泵体的热流道注塑成型过程模拟分析
注塑模设计中冷、热流道技术在Moldflow中的比较分析
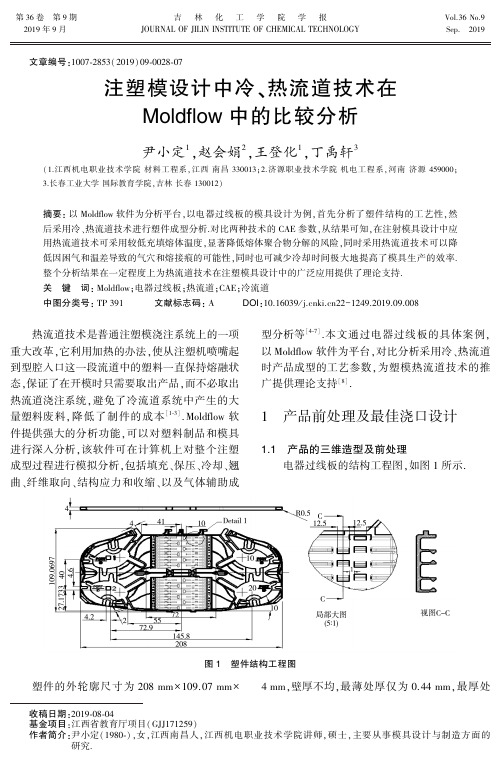
第36卷㊀第9期㊀吉㊀林㊀化㊀工㊀学㊀院㊀学㊀报Vol.36No.9㊀2019年9月JOURNALOFJILININSTITUTEOFCHEMICALTECHNOLOGYSep.㊀2019收稿日期:2019 ̄08 ̄04基金项目:江西省教育厅项目(GJJ171259)作者简介:尹小定(1980 ̄)ꎬ女ꎬ江西南昌人ꎬ江西机电职业技术学院讲师ꎬ硕士ꎬ主要从事模具设计与制造方面的研究.㊀㊀文章编号:1007 ̄2853(2019)09 ̄0028 ̄07注塑模设计中冷㊁热流道技术在Moldflow中的比较分析尹小定1ꎬ赵会娟2ꎬ王登化1ꎬ丁禹轩3(1.江西机电职业技术学院材料工程系ꎬ江西南昌330013ꎻ2.济源职业技术学院机电工程系ꎬ河南济源459000ꎻ3.长春工业大学国际教育学院ꎬ吉林长春130012)摘要:以Moldflow软件为分析平台ꎬ以电器过线板的模具设计为例ꎬ首先分析了塑件结构的工艺性ꎬ然后采用冷㊁热流道技术进行塑件成型分析.对比两种技术的CAE参数ꎬ从结果可知ꎬ在注射模具设计中应用热流道技术可采用较低充填熔体温度ꎬ显著降低熔体聚合物分解的风险ꎬ同时采用热流道技术可以降低因困气和温差导致的气穴和熔接痕的可能性ꎬ同时也可减少冷却时间极大地提高了模具生产的效率.整个分析结果在一定程度上为热流道技术在注塑模具设计中的广泛应用提供了理论支持.关键词:Moldflowꎻ电器过线板ꎻ热流道ꎻCAEꎻ冷流道中图分类号:TP391文献标志码:ADOI:10.16039/j.cnki.cn22-1249.2019.09.008㊀㊀热流道技术是普通注塑模浇注系统上的一项重大改革ꎬ它利用加热的办法ꎬ使从注塑机喷嘴起到型腔入口这一段流道中的塑料一直保持熔融状态ꎬ保证了在开模时只需要取出产品ꎬ而不必取出热流道浇注系统ꎬ避免了冷流道系统中产生的大量塑料废料ꎬ降低了制件的成本[1 ̄3].Moldflow软件提供强大的分析功能ꎬ可以对塑料制品和模具进行深入分析ꎬ该软件可在计算机上对整个注塑成型过程进行模拟分析ꎬ包括填充㊁保压㊁冷却㊁翘曲㊁纤维取向㊁结构应力和收缩㊁以及气体辅助成型分析等[4 ̄7].本文通过电器过线板的具体案例ꎬ以Moldflow软件为平台ꎬ对比分析采用冷㊁热流道时产品成型的工艺参数ꎬ为塑模热流道技术的推广提供理论支持[8].1㊀产品前处理及最佳浇口设计1.1㊀产品的三维造型及前处理电器过线板的结构工程图ꎬ如图1所示.图1㊀塑件结构工程图㊀㊀塑件的外轮廓尺寸为208mmˑ109.07mmˑ4mmꎬ壁厚不均ꎬ最薄处厚仅为0.44mmꎬ最厚处为1.0mmꎬ平均壁厚约为0.56mm.该产品生产批量为50万ꎬ材料为PC+ABS亦称聚碳酸酯与丙烯腈 ̄丁二烯 ̄苯乙烯共聚物塑料合金.该塑件整体上为平板件ꎬ不允许表面出现熔接痕㊁缩孔㊁缩痕㊁飞边和平面翘曲变形ꎬ总体尺寸要求精度较高.从图1中的局部扩大视图中可知ꎬ塑件背面有多个尺寸很小的卡扣结构ꎬ该结构对产品成型极为不利ꎬ如何选择合适的浇注系统是保证产品成型质量要求的关键.将该产品3D模型转换为STP格式后导入到Moldflow软件中ꎬ生成43170个单元网格ꎬ最小网格纵横比值为1.16ꎬ最大值为18.32ꎬ平均值为2.08ꎬ匹配率大于90%达到93.2%ꎬ网格模型完全满足模流分析的要求.1.2㊀最佳浇口设计浇口位置的设定直接关系到熔体到模具型腔内的流动ꎬ从而影响聚合物分子的取向和产品成型后的质量[9].利用Moldflow分析ꎬ选取最佳位置的结果如图2所示的箭头位置.为使塑件表面不受损伤ꎬ增设了小凸台保证脱模时浇口断裂在凸台小端处[10].图2㊀最佳浇口设计2㊀基于Moldflow的冷㊁热流道技术的CAE㊀㊀该塑件材料的成型工艺参数为:熔体温度280ħꎬ模具表面温度75ħꎬ顶出温度94ħꎬ绝对最大熔体温度为360ħꎬ最大剪切速率4000s-1ꎬ最大剪切应力0.4MPa.2.1㊀冷流道分析2.1.1㊀充填时间和充填温度由图3充填时间和充填温度结果可知ꎬ熔融的料流从浇口开始进入型腔ꎬ分别向周边充填.最后四股料流在中间汇合ꎬ充填完成时间为1.060s.浇口料流温度为283.3ħ稍高于该熔体温度ꎬ到达中间汇合处的温度为257.3ħꎬ温度梯降为25.9ħ.(a)充填时间(b)充填温度图3㊀充填时间和充填温度2.1.2㊀注射压力和剪切速率由图4所示注射压力和剪切速率分析结果可知ꎬ为了充填满型腔ꎬ塑料熔体的注射压力为105.7MPa.为了提高熔体的流动效率ꎬ主要是提高充填的温度ꎬ在注射压力上并没有太大的提高ꎬ但是塑料熔体却受到了很大的剪切ꎬ在充填结束时ꎬ其剪切速率达到了1.075E+05ꎬ远远大于该塑料合金的最大剪切速率4000s-1.一般剪切速率大ꎬ表观粘度降低ꎬ越利于注射ꎬ但是过大剪切速率会导致塑料分解[11].(a)注射压力92㊀㊀第9期尹小定ꎬ等:注塑模设计中冷㊁热流道技术在Moldflow中的比较分析㊀㊀㊀(b)剪切速率图4㊀注射压力和剪切速率2.1.3㊀冷却时间和收缩率从图5结果分析可知ꎬ为了到达该塑料合金的顶出温度ꎬ用了10.96s的冷却定型时间.此时达到顶出温度时的塑件的体积收缩率为6.936%ꎬ如图5(b)所示.(a)冷却时间(b)收缩率图5㊀冷却时间和收缩率2.1.4㊀气穴图6为塑件正㊁反两面产生气穴的分析结果.在中间最后的料流汇合的位置有气穴ꎬ塑件的两端转折处也出现了气穴ꎬ还有就是塑件反面的卡扣位置气穴也较多.这些部位困气较严重ꎬ容易出现缺胶ꎬ在这些部位建议采用排气镶件来解决困气.(a)正面气穴(b)反面气穴图6㊀正㊁反面产生气穴2.1.5㊀熔接痕分析评估熔接痕是否影响外观的标准主要有两个:一是熔接痕形成的温度及周围的温度差ꎬ二是形成熔接痕的料流汇合角度及是否困气[12].结合图3中的充填温度和图7的分析结果可知ꎬ其温度并没有太大的差异ꎬ熔接痕呈现十字行ꎬ主要是左右和前后两股料流前沿相遇造成的ꎬ同时从汇流角度以及结合气穴结果分析ꎬ该熔接痕主要因困气造成的可能性也比较大些.图7㊀熔接痕2.1.6㊀翘曲分析成型中各种因素导致的翘曲变形分析是CAE软件中求解非线性结果的高性能程序[13].从03㊀㊀吉㊀林㊀化㊀工㊀学㊀院㊀学㊀报㊀㊀2019年㊀㊀图8结果可知ꎬX方向的变形为0.2056mmꎬY方向的变形为0.2861mmꎬZ方向的变形为0.3774mmꎬ总的变形为0.4294mm.这是一个比较好的翘曲变形值ꎬ各向变形结果均小于0.5mm.(a)总变形(b)X方向(c)Y方向(d)Z方向图8㊀翘曲分析2.2㊀热流道分析2.2.1㊀充填时间和充填温度由图9充填时间和充填温度结果可知ꎬ熔融的料流从浇口开始进入型腔ꎬ分别向周边充填.最后四股料流在中间汇合ꎬ充填完成时间为0.7498s.浇口料流温度为263.4ħ稍高于该熔体的温度ꎬ到达中间汇合处的温度为213.4ħꎬ温度梯降为50ħ.由于温度差降较大ꎬ可能会对后续分析带来一定的影响.(a)充填时间(b)充填温度图9㊀充填时间和充填温度2.2.2㊀注射压力和剪切速率由图10的注射压力和剪切速率分析结果可知ꎬ充填满型腔时ꎬ塑料熔体的注射压力为113.0MPaꎬ在压力上稍有提高.充填结束时ꎬ塑料熔体的剪切速率为43127s-1ꎬ大于该塑料合金的最大剪切速率4000s-1.但是相对于冷流道时所产生的剪切速率要小很多.这在一定程度上提高了注射效率ꎬ同时减少了塑料发生分解的可能性.(a)注射压力13㊀㊀第9期尹小定ꎬ等:注塑模设计中冷㊁热流道技术在Moldflow中的比较分析㊀㊀㊀(b)剪切速率图10㊀注射压力和剪切速率2.2.3㊀冷却时间和收缩率从图11(a)结果分析可知ꎬ为了到达该塑料制品的顶出温度ꎬ用了4.159s的冷却定型时间.此时达到顶出温度时塑件的体积收缩率为6.177%ꎬ如图11(b)所示.(a)冷却时间(b)收缩率图11㊀冷却时间和收缩率2.2.4㊀气穴图12中为塑件的正㊁反两面产生气穴的分析结果.出现困气的地方于冷流道浇注系统的位置差不多ꎬ但是比较困气的大小可以知道ꎬ热流道产生的气穴没有冷流道的大ꎬ同时数量上也有所减少ꎬ这和充填的料流温度有关ꎬ冷流道到的料流温度大ꎬ通过模具排气较困难ꎬ而热流道的充填料流温度要小ꎬ有利于型腔气体的快速排出.但是同样也需要困气部位进行模具结构的镶件设计.(a)正面气穴(b)反面气穴图12㊀正㊁反面产生气穴2.2.5㊀熔接痕分析图13的分析结果可知ꎬ熔接痕主要呈现中间一字行ꎬ由左右各两股料流前沿相遇造成其温度并没有太大的差异ꎬ该熔接痕主要因困气造成的ꎬ模具结构设计时需要加强排气.图13㊀熔接痕2.2.6㊀翘曲分析从图结果可知ꎬX方向的变形为0.2468mmꎬY方向的变形为0.2937mmꎬZ方向的变形为0.6524mmꎬ总的变形为0.7198mm.翘曲变形值相对于冷流道要大出很多ꎬ从翘曲产生的原因分析ꎬ是料流温差过大造成的ꎬ主要是采用的针阀式热流道ꎬ该充填方式决定了从浇口到料流末端的温差较大.为减少该塑件的翘曲变形ꎬ只需要从Z向的脱模方向进行考虑ꎬ加强Z向的平稳脱模ꎬ加强中间卡扣部分的均匀推出ꎬ是该模具结构设计要考虑的问题[14].