装配线平衡实例
生产线平衡率实例

Nt
=
11.35 mins/台 4.2 mins/台
=
2.702,
or 3
(5)根据排程排产
2
1
1
A
B
G
1.4
H
C
D
E
F
3.25
1.2
.5
1
任务 A C D B E F G H
工位 1
工位2
后续任务 6 4 3 2 2 1 1 0
时间 (Mins) 2
3.25 1.2 1 0.5 1 1 1.4
工位 3
流水线平衡
1.4 H
F 1
任务
A C D B E F G H
工位2
后续任务
6 4 3 2 2 1 1 0
时间 (Mins) 2
3.25 1.2 1 0.5 1 1 1.4
工位 3
C (4.2-3.25)=0.95
Idle=0.2
流水线平衡
2
1
1
A
B
G
C
D
E
3.25
1.2
.5
工位 1
A (4.2-2=2.2) B (2.2-1=1.2) G (1.2-1= 0.2)
Idle=0.2
Idle =0.95
2
1
1
A
B
G
C
D
E
3.25
1.2
.5
工位 1
A (4.2-2=2.2) B (2.2-1=1.2) G (1.2-1=0.2)
流水线平衡
1.4 H
F 1
任务 A C D B E F G H
工位2
后续任务 6 4 3 2 2 1 1 0
【推荐】装配生产线平衡的改善
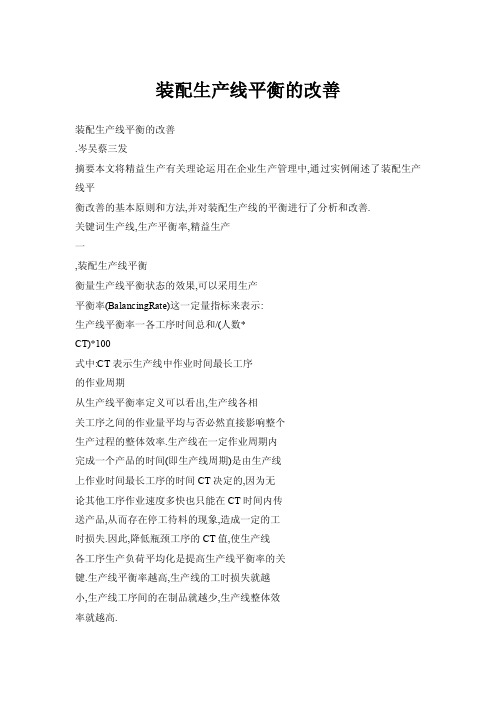
装配生产线平衡的改善装配生产线平衡的改善.岑吴蔡三发摘要本文将精益生产有关理论运用在企业生产管理中,通过实例阐述了装配生产线平衡改善的基本原则和方法,并对装配生产线的平衡进行了分析和改善.关键词生产线,生产平衡率,精益生产一,装配生产线平衡衡量生产线平衡状态的效果,可以采用生产平衡率(BalancingRate)这一定量指标来表示:生产线平衡率一各工序时间总和/(人数*CT)*100式中:CT表示生产线中作业时间最长工序的作业周期从生产线平衡率定义可以看出,生产线各相关工序之间的作业量平均与否必然直接影响整个生产过程的整体效率.生产线在一定作业周期内完成一个产品的时间(即生产线周期)是由生产线上作业时间最长工序的时间CT决定的,因为无论其他工序作业速度多快也只能在CT时间内传送产品,从而存在停工待料的现象,造成一定的工时损失.因此,降低瓶颈工序的CT值,使生产线各工序生产负荷平均化是提高生产线平衡率的关键.生产线平衡率越高,生产线的工时损失就越小,生产线工序间的在制品就越少,生产线整体效率就越高.装配线改善的基本原则和方法应该是:对瓶颈工序进行作业改善,如增加工装,工装自动化等;将瓶颈工序的作业内容分担给其它工序;增加作业人员,只要平衡率提高,人均产量也会提高, 单位产品成本会随之下降;合并相关工序,重新进行工序排布;分解作业时间较短的工序,将该工序拆分后并入其它工序;以顾客的需求CT为接近目标.装配生产线的平衡率分析和改善是装配型企业生产管理过程中的一项十分重要的工作,涉及到生产效率的提高,生产成本的降低,消除浪费, 准时化生产等生产指标的达成和不断改进. 二,精益生产精益生产的基本原理是:不断改进;消除对资源的浪费:协力工作;沟通.不断改进是精益生产的指导思想;消除浪费是精益生产的目标;协力工作和沟通是实现精益生产的保证.精益生产的主要内容包括工厂现场管理,新产品开发,与用户的关系,与供应厂家的关系等方面.对于现场管理,主要内容为如何通过看板系统来组织生产过程,实现准时化生产(JIT).准时化生产是指在顾客需要的时候,按顾客需要的量和产品品质,提供顾客需要的产品.准时化生产系统由一系列工具和方法构成:平衡生产周期;持续改进;一个流生产;单元生产;价值流分析;方法研究;拉动式生产;可视化管理;全面生产维护;快速换模.三,实例分析本文以某装配生产线(FIAT出风口装配线)为例,通过精益生产有关理论的运用,对该装配生产线的平衡进行分析和改进,取得了较好的效果.1.现状分析FIAT出风口装配线平面流程现状示意图如图1所示:园圈圈圉囡图圈圉曰图1装配线平面流程现状示意图FIAT出风口装配线一个组的作业密度及平作者简介:岑吴,同济大学经济与管理学院硕士研究生;蔡三发,同济大学经济与管理学院讲师.16《上海管理科学}2005年第5期衡分析如表1和图2所示:2.改善的对策和实施通过以上分析,可以提出该装配线改善的目标为:尽量接近顾客的CT一9.0秒;减少人员;提高平衡率;提高总产量和人均产量;降低生产成本.表1作业密度及平衡分析表工序号123456789装组装弹贴海工序名称装叶片装连杆装胶垫抹油打螺丝总装合件簧片绵垫作业5.693.505.184.505.144.867.386.983.50时间(秒)操作人数111111111CT(cycletime)一PT(pitchtime)一7.38s生产线平衡率一各工序时间总和/(人数*厘鲁平衡分析一厂1厂_]——..LIf.....—JLIrlIlr工序图2作业密度及平衡分析图因此,实施了如下工序作业改善对策表,见表2:3.