发电机组出厂检验规定
发电机组运行检查规程范文(三篇)
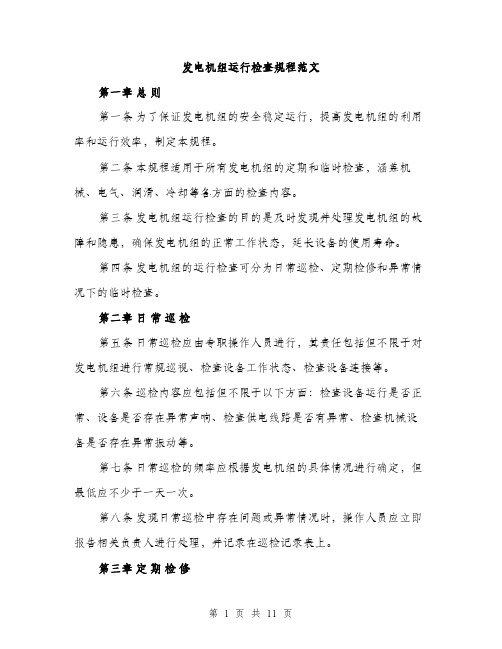
发电机组运行检查规程范文第一章总则第一条为了保证发电机组的安全稳定运行,提高发电机组的利用率和运行效率,制定本规程。
第二条本规程适用于所有发电机组的定期和临时检查,涵盖机械、电气、润滑、冷却等各方面的检查内容。
第三条发电机组运行检查的目的是及时发现并处理发电机组的故障和隐患,确保发电机组的正常工作状态,延长设备的使用寿命。
第四条发电机组的运行检查可分为日常巡检、定期检修和异常情况下的临时检查。
第二章日常巡检第五条日常巡检应由专职操作人员进行,其责任包括但不限于对发电机组进行常规巡视、检查设备工作状态、检查设备连接等。
第六条巡检内容应包括但不限于以下方面:检查设备运行是否正常、设备是否存在异常声响、检查供电线路是否有异常、检查机械设备是否存在异常振动等。
第七条日常巡检的频率应根据发电机组的具体情况进行确定,但最低应不少于一天一次。
第八条发现日常巡检中存在问题或异常情况时,操作人员应立即报告相关负责人进行处理,并记录在巡检记录表上。
第三章定期检修第九条定期检修是对发电机组进行全面维护和检修的活动,旨在确保发电机组的长期稳定运行。
第十条定期检修应由专业维修人员进行,并按照相关制度和规程进行操作。
第十一条定期检修的内容包括但不限于:润滑油更换、滤芯更换、冷却系统清洗、电气系统检测等。
第十二条定期检修的频率应根据发电机组的使用时间和工作环境进行确定,通常为每半年一次。
第十三条定期检修完成后,应填写维修记录表,并进行签字确认。
第四章异常情况的临时检查第十四条在发现发电机组出现异常情况时,操作人员应立即停止运行,并进行检查和处理。
第十五条异常情况的临时检查应由专业人员进行,并按照相关规程进行操作。
第十六条异常情况的临时检查内容包括但不限于:设备的进一步检测、故障处理、设备的更换等。
第十七条异常情况的临时检查需要记录详细信息,并填写相应的故障处理报告。
第五章质量控制第十八条发电机组运行检查的质量控制从严,要求检查人员具有相应的专业知识和技能。
发电机组出厂试验测试工艺规程

出厂试验测试工艺规程测试人员必须熟悉各种型号机组的电气原理图、机械结构,熟练掌握机组的测试方法。
1 机组的检查1.1 检查机组表面是否清洁,飞轮螺栓及其他紧固螺帽有无松动现象,发现问题及时解决。
1.2 检查发电机绝缘电阻,发电机绕组对机壳的绝缘电阻应不低于30MΩ。
检查开关箱出线盒相序是否符合从左到右U、V、W、N,接线螺栓有无松动,发现问题及时解决。
1.3 检查控制箱是否有工序合格标记。
各开关、按钮操作是否灵活,接触是否良好。
各仪表外观是否完好,指针是否在零位。
各元器件安装是否牢固。
2测试前的准备2.1 检查水箱是否正常,向水箱中加入足量清洁软水,打开各排气阀、排放阀、排放塞,排尽机体内空气,直至有水流出为止。
检查水管接头处有无漏水现象,检查冷却水泵的叶轮是否灵活,传动皮带松紧是否合适,发现问题及时解决。
2.2 向油底壳加入适量机油,检查油底壳的机油量,发现油量不足或过多及时处理解决。
检查机油管道有无漏油现象,发现问题及时解决。
2.3 根据机组功率规格选择合适的负载接线柜,连接好发电机的输出线,并将开关箱空气开关断开,接好负载与开关箱的电线。
2.4 根据机组规格选择合适的排气管并将其装上机组,并能与排气系统连接。
2.5 将燃油进油管、回油管与机组可靠连接,检查燃油系统各部件有无漏油现象,发现问题及时解决,检查油量是否充足,若油量不足需及时加满,并打开油路开关。
2.6 启动柴油发电机组测试系统,并根据发电机组规格设置各参数,将机组上的各参数正确输入测试系统中,选择正确负载及电流变化。
2.7 根据机组规格选择合适的蓄电池,并将其与机组可靠连接。
2.8 将装电调机组的控制屏中调速板各电位器调至中间位置。
3 测试3.1 启动机组,调整调速板中各电位器,使柴油机处于最佳运行状态。
3.2 调整转速电位器,使频率表显示50HZ(即1500转/分),调整发电机上电压调整电位器,使发电机组电压显示400V。
3.3 检查报警电路是否正常,发现问题及时解决。
电厂新装发电机及电动机验收标准

发电机的试验跟踪检查标准
试验项目
试验电压
标准
备注
电阻测温元件
250伏
≥5兆欧
轴承绝缘
密封支座及中间环绝缘
1000伏
500伏
发电机汽励两端轴瓦的密封瓦及中间环、左右轴承座、外恻挡油盖、轴瓦衬垫、高压进油管绝缘电阻不小于10MΩ
转子绕组
500伏
10-50兆欧
定子绕组(10分钟)
2500伏
定子三相绕组对地及相间绝缘电阻≥500MΩ,吸收比≥1.6,极化指数≥2.0,三相不平衡系数小于2(吹干水);如通水汽励端两端汇水管和引线部分汇水管对地绝缘电阻≥30KΩ,绕组对汇水管绝缘电阻≥100KΩ,(定冷水水质合格并正常循环)
380V电动机试验跟踪检查标准
序号
项目
标准
内容
备注
1
核相
电源侧与电机侧的ABC三相相序一致
2
相序校核
ABC三相相序与转向一致
3
绝缘电阻
.绝缘电阻>6MΩ吸收比>1.3
4
直流电阻
三相直流电阻互差不超过最小值的2%,线间的为1%与出厂时无明显的差别
5
交流耐压
可用2500V摇表代替
6KV电动机试转跟踪检查标准
泵压1 MPa压力维持8小时,在汽、励两侧引水管接头及进出汇水管接头处无渗漏。
定子绕组出厂前泵压试验,泵压1 MPa压力维持8小时,在汽、励两侧引水管接头及进出汇水管接头处无渗漏。
16
定子耐电压试验
