铰孔
铰孔最小孔径-概述说明以及解释

铰孔最小孔径-概述说明以及解释1.引言1.1 概述铰孔是一种常见的加工方法,它在工业领域中被广泛应用。
铰孔是指通过切削工具,在工件上形成一个圆柱形孔。
这种加工方法常用于制造零件、组装设备以及修复损坏的孔径。
铰孔最小孔径是指在进行铰孔时,所能达到的最小孔径尺寸。
它在加工过程中扮演着至关重要的角色。
最小孔径的大小直接影响到零件的质量和性能。
通常情况下,铰孔最小孔径越小,所能加工的工件尺寸范围就越广。
铰孔最小孔径的重要性不容忽视。
首先,它决定了孔的精度和光洁度。
较小的孔径能够提供更高的精度和光洁度,从而保证了零件的质量。
其次,最小孔径的大小也影响到零件的强度和稳定性。
较小的孔径能够增加零件的强度,提高其抗压能力和抗震能力。
然而,铰孔最小孔径受到多个因素的影响。
首先,切削工具的质量和尺寸会直接影响到最小孔径的大小。
高质量的切削工具能够提供更小的最小孔径。
其次,工件材料的性质也会对最小孔径产生影响。
不同材料的切削性能不同,从而对最小孔径的要求也不同。
最后,加工环境和操作技术也能够对最小孔径产生一定的影响。
铰孔最小孔径的应用领域非常广泛。
无论是在汽车制造、航空航天、还是在机械制造等领域,铰孔都扮演着重要的角色。
铰孔最小孔径的研究和应用,有助于提高加工效率,提高零件质量,并推动工业制造的发展。
综上所述,铰孔最小孔径是影响零件质量和性能的关键因素。
它决定了零件的精度、光洁度、强度和稳定性。
铰孔最小孔径的研究和应用在工业领域具有重要意义,将为工业制造的发展带来更多机遇和挑战。
1.2 文章结构文章结构是论文撰写中非常重要的一部分,它为读者提供了整篇文章的框架和逻辑顺序。
一个清晰、有条理的结构能够帮助读者更好地理解和吸收文章的内容。
本文将按照以下结构进行展开:1. 引言1.1 概述在引言部分,我们将首先介绍铰孔的定义和作用,以便读者对铰孔有一个基本的了解。
然后,我们将描述本篇文章的结构和目的,为读者提供一个文章整体的框架。
铰孔

使铰刀温度升高
5.余量太多 1.铰刀刀刃不锋利及刀刃上有崩 口、毛刺 表面粗糙 2.余量过大或过小 度差 3.切削速度太高,产生积屑瘤 4.切削液选择不当
2.留适当的铰削余量
3.降低切削速度,用油石把积屑瘤从刀刃上磨去 4.合理选择切削液
10
(1)柄部
用来夹持和传递转矩。(见图)
(2)工作部分 由引导部分l1、切削部分l2、修光部分l3、和 倒锥l4组成。(见图)
1)引导部分 铰刀开始进入孔内时的导向部分。
2)切削部分 担负主要切削工作,铰削时定心好,切屑薄。 3)修光部分 有棱边,起定向、碾光孔壁、控制铰刀直径和 便于测量等作用。 4)倒锥部分 减小铰刀与孔壁之间的摩擦,还可防止产生喇 叭孔和孔径扩大。
③将内孔擦净后,检查孔径尺寸。 2)铰不通孔(见图) ①注意铰削深度,及时退刀。 ②中途退刀几次清除切屑。 注:铰钢件,新刀加乳化液,旧刀加切削油;铰铸件,新 刀加煤油,旧刀不加。
8
二、铰孔方法
9
三、铰孔废品分析
铰孔时产生废品的原因及预防方法
废品种类 产生原因 1.铰刀直径太大 2.铰刀刃口径向振摆过大 孔径扩大 3.尾座偏,铰刀与孔中心不重合 4.切削速度太高,产生积屑瘤和 预防方法 1.仔细测量尺寸,根据孔径尺寸要求,研磨铰刀 2.重新修磨铰刀刃口 3.校正尾座,使其对中,最好采用浮动套筒 4.降低切削速度,加充分的切削液 5.正确选择铰削余量 1.重新刃磨,表面粗糙度要低,刃磨后保管好, 不许碰毛
铰孔前的内孔表面粗糙度不得大于Ra6.3µ m。
2、铰孔方法
(1)准备工作 1)找正尾座中心。
2)固定尾座,尾座套筒伸出50~60mm。
3)选好铰刀。
7
二、铰孔方法
钳工铰刀铰孔的方法有哪些
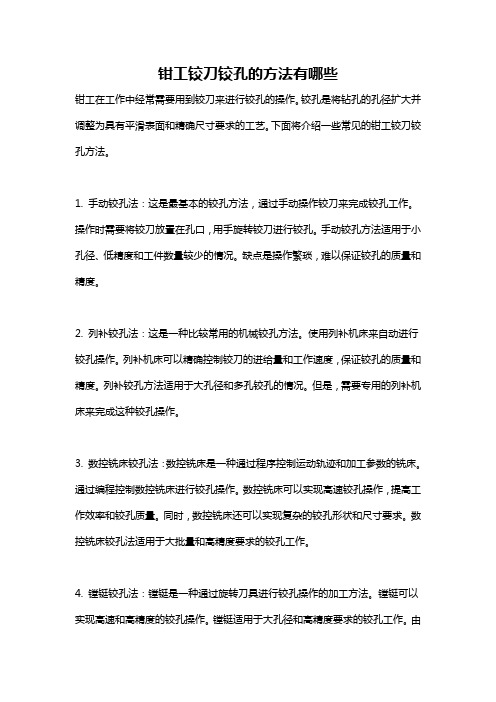
钳工铰刀铰孔的方法有哪些钳工在工作中经常需要用到铰刀来进行铰孔的操作。
铰孔是将钻孔的孔径扩大并调整为具有平滑表面和精确尺寸要求的工艺。
下面将介绍一些常见的钳工铰刀铰孔方法。
1. 手动铰孔法:这是最基本的铰孔方法,通过手动操作铰刀来完成铰孔工作。
操作时需要将铰刀放置在孔口,用手旋转铰刀进行铰孔。
手动铰孔方法适用于小孔径、低精度和工件数量较少的情况。
缺点是操作繁琐,难以保证铰孔的质量和精度。
2. 列补铰孔法:这是一种比较常用的机械铰孔方法。
使用列补机床来自动进行铰孔操作。
列补机床可以精确控制铰刀的进给量和工作速度,保证铰孔的质量和精度。
列补铰孔方法适用于大孔径和多孔铰孔的情况。
但是,需要专用的列补机床来完成这种铰孔操作。
3. 数控铣床铰孔法:数控铣床是一种通过程序控制运动轨迹和加工参数的铣床。
通过编程控制数控铣床进行铰孔操作。
数控铣床可以实现高速铰孔操作,提高工作效率和铰孔质量。
同时,数控铣床还可以实现复杂的铰孔形状和尺寸要求。
数控铣床铰孔法适用于大批量和高精度要求的铰孔工作。
4. 镗铤铰孔法:镗铤是一种通过旋转刀具进行铰孔操作的加工方法。
镗铤可以实现高速和高精度的铰孔操作。
镗铤适用于大孔径和高精度要求的铰孔工作。
