反应釜温度控制
控制反应温度100到120度的方法

控制反应温度100到120度的方法
要控制反应的温度在100到120度之间,可以采取以下方法:
1.恒温水浴:使用恒温水浴设备可以很好地控制反应的温度。
将反应容器放置在恒温水浴中,通过调节水浴的温度可以使反应保持在所需的温度范围内。
2.加热/降温装置:根据反应需要,可以使用加热器或冷却器来调节反应体系的温度。
通过控制加热或降温装置的温度和功率,可以使反应体系保持在目标温度范围内。
3.反应釜控温:如果是在反应釜中进行反应,可以使用反应釜自带的控温系统来实现温度的精确控制。
根据反应釜的型号和功能,可以设置目标温度并进行实时监控调节。
4.温度计监控:在反应过程中,使用温度计实时监控反应体系的温度变化,及时调整加热或冷却设备,保持反应温度在100到120度之间。
5.反应条件优化:除了控制温度,还需要考虑其他反应条件对反应的影响,如反应时间、反应物浓度等。
优化这些条件可以更好地控制反应的温度范围。
通过以上方法,可以有效地控制反应的温度在100到120度之间,确保反应过程的顺利进行并达到预期的效果。
反应釜温控系统课程设计

反应釜温控系统课程设计一、课程目标知识目标:1. 学生能理解反应釜的基本原理和温度控制的重要性。
2. 学生能掌握反应釜温度控制系统的组成、工作原理及各部分功能。
3. 学生能了解温度传感器、控制器、执行器等关键部件的类型及选用原则。
技能目标:1. 学生能运用所学知识分析反应釜温度控制系统的故障原因并进行排查。
2. 学生能设计简单的反应釜温度控制方案,包括参数设置、设备选型等。
3. 学生能通过实验操作,验证温度控制系统的稳定性和可靠性。
情感态度价值观目标:1. 学生培养对化学反应过程的兴趣,增强对化学工程领域的认识。
2. 学生树立安全意识,认识到温度控制在化学反应过程中的重要性。
3. 学生培养团队协作精神,提高沟通与表达能力,为未来从事相关工作奠定基础。
分析课程性质、学生特点和教学要求,本课程目标旨在使学生在理解反应釜温控系统基本原理的基础上,掌握实际操作和设计能力,同时培养安全意识、团队协作和沟通能力,为未来从事化学工程及相关领域工作打下坚实基础。
通过本课程的学习,学生将能够具备解决实际问题的能力,为我国化学工业的发展贡献力量。
二、教学内容1. 反应釜基本原理及温度控制概述- 介绍反应釜的作用、类型及在化工生产中的应用。
- 阐述温度控制在反应釜操作中的重要性。
2. 反应釜温度控制系统组成与工作原理- 分析温度控制系统的组成部分,包括温度传感器、控制器、执行器等。
- 讲解各部分的工作原理及相互关系。
3. 温度传感器及其选用- 介绍常见温度传感器的类型、特点及应用场景。
- 分析温度传感器的选用原则,包括精度、响应时间等方面。
4. 温度控制器原理与操作- 阐述温度控制器的原理,包括PID控制算法。
- 指导学生操作温度控制器,实现反应釜温度的精确控制。
5. 反应釜温度控制方案设计- 分析反应釜温度控制方案的设计原则,包括设备选型、参数设置等。
- 指导学生设计简单的反应釜温度控制方案。
6. 实验操作与故障排查- 安排实验操作环节,让学生动手验证温度控制系统的稳定性和可靠性。
dcs反应釜控温技巧
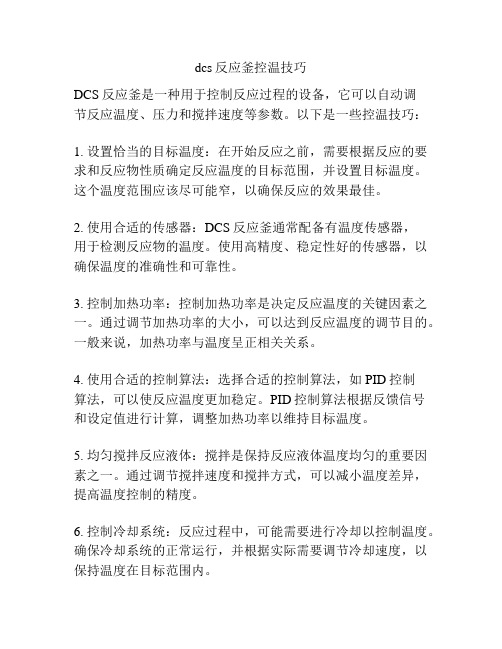
dcs反应釜控温技巧DCS反应釜是一种用于控制反应过程的设备,它可以自动调节反应温度、压力和搅拌速度等参数。
以下是一些控温技巧:1. 设置恰当的目标温度:在开始反应之前,需要根据反应的要求和反应物性质确定反应温度的目标范围,并设置目标温度。
这个温度范围应该尽可能窄,以确保反应的效果最佳。
2. 使用合适的传感器:DCS反应釜通常配备有温度传感器,用于检测反应物的温度。
使用高精度、稳定性好的传感器,以确保温度的准确性和可靠性。
3. 控制加热功率:控制加热功率是决定反应温度的关键因素之一。
通过调节加热功率的大小,可以达到反应温度的调节目的。
一般来说,加热功率与温度呈正相关关系。
4. 使用合适的控制算法:选择合适的控制算法,如PID控制算法,可以使反应温度更加稳定。
PID控制算法根据反馈信号和设定值进行计算,调整加热功率以维持目标温度。
5. 均匀搅拌反应液体:搅拌是保持反应液体温度均匀的重要因素之一。
通过调节搅拌速度和搅拌方式,可以减小温度差异,提高温度控制的精度。
6. 控制冷却系统:反应过程中,可能需要进行冷却以控制温度。
确保冷却系统的正常运行,并根据实际需要调节冷却速度,以保持温度在目标范围内。
7. 进行定期检查和维护:定期检查和维护DCS反应釜及其相关设备,确保其正常运行和准确控温。
清洁传感器、校准温度控制系统、维护加热和冷却系统等都是必要的。
总之,DCS反应釜的控温技巧包括设置恰当的目标温度、使用合适的传感器、控制加热功率、选择合适的控制算法、均匀搅拌反应液体、控制冷却系统以及定期检查和维护等。
这些技巧有助于提高反应温度的稳定性和控制精度。
反应釜温控方案
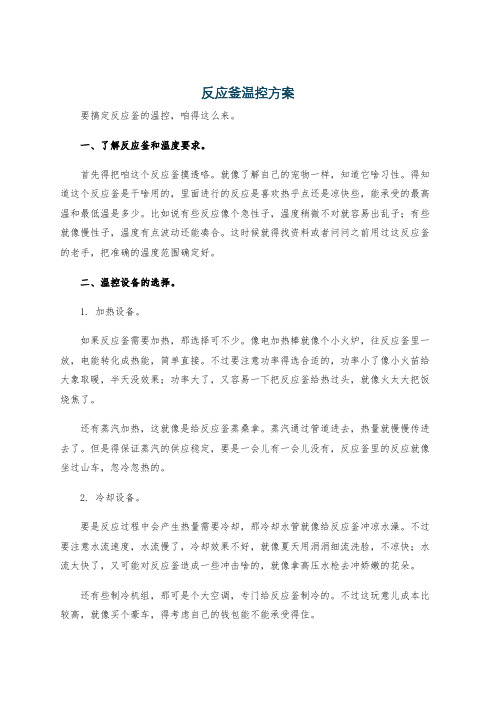
反应釜温控方案要搞定反应釜的温控,咱得这么来。
