民用型煤固硫剂的研究
固硫剂
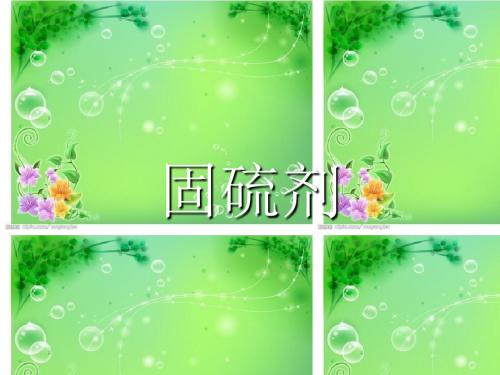
燃煤固硫剂
凡能与煤在燃烧过程中生成 的SO2或 SO3起化学或物理 吸附反应,形成 固态残渣而 留在煤灰中的物质均可作 为固硫剂。燃煤燃烧过程中,大部分硫以SO2的形式外 排.目前采用在原煤中加入石灰并以黏土黏合的方法固 硫。固硫剂种类很多,如 CaCO3、CaO、Ca(OH)2、 MgCO3、MgO、Na2CO3、NaOH 等 。但 目前使 用最 多,价廉易得的是钙基固硫剂 ,即 CaCO3、CaO、 Ca(OH)2。有时也选用电石渣、造纸废液、硼泥等工业 废料。还有高温钡基固硫剂,贝壳也可用作 固硫剂。采 用钙基 、镁基、钡基固硫剂,其 固硫反应发生在SO2或 SO3与金属氧化物之间,其主要化学反应为:
民用型煤固硫剂的分类
固硫剂可分为两类 :一类是单一的钙基固硫 剂:另一类是含有两种以上单一固硫剂的复 合固硫剂。后者燃烧时同时发生两种或多种 固硫反应,或其中一种能起催化作用使另一 种固硫剂的固硫效率提高,因此,复合固硫 剂具有更好的固硫效果。
目前 ,普遍应用的固硫剂是钙基固硫剂,主要包括天 然石灰石、白云石等。钙基固硫剂具有原料丰富,价格 便宜的优势,其主要化学成分包括 Ca(OH)2,CaCO3, CaO。利用钙基固硫剂进行燃烧过程脱硫是指将钙基物 质预混合在燃料中或将其在燃烧锅炉的合适位置喷入炉 膛进行脱硫。目前,钙基固硫剂利用率较低 ,炉内脱 硫率仅为 30%~40%为了提高钙基固硫剂的利用率, 人们进行了大量的研究工作 .主要分为 3类:一是利用 一些特殊的含钙基物质成分或结构上的特点来提高脱硫 率;二是利用调质方法来改善固硫剂的活性;三是利用 添加剂来增强脱硫能力。针对一般型煤固硫剂的研究主 要是围绕 CaO来进行,常用的固硫剂有石灰石、白云 石 、生石灰、消石灰、电石渣、白泥等。固硫添加剂 主要有 Fe2O3,V2O5,KCO3,Na2CO3,NaCl SiO2及含 Sr工业废料等。
【强烈推荐】固(脱)硫催化剂和添加剂项目可研报告

固(脱)硫催化剂和添加剂项目可行性分析一、固(脱)硫催化剂和添加剂概述(一)固(脱)硫催化剂及添加剂的概念固(脱)硫催化剂及添加剂是一种新型的燃煤脱硫添加剂。
主要由助硫氧化催化剂和脱硫剂组成,外观为浅灰白色粉末,具有无毒、无腐蚀性等特点。
该产品主要用于脱除燃料煤中的硫分,同时具有明显的助燃作用。
使用该技术,煤在燃烧过程中,其所含硫与添加剂结合转化为硫酸盐进入炉渣中,当燃料煤中所含的硫量为3%时,可使尾气中的硫氧化物含量降低47%-57%,当含硫量<1.5%时,尾气中硫氧化物含量下降65%,从而达到保护环境的目的。
(二)固(脱)硫催化剂及添加剂的构成固(脱)硫催化剂是燃煤催化剂的一种。
其化学成分主要是碱金属、碱土金属和过渡元素的氧化物、氢氧化物及其盐类,(C、FeCl3、FeCl2和Fe2O3、K2CO3、Na2CO3、Ca(OH)2、CaO、Fe2O3、NaC1、K2MnO3等)。
物理构成主要由60%−98%的固硫剂和2%−40%固硫催化剂制成;其中固硫催化剂是包括下述重量百分比的原料制成:钒类氧化剂2%−12%、抑制剂2%−25%、至少一种镧系催化剂5%−30%、大白土(甘肃产,含Sc、Ce、Fe、Ti、Sn、Ca离子)50%−89%。
(三)固(脱)硫催化剂及添加剂的主要用途固(脱)硫催化剂及添加剂主要应用于燃煤电厂、企业锅炉、高硫煤矿、各种煤质、民用炉、手烧炉、链条炉、往复锅炉、抛煤机炉、反射炉、沸腾炉、粉煤灰炉等工业锅炉。
该产品是解决工业锅炉、窑炉工况差、热效率低、劣质煤利用率低、SO2污染严重等问题的环保产品。
用于工业生产无需改变燃煤设备及条件,劣质煤或优、劣混合煤应用可达到优质煤燃烧效果,添加固硫剂在灼热时将硫迅速固定住,固硫率可达60%−80%,减少SO2的排放量。
二、固(脱)硫催化剂和添加剂技术(一)国内外技术发展现状固硫添加剂是针对治理燃煤造成的大气污染问题应用而产生的一种新型环保产品。
型煤固硫剂的研究与开发的开题报告

型煤固硫剂的研究与开发的开题报告一、选题的背景及意义随着我国经济的高速发展,能源需求量不断增大,而煤炭一直是我国主要的能源,占据了我国能源消费的很大比例。
但是,煤炭中的硫、氮等有害成分对环境和人类健康有着极大的影响,同时也会影响煤炭的利用,提高煤炭利用效率和降低对环境的影响,是当前我国煤炭行业亟待解决的问题。
目前,利用型煤技术是解决煤炭中有害成分问题的一种有效途径,而型煤固硫剂是制备型煤的关键技术之一。
因此,开发一种高效、绿色型煤固硫剂,对于提高煤炭利用效率、降低对环境的影响具有重要意义。
二、研究的目的和内容本项目的目的是研究开发一种高效、环保的型煤固硫剂,主要包括以下内容:1. 对型煤制备工艺进行优化,确定最佳的制备条件和工艺参数。
