轮对压装曲线不合格的原因分析和改进措施
轮对压装曲线影响因素分析
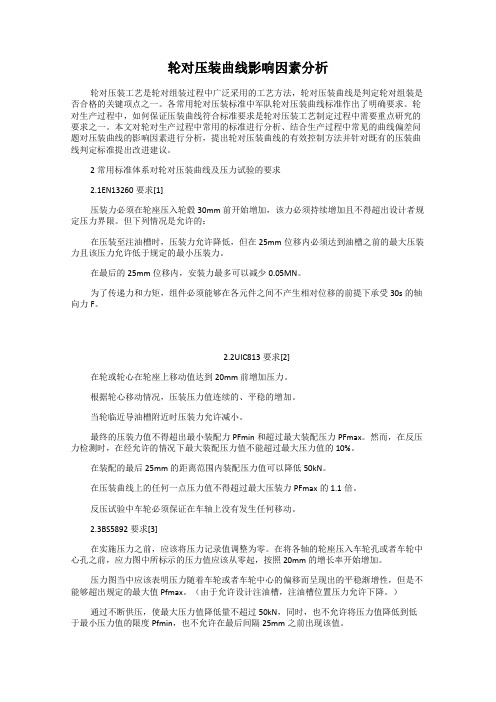
轮对压装曲线影响因素分析轮对压装工艺是轮对组装过程中广泛采用的工艺方法,轮对压装曲线是判定轮对组装是否合格的关键项点之一。
各常用轮对压装标准中军队轮对压装曲线标准作出了明确要求。
轮对生产过程中,如何保证压装曲线符合标准要求是轮对压装工艺制定过程中需要重点研究的要求之一。
本文对轮对生产过程中常用的标准进行分析、结合生产过程中常见的曲线偏差问题对压装曲线的影响因素进行分析,提出轮对压装曲线的有效控制方法并针对既有的压装曲线判定标准提出改进建议。
2常用标准体系对轮对压装曲线及压力试验的要求2.1EN13260要求[1]压装力必须在轮座压入轮毂30mm前开始增加,该力必须持续增加且不得超出设计者规定压力界限。
但下列情况是允许的:在压装至注油槽时,压装力允许降低,但在25mm位移内必须达到油槽之前的最大压装力且该压力允许低于规定的最小压装力。
在最后的25mm位移内,安装力最多可以减少0.05MN。
为了传递力和力矩,组件必须能够在各元件之间不产生相对位移的前提下承受30s的轴向力F。
2.2UIC813要求[2]在轮或轮心在轮座上移动值达到20mm前增加压力。
根据轮心移动情况,压装压力值连续的、平稳的增加。
当轮临近导油槽附近时压装力允许减小。
最终的压装力值不得超出最小装配力PFmin和超过最大装配压力PFmax。
然而,在反压力检测时,在经允许的情况下最大装配压力值不能超过最大压力值的10%。
在装配的最后25mm的距离范围内装配压力值可以降低50kN。
在压装曲线上的任何一点压力值不得超过最大压装力PFmax的1.1倍。
反压试验中车轮必须保证在车轴上没有发生任何移动。
2.3BS5892要求[3]在实施压力之前,应该将压力记录值调整为零。
在将各轴的轮座压入车轮孔或者车轮中心孔之前,应力图中所标示的压力值应该从零起,按照20mm的增长率开始增加。
压力图当中应该表明压力随着车轮或者车轮中心的偏移而呈现出的平稳渐增性,但是不能够超出规定的最大值Pfmax。
影响轮对压装质量因素及对策

影响轮对压装质量因素及对策发表时间:2020-12-22T08:30:34.811Z 来源:《中国电业》(发电)》2020年第19期作者:王俊杰[导读] 因此在轮对压装时研究材料对它的影响是必不可少的环境,下面就对此因素分析如下:中车铺镇车辆有限公司摘要轮对压装常见问题主要有:压装末端抖吨现象、终止压装力小于最小压装力及试制中轮对压装试制周期较长。
本文的主要要目的是通过车轴车轮材质、过盈量、压装配合表面的几何形状及粗糙度等方面分析以解决压装末端抖吨、终止压装力小于最小压装力及试制中轮对压装试制周期较长现象关键字:轮对压装 , 车轴车轮材质 ,过盈量, 轮轴锥度, 粗糙度一、轮轴材料对轮对压装的影响及对策1.1轮轴材料的影响原理及现有项目数据统计分析材料是代表轮轴加工特性、疲劳特性等,因此在轮对压装时研究材料对它的影响是必不可少的环境,下面就对此因素分析如下:不同项目轮对的材质不同,立式车床所加工的粗糙度不同,因为粗糙度是跟材料的性能及立式车床的进给量有关系的,因此不同项目所给的进给量是不一样的.上述原因为压装不合格提供了可能性,现就轮对压装问题进行理论分析:(1)单位接触面的压力P压装力F= N 因此影响压装质量的因素有一方面是动摩擦系数是与粗糙度有直接关系,因此粗糙度的值直接影响压装质量;另一方面是材料的弹性系数的大小也影响压装质量,这两方面因素都是由不同材料决定的。
现对于现场立车车轮加工时不同材料、不同项目、不同进给量、糙度、压装力统计如下:上述统计表明:①材料ER7刚性强度相对较大,加工得出的粗糙度较高。
因为影响粗糙度的原因有进给量、材料的刚度等.②同一车轮材料所匹配的轴的材料不同,所要求的粗糙度不一样,因为不同材料的摩擦粘着力不一样。
总结如下:材料为ER9车轮在分别配上EA1N及EA4T的轴时;即使轴加工后的粗糙度相差不大,但是由于轴的材料特性及加工时由于915rad/mind 转速带来的轴表面的加工硬化不同,从上表来看EA1N加工硬化程度明显要比EA4T加工硬化程度要高,因此只需要较小的粗糙度就能达到压装力范围。
货车轮对轴承压装不合格原因分析及应对措施

综 合过 滤是 近几 年来 氧化铝 生产 中出现 的 的新 型技术 , 共凭借 着 节能 型和 创新 型的特 点得到 了广 泛 的推广 和应 用 , 同时 现 场 问题 也在 不断地 反馈 , 这 就需 要我们结合业 主的建议 , 对设 计不断进行改 进和改
善, 才能 使该技 术能更好 的为现场服务。
够, 造成 下料不 畅的 问题 。 立 盘过 滤机 过滤 完的氢 氧化铝 , 是 通过 精液 冲立盘 过滤 机 至分 解首 槽的 联通 漏斗 , 将干氢 氧化铝 稀释成 料浆 完成
结 束语
公交企业 , 虽然 是 比较 特殊 的企业 , 但是 作为现代企 业 , 人力资源
