反应釜温度控制(DOC)
反应釜温控系统课程设计

反应釜温控系统课程设计一、课程目标知识目标:1. 学生能理解反应釜的基本原理和温度控制的重要性。
2. 学生能掌握反应釜温度控制系统的组成、工作原理及各部分功能。
3. 学生能了解温度传感器、控制器、执行器等关键部件的类型及选用原则。
技能目标:1. 学生能运用所学知识分析反应釜温度控制系统的故障原因并进行排查。
2. 学生能设计简单的反应釜温度控制方案,包括参数设置、设备选型等。
3. 学生能通过实验操作,验证温度控制系统的稳定性和可靠性。
情感态度价值观目标:1. 学生培养对化学反应过程的兴趣,增强对化学工程领域的认识。
2. 学生树立安全意识,认识到温度控制在化学反应过程中的重要性。
3. 学生培养团队协作精神,提高沟通与表达能力,为未来从事相关工作奠定基础。
分析课程性质、学生特点和教学要求,本课程目标旨在使学生在理解反应釜温控系统基本原理的基础上,掌握实际操作和设计能力,同时培养安全意识、团队协作和沟通能力,为未来从事化学工程及相关领域工作打下坚实基础。
通过本课程的学习,学生将能够具备解决实际问题的能力,为我国化学工业的发展贡献力量。
二、教学内容1. 反应釜基本原理及温度控制概述- 介绍反应釜的作用、类型及在化工生产中的应用。
- 阐述温度控制在反应釜操作中的重要性。
2. 反应釜温度控制系统组成与工作原理- 分析温度控制系统的组成部分,包括温度传感器、控制器、执行器等。
- 讲解各部分的工作原理及相互关系。
3. 温度传感器及其选用- 介绍常见温度传感器的类型、特点及应用场景。
- 分析温度传感器的选用原则,包括精度、响应时间等方面。
4. 温度控制器原理与操作- 阐述温度控制器的原理,包括PID控制算法。
- 指导学生操作温度控制器,实现反应釜温度的精确控制。
5. 反应釜温度控制方案设计- 分析反应釜温度控制方案的设计原则,包括设备选型、参数设置等。
- 指导学生设计简单的反应釜温度控制方案。
6. 实验操作与故障排查- 安排实验操作环节,让学生动手验证温度控制系统的稳定性和可靠性。
反应釜降温操作方法
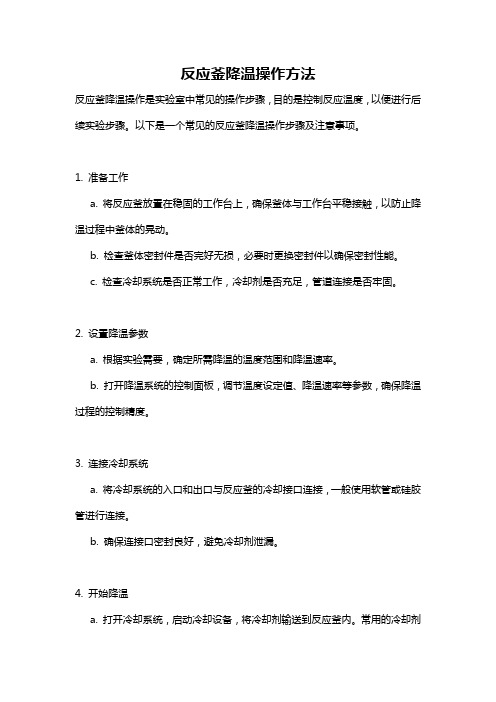
反应釜降温操作方法反应釜降温操作是实验室中常见的操作步骤,目的是控制反应温度,以便进行后续实验步骤。
以下是一个常见的反应釜降温操作步骤及注意事项。
1. 准备工作a. 将反应釜放置在稳固的工作台上,确保釜体与工作台平稳接触,以防止降温过程中釜体的晃动。
b. 检查釜体密封件是否完好无损,必要时更换密封件以确保密封性能。
c. 检查冷却系统是否正常工作,冷却剂是否充足,管道连接是否牢固。
2. 设置降温参数a. 根据实验需要,确定所需降温的温度范围和降温速率。
b. 打开降温系统的控制面板,调节温度设定值、降温速率等参数,确保降温过程的控制精度。
3. 连接冷却系统a. 将冷却系统的入口和出口与反应釜的冷却接口连接,一般使用软管或硅胶管进行连接。
b. 确保连接口密封良好,避免冷却剂泄漏。
4. 开始降温a. 打开冷却系统,启动冷却设备,将冷却剂输送到反应釜内。
常用的冷却剂有冷水、乙二醇、液氮等,具体选择应根据实验需求和反应体系特点来确定。
b. 根据所设定的降温速率,逐步降低冷却剂的温度,以达到实验要求的降温速度。
c. 在降温过程中,可以通过监测反应釜壁温或反应体系温度变化来调节冷却剂的流量和温度,以保持合适的降温速度和稳定的温度控制。
5. 监测和控制a. 在降温过程中,及时监测反应釜壁温,以确保反应釜内温度随预定的降温速率下降。
可以使用温度计、红外线测量仪等设备进行监测。
b. 根据监测数据,及时调节冷却剂的流量和温度,使反应釜内的温度控制在设定的范围内。
注意要避免温度过快或过慢地降低,以免影响实验结果。
6. 完成降温a. 在达到预定的降温温度后,停止冷却系统,关闭冷却剂的供给。
b. 将冷却系统与反应釜分离,并将冷却系统的管路和设备清洗干净,以防止冷却剂残留和污染。
c. 检查反应釜密封性能,确保釜体已经降至所需温度范围内。
d. 取出反应物或继续进行后续实验步骤。
在进行反应釜降温操作时,需要注意以下几点:1. 安全操作。
反应釜操作维护保养规程范本

反应釜操作维护保养规程范本一、引言反应釜是一种常见的化学实验设备,广泛应用于化工、医药、食品等领域。
为了确保反应釜的正常运行和安全使用,制定了本操作维护保养规程,以指导操作人员进行正确的操作和维护保养工作。
二、操作规程1. 操作前准备(1)安全检查:操作人员在进行反应釜操作前必须进行安全检查,确保相关设备和设施安全可靠,检查电源、排风、进出口管路、温度传感器等是否正常。
(2)物料准备:准备所需物料,并按照操作要求进行准确和精确的称量,确保物料的准确性和纯度。
(3)操作规程:操作人员必须熟悉反应釜的操作规程,了解操作流程和关键操作点,严格按照规程进行操作。
2. 填充物料和溶剂(1)选择合适的容器:根据需要填充的物料和溶剂的性质选择合适的容器,并确保容器干净、无杂质。
(2)准确称量:按照配比要求准确称量填充物料和溶剂,并注意安全操作,避免产生气体或溶液溅出。
(3)搅拌混合:使用适当的搅拌器搅拌混合物料和溶剂,确保均匀混合。
3. 温度控制(1)温度传感器安装:将温度传感器正确安装在反应釜内部,保证传感器与物料充分接触,并确保测量准确。
(2)温度调节:根据需要控制反应釜的温度,调节加热器的功率和搅拌器的速度,确保温度的稳定和均匀分布。
(3)温度记录:记录温度的变化,以便后续分析和调整操作参数。
4. 压力控制(1)安全阀设置:根据反应釜的设计压力,设置合适的安全阀,并确保安全阀的正常工作。