一、了解反应釜和温度要求。
首先得把咱这个反应釜摸透咯。
就像了解自己的宠物一样,知道它啥习性。
得知道这个反应釜是干啥用的,里面进行的反应是喜欢热乎点还是凉快些,能承受的最高温和最低温是多少。
比如说有些反应像个急性子,温度稍微不对就容易出乱子;有些就像慢性子,温度有点波动还能凑合。
这时候就得找资料或者问问之前用过这反应釜的老手,把准确的温度范围确定好。
二、温控设备的选择。
1. 加热设备。
如果反应釜需要加热,那选择可不少。
像电加热棒就像个小火炉,往反应釜里一放,电能转化成热能,简单直接。
不过要注意功率得选合适的,功率小了像小火苗给大象取暖,半天没效果;功率大了,又容易一下把反应釜给热过头,就像火太大把饭烧焦了。
还有蒸汽加热,这就像是给反应釜蒸桑拿。
蒸汽通过管道进去,热量就慢慢传进去了。
但是得保证蒸汽的供应稳定,要是一会儿有一会儿没有,反应釜里的反应就像坐过山车,忽冷忽热的。
2. 冷却设备。
要是反应过程中会产生热量需要冷却,那冷却水管就像给反应釜冲凉水澡。
不过要注意水流速度,水流慢了,冷却效果不好,就像夏天用涓涓细流洗脸,不凉快;水流太快了,又可能对反应釜造成一些冲击啥的,就像拿高压水枪去冲娇嫩的花朵。
还有些制冷机组,那可是个大空调,专门给反应釜制冷的。
不过这玩意儿成本比较高,就像买个豪车,得考虑自己的钱包能不能承受得住。
三、温度监测。
1. 温度计。
普通的玻璃温度计就像个老实巴交的小兵,便宜又简单。
但是读数不太方便,得凑近了看,而且容易碎,就像个脆弱的小瓷人。
热电偶温度计就高级一些,能把温度信号变成电信号,然后传输到控制系统那里。
就像个小间谍,偷偷把温度情报送出去。
它的精度也比较高,不过也得定期检查校准,不然小间谍也可能传递错误情报呢。
2. 温度传感器。
除了热电偶,还有热电阻传感器之类的。
这些传感器就像一群小侦探,分布在反应釜的各个关键位置,把不同地方的温度都监测到。
反应釜自动化控制说明
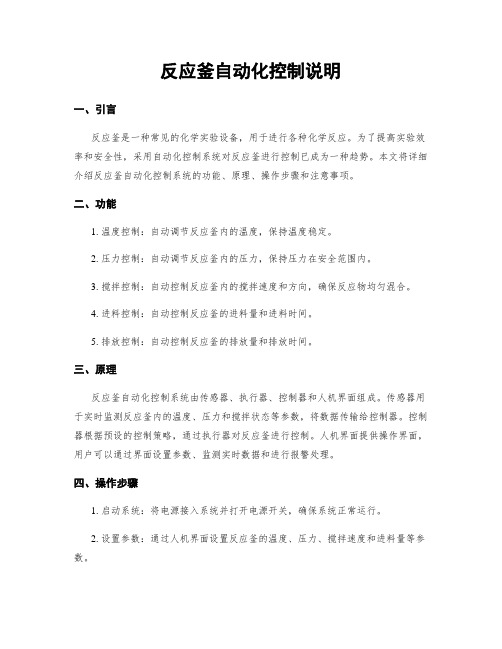
反应釜自动化控制说明一、引言反应釜是一种常见的化学实验设备,用于进行各种化学反应。
为了提高实验效率和安全性,采用自动化控制系统对反应釜进行控制已成为一种趋势。
本文将详细介绍反应釜自动化控制系统的功能、原理、操作步骤和注意事项。
二、功能1. 温度控制:自动调节反应釜内的温度,保持温度稳定。
2. 压力控制:自动调节反应釜内的压力,保持压力在安全范围内。
3. 搅拌控制:自动控制反应釜内的搅拌速度和方向,确保反应物均匀混合。
4. 进料控制:自动控制反应釜的进料量和进料时间。
5. 排放控制:自动控制反应釜的排放量和排放时间。
三、原理反应釜自动化控制系统由传感器、执行器、控制器和人机界面组成。
传感器用于实时监测反应釜内的温度、压力和搅拌状态等参数,将数据传输给控制器。
控制器根据预设的控制策略,通过执行器对反应釜进行控制。
人机界面提供操作界面,用户可以通过界面设置参数、监测实时数据和进行报警处理。
四、操作步骤1. 启动系统:将电源接入系统并打开电源开关,确保系统正常运行。
2. 设置参数:通过人机界面设置反应釜的温度、压力、搅拌速度和进料量等参数。
3. 开始控制:点击开始按钮,系统开始自动控制反应釜。
4. 监测数据:通过人机界面实时监测反应釜内的温度、压力和搅拌状态等数据。
5. 处理报警:如果系统检测到异常情况,及时处理报警信息,确保实验安全。
6. 停止控制:实验结束后,点击停止按钮,系统停止对反应釜的控制。
7. 关闭系统:关闭电源开关,断开电源供应。
五、注意事项1. 操作前应仔细阅读反应釜的使用说明书,并按照要求进行操作。
2. 在操作过程中,应保持反应釜周围的环境清洁和整洁,防止杂质进入反应釜。
3. 在设置参数时,应根据实验要求合理设置温度、压力、搅拌速度和进料量等参数。
4. 在操作过程中,应随时监测反应釜内的温度、压力和搅拌状态等数据,确保实验安全。
5. 如遇到异常情况,应及时处理报警信息,采取相应的措施,确保实验顺利进行。
化工反应釜控制温度的操作方法

化工反应釜控制温度的操作方法
化工反应釜控制温度的操作方法可以通过以下几个步骤实施:
1. 设定目标温度:根据反应需要和工艺要求,确定反应釜应该维持的目标温度。
2. 开启恒温系统:打开反应釜的恒温系统,确保温度控制回路正常运行。
3. 调节加热功率:根据实际温度和目标温度之间的差异,调节反应釜的加热功率。
如果实际温度低于目标温度,增加加热功率;如果实际温度高于目标温度,降低加热功率。
4. 监控温度变化:持续监控反应釜内的温度变化情况。
可以使用温度传感器和温度控制仪表等设备进行实时监测。
5. 调整控制参数:根据实际情况和温度变化趋势,适时调整温度控制参数,例如调整温度控制器的比例、积分和微分参数,以使温度控制更加精确。
6. 考虑安全性:在控制温度的过程中,要确保反应釜内的温度不超出安全限制,并采取措施防止温度过高或过低,例如使用降温装置或停止加热。
7. 记录数据:及时记录温度变化和控制过程中的关键数据,以便后续分析和改进。