输送。 但 是在干滤 饼落 下 时, 如果 精液 冲稀不够 充分 , 干料与 精液 混合 发挥着 十分重要的作用 。 在 公交行 业里面 , 虽然人 力资 源不是直接 参与 不匀 , 加上 溜槽斜度 满足不 了固含较 大的物 料 的输 送要求 , 就会造 成积 企业 运营 和管 理 , 但是 无形 中影 响着企 业 的运营成 本和 效 益。 毕 竟随 料及下料不畅 但 是如果 单纯 的增 加溜槽 的斜度, 那 么厂房最 上面 立盘 企业 的壮 大 , 劳 动法 的不 断完 善, 人力成 本 构成了企业不低 的开支 , 有 效地 管理好 , 运用好 各类人 力资源,在企业 增效 中有很 大的好 处 。 谈到 过 滤机 层的 高度 还要抬 高, 致使 整个厂房的造价 增加 。 为解 决此 问题 , 人们马上 会想到 节电、 节水 、 节约 各种资 源。固然, 这 些都是 现场对 溜槽 进行 了改造 , 在 不改变其 斜度的 情况下, 在溜槽 内部增 加了 降本 增效 , 但我们 以为 , 要 真正做 到降本 增效 , 首先应该从 人抓 折流板 , 这样 被精液 冲下的氢 氧化铝 料浆 形成湍流 , 达 到充分 混 合, 使 降低 成本 的措施 , 起, 通过 人尽 其才、 才尽其用 、 合 理配 置, 达 到提高人 才使用效率 , 节约 下料通畅 。 人力资源的效 果。 ( 3 ) 对于 我 们现在 设计 的1 0 0 万 吨/ 年 综合 过滤 厂房 , 四台1 8 0 m 上的 立盘 过滤 机 几乎 均采用 两两 配 置模 式 , 两 台立 盘过 滤机 溜槽 联通 对应一 组5 0 万吨/ 年 的分 解 槽 系列 。 有 些业 主就 已有 的现 场 情况 和生 产经验提 出了最好 每台立盘要求 对应一条溜槽 , 也就说 四台立 盘对应 四 条溜槽 , 以便清 理检 修。 但 使用这 种 配置方式 , 尤 其是业 主采 用双面 出 滤 液 方式的立 盘过 滤机 , 会造成 整个厂房的面积增加 , 加 大投资成 本, >. >上 接第2 2 8 页) 而且 与分解 之间的联 通溜 槽也不好 配 置, 平 面上拐 弯较多, 很 容易造成 ( 防锈脂 涂抹过厚且 不均匀 , 厚度 超过 1 mm。 轴 承压装 时, 轴颈 上的油 脂 积料 , 所 以在 已有的施 工图项 目中还未 体现 。 还 有的业主 建议 为预防溜 产生一个 反向力, 导致轴 承压 槽结 疤、 避免 立盘 卸料 处堵 料、 结疤 、 外漏等 现象 , 建 议增加空 气炮装 被挤压 到后 挡与防尘板 座的 密闭空 间中, 装不到位 。 置。
轮对一次压装不合格问题分析

第2期(总第213期)2019年4月机械工程与自动化MECHANICAL ENGINEERING & AUTOMATIONNo.2Apr.文章编号:1672-6413(2019)02-0191-02轮对一次压装不合格问题分析雷建中,李树林,王 科(太原重工轨道交通设备有限公司技术中心,山西 太原 030032)摘要:针对铁路机车车辆轮对压装过程一次压装不合格率较高的情况,分别从设备、工装、轮轴部件配合部位质量、检测量具等方面进行了研究分析,提出了设备校正、工装优化设计、轮轴部件配合部位质量控制、专用检测量具校准等控制方法,降低了轮对一次压装不合格率,使轮对压装质量趋于稳定,同时提高了生产效率。
关键词:轮对压装;不合格;校准;优化设计中图分类号:U260.331+.1 文献标识码:B收稿日期:2018-11-05;修订日期:2019-01-15作者简介:雷建中(1983-),男,山西吕梁人,工程师,硕士,主要从事铁路车轴及轮对工艺开发。
0 引言轮对作为铁路机车车辆走行部的关键部件,轮对压装的质量直接关系到机车车辆的运行安全。
铁路机车车辆轮对压装一般使用轮对压装机通过压力将车轮冷压至车轴上,轮对压装后主要通过检查压装压力曲线、轮对尺寸、轮轴部件静不平衡位置相位差等项目来判定是否合格。
在实际生产过程中,轮对压装机长期超负荷运转以及不同规格产品之间的设备调整都会使轮对压装机运行精度发生变化,同时由于轮轴部件配合部位质量控制不一致以及检测手段限制等原因,使得轮对压装过程容易产生压装压力曲线、轮对尺寸及轮轴部件静不平衡位置相位差不合格等情况,严重时发生轮轴配合部位拉伤,造成产品报废。
通过对某公司一段时间内轮对压装情况的统计发现,轮对一次压装不合格率较高,严重影响轮对产品质量,同时降低了生产效率。
本文针对上述情况展开分析研究,并制定相应对策从而降低轮对一次压装不合格率。
1 轮对一次压装不合格原因分析基于轮对一次压装不合格情况分别对轮对压装过程中轮对压装机状态(包括使用工装)、轮轴部件配合部位质量、检测器具情况等进行了跟踪分析。
轮对及制动盘压装失败原因分析
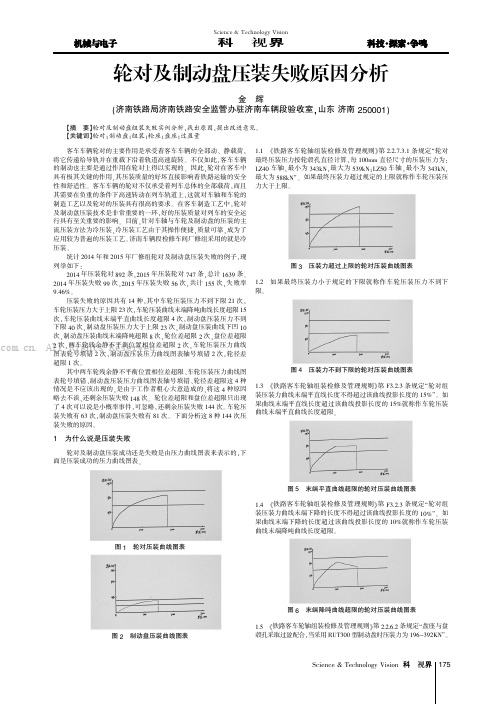
面是压装成功的压力曲线图表。
图1轮对压装曲线图表图2制动盘压装曲线图表。
图3压装力超过上限的轮对压装曲线图表如果最终压装力小于规定的下限就称作车轮压装压力不到下图4压装力不到下限的轮对压装曲线图表铁路客车轮轴组装检修及管理规则》第F3.2.3条规定装压装力曲线末端平直线长度不得超过该曲线投影长度的果曲线末端平直线长度超过该曲线投影长度的15%就称作车轮压装曲线末端平直曲线长度超限。
图5末端平直曲线超限的轮对压装曲线图表铁路客车轮轴组装检修及管理规则》第F3.2.3条规定装压装力曲线末端下降的长度不得超过该曲线投影长度的果曲线末端下降的长度超过该曲线投影长度的10%就称作车轮压装曲线末端降吨曲线长度超限。
图6末端降吨曲线超限的轮对压装曲线图表铁路客车轮轴组装检修及管理规则》第2.2.6.2条规定毂孔采取过盈配合,当采用RUT300型制动盘时压装力为196-392KN”。
Science&Technology Vision科技如果压装力小于196KN就称作制动盘压装压力不到下限图7压装压力不到下限的制动盘压装曲线图表如果压装力大于392KN就称作制动盘压装压力大于上限图8压装压力大于上限的制动盘压装曲线图表铁路客车轮轴组装检修及管理规则》第2.2.7.3.2条规定盘压力曲线末端降吨≤29.4kN”。
如果制动盘压力曲线末端降吨大于就称作制动盘压装曲线末端降吨超限。
. All Rights Reserved.9压装曲线末端降吨超限的制动盘压装曲线图表铁路客车轮轴组装检修及管理规则》第2.2.7.3.2条规定盘压力曲线开始上升的一点与终点处的一点连成一直线,组装曲线须全部在此直线以上”。
