Modex3D在注塑成型模拟分析中的应用
Moldex3D软件

Moldex3D软件简介及其在模拟注塑中的应用Moldex3D是一款专业的注塑模拟软件,它通过数值计算和仿真技术,模拟出注塑过程中的流变性能、热力学性能和变形性能等,能够帮助企业更好地研发新产品、优化设计和生产工艺。
注塑模拟软件的作用在于减少实际操作过程中的试错成本,节省时间和成本。
因此,在制造业中应用广泛,尤其是在汽车、家电、电子等行业中得到了广泛的应用,下面将详细介绍的应用及其优势。
1.模拟出注塑过程中的流变性能在注塑过程中,材料的流变性能是非常关键的。
可以模拟出材料在注塑过程中的流动状态,以及热传递、凝固等关键过程,从而帮助企业更准确地确定注塑工艺参数,确保产品的设计成型度和力学性能达标。
2.优化模具设计可以对模具结构进行优化设计,通过模拟仿真,可以检测出模具结构的缺陷,并采取相应的优化措施。
同时,还可以预测产品的变形情况,进一步改进模具设计,从而提高整个生产流程的质量和效率。
3.节约成本通过的模拟仿真,企业可以避免实际操作中的试错成本,及时发现问题并进行改进,从而减少生产成本。
同时,还可以预测产品的缺陷,帮助企业尽早解决问题,避免后期返工和投诉。
4.提高产品质量通过的模拟仿真,企业可以在最短的时间内找到最佳的工艺参数和最适合的模具设计,确保产品的成型度和力学性能达到标准要求,从而提高产品质量和市场竞争力。
5.智能化生产可以与其他自动化设备相结合,实现生产过程的自动化和智能化。
通过与MES系统(制造执行系统)相集成,可以实现产量统计、在线监测等功能,从而提高生产效率和质量。
总的来说,可以模拟出产品的相关性能,包括材料流动、热传递、凝固变形等方面,对企业研发新产品、设计模具和生产工艺等都有很好的帮助。
其主要优势在于可以节约成本、提高产品质量和智能化生产,为制造业提供更有效的解决方案,帮助企业在市场中取得更大的竞争优势。
Mold EX - Press 软件在“塑料模具设计”课程教学中的作用
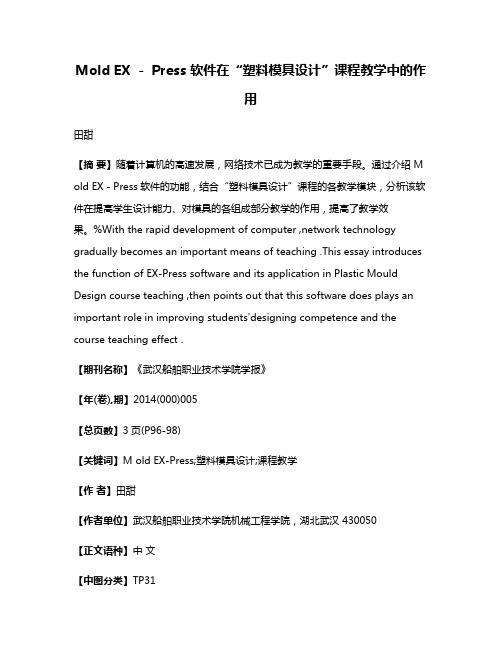
Mold EX - Press 软件在“塑料模具设计”课程教学中的作用田甜【摘要】随着计算机的高速发展,网络技术已成为教学的重要手段。
通过介绍M old EX-Press软件的功能,结合“塑料模具设计”课程的各教学模块,分析该软件在提高学生设计能力、对模具的各组成部分教学的作用,提高了教学效果。
%With the rapid development of computer ,network technology gradually becomes an important means of teaching .This essay introduces the function of EX‐Press software and its application in Plastic Mould Design course teaching ,then points out that this software does plays an important role in improving students'designing competence and the course teaching effect .【期刊名称】《武汉船舶职业技术学院学报》【年(卷),期】2014(000)005【总页数】3页(P96-98)【关键词】M old EX-Press;塑料模具设计;课程教学【作者】田甜【作者单位】武汉船舶职业技术学院机械工程学院,湖北武汉 430050【正文语种】中文【中图分类】TP31随着新技术的应用,塑料制品在使用性能、工艺性能以及价格等方便都比金属材料更具优势,因此塑料制品的应用日益广泛。
为顺应市场需求,国内许多高校机械类的模具专业都开设了“塑料模具设计”课程,并将其作为模具专业的主干、核心课程。
该课程具有理论性和实践性强、多学科渗透的特点,综合性要求比较高,学生学习起来有一定的难度。
基于虚拟仿真技术的塑料成型工艺优化分析

基于虚拟仿真技术的塑料成型工艺优化分析在制造业领域中,塑料成型是一种非常广泛应用的加工技术。
然而,生产过程中存在着各种问题,例如工艺不稳定、工件损伤、生产线停机时间长等等。
因此,优化塑料成型工艺变得尤为重要。
基于虚拟仿真技术,可实现对塑料成型工艺进行全面分析和优化,为企业提供更多的选择和决策依据。
一、虚拟仿真技术在塑料成型中的应用虚拟仿真技术可以帮助企业判断加工中的问题,预测生产线瓶颈,防止产品损坏等问题。
具体地说,在塑料成型中的应用有以下方面:1.模具设计塑料制品的成形过程必须依靠模具,而模具的设计是一个非常复杂的过程。
虚拟仿真技术可以基于已有的参数和规定,对模具进行三维建模,通过模拟实验预测塑料成型过程中的问题,例如模具间隙调整、材料的流动特性等。
2.生产线方案设计生产线方案设计也是塑料成型过程中的一个重要环节。
虚拟仿真技术可以在计算机上建立复杂的生产线模型,分析生产过程中的每一步,以及生产效率和安全性等。
这种方法可以在没有实际生产线的情况下进行仿真,在不同的参数下进行优化工艺,找到最佳的方案。
3.塑料制品设计塑料零件的设计是在产品概念确定后确定的。
虚拟仿真技术可以对零件进行建模,预测在成型中可能发生的问题,例如物料成本、在设备上的塑料强度和在成型过程中的材料流动等。
此外,它还可以计算零件的可靠性和性能,并优化设计。
二、虚拟仿真技术在工艺优化中的应用1.材料流分析在塑料成型过程中,材料流的控制和优化在工艺中起着至关重要的作用。
虚拟仿真技术可以通过模拟实验来了解塑料在流动过程中的流体动力学和特性,并分析材料流的问题,包括料缸淀积、流道温度、注射速度等。
2.成型温度分析温度是影响塑料成型过程中最重要的因素之一。
虚拟仿真技术可以计算热传递和流体流动,及时的预测材料的温度和热历史。
同时,技术还可以帮助企业更好的掌握加热和制冷系统,从而了解温度变化的波动,更好的控制塑料加工过程。
3.成型拉伸分析拉伸也是塑料加工过程中的非常关键的环节。
注塑成型模拟技术在注塑工艺中的应用
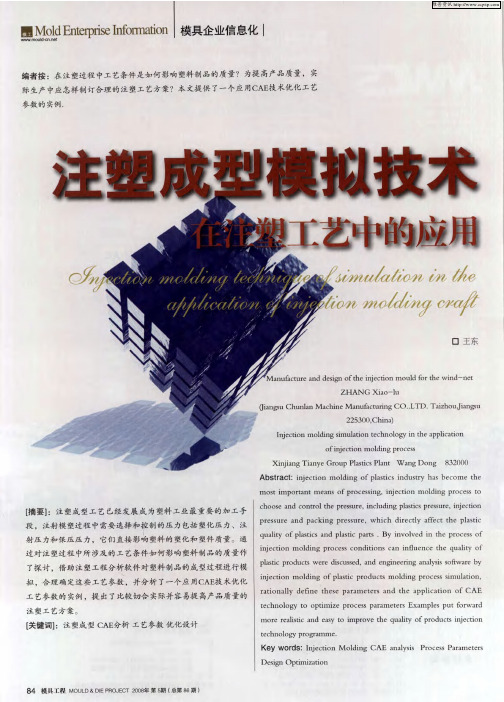
v o
lv
d in
he pr h
e
o c e ss
f f
过 对 注 塑 过 程 中所 涉 及 的 工 艺 条 件 如 何 影 响 塑 料 制 品 的 质 量 作 了探 讨
,
je
io
n
ldin g p r o
c ts
w
c e s s
c o n
ditio
a n
in f l
u e n c e
t
qu
s o
a
lity
a r e
o
借 助 注 塑 工 程 分 析 软 件 对 塑料 制 品 的 成 型 过 程 进 行 模
,
p la s t i c p r o d u im
r a t
e c
e r e
dis c f p la
e s e
u ss e
d
,
d
e n
gin
m o
e e r
in g
a n a
ly s is
ftw
l th e p r e kin g p
a n
ssu r e
,
in
,
l u d i n g p la h ic h dir
.
