不锈钢管道氩弧焊的焊缝背面保护方法6页
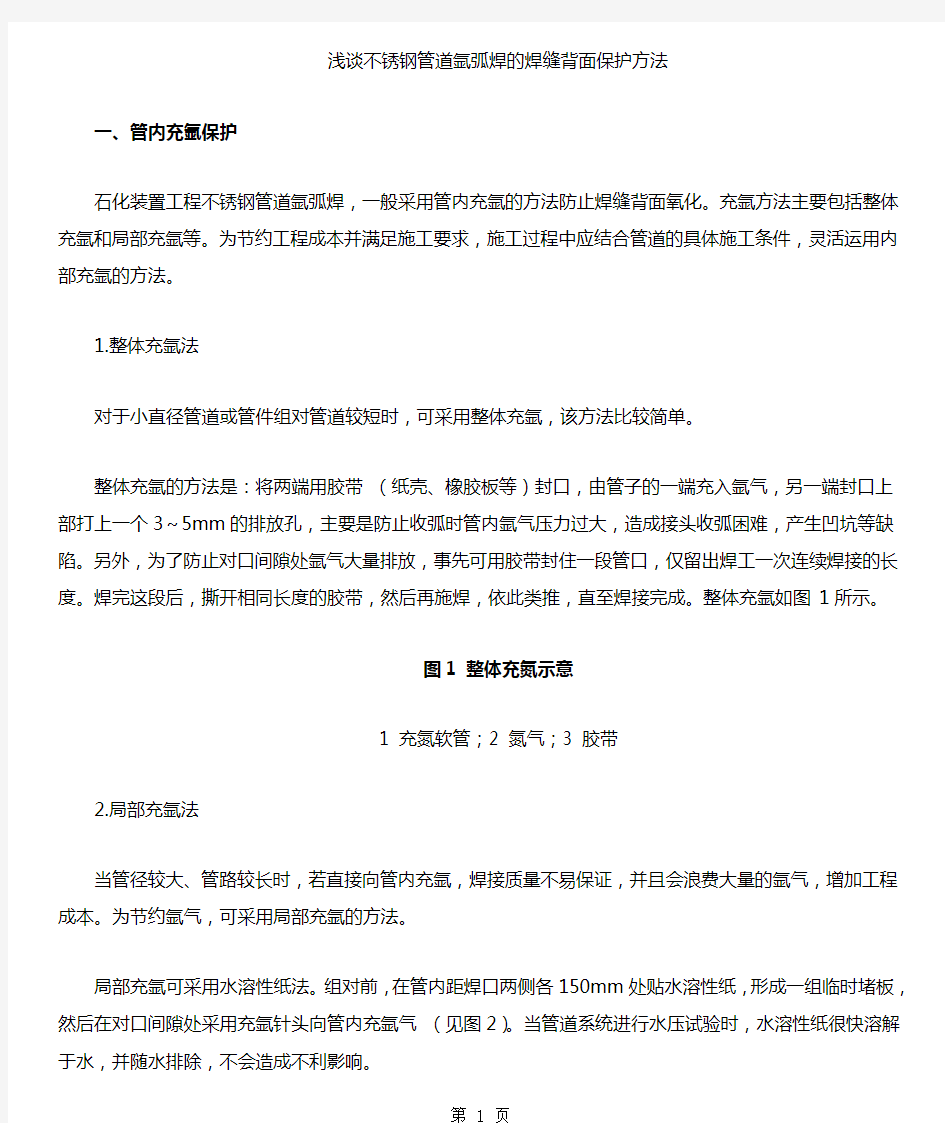

浅谈不锈钢管道氩弧焊的焊缝背面保护方法
一、管内充氩保护
石化装置工程不锈钢管道氩弧焊,一般采用管内充氩的方法防止焊缝背面氧化。充氩方法主要包括整体充氩和局部充氩等。为节约工程成本并满足施工要求,施工过程中应结合管道的具体施工条件,灵活运用内部充氩的方法。
1.整体充氩法
对于小直径管道或管件组对管道较短时,可采用整体充氩,该方法比较简单。
整体充氩的方法是:将两端用胶带(纸壳、橡胶板等)封口,由管子的一端充入氩气,另一端封口上部打上一个3~5mm的排放孔,主要是防止收弧时管内氩气压力过大,造成接头收弧困难,产生凹坑等缺陷。另外,为了防止对口间隙处氩气大量排放,事先可用胶带封住一段管口,仅留出焊工一次连续焊接的长度。焊完这段后,撕开相同长度的胶带,然后再施焊,依此类推,直至焊接完成。整体充氩如图1所示。
图1 整体充氮示意
1 充氮软管;
2 氮气;
3 胶带
2.局部充氩法
当管径较大、管路较长时,若直接向管内充氩,焊接质量不易保证,并且会浪费大量的氩气,增加工程成本。为节约氩气,可采用局部充氩的方法。
局部充氩可采用水溶性纸法。组对前,在管内距焊口两侧各150mm处贴水溶性纸,形成一组临时堵板,然后在对口间隙处采用充氩针头向管内充氩气(见图2)。当管道系统进行水压试验时,水溶性纸很快溶解于水,并随水排除,不会造成不利影响。
另外,可制作充氩夹具进行局部充氩保护,充氩夹具如图3所示。焊接前将充氩夹具堵板事先放置于管子两侧,焊接完成后将夹具从管内抽出。此种方法适用于不锈钢管的地面预制,简单易行。
3.反面保护盒法充氩
管道直径只要人能进入就可以采用跟踪保护盒法充氩,保护盒滑动与正面焊接同步进行。充氩时,氩气流量不能过大,并且不能正对熔池送气。
4.氩气保护效果判断
氩气保护效果可根据焊缝颜色进行判断。焊接过程中,焊工可根据颜色调整保护气,使焊缝达到昀好的保护效果。焊缝颜色和保护效果的对照见下表。
5.充氩保护的注意事项
(1)氩弧焊时焊缝背面应提前送气,流量适当加大,空气排出后,流量逐渐减小。焊接过程中应不间断地向管内充氩。停焊时滞后停气,使焊缝得到充分的保护。另外应特别注意的是,空气排净后才能进行焊接,否则影响充氩的保护效果。
(2)氩气流量应适当。流量过小,保护不好,焊缝背面容易氧化;流量过大,焊接时产生涡流带入空气,保护效果也会变坏,同时会引起焊缝根部内凹等缺陷,影响焊接质量。
(3)氩气入口应置于封闭段尽可能低的位置,空气排出孔应置于封闭段昀高位置。因为氩气比空气重,从较低位置充入氩气容易保证获得更高的浓度,充氩保护效果也就更好。
(4)为了减少管内氩气从对口间隙处流失,影响保护效果,增加成本,焊接前可沿焊口间隙贴上胶带,仅留出焊工一次连续焊接的长度,边焊边揭去胶带。
二、背面自保护不锈钢TGF系列焊丝焊接
背面自保护不锈钢TGF系列焊丝是一种带有特殊涂层的焊丝。焊接时,其保护药皮会渗透到熔池背面,形成一层致密的保护层,使焊道背面不被氧化,冷却后这层渣壳会自动脱落,用压缩空气或水冲的方式容易清除。这种焊丝的使用方法与普通氩弧焊实芯焊丝基本相同,涂层不会影响正面的电弧和熔池形态,焊缝金属在性能上可满足要求。
使用自保护焊丝不受管材规格、焊接位置等因素的限制,操作灵活,并且减少了充氩时的准备工作。但由于焊丝表面有较薄的涂层,在焊接操作上出现了一些不适应性,往往会出现内凹等缺陷,因此对焊工的操作水平要求较高。自保护焊丝适用于焊缝打底,不宜用于第二层以上的焊道,否则易造成夹渣,且焊缝成形不美观。采用全氩弧焊多层多道焊接时,宜与实芯焊丝配合使用。另外,目前市场上基本没有性能稳定的国产自保护不锈钢焊丝,进口自保护焊丝价格较贵,成本较高,因此在应用上受到了一定的限制。
三、免充氩焊接保护剂的应用
近年来,在石油化工、火电建设等工程的不锈钢管道(炉管)焊接中使用了一种免充氩焊接保护剂。保护剂在供货状态下为粉末状,使用时需要与甲醇或专用粘合剂混合。作为背面保护剂,焊接过程中在焊接背面形成保护涂层,可以有效地防止焊缝背面的氧化。
保护剂的使用方法:
(1)首先把焊缝背面的油污等清除干净。
(2)取出适量的保护剂,放于装有适量甲醇(或专用粘合剂)的器皿中按比例混合,二者搅拌均匀后涂覆在管内壁焊缝保护面上(宽度5~10mm)。需要注意的是:涂完后,在涂层表面会形成连续的粘合剂膜,在膜的下面包敷着粉末,所以不能对涂层进行划擦,以防粘合剂膜破损造成粉末外泄,从而影响保护效果。
(3)涂后放置5min,待干燥后即可进行焊接。焊后在焊缝背面形成一种难溶的化学性质呈惰性的薄膜,该薄膜紧紧地粘附在焊缝表面,对射线检测没有影响。
保护剂适用性好,可以使用正常的焊接电流进行焊接,也可使用比正常焊接大10%的电流进行焊接。保护剂对焊接操作没有影响,不仅可以防止背面氧化,还会对焊缝背面的熔化金属起到支托作用,得到优良的打底焊道,而且不会出现焊瘤、咬边或深度凹陷,焊接一次合格率高。
免充氩焊接保护剂操作简单,即涂即焊,节省时间,效率提高。应用在小管径焊接时,其成本要比充氩保护稍高;但在固定口焊接或大管径焊接时,值得推广应用。目前,免充氩保护剂的应用在国内处于起步阶段。
四、结语
针对不锈钢管道氩弧焊而言,采用管内充氩、自保护焊丝以及免充氩焊接保护剂等方法,均能很好地防止焊缝背面氧化,使焊缝的力学性能和耐腐蚀性能得到有效保证。
在实际工作中,应根据焊接工程量、管材规格和操作的适用性等因素综合考虑,灵活选择焊缝背面的保护方法,以确保焊接质量,并昀大限度地降低工程成本。
希望以上资料对你有所帮助,附励志名言3条:
1、宁可辛苦一阵子,不要苦一辈子。
2、为成功找方法,不为失败找借口。
3、蔚蓝的天空虽然美丽,经常风云莫测的人却是起落无从。但他往往会成为风云人物,因为他经得起大风大浪的考验。
手工钨极氩弧焊接工艺指导规程
手工钨极氩弧焊接工艺操作规程 ,保护电极和溶池不受大气有害气体的危害。 (一)手工钨极氩弧焊工艺参数 20~30A 的 、 ,也会使焊缝氧 化或产生焊透不匀等缺陷。应在保证良好视线的前提下短弧操作。通常电弧电压的选用范围是10~20V 。 4、焊丝直径和氩气流量: D=(2.5-3.5)d D---表示喷嘴直径(mm )d---表示钨针直径(mm ) 空气侵入。气体流量取决于喷嘴形状、尺寸、坡口形式、焊接电流及喷嘴与工件间