由于镗铤操作比较复杂,需要相应的设备和技术支持,因此一般用于专业铰孔加工。
5. 铰孔刀铰孔法:铰孔刀是一种专门用于铰孔操作的刀具。
铰孔刀一般由多刃刀片组成,可以实现高速和高精度的铰孔操作。
铰孔刀适用于各种孔径和尺寸要求的铰孔工作。
同时,铰孔刀还可以实现不同形状和角度的铰孔加工。
6. 内外复合铰孔法:内外复合铰孔是一种通过内外两个铰孔刀进行铰孔操作的加工方法。
通过内外复合铰孔可以实现同时铰削内外两侧的铰孔加工,提高工作效率和铰孔质量。
内外复合铰孔法适用于需要同时加工内外铰孔的工件。
7. 其他特殊铰孔法:还有一些特殊铰孔方法,如刀座铰孔法、补偿铰孔法、动力铰孔法等。
这些方法一般用于特殊的铰孔工艺和特殊的工件加工要求。
铰孔的工艺

铰孔的工艺铰孔是一种常用的加工工艺,用于制造零件的孔加工。
它是通过铰刀在工件上进行旋转运动,以削除工件上的金属材料,最终形成所需的孔形状和尺寸。
铰孔工艺主要包括以下几个方面:工具选择、加工参数、加工步骤和注意事项。
首先,工具选择是铰孔工艺中非常重要的一步。
常见的铰刀有手动铰刀、机械铰刀和数控铰刀。
手动铰刀适用于简单的孔加工,操作简单方便;机械铰刀适用于批量生产,能够提高工作效率;数控铰刀适用于复杂的孔加工,可以实现高精度的加工。
其次,加工参数也是铰孔工艺中需要注意的一个方面。
首先是转速,一般根据工件材料和孔径大小选择合适的转速,以保证加工效果和工具寿命。
其次是进给速度,进给速度过快容易造成毛刺和刀具损坏,进给速度过慢则会影响加工效率。
最后是切削深度,切削深度应根据工件的强度和刚度选取适当的值,以避免过大的切削力和振动。
加工步骤是铰孔工艺中需要严格按照规定执行的步骤。
首先是确定铰刀的位置和夹持工件。
工件应安装牢固,以免产生振动和偏差。
然后是设置加工参数,包括转速、进给速度和切削深度。
接下来是进行试切,通过试切来调整和校准加工参数,确定最佳的加工条件。
最后是正式加工,进行铰孔操作,及时清理切屑和冷却润滑。
最后,铰孔工艺中还需要注意一些事项。
首先是要选择合适的冷却润滑剂,以降低切削温度和减少刀具磨损。
其次是要保持切削刃的锋利度,定期检查和更换刀具,以保证加工质量。
另外,需要注意加工过程中的安全问题,采取必要的防护措施,避免事故发生。
总之,铰孔是一种常用的加工工艺,通过选择合适的工具、设置有效的加工参数、执行正确的加工步骤和注意事项,可以保证加工质量和效率。
同时,铰孔工艺也需要根据具体的情况进行调整和优化,以满足不同零件的加工需求。
铰孔底孔的计算公式
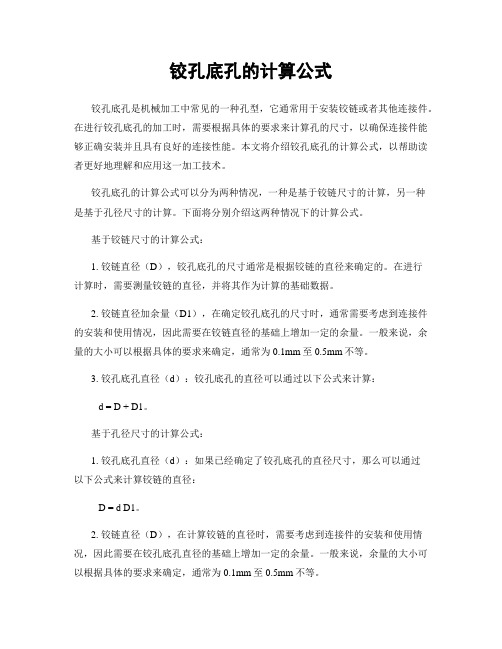
铰孔底孔的计算公式铰孔底孔是机械加工中常见的一种孔型,它通常用于安装铰链或者其他连接件。
在进行铰孔底孔的加工时,需要根据具体的要求来计算孔的尺寸,以确保连接件能够正确安装并且具有良好的连接性能。
本文将介绍铰孔底孔的计算公式,以帮助读者更好地理解和应用这一加工技术。
铰孔底孔的计算公式可以分为两种情况,一种是基于铰链尺寸的计算,另一种是基于孔径尺寸的计算。
下面将分别介绍这两种情况下的计算公式。
基于铰链尺寸的计算公式:1. 铰链直径(D),铰孔底孔的尺寸通常是根据铰链的直径来确定的。
在进行计算时,需要测量铰链的直径,并将其作为计算的基础数据。
2. 铰链直径加余量(D1),在确定铰孔底孔的尺寸时,通常需要考虑到连接件的安装和使用情况,因此需要在铰链直径的基础上增加一定的余量。
一般来说,余量的大小可以根据具体的要求来确定,通常为0.1mm至0.5mm不等。
3. 铰孔底孔直径(d):铰孔底孔的直径可以通过以下公式来计算:d = D + D1。
基于孔径尺寸的计算公式:1. 铰孔底孔直径(d):如果已经确定了铰孔底孔的直径尺寸,那么可以通过以下公式来计算铰链的直径:D = d D1。
2. 铰链直径(D),在计算铰链的直径时,需要考虑到连接件的安装和使用情况,因此需要在铰孔底孔直径的基础上增加一定的余量。
一般来说,余量的大小可以根据具体的要求来确定,通常为0.1mm至0.5mm不等。
3. 铰链直径加余量(D1),在确定铰链的直径时,需要考虑到连接件的安装和使用情况,因此需要在铰孔底孔直径的基础上增加一定的余量。
一般来说,余量的大小可以根据具体的要求来确定,通常为0.1mm至0.5mm不等。
通过上述的计算公式,我们可以根据具体的要求来计算铰孔底孔的尺寸,从而确保连接件能够正确安装并且具有良好的连接性能。
在实际的加工过程中,需要根据具体的情况来选择合适的计算公式,并且在计算时需要考虑到连接件的安装和使用情况,以确保计算结果的准确性和可靠性。
《铰孔加工技术》课件

提高装夹稳定性
采用合适的夹具或辅助支撑,确保工件装夹牢固 。
ABCD
加强刀具管理
定期检查刀具磨损情况,及时更换刀片。
使用冷却液并控制切削热
选用合适的冷却液,保持切削区域充分冷却,减 少刀具热磨损。
06
铰孔加工技术的发展趋势与展望
硬质合金铰刀
适用于高硬度材料的加工。
可转位铰刀
适用于高效、高精度的加工。
铰孔刀具的安装与调整
刀具安装
确保刀具与主轴连接牢固,无松动现象。
刀具调整
