薄膜力学性能评价技术
薄膜检测标准与方法简介
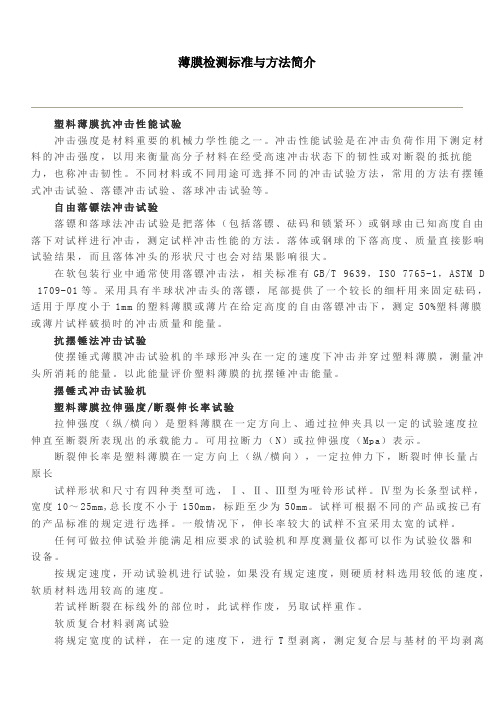
薄膜检测标准与方法简介塑料薄膜抗冲击性能试验冲击强度是材料重要的机械力学性能之一。
冲击性能试验是在冲击负荷作用下测定材料的冲击强度,以用来衡量高分子材料在经受高速冲击状态下的韧性或对断裂的抵抗能力,也称冲击韧性。
不同材料或不同用途可选择不同的冲击试验方法,常用的方法有摆锤式冲击试验、落镖冲击试验、落球冲击试验等。
自由落镖法冲击试验落镖和落球法冲击试验是把落体(包括落镖、砝码和锁紧环)或钢球由已知高度自由落下对试样进行冲击,测定试样冲击性能的方法。
落体或钢球的下落高度、质量直接影响试验结果,而且落体冲头的形状尺寸也会对结果影响很大。
在软包装行业中通常使用落镖冲击法,相关标准有GB/T 9639,ISO 7765-1,ASTM D 1709-01等。
采用具有半球状冲击头的落镖,尾部提供了一个较长的细杆用来固定砝码,适用于厚度小于1mm的塑料薄膜或薄片在给定高度的自由落镖冲击下,测定50%塑料薄膜或薄片试样破损时的冲击质量和能量。
抗摆锤法冲击试验使摆锤式薄膜冲击试验机的半球形冲头在一定的速度下冲击并穿过塑料薄膜,测量冲头所消耗的能量。
以此能量评价塑料薄膜的抗摆锤冲击能量。
摆锤式冲击试验机塑料薄膜拉伸强度/断裂伸长率试验拉伸强度(纵/横向)是塑料薄膜在一定方向上、通过拉伸夹具以一定的试验速度拉伸直至断裂所表现出的承载能力。
可用拉断力(N)或拉伸强度(Mpa)表示。
断裂伸长率是塑料薄膜在一定方向上(纵/横向),一定拉伸力下,断裂时伸长量占原长试样形状和尺寸有四种类型可选,Ⅰ、Ⅱ、Ⅲ型为哑铃形试样。
Ⅳ型为长条型试样,宽度10~25mm,总长度不小于150mm,标距至少为50mm。
试样可根据不同的产品或按已有的产品标准的规定进行选择。
一般情况下,伸长率较大的试样不宜采用太宽的试样。
任何可做拉伸试验并能满足相应要求的试验机和厚度测量仪都可以作为试验仪器和设备。
按规定速度,开动试验机进行试验,如果没有规定速度,则硬质材料选用较低的速度,软质材料选用较高的速度。
薄膜力学性能解析

19
二、残余应力的测量
1. Stoney公式
在薄膜残余应力的作用下,基底会发生挠曲,这
种变形尽管很微小,但通过激光干涉仪或者表面轮廓
仪,能够测量到挠曲的曲率半径。基底挠曲的程度反
映了薄膜残余应力的大小,Stoney给出了二者之间的
3
分类
脆性薄膜
按
脆性基底
力
学
性
质 分
脆性薄膜
类
韧性基底
韧性薄膜 脆性基底
韧性薄膜 韧性基底
4
4.1 薄膜的弹性性能
一、薄膜的弹性常数
弹性模量是材料最基本的力学性能参之一,由于 薄膜的某些本质的不同之处,其弹性模量可能完全不 同于同组分的大块材料。
5
三点弯曲
如图所示,加载和挠度的测量均在两支点中心位置,
2
y
2bdy
hs 2
hs 2h f
I f y2bdy
hs 2
(4.3)
实验中测出载荷增量与中心挠度增量的关系曲线(近似 线性),求出其斜率,用(4.1)式求出薄板的抗弯刚度,若基 体弹性模量已知,则利用(4.2)式可求得薄膜的弹性模量。
7
压痕法
纳米压痕技术可用以测定薄膜的硬度、弹性模量以
及薄膜的蠕变行为等,其理论基础是Sneddon关于轴
详细推导过程见流程图2。
15
表4.1 式(4.21)中对应于hg /R 的系数
16
17
图2 根据p-h 曲线确定应力-应变关系的流程图
4.2 薄膜的残余应力
一、残余应力的来源
通常认为,薄膜中的残余应力分为热应力和内应力两种 。
薄膜材料物理-薄膜的力学性质
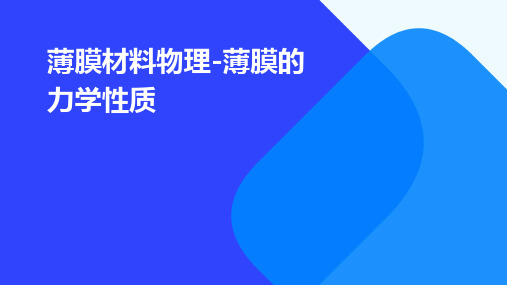
塑性变形机制
屈服强度是描述材料抵抗塑性变形能力的物理量,当外力达到屈服强度时,材料开始发生不可逆的塑性变形。
应力-应变曲线是描述材料在受力过程中应力与应变关系的曲线,通过该曲线可以确定材料的弹性模量和屈服强度等力学性能参数。
屈服强度与应力-应变曲线
应力-应变曲线
屈服强度
塑性形变对薄膜物理性能的影响
断裂表面形貌与机理
温度对薄膜的力学性能产生影响,低温下材料脆性增大,高温下材料韧性增强。
温度
湿度
加载速率
湿度对薄膜材料的力学性能产生影响,湿度过高可能导致材料吸湿膨胀,降低力学性能。
加载速率越快,材料吸收的能量越少,断裂强度越低。
03
02
01
பைடு நூலகம்
环境因素对薄膜断裂性质的影响
05
薄膜的疲劳性质
薄膜在循环应力作用下,经过一段时间后发生断裂的现象。
屈服强度
断裂强度是描述材料在受到外力作用时发生断裂行为的应力值,对于薄膜材料,其断裂强度也是衡量其力学性能的重要参数之一。
断裂强度
薄膜的力学性能参数
02
薄膜的弹性性质
弹性模量
是指材料在受到外力作用时,单位面积上产生的正应力与应变之比,是衡量材料抵抗弹性变形能力的物理量。对于薄膜材料,其弹性模量决定了材料在受力时的刚度和变形程度。
疲劳现象
循环应力导致薄膜内部产生微裂纹,裂纹逐渐扩展导致薄膜断裂。
疲劳机理
循环应力的幅值、频率、温度、薄膜材料的性质等。
影响因素
疲劳现象与机理
疲劳寿命预测与实验验证
疲劳寿命预测
基于疲劳裂纹扩展速率和应力强度因子幅值,预测薄膜的疲劳寿命。
实验验证