改善前后对比经过改善,装配生产线平衡率得到了提高,见图3:表3有关数据也可以看出改善后和改善前对比的差距:CT)*100%一71.70%表2工序作业改善对策表NO工序作业时间改善措施PTS预置时间目的与效果1装叶片5.692装连杆3.5O合并为一道工序9.1减少一道工序3装组合件5.184装胶垫4.5O合并为一道工序9.6减少一道工序5装弹簧片5.14合并为一道工序9.8改变作业周期6贴海绵垫4.86增加作业内容,7抹油7.38将8的部分作业调整过来9.6平衡工序时间8打螺丝6.98与9合并8.26合并工序9总装3.5O取消省0.5人说明生产线由原来17人两组,改为15人=组,由此带来生产线平衡率,综合产能及人均产量上的提高厘蓝平衡分析姆图3改善后作业密度及平衡分析图表3改善前后的有关数据对比表项目改善前改善后变化量变化率人员数1715—2—12总产量870pcs/h98lpcs/h11113%人均产量51.265.414.228生产线平衡率71.7O%94.61%22.9%31.10%单件工时消耗70.3s55s——15s一21cycle7.389.80参考文献邱灿华,蔡三发,粟山.运作管理[M].上海;同济大学出版社,2004.刘胜军.精益生产方式现场IEEM].深圳:海天出版社,2002.周密.IE方法实战精解I-M].广州:广东经济出版社,2002.吴杰明.应用FOG方法提高生产线平衡率浅析EJ].上海电力学院,2004,6:49~53.ImprovementofAssemblyLineBalancingCenHaoCaiSanfaAbstract:Thispaperexplainstheapplicationsoflean productionknowledgeinenterpriseproductionmanagement, advancesthebasicprincipleandmethodofassemblylinehal—ancing,analysisandimprovementofoneassemblylinebal—ancing.Keywords:assemblyline;balancingrate;leanpro—duction17?。
装配线平衡实例

作业
作业时间(s)
剩余时间
(s)
可安排的
紧后作业
紧后作业最多的作业
时间最长的作业
1
A
225
7空闲
无
2
D
250
2空闲
无
3
B
55
197
C、E
C、E
E
E
75
122
C、H、I
C
F、G、H、I
C
45
77
F、G、H、I
F、G、H、I
F
60
17空闲
无
4
G
60
192
H、I
H、I
H
60
132
I
I
60
72
J
J
40
作业
时间(秒)
描述
必须提前的作业
A
45
安装后轴支架,拧紧4个螺母
—
B
11
插入后轴
A
C
9
拧紧后轴支架螺栓
B
D
50
安装前轴,用手拧紧4个螺母
—
E
15
拧紧前轴螺栓
D
F
12
安装1#后车轮,拧紧轮轴盖
C
G
12
安装2#后车轮,拧紧轮轴盖
C
H
12
安装1#前车轮,拧紧轮轴盖
E
I
12
安装2#前车轮,拧紧轮轴盖
E
J
8
安装前轴上的车把手,拧紧螺栓和螺钉
C
H
12
安装1#前车轮,拧紧轮轴盖
E
I
12
安装2#前车轮,拧紧轮轴盖
E
一个MOD法在装配线平衡中应用案例

一个MOD法在装配线平衡中应用案例装配线平衡是指在保证生产效率和质量的前提下,通过合理的工作任务分配和工作站布局,使得每个工作站的工作时间基本相等,避免了一些工作站工作时间过长,造成生产线整体效率低下的问题。
其中,MOD法(Method of Difference)是一种常用的装配线平衡方法,它通过对比两个工作站的工作任务,并根据差异量来决定任务分配。
下面将介绍一个在装配线平衡中应用MOD法的案例。
假设有一个汽车零部件生产线,其中有4个工作站,每个工作站的工作内容如下:工作站1:装配发动机零部件A(每个零部件的操作时间为6分钟)工作站2:装配发动机零部件B(每个零部件的操作时间为5分钟)工作站3:装配发动机零部件C(每个零部件的操作时间为4分钟)工作站4:装配发动机零部件D(每个零部件的操作时间为3分钟)现在需要平衡这条生产线,使得每个工作站的工作时间基本相等。
下面是使用MOD法进行任务分配的步骤:1.计算工作站间的工作时间差异量首先,计算每个工作站的工作时间。
工作站1的工作时间为6分钟,工作站2的工作时间为5分钟,工作站3的工作时间为4分钟,工作站4的工作时间为3分钟。
然后,计算相邻工作站之间的工作时间差异量:-工作站1和工作站2的差异量为6分钟-5分钟=1分钟-工作站2和工作站3的差异量为5分钟-4分钟=1分钟-工作站3和工作站4的差异量为4分钟-3分钟=1分钟2.选择差异量最大的相邻工作站根据计算所得的差异量,选择差异量最大的相邻工作站。
在这个案例中,差异量最大的是工作站1和工作站2,差异量为1分钟。
3.分配任务至差异量最大的相邻工作站将工作站1的一个任务分配给工作站2,使得它们的工作时间相等化。
此时,工作站1有5个任务,工作站2有6个任务。
4.重新计算工作站间的工作时间差异量分配任务后,重新计算工作站间的工作时间差异量:-工作站1和工作站2的差异量为5分钟-5分钟=0分钟-工作站2和工作站3的差异量为4分钟-4分钟=0分钟-工作站3和工作站4的差异量为4分钟-3分钟=1分钟5.如果存在差异量不为0的相邻工作站,返回步骤2,否则结束。
装配线平衡问题分析

装配线平衡问题分析一、引言装配线平衡问题是指在生产流水线上,各个工序之间的任务分配不均衡,导致生产效率下降的情况。