根据孔径和精度要求,调整刀具的伸出量和 刃磨角度。
刀具磨损
定期检查刀具磨损情况,及时更换或刃磨。
03
铰孔加工工艺流程
铰孔加工前的准备
01
确定工件材料和规 格
列举铰孔加工的应用场景,并解释其原因。
详细描述
铰孔加工广泛应用于机械制造、航空航天、汽车、船舶等领域。对于需要高精度孔系、 密封性要求较高的场合,铰孔加工具有不可替代的作用。例如,在发动机制造中,气缸 和活塞环的配合孔需要高精度的铰孔加工来保证其密封性和使用寿命。此外,在桥梁、
建筑等基础设施领域,铰孔加工也用于连接件的孔加工和维修等。
随着制造业的发展,对铰孔加工技术的要求也越 来越高,如何提高加工精度、降低成本、提高效 率成为亟待解决的问题。
铰孔加工技术的未来发展趋势
智能化
随着智能制造技术的不断发展,铰孔加工技术将向智能化 方向发展,实现加工过程的自动化和智能化控制。
高精度
随着制造业对产品精度要求的不断提高,铰孔加工技术将 向高精度方向发展,进一步提高孔的加工精度和表面质量 。
手动铰孔应注意什么
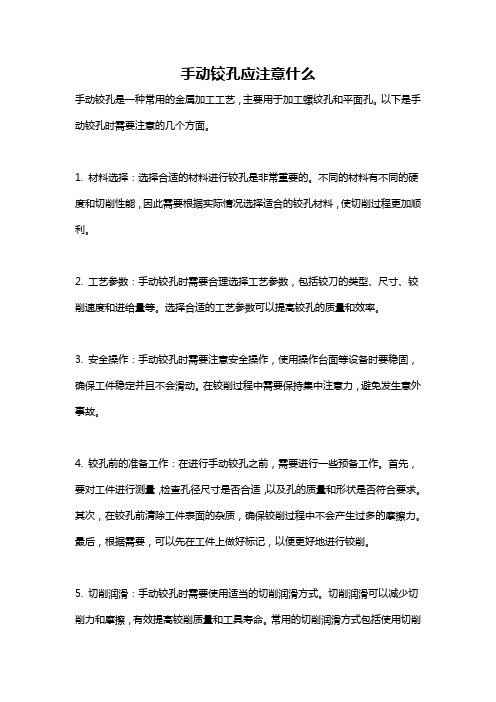
手动铰孔应注意什么手动铰孔是一种常用的金属加工工艺,主要用于加工螺纹孔和平面孔。
以下是手动铰孔时需要注意的几个方面。
1. 材料选择:选择合适的材料进行铰孔是非常重要的。
不同的材料有不同的硬度和切削性能,因此需要根据实际情况选择适合的铰孔材料,使切削过程更加顺利。
2. 工艺参数:手动铰孔时需要合理选择工艺参数,包括铰刀的类型、尺寸、铰削速度和进给量等。
选择合适的工艺参数可以提高铰孔的质量和效率。
3. 安全操作:手动铰孔时需要注意安全操作,使用操作台面等设备时要稳固,确保工件稳定并且不会滑动。
在铰削过程中需要保持集中注意力,避免发生意外事故。
4. 铰孔前的准备工作:在进行手动铰孔之前,需要进行一些预备工作。
首先,要对工件进行测量,检查孔径尺寸是否合适,以及孔的质量和形状是否符合要求。
其次,在铰孔前清除工件表面的杂质,确保铰削过程中不会产生过多的摩擦力。
最后,根据需要,可以先在工件上做好标记,以便更好地进行铰削。
5. 切削润滑:手动铰孔时需要使用适当的切削润滑方式。
切削润滑可以减少切削力和摩擦,有效提高铰削质量和工具寿命。
常用的切削润滑方式包括使用切削油、切削脂、切削液等。
6. 切削方向和切削力控制:手动铰孔时需要注意切削方向和切削力的控制。
一般来说,铰削的切削方向应与工件的主轴线平行,以避免切削力不稳定或切削刃损坏。
在铰削过程中,需要通过合适的力量控制技巧来控制切削力的大小和方向,使铰削更加稳定。
7. 放样和磨削:手动铰孔之后,需要进行刀具的磨削和修整,以保持刀具的良好状态和铰孔的质量。
同时,也需要对铰孔进行放样,检查铰孔的尺寸精度和形状是否符合要求,以及表面质量是否良好。
总而言之,手动铰孔是一项需要技术和经验的工艺,需要注意以上几个方面。
只有在合适的材料、合理的工艺参数、安全的操作、良好的切削润滑、正确的切削方向和切削力控制的基础上,才能获得满意的铰孔结果。
铰孔的手工操作方法

铰孔的手工操作方法铰孔是制造过程中常见的一种加工方法,用于在工件上加工出与螺栓或螺纹紧固件配合的孔。
下面将详细介绍铰孔的手工操作方法。
铰孔工具的选择:铰孔操作中最常用的工具是铰刀,铰刀一般由高速钢或硬质合金制成,具有不同规格和形状。
根据工件材料、孔径尺寸和要求的精度,选择合适的铰刀。
准备工作:1. 对要加工的工件进行清洁,确保其表面光滑无杂质。
2. 检查铰刀的整体状况和刃口的钝利度,如有磨损或损坏应更换。
铰孔操作步骤:1. 将工件夹紧在工作台上,确保工件在加工过程中的稳定性。
2. 根据需要,选取合适的铰刀。
3. 使用手动铰刀或机械铰刀,将铰刀插入工件孔中,保持刀具的垂直和水平位置。
4. 抓住铰刀柄,使铰刀刃缓慢切入,不要用力过猛,以免造成切削刃折断或工件变形。
5. 在切削过程中,保持适当的切削润滑,如加水或切削液,以提高切削质量和延长刀具寿命。
6. 轻轻转动手柄,保证切削刃的平稳运动,避免过快或过慢拉刀,影响切削效果。
7. 当切削刃完全进入工件后,继续轻轻转动手柄,使刀具顺畅地穿过工件,直至铰刀的穿孔面与工件表面接触。
8. 在切削过程中,注意观察切屑的排出情况,必要时使用吹气枪清洁切屑,防止切屑积聚影响切削。
9. 切削结束后,将铰刀逆时针旋转拉出,用毛刷清理孔底和孔壁,确保切削面光滑无毛刺。
操作技巧与注意事项:1. 在切削过程中,切不可用手指触摸切削刃或切削区域,以免导致手指受伤。
操作时应戴好手套和护目镜等个人防护装备。
2. 切削中要保持平稳推拉刀具,避免过度挤压或过快拉刀,以保证加工质量和延长刀具寿命。
3. 加工过程中要保持集中注意力,注意观察切削反应,发现异常及时停机检查问题。
4. 铰孔时尽量避免材料变热,可适时进行冷却,以保证刀削面的质量,并减小工件的热变形。
5. 在规定直径范围内可选用合适的背吃刀量,背吃刀量过大容易导致刀具损坏或切削剧变,而背吃刀量过小则可能影响铰孔质量。
6. 操作完毕后,及时清理切屑和切削液,保持工具的整洁。
详细说明铰孔工艺的操作流程及注意事项