2. 筛选和评价不同类型的固硫剂,比较它们的固硫效果、对型煤质量的影响和环境友好性等方面的差异。
3. 对最佳方案进行优化,如增强稳定性、降低成本等,并进行测试和评价。
三、研究的方法和技术路线本研究采用以下方法和技术路线:1. 通过文献资料、煤炭样品分析和实验,确定最佳的型煤制备工艺和工艺参数。
2. 筛选和评价不同类型的固硫剂,采用包括固硫剂浸渍、干燥、煅烧、型煤制备等多个环节的实验流程,比较它们的固硫效果、对型煤质量的影响和环境友好性等方面的差异。
3. 优化方案,如增强稳定性、降低成本等,并进行多次测试和评价以确定最佳的方案。
四、预期研究结果和意义通过本项研究,预计可以实现以下结果:1. 确定最佳的型煤制备工艺和工艺参数。
2. 筛选出具有较好固硫效果、对型煤质量影响小、环境友好等特点的固硫剂,为型煤制备提供重要保障。
3. 优化最佳方案,如增强稳定性、降低成本等,为煤炭行业提供有利的技术支持。
本项研究有望为我国型煤技术的发展和煤炭清洁利用提供新的技术手段和思路,具有重要的理论和应用价值。
一种简便实用的型煤固硫效果测定法

悬浮粉尘 和有害 金属颗 粒是 大气 的最大污 染源和 最 主要
的危 害 。目前我 国 酸 雨面积 已达 国土 的 4 %以上 , 0 而燃 煤 则 是我 国最主 要 的 S 排 放 源 ,约 占 S 放总 量 的 O: O排
9 %以上 。 0
实 验 在管 式 加热 炉 上进 行 , 用硅 碳棒 加热 , 温带 高
5 月 刊 ・ 0 2 1 .0 21 2 0 .03
式 中 ,S : 样 中全 硫 含量 ( 。煤 质量 分 数 ) 2 型煤 燃烧 中硫释 放 量测 定 实验 条件 优 化
i
维普资讯
一 , — — — — — — — — — —
ENERG YCONS RV I E Al ON AND ENV RONM ENT I AL PR0 T ECT ON I
:
固硫 剂 、 加 剂 混 合 压 制 而 成 的 一 种 清 洁 燃 料 。本 文 添 探讨 型 煤 在 燃 烧 中硫 的 释 放 , 立 测 试 方 法 , 制 添 建 研
加的 固硫 剂 。
煤 样 测 定时 标 准 Na OH溶 液耗 用 量 ( mL 空 白测定 时标 准 Na OH溶液 耗 用 量 ( ) mL
SO2 +SO3 +H2 O+H2 — — O2 +2H2 SO4
H204 Na —一NaS + H2 S +2 OH 2O4 2 O
煤 中释 放 的硫 量 ( 量 分数 )计 算 如 下 : 质 S -(-V) r-V o C×0 0 6 m ×1 0 .1/ 0% 式 中 s : 样 中硫 释 放量 ( 量 分数 ) r煤 质
煤
c 2 H2 S + O + + l 灰 分 o + O+ O2 S 3 N2 e 2 +
固硫剂的研究现状(国内)

固硫剂的研究现状(国内)
• 石灰石(主要成分是CaCO3)、电石渣(电石厂废渣,主 要成分有Ca(OH)2、SiO2、Al2O3、Fe2O3等)、白泥(含 Sr 的工业废弃物)、CaO,其中CaO 是用石灰石在 900℃下灼 20 分钟制成的。实验表明,白泥和电石渣在1 000~ 1100 ℃时固硫率较高,其中白泥在1 000 ℃时固硫 率高达84.5%,甚至高于CaO 的固硫率。但当温度升高 到1 200 ~ 1 300 ℃时,白泥和电石渣的固硫率迅速降低, 即白泥和电石渣具有较高的低温固硫效果。石灰石在1 000~1100℃时固硫率只有50%左右,而到1200℃以上, 石灰石的固硫率开始明显高于白泥和电石渣。也就是说, 石灰石的高温固硫效果比白泥和电石渣要好。 • 石灰石和电石渣相配合比单一石灰石或电石渣的固硫效果 好,其最佳配比为 40: 60 ~ 60: 40 之间。这两种固硫剂 相配合,在1300℃时不能形成稳定的高温固硫产物,为 此又添加了一些含金属盐或金属氧化物的工业废料,以促 进钙基固硫剂的固硫效果。
•
固硫剂的研究现状(国内)
• 2.固硫剂的研制现状 • 2.1钙基固硫剂 • 试验表明,CaCO3、CaO、Ca(OH)2 三种固硫剂Ca(OH)2 的固硫效果最好,其次是 CaO 和 CaCO3。这和其发生固 硫反应的温度和其颗粒的结构有关。Ca(OH)2固硫反应开 始的温度低(500℃),在500℃即可发生分解反应生成 CaO,固硫反应和煤大部分硫析出的温度区间相吻合,因 此固硫效果好。而CaCO3分解生成CaO所需的温度高, 即900℃才发生煅烧反应,它不能在低温阶段进行有效的 固硫,低温时会有部分SO2随烟气逸出,固硫效果较差。 从固硫颗粒结构上分析,Ca(OH)2分解释放SO2反应速率 高,所以Ca(OH)2固硫效果好于CaO,其最佳固硫温度是 800 ~1000℃。
燃煤固硫剂研究进展
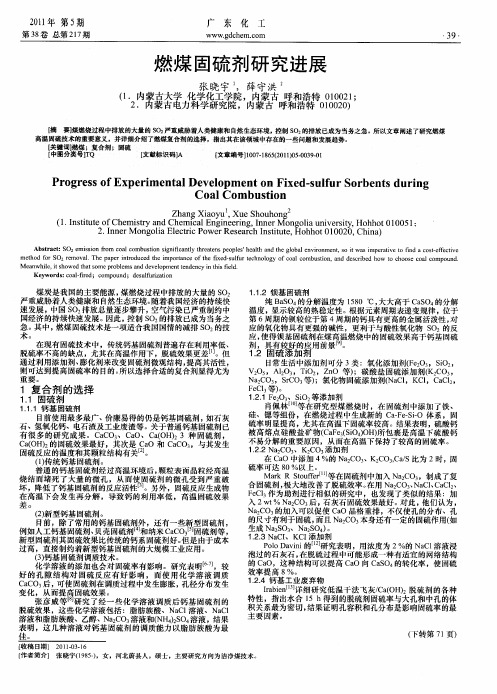