距 Q=KD Q—表示氩气流量(L/min)D---表示喷嘴直径(mm) K—表示系数K值=0.8~1.2 5、钨极伸出长度: 5~10 颜色观察法以鉴别气体保护效 ;铝焊缝表面呈银白本色。 2.电源种类和极性的选择: 金属 类别 碳钢 3.坡口形式和尺寸: 常用坡口形式有V形、U形、双面V形和V-U组合形等。
(三)焊前清理及预热: 1、焊前清理:施焊前必须严格清理焊接区及填充焊丝,去除氧化膜、油脂及水分。工件表面未形成氧化膜时,可用丙酮进行脱脂处理,当已生成氧化膜时应进行酸化处理或用机械法打磨掉,焊前再用丙酮去污。 2、预热:黑色金属焊接一般不须预热,δ> 26mm时,可适当预热。预热可加快焊接速度、防止过热、减少合金元素烧损,并利 (四) 1 缝长 接口口融合。 2、引弧:可采用短路接触法引弧,既钨极在引弧板上轻轻接触一下并随即抬起2mm左右即可引燃电弧。使用普通氩弧焊机, 3~5mm 3、填丝施焊: 75~80 150~200 以防扰乱氩气保护。不能象气焊那样在熔池中搅拌, 或者将焊丝端头浸入熔池中不断填入并向前移动。视装配间隙大小,焊丝 与焊枪可同步缓慢地稍做横向摆动,以增加焊缝宽度。防止焊丝与钨极接触、碰撞 ,打底焊应1次连续完成,避免停弧以减少接头。焊接时发现有缺陷,如加渣、气孔等应将缺陷清除,
氩弧焊焊接工艺参数(精)
氩弧焊焊接工艺参数 一、电特性参数 1.焊接电流钨极氩弧焊的焊接电流通常是根据工件的材质、厚度和接头的空间位置来选择的,焊接电流增加时,熔深增大,焊缝的宽度和余高稍有增加,但增加很少,焊接电流过大或过小都会使焊缝成形不良或产生焊接缺陷。 2.电弧电压钨极氩弧焊的电弧电压主要是由弧长决定的,弧长增加,电弧电压增高,焊缝宽度增加,熔深减小。电弧太长电弧电压过高时,容易引起未焊透及咬边,而且保护效果不好。但电弧也不能太短,电弧电压过低、电弧太短时,焊丝给送时容易碰到钨极引起短路,使钨极烧损,还容易夹钨,故通常使弧长近似等于钨极直径。 3.焊接速度焊接速度增加时,熔深和熔宽减小,焊接速度过快时,容易产生未熔合及未焊透,焊接速度过慢时,焊缝很宽,而且还可能产生焊漏、烧穿等缺陷。手工钨极氩弧焊时,通常是根据熔池的大小、熔池形状和两侧熔合情况随时调整焊接速度。 二、其它参数 1.喷嘴直径喷嘴直径(指内径)增大,应增加保护气体流量,此时保护区范围大,保护效果好。但喷嘴过大时,不仅使氩气的消耗增加,而且不便于观察焊接电弧及焊接操作。因此,通常使用的喷嘴直径一般取8mm~20mm为宜。 2.喷嘴与焊件的距离喷嘴与焊件的距离是指喷嘴端面和工件间的距离,这个距离越小,保护效果越好。所以,喷嘴与焊件间的距离应尽可能小些,但过小将不便于观察熔池,因此通常取喷嘴至焊件间的距离为7mm~15mm。 3.钨极伸出长度为防止电弧过热烧坏喷嘴,通常钨极端部应伸出喷嘴以外。钨极端头至喷嘴端面的距离为钨极伸出长度,钨极伸出长度越小,喷嘴与工件间距离越近,保护效果越好,但过小会妨碍观察熔池。通常焊对接缝时,钨极伸出长度为5mm~6mm较好;焊角焊缝时,钨极伸出长度为7mm~8mm较好。 4.气体保护方式及流量钨极氩弧焊除采用圆形喷嘴对焊接区进行保护外,还可以根据施焊空间将喷嘴制成扁状(如窄间隙钨极氩弧焊)或其他形状。 焊接根部焊缝时,焊件背部焊缝会受空气污染氧化,因此必须采用背部充气保护。氩气和氦气是所有材料焊接时,背部充气最安全的气体。而氮气是不锈钢和铜合金焊接时,背部充气保护最安全的气体。一般惰性气体背部充气保护的气体流量范围为0.5~42L/min。当喷嘴直径、钨极伸出长度增加时,气体流量也应相应增加。若气流量过小,保护气流软弱无力,保护效果不好,易产生气孔和焊缝被氧化等缺陷;若气流量过大,容易产生紊流,保护效果也不好,还会影响电弧的稳定燃烧。 对管件内充气时,应留适当的气体出口,防止焊接时管内气体压力过大。在根部焊道焊接结束前的25~50毫米时,要保证管内内充气体压力不能过大,以便防止焊接熔池吹出或根部内凹。当采用氩气进行管件焊接背面保护时,最好从下部进入,使空气向上排出,并且使气体出口远离焊缝。
冷轧酸洗工艺流程 (1)
酸洗工艺流程 原料→开卷→入口剪切→焊接→破鳞→夹送机→活套→酸 洗→回酸槽→清洗槽→吹扫→漂洗槽→中和槽→吹扫→烘 干→出口夹送→出口剪切→卷取。 酸洗工艺参数 酸液浓度:黑退火钢带5-20%、光亮退火钢带7-20%、冷硬 钢带7-20%, 在酸液浓度下限附近时合理温度上限调整酸液温度,保证酸洗质量。 酸液温应:60℃~80℃, 二氯化铁含量:≤150ɡ/1。 酸洗速度:≤90m/min。 中和工艺 碱液温度:60-80℃ 碱液PH值:8-12[用PH值试纸检测] 蒸汽压力:≤0.4MPa 1、酸洗工艺过程中酸液温度对保证酸洗质量和酸牦在合理 水平至关重要,因此应避免蒸汽的长时间中断,同时蒸汽压力的大幅波动会造成酸液加热管束的非正常损坏,增加成本。 2、因退火是必需连续的工艺过程,因此退火中需避免煤气、电等突然中断,重新退火对带钢组织和性能有较大影响。 3、热轧带钢表面覆盖着一层氧化铁皮,其重量可达33-55ɡ/
㎡,厚度为7.5~15um,甚至可达20um,现代化热连轧机生产的带钢,其表面氧化铁皮厚度也约为10um。 4、为孓保证成口带钢的表面质量,降低力能消牦,减少轧辊磨损和有利带钢深加工,因此钢带冷轧前必须将氧化铁皮处除掉。 5、我们利用氧化铁皮与酸发生化学反应的基本原理,将钢带浸泡在一定浓度和温度的酸液中,并使钢带与酸液相对运动,加速化学反应速度,从而达到清除氧化铁皮的目的。 酸再生工艺流程:废酸收集→废酸过滤→废酸预浓缩→培烧再生→再生酸收集 酸再生是将废酸液定量的送往酸再生装置再生成游离酸返回酸洗机组,同时得到氧化铁粉的一个体系。 酸再生过程是一个化学过程,浓缩废酸通过啧抢以雾状喷入焙烧炉内,焙烧炉通过两个喷嘴进行操作,操作期间煤气和空气流量自动控制,流量由孔板和差压传感器测量并在显示屏上显示。 煤气流量:200~300m /h,煤气压力:0.01mpa
