、水玻璃混合物填补,保证修补后阴极表面平整紧实;侧部碳块根据氧化情况,氧化轻微的地方使用石墨碎配合液态碳焦泥填充,再用气动锤夯实,氧化较宽、较深的使用条状碳块拼接修补(提前量好修补点尺寸),间隙位置填入液态碳焦泥和石墨碎,将整个氧化位置填补饱满、充实。
焙烧启动工艺技术标准
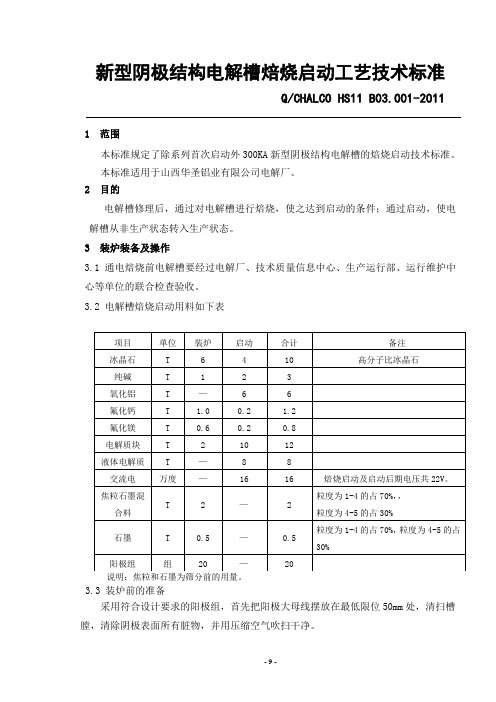
新型阴极结构电解槽焙烧启动工艺技术标准Q/CHALCO HS11 B03.001-20111 范围本标准规定了除系列首次启动外300KA新型阴极结构电解槽的焙烧启动技术标准。
本标准适用于山西华圣铝业有限公司电解厂。
2 目的电解槽修理后,通过对电解槽进行焙烧,使之达到启动的条件;通过启动,使电解槽从非生产状态转入生产状态。
3 装炉装备及操作3.1通电焙烧前电解槽要经过电解厂、技术质量信息中心、生产运行部、运行维护中心等单位的联合检查验收。
3.2 电解槽焙烧启动用料如下表说明:焦粒和石墨为筛分前的用量。
3.3 装炉前的准备采用符合设计要求的阳极组,首先把阳极大母线摆放在最低限位50mm处,清扫槽膛,清除阴极表面所有脏物,并用压缩空气吹扫干净。
3.4 铺设焦粒和挂极铺设前先用石墨将炉底找平,焦粒铺设及阳极的安放自A10、B10开始连续铺设至A1、B1结束,焦粒石墨混合料铺设厚度要求20-25mm,阳极与焦粒的压实面应大于80%,铝导杆和水平母线压接处的缝隙不大于6mm,安放阳极后用纸板封堵极间缝。
3.5 安放热电偶套管在A1-B1、A6-B6、A10-B10阳极中间对应的中缝处及A10、B10角部各装上一支热电偶保护管,热电偶套管斜放,下面封口不得与阴、阳极接触。
3.6 装炉在槽膛四周紧贴阳极的底掌边沿添加60-100mm冰晶石,在人造伸腿上均匀铺上1 T氟化钙,在氟化钙上均匀添加氟化镁0.6 T,紧靠阳极周边均匀添加纯碱1吨,在纯碱上装电解质块2T,要求紧靠侧砖,装到距槽上沿50mm,在电解质块上全部加冰晶石至满槽,阳极组表面冰晶石厚度不低于150mm,中缝添加100-150mm冰晶石,阳极中缝用不小于5mm厚的钢板盖严。
3.7 安装软连接器3.8 分流器的安装装炉结束后进行分流器的安装,末端槽采用钢带分流,钢带一端焊于阳极钢梁上,另一端焊于阴极钢棒处。
4 短路口操作及通电4.1 使用设备、工具、材料不停电开停槽装置、短路口绝缘板、绝缘套管、呆扳手、摇表工器具等。
KA电解槽焦粒焙烧启动方案
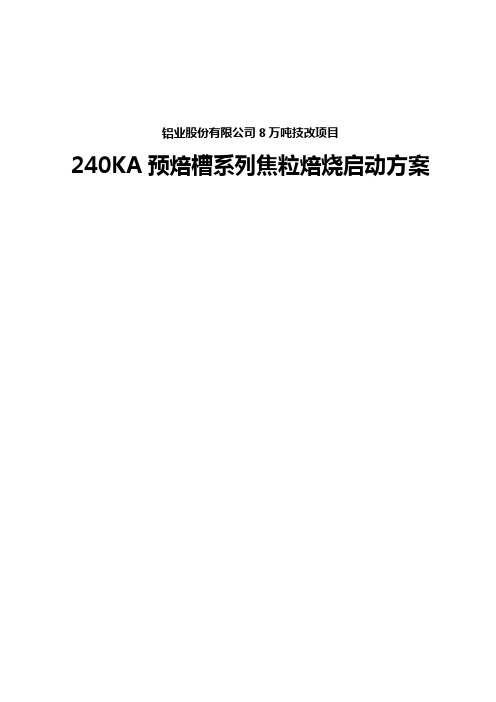
铝业股份有限公司8万吨技改项目240KA预焙槽系列焦粒焙烧启动方案编制单位:铝业股份有限公司公司SY240KA预焙槽系列焙烧启动方案焙烧启动工作是电解槽生产管理中一个重要环节,它不仅关系到铝电解槽能否顺利投产,而且影响生产后期铝电解槽的技术经济指标及槽寿命。
焙烧启动方案是整个系列通电投产的纲领性文件,指导整个系列的焙烧启动工作,是系列投产执行程序的关键。
1、制定目的:为240KA系列电解槽焙烧启动提供技术规范和操作支持,保证系列焙烧启动工作科学、规范进行,安全顺利完成系列电解槽的焙烧启动工作。
2、焙烧启动方案的基本原则1、240KA系列电解槽的焙烧启动采用焦粒焙烧法、干法无效应启动。
2、焙烧分流采用钢带分流法(每组阳极2片,共64片钢带)。
3、240KA预焙槽原则上通电分流焙烧时间为12小时,全电流焙烧108小时,全过程120小时后即可做启动准备工作。
3、通电前准备工作设备验收交付1、整流所需提前10天调试完毕。
2、微机控制系统安装调试需提前10天完成。
3、氧化铝输送系统需提前10天经调试验收合格后交付使用。
4、通电前电解槽必须满足《240KA中间下料预焙槽安装验收技术条件》的要求。
5、电解一、二车间电解槽母线具备通电条件,其中前20台槽需提前10天验收完毕,并交付电解生产。
主要原材料准备240KA电解槽通电焙烧启动原材料需要量:(单槽)对原材料质量要求:1、使用的预焙阳极炭块、氧化铝、氟化盐均为一级品,使用前我厂必须检验,合格后方可使用。
2、煅后石油焦,粒度为1~3mm,其中小于1mm的粉料不大于1%,水分小于%,灰分小于%,粒度均匀。
4、通电焙烧进度1、通电焙烧前5天,人员必须到岗,各种重要物料运至现场,各种测量仪器及操炉工具准备就绪。
2、计划一期通电电解槽70台,通电进度如下:首批通电焙烧槽确定为6台,每个车间各3台;第二批电解槽通电在首批槽通电第三天进行,通电2台,每个车间各1台;以后每1天,每个车间各通电一台槽。
240KA电解槽环流空腔焙烧启动方案设计
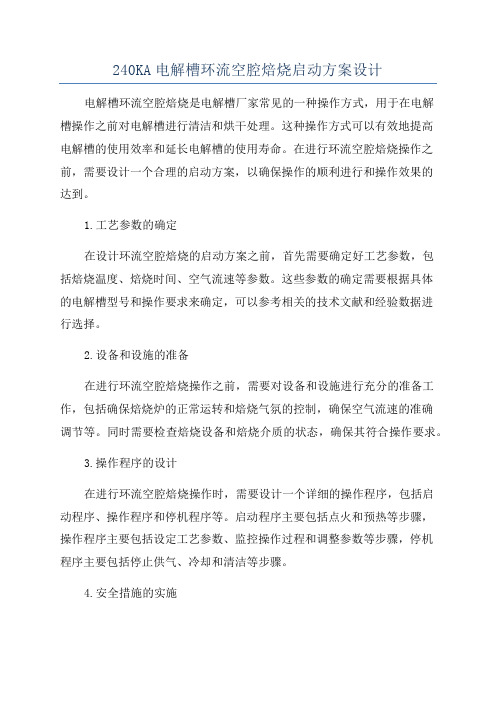
240KA电解槽环流空腔焙烧启动方案设计电解槽环流空腔焙烧是电解槽厂家常见的一种操作方式,用于在电解槽操作之前对电解槽进行清洁和烘干处理。