s t ic s
pr
a
in j
e
e c t
io
s t
n
段
,
注 射 模 塑 过 程 中 需 要 选 择 和 控 制 的 压 力 包括 塑 化 压 力
,
p
r e s s u r e
注
展 成 为 塑 料 工 业 最 重 要 的 加 工 手 段 ,适 于 大 批 量 生 产 形 状 复 杂 、尺 寸 要 求 精 确
注塑模模流分析技术-MOLDFLOW
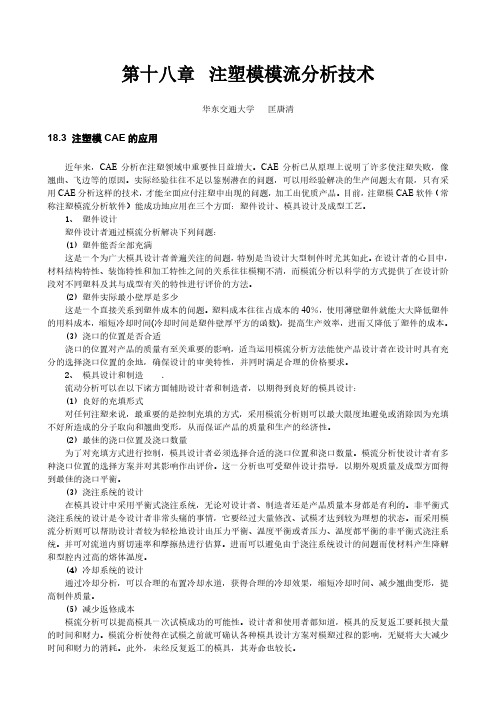
第十八章注塑模模流分析技术华东交通大学匡唐清18.3 注塑模CAE的应用近年来,CAE分析在注塑领域中重要性日益增大。
CAE分析已从原理上说明了许多使注塑失败,像翘曲、飞边等的原因。
实际经验往往不足以鉴别潜在的问题,可以用经验解决的生产问题太有限,只有采用CAE分析这样的技术,才能全面应付注塑中出现的问题,加工出优质产品。
目前,注塑模CAE软件(常称注塑模流分析软件)能成功地应用在三个方面:塑件设计、模具设计及成型工艺。
1、塑件设计塑件设计者通过模流分析解决下列问题:(1)塑件能否全部充满这是一个为广大模具设计者普遍关注的问题,特别是当设计大型制件时尤其如此。
在设计者的心目中,材料结构特性、装饰特性和加工特性之间的关系往往模糊不清,而模流分析以科学的方式提供了在设计阶段对不同塑料及其与成型有关的特性进行评价的方法。
(2)塑件实际最小壁厚是多少这是一个直接关系到塑件成本的问题。
塑料成本往往占成本的40%,使用薄壁塑件就能大大降低塑件的用料成本,缩短冷却时间(冷却时间是塑件壁厚平方的函数),提高生产效率,进而又降低了塑件的成本。
(3)浇口的位置是否合适浇口的位置对产品的质量有至关重要的影响,适当运用模流分析方法能使产品设计者在设计时具有充分的选择浇口位置的余地,确保设计的审美特性,并同时满足合理的价格要求。
2、模具设计和制造.流动分析可以在以下诸方面辅助设计者和制造者,以期得到良好的模具设计:(1)良好的充填形式对任何注塑来说,最重要的是控制充填的方式,采用模流分析则可以最大限度地避免或消除因为充填不好所造成的分子取向和翘曲变形,从而保证产品的质量和生产的经济性。
(2)最佳的浇口位置及浇口数量为了对充填方式进行控制,模具设计者必须选择合适的浇口位置和浇口数量。
模流分析使设计者有多种浇口位置的选择方案并对其影响作出评价。
这一分析也可受塑件设计指导,以期外观质量及成型方面得到最佳的浇口平衡。
(3)浇注系统的设计在模具设计中采用平衡式浇注系统,无论对设计者、制造者还是产品质量本身都是有利的。
精密注塑成型过程模拟及优化分析
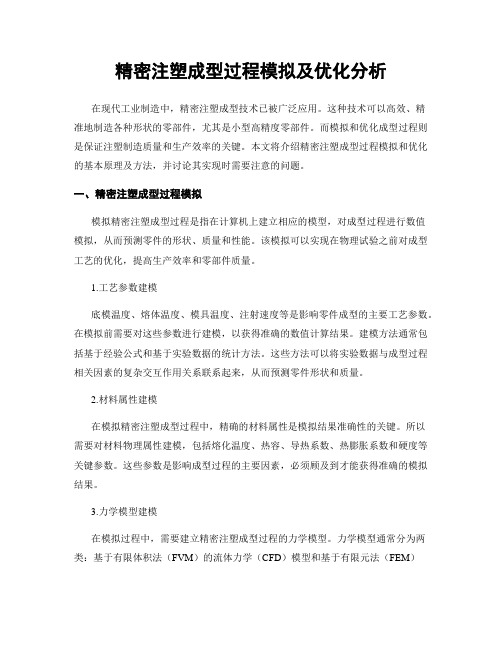
精密注塑成型过程模拟及优化分析在现代工业制造中,精密注塑成型技术已被广泛应用。
这种技术可以高效、精准地制造各种形状的零部件,尤其是小型高精度零部件。
而模拟和优化成型过程则是保证注塑制造质量和生产效率的关键。
本文将介绍精密注塑成型过程模拟和优化的基本原理及方法,并讨论其实现时需要注意的问题。
一、精密注塑成型过程模拟模拟精密注塑成型过程是指在计算机上建立相应的模型,对成型过程进行数值模拟,从而预测零件的形状、质量和性能。
该模拟可以实现在物理试验之前对成型工艺的优化,提高生产效率和零部件质量。
1.工艺参数建模底模温度、熔体温度、模具温度、注射速度等是影响零件成型的主要工艺参数。
在模拟前需要对这些参数进行建模,以获得准确的数值计算结果。
建模方法通常包括基于经验公式和基于实验数据的统计方法。
这些方法可以将实验数据与成型过程相关因素的复杂交互作用关系联系起来,从而预测零件形状和质量。
2.材料属性建模在模拟精密注塑成型过程中,精确的材料属性是模拟结果准确性的关键。
所以需要对材料物理属性建模,包括熔化温度、热容、导热系数、热膨胀系数和硬度等关键参数。
这些参数是影响成型过程的主要因素,必须顾及到才能获得准确的模拟结果。
3.力学模型建模在模拟过程中,需要建立精密注塑成型过程的力学模型。
力学模型通常分为两类:基于有限体积法(FVM)的流体力学(CFD)模型和基于有限元法(FEM)的结构力学模型。
这些模型可以预测零件的形状和质量等关键参数,为注塑工艺优化提供参考。
4.成型过程数值模拟在完成上述工作后,可以对注塑成型过程进行数值模拟。
模拟可以实现在物理试验之前对成型工艺的优化,并预测成型过程中各个参数的趋势和偏差,以及零件的形状和质量,从而为实际生产提供指导意义。
二、精密注塑成型过程优化通过模拟精密注塑成型过程,可以对注塑工艺进行优化,以提高成型过程质量和生产效率。
1.注塑成型参数优化对注塑成型参数进行优化可以使生产过程效率高,并降低零件的质量问题。
Moldex3D用于压力泵组件开发,优化真圆度案例解析
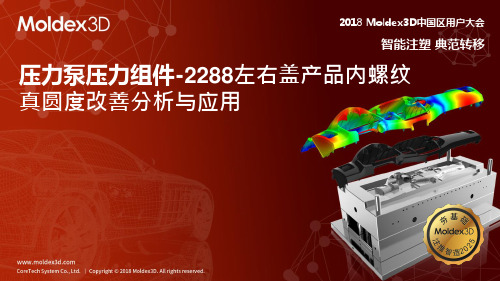
模次数,提升产品品质
> 未来研究计划 > 纤维配向在复杂结构中的取向变异 > 浇口位置,产品结构对纤维取向的影响 > 纤维向如何影响螺纹
44
专案组对讨论的结果一致认为: 1,产品材料纤维配向对产品最终变形有着重要的影响 2,产品的整体结构与料流走向,最后收缩内应力也对产品最后变形起关键作用。 对策: 1,换材料,用不带纤维的材料打样出来分析出,纤维对变形的影响因子占比是多少
(但是即使真圆度符合要求,因其强度不够也是不能够替代现有材料) 2,再次验证多种注塑工艺,尽可能找出既经济又合尺寸的工艺。 前俩项由注塑工程师,评审高工负责进行验证 3,利用CAE进行浇口位置模拟,找出最佳位置 4,利用CAE技术进行模拟,改变产品结构胶位,寻找改善的办法 后俩项由CAE工程师与研发工程师,评审高工负责进行
总位移 总位移
真圆度 0.95
真圆度 0.651
结论:最终改模后,实际量测产品的数据
最后方案6与方案7的效果是差不多的,从 修模成本考虑。优先选用方案六“改变浇
口位置B”来执行。