如果曲线开始上升的一点与终点处的一点连成有曲线在此直线以下,就称作制动盘压装曲线下凹。
图10压装曲线下凹的制动盘压装曲线图表轮对及制动盘压装的原理首先将车轴水平放置,将车轮或制动盘套在车轴上,在压装力的使车轮或制动盘沿轴向向内运动,在车轮或制动盘与车轴接触面产生弹塑性变形。
轮对压装曲线不合格的原因分析和改进措施
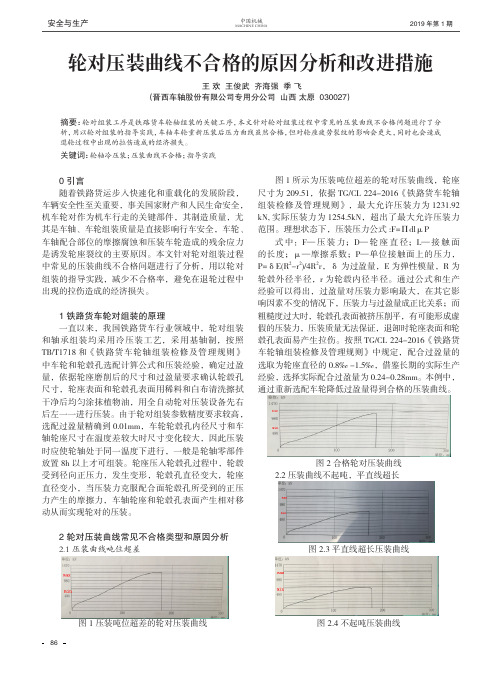
86安全与生产2019年第1期中国机械MACHINE CHINA轮对压装曲线不合格的原因分析和改进措施王 欢 王俊武 齐海强 季 飞(晋西车轴股份有限公司专用分公司 山西 太原 030027)0 引言随着铁路货运步入快速化和重载化的发展阶段,车辆安全性至关重要,事关国家财产和人民生命安全,机车轮对作为机车行走的关键部件,其制造质量,尤其是车轴、车轮组装质量是直接影响行车安全,车轮、车轴配合部位的摩擦腐蚀和压装车轮造成的残余应力是诱发轮座裂纹的主要原因。
本文针对轮对组装过程中常见的压装曲线不合格问题进行了分析,用以轮对组装的指导实践,减少不合格率,避免在退轮过程中出现的拉伤造成的经济损失。
1 铁路货车轮对组装的原理一直以来,我国铁路货车行业领域中,轮对组装和轴承组装均采用冷压装工艺,采用基轴制,按照TB/T1718和《铁路货车轮轴组装检修及管理规则》中车轮和轮毂孔选配计算公式和压装经验,确定过盈量,依据轮座磨削后的尺寸和过盈量要求确认轮毂孔尺寸,轮座表面和轮毂孔表面用稀料和白布清洗擦拭干净后均匀涂抹植物油,用全自动轮对压装设备先右后左一一进行压装。
由于轮对组装参数精度要求较高,选配过盈量精确到0.01mm,车轮轮毂孔内径尺寸和车轴轮座尺寸在温度差较大时尺寸变化较大,因此压装时应使轮轴处于同一温度下进行,一般是轮轴零部件放置8h 以上才可组装。
轮座压入轮毂孔过程中,轮毂受到径向正压力,发生变形,轮毂孔直径变大,轮座直径变小,当压装力克服配合面轮毂孔所受到的正压力产生的摩擦力,车轴轮座和轮毂孔表面产生相对移动从而实现轮对的压装。
2 轮对压装曲线常见不合格类型和原因分析2.1 压装曲线吨位超差图1压装吨位超差的轮对压装曲线图1所示为压装吨位超差的轮对压装曲线,轮座尺寸为209.51,依据TG/CL 224-2016《铁路货车轮轴组装检修及管理规则》,最大允许压装力为1231.92 kN,实际压装力为1254.5kN,超出了最大允许压装力范围。
铁路货车轴承压装曲线异常原因分析及措施
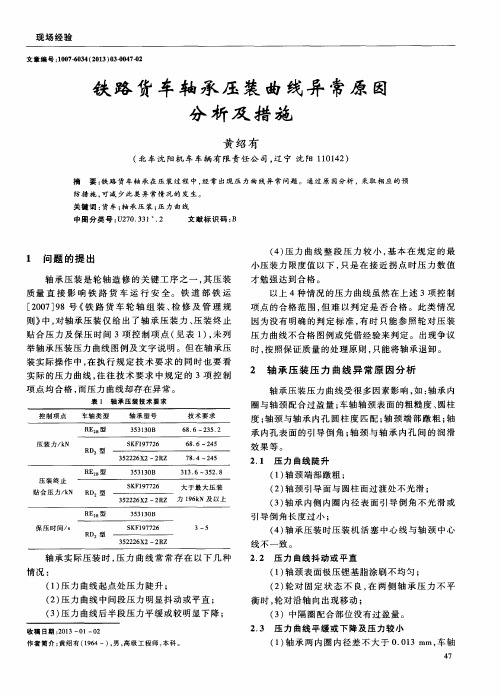
1 问题 的提 出
轴 承压 装 是 轮轴 造 修 的关键 工 序 之 一 , 其 压装 质量 直 接 影 响 铁 路 货 车 运 行 安 全 。铁 道 部 铁 运
( 4 ) 压力 曲线 整 段 压 力 较 小 , 基 本 在 规 定 的最
小 压装 力 限度值 以下 , 只 是 在 接 近 拐点 时 压 力 数值
内径相 对小 的一 端 组 装 在 轴颈 内侧 大 端 , 内圈 内径
( 3 ) 在规定过盈量 ( 见表 5 ) 范 围内, 适 当提 高
Hale Waihona Puke 过 盈量 值 , 建议按不小 于 0 . 0 7 0 m m 的过 盈 量 对 轴
颈、 轴 承进行 选 配 ; ( 4 ) 轴 承压 装 前 , 轴 颈 上 须 均 匀 涂 刷 Ⅱ号 防 锈 极 压 锂基脂 ; ( 5 ) 轴承压装时 , 按之前标注的大 、 小端方 向,
( 1 ) 压力 曲线 起点 处压 力 陡升 ;
( 2 ) 压力 曲线 中间段压 力 明显抖 动 或平 直 ; ( 3 ) 压力 曲线 后半 段压 力平 缓或 较 明显 下降 ;
收 稿 日期 : 2 0 1 3— 0 l一 0 2
( 3 )中隔 圈配合 部位 没有 过盈 量 。
2 . 3 压 力 曲线 平缓 或下 降及 压力较 小
才 勉强 达到 合格 。 以上 4种情况 的压力 曲线 虽然在 上述 3项 控制
[ 2 0 0 7 ] 9 8号 《 铁路 货 车轮轴 组装 、 检 修 及 管 理 规
则》 中, 对 轴 承压 装仅 给 出 了轴 承压 装 力 、 压 装 终 止 贴合 压 力 及 保压 时间 3项控 制 项 点 ( 见表 1 ) , 未 列 举轴 承压 装 压力 曲线 图例及 文 字说 明 。但 在轴 承 压 装 实际操 作 中 , 在 执 行 规 定技 术 要 求 的 同时 也 要 看 实 际 的压 力 曲线 , 往 往 技 术要 求 中规 定 的 3项 控 制 项点 均合 格 , 而压 力 曲线却存 在 异常 。
城轨轮对轴承压装不合格原因分析及改进措施
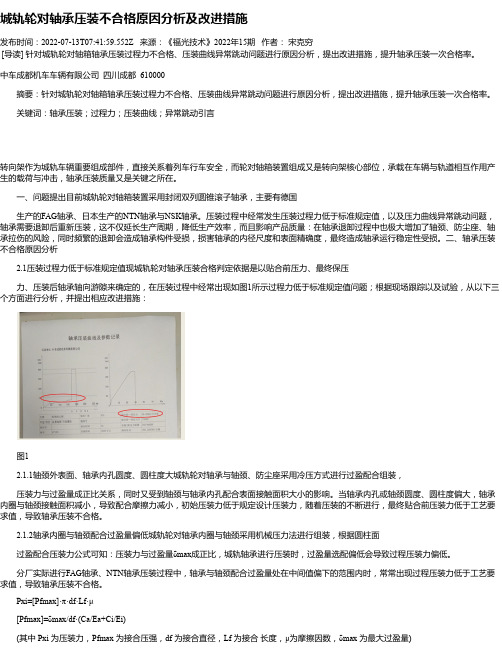
城轨轮对轴承压装不合格原因分析及改进措施发布时间:2022-07-13T07:41:59.552Z 来源:《福光技术》2022年15期作者:宋克穷[导读] 针对城轨轮对轴箱轴承压装过程力不合格、压装曲线异常跳动问题进行原因分析,提出改进措施,提升轴承压装一次合格率。
中车成都机车车辆有限公司四川成都 610000摘要:针对城轨轮对轴箱轴承压装过程力不合格、压装曲线异常跳动问题进行原因分析,提出改进措施,提升轴承压装一次合格率。
关键词:轴承压装;过程力;压装曲线;异常跳动引言转向架作为城轨车辆重要组成部件,直接关系着列车行车安全,而轮对轴箱装置组成又是转向架核心部位,承载在车辆与轨道相互作用产生的载荷与冲击,轴承压装质量又是关键之所在。
一、问题提出目前城轨轮对轴箱装置采用封闭双列圆锥滚子轴承,主要有德国生产的FAG轴承、日本生产的NTN轴承与NSK轴承。