需要注意的是,化工反应釜控制温度的操作方法可能因具体工艺和设备而异,以上步骤仅供参考,在实际操作中需要结合具体情况进行调整和改进。
夹套反应釜温度控制浅析

化工设备夹套反应釜温度控制浅析吴康明 李嘉斌(中国天辰化学工程公司黑龙江分公司 150076) 摘 要:在叔十二碳乙硫醇的设计中,采用分程控制系统来保持釜温的稳定并使反应釜的起动和正常生产都能自动操作。
关键词:反应釜;分程控制;气开式;气关式中图分类号:T Q 052 文献标识码:BSimple Explanation for Stillage T emperatureWu Kangming Li Jiabin(China T ianchen Chem ical Enginceing corp.Heilong Jiang Branch 150076)Abstract :During the designing of producing tert -dode -canoic E thylsulfhydrate ,we use the step control system to stabilize the stillage tem perature and to operate the start and normal production of stillage automatically.K eyw ords :S tillage ;S tep control ;Air open ;Air close 在叔十二碳乙硫醇的设计中,夹套反应釜的温度控制是一个难点。
当十二烯等原料及催化剂在反应釜中配置好后,一开始时,需要对反应釜加热,以起动反应过程,反应起动后,因为此化学反应是放热反应,所以会放出大量的热量,为了使反应持续平稳地进行下去,就需要保持釜温的稳定,这样必须要把反应热取走。
在这种场合,若要反应釜的起动和正常生产都能自动操作,就必须要采用分程控制系统。
在简单控制系统中,一个调节器的输出只带动一个调节阀。
而所谓的分程控制系统,就是一个调节器的输出去带动两个或两个以上的调节阀工作。
每个调节阀仅在调节器输出的某段信号范围内动作。
反应釜的工作原理
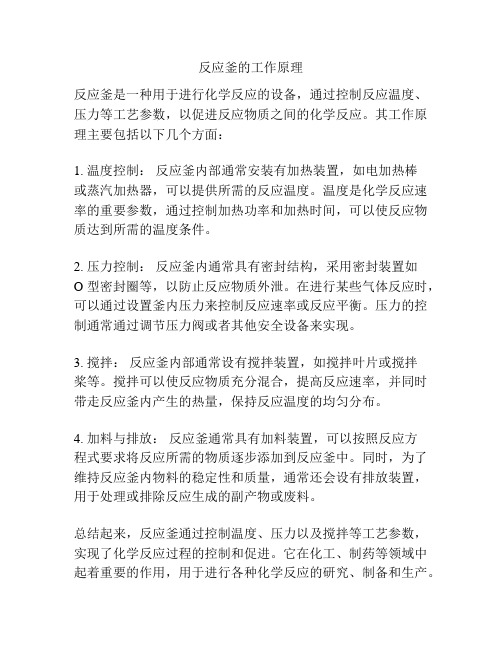
反应釜的工作原理
反应釜是一种用于进行化学反应的设备,通过控制反应温度、压力等工艺参数,以促进反应物质之间的化学反应。
其工作原理主要包括以下几个方面:
1. 温度控制:反应釜内部通常安装有加热装置,如电加热棒
或蒸汽加热器,可以提供所需的反应温度。
温度是化学反应速率的重要参数,通过控制加热功率和加热时间,可以使反应物质达到所需的温度条件。
2. 压力控制:反应釜内通常具有密封结构,采用密封装置如
O型密封圈等,以防止反应物质外泄。
在进行某些气体反应时,可以通过设置釜内压力来控制反应速率或反应平衡。
压力的控制通常通过调节压力阀或者其他安全设备来实现。
3. 搅拌:反应釜内部通常设有搅拌装置,如搅拌叶片或搅拌
桨等。
搅拌可以使反应物质充分混合,提高反应速率,并同时带走反应釜内产生的热量,保持反应温度的均匀分布。
4. 加料与排放:反应釜通常具有加料装置,可以按照反应方
程式要求将反应所需的物质逐步添加到反应釜中。
同时,为了维持反应釜内物料的稳定性和质量,通常还会设有排放装置,用于处理或排除反应生成的副产物或废料。
总结起来,反应釜通过控制温度、压力以及搅拌等工艺参数,实现了化学反应过程的控制和促进。
它在化工、制药等领域中起着重要的作用,用于进行各种化学反应的研究、制备和生产。
反应釜的控制方案
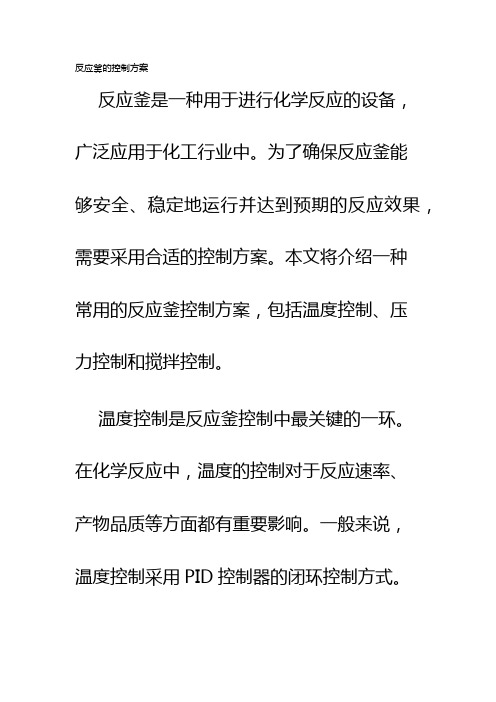
反应釜的控制方案反应釜是一种用于进行化学反应的设备,广泛应用于化工行业中。
为了确保反应釜能够安全、稳定地运行并达到预期的反应效果,需要采用合适的控制方案。
本文将介绍一种常用的反应釜控制方案,包括温度控制、压力控制和搅拌控制。
温度控制是反应釜控制中最关键的一环。
在化学反应中,温度的控制对于反应速率、产物品质等方面都有重要影响。
一般来说,温度控制采用PID控制器的闭环控制方式。
PID控制器通过不断地测量反应釜中的温度,并与设定的目标温度进行比较,然后通过调节加热器的功率来实现温度的控制。
在实际应用中,由于反应釜的惯性比较大,反应过程中温度的变化较为迟缓,因此需要合理设置PID控制器的参数,使其能够快速、准确地响应温度变化。
压力控制是反应釜控制的另一个重要方面。
反应釜在进行化学反应时,会产生一定的气体压力。
过高的压力可能导致反应釜爆炸的危险,而过低的压力则可能影响反应的进行。
因此,需要采用合适的控制方案来控制反应釜的压力。
一种常用的压力控制方案是采用PID控制器进行闭环控制。
PID控制器通过不断地测量反应釜的压力,并与设定的目标压力进行比较,然后通过调节进气阀的开度来实现压力的控制。
类似于温度控制,压力控制也需要合理设置PID控制器的参数,使其能够快速、准确地响应压力的变化。
搅拌控制是反应釜控制的另一个重要方面。
在化学反应中,通过搅拌可以提高反应物的混合程度,加快反应速率,并保持反应物和产物的均匀性。
因此,搅拌控制对于反应釜的控制效果具有重要影响。