这种操作方式可以有效地提高电解槽的使用效率和延长电解槽的使用寿命。
在进行环流空腔焙烧操作之前,需要设计一个合理的启动方案,以确保操作的顺利进行和操作效果的达到。
1.工艺参数的确定在设计环流空腔焙烧的启动方案之前,首先需要确定好工艺参数,包括焙烧温度、焙烧时间、空气流速等参数。
这些参数的确定需要根据具体的电解槽型号和操作要求来确定,可以参考相关的技术文献和经验数据进行选择。
2.设备和设施的准备在进行环流空腔焙烧操作之前,需要对设备和设施进行充分的准备工作,包括确保焙烧炉的正常运转和焙烧气氛的控制,确保空气流速的准确调节等。
同时需要检查焙烧设备和焙烧介质的状态,确保其符合操作要求。
3.操作程序的设计在进行环流空腔焙烧操作时,需要设计一个详细的操作程序,包括启动程序、操作程序和停机程序等。
启动程序主要包括点火和预热等步骤,操作程序主要包括设定工艺参数、监控操作过程和调整参数等步骤,停机程序主要包括停止供气、冷却和清洁等步骤。
4.安全措施的实施在进行环流空腔焙烧操作时,需要严格遵守相关的安全规定,确保操作过程的安全性。
需要对焙烧设备和设施进行定期检查和维护,并采取必要的安全措施,如使用防爆设备、佩戴个人防护用具等。
5.参数调控和监控在进行环流空腔焙烧操作时,需要对工艺参数进行实时监控和调控,确保焙烧的效果达到预期。
需要根据操作过程中的实际情况进行参数的调整,如调节焙烧温度、调节空气流速等,以达到最佳的焙烧效果。
总结来说,240KA电解槽环流空腔焙烧启动方案的设计需要充分考虑工艺参数、设备和设施的准备、操作程序的设计、安全措施的实施、参数调控和监控等方面。
只有在这些方面都做到位,才能确保环流空腔焙烧操作的顺利进行和操作效果的达到。
同时还需要不断总结经验,积累操作技巧,以提高操作效率和保障电解槽的使用寿命。
500kA电解槽焙烧启动安全技术操作规程
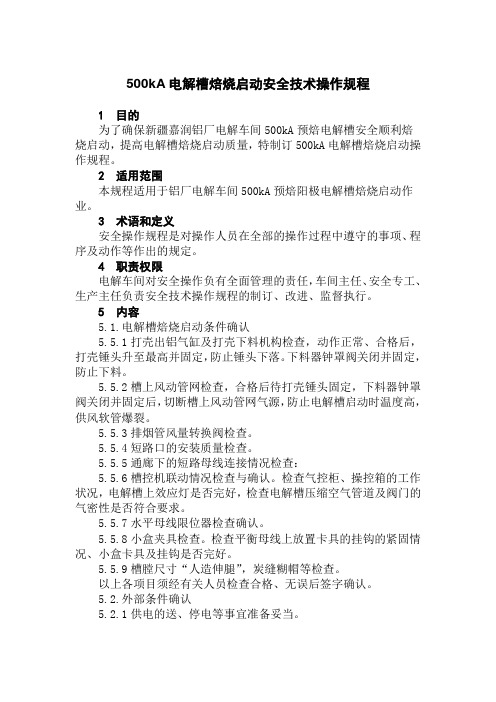
500kA电解槽焙烧启动安全技术操作规程1 目的为了确保新疆嘉润铝厂电解车间500kA预焙电解槽安全顺利焙烧启动,提高电解槽焙烧启动质量,特制订500kA电解槽焙烧启动操作规程。
2 适用范围本规程适用于铝厂电解车间500kA预焙阳极电解槽焙烧启动作业。
3 术语和定义安全操作规程是对操作人员在全部的操作过程中遵守的事项、程序及动作等作出的规定。
4 职责权限电解车间对安全操作负有全面管理的责任,车间主任、安全专工、生产主任负责安全技术操作规程的制订、改进、监督执行。
5 内容5.1.电解槽焙烧启动条件确认5.5.1打壳出铝气缸及打壳下料机构检查,动作正常、合格后,打壳锤头升至最高并固定,防止锤头下落。
下料器钟罩阀关闭并固定,防止下料。
5.5.2槽上风动管网检查,合格后待打壳锤头固定,下料器钟罩阀关闭并固定后,切断槽上风动管网气源,防止电解槽启动时温度高,供风软管爆裂。
5.5.3排烟管风量转换阀检查。
5.5.4短路口的安装质量检查。
5.5.5通廊下的短路母线连接情况检查:5.5.6槽控机联动情况检查与确认。
检查气控柜、操控箱的工作状况,电解槽上效应灯是否完好,检查电解槽压缩空气管道及阀门的气密性是否符合要求。
5.5.7水平母线限位器检查确认。
5.5.8小盒夹具检查。
检查平衡母线上放置卡具的挂钩的紧固情况、小盒卡具及挂钩是否完好。
5.5.9槽膛尺寸“人造伸腿”,炭缝糊帽等检查。
以上各项目须经有关人员检查合格、无误后签字确认。
5.2.外部条件确认5.2.1供电的送、停电等事宜准备妥当。
5.2.2空压站运转正常,气源压力达到要求,空压管路能够正常供风。
5.2.3多功能天车调试合格,其它工艺车辆齐全到位。
5.2.4真空抬包、开口抬包预热。
5.2.5.操作工具齐全(万用表2块、停起槽工具一套、卡具扳手4把、活动扳手4把、焦粒框架1个、分流器一套、电焊机2台、溜槽1个侧壁吹风管两根、小盒卡具48个、阳极炭块48块、短路口保护罩6个、门型立柱保护罩4个等)。
一种500ka新型节能预焙阳极铝电解槽焙烧启动方法

一、引言随着工业化进程的不断推进,铝产业也迎来了飞速发展的时代。
铝的应用范围越来越广,需求量也在不断增加。
作为铝的主要原料之一,预焙阳极铝电解槽在铝生产中扮演着重要的角色。
然而,传统的预焙阳极铝电解槽在启动过程中存在能耗高、效率低的问题。
研究一种500ka新型节能预焙阳极铝电解槽焙烧启动方法显得十分必要和迫切。
二、现状分析1. 传统启动方法存在的问题传统的预焙阳极铝电解槽在启动过程中,通常需要通过大量的能源输入来完成焙烧和预热的过程。
这样不仅费时费力,而且能耗较高,且效率低下。
2. 新型节能预焙阳极铝电解槽的需求随着国家对节能环保政策的不断推进,对铝产业的节能环保要求也越来越高。
研发一种新型的节能预焙阳极铝电解槽焙烧启动方法成为了产业发展的需要。