压装过程中经常发生压装过程力低于标准规定值,以及压力曲线异常跳动问题,轴承需要退卸后重新压装,这不仅延长生产周期,降低生产效率,而且影响产品质量:在轴承退卸过程中也极大增加了轴颈、防尘座、轴承拉伤的风险,同时频繁的退卸会造成轴承构件受损,损害轴承的内径尺度和表面精确度,最终造成轴承运行稳定性受损。
二、轴承压装不合格原因分析2.1压装过程力低于标准规定值现城轨轮对轴承压装合格判定依据是以贴合前压力、最终保压力、压装后轴承轴向游隙来确定的,在压装过程中经常出现如图1所示过程力低于标准规定值问题;根据现场跟踪以及试验,从以下三个方面进行分析,并提出相应改进措施:图12.1.1轴颈外表面、轴承内孔圆度、圆柱度大城轨轮对轴承与轴颈、防尘座采用冷压方式进行过盈配合组装,压装力与过盈量成正比关系,同时又受到轴颈与轴承内孔配合表面接触面积大小的影响。
当轴承内孔或轴颈圆度、圆柱度偏大,轴承内圈与轴颈接触面积减小,导致配合摩擦力减小,初始压装力低于规定设计压装力,随着压装的不断进行,最终贴合前压装力低于工艺要求值,导致轴承压装不合格。
探讨提升货车轮对压装合格率的策略

探讨提升货车轮对压装合格率的策略提升货车轮对压装合格率一直是货车制造企业关注的重点问题,合格的轮对压装是保障货车安全行驶的重要环节。
目前货车轮对压装合格率并不十分理想,存在一定的提升空间。
本文将从工艺流程、技术设备、人员管理等方面探讨提升货车轮对压装合格率的策略,并提出相应的改进措施。
一、完善工艺流程工艺流程是影响货车轮对压装合格率的重要因素之一。
在完善工艺流程方面,首先要加强对原材料的品质管控,确保轮对及其零部件的质量符合要求;其次要优化压装工艺流程,确保每个环节严格按照标准操作;最后要加强对成品的检测和验收,确保每个轮对都符合要求。
还可以通过技术手段,引入自动化设备进行生产,提高生产效率和产品质量。
针对工艺流程方面存在的问题,货车制造企业可以制定相应的改进计划,加强对工艺流程的管理和控制,确保每个流程环节都能够严格按照标准操作,从而提升货车轮对压装合格率。
二、优化技术设备技术设备是影响货车轮对压装合格率的另一个关键因素。
货车制造企业可以考虑引进先进的轮对压装设备,提升生产效率和产品质量。
对现有设备进行性能优化和升级,确保设备的运行稳定和可靠性。
货车制造企业还可以通过技术手段,引入智能化设备和生产线,提高生产效率和产品质量。
通过对技术设备的优化,可以有效提升货车轮对压装合格率,提高产品质量。
三、加强人员管理人员管理是保障货车轮对压装合格率的重要保障。
货车制造企业可以加强对生产人员的技术培训和管理,提高员工的技术水平和责任意识。
同时要建立健全的激励机制,激发员工的积极性和创造性,提高整个生产团队的凝聚力和执行力。
货车制造企业还可以加强对生产人员的岗位管理,明确每个岗位的责任和权限,确保每个生产环节都得到严格执行。
通过加强人员管理,可以有效提高货车轮对压装合格率,降低质量风险。
探讨提升货车轮对压装合格率的策略

探讨提升货车轮对压装合格率的策略提升货车轮对压装合格率是提高货车安全性能的重要举措。
货车轮对是货车的重要部件,其安全稳定性直接关系到货车的行驶安全。
在货车生产和使用过程中,轮对压装合格率不高的问题依然存在,给货车的安全性能带来了很大隐患。
探讨提升货车轮对压装合格率的策略就显得尤为重要。
一、分析当前货车轮对压装合格率存在的问题1. 技术水平不够高当前国内货车轮对生产企业的生产技术水平参差不齐,一些小型企业由于资金、技术、设备等方面的限制,无法保证产品的质量。
而一些中型企业由于缺乏核心技术和创新意识,产品质量也难以得到保障。
这就导致了货车轮对的生产质量不稳定,影响了压装合格率的提高。
2. 生产管理不严格一些货车轮对生产企业在生产过程中存在管理不严格的问题,没有建立完善的生产管理体系和质量控制体系,对生产过程中的质量问题缺乏有效的监控手段和手段,导致产品质量无法得到有效保证。
3. 检验标准不统一当前各地对货车轮对的压装标准存在较大差异,导致检验结果的可比性不强。
一些地方对货车轮对的质量检验标准不够严格,对于不合格产品的认定和处理不够及时和严格,这就给了一些不法商家以钻空子的机会,导致了货车轮对压装合格率的下降。
1. 加强技术研发,提高产品质量货车轮对的生产企业应该加强技术研发工作,不断提升产品的技术水平和质量水平。
通过引进国外先进的生产设备和工艺技术,提高生产工艺水平和产品质量,确保产品的安全性和稳定性。
3. 推动行业标准的统一和提高相关政府部门应该加强对货车轮对压装标准的统一和提高,在全国范围内建立统一的货车轮对压装标准,并对标准进行修订和提高,确保标准的科学合理性和严格性。
加大对货车轮对压装质量的检测力度,提高对不合格产品的处理力度,严惩违法企业,确保货车轮对的压装合格率的提高。
4. 强化监管力度,加大对违法企业的打击力度相关政府部门应该加强对货车轮对生产企业和产品的监管力度,建立健全的监管体系,确保对不合格产品的及时发现和处理,加大对违法企业的打击力度,确保货车轮对的质量和安全性能。
探讨提升货车轮对压装合格率的策略
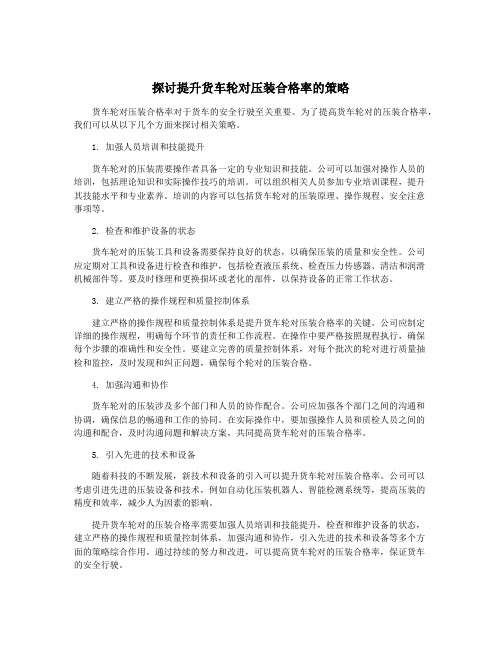
探讨提升货车轮对压装合格率的策略货车轮对压装合格率对于货车的安全行驶至关重要。
为了提高货车轮对的压装合格率,我们可以从以下几个方面来探讨相关策略。
1. 加强人员培训和技能提升货车轮对的压装需要操作者具备一定的专业知识和技能。
公司可以加强对操作人员的培训,包括理论知识和实际操作技巧的培训。
可以组织相关人员参加专业培训课程,提升其技能水平和专业素养。
培训的内容可以包括货车轮对的压装原理、操作规程、安全注意事项等。
2. 检查和维护设备的状态货车轮对的压装工具和设备需要保持良好的状态,以确保压装的质量和安全性。