目前 ,除了常 用的钙基 固硫剂外 ,还有一些新型 固硫剂 , 例如人工钙基 固硫 剂、 壳固硫剂 l和纳米 C C 3] 剂等 , 贝 4 a O l固硫 s 新型 固硫剂其 固硫效果 比传统的钙系 固硫剂好 。 但是 由于成本 过高 ,直接制约着新 型钙基 固硫剂的大规模工业应 用。 () 3钙基 固硫剂调质技术 。 化学溶液 的添加也会对 固硫 率有影响 。研究表 明 J ,较 好 的 孔隙结 构对 固硫 反应 有好 影 响 ,而使 用 化 学溶 液调 质 CC 3 , a O 后 可使 固硫剂在 调质 过程 中发生膨胀 , 孔径 分布发生 变化 ,从而提高 固硫效果 。
,
煤炭 是我国的主要能源 , 煤燃烧过程 中排放 的大量 的 S O 严重威胁着 人类健 康和 自然生态环境 。 随着我 国经济 的持 续快 速发展 ,中国 S z O 排放总量逐步攀升 , 空气污染 已严重制约 中 № 国经济 的持 续快速 发展。因此 , 制 S 2 控 O 的排放 已成为 当务之 急 。 中, 其 燃煤 固硫技术是一项适合 我国国情的减排 S O 的技
重要 。
纯 BS 4 a O 的分解温度为 1 8 ℃, 50 大大高于 C S 4 a O 的分解 温度 , 显示 较高的热 稳定性。根据元素 周期表递变规 律 , 位于 第 6周期的钡较位于第 4周期 的钙具有更高 的金属活泼性 , 对 应 的氧化物具有更强 的碱性 ,更利于 与酸性氧 化物 S 的反 Oz 应, 使得钡基 固硫 剂在 煤高温燃烧中的 固硫效果高于钙基 固硫 剂 ,具有较好的应用前景 。 J
Ab t a t 02e si n f m o lc mb si n sg i c n l h e t n e p e ’ e l n h lba e v r n n s t a mp r t e t n o te f ci e s r c :S miso r o c a o u t i n f a t t r ae sp o l s h a t a d te g o l n io me t o i w s i e a i o f d a c s. f t o i y h v i e v
添加剂强化粉煤燃烧固硫剂的研究
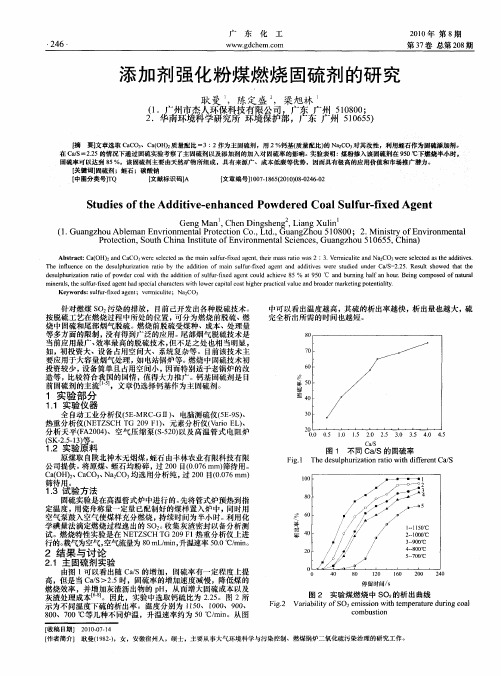
,
(. u n z o A l nE vin na Poet nC . t. a g h u5 0 0 ; 2 Mii r f n i n na 1G ag h u be n r metl rtc o o, d, ma o i L Gu n Z o 1 8 0 . ns yo E vr metl t o Poet n S uhC iaIstt o n i n na S i csG a gh u5 5 , hn ) rtci , o t hn tue f vr me tl ce e, u n z o 1 6 5 C ia o ni E o n 0
f 要】 选取 C C 3 aO )质量 配 比 一3: 摘 文章 a 0 、C ( H 2 2作为 石作 为 固硫添 加剂 质 的 aC 3 在 Ca =22 / :.5的情况下通过固硫实验考察了主固硫剂以及添加剂的加入对固硫率的影喃。 S 实验表明: 煤粉掺入该圃硫剂在 90℃下燃烧半小时, 5 阉硫率 可 以达到 8 5%,该 困硫 剂主 要 由天 然矿 物所 组成 ,具 有来 源广 、成 本低廉 等优 势 ,因而 具有极 高 的应用价 值 和市场 推广 潜力 。 【 键词悃 硫 剂 ;蛭石 ;碳酸 钠 关 t 中圉分类号]Q T 【 文献标识码】 A 【 文章编号]0716 (000 —2 60 10.852 1)80 4.2
钙铁复合助剂对民用型煤洁净化作用
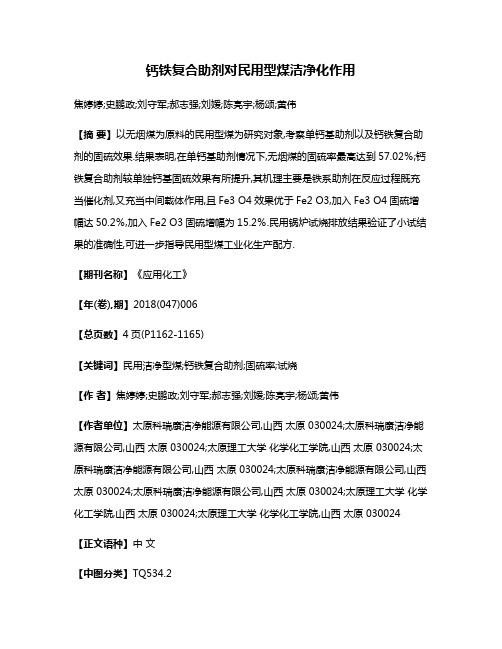
钙铁复合助剂对民用型煤洁净化作用焦婷婷;史鹏政;刘守军;郝志强;刘媛;陈亮宇;杨颂;黄伟【摘要】以无烟煤为原料的民用型煤为研究对象,考察单钙基助剂以及钙铁复合助剂的固硫效果.结果表明,在单钙基助剂情况下,无烟煤的固硫率最高达到57.02%;钙铁复合助剂较单独钙基固硫效果有所提升,其机理主要是铁系助剂在反应过程既充当催化剂,又充当中间载体作用,且Fe3 O4效果优于Fe2 O3,加入Fe3 O4固硫增幅达50.2%,加入Fe2 O3固硫增幅为15.2%.民用锅炉试烧排放结果验证了小试结果的准确性,可进一步指导民用型煤工业化生产配方.【期刊名称】《应用化工》【年(卷),期】2018(047)006【总页数】4页(P1162-1165)【关键词】民用洁净型煤;钙铁复合助剂;固硫率;试烧【作者】焦婷婷;史鹏政;刘守军;郝志强;刘媛;陈亮宇;杨颂;黄伟【作者单位】太原科瑞康洁净能源有限公司,山西太原 030024;太原科瑞康洁净能源有限公司,山西太原 030024;太原理工大学化学化工学院,山西太原 030024;太原科瑞康洁净能源有限公司,山西太原 030024;太原科瑞康洁净能源有限公司,山西太原 030024;太原科瑞康洁净能源有限公司,山西太原 030024;太原理工大学化学化工学院,山西太原 030024;太原理工大学化学化工学院,山西太原 030024【正文语种】中文【中图分类】TQ534.2煤炭作为不可替代的一次性能源,在能源消费中所占的比例高达75%,二氧化硫的90%来自燃煤[1-3]。