这种问题在生产制造领域是非常常见的,解决装配线平衡问题对于提高生产效率和降低生产成本具有重要意义。
本文将从生产流水线的基本概念、装配线平衡的重要性和影响因素、以及常见的解决方法等方面进行分析和探讨。
二、生产流水线的基本概念生产流水线是指将生产过程按照一定的顺序划分为若干个工序,并将每个工序之间形成一个流水线的生产模式。
生产流水线的设计和优化可以大大提高生产效率和质量稳定性。
三、装配线平衡的重要性和影响因素装配线平衡是指在流水线上均衡地分配工作任务,以达到最大化生产效率的目标。
装配线平衡的重要性有以下几个方面:1. 提高生产效率:装配线平衡可以避免生产过程中的工序瓶颈和空闲,提高生产效率,减少生产周期。
2. 降低生产成本:通过合理的装配线平衡,可以避免不必要的等待和重复工作,减少能耗和人力成本。
3. 提高产品质量稳定性:均衡的装配线可以减少产品在不同工序间的拖延和等待,从而提高产品质量的稳定性和可控性。
装配线平衡受到以下几个主要因素的影响:1. 工序时间:不同工序的处理时间不同,可能会形成工序之间的瓶颈。
合理安排工序时间,可以减少瓶颈,提高生产效率。
2. 任务分配:将任务均衡地分配到各个工序中,避免某个工序任务过重或过轻,从而实现装配线的平衡。
3. 人力资源:充足的人力资源可以保证各个工序的顺利进行,缺乏人力资源会影响装配线平衡。
四、装配线平衡问题的解决方法为了解决装配线平衡问题,可以采取以下几种方法:1. 任务重分配:对不均衡的工序进行任务重分配,将任务均衡地分配到各个工序中。
这需要根据各个工序的处理能力和任务需求进行合理的评估和调整。
2. 工序优化:通过技术手段和工艺改进,缩短处理时间,提高工序的效率。
这可以通过引入自动化设备、改进工艺流程等方式来实现。
3. 人力资源管理:合理配置人力资源,确保各个工序有足够的人手,避免产生人力资源不足的问题。
装配线平衡模型

§7综合举例
例 求解非线性方程组
其LINGO代码如下:
model:
xA2+yA2=2;
2*xA2+x+yA2+y=4;
end
计算的部分结果为
Feasible solution found at iteration: 0
Variable Value
X
Y
例 装配线平衡模型 一条装配线含有一系列的工作站, 在最终产品的加工过程中每个 工作站执行一种或几种特定的任务。装配线周期是指所有工作站完成分配给它们各自的任 务所化费时间中的最大值。平衡装配线的目标是为每个工作站分配加工任务,尽可能使每 个工作站执行相同数量的任务,其最终标准是装配线周期最短。不适当的平衡装配线将会 产生瓶颈——有较少任务的工作站将被迫等待其前面分配了较多任务的工作站。
这样我们把TSP转化成了一个混合整数线性规划问题。
显然,当城市个数较大(大于30)时,该混合整数线性规划问题的规模会很大,从而
给求解带来很大问题。TSP已被证明是NP难问题,目前还没有发现多项式时间的算法。对于小规模问题,我们求解这个混合整数线性规划问题的方式还是有效的。
TSP是 一个重要的组合优化问题,除了有直观的应用外,许多其它看似无联系的优化问 题也可转化为TSP例如:
钢铁工业是国家工业的基础之一,铁矿是钢铁工业的主要原料基地。许多现代化铁矿 是露天开采的,它的生产主要是由电动铲车(以下简称电铲)装车、电动轮自卸卡车(以 下简称卡车) 运输来完成。 提高这些大型设备的利用率是增加露天矿经济效益的首要任务。
装配生产线改善案例

装配生产线改善案例01.装配部部门简介装配部,作为车模生产的最后一道工序,肩负着车模成品的组装和包装的全部生产过程。
装配部现有六条生产线和一条样办组装线。
常用的设备有:钻床,电批,手啤机,风批,烙铁,高周波,封口机等。
为了更好的完成生产任务,装配部引入了精益生产工艺流程。
精益生产是目前工业界公认最佳的一种生产组织体系和方式。
通过合理的排拉,达到合理生产,提高效率和质量的目的。
02.例子(一):DCP1/25货车,按流程标准可分成:车身半品( 10人),车身组合(16人),内座组合(4人),车底组合(11人),成品组装(7人)和包装(9人)共六个小组(57人)来完成。
每个小组会有一次或以上的自检。
(二):YTB002 1/42莱茵之星单层客车,按流程标准可分成:内座组装(12人),车底组装(9人),车身组装(20人),成品包装(6人)共四个小组(47人)来完成,在其中也加入了多次的自检。
03.装配车间平面分布图04.装配生产线平衡改善过程•了解产品组装工艺•对U型拉进行工时测定,得到统计数据•从统计数据分析U型拉平衡状况•识别瓶颈工位,找出不平衡的原因•运用平衡改善法则(ECRS法则)、动作经济原则等方法制定改善方案•将改善方案告知组长或装配主任,实施现场改善•改善效果分析总结05.平衡改善法则-ECRS法则简介以上ECRS法则,具体可通过下列图片来说明生产中如何运用改善:06.装配线平衡典型案例•U拉序号:U24、U25•产品编号:53072(太空车)•组装部分:成品和包装改善前各工位组装工艺此款产品的装配线由U25、U24两个U型拉组成,工位分布如下图所示:平衡率=各工序的作业时间/(瓶颈工位时间*人数)=(9.5+11+6+13+8+8+8+6+9+10+6+8)/(13*12)=65.71% 平衡损失率=1-平衡率=34.29%改善前装配线工位平衡图改善措施从统计数据分析这条装配线,可以发现瓶颈工位是工位4。