(2)压力控制:根据工艺要求和反应过程的变化,调节压力控制阀,确保反应釜内部的压力控制在安全范围内。
(3)压力记录:记录压力的变化,以便后续分析和调整操作参数。
5. 操作完成(1)关闭加热器和搅拌器:在反应完成后,先关闭加热器和搅拌器,停止供热和搅拌。
(2)排空反应釜:将反应釜内的气体和液体排空,确保反应釜内的压力减至零。
(3)清洁与消毒:清洁反应釜内的残留物和污垢,并进行消毒处理,保持反应釜干净卫生。
三、维护保养规程1. 定期检查(1)设备外观:定期检查反应釜的外观,检查是否有异常损坏或腐蚀情况,如果发现问题及时修复或更换。
反应釜 控制方案(一)

反应釜控制方案(一)反应釜控制方案1. 方案背景•反应釜作为化工领域的重要设备,需要进行精确的控制,以确保反应过程的安全和高效。
•在复杂的反应过程中,精确的控制可以提高产品的质量和产量,降低生产成本,减少环境污染。
2. 目标与需求•实现反应釜的自动控制,包括温度、压力、搅拌速度等参数的精确控制和调节。
•提供远程监控和操作的功能,方便运营人员进行实时监测和调整。
3. 方案概述1.硬件选型:–选择具有高精度和可靠性的传感器,如温度传感器、压力传感器和流量传感器,用于实时测量反应釜的各项参数。
–选用高性能的控制器,能够实现多参数的精确控制和调节,同时支持远程通信功能。
–确保与反应釜现有系统的接口兼容性,避免对设备进行过多的改造和调整。
2.软件开发:–开发控制系统的软件,实现对反应釜各项参数的测量、调节和控制。
–实现数据采集和存储功能,用于分析和监测反应过程的变化和趋势。
–开发远程监控和操作的界面,方便运营人员实时查看和控制反应釜的状态。
3.系统集成:–将硬件和软件进行整合和调试,确保系统的稳定性和可靠性。
–进行反应釜的现场调试和测试,解决可能出现的问题和优化系统参数。
–提供培训和技术支持,确保运营人员能够熟练操作和维护控制系统。
4. 实施计划1.硬件选型和采购:2周2.软件开发和调试:4周3.系统集成和现场调试:2周4.培训和技术支持:1周5. 风险与挑战•兼容性问题:确保所选硬件与已有反应釜系统的兼容性,避免出现不匹配或无法集成的情况。
•数据安全:加强系统的数据保护和安全性,避免敏感数据被泄露或篡改。
•反应过程复杂性:对于不同类型的反应釜,需要针对其特点和工艺进行个性化的控制算法开发。
6. 总结通过本方案,我们可以实现对反应釜的精确控制和调节,提高生产效率和产品质量,并实现远程监控和操作的功能。
在保证反应过程安全的前提下,降低生产成本,提升竞争力,并对环境保护做出积极贡献。
7. 实施效果评估•监测产量和产品质量:比较实施方案前后的产量和产品质量数据,评估实施效果。
反应釜温控方案
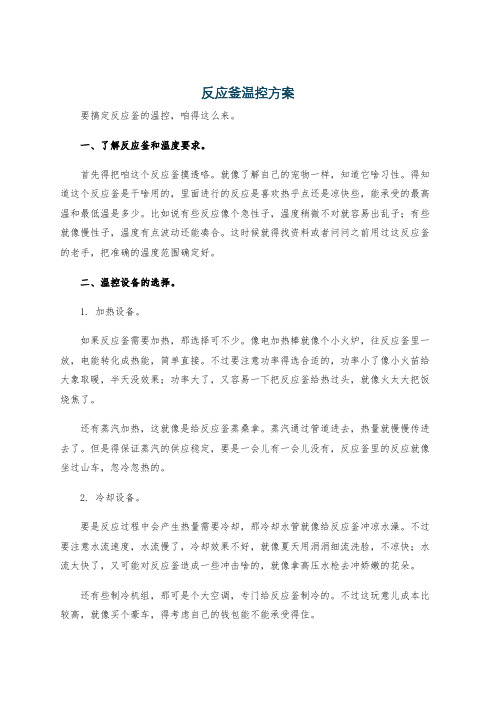
反应釜温控方案要搞定反应釜的温控,咱得这么来。
一、了解反应釜和温度要求。
首先得把咱这个反应釜摸透咯。
就像了解自己的宠物一样,知道它啥习性。
得知道这个反应釜是干啥用的,里面进行的反应是喜欢热乎点还是凉快些,能承受的最高温和最低温是多少。
比如说有些反应像个急性子,温度稍微不对就容易出乱子;有些就像慢性子,温度有点波动还能凑合。
这时候就得找资料或者问问之前用过这反应釜的老手,把准确的温度范围确定好。
二、温控设备的选择。
1. 加热设备。
如果反应釜需要加热,那选择可不少。
像电加热棒就像个小火炉,往反应釜里一放,电能转化成热能,简单直接。
不过要注意功率得选合适的,功率小了像小火苗给大象取暖,半天没效果;功率大了,又容易一下把反应釜给热过头,就像火太大把饭烧焦了。
还有蒸汽加热,这就像是给反应釜蒸桑拿。
蒸汽通过管道进去,热量就慢慢传进去了。
但是得保证蒸汽的供应稳定,要是一会儿有一会儿没有,反应釜里的反应就像坐过山车,忽冷忽热的。
2. 冷却设备。
要是反应过程中会产生热量需要冷却,那冷却水管就像给反应釜冲凉水澡。
不过要注意水流速度,水流慢了,冷却效果不好,就像夏天用涓涓细流洗脸,不凉快;水流太快了,又可能对反应釜造成一些冲击啥的,就像拿高压水枪去冲娇嫩的花朵。
还有些制冷机组,那可是个大空调,专门给反应釜制冷的。
不过这玩意儿成本比较高,就像买个豪车,得考虑自己的钱包能不能承受得住。
三、温度监测。
1. 温度计。
普通的玻璃温度计就像个老实巴交的小兵,便宜又简单。
但是读数不太方便,得凑近了看,而且容易碎,就像个脆弱的小瓷人。
热电偶温度计就高级一些,能把温度信号变成电信号,然后传输到控制系统那里。
就像个小间谍,偷偷把温度情报送出去。
它的精度也比较高,不过也得定期检查校准,不然小间谍也可能传递错误情报呢。
2. 温度传感器。
除了热电偶,还有热电阻传感器之类的。
这些传感器就像一群小侦探,分布在反应釜的各个关键位置,把不同地方的温度都监测到。
化工反应釜控制温度的操作方法

化工反应釜控制温度的操作方法
化工反应釜控制温度的操作方法可以通过以下几个步骤实施:
1. 设定目标温度:根据反应需要和工艺要求,确定反应釜应该维持的目标温度。
2. 开启恒温系统:打开反应釜的恒温系统,确保温度控制回路正常运行。
3. 调节加热功率:根据实际温度和目标温度之间的差异,调节反应釜的加热功率。
如果实际温度低于目标温度,增加加热功率;如果实际温度高于目标温度,降低加热功率。
4. 监控温度变化:持续监控反应釜内的温度变化情况。
可以使用温度传感器和温度控制仪表等设备进行实时监测。
5. 调整控制参数:根据实际情况和温度变化趋势,适时调整温度控制参数,例如调整温度控制器的比例、积分和微分参数,以使温度控制更加精确。
6. 考虑安全性:在控制温度的过程中,要确保反应釜内的温度不超出安全限制,并采取措施防止温度过高或过低,例如使用降温装置或停止加热。