搅拌控制中常用的方法是采用变频调速器控制搅拌电机的转速。
通过调节搅拌电机的转速,可以实现搅拌效果的调节。
在设计搅拌控制方案时,需要根据具体的反应釜和反应物的特性,合理选择搅拌电机的转速范围和变频调速器的参数。
除了温度、压力和搅拌控制之外,还需要考虑其他的控制因素。
例如,反应釜的加热方式、冷却方式、进料方式等对反应过程中的温度、压力和搅拌等参数也有影响。
因此,在设计反应釜的控制方案时,需要综合考虑这些因素,并进行合理的协调。
PID控制例1:反应釜温度自动控制回路资料
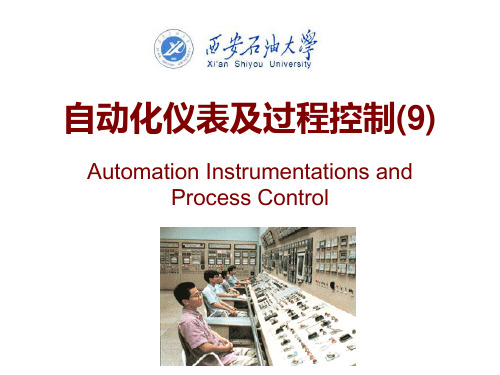
•两步法:先副后主 •一步法:定副调主
x1
x2
+ - Gc1 +
Gc2 -
y2
y1
Go2
Go1
TN
21
串级调节系统例:
夹套式反应釜温度控制
TN
22
比值调节系统
保证两种(或两种以上)物料流量保持 一定比例的调节系统。 FC:比值调节器, 比值=K
QB=KQA
开环比值系统
TN
23
比值调节系统
单闭环比值调节系统
而引入的一个中间参数)
Gc1(s):主调节器 Gc2(s):副调节器
TN
16
串级调节系统特点
•副回路中的干扰,主要在副回路中克服。 •减少了副对象的T,提高了副环的调节 品质。 •提高了系统的频率响应,加快了抗干扰 过程的速度。 •提供了灵活的控制方式
TN
17
串级调节系统应用
TN
18
串级调节系统应用
自动化仪表及过程控制(9)
Automation Instrumentations and Process Control
PID控制例1:反应釜温度自动控制回路
TN
2
PID控制例2:供水水压自动控制回路
TN
3
系统调节方案的选择
间接指标控制:对于不便直接 调节的工艺直接指标,可以选 择一个与直接指标相关的量进 行调节,间接完成控制任务。 例:精馏塔生产过程,
调节系统过渡过程的稳态误差超过工艺规定,则下 列哪项调整方法可以改善上述不足?
(A)增加比例度; (B)减少积分时间 ; (C)增加积分时间; (D)减少微分时间。
TN
9
第6章 单回路调节系统
搪瓷反应釜目标温度优化与控制算法的研究

搪瓷反应釜目标温度优化与控制算法的研究目标温度优化是指在搪瓷反应过程中,通过合理地选择目标温度,使得化学反应能够以最佳速率进行,从而提高反应效率和产品质量。
目标温度优化涉及到多个方面的因素,例如反应速率、反应热和反应体积等。
一般来说,目标温度应该能够最大程度地提高反应速率,同时也要考虑到反应热带来的影响,以及反应体积对于温度的敏感度。
为了实现目标温度优化,需要设计相应的控制算法。
常见的控制算法包括PID控制算法、模型预测控制(MPC)算法和模糊控制算法等。
PID 控制算法是最常用的控制算法之一,它通过调整温度控制器的比例、积分和微分参数,实现对温度的精确控制。
MPC算法是一种基于数学模型的预测控制算法,它可以考虑到系统的约束条件,从而更加适用于复杂的搪瓷反应过程。
模糊控制算法则是一种基于模糊推理的控制算法,它能够处理系统的非线性和不确定性,因此在一些特殊情况下也能够发挥重要作用。
在研究搪瓷反应釜的目标温度优化和控制算法时,需要考虑到具体的搪瓷反应过程和设备特点。
首先,需要对搪瓷反应过程进行建模,并确定关键的温度控制参数。
其次,需要选择合适的控制算法,并根据实际情况对控制算法进行调整和优化。
最后,需要通过实验和仿真等方法验证所设计的目标温度优化和控制算法的性能。
总之,搪瓷反应釜目标温度优化与控制算法的研究是一个复杂而关键的问题,它对于提高反应效率和产品质量有着重要意义。
通过合理地选择目标温度和设计控制算法,可以实现对搪瓷反应过程的精确控制,从而提高反应过程的效果和产品的质量。
反应釜操作规程(3篇)

反应釜操作规程反应釜是一种常见的实验设备,用于进行化学反应。
为了保证操作的安全和实验的成功,反应釜的操作规程非常重要。
下面是一份关于反应釜操作规程的例子,供参考:第一章总则第一条为保证实验的安全、有效进行,所有使用反应釜的人员必须熟悉并遵守本操作规程。
第二章设备准备第一条检查反应釜的设备是否完好,如螺丝、夹持装置、搅拌器、温度计等是否正常工作。
第二条确保反应釜内部干净整洁,如有污垢应清除干净。
第三条检查反应釜的密封性能,确认密封件是否完好。
第四条确保反应釜周围的通风设备正常工作。
第三章实验准备第一条确认所需的实验试剂及所需的实验条件。
第二条准备实验所需的辅助设备和工具。
第四章操作步骤第一节加料第一条将反应釜放在支架上并固定。
第二条检查加料阀门是否正常开启或关闭。
第三条打开加料阀门,将所需试剂慢慢加入反应釜。
第四条关闭加料阀门,确保密封性。
第二节加热第一条检查加热装置是否正常工作,确认温度控制器是否可调。
第二条打开加热装置,将反应釜加热到所需温度。
第三条注意观察反应过程中的温度变化,根据需要调整加热功率。
第四节搅拌第一条打开搅拌装置,选择适当的搅拌速度。
第二条观察反应过程中的搅拌情况,根据需要进行调整。
第五章实验结束第一节降温第一条关闭加热装置,待反应釜冷却到室温后,打开降温阀门。