综合上述数据进行表1的对比ꎬ从结果可知ꎬ冷流道的充填相对比较难ꎬ因此靠提高塑料熔体的充填温度来提高塑料的流动性能ꎬ但是加快了高分子聚合物的相互剪切ꎬ使其剪切速率过大ꎬ聚合物分解的危险性增大.在充填压力和保压压力23㊀㊀吉㊀林㊀化㊀工㊀学㊀院㊀学㊀报㊀㊀2019年㊀㊀上没有提高ꎬ但是冷却保压时间却相应的增加.(a)总变形(b)X方向(c)Y方向(d)Z方向图14㊀翘曲分析采用热流道充填ꎬ不需提高充填温度ꎬ只增大了充填压力和保压压力ꎬ结果体现了熔接痕和气穴方面有减少优势ꎬ也避免了剪切速率过大引起聚合物分解的危险性ꎬ但另一方面却增大了翘曲变形的趋势.从生产效率上来讲ꎬ开模时间为3s.冷流道生产周期:1.061s+10.96s+3s=15.021sꎻ热流道生产周期:0.7498s+4.159s+3s=7.9088s.热流道的生产效率几乎是冷流道的一倍.另外冷流道还需要去除冷流道凝料和去浇口的时间ꎬ热流道无需人工操作ꎬ生产效率会有更进一步的提高ꎬ自动化程度更高.表1㊀冷㊁热流道分析对比结果对比项目冷流道热流道充填时间/s1.0600.7498充填温度/ħ283.2263.4充填压力/MPa105.7113.0体积收缩率/%6.9366.117翘曲总变形量/mm0.42940.71983㊀结㊀㊀论通过电器过线板注塑的具体案例ꎬ采用Moldflow分析软件对冷㊁热流道进行分析对比.结果表明ꎬ采用热流道技术虽然使塑件在翘曲分析结果不理想ꎬ但是该塑件从尺寸质量上主要控制平面尺寸精度ꎬ从脱模结构上采用平稳脱模方式ꎬ可极大确保了脱模方向的尺寸精度ꎬ同时能实现降低注射温度无聚合物分解的危险ꎬ也不需要考虑浇注系统凝料产生的废料和人工费用ꎬ大大提高了生产效率.参考文献:[1]㊀董祥忠ꎬ李年伟ꎬ沈洪雷.奥拓轿车前保险杠注塑模浇注系统的CAE分析[J].工程塑料应用ꎬ2014ꎬ27(12):28 ̄31.[2]㊀马文静ꎬ葛正浩ꎬ张凯凯ꎬ等.基于Pro/E和Moldflow的键盘框架热流道注射模具设计[J].塑料.2011ꎬ40(2):118 ̄121.[3]㊀SODERGANDAꎬSTOLTM.Propertiesoflacticacidbasedpolymersandtheircorrelationwithcomposition[J].ProgPolymSciꎬ2002ꎬ27(6):1123 ̄1163.[4]㊀单志ꎬ邵会菊ꎬ郭建兵ꎬ等.基于CAE技术的汽车外饰件翘曲分析及工艺优化[J].塑料ꎬ2010ꎬ39(3):110 ̄112.[5]㊀尹小定.基于CAD/CAE技术的控制面板注塑模设33㊀㊀第9期尹小定ꎬ等:注塑模设计中冷㊁热流道技术在Moldflow中的比较分析㊀㊀㊀计[J].塑料科技ꎬ2016ꎬ44(6):61 ̄65. [6]㊀黄先.液晶电视前壳热流道顺序阀进浇方案Moldflow分析[J].塑料工业ꎬ2011ꎬ39(7):50 ̄52. [7]㊀尹小定ꎬ黄有华ꎬ王春燕.CAE技术在咖啡机控制面板冷却系统设计中的应用[J].吉林化工学报ꎬ2017ꎬ34(5):48 ̄52.[8]㊀陈进武ꎬ曹秩杰ꎬ苏庆勇.Moldflow在塑料模热流道技术中的应用[J].塑料工业ꎬ2014ꎬ42(4):31 ̄34[9]㊀黄桂坚ꎬ洪建明ꎬ伍晓宇ꎬ等.电梯人口盖板热流道注塑模具设计[J].工程塑料应用ꎬ2009ꎬ37(8):72 ̄76.[10]屈华昌ꎬ吴梦陵.塑料成型工艺与模具设计[M].北京:高等教育出版社ꎬ2007:109 ̄110.[11]叶东ꎬ谭方云.剪切速率在大型塑料注射模设计中的拓展应用[J].模具工业ꎬ2005ꎬ294(8):27 ̄30. [12]余玲ꎬ陈是德ꎬ张诗.CAE在汽车仪表板浇注系统设计的应用[J].塑料科技ꎬ2010ꎬ38(11):69 ̄73. [13]谢鹏程ꎬ多田和美ꎬ杨卫民.高分子材料注射成型CAE理论及应用[M].北京:化学工业出版社ꎬ2008:118 ̄119.[14]尹小定ꎬ王登化ꎬ赵会娟.电器过线板的热流道注塑模设计[J].塑料科技ꎬ2018ꎬ46(11):85 ̄89.ComparativeAnalysisofColdRunnerTechnologyandHotRunnerTechnologyinModDesignBasedonMoldflowSoftwareYINXiaoding1ꎬZHAOHuijuan2ꎬWANGDenhua1ꎬDINGYuxuan3(1.JiangxiVocationalCollegeofMechanical&ElectricalTechnologyꎬNanchangꎬ330013ꎬChinaꎻ2.DepartmentofMechanicalandElectricalEngineeringꎬJiyuanVocationalandTechnicalCollegeꎬJiyuanꎬ459000ꎬChinaꎻ3.CollegeofiternationaleducationꎬChangchunUniversityThecnologyꎬChangchun130012ꎬChina)Abstract:Usingmoldflowsoftwareasananalysisplatformꎬtakinganelectricalplateofover ̄wireasaspecificcaseꎬtheplasticpartstructurewasanalyzedfirstlyꎬthentheplasticpartwasfor ̄medandanalyzedusingcoldandhotflowchanneltechnology.ComparingtheCAEparametersofthetwotechnologiesꎬthengettheresults.Theapplicationofthermalchanneltechnologytoinject ̄tionmolddesigncanuselowerfillingmelttemperatureꎬreducetheriskofmeltpolymerdecompo ̄sitionsignificantlyꎬandtheapplicationofthermalchanneltechnologycanreducethepossibilityofcavitationandfusionmarksduetogasdistressandtemperaturedifference.Atthesametimeꎬthecoolingtimecanbereducedandtheefficiencyofdieproductioncanbegreatlyimproved.Theanalysisresultsprovidetheoreticalsupportforthewideapplicationofhotchanneltechnologyininjectionmolddesign.Keywords:MoldflowꎻElectricpassingplateꎻHotrunnerꎻCAEꎻColdrunner43㊀㊀吉㊀林㊀化㊀工㊀学㊀院㊀学㊀报㊀㊀2019年㊀㊀。
数值仿真分析方法的研究与实践在注射模热流道温度场的应用

数值仿真分析方法的研究与实践在注射模热流道温度场的应用陈凤浙江机械与电气工程学院机械工程系邮箱:cfeng0096@yahoo.co 关键词:热流道,温度场,数值仿真分析摘要:在本文中,学习如何建立和解决数值模拟对热流道注塑模具温度场的可视化分析并在计算机上实现,最后引用相应的例子。
I 介绍热流道的温度分布不仅可以直接影响塑料的融化性能,还会影响注塑成型产品的质量和生产效率。
通过分析温度场和热流道的温度控制,控制注塑成型的过程,不仅可以减少变形,提高力学性能,还能改善外观质量,提高尺寸精度。
在注塑模具的总体设计中,温度场分析通常比采用与计算结果比较更接近实际情况,也更稳定。
但在热流道的应用中,温度的要求更高,因此有必要建立一个数学模型来分析不稳定温度场。
II 如何建立和解决温度场数学模型为了方便分析,从喷嘴到喷射流道的热流道几何模型可以视为一个沿流道中心线的轴对称体。
热流道在注射后,熔融态的热流道仍然不受任何压力。
如果忽视塑料结晶的话,则该融化基本上可以视为粘性流体在无内热源状态下的能量转换。
其温度的传导主要是通过静态而交换的。
热流道在注射成型过程中,温度现象非常复杂。
考虑温度的实际分析,热流道中有四种热量交换,主要是:熔体内部交换热量;热流道系统之间的热量交换;热流道系统内部交换热量;热流道系统和冷却剂之间交换热量。
这大大增加了分析的困难,因此是分析之前必须进行以下假设:(1)熔融状态下塑料的性能不会改变,也就是说,密度、比热容、恒定压力和熔体热导率都是常数。
(2)热流道加热器在多方面上是对称的,所以可以这么认为,流道是均匀加热,融化的周向温度沿流道是均匀分布的,融化过程是沿热流道的几何模型的中心线轴对称的。
数字模型:基于上述假设和热传导的原则,温度场的数学模型可以用傅里叶热微分方程进行如下描述:(1)在公式中,K——熔体热导率,W/(m℃);T——熔化瞬间温度,℃;t——时间,s;ρ——熔体密度,kg/m³;C——熔化的定压比热容J/(kg℃);x,y,z——三维坐标。
热流道(一)热流道的发展过程注塑模热流道是通过加热的办法来保证...