通过实验测试薄膜的疲劳寿命,与预测结果进行对比,评估预测模型的准确性。
第五章 薄膜材料的评价表征及物性测定

(5-5)
优点
不必知道Δ L,L的绝对值 测量范围:及纳米到几百纳米 测量精度:1nm或更高
33
5.3 薄膜材料的评价表征
椭圆偏振法
属于精确测量方法 属于无损检测方法 原理
34
5.3 薄膜材料的评价表征
二、结晶状态和晶体结构
X射线衍射评价表征薄膜具有特殊性
评价表征项目 成分(构成元素) 表面状态 组织、形态
评价表征内容 构成薄膜材料的主要元素及其比例 特意掺入的微量元素及杂质等 元素在膜面内的分布,在膜厚方向的分布等 气体吸附状态,化学结合状态,与基板的界面状态 单体,合金,化合物,混合物,相状态 晶态,非晶态,单晶,多晶超点阵,等 各向同性多晶体,择优取向,纤维构造 晶体学取向,晶粒尺寸,结晶状态 晶体缺陷:点缺陷、线缺陷、面缺陷、体缺陷
也能进行破 坏性分析 也能进行破 坏性分析
10-9~10-6 破坏性分析 与质量大小相关
10
RBS
·(100~5000) +
Li~U
5.2 薄膜材料评价表征方法及其选择
(b) 根据显微图像+衍射(microscopy & diffraction)确定结构
入射探针
方法 XRD SEM TEM AFM 射线·电压 / kV X射线<30(射线源) 电子·(0.5~40) 电子·(50~1000) 固体探针 束径 / nm / / 2~20 检测 信号 X射线 电子 电子 最表面 深度 / μm 1~10 ≈ 0.01 0.001~1
薄膜很薄 表面和界面所占比例很大 会形成非稳态结构 气相沉积薄膜一般具有非化学计量组成 含有更多的缺陷 存在应力 有些具有择优取向和多层结构
薄膜拉伸率
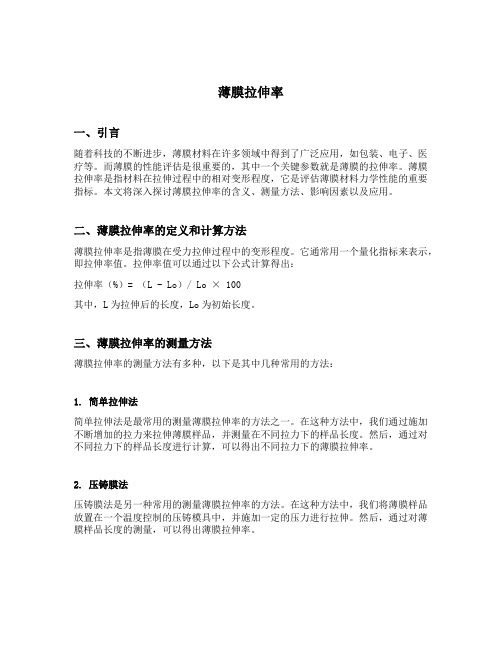
薄膜拉伸率一、引言随着科技的不断进步,薄膜材料在许多领域中得到了广泛应用,如包装、电子、医疗等。
而薄膜的性能评估是很重要的,其中一个关键参数就是薄膜的拉伸率。
薄膜拉伸率是指材料在拉伸过程中的相对变形程度,它是评估薄膜材料力学性能的重要指标。
本文将深入探讨薄膜拉伸率的含义、测量方法、影响因素以及应用。
二、薄膜拉伸率的定义和计算方法薄膜拉伸率是指薄膜在受力拉伸过程中的变形程度。
它通常用一个量化指标来表示,即拉伸率值。
拉伸率值可以通过以下公式计算得出:拉伸率(%)= (L - Lo)/ Lo × 100其中,L为拉伸后的长度,Lo为初始长度。
三、薄膜拉伸率的测量方法薄膜拉伸率的测量方法有多种,以下是其中几种常用的方法:1. 简单拉伸法简单拉伸法是最常用的测量薄膜拉伸率的方法之一。
在这种方法中,我们通过施加不断增加的拉力来拉伸薄膜样品,并测量在不同拉力下的样品长度。
然后,通过对不同拉力下的样品长度进行计算,可以得出不同拉力下的薄膜拉伸率。
2. 压铸膜法压铸膜法是另一种常用的测量薄膜拉伸率的方法。
在这种方法中,我们将薄膜样品放置在一个温度控制的压铸模具中,并施加一定的压力进行拉伸。
然后,通过对薄膜样品长度的测量,可以得出薄膜拉伸率。
3. 拉伸试验机法拉伸试验机法是一种更为精确的测量薄膜拉伸率的方法。
在这种方法中,我们使用专门的拉伸试验机来对薄膜样品施加拉力,并实时测量样品的长度。
通过记录不同拉力下的样品长度,可以计算出薄膜的拉伸率。
四、影响薄膜拉伸率的因素薄膜拉伸率受到许多因素的影响,以下是其中几个主要因素:1. 材料性质材料的物理和化学性质会明显影响薄膜的拉伸率。
例如,材料的硬度、弹性模量以及分子间相互作用力等因素会改变材料的拉伸性能。
2. 温度温度对薄膜的拉伸率有重要影响。
通常情况下,随着温度的升高,薄膜的拉伸率会增加。
这是因为温度升高会导致材料分子的热运动增加,分子间距离增大,从而使材料更容易发生变形。
薄膜力学测试国标
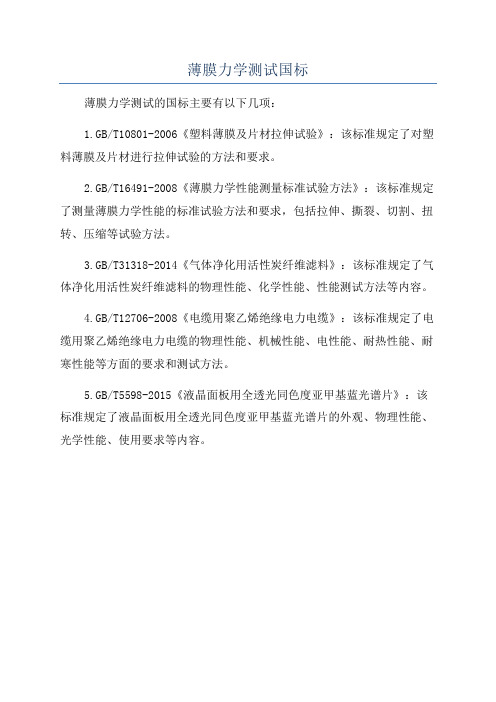
薄膜力学测试国标
薄膜力学测试的国标主要有以下几项:
1.GB/T10801-2006《塑料薄膜及片材拉伸试验》:该标准规定了对塑料薄膜及片材进行拉伸试验的方法和要求。
2.GB/T16491-2008《薄膜力学性能测量标准试验方法》:该标准规定了测量薄膜力学性能的标准试验方法和要求,包括拉伸、撕裂、切割、扭转、压缩等试验方法。
3.GB/T31318-2014《气体净化用活性炭纤维滤料》:该标准规定了气体净化用活性炭纤维滤料的物理性能、化学性能、性能测试方法等内容。
4.GB/T12706-2008《电缆用聚乙烯绝缘电力电缆》:该标准规定了电缆用聚乙烯绝缘电力电缆的物理性能、机械性能、电性能、耐热性能、耐寒性能等方面的要求和测试方法。
5.GB/T5598-2015《液晶面板用全透光同色度亚甲基蓝光谱片》:该标准规定了液晶面板用全透光同色度亚甲基蓝光谱片的外观、物理性能、光学性能、使用要求等内容。
薄膜力学性能评价技术

薄膜力学性能评价技术一、薄膜概述薄膜可定义为用物理、化学等方法,在金属或非金属基底表面形成的一层具有一定厚度的、不同于基体材料性质、且具有一定的强化、防护或特殊功能的覆盖层[1]。
薄膜与基体是不可分割的,薄膜在基体上生长,彼此相互作用,薄膜的一面附着在基体上,并受到约束产生内应力。
附着力和内应力是薄膜极为重要的固有特性[2,3]。