氩弧焊的焊接技术与过程
氩弧焊的焊接技术 摘要:氩弧焊是以惰性气体“氩气”作为保护气体的一种电弧焊方法,氩气从喷嘴中喷出,在焊接区形成惰性气体保护层,隔绝了空气的侵入,从而对电弧及熔池进行保护。氩弧焊焊接具有许多普通电弧焊所不具有的优点。焊前工件表面的清洁度、焊接过程的良好环境控制及合理参数选择等因素是保证氩弧焊焊接质量的重要条件。选择合理的焊接规范是保证焊接质量的重要措施。手工钨极氩弧焊的规范参数主要有:焊接电流、焊接电压、氩气流量、喷嘴直径、电极伸出长度、填充焊丝直径、钨极直径、接头破口形式、焊接层数以及预热温度、焊接规范主要是根据不同的被焊金属、工件厚度以及结构形式而进行合理的选择。平时多用的钍钨极在磨削时,所产生的粉末进入人体是不利的,所以在沙轮机上磨削时,必须注意防护。 关键词:氩弧焊非熔化极直流反接直流正接 1、氩弧焊的基本原理及优缺点 1.1、氩弧焊就是在电弧焊的周围通上氩弧保护性气体,将空气隔离在焊区之外,防止焊区 的氧化。氩弧焊按照电极的不同分为熔化极氩弧焊和非熔化极氩弧焊两种,通常作业过程中手工焊接采用非熔化极氩弧焊。 1.2、非熔化极氩弧焊的工作原理及特点: 非熔化极氩弧焊是电弧在非熔化极(通常是钨极)和工件之间燃烧,在焊接电弧周围流过一种不和金属起化学反应的惰性气体(常常用氩气),形成一个保护气罩,使钨极端头,电弧和熔池及已处于高温的金属不与空气接触,能防止氧化和吸收有害气体。从而形成致密的焊接接头,其力学性能非常好。氩气是一种比较理想的保护气体,比空气密度大25%,在平焊时有利于对焊接电弧进行保护,降低了保护气体的消耗。氩气是一种化学性质非常不活泼的气体,即使在高温下也不和金属发生化学反应,从而没有了合金元素氧化烧损及由此带来的一系列问题。氩气也不溶于液态的金属,因而不会引起气孔。氩是一种单原子气体,以原子状态存在,在高温下没有分子分解或原子吸热的现象。氩气的比热容和热传导能力小,即本身吸收量小,向外传热也少,电弧中的热量不易散失,使焊接电弧燃烧稳定,热量集中,有利于焊接的进行。氩气的缺点是电离势较高。当电弧空间充满氩气时,电弧的引燃较为困难,但电弧一旦引燃后就非常稳定。 1.3、氩弧焊的优缺点 1.3.1、氩弧焊的优点:氩气保护可隔绝空气中氧气、氮气、氢气等对电弧和熔池产生的不良影响,减少合金元素的烧损,以得到致密、无飞溅、质量高的焊接接头。氩弧焊的电弧燃烧稳定,热量集中,弧柱温度高,焊接生产效率高,热影响区窄,所焊的焊件应力、变形、裂纹倾向小;氩弧焊为明弧施焊,操作、观察方便;电极损耗小,弧长容易保持。氩弧焊几乎能焊接所有金属,特别是一些难熔金属、易氧化金属,如镁、钛、钼、锆、铝等及其合金1.3.2、氩弧焊的缺点:氩弧焊因为热影响区域大,工件在修补后常常会造成变形、硬度降低、砂眼、局部退火、开裂、针孔、磨损、划伤、咬边、或者是结合力不够及内应力损伤等缺点。尤其在精密铸造件细小缺陷的修补过程在表面突出。在精密铸件缺陷的修补领域可以使用冷焊机来替代氩弧焊,由于冷焊机放热量小,较好的克服了氩弧焊的缺点,弥补了精密铸件修复难题。 2、焊接程序及技术控制 2.1、焊前准备检查电源线路、气路等是否正常。钨极氩弧焊通常采用直径0.5~ 3.0毫米的钍钨极,顶部磨成圆锥形,其顶部稍留0.~1.0毫米直径的小圆台为宜。电极的外伸长度约为3~5毫米左右,工件的被焊处应按规定开成坡口。两侧距坡口边缘25~30毫米处及焊丝用丙
氩弧焊焊接工艺规程
氩弧焊焊接工艺规程 1、焊接方法: 手工钨极氩弧焊 2、焊接材料: 不锈钢药芯焊丝不锈钢实心焊丝 3、焊接工艺参数:见焊接工艺卡 4、焊前准备: (1)检查焊接设备,按焊接工艺卡调整电弧电压、焊接电流、钨极等焊接工艺参数。(2)焊前100-150℃烘干不锈钢药芯焊丝。 5、焊接工艺: (1)清理焊件坡口及其两侧各宽20mm围的油、污、锈等杂质,直至露出金属光泽。 清理不锈钢焊丝表面油污等赃物。 (2)组对焊接接头,注意按图纸及工艺卡要求留出间隙。 (3)使用焊接活性剂时,将活性剂与丁酮以1:1的比例混合,然后均匀涂抹在坡口面,待丁酮挥发后再施焊。渗透剂的用量要适当,若太少,熔池粘度降低不多,流动性改善不明显;若太多,熔池粘度降低太多,流动性变差。 (4)定位焊采用与打底焊相同的焊丝和工艺,定位焊缝长10~15mm,定位点固2—3处。(5)第一层氩弧焊打底焊焊接,使用不锈钢药芯焊丝,打底焊应一次连续完成,避免停弧以减少接头,焊接时发现有缺陷,如夹钨、气孔等应将缺陷清除,不允许通过重复熔化的方法来消除缺陷。电弧熄灭后,焊枪喷嘴仍要对准熔池,以延续氩气保护,防止氧化。 (6)使用不锈钢实心焊丝进行第二层以后的层焊和罩面
射线检测工艺规程 1.主题容与适用围 本规程规定了焊缝射线人员具备的资格、所用器材、检测工艺和验收标准等容。 本规程依据JB/T4730-2005的要求编写。适用于本公司P≥10Mpa产品的对接焊接接头的X 射线AB级检测技术。满足《压力容器安全技术监察规程》、GB150的要求。检测工艺卡容是本规程的补充,由Ⅱ级人员按本规程等要求编写,其参数规定的更具体。 2.引用标准、法规 JB/T4730-2005《承压设备无损检测》 GB150-1998《钢制压力容器》 GB18871-2002《电离辐射防护及辐射源安全基本标准》 GB16357-1996《工业X射线探伤放射卫生放护标准》 JB/T7902《线型象质计》 《特种设备无损检测人员考核与监督管理规则》 《压力容器安全技术监察规程》. 3.一般要求 3.1射线检测人员必须经过技术培训,按《特种设备无损检测人员考核与监督管理规则》考核并取得与其工作相适应的书。 3.1.1检测人员应每年检查一次视力,校正视力≮1.0。评片人员还应辨别出400mm距离处高0.5mm、间距0.5mm的一组印刷字母。 3.2辐射防护 射线防护应符合GB18871、GB16357的有关规定。 3.3胶片和增感屏 3.3.1胶片:在满足灵敏度要求的情况下,一般X射线选用T3或T2型胶片。 3.3.2 增感屏:采用前屏为0.03mm、后屏为0.03~0.10mm的铅箔增感屏。. 3.3.3 胶片和增感屏在透照过程中应始终紧密接触。 3.4象质计