第二条根据实验需要,选择适当的降温方法和时间。
第三条等待反应釜冷却完全,才可以打开反应釜。
第二节清洗第一条使用适当的溶剂清洗反应釜内部。
第二条将反应釜内部的残留物清除干净。
第三条检查反应釜的密封件和设备是否正常。
第四条将反应釜进行彻底的清洗和消毒,确保下一次使用前安全可靠。
第六章安全注意事项第一条反应釜操作时,应戴好防护眼镜、手套等个人防护用品。
第二条在加热反应釜时,应注意防止加热过程中的溅油。
第三条在操作反应釜时应注意避免产生或接触有毒、易燃、易爆等物质。
第四条在加热和搅拌反应时,应注意不要使反应釜过度增温或过度搅拌。
光催化反应釜 温度
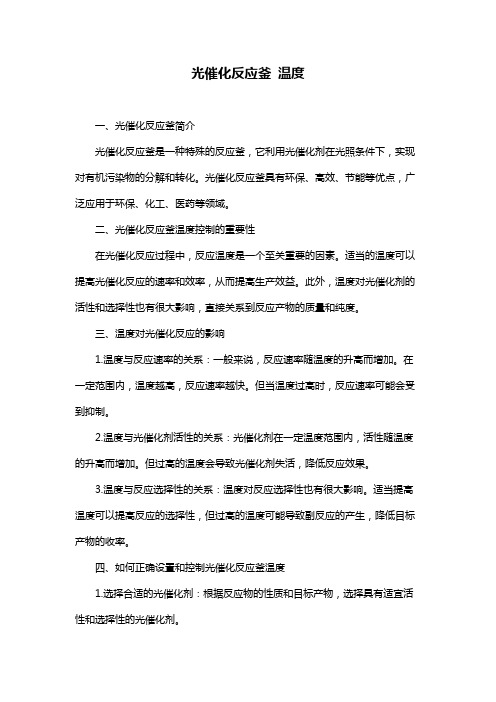
光催化反应釜温度一、光催化反应釜简介光催化反应釜是一种特殊的反应釜,它利用光催化剂在光照条件下,实现对有机污染物的分解和转化。
光催化反应釜具有环保、高效、节能等优点,广泛应用于环保、化工、医药等领域。
二、光催化反应釜温度控制的重要性在光催化反应过程中,反应温度是一个至关重要的因素。
适当的温度可以提高光催化反应的速率和效率,从而提高生产效益。
此外,温度对光催化剂的活性和选择性也有很大影响,直接关系到反应产物的质量和纯度。
三、温度对光催化反应的影响1.温度与反应速率的关系:一般来说,反应速率随温度的升高而增加。
在一定范围内,温度越高,反应速率越快。
但当温度过高时,反应速率可能会受到抑制。
2.温度与光催化剂活性的关系:光催化剂在一定温度范围内,活性随温度的升高而增加。
但过高的温度会导致光催化剂失活,降低反应效果。
3.温度与反应选择性的关系:温度对反应选择性也有很大影响。
适当提高温度可以提高反应的选择性,但过高的温度可能导致副反应的产生,降低目标产物的收率。
四、如何正确设置和控制光催化反应釜温度1.选择合适的光催化剂:根据反应物的性质和目标产物,选择具有适宜活性和选择性的光催化剂。
2.设计合理的反应条件:根据光催化反应的特点,确定合适的反应温度、光照强度、反应时间等条件。
3.温度控制设备:选用具有温度控制功能的反应釜,如恒温加热套、智能温度控制器等。
4.监测与调整:在反应过程中,实时监测反应温度,根据实际情况进行调整,确保反应在最佳温度下进行。
五、总结光催化反应釜温度对反应效果具有重要影响。
正确设置和控制反应温度,可以提高光催化反应的速率和效率,提高产物的质量和纯度。
反应釜自动化控制说明
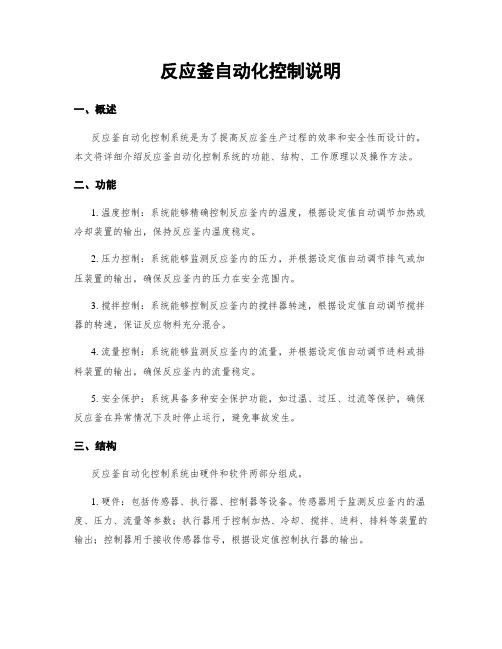
反应釜自动化控制说明一、概述反应釜自动化控制系统是为了提高反应釜生产过程的效率和安全性而设计的。
本文将详细介绍反应釜自动化控制系统的功能、结构、工作原理以及操作方法。
二、功能1. 温度控制:系统能够精确控制反应釜内的温度,根据设定值自动调节加热或冷却装置的输出,保持反应釜内温度稳定。
2. 压力控制:系统能够监测反应釜内的压力,并根据设定值自动调节排气或加压装置的输出,确保反应釜内的压力在安全范围内。
3. 搅拌控制:系统能够控制反应釜内的搅拌器转速,根据设定值自动调节搅拌器的转速,保证反应物料充分混合。
4. 流量控制:系统能够监测反应釜内的流量,并根据设定值自动调节进料或排料装置的输出,确保反应釜内的流量稳定。
5. 安全保护:系统具备多种安全保护功能,如过温、过压、过流等保护,确保反应釜在异常情况下及时停止运行,避免事故发生。
三、结构反应釜自动化控制系统由硬件和软件两部分组成。
1. 硬件:包括传感器、执行器、控制器等设备。
传感器用于监测反应釜内的温度、压力、流量等参数;执行器用于控制加热、冷却、搅拌、进料、排料等装置的输出;控制器用于接收传感器信号,根据设定值控制执行器的输出。
2. 软件:包括控制算法和人机界面。
控制算法根据传感器信号和设定值进行计算,生成控制信号;人机界面提供操作界面,用户可以通过界面设置设定值、监测参数、查看报警信息等。
四、工作原理1. 温度控制:系统通过传感器监测反应釜内的温度,并将实际温度与设定值进行比较。
根据比较结果,控制器调节加热或冷却装置的输出,使温度保持在设定值附近。
2. 压力控制:系统通过传感器监测反应釜内的压力,并将实际压力与设定值进行比较。
根据比较结果,控制器调节排气或加压装置的输出,使压力保持在设定值范围内。
3. 搅拌控制:系统通过传感器监测反应釜内的搅拌器转速,并将实际转速与设定值进行比较。
根据比较结果,控制器调节搅拌器的转速,使转速保持在设定值附近。
4. 流量控制:系统通过传感器监测反应釜内的流量,并将实际流量与设定值进行比较。
反应釜的温度要怎么控制

反应釜的温度要怎么控制
反应釜一般都有搅拌器,保证反应釜内温度均匀。
反应釜温度控制分升温和降温两种(视内部是放热反应还是吸热),升温采用蒸汽、熔盐或者其他加热介质,降温一般是冷却水或者其他介质,不论加热或者降温都是采取加热或者冷却介质流量控制,手动开关阀门,或者用自动控制采用温度显示信号通过控制器控制加热、冷却介质的调节阀调节流量来控制。
岩征反应釜的控制法则如下:
整个液体循环是真正的全封闭的系统,打破传统,全球独家。
2、升温和降温的速度块,精确控制化学反应系统