薄膜的制备方法有很多,其中实验室里最常用的方法有物理气相沉积法(PVD)和化学气相沉积法(CVD)。
薄膜按照形成方法分为天然薄膜和人工合成薄膜;按照晶体结构可以分为单晶、多晶以及非晶薄膜[4]。
另外,薄膜从用途上还可以分为光学薄膜、导电薄膜、以及耐磨防腐薄膜等等。
不同用途的薄膜对自身的性能要求不统一,薄膜要达到使用需求,就需要对自身相应的性能进行表征。
在机械工业中,薄膜主要用于改善工件的承载能力或者摩擦学性能。
这些性能与薄膜的力学特性密切相关。
例如增加工件的硬度就可以相应的增加其承载能力,在工件表面沉积一层减磨涂层可以显著改善其摩擦学性能等[5~12]。
薄膜力学性能表征方法有很多,但目前来说这些表征方法还存在一些问题。
首先,对于有基体支撑的薄膜,其表征手段难以消除基体对薄膜性能的影响;无基体支撑的薄膜一是在制备上比较困难,二是其界面结合问题与实际情况也相差甚远,直接影响到薄膜的力学性能的测试[13~18]。
其次,对于大块样品的力学性能检测手段不能直接用来测试接近二维结构的薄膜样品。
本文主要介绍当下较为常用的几种薄膜力学性能检测手段。
二、薄膜硬度的测量硬度的经典定义是材料抵抗另一种较硬材料压入产生永久压痕的能力。
硬度从物理意义上讲是材料本质结合力的度量,它与材料抵抗弹性、塑性变形的能力、拉伸强度、疲劳强度、耐磨性以及残余应力等密切相关,是材料综合力学性能的反映[19,20]。
目前薄膜硬度的测量方法主要有显微硬度和纳米压痕硬度两种。
1.薄膜显微硬度测量方法显微硬度计是一种压入硬度,测量的仪器是显微硬度计,它实际上是一台设有加负荷装置带有目镜测微器的显微镜。
塑料薄膜力学性能检测标准有哪些塑料薄膜力学性能检测方法汇总

塑料薄膜力学性能检测标准有哪些塑料薄膜力学性能检测方法汇总塑料薄膜被广泛应用在各种包装材料当中,不同的包装需求,需要用到不同的材料。
塑料薄膜的力学性能是衡量包装在生产、运输、货架展示、使用等环节对内容物实施保护的基础指标,一般包括:抗拉强度与伸长率、复合膜剥离强度、热合强度、耐穿刺性能、耐冲击性能、耐撕裂性能、抗揉搓性能、耐压性能等指标。
检测橡塑材料检测实验室可各类塑料薄膜力学性能检测服务。
作为第三方检测中心,机构拥有CMA、CNAS检测资质,检测设备齐全、数据科学可靠。
塑料力学性能:拉伸性能塑料的拉伸性能试验包括拉伸强度、拉伸断裂应力、拉伸屈服应力、断裂伸长率等试验。
塑料拉伸性能试验的方法国家标准有几个,适用于不同的塑料拉伸性能试验。
GB/T 1040-1992 《塑料拉伸性能试验方法》一般适用于热塑性、热固性材料,这些材料包括填充和纤维增强的塑料材料以及塑料制品。
适用于厚度大于1 mm的材料。
GB/T13022-1991《塑料薄膜拉伸性能试验方法》是等效采用国际标准ISO1184-1983《塑料薄膜拉伸性能的测定》。
适用于塑料薄膜和厚度小于1mm 的片材,该方法不适用于增强薄膜、微孔片材、微孔膜的拉伸性能测试。
以上两个标准中分别规定了几种不同形状的试样,和拉伸速度,可根据不同产品情况进行选择。
如伸长率较大的材料,不宜采用太宽的试样;硬质材料和半硬质材料可选择较低的速度进行拉伸试验,软质材料选用较高的速度进行拉伸试验等等。
塑料力学性能:撕裂性能撕裂性能一般用来考核塑料薄膜和薄片及其它类似塑料材料抗撕裂的性能。
GB/T 16578-1996《塑料薄膜和薄片耐撕裂性能试验方法裤形撕裂法》是等效采用国际标准ISO 6383-1:1983《塑料-薄膜和薄片-耐撕裂性能的测定第1部分;裤形撕裂法》适用于厚度在1mm以下软质薄膜或片材。
试验方法是将长方形试样在中间预先切开一定长度的切口,像一条裤子。
故名裤形撕裂法。
薄膜技术第五章薄膜材料的评价表征及物性测量ppt课件
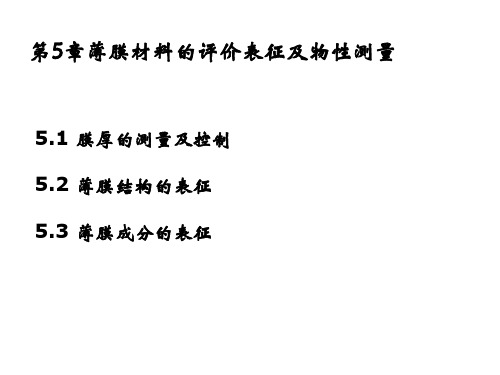
5.3 薄膜成分的表征
X射线光电子能谱(XPS)
X射线光电子能谱法是用特征X射线作入射束,在与样品表面原子相互作
用后,将原子内壳层电子激发电离。被入射特征X射线激发电离的电子称
为光电子。
工作原理:光子能谱从10ev开始延伸,具有这些能量的光子可以穿入固
体内与内壳层电子发生作用。入射光子将整个能量转移给束缚电子,只要
是一种表面离子谱型分析技术。就是用质谱仪对从样品表
面发射出来的正负二次离子进行质量分析的鉴别表面元素。
工作原理:入射离子溅射膜材料,产生的二次离子进入能量
过滤器,然后在质谱仪中被收集。
结构原理:从离子枪产生的一次离子经过质量聚焦、电磁焦
距后入射到样品的系统称为一次离子光学系统。二次离子从
样品发射之后,经过质谱分析和测量称为分析测量系统。用
量的光子。将这一系列的信号分
别接受处理之后,即可得到样品
表层的各种信息。
5.2 薄膜结构的表征------扫描电镜
5.2 薄膜结构的表征------透射电镜
被加速的电子束穿过厚度很薄的样品,并在这一过程中与
样品中的原子点阵发生相互作用,从而产生各种形式的有
关薄膜结构和成分的信息。
基本工作模式:
影像模式和衍射模式。
反射式高能电子衍射(RHEED)
RHEED: AlN
Line profile of AlN <1120>
1、Surface periodicity given by spacing between peaks.