钨极氩弧焊的工艺参数主要有焊接电流种类及极性
钨极氩弧焊的工艺参数主要有焊接电流种类及极性、焊接电流、钨极直径及端部形状、保护气体流量等,对于自动钨极氩弧焊还包括焊接速度和送丝速度。 脉冲钨极氩弧焊主要参数有Ip 、tp 、Ib 、tb 、fa 脉幅比RA = Ip / Ib 、脉冲电流占空比Rw =tp / tb+ tp (1) 钨极氩弧焊工艺参数 1) 焊接电流种类及大小一般根据工件材料选择电流种类,焊接电流大小是决定焊缝熔深的最主要参数,它主要根据工件材料、厚度、接头形式、焊接位置,有时还考虑焊工技术水平( 钨极氩弧时) 等因素选择。 2) 钨极直径及端部形状,钨极直径根据焊接电流大小、电流种类选择。 钨极端部形状是一个重要工艺参数。根据所用焊接电流种类,选用不同的端部形状。尖端角度α 的大小会影响钨极的许用电流、引弧及稳弧性能。表1列出了钨极不同尖端尺寸推荐的电流范围。小电流焊接时,选用小直径钨极和小的锥角,可使电弧容易引燃和稳定;在大电流焊接时,增大锥角可避免尖端过热熔化,减少损耗,并防止电弧往上扩展而影响阴极斑点的稳定性。 表1 钨极尖端形状和电流范围(直流正接)
钨极尖端角度对焊缝熔深和熔宽也有一定影响。减小锥角,焊缝熔深减小,熔宽增大,反之则熔深增大,熔宽减小。 3) 气体流量和喷嘴直径在一定条件下,气体流量和喷嘴直径有一个最佳范围,此时,气体保护效果最佳,有效保护区最大。如气体流量过低,气流挺度差,排除周围空气的能力弱,保护效果不佳:流量太大,容易变成紊流,使空气卷入,也会降低保护效果。同样,在流量子定时,喷嘴直径过小,保护范围小,且因气流速度过高而形成紊流;喷嘴过大,不仅妨碍焊工观察,而且气流流速过低,挺度小,保护效果也不好。所以,气体流量和喷嘴直径要有一定配合。一般手工氩弧焊喷嘴孔径和保护气流量的选用见表2。 表 2 喷嘴孔径与保护气流量选用范围
氩弧焊的焊接方法
氩弧焊的焊接方法 ?教学目的:掌握好手工钨极氩弧焊的焊前准备、运焊把、送丝、引弧、焊接、收弧的技巧 ?具体要求: ?1、了解焊弧焊的原理、特点和分类 ?2、掌握好氩弧焊焊前准备和焊接方法 ?3、掌握好氩焊在焊接过程中产的缺陷和解决的办法 ?4、适用于有接焊接基础人员,其焊件需要进行无损检测、内部和外观要求有较高要求的标准焊件。 ?1、氩弧焊的原理: ?氩弧焊是使用惰性气体氩气作为保护气体的一种气电保护焊的焊接方法。 ?2、氩弧的特点: ?(1)焊缝质量高,由于氩气是一种惰性气体,不与金属起化学反应,合金元素不会被烧损,而氩气也不熔于金属,焊接过程基本上是金属熔化和 结晶的过程,因此,保护较果好,能获得较为纯净及高质量的焊缝 ?(2)焊接变形应力小,由于电弧受氩气流的压缩和冷却作用,电弧热量集中,且氩弧的温度又很高,故热影响区小,故焊接时应力与变形小,特 别造用于薄件焊接和管道打底焊。 ?(3)焊接范围广,几乎可以焊接所有金属材料,特别适宜焊接化学成份活泼的金属和合金。 ?3、氩弧焊的分类: ?氩弧焊根据电极材料的不同可分为钨极氩弧焊(不熔化极)和熔化极氩弧焊。根据其操作方法可分为手工、半自动和自动氩弧焊。根据电源又可以 分为直流氩弧焊、交流氩弧焊和脉冲氩弧焊。 ?4、焊前准备: ?(1)阅读焊接工艺卡,了解施焊工件的材质、所需要的设备、工具和相关工艺参数,其中包括选用正确的焊机,(如焊接铝合金则需要用交流焊 机),正确的选用钨极和气体流量, ?首先,要从焊接工艺卡上得知焊接电流的大小等工艺参数。然后选用钨
极(一般来说直径2.4mm用的比较多,它的电流造应范围是150A—250A,铝例外)。 ?再根据钨极的直径选用多大的喷嘴,钨极直径的2.5—3.5倍是喷嘴的内径D=(2.5—3.5)dw其中D表示喷嘴内径(mm),dw表示钨极直径(mm)。 ?最后根据喷嘴的内径选用气体流量,喷嘴内径的0.8—1.2倍是气的流量。 Q=(0.8—1.2)D,其中Q表示气体流量(L/min)钨极的申出长度不可超过其喷嘴的内径直径,否则容易产生气孔。 ?(2)检查焊机、供气系统、供水系统、接地是否完好。 ?(3)检查工件是否合格:1.是否有油、锈等脏物(焊缝20mm内必须干净、干燥)2.坡口角度、间隙、钝边是否合适。坡口角度、间隙大、则曾大焊接量大,易产生焊瘤。坡口角度小、间隙小、钝边厚则容易产生未熔合和焊不透。一般来说坡口角度为30—32度,间隙为0—4mm,钝边为0—1mm。3.错边不能过大,一般在1mm内。4.定位焊的长度、点数是否达到要求,定位焊本身要没有缺陷。 ?5、氩弧焊的操作手法:氩弧是一种左右手同时动作的操作,与我们平时生活中的左手画圆右手画方相同,所以建议在刚开始学习氩弧焊的人员进行类似的训练,对学习氩弧焊有一定的帮助。 ?(1)送丝:分内填丝和外填丝。 ?外填丝可以用于打底和填充,是用较大的电流,其焊丝头在坡口正面,左手捏焊丝,不断送进熔池进行焊接,其坡口间隙要求较小或没有间隙。 ?其优点因为电流大、和间隙小,所以生产效率高,操作技能容易掌握。其缺点是用于打底的话因为操作者看不到钝边熔化和反面余高情况,所以容易产生未熔合和得不到理想的反面成形。 ?内填丝只能用于打底焊,是用左手拇指、食指或中指配合送丝动作,小指和无名指夹住焊丝控制方向,其焊丝则紧贴坡口内侧钝边处,与钝边一起熔化进行焊接,要求坡口间隙大于焊丝直径,是板材的话可以将焊丝弯成弧形。 ?其优点因为焊丝在坡口的反面,可以清晰地看清钝边和焊丝的熔化情况,眼睛的余光也可以看见反面余高的情况,所以焊缝熔合好好,反面
氩弧焊16MnDG管对接__焊接工艺评定
焊接工艺评定报告书评定报告书编号: 材料牌号:16MnDG+16MnDG 材料规格:Φ159×6 焊缝型式:对接焊缝 焊接方法:氩弧焊 试件编号: 填报日期:
预焊接工艺规程(pWPS ) 单位名称 预焊接工艺规程编号 日期 所依据焊接工艺评定报告编号: NB47014-2011 焊接方法 氩弧焊 机械化程度: 手工 焊接接头:对接 坡口形式: V 型 衬垫(材料及规格) 无 其他 共焊3层:单道焊采用单面焊双面 成形技术焊接,先焊第一层(打底层),再 焊二层(中间层),最后焊第三层(盖面层) 都采用手工钨极氩弧焊。 简图:(接头形式、坡口形式与尺寸、焊层、焊道布置及顺序) 母材: 类别号 Fe-1 组别号 Fe-1-2 与类别号 Fe-1 组别号Fe-1-2 相焊或 标准号 GB/T18984材料代号 16MnDG 与标准号GB/T18984材料代号16MnDG 相焊 对接焊缝焊件母材厚度范围 1.5--12 mm 角焊缝焊件母材厚度范围 / 管子直径、壁厚范围:对接焊缝 Φ159×6 角焊缝 / 其他 无 填充金属: 氩弧焊丝 焊材类别: FeS-1-2 焊材标准: GB/T8110-2008 填充金属尺寸: Φ2.5mm 焊材型号: ER50-6 焊材牌号(金属材料代号): THT50-6 填充金属类别: Fe-1-1 其他: 无 对接焊缝焊件焊缝金属厚度范围: 5mm 角焊缝焊件焊缝金属厚度范围 / 耐蚀堆焊金属化学成份(%) C Si Mn P S Cr Ni Mo V Ti Nb 其他: 注:对每一种母材与焊接材料的组合均需分别填表 0.5-1.5 3—4 55o -60 o 6 0.5-3
碳钢管酸洗和钝化工艺
碳钢管酸洗和钝化工艺 Pickling and passivation technics for Carbon steel pipe 工艺材料: 工艺流程:
除锈除油二合一处理→中和处理→皮膜钝化处理→自然干燥→管件外部涂防锈剂。 Process: Rust removing and oil cleaning at one time →Neutralization→passivation →Natural drying →Coat the pipe outside with Antirust . (1)防锈除油二合一处理槽: Rust removing and oil cleaning tank: 按体积比:BR-101A :CA-66:水=1:6:3配制工作液。当大气气压低或者天气有雾时,按1%向槽内加入BN-111酸雾抑制剂,用来控制槽液酸雾挥发。 As the ratio by volume to make the working solution .When the atmos is
low or there is any fog , add 1% Acid fog inhibitor BN-111 by volume . (2)中和处理槽: Neutralizer Tank : 春、夏、秋季时:按重量比8~10%加入中和剂BH-008配制工作液。 冬季气温低时:按比重3~5%加入TS-300配制工作液。 春夏秋工件以中和为主;冬季以清洗为主。 In the season of spring ,summer and autumn :Add Neutralizer BH-008 8~10% by weight to make the working solution . In winter ,when the temperature is low :Add Passivator TS-300 3~5% by weight to make the working solution . (3)皮膜钝化处理槽: Passivation tank : 按重量比10~15%加入水质调节剂TS-300配制工作溶液。 Add Passivator 10~15% by weight to make the working solution . 工作槽液的工艺参数: technic data for the Working solution liquid in the tanks : 除锈除油二合一处理槽:常温浸渍,时间:30~90min,PH值≤1.5 Rust removing and oil cleaning tank: soakage at the normal temperature , time :30~90min ,PH≤1.5 . 中和槽: 春夏秋季:PH≧12,常温浸渍时间3~5min;冬季PH≧9,浸渍时间3~5min,温度30℃左右。 Neutralizer Tank :
热镀锌工艺流程
热镀锌工艺流程 一.进厂 1.进场车辆经过地磅室过磅 2.黑件区卸车 3.卸车后空车过磅 二.加工件检查 卸车前应检查待加工件是否存在变形、损坏,核实实际数量是否与送货单相符合。如发现变形、损坏或数量不符,应立即报告班长。 三.加工件保管 1.待加工件以客户每车为单位,分别堆放保管,并在产品标识卡上注明客户,防止混杂。 2.产品堆放整齐、合理、安全。产品下方应放置垫木以防止碰伤及方便吊运入池。产品不能堆放过高,以防坍塌造成构件损坏或人员伤亡。 3. 严禁将壁厚的、大型的构件压在壁薄的构件之上。 四.处理前准备 在工件进入酸池前,酸洗工应检查工件是否有损坏变形,工艺孔开设是否合理,表面是否有油漆、油污。如检查发现工件有损坏变形或者工艺孔开设不合理,应立即将工件隔离堆放并通知质检人员。如果检查发现工件表面存在油漆油污,应清洁油漆油污后进行酸洗,无法处理的,应立即通知质检人员。 五.酸洗处理 1. 酸洗时间根据工件表面锈蚀情况而定: 一级:表面基本无锈蚀,或已进行过机加工(酸洗时间30—60分钟); 二级:氧化层较薄且表面光洁(酸洗时间60—120分钟); 三级:有较厚的氧化层,表面不平整(酸洗时间120—200分钟); 四级:表面锈蚀严重,氧化层已严重坑洼不平(酸洗时间200分钟以上)。 铸铁件要严格掌握酸洗时间(15-30分钟)防止过酸洗。 2. 酸洗时间以工件表面不留氧化层为准。由操作者目测工件表面不留氧化物、不过酸洗为准,对于局部区域的锈迹、油污,应打磨、擦拭干净,对于酸洗不合格的工件,必须重新进行酸洗,严禁把酸洗不合格品转入下道工序。