分相施以交流耐压45.9kv,维持3分钟,无电击穿等现象
定子绕组交流耐压试验,耐压前测量三相绕组绝缘电阻均为3000兆欧,大于标准的1000兆欧,吸收比大于1.3,绝缘电阻合格后才分相施以交流耐压45.9kv,维持3分钟,无电击穿等现象,其三相绕组泄漏电流平衡,为3.1安
水轮发电机组设备出厂检验一般规定

中华人民共和国电力行业标准水轮发电机组设备出厂检验一般规定发布实施中华人民共和国能源部发布总则水轮机水轮发电机进水阀配套自动化元件附录本办法主要适用于额定容量为制造质量的出厂检验额定容量大于或小于此范围的或其他型式的水轮发电机组及附属设备可参制造质量检验的依据出厂检验机构检验机构的职责参与产品主要部件的试验与装配出厂试验等了解产品的设计修改和质量问题的处理情况如在完工前未通知监造代表监造代表有权要求制造厂职责在进行凡需监造代表签证的部件应提供正保管技术条件注符号为驻厂监造代表签证的项目检验依据水轮机通流部件验收标准检查项目尾水管里衬转轮室座环外切圆直径以及进口节距在工地组装的导叶蜗壳接缝间隙及内壁错口机坑里衬导叶顶盖支持盖底环导水机构厂内总装配混流式转轮轴流式转轮厂内装配试验主轴主轴联接后导轴瓦接力器厂内总装附属设备应抽查真空破坏阀动作试验混流式转轮需有以下记录轴流式转轮应有以下记录以下零部件需有材料的机械性能和化学成分分析的试验报告蜗壳采用高强度合金钢材料时钢材时水轮发电机检查依据检查项目定子对分瓣制造的定子定子槽楔紧度并头套采用环氧浇灌时检查汇流母线的成形尺转子磁轭冲片表面平整转子连接件采用制动环的厚度推力轴承和导轴承推力头如需与主轴套装时镜板与推力头同轴度检查销钉的配合情况在拆除压具的情况下对弹簧支撑的推力轴承机架机架预装检查各合缝面间隙上机架与定子预装制动器制动器耐压试验后应将管口用丝堵封好励磁机其他各种测温元件试验应提供的检查记录和试验记录调速器及油压装置检验依据调速器及油压装置出厂检验除应符合总则水轮机电液调节系统及装置技术规程油压装置检验项目油冷却器螺旋泵电动机组联轴节联结油压装置各油压和油位信号整定值校验油压装置严密性试验检验后飞摆加工装配主配压阀装配后缓冲器加工装配装配后电液转换器加工装配协联机构加工装配飞摆特性试验缓冲器特性试验电液转换器特性试验各机构表计的检验电气液压调速器的电气装置检验项目各单元特性试验和整定参数刻度校验调速系统厂内试验检查项目电液转换器静特性试验电液伺服阀与中间接力器静特性试验检查永态转差系数调速系统静特性试验试验应分别在永态转差系数计算测至主接力器的转速死区并校验具有双重调节的水轮机调速系统检查随动系统不准确度管路检验项目进水阀适用范围检验依据大中型水轮机进水阀门基本技术条件蝴蝶阀检查项目阀体活门轴瓦空气围带蝴蝶阀装配球形阀检查项目活门前后止漏环轴瓦球形阀装配操作接力器空气阀旁通阀及管路伸缩节配套自动化元件适用范围检查试验项目外观检查可控硅励磁装置检验依据大中型水轮发电机静止整流励磁系统及装置技术条件检验项目工艺检查可控硅等必须符合绝缘电阻测定与介电强度试验自动励磁调节器各单元静态特性检查功率整流装置试验随同设备向用户提供至随同设备向用户提供关于本标准的几点说明考因为验收工作要在安装在条文中也增加了蜗壳的厂内拼装问题用户希望全部预装现规定第一台全部预但在一和机械部东方电机厂意见为附加说明本标准主要起草人。
工频汽油发电机组抽检细则

xx市产品质量监督抽查实施细则xxXZ 071801.1—2014工频汽油发电机组XXXX—XX—XX发布 XXXX—XX—XX实施xx市质量技术监督局工频汽油发电机组产品质量监督抽查实施细则1 范围本细则适用于工频汽油发电机组产品质量xx市监督抽查,针对特殊情况的全市专项监督抽查、区县质量技术监督部门组织的监督抽查可参照执行。
监督抽查产品范围包括各种型号规格的工频汽油发电机组。
本细则内容包括工频汽油发电机组产品分类、术语和定义、企业规模划分、检验依据、抽样、检验要求、判定原则、异议处理复检、附则及编制说明。
注:针对特殊情况的专项监督抽查是指应急工作需要而进行的或者由于某种特殊情况(或原因)仅需要对部分项目进行抽样检验的专项监督抽查。
2 产品分类2.1 产品分类及代码产品分类及代码见表1 。
表1 产品分类及代码产品分类一级分类二级分类三级分类分类代码07.00.00 07.18.00 07.18.01分类名称工业生产资料通用设备汽油发电机组2.2产品种类本细则适用于由往复式内燃( RIC)发动机、交流(a.c.)发电机、控制装置和辅助设备组成的额定频率为50 Hz、发动机为汽油机的工频汽油发电机组,60 Hz的机组可参照使用。
3 术语和定义本细则中未列出的术语和定义同相关引用标准4 企业规模划分根据工频汽油发电机组产品行业的实际情况,生产企业规模以工频汽油发电机组产品年销售额为标准划分为大、中、小型企业。
见表2。
表2 企业规模划分企业规模大型企业中型企业小型企业销售额/万元≥30000 ≥3000且<30000 <30005 检验依据凡是注日期的文件,其随后所有的修改单(不包括勘误的内容)或修改版不使用于本细则。
凡是不注日期的引用文件,其最新版本适用于本细则。