型煤固硫技术在SO2减排方面起着非常重要的作用[4-5]。
目前所用的固硫剂主要是钙基固硫剂[6-7],研究表明在钙基固硫剂中添加金属化合物可以有效地提高传统钙基固硫剂的活性[8-9]。
何方等[10]认为Fe2O3的加入,可以使CaSO4的分解温度有一定的提高,加快CaSO3的氧化反应,同时可有效降低脱硫反应的活化能,使反应能更容易进行。
民用洁净固硫型煤-编制说明

染物少指洁净型煤在各类锅炉燃烧后排放的污染物达到《民用洁净固硫型煤》。 (二)先进性 标准的先进性应体现在两方面: 1.指标控制要求方面:由于山西省的能源结构以煤炭为主,单位面积的锅炉
台数远大于其它地区,现有的和需要改造后使用洁净型煤的锅炉也很多,因此, 标准规定主要限值控制要求应严于国家和其它地方同类标准和现行标准。
862
6
84.0-98.8
91.9
6
168-6401
384
3
620-680
503
六、技术经济分析及效益分析 本标准提出的洁净型煤产品是指应用于不同类型的锅炉燃料,旨在洁净、高
效地利用能源,减少燃煤对环境大气造成的污染。洁净型煤技术是洁净煤技术之 一,同其他洁净煤技术相比,型煤产品生产成本低、节能与环保效益显著、工艺 简单、投资少、见效快。
表 3 太原市各类型煤煤质分析结果统计表
型煤种类
项目
单位
收到基低位发 热量
MJ/kg
干燥基全硫 %
收到基水分 %
干燥基灰分 %
干燥无灰基挥 发分
%
方形型煤
统计量
范围
31
15.23-29.17
95
0.11-2.42
31
1.15-10.00
31
11.06-52.03
31
1.89-19.11
均值 18.44 0.76 2.81 35.6 11.23
民用洁净固硫型煤
( 山西省化学工业协会团体标准编 制 说 明 )
山西省化学工业协会 2020.5
《民用洁净固硫型煤》编制说明
一、任务来源和编制过程 为改善山西省环境空气质量,山西省近年来出台了多项治理措施,其中燃料
复合固硫剂对型煤固硫的影响研究
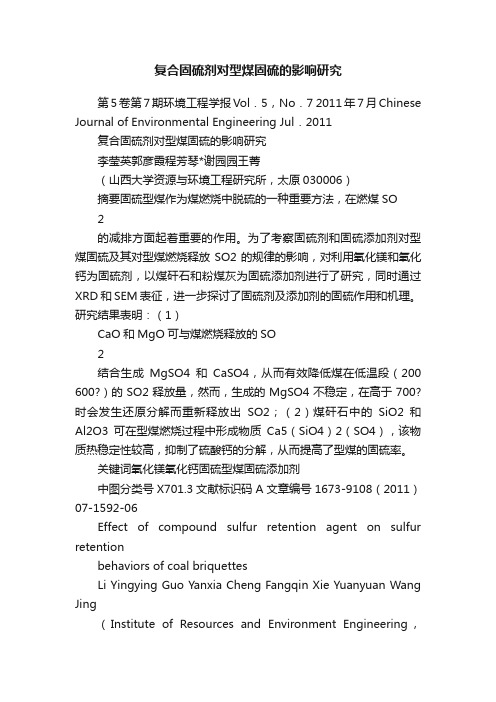
复合固硫剂对型煤固硫的影响研究第5卷第7期环境工程学报Vol.5,No.7 2011年7月Chinese Journal of Environmental Engineering Jul.2011复合固硫剂对型煤固硫的影响研究李莹英郭彦霞程芳琴*谢园园王菁(山西大学资源与环境工程研究所,太原030006)摘要固硫型煤作为煤燃烧中脱硫的一种重要方法,在燃煤SO2的减排方面起着重要的作用。
为了考察固硫剂和固硫添加剂对型煤固硫及其对型煤燃烧释放SO2的规律的影响,对利用氧化镁和氧化钙为固硫剂,以煤矸石和粉煤灰为固硫添加剂进行了研究,同时通过XRD和SEM表征,进一步探讨了固硫剂及添加剂的固硫作用和机理。
研究结果表明:(1)CaO和MgO可与煤燃烧释放的SO2结合生成MgSO4和CaSO4,从而有效降低煤在低温段(200 600?)的SO2释放量,然而,生成的MgSO4不稳定,在高于700?时会发生还原分解而重新释放出SO2;(2)煤矸石中的SiO2和Al2O3可在型煤燃烧过程中形成物质Ca5(SiO4)2(SO4),该物质热稳定性较高,抑制了硫酸钙的分解,从而提高了型煤的固硫率。
关键词氧化镁氧化钙固硫型煤固硫添加剂中图分类号X701.3文献标识码A文章编号1673-9108(2011)07-1592-06Effect of compound sulfur retention agent on sulfur retentionbehaviors of coal briquettesLi Yingying Guo Yanxia Cheng Fangqin Xie Yuanyuan Wang Jing(Institute of Resources and Environment Engineering,Shanxi University,Taiyuan030006,China)Abstract Clean coal briquette is one of the most effective techniques of sulfur fixing during coal burning,it plays an important role in reducing sulfur dioxide.In order to find out the sulfur