3. 行车提升速度为7米/分,物件起吊斜角为20-35度,起吊后应使工件在酸槽上面停留适当时间,待工件上的酸液成滴状时,再转入下道工序。 4. 工件进出酸池时应缓慢轻放,禁止野蛮操作,防止损坏工件和酸槽设备。在酸洗过程中应上、下摆动工件,使工件酸洗充分周到。操作者操作时应站在上风口、禁止站在酸槽槽口上面进行操作、防止发生意外伤害。 5. 产品翻动时禁止野蛮操作,避免损坏构件。选择合理、安全的吊装方式,确保镀锌安全和镀锌质量。 6. 填写酸洗时间记录表。 六.水洗处理 漂洗的水质要求清洁,漂洗洗时要求操作者前后左右摆动镀件,使其充分去除污染物,水洗的时间为1至3分钟,水温为室温。行车升降速度7米/分钟,起吊斜角为20—35度。工件离开液面后停留片刻,待工件上的漂洗水基本滴净后方可进入助镀池进行助镀处理。 七.助镀处理 助镀液温度40-80℃,由自动测温仪测定控制,操作人员应经常观察显示仪表上的温度读数,超出规定范围时及时通知当班班长进行检查处理。助镀时间通常在2±1分钟,对于钢材较厚的产品,助镀时间应适当增加。助镀处理时工件必须完全浸入助镀液中,必要时应上下摆动,达到充分助镀的作用,确保浸镀工序顺利进行。助镀液表面保持清洁,不得有飘浮污染物,防止镀件在浸镀时产生漏镀。行车升降速度7米/分钟,起吊斜角为20—35度,待工件表面的助镀液基本滴净后方可吊离助镀池。 八.镀锌 锌缸工在工件浸入锌液前必须认真检查工件所有镀锌表面是否存在没有酸洗干净的锈迹,油污等。如存在,则必须在打磨清洁,用氯化铵擦拭后方可进行浸镀,无法处理的,必须返回酸洗工序重新进行处理。锌缸工在工件浸入锌液前必须检查工件的吊装方式是否合理、安全,工件的排气、排液孔是否顺畅。如果发现问题,必须经过相应处理后才能浸镀,无法处理的,通知当班班长。待镀工件浸入锌液前表面各部位必须已经充分干燥,严禁潮湿的工件进入锌液,防止锌液飞溅,造成人体伤害和锌液浪费。潮湿的工件浸入锌液,有可能会造成漏镀,影响质量。
氩弧焊的焊接方法
氩弧焊的焊接方法 ? 教学目的:掌握好手工钨极氩弧焊的焊前准备、运焊把、送丝、 引弧、焊接、收弧的技巧 ? 具体要求: ? 1、了解焊弧焊的原理、特点和分类 ? 2、掌握好氩弧焊焊前准备和焊接方法 ? 3、掌握好氩焊在焊接过程中产的缺陷和解决的办法 ? 4、适用于有接焊接基础人员,其焊件需要进行无损检测、内部和外观要求有较高要求的标准焊件。 ? 1、氩弧焊的原理: ? 氩弧焊是使用惰性气体氩气作为保护气体的一种气电保护焊的焊接方法。? 2、氩弧的特点: ? (1)焊缝质量高,由于氩气是一种惰性气体,不与金属起化学反应,合 金元素不会被烧损,而氩气也不熔于金属,焊接过程基本上是金属熔化和 结晶的过程,因此,保护较果好,能获得较为纯净及高质量的焊缝? (2)焊接变形应力小,由于电弧受氩气流的压缩和冷却作用,电弧热量 集中,且氩弧的温度又很高,故热影响区小,故焊接时应力与变形小,特 别造用于薄件焊接和管道打底焊。 ? (3)焊接范围广,几乎可以焊接所有金属材料,特别适宜焊接化学成份 活泼的金属和合金。 ? 3、氩弧焊的分类: ? 氩弧焊根据电极材料的不同可分为钨极氩弧焊(不熔化极)和熔化极氩弧 焊。根据其操作方法可分为手工、半自动和自动氩弧焊。根据电源又可以
分为直流氩弧焊、交流氩弧焊和脉冲氩弧焊。 ? 4、焊前准备: ? (1)阅读焊接工艺卡,了解施焊工件的材质、所需要的设备、工具和相 关工艺参数,其中包括选用正确的焊机,(如焊接铝合金则需要用交流焊 机),正确的选用钨极和气体流量, ? 首先,要从焊接工艺卡上得知焊接电流的大小等工艺参数。然后选用钨 极(一般来说直径2.4mm用的比较多,它的电流造应范围是150A—250A, 铝例外)。 ? 再根据钨极的直径选用多大的喷嘴,钨极直径的2.5—3.5倍是喷嘴的内径D=(2.5—3.5)dw其中D表示喷嘴内径(mm),dw表示钨极直径(mm)。? 最后根据喷嘴的内径选用气体流量,喷嘴内径的0.8—1.2倍是气的流量。 Q=(0.8—1.2)D,其中Q表示气体流量(L/min)钨极的申出长度不可超过 其喷嘴的内径直径,否则容易产生气孔。 ? (2)检查焊机、供气系统、供水系统、接地是否完好。? (3)检查工件是否合格:1.是否有油、锈等脏物(焊缝20mm内必须干 净、干燥)2.坡口角度、间隙、钝边是否合适。坡口角度、间隙大、则曾 大焊接量大,易产生焊瘤。坡口角度小、间隙小、钝边厚则容易产生未熔 合和焊不透。一般来说坡口角度为30—32度,间隙为0—4mm,钝边为 0—1mm。3.错边不能过大,一般在1mm内。4.定位焊的长度、点数是否 达到要求,定位焊本身要没有缺陷。 ? 5、氩弧焊的操作手法:氩弧是一种左右手同时动作的操作,与我们 平时生活中的左手画圆右手画方相同,所以建议在刚开始学习氩弧焊的人 员进行类似的训练,对学习氩弧焊有一定的帮助。 ? (1)送丝:分内填丝和外填丝。
氩弧焊焊接工艺规程
氩弧焊焊接工艺规程 1、焊接方法: 手工钨极氩弧焊 2、焊接材料: 不锈钢药芯焊丝不锈钢实心焊丝 3、焊接工艺参数:见焊接工艺卡 4、焊前准备: (1)检查焊接设备,按焊接工艺卡调整电弧电压、焊接电流、钨极等焊接工艺参数。 (2)焊前100-150℃烘干不锈钢药芯焊丝。 5、焊接工艺: (1)清理焊件坡口及其两侧各宽20mm范围内的油、污、锈等杂质,直至露出金属光泽。 清理不锈钢焊丝表面油污等赃物。 (2)组对焊接接头,注意按图纸及工艺卡要求留出间隙。 (3)使用焊接活性剂时,将活性剂与丁酮以1:1的比例混合,然后均匀涂抹在坡口面内, 待丁酮挥发后再施焊。渗透剂的用量要适当,若太少,熔池粘度降低不多,流动性改 善不明显;若太多,熔池粘度降低太多,流动性变差。 (4)定位焊采用与打底焊相同的焊丝与工艺,定位焊缝长10~15mm,定位点固2—3处。 (5)第一层氩弧焊打底焊焊接,使用不锈钢药芯焊丝,打底焊应一次连续完成,避免停弧以减少接头,焊接时发现有缺陷,如夹钨、气孔等应将缺陷清除,不允许通过重复熔 化的方法来消除缺陷。电弧熄灭后,焊枪喷嘴仍要对准熔池,以延续氩气保护,防止 氧化。 (6)使用不锈钢实心焊丝进行第二层以后的层焊与罩面 射线检测工艺规程 1、主题内容与适用范围 本规程规定了焊缝射线人员具备的资格、所用器材、检测工艺与验收标准等内容。 本规程依据JB/T4730-2005的要求编写。适用于本公司P≥10Mpa产品的对接焊接接头的X 射线AB级检测技术。满足《压力容器安全技术监察规程》、 GB150的要求。检测工艺卡内容就是本规程的补充,由Ⅱ级人员按本规程等要求编写,其参数规定的更具体。
2、手工钨极氩弧焊作业指导书.