公司应定期对工具和设备进行检查和维护,包括检查液压系统、检查压力传感器、清洁和润滑机械部件等。
要及时修理和更换损坏或老化的部件,以保持设备的正常工作状态。
3. 建立严格的操作规程和质量控制体系建立严格的操作规程和质量控制体系是提升货车轮对压装合格率的关键。
公司应制定详细的操作规程,明确每个环节的责任和工作流程。
在操作中要严格按照规程执行,确保每个步骤的准确性和安全性。
要建立完善的质量控制体系,对每个批次的轮对进行质量抽检和监控,及时发现和纠正问题,确保每个轮对的压装合格。
4. 加强沟通和协作货车轮对的压装涉及多个部门和人员的协作配合。
公司应加强各个部门之间的沟通和协调,确保信息的畅通和工作的协同。
在实际操作中,要加强操作人员和质检人员之间的沟通和配合,及时沟通问题和解决方案,共同提高货车轮对的压装合格率。
5. 引入先进的技术和设备随着科技的不断发展,新技术和设备的引入可以提升货车轮对压装合格率。
公司可以考虑引进先进的压装设备和技术,例如自动化压装机器人、智能检测系统等,提高压装的精度和效率,减少人为因素的影响。
提升货车轮对的压装合格率需要加强人员培训和技能提升,检查和维护设备的状态,建立严格的操作规程和质量控制体系,加强沟通和协作,引入先进的技术和设备等多个方面的策略综合作用。
通过持续的努力和改进,可以提高货车轮对的压装合格率,保证货车的安全行驶。
轮对压装机压装曲线不合格原因分析及应对措施

轮对压装机压装曲线不合格原因分析及应对措施发布时间:2023-03-08T03:33:23.121Z 来源:《中国科技信息》2022年19期第10月作者:李丽娜于涛[导读] 本文介绍了TG0101微机控制轮轴压装机及其压装过程中的加工工艺要求,分析了不合格压装曲线的具体情形及合格压装曲线的范例,强调了合格压装的重要性李丽娜于涛中车沈阳机车车辆有限公司,辽宁沈阳 110142摘要:本文介绍了TG0101微机控制轮轴压装机及其压装过程中的加工工艺要求,分析了不合格压装曲线的具体情形及合格压装曲线的范例,强调了合格压装的重要性。
介绍了压装机的日常维护内容。
[关键词]:轮轴压装机工艺分析压装曲线日常维护1绪论1.1 概述车辆轮对,是由两个同类型和同材质的车轮与一根车轴按规定压力和规定尺寸紧压配合组装成的一个整体。
它承受着车辆的全部载荷,并在负重的条件下沿轨道作高速运转。
因此,要求它能圆滑地滚动并坚固耐用,以确保行车的安全、平稳。
采用压装法,紧密配合联接无需用键和螺钉,便能传递较大的扭矩和承受轴向载荷。
因而在相同载荷下,能减小零件尺寸,节省金属材料。
转向架分厂TG0101微机控制轮轴压装机主要承担轮对组装任务。
该压装机是一台具有自动记录铁路车辆轮轴压装过程中产生的位移---压力关系曲线及有关数据的新一代压装机,是铁路车辆轮轴压装的专用设备。
1.2 轮轴压装TG0101微机控制轮轴压装机是由转向架分厂新引进的,适用于铁路新造及检修客货车轮对组装的专用装备。
TG0101微控制轮对压装机主要由主机、测量系统、液压系统、曲线记录系统、曲线输出系统、控制系统等组成。
该设备可与车间的HIMS系统进行通讯。
可压装目前及今后提速的客货车轮对及制动盘,以RD2、RE2B等国内客货车轮对为典型压装轮对。
2组装加工工艺要求分析轮对组装的工艺要求很高,它直接影响压装的效果和压装曲线的好坏。
以RD2车轴为例,在组装中应满足以下的工艺要求:1)、在轮对压装前,轮座表面及轮毂孔内径面必须清洁,均匀涂抹纯植物油。
关于动车组轮对压装曲线分析判定及建议_景彪

文章编号:1002-7602(2011)04-0040-03关于动车组轮对压装曲线分析判定及建议景彪(铁道部驻太原机车车辆验收室,山西太原030009)摘要:针对动车组轮对压装出现的不合格F-S曲线,分析了EN标准动车组轮对压装F-S曲线的正确判定方法,并提出了建议。
关键词:动车组;轮对压装;F-S曲线;判定方法;建议中图分类号:U279.3+3文献标识码:B目前,国内动车组轮对的生产制造依据的是欧洲技术标准(EN13260:20095铁路应用轮对和转向架轮对产品要求6、EN13261:20095铁路应用轮对和转向架车轴产品要求6、EN13262:2004+A1:20085铁路应用轮对和转向架车轮产品要求6),通过引进、消化、创新,动车组轮对已完全实现了国产化。
在动车组轮对的验收过程中,发现一些典型的不合格压装F-S 曲线被误判为合格曲线。
压装曲线是鉴定轮对组装质量的唯一标准,压装曲线及终点压力需要符合标准要求才能确认轮轴联结程度的可靠性,而压装质量关系到动车组的行车安全。
1动车组轮对压装F-S曲线典型实例分析图1是2010年8月25日压装的一条CRH3) 380型动车轮对左侧车轮压装曲线。
图2是2010年3月19日压装的一条CRH3型拖车轮对左侧制动盘压装曲线。
上述2条曲线被误判为合格曲线进行交验。
目前动车组轮对压装曲线的判定依据是EN标准及该型轮对的压装力要求,并通过对曲线进行目测观察做出判定,而肉眼的分辨力有限,因此给出了错误的结论。
收稿日期:2010-06-18;修订日期:2011-01-29作者简介:景彪(1965-),男,高级工程师。
图1CRH3)380型动车轮对左侧车轮压装曲线图2C RH3型拖车轮对左侧制动盘压装曲线通过检查压装机电脑中存贮的Log界面(压装过程记录日志),发现图1中压装曲线的AB段降吨4516kN,降吨位移为28mm;图2中压装曲线过油槽部的B点压装力与A点压装力相同,但A B段位移为28mm,这说明过油槽25mm处没有恢复到油槽前的最大压装力。
铁路货车轮对压装压力曲线问题分析的建议