详细说明铰孔工艺的操作流程及注意事项下载温馨提示:该文档是我店铺精心编制而成,希望大家下载以后,能够帮助大家解决实际的问题。
文档下载后可定制随意修改,请根据实际需要进行相应的调整和使用,谢谢!并且,本店铺为大家提供各种各样类型的实用资料,如教育随笔、日记赏析、句子摘抄、古诗大全、经典美文、话题作文、工作总结、词语解析、文案摘录、其他资料等等,如想了解不同资料格式和写法,敬请关注!Download tips: This document is carefully compiled by theeditor.I hope that after you download them,they can help yousolve practical problems. The document can be customized andmodified after downloading,please adjust and use it according toactual needs, thank you!In addition, our shop provides you with various types ofpractical materials,such as educational essays, diaryappreciation,sentence excerpts,ancient poems,classic articles,topic composition,work summary,word parsing,copy excerpts,other materials and so on,want to know different data formats andwriting methods,please pay attention!铰孔工艺的操作流程及注意事项详解铰孔是一种精密的机械加工工艺,主要用于改善孔的尺寸精度、形状精度和表面粗糙度。
钻孔、扩孔、锪孔与铰孔

• 可持续性与环保:随着全球环保意识的提高,可持续性和环保将成为切削加工 发展的重要方向。新型切削液和冷却技术的研发将减少切削过程中的冷却液使 用和废弃物产生,同时新型切削工具和设备的研发也将进一步提高切削效率, 减少能源消耗和碳排放。
扩孔钻
扩孔钻是一种具有切削刃的刀具,其 切削刃呈圆柱形或圆锥形,用于扩大 已钻孔的直径。
扩孔应用
适用范围
扩孔适用于各种材料,如铸件、 锻件、有色金属等,尤其适用于 大型工件和不易进行镗削加工的
工件。
应用场景
扩孔常用于修正已钻孔的误差、提 高孔的精度和减小表面粗糙度,也 可用于大型工件中打通孔或深孔。
铰孔
铰孔是用铰刀对已钻出的孔进行 精加工的过程,以提高孔的尺寸
精度和减小孔的表面粗糙度。
目的和意义
01
提高孔的加工精度和质量
通过钻孔、扩孔、锪孔和铰孔等加工方法,可以减小孔的尺寸误差、提
高孔的位置精度和减小表面粗糙度,从而提高孔的加工精度和质量。
02
满足不同的工艺要求
不同的加工方法适用于不同的工艺要求 WATCHING
感谢您的观看
冷却润滑
使用冷却液或润滑剂进行冷却和润滑, 以减小切削热和摩擦力,提高加工精 度和表面质量。
检测与修正
在加工过程中,应定期检测孔的尺寸 和形状,如有误差应及时修正。
06 总结
钻孔、扩孔、锪孔与铰孔的比较
钻孔
钻孔是使用钻头在实心材料上打孔的过程。它通常用于在 金属、木材、塑料等材料上打孔,是加工过程中的基础步 骤。
铰孔所能达到的表面粗糙度

铰孔所能达到的表面粗糙度铰孔是一种常用的孔加工方法,广泛应用于各种机械制造业中。
在铰孔过程中,刀具以一定的切削速度和进给量对孔壁进行切削,从而实现对孔的加工。
铰孔所能达到的表面粗糙度是衡量铰孔加工质量的重要指标之一。
表面粗糙度是指加工表面上微小峰谷不平整程度的度量,通常用Ra值来表示。
Ra值越小,表面越光滑;反之,表面越粗糙。
在铰孔过程中,由于切削力和切削热的影响,孔壁表面会产生一定的微观不平整度,这就是表面粗糙度的来源。
铰孔所能达到的表面粗糙度与多个因素有关。
首先是刀具的选用。
铰刀的材质、刃磨质量和几何参数等因素都会对铰孔表面的粗糙度产生影响。
合理的刀具选用能够有效提高铰孔的加工质量。
其次是切削参数的选择。
切削速度、进给量和切削深度等切削参数的选择也会直接影响到铰孔表面的粗糙度。
过高的切削速度和过大的进给量会导致切削力增大,孔壁表面粗糙度增加;而切削深度过大则可能导致刀具磨损加剧,进一步恶化表面粗糙度。
此外,工件材料的质量和硬度也会对铰孔表面的粗糙度产生影响。
硬度较高的材料加工难度较大,表面粗糙度可能相对较高;而工件表面存在的油污、氧化皮等杂质也会对铰孔加工产生不良影响,增加表面粗糙度。
为了获得较低的表面粗糙度,需要采取相应的措施。
首先,要选择合适的刀具,并确保刀具的质量和刃磨精度。
其次,要合理选择切削参数,避免过高的切削速度和过大的进给量。
同时,对于工件材料的选择和处理也要加以重视,确保工件表面清洁、无杂质。
在实际应用中,铰孔所能达到的表面粗糙度往往受到多种因素的共同影响。