JB/T 10304-2001 工频汽油发电机组技术条件GB/T 2820.1-2009 往复式内燃机驱动的交流发电机组第1部分:用途、定额和性能GB/T 2820.4-2009 往复式内燃机驱动的交流发电机组第4部分:控制装置和开关装置GB/T 2820.5-2009 住复式内燃机驱动的交流发电机组第5部分:发电机组GB/T 2820.6-2009 往复式内燃机驱动的交流发电机组第6部分:试验方法GB/T 2820.8-2002 往复式内燃机驱动的交流发电机组第8部分:对小功率发电机组的要求和试验GB/T 2820.9-2002 往复式内燃机驱动的交流发电机组第9部分:机械振动的测量和评价GB/T 2820.10-2002往复式内燃机驱动的交流发电机组第10部分:噪声的测量(包面法) 经备案现行有效的企业标准及产品明示质量要求相关的法律法规、部门规章和规范6 抽样6.1抽样型号或规格按本细则2.2条所列出的产品种类抽取样机。
出厂电机检验规范
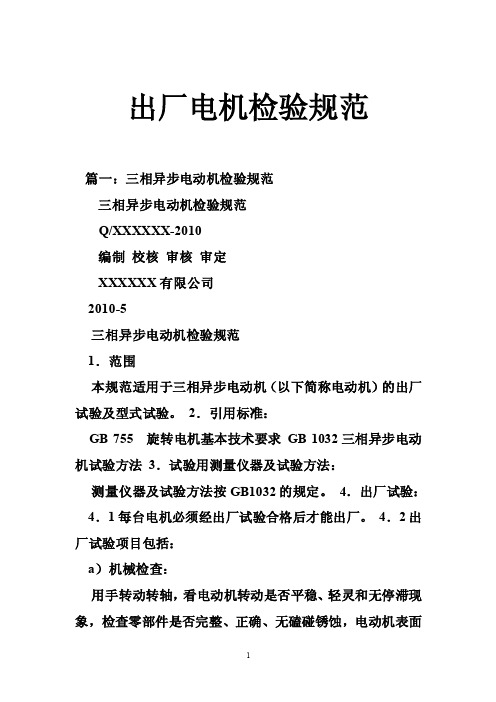
出厂电机检验规范篇一:三相异步电动机检验规范三相异步电动机检验规范Q/XXXXXX-2010编制校核审核审定XXXXXX有限公司2010-5三相异步电动机检验规范1.范围本规范适用于三相异步电动机(以下简称电动机)的出厂试验及型式试验。
2.引用标准:GB 755 旋转电机基本技术要求GB 1032三相异步电动机试验方法3.试验用测量仪器及试验方法:测量仪器及试验方法按GB1032的规定。
4.出厂试验: 4.1每台电机必须经出厂试验合格后才能出厂。
4.2出厂试验项目包括:a)机械检查:用手转动转轴,看电动机转动是否平稳、轻灵和无停滞现象,检查零部件是否完整、正确、无磕碰锈蚀,电动机表面油漆干燥完整、均匀、无污损、碰坏、裂痕等现象。
b)定子绕组对机壳及绕组相互间绝缘电阻的测定:电动机绝缘电阻在实际冷状态时应不低于1MΩ,在热状态或温升试验结束后,应不低于0.38 MΩ(额定电压为380V)或0.66 MΩ(额定电压为660V)。
高压电机绝缘电阻值按技术条件规定。
c)定子绕组实际冷状态下直流电阻的测定:电动机测得任何一相电阻与三相平均值的偏差应不大于三相平均值的3%,测试值应符合HD·R-01-063规定。
d)空载电流和损耗的测定:电动机测得的三相空载电流中任一相与三相平均值的偏差应不大于相平均值的10%,测试值应符合HD·R-01-063规定。
e)堵转电流和损耗的测定:在电动机额定电流值附近的一点测量(电压约在80~100V),测试值应符合HD·R-01-063规定。
f)匝间绝缘试验:试验电压峰值按表1规定。
表1g)噪声、振动检查:噪声凭听觉,电动机运转时应无异常声音,振动凭手感,如发现异常噪声与振动时,应用噪声仪器和振动仪测定。
每年必须对每个型号的电机进行一次抽查,按规定进行噪声和振动试验。
h)耐电压试验:试验电压的频率为50Hz,并尽可能为正弦波。
试验电压按表2。
表2i)转向检查:在出线端标志字母顺序与三相电源相序方向相同时,从主轴伸端视之,电动机就顺时针方向转。
水轮发电机组设备出厂检验一般规定

水轮发电机组设备出厂检验一般规定DL443—911991-10-28发布1992-04-01实施中华人民共和国能源部发布1总则1.1本办法主要适用于额定容量为10~300MW的混流式和轴流式水轮发电机组及其附属设备的制造质量的出厂检验,额定容量大于或小于此范围的或其他型式的水轮发电机组及附属设备可参照执行。
产品型式试验的出厂验收办法供需双方可另行商定。
1.2制造质量检验的依据1.2.1经济合同及其所附的产品技术规范书和在合同中指定的专业标准。
1.2.2有关水轮机、水轮发电机及其附属设备的国家标准。
1.2.3制造厂的设计文件、制造图纸。
1.2.4其他双方认可的有关标准。
1.3出厂检验机构由用户驻制造厂监造代表组或临时检验小组作为机组出厂的检验机构。
1.4检验机构的职责1.4.1对合同产品的制造质量实行全面监督。
1.4.2参与或了解重要部件的原材料、铸锻件的材质检验和元器件的筛选检验。
1.4.3了解重要部件的加工、焊接和热处理工艺以及保证质量的措施,并参与质量检查和签证。
1.4.4参与产品主要部件的试验与装配,如电气试验、水压试验、油压试验、联动试验、总装试验和出厂试验等,并对试验结果进行签证。
1.4.5了解产品的设计修改和质量问题的处理情况。
1.4.6了解和检查产品的除锈、油漆和包装发运。
1.4.7需要签证的项目,要及时通知监造代表。
如在完工前未通知监造代表,监造代表有权要求复检或复试。
监造代表审阅检查记录有怀疑时,有权对产品进行抽查,制造厂应主动提供方便和配合。
若制造厂已事先通知监造代表,而监造代表未参加,制造厂不停产等侯,事后一般不重检或重试。
1.5制造厂职责1.5.1向监造代表介绍产品计划安排,重要部件的加工焊接工艺、检验方法和保证质量的措施、设计改进和质量问题的处理情况。
1.5.2在进行1.4.4条主要部件的试验与装配前,通知监造代表参加。
1.5.3提出产品主要部件的加工检验标准和检查试验记录。
出厂电机检验规范
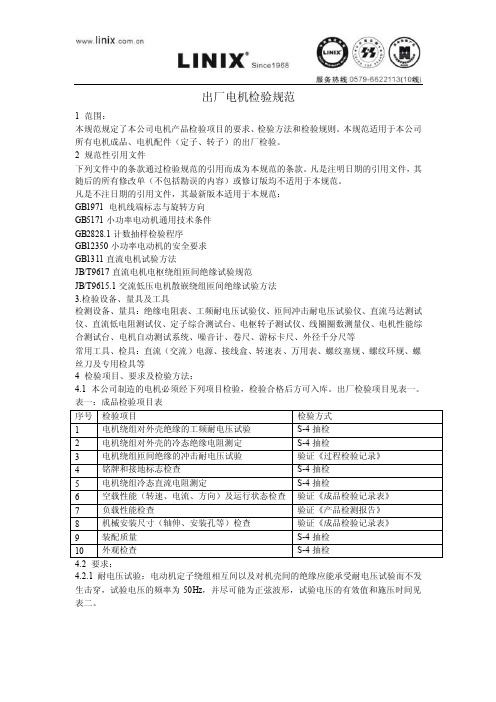
出厂电机检验规范1 范围:本规范规定了本公司电机产品检验项目的要求、检验方法和检验规则。
本规范适用于本公司所有电机成品、电机配件(定子、转子)的出厂检验。
2 规范性引用文件下列文件中的条款通过检验规范的引用而成为本规范的条款。
凡是注明日期的引用文件,其随后的所有修改单(不包括勘误的内容)或修订版均不适用于本规范。