基于改进遗传算法的汽车装配生产线平衡问题

汇报人:2023-12-01contents •引言•汽车装配生产线平衡问题概述•基于遗传算法的汽车装配生产线平衡问题求解•基于改进遗传算法的汽车装配生产线平衡问题求解目录contents•基于改进遗传算法的汽车装配生产线平衡问题的应用案例目录•结论与展望•参考文献01引言03基于改进遗传算法的解决方案01汽车装配生产线平衡问题的重要性02传统解决方法的局限性研究背景与意义国内外研究现状存在的问题和不足研究现状与问题研究内容与方法研究内容介绍本研究的主题和主要研究内容,包括对汽车装配生产线平衡问题的定义、特点和分类,以及基于改进遗传算法的解决方案的详细阐述。
研究方法介绍本研究采用的研究方法和技术路线,包括对遗传算法的改进、数据采集和分析、模型构建和验证等环节的详细说明。
02汽车装配生产线平衡问题概述定义约束条件生产线平衡问题的定义与约束条件数学模型变量与约束目标函数生产线平衡问题的数学模型生产线平衡问题是一个NP难问题,传统的求解方法包括启发式算法、分枝定界法、遗传算法等。
遗传算法作为一种高效的优化算法,在求解复杂、非线性、离散的生产线平衡问题时具有优势。
遗传算法遗传算法是一种基于生物进化原理的优化算法,通过模拟自然选择和遗传机制,不断迭代优化种群中的个体,以获得最优解。
在求解生产线平衡问题时,遗传算法可以针对不同的生产线类型、规模和约束条件,设计适应的编码方式、适应度函数和遗传操作方法。
求解方法生产线平衡问题的求解方法VS03基于遗传算法的汽车装配生产线平衡问题求解1)初始化种群;2)计算适应度函数;3)选择操作;4)交叉操作;5)变异操作;6)迭代更新种群直至达到终止条件。
遗传算法的基本原理与实现过程遗传算法的实现过程遗传算法的基本原理基于遗传算法的求解流程1)定义问题参数和约束条件;2)构建染色体编码方案;3)初始化种群;4)计算适应度函数;5)选择、交叉、变异操作;6)更新种群直至达到终止条件;7)输出最优解。
车身装配生产线平衡改善案例
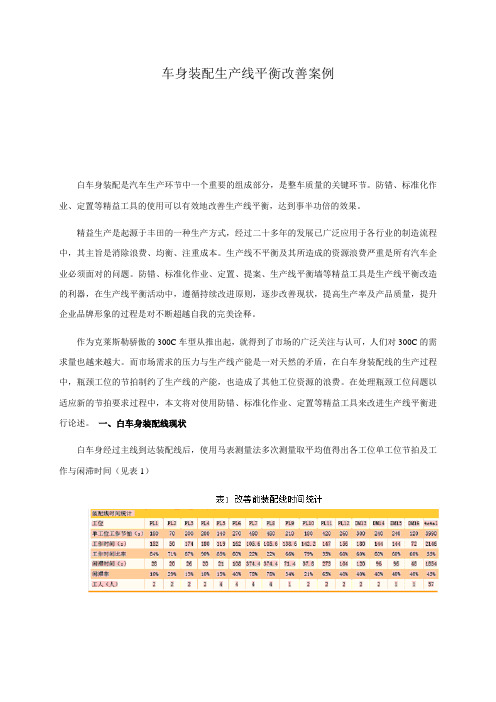
车身装配生产线平衡改善案例白车身装配是汽车生产环节中一个重要的组成部分,是整车质量的关键环节。
防错、标准化作业、定置等精益工具的使用可以有效地改善生产线平衡,达到事半功倍的效果。
精益生产是起源于丰田的一种生产方式,经过二十多年的发展已广泛应用于各行业的制造流程中,其主旨是消除浪费、均衡、注重成本。
生产线不平衡及其所造成的资源浪费严重是所有汽车企业必须面对的问题。
防错、标准化作业、定置、提案、生产线平衡墙等精益工具是生产线平衡改造的利器,在生产线平衡活动中,遵循持续改进原则,逐步改善现状,提高生产率及产品质量,提升企业品牌形象的过程是对不断超越自我的完美诠释。
作为克莱斯勒骄傲的300C车型从推出起,就得到了市场的广泛关注与认可,人们对300C的需求量也越来越大。
而市场需求的压力与生产线产能是一对天然的矛盾,在白车身装配线的生产过程中,瓶颈工位的节拍制约了生产线的产能,也造成了其他工位资源的浪费。
在处理瓶颈工位问题以适应新的节拍要求过程中,本文将对使用防错、标准化作业、定置等精益工具来改进生产线平衡进行论述。
一、白车身装配线现状白车身经过主线到达装配线后,使用马表测量法多次测量取平均值得出各工位单工位节拍及工作与闲滞时间(见表1)图1中,最长工序时间(480s)决定装配线节拍,装配线整体节拍为7.5件/h,8h单班日产量为60件。
图1 工作与闲滞时间二、瓶颈分析1、工序分析:BPT1(Basic Pitch Time):工序平均所持加工净值(不含浮余率)。
BPT2:人均所持加工净值(不含浮余率)。
BPT1=总加工时间净值/工序数=(PL1+PL3+PL4+PL4+PL5+PL6+PL7+PL8+PL9+PL10+PL11+ PL12+ DM13+DM14+DM15+DM16)/16=3990/16=249.375s。
BPT2=总加工时间净值/作业人员人数=3990/37=107.9s。
2、制成作业平均时间表□按照工序顺序,记入必要事项:工序号码、工序名称、PT线、加工时间净值。
现代制造业中的装配线平衡研究

现代制造业中的装配线平衡研究在现代制造业中,装配线是非常常见的一种工艺,可以大幅降低生产成本,提高生产效率。
而装配线平衡则是一种优化工具,能够最大程度地利用每一秒钟,从而增加生产率并降低生产成本。
一. 装配线平衡的定义及作用装配线平衡是指在满足生产要求的情况下,使每个工作站的工作时间尽可能接近,以达到生产效率最大化的一种工艺。
它的作用包括:1. 提高生产效率平衡装配线可以明显提高生产效率,尤其在大规模生产时效果更为明显。
通过优化流程,减少废品和重复工作,可以加速生产流程,从而提高产品质量以及生产效率。
2. 降低生产成本装配线平衡可以优化流程并避免重复工作,从而减少人力成本和浪费。
通过合理的调配生产线,可以降低设备维修费用和耗损率。
因此,在生产大规模产品时,使用装配线平衡可以极大地降低生产成本。