41
PART V: 结论及未来应用
结论
> 运用Moldex3D平台,进行CAE技术模拟的有效性是可靠的。 > 在本案中对浇口位置的改变,产品胶位的变化后进行虚拟的改模验
问题
材料
纤维取向
对策
变更材料
对策 变更位置不同位置
真 圆 度
成型工艺
保压压力
进行CAE模拟验证 重新编写试模测划,与
保压时间
换料重新上模验证一次
壁厚均衡
在不对称的俩侧增加胶位,改
注射成型典型缺陷形成的原因及解决措施

注射成型典型缺陷形成的原因及解决措施严志云;谢鹏程;丁玉梅;杨卫民【摘要】对注射成型过程中常见的成型缺陷进行了分类,并从材料、模具、注塑机和工艺方面分析了缺陷产生的原因,进而提出解决措施.【期刊名称】《模具制造》【年(卷),期】2010(010)003【总页数】10页(P60-69)【关键词】注射成型;缺陷;熔接痕;喷射痕;流痕;翘曲【作者】严志云;谢鹏程;丁玉梅;杨卫民【作者单位】北京化工大学机电工程学院,北京,100029;北京化工大学机电工程学院,北京,100029;北京化工大学机电工程学院,北京,100029;北京化工大学机电工程学院,北京,100029【正文语种】中文【中图分类】TQ320.661 引言一般来说,对于塑料制品性能优劣的评价主要有3个方面:(1)外观质量,包括完整性、颜色、光泽等。
(2)尺寸和相对位置间的准确性,即尺寸精度和位置精度。
(3)与用途相应的机械性能、化学性能、电学性能等,即功能性。
如果由于上述3个方面中的任何一个环节出现问题,就会导致制品缺陷的产生和扩展。
依据以上3方面的评价标准,注射成型制品常见缺陷具体可分为两大类:(1)外观问题类:包括欠注、飞边、充填不平衡、缩痕缩孔、熔接痕、波流痕、喷射痕、浇口晕、焦痕、气泡、银纹、色差、白化、龟裂、表面浮纤、翘曲变形等。
(2)性能问题类:脆化、残余应力、尺寸不稳定、超重欠重等。
2 注射成型典型缺陷2.1 欠注欠注又称短射、充填不足,是指料流末端出现部分不完整现象或一模多腔中一部分填充不满,特别是薄壁区或流动路径的末端区域。
(1)形成原因。
a.材料:①材料流动性不好;②润滑剂过多或材料中有异物。
b.模具:①流道过小、过薄或过长;②制品结构复杂、转折多、局部断面很薄;③浇口位置或形式不当、数量不足;④模具型腔排气不良;⑤制品为一模多腔,充填不平衡。
c.注塑机:①注塑机选型不当,塑化容量不足;②进料处遭异物阻塞;③喷嘴与主流道入口配合不良。
基于DOE法的注塑成型工艺仿真优化本科毕业论文

摘要注塑成型制品质量控制方面存在的困难主要来源于力学的复杂性和在温度、压力波动下材料行为的不可预测性,研究工艺参数对注塑制品质量的影响关系,建立工艺参数与制品质量之间的关系模型,并用DOE法对工艺进行仿真优化是注塑制品工艺优化的前提。
本文选用半结晶型和无定型ABS两种材料,针对一维流动平板两个方向上的收缩、强度,熔接线强度、制品重量及沉降斑等质量指标进行了实验研究。
研究了工艺参数对质量指标的影响及因素之间的交互作用。
本文主要工作包括以下几方面: 1 工艺参数对制品质量的交互影响分析;2 应用DOE法结合析因分析结果;3.CAE技术结合DOE法进行设计,并用MOLDFLOW进行仿真分析,为质量控制技术提供了工艺模型。
关键词: 注塑成型,正交实验,Moldflow,三维建模,工艺仿真优化,实验设计AbstractQuality control of injection molding products, mainly difficulties from that exist in the complexity of process dynamics and in the temperature and pressure fluctuations unpredictable behavior of materials, of process parameters on product quality of injection molding between the relationship,DOE method with simulation and optimization technology of injection molding products, process optimization is a prerequisite.Semi-crystalline and amorphous ABS we usd in this paper,For a flat that two-dimensional flow direction shrinkage, strength, weld line strength, weight and sink marks and other products, the quality indicators studied. In this paper, include the following:1. Process parameters on product quality of interaction analysis;2. Application of DOE method with the results of factorial analysis;3. CAE design method combined with DOE,Simulation and analysis with MOLDFLOW,quality control technology provides for the process model.Key words:Injection Molding,Orthogonal,Moldflow,Three-dimensional modeling,Process simulation and optimization,design of experiment.