凡是不注日期的引用文件,其最新版本适用于本规范:GB1971 电机线端标志与旋转方向GB5171小功率电动机通用技术条件GB2828.1计数抽样检验程序GB12350小功率电动机的安全要求GB1311直流电机试验方法JB/T9617直流电机电枢绕组匝间绝缘试验规范JB/T9615.1交流低压电机散嵌绕组匝间绝缘试验方法3.检验设备、量具及工具检测设备、量具:绝缘电阻表、工频耐电压试验仪、匝间冲击耐电压试验仪、直流马达测试仪、直流低电阻测试仪、定子综合测试台、电枢转子测试仪、线圈圈数测量仪、电机性能综合测试台、电机自动测试系统、噪音计、卷尺、游标卡尺、外径千分尺等常用工具、检具:直流(交流)电源、接线盒、转速表、万用表、螺纹塞规、螺纹环规、螺丝刀及专用检具等4 检验项目、要求及检验方法:4.1 本公司制造的电机必须经下列项目检验,检验合格后方可入库。
出厂检验项目见表一。
表一:成品检验项目表4.2.1耐电压试验:电动机定子绕组相互间以及对机壳间的绝缘应能承受耐电压试验而不发生击穿,试验电压的频率为50Hz,并尽可能为正弦波形,试验电压的有效值和施压时间见表二。
表二:耐电压试验试验电压有效值电机额定电压注:U 为电机额定电压,U G为耐电压试验有效电压值,当图纸有具体说明时,耐电压值和泄漏电流按图纸规定执行。
4.2.2电机定(转)子绕组对机壳间的冷态绝缘电阻测定:电动机定子绕组(主、副相绕组)相互间以及对机壳间的绝缘电阻在常温冷态下用绝缘电阻表(当电机电压小于36V时选用250伏绝缘电阻表,当电压大于36V时用500V)测定,其绝缘电阻应不低于50MΩ。
单相柴油发电机组出厂试验规范
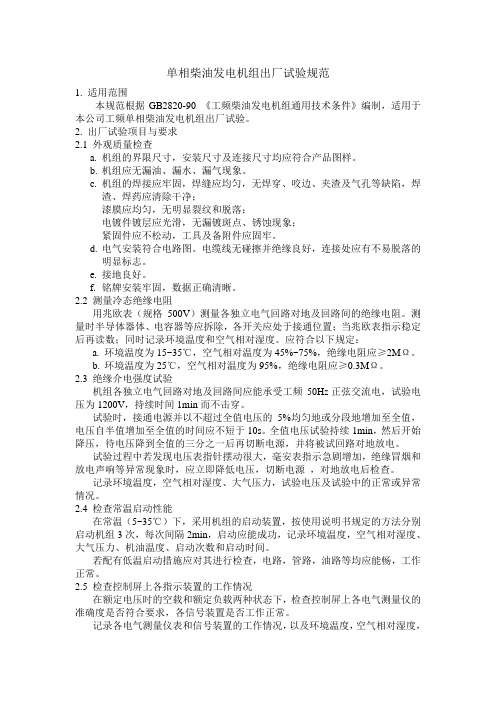
单相柴油发电机组出厂试验规范1. 适用范围本规范根据GB2820-90 《工频柴油发电机组通用技术条件》编制,适用于本公司工频单相柴油发电机组出厂试验。
2. 出厂试验项目与要求2.1 外观质量检查a.机组的界限尺寸,安装尺寸及连接尺寸均应符合产品图样。
b.机组应无漏油、漏水、漏气现象。
c.机组的焊接应牢固,焊缝应均匀,无焊穿、咬边、夹渣及气孔等缺陷,焊渣、焊药应清除干净;漆膜应均匀,无明显裂纹和脱落;电镀件镀层应光滑,无漏镀斑点、锈蚀现象;紧固件应不松动,工具及备附件应固牢。
d.电气安装符合电路图。
电缆线无碰擦并绝缘良好,连接处应有不易脱落的明显标志。
e.接地良好。
f.铭牌安装牢固,数据正确清晰。
2.2测量冷态绝缘电阻用兆欧表(规格500V)测量各独立电气回路对地及回路间的绝缘电阻。
测量时半导体器体、电容器等应拆除,各开关应处于接通位置;当兆欧表指示稳定后再读数;同时记录环境温度和空气相对湿度。
应符合以下规定:a.环境温度为15~35℃,空气相对温度为45%~75%,绝缘电阻应≥2MΩ。
b.环境温度为25℃,空气相对温度为95%,绝缘电阻应≥0.3MΩ。
2.3绝缘介电强度试验机组各独立电气回路对地及回路间应能承受工频50H Z正弦交流电,试验电压为1200V,持续时间1min而不击穿。
试验时,接通电源并以不超过全值电压的5%均匀地或分段地增加至全值,电压自半值增加至全值的时间应不短于10s。
全值电压试验持续1min,然后开始降压,待电压降到全值的三分之一后再切断电源,并将被试回路对地放电。
试验过程中若发现电压表指针摆动很大,毫安表指示急剧增加,绝缘冒烟和放电声响等异常现象时,应立即降低电压,切断电源,对地放电后检查。
记录环境温度,空气相对湿度、大气压力,试验电压及试验中的正常或异常情况。
2.4检查常温启动性能在常温(5~35℃)下,采用机组的启动装置,按使用说明书规定的方法分别启动机组3次,每次间隔2min,启动应能成功,记录环境温度,空气相对湿度、大气压力、机油温度、启动次数和启动时间。
汽油机组出厂检验规定

福建泰格动力机械有限公司汽油发电机组性能检测规范TG-JS88-2005本标准适用于950、900、850、800、750、700、650、600、851、801 系列汽油发电机组的机械检查和电气性能检验一、检验项目1、空载电压、频率检验2、负载电压、频率检验3、噪音检验二、技术要求1. 空载电压、频率检验空载时频率为52Hz~56Hz,60Hz时为60~64Hz,电压为≤270V2. 负载电压、频率检验负载功率为950和900为≥720W,850和800为≥550W,700和750为≥500W,600和650为≥450W,851和801为≥650W负载时频率为≥49Hz,60Hz时为≥59Hz,电压为210~240V3.空载和负载时应无异常声音。
4.各绕组对地应能耐电压1500V历时1秒钟不击穿。
三、检验方法1. 空载电压、频率检验a.检查各插件连接牢固后,电源插头插入面板上的电源插座,进油管接入进油开关,打开油开关,使停机开关处于“ON”状态,用手快速拉动起动绳,使动力起动,启动不超过5次。
用耳朵听是否有异常声音。
b.用螺丝刀调整调速螺钉,使频率在52Hz~56Hz, 60Hz时为60~64Hz,电压≤270V,观察化油器油门是否会摆动,若摆动应进行调整,无法调整的应判为不合格。
2. 负载电压、频率、功率检验a. 按下负载按钮,负载功率为950和900为≥720W,850和800为≥550W,700和750为≥500W,600和650为≥450W,851和801为≥650W负载时频率为≥49Hz,60Hz时为≥59Hz,电压为210~240V 时间为不少于二分钟b. 按空载按钮,化油器油门摆动次数应不高于5次,检查电压和频率应符合空载时的标准。
c.用螺丝刀旋开化油器上放油螺丝,放干油后旋紧放油螺钉。
d.不合格品的应用粉笔在导风罩上写上不合格项目。