3、低温时导热介质不会吸收水汽
4、导热介质不会被氧化,变色,或褐化
高温时没有油雾产生
6、快速响应系统的热动力学变化,不论是剧烈的吸热或者放热反应,不会有控温滞后现象。
7、一种导热介质可以用于低温和高温,可以用于-90℃—200℃的温度范围(独家)。
8、使用成本低,一劳永逸。
反应釜温度控制(DOC)
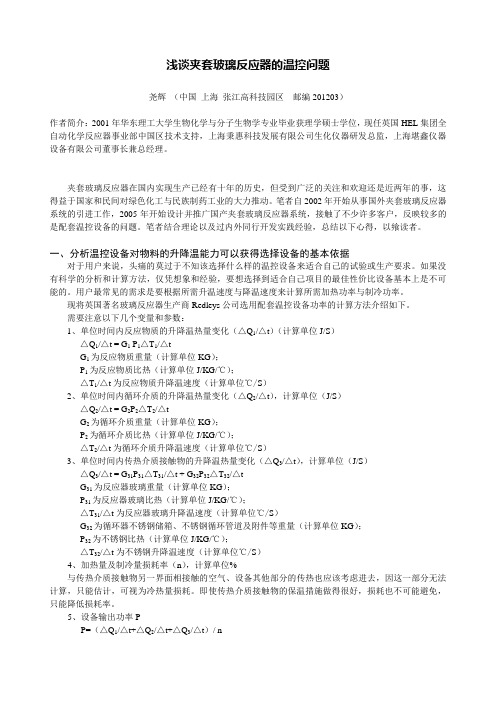
浅谈夹套玻璃反应器的温控问题尧辉(中国上海张江高科技园区邮编201203)作者简介:2001年华东理工大学生物化学与分子生物学专业毕业获理学硕士学位,现任英国HEL集团全自动化学反应器事业部中国区技术支持,上海秉惠科技发展有限公司生化仪器研发总监,上海堪鑫仪器设备有限公司董事长兼总经理。
夹套玻璃反应器在国内实现生产已经有十年的历史,但受到广泛的关注和欢迎还是近两年的事,这得益于国家和民间对绿色化工与民族制药工业的大力推动。
笔者自2002年开始从事国外夹套玻璃反应器系统的引进工作,2005年开始设计并推广国产夹套玻璃反应器系统,接触了不少许多客户,反映较多的是配套温控设备的问题。
笔者结合理论以及过内外同行开发实践经验,总结以下心得,以飨读者。
一、分析温控设备对物料的升降温能力可以获得选择设备的基本依据对于用户来说,头痛的莫过于不知该选择什么样的温控设备来适合自己的试验或生产要求。
如果没有科学的分析和计算方法,仅凭想象和经验,要想选择到适合自己项目的最佳性价比设备基本上是不可能的。
用户最常见的需求是要根据所需升温速度与降温速度来计算所需加热功率与制冷功率。
现将英国著名玻璃反应器生产商Redleys公司选用配套温控设备功率的计算方法介绍如下。
需要注意以下几个变量和参数:1、单位时间内反应物质的升降温热量变化(△Q1/△t)(计算单位J/S)△Q1/△t = G1 P1△T1/△tG1为反应物质重量(计算单位KG);P1为反应物质比热(计算单位J/KG/℃);△T1/△t为反应物质升降温速度(计算单位℃/S)2、单位时间内循环介质的升降温热量变化(△Q2/△t),计算单位(J/S)△Q2/△t = G2P2△T2/△tG2为循环介质重量(计算单位KG);P2为循环介质比热(计算单位J/KG/℃);△T2/△t为循环介质升降温速度(计算单位℃/S)3、单位时间内传热介质接触物的升降温热量变化(△Q3/△t),计算单位(J/S)△Q3/△t = G31P31△T31/△t + G32P32△T32/△tG31为反应器玻璃重量(计算单位KG);P31为反应器玻璃比热(计算单位J/KG/℃);△T31/△t为反应器玻璃升降温速度(计算单位℃/S)G32为循环器不锈钢储箱、不锈钢循环管道及附件等重量(计算单位KG);P32为不锈钢比热(计算单位J/KG/℃);△T32/△t为不锈钢升降温速度(计算单位℃/S)4、加热量及制冷量损耗率(n),计算单位%与传热介质接触物另一界面相接触的空气、设备其他部分的传热也应该考虑进去,因这一部分无法计算,只能估计,可视为冷热量损耗。
反应釜间歇反应过程温度控制特点

反应釜间歇反应过程温度控制特点反应釜是一种广泛应用于化学、医药、食品、冶金等领域的设备,其采用了间歇反应的方式进行化学反应。
在反应釜内,温度是一个至关重要的控制因素,能够影响到反应的速率、产物的选择和质量,甚至是反应是否能够成功实施。
因此,在间歇反应过程中,温度控制是一个非常重要和特殊的问题。
首先,反应釜间歇反应过程温度控制的特点之一是瞬时性。
由于反应釜是一个封闭的体系,外部热量输入量是不稳定的。
在反应釜内,化学反应会放出大量的热能,进而会导致反应釜内部的温度急剧上升。
因此,必须采取一定的措施,及时地调节反应釜内的温度以保证反应的稳定进行。
其次,反应釜间歇反应过程温度控制的特点之二是持续性。
由于反应釜内的反应是间歇式的,因此每次进行反应之前都需要保持反应釜内部的温度恒定。
当反应开始后,反应釜内的温度会急剧上升,此时需要通过冷却系统来降低温度,以保证反应稳定进行。
一旦反应结束,还需要及时地恢复反应釜内的温度到初始状态,以方便下次反应的开始。
最后,反应釜间歇反应过程温度控制的特点之三是灵活性。
反应釜内的化学反应需要合理选取不同的反应条件,包括反应时间、反应温度、反应物浓度等参数。
因此,温度控制系统需要具备良好的控制灵活性,以便根据反应物和反应条件的不同需要进行调整和优化。
总之,反应釜间歇反应过程温度控制是一个非常关键和特殊的问题,必须采取一定的措施来确保反应的稳定性和成功性。
在使用反应釜进行化学反应时,必须深刻理解温度控制的特点,采取相应的措施,才能够取得优异的反应效果和结果。
- 1、下载文档前请自行甄别文档内容的完整性,平台不提供额外的编辑、内容补充、找答案等附加服务。
- 2、"仅部分预览"的文档,不可在线预览部分如存在完整性等问题,可反馈申请退款(可完整预览的文档不适用该条件!)。
- 3、如文档侵犯您的权益,请联系客服反馈,我们会尽快为您处理(人工客服工作时间:9:00-18:30)。