2、Surface quality given by full-width at half-max of peaks.
生弹性散射,反射衍射图像CRT显示,反映出表面的结构信息。
薄膜屈曲力学分析
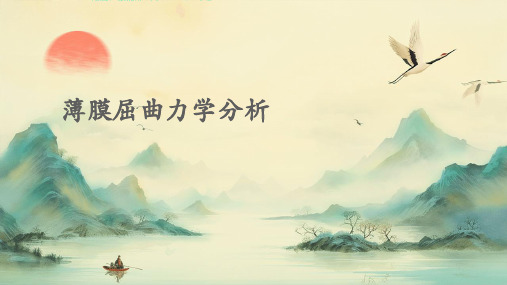
针对薄膜屈曲现象中的复杂现象和机理,开展深入研究,揭示其内在 规律和机制,为解决实际问题提供更加有效的解决方案。
THANKS
感谢观看
能量法具有简单、直观的优点,可以快速得到屈曲临界载荷 和屈曲模态,适用于求解简单形状和边界条件的薄膜屈曲问 题。
有限元法
有限元法是一种数值分析方法,通过 将连续的弹性体离散化为有限个小的 单元,利用这些单元的力学特性来逼 近整个弹性体的行为。
有限元法可以处理复杂的形状和边界 条件,能够得到薄膜屈曲的详细应力 分布和变形情况,适用于求解各种形 状和边界条件的薄膜屈曲问题。
工程应用
薄膜屈曲力学分析在建筑、航空航天、 汽车、包装等领域有广泛应用,是结 构设计的重要依据。
优化设计
通过对薄膜屈曲力学分析,可以优化 结构设计,降低重量、提高刚度、减 少成本等。
安全性能
通过薄膜屈曲力学分析,可以评估结 构的稳定性、承载能力和安全性,确 保结构在使用过程中不会发生屈曲失 效。
薄膜屈曲的应用领域
薄膜屈曲的临界温
度
某些材料在特定温度下会失去稳 定性,导致薄膜发生屈曲。临界 温度与材料的物理性质和化学性 质有关。
03
薄膜屈曲的力学分析方法
能量法
能量法是一种基于能量守恒和能量变分原理的屈曲分析方法 。通过将薄膜视为弹性体,利用弹性力学的基本方程,计算 薄膜在受到外部载荷作用时的屈曲临界载荷和屈曲模态。
06
结论与展望
研究结论
薄膜屈曲现象在不同应用领域中具有广泛的应 用前景,如柔性电子、生物医学和光学器件等
。
当前研究还存在一些挑战和问题,如实验验证的难度 、理论模型的精度和适用范围等,需要进一步深入研
究。
薄膜屈曲力学分析在理论和实验方面均取得了 重要进展,为理解薄膜的力学行为提供了有力 支持。
聚合物薄膜材料力学性能研究

聚合物薄膜材料力学性能研究聚合物薄膜是一种具有广泛应用前景的高分子材料,广泛应用于电子、光学、航空航天、医学、生物等领域。
随着科学技术的不断发展,聚合物薄膜材料力学性能研究成为研究热点。
本文将从聚合物薄膜材料的基本力学性能、材料表征及其应用等方面进行阐述。
一、聚合物薄膜材料的基本力学性能1. 力学性能聚合物薄膜材料是一种柔性的高分子材料,具有较好的弯曲性和拉伸性。
其力学性能主要包括弹性模量、屈服强度、断裂伸长率等。
以家用保鲜膜为例,该膜材料通常具有较高的强度和柔韧性,能够在拉伸和弯曲后能够恢复原状。
其弹性模量通常在1-3 GPa之间,屈服强度为20-70 MPa,断裂伸长率可达到200%-500%。
2. 摩擦学性能由于聚合物薄膜材料表面的微观结构和物理化学性质的影响,其摩擦学性能表现出丰富多样的特性。
对于摩擦学性能,主要包括摩擦系数、磨损率、界面特性、表面粗糙度等。
例如,聚四氟乙烯薄膜材料表面光滑,摩擦系数较低,磨损率小,可用于制造高精度机械部件。
而聚乙烯薄膜材料表面较粗糙,摩擦系数较高,磨损率较大,适用于汽车零件等耐磨性要求不高的领域。
二、聚合物薄膜材料的材料表征1. 形貌表征聚合物薄膜材料的形貌包括膜材料表面形貌和晶体结构形貌两个方面。
对于表面形貌,常用的表征手段主要是原子力显微镜(AFM)和扫描电子显微镜(SEM)。
对于晶体结构形貌,X射线衍射(XRD)和透射电子显微镜(TEM)是常用的表征方法。
2. 化学表征聚合物薄膜材料的表面物理化学性质是影响其应用性能的主要因素之一。
表面化学表征包括原子吸附光谱(XPS)、傅里叶变换红外光谱(FTIR)和拉曼光谱等,可以用于表征材料的元素组成和化学键构成等方面的信息。
3. 动力学表征由于聚合物薄膜材料往往在外界环境下使用,因此动力学表征包括热力学性质、溶解性质、流变学性质等,也是研究其应用性能的重要方面。
热重分析(TGA)、差示扫描量热(DSC)和扫描电镜红外显微光谱(SEM-IR)等分析技术能够有效地评价聚合物薄膜的动力学性能。
薄膜材料的表征方法

紫外-可见光谱法利用紫外-可见光波段的光子能量与材料中价电子的跃迁能量相匹配的特性,通过测量材料对不 同波长光的吸收程度,得到吸收光谱。通过对光谱的分析,可以了解材料的电子结构和分子组成,从而推断材料 的性质和结构。
红外光谱法
总结词
通过测量材料在红外光波段的吸收光谱,分析材料中分子的振动和转动模式。
俄歇电子能谱法
总结词
俄歇电子能谱法是一种高灵敏度、高分辨率的表面分析技术,用于检测薄膜材 料表面的元素组成和化学状态。
详细描述
该方法利用高能电子束轰击薄膜表面,使表面原子发射出俄歇电子,通过测量 俄歇电子的能量分布,可以推断出薄膜表面的元素组成、化学键合状态以及元 素化合物的存在形式。
红外光谱法
详细描述
红外光谱法利用红外光波段的光子能量与材料中分子振动和转动能量相匹配的特性,通过测量材料对 不同波长光的吸收程度,得到吸收光谱。通过对光谱的分析,可以了解材料中分子的振动和转动模式 ,进一步推断材料的结构和性质。
拉曼光谱法
总结词
通过测量材料在拉曼散射过程中的光谱 ,分析材料中分子的振动和旋转模式。
剪切韧性测试
通过测量材料在剪切载荷下的剪切位移或剪切强度,评估材料的 韧性。
感谢您的观看
THANKS
各种类型的薄膜材料。
原子力显微镜
总结词
原子力显微镜是一种高分辨率的表面形貌表征技术,可以用来观察薄膜表面的微观结构 和形貌特征。
详细描述
原子力显微镜利用微悬臂探针在薄膜表面扫描,通过测量探针与薄膜表面之间的相互作 用力,可以实时获得薄膜表面的形貌信息。该方法具有极高的分辨率,能够观察到薄膜
表面的原子级结构,适用于各种类型的薄膜材料。