三、500ka新型节能预焙阳极铝电解槽焙烧启动方法的研究与开发1. 利用先进的加热技术500ka新型节能预焙阳极铝电解槽焙烧启动方法,首先利用了先进的加热技术。
通过采用高效的电加热装置和新型的加热材料,可以在较短的时间内将电解槽进行高温预热,大大缩短了启动时间。
2. 优化焙烧过程在500ka新型节能预焙阳极铝电解槽的研发过程中,针对传统焙烧过程中能量浪费和效率低下的问题进行了优化。
通过控制焙烧温度、时间和气氛等因素,使焙烧过程更加精准、高效,进而降低能耗。
3. 结合智能控制技术500ka新型节能预焙阳极铝电解槽焙烧启动方法还结合了智能控制技术。
利用现代化的自动控制设备和智能化的控制算法,可以对焙烧过程进行精确控制和优化调整,确保焙烧过程的稳定性和高效性。
四、500ka新型节能预焙阳极铝电解槽焙烧启动方法的技术特点1. 节能高效新型的500ka预焙阳极铝电解槽焙烧启动方法,采用了先进的加热技术和智能控制技术,能够大幅降低能耗,提高生产效率,实现节能高效。
2. 启动时间短通过优化焙烧过程和结合智能控制技术,500ka新型节能预焙阳极铝电解槽焙烧启动方法能够在较短的时间内完成电解槽的高温预热,实现了启动时间的缩短。
电解槽焙烧启动标准模板
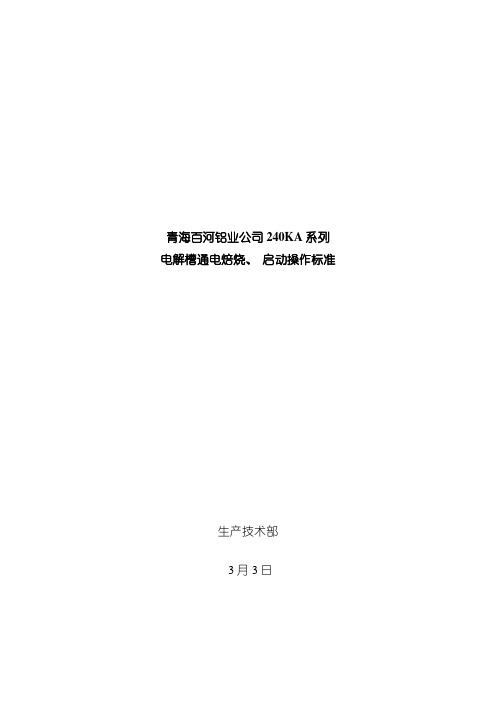
青海百河铝业公司240KA系列电解槽通电焙烧、启动操作标准生产技术部3月3日240KA电解槽通电焙烧、启动操作标准③铺设要求: 将焦粒框平整地放在阳极组投影区域, 然后将焦粒石墨粉混合料倒入框内, 用刮尺沿着焦粒框的长度方向刮平。
2.安放阳极①安放阳极之前先检查阳极质量、检查阳极底掌是否平整有杂物, 铝导杆是否与阳极垂直, 磷生铁浇铸是否饱满, 有无夹渣和裂纹等( 质量不符合要求的阳极不准许装槽) 。
②安放阳极要求a.将阳极坐在焦粒上的同时, 检查其周边是否已与焦粒充分接触; 如有明显未接触的地方, 要重新安放或重铺焦粒再装阳极。
安放阳极时, 大母线要与导杆接触面贴紧。
b.阳极挂好后, 由专人负责检查软连接安装质量, 并挂好小盒夹具。
③在阳极导杆与大母线下边沿对齐位置画好平行定位线。
3.安放热电偶套管①装炉前在人造伸腿下部预埋”6-11根热电偶套管”, 便于测量焙烧期间温度;②要求热电偶套管要斜放, 并放置到焦粒层, 并用冰晶石固定, 上口用纸塞住, 但不能接触到阳极。
4.加原、辅料①用石棉板堵住阳极的上部及四周缝隙, 防止物料漏入阳极底下或阳极缝隙内;②在槽膛靠近阳极的地方添加5—10cm厚的冰晶石约0.6吨;③在冰晶石的上面均匀撒一层氟化钙约1.5吨;④用φ80mm的电解质块3吨垒在人工炉帮上, 要求大块在外, 小块在里;⑤在电解质上均匀倒入约1吨纯碱;⑥在纯碱上用冰晶石填满槽膛四周和阳极碳块上表面, 防止在焙烧过程中发生阳极氧化。
要求阳极和中缝较高而边部较低。
5.装分流器、软连接①将4组分流器一端装置在前一台已启动槽的阳极平衡母线上, 并紧螺丝, 另一端卡在要启动槽立柱母线上卡紧, 连接方式采用压板连接, 紧固好螺丝, 再次复紧;。
电解槽的焙烧启动和后期管理

电解槽的焙烧启动和后期管理电解槽的预热焙烧与启动是铝电解生产中的两个重要阶段,新建或二次启动的电解槽在进入生产前,要经过焙烧与启动过程。
电解槽的焙烧启动虽然只有短短的几天,但对电解槽启动后的工作状态产生重大影响,尤其是对电解槽的寿命产生决定性的影响,因此必须足够的重视。
一.焙烧所谓焙烧(对于预焙槽而言,又称为预热),就是利用置于铝电解槽阴、阳两极间的发热物质产生热量,使电解槽阳极、阴极(含内衬)的温度升高。
电解槽预热焙烧的目的主要有:1.1 预热阴极。
阴极碳块间边缝和槽周边的扎糊进行烧结焦化,形成密实的碳素槽膛。
1.2 烘干电解槽内衬。
通过一定时间的缓慢加热排除槽体内耐火材料、保温材料等砌体的水分,提高槽膛温度,使阴、阳极温度接近或达到电解槽正常生产温度。
1.3 预焙槽的预热焙烧方法主要有:1.铝液预热法;2.焦粒焙烧法;3.石墨粉焙烧法;4.燃料预热法。
焦粒焙烧现在大型预焙槽的焙烧大部分采用焦粒焙烧法,焦粒焙烧相比铝水焙烧可避免铝液对槽内衬材料的冲击,同时电解质提前进入从而阻挡了铝液从炉底及侧部缝隙向外渗透。
根据我们厂实际焙烧的方法,我们这种来主要探讨一下焦粒焙烧法。
焦粒焙烧法是在阴、阳极之间铺上一层煅烧过的焦炭颗粒,其厚度为15-20mm。
如果炉底平整,焦粒厚度可为10-20mm。
焦粒粒度在1-5mm之间,严格控制1mm一下的焦粉。
1.焙烧前准备工作1.1铺焦与放阳极要求及影响电解槽焙烧前要求铺焦,对于焦粒的铺设有严格的要求,铺焦所用的焦粒粒度为1~5mm,要求铺焦平整,阳极自然下落后与焦粒充分接触,可用钢板尺检查焦粒与阳极底掌是否接触完全,对于接触面积小的应重新调整阳极导杆位置,尽可能使阳极底掌与阴极碳块接触面积较大。
放下阳极后,可将阳极周围焦粒向填充不实的部位塞进去。