7. 记录数据:及时记录温度变化和控制过程中的关键数据,以便后续分析和改进。
需要注意的是,化工反应釜控制温度的操作方法可能因具体工艺和设备而异,以上步骤仅供参考,在实际操作中需要结合具体情况进行调整和改进。
化工反应釜控制系统

化工反应釜控制系统化工反应釜作为化学反应的主要设备,在一定温度、压力和物质的条件下实现化学反应。
在化工生产过程中,由于反应釜内的化学反应涉及到放热和吸热等过程,因此需要对反应釜进行精确的控制和调节。
为此,化工反应釜控制系统应运而生。
一、化工反应釜控制系统的构成化工反应釜控制系统是由加热系统、压力传感器、流量传感器、液位传感器、温度控制系统、数据采集系统和计算机控制系统等组成的一套完整的系统。
加热系统:加热系统用于反应釜内物质的加热,可分为电加热、蒸汽加热、导热油加热等多种形式。
加热系统的主要作用是提供反应釜内所需的温度。
压力传感器:反应釜内的压力是反应速率的重要因素之一。
因此,要控制反应釜内的压力,就需要使用压力传感器检测反应釜内的压力,再通过计算机控制系统来实现压力的控制。
流量传感器:反应釜内反应物料的进出口需要通过管路进行调节,而流量传感器可以实时监测反应物料的流量,确保反应物料进出的平衡性和恰当性。
液位传感器:液位传感器用于测量反应釜的液位高度,保证反应釜内反应物料在标准液位范围内运行,以免发生溢出或过量情况。
温度控制系统:温度控制系统是化工反应釜控制系统的核心部分。
通过温度控制系统可以实时控制反应物料的温度,确保反应物料在最适温度下进行反应,从而保证反应过程的有效完成。
数据采集系统:数据采集系统用于收集和存储反应釜内的各项参数(如温度、压力、液位、流量等),并将其转换成计算机可处理的信号。
计算机控制系统:计算机控制系统是化工反应釜控制系统的灵魂。
通过对各种传感器监测到的数据进行处理和分析,计算机控制系统可以自动调节反应釜内的温度、压力、流量和液位等参数,实现化学反应的精确控制。
二、化工反应釜控制系统的优势化工反应釜控制系统的优势主要表现在以下几个方面:1. 提高化学反应的安全性。
控制系统可实现对反应釜内压力、温度和液位等参数的实时监测和控制,以确保反应物料在安全的温度、液位和压力下进行反应。
夹套反应釜温度控制浅析

化工设备夹套反应釜温度控制浅析吴康明 李嘉斌(中国天辰化学工程公司黑龙江分公司 150076) 摘 要:在叔十二碳乙硫醇的设计中,采用分程控制系统来保持釜温的稳定并使反应釜的起动和正常生产都能自动操作。
关键词:反应釜;分程控制;气开式;气关式中图分类号:T Q 052 文献标识码:BSimple Explanation for Stillage T emperatureWu Kangming Li Jiabin(China T ianchen Chem ical Enginceing corp.Heilong Jiang Branch 150076)Abstract :During the designing of producing tert -dode -canoic E thylsulfhydrate ,we use the step control system to stabilize the stillage tem perature and to operate the start and normal production of stillage automatically.K eyw ords :S tillage ;S tep control ;Air open ;Air close 在叔十二碳乙硫醇的设计中,夹套反应釜的温度控制是一个难点。
当十二烯等原料及催化剂在反应釜中配置好后,一开始时,需要对反应釜加热,以起动反应过程,反应起动后,因为此化学反应是放热反应,所以会放出大量的热量,为了使反应持续平稳地进行下去,就需要保持釜温的稳定,这样必须要把反应热取走。
在这种场合,若要反应釜的起动和正常生产都能自动操作,就必须要采用分程控制系统。
在简单控制系统中,一个调节器的输出只带动一个调节阀。
而所谓的分程控制系统,就是一个调节器的输出去带动两个或两个以上的调节阀工作。
每个调节阀仅在调节器输出的某段信号范围内动作。
PID控制例1:反应釜温度自动控制回路资料
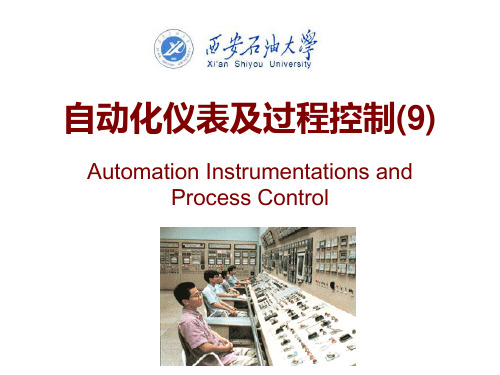
•两步法:先副后主 •一步法:定副调主
x1
x2
+ - Gc1 +
Gc2 -
y2
y1
Go2
Go1
TN
21
串级调节系统例:
夹套式反应釜温度控制
TN
22
比值调节系统
保证两种(或两种以上)物料流量保持 一定比例的调节系统。 FC:比值调节器, 比值=K
QB=KQA
开环比值系统
TN
23
比值调节系统
单闭环比值调节系统
而引入的一个中间参数)
Gc1(s):主调节器 Gc2(s):副调节器
TN
16
串级调节系统特点
•副回路中的干扰,主要在副回路中克服。 •减少了副对象的T,提高了副环的调节 品质。 •提高了系统的频率响应,加快了抗干扰 过程的速度。 •提供了灵活的控制方式
TN
17
串级调节系统应用
TN
18
串级调节系统应用
自动化仪表及过程控制(9)
Automation Instrumentations and Process Control
PID控制例1:反应釜温度自动控制回路
TN
2
PID控制例2:供水水压自动控制回路
TN
3
系统调节方案的选择
间接指标控制:对于不便直接 调节的工艺直接指标,可以选 择一个与直接指标相关的量进 行调节,间接完成控制任务。 例:精馏塔生产过程,
调节系统过渡过程的稳态误差超过工艺规定,则下 列哪项调整方法可以改善上述不足?