二. 装配线平衡的优化步骤优化装配线平衡并不是一件容易的事情,需要经过一系列的步骤才能够达到最佳效果。
1. 测量并收集数据首先需要测量工作站的工作时间,并记录每个工作站的工作台数和工作内容。
通过这些数据,可以客观地分析每个工作站的生产效率以及优化的空间。
2. 设计模型其次需要使用一些常用的工作模型,比如Gantt图,以确定整个生产线的工作流程和时间分配。
通过绘制图表,可以更加清晰地了解各个工作站之间的关系。
3. 优化法则优化法则是一组用于平衡装配线的技巧和规则,可以用于分析和优化流程。
一些常用的法则包括最小处理时间法、虚构工作站法、双线平衡法、轮换法等。
这些法则可以根据实际情况进行选用,并适当变更以优化生产线效率。
4. 进行模拟测试在对生产线进行优化前,需要进行模拟测试以确定最优解,根据测试结果判断是否需要继续调整。
通过模拟测试,可以减少实验成本以及确保最佳效果。
5. 实施和监测最后就是进行实施和监测了。
在进行实施前需要进行详细的工作说明书编制和工人培训,对于常规工人需要满足进行操作要求,并了解当前的工艺流程。
实验二装配生产线平衡实验

实验二装配生产线平衡实验一、实验任务1.对玩具小车装配过程进行装配生产线平衡;2.在实验室生产模拟系统上模拟玩具小车装配生产线运行过程,并分析平衡效果。
二、实验目的及训练要点1.训练学生合理设计和实施一个工序平衡的生产线。
2.学会装配线平衡的基本方法和步骤。
3.在实验室生产线模拟系统上进行实际模拟,检验数据的准确性,同时掌握生产线模拟系统的操作过程。
另外,训练学生组织活动的能力。
三、实验原理1.定义工作站——操作者为了完成指定的装配作业在装配线上的工作位置。
有时候也把工作站称为“工位”或“工序”。
作业单元——作业的最小单元,一般情况下,这些操作单元不能再分。
对于很复杂的装配作业,例如汽车装配,作业单元如果划分得过细,会使整个平衡过程十分复杂,划分的过粗,又会使平衡难以很好进行,因此,必须寻找一个最佳尺度。
作业单元时间——完成某一个作业单元所用的标准时间,一般是经过工作研究和作业测定的操作时间。
节拍或周期——流水线上生产出一个产品所需要的时间,即相当于从装配线上出来成品的时间间隔。
工作站时间——完成分配给一个工作站的全部作业单元所需要的时间。
工作站空闲时间——在节拍内完成分配给一个工位的全部作业后所剩余的时间,它等于节拍减去工作站时间。
总作业时间——完成整个产品装配过程所需要时间,它等于所有作业元素时间之和。
总空闲时间——整个装配过程汇中,所有工作站空闲时间之和。
平衡效率——是衡量装配线上各工作站间均衡程度好与差的指标。
后续作业——从该作业单元出发沿着装配优先顺序图上所有路径前进直道终点所遇到的所有作业。
先行作业——从该作业开始逆路径方向而行直至起点所遇到的所有作业。
2.流水线平衡的基本步骤(1)完成初步的工艺流程的设计与优化。
制订初步的装配工艺过程,然后利用工艺程序分析方法、5W1H以及ECRS(取消、合并、重排、简化)四大准则对工艺程序进行改善,利用动作研究改善各操作单元的动作等。
改善的目的是为了消除工艺流程中存在的各种不合理的现象、减少浪费等。
生产组装线平衡实例
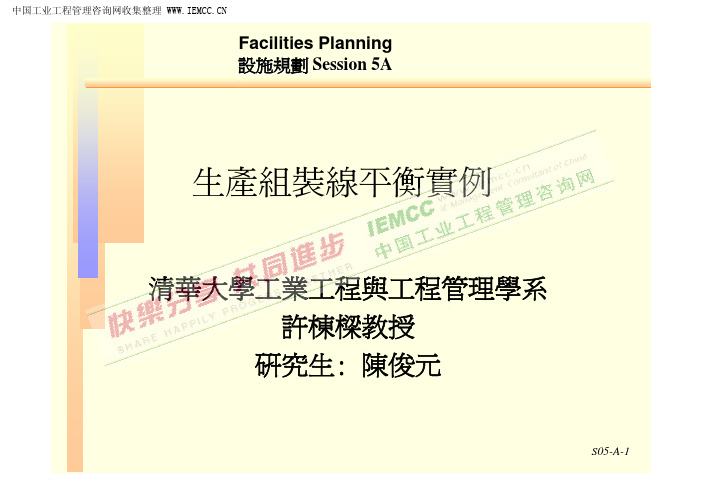
生產組裝線平衡實例清華大學工業工程與工程管理學系許棟樑教授研究生: 陳俊元Project List for a major NB maker Project 1:•系統組裝線分析診斷<Skip>•系統組裝線Line BalanceProject 2:物流與倉儲佈置分析改善Project 3:•電路板組裝線分析診斷<Skip>電路板組裝線Line Balance <Skip>Use in-depth optimization techniques to balance the line by properly assigning tasks to work stations in order to:•Maximize the outputs with given input resources (Outputoriented)•Minimize the input resources with given outputrequirements. (Input oriented)•Or, somewhere in between the above two –looking formore outputs with less inputs so that the efficiency ismaximized.Methodology Briefing¾建立一數學模型來使得各工作站在考慮組裝前後次序下能以較佳的時間分配其動作(task)項目, 並以ILOG CPLEX軟體迅速求解。
利用此模式系統組裝線進行工作站數及作業內容的最佳化分配,以提昇平衡率並減少工作站數。
¾最佳化之目標導向可分為兩類:1.Input-Oriented:在固定產出率下,最佳化(極小化)資源投入量。