目录1.1 引言 (1)1.2 注塑成型工艺过程简介 (1)1.3注塑成型工艺的发展趋势 (3)1.4 注塑成型工艺优化国内外研究概况 (6)1.5本文主要工作内容及其意义 (10)2. 注塑成型工艺参数影响性分析 (13)2.1 压力参数分析 (13)2.1.1注塑压力 (13)2.1.2保压压力 (13)2.1.3 塑化压力(背压) (14)2.2 温度参数分析 (14)2.2.1模具温度 (14)2.2.2熔体温度 (15)2.3时间参数分析 (15)2.3.1注射时间 (16)2.3.2保压时间 (16)2.4注射速度分析 (16)3. 基于DOE法的注塑成型仿真优化 (18)3.1软件Moldflow以及正交实验助手的介绍 (19)3.1.1 moldflow软件简介 (19)3.1.2 正交实验助手介绍 (20)3.2材料的选取及模型的导入 (23)3.3本次实验设计法的分析理论依据 (27)3.3.1.实验基本参数取值范围的确定及输入 (28)3.3.2.正交表的设置及数据生成 (29)3.3.3实验分析类型以及结果的选取 (31)3.4实验设计法的仿真优化过程 (34)3.4.1 Moldflow与正交表的数据结合分析 (34)3.4.2实验数据的反馈与整合 (43)4.模具设计 (47)4.1塑件用途及其性能要求 (47)4.2注射量的计算 (48)4.3锁模力的计算 (48)4.4注塑机的选择及参数 (49)4.5 分型面的确定 (50)4.6 浇注系统的设计 (51)4.7 成型零部件的设计与计算 (57)4.8 推出机构设计 (59)4.9标准模架的选取 (59)4.10 开模行程的校核 (61)4.11 推出脱模机构设计 (62)4.12合模导向机构的设计 (64)4.13 排气系统与冷却系统的设计 (67)5. 结论 (68)5.1设计的总结与创新点: (68)5.2论文所存在的问题及其解决方案: (69)谢辞 (70)参考文献: (72)1.绪论1.1 引言随着科学技术水平的不断提高以及加工方法的改进,塑料这一20世纪才发展起来的新材料已经在我们的日常生活中占据了重要的地位,成为国民经济中不可缺少的一部分。
MODEX 3D模流分析教材
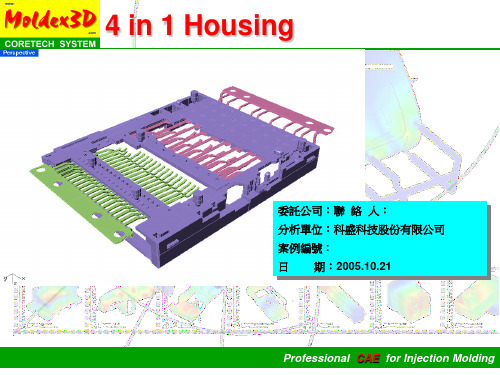
藉由不同範圍的流動波前圖或是流動波前動畫,可看塑料在模穴中各時刻的充填情形,可預測縫合線及包 封位置,且可判斷是否會有短射現象發生,提供排氣孔位置安排等參考。
流道效應的分析需重新修改幾何模型,預計於10/25再提供完整 CAE分析報告
雖然本報告尚未考慮流道效應,厚度設計的驗證仍可以從流動分 析中獲得。
(3/121)
Professional CAE for Injection Molding
原始設計 材料特性LCP (Polyplastics VECTRA VE130i)
0.15 0.2 0.55
此橫肋區肉厚 由0.2~0.4mm, 有遲滯現象
(21/121)
此區域有遲滯現象,由剖面可知 該處肉厚較薄且與Ping相接觸最 薄處僅約0.15mm。
0.2mm 0.4mm
Professional CAE for Injection Molding
原始設計Ⅰ 流動波前 95%
原始設計 材料特性LCP (Polyplastics VECTRA VE130i)
• 比熱(Heat Capacity)
» 欲將單位塑料溫度提高一度所需的熱量,是塑料溫度容易改變與否的度量。比熱 越高,塑料溫度越不容易變化,反之亦然。
• 熱傳導係數(Thermal Conduction)
» 塑料熱傳導(thermal conduction)特性的度量。熱傳導係數越高,熱傳導效果越 佳,塑料於加工過程中溫度傾向均勻,較不會因熱量局部堆積而有熱點(hot spot) 產生。熱傳導係數及比熱攸關塑料之熱傳、冷卻性質,亦影響到冷卻時間長短。
原始設計Ⅰ 流動波前 10%
藉由不同範圍的流動波前圖或是流動波前動畫,可看塑料在模穴中各時刻的充填情形,可預測縫合線及包 封位置,且可判斷是否會有短射現象發生,提供排氣孔位置安排等參考。
Mold EX - Press 软件在“塑料模具设计”课程教学中的作用
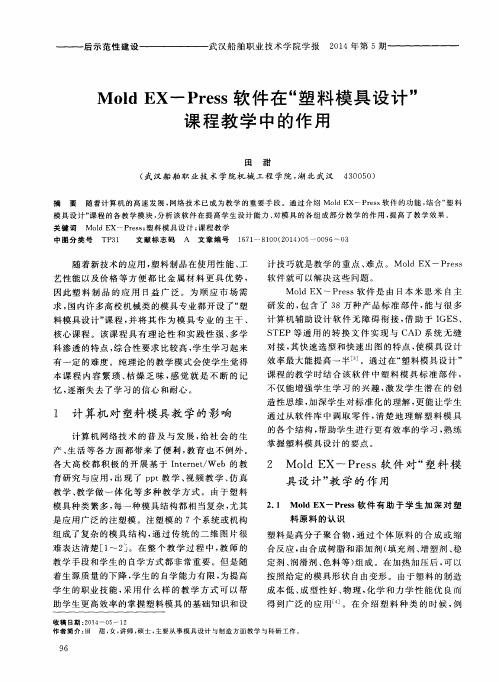
塑料 是高分 子 聚合 物 , 通 过 个 体 原 料 的合 成 或 缩 合反应 , 由合成树 脂 和添加 剂 ( 填 充剂 、 增 塑剂 、 稳 定剂 、 润滑 剂 、 色 料等 ) 组成 。在 加热 加压 后 , 可 以 按 照 给定 的模具形 状 自由变形 。 由于塑 料的制 造 成 本低 、 成 型性 好 、 物理, 化 学 和力 学 性 能优 良而
摘 要 随 着 计 算 机 的高 速 发 展 , 网 络 技 术 已成 为 教 学 的 重 要 手 段 。通 过 介 绍 Mo l d E x~ P r e s s 软 件 的功 能 , 结合“ 塑料 模具设计” 课程的各教学模块 , 分析该软件在提高学生设计能力 、 对模具的各组成部分教学的作用 , 提 高 了 教学 效 果 。 关 键 词 Mo l d E X—P r e s s ; 塑 料模 具设 计 ; 课 程 教 学
后示范 性 建设
武 汉船 舶职业 技术 学 院学报
2 0 1 4年第 5期
Mo l d E X P r e s s 软 件在 “ 塑 料 模 具 设计 ’ ’ 课 程 教 学 中 的 作 用
田 甜
( 武汉船 舶职 业技 术 学院机械 工程 学院 , 湖 北武 汉
4 3 0 0 5 0 )
研发 的, 包含了 3 8万 种 产 品标 准 部 件 , 能 与很 多
料 模具设 计 ” 课程 , 并 将 其作 为模 具 专 业 的 主干 、
核 心课 程 。该课 程 具 有 理论 性 和 实 践 性 强 、 多学
计算 机辅 助设 计 软件 无 障碍 衔 接 , 借助于 I GE S 、 S T E P等 通 用 的转 换 文件 实 现 与 c AD 系统 无 缝