(A)增加比例度; (B)减少积分时间 ; (C)增加积分时间; (D)减少微分时间。
TN
9
第6章 单回路调节系统
反应釜的温度要怎么控制

反应釜的温度要怎么控制
反应釜一般都有搅拌器,保证反应釜内温度均匀。
反应釜温度控制分升温和降温两种(视内部是放热反应还是吸热),升温采用蒸汽、熔盐或者其他加热介质,降温一般是冷却水或者其他介质,不论加热或者降温都是采取加热或者冷却介质流量控制,手动开关阀门,或者用自动控制采用温度显示信号通过控制器控制加热、冷却介质的调节阀调节流量来控制。
岩征反应釜的控制法则如下:
整个液体循环是真正的全封闭的系统,打破传统,全球独家。
2、升温和降温的速度块,精确控制化学反应系统
3、低温时导热介质不会吸收水汽
4、导热介质不会被氧化,变色,或褐化
高温时没有油雾产生
6、快速响应系统的热动力学变化,不论是剧烈的吸热或者放热反应,不会有控温滞后现象。
7、一种导热介质可以用于低温和高温,可以用于-90℃—200℃的温度范围(独家)。
8、使用成本低,一劳永逸。
反应釜温度控制(DOC)
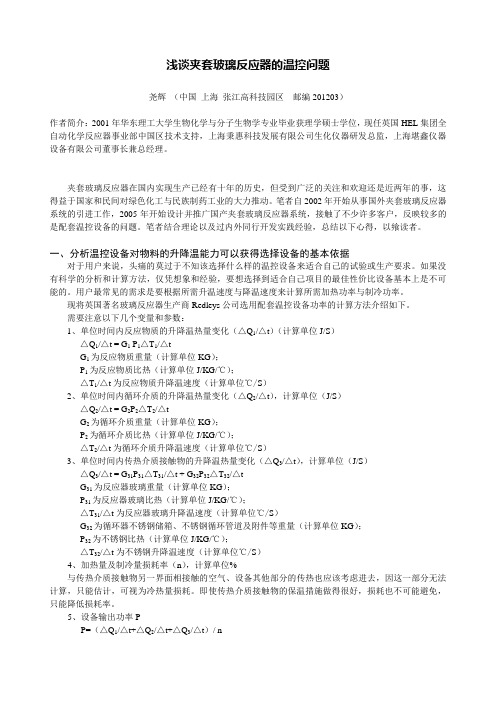
浅谈夹套玻璃反应器的温控问题尧辉(中国上海张江高科技园区邮编201203)作者简介:2001年华东理工大学生物化学与分子生物学专业毕业获理学硕士学位,现任英国HEL集团全自动化学反应器事业部中国区技术支持,上海秉惠科技发展有限公司生化仪器研发总监,上海堪鑫仪器设备有限公司董事长兼总经理。
夹套玻璃反应器在国内实现生产已经有十年的历史,但受到广泛的关注和欢迎还是近两年的事,这得益于国家和民间对绿色化工与民族制药工业的大力推动。
笔者自2002年开始从事国外夹套玻璃反应器系统的引进工作,2005年开始设计并推广国产夹套玻璃反应器系统,接触了不少许多客户,反映较多的是配套温控设备的问题。
笔者结合理论以及过内外同行开发实践经验,总结以下心得,以飨读者。
一、分析温控设备对物料的升降温能力可以获得选择设备的基本依据对于用户来说,头痛的莫过于不知该选择什么样的温控设备来适合自己的试验或生产要求。
如果没有科学的分析和计算方法,仅凭想象和经验,要想选择到适合自己项目的最佳性价比设备基本上是不可能的。
用户最常见的需求是要根据所需升温速度与降温速度来计算所需加热功率与制冷功率。
现将英国著名玻璃反应器生产商Redleys公司选用配套温控设备功率的计算方法介绍如下。
需要注意以下几个变量和参数:1、单位时间内反应物质的升降温热量变化(△Q1/△t)(计算单位J/S)△Q1/△t = G1 P1△T1/△tG1为反应物质重量(计算单位KG);P1为反应物质比热(计算单位J/KG/℃);△T1/△t为反应物质升降温速度(计算单位℃/S)2、单位时间内循环介质的升降温热量变化(△Q2/△t),计算单位(J/S)△Q2/△t = G2P2△T2/△tG2为循环介质重量(计算单位KG);P2为循环介质比热(计算单位J/KG/℃);△T2/△t为循环介质升降温速度(计算单位℃/S)3、单位时间内传热介质接触物的升降温热量变化(△Q3/△t),计算单位(J/S)△Q3/△t = G31P31△T31/△t + G32P32△T32/△tG31为反应器玻璃重量(计算单位KG);P31为反应器玻璃比热(计算单位J/KG/℃);△T31/△t为反应器玻璃升降温速度(计算单位℃/S)G32为循环器不锈钢储箱、不锈钢循环管道及附件等重量(计算单位KG);P32为不锈钢比热(计算单位J/KG/℃);△T32/△t为不锈钢升降温速度(计算单位℃/S)4、加热量及制冷量损耗率(n),计算单位%与传热介质接触物另一界面相接触的空气、设备其他部分的传热也应该考虑进去,因这一部分无法计算,只能估计,可视为冷热量损耗。
化学反应釜最优温度控制系统的设计与实现
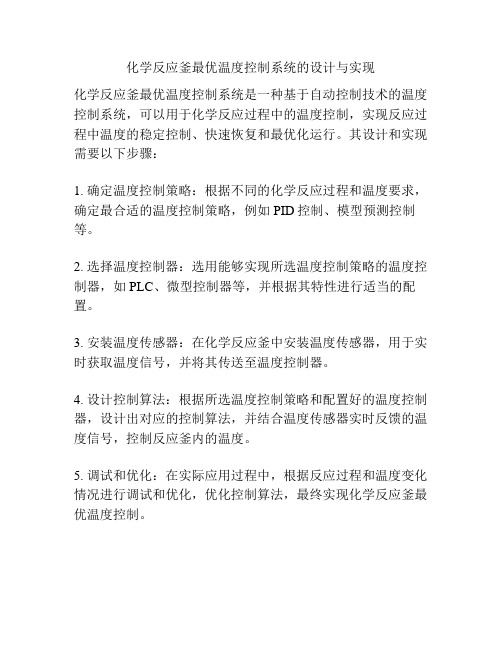
化学反应釜最优温度控制系统的设计与实现
化学反应釜最优温度控制系统是一种基于自动控制技术的温度控制系统,可以用于化学反应过程中的温度控制,实现反应过程中温度的稳定控制、快速恢复和最优化运行。
其设计和实现需要以下步骤:
1. 确定温度控制策略:根据不同的化学反应过程和温度要求,确定最合适的温度控制策略,例如PID控制、模型预测控制等。
2. 选择温度控制器:选用能够实现所选温度控制策略的温度控制器,如PLC、微型控制器等,并根据其特性进行适当的配置。
3. 安装温度传感器:在化学反应釜中安装温度传感器,用于实时获取温度信号,并将其传送至温度控制器。
4. 设计控制算法:根据所选温度控制策略和配置好的温度控制器,设计出对应的控制算法,并结合温度传感器实时反馈的温度信号,控制反应釜内的温度。
5. 调试和优化:在实际应用过程中,根据反应过程和温度变化情况进行调试和优化,优化控制算法,最终实现化学反应釜最优温度控制。
BP-Amoco工艺聚丙烯装置反应釜的温度控制
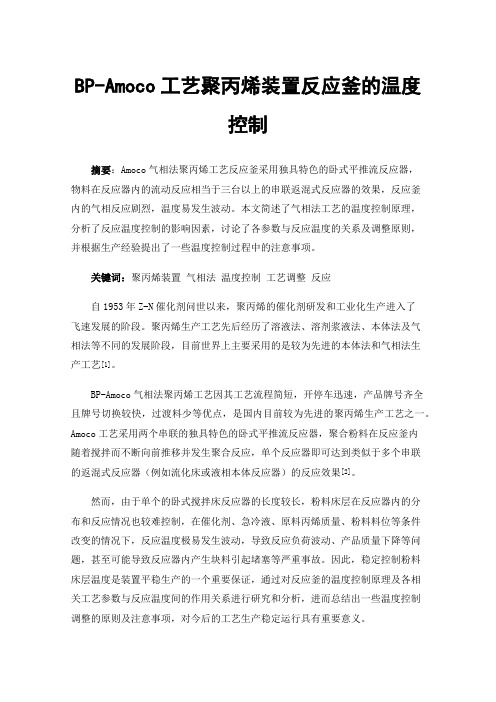
BP-Amoco工艺聚丙烯装置反应釜的温度控制摘要:Amoco气相法聚丙烯工艺反应釜采用独具特色的卧式平推流反应器,物料在反应器内的流动反应相当于三台以上的串联返混式反应器的效果,反应釜内的气相反应剧烈,温度易发生波动。