保证阳极与阴极底掌完全接触。
实际铺焦过程中经常容易出现这样的问题,作业人员为保证阳极导杆与阳极大母线之间缝隙较小,铺焦过程中往往将阳极外侧焦粒铺的比内侧稍厚一点,这样阳极碳块放下后阳极导杆向大母线方向倾斜,容易保证阳极导杆与大母线的间隙较小,但这种铺焦方式会为以后的焙烧启动工作带来麻烦,具体表现在由于阳极外侧焦粒较厚,阳极外侧接触好,通电焙烧后外侧电流就比内侧大,外侧发热量多导致冰晶石靠槽帮一侧先熔化,靠中缝侧由于发热量少中缝冰晶石熔化速度慢,由于中缝熔化差,不具备启动条件造成焙烧时间被迫延长情况发生。
2-4电解槽焙烧与启动

三、铝电解槽非正常期生产管理
• 电解槽启动后24小时即可灌铝,灌铝后的电解槽即进入启动后期。 • 目的: • 这期间电解槽将逐渐转入正常运行: • 一是各项技术条件逐步过渡到正常生产控制范围; • 二是形成一定的槽膛内型; • 三是能量平衡、物料平衡逐渐建立、稳定。
• 当这些变化完成之后,电解槽即进入了正常。
一、目的和方法
• 电解槽预热焙烧的目的: • 1)加热并焙烧阴极 。提高阴极温度,对阴极碳块间缝和槽周边的扎
糊进行烧结焦化,以形成密实的炭素槽膛。 • 2)烘干电解槽内衬材料。通过一定时间的缓慢加热,以排除槽体内耐
火材料、保温材料、浇注材料等砌体的水分。 • 3)提高槽膛温度。使阴、阳极温度接近或达到电解槽生产温度,以能
天,低效高耗。
一、目的和方法
• 焦粒焙烧法: • 在阴、阳极之间铺上一层煅烧过的焦炭颗粒,其厚度为15一20mm 。焦粒粒
度在1一4mm之间。电解槽通电后,焦粒层作为电阻体在阴、阳极之间产生焦 耳热来预热电解槽,同时,阴极和阳极本身的电阻也产生热量,在其内部预 热。因阳极碳块直接坐在焦粒层上,为解决预热过程中产生的热应力,阳极 导杆与阳极母线之间用临时导电软母线联接,因为这种软连接可以使阳极碳 块有一定的活动自由度,以释放在焙烧时焦粒上抬的膨胀力,并使阳极重量 能全部压实在焦粒上,保证阳极与焦粒良好接触, 以获得均匀的阴阳极电流 分布。在启动前拆除临时导电软母线。
过快。
一、目的和方法
• 燃料预热法 • 加热采用燃烧喷嘴喷射火焰,在阳极上面加盖保温罩,使高温气体停留在
槽内,并防止冷空气窜入。火焰在阴`阳极之间燃烧,依靠传导、对流和 辐射,将热量传输到其他部位。 • 此法的最大优点为升温快,可以控制加热速度,使阴极表面均匀受 热,节省电能。 • 其缺点是操作比较复杂,只能控制表面温度,内部温度靠热传导, 温差较大,火焰燃烧时易使阴极和阳极表面烧损。
240KA电解槽燃气焙烧启动方案
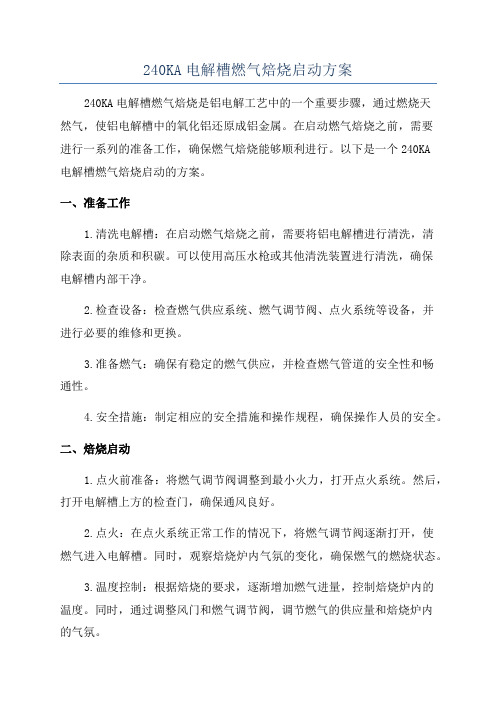
240KA电解槽燃气焙烧启动方案240KA电解槽燃气焙烧是铝电解工艺中的一个重要步骤,通过燃烧天然气,使铝电解槽中的氧化铝还原成铝金属。
在启动燃气焙烧之前,需要进行一系列的准备工作,确保燃气焙烧能够顺利进行。
以下是一个240KA电解槽燃气焙烧启动的方案。
一、准备工作1.清洗电解槽:在启动燃气焙烧之前,需要将铝电解槽进行清洗,清除表面的杂质和积碳。
可以使用高压水枪或其他清洗装置进行清洗,确保电解槽内部干净。
2.检查设备:检查燃气供应系统、燃气调节阀、点火系统等设备,并进行必要的维修和更换。
3.准备燃气:确保有稳定的燃气供应,并检查燃气管道的安全性和畅通性。
4.安全措施:制定相应的安全措施和操作规程,确保操作人员的安全。
二、焙烧启动1.点火前准备:将燃气调节阀调整到最小火力,打开点火系统。
然后,打开电解槽上方的检查门,确保通风良好。
2.点火:在点火系统正常工作的情况下,将燃气调节阀逐渐打开,使燃气进入电解槽。
同时,观察焙烧炉内气氛的变化,确保燃气的燃烧状态。
3.温度控制:根据焙烧的要求,逐渐增加燃气进量,控制焙烧炉内的温度。
同时,通过调整风门和燃气调节阀,调节燃气的供应量和焙烧炉内的气氛。
4.监测指标:在焙烧过程中,需要监测各项指标,如焙烧炉内的温度、燃气流量、气氛成分等。
如有异常情况,及时采取措施进行调整和修正。
5.稳定运行:在燃气焙烧的初期,需要进行适当的调整和试验,确保焙烧炉内的温度和气氛稳定。
同时,对电解槽的运行情况进行监测和评估,确保整个系统的稳定运行。
6.燃气管理:在焙烧启动后,需要建立和完善燃气管理制度,对燃气的供应、使用和储存进行规范和管理,确保安全和高效运行。
以上是一个240KA电解槽燃气焙烧启动的方案。
在实际操作中,还需要根据具体情况进行调整和补充。
同时,为了确保安全和效果,还需要密切关注焙烧过程中的各项指标和设备运行情况,及时采取措施进行调整和修正。
电解槽的焙烧启动和后期管理

电解槽的焙烧启动和后期管理电解槽的预热焙烧与启动是铝电解生产中的两个重要阶段,新建或二次启动的电解槽在进入生产前,要经过焙烧与启动过程。