05 化学性能表征方法
薄膜材料性能表征方法介绍

磁损耗法
01
磁损耗法是通过测量磁场中材 料因磁滞、涡流等效应而产生 的能量损耗来表征材料磁学性 能的方法。
02
磁损耗法通常采用交流磁场进 行测量,能够反映材料的动态 磁特性,如磁损耗角正切值等 。
电学性能表征
电导率测试
总结词
电导率测试是评估薄膜材料导电性能的重要手段,通过测量电流与电压的关系,可以获 得材料的电导率。
详细描述
在电导率测试中,将薄膜材料置于电极之间,施加一定的电压,测量流过材料的电流。 通过计算电流与电压的比值,可以得到材料的电导率。电导率的大小反映了材料导电性
能的优劣。
霍尔效应法
磁畴观察法可以用于研究薄膜材料的磁畴行为、磁反转机制等,有助于理 解材料的磁学性质和应用潜力。
06
环境稳定性表征
耐腐蚀性测试
盐雾试验
将薄膜材料置于盐雾环境中,模拟海洋大气环境,观察其抗腐蚀 性能。
酸碱腐蚀试验
将薄膜材料暴露在酸、碱等腐蚀性环境中,检测其抗腐蚀性能。
电化学腐蚀试验
通过电化学方法检测薄膜材料的耐腐蚀性能,包括电化学阻抗谱 和恒电位腐蚀等。
性能表征的必要性
对薄膜材料进行性能表征有助于了解 其物理、化学和机械性质,从而优化 制备工艺和提高产品质量。
性能表征是评估薄膜材料性能与可靠 性,以及进行材料选择和设计的重要 依据。
02
光学性能表征
透射光谱法
总结词
透射光谱法是通过测量薄膜材料透射光强随波长的变化来表征其光学性能的方法。
详细描述
通过测量划痕阻力来确定材料的硬度和韧性。
塑料包装薄膜的力学性能检测方法及标准
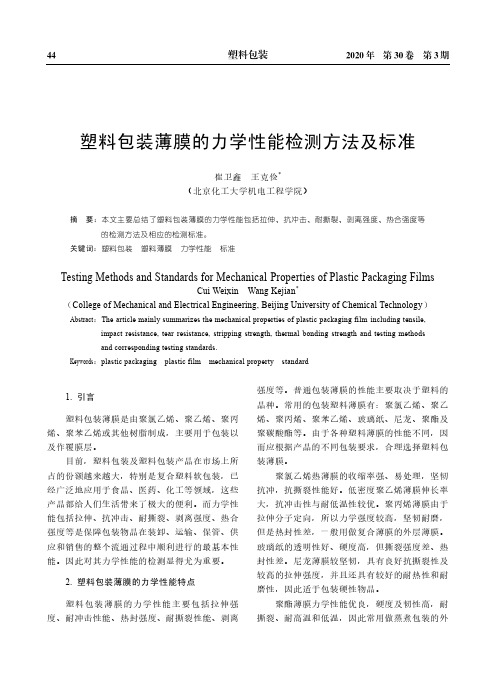
1. 引言塑料包装薄膜是由聚氯乙烯、聚乙烯、聚丙烯、聚苯乙烯或其他树脂制成,主要用于包装以及作覆膜层。
目前,塑料包装及塑料包装产品在市场上所占的份额越来越大,特别是复合塑料软包装,已经广泛地应用于食品、医药、化工等领域,这些产品都给人们生活带来了极大的便利。
而力学性能包括拉伸、抗冲击、耐撕裂、剥离强度、热合强度等是保障包装物品在装卸、运输、保管、供应和销售的整个流通过程中顺利进行的最基本性能。
因此对其力学性能的检测显得尤为重要。
2. 塑料包装薄膜的力学性能特点塑料包装薄膜的力学性能主要包括拉伸强度、耐冲击性能、热封强度、耐撕裂性能、剥离强度等。
普通包装薄膜的性能主要取决于塑料的品种。
常用的包装塑料薄膜有:聚氯乙烯、聚乙烯、聚丙烯、聚苯乙烯、玻璃纸、尼龙、聚酯及聚碳酸酯等。
由于各种塑料薄膜的性能不同,因而应根据产品的不同包装要求,合理选择塑料包装薄膜。
聚氯乙烯热薄膜的收缩率强、易处理,坚韧抗冲,抗撕裂性能好。
低密度聚乙烯薄膜伸长率大,抗冲击性与耐低温性较优。
聚丙烯薄膜由于拉伸分子定向,所以力学强度较高,坚韧耐磨,但是热封性差,一般用做复合薄膜的外层薄膜。
玻璃纸的透明性好、硬度高,但撕裂强度差、热封性差。
尼龙薄膜较坚韧,具有良好抗撕裂性及较高的拉伸强度,并且还具有较好的耐热性和耐磨性,因此适于包装硬性物品。
聚酯薄膜力学性能优良,硬度及韧性高,耐撕裂、耐高温和低温,因此常用做蒸煮包装的外塑料包装薄膜的力学性能检测方法及标准崔卫鑫王克俭*(北京化工大学机电工程学院)摘要:本文主要总结了塑料包装薄膜的力学性能包括拉伸、抗冲击、耐撕裂、剥离强度、热合强度等的检测方法及相应的检测标准。
关键词:塑料包装塑料薄膜力学性能标准Testing Methods and Standards for Mechanical Properties of Plastic Packaging FilmsCui Weixin Wang Kejian*(College of Mechanical and Electrical Engineering, Beijing University of Chemical Technology)Abstract:The article mainly summarizes the mechanical properties of plastic packaging film including tensile, impact resistance, tear resistance, stripping strength, thermal bonding strength and testing methodsand corresponding testing standards.Keywords:plastic packaging plastic film mechanical property standard层材料。
薄膜的制备及其力学性能测试方法

薄膜的制备及其力学性能测试方法摘要:本文介绍了多种薄膜的制备方法和优缺点,同时介绍了纳米压痕和鼓泡法两种力学性能测试方法。
关键词:薄膜制备纳米压痕法鼓泡法力学性能0引言近年来,随着工业的现代化、规模化、产业化,以及高新技术和国防技术的发展,对各种材料表面性能的要求越来越高。
20世纪80年代,现代表面技术被国际科技界誉为最具发展前途的十大技术之一。
薄膜、涂层和表面处理材料的极薄表层的物理、化学、力学性能和材料内部的性能常有很大差异,这些差异在摩擦磨损、物理、化学、机械行为中起着主导作用,如计算机磁盘、光盘等,要求表层不但有优良的电、磁、光性能,而且要求有良好的润滑性、摩擦小、耐磨损、抗化学腐蚀、组织稳定和优良的力学性能。
因此,世界各国都非常重视材料的纳米级表层的物理、化学、机械性能及其检测方法的研究。
[1]同时随着材料设计的微量化、微电子行业集成电路结构的复杂化,传统材料力学性能测试方法已难以满足微米级及更小尺度样品的测试精度,不能够准确评估薄膜材料的强度指标和寿命 ;另外在材料微结构研究领域中, 材料研究尺度逐渐缩小,材料的变形机制表现出与传统块状材料相反的规律[2],所以薄膜的制备及其力学性能测试方法就成了重点。