retention and behaviors of sul-fur retention agent and additive agent,the coal gangue and coal ash based on magnesia-and calcium-base sulfur retention agents were studied.Furthermore,sulfur retention mechanisms were discussed based on XRD and SEMcharacterizations.The results show that:(1)CaO and MgO can react with SO2and turn into CaSO4and MgSO4atlow temperatures(200 600?).MgSO4,however,is easily decomposed at700 900?and decrease the sulfurretention rates.(2)SiO2and Al2O3in coal gangue can react with CaSO4into a more stable substanceCa5(SiO4)2(SO4)at high temperatures and thus restrain the decomposition of sulfate species.Key words magnesia;calcium oxide;sulfur retention;coal briquette;sulfur retention additive agent基金项目:山西省科技攻关项目(2007031148);国家国际科技合作项目(2011DFA90830);山西省回国留学人员科研资助项目收稿日期:2010-01-28;修订日期:2010-04-21作者简介:李莹英(1983 ),女,硕士研究生,主要从事洁净煤方面的研究工作。
应用固硫型煤控制民用小煤炉大气二氧化硫的污染
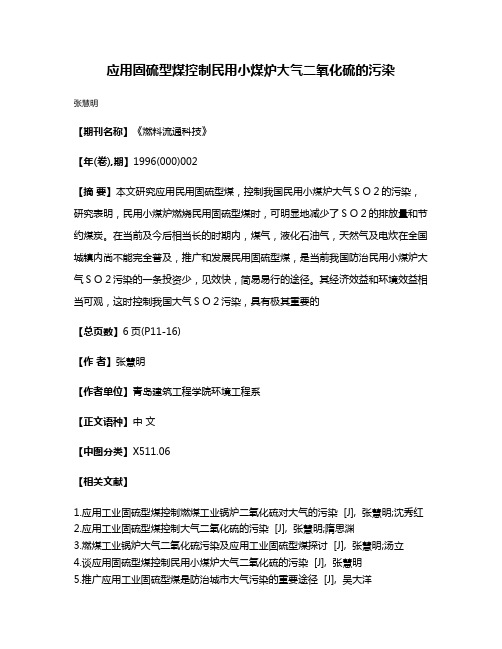
应用固硫型煤控制民用小煤炉大气二氧化硫的污染
张慧明
【期刊名称】《燃料流通科技》
【年(卷),期】1996(000)002
【摘要】本文研究应用民用固硫型煤,控制我国民用小煤炉大气SO2的污染,研究表明,民用小煤炉燃烧民用固硫型煤时,可明显地减少了SO2的排放量和节约煤炭。
在当前及今后相当长的时期内,煤气,液化石油气,天然气及电炊在全国城镇内尚不能完全普及,推广和发展民用固硫型煤,是当前我国防治民用小煤炉大气SO2污染的一条投资少,见效快,简易易行的途径。
其经济效益和环境效益相当可观,这时控制我国大气SO2污染,具有极其重要的
【总页数】6页(P11-16)
【作者】张慧明
【作者单位】青岛建筑工程学院环境工程系
【正文语种】中文
【中图分类】X511.06
【相关文献】
1.应用工业固硫型煤控制燃煤工业锅炉二氧化硫对大气的污染 [J], 张慧明;沈秀红
2.应用工业固硫型煤控制大气二氧化硫的污染 [J], 张慧明;隋思渊
3.燃煤工业锅炉大气二氧化硫污染及应用工业固硫型煤探讨 [J], 张慧明;汤立
4.谈应用固硫型煤控制民用小煤炉大气二氧化硫的污染 [J], 张慧明
5.推广应用工业固硫型煤是防治城市大气污染的重要途径 [J], 吴大洋
因版权原因,仅展示原文概要,查看原文内容请购买。
型煤固硫添加剂对固硫剂固硫效率的影响

型煤固硫添加剂对固硫剂固硫效率的影响李雪;徐东耀;孙峥【摘要】论述了实验室中固硫剂固硫率的测定方法,试验研究了Ca/S对不同煤样固硫率的影响,并对以Ca(OH)2为固硫吸收剂,Mg,Si,Al氧化物为固硫添加剂的型煤在高温燃烧过程中的固硫效果进行了研究,通过正交试验确定出最好的添加剂比例.【期刊名称】《煤炭加工与综合利用》【年(卷),期】2009(000)006【总页数】3页(P40-42)【关键词】型煤;固硫剂;添加剂;正交试验;研究【作者】李雪;徐东耀;孙峥【作者单位】中国矿业大学(北京)化学与环境工程学院,北京,100083;中国矿业大学(北京)化学与环境工程学院,北京,100083;中国矿业大学(北京)化学与环境工程学院,北京,100083【正文语种】中文【中图分类】TQ53对于用于燃烧的煤炭,可以把钙系化合物加入到煤中制成型煤,使大部分硫在煤燃烧后残留在煤渣中,这是解决燃煤对大气污染的有效方法之一。
钙系化合物包括石灰石(主要成份为CaCO3)、生石灰(主要成份是CaO)和熟石灰(主要成份是Ca(OH)2),它们被用作固硫剂时,称为钙系固硫剂。
采用钙系固硫剂成本低,在简化净化操作过程达到固硫效果的同时,还能提高煤的热利用率,从而受到了人们的普遍关注。
钙系化合物来源广、价格低廉,广泛应用于煤燃烧过程中的固硫。