3.机械、电气部分检查a.气缸盖与气缸体之间是否漏气;b.火花塞密封垫与气缸盖之间是否漏气;c.曲轴箱是否漏气;d.化油器、进气阀与箱体是否漏气;e.发电机是否磨底;f.大小油封是否漏油;g.电压表是否偏差;h.消声器是否平整、不倾斜;i.电气插头是否牢固,不脱落;j.过流开关是否跳开;k.其余项目见<<汽油发电机组出厂检验记录单>>四、噪音检验(为试验员抽检)a.汽油机中心前后左右各1米,测量噪音;b.普通汽油机噪音检验不高于84分贝,低噪音检验不高于81分贝;c.噪音检验时环境不高于70分贝;d.汽油机噪音检验不得有敲缸、曲轴滚针、轴承、启动罩等机械声响。
柴油发电机组(含高压柴油发电机组)的出厂试验检验指导书
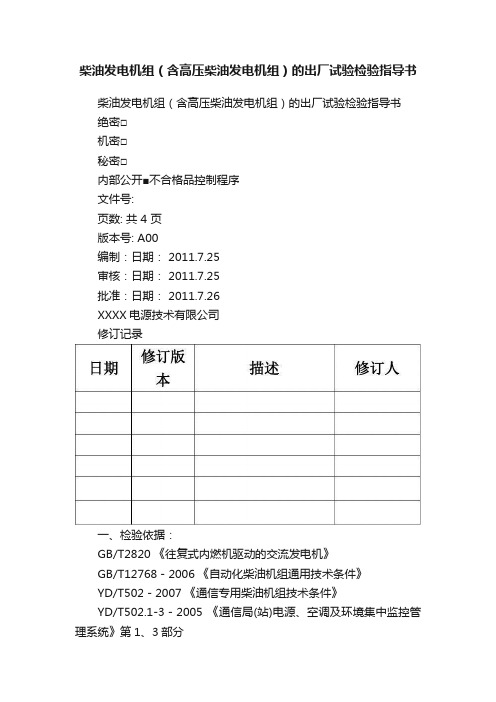
柴油发电机组(含高压柴油发电机组)的出厂试验检验指导书柴油发电机组(含高压柴油发电机组)的出厂试验检验指导书绝密□机密□秘密□内部公开■不合格品控制程序文件号:页数: 共 4 页版本号: A00编制:日期: 2011.7.25审核:日期: 2011.7.25批准:日期: 2011.7.26XXXX电源技术有限公司修订记录一、检验依据:GB/T2820 《往复式内燃机驱动的交流发电机》GB/T12768-2006 《自动化柴油机组通用技术条件》YD/T502-2007 《通信专用柴油机组技术条件》YD/T502.1-3-2005 《通信局(站)电源、空调及环境集中监控管理系统》第1、3部分GB/T13032-1991 《船用柴油发电机组通用技术条件》GB/T20136-2006 《内燃机电站通用试验方法》二、适用范围:适用于本厂生产的2000kW以下,额定频率为50Hz/60 Hz的柴油发电机组(含高压柴油发电机组)的出厂试验检验。
三、编制目的:对柴油发电机组出厂试验检验涉及的内容项目及要求等作出规范化的规定,明确柴油发电机组出厂试验检验内容项目和要求,用于指导柴油发电机组出厂试验检验。
四、机组开机前质量检查:按水箱、油机、控制屏、发电机、底盘的顺序逐一检查机组的外观质量、接线质量、铭牌、零部件质量和总体质量、接地检查、认证产品的一致性检查(通信专用机组)等。
4.2接线质量检查:各连线接触良好,紧固牢靠,标志清楚,布线合理,连接正确。
机组的电气安装应符合电路图,机组控制屏接线端子的相序从屏正面看应自左到右或自上至下排列。
各线连接处应有不易脱落的明显标志,积极标牌如铭牌、方向牌、接地牌等设置牢固,内容清晰准确,并设置良好的接地端子。
4.3铭牌检查:机组铭牌、发电机铭牌、柴油机铭牌应在明显位置,铭牌数据应符合生产技术方案要求,内容齐全、数据完整、正确。
机组铭牌应包括下列内容:a.机组名称;h额定电流;b.机组型号;i.额定功率因数;c.相数;j.质量,Kg;d.额定转速,r/min;k.生产厂名;e.额定频率,Hz;l.机组编号;f.额定功率,KW;m.出厂日期;g.额定电压,V;n.标准代号及编号;4.4零部件质量:柴油机、发电机、控制屏等部件及零件均应完好无损,表面无明显划痕、裂纹,控制屏仪表无损坏,表面清洁;4.5总体质量:各部件之间固定、连接可靠,整机无漏装零部件,无漏装螺母、垫圈等现象。
风力发电机组验收标准

国电电力山西新能源开发有限公司风力发电机组验收规范为确保风力发电机组在现场安装调试完成后,综合检验风电机组的安全性、功率特性、电能质量、可利用率和噪声水平,并形成稳定生产能力,制定本验收标准。
一、编制依据:1、风力发电机组验收规范 GB/T20319-20062、建筑工程施工质量验收统一标准GB503003、风力发电场项目建设工程验收规程 DL/T5191-20044、电气设备交接试验标准GB501505、电气装置安装工程接地装置施工及验收规范GB501696、电气装置安装工程盘、柜及二次回路结线施工及验收规范GB501717、电气装置安装工程低压电器施工及验收规范GB502548、电器安装工程高压电器施工及验收规范GBJ1479、建筑电气工程施工质量验收规范GB5030310、风力发电厂运行规程DL/T66611、电力建设施工及验收技术规程DL/T500712、联合动力风电机组技术说明书、使用手册和安装手册13、风电机组订货合同中的有关技术性能指标要求14、风力发电机组塔架及其基础设计图纸与有关标准二、验收组织机构风电机组工程调试完成后,建设单位组建验收领导小组,设组长1名、副组长4名、组员若干名,由建设、设计、监理、施工、安装、调试、生产厂家等有关单位负责人及有关专业技术人员组成。
三、验收程序1 现场调试(1)风力发电机组安装工程完成后,设备通电前应符合下列要求:(a)现场清扫整理完毕;(b)机组安装检查结束并经确认(内容见附表1);(c)机组电气系统的接地装置连接可靠,接地电阻经检测符合机组的设计要求(小于4欧姆);(d) 测定发电机定子绕组、转子绕组的对地绝缘电阻,符合机组的设计要求;(e) 发电机引出线相序正确,固定牢固,连接紧密;(f) 照明、通讯、安全防护装置齐全。
(2) 机组启动前应进行控制功能和安全保护功能的检查和试验,确认各项控制功能好安全保护动作准确、可靠。
(3) 检查设定风力发电机组控制系统的参数,控制系统应能完成风力发电机组的正常运行控制。
GB2820-90工频柴油发电机组通用技术条件

GB2820-90工频柴油发电机组通用技术条件1 主题内容与运用范畴本标准规定了额定功率为1~3150kw工频柴油发电饥组的技术要求、试验方法、检验规则、标志、包装及贮运要求。
本标准适用于额定频率为50Hz、原动机为柴油机的固定式发电机组(以下简称机组)。
注:可供60Hz机组参考使用。