实际注塑成型工艺在MOLDFLOW中的设定方法
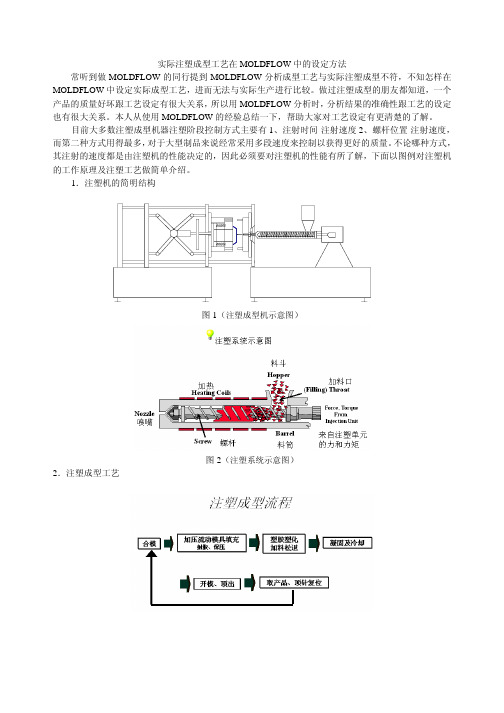
实际注塑成型工艺在MOLDFLOW中的设定方法常听到做MOLDFLOW的同行提到MOLDFLOW分析成型工艺与实际注塑成型不符,不知怎样在MOLDFLOW中设定实际成型工艺,进而无法与实际生产进行比较。
做过注塑成型的朋友都知道,一个产品的质量好坏跟工艺设定有很大关系,所以用MOLDFLOW分析时,分析结果的准确性跟工艺的设定也有很大关系。
本人从使用MOLDFLOW的经验总结一下,帮助大家对工艺设定有更清楚的了解。
目前大多数注塑成型机器注塑阶段控制方式主要有1、注射时间-注射速度2、螺杆位置-注射速度,而第二种方式用得最多,对于大型制品来说经常采用多段速度来控制以获得更好的质量。
不论哪种方式,其注射的速度都是由注塑机的性能决定的,因此必须要对注塑机的性能有所了解,下面以图例对注塑机的工作原理及注塑工艺做简单介绍。
1.注塑机的简明结构图1(注塑成型机示意图)图2(注塑系统示意图)2.注塑成型工艺接下来用我本人做的一个案例来介绍的是怎样在MOLDFLOW 中设定注塑工艺参数(螺杆位置-注射速度即stroke vs % maximun ram speed ).1. 注塑机选择或定义由于moldflow 数据库中的注塑机大多是国外品牌,如雅宝(Auburg )、赫斯基(Husky )、徳马格(Demag )等,很多牌子是没有的,需要自定义,定义方法如下(以我公司的东芝EC350为例,其它品牌可参照)1) 点toosl-new personal database,出现如下对话框:产品模型和网格统计,分析材料选的是pc+abs (GE C6600)在category(类别)拦中选择process condition(工艺条件)下面的 injection molding machine (注塑机),点OK,进入下一步,点new(新建),出现新对话框如下第1栏为description(描述),trade name中输入名称EC350,manufacturer输入厂家toshiba, data source 输入toshiba,data last modified输入sep 10 ,2002, data status默认,这一页的内容主要是注塑机的一些信息,无关紧要的东西,输入结果如下:第2栏为注射部分(重点),maximum machine injection stroke中输入最大计量行程300mm, maximum machine injection rate中输入最大注射率314cm^3/s,machine screw diameter输入螺杆直径50mm,fill control默认stroke vs ram speed)。
_一种特殊结构的指纹产品模流仿真设计及Strip Warpage改善报告
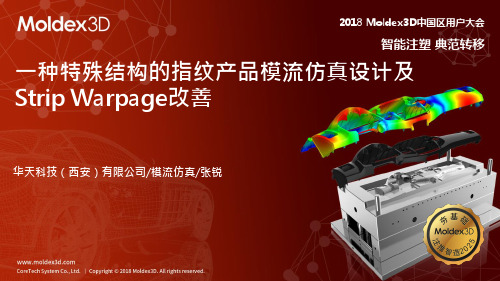
针对封装过程和产品使用过程中 的各种可靠性问题进行模拟分析。 提供封装热阻数据及散热瓶颈分析, 翘曲应力分析,SI分析,PI分析, EMI分析及寄生参数等仿真分析服务。 在MEMS封装、指纹识别系统、系统 级高密度封装、射频电路、Serdes12.5G高速信号、DDR4模块和HDMI 模块等高端产品设计中均有成功应用。
4
高密度高散热封装系统级仿真应用 SerDes-12.5G bps高速信号仿真验证
FCLGA产品25A电流分布图 10GHz光收发模块QFN封装电仿真应用
仿真应用
高功率封装散热器设计分析 FC封装射频信号电仿真应用
指纹识别系统仿真模拟应用
硅麦克风产品翘曲分析 封装塑封冲线模流分析
产品介绍 I
指纹识别模块中的电容值越大其识别度越高。其中容值的大小与塑封料的介电常数、芯 片感应区域面积成正比,与其芯片表面到塑封体表面距离d成反比。
14
模流改善方案 1
模流方向旋转90°后填充结果如图所示,用不同颜色显示充填的先后时间, 从流动波前图可以看出注塑过 程中远浇口端产品芯片末端处有包封不满风险。
15
模具厂商两种Gate设计模流改善
16
模流改善方案 2
模流方向旋转180°后填充结果如图所示, 从流动波前图可以看出PKG旋转180°后90%填充时PKG 薄部最后一排已完成填充,而原设计的PKG薄部最后一排才开始填充。
De-Tape & Tape Mount
Strip Grinding
EVI
Compression
Molding
Packing & Shipping
Protect Film Tape &PMC& Strip Grinding
moldex3d所需的工艺参数

一、概述Moldex3D 是一款专业的注塑模流分析软件,可以帮助用户预测和优化注塑模流过程,提高产品质量,减少生产成本。
在使用这款软件进行注塑模流分析时,需要设置一些工艺参数,以确保分析的准确性和有效性。
本文将介绍 moldex3d 所需的工艺参数及其设置方法。
二、注塑机参数1. 射出压力:射出压力是指塑料材料在注塑机中由螺杆推动产生的压力,影响着塑料的射出速率和温度。
在进行模流分析时,需要准确设置射出压力,以保证模流模拟的真实性。
一般来说,根据实际生产中的数据及经验,设置合适的射出压力值。
2. 射出速度:射出速度是指塑料材料在注塑机中射出的速度,对产品的成型和表面质量有重要影响。
在进行模流分析时,需要根据实际情况来设置合适的射出速度,以确保模拟结果的准确性。
三、模具参数1. 冷却时间:冷却时间是指从注塑成型完成到模具完全冷却的时间。
在模流分析中,需要设置合理的冷却时间,以确保在模流模拟中考虑到了塑料充填后的冷却过程,并据此优化冷却系统。
2. 模具温度:模具温度是指模具在注塑过程中的温度,对产品的成型质量有很大影响。
在进行模流分析时,需要准确设置模具温度,以确保模拟结果的准确性。