¾收集所需資料1.動作先行圖(Precedence Diagram)2.各細項動作時間(detail task perform time)3.工作站數(number of workstations)4.產出間隔時間(Takt time)¾依所收集之資料建立數學模式¾O/P oriented: objective func: minimize takt time ( optimize production vol.)¾I/P oriented: OF: given takt time minimize # W/S.¾以ILOG CPLEX求得最佳解。
装配生产线平衡原理讲义

装配生产线平衡原理讲义引言装配生产线平衡是一种将工作任务在装配生产线内进行分配和均衡的方法。
通过平衡装配线上的工作任务,可以提高生产效率,减少浪费,并确保整个生产过程顺利进行。
本讲义将介绍装配生产线平衡的原理和方法。
1. 装配生产线平衡的概述装配生产线平衡是指将不同工作任务均匀地分配给装配线上的工人,以达到生产线各工位的动态平衡。
通过平衡工作任务,可以减少装配线上的空闲时间和工人之间的等待时间,从而提高生产效率。
2. 装配生产线平衡的重要性装配生产线平衡可以带来以下几个重要好处: - 提高生产效率:通过优化工作任务的分配,可以缩短生产周期,提高生产效率。
- 减少浪费:平衡装配生产线可以减少工人之间的等待时间和装配线上的空闲时间,从而减少浪费。
- 降低成本:通过平衡装配线,可以减少人力资源的浪费,从而降低生产成本。
3. 装配生产线平衡的原理装配生产线平衡的原理包括以下几个方面: - 工作任务分析:首先要对装配线上的工作任务进行分析,确定每个工位所需的时间和工作内容。
- 平衡指标确定:根据工作任务的分析结果,确定装配线平衡的指标,如生产周期、生产数量等。
-工作任务分配:根据装配线平衡的指标,将工作任务均匀地分配给每个工位的工人。
- 定期调整:由于生产线上的工作任务可能会随着时间的推移而发生变化,因此需要定期对工作任务进行调整,以保持装配线的平衡状态。
4. 装配生产线平衡的方法装配生产线平衡的方法包括以下几个步骤: 1. 工作任务分析:对装配线上的工作任务进行仔细分析,确定每个工位所需的时间和工作内容。
2. 平衡指标确定:根据工作任务的分析结果,确定装配线平衡的指标,如生产周期、生产数量等。
3. 工作任务分配:根据平衡指标,将工作任务均匀地分配给每个工位的工人。
4. 定期调整:定期对工作任务进行调整,以适应生产线上的变化。
5. 装配生产线平衡的实施步骤装配生产线平衡的实施步骤包括以下几个阶段: 1. 数据收集:收集和整理装配线上的相关数据,如工作任务的时间和内容。
装配线平衡习题.docx

流水线平衡习题参考答案一、可变流水线设计实例某可变流水线加工A、B、C三种制品,三种制品的产量及工艺资料如表所示。
若设备修理及流水线调整的时间占10%,年制度工作时间300天,两班制,每班8小时,试确定:1、三种产品的节拍;2、各工序设备需要及采用量;3、各工序设备负荷系数及流水线总负荷系数。
解:1、流水线的节拍(1)计算各产品的单件加工时间TA= 10+20+10 =40 (分)TB = 20+10+20 = 50 (分)TC = 5+5+10 =20 (分)(2)用加工劳动量比重法求节拍N=40X25000+50X10000+20X20000= 1900000aA= 40*25000/1900000=0.53同理可得:aB = 0.26 aC=0.21(3)确定节拍rA=F A/N A = aA* F/N A =0.53*300*2*8*60* (1-10%) /25000=5.5 (分/件)同理可得:rB=6.7 (分/件)rC=2.7 (分/件)2、确定各工序设备需要量:S A i=T A i/rA=10/5.5 =1.8 (单位)=2S B i=TA2/rB = 20/6.7 =2.9 (单位)=3■ (2) r=50/200=0.25 (分/件) ■(3) Smin=1.14/0.25=4.56^5■ (4)组织工作地。
根据装配作业顺序图,用试算法进行工作地重新划分, 供划分出5个工作地,如下图所示:Sci=TA3/rC = 5/2.7 =1.9 (单位)=2 同理: S A 2=3.6=4 S B2= 1.5=2 S C2= 1-9=2 S A 3=L8=2 S B 3=2.9=3 S C3=3.7 =4由取大原则,各工序的设备实际采用是: 第一工序:3第二工序:4第三工序:4 3、确定各工序设备负荷系数与流水线总负荷系数 N A' t A ■ + N D , D ; + , , • + N c • t c i叱 ___ A A I D D I Q Q I '_ S ei T 牧 _q£ N j.顶=1S eg 效 第一工序:Ki= (25000*10+10000*20+20000*5)/3* 300*2*8*60* (1-10%) =70.73% K 2=61.5% K 3=62.7%流水线总负荷系数: K 二 =66.6% aq ZN J T J j = i■计算装配线的时间损失系数&平滑系数:■ &L= (5X0.25-1.14) /5X0.25X100% = 8.8%政=瑚0.25- 0.25)2+ (0.25—0.24沪+ (0.25 — 0.2驴 +(0.25- 0.17)2+(0.25—0.23)2 ^0 083■计算装配线的时间损失系数&平滑系数:■&L= (5X0.25-1.14) /5X0.25X100% = 8.8%■SI=[(0.25-0.25)2+ (0.25-0.21)2+ (0.25-0.23)2+ (0.25-0.22)2+ (0.25-0.23)2] 1/2还有其他方案,只要各工作地时间和不超过节拍都可行。