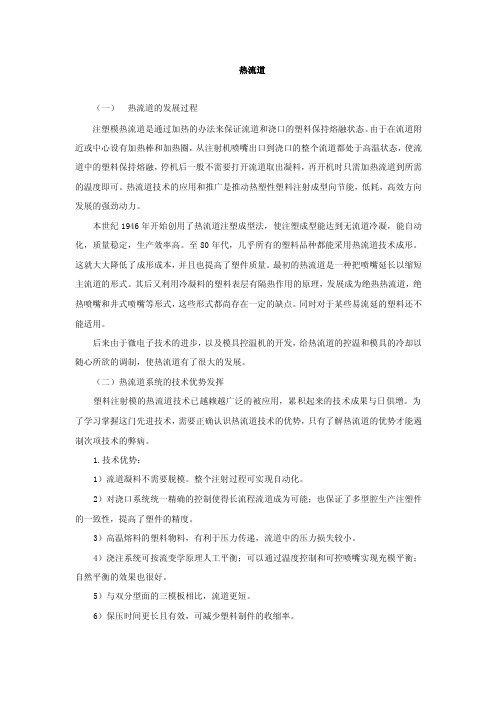
热流道(一)热流道的发展过程注塑模热流道是通过加热的办法来保证流道和浇口的塑料保持熔融状态。
由于在流道附近或中心设有加热棒和加热圈,从注射机喷嘴出口到浇口的整个流道都处于高温状态,使流道中的塑料保持熔融,停机后一般不需要打开流道取出凝料,再开机时只需加热流道到所需的温度即可。
热流道技术的应用和推广是推动热塑性塑料注射成型向节能,低耗,高效方向发展的强劲动力。
本世纪1946年开始创用了热流道注塑成型法,使注塑成型能达到无流道冷凝,能自动化,质量稳定,生产效率高。
至80年代,几乎所有的塑料品种都能采用热流道技术成形。
这就大大降低了成形成本,并且也提高了塑件质量。
最初的热流道是一种把喷嘴延长以缩短主流道的形式。
其后又利用冷凝料的塑料表层有隔热作用的原理,发展成为绝热热流道,绝热喷嘴和井式喷嘴等形式,这些形式都尚存在一定的缺点。
同时对于某些易流延的塑料还不能适用。
后来由于微电子技术的进步,以及模具控温机的开发,给热流道的控温和模具的冷却以随心所欲的调制,使热流道有了很大的发展。
(二)热流道系统的技术优势发挥塑料注射模的热流道技术已越赖越广泛的被应用,累积起来的技术成果与日俱增。
为了学习掌握这门先进技术,需要正确认识热流道技术的优势,只有了解热流道的优势才能遏制次项技术的弊病。
1.技术优势:1)流道凝料不需要脱模。
整个注射过程可实现自动化。
2)对浇口系统统一精确的控制使得长流程流道成为可能;也保证了多型腔生产注塑件的一致性,提高了塑件的精度。
3)高温熔料的塑料物料,有利于压力传递,流道中的压力损失较小。
4)浇注系统可按流变学原理人工平衡;可以通过温度控制和可控喷嘴实现充模平衡;自然平衡的效果也很好。
5)与双分型面的三模板相比,流道更短。
6)保压时间更长且有效,可减少塑料制件的收缩率。
应用热流道技术明显的优点,是原材料损耗减少和易于实现注塑加工的自动化,某些大型的薄壁制件的注射,没有流道技术是困难的,甚至是不可能的。
注塑成型数值模拟报告
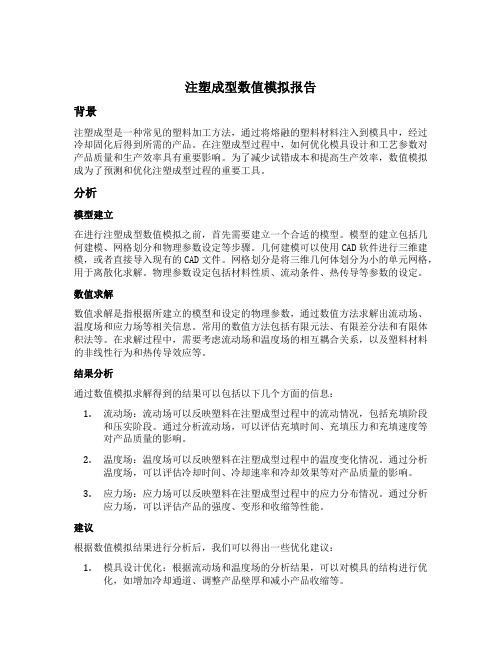
注塑成型数值模拟报告背景注塑成型是一种常见的塑料加工方法,通过将熔融的塑料材料注入到模具中,经过冷却固化后得到所需的产品。
在注塑成型过程中,如何优化模具设计和工艺参数对产品质量和生产效率具有重要影响。
为了减少试错成本和提高生产效率,数值模拟成为了预测和优化注塑成型过程的重要工具。
分析模型建立在进行注塑成型数值模拟之前,首先需要建立一个合适的模型。
模型的建立包括几何建模、网格划分和物理参数设定等步骤。
几何建模可以使用CAD软件进行三维建模,或者直接导入现有的CAD文件。
网格划分是将三维几何体划分为小的单元网格,用于离散化求解。
物理参数设定包括材料性质、流动条件、热传导等参数的设定。
数值求解数值求解是指根据所建立的模型和设定的物理参数,通过数值方法求解出流动场、温度场和应力场等相关信息。
常用的数值方法包括有限元法、有限差分法和有限体积法等。
在求解过程中,需要考虑流动场和温度场的相互耦合关系,以及塑料材料的非线性行为和热传导效应等。
结果分析通过数值模拟求解得到的结果可以包括以下几个方面的信息:1.流动场:流动场可以反映塑料在注塑成型过程中的流动情况,包括充填阶段和压实阶段。
通过分析流动场,可以评估充填时间、充填压力和充填速度等对产品质量的影响。
2.温度场:温度场可以反映塑料在注塑成型过程中的温度变化情况。
通过分析温度场,可以评估冷却时间、冷却速率和冷却效果等对产品质量的影响。
3.应力场:应力场可以反映塑料在注塑成型过程中的应力分布情况。
通过分析应力场,可以评估产品的强度、变形和收缩等性能。
建议根据数值模拟结果进行分析后,我们可以得出一些优化建议:1.模具设计优化:根据流动场和温度场的分析结果,可以对模具的结构进行优化,如增加冷却通道、调整产品壁厚和减小产品收缩等。
2.工艺参数优化:根据流动场和温度场的分析结果,可以对注塑成型过程中的工艺参数进行优化,如调整充填时间、充填压力和冷却时间等。
3.材料选择优化:根据应力场的分析结果,可以对材料的选择进行优化,以满足产品的强度和变形要求。
4-2热塑性塑料注射成型过程分析
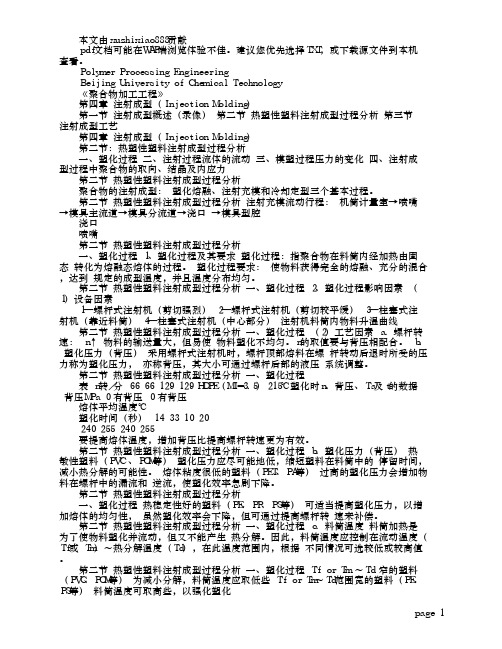
本文由xuzhixiao888贡献 pdf文档可能在WAP端浏览体验不佳。
建议您优先选择TXT,或下载源文件到本机查看。
Polymer Processing Engineering Beijing University of Chemical Technology 《聚合物加工工程》 第四章 注射成型(Injection Molding) 第一节 注射成型概述(录像) 第二节 热塑性塑料注射成型过程分析 第三节 注射成型工艺 第四章 注射成型(Injection Molding) 第二节:热塑性塑料注射成型过程分析 一、塑化过程 二、注射过程流体的流动 三、模塑过程压力的变化 四、注射成型过程中聚合物的取向、结晶及内应力 第二节 热塑性塑料注射成型过程分析 聚合物的注射成型: 塑化熔融、注射充模和冷却定型三个基本过程。
第二节 热塑性塑料注射成型过程分析 注射充模流动行程: 机筒计量室→喷嘴→模具主流道→模具分流道→浇口 →模具型腔 浇口 喷嘴 第二节 热塑性塑料注射成型过程分析 一、塑化过程 1、塑化过程及其要求 塑化过程:指聚合物在料筒内经加热由固态 转化为熔融态熔体的过程。
塑化过程要求: 使物料获得完全的熔融、充分的混合,达到 规定的成型温度,并且温度分布均匀。
第二节 热塑性塑料注射成型过程分析 一、塑化过程 2、塑化过程影响因素 (1)设备因素 1—螺杆式注射机(剪切强烈) 2—螺杆式注射机(剪切较平缓) 3—柱塞式注射机(靠近料筒) 4—柱塞式注射机(中心部分) 注射机料筒内物料升温曲线 第二节 热塑性塑料注射成型过程分析 一、塑化过程 (2)工艺因素 a. 螺杆转速: n↑ 物料的输送量大,但易使 物料塑化不均匀。
n的取值要与背压相配合。
b. 塑化压力(背压) 采用螺杆式注射机时,螺杆顶部熔料在螺 杆转动后退时所受的压力称为塑化压力, 亦称背压,其大小可通过螺杆后部的液压 系统调整。
模拟注塑分析报告

模拟注塑分析报告1. 引言本报告旨在对模拟注塑进行分析,并对其原理、应用以及优势进行说明。
模拟注塑是一种重要的工艺方法,用于生产塑料制品。
2. 模拟注塑原理模拟注塑是一种将可塑性材料加热熔化后,通过注塑机将熔融物料注入模具中形成特定形状的工艺。
注塑过程主要分为以下几个步骤:1.加料:将塑料颗粒或粉末投入注塑机的料斗中。
2.熔化:注塑机中的加热器将塑料加热并融化。
3.注射:通过注塑机的螺杆将熔融物料注入模具中。
4.冷却:待熔融物料填充模具后,冷却使其凝固。
5.脱模:待熔融物料完全凝固后,打开模具并将制品取出。
3. 模拟注塑的应用模拟注塑广泛应用于各个行业,包括汽车工业、电子电器行业、日用品行业等。
它可以生产出各种塑料制品,如塑料零件、塑料容器、塑料包装等。
模拟注塑的应用优势主要体现在以下几个方面:•生产效率高:模拟注塑可以实现自动化生产,提高生产效率。
•产品质量好:模拟注塑可以控制注塑过程中的温度、压力等参数,确保产品质量稳定。
•成本较低:模拟注塑生产的成本相对较低,可以大批量生产,降低单位产品成本。
4. 模拟注塑分析工具模拟注塑分析过程中常用的工具包括:•注塑模拟软件:通过建立模拟模型,模拟注塑过程并预测产品质量和性能。
•CAD软件:用于设计注塑产品的三维模型,并进行模拟分析。
5. 模拟注塑分析方法模拟注塑分析的方法主要包括:1.建立模拟模型:使用CAD软件将注塑产品进行三维建模,确定模具形状。
2.设定注塑参数:根据注塑材料的特性和产品要求,设定注塑参数,如温度、注射速度等。
3.进行模拟分析:使用注塑模拟软件,对注塑过程进行模拟分析,预测产品的填充、冷却和变形情况。
4.优化设计:根据模拟分析结果,对模具形状和注塑参数进行优化设计,以提高产品质量和生产效率。
6. 模拟注塑分析的应用案例以下是一个应用模拟注塑分析的案例:公司X需要生产一个塑料零件,要求精度高、壁厚均匀。
他们使用CAD软件设计了零件的三维模型,并使用注塑模拟软件进行了模拟分析。
注塑成型中的流体模拟技术研究
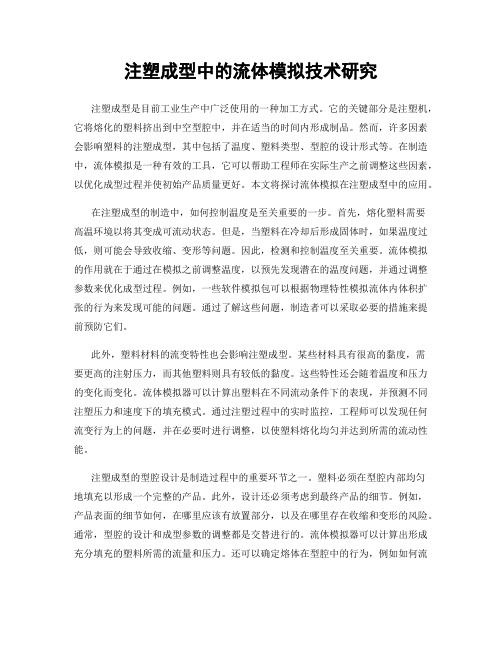
注塑成型中的流体模拟技术研究注塑成型是目前工业生产中广泛使用的一种加工方式。
它的关键部分是注塑机,它将熔化的塑料挤出到中空型腔中,并在适当的时间内形成制品。
然而,许多因素会影响塑料的注塑成型,其中包括了温度、塑料类型、型腔的设计形式等。
在制造中,流体模拟是一种有效的工具,它可以帮助工程师在实际生产之前调整这些因素,以优化成型过程并使初始产品质量更好。
本文将探讨流体模拟在注塑成型中的应用。
在注塑成型的制造中,如何控制温度是至关重要的一步。
首先,熔化塑料需要高温环境以将其变成可流动状态。
但是,当塑料在冷却后形成固体时,如果温度过低,则可能会导致收缩、变形等问题。
因此,检测和控制温度至关重要。
流体模拟的作用就在于通过在模拟之前调整温度,以预先发现潜在的温度问题,并通过调整参数来优化成型过程。
例如,一些软件模拟包可以根据物理特性模拟流体内体积扩张的行为来发现可能的问题。
通过了解这些问题,制造者可以采取必要的措施来提前预防它们。
此外,塑料材料的流变特性也会影响注塑成型。
某些材料具有很高的黏度,需要更高的注射压力,而其他塑料则具有较低的黏度。
这些特性还会随着温度和压力的变化而变化。
流体模拟器可以计算出塑料在不同流动条件下的表现,并预测不同注塑压力和速度下的填充模式。
通过注塑过程中的实时监控,工程师可以发现任何流变行为上的问题,并在必要时进行调整,以使塑料熔化均匀并达到所需的流动性能。
注塑成型的型腔设计是制造过程中的重要环节之一。
塑料必须在型腔内部均匀地填充以形成一个完整的产品。
此外,设计还必须考虑到最终产品的细节。
例如,产品表面的细节如何,在哪里应该有放置部分,以及在哪里存在收缩和变形的风险。
通常,型腔的设计和成型参数的调整都是交替进行的。
流体模拟器可以计算出形成充分填充的塑料所需的流量和压力。
还可以确定熔体在型腔中的行为,例如如何流动、分配和降温,以及必要的时候如何剪切或旋转。
通过对模拟结果进行分析,可以调整型腔的设计和成型条件。
注塑模设计中冷、热流道技术在Moldflow中的比较分析