电解槽的焙烧启动虽然只有短短的几天,但对电解槽启动后的工作状态产生重大影响,尤其是对电解槽的寿命产生决定性的影响,因此必须足够的重视。
一.焙烧所谓焙烧(对于预焙槽而言,又称为预热),就是利用置于铝电解槽阴、阳两极间的发热物质产生热量,使电解槽阳极、阴极(含内衬)的温度升高。
电解槽预热焙烧的目的主要有:1.1 预热阴极。
阴极碳块间边缝和槽周边的扎糊进行烧结焦化,形成密实的碳素槽膛。
1.2 烘干电解槽内衬。
通过一定时间的缓慢加热排除槽体内耐火材料、保温材料等砌体的水分,提高槽膛温度,使阴、阳极温度接近或达到电解槽正常生产温度。
1.3 预焙槽的预热焙烧方法主要有:1.铝液预热法;2.焦粒焙烧法;3.石墨粉焙烧法;4.燃料预热法。
焦粒焙烧现在大型预焙槽的焙烧大部分采用焦粒焙烧法,焦粒焙烧相比铝水焙烧可避免铝液对槽内衬材料的冲击,同时电解质提前进入从而阻挡了铝液从炉底及侧部缝隙向外渗透。
根据我们厂实际焙烧的方法,我们这种来主要探讨一下焦粒焙烧法。
焦粒焙烧法是在阴、阳极之间铺上一层煅烧过的焦炭颗粒,其厚度为15-20mm。
如果炉底平整,焦粒厚度可为10-20mm。
焦粒粒度在1-5mm之间,严格控制1mm一下的焦粉。
1.焙烧前准备工作1.1铺焦与放阳极要求及影响电解槽焙烧前要求铺焦,对于焦粒的铺设有严格的要求,铺焦所用的焦粒粒度为1~5mm,要求铺焦平整,阳极自然下落后与焦粒充分接触,可用钢板尺检查焦粒与阳极底掌是否接触完全,对于接触面积小的应重新调整阳极导杆位置,尽可能使阳极底掌与阴极碳块接触面积较大。
放下阳极后,可将阳极周围焦粒向填充不实的部位塞进去。
保证阳极与阴极底掌完全接触。
实际铺焦过程中经常容易出现这样的问题,作业人员为保证阳极导杆与阳极大母线之间缝隙较小,铺焦过程中往往将阳极外侧焦粒铺的比内侧稍厚一点,这样阳极碳块放下后阳极导杆向大母线方向倾斜,容易保证阳极导杆与大母线的间隙较小,但这种铺焦方式会为以后的焙烧启动工作带来麻烦,具体表现在由于阳极外侧焦粒较厚,阳极外侧接触好,通电焙烧后外侧电流就比内侧大,外侧发热量多导致冰晶石靠槽帮一侧先熔化,靠中缝侧由于发热量少中缝冰晶石熔化速度慢,由于中缝熔化差,不具备启动条件造成焙烧时间被迫延长情况发生。
一种500ka新型节能预焙阳极铝电解槽焙烧启动方法
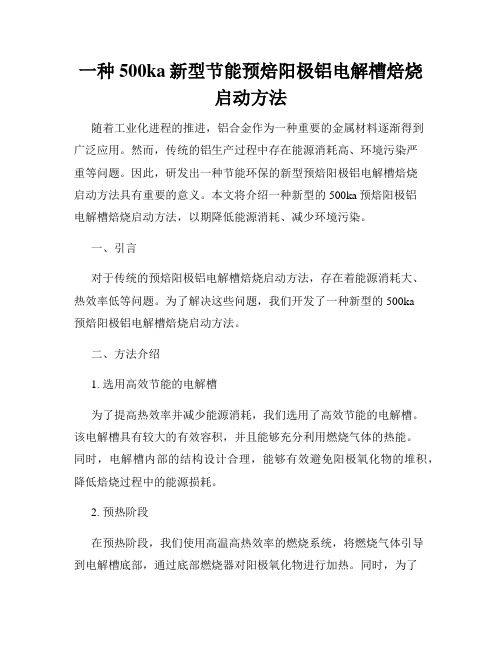
一种500ka新型节能预焙阳极铝电解槽焙烧启动方法随着工业化进程的推进,铝合金作为一种重要的金属材料逐渐得到广泛应用。
然而,传统的铝生产过程中存在能源消耗高、环境污染严重等问题。
因此,研发出一种节能环保的新型预焙阳极铝电解槽焙烧启动方法具有重要的意义。
本文将介绍一种新型的500ka预焙阳极铝电解槽焙烧启动方法,以期降低能源消耗、减少环境污染。
一、引言对于传统的预焙阳极铝电解槽焙烧启动方法,存在着能源消耗大、热效率低等问题。
为了解决这些问题,我们开发了一种新型的500ka预焙阳极铝电解槽焙烧启动方法。
二、方法介绍1. 选用高效节能的电解槽为了提高热效率并减少能源消耗,我们选用了高效节能的电解槽。
该电解槽具有较大的有效容积,并且能够充分利用燃烧气体的热能。
同时,电解槽内部的结构设计合理,能够有效避免阳极氧化物的堆积,降低焙烧过程中的能源损耗。
2. 预热阶段在预热阶段,我们使用高温高热效率的燃烧系统,将燃烧气体引导到电解槽底部,通过底部燃烧器对阳极氧化物进行加热。
同时,为了进一步提高燃烧效率,我们在电解槽顶部设置了烟气排出装置,将产生的烟气及时排出,减少能源的浪费。
3. 动力引入在预焙阳极铝电解槽焙烧过程中,为了保证阳极铝块能够充分燃烧,我们采用了一种新型的动力引入装置。
该装置能够将燃烧气体均匀地引入电解槽内部,使阳极铝块受到均匀的加热,提高燃烧效率。
4. 控制系统优化为了保证预焙阳极铝电解槽焙烧启动的顺利进行,我们对控制系统进行了优化。
通过对电解槽温度、燃烧气体流量等参数进行实时监控和调节,能够确保阳极铝块在焙烧过程中得到充分的加热,提高能源利用效率。
三、实验结果我们通过实验验证了该500ka新型节能预焙阳极铝电解槽焙烧启动方法的有效性。
实验结果显示,采用该方法进行预焙阳极铝电解槽焙烧可以显著降低能源消耗,提高热效率。
与传统方法相比,该方法在能源利用上具有明显的优势。
四、结论本文介绍了一种新型的500ka预焙阳极铝电解槽焙烧启动方法。
科技成果——铝电解槽新型阴极结构及焙烧启动与控制技术

科技成果——铝电解槽新型阴极结构及焙烧启动与控制技术适用范围有色金属行业电解铝企业行业现状传统铝电解槽技术直流电耗13000-13500kWh/t-Al,其中2008年全国产铝1318万t,平均直流电耗13260kWh/t-Al,综合交流电耗14323kWh/t-Al,吨铝生产排放10.82tCO2,铝电解槽大修投资约80元/t-Al(依据电解槽容量大小、槽寿命长短)。