因此,在铰孔加工过程中,需要综合考虑各种因素,采取有效的措施来提高铰孔的加工质量,实现较低的表面粗糙度。
只有这样,才能满足不断提高的机械加工要求,为机械制造业的发展做出贡献。
铰孔加工常见的问题及解决措施

序号
问题
解决措施
1
孔径变大
(1)减小铰刀直径
(2)铰刀的中心没有对准工件的中心,提高铰刀与铰孔的同轴度
(3)铰刀径向跳动过大,好的径向跳动是铰削成功的关键
(4)铰刀的柄部存在碰撞划痕
(5)使用套管、套筒时,锥柄部应该保持干净,无杂物
(6)出现积屑瘤,使用合适的切削液,调整切削条件
7
铰刀的柄部破损
(1)柄部的硬度是否足够,太低可能会导致疲劳或变形;太高可能会破损
(2)检查刀柄与套管的配合是否不良,不要使用有缺陷的刀柄
8
寿命较短
(1)提高铰刀的刃部硬度
(2)铰刀的刃部采用高级材料
(3)检查切削液
(4)采用软氮化等表面处理
(5)将直刃改为螺旋刃
(6)综合检查影响铰刀加工精度的各因素
(8)确定铰刀倒锥与被加工材料是否匹配
(9)适当增大刃带宽和刃背宽
5
孔的加工精度较差
(1)铰刀退刀时,应向同一方向旋转的同时拔出,绝不可反转
(2)降低转速
(3)增加刃数
(4)适当扩大刃带宽增强导向性能和挤压效果
(5)通过表面处理增加润滑性
(6)选择合适的切削液
6
铰刀出现折断、烧伤
(1)导孔在铰削前存在缺陷,比如说导孔直线度较差
(4)调整导孔与铰刀的同轴度
(5)确保铰削余量均匀
4
孔的精加工面表面粗糙度较差
(1)铰刀切入部的表面粗糙度太差
(2)降低转速
(3)确保铰削余量正确。太大或太小都会导致表面粗糙度变差
(4)确定铰刀的容屑槽足够,避免切屑的堵塞
(5)增大铰刀切入部的后角
(6)切入部及刃带面有无熔着物
(完整版)铰孔方法
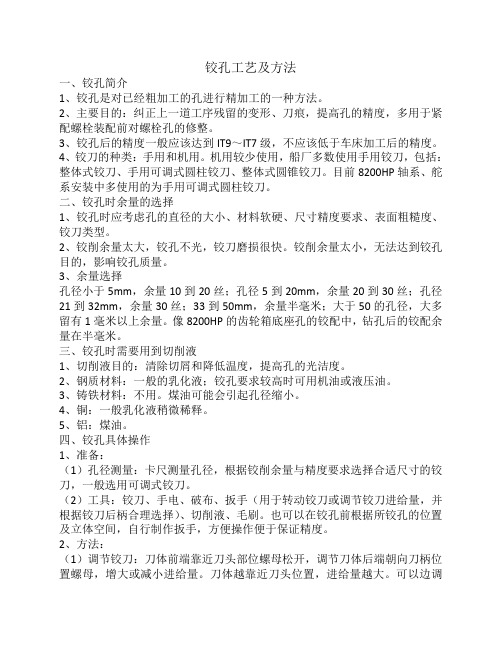
铰孔工艺及方法一、铰孔简介1、铰孔是对已经粗加工的孔进行精加工的一种方法。
2、主要目的:纠正上一道工序残留的变形、刀痕,提高孔的精度,多用于紧配螺栓装配前对螺栓孔的修整。
3、铰孔后的精度一般应该达到IT9~IT7级,不应该低于车床加工后的精度。
4、铰刀的种类:手用和机用。
机用较少使用,船厂多数使用手用铰刀,包括:整体式铰刀、手用可调式圆柱铰刀、整体式圆锥铰刀。
目前8200HP轴系、舵系安装中多使用的为手用可调式圆柱铰刀。
二、铰孔时余量的选择1、铰孔时应考虑孔的直径的大小、材料软硬、尺寸精度要求、表面粗糙度、铰刀类型。
2、铰削余量太大,铰孔不光,铰刀磨损很快。
铰削余量太小,无法达到铰孔目的,影响铰孔质量。
3、余量选择孔径小于5mm,余量10到20丝;孔径5到20mm,余量20到30丝;孔径21到32mm,余量30丝;33到50mm,余量半毫米;大于50的孔径,大多留有1毫米以上余量。
像8200HP的齿轮箱底座孔的铰配中,钻孔后的铰配余量在半毫米。
三、铰孔时需要用到切削液1、切削液目的:清除切屑和降低温度,提高孔的光洁度。
2、钢质材料:一般的乳化液;铰孔要求较高时可用机油或液压油。
3、铸铁材料:不用。
煤油可能会引起孔径缩小。
4、铜:一般乳化液稍微稀释。
5、铝:煤油。
四、铰孔具体操作1、准备:(1)孔径测量:卡尺测量孔径,根据铰削余量与精度要求选择合适尺寸的铰刀,一般选用可调式铰刀。
(2)工具:铰刀、手电、破布、扳手(用于转动铰刀或调节铰刀进给量,并根据铰刀后柄合理选择)、切削液、毛刷。
也可以在铰孔前根据所铰孔的位置及立体空间,自行制作扳手,方便操作便于保证精度。
2、方法:(1)调节铰刀:刀体前端靠近刀头部位螺母松开,调节刀体后端朝向刀柄位置螺母,增大或减小进给量。
刀体越靠近刀头位置,进给量越大。
可以边调节边插进孔内进行试验,以铰刀刀体插入孔内大约一半位置为最理想。
进给量调节好后锁紧上下螺母。
一般情况下,每次的进给量逐步减小,最后一刀完成后可达到铰孔的光洁度和精度要求。
铰孔
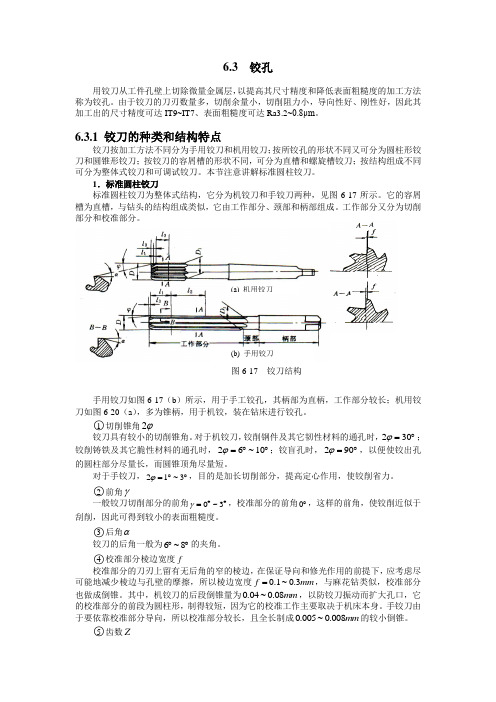
6.3 铰孔用铰刀从工件孔壁上切除微量金属层,以提高其尺寸精度和降低表面粗糙度的加工方法称为铰孔。
由于铰刀的刀刃数量多,切削余量小,切削阻力小,导向性好、刚性好,因此其加工出的尺寸精度可达IT9~IT7、表面粗糙度可达Ra3.2~0.8μm 。
6.3.1 铰刀的种类和结构特点铰刀按加工方法不同分为手用铰刀和机用铰刀;按所铰孔的形状不同又可分为圆柱形铰刀和圆锥形铰刀;按铰刀的容屑槽的形状不同,可分为直槽和螺旋槽铰刀;按结构组成不同可分为整体式铰刀和可调试铰刀。
本节注意讲解标准圆柱铰刀。
1.标准圆柱铰刀标准圆柱铰刀为整体式结构,它分为机铰刀和手铰刀两种,见图6-17所示。
它的容屑槽为直槽,与钻头的结构组成类似,它由工作部分、颈部和柄部组成。
工作部分又分为切削部分和校准部分。
手用铰刀如图6-17(b )所示,用于手工铰孔,其柄部为直柄,工作部分较长;机用铰刀如图6-20(a ),多为锥柄,用于机铰,装在钻床进行铰孔。
○1切削锥角2ϕ 铰刀具有较小的切削锥角。