本文简述了气相法工艺的温度控制原理,分析了反应温度控制的影响因素,讨论了各参数与反应温度的关系及调整原则,并根据生产经验提出了一些温度控制过程中的注意事项。
关键词:聚丙烯装置气相法温度控制工艺调整反应自1953年Z-N催化剂问世以来,聚丙烯的催化剂研发和工业化生产进入了飞速发展的阶段。
聚丙烯生产工艺先后经历了溶液法、溶剂浆液法、本体法及气相法等不同的发展阶段,目前世界上主要采用的是较为先进的本体法和气相法生产工艺[1]。
BP-Amoco气相法聚丙烯工艺因其工艺流程简短,开停车迅速,产品牌号齐全且牌号切换较快,过渡料少等优点,是国内目前较为先进的聚丙烯生产工艺之一。
Amoco工艺采用两个串联的独具特色的卧式平推流反应器,聚合粉料在反应釜内随着搅拌而不断向前推移并发生聚合反应,单个反应器即可达到类似于多个串联的返混式反应器(例如流化床或液相本体反应器)的反应效果[2]。
然而,由于单个的卧式搅拌床反应器的长度较长,粉料床层在反应器内的分布和反应情况也较难控制,在催化剂、急冷液、原料丙烯质量、粉料料位等条件改变的情况下,反应温度极易发生波动,导致反应负荷波动、产品质量下降等问题,甚至可能导致反应器内产生块料引起堵塞等严重事故。
因此,稳定控制粉料床层温度是装置平稳生产的一个重要保证,通过对反应釜的温度控制原理及各相关工艺参数与反应温度间的作用关系进行研究和分析,进而总结出一些温度控制调整的原则及注意事项,对今后的工艺生产稳定运行具有重要意义。
1气相反应釜的温度控制原理Amoco工艺的反应釜为卧式平推流反应器,反应釜的设计反应温度为66 ℃,压力为2.2 MPa。
催化剂与气相丙烯在反应釜内发生聚合反应,释放出大量的聚合反应热。
反应釜自动化控制说明

反应釜自动化控制说明一、引言反应釜是一种常用的化学试验设备,用于进行各种化学反应。
为了提高实验效率和安全性,采用自动化控制系统对反应釜进行控制是必要的。
本文将详细介绍反应釜自动化控制的相关内容。
二、反应釜自动化控制系统概述反应釜自动化控制系统由硬件和软件两部分组成。
硬件包括传感器、执行器、控制器等,用于采集反应釜内部的各种参数,并控制反应过程。
软件则负责数据处理、控制算法实现等功能。
三、传感器1. 温度传感器:用于测量反应釜内部温度,常用的传感器有热电偶和红外线温度传感器。
2. 压力传感器:用于测量反应釜内部压力,常用的传感器有压阻式传感器和压电式传感器。
3. 流量传感器:用于测量反应釜内部流体的流量,常用的传感器有涡轮流量计和电磁流量计。
4. 液位传感器:用于测量反应釜内部液体的液位,常用的传感器有浮子液位传感器和压阻式液位传感器。
四、执行器1. 加热器:用于控制反应釜内部的加热,常用的执行器有电加热器和蒸汽加热器。
2. 冷却器:用于控制反应釜内部的冷却,常用的执行器有冷却水流量阀和冷却水温度控制阀。
3. 搅拌器:用于控制反应釜内部的搅拌,常用的执行器有电动搅拌器和气动搅拌器。
五、控制器反应釜自动化控制系统的控制器采用PID控制算法,通过对传感器采集的数据进行处理,计算出控制信号,控制执行器的运行状态,以达到对反应釜内部温度、压力、流量和液位等参数的精确控制。
六、自动化控制流程1. 数据采集:通过传感器对反应釜内部的温度、压力、流量和液位等参数进行实时采集。
2. 数据处理:将采集到的数据送入控制器进行处理,包括滤波、数据校正等操作。
3. 控制算法实现:根据控制要求和采集到的数据,控制器通过PID控制算法计算出控制信号。
4. 执行器控制:控制信号送入执行器,控制加热器、冷却器和搅拌器的运行状态。
5. 反馈控制:通过传感器实时监测反应釜内部的温度、压力、流量和液位等参数,并将反馈信息送回控制器进行调整,以实现闭环控制。
反应釜高低温循环控温系统的基本原理和作用
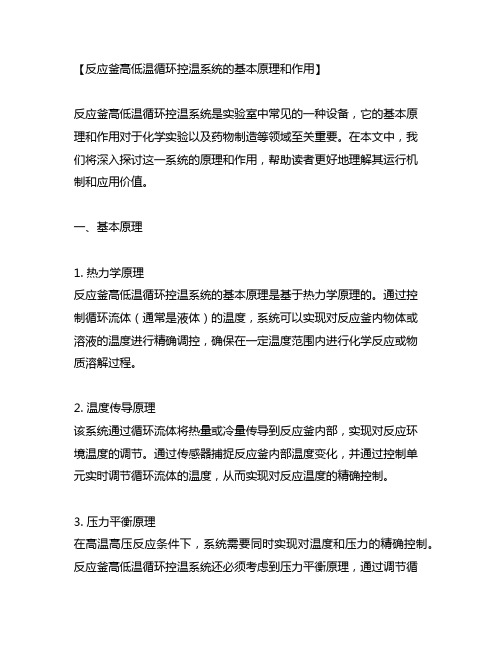
【反应釜高低温循环控温系统的基本原理和作用】反应釜高低温循环控温系统是实验室中常见的一种设备,它的基本原理和作用对于化学实验以及药物制造等领域至关重要。
在本文中,我们将深入探讨这一系统的原理和作用,帮助读者更好地理解其运行机制和应用价值。
一、基本原理1. 热力学原理反应釜高低温循环控温系统的基本原理是基于热力学原理的。
通过控制循环流体(通常是液体)的温度,系统可以实现对反应釜内物体或溶液的温度进行精确调控,确保在一定温度范围内进行化学反应或物质溶解过程。
2. 温度传导原理该系统通过循环流体将热量或冷量传导到反应釜内部,实现对反应环境温度的调节。
通过传感器捕捉反应釜内部温度变化,并通过控制单元实时调节循环流体的温度,从而实现对反应温度的精确控制。
3. 压力平衡原理在高温高压反应条件下,系统需要同时实现对温度和压力的精确控制。
反应釜高低温循环控温系统还必须考虑到压力平衡原理,通过调节循环流体的流动速度和压力来实现对反应环境的压力控制。
二、作用1. 温度控制反应釜高低温循环控温系统的最基本作用是实现对反应环境温度的控制。
它可以将反应环境快速升温或降温至设定温度,精确控制在一定温度范围内,满足不同实验或生产过程的温度要求。
2. 反应加速通过控制反应环境的温度,系统可以加速化学反应的进行。