前人在实际工作中发现,往固硫吸收剂中加入少许碱金属化合物,能大大改善其脱硫效率。
因此往固硫剂中加入有效且廉价易得的固硫添加剂是一项重要的研究工作。
1 实验方法固硫率的测定采用化学法,根据灰渣中的硫酸钙难溶于水,但易溶于盐酸,而硫酸盐矿物不溶于盐酸的原理,把灰渣中的硫酸盐全部转化成沉淀物,称其重量,即可计算固硫率。
称取200目以下原煤与不同的主固硫剂、固硫添加剂,用研钵研磨均匀,准确称取煤样1±0.1g分别放入两个瓷舟中,将两瓷舟同时放入已升温到1000℃的管式炉炉管中,同时通入空气,待温度稳定后,计时,15min后取出。
煤炭燃烧中添加固硫剂及固硫助剂的研究
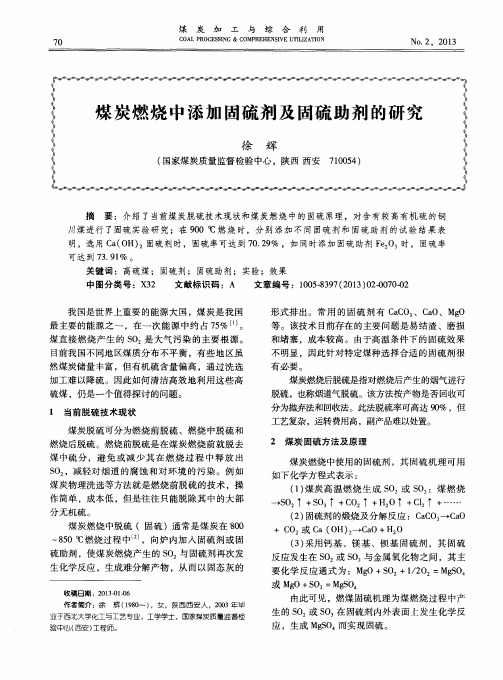
经 浮选 后精 煤样 的硫 分为 1 . 4 5 %。
3 . 1 最佳 固硫 剂的 选择 实验 选 取 C a ( O H) : 、N a C O 、Mg O 为 固硫 4 结果 与讨 论
通过 试 验 研 究 可 知 ,对 于 陕 西 铜 川 的 高 硫
剂 ,在 9 0 0℃ 时 ,分 别 添 加 质 量 为 原 煤 样 质 量 1 0 %_ 3 的各种 固硫 剂 ,测定 煤样 燃 烧所 排 烟气 中
的S 0 含 量 ,结果 见表 1 。
表 1 添加不 同固硫剂的 固硫实验
煤 ,在燃 烧 中添加 固硫 剂 和 固硫 助 剂 ,可 达 到较 好 的脱 硫 效果 。实 验选 出固硫 效 果 明显 的 固硫 剂 和助 剂分 别是 C a ( O H) 和F e : 0 , 。添 加 单 一 固硫
煤炭燃烧后脱硫是指对燃烧后 产生的烟气进行 脱硫 ,也称 烟道气脱硫 。该方 法按产 物是否 回收可 分为抛弃法 和回收法。此法脱硫率可高达 9 O % ,但
工艺复杂 ,运转费用高 ,副产 品难 以处置。
燃烧 后脱 硫 。燃烧前 脱硫 是 在煤 炭燃 烧 前 就脱 去
煤 中硫 分 ,避 免 或 减 少 其 在 燃 烧 过 程 中 释 放 出
( 3 ) 采用 钙 基 、镁 基 、钡 基 固硫 剂 ,其 固 硫 反 应发 生在 S O 或S O 与金 属 氧化 物之 间 ,其 主 要 化学 反 应 通 式 为 :Mg O+S 0 2 +1 / 2 0 2 =M g S O 4
或 M g O+ S O 3 =Mg S O 4
徐
辉 :煤 炭燃 烧 中添加 固硫 剂及 固硫 助 剂 的研 究
表 2 添 加 不 同 固硫 助 剂 的 固硫 实 验 结 果
煤用固硫剂项目可行性研究报告
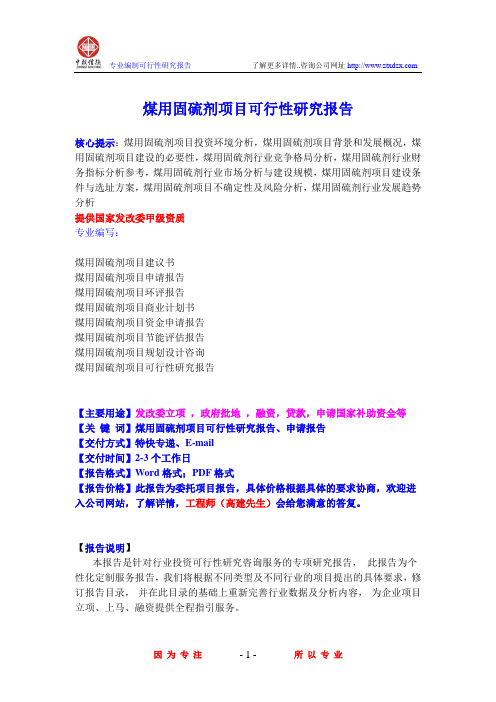
煤用固硫剂项目可行性研究报告核心提示:煤用固硫剂项目投资环境分析,煤用固硫剂项目背景和发展概况,煤用固硫剂项目建设的必要性,煤用固硫剂行业竞争格局分析,煤用固硫剂行业财务指标分析参考,煤用固硫剂行业市场分析与建设规模,煤用固硫剂项目建设条件与选址方案,煤用固硫剂项目不确定性及风险分析,煤用固硫剂行业发展趋势分析提供国家发改委甲级资质专业编写:煤用固硫剂项目建议书煤用固硫剂项目申请报告煤用固硫剂项目环评报告煤用固硫剂项目商业计划书煤用固硫剂项目资金申请报告煤用固硫剂项目节能评估报告煤用固硫剂项目规划设计咨询煤用固硫剂项目可行性研究报告【主要用途】发改委立项,政府批地,融资,贷款,申请国家补助资金等【关键词】煤用固硫剂项目可行性研究报告、申请报告【交付方式】特快专递、E-mail【交付时间】2-3个工作日【报告格式】Word格式;PDF格式【报告价格】此报告为委托项目报告,具体价格根据具体的要求协商,欢迎进入公司网站,了解详情,工程师(高建先生)会给您满意的答复。
【报告说明】本报告是针对行业投资可行性研究咨询服务的专项研究报告,此报告为个性化定制服务报告,我们将根据不同类型及不同行业的项目提出的具体要求,修订报告目录,并在此目录的基础上重新完善行业数据及分析内容,为企业项目立项、上马、融资提供全程指引服务。
可行性研究报告是在制定某一建设或科研项目之前,对该项目实施的可能性、有效性、技术方案及技术政策进行具体、深入、细致的技术论证和经济评价,以求确定一个在技术上合理、经济上合算的最优方案和最佳时机而写的书面报告。
可行性研究报告主要内容是要求以全面、系统的分析为主要方法,经济效益为核心,围绕影响项目的各种因素,运用大量的数据资料论证拟建项目是否可行。
对整个可行性研究提出综合分析评价,指出优缺点和建议。
为了结论的需要,往往还需要加上一些附件,如试验数据、论证材料、计算图表、附图等,以增强可行性报告的说服力。
- 1、下载文档前请自行甄别文档内容的完整性,平台不提供额外的编辑、内容补充、找答案等附加服务。
- 2、"仅部分预览"的文档,不可在线预览部分如存在完整性等问题,可反馈申请退款(可完整预览的文档不适用该条件!)。
- 3、如文档侵犯您的权益,请联系客服反馈,我们会尽快为您处理(人工客服工作时间:9:00-18:30)。