1.薄膜材料的制备方法1.1化学气相沉积法化学气相沉积是一种材料的合成过程,气相原子或分子被输运到衬底表面附近,在衬底表面发生化学反应,生成与原料化学成分截然不同的薄膜。
化合物蒸汽一般是常温下具有较高蒸汽压的气体,多采用碳氧化物、氧氧化物、卤化物、有机金属化合物等。
化学气相沉积法成膜材料范围广泛,除了碱金属、碱土金属以外,几乎所有的材料均可以成膜,特别适用于绝缘膜、超硬膜等特殊功能膜的沉积。
1.2真空热键法真空蒸镀法是将镀料在真空中加热、蒸发,使蒸发的原子或原子团在温度较低的基底上析出进而形成薄膜。
加热镀料的方法主要是利用湾等高溶点金属通电加热(电阻加热法)和电子束加热法为主。
为了防止高温热源的燃烧和镀料、膜层的氧化,必须把蒸镀室抽成真空。
薄膜的力学测试技术

CHEN Lo ngqing ZHAO Minghao ZHAN G To ng2Y i ( Department of Mechanical Engineering , Hong Kong University of Science and Technology , Hong Kong , China )
MEMS 器件寿命与可靠性的关键 。薄膜材料的力学性
2 压痕( Indentation) 法
压痕法作为一种试验方法用来测量材料的弹性模 [10~12 ] 量始于本世纪 70 年代 。纳米压痕 ( Nanoindenta2
[13~21 ] tion) 技术近年来更得到较广泛的使用 , 该技术的
显著特点在于其极高的力分辨率和位移分辨率 ( 位移 [16 ] 分辨率可达 0. 3 nm , 力分辨率可达 0. 5 μ N) 。能连 续记录加载与卸载期间载荷与位移的变化 , 从而使得 该技术特别适合于薄膜材料力学性能的测量 。纳米压 痕技术可用以测定薄膜的硬度 H 、 弹性模量 E 以及薄 膜的蠕变行为等 , 其理论基础是 Sneddon 结果为
1 引言
各类薄膜在工业中有广泛的应用 , 例如用于机械 部件 、 建筑构件或装饰品的耐氧化 、 防腐蚀和力学性能 改善薄膜等等 。薄膜制造技术是微电子器件和微电光 器件的基础 。近来薄膜制造技术更促进了微电子机械 系统 ( MEMS — — — micro2electro2mechanical system) 的兴起 和发展 。MEMS 器件要求薄膜不仅有很好的电磁光性 质 ,还要求器件中的薄膜结构能够承受机械载荷 、 传递 力和运动 。微电子机械的研制和发展反过来又加速了 薄膜力学性能的研究 。人们日益认识到对薄膜制造工 艺、 显微组织与力学性能之间关系的深入理解是预测 、 改善和充分发挥薄膜材料的包括力学性能在内的各类 性能 , 优 化 MEMS 器 件 设 计 , 扩 大 选 材 范 围 和 提 高
第四章-2薄膜力学性能
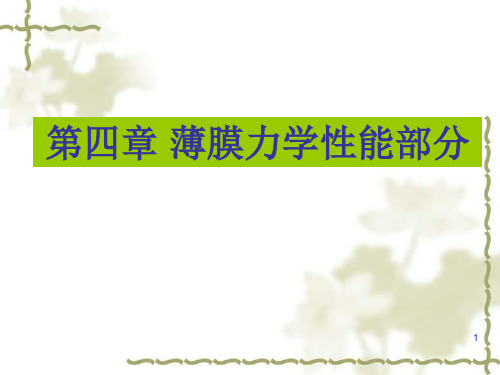
(4.22)
th
E th 1 f
(4.23)
18
薄膜—基底体系中由于晶格常数失配在薄膜中产生的内
应力由Hoffman的晶界松弛模型得到
Ef i 1 f
xa Ef a 1 f
即可算出晶面间距的变化量,再根据弹性力学定律计算出该 方向上的应力数值。
30
X射线衍射法测量残余应力中最常用的方法是 sin2 法, 其基本原理简述如下。 下图为测试的试样表面,图中 1 、 2 和 3 为主应 力方向。由于X射线对物体的穿入能力有限,因而X射 线测量的是物体表层应力(记为 )。因为物体表层 不受外力时即处于平面应力状态,所以 3 0 。设任 意方向应变为 (以 与试样表面法向方向的夹 角表示的方位),按弹性力学原理,有
S dP 2 Er dh A
(4.4)
这里, 为压头的纵向位移, dP dh为试验载荷曲线 h S 的薄膜材料刚度, A 是压头的接触面积。
8
E r 为约化弹性模量
1 Er
1 1
2 f 2 i
(4.5)
Ef
Ei
其中的 E f 、Ei 、 f 、 i 分别为被测薄膜和压头的
Hale Waihona Puke (4.27)式中下标1,2,…,n分别代表各层薄膜的编号, 为残余应 力,其余字符的意义与式(4.26)相同。
22
3. 薄膜厚度与基底可比时的情形
如图所示, t 和 t s 相差不大,采取图中所示的柱坐标 f 系统,显然,不为零的残余应力分量只有 rr r, z 和 r, z , 相应的弹性应变能密度为
塑料薄膜拉伸强力测试标准

塑料薄膜拉伸强力测试标准一、测试原理塑料薄膜拉伸强力测试是通过拉伸试样,测定其在拉伸过程中的强度和性能变化。
本测试方法主要用于评估塑料薄膜在受力情况下的力学性能,包括拉伸强度、弹性模量、屈服点等参数。
二、测试仪器1.拉伸试验机:用于施加拉伸力,控制试样的拉伸速度,并测量试样的变形和受力情况。
2.电子天平:用于称量试样,保证测量准确度。
3.钢尺或标距仪:用于测量试样尺寸,确保测量精度。
4.恒温恒湿箱:用于保持试样环境温度和湿度,以进行环境控制试验。
三、试样准备1.按照相关标准制备塑料薄膜试样,确保试样平整、无气泡、无缺陷。
2.根据测试要求,确定试样尺寸和数量,并标记试样编号。
3.将试样放置在恒温恒湿箱中,调节环境温度和湿度,保持试样状态稳定。
四、实验操作1.将试样放置在拉伸试验机上,调整试样位置,确保有效受力面积。
2.设置拉伸速度、测量范围等参数,启动试验机进行拉伸测试。
3.观察并记录试样在拉伸过程中的受力情况,包括拉伸强度、弹性模量、屈服点等参数。
4.重复进行多次试验,取平均值作为最终结果。
五、数据处理1.根据试验数据,计算各项力学性能参数,如拉伸强度、弹性模量、屈服点等。
2.将数据整理成表格或图表形式,便于分析和比较。