在高温下,反应物的分子活动增强,反应速率加快;而低温下,反应速率减缓,从而实现对反应速度的调节。
3. 产品纯度控制在某些化学反应或物质分离过程中,需要对产品的纯度进行精确控制。
反应釜高低温循环控温系统可以通过温度控制,促进有机物质的结晶或凝固,提高产品的纯度。
4. 能源节约该系统可以通过反馈控制循环流体的温度和流速,实现能源的有效利用。
在高温高压条件下,能够减少反应釜内部温度波动,降低温度控制系统对能源的消耗。
5. 安全保障反应釜高低温循环控温系统在高温高压条件下,可以为反应釜提供安全保障。
通过实时监测和调节反应环境的温度和压力,确保反应过程稳定进行,避免因温度或压力突变而导致的意外情况。
聚合反应釜温度控制系统设计

聚合反应釜温度控制系统设计摘要聚合反应机理复杂,是强放热反应,过程具有大滞后、大惯性、非线性等特性.温度、压力、浓度及催化剂的活性与牌号等都对化学平衡产生重要影响。
因此,反应釜温度控制的效果将直接影响产品的质量及装置的正常运行,为此将反应釜温度控制回路列为重点监控回路,严格将反应釜温度控制在要求范围内。
传统的PID控制是一种基于过程参数的控制方法,具有控制原理简单、稳定性好、可靠性高、参数易调整等优点,但其设计依赖于被控对象的精确数学模型,在线整定参数的能力差,因反应釜机理复杂,各个参数在系统反应过程中时变。
因而采用一般的PID控制器无法实现对反应釜的精确控制.模糊控制和预测控制都是对不确定系统进行控制的有效方法.本文将模糊控制和预测控制结合起来运用于聚合反应釜温度控制器的设计,设计以聚合反应釜温度控制系统为中心,从控制系统的硬件系统组成、软件选用到系统的设计。
单片机以其功能强、体积小、可靠性高、造价低和开发周期短等优点,成为自动化和各个测控领域中广泛应用的器件,在温度控制系统中,单片机更是起到了不可替代的核心作用。
在工业生产中,如用于热处理的加热炉、用于融化金属的坩锅电阻炉等,都用到了电阻加热的原理.鉴于单片机技术应用的广泛性和优越性,温度控制的重要性,因而设计一种较为理想的温度控制系统是非常有价值的。
本文就是根据这一思想来展开的.结果表明预测模糊控制作为模糊控制和预测控制相结合的产物该控制方法具有使系统超调量小、调整时间短、对系统参数变化和外界干扰有较强的鲁棒性等优点,是一种提高聚合反应釜温度控制效果的有效方法。
关键词:聚合反应;预测控制;模糊控制;单片机Summary of polymerization Kettle temperature controlsystem designABSTRACTPolymerization reaction mechanism for complex,is a strong exothermic reaction, process with large time delays, large inertia, nonlinear and other features。
反应釜工艺制冷加热温控方案
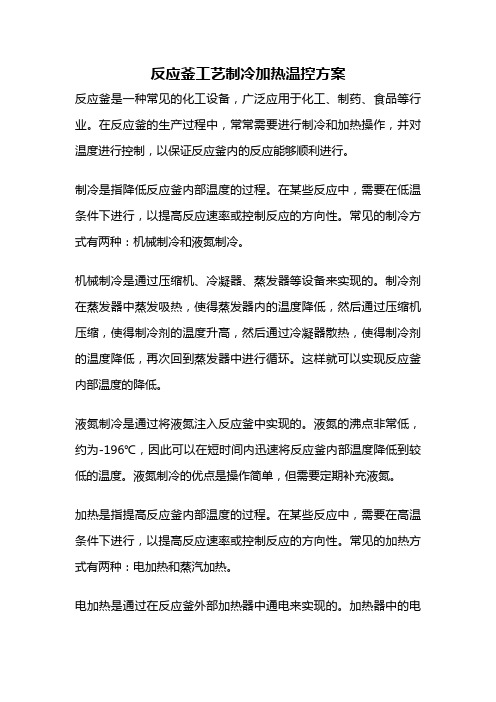
反应釜工艺制冷加热温控方案反应釜是一种常见的化工设备,广泛应用于化工、制药、食品等行业。
在反应釜的生产过程中,常常需要进行制冷和加热操作,并对温度进行控制,以保证反应釜内的反应能够顺利进行。
制冷是指降低反应釜内部温度的过程。
在某些反应中,需要在低温条件下进行,以提高反应速率或控制反应的方向性。
常见的制冷方式有两种:机械制冷和液氮制冷。
机械制冷是通过压缩机、冷凝器、蒸发器等设备来实现的。
制冷剂在蒸发器中蒸发吸热,使得蒸发器内的温度降低,然后通过压缩机压缩,使得制冷剂的温度升高,然后通过冷凝器散热,使得制冷剂的温度降低,再次回到蒸发器中进行循环。
这样就可以实现反应釜内部温度的降低。
液氮制冷是通过将液氮注入反应釜中实现的。
液氮的沸点非常低,约为-196℃,因此可以在短时间内迅速将反应釜内部温度降低到较低的温度。
液氮制冷的优点是操作简单,但需要定期补充液氮。
加热是指提高反应釜内部温度的过程。
在某些反应中,需要在高温条件下进行,以提高反应速率或控制反应的方向性。
常见的加热方式有两种:电加热和蒸汽加热。
电加热是通过在反应釜外部加热器中通电来实现的。
加热器中的电阻丝会发热,将热量传导给反应釜,从而提高反应釜内部的温度。
电加热的优点是加热速度快,温度控制精度高,但需要注意安全问题。
蒸汽加热是通过将蒸汽送入反应釜的夹套中实现的。
蒸汽的热量可以通过夹套传导给反应釜,从而提高反应釜内部的温度。
蒸汽加热的优点是加热效率高,但需要注意蒸汽的供应和控制。
温控是指对反应釜内部温度进行控制的过程。
温度的控制可以通过控制制冷和加热操作的开关和参数来实现。
常见的温控方式有两种:PID控制和PLC控制。
PID控制是一种常见的温控方式,通过调节制冷和加热操作的开关和参数,使得反应釜内部的温度稳定在设定的值附近。
PID控制根据温度的偏差、偏差的变化率和偏差的累积值来计算控制量,从而实现温度的控制。
PLC控制是一种更高级的温控方式,通过使用可编程逻辑控制器(PLC)来实现温度的控制。
- 1、下载文档前请自行甄别文档内容的完整性,平台不提供额外的编辑、内容补充、找答案等附加服务。