2 引用标准GB 146.1 标准轨距铁路机车车辆限界GB 146.2 标准轨距铁路建筑限界GB 755 旋转电机差不多技术要求GB l105 内燃机台架性能实验方法GB 1859 内燃机噪声测定方法GB 2423.4 电工电子产品差不多环境试验规程试验Db:交变湿热试验方法GB 2423.16 电工电子产品差不多环境试验规程试验J:长霉试验方法GB 3907 工业无线电干扰差不多测量方法GB 5320 内燃机电站名词术语GB l2699 工频柴油发电机组额定功率、电压及转速ZB J91 005内燃发电机组轴系扭转振动的限值及测量方法JB 8 产品标牌3 术语按GB 5320。
4 技术要求4.1 总则4.1.1 机组应符合本标准规定;应按GB 12699规定制造。
机组的额定功率因数为0.8(滞后).单相讥组承诺为0.9(滞后)或1.0。
4.1.2 机组的各配套件,本标准未作规定者,应符合各自的技术条件规定。
4.1.3 对机组有专门要求时,应在产品技术条件中补充规定。
4.2 工作条件4.2.1 机组在符合GB II05规定的标准环境状况下应能输出额定功率。
4.2.2 机组在下述条件下应能输出规定功率并可靠地工作。
a . 海拔高度分别不超过1000m.2000m.3000m、4000m;b.环境温度:上限值分别为40℃、45℃;下限值分别为5℃、一15℃、一25℃、一40℃;c. 空气相对湿度及其它应符合表1规定表1注:1)指该月的月平均最低温度为25℃,月平均最低温度是指该月每天最低温度的月平均值。
2)指该月的月平均最高温度为40℃、月平均最高温度是指该月每天最高温度的月平均值。
发电机检验规范

1.主题内容及适用范围:本规范规定了ST单相交流同步发电机和STC交流同步发电机的出厂检验项目及试验方法。
本规范适用于ST系列单相交流同步发电机和STC系列交流同步发电机,凡属ST系列和STC系列发电机所派生的产品均可参照执行。
2.引用标准:JB/T3320.2-2000《小型单相同步发电机技术条件》JB/T8981-1999《有刷三相同步发电机技术条件》GB/T14481-93《单相同步电机试验方法》GB/T1029-2005《三相同步电机试验方法》3.检验项目:1)机械检验2)各独立电气回路对机壳及其相互间冷态绝缘电阻的测定;3)绕组在实际冷确状态下直流电阻的测定;4)耐压试验5)冷态空载电压整定范围的检查;6)冷态稳态电压调整率的测定;7)超速试验8)短时升高电压试验;4.检验方法:4.1 机械检查:4.1.1 外观检查发电机的装配是否完整正确,各部位紧固件是否上紧,引出线排列是否整齐、端正,固定牢靠,以及各绕组标识是否正确。
4.1.2 转动检查:1)用手转动转子轴伸,旋转是否灵活,无异响。
碳刷与滑环是否接触到位。
2)发电机在空转运行时,(低速、未充磁情况下)轴承应平稳轻快、无停滞现象,声音均匀和谐,而无有害的杂音。
4.2 各独立电气回路对机壳及其相互间冷态绝缘电阻的测定:用于500V兆欧表测量各独立电气回路对机壳及绕组相互间绝缘电阻不低于20MΩ(冷态)4.3 绕组在实际冷态下直流电阻的测定。
采用电桥法测量各绕组和转子绕组的冷态直流电阻应在规定范围内,即误差不超过3%,(此项测量结果同规格型号许5台之中只记录1台数值)4.4耐电压试验:各发电机各绕组对机壳及主副绕组间应承受下表规定的耐电压试验而无击穿现象,试验电压频注:1)半导体器件不做此项试验,试验时应断开器件与绕组之间的联结。
2)以上两种试验方法任选一种。
4.5冷态空载电压整定范围的检查:发电机建压后,调到空载转速,调整瓷盘变阻器,读取电压的最大值和最小值,最大值要大于105%UN(额定电压),最小值小于95%UN。
出厂电机检验规范精品word

精品word出厂电机检验规范1 范围:本规范规定了本公司电机产品检验项目的要求、检验方法和检验规则。
本规范适用于本公司所有电机成品、电机配件(定子、转子)的出厂检验。
2 规范性引用文件下列文件中的条款通过检验规范的引用而成为本规范的条款。
凡是注明日期的引用文件,其随后的所有修改单(不包括勘误的内容)或修订版均不适用于本规范。
凡是不注日期的引用文件,其最新版本适用于本规范:GB1971 电机线端标志与旋转方向GB5171小功率电动机通用技术条件GB2828.1计数抽样检验程序GB12350小功率电动机的安全要求GB1311直流电机试验方法JB/T9617直流电机电枢绕组匝间绝缘试验规范JB/T9615.1交流低压电机散嵌绕组匝间绝缘试验方法3.检验设备、量具及工具检测设备、量具:绝缘电阻表、工频耐电压试验仪、匝间冲击耐电压试验仪、直流马达测试仪、直流低电阻测试仪、定子综合测试台、电枢转子测试仪、线圈圈数测量仪、电机性能综合测试台、电机自动测试系统、噪音计、卷尺、游标卡尺、外径千分尺等常用工具、检具:直流(交流)电源、接线盒、转速表、万用表、螺纹塞规、螺纹环规、螺丝刀及专用检具等4 检验项目、要求及检验方法:4.1 本公司制造的电机必须经下列项目检验,检验合格后方可入库。
出厂检验项目见表一。
4.2 要求:4.2.1耐电压试验:电动机定子绕组相互间以及对机壳间的绝缘应能承受耐电压试验而不发生击穿,试验电压的频率为50Hz,并尽可能为正弦波形,试验电压的有效值和施压时间见表二。
部分内容来源于网络,如有侵权请联系删除!注:U 为电机额定电压,U G为耐电压试验有效电压值,当图纸有具体说明时,耐电压值和泄漏电流按图纸规定执行。
4.2.2电机定(转)子绕组对机壳间的冷态绝缘电阻测定:电动机定子绕组(主、副相绕组)相互间以及对机壳间的绝缘电阻在常温冷态下用绝缘电阻表(当电机电压小于36V时选用250伏绝缘电阻表,当电压大于36V时用500V)测定,其绝缘电阻应不低于50MΩ。