注塑模设计中冷、热流道技术在Moldflow中的比较分析尹小定; 赵会娟; 王登化; 丁禹轩【期刊名称】《《吉林化工学院学报》》【年(卷),期】2019(036)009【总页数】7页(P28-34)【关键词】Moldflow; 电器过线板; 热流道; CAE; 冷流道【作者】尹小定; 赵会娟; 王登化; 丁禹轩【作者单位】江西机电职业技术学院材料工程系江西南昌 330013; 济源职业技术学院机电工程系河南济源 459000; 长春工业大学国际教育学院吉林长春130012【正文语种】中文【中图分类】TP391热流道技术是普通注塑模浇注系统上的一项重大改革,它利用加热的办法,使从注塑机喷嘴起到型腔入口这一段流道中的塑料一直保持熔融状态,保证了在开模时只需要取出产品,而不必取出热流道浇注系统,避免了冷流道系统中产生的大量塑料废料,降低了制件的成本[1-3].Moldflow软件提供强大的分析功能,可以对塑料制品和模具进行深入分析,该软件可在计算机上对整个注塑成型过程进行模拟分析,包括填充、保压、冷却、翘曲、纤维取向、结构应力和收缩、以及气体辅助成型分析等[4-7].本文通过电器过线板的具体案例,以Moldflow软件为平台,对比分析采用冷、热流道时产品成型的工艺参数,为塑模热流道技术的推广提供理论支持[8].1 产品前处理及最佳浇口设计1.1 产品的三维造型及前处理电器过线板的结构工程图,如图1所示.图1 塑件结构工程图塑件的外轮廓尺寸为208 mm×109.07 mm×4 mm,壁厚不均,最薄处厚仅为0.44 mm,最厚处为1.0 mm,平均壁厚约为0.56 mm.该产品生产批量为50万,材料为PC+ABS亦称聚碳酸酯与丙烯腈-丁二烯-苯乙烯共聚物塑料合金.该塑件整体上为平板件,不允许表面出现熔接痕、缩孔、缩痕、飞边和平面翘曲变形,总体尺寸要求精度较高.从图1中的局部扩大视图中可知,塑件背面有多个尺寸很小的卡扣结构,该结构对产品成型极为不利,如何选择合适的浇注系统是保证产品成型质量要求的关键.将该产品3D模型转换为STP格式后导入到Moldflow软件中,生成43 170个单元网格,最小网格纵横比值为1.16,最大值为18.32,平均值为2.08,匹配率大于90%达到93.2%,网格模型完全满足模流分析的要求.1.2 最佳浇口设计浇口位置的设定直接关系到熔体到模具型腔内的流动,从而影响聚合物分子的取向和产品成型后的质量[9].利用Moldflow分析,选取最佳位置的结果如图2所示的箭头位置.为使塑件表面不受损伤,增设了小凸台保证脱模时浇口断裂在凸台小端处[10].图2 最佳浇口设计2 基于Moldflow的冷、热流道技术的CAE该塑件材料的成型工艺参数为:熔体温度280 ℃,模具表面温度75 ℃,顶出温度94 ℃,绝对最大熔体温度为360 ℃,最大剪切速率4 000 s-1,最大剪切应力0.4 MPa.2.1 冷流道分析2.1.1 充填时间和充填温度由图3充填时间和充填温度结果可知,熔融的料流从浇口开始进入型腔,分别向周边充填.最后四股料流在中间汇合,充填完成时间为1.060 s.浇口料流温度为283.3 ℃稍高于该熔体温度,到达中间汇合处的温度为257.3 ℃,温度梯降为25.9 ℃.(a) 充填时间(b) 充填温度图3 充填时间和充填温度2.1.2 注射压力和剪切速率由图4所示注射压力和剪切速率分析结果可知,为了充填满型腔,塑料熔体的注射压力为105.7 MPa.为了提高熔体的流动效率,主要是提高充填的温度,在注射压力上并没有太大的提高,但是塑料熔体却受到了很大的剪切,在充填结束时,其剪切速率达到了1.075E+05,远远大于该塑料合金的最大剪切速率4 000 s-1.一般剪切速率大,表观粘度降低,越利于注射,但是过大剪切速率会导致塑料分解[11].(a) 注射压力(b) 剪切速率图4 注射压力和剪切速率2.1.3 冷却时间和收缩率从图5结果分析可知,为了到达该塑料合金的顶出温度,用了10.96 s的冷却定型时间.此时达到顶出温度时的塑件的体积收缩率为6.936%,如图5(b)所示.(a) 冷却时间(b) 收缩率图5 冷却时间和收缩率2.1.4 气穴图6为塑件正、反两面产生气穴的分析结果.在中间最后的料流汇合的位置有气穴,塑件的两端转折处也出现了气穴,还有就是塑件反面的卡扣位置气穴也较多.这些部位困气较严重,容易出现缺胶,在这些部位建议采用排气镶件来解决困气.(a) 正面气穴(b) 反面气穴图6 正、反面产生气穴2.1.5 熔接痕分析评估熔接痕是否影响外观的标准主要有两个:一是熔接痕形成的温度及周围的温度差,二是形成熔接痕的料流汇合角度及是否困气[12].结合图3中的充填温度和图7的分析结果可知,其温度并没有太大的差异,熔接痕呈现十字行,主要是左右和前后两股料流前沿相遇造成的,同时从汇流角度以及结合气穴结果分析,该熔接痕主要因困气造成的可能性也比较大些.图7 熔接痕2.1.6 翘曲分析成型中各种因素导致的翘曲变形分析是CAE软件中求解非线性结果的高性能程序[13].从图8结果可知, X方向的变形为0.205 6 mm,Y方向的变形为0.286 1 mm,Z方向的变形为0.377 4 mm,总的变形为0.429 4 mm.这是一个比较好的翘曲变形值,各向变形结果均小于0.5 mm.(a)总变形(b)X方向(c)Y方向(d)Z方向图8 翘曲分析2.2 热流道分析2.2.1 充填时间和充填温度由图9充填时间和充填温度结果可知,熔融的料流从浇口开始进入型腔,分别向周边充填.最后四股料流在中间汇合,充填完成时间为0.749 8 s.浇口料流温度为263.4 ℃稍高于该熔体的温度,到达中间汇合处的温度为213.4 ℃,温度梯降为50 ℃. 由于温度差降较大,可能会对后续分析带来一定的影响.(a) 充填时间(b) 充填温度图9 充填时间和充填温度2.2.2 注射压力和剪切速率由图10的注射压力和剪切速率分析结果可知,充填满型腔时,塑料熔体的注射压力为113.0 MPa,在压力上稍有提高.充填结束时,塑料熔体的剪切速率为43 127 s-1,大于该塑料合金的最大剪切速率4 000 s-1.但是相对于冷流道时所产生的剪切速率要小很多.这在一定程度上提高了注射效率,同时减少了塑料发生分解的可能性.(a) 注射压力(b) 剪切速率图10 注射压力和剪切速率2.2.3 冷却时间和收缩率从图11(a)结果分析可知,为了到达该塑料制品的顶出温度,用了4.159 s的冷却定型时间.此时达到顶出温度时塑件的体积收缩率为6.177%,如图11(b)所示.(a) 冷却时间(b) 收缩率图11 冷却时间和收缩率2.2.4 气穴图12中为塑件的正、反两面产生气穴的分析结果.出现困气的地方于冷流道浇注系统的位置差不多,但是比较困气的大小可以知道,热流道产生的气穴没有冷流道的大,同时数量上也有所减少,这和充填的料流温度有关,冷流道到的料流温度大,通过模具排气较困难,而热流道的充填料流温度要小,有利于型腔气体的快速排出.但是同样也需要困气部位进行模具结构的镶件设计.(a) 正面气穴(b) 反面气穴图12 正、反面产生气穴2.2.5 熔接痕分析图13的分析结果可知,熔接痕主要呈现中间一字行,由左右各两股料流前沿相遇造成其温度并没有太大的差异,该熔接痕主要因困气造成的,模具结构设计时需要加强排气.图13 熔接痕2.2.6 翘曲分析从图结果可知, X方向的变形为0.246 8 mm,Y方向的变形为0.293 7 mm,Z 方向的变形为0.652 4 mm,总的变形为0.719 8 mm.翘曲变形值相对于冷流道要大出很多,从翘曲产生的原因分析,是料流温差过大造成的,主要是采用的针阀式热流道,该充填方式决定了从浇口到料流末端的温差较大.为减少该塑件的翘曲变形,只需要从Z向的脱模方向进行考虑,加强Z向的平稳脱模,加强中间卡扣部分的均匀推出,是该模具结构设计要考虑的问题[14].综合上述数据进行表1的对比,从结果可知,冷流道的充填相对比较难,因此靠提高塑料熔体的充填温度来提高塑料的流动性能,但是加快了高分子聚合物的相互剪切,使其剪切速率过大,聚合物分解的危险性增大.在充填压力和保压压力上没有提高,但是冷却保压时间却相应的增加.(a)总变形(b)X方向(c)Y方向(d)Z方向图14 翘曲分析采用热流道充填,不需提高充填温度,只增大了充填压力和保压压力,结果体现了熔接痕和气穴方面有减少优势,也避免了剪切速率过大引起聚合物分解的危险性,但另一方面却增大了翘曲变形的趋势.从生产效率上来讲,开模时间为3 s.冷流道生产周期:1.061 s+10.96 s+3 s=15.021 s;热流道生产周期:0.7498 s+4.159 s+3 s=7.908 8 s.热流道的生产效率几乎是冷流道的一倍.另外冷流道还需要去除冷流道凝料和去浇口的时间,热流道无需人工操作,生产效率会有更进一步的提高,自动化程度更高.表1 冷、热流道分析对比结果对比项目冷流道热流道充填时间/s1.0600.7498充填温度/℃283.2263.4充填压力/MPa105.7113.0体积收缩率/%6.9366.117翘曲总变形量/mm0.42940.71983 结论通过电器过线板注塑的具体案例,采用Moldflow分析软件对冷、热流道进行分析对比.结果表明,采用热流道技术虽然使塑件在翘曲分析结果不理想,但是该塑件从尺寸质量上主要控制平面尺寸精度,从脱模结构上采用平稳脱模方式,可极大确保了脱模方向的尺寸精度,同时能实现降低注射温度无聚合物分解的危险,也不需要考虑浇注系统凝料产生的废料和人工费用,大大提高了生产效率.【相关文献】[1] 董祥忠,李年伟,沈洪雷.奥拓轿车前保险杠注塑模浇注系统的CAE分析[J].工程塑料应用,2014,27(12):28-31.[2] 马文静,葛正浩,张凯凯,等.基于Pro/E和Moldflow的键盘框架热流道注射模具设计[J].塑料.2011,40(2):118-121.[3] SODERGAND A,STOLT M.Properties of lactic acid based polymers and their correlation with composition[J].Prog Polym Sci,2002,27(6):1123-1163.[4] 单志,邵会菊,郭建兵,等.基于CAE技术的汽车外饰件翘曲分析及工艺优化[J].塑料,2010,39(3):110-112.[5] 尹小定.基于CAD/CAE技术的控制面板注塑模设计[J].塑料科技,2016,44(6):61-65.[6] 黄先.液晶电视前壳热流道顺序阀进浇方案Moldflow分析[J].塑料工业,2011,39(7):50-52.[7] 尹小定,黄有华,王春燕.CAE技术在咖啡机控制面板冷却系统设计中的应用[J].吉林化工学报,2017,34(5):48-52.[8] 陈进武,曹秩杰,苏庆勇.Moldflow在塑料模热流道技术中的应用[J].塑料工业,2014,42(4):31-34[9] 黄桂坚,洪建明,伍晓宇,等.电梯人口盖板热流道注塑模具设计[J].工程塑料应用,2009,37(8):72-76.[10] 屈华昌,吴梦陵.塑料成型工艺与模具设计[M].北京:高等教育出版社,2007:109-110.[11] 叶东,谭方云.剪切速率在大型塑料注射模设计中的拓展应用[J].模具工业,2005,294(8):27-30.[12] 余玲,陈是德,张诗.CAE在汽车仪表板浇注系统设计的应用[J].塑料科技,2010,38(11):69-73.[13] 谢鹏程,多田和美,杨卫民.高分子材料注射成型CAE理论及应用[M].北京:化学工业出版社,2008:118-119.[14] 尹小定,王登化,赵会娟.电器过线板的热流道注塑模设计[J].塑料科技,2018,46(11):85-89.。
注塑件moldflow模拟报告

最大锁模力为:5600.18t,最大注射压力为:140.00Mpa,最佳浇口位置附近的节点编号为N6888.