对于机铰刀,铰削钢件及其它韧性材料的通孔时,230ϕ=︒;铰削铸铁及其它脆性材料的通孔时,26~10ϕ=︒︒;铰盲孔时,290ϕ=︒,以便使铰出孔的圆柱部分尽量长,而圆锥顶角尽量短。
对于手铰刀,21~3ϕ=︒︒,目的是加长切削部分,提高定心作用,使铰削省力。
○2前角γ 一般铰刀切削部分的前角0~3γ=︒︒,校准部分的前角0︒,这样的前角,使铰削近似于刮削,因此可得到较小的表面粗糙度。
○3后角α 铰刀的后角一般为6~8︒︒的夹角。
○4校准部分棱边宽度f校准部分的刀刃上留有无后角的窄的棱边,在保证导向和修光作用的前提下,应考虑尽可能地减少棱边与孔壁的摩擦,所以棱边宽度0.1~0.3f mm =,与麻花钻类似,校准部分也做成倒锥。
其中,机铰刀的后段倒锥量为0.04~0.08mm ,以防铰刀振动而扩大孔口,它的校准部分的前段为圆柱形,制得较短,因为它的校准工作主要取决于机床本身。
打孔加工中的铰孔技术

打孔加工中的铰孔技术在机械制造领域,孔的加工是一项很重要的工作。
钻孔、铰孔、镗孔等加工方法都是常见的,其中铰孔技术在一些特定的制造场合中,显得非常重要。
本文将重点介绍打孔加工中的铰孔技术,包括铰孔的定义、工作原理、加工方法、技巧以及应用领域等方面,希望能对相关领域的工作者有所帮助。
一、铰孔的定义和工作原理铰孔,是指在制造工艺中,在一定直径范围内先进行一定直径的钻孔或者镗孔,再用一把铰刀进行铰孔,并得到具有一定直径精度和柔性的倒锥孔。
铰孔的作用是让螺纹和轴类零件的安装更加方便和准确。
为了保证铰孔的质量,关键需要掌握铰孔的工作原理。
铰孔技术分为交替铰削和连续铰削两种。
交替铰削就是指在铰刀做上下或前后往复运动时,在铰孔内交替切削,以获得形状精度高、表面质量好的铰孔。
连续铰削是指用铰刀持续运动,直到达到所需要的深度为止。
铰孔的工作原理主要就是进行侧向切削和径向扩孔。
二、铰孔的加工方法铰孔是采用铰孔刀进行加工的。
铰孔刀通常由刀柄、承钳、刀片等三部分构成。
刀旋转时,铰刀的刀片沿孔深向下移动,同时在侧向移动。
通过分离刃和导向刃的不同运动状态来吸取切屑。
铰孔的加工方法分为手动、机械以及数控加工三种。
1. 手动铰孔:手动铰孔是铰孔技术最简单、常见的一种加工方式。
手动铰孔即是用手动工具进行加工。
手动铰孔工具主要包括手动操作铰孔刀和滑板两种。
手动加工通常适用于小型、少量零件生产。
2. 机械铰孔:机械铰孔是指在铰孔刀上通过节流蝶阀或者变压调整深度的加工方法,多用于深孔加工和大批量生产。
3. 数控铰孔:数控铰孔是采用计算机进行控制的铰孔加工方式。
数控铰孔可以实现高度自动化程度和质量,以及提高生产效率等优点。
三、铰孔的技巧铰孔虽然是一项在制造工艺中非常基础的技术,但要想掌握好铰孔技术,还需要注意以下几个方面的技巧:1. 铰孔切屑处理:由于铰孔刀的侧向切削和径向扩孔方式,会形成大量切屑,如果切屑积聚在铰孔中,会影响铰孔的成形精度。
铰孔加工基础知识
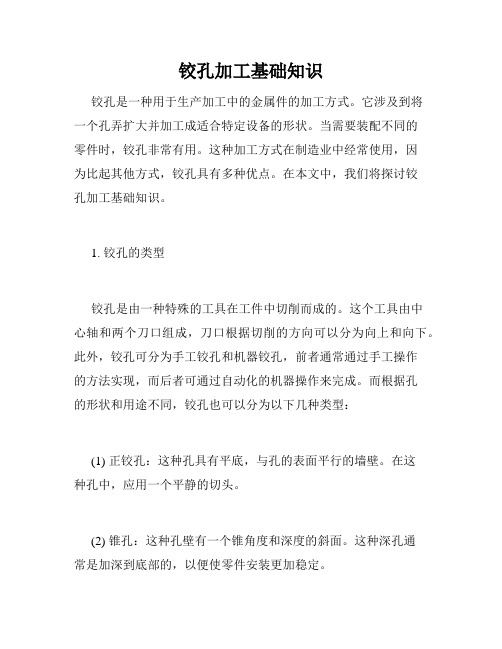
铰孔加工基础知识铰孔是一种用于生产加工中的金属件的加工方式。
它涉及到将一个孔弄扩大并加工成适合特定设备的形状。
当需要装配不同的零件时,铰孔非常有用。
这种加工方式在制造业中经常使用,因为比起其他方式,铰孔具有多种优点。
在本文中,我们将探讨铰孔加工基础知识。
1. 铰孔的类型铰孔是由一种特殊的工具在工件中切削而成的。
这个工具由中心轴和两个刀口组成,刀口根据切削的方向可以分为向上和向下。
此外,铰孔可分为手工铰孔和机器铰孔,前者通常通过手工操作的方法实现,而后者可通过自动化的机器操作来完成。
而根据孔的形状和用途不同,铰孔也可以分为以下几种类型:(1) 正铰孔:这种孔具有平底,与孔的表面平行的墙壁。
在这种孔中,应用一个平静的切头。
(2) 锥孔:这种孔壁有一个锥角度和深度的斜面。
这种深孔通常是加深到底部的,以便使零件安装更加稳定。
(3) 带肩锥孔:这种孔具有不同的角度和深度。
深度和角度有多个可变因素,因此必须选择适合特定零件的铰孔。
(4) 法兰孔:这是一种具有附加平面的孔,可以用于安装特殊类型的配件。
(5) 平底孔:这种孔在底部可以形成一种平面,通常适用于固件制造。
2. 铰孔的加工方法铰孔的加工方法可以分为三个步骤:预铰孔、粗加工和精加工。
(1) 预铰孔:这个过程旨在用一个预设的孔来开发空间,以便后续铰孔。
这通常是通过钻一个与最终孔直径相等或略小的孔来实现的。
(2) 粗加工:本阶段主要通过粗铰刀头将预铰孔的外形设计进行铰成最终孔的外形。
(3) 精加工:这个过程旨在让铰孔与钻孔的直径相等,并扩大孔的深度。
精加工的精度和精密度要求更高,并且可以使用定制工具和设备来完成。
3. 铰孔的应用铰孔可以在制造业中应用于各种用途。
如机床上的滑动界面和支撑表面,可以采用铰孔加工方法来保证精度。
此外,铰孔还可以用于制造汽车发动机缸体,以便使汽缸头和汽缸套的接口精度更高,并提高执行效率。
此外,精加工后的铰孔可以在高速列车行驶过程中确保信息的精确传输,可以用于加工高功率电器的安装领域,以确保设备可以牢固安装。
铰孔注意事项

铰孔注意事项
嘿,朋友们!今天咱就来聊聊铰孔那些事儿,这可真的太重要啦!