某公司采用数控立式车床加工货车车轮毂孔,在车轮进行组装时,出现图1-a 和图1-b 所示压装曲线的现象,压装曲线不起吨(欠吨)、末端平直降吨不符合TB/T 1718—2003铁道车辆轮对组装技术条件要求,严重影响轮对的组装质量,导致轮对进行退轮返工,在退卸车轮过程中可能会产生车轴轮座和车轮轮毂孔内表拉伤的风险,造成车轴和车轮的报废。
1轮对压装原理铁路货车轮对组装采用过盈配合、冷压装的方式进行。
车轴的轮座部分在压装力的作用下沿着车轮轮毂孔轴向移动,在压装配合面产生弹性和塑性变形,当压装力克服压装配合面轮毂上正压力产生的摩擦阻力时,车轴与轮毂孔表面产生相对移动,从而实现轮轴的压装,确保轮对能有效传递力和扭矩。
轮对压装时,压力曲线形状及终点压装力主要与配合面粗糙度、过盈量、几何形状、润滑等因素有关。
一般来说过盈量对压入力影响最大,压装力与过盈量成正比关系;粗糙度值过小时,压装不容易起吨,粗糙度值过大时,轮毂孔表面波峰被挤压削平,有可能形成虚假的最终压装力,压装质量得不到保证,甚至形成金属粉末,在退卸时容易产生轮、轴表面的拉伤;几何形状尤其是配合面的圆柱度相差不大时,对压力曲线末端压装力的下降能起到补偿的作用;表面的润滑主要是防止卡住、擦伤,并用于降低摩擦系数。
2压装曲线不起吨的原因分析1)使用数控立式车床与普通立式车床加工车轮,唯一不同的是刀具的改变;由于数控立式车床加工车轮毂孔时,精车采用的是机夹车刀(CNMG120412-P),加工后轮毂孔表面粗糙度在R a(2.0~3.6)μm 范围之间,压装时不容易起吨,出现铁路货车轮对压装压力曲线问题分析的建议王艳萍收稿日期:2013-03-18;修回日期:2013-04-18作者简介:王艳萍(1983-),女,甘肃白银人,助理工程师,主要从事车辆工程研究,E-mail :Yp.wang@ 。
文章编号:1674-9146(2013)05-0101-0211位移/mm1-a1<minF m F 11位移/mm1-b2+3/0>15%F F m 图1铁路货车轮对压装压力不合格压装曲线. All Rights Reserved.图1-a 的压装力达不到规定的最小值。
探讨提升货车轮对压装合格率的策略

探讨提升货车轮对压装合格率的策略货车轮对是货车行驶的关键部件之一,其质量直接影响货车的行驶安全性和可靠性。
目前,货车轮对在压装过程中存在一定的质量问题,例如轮对拧断、卡不牢等问题,严重影响货车的正常行驶。
因此,提升货车轮对压装合格率是一个重要的课题,本文将从多个方面探讨提升货车轮对压装合格率的策略。
一、规范压装流程货车压装的流程应该严格按照标准进行规范化,有效避免因人为操作不当而导致的质量问题。
在压装前,应该认真检查压装设备和工具的质量,确保其符合标准,同时还要对轮对和轴箱进行质量检查,判断是否已经达到了压装的要求。
在压装过程中,要注意使用正确的工具和操作方法,并确保操作人员的专业技能和经验水平。
这样可以有效提升货车压装的合格率,并保证货车的正常行驶。
二、加强压装设备的维护货车压装设备的稳定性和准确性对压装合格率影响非常大,因此加强设备的维护是必不可少的。
为确保压装设备的可靠性和准确性,需要建立完善的设备维护和保养制度,定期对设备进行保养和检修,在设备出现故障时及时报修。
另外还可以针对设备进行技术改进和优化,提升设备的性能指标,降低故障率和维修成本。
三、培养专业技能人才货车轮对压装是高技能操作,对操作人员的专业技能要求非常高。
因此,有效提升操作人员的技能和认知水平,是提高货车轮对压装合格率的重要手段。
可以通过拟订完善的培训方案,针对操作人员的不同需求,提供系统的培训和技能交流,使操作人员逐步掌握高效交互技能,从而提升其技能水平和综合素质。
四、引进先进的压装技术设备引进先进的压装技术设备是提高货车轮对压装品质的重要途径。
通过引进先进的设备和技术,可以提升压装效率和压装质量,并有效降低成本。
现代化的压装技术可以实现对轴箱和轮对的精确测量和对准,从而可以有效避免压装过程中的偏差和误差,确保货车的正常行驶。
五、加强质量管理货车轮对压装的质量管理是提高合格率的关键。
建立科学严密的质量管理体系,监控压装全过程,确保质量符合国家标准和公司要求,做到事前预防、事中控制和事后追踪。
铁路货车滚动轴承压装曲线异常原因分析及对策
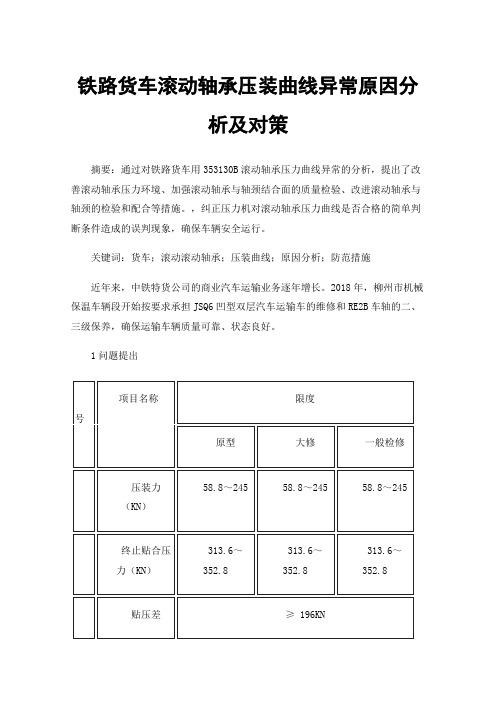
铁路货车滚动轴承压装曲线异常原因分析及对策摘要:通过对铁路货车用353130B滚动轴承压力曲线异常的分析,提出了改善滚动轴承压力环境、加强滚动轴承与轴颈结合面的质量检验、改进滚动轴承与轴颈的检验和配合等措施。
,纠正压力机对滚动轴承压力曲线是否合格的简单判断条件造成的误判现象,确保车辆安全运行。
关键词:货车;滚动滚动轴承;压装曲线;原因分析;防范措施近年来,中铁特货公司的商业汽车运输业务逐年增长。
2018年,柳州市机械保温车辆段开始按要求承担JSQ6凹型双层汽车运输车的维修和RE2B车轴的二、三级保养,确保运输车辆质量可靠、状态良好。
1问题提出4保压时间(S)3S 及以上353130B滚动轴承的压装是RE2B车轴维修的关键工序之一,其质量直接影响JSQ6货车的运输安全。
《铁路货车车轴装配维护管理规则》(铁运[〔2016〕191号)仅规定滚动轴承的质量检验包括轴承压装力、压装终止压力、压差、压装时间四项,需要满足相应的参数要求(见表1),但对滚动轴承的压装压力曲线没有给出标准图例和文字说明,容易出现质量漏洞。
比如在实际工作中,经常会发现被判断为压力拟合合格的P-S压力曲线满足表1的要求,但压力曲线有异常趋势。
为了保证车辆的安全运行,有必要找出问题的原因,制定有效的措施,切实解决问题。
表1 353130B型滚动轴承压装限度要求1 )压力曲线起点处压力陡升(见图2)2)压力曲线中段压力明显震荡(见图3);3)压力曲线全断面压力较小,基本低于规定的最小压力限值,接近拐点时压力值勉强达到合格(见图4)。