- 2、"仅部分预览"的文档,不可在线预览部分如存在完整性等问题,可反馈申请退款(可完整预览的文档不适用该条件!)。
- 3、如文档侵犯您的权益,请联系客服反馈,我们会尽快为您处理(人工客服工作时间:9:00-18:30)。
浅谈夹套玻璃反应器的温控问题尧辉(中国上海张江高科技园区邮编201203)作者简介:2001年华东理工大学生物化学与分子生物学专业毕业获理学硕士学位,现任英国HEL集团全自动化学反应器事业部中国区技术支持,上海秉惠科技发展有限公司生化仪器研发总监,上海堪鑫仪器设备有限公司董事长兼总经理。
夹套玻璃反应器在国内实现生产已经有十年的历史,但受到广泛的关注和欢迎还是近两年的事,这得益于国家和民间对绿色化工与民族制药工业的大力推动。
笔者自2002年开始从事国外夹套玻璃反应器系统的引进工作,2005年开始设计并推广国产夹套玻璃反应器系统,接触了不少许多客户,反映较多的是配套温控设备的问题。
笔者结合理论以及过内外同行开发实践经验,总结以下心得,以飨读者。
一、分析温控设备对物料的升降温能力可以获得选择设备的基本依据对于用户来说,头痛的莫过于不知该选择什么样的温控设备来适合自己的试验或生产要求。
如果没有科学的分析和计算方法,仅凭想象和经验,要想选择到适合自己项目的最佳性价比设备基本上是不可能的。
用户最常见的需求是要根据所需升温速度与降温速度来计算所需加热功率与制冷功率。
现将英国著名玻璃反应器生产商Redleys公司选用配套温控设备功率的计算方法介绍如下。
需要注意以下几个变量和参数:1、单位时间内反应物质的升降温热量变化(△Q1/△t)(计算单位J/S)△Q1/△t = G1 P1△T1/△tG1为反应物质重量(计算单位KG);P1为反应物质比热(计算单位J/KG/℃);△T1/△t为反应物质升降温速度(计算单位℃/S)2、单位时间内循环介质的升降温热量变化(△Q2/△t),计算单位(J/S)△Q2/△t = G2P2△T2/△tG2为循环介质重量(计算单位KG);P2为循环介质比热(计算单位J/KG/℃);△T2/△t为循环介质升降温速度(计算单位℃/S)3、单位时间内传热介质接触物的升降温热量变化(△Q3/△t),计算单位(J/S)△Q3/△t = G31P31△T31/△t + G32P32△T32/△tG31为反应器玻璃重量(计算单位KG);P31为反应器玻璃比热(计算单位J/KG/℃);△T31/△t为反应器玻璃升降温速度(计算单位℃/S)G32为循环器不锈钢储箱、不锈钢循环管道及附件等重量(计算单位KG);P32为不锈钢比热(计算单位J/KG/℃);△T32/△t为不锈钢升降温速度(计算单位℃/S)4、加热量及制冷量损耗率(n),计算单位%与传热介质接触物另一界面相接触的空气、设备其他部分的传热也应该考虑进去,因这一部分无法计算,只能估计,可视为冷热量损耗。
即使传热介质接触物的保温措施做得很好,损耗也不可能避免,只能降低损耗率。
5、设备输出功率PP=(△Q1/△t+△Q2/△t+△Q3/△t)/ n油槽加热功率计算:水比热:4200J/KG/℃硅油比热:1630 J/KG/℃玻璃平均比热:920J/KG/℃304不锈钢比热:460 J/KG/℃物料(以水计算)要求升温速度:80℃/3600S(从室温20℃升到100℃)物料(以水计算)量:14KG油箱装油量:15KG油管装油量:0.5KG夹套装油量:6KG20升夹套玻璃反应器重量:16 KG304不锈钢箱、泵、阀门及接头等重量:35KG根据经验,在保温措施较好和传热介质流速足够的情况下,20升反应器的物料(以水计算)达到要求温度(t℃)时,夹套平均油温约为:t+10℃;油管平均温度约为t+15℃;油槽平均温度为t+20℃。
油直接受热部位为油槽。
无加热量损耗的理想状态下的最小功率为(4200J/KG/℃×80℃×14KG +1630J/KG/℃×100℃×21.5KG水的热量变化油的热量变化+920 J/KG/℃×90℃×16KG +460 J/KG/℃×100℃×35KG)÷3600S玻璃的热量变化不锈钢的热量变化单位时间=3095.35W考虑到保温不完全导致的损耗、设备加热温控能力的弹性、泵速促进及时充分地进行热交换的水平,功率至少应设计为4KW。
制冷设备功率计算如下:油泵制冷功率稍微要复杂一些,因为压缩机的制冷输入功率与制冷量是两个概念,而且这两项还是随不同制冷剂蒸发温度和冷凝温度而异,以本公司DL-45-20全封闭制冷恒温循环油泵(无氟制冷)采用的丹麦Danfoss NTZ048制冷压缩机(2匹)与R404A制冷剂组合为例,其在不同蒸发温度和冷凝温度的制冷量与输入功率见下表:oT c Q O P e Q O P e Q O P e Q O P e Q O P e Q O P e Q O P e Q O P e NTZ048 30 466 0.50 774 0.70 1160 0.90 1636 1.10 2211 1.27 2896 1.42 3700 1.54 4635 1.6235 371 0.47 655 0.67 1010 0.89 1445 1.10 1972 1.31 2600 1.49 3340 1.64 4202 1.76T o:蒸发温度(℃)T c:冷凝温度(℃)Q o:制冷量(W)P e:输入功率(kW)而且计算还应以所需最低温度时的制冷量来计算。