汽车装配线平衡方法的

模拟退火算法在求解装配线平衡问题中的优势与局限
优势
能够有效避免局部最小值,获得全局最优解。
对于非线性、多峰值、复杂的优化问题具有较好 的求解效果。
模拟退火算法在求解装配线平衡问题中的优势与局限
• 具有较强的鲁棒性和广泛的适用性。
模拟退火算法在求解装配线平衡问题中的优势与局限
局限
算法的运行时间较长,需要较 高的计算成本。
汽车装配线平衡方法
汇报人: 日期:
目录
• 装配线平衡问题概述 • 装配线平衡问题的基本理论 • 遗传算法在装配线平衡问题中的
应用 • 模拟退火算法在装配线平衡问题
中的应用
目录
• 基于粒子群优化算法的装配线平 衡问题求解方法
• 实例分析
01
装配线平衡问题概述
装配线的定义与特点
装配线的定义
装配线是一种将零部件组装到一起的生产线,通常包括多个 工作站和工序。
装配线的特点
装配线具有高效、连续、重复性高的特点,能够快速大量地 生产产品。
装配线平衡问题的定义与重要性
装配线平衡问题的定义
装配线平衡问题是指如何安排工作站和工序的顺序和时间,以使整个装配线的 生产效率最高。
装配线平衡问题的重要性
良好的装配线平衡可以提高生产效率、降低生产成本、减少工人的疲劳程度, 提高产品质量。
02
装配线平衡问题的基本理论
装配线平衡问题的数学模型
01 02
定义与公式
装配线平衡问题可以定义为在满足一系列约束条件下,寻找使得生产线 总运行时间最短的工站排列组合方式。数学模型通常涉及线性规划、整 数规划、动态规划等。
变量与参数
数学模型中涉及的变量和参数包括工站数量、每个工站的工作时间、生 产节拍、工作站的约束条件等。
简单装配线平衡问题

作业元素的标识变量
{ xik =
1, 0,
如果作业 i 分配到第 k 工作站 如果作业 i 没有分配到第 k 工作站
式中: i = 1,2,…,n;k = 1,2,…,m0 。 工作站的标识变量
{ Wk =
1, 0,
如果第 k 工作站开启 如果第 k 工作站没有开启
式中: k = 1,2,…,m0 。 显然, Model( Ib) 是线性的 0鄄1 规划, 其中: 0鄄1 变量的数量为 m0 ( n + 1) 个, 线性约束
SALBP鄄E, SALBP鄄F 以及工作站负荷均衡问题( SALBP鄄III) 和装配线上作业元素之间的相关 性问题( SALB鄄IV) 。
接下来我们将分别建立这几类问题的数学模型, 其中, 重点介绍 SALBP鄄I, SALBP鄄II。
2. 2摇 第一类装配线平衡问题( SALBP鄄I)
2. 2. 1摇 第一类装配线平衡问题的描述
在装配线的设计与安装阶段,主要以生产能力满足市场需求、系统投资少和装配线的 效率高为目标。这一阶段是基于对市场需求的预测以及设备能力的估算,来最小化工作站 数。最小化工作站数就意味着设备与人员的减少,从而降低设备与人员费用,优化生产流 程,提高生产效率。系统一旦安装,短期内人员和设备难以调整,此即第Ⅰ类装配线平衡 问题。随着装配线应用的日益熟练以及环境的不断变化,装配线也需要随之不断调整,此 时就会出现考虑调整装配线节拍(SALBPII),工作站负荷均衡的问题,以及装配线上作业 元素之间相关性等问题。
第 2 章摇 简单装配线平衡问题摇 01摇 5
摇 摇 (1)目标函数 摇 摇 (2)约束条件
m0
min移 Wk k =1
m0
移 xikti 臆 C,k = 1,2,…,m0 摇 摇 摇 i =1 m0
装配生产线平衡
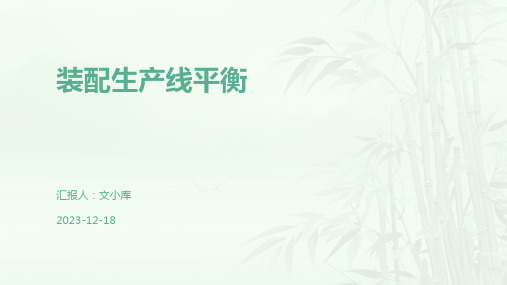
经过平衡优化后,服装生产线的生产效率得到提高,员工技能水平得到提升,产品质量得到保障。
06
生产线平衡的挑战与对策
设备故障与停机时间
设备老化与维护不足
长时间运行的设备容易出现故障,影响生产线的连续性和稳定性 。
停机维修与调试
设备故障时需要停机进行维修和调试,导致生产暂停和产能损失 。
预防措施与定期维护
制定优化方案与实施
制定优化方案
针对瓶颈工序和生产线平衡率低 的问题,制定优化方案,如改进 工艺、引入新设备、调整工序顺 序等。
方案评审与批准
组织专家对优化方案进行评审, 确保方案的可行性和有效性,并 获得批准。
方案实施
按照优化方案的要求,组织人力 、物力等资源,对生产线进行调 整和改进。
效果评估与持续改进
效果评估
收集实施后的生产线数据,计算生产线平衡率和 生产效率等指标,评估优化方案的效果。
持续改进
针对评估结果中仍然存在的问题和不足,制定持 续改进计划,不断完善和优化生产线平衡工作。
经验总结与分享
总结生产线平衡工作的经验和教训,与其他部门 或企业分享,促进共同进步。
05
生产线平衡案例分析
案例一:汽车装配生产线平衡
02
生产线平衡现状分析
生产线布局与设备配置
生产线布局
分析生产线的整体布局,包括设 备排列、工作站设置、物料流动 路径等,以评估生产线的效率和 平衡性。
设备配置
评估设备的数量、类型、性能和 生产能力,以确定生产线各工序 的设备需求和配置是否合理。
生产流程与作业时间
生产流程