你想想看,要是在铰孔的时候马马虎虎,那会出多大乱子呀!比如说,在给一块金属板铰孔时,要是不注意刀具的选择,那铰出来的孔可能就不光滑,坑坑洼洼的,这能行吗?
首先呢,刀具的选择可不能马虎!就像战士上战场得挑把趁手的兵器一样,得选对刀具。
不同的材料要用不同的刀具,不然就像让短跑运动员去跑马拉松,那肯定不合适呀!比如铰钢件和铰铝件的刀具能一样吗?当然不能!
还有啊,铰孔的速度也要控制好!你总不能像开赛车似的,一股脑地猛冲吧!比如在铰一个很薄的零件时,速度太快,那不就直接弄变形啦,多糟糕呀!
再有就是要注意冷却液的使用。
这就好比大热天你赶路,不得喝点水凉快凉快呀!要是没有冷却液,刀具和工件都得“发烧”,那可就麻烦大了。
我就见过有人在铰孔的时候,啥都不管,最后弄得一塌糊涂,这不是自找麻烦吗?咱可不能学他!要认真对待每一个步骤。
哎呀,总之呀,铰孔这事可容不得半点马虎!就像建房子得把根基打牢一样,铰孔的每个细节都得处理好,才能得到让人满意的结果呀!咱千万别不当回事,不然到时候出了问题,后悔都来不及呢!这就是我的看法,大家可得记住啦!。
铰孔名词解释

铰孔名词解释
铰孔 (hinge hole) 是指在塑料制品、木材制品、金属制品等物体上存在的,用于连接两个部分的缝隙或孔洞。
这种孔洞通常是成对出现的,位于物体的两个不同方向上。
铰孔通常用于连接两个部件,使其相互连接并固定。
例如,在家具上,铰孔可以用来连接椅子的坐垫和靠背,使它们能够相互连接并保持稳定。
在建筑中,铰孔可以用来连接墙壁和天花板,以便在它们之间形成缝隙,以便安装管道和电线。
铰孔的存在可以使物体更加稳定,因为它们提供了两个方向上的固定点,使得物体更加牢固。
此外,铰孔还可以为物体提供更多的灵活性,例如,可以在物体的两个方向上自由移动或调整位置。
铰孔是一种重要的制造技术,在许多领域中都有广泛的应用。
在设计和制造物体时,需要考虑铰孔的存在,以便确保物体能够稳定、可靠地连接和固定。
铰孔工作总结

铰孔工作总结
铰孔是一种常见的加工工艺,用于在工件上加工圆孔或者调整孔的尺寸。
铰孔工作通常需要精准的操作和高质量的加工,以确保工件的质量和精度。
在铰孔工作中,操作者需要具备一定的技能和经验,同时需要使用适当的设备和工具。
首先,铰孔工作需要根据工件的要求选择合适的铰刀和切削参数。
不同的工件材料和尺寸需要不同类型和规格的铰刀,同时切削速度和进给速度也需要根据具体情况进行调整。
在选择铰刀和切削参数时,需要考虑到工件的材质、硬度和加工要求,以确保加工效果和加工质量。
其次,铰孔工作需要进行精准的定位和夹紧。
工件的定位和夹紧对于加工质量至关重要,如果定位不准确或者夹紧不牢固,会导致加工误差和工件质量不合格。
因此,在铰孔工作中,操作者需要严格按照工艺要求进行工件的定位和夹紧,确保工件在加工过程中保持稳定和精准。
最后,铰孔工作需要进行精细的加工和检测。
在铰孔过程中,操作者需要控制好切削参数和加工过程,确保加工的孔径和表面质量符合要求。
同时,需要对加工后的孔径进行精密的测量和检测,以确保加工质量和尺寸精度。
总的来说,铰孔工作需要操作者具备一定的技能和经验,同时需要使用适当的设备和工具。
精准的切削参数、精准的定位和夹紧、精细的加工和检测,是保证铰孔工作质量和精度的关键。
只有严格按照工艺要求进行操作,才能确保铰孔工作的质量和效果。
- 1、下载文档前请自行甄别文档内容的完整性,平台不提供额外的编辑、内容补充、找答案等附加服务。
- 2、"仅部分预览"的文档,不可在线预览部分如存在完整性等问题,可反馈申请退款(可完整预览的文档不适用该条件!)。
- 3、如文档侵犯您的权益,请联系客服反馈,我们会尽快为您处理(人工客服工作时间:9:00-18:30)。
提高铰孔加工质量之浅见
李文武
【摘要】:通过对铰孔加工工艺、加工质量分析,合理改进刀具结构,提高加工精度。
【关键词】:铰孔工艺切削用量质量控制刀具改进提高质量
铰孔在机械制造及装配维修加工中应用广泛,这要求学生在钳工实习中熟练掌握铰孔加工技术,严格控制铰孔质量。
经过实践总结,提高铰孔加工质量就要正确编制加工工艺,合理选择切削用量,对铰孔产生的质量问题进行正确分析、加以控制,对铰刀结构进行必要的改进。
具体方法如下:
一、铰孔工艺
1、提高预加工工序质量
提高预加工孔精度是保证铰孔质量的前提。
必须保证底孔不出现弯曲、锥度、椭圆、轴线歪斜、表面粗糙等缺陷。
2、合理编排工艺过程
对于精度为IT7-IT8、Ra1.6-0.8μm、D>20mm的孔,其铰孔加工工艺一般为:钻孔→扩孔→(镗孔)→粗铰→精铰。
其中,镗孔是在条件具备的情况下进行的,可以提高孔的直线度、降低表面粗糙度值。
二、合理选择切削用量
1、铰削余量
铰削余量过大,加工时铰刀易折断;铰削余量过小,则不能完全去除上道工序留下的加工痕迹,影响孔的尺寸精度和表面粗糙度。
根据加工经验,在钻床上铰削时(铰削余量/铰孔直径)分别取:0.1mm/3~4mm、0.2mm/5~10mm、1mm/12~16mm和2mm/18~30mm。
2、铰削速度
铰削速度过高或过低均易产生卷屑,影响加工表面粗糙度。
考虑到刀具的寿命,加工孔的质量。
铰孔时根据工件材料选择:v铰=5~12m/min。
3、进给量
进给量会使工件孔产生表面硬化和粗糙,应加以控制。
根据工件材料的不同,在钻床上铰孔时,f铰=0.18~1.5mm/r。
三、铰孔存在的质量问题,产生原因及控制方法