最佳浇口位置:
最佳浇口位置
深蓝色部分即为最佳浇口位置。
Fill过程分析结果:
由上图看到,熔体几乎同时到达制品的边缘,说明浇口位置设置合理。
熔体流动前沿温度分布图
可以看出,温度分布基本均匀,温差值为3.3℃,小于允许值20℃,符合注射成
型的要求。
浇口处压力曲线如图所示,不存在压力不稳定现象。
气穴的位置大多数位于制品表面,可通过分型面排掉。
熔接痕位置
孔洞部分附近是必然会产生熔接痕的
Flow分析结果:
缩凹结果
由图可以看到最大缩凹为5.081%,这是由于该处厚度比较大,通过修改厚度,可以减少缩
凹。
锁模力随时间变化曲线
第一主方向残余应力
理论上,残余应力的正值表示处于拉伸状态,负值表示压缩状态,数值越大对产品越不利。
Cool分析结果:
制件冷却时间
从上图可看出,冷却液的出口温度和入口温度差为0.34,说明冷却液的冷却能力没有问题。
冷却管道温度分布
该结果显示了冷却管道温度分布。
这个温度不能高于冷却介质温度的5°C。
由上图可知符
合要求。
制件表面温度。
注塑模流分析报告
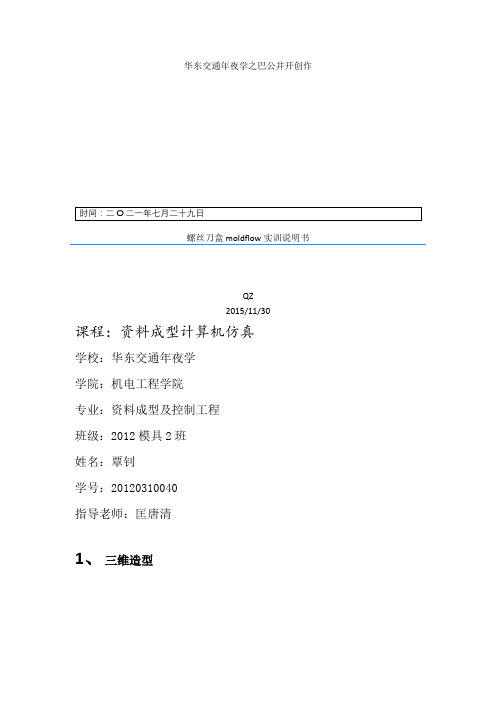
华东交通年夜学之巴公井开创作螺丝刀盒moldflow实训说明书QZ2015/11/30课程:资料成型计算机仿真学校:华东交通年夜学学院:机电工程学院专业:资料成型及控制工程班级:2012模具2班姓名:覃钊学号:20120310040指导老师:匡唐清1、三维造型壁厚均匀,但在盖钩和挂孔处厚度和壁厚相差较年夜,体积收缩率在这两个处所应该会呈现一些问题.主分型面在上概况,正面有卡勾及圆孔,需要做侧抽芯.资料选用普通PP资料.模型建好之后导出为IGES格式.2、模型修复与简化翻开CAD Doctor后导入IGES模型,检查并修复,直到所有毛病都为0,修复完成之后将模型导出,格式为udm格式. 3、moldflow模流分析(1)新建工程,输入工程名称,导入模型,在导入窗口选择双层面.(2)网格划分,网格变长取壁厚的3倍,为4.5mm,合并容差默认为0.1,启用弦高控制0.1mm,立即划分网格,划分之后翻开网格统计,看到网格的基本情况,不存在自由边和多个连通区域的问题后进行下一步.一般来说初始划分的网格纵横比都比力年夜,所以要进行修复.纵横比诊断结果如图3.1.1:最年夜纵横比到达了45.57.点击【网格】——【网格修复向导】,前进到选择目标纵横比,输入6,点击修复.之后在进行手动修复,通过合并节点移动节点等方式进行,直到获得满意的结果.如下图3.2.1:修复后的纵横比为13.68,只呈现少数,可以接受.修复后的网格统计如下图3.2.2:由统计结果知,匹配率都到达了91%以上,合理.重复上述方案并冲命名为【浇口位置确定】,设置分析序列为【浇口位置】,选择资料为默认的PP资料(由于产物上信息为PP,且没有太高使用要求故选用默认的PP资料),该资料的推荐工艺如下图 3.3.1:最年夜剪切速率为100000(1/s),最年夜剪应力为0.25MPa.分析并等候结果,获得最佳的浇口位置如下圈出的位置由于该零件比力小,需要年夜批量生产,故应做成一模多腔的形式,且考虑到美观的问题,浇口应设置在边缘位置,做成侧进浇,如下图3.3.3和3.3.4:方案1:方案2:考虑过双浇口,可是快速成型分析发现双浇口的熔接痕比单浇口的要多,成型质量也相差无机.因此放弃,综合考虑之下选择这两个方案进行比较.【充填时间的分歧】:方案一为1的充填时间为1.151秒,方案二的充填时间为1.135秒,相差不年夜.【压力之间的比较】方案一为38.26MPa,方案2为36.68,方案二的压力更小一些.到达顶出温度的时间比较:方案一为22.40秒:方案二为24.40秒,方案2要更多2秒.方案一更优.【熔接痕的比较】方案一的:然后方案二的:从图中可以看出方案2的熔接线更少,呈现的位置也不是很影响美观,因此方案2更优.但总体来说两个方案是差未几的.相差不年夜【气穴】方案一的:方案二的:从此处可以看出方案2的气穴更多,方案一更优.但总的来说,畴前面分析结果来看,两个方案的结果相差都不太年夜,因而下面先检验考试着用方案一进行下面的分析工作.(1)复制上述方案重命名【成型窗口】,并设置分析序列为【成型窗口】(2)设置工艺条件:注塑机最年夜注塑压力为140MPa,高级选项如图3.4.1.(3)获得结果:最年夜剪切应力3.4.3(远小于资料的0.25MPa,可以接受)区域切片图3.4.4,因此可以选择注射时间为1S.因此,选用此方案,模具温度为42(42.2)°C,熔体温度为250(249.5)°C.(1)复制上方案并命名为【充填分析】,设置分析序列为充填,(2)设置工艺参数:模具温度42°C,熔体温度250°C,注射时间1s,【速度/压力切换】设置为【由%充填体积】,取值99%,其他取默认值.(3)分析结果:充填时间图3.5.1:可看出等值线的间距基本一致,说明料流前锋的前进速度一致.壁上最年夜剪切应力,图3.5.2,均小于资料的许用最年夜剪切应力0.25,注射位置处的压力,图3.5.3,最年夜为38.25MPa.最年夜锁模力为20.8吨,均发生在速度/压力切换的时候.(1)复制上方案偏重命名为【流道系统】(2)设置浇注系统,因为结构比力简单,不需要手工创立浇口和流道,因此利用型腔重复向导,设置一模两腔,列间距设置为200,如图 3.6.1.(UG8.0注塑模向导中初始化后一个模具内工件长为195,因此取200).之后下一步,分流道按表8-1,查的直径为5-10mm,取6mm,计算得主流道直径为7.56mm,长度依据模具模架取60,拔模角去2.4deg(取值范围1-3deg),浇口为直浇口,入口直径为3mm,长度为1.5mm,拔模角2.4deg,点击完成,如图3.6.3、3.6.4.获得流道系统如图3.6.5.通过连通性诊断无误后准备进行下一步【流道平衡分析】.因为是边缘浇口(标准浇口),设置在分型面上,所以浇口形状应为矩形.复制上方案,设置分析序列为【流道平衡】充填控制选为自动,压力选择38MPa.分析结果如下图3.6.8:优化为分流道的体积更改-12.58%,说明流道设计比力合理.注射处压力最年夜为42.64MPa.(1)复制上方案偏重命名【冷却分析】,设置分析序列为冷却.(2)设置冷却系统由于模型工件结构简单、规则,方方正正,没有年夜的曲面,因此采纳冷却回路向导设计冷却回路.指定水管与直径为10mm,其他选择默认.管道数量设置为4,如图 3.7.1.获得冷却回路(图3.7.2)并进行分析.设置的参数如下图.目标温度为42°C,因此设置水温为25°C,分析后获得结果:管壁温度为29.14,和水温温度差小于5°C,合理,回路管壁温度如下图3.7.5:零件到达顶出温度的时间为25.78s,所以IPC时间设置为26S.复制上述方案重命名【填充+保压】,进行恒温保压分析.由前面的分析结果可知最年夜注射压力为44.68MPa,所以初涉保压压力设置为44.7MPa,保压时间=IPC时间25s-充填时间1s=25s,保压工艺设置如下图.分析后得召盘出时的体积收缩率最年夜为12.54%,壁厚为1.5mm的PP塑料制件体积收缩率范围应在1.39%到5.43%之间,此方案的体积收缩率局部过年夜,需要改善,再根据结果取合适的方案.由图可知到达最年夜压力时间为2.76s,凝固时间为5.28,取中间值4s为恒压/降压转换点,检查分析日志,压力/速度转换时间为1.12s,因此第一段恒压保压时间为2.9s,检查解冻层因子,发现浇口在14s时解冻.进行优化后的结果如下:压力XY图优化后的压力XY图曲线发生了明显的变动,制件年夜部份的体积体积收缩率颜色相近可以看出体积收缩更为均匀,可是制件厚度较年夜的处所的最年夜的收缩率仍在11.78%,仍需要进一步优化.其他条件不变,将保压压力提高到65MPa,体积收缩率仍没有改善,反而下限更年夜,因此排除是保压压力的因素影响,此处不再贴出图片.顶出时的体积收缩率:最小不小于0,最年夜仍为12.42,可见优化有效,可是制件最厚的处所的收缩率仍然无法获得年夜的改善.原因可能是因为该处比制件年夜部份壁厚要厚很多且在充填末端,无法防止.检验考试过很多种方法,仍然无法获得明显的改观.因此,检验考试着再次更改浇口位置,再次检验考试方案二.4、再次检验考试方案22(1)复制上述方案二重命名【成型窗口】,并设置分析序列为【成型窗口】(3)获得结果:区域切片图最年夜剪切应力,图4.1.3,远小于资料许用应力,合理2(1)复制上方案并命名为【充填分析2】,设置分析序列为充填,(2)设置工艺参数:模具温度42°C,熔体温度250°C,注射时间0.6s,【速度/压力切换】设置为【由%充填体积】,取值99%,其他取默认值.(3)分析结果:壁上剪切应力:小于资料的许用应力0.25,图4.2.1,合理.压力:37.54为注射位置处最年夜压力.到达顶出温度的时间:检查其他各项,没有分歧理的处所,进行下一步.2年夜体步伐如前面 3.6流道系统与平衡分析,不再赘述,只讨论分析结果.注射位置处的压力最年夜注射压力为42MPa.剪切应力方面:,可知远小于资料的0.25,合理.可知系统将分流道的体积缩小了12.5%,优化结束.进行下一步——冷却系统的分析.冷却液温度依然设置为默认的25°C,获得结果图4.4.2:1型腔温度数据型腔概况温度平均值为42.8744,与模具温度非常接近,非常合理.温差不超越2℃,合理.3回路管壁温度:最年夜为29.04℃,也不超越冷却液入口温度5℃,合理.2然后进行分析,获得结果如下,图4.5.4:1顶出时的体积收缩率:到达了12.97%,主要仍然集中在制件最厚的处所以及浇口处.