详细了解生产线的生产流程,包括各 工序的操作步骤、工艺要求、检验标 准等,以找出潜在的瓶颈和浪费环节 。
《装配线平衡计算》课件
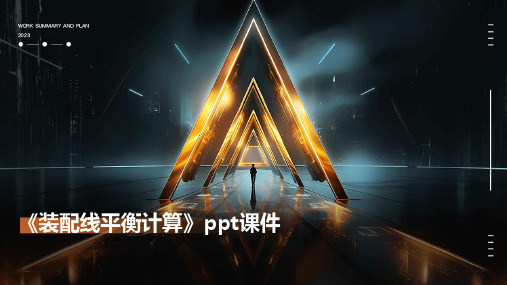
目录 CONTENTS
• 装配线平衡计算概述 • 装配线平衡计算方法 • 装配线平衡计算实例 • 装配线平衡优化策略 • 装配线平衡计算软件介绍
01
装配线平衡计算概述
装配线平衡计算的定义
装配线平衡计算是指通过合理安排装配线上的作业人员、作 业时间和作业顺序,使得装配线在稳定运行状态下完成一定 数量的产品,同时达到最优化的作业效率和资源利用率的计 算过程。
线性规划法
总结词
通过建立线性规划模型,求解最优解, 实现装配线的平衡计算。
VS
详细描述
线性规划法是一种数学优化方法,通过建 立线性方程或不等式来描述装配线平衡问 题。该方法将装配线上的作业要素、时间 、资源等作为变量,建立数学模型并求解 最优解。通过调整变量的值,可以找到最 优的装配线平衡方案,提高生产效率。
选择建议
根据企业规模和需求选择合适的软件;考虑软件的 易用性和技术支持;结合实际预算进行购买决策。
THANKS
THANK YOU FOR YOUR WATCHING
适应性和灵活性
装配线平衡计算应具有一定的适应性和灵活 性,以应对产品变化和生产调整。
02
装配线平衡计算方法
作业要素分析法
总结词
通过对作业要素的详细分析,确定各作业要素所需的时间,进而找出瓶颈作业和空闲时间,以达到装配线的平衡 。
详细描述
作业要素分析法首先对装配线上的每个作业要素进行详细分析,包括作业要素的类型、所需工具、操作步骤等, 并估算每个作业要素所需的时间。通过分析这些数据,可以找出装配线上的瓶颈作业(即耗时最长的作业要素) 和空闲时间,从而对装配线进行平衡调整,提高生产效率。
作业要素调整
《装配线平衡计算》课件
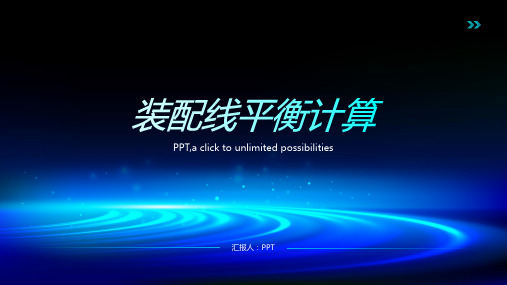
提高生产效率:通过平衡装配线,可以减少等待时间,提高生产效率。
降低生产成本:平衡装配线可以减少浪费,降低生产成本。
提高产品质量:平衡装配线可以减少错误,提高产品质量。
提高员工满意度:平衡装配线可以减少员工的工作压力,提高员工满意度。
提高生产灵活性:通过优化装配线布局,提高生产灵活性,适应市场需求变化
提高企业竞争力:通过优化装配线布局,提高企业竞争力,增强企业盈利能力
汇报人:PPT
优缺点比较:每种计算方法都有其优点和缺点,需要根据实际情况进行选择
选择原则:根据生产效率、成本、质量等因素进行综合考虑,选择最合适的计算方法
添加标题
添加标题
添加标题
添加标题
添加标题
添加标题
添加标题
确定装配线平衡计算的目标:提高生产效率,减少生产成本
计算工件加工时间:根据工件类型和加工时间,计算每个工件的加工时间
瓶颈工序分析法:分析瓶颈工序的原因,采取措施进行改进
线平衡率计算法:通过计算各工序的线平衡率,找出瓶颈工序,进行优化
工序时间优化法:通过优化工序时间,提高装配线的效率
生产线布局优化法:通过优化生产线布局,提高装配线的效率和灵活性
计算方法:包括时间计算法、效率计算法、成本计算法等
适用场景:不同计算方法适用于不同的生产环境和生产条件
计算工件加工时间总和:将所有工件的加工时间相加,得到总加工时间
优化工件加工顺序:根据工件加工效率,调整工件的加工顺序,以提高生产效率
数据整理:整理收集到的数据,确保数据的准确性和完整性
实例选择:选择具有代表性的装配线进行平衡计算
- 1、下载文档前请自行甄别文档内容的完整性,平台不提供额外的编辑、内容补充、找答案等附加服务。
- 2、"仅部分预览"的文档,不可在线预览部分如存在完整性等问题,可反馈申请退款(可完整预览的文档不适用该条件!)。
- 3、如文档侵犯您的权益,请联系客服反馈,我们会尽快为您处理(人工客服工作时间:9:00-18:30)。
某玩具小车装配线是一混合流水线,主要生产A和B两种类型的玩具车,这两类玩具小车的装配步骤及其定额时间分别如表3-1和表3-2所示,现计划A 型小车每天生产100辆,B型小车每天生产400辆,每天的生产时间为420分钟。
求使工作站数量最少的生产线平衡方式。
图1 A型产品的工艺顺序图
图2 B型产品的工艺顺序图
图2 综合工艺顺序图生产节拍:C=420*60/100=252s
B产品K 40 安装备用轮胎J
B产品M 36 上紧全部螺栓和
螺钉
K
合计1115
最小工作站数:1115/252=4.42=5
平衡规则1:后续作业数量最多者优先排列
工作站作业作业时间
(s)剩余时间
(s)
可安排的
紧后作业
紧后作业最多的
作业
时间最长的
作业
1A2257空闲无2D2502空闲无
3B55197C、E C、E E
E75122C、H、I C
F、G、H、
I
C4577F、G、H、I F、G、H、I
F6017空闲无
4G60192H、I H、I H60132I
I6072J
J4032
L 9 23
5K40212M M 36 176
工作地工作地作业元素工作地作业时间工作地负荷率(%)
1 2 3 4 5
A
D
B,E,C,F
G,H,I,J,L
K,M
225
250
205
229
76
89.29
99.21
81.35
90.87
30.16。