- 1、下载文档前请自行甄别文档内容的完整性,平台不提供额外的编辑、内容补充、找答案等附加服务。
- 2、"仅部分预览"的文档,不可在线预览部分如存在完整性等问题,可反馈申请退款(可完整预览的文档不适用该条件!)。
- 3、如文档侵犯您的权益,请联系客服反馈,我们会尽快为您处理(人工客服工作时间:9:00-18:30)。
对应的旧标准:SD342-89水轮发电机组设备出厂检验一般规定DL443—911991-10-28发布1992-04-01实施中华人民共和国能源部发布1总则1.1本办法主要适用于额定容量为10〜300MW的混流式和轴流式水轮发电机组及其附属设备的制造质量的出厂检验,额定容量大于或小于此范围的或其他型式的水轮发电机组及附属设备可参照执行。
产品型式试验的出厂验收办法供需双方可另行商定。
1.2制造质量检验的依据1.2.1经济合同及其所附的产品技术规范书和在合同中指定的专业标准。
1.2.2有关水轮机、水轮发电机及其附属设备的国家标准。
1.2.3制造厂的设计文件、制造图纸。
1.2.4其他双方认可的有关标准。
1.3出厂检验机构由用户驻制造厂监造代表组或临时检验小组作为机组出厂的检验机构。
1.4检验机构的职责1.4.1对合同产品的制造质量实行全面监督。
1.4.2参与或了解重要部件的原材料、铸锻件的材质检验和元器件的筛选检验。
1.4.3了解重要部件的加工、焊接和热处理工艺以及保证质量的措施,并参与质量检查和签证。
1.4.4参与产品主要部件的试验与装配,如电气试验、水压试验、油压试验、联动试验、总装试验和出厂试验等,并对试验结果进行签证。
1.4.5了解产品的设计修改和质量问题的处理情况。
1.4.6了解和检查产品的除锈、油漆和包装发运。
1.4.7需要签证的项目,要及时通知监造代表。
如在完工前未通知监造代表,监造代表有权要求复检或复试。
监造代表审阅检查记录有怀疑时,有权对产品进行抽查,制造厂应主动提供方便和配合。
若制造厂已事先通知监造代表,而监造代表未参加,制造厂不停产等侯,事后一般不重检或重试。
1.5制造厂职责1.5.1向监造代表介绍产品计划安排,重要部件的加工焊接工艺、检验方法和保证质量的措施、设计改进和质量问题的处理情况。
1.5.2在进行1.4.4条主要部件的试验与装配前,通知监造代表参加。
1.5.3提出产品主要部件的加工检验标准和检查试验记录。
凡需监造代表签证的部件应提供正式记录。
1.5.4为监造代表提供工作方便。
1.5.5经监造代表检验签证的项目,制造厂仍应对其质量负全部责任。
1.6凡能整体运输的部件都在工厂内组装完整,调试合格整体发运。
不能整体运输的部件,是否在厂内预装由双方协议商定。
1.7试验合格的部(套)件及自动化元器件,按“水轮发电机组包装、运输、保管技术条件”进行包装、发运、检查、存放。
在一年内或双方协议的日期内安装,制造厂应保证在工地不需再分解清扫,设备应能投入正常运行。
1.8制造厂自制及外购的元器件、所有部件,在总体合同保证期内发生质量问题,由制造厂无偿修复或更换。
2水轮机2.1检验依据水轮机产品的检验,除应符合总则1.2中规定外,还应符合下列标准:2.1.1DL445—91《水轮机基本技术规范》2.1.2《水轮机通流部件验收标准》。
2.2检查项目2.2.1尾水管里衬2.2.1.1整体制作的尾水管里衬,应测量上、下管口直径、圆度、周长和高度。
2.2.1.2大型尾水管里衬组装后应测量各环节高度、直径以及内部加固情况。
2.2.1.3进人门应进行装配检查各配合尺寸。
2.2.21)转轮室:2.2.2.1铸焊件的缺陷及修补情况。
2.2.2.2抗空蚀层的铺焊质量及加工后的厚度、粗糙度。
2.2.2.3中环内径、高度、粗糙度、焊缝质量以及有关配合尺寸等加工情况。
2.2.2.4上、中、下三环预装时,各部错口、螺孔的对位以及X、Y 线标记。
注:1)驻厂监造代表签证的项目(下同)。
2.2.3座环:2.2.3.1与顶盖、底环配合面的相对高度、直径和平行度。
2.2.3.2分瓣座环应进行预装,检查合缝面间隙、错口、螺孔、销子等配合情况。
2.2.3.3固定导叶内、外切圆直径以及进口节距、高度。
在工地组装的导叶,检查导叶上、下平面和平行度。
2.2.3.4过流表面的平滑性及粗糙度。
2.2.4蜗壳:2.2.4.11)各电站第一台机组的焊接蜗壳,各节应在厂内预装,检查各节编号、对装情况和焊缝检查记录,必要时可指定部位探伤抽查。
以后各台可部分预装。
2.2.4.2各节开口、腰长、最高点与最低点的直径,最远点及进水管中心线与机组中心线的距离,接缝间隙及内壁错口,抽查各节中心偏差值。
2.2.4.3整体铸造蜗壳的水压试验和整体焊接蜗壳的水压试验。
2.2.4.4蜗壳进人门装配完整情况。
2.2.5机坑里衬:抽查上、下口圆度、垂直度、焊缝及加固情况。
2.2.6导叶:2.2.6.1导叶高度。
2.2.6.2过流面粗糙度及型线。
2.2.6.3导叶立面密封压板及螺钉配合情况。
2.2.7顶盖:2.2.7.1与座环配合段的高度、直径。
2.2.7.2止漏环内径及圆度。
2.2.7.3法兰下面与过流面的高度尺寸及平行度。
2.2.7.4分辨顶盖合缝面间隙。
2.2.7.5焊接顶盖的焊缝外观质量。
2.2.7.6抗磨板紧固情况。
2.2.7.7橡胶密封压板紧固情况。
2.2.8支持盖:2.2.8.1总高度。
2.2.8.2上平面至导轴承安装面高度。
2.2.8.3过流面光滑度。
2.2.8.4合缝面间隙。
2.2.8.5中锥底面与上平面距离,底端柱面直径及圆度。