浅谈夹套玻璃反应器的温控问题尧辉(中国上海张江高科技园区邮编201203)作者简介:2001年华东理工大学生物化学与分子生物学专业毕业获理学硕士学位,现任英国HEL集团全自动化学反应器事业部中国区技术支持,上海秉惠科技发展有限公司生化仪器研发总监,上海堪鑫仪器设备有限公司董事长兼总经理。
夹套玻璃反应器在国内实现生产已经有十年的历史,但受到广泛的关注和欢迎还是近两年的事,这得益于国家和民间对绿色化工与民族制药工业的大力推动。
笔者自2002年开始从事国外夹套玻璃反应器系统的引进工作,2005年开始设计并推广国产夹套玻璃反应器系统,接触了不少许多客户,反映较多的是配套温控设备的问题。
笔者结合理论以及过内外同行开发实践经验,总结以下心得,以飨读者。
一、分析温控设备对物料的升降温能力可以获得选择设备的基本依据对于用户来说,头痛的莫过于不知该选择什么样的温控设备来适合自己的试验或生产要求。
如果没有科学的分析和计算方法,仅凭想象和经验,要想选择到适合自己项目的最佳性价比设备基本上是不可能的。
用户最常见的需求是要根据所需升温速度与降温速度来计算所需加热功率与制冷功率。
现将英国著名玻璃反应器生产商Redleys公司选用配套温控设备功率的计算方法介绍如下。
需要注意以下几个变量和参数:1、单位时间内反应物质的升降温热量变化(△Q1/△t)(计算单位J/S)△Q1/△t = G1 P1△T1/△tG1为反应物质重量(计算单位KG);P1为反应物质比热(计算单位J/KG/℃);△T1/△t为反应物质升降温速度(计算单位℃/S)2、单位时间内循环介质的升降温热量变化(△Q2/△t),计算单位(J/S)△Q2/△t = G2P2△T2/△tG2为循环介质重量(计算单位KG);P2为循环介质比热(计算单位J/KG/℃);△T2/△t为循环介质升降温速度(计算单位℃/S)3、单位时间内传热介质接触物的升降温热量变化(△Q3/△t),计算单位(J/S)△Q3/△t = G31P31△T31/△t + G32P32△T32/△tG31为反应器玻璃重量(计算单位KG);P31为反应器玻璃比热(计算单位J/KG/℃);△T31/△t为反应器玻璃升降温速度(计算单位℃/S)G32为循环器不锈钢储箱、不锈钢循环管道及附件等重量(计算单位KG);P32为不锈钢比热(计算单位J/KG/℃);△T32/△t为不锈钢升降温速度(计算单位℃/S)4、加热量及制冷量损耗率(n),计算单位%与传热介质接触物另一界面相接触的空气、设备其他部分的传热也应该考虑进去,因这一部分无法计算,只能估计,可视为冷热量损耗。
即使传热介质接触物的保温措施做得很好,损耗也不可能避免,只能降低损耗率。
5、设备输出功率PP=(△Q1/△t+△Q2/△t+△Q3/△t)/ n油槽加热功率计算:水比热:4200J/KG/℃硅油比热:1630 J/KG/℃玻璃平均比热:920J/KG/℃304不锈钢比热:460 J/KG/℃物料(以水计算)要求升温速度:80℃/3600S(从室温20℃升到100℃)物料(以水计算)量:14KG油箱装油量:15KG油管装油量:0.5KG夹套装油量:6KG20升夹套玻璃反应器重量:16 KG304不锈钢箱、泵、阀门及接头等重量:35KG根据经验,在保温措施较好和传热介质流速足够的情况下,20升反应器的物料(以水计算)达到要求温度(t℃)时,夹套平均油温约为:t+10℃;油管平均温度约为t+15℃;油槽平均温度为t+20℃。
油直接受热部位为油槽。
无加热量损耗的理想状态下的最小功率为(4200J/KG/℃×80℃×14KG +1630J/KG/℃×100℃×21.5KG水的热量变化油的热量变化+920 J/KG/℃×90℃×16KG +460 J/KG/℃×100℃×35KG)÷3600S玻璃的热量变化不锈钢的热量变化单位时间=3095.35W考虑到保温不完全导致的损耗、设备加热温控能力的弹性、泵速促进及时充分地进行热交换的水平,功率至少应设计为4KW。
制冷设备功率计算如下:油泵制冷功率稍微要复杂一些,因为压缩机的制冷输入功率与制冷量是两个概念,而且这两项还是随不同制冷剂蒸发温度和冷凝温度而异,以本公司DL-45-20全封闭制冷恒温循环油泵(无氟制冷)采用的丹麦Danfoss NTZ048制冷压缩机(2匹)与R404A制冷剂组合为例,其在不同蒸发温度和冷凝温度的制冷量与输入功率见下表:T Q P Q P Q P Q P Q P Q P Q P Q P NTZ048 30 466 0.50 774 0.70 1160 0.90 1636 1.10 2211 1.27 2896 1.42 3700 1.54 4635 1.6235 371 0.47 655 0.67 1010 0.89 1445 1.10 1972 1.31 2600 1.49 3340 1.64 4202 1.76T o:蒸发温度(℃)T c:冷凝温度(℃)Q o:制冷量(W)P e:输入功率(kW)而且计算还应以所需最低温度时的制冷量来计算。
但计算方式与油槽加热功率基本相同。