在上述三种情况下,根据《铁路货车车轴装配、检修和管理规则》,轴承压装的四个压装参数均在规定范围内,由轴承压装判定为合格。
但对压配曲线不良的滚动轴承进行退圈检查后,发现曲线不良是由于滚动轴承与轴颈配合不良造成压力变化所致。
如果不及时返工,将会给车轴的运行带来安全隐患。
2原因分析经过深入调查、讨论和判断,得出导致滚动轴承压装压力曲线异常的主要因素有:滚动轴承压装室内的温度和湿度、滚动轴承内圈和轴颈之间的干涉、轴颈表面的粗糙度和圆柱度、轴颈端部的厚度、滚动轴承内圈和轴颈的润滑效果、轴承压装的运行状态等。
轴承压装曲线不良原因分析

轴承压装曲线不良原因分析摘要:通过对轴承压装机理、压装曲线及构件分析,阐述了压装曲线不良的原因及解决措施。
关键词:轮对;轴承;后挡;压装曲线;原因分析1问题的提出目前,轴承、后挡与轴颈的组装多采用冷压装工艺,压装设备为油压机和微机控制的记录系统。
车轴磨削加工、后挡车削加工并磷化后与轴承一起按基轴制进行配置,通过位移-压力复合曲线真实反映出压装的质量。
一般情况下轴承一次压装合格率可达96.3%以上,少数轴承一次压装不良的原因集中反映在压装曲线上,常出现曲线尖峰或滞后、陡吨的情况,特别是在RD2(A)型车轴组装时,此类现象更突出。
部标准规定:轴承压装要慢速推进,压力应平稳上升。
2原因分析2.1轴承组装的机理分析轴承组装为过盈冷压装,采用的密封座内径、轴承内圈内径与轴颈过盈量在0.05~0.102mm之间,后挡内径与防颈过盈量在0.018~0.085mm之间。
在图1的组装过程中,轴承压装机的顶尖1伸出,使轮对精确定位,夹紧装置将轮对固定。
随后压装油缸2推动放置在轴承托架上的轴承,当压装力克服了压装配合面上正压力(压装过程中轴颈、后挡及轴承各部件都会产生弹性和塑性变形,配合面上便形成了正压力)产生的摩擦力时,轴承(前后密封座3、7,两内圈4、6,中隔圈5)和后挡8与车轴轴颈防颈产生相对移动,从而实现轴承的组装,最后打印出反映压力随位置变化及保压时间情况的位移——压力曲线。
2.2轴承压装曲线分析1.合格曲线图2轴承压装曲线中纵坐标为压力值(kN),横坐标为位移量(mm),并有一反映保压状况的时间轴(s)。
自设备工进开始,每0.1mm记录一个对应的压力值,将这些点联起来,便形成一条曲线,从而反映轴承在压入轴颈过程中的每一位置的压力变化。
从下拐点A到上拐点B间,纵坐标是压力值,而横坐标虽还是位移量,但意义不同了,因为此时轴承已经紧贴轴颈台阶,其移动量反映的是床身变形。
从上拐点B向右至C点,横坐标变为时间量,纵坐标仍为压力值,它反映了时间与压力的关系(保压5s),从而完成整个组装过程的曲线记录。
轮对组装常见故障及原因浅析

轮对组装常见故障及原因浅析摘要:货车轮对组装是轮对四级修的关键环节,轮对组装质量是决定列车安全可靠运行的关键,也是维护货运安全的保证。
本文结合压装曲线对常见的轮对组装故障及压装不合格分解后出现的轮座、轮毂孔拉伤原因进行了简要分析,并提出相关质量保证措施。
关键词:轮对组装;原因分析;压装曲线;保证措施1.前言轮对是车辆转向架的关键部件,如果轮对组装质量未能满足要求,车辆在运行过程中就会出现车轴和车轮的松动,内侧距超差等现象,其直接后果是造成列车脱轨事故,更会直接影响铁路干线的安全畅通。
因此,轮对组装质量关键性、重要性不言而喻。
2.轮对组装机理分析及相关工艺要求货车轮对组装采用过盈配合冷压装,在组装过程中,当压装力克服了压装配合面上径向压力产生的摩擦力时,两者间完成于水平方向产生的相对移动,从而实现轮对的组装。
压装压力曲线图是评价压装合格与否的重要条件,轮对压装时,压装压力曲线形状及终点压装力主要与配合面粗糙度、过盈量、几何形状、润滑等因素有关,曲线合格与否为多因素共同作用的结果而非单一因素造成。
压装压力曲线不合格将导致轮对进行退卸返工,分解的原车轮与原车轴不得原位进行第二次压装,须重新选配其他车轮。
且在退卸车轮过程中可能会产生车轴轮座和车轮轮毂孔内的表面拉伤,造成车轴和车轮的报废,在造成了配件材料、生产工时的浪费的同时,也影响了车间的生产节奏和生产安排,同时也会对操作工的心理造成一定的不利影响。
3.常见压装曲线不合格的产生原因及预防措施3.1压装不合格的主要表现形式及原因分析(1)压装力高于理论最大值或低于最小值,即“吨大”、“吨小”。
车轴轮座与车轮轮毂孔间为过盈配合,一般来说过盈量对压装力影响最大,轮座压入轮毂孔过程中,两者接触面上会形成垂直于接触面的径向压力,压装力与过盈量成正比关系;过盈量越大,配合面径向正压力越大,轮对组装过程中配合面的摩擦力越大,那么就可能出现轮座拉伤或吨大等问题。
反之,轮对组装过程中可能会出现吨小或曲线平直问题,从而对轮对在货车车辆运输运用过程中的安全可靠性失去保证。
轴承压装力曲线不合格的原因及处理
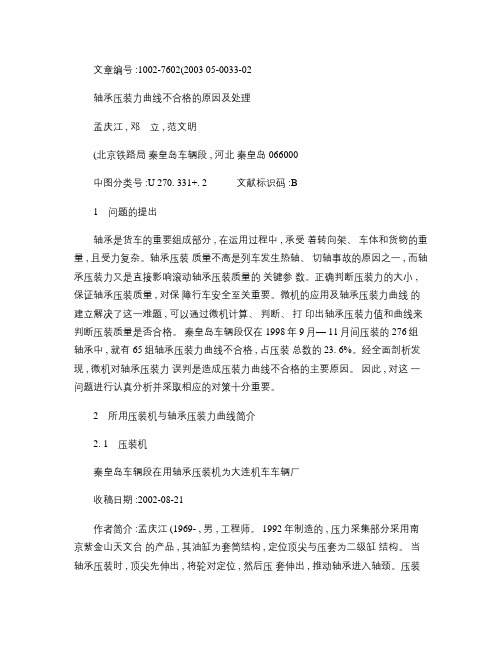
文章编号 :1002-7602(2003 05-0033-02轴承压装力曲线不合格的原因及处理孟庆江 , 邓立 , 范文明(北京铁路局秦皇岛车辆段 , 河北秦皇岛 066000中图分类号 :U 270. 331+. 2文献标识码 :B1问题的提出轴承是货车的重要组成部分 , 在运用过程中 , 承受着转向架、车体和货物的重量 , 且受力复杂。
轴承压装质量不高是列车发生热轴、切轴事故的原因之一 , 而轴承压装力又是直接影响滚动轴承压装质量的关键参数。
正确判断压装力的大小 , 保证轴承压装质量 , 对保障行车安全至关重要。
微机的应用及轴承压装力曲线的建立解决了这一难题 , 可以通过微机计算、判断、打印出轴承压装力值和曲线来判断压装质量是否合格。