但计算方式与油槽加热功率基本相同。
以本公司生产的DL-45系列全封闭低温恒温循环油泵为例,油泵制冷功率(制冷量)计算如下:水比热:4200J/KG/℃硅油比热:1630 J/KG/℃玻璃平均比热:920J/KG/℃304不锈钢比热:460 J/KG/℃物料(以水计算)要求降温速度:40℃/3600S(从室温20℃降到-20℃)物料(以水计算)量:14KG油箱装油量:2KG油管装油量:0.5KG夹套装油量:6KG交换器装油量:0.5KG20升夹套玻璃反应器重量:16 KG304不锈钢箱、泵、阀门及接头等重量:20KG根据经验,在保温措施较好和传热介质流速足够的情况下,20升反应器的物料(以水计算)达到要求温度(t℃)时,夹套平均油温约为:t-10℃;油管平均温度约为t-15℃;制冷剂和油热交换器平均温度为t-20℃。
油直接受冷部位为热交换器即制冷设备的蒸发器。
无制冷量损耗的理想状态下的最小功率为(4200J/KG/℃×40℃×14KG +1630J/KG/℃×60℃×9KG水的热量变化油的热量变化+920 J/KG/℃×50℃×16KG +460 J/KG/℃×60℃×20KG)÷3600S玻璃的热量变化不锈钢的热量变化单位时间=1255.59W制冷剂蒸发温度要求至少-35℃。
从上表中可以看到丹麦Danfoss NTZ048制冷压缩机(2匹)制冷剂蒸发温度-35℃、冷凝温度30℃时,制冷量为1160W。
此时该型压缩机制冷量虽接近1255.59W的数值,但考虑到保温不完全导致的损耗、设备制冷温控能力的弹性、制冷剂蒸发器热交换面积发挥压缩机制冷能力的水平、泵速促进充分及时进行热交换的水平,该型压缩机也不能满足要求,所以应该选择使用3匹以上的制冷压缩机。
二、用户选择反应器及温控设备应该注意的几个问题1、反应器及保温措施1)循环介质进、出口的选择目前国内生产的夹套玻璃反应器循环介质进出口主要有宝塔头、法兰口两种,以宝塔头居多。
笔者认为宝塔头接口虽然方便,但却有许多弊端:首先,外型上呈逐渐缩小的造型容易产生阻力影响循环介质的流速,高速流动的液体还会因此形成对玻璃的冲力进而形成对夹套的压力,对玻璃反应器具有潜在的破坏力;其次宝塔形和玻璃的脆性决定了它只能与软管直接连接,因为目前软橡胶类材料的耐温能力不超过250℃,因此使用宝塔头接口意味着您选择的产品物料温度很难超过210℃,对于20升以上的中试级反应器而言,传热阻力更大,可达到的温度值只会更低;而且,使用橡胶软管还不能避免橡胶会老化的问题。
所以,笔者推荐使用法兰接口,这也是国外同行通用的接口,它可以避免宝塔头接口的许多弊端,唯一的缺点就是装卸较烦琐一些。
现在也有快开式连接,其实使用起来也很方便快捷,比宝塔头与橡胶类软管连接还更省力些。
笔者所在公司开发的夹套玻璃反应器全部使用法兰接口,目前尚无用户提出不同意见。
2)内置耐腐蚀盘管该配件也可起到加热、冷却器的功能,还可充当支撑骨架固定柔性温度测量探头,不影响搅拌桨的尽量放大,可谓功能多多。
作为加热器时可通蒸汽、热水或热油;作为冷却器时可通水、冷的醇水混合液和冷油甚至液氮。
常见的制作方法有薄壁PTFE包被金属管道。
有不少人排斥使用内置盘管,认为它清洗不方便,其实包被薄壁PTFE的金属管道与固定在大型金属反应釜体上的盘管不一样,前者很容易拆卸和清洗,而且造价并不高,可更换使用。
须注意不锈钢喷镀PTFE的方法并不可取,不仅是因为渡层太薄易剥落而且喷镀成本高,最重要的原因是喷镀完毕后形成的是有细小网孔的网状镀层,并不能起到防止化学腐蚀的作用。
3)真空夹层其原理在于消除热传导中的空气对流因素,就象保温瓶胆抽真空。
玻璃反应容器采用三层设计时,对外层夹套抽真空并封闭形成真空夹层,这样反应保温效果好。
而且低温时,外层玻璃表面无水雾亦不会结霜,反应清晰可见;高温时外层玻璃表面不炙热,可免除烫伤危险。
但三层玻璃反应器的应力点很多,烧制成功率不高,容积越大的反应器越是这样。
4)测温套及测温点目前市场上大多数玻璃反应器使用的是固定式温度计玻璃套管来测物料温度,套管从盖子上固定处深入釜内某一深度。
这样做的缺点很多:1)搅拌棒在某一转速段可能出现强烈的共振,可能撞击温度计玻璃套管;2)中试级的反应器(20~50升)的玻璃套管处于搅拌轴与内壁的中央,使用涡轮式搅拌桨时很容易被页片打到,致使叶片不能做到尽可能的大而影响搅拌效果;3)当物料装得多的时候,套管受力大易折裂,物料装得少的时候则套管可能接触不到物料而无法测温。
我们开发了插入深度可调的温度计套管可弥补第三种缺陷。
另外还开发了可与内置换热盘管捆绑使用的可任意弯曲的温度探头,这样就可将测温点置于靠近反应器内壁的任一深度,并且不影响使用更大搅拌半径的搅拌桨页。
当然这种应用的前提是须同时使用内置换热盘管。
另外,国外已有从底部阀门中央突出部位内置温度探头来进行温度的数字测量,一般突出部位最高点比釜底高1~2cm。
这种方式测量的是底部物料的温度,比较适合于小型反应器和应搅动混匀的液体,对于较大的反应器或粘度大的物料不合适。
而且,对于较大的反应器而言,夹套高度也大,因为高温流体密度小,低温流体密度大,一般在夹套下部循环介质温度要比上部低。
所以对大型反应器而言,底部测温的方式测得物料温度是偏低的。