3.根据需要,进行数据分析,评估塑料薄膜在不同条件下的性能差异。
六、实验报告1.报告应包括测试原理、仪器设备、试样准备、实验操作、数据处理等方面的详细描述。
2.报告应包含实验数据的汇总表格和图表,以便对结果进行直观分析和比较。
3.对实验结果进行评估,给出结论性意见和建议。
4.报告应按照规范格式书写,确保信息准确、清晰、完整。
七、注意事项1.在测试过程中,应保证试样不受外界干扰,如气流、振动等影响测试结果的因素应尽量避免。
2.试验机的使用应符合相关规定,避免因操作不当导致设备损坏或测试结果不准确。
3.在处理数据时,应注意数据的准确性和可靠性,避免误导分析结果。
- 1、下载文档前请自行甄别文档内容的完整性,平台不提供额外的编辑、内容补充、找答案等附加服务。
- 2、"仅部分预览"的文档,不可在线预览部分如存在完整性等问题,可反馈申请退款(可完整预览的文档不适用该条件!)。
- 3、如文档侵犯您的权益,请联系客服反馈,我们会尽快为您处理(人工客服工作时间:9:00-18:30)。
薄膜力学性能评价技术一、薄膜概述薄膜可定义为用物理、化学等方法,在金属或非金属基底表面形成的一层具有一定厚度的、不同于基体材料性质、且具有一定的强化、防护或特殊功能的覆盖层[1]。
薄膜与基体是不可分割的,薄膜在基体上生长,彼此相互作用,薄膜的一面附着在基体上,并受到约束产生内应力。
附着力和内应力是薄膜极为重要的固有特性[2,3]。
薄膜的制备方法有很多,其中实验室里最常用的方法有物理气相沉积法(PVD)和化学气相沉积法(CVD)。
薄膜按照形成方法分为天然薄膜和人工合成薄膜;按照晶体结构可以分为单晶、多晶以及非晶薄膜[4]。
另外,薄膜从用途上还可以分为光学薄膜、导电薄膜、以及耐磨防腐薄膜等等。
不同用途的薄膜对自身的性能要求不统一,薄膜要达到使用需求,就需要对自身相应的性能进行表征。
在机械工业中,薄膜主要用于改善工件的承载能力或者摩擦学性能。
这些性能与薄膜的力学特性密切相关。
例如增加工件的硬度就可以相应的增加其承载能力,在工件表面沉积一层减磨涂层可以显著改善其摩擦学性能等[5~12]。
薄膜力学性能表征方法有很多,但目前来说这些表征方法还存在一些问题。
首先,对于有基体支撑的薄膜,其表征手段难以消除基体对薄膜性能的影响;无基体支撑的薄膜一是在制备上比较困难,二是其界面结合问题与实际情况也相差甚远,直接影响到薄膜的力学性能的测试[13~18]。
其次,对于大块样品的力学性能检测手段不能直接用来测试接近二维结构的薄膜样品。
本文主要介绍当下较为常用的几种薄膜力学性能检测手段。
二、薄膜硬度的测量硬度的经典定义是材料抵抗另一种较硬材料压入产生永久压痕的能力。
硬度从物理意义上讲是材料本质结合力的度量,它与材料抵抗弹性、塑性变形的能力、拉伸强度、疲劳强度、耐磨性以及残余应力等密切相关,是材料综合力学性能的反映[19,20]。
目前薄膜硬度的测量方法主要有显微硬度和纳米压痕硬度两种。
1.薄膜显微硬度测量方法显微硬度计是一种压入硬度,测量的仪器是显微硬度计,它实际上是一台设有加负荷装置带有目镜测微器的显微镜。
测试过程中要求试样表面光洁,粗糙度不能过大,压头在一定载荷下压入样品表面,保载一定时间后卸载,在样品表面产生永久压痕,通过显微镜上的测量装置测得压痕对角线长度,计算得出压痕表面积或投影面积,显微硬度值即为载荷与面积的比值[21-25]。
图1 维氏硬度与努氏硬度压头及压痕形貌示意图显微硬度按照压头形状的不同又分为维氏显微硬度和努氏显微硬度。
维氏压头是两相对面夹角为136°的金刚石正四棱锥体;努氏压头为长棱形金刚石压头,两长棱夹角为172. 5°,两短棱夹角为130°。
维氏硬度等于载荷P与压痕表面积F之比,努氏硬度等于载荷P与压痕投影面积A之比,如公式1,2。
维氏硬度HV=P/F=1854.4P/D2 (kg/mm2) 公式1 D——维氏压痕对角线长度平均值努氏硬度HK=P/A=14229P/L2 (kg/mm2 )L——努氏硬度长对角线长度公式2 目前维氏硬度试验方法已经形成国家标准,即为标准硬度。
当维氏硬度的值以kg/mm2为单位时,可以将单位省去,例如HV300,表示其显微硬度为300kg/mm2。
努氏硬度试验方法暂时没有国家标准,但也是一种获得大家认可的硬度测量方式,相比于维氏四棱锥体压头压痕对角线长度D与压人深度h之比D/h=7,努氏压头压痕长对角线长度L与压人深度h之比为L/h =30 , 所以在载荷相同的情况下才,努氏硬度的压头压入深度更浅,更适于较薄的涂层硬度的测定[26~29]。
在薄膜硬度的测试过程中,一般压痕深度为薄膜厚度的1/10到3/10时,我们才认为测得的硬度为薄膜的本征硬度[30,31]。
但是显微硬度测试时一般会得到微米级深度的压痕,深度大于薄膜的厚度,这样以来测得的硬度就不可避免的会受到基体的影响,为薄膜与基体的复合硬度[32-35]。
所以显微硬度大多用来横向定性的对比几种薄膜的硬度大小,一般不认为它是薄膜的本征硬度。
另外,显微硬度的测试过程中,同一压痕,由于测试者的身体状态(如视力)或评定标准的不同,测得的显微硬度值也会有偏差,所以同一批作横向对比的样品最好由同一测试人员在一次实验中完成测试。
为了减少测试误差对硬度评定的影响,在显微硬度测量时一般都需要用硬度标准块对测量值进行校正[36-38]。
2.纳米压痕硬度测试纳米压痕硬度需要在纳米硬度计上测得,如图2,纳米压头在电磁力作用下以一定的速率压入试件表面,通过高精度力、位移传感器(分辨率高达10nN和0.1nm)测量并记录压入深度h和载荷P的关系,根据载荷-深度曲线及接触面积,通过相应的算法可得到材料的压痕硬度以及其它多种力学性能[39,40]。
图2 纳米压痕硬度计工作示意图纳米压痕法最常用的的压头是尖三棱锥形金刚石玻氏(Berkovich)压头,得到加载-卸载曲线,如图3。