四、材料参数1. 熔体指数:熔体指数是指树脂在一定温度下的流动性能,不同的熔体指数对产品的成型质量有很大的影响。
在进行模流分析时,需要根据实际情况设置合适的熔体指数值,以确保模拟结果的准确性。
2. 热性能:材料的热性能包括熔体温度、热传导系数等参数,对模流模拟结果的准确性和真实性有很大的影响。
在进行模流分析时,需要准确设置材料的热性能参数。
五、其他参数1. 其他参数:除了上述的参数外,还有很多其他的工艺参数会对模流模拟结果产生影响,比如模具设计、模具结构、射胶系统等方面的参数。
在使用 Moldex3D 进行模流分析时,需要综合考虑这些参数,并根据实际情况进行合理的设置。
六、总结Moldex3D 是一款功能强大的注塑模流分析软件,可以帮助用户准确预测和优化注塑过程,提高产品质量,降低生产成本。
注塑成型过程仿真模拟

注塑成型过程仿真模拟注塑成型过程仿真模拟注塑成型是一种常用的塑料加工方法,通过在模具中加热和压力的作用下,将熔融的塑料材料注入模具中,形成所需的产品形状。
然而,在实际生产中,由于材料和工艺的复杂性,注塑成型过程中常常会出现一些问题,如产品缺陷、模具磨损等。
为了解决这些问题,提高生产效率和产品质量,注塑成型过程仿真模拟应运而生。
注塑成型过程仿真模拟是利用计算机技术对注塑成型过程进行数字化模拟和分析的方法。
通过建立注塑成型的数学模型,并运用计算流体力学和有限元分析等方法,可以模拟和预测材料的流动、温度分布、变形等情况,从而优化模具设计和工艺参数,提高生产效率和产品质量。
注塑成型过程仿真模拟的基本流程包括几何建模、网格划分、物理参数设定、边界条件设定、数值计算和结果分析等步骤。
首先,根据实际产品的几何形状,利用计算机辅助设计软件进行三维几何建模。
然后,将几何模型转化为计算所需的网格模型,即将几何体划分为无数小的单元格,以便进行数值计算。
接下来,根据材料的物理参数,设定模拟过程中的温度、压力、速度等参数,并确定边界条件,如模具表面的温度和压力。
然后,利用数值方法对模型进行计算,得出模拟结果。
最后,对模拟结果进行分析,评估模具设计和工艺参数的合理性,并根据需求进行优化。
注塑成型过程仿真模拟具有多方面的优势。
首先,它可以提前发现和解决注塑成型过程中可能出现的问题,如翘曲、热应力、气泡等缺陷,从而避免因产品缺陷导致的生产损失。
其次,它可以优化模具设计和工艺参数,提高生产效率和产品质量。
再次,它可以减少试模次数,节省原材料和时间成本。
此外,注塑成型过程仿真模拟还可以提供详细的数值结果和可视化的模拟图像,为工程技术人员提供参考和决策依据。
总之,注塑成型过程仿真模拟是一种有效的工具,可以帮助企业解决注塑成型过程中的问题,提高生产效率和产品质量。
随着计算机技术的不断发展和成熟,注塑成型过程仿真模拟将会得到更广泛的应用和推广。
MoldFlow软件在注塑模具设计中的应用.
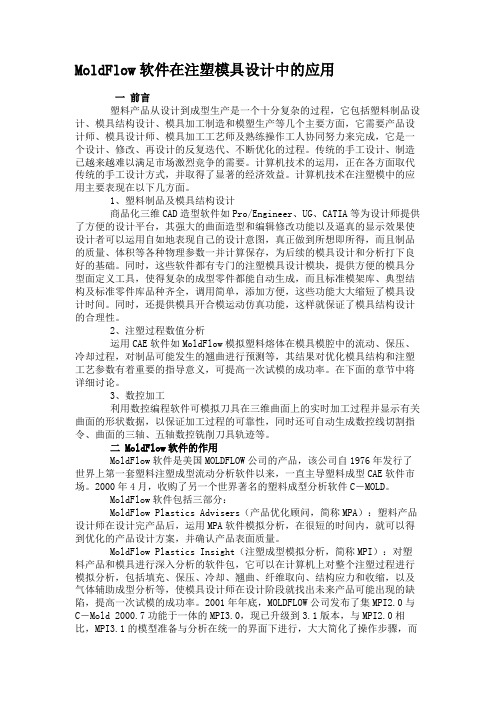
MoldFlow软件在注塑模具设计中的应用一前言塑料产品从设计到成型生产是一个十分复杂的过程,它包括塑料制品设计、模具结构设计、模具加工制造和模塑生产等几个主要方面,它需要产品设计师、模具设计师、模具加工工艺师及熟练操作工人协同努力来完成,它是一个设计、修改、再设计的反复迭代、不断优化的过程。
传统的手工设计、制造已越来越难以满足市场激烈竞争的需要。
计算机技术的运用,正在各方面取代传统的手工设计方式,并取得了显著的经济效益。
计算机技术在注塑模中的应用主要表现在以下几方面。
1、塑料制品及模具结构设计商品化三维CAD造型软件如Pro/Engineer、UG、CATIA等为设计师提供了方便的设计平台,其强大的曲面造型和编辑修改功能以及逼真的显示效果使设计者可以运用自如地表现自己的设计意图,真正做到所想即所得,而且制品的质量、体积等各种物理参数一并计算保存,为后续的模具设计和分析打下良好的基础。
同时,这些软件都有专门的注塑模具设计模块,提供方便的模具分型面定义工具,使得复杂的成型零件都能自动生成,而且标准模架库、典型结构及标准零件库品种齐全,调用简单,添加方便,这些功能大大缩短了模具设计时间。
同时,还提供模具开合模运动仿真功能,这样就保证了模具结构设计的合理性。
2、注塑过程数值分析运用CAE软件如MoldFlow模拟塑料熔体在模具模腔中的流动、保压、冷却过程,对制品可能发生的翘曲进行预测等,其结果对优化模具结构和注塑工艺参数有着重要的指导意义,可提高一次试模的成功率。
在下面的章节中将详细讨论。
3、数控加工利用数控编程软件可模拟刀具在三维曲面上的实时加工过程并显示有关曲面的形状数据,以保证加工过程的可靠性,同时还可自动生成数控线切割指令、曲面的三轴、五轴数控铣削刀具轨迹等。
二 MoldFlow软件的作用MoldFlow软件是美国MOLDFLOW公司的产品,该公司自1976年发行了世界上第一套塑料注塑成型流动分析软件以来,一直主导塑料成型CAE软件市场。
使用3D打印技术制作可注塑模具的技巧与方法
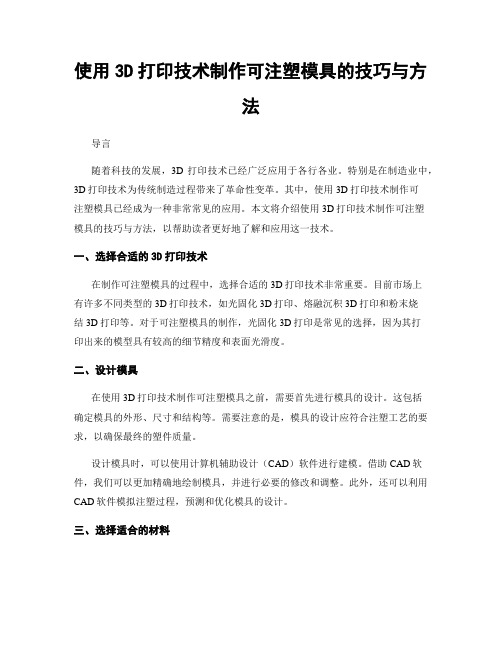
使用3D打印技术制作可注塑模具的技巧与方法导言随着科技的发展,3D打印技术已经广泛应用于各行各业。
特别是在制造业中,3D打印技术为传统制造过程带来了革命性变革。
其中,使用3D打印技术制作可注塑模具已经成为一种非常常见的应用。
本文将介绍使用3D打印技术制作可注塑模具的技巧与方法,以帮助读者更好地了解和应用这一技术。
一、选择合适的3D打印技术在制作可注塑模具的过程中,选择合适的3D打印技术非常重要。
目前市场上有许多不同类型的3D打印技术,如光固化3D打印、熔融沉积3D打印和粉末烧结3D打印等。
对于可注塑模具的制作,光固化3D打印是常见的选择,因为其打印出来的模型具有较高的细节精度和表面光滑度。
二、设计模具在使用3D打印技术制作可注塑模具之前,需要首先进行模具的设计。