成果简介1、技术原理电解铝生产采用熔盐电解法,即将氧化铝、冰晶石、氟化铝等加入电解槽中,在直流电作用下,电解质在电解槽内发生电化学反应,在阴极上析出铝液,阳极上析出CO2和CO,铝液用真空抬包抽出铸造成铝锭,阳极逐渐消耗定期更换。
本技术的技术原理是:(1)采用其阴极表面带有凸起结构的铝电解槽新型阴极技术,将现行电解槽的阴极结构改变为新型的电解槽阴极结构和内衬结构,上限减少阴极铝液波动,提高阴极铝液面稳定性,从而提高电流效率,降低槽电压,降低电耗;(2)应用国际上通用的以电解槽阴极表面温度分布和垂直分布情况判定电解槽焙烧质量的方法,以电解槽阴极和电解质温度为控制中心,利用火焰焙烧,取代传统的铝液焙烧和焦粒焙烧,利用燃气量和风量控制火焰温度和燃烧热量,实现焙烧温度与升温速度的控制,通过合理地设置燃烧器,达到温度均匀的目的,最终得以提高电解槽的焙烧质量,节省能耗。
2、关键技术(1)新型阴极结构电解槽的关键技术是在炭阴极表面设计和构建凸起结构,这种凸起结构具有阻流和铝液波动,提高铝液的电磁流动动力学稳定性的作用。
新型阴极结构电解槽的阴极结构如图1、2、3所示,图4是由计算机根据电磁流体动力学理论计算出来的新型阴极结构电解槽与传统阴极结构电解槽的阴极铝液面波动高度的比较。
由图4可以看出,铝电解使用新型阴极结构电解槽,可使槽中铝液面波动减少2cm左右,从而实现了电解槽阴极铝液面稳定性提高,这为电解槽电流效率的提高和极距与槽电压的降低提供了技术保障,这也是新型阴极结构电解槽的关键技术所在。
400KA电解槽焙烧启动方案

400KA预焙阳极电解槽焙烧启动方案二〇二〇年五月400KA预焙阳极电解槽焙烧启动方案为了使电解槽焙烧启动工作组织有序、分工明确、顺利实施,特制定400kA预焙阳极电解槽焙烧启动方案。
一、焙烧启动方法1、300台电解槽采用燃气焙烧和湿法无效应启动。
2、考虑到在焙烧过程中出现燃烧器故障或启动进度要求等不可预估的因素,可能会导致不能满足3台槽的启动计划要求时,部分槽采用焦粒焙烧和湿法无效应启动作为应急备案。
3、本启动方案分燃气焙烧启动方案和焦粒焙烧启动方案两部分。
二、焙烧启动准备-----燃气焙烧启动部分(一)焙烧启动前的检查及流程1、燃气焙烧启动前的检查:(二)焙烧启动用料量及要求单槽物料启动用量及总量计划表空耗交流电南北厂房过道压降0.559v,整流所与厂房中间压降1.06v,4#通廊及过道母线压降1.071v,启动期间整流效率按97%预测。
11 导杆钢爪组组40 10560 利旧1、冰晶石的标准符合要求:GB/T4291-20072、氟化钙的标准符合要求:GB/T 27804-20113、碳酸钠的标准符合要求:GB210.1-20044、预焙阳极的标准符合要求:启动挂极使用的预焙阳极块与正常生产使用阳极块均按设计标准执行,具体如下:能够承受阳极电流密度要求:>0.796A/cm2,碳渣的吨铝单耗:<15kg/t.al。
5、氧化铝的标准符合要求:执行标准:YS/T803-2012中YAO-1化学成分符合标准如下:说明:检验数值采用修约比较法,执行GB/T8170。
化学成分按350±5℃温度下烘干2小时的干基计算。
微量元素的含量符合如下(百万分之一)氧化铝的物理特性如下:6、外购电解质块符合:Q/BL J 03.44-2012(1)成分电解质块主要成分是冰晶石和氧化铝组成的熔融物,各物质成分所占电解质块的比例及各元素含量要求应符合下表的规定:(2)水分:质量百分数应小于0.2%。
(3)电解质的摩尔比:(NaF/ALF3)≤2.6。
400KA电解槽新焙烧启动方案g
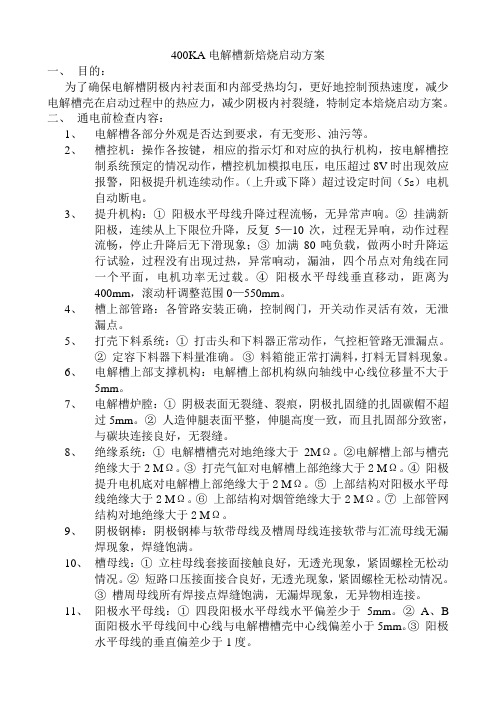
400KA电解槽新焙烧启动方案一、目的:为了确保电解槽阴极内衬表面和内部受热均匀,更好地控制预热速度,减少电解槽壳在启动过程中的热应力,减少阴极内衬裂缝,特制定本焙烧启动方案。
二、通电前检查内容:1、电解槽各部分外观是否达到要求,有无变形、油污等。
2、槽控机:操作各按键,相应的指示灯和对应的执行机构,按电解槽控制系统预定的情况动作,槽控机加模拟电压,电压超过8V时出现效应报警,阳极提升机连续动作。
(上升或下降)超过设定时间(5s)电机自动断电。
3、提升机构:①阳极水平母线升降过程流畅,无异常声响。
②挂满新阳极,连续从上下限位升降,反复5—10次,过程无异响,动作过程流畅,停止升降后无下滑现象;③加满80吨负载,做两小时升降运行试验,过程没有出现过热,异常响动,漏油,四个吊点对角线在同一个平面,电机功率无过载。
④阳极水平母线垂直移动,距离为400mm,滚动杆调整范围0—550mm。
4、槽上部管路:各管路安装正确,控制阀门,开关动作灵活有效,无泄漏点。
5、打壳下料系统:①打击头和下料器正常动作,气控柜管路无泄漏点。
②定容下料器下料量准确。
③料箱能正常打满料,打料无冒料现象。