玻氏压头每个面都是正三角形,三棱锥形状比四棱锥尖锐,更能反映材料的塑性性能。
卸载曲线开始的部分为材料的弹性恢复阶段,形状接近于直线,h r为卸载曲线最大实验力时切线与深度坐标轴的交点[41-43]。
在采用纳米压入技术测量薄膜硬度时,硬度通常被定义为压头下方的平均应力,硬度数值H通过公式3计算:压痕硬度H=P max/A 公式3式中,H为硬度,A为压痕面积的投影,是压入接触深度hc的函数,不同形状压头的A的表达式不同。
图3 纳米压痕硬度标准压头以及测试曲线示意图a.加载曲线b.卸载曲线c.曲线b在Fmax处切线hp.卸载后残余压痕深度当压头为维氏压头时,A=24.50×hc2当压头为玻氏压头时,A=23.96×hc2上式中hc为压头与试样接触深度,可由公式4计算:公式4公式4中,ε取决于压头的形状,玻氏和维氏压头均为3/4。
hr的确定有两种方法,一是在实验力-压痕深度曲线上,卸载曲线切线与深度轴的交点即为hr,如图3。
此法假设卸载曲线的初始阶段是线性的,较为简便常用。
另一种方法称为幂指数法,事实上卸载曲线初始阶段是非线性的,采用简单的幂指数关系,如公式5:公式5公式5中K为常数,m为与压头几何形状有关的指数,hp为残余压痕深度[44]。
根据卸载曲线不同,通常取卸载曲线的50%以上或80%以上部分,用最小二乘法拟合成幂指数函数。
该函数在最大实验力时的切线和位移坐标轴的截距即为hr。
纳米压痕法可以获得的其它材料力学性能参数卸载刚度刚度是材料抵抗弹性变形的能力,它的物理意义是引起材料单位形变所需要的载荷。
图4为典型的弹塑性变形材料的压头载荷-压痕曲线[45]。
该曲线由加载曲线和卸载曲线组成。
卸载曲线在最大压力深度处的斜率包含的材料弹性的信息,称为卸载刚度S。
公式6图4 典型纳米压入载荷-位移(p-h)曲线压痕模量Err压痕模量Err可通过计算卸载曲线切线斜率得出[46~48],如公式11,12:公式11公式12Er为约化弹性模量,又叫接触压痕弹性模量Ei为压头材料弹性模量(金刚石为1.14×106N/mm2)νs为试样泊松比νi为压头材料泊松比(金刚石为0.07)C接触柔度,接触刚度的倒数,它的值为最大实验力时卸载曲线dh/dF。
压痕模量与材料的杨氏模量具有可比性,有文献[49][50]将其看作为材料的弹性模量,但压痕若出现突起或凹陷的现象,则压痕模量和杨氏模量有明显不同。
压痕蠕变Crr压痕蠕变是指恒定实验力下压痕深度的相对变化量。
如公式13:公式13h1开始保持实验力时的压痕深度h2结束保持实验力时的压恨深度压痕松弛Rrr压痕松弛是指在保持恒定的压痕深度时实验力的相对变化量。
如公式14:公式14F1压痕深度达到恒定时的实验力F2压痕深度保持恒定一段时间后的实验力纳米压痕法精度高,压人深度小,基体的影响可以忽略,可以测量很薄的膜的硬度。
它把压痕对角线的测量转化为压头压入位移的测量,无须光学观察,用计算机进行数据收集,避免人为误差,与显微硬度相比具有一定的优势。
然而由于纳米压入仪对测试环境有严格要求,样品表面粗糙度要限制得很小,且仪器价格昂贵,因而它的使用受到一定限制。
另外,在纳米压痕硬度测试过程中会存在尺寸效应的问题,即在压入深度很小的时侯,随着压入深度的减小,测得的硬度值会相应的增大[51]。
尺寸效应使测量值数据间有一定的漂移和不确定性,适当加大测量深度可以减小这种影响。
三、薄膜摩擦学性能的表征摩擦学是研究相对运动的作用表面间的摩擦、润滑和磨损,以及三者间相互关系的理论与应用的一门边缘。
摩擦磨损是一个极其复杂的过程,他不仅与两相运动的表面有关,而是与整个摩擦学系统有关,对整个系统有很大的依赖性。
摩擦磨损试验可根据实验条件和目的分为两大类:第一类是现场实物摩擦磨损试验;第二类是实验室摩擦磨损模拟试验。
第一类是摩擦磨损试验是在实际使用条件下进行的,这种实验的真实性和可靠性较好,但机器零件在实际使用中的磨损一般较慢,因而需要较长的周期才能得到实验结果,而且磨损量还需要可靠和精确的仪器测量。
机器在不同工况下运行,由于运行的条件不固定,因而所取得的测试数据重现性和规律性较差,不便研究摩擦磨损的规律性,也难以进行单项因素对摩擦磨损影响的观察。
第二类试验方法不需要进行整机试验,只需要模拟机器零件和部件在实际使用条件下进行试验,同时可改变各种参数来分别测定其对摩擦磨损的影响,而且测试数据重现性和规律性较好,便于进行对比分析,还可以使用条件,缩短使用周期,减少试验费用,可用来重复地对大量的试件进行实验。
但这类试验方法所得到的结果,不能完全反映实际的复杂的摩擦磨损状况,往往不能直接应用,只有精确的模拟试验得到的结果才能有较好的实用性。
在实验室条件下,如何确定影响摩擦磨损的主要因素也是较为复杂的问题,因为摩擦、磨损本身就是复杂的,而且影响它的因素也较多。
稍许改变某一因素,可导致磨损量成倍的增加,即使在同一时间、同一因素对不同的磨损形式产生的影响也不同,而且各因素有时相互关联的,有很难把它们完全区分开来。
材料的耐磨性与材料的强度、硬度不同,它不是材料的固有特性,而是在一定条件下物理和化学特性的综合表现,若条件改变材料的耐磨性也随之改变,故材料的耐磨性是相对的,有条件的[52]。
目前笔者接触的薄膜材料的摩擦学性能表征一般在实验室中进行,球-盘摩擦实验可以较为全面的对样品摩擦学特性进行表征,划痕法也可以获得材料表面的摩擦系数(磨擦副为金刚石)。
1.划痕法表征样品摩擦系数图5 典型纳米划痕实验图解1划痕前表面轮廓线 2划痕后表面轮廓线3切向力 4划痕曲线 5法向力如图5,在纳米划痕试验中,用金刚石压头在薄膜表面上进行划痕试验,深度敏感系统记录压头的垂直位移,可以得出压头进入薄膜深度随前进位移的变化曲线,划痕过程结束后,用压头在20μN载荷作用下扫描划痕后表面形貌(Post-scanning),得到划痕残留深度。