秦皇岛车辆段仅在 1998年 9月— 11月间压装的 276组轴承中 , 就有 65组轴承压装力曲线不合格 , 占压装总数的 23. 6%。
经全面剖析发现 , 微机对轴承压装力误判是造成压装力曲线不合格的主要原因。
因此 , 对这一问题进行认真分析并采取相应的对策十分重要。
2所用压装机与轴承压装力曲线简介2. 1压装机秦皇岛车辆段在用轴承压装机为大连机车车辆厂收稿日期 :2002-08-21作者简介 :孟庆江 (1969- , 男 , 工程师。
1992年制造的 , 压力采集部分采用南京紫金山天文台的产品 , 其油缸为套筒结构 , 定位顶尖与压套为二级缸结构。
当轴承压装时 , 顶尖先伸出 , 将轮对定位 , 然后压套伸出 , 推动轴承进入轴颈。
压装过程中 , 顶尖油缸内的液压油是靠压装油缸的压力通过溢流阀返回油箱的 , 顶尖油缸内的压力保持溢流阀调定的压力。
2. 2轴承压装力曲线把轴承整个压装过程各个阶段压装力的数值用图形显示出来即为轴承压装力曲线 , 它用来对轴承压装质量进行最终控制。
轴承与轴颈的压装过程主要是前后 2列轴承、 2个密封座和 1个后挡串联压入的过程。
- 1、下载文档前请自行甄别文档内容的完整性,平台不提供额外的编辑、内容补充、找答案等附加服务。
- 2、"仅部分预览"的文档,不可在线预览部分如存在完整性等问题,可反馈申请退款(可完整预览的文档不适用该条件!)。
- 3、如文档侵犯您的权益,请联系客服反馈,我们会尽快为您处理(人工客服工作时间:9:00-18:30)。
轮对压装曲线不合格的原因分析和改进措施作者:王欢王俊武齐海强季飞
来源:《中国机械·上半月》2019年第01期
摘要:轮对组装工序是铁路货车轮轴组装的关键工序,本文针对轮对组装过程中常见的压装曲线不合格问题进行了分析,用以轮对组装的指导实践,减少不合格率,避免在退轮过程中出现的拉伤造成的经济损失。
关键词:轮轴冷压装;压装曲线不合格;指导实践
0 引言
随着铁路货运步入快速化和重载化的发展阶段,车辆安全性至关重要,事关国家财产和人民生命安全,机车轮对作为机车行走的关键部件,其制造质量,尤其是车轴、车轮组装质量是直接影响行车安全,车轮、车轴配合部位的摩擦腐蚀和压装车轮造成的残余应力是诱发轮座裂纹的主要原因。
本文针对轮对组装过程中常见的压装曲线不合格问题进行了分析,用以轮对组装的指导实践,车轴车轮重新压装后压力曲线虽然合格,但对轮座疲劳裂纹的影响会更大,同时也会造成退轮过程中出现的拉伤造成的经济损失。
1 铁路货车轮对组装的原理
一直以来,我国铁路货车行业领域中,轮对组装和轴承组装均采用冷压装工艺,采用基轴制,按照TB/T1718和《铁路货车轮轴组装检修及管理规则》中车轮和轮毂孔选配计算公式和压装经验,确定过盈量,依据轮座磨削后的尺寸和过盈量要求确认轮毂孔尺寸,轮座表面和轮毂孔表面用稀料和白布清洗擦拭干净后均匀涂抹植物油,用全自动轮对压装设备先右后左一一进行压装。
由于轮对组装参数精度要求较高,选配过盈量精确到0.01mm,车轮轮毂孔内径尺寸和车轴轮座尺寸在温度差较大时尺寸变化较大,因此压装时应使轮轴处于同一温度下进行,一般是轮轴零部件放置8h以上才可组装。
轮座压入轮毂孔过程中,轮毂受到径向正压力,发生变形,轮毂孔直径变大,轮座直径变小,当压装力克服配合面轮毂孔所受到的正压力产生的摩擦力,车轴轮座和轮毂孔表面产生相对移动从而实现轮对的压装。
2 轮对压装曲线常见不合格类型和原因分析
2.1 压装曲线吨位超差
图2.1所示为压装吨位超差的轮对压装曲线,轮座尺寸为209.51,依据TG/CL 224-2016《铁路货车轮轴组装检修及管理规则》,最大允许压装力为1231.92 kN,实际压装力为1254.5kN,超出了最大允许压装力范围。
理想状态下,压装压力公式:
式中:F—压装力;D—轮座直径;L—接触面的长度;μ—摩擦系数;P—单位接触面上的压力,P=δE(R2-r2)/4R2r,δ为过盈量,E为弹性模量,R为轮毂外径半径,r为轮毂内径半径。
通过公式和生产经验可以得出,过盈量对压装力影响最大,在其它影响因素不变的情况下,压装力与过盈量成正比关系;而粗糙度过大时,轮毂孔表面被挤压削平,有可能形成虚假的压装力,压装质量无法保证,退卸时轮座表面和轮毂孔表面易产生拉伤。
按照TG/CL 224-2016《铁路货车轮轴组装检修及管理规则》中规定,配合过盈量的选取为轮座直径的0.8‰-1.5‰,借鉴长期的实际生产经验,选择实际配合过盈量为0.24-0.28mm。
本例中,通过重新选配车轮降低过盈量得到合格的压装曲线。
2.2 压装曲线不起吨,平直线超长
观察压装曲线的变化趋势,压装力呈上升趋势,曲线末端平直线超长且有降吨现象,轮轴配合的过盈量在整个压装过程变化不大,可推断是过盈量比(过盈量/轮毂直径)的变化引起的,过盈量比降低使得压装曲线出现平直降吨。
为实现末端压装曲线的压力补偿,通过增加轮毂孔圆柱度或减少轮座圆柱度,使得轮毂孔圆柱度接近并小于輪座圆柱度,本例中通过减少车轮轮毂孔圆柱度,车轮轮毂圆柱度接近轮座圆柱度得到合格的压装压力曲线。
3 结语
如何提升货车轮对组装合格率是货车制造生产单位必须要面对的课题,也是货车运行安全的重要保证,轮对组装合格率要受到很多因素的影响,包括压装机状态、压装速度、配合面状态、过盈量、圆柱度、加工精度、工艺落实、管理水平、人员素质、环境温度等,轮对组装合格率的提升必须要从日常作业来抓,从方方面面入手,从而达到预期的目标。
参考文献:
[1]王艳萍.铁路货车轮对压装曲线问题分析的建议[J].铁道车辆,2013(5).
[2]袁旭芳.铁路车辆轮对压装曲线陡跳工艺探讨[J].煤矿机械,2005(5).
[3]张利强.机车轮对轮轴冷压工艺仿真与试验研究[D].上海交通大学,2010(4)。