6、电解槽上部支撑机构:电解槽上部机构纵向轴线中心线位移量不大于5mm。
7、电解槽炉膛:①阴极表面无裂缝、裂痕,阴极扎固缝的扎固碳帽不超过5mm。
②人造伸腿表面平整,伸腿高度一致,而且扎固部分致密,与碳块连接良好,无裂缝。
8、绝缘系统:①电解槽槽壳对地绝缘大于2MΩ。
②电解槽上部与槽壳绝缘大于2 MΩ。
③打壳气缸对电解槽上部绝缘大于2 MΩ。
④阳极提升电机底对电解槽上部绝缘大于2 MΩ。
⑤上部结构对阳极水平母线绝缘大于2 MΩ。
⑥上部结构对烟管绝缘大于2 MΩ。
⑦上部管网结构对地绝缘大于2 MΩ。
9、阴极钢棒:阴极钢棒与软带母线及槽周母线连接软带与汇流母线无漏焊现象,焊缝饱满。
10、槽母线:①立柱母线套接面接触良好,无透光现象,紧固螺栓无松动情况。
- 1、下载文档前请自行甄别文档内容的完整性,平台不提供额外的编辑、内容补充、找答案等附加服务。
- 2、"仅部分预览"的文档,不可在线预览部分如存在完整性等问题,可反馈申请退款(可完整预览的文档不适用该条件!)。
- 3、如文档侵犯您的权益,请联系客服反馈,我们会尽快为您处理(人工客服工作时间:9:00-18:30)。
几种电解槽焙烧启动工艺的节能分析
焙烧启动在电解铝生产过程中占据着重要角色,对电解铝纯生产而言只是一个“无用功”,不仅要消耗大量能源,而且对环境又造成污染,对企业生产又不能产生直接经济效益,但它是电解生产的前奏,必不可少,特别关键。
长期以来大家一直在探讨焙烧启动的方法和效果,对焙烧启动期间的能源消耗和成本控制很少谈起。
一、铝电解槽的焙烧启动
1、就当前的铝电解工业而言,电解槽的正常生产流程分为焙烧、启动和正常生产三个过程。
铝电解槽的焙烧即把电解槽由室温状态加热到正常生产状态(945-955℃)的过程,是电解槽正常生产的前提,也是电解槽实现高效产铝过程的关键时期,对于电解槽的后期管理显得尤为重要。
铝电解槽的焙烧目的有:
1)焙烧阴极和侧部炭块。
通过焙烧阴极炭块和侧部炭块之间的扎固糊进行焦化,使阴极炭块和侧部炭块成为一个整体;
2)排除内衬中含有的水分。
因为水分在高温内衬中极易形成气体,如不及时排出,则会在启动期或生产期使内衬产生膨胀,造成内衬漏洞;
3)均匀升高内衬温度。
在焙烧过程中使内衬按不同层次、一定梯度均匀升温,以满足正常生产之需要;
4)提高阳极和阴极的温度,以利用下一步的顺利启动。
目前国内外通常使用的焙烧方法有:铝液焙烧、焦粒焙烧和燃料焙烧等。
铝液焙烧是电解槽内灌入高温铝液,再通以直流电,利用铝液和阴、阳极炭块在通以直流电的状态下产生的焦耳热来焙烧电解槽;焦粒焙烧是在电解槽的阴极炭块上预先铺设一层焦粒,再坐上阳极,通以直流电,靠焦粒电阻本身产生的焦耳热来焙烧电解槽;燃烧焙烧,是利用燃料系统和温度控制系统的配合,按事先设置好的温度曲线要求,通过燃烧油类或天然气等来加热焙烧电解槽。
2、铝电解槽的启动
铝电解槽的焙烧结束就是铝电解槽启动的开始,两者完全是一个“无缝”的衔接过程,一般经过24-48小时的启动,将步入启动后期管理过程,预示着电解槽缓慢进入正常生产过程。
铝电解槽的启动是指使电解槽槽内拥有足量多的液体电解质,以适应电解槽正常生产的需要,目前的启动工艺主要分为干法效应启动、湿法效应启动和湿法无效应启动三种。
干法效应启动,即利用升高槽电压使电解槽发生阳极效应,靠阳极效应产生的热量来熔化冰晶石等物料,使槽内电解质达到一定水平,来满足电解槽正常生产的要求。
湿法效应启动,是将其它槽内液体电解质注入待启动的电解槽内,使槽内电解质达到一定水平,此时再利用升高槽电压使槽子发生阳极效应,来逐步熔化槽内物料,使槽子电解质水平达到正常生产的要求。
湿法无效应启动,也是将其它槽内液体电解质注入待启动的电解槽内,只是要求有足够多的量,再将槽电压保持稍高于正常生产槽电压,适当保持一段时间来熔化槽内物料,使电解槽逐步进入正常生产。
二、焙烧启动工艺的节能分析
1、焙烧工艺节能分析
具体要分析哪种焙烧工作节能效果更好,其一,这种工艺首先能达到满意的电解槽焙烧效果,完全满足电解槽的启动要求;第二,焙烧时间最短,可以保证
电解槽在最短的时间内具备启动条件,开始正常生产,提高电解槽的年生产昼夜数;第三,焙烧过程中的能量利用率最高,即热损失率低;第三,焙烧过程中的能量利用率最高,即热损失率低;第四,此工艺简单,易操作;最后,这种工艺对周围环境的“综合”污染指数最小。
1)焙烧效果分析
对于大型和特大型电解槽而言,由于阴极表面积很大,如果用铝液焙烧,待注入铝液时,铝液在来不及完全充满阴极表面时就会部分凝固,很难使铝液以液体形式在短时间内均匀的平铺于阴极表面。
另外,高温铝液对阴极炭块表现的热冲击很大,极易造成阴极在焙烧过程中出现致命损伤,使阴极表面生产缺陷和细小裂纹和裂缝,此时的液体铝液便会直接进入阴极裂缝,给电解槽的正常生产留下隐患等。