这包括确定模具的外形、尺寸和结构等。
需要注意的是,模具的设计应符合注塑工艺的要求,以确保最终的塑件质量。
设计模具时,可以使用计算机辅助设计(CAD)软件进行建模。
借助CAD软件,我们可以更加精确地绘制模具,并进行必要的修改和调整。
此外,还可以利用CAD软件模拟注塑过程,预测和优化模具的设计。
三、选择适合的材料在使用3D打印技术制作可注塑模具时,选择适合的材料也是至关重要的。
最常用的材料是光敏树脂,因为它具有高强度、精度和表面质量。
此外,还有热塑性材料,如尼龙和ABS等,可以用于一些特殊的注塑应用。
在选择材料时,还需要考虑模具的使用寿命和注塑材料的特性。
一些注塑材料可能具有很高的熔点和粘度,要求模具具备良好的热稳定性和耐磨性。
四、进行3D打印在模具设计和材料选择完成后,接下来是进行3D打印。
在打印过程中,需要注意以下几点:1.根据设计要求,设置适当的打印参数,如打印速度、打印厚度等。
这些参数会直接影响打印出来的模型的质量。
2.在打印之前,要确保3D打印机的工作台平整,并适当地进行校准,以保证打印时的精度和稳定性。
3.在打印过程中,要时刻检查模具的打印状态。
- 1、下载文档前请自行甄别文档内容的完整性,平台不提供额外的编辑、内容补充、找答案等附加服务。
- 2、"仅部分预览"的文档,不可在线预览部分如存在完整性等问题,可反馈申请退款(可完整预览的文档不适用该条件!)。
- 3、如文档侵犯您的权益,请联系客服反馈,我们会尽快为您处理(人工客服工作时间:9:00-18:30)。
初e gating system
改进方案
填充结果比较:
初始方案
改进方案 图 3 填充结果比较 Fig3 Comparison of filling results
翘曲变形结果比较:
初始方案 图 4 翘曲变形结果比较 Fig 4 Comparison of warp results
图 8 初始方案冷却水道布置 Fig8 Cooling water arrangement of the initial program
初始方案 工艺参数设置:
填充结果:
51%
82%
95%
98%
流动速率结果:
由图可知,SN4 浇口的流动速率最大,SN3 和 SN2 浇口的流动速率相当。 注射点压力结果:
p I ( u u T ) C p (
T uT ) (k T ) 2 t
其中 u 表示速度向量,T 表示温度,t 表示时间, p 表示压力, 表示全部的应力分量,
表示密度, 表示黏度, k 表示热传导系数, C p 表示比热, 表示剪切速率。熔胶黏度
X 方向变形范围为-1.4mm~2.1mm。
Y 方向变形范围为-0.6mm~1.4mm。
Z 方向变形范围为-1.2mm~1.2mm。 改进方案 为了降低制品两侧部位的收缩率和翘曲变形量,增大注射速度,延长保压时间,降低模 具温度。 工艺参数设置:
注射点压力结果:
改变工艺参数后最大注射压力为 101MPa,压力降为 33MPa,为最大注射压力的 33%。 可见增大注射速度导致流道压力降增大,但是降低了注射压力。
最大注射压力为 106MPa,压力降为 32MPa,达到注射压力的 30%。 体积收缩率结果:
制品体积收缩率范围为 0%~4.66%,收缩不均匀。图中流动末端孔周围收缩率较大,容易产 生翘曲变形。
冷却后模具温度结果:
型腔侧温度分布(范围:55~79℃)
型芯侧温度分布(范围:47~79℃)
翘曲变形结果:
会因温度而改变,采用的方程式为 Modified-Cross Model
(T , )
0 (T ) 1 (0 / )1 n
Tb ) T
(5)
其中 0 (T ) B Exp(
(6)
3. Moldex3D 优化模具结构
实例模型为镜头筒, 初始分析方案浇注系统及模型如图 1 所示。 镜头筒为镜头安装组件 中的重要零件,要求塑料筒的圆度较高,因此要控制制品的翘曲变形。制品长度为 50mm, 直径为 39mm,体积为 5.5cm3,材料为 PC+20%GF,工艺条件为:注射时间 0.8s,熔体温度 为 310℃,模具温度为 105℃。
分析。最具代表性的应用包含未饱和多元酯纤维、聚氨酯、液态硅橡胶及利用环氧 基树酯调和成型的微芯片封装之射出成型。 I2 模块接口数据处理功能,可进一步整合 Moldex3D/Solid 分析结果与常见的结构 分析软件,如 ABAQUS、ANSYS、MSC.Nastran 等。 Parallel Computing 并行计算,提高计算效率,节省计算时间。 Viscoelasticity 黏弹性分析模块,可以进一步由流动残留应力的最大正向应力推估 出非等向性的分子排向, 再辅以最大正向应力与最大剪切应力量值提供使用者了解 成品的分子排向与残余应力分布是否符合设计,并进行模具设计与加工条件调整。 后续并可以作为光学非等向性质分析变形之基础, 与纳入翘曲分析之考虑, 以取得 更精确之预测。 OPTICS(实体光学分析模块)除了可精准模拟出射出各阶段下的流动导致之双折 射与受热应力导致之双折射, 并进一步整合光弹分析理论, 提供使用者在光线穿过 物体后所累积之光程差、 条纹级数与光弹条纹等实用信息, 真正做到与实务紧密结 合,提供使用者方便易判读结果之计算机辅助工具。 IC Package 封装模块,可帮助使用者建立微芯片网格,并进行金线布局的设计,以 利进行微芯片封装之金线偏移及导线架偏移等计算。 透过金线偏移计算可预测出充 填过程中, 塑料流动的拖曳力是否造成金线偏移量过大, 导致金线接触而造成成品 短路或金线断裂等问题。此外,导线架受到塑料流动拖曳力所造成的偏移,亦可透 过导线架偏移计算得之。 经由上述的计算分析, 使用者即可在生产前提早预测出因 制程所产生的缺陷并加以避免。
图 1 镜头筒模型及浇注系统 Fig1 Model and gating system of the lens module
填充结果:
填充 50%
填充 60%