山东天元建设集团安装工程有限 公司工业设备安装公司企业标准 SDTY/GAQMSⅢ-003(2) 手工钨极氩弧焊作业指导书 2005—03—01 发布 2005—03—01实施山东天元建设集团安装工程有限公司工业设备安装公司发布
SDTY/GAQMSⅢ-003(2) 前言 本标准主要起草人:刘珍 本标准审核人:林青友王文高 本标准批准人:沈银根 本标准自2005年03月01日发布,自发布之日起在全公司范围内试行。 本标准由公司焊接与无损检测室负责解释。
手工钨极氩弧焊作业指导书 1 范围 本标准适用于锅炉本体受热面、锅炉本体管路、主蒸汽管道、主给水管道、工业管道、公用管道和长输管道的手工钨极氩弧焊焊接工作。本标准也适用于电站锅炉受热工仪表管道的手工钨极氩弧焊焊接工作。 2 规范性引用文件 下列文件中的条款通过本标准的引用而成为本标准的条款,凡是注日期的引用文件,其随后的修改单(不包括勘误的内容)或修订版均不适用于标准,然而,鼓励根据本部分达成协议的各方研究是否可使用这些文件的最新版本。凡是不注日期的引用文件,其最新版本适用于本标准。 GB/T 983—95 《不锈钢焊条》 DL/T 869-2012 《火力发电厂焊接技术规程》 DL/T 5210.7-2010《电力建设施工质量验收及评价规程》—焊接篇 SY0401-98 《输油输气管道线路工程施工及验收规范》 劳人部[1988]1号《锅炉压力容器焊工考试规则》 HYDBP006-2004《压力管道安装工程焊接、热处理过程控制程序》 HYDBP018-2004《压力管道安装工程焊接材料管理程序》 HYDBP008-2004《压力管道安装工程计量管理手册》 HYDBP007-2004《压力管道安装工程检验和试验控制程序》 HYDBP010-2004《压力管道安装工程不合格品控制程序》 3 先决条件 3.1 环境 3.1.1 施工环境应符合下列要求: 3.1.1.1 风速:手工氩弧焊风速应小于2M/S。
不锈钢氩弧焊工艺指导书
不锈钢氩弧焊工艺指导书 1、范围: 本工艺适用于各种不锈钢板、不锈钢材料的焊接2、设备: 直流钨极氩焊机TIG-250 额定输入电压:单相380V±10%/50Hz 焊接电流调节范围:5A—250A 最小焊接电流:≤40A 最大焊接电流:≥250A 预送气时间:0.3S 气体延时:0.3—16S 冷却方式:风冷 3、操作工艺: 1、焊接操作前应首先检查被焊工件部位有无氧化物、油脂、涂层等垃圾物,焊前必须严格清理,否则极易引起熔核成形不良,甚至会产生未焊透等质量的发生。 2、焊接前应领会图纸的技术要求,严格按照图纸要求进行施工,在将焊接件按图纸尺寸要求定位好后,应用工艺撑杆加强、加固,以防止或减小在焊接过程中产生的焊接变形,确保产品质量。 3、焊接前应检查所用钨电极是否符合当前焊接的板厚,否则将其更换成合适的钨电极。 4、在进行氩弧焊前,钨电极的伸出喷嘴的长度一般取钨电极直径的1—2倍。 5、焊接前打开氩气瓶阀门,将氩气的焊接流量调至所需的流量,见下表。 6、调整好合适的电流,具体的不同板厚的焊接电流见下表。 7、选用好合适的不锈钢焊丝,不同板厚不锈钢焊丝的选取见下表。在进行氩弧焊时,钨电极与焊件距离(弧长)一般不超过钨电极直径的1.5倍。 8、在焊接时一般焊丝与工件的角度成10?夹角,而钨电极焊枪与工件成75?夹角。 9、在焊接时的焊接速度一般每分钟约为250—300毫米,具体情况跟据个人的实际能力而确定氩弧 焊速度。
10、焊接时手势应平稳,焊丝应均速送入溶池内。 11、焊缝宽度应均匀、高低起伏应一致,焊缝应美观、漂亮。 4、注意事项: 1、在操作前应严格按照图纸及工艺要求作相关的准备工作。 2、在操作前应检查逆变式交直流氩弧焊机的电流选择开关是否在交流电的档位中。 3、在焊接过程中如遇板材不平,应先将其校平、校直,方可进行焊接。 4、不锈钢氩弧焊操作者,必须戴好头面罩、手套、穿好工作服、工作鞋,以避免电弧光中的紫外线和红外线灼伤。 5、在焊接过程中,特别是在夏天不能吹电风扇,以避免把保护气体吹散,确保焊接质量。 6、在焊接过程中,应确保焊机内风机正常运作,以保护设备正常使用。 7、焊接过程中,不能有影响产品质量的各种缺陷,如:焊瘤、未焊透等。 8、焊接完成待焊接件冷却后应将工艺撑杆去除,并将焊疤磨平。 9、焊后应去除焊渣等飞溅物,保证焊后产品清洁、美观。 10、在焊接过程中会产生一定的焊接变形,焊后应根据图纸的技术要求作相应的焊后校正。 11、当操作者在工作过程中发现有任何影响设备或产品质量的不确定因素都应立即停止工作,并切断电源,排除不确定因素后方可继续工作。如遇难以解决的问题应立即通知班组长或设备维修部。 12、操作完成后应对产品按图纸、工艺要求进行自检,并填写相应的单据(如:生产日报表、工序卡等),填写要认真、详细、规范。 13、未经培训人员不得擅自操作。
酸洗工艺流程
(一)利用酸溶液去除钢铁表面上的氧化皮和锈蚀物的方法称为酸洗。氧化皮、铁锈等铁的氧化物(Fe3O4,Fe2O3,FeO等)与酸溶液发生化学反应,形成盐类溶于酸溶液中而被除去。酸洗用酸有硫酸、盐酸、磷酸、硝酸、铬酸、氢氟酸和混合酸等。最常用的是硫酸和盐酸。酸洗工艺主要有浸渍酸洗法、喷射酸洗法和酸膏除锈法。一般多用浸渍酸洗法,大批量生产中可采用喷射法。钢铁零件一般在10%~20%(体积)硫酸溶液中酸洗,温度为40℃。当溶液中含铁量超过80g/L,硫酸亚铁超过215g/L时,应更换酸洗液。常温下,用20%~80%(体积)的盐酸溶液对钢铁进行酸洗,不易发生过腐蚀和氢脆现象。由于酸对金属的腐蚀作用很大,需要添加缓蚀剂。清洗后金属表面成银白色,同时钝化表面,提高不锈钢抗腐蚀能力。?? ??(二)为了消除硅藻土载体表面吸附,减少色谱峰拖尾,载体在使用前需进行酸洗或碱洗处理。酸洗是把载体用6mol/L盐酸浸煮2h或浓盐酸加热浸煮30min,过滤,用水洗至中性,烘干。酸洗可除去表面上的铁、铝、钙、镁等杂质,但不能除去硅醇基。酸洗载体适宜于分析酸性样品。?? ??(三)酸洗常用的酸为:盐酸、硫酸、硝酸、磷酸、氢氟酸。在酸洗时务必加入 酸洗缓蚀剂,防止酸对金属的腐蚀。 ?????钢丝酸洗后还要中和与润滑,因此它的工艺过程包括去锈、酸洗、水洗、涂层、干燥等5~8个流程。由于各种钢丝的生产工艺不同,其酸洗工艺也不同。??????1.适用于线材、半成品拉制的酸洗方法? ?????现以线材为例,叙述几种常用酸洗工艺。至于经过热处理的半成品,一般不另行剥壳去锈即直接进入酸洗。其它操作顺序则与线材相同。? ?????(1)以剥壳、上石灰糊为主的酸洗工艺其工艺流程为。? ?????线材—啼剥壳去锈—→酸洗—→水洗—→高压水冲洗—→上油脂石灰糊—→干燥?