2.2.9底环:2.2.9.1顶盖、底环导叶轴孔同轴度(或划线及镗孔准确性)。
2.2.9.2与座环(或基础环)配合面到过流面的高度及平行度。
2.2.9.3抗磨板紧固情况。
2.2.9.4过流面粗糙度。
2.2.9.5橡胶密封压板紧固情况。
2.2.101)导水机构厂内总装配:2.2.10.1导叶端部总间隙。
2.2.10.2导叶全关时的立面间隙。
2.2.10.3导叶转动灵活性。
2.2.10.4双连臂、连杆长度偏差。
2.2.10.5导叶最大开口值。
2.2.10.6导叶上轴颈与轴套间隙。
2.2.10.7所有装配孔的对位及各部件编号情况。
2.2.10.8导叶关闭时立面接触位置。
2.2.11检查导水机构装配部件对基准件的中心偏差,以及钻铰安况。
装用定位销钉孔的情2.2.12上、下固定止漏环与转动止漏环如在厂内套装时,检查圆度及总间隙。
2.2.131)混流式转轮:2.2.13.1与主轴配合止口直径、法兰平面端面跳动量及粗糙度。
2.2.13.2上、下止漏环直径及圆度。
2.2.13.3抗磨、抗空蚀部位的补焊质量、波浪度及粗糙度。
2.2.13.4叶片叶型。
2.2.13.5叶片进口角和出口角。
2.2.13.6叶片出水边平均开口偏差。
2.2.141)轴流式转轮厂内装配试验:2.2.14.1活塞与接力器缸间隙。
2.2.14.2枢轴铜瓦间隙。
2.2.14.3叶片螺栓预装情况。
2.2.14.4叶片螺栓与转臂螺栓孔装配情况。
2.2.14.5叶片密封部位粗糙度。
2.2.14.6顶紧环与螺栓卡阻情况。
2.2.14.7叶片正面、背面的波浪度、粗糙度及叶片叶型。
2.2.14.8叶片外圆尺寸及圆度。
2.2.14.9叶片动作试验。
2.2.14.10叶片密封渗漏试验。
2.2.14.11内部刷漆前的检查及刷漆质量。
2.2.15转轮非加工面的平滑性检查。
2.2.161)转轮静平衡试验。
2.2.171)主轴:2.2.17.1主轴长度、轴承段直径及粗糙度。
2.2.17.2上、下端面止口直径及端面跳动量。
2.2.17.3联轴螺栓与螺栓孔配合质量及互换情况。
2.2.17.4一字键选配尺寸或销钉选配情况。
2.2.17.5主轴联接后,同找摆度情况。
2.2.18导轴瓦:2.2.18.1瓦的内径和瓦面粗糙度。
2.2.18.2轴承合金与瓦坯浇合质量。
2.2.18.3筒式瓦的油沟方向。
2.2.18.4测温孔的加工深度。
2.2.18.5铬钢垫装配、压制情况。
2.2.19分块瓦的顶瓦螺套压配、接触情况,螺栓与螺套配合情况。
2.2.20油盆、油箱、水箱等的渗漏试验。
2.2.21抽查冷却器的耐压试验。
2.2.22轴承密封应总装检查各零件的配合尺寸。
2.2.23橡胶制品进行外观检查。
2.2.241)接力器厂内总装:2.2.24.1与行程、缓冲行程有关的尺寸。
2.2.24.2耐压试验检查密封与活塞环渗漏情况。
2.2.24.3接力器动作试验,并测定行程偏差。
2.2.25分油器耐压试验。
2.2.26锁锭或锁锭配压阀动作试验。
2.2.27活塞杆防锈徐层质量。
2.2.28附属设备应抽查:2.2.28.1真空破坏阀、空气阀密封面的渗漏试验。
2.2.28.2真空破坏阀动作试验,并测定开口尺寸。
2.2.28.3蜗壳及尾水管排水阀接力器耐压试验。
2.2.28.4漏油箱渗漏试验。
2.2.29对重要部位的弹簧进行力特性试验抽查。
2.3应提供的检查记录及试验记录2.3.1尾水管里衬拼装时各环节的直径、圆度、高度和相连接的各环节的周长2.3.2转轮室内径、喉部尺寸及有关配合尺寸的检查记录。
2.3.3转轮室相配合端面的高度记录。
2.3.4基础环加工有关配合尺寸的检查记录。
2.3.5座环加工有关配合尺寸的检查记录。
2.3.6蜗壳拼装记录。
2.3.7焊接蜗壳的探伤检查记录。
2.3.8蜗壳的耐压试验记录。
2.3.9底环加工有关配合尺寸的检查记录。
2.3.10顶盖加工有关配合尺寸及止漏环内径的检查记录。
2.3.11支持盖加工有关配合尺寸的检查记录。
2.3.12导叶加工有关配合尺寸的检查记录。
2.3.13导叶总装配时最大开口测量记录。
2.3.14导叶轴套装压后内径测量记录。
2.3.15主轴加工主要尺寸、端面跳动量、轴颈和法兰粗糙度检查记录2.3.16主轴联轴摆度值。
2.3.17轴瓦加工检查记录。
2.3.18分块瓦支顶螺栓头部及铬钢垫的硬度记录。
2.3.19混流式转轮需有以下记录:2.3.19.1叶片进口和出口型线偏差值。
2.3.19.2叶片进口角和出口角偏差。
2.3.19.3叶片出口边厚度偏差。
2.3.19.4叶片进口节距偏差。
2.3.19.5叶片出水边平均开口偏差。
2.3.19.6转轮加工检查记录。
2.3.19.7分瓣转轮接头焊缝坡口尺寸和坡口探伤记录。
2.3.19.8焊接转轮单个叶片正面组合样板检查记录。
2.3.19.9转轮叶片根部焊缝探伤记录。
2.3.20轴流式转轮应有以下记录:2.3.20.1叶片型线检查记录。
2.3.20.2叶片头部型线检查记录。
2.3.20.3叶片出口边缘厚度检查记录。
2.3.20.4转臂加工检查记录。
2.3.20.5枢轴加工检查记录。
2.3.20.6枢轴铜瓦检查记录。
2.3.20.7活塞与接力器缸加工检查记录。
2.3.20.8转轮体加工尺寸检查记录。
2.3.20.9叶片主要加工尺寸检查记录。
2.3.20.10连杆加工尺寸检查记录。
2.3.20.11操作架加工尺寸检查记录。
2.3.20.12叶片外圆尺寸及叶片漏油试验记录。
2.3.20.13叶片装置角检查记录。