该PP资料制件体积收缩率范围(1.5mm)应在1.39%到5.43%之间,明显需要进行优化.2压力XY图:体积收缩率过小的处所,说明该处过保压,制件较厚处收缩率年夜,说明保压补缩不够,还需要提高保压压力.(2)保压优化方案1:将保压压力设置为40MPa,其他参数不变,分析获得结果:最年夜的收缩率降低到9.275,但最小的体积收缩也呈现了-0.636,说明过保压加剧了.检验考试其他方案:将压力分别设置成:方案2为60MPa、方案3为75MPa,其他参数不变,依次分析获得结果.还是未能到达要求.通过比较数据发现在40-75MPa的范围内,压力越年夜,体积收缩率约小,但同时也会呈现负收缩越来越年夜的情况,也就是过保压越来越严重.综合比对,最终选择以40MPa为恒压保压压力.而且通过创立保压曲线并优化,以缩小制件上主体积的收缩率的不同.尽可能实现均衡收缩.压力XY图如下通过分析,充填末端在2.5s时到达最年夜, 5s的时候为0,取中间值 3.8s作为恒压/降压转换点.检查解冻层因子结果,获得浇口在15s处解冻.速度压力时间切换为0.66s,由此确定第一段恒压保压时间为3.1s,第二段卸压时间为12.2s.设置参数如图:获得的结果如下:最年夜的体积收缩率为9.798,最小为0.0650,(壁厚为1.5mm的收缩率应在1.39%到5.43%之间,壁厚为5mm的收缩率应在 1.71%到 6.75%之间)没有过保压现象.主要问题还是集中在制件较厚的处所还有浇口附近,但相比之前的方案获得了很年夜的改善,且收缩率年夜的区域十分小,制件主体的收缩率也很均衡.如果要改善浇口附近制件较厚处的收缩率过年夜的情况,那么就要增年夜保压压力,可是通过分析可以发现这样会使其他区域的收缩率年夜年夜降低,而且区域会想当年夜,甚至很多区域会呈现过保压的情况.制件主体部份也会受到影响.所以到此保压优化完成,最终确定使用此方案.2翘曲分析与优化是分析流程的最后一个步伐,充填、冷却、保压这三个因素都是翘曲变形的主要因素.翘曲分析结果的好坏说明前面工作的质量.若翘曲变形过年夜,则需要重新对前面的方案进行优化.分析后的结果:所有因素:可以看到在正面的孔洞处的变形为0.28mm,其他各个处所的变形都很小,图4.6.1变形,所有因素图4.6.2 变形因素Y方向X方向:变形量为0.1761,变形量较小.图4.6.3 变形因素X方向图4.6.4变形,冷却不均图4.6.5变形,收缩不均取向因素:图4.6.6变形,取向因素从上面的结果可以得出,变形量主要是由于收缩不均匀引起的,接近总的变形量.由上图可以分析得出,收缩不均匀的处所是注射末端以及制件厚度突变的卡扣处和侧孔,而引起收缩不均匀的原因一部份是制件厚度其实不是一致,以及保压方面的问题.总之还是不成防止地引起了翘曲变形,但总体来说变形量不算很年夜,可以接受.5、总结分析(最终方案)浇口位置应设置在如下图圈出的位置处.选用一般的PP料.主流道直径为7.56mm,拔模角 2.4度,长度60mm.分流道直径为6mm,模具资料选用P20;模具温度:42℃;熔体温度250℃,开模时间5s,注射时间0.6s,保压压力为40MPa,保压控制如下,【注射+保压+冷却时间】设置为25s.水管直径为d=10mm,水管与零件间的距离为25mm,水管与零件排列方式为沿X方向.冷却介质选用纯水,冷却介质入口温度设置为25℃.流动类型为层流,所以雷诺数Re设置为2000.查表得纯水在25℃时的密度为ρ=0.997kg每平方毫米,粘度为η=0.8937N*s每平方毫米,冷却液平均流速U=Re*η/(ρd)=17.928mm/s=0.17928m/s取0.18米每秒.6、致谢非常感谢匡老师,不辞辛劳地解答各种疑问.现在看来,现在的问题很多都问得甚至是相当的愚蠢,例如纵横比修复和优化这种比力初级问题,但匡博还是手把手教到会为止,不胜忸捏.很难想象匡博这样的忙人,怎样抽出时间,才华录制了近十五个小时的教学视频,孜孜不倦地一点一点地教会,再简单再细小的细节也没有略过,语言已经无法来形容这种敬业的态度,五体投地也不能.甚至在有些视频里甚至可以听得出匡博是感冒了的,声音明显变了,还咳嗽……这种情况下老师依然给我们录制视频.有此良师,只能说三生有幸.7、感受与建议总体来说,这个课设总算是亲力亲为一步一个脚印做下来了,不竭地重复和更改,花了年夜量的精力去优化和改进,最终才获得相对满意的结果,然而并没有做到完美,有比力细小的处所仍然是无法优化,累觉不爱.在这个设计和分析的过程傍边,就是不竭地检验考试,修改,得出结果,比对,在检验考试在修改再比对,不竭地循环不竭的改进.每个方案,每个数据,都是亲力亲为,用心血写成,虽然到最后还是得不到最满意的结果,但看着自己的功效还是有小小的成绩感.在这个课设里,最年夜的感触就是,行就是行,不成绩是不成,没有“年夜概可以了”“差未几”的说法,要求的就是一丝不苟,精益求精.有时候,为了百分之几的数据,都要进行数十次的检验考试优化,虽然相差不是太年夜,但更好就是更好,获得更优解总会让人欣慰.收获还是有的,对这款软件的认识和掌控基本上已经进入了入门阶段,有了一定的理解和认知,这对以后走更远的路来说,起码我已经迈出了7、8个法式.很喜欢这种讲课之后马上实践的模式,课堂上讲理论和注意事项,机房入手,防止走弯路,上手更快.接受起来也比力快.建议的话,感觉要是上机课再多一些比力好,理论:实践的比例在1:2这样,把持更多一些,在把持中发现问题并及时解决会有更好的效果.固然因人而异,这只是个人观点.以上,为所有陈说内容.目录1、三维造型12、模型修复与简化23、MOLDFLOW模流分析24、再次检验考试方案220时间:二O二一年七月二十九日5、总结分析(最终方案)346、致谢377、感受与建议37时间:二O二一年七月二十九日。
moldflow 注塑成型分析 模流分析报告

1. 熔体密度 2.实体密度 3.顶出温度 4.推荐模具温度 5.推荐熔料温度 6.材料失效温度
0.88 g/cu.cm 1.06 g/cu.cm
119 deg.C 45 deg.C 225 deg.C 290 deg.C
7. 熔料温度下限 8. 熔料温度上限 9. 模具温度上限 10.模具温度下限 11.最大剪切速率 12.最大剪切应力
Page 8
体积收缩
体积收缩结果用来判断产 品各处的体积收缩情况,收 缩不均匀会造成翘曲变形, 收缩较大则造成缩痕。 由图可见产品内部收缩较小, 且比较均匀。出现缩痕风险 小。
Page 9
困气位置
1
Air traps可提供模具的困气位 置。air traps产生在填充末端包 括高rib和boss柱位置、结合线、 流动包封位置。故而在这些位置 一般需要开设排入槽或排气入子。 另外在熔体温降较大处也应增加 排气,提高流动性。
pagepage1919尾部分子剪切作用较高故而分子取向度高并且分子结晶度高取向诱导结晶在取向方向上收缩较大故而收缩应力导致产品尾部收拉力而张开变形
Moldflow注塑成型分析
For
滨海
Reporter : 孟栋梁 sduan@
2010-07-16
分析描述
▪ 产品描述 此是汽车用产品,使用热浇道系统注射成型。
200.0 deg.C 250.0 deg.C 30.0 deg.C 60.0 deg.C 100000.0 1/s
0.25 Mpa
PVT Plow材料数据库
Page 3
工艺条件
注塑机设定:
最大锁模力:
未限定
最大注塑压力:
未限定
最大注射速度:
结合线
Moldflow注塑模具成型过程分析实例_完整经典

冷却+流动+翘曲分析 实验报告一、 问题描述用Moldflow分析如图1所示产品在注塑过程中的冷却(Cool)、流动(Flow)、翘曲(Warp)情况。
图1 分析产品模型其中,相关参数设置如下:材料:Generic PP:Generic Default模具温度:40℃料温:230℃开模时间:5S填充+保压+冷却时间:参数值为30SFilling control: AutomaticVelocity/pressure switch-over: By %volume filled 设置为97%选中Isolate cause of warpage二、 问题分析按照Moldflow的一般分析过程,本产品的分析流程图如图2所示。
图2 本产品分析流程图三、 解题步骤1.导入产品模型点击File→Import,选取待分析的产品模型,点击“打开”。
在弹出的“模型导入选项设置”对话框中,网格类型选“Fusion”,模型单位设置为“Millimeters”。
单击“OK”完成设置。
此时弹出“项目创建”对话框,在“Project”一栏设置项目名称,本实验取名为“CFW”。
在“Create in”一栏选取项目保存地址。
单击“OK”完成项目创建。
此时,窗口中会显示出导入的模型。
以防分析中修改变动,习惯先对模型进行复制。
对着左上角“Project”栏内的模型名称,在右击菜单中选择“Duplicate”,完成模型复制。
其后操作都在复制的模型中进行。
一般在做流动分析时,要求产品锁模力方向(一般也为产品分型面的垂直方向)与Z轴的正方向一直。
此时的模型位姿不对(如图3所示),需要用旋转命令对模型进行旋转操作。
执行Modeling→Move\Cope→Rotate,在左侧选项栏中,点击“Select”一栏的选框,其意思为选取旋转对象,框选产品模型。
“Axis”一栏选取X轴。
“Angle”填写90。
选取“Move”,其他不变。
点击“Apply”。