1、孔径增大
产生原因:1)铰刀外径尺寸偏大;2)铰削速度过高;3)进给量不当或加工余量过大;4)铰刀主偏角过大;5)铰刀弯曲;6)铰刀刃口粘附着切屑瘤;7)铰刀刃口摆差超差;8)切削液选择不合适;9)安装铰刀时锥柄表面未擦净;10)主轴轴承过松或损坏,铰刀在加工中晃动;11)铰孔时余量偏心,与工件不同轴;
控制方法:1)选择适当的铰刀外径;2)降低铰削速度;3)适当调整进给量或减少加工余量;4)适当减小主偏角;5)更换铰刀;6)刃口用油石修整或进行表面硬化处理;7)控制摆差在允许的范围内;8)选择冷却性能好的切削液;9)安装前将刀柄及主轴锥孔内部油污擦净;10)调整或更换主轴轴承;11)调整同轴度。
2、孔径缩小
产生原因:1)铰刀外径尺寸偏小;2)铰削速度过低;3)进给量过大;4)铰刀主偏角过小;5)切削液选择不合适;6)铰刀磨损部分未磨掉,弹性恢复使孔径缩小;7)铰削余量太大或铰刀不锋利,产生弹性恢复,使孔径缩小;8)内孔不圆,孔径不合格。
控制方法:1)选择适当的铰刀外径;2)适当提高铰削速度;3)适当降低进给量;4)适当增大主偏角;5)选择润滑性能好的油性切削液;6)定期更换铰刀;7)选取适当的铰削余量和刀具切削角度;8)提高孔加工与刀具刃磨的质量。
3、铰出的内孔不圆
产生原因:1)内孔表面有交叉孔;铰刀过长,刚性不足,铰削时产生振动;2)铰刀主偏角过小;3)铰刀刃带窄;4)铰孔余量偏心;5)薄壁工件装夹过紧,工件变形。
控制方法:1)采用不等分齿距的铰刀和较长、较精密的导向套;铰刀的安装采用刚性联接;2)增大主偏角;3)选用合格铰刀;4)控制底孔位置公差;5)采用恰当的夹紧方法,减小夹紧力。
4、孔内表面有明显棱面
产生原因:1)铰孔余量过大;2)铰刀切削部分后角过大;3)铰刀刃带过宽;4)主轴摆差过大。
控制方法:1)减小铰孔余量;2)减小切削部分后角;3)修磨刃带宽度;4)调整机床主轴。
5、内孔表面粗糙度值高
产生原因:1)铰削速度过高;2)切削液选择不合适,未能顺利流到切削处;3)铰刀主偏角过大且刃口不在同一圆周上;4)铰孔余量太大;5)铰孔余量不均匀或太小,局部表面未铰到;6)铰刀切削部分刃口不锋利,表面粗糙;7)铰刀刃带过宽;8)铰孔时排屑不畅;9)铰刀过度磨损;10)刃口有毛刺、积屑瘤。
控制方法:1)降低切削速度;2)正确选择切削液,经常清除切屑,用足够压力浇注切削液;3)适当减小主偏角,正确刃磨铰刀刃口;4)适当减小铰孔余量;5)提高底孔位置精度或增加铰孔余量;6)经过精磨或研磨达到要求;7)修磨刃带宽度;8)减少铰刀齿数,加大容屑槽空间;9)定期更换铰刀;10)用油石修整刃口。
6、铰刀刀齿崩刃
产生原因:1)铰孔余量过大;2)工件材料硬度过高;3)切削刃摆差过大,切削负荷不均匀;4)铰刀主偏角太小;5)铰深孔或盲孔时,切屑未及时清除;6)刃磨时刀齿已磨裂。
控制方法:1)修整底孔的孔径尺寸;2)降低材料硬度或采用硬质合金铰刀;3)控制摆差在合格范围内;4)加大主偏角;5)及时清除切屑;6)注意刃磨质量。
7、铰刀柄部折断
产生原因:1)铰孔余量过大;2)铰削余量分配及切削用量选择不合适;3)铰刀刀齿容屑空间小,切屑堵塞。
控制方法:1)修整底孔的孔径尺寸;2)修改余量分配,合理选择切削用量;3)减少铰刀齿数,加大容屑空间。
8、铰孔后孔的中心线不直
产生原因:1)底孔偏斜,铰刀不能纠正原有的弯曲度;2)导向不良,使铰刀在铰削中易偏离方向;3)铰刀安装偏斜,破坏了铰孔的垂直度。
控制方法:1)采用扩孔等工序校正孔;2)修整铰刀导向部分;3)注意正确操作。
四、改进刀具结构,提高铰孔质量
1、深孔铰刀的改进
铰削深孔(铰刀长度/铰刀直径为:L/D>5)时,经常出现铰刀折断现象,孔的表面质量达不到加工要求,主要原因是深孔排屑困难,堵塞在孔内的切屑容易刮伤已加工表面,并挤坏铰刀刀刃;冷却液不易到达切削区,难以对铰刀进行有效冷却,加剧了铰刀磨损甚至使铰刀折断。
为解决这一问题,需对铰刀的结构进行改进(如下图)。
方法如下:
将标准铰刀的切削部分每隔一齿磨去一段,使切削齿减少一半。
这样增大了容屑空间,使刀具排屑性能大为改善,避免了加工中切屑挤坏刀齿。
刀齿减少后,冷却液可顺利流入切削区,使刀具在加工过程中得到充分冷却,避免刀齿因切削温度过高而卷刃。
改进后的铰刀使用寿命大大提高。
为避免铰刀齿数减少后对加工质量的不利影响,在磨齿时,铰刀校正部分约t/4(t 为刀刃全长)处的一段刀刃仍保留。
2、铰刀几何角度的改进:图1 图2
1)将铰刀切削部分的刃口用细油石研磨成0.1mm左右的小圆角(如图1),加工时,先用粗铰刀对孔进行粗铰,留精铰余量0.04~0.08mm,然后用研磨后的精铰刀进行精铰,可以降低表面粗糙度值。
为防止铰孔后出现孔径收缩,铰刀可用旧铰刀修磨,其直径比铰孔的直径大0.02mm左右,以抵消铰孔后的收缩量。
2)在塑性较大的金属上铰孔时(如图2),用油石在铰刀的刃口前面研磨出0.5mm宽的棱带,并形成-2°~-3°的前角,保留刃带宽度为原有的2/3,从而减弱刃口的锋利程度,由于尖角加大,改善了散热条件,而且又不容易崩裂,铰孔的表面粗糙度可以保证在Ra0.8μm以上。
三、结论
铰孔加工过程中所产生的质量问题是普遍存在的,需要对铰孔过程进行必要的控制。
要根据工件材料、加工精度、铰削用量、刀具结构、切削液的选用等情况具体分析。
在实践中不断改进工艺方法,提高铰孔的加工质量和生产效率。