氩弧焊通用焊接工艺
氩弧焊通用焊接工艺 Modified by JACK on the afternoon of December 26, 2020
手工钨极氩弧焊 通 用 焊 接 工 艺 目录 1、一般要求 2、应用范围 3、焊接准备 4、操作技术 5、焊接 6、氩气焊丝和焊条 7、焊接工艺
8、质量记录 9、焊接及注意事项 10、钨极氩弧焊安全规程 11、焊接危险点危险源辩识、评价及控制对策表 一、一般要求 1、焊接材料 焊丝:用于GB的焊丝应符合GB/T8110的有关规定,对于入库时间长而有锈斑,影响使用的应予报废。 保护气体的种类和质量:采用纯度大于%纯氩。 钨极的种类:采用钍钨极或铈钨电极,其端头的几何形状应根据电流的大小选择,采用小电流时,端头夹角为30度。 焊接设备:氩弧焊机。 焊接辅助装备:安全防护用品、手锤、角向砂轮等。 焊工资格:焊工必须经过南昌市技术质量监督局培训,并且取得相应的合格项目,方可从事相关焊接工作。 焊接工作必须按照技要、技术标准进行。 焊接环境:当风速大于2m/s、相对湿度大于90%、雨、雪环境、焊件温度低于0℃时,均应采取相应的措施来保证焊接质量。当焊件温度在-18~0℃之间时,应将始焊点周围100mm的母材预热到约15℃再开始焊接。否则禁止施焊。 焊接极性:直流正接既焊枪接负极,工件接正极。 在操作过程中若有个人无法解决的问题,应立即与班组长、检验员或焊接工程师联系。
根据焊接位置、持证项目、接头形式和作业情况等选择合适的焊接辅助装置。 去除坡口内、外20mm范围内的水、锈、油污等杂质。 根据图纸、工艺要求核对坡口形式及角度、材质、坡口尺寸及装配质量。 如需要标记移植,检查标记移植情况。 检查所用设备是否完好情况。 不锈钢管焊接的接头,应内部充氩保护,保护时,管子两头和管子四周的孔应该用美纹纸或铁板封住,以增强保护效果。 试焊,根据表1调节焊接参数。 表1焊接参数 二、应用范围 不同直径的钢管及耐热合金钢管子一般采用钨极氩弧焊打底,手工电弧焊填充及盖面层焊接,小直径管子可用手工钨极氩弧焊打底及盖面层焊接。 采用手工钨极氩弧焊打底的焊接工艺,具有很多优越性,它不仅能充分保证母材根部的良好熔透,焊缝具有良好的成型,同时可提高根部焊缝的塑性和韧性,减少焊接应力,从而可以避免产生根部裂纹,施焊中也不易出现未焊透、夹渣、气孔等缺陷。所以,已广泛用于一般重要设备,如承压管道、高压容器和高温高压锅炉中管子的焊接。 钨极氩弧焊焊接管子,主要有两种形式,一种是水平钨极自动氩弧焊(管子转动),主要用于可转动的直管子对接焊缝,另一种是全位置自动钨极氩弧焊(焊枪或机头围绕管子转动),主要用于焊接不可转动的弯管,这种焊接方法多采用程控脉冲电源。
不锈钢焊接工艺(氩弧焊工艺)
不锈钢焊接工艺 ( 第一部分:氩弧焊接 ) 焊接工艺指导书 一氩弧焊接 1.目的 为规范焊工操作,保证焊接质量,不断提高焊工的实际操作技术水平 , 特编制本指导书。 2.编制依据 2.1.设计图纸 2.2. 《手工钨极氩弧焊技术及其应用》 2.3. 《焊工技术考核规程》 3.焊接准备 3.1. 焊接材料 焊丝: H1Cr18Ni9Ti φ0.8 、φ 1、φ1.2 、φ 1.5 、φ2.0 焊丝应有制造厂的质量合格证,领取和发放有焊材管理员统一管理。焊丝在使用前应清除油锈及其他污物,露出金属光泽。 3. 2. 氩气 氩气瓶上应贴有出厂合格标签,其纯度≥ 99.95%,所用流量 6-9 升/ 分钟,气瓶中的氩气不能用尽,瓶内余压不得低于 0.5MPa ,以保证充氩纯度。 3.3. 焊接工具 3.3.1. 采用直流电焊机,本厂用WSE-315和 TIG400 两种型号焊机。 3.3.2. 选用的氩气减压流量计应开闭自如,没有漏气现象。切记不可先开流量计、后开气瓶,造成高压气流直冲低压,损坏流量计;关时先关流量计而后关氩气瓶。 3.3.3. 输送氩气的胶皮管,不得与输送其它气体的胶皮管互相串用,可用新的氧 气胶皮管代用,长度不超过 30 米。 3.4. 其它工器具 焊工应备有:手锤、砂纸、扁铲、钢丝刷、电磨工具等,以备清渣和消缺。
4.工艺参数 不锈钢焊接工艺参数选取表表一 壁厚焊丝直钨极直焊接电流 氩气流焊接喷嘴直电源焊缝余焊缝宽 mm 径 mm 径 mm A 量 L/min层次径 mm 极性高 mm 度 mm 0.8 0.8 160-8061 6 正接13 1.0 1.0 1.560-9061 6 正接14 1.2 1.0 1.580-10081-2 6 正接 1- 2.5 5 1.5 1.2 2.080-13081-2 6 正接 1-2.0 6 2.0 1.5 2.090-14082-38 正接 1-2.5 7-8 2.5 2.0 2.0100-15082-38 正接 1-2.0 8-9 3.0 2.0 3.0110-1601038 正接1-211-12 4.0 2.0 3.0120-180103-48 正接 1.5-2 12-13 5.工序过程 5.1. 焊工必须按照“考规”规定经相应试件考试合格后,方可上岗位焊接。 5.2. 严禁在被焊件表面随意引燃电弧、试验电流或焊接临时支撑物等。 5.3. 焊工所用的氩弧焊把、氩气减压流量计,应经常检查,确保在氩弧焊封底时 氩气为层流状态。 5.4. 接口前应将坡口表面及母材内、外壁的油、漆、垢锈等清理干净,直至发出 金属光泽,清理范围为每侧各为 10-15mm,对口间隙为 2.5 ~3.5mm。 5.5. 接口间隙要匀直,禁止强力对口,错口值应小于壁厚的10%,且不大于1mm。 5.6. 接口局部间隙过大时,应进行修整,严禁在间隙内添加塞物。 5.7. 接口合格后,应根据接口长度不同点 4-5 点,点焊的材料应与正式施焊相同, 点焊长度 10-15mm,厚度 3-4mm。 5.8. 打底完成后,应认真检查打底焊缝质量,确认合格后再进行氩弧焊盖面焊接。5.9. 引弧、收弧必须在接口内进行,收弧要填满熔池,将电弧引向坡口熄弧。 5.10. 点焊、氩弧焊、盖面焊,如产生缺陷,必须用电磨工具磨除后,再继续施焊,不得用重复熔化方法消除缺陷。 5.11. 应注意接头和收弧质量,注意接头熔合应良好,收弧时填满熔池。为保证焊缝严密性。 5.12. 盖面完毕应及时清理焊缝表面熔渣、飞溅。