快速热循环注塑成型过程数值模拟与工艺参数优化研究的开题报告

快速热循环注塑成型过程数值模拟与工艺参数优化研究的开题报告尊敬的评审专家:我所选课题为“快速热循环注塑成型过程数值模拟与工艺参数优化研究”,以下为开题报告。
一、研究背景及意义注塑成型是一种重要的塑料加工技术,广泛应用于制造各种工程塑料制品。
快速热循环注塑成型是一种新兴的注塑技术,它在原有注塑成型工艺的基础上引入了快速热循环和先进的生产设备,在制造高质量、高复杂度的塑料制品方面具有明显的优势。
由于热循环时间短、注塑周期快、温度分布均匀等特点,可以大幅度提升制品的品质和生产效率。
然而,快速热循环注塑成型也存在一些问题,如加热系统控制不精确、喷嘴设计不合理、制品表面质量不稳定等。
这些问题需要通过数值模拟和工艺参数优化来解决,提高制品的质量和稳定性。
因此,开展快速热循环注塑成型过程数值模拟与工艺参数优化研究具有重要现实意义。
二、研究内容和研究方法本研究的主要内容包括:建立快速热循环注塑成型的数值模拟模型、验证模型的准确性、优化工艺参数以提高制品的品质和生产效率。
数值模拟模型的建立将采用计算流体力学(CFD)方法,考虑了快速热循环、注塑压力、熔体流动、固化过程等因素。
在模型的基础上,将进行流场、温度场、应力场的计算和分析,以评估制品质量和加工效率。
模型验证将分别采用位移传感器、光学三维扫描仪等工具来实现。
优化工艺参数将考虑注塑压力、温度、速度、固化时间等因素,采用响应面分析和遗传算法等数学方法实现。
三、研究进度和预期成果目前,已完成了快速热循环注塑成型过程数值模拟模型的建立和初步验证。
下一步将进行模型的改进和验证,进一步完善模型的精度和可靠性。
同时,还将开展工艺参数优化的研究工作,以验证模型预测结果,提高制品的质量和生产效率。
预计本研究将取得以下成果:1、建立快速热循环注塑成型的数值模拟模型,并验证模型的准确性。
2、优化工艺参数,提高制品的品质和生产效率。
3、在理论研究的基础上,开发出适用于快速热循环注塑成型的新型注塑设备和加热控制系统。
注塑模浇注流道系统——热流道成型工艺简单介绍

注塑模浇注流道系统——热流道成型工艺简单介绍一什么是热流道?理想的注塑系统应形成密度一致的部件,不受所有的流道、飞边和浇口水口的影响。
相对冷流道来讲,热流道要做到这一点,就必须维持材料在热流道内的熔融状态,不会随成形件送出。
热流道工艺有时称为热集流管系统,或者称为无流道模塑。
基本来讲,可以把热集流管视为机筒和注塑机喷嘴的延伸部分。
热流道系统的作用就是把材料送到模内的每一浇口。
二、组合式热流道系统优势多热流道系统作为模具系统的一个常用部件,能够有效地提高塑料制品的质量、提高生产效率,并使资本的投入得到更高的回报。
现在,一种新型的组合式热流道系统闪亮登场,它又会给我们带来哪些惊喜呢?今天,嵌件成型技术、共注射成型技术以及多组分注塑成型技术都离不开热流道的支持。
大量的部件诸如汽车保险杠等因为流动路径的限制、壁厚的比率以及熔合缝问题而只能采用热流道模具进行加工成型。
在注射成型中,热流道系统所扮演的角色越来越重要。
尽管热流道和注射模具是一个整体,然而它的作用和功能与模具本身相比是完全不同的。
对于系统组成的独立单元,其安装、连接和运行都有特殊的高精度的位置要求。
由于这些原因,热流道系统的装配就成为模具安装的一个瓶颈。
因此,避免热流道系统安装过程中的错误以及简化系统连接并节约装配时间就成为一个很重要的课题。
三、常规的热浇道设计热浇道系统源于热流道系统。
通常,喷嘴不一定总是安装在分流板上,也可以虚连在喷嘴法兰上,但是这类系统需要固定板以保持系统的一体性。
对于大多数塑料加工过程来说,由于模具的温度接近200℃,所以在热流道与模具之间存在着温度差异。
如果系统被连接在模具板上,将会升高温度并增加热量的损失,并且在分流板和喷嘴之间也可能产生流动*角。
当热流道需要维修时,热浇道必须完全从模具上拆除。
由于喷嘴没有连接到分流板上,电气和液压线路必须完全拆开,并在检修结束后再进行连接。
四、组合式热流道系统在组合式热流道系统中,喷嘴、分流板形成了一个简单的单元。
注塑热流道工艺流程
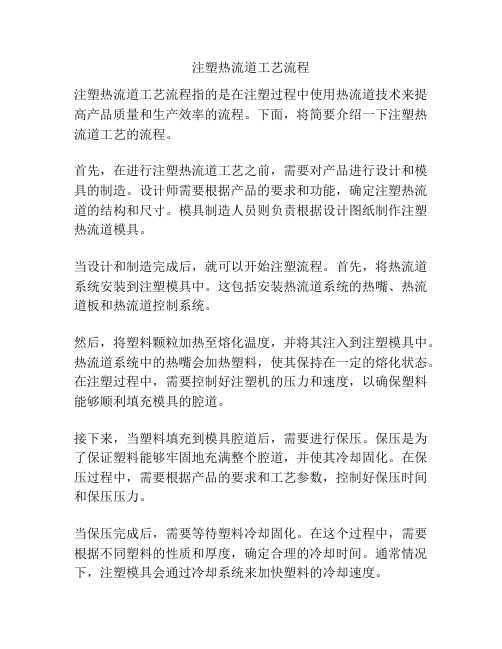
注塑热流道工艺流程注塑热流道工艺流程指的是在注塑过程中使用热流道技术来提高产品质量和生产效率的流程。
下面,将简要介绍一下注塑热流道工艺的流程。
首先,在进行注塑热流道工艺之前,需要对产品进行设计和模具的制造。
设计师需要根据产品的要求和功能,确定注塑热流道的结构和尺寸。
模具制造人员则负责根据设计图纸制作注塑热流道模具。
当设计和制造完成后,就可以开始注塑流程。
首先,将热流道系统安装到注塑模具中。
这包括安装热流道系统的热嘴、热流道板和热流道控制系统。
然后,将塑料颗粒加热至熔化温度,并将其注入到注塑模具中。
热流道系统中的热嘴会加热塑料,使其保持在一定的熔化状态。
在注塑过程中,需要控制好注塑机的压力和速度,以确保塑料能够顺利填充模具的腔道。
接下来,当塑料填充到模具腔道后,需要进行保压。
保压是为了保证塑料能够牢固地充满整个腔道,并使其冷却固化。
在保压过程中,需要根据产品的要求和工艺参数,控制好保压时间和保压压力。
当保压完成后,需要等待塑料冷却固化。
在这个过程中,需要根据不同塑料的性质和厚度,确定合理的冷却时间。
通常情况下,注塑模具会通过冷却系统来加快塑料的冷却速度。
最后,在完成冷却固化后,可以打开注塑模具,取出成型的产品。
然后,进行产品的修整和加工,使其达到设计要求。
根据产品的要求,可能还需要进行一些表面处理,如喷漆、丝印等。
总之,注塑热流道工艺流程是一个复杂而精细的过程。
只有在合理的设计和正确的操作下,才能生产出高质量的注塑产品。
通过使用热流道技术,不仅可以提高产品的质量和生产效率,还可以减少废品率和材料浪费,为企业带来更大的经济效益。
注塑热流道工艺流程

注塑热流道工艺流程首先,确定产品设计和模具结构。
根据产品的尺寸、形状和要求确定模具的结构设计,包括模具尺寸、注射系统、热流道系统等。
然后,进行模具加工和组装。
根据设计图纸进行模具零件的加工,包括铣削、刨削、钻孔、车削等工序。
然后将加工好的模具零件进行组装,以得到完整的注塑模具。
接下来,进行热流道系统组装和调试。
根据模具设计,将热流道系统的各个零件进行组装,包括热流道板、热流道嘴、加热管等。
然后进行系统的调试,通过调整温度、压力、流量等参数,确保热流道系统能正常工作。
然后,进行材料预处理。
将塑料原料进行加热和干燥处理,以去除杂质和水分,并使其达到适合注塑加工的熔融状态。
接着,进行注塑机调试。
将已组装好的注塑模具安装到注塑机上,并根据产品要求设置注射参数,如注射压力、注射速度、保压时间等。
通过注塑机的操作界面进行参数设置和调试,以确保注射过程的稳定性。
之后,进行试模和调整。
在注塑机的运行下,进行试模操作,注入塑料熔融料到模具腔内,融合成产品。
根据试模的结果,对注射参数进行调整,以使得产品能够满足设计要求,如尺寸精度、外观质量等。
最后,进行正式生产。
在试模调整完毕后,根据产品批量需求,进行正式生产。
在生产过程中,对注射参数、热流道温度等进行监控和调整,以确保产品质量的稳定性和生产效率的高效性。
总结起来,注塑热流道工艺流程包括产品设计和模具结构确定、模具加工和组装、热流道系统组装和调试、材料预处理、注塑机调试、试模和调整、正式生产等环节。
通过科学的流程和合理的操作,在注塑热流道工艺中可以实现高质量、高效率的生产。
注塑热流道系统的优缺点与常见问题分析及解决方法
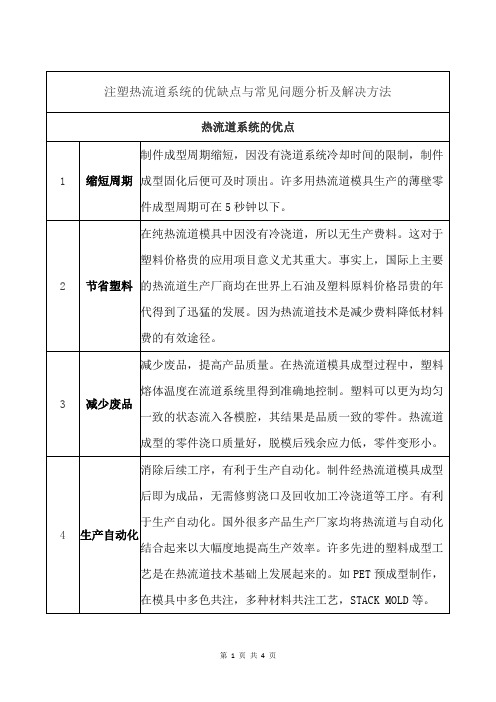
热分流板补偿塞漏胶
无垫块。
安装垫块。
7
油(气)缸不工作
无空气/液压油进入缸体内,气动/液压缸系统卡住,系统压力不足。
检察管路、泵是否有泄漏、堵塞现象,检查缸体及活塞配合检查进给管路是否过分弯曲,活塞及阀针是否灵活。
8
缸体系统被咬死
缸体、热分流板、热喷嘴等不同心,定模固定板(底板)积过多。
调整缸体、分流板、热喷嘴同心度在缸体周围增加冷却。
3
减少废品
减少废品,提高产品质量。在热流道模具成型过程中,塑料熔体温度在流道系统里得到准确地控制。塑料可以更为均匀一致的状态流入各模腔,其结果是品质一致的零件。热流道成型的零件浇口质量好,脱模后残余应力低,零件变形小。
4
生产自动化
消除后续工序,有利于生产自动化。制件经热流道模具成型后即为成品,无需修剪浇口及回收加工冷浇道等工序。有利于生产自动化。国外很多产品生产厂家均将热流道与自动化结合起来以大幅度地提高生产效率。许多先进的塑料成型工艺是在热流道技术基础上发展起来的。如PET预成型制作,在模具中多色共注,多种材料共注工艺,STACK MOLD等。
3
热分流板温度不稳定
热电偶接触不良。
检查热电偶。
4
熔体中存在金属碎片
注塑机螺杆上的碎片,注塑材料中的金属碎片
清除金属碎片修补螺杆过滤塑料中的杂质。
5
热分流板与热喷嘴结合面漏料
膨胀量计算不对,W面加工高度不一致,定模固定板(底板)材料太软,热分流板短时间温度太高,“O”型密封圈安装有问题。
重新计算并检查膨胀量,检查修正W面高度,更换有适当硬度的定模固定板(底板),更换已损坏的零部件及“O”型密封圈
9
缸体过热后卡死
缸体、热分流板、热喷嘴等不同心,定模固定板(底板)积热过多垫片与阀针固定螺帽产生摩擦。
注塑成型模拟分析
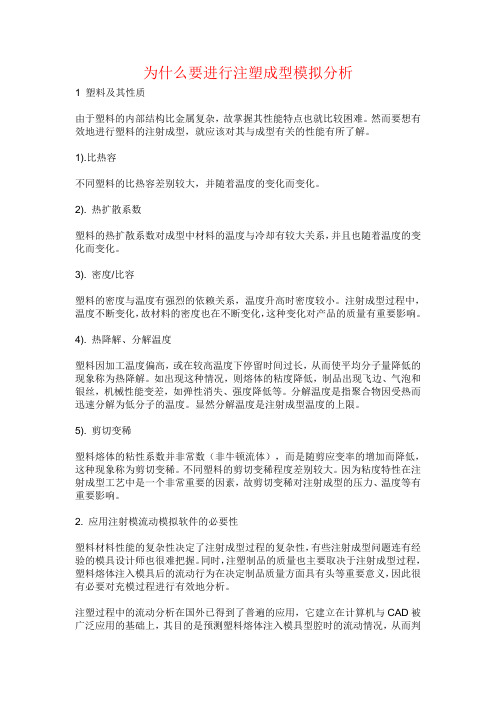