而在焦粒焙烧中,用焦粒充当发热体,采用软连接器和分流器技术,可以大大减少焙烧过程中全电流对电解槽的热冲击,而且焦粒也充当填充物,及时进入阴极表现的裂缝内,与阴极形成一个整体,减少启动后期铝液直接进入的可能性,对延长槽寿命有一定的现实意义。
与前两种工艺相比,燃料焙烧由于升温控制的不足,因而整体焙烧效果最好,只是在焙烧过程中造成阴、阳极炭块的氧化比较严重。
2)焙烧时间的分析
焙烧时间,指从焙烧开始达到启动条件所用的时间,很显然时间越短越好。
由于铝本身的电阻较小,在焙烧过程中产生热量较低,因此,铝液焙烧时间较长,一般需要7-8昼夜。
与铝相比,焦粒的电阻大的多,在焙烧过程中产生的热量很高,大大加快了焙烧速度,一般来讲,经过72小时左右,电解槽就具备启动条件。
燃料焙烧完全是在人为控制下进行,可以改善焙烧过程中阴极炭块和侧部炭块的热分析状况,进而制定科学、合理的升温速度,因而焙烧时间更短。
3)能量利用分析
能量利用是指焙烧过程中产生的能量,用于焙烧阴极炭块和侧部炭块所占用的比例。
从铝液焙烧操作过程来看,先往槽内注入适量铝液,再下降阳极,使电解槽的阴、阳极形成回路,然后在断开短路口,往阳极炭块的间隙及其上表面添加冰晶石起保温作用,由此过程可以发现在添加冰晶石保温料前会造成能量的快速扩散。
而焦粒焙烧是在阴极炭块表面铺好焦粒,将阳极下降到位后,再在阳极炭块上面及阳极炭块间隙中覆盖冰晶石保温料,然后断开短路口,开始通电焙烧,与铝液焙烧相比,能量损失则小的多。
燃料焙烧受其焙烧原理所致,在焙烧过程中,保温措施无法做的很好,期间会造成能量的大量损失,能量利用率不会很高。
4)操作简易分析
铝液焙烧,先注入铝液,再下降阳极,断开短路口,就可进入焙烧过程,显然它的操作最简单、最方便、最容易。
焦粒焙烧必须事先往阴极炭块上铺设一层粒度和厚度均匀的焦粒,再下降阳极坐于焦粒下,阳极导杆与阳极大母线间还得安装软连接器,阳极大母线与进电端立柱线间也得安装分流器等等,在焙烧期间还的时刻关注阳极电流分布是否均匀。
与铝液焙烧相比,焦粒焙烧要复杂的多,操作难度也增加了不少.燃料焙烧的设备就更复杂,它由一套控制系统和燃烧系统组成,主要包括控制热电偶、专用绝热罩、喷油嘴、供油系统、空气管、燃油管和贮油罐或贮气罐等等,在电解车间使用安全性也很差,况且整套设备的造价也不菲,设备的现场安装、拆卸和使用极不方便,需要专业人员完成。
5)环境污染分析
铝液焙烧中,在铝液注入电解槽的瞬间,会对阴极造成高温热冲击,铝与炭会发生化学反应,生成复杂的铝炭化合物,对周围环境造成轻微污染。
焦粒焙烧是由焦粒的常温升温开始,上面又有一层厚厚的保温料覆盖,对周围环境污染很小。
而燃烧焙烧会造成大量的能量扩散到周围环境中,同时阴、阳极的大面氧化,首先大量CO和CO2气体,相比而言,对周围环境造成的污染最大。
通过对上述三种焙烧工艺的综合分析、评价和比较,焦粒焙烧的整体节能效果更突出。
2、启动工艺节能分析
在电解槽的启动过程中,要想更好的节能,首先启动时间越短越节能;第二,保持槽电压稳定,避免阳极效应的频繁发生,使槽内电解质温度波动尽可能的小;第三,尽可能多从其它槽抽取液体电解质,减少在高温下过多的熔化冰晶石等物料,这样不但能量利用率低,而且会造成大量氟盐挥发,污染环境。
由上述三点分析,可以得知湿法无效应用启动最节能,因为此工艺在启动过程中不用人为制造阳极效应,所用电解质绝大部分从其他槽抽取,不用熔化,大大减少了粉状物料的挥发,启动时间也较短。
干法效应启动和湿法效应启动都是通过人为制造阳极效应提高槽内温度,达到快速熔化冰晶石等粉状物料,期间,一方面会造成电能大量浪费,另一方面也会造成AlF3等物料的大量挥发,增加启动成本。
三、焙烧启动过程的节能措施
在电解槽的焙烧启动过程中,选择最佳的焙烧工艺――“焦粒焙烧+湿法无效应启动”可以达到节能的目的,但在整个焙烧期间也应该抓好以下节能措施:1)选择最佳的发热体材质――焦粒,要求焦粒的灰分小,焦油含量低,粒度大小比例适中,电阻比较大,在焙烧启动过程中产生的热量多,启动后期产生得炭渣少,且捞取容易。
2)焙烧前在阳极炭块上表面和阳极炭块上加足石保温料,加强保温效果,防止焙烧期间造成热量的不必要散失,提高能量利用率。
3)加强培训,提高工人的操作技能。
保证焙烧前槽底铺设的焦料厚度均匀,以使焙烧过程阳极电流分布更加均匀;在启动过程往槽内加料和提升阳极做到“两及时”,提高能量利用率。
对几种焙烧启动工艺进行综合分析、比较,得出“焦粒焙烧+湿法无效应启动”是目前最节能的一种焙烧启动工艺。
但这种工艺在实际应用中还存在一些缺点,特别是焙烧过程中,阳极电流分布不均匀,极易引起电解槽局部升温过快,对槽内衬有较强的热冲击。
不过这些缺点和不足只要经过生产技术人员认真攻关,一定会被大大改善的,“焦粒焙烧+湿法无效应启动”终究会成为一种最节能、最适用的焙烧启动工艺。
摘自《中国有色工程》2008年第三期
(党建平宁建文供稿)。