填充 70%
填充 80%
填充 90%
填充 95%
保压结果:
体积收缩率结果:
1.5%
3%
翘曲变形结果:
X 方向变形(-0.1~0.1mm)
Y 方向方向变形(-0.02~0.02mm)
1. Moldex3D 简介
Moldex3D 是台湾科盛科技公司自行开发成功并商业化的注射成型计算机辅助工程分析 (CAE)软件,其中 Moldex 是 Mold Expert(模具专家)的缩写[1]。Moldex3D 完整提供设计链 各个阶段所需要的不同分析工具。eXplorer 直接建构在各种主流 CAD 软件的操作接口,设 计者可直接进行流动分析。eDesign 系列则是一套完整的产品与模具设计工具,方便模具设 计者在模具加工前快速进行验证。Solid/Shell 则是高阶的注塑成型工程分析与优化软件,对 各种塑件均提供深入完整的分析功能。Moldex3D 目前已经发布最新 R9.1 版本。Moldex3D 产品包括以下一些分析模块[2,3,4,5]: Flow(实体流动分析模块)以完整三维不等温 Navier-Stokes 理论为分析基础,可 正确预测流道中受剪切力流影响导致之流动不平衡现象, 可提供实体熔胶流动宏观 及微观的深入分析见解,如喷泉流、惯性效用、重力效用等。 Pack(实体保压分析模块)可提供保压程序问题分析与解析,进一步预测塑料压缩 值(PVT 比容变化) ,以计算保压程序中热塑性材质之流动行为及其密度变化。可 准确决定浇口固化时间、 正确保压时间及适当的保压压力, 最小化高体积收缩率范 围。 Cool(实体冷却分析模块)为分析射出冷却的真实三维分析工具,可供使用者针对 粗厚件、厚度差异大、以及复杂几何塑件进行冷却模拟。在设计阶段能有效且准确 地分析模温、水路配置效能以及冷却时间。 Warp(Moldex3D 翘曲分析模块)为真实三维翘曲模拟分析工具,可详细剖析收缩 与翘曲成因,在开模之前即可修正问题。 Fiber(实体纤维配向分析模块)可精准仿真充填过程的纤维三维配向,并进一步 计算纤维强化塑件内, 因加工过程引起非等向热机械特性。 可让使用者了解纤维三 维配向, 并可进一步控制强化纤维塑件之非等向收缩。 纤维配向模块基于真实三维 技术,提供正确且详尽的三维纤维配向信息;因此,由纤维配向导致之加工非等向 收缩和机械性能可纳入分析之考虑,以取得更精准的翘曲预测分析。 MCM 多材质成型分析模块, 包含嵌件成型 (insert molding) 、 双射出 (over molding) 和多射依序成型(multi-shot sequential molding) 。以精准的分析能力正确地分析不 同塑件的交互作用行为, 进而优化产品设计。 使用者可以自由铸造金属或塑料嵌件 的模型并进行全面性流动、保压、冷却、翘曲分析。Moldex3D/Solid-MCM 帮助您 预测延迟冷却时间、双色或双射过程中不对称收缩及相异塑料因 CTE (热扩张系 数)产生的翘曲问题。 RIM 反应注射模块为针对热固性塑料的真实三维模拟工具,可进行反应射出成型
图 5 LCD 外壳 Fig5 Model of the LCD cover
图 6 制品厚度分布 Fig6 Thickness distribution of the LCD cover
图 7 浇注系统 Fig7 Gating system of the LCD cover
冷却水道布置如图 8 所示,图中蓝色水道靠近型腔侧温度为 60℃,其余水道靠近型腔 侧温度为 25℃,冷却系统共有 20 个出入口和 20 组冷却介质。
纤维取向结果:
X 方向
Y 方向
总体变形结果:
不考虑纤维取向
考虑纤维取向
分析结果与实际成型结果比较:
分析结果:最大直径 38.60mm,最小直径 38.36mm,圆度 0.24。 实际结果:最大直径 38.68mm,最小直径 38.24mm,圆度 0.44。 从分析结果和实际结果可以看出制品翘曲变形,镜筒截面圆度不佳。 从以上分析结果可以看出熔体流动不平衡, 保压压力不平衡是导致制品收缩不均衡和翘 曲变形的主要原因。改进方案增大浇注系统尺寸如图 2 所示。
2. Moldex3D 充模流动数学模型
Moldex3D 中采用 3D 网格,聚合物的塑胶行为被假设为牛顿流体,因此非等温三维流 动行为可由以下的数学式表示[6]:
u 0 t ( u) ( u u ) g t
(1) (2) (3) (4)
改进方案
初始方案:最大直径 38.60mm,最小直径 38.36mm,圆度 0.24。 改进方案:最大直径 38.74mm,最小直径 38.55mm,圆度 0.19。 由结果可知,通过改进浇注系统,制品翘曲变形得到改善,圆度提高。
4.Moldex3D 优化注射工艺
实例模型为 LCD 外壳,模型如图 5 所示,制品厚度分布如图 6 所示。LCD 外壳广泛用 于电脑电视机,制品长度 458mm,宽度 174mm,高度 116.5mm,体积 260cm3。材料为
体积收缩率结果:
改变工艺参数后,体积收缩率范围为 0%~3.8%,分布仍然不均匀,但是流动末端孔周 围区域的收缩率从 4.6%下降到 3.8%。
表 1 初始方案与改进方案项目比较 项目 注射压力 压力降 注射时间 最大体积收缩率 填充体积 初始方案 106MPa 32MPa 6.7Sec 4.66% 231.55cc 1.4mm 2.1mm 0.6mm 1.4mm 1.2mm 1.2mm 改进方案 101MPa 33MPa 10.6Sec 3.84% 231.55cc 翘曲变形比较 X 方向最小变形量 X 方向最大变形量 Y 方向最小变形量 Y 方向最大变形量 Z 方向最小变形量 Z 方向最大变形量 1.3mm 1.6mm 0.5mm 1.2mm 1.0mm 1.0mm 7.1% 23.8% 16.7% 14.2% 16.7% 16.7% 改善 4.7% -3.1% -58.2% 17.6% 0.0%