以本公司生产的DL-45系列全封闭低温恒温循环油泵为例,油泵制冷功率(制冷量)计算如下:水比热:4200J/KG/℃硅油比热:1630 J/KG/℃玻璃平均比热:920J/KG/℃304不锈钢比热:460 J/KG/℃物料(以水计算)要求降温速度:40℃/3600S(从室温20℃降到-20℃)物料(以水计算)量:14KG油箱装油量:2KG油管装油量:0.5KG夹套装油量:6KG交换器装油量:0.5KG20升夹套玻璃反应器重量:16 KG304不锈钢箱、泵、阀门及接头等重量:20KG根据经验,在保温措施较好和传热介质流速足够的情况下,20升反应器的物料(以水计算)达到要求温度(t℃)时,夹套平均油温约为:t-10℃;油管平均温度约为t-15℃;制冷剂和油热交换器平均温度为t-20℃。
油直接受冷部位为热交换器即制冷设备的蒸发器。
无制冷量损耗的理想状态下的最小功率为(4200J/KG/℃×40℃×14KG +1630J/KG/℃×60℃×9KG水的热量变化油的热量变化+920 J/KG/℃×50℃×16KG +460 J/KG/℃×60℃×20KG)÷3600S玻璃的热量变化不锈钢的热量变化单位时间=1255.59W制冷剂蒸发温度要求至少-35℃。
从上表中可以看到丹麦Danfoss NTZ048制冷压缩机(2匹)制冷剂蒸发温度-35℃、冷凝温度30℃时,制冷量为1160W。
此时该型压缩机制冷量虽接近1255.59W的数值,但考虑到保温不完全导致的损耗、设备制冷温控能力的弹性、制冷剂蒸发器热交换面积发挥压缩机制冷能力的水平、泵速促进充分及时进行热交换的水平,该型压缩机也不能满足要求,所以应该选择使用3匹以上的制冷压缩机。
二、用户选择反应器及温控设备应该注意的几个问题1、反应器及保温措施1)循环介质进、出口的选择目前国内生产的夹套玻璃反应器循环介质进出口主要有宝塔头、法兰口两种,以宝塔头居多。
笔者认为宝塔头接口虽然方便,但却有许多弊端:首先,外型上呈逐渐缩小的造型容易产生阻力影响循环介质的流速,高速流动的液体还会因此形成对玻璃的冲力进而形成对夹套的压力,对玻璃反应器具有潜在的破坏力;其次宝塔形和玻璃的脆性决定了它只能与软管直接连接,因为目前软橡胶类材料的耐温能力不超过250℃,因此使用宝塔头接口意味着您选择的产品物料温度很难超过210℃,对于20升以上的中试级反应器而言,传热阻力更大,可达到的温度值只会更低;而且,使用橡胶软管还不能避免橡胶会老化的问题。
所以,笔者推荐使用法兰接口,这也是国外同行通用的接口,它可以避免宝塔头接口的许多弊端,唯一的缺点就是装卸较烦琐一些。
现在也有快开式连接,其实使用起来也很方便快捷,比宝塔头与橡胶类软管连接还更省力些。
笔者所在公司开发的夹套玻璃反应器全部使用法兰接口,目前尚无用户提出不同意见。
2)内置耐腐蚀盘管该配件也可起到加热、冷却器的功能,还可充当支撑骨架固定柔性温度测量探头,不影响搅拌桨的尽量放大,可谓功能多多。
作为加热器时可通蒸汽、热水或热油;作为冷却器时可通水、冷的醇水混合液和冷油甚至液氮。
常见的制作方法有薄壁PTFE包被金属管道。
有不少人排斥使用内置盘管,认为它清洗不方便,其实包被薄壁PTFE的金属管道与固定在大型金属反应釜体上的盘管不一样,前者很容易拆卸和清洗,而且造价并不高,可更换使用。
须注意不锈钢喷镀PTFE的方法并不可取,不仅是因为渡层太薄易剥落而且喷镀成本高,最重要的原因是喷镀完毕后形成的是有细小网孔的网状镀层,并不能起到防止化学腐蚀的作用。
3)真空夹层其原理在于消除热传导中的空气对流因素,就象保温瓶胆抽真空。
玻璃反应容器采用三层设计时,对外层夹套抽真空并封闭形成真空夹层,这样反应保温效果好。
而且低温时,外层玻璃表面无水雾亦不会结霜,反应清晰可见;高温时外层玻璃表面不炙热,可免除烫伤危险。
但三层玻璃反应器的应力点很多,烧制成功率不高,容积越大的反应器越是这样。
4)测温套及测温点目前市场上大多数玻璃反应器使用的是固定式温度计玻璃套管来测物料温度,套管从盖子上固定处深入釜内某一深度。
这样做的缺点很多:1)搅拌棒在某一转速段可能出现强烈的共振,可能撞击温度计玻璃套管;2)中试级的反应器(20~50升)的玻璃套管处于搅拌轴与内壁的中央,使用涡轮式搅拌桨时很容易被页片打到,致使叶片不能做到尽可能的大而影响搅拌效果;3)当物料装得多的时候,套管受力大易折裂,物料装得少的时候则套管可能接触不到物料而无法测温。
我们开发了插入深度可调的温度计套管可弥补第三种缺陷。
另外还开发了可与内置换热盘管捆绑使用的可任意弯曲的温度探头,这样就可将测温点置于靠近反应器内壁的任一深度,并且不影响使用更大搅拌半径的搅拌桨页。
当然这种应用的前提是须同时使用内置换热盘管。
另外,国外已有从底部阀门中央突出部位内置温度探头来进行温度的数字测量,一般突出部位最高点比釜底高1~2cm。
这种方式测量的是底部物料的温度,比较适合于小型反应器和应搅动混匀的液体,对于较大的反应器或粘度大的物料不合适。
而且,对于较大的反应器而言,夹套高度也大,因为高温流体密度小,低温流体密度大,一般在夹套下部循环介质温度要比上部低。
所以对大型反应器而言,底部测温的方式测得物料温度是偏低的。
如果循环介质的流速足够的快,这种偏差要小些,但高速流体也同时对反应器的强度提出了更高的要求,这恰恰是大型玻璃反应器夹套不如小型玻璃反应器的地方。