1) Fe2O3-SiO2 固 硫 添 加 剂 。 在 CaO 中 添 加 适 量 的 Fe2O3-SiO2 可 以 提 高 高 温 固 硫 效 果 。 研 究 发 现, 加入质量分数为 0.6%的 Fe2O3 时, 固硫率达到 最高; 加入质量分数为 0.4% 的 Fe2O3 时, CaSO4 分 解率最低。 同时加入 Fe, Si 组分, 在 l 200 ℃以上 高温燃烧时, 型煤固硫率仍可达 93%; 在 1 300 ℃ 条 件 下 恒 温 30 min, 其 固 硫 率 为 77% 。 可 见 , Fe2O3, SiO2 的协同作用可大大提高石灰石的固硫效 果, 而高温、 恒温反而降低石灰石的固硫能力。
型煤固硫就是把固硫剂和黏结剂加入原煤中一 起压制成型, 从而将硫固定在燃烧灰渣中, SO2 是
酸性气体, 用碱性氧化物和它反应可达到固硫目 的。 CaO 是一种廉价易得, 且有较好反应性的碱性 氧化物。 Ca (OH)2, CaCO3 在加热条件下分解生成 CaO, 也可用于固硫。 1.2.1 固硫剂种类
4) 其他固硫剂。 有关文献报道, 电石渣、 白 泥、 石灰渣等钙基工业废弃物的组成成分中含 CaO, 具有脱硫作用, 同时, 其含有的金属及碱金 属氧化物, 对固硫过程起催化促进作用。 经试验, 在 Ca/S 摩 尔 比 为 1.32 ~2.30, 链 条 炉 料 层 温 度 为 1 100 ℃时, 脱硫率可达 50%。 电石渣有较好的低 温固硫特性, 如果再加入铝土粉, 在高温下会形成 耐热物相 3CaO·3A12O3·CaSO4, 可减少 CaSO4 的 高 温分解, 有利于总脱硫率的提高; 白泥在高温下具 有较高的固硫性能, 但能否利用 “电石渣+白泥” 进一步提高脱硫率, 仍有待进一步研究。 另有一种 皮革生产行业产生的有机钙 废 弃 物 , 在 Ca/S 摩 尔 比为 2 的条件下, 其脱硫率也可达 50%。 1.2 影响型煤固硫效果的因素
2) 碳 酸 盐 添 加 剂 。 碳 酸 盐 类 添 加 剂 主 要 有 K2CO3, Na2CO3, SrCO3 等 , 在 CaO 固 硫 剂 中 添 加 质量分数为 4%的 Na2CO3, 当 Ca/S 摩尔比为 2 时, 固 硫 率 可 达 80%, 固 硫 率 提 高 10%。 在 CaCO3 中 添加一定量的 SrCO3, 固硫率也可以提高约 10%。
固硫剂可分为两类: 一类是单一的钙基固硫 剂; 另一类是含有两种以上单一固硫剂的复合固硫 剂。 后者燃烧时同时发生两种或多种固硫反应, 或 其中一种能起催化作用使另一种固硫剂的固硫效率 提高, 因此, 复合固硫剂具有更好的固硫效果。
尽管目前研究和应用的固硫剂有效组分大多是 CaO, 但不同的存在形态其固硫效果不同。 石灰石 和白云石是常用固硫剂, 经高温煅烧所制得的多孔 结构 CaO, 由于其表面积和孔隙率均比由 Ca(OH)2 煅烧而成的 CaO 小, 孔径结构也不相同, 因而其转 化率和固硫效果均不如由 Ca (OH)2 煅烧所 制 得 的 CaO。 Ca (OH)2 分解温度低, 可在型煤燃烧初期中 低温条件下固硫, 而 CaCO3 分解温度较高, 在高温 下才能表现出固硫能力。 1.2.2 Ca/S 摩尔比
研究 Fe2O3-SiO2 对煤燃烧过程 中 石 灰 石 固 硫 特 性的影响时发现, 在程序升温过程中, 硫分解释放 主 要 发 生 在 燃 烧 初 期 , 在 200 ℃ 时 开 始 释 放 , 在 400~ 500 ℃时达最大值。 固硫剂种类不同其固硫效 果也不一样。Ca(OH)2 在 300~400 ℃条件下分解生成 CaO, 当 型 煤 着 火 燃 烧 时 就 能 与 SO2 或 SO3 发 生 反 应生成 CaSO3 和 CaSO4, 前 者 在 炉 内 可 以 被 空 气 中 的氧氧化为后者。 CaCO3 在 600~900 ℃范围内分解, 温度为 809 ℃时, 分解率最大。 因此, 在 600 ℃以 下石灰石基本没有固硫能力, 700 ℃以 上 固 硫 效 果 才显著, 900 ℃以上固硫率增长缓慢, 超过 1 000 ℃
·73·
研究与探讨
太原科技 2009 年第 11 期 TAIYUAN S CI- TECH
1.3 民用型煤固硫剂研究 1.3.1 民用炉灶特点
目前国内居民使用的炉灶有如下共性: 炉灶采 取自然通风, 型煤采用两块煤叠置燃烧方式, 块煤 采用散堆燃烧方式, 型煤在燃烧过程中, 烟尘量 少, 燃烧完全, 烟气收集较难, 以传导方式从炉壁 损失部分热量, 主要靠辐射和对流提供有效热能, 热量在吸收和传递中, 温度对受热体吸热很重要。 1.3.2 民用燃煤烟尘特征
*2006 年北京市科技局环保应用型项目
收稿日期:2009-08-24;修回日期:2009-10-09 作者简介:王 波( 1971- ) ,男,山西垣曲人。 2007 年 7 月 毕