为什么要进行注塑成型模拟分析1 塑料及其性质由于塑料的内部结构比金属复杂,故掌握其性能特点也就比较困难。
然而要想有效地进行塑料的注射成型,就应该对其与成型有关的性能有所了解。
1).比热容不同塑料的比热容差别较大,并随着温度的变化而变化。
2). 热扩散系数塑料的热扩散系数对成型中材料的温度与冷却有较大关系,并且也随着温度的变化而变化。
3). 密度/比容塑料的密度与温度有强烈的依赖关系,温度升高时密度较小。
注射成型过程中,温度不断变化,故材料的密度也在不断变化,这种变化对产品的质量有重要影响。
4). 热降解、分解温度塑料因加工温度偏高,或在较高温度下停留时间过长,从而使平均分子量降低的现象称为热降解。
如出现这种情况,则熔体的粘度降低,制品出现飞边、气泡和银丝,机械性能变差,如弹性消失、强度降低等。
分解温度是指聚合物因受热而迅速分解为低分子的温度。
显然分解温度是注射成型温度的上限。
5). 剪切变稀塑料熔体的粘性系数并非常数(非牛顿流体),而是随剪应变率的增加而降低,这种现象称为剪切变稀。
不同塑料的剪切变稀程度差别较大。
因为粘度特性在注射成型工艺中是一个非常重要的因素,故剪切变稀对注射成型的压力、温度等有重要影响。
2. 应用注射模流动模拟软件的必要性塑料材料性能的复杂性决定了注射成型过程的复杂性,有些注射成型问题连有经验的模具设计师也很难把握。
同时,注塑制品的质量也主要取决于注射成型过程,塑料熔体注入模具后的流动行为在决定制品质量方面具有头等重要意义,因此很有必要对充模过程进行有效地分析。
注塑过程中的流动分析在国外已得到了普遍的应用,它建立在计算机与CAD被广泛应用的基础上,其目的是预测塑料熔体注入模具型腔时的流动情况,从而判断熔体流动给注塑件质量带来的影响。
流动模拟软件的应用主要包括三个方面:第一是利用软件来预计所设定注塑方案的压力、温度等的分布;第二是利用预计的压力、温度等的分布来改善模具和塑料制品的设计;第三是对多个候选的注塑方案进行比较优化,选择最佳方案。
泵体模流分析
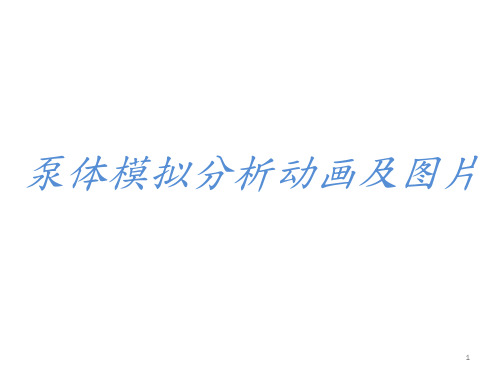
氧化夹渣
22
氧化夹渣
12
方案二工艺参数:
类型 熔汤 压室中金属液的温度 模具材料
冲头速度
零件体积 内浇口速度
冲头直径 模拟软件
参数 ADC12 660℃ dievar 低速速度 : 0.1m/ s 高速速度: 0.1m /s 708899.1079mm3 40m/ s 90mm AnyCasting
13
整体充型过程仿真结果
7
最后凝固部位:
8
粒子追踪过程仿真结果
双击图片播放
溶体流动分布均匀情况
9
料液追踪过程仿真结果
料液追踪动画
不同浇口流出的熔体用不同 的颜色显示。我们可以根据 这一结果方便地优化流道和 浇口设计
双击图片播1放0
模具侵蚀结果
模具侵蚀(红色部位)的分析研究了侵蚀率 与冲击角度和冲击速度的关系,给出充型时 模具侵蚀的结果。我们可以根据这一结果优 化流道、浇口及模具的设计,提高模具11寿命。
18
粒子追踪过程仿真结果
双击图片播放
溶体流动分布均匀情况
19
料液追踪过程仿真结果
料液追踪动画
不同浇口流出的熔体用不同 2放0
模具侵蚀结果
模具侵蚀(红色部位)的分析研究了侵蚀率 与冲击角度和冲击速度的关系,给出充型时 模具侵蚀的结果。我们可以根据这一结果优 化流道、浇口及模具的设计,提高模具21寿命。
泵体模拟分析动画及图片
1
方案一工艺参数:
类型 熔汤 压室中金属液的温度 模具材料
冲头速度
零件体积 内浇口速度
冲头直径 模拟软件
参数 ADC12 660℃ dievar 低速速度 : 0.2m/ s 高速速度 : 2 m /s 708899.1079mm3 40m/ s 90mm AnyCasting
- 1、下载文档前请自行甄别文档内容的完整性,平台不提供额外的编辑、内容补充、找答案等附加服务。
- 2、"仅部分预览"的文档,不可在线预览部分如存在完整性等问题,可反馈申请退款(可完整预览的文档不适用该条件!)。
- 3、如文档侵犯您的权益,请联系客服反馈,我们会尽快为您处理(人工客服工作时间:9:00-18:30)。
3 . ; n h xmu ne t n pe s r e urdb ne t ns se s2 .5MP . h d pin 26t a d tema i m ijci rsu erq i yijci y tm i 5 1 a T ea o t o e o o
p o u t Th h t u n r y t m i b te t a t e od u ne s se rd c. e o r n e s se s et r h n h c l r n r y t m i e e g s v n a d n n ry a ig n
c n u to e u t n a d i o rn r d ci n c s. o s mp i n r d c i n n l we i gp o u to o t o
第2 4卷 第 3期
2 0在 01
五 邑大学学报 ( 自然科学版 )
J R AL F OU N O r U VE ST ( trl c n e dt n YI NI R IY Na a u S i c E io 1 e i
V_.4 No3 0 2 1 .
Au . g 2 0 0l
冻 结 时 间 在 泵体 法 兰 凹 槽 处 最 长 , 大翘 曲量 位 于 泵 体 法 兰 底 部 , 模 系统 所 需 最 大 锁 模 力 为 最 合 3 . t 注 射 系统 所 需 最 大 注 射 压 力 为 2 . a 26 , 51 MP ,采 用 三 排 管路 冷 却 系 统 可 以 有 效 降低 泵体 制 5 品 成 型 加 工 后 的 最 高 温 度 ,热 流 道 系统 在 节 能 降耗 、 降低 生 产 成 本 等 方 面 比 冷 流 道 优 越 .
关 键 词 : 泵 体 ; 热 流 道 ; 注 塑 成 型过 程 ;模 拟
中 图 分 类 号 : H1 2 T 2
文 献 标 志码 : A
S mua ino eHo n e n e t nMod n r c s rt eP mpB d i lt f h t o t Ru n rI j ci l igP o e s o u o y o f h
A sre:S muain o h o u n rijcin modn rc s ft e p mp u i g MP ot ae b ta t i lt fte h trn e ne t lig p o e so h u sn Isf r o o w
s o h tp a i g t e g t n t e c n e ft e p mp b d o e c n a h e e e u lb i m iln ;t e h wst a lc n h a e i h e t ro h u o y c n a c i v q ii ru fli g h ma i m o u ti h i k g a e a d t e p o u tma i u t mpe au e o c ri h mp c n ; x mu v l me rc s rn a e r t n h r d c xm m e r t r c u n t e pu o e t e p o u tsfe zn i st e lng s n t ep m p b d sfa g r o e ; h xm u wa p g s h r d c ’ r e i g tme i h o e ti h u o y’ n e g o v s t e ma i m r a ei l
K yw rs tep mpb d ; o u n r ijcinmodn r c s; i lt n e od :h u o y h t n e ;ne t ligp o e s smuai r o o
a h ot m ft e pu a g ;t e ma i m lmpig f r e r q ie y t e c a i g s se i tt e b to o h mp f n e h x mu c a l n o c e u r d b h l mp n y tm s
o h h e - o i e c oi g s s e c n e e tv l e u e t xm u t mp r t r f te p mp ft e t r e r w p p o ln y tm a f ci ey r d c he ma i m e e a u e o h u
DU ya - e LI O XU . U T a in—ii e
(c o l f e tia n c a ia E gn eig Wu iU iest, in me 2 0 0 C ia S h o cr l d Me h nc l n ie rn , y nv ri Ja g n5 9 2 , hn ) o El c a y
8月
文 章编 号 :1 0 .3 2 ( 0 0 30 0 . l 0 67 0 2 1 )0 .0 6O
泵体 的 热 流 道 注塑成 型 过 程模 拟分 析
杜 遥 雪 , 柳 天 磊
( 邑大学 机 电工程 学院 ,广 东 江 门 5 9 2 五 2 0 0) 摘 要 :利 用 MP I软件 对 泵体 的热流道 注塑成 型过程进行 模拟仿 真 ,结果表 明 :将 浇 口设置在 泵体锥 部 中心 可 以实现平衡 充模 , 大体 积收 缩率和制 品最 高温度发 生在 泵体锥部 中心 , 最 制品