业于太原理工大学化学工程学院,硕士,工程师。
固 硫 剂 利 用 率 较 低 , 炉 内 脱 硫 率 仅 为 30%~40% 。 为了提高钙基固硫剂的利用率, 人们进行了大量的 研究工作, 主要分为 3 类: 一是利用一些特殊的含 钙基物质成分或结构上的特点来提高脱硫率; 二是 利用调质方法来改善固硫剂的活性; 三是利用添加 剂来增强脱硫能力。 针对一般型煤固硫剂的研究主 要是围绕 CaO 来进行, 常用的固硫剂有石灰石、 白 云石、 生石灰、 消石灰、 电石渣、 白泥等。 固硫添 加 剂 主 要 有 Fe2O3, V2O5, KCO3, Na2CO3, NaCl, SiO2 及含 Sr 工业废料等。 1.1.1 煤燃烧过程中硫的析出规律与固硫剂
目前, 我国 80%以上的煤炭用于直接燃烧, 煤 炭的大量燃烧造成我国大气环境普遍呈煤烟型污 染。 随着工业炉窑的技术改造, 民用燃煤的污染分 担率在逐年提高, 据统计, 全国现有 1 亿多个民用 炊事燃煤灶, 且民用炉灶量多面广、 结构简陋、 多 集中于居民区、 烟气排放于低空呼吸带不易扩散, 可以说, 民用炉灶燃煤烟气污染是造成人们呼吸系 统急慢性疾病的祸首之一。 针对民用燃料用煤、 燃 烧结构、 烟尘污染等特点, 笔者在燃煤及其排放烟 尘的矿物学研究基础上, 开发研制了民用燃煤环境 矿物材料添加剂。 1 固硫剂的基础研究 1.1 型煤固硫剂及添加剂的研究
添加剂对型煤固硫效果的影响十分显著。 如加 入 Fe2O3-SiO2 可提高 CaO 的高温固硫效果; 添加含 有 K, Na, Sr 元素的某些化合物, 可提高型煤固硫 率 10% 以上。 MgO 对石灰石固硫具有催化作用。 1.2.4 炉温及炉内气氛
炉温对型煤固硫效果的影响主要表现在 2 个方 面: 一是 CaO 的表面性质, 如 CaCO3, Ca(OH)2 在 煅烧温度为 800~1 300 ℃范围内, 随温度升高, 比 面积降低; 二是固硫产物的分解, 炉温越高, CaSO4 分解率越高, 并且在还原性气氛中, 当温度高于 800 ℃时, CaSO4 就开始分解, 炉温过高也会使固硫 剂表面积降低。 此外, CaO 粒度对型煤固硫效果也 有一定影响。
Ca/S 摩尔比是影响型煤固硫效果的主要因素之 一。 Ca/S 摩尔比一般为 l~3, 超过 3 时, 增加 固 硫 剂 而 固 硫 率 增 加 不 明 显 ; 最 佳 Ca/S 摩 尔 比 为 l.5~ 2.0, 如 Ca/S 摩 尔 比 为 2.0, 并 添 加 质 量 分 数 为 0.1% 的白泥制作的型煤在工业锅炉中燃烧, 其固硫 率可达 70%。 在程序升温条件下, Ca/S 摩 尔 为 1.5 时, 固硫率基本上达到最佳值, 而恒温条件下固硫 率随 Ca/S 摩尔比增加而增大。 石灰石煅烧产生的活 性钙离子的多少及其利用也是影响其固硫率的重要 因素。 1.2.3 添加剂
型煤燃烧形成烟雾状尘粒, 粒度小, 并夹有油 分, 烟尘浓度大, 呈黄褐色, 含有较多的黏土质和 玻璃质成分。 型煤和烟煤受民用炉灶燃烧方式的限 制, 产生的烟尘均含有较高比例的碳质组分, 如能 改善和增强燃煤内部的氧化气氛, 将会降低烟尘的 碳质含量, 提高热能利用率, 同时也减少了碳质粉 尘的污染。 型煤烟尘的主要物相为石英和非晶质 体; 烟煤物相复杂, 以石英为主, 另含非晶质体、 云母、 高岭石、 长石、 莫来石和少量含铁矿物。 1.3.3 民用燃煤固硫
研究与探讨
太原科技 2009 年第 11 期 TAIYUAN S CI- TECH
文章编号:1006-4877(2009)11-0072-03
民用型煤固硫剂的研究 *
王波
( 太原市环境科学研究设计院, 山西 太原 030002)
摘 要:在固硫剂研究的基础上, 分析 了 影 响 型 煤 固 硫 效 果 的 因 素 ; 针 对 民 用 型 煤 的 特 点 , 经 过 试 验 比 较 , 确 定 了 将废料与其他废弃物按合适的比例配合并添加适当的催化剂制成廉价的固硫剂的最终配方; 提出了将催化概念引入 固硫剂的新设计思路。 关键词:固 硫 剂 ; 固 硫 效 果 ; 催 化 剂 中图分类号:X701.3 文献标志码:A
·72·
太原科技 2009 年第 11 期 TAIYUAN S CI- TECH
研究与探讨
时固硫率下降。 1.1.2 固硫添加剂
CaO 为主要固硫成分生成的 CaSO4 在高温下要 发 生 分 解 反 应 , 重 新 生 成 CaO 并 释 放 SO3 。 资 料 表 明 , 在 1 000 ℃ 以 下 , CaSO4 分 解 率 小 于 等 于 10%; 在 1 000~1 200 ℃, 分 解 率 达 到 25%; 而 到 1 300 ℃时, 分解率超过 50%。 因此, 高温固硫添 加剂及固硫机理是型煤固硫研究的主要方向。