从湿法炼锌锑盐净化钴渣中回收钴_锌_镉_铜解读
湿法炼锌提高银,铜等有价金属的生产实践

湿法炼锌提高银,铜等有价金属的生产实践发布时间:2023-06-15T06:55:29.063Z 来源:《新型城镇化》2023年11期作者:妥正东[导读] 常规浸出工艺,锌精矿经沸腾炉焙烧后得到锌焙砂,锌焙砂经中性、酸性两段浸出,常规浸出工艺得到的锌浸出渣含锌在20%左右,以及银、铅、铜、铁等其他有价金属;新疆紫金有色金属有限公司新疆克州 845350摘要:湿法炼锌常规浸出工艺被广为采用。
某锌冶炼厂产锌10万t/年,采用一套10万t/年的常规两段浸出工艺和一套10万t/年的“常规浸出-浮选回收银-浸出渣回转窑处理”工艺。
其中在常规浸出工艺条件下,锌精矿中的银主要以硫化物形态富集于焙砂酸浸出渣中,经浮选得到银精矿,浮选尾矿进入回转窑处理得到氧化锌,再经低浸、高浸两段浸出、浓密、过滤,回收锌、铜,铅、银等浸出富集于氧化锌酸浸渣中。
本文通过实验论证使浮选后的银精矿在高温、高酸及添加氧化剂的浸出工艺,达到了锌、铜等有价金属的进一步回收,以及银精矿中银、铅品位进一步富集的双重目的,使资源达到了综合利用的目的;并在工况化生产改造过程中,充分利用原有闲置的槽罐、管道、压滤机等设备,减少了改造投资,并在工况化生产中起到了良好效果。
关键词:银精矿;综合利用;高温高酸;工况化生产、经济效益;常规浸出工艺,锌精矿经沸腾炉焙烧后得到锌焙砂,锌焙砂经中性、酸性两段浸出,常规浸出工艺得到的锌浸出渣含锌在20%左右,以及银、铅、铜、铁等其他有价金属;在锌浸出过程中,其他杂质金属也会不同程度溶解于水溶液中,影响锌电积过程,进而降低锌产品纯度,因此需对浸出液进行净化处理。
其中主要杂质分为三类:第一类是影响产品质量的杂质如Cd、Cu和Fe;第二类杂质为Mg、Ca,会结晶阻塞管道,影响生产稳定运行;第三类是影响锌电积过程的Ni、Co、Ge、Sb、As、Cl及F等杂质。
湿法炼锌工艺产生的含锌浸出渣,一般采用回转窑还原挥发技术处理,回收其中的锌。
湿法炼锌中应用压滤机改善净液渣渣性的实践

湿法炼锌中应用压滤机改善净液渣渣性的实践作者:罗伟来源:《中外企业家·下半月》 2013年第12期罗伟(赤峰中色锌业有限公司,内蒙古赤峰024000)摘要:叙述了压滤机在湿法炼锌的净化溶液中除铜、镉、钴、镍、砷、锑、锗、铁渣的应用情况以及在运行中发现的存在问题和形成问题的原因;介绍了针对所存在的问题,对压滤机结构所进行的改进措施以及改造后所产生的效果。
关键词:湿法炼锌;压滤机;翻板;渣性改变的效果中图分类号:TK416+.1 文献标志吗:A 文章编号:1000-8772(2013)35-0235-01在赤峰中色库博红烨锌业有限公司湿法锌冶炼循环系统中,净液工段的主要生产目的就是把由浸出工段送过来的中上清液体内所含的铜、镉、钴、镍、砷、锑、锗、铁等杂质去除,得到符合电解锌工艺所需要的硫酸锌溶液。
其工艺流程图见图1。
去除杂质的方法就是通过加入锑盐、锌粉、硫酸铜、蒸汽加热等,使铜、镉、钴、镍、砷、锑、锗、铁等杂质元素形成沉淀,液体经过压滤机的过滤后,使沉淀物从溶液中分离出来,达到去除杂质的目的。
而净液渣中由于含有铜、镉、钴、锌等有价金属元素,具有很好的经济效益;所以净液渣在经过浸出、电解、压团、蒸馏等工序,回收其中的铜、镉、锌。
而净液渣中对含锌量和渣含水有很高的要求,净液渣中含锌的多少以及渣含水的多少,是衡量压滤机工作性能的一个重要指标。
一、净液压滤机存在的主要问题自公司于1997年一期投产,到2004年和2007年二、三期两次生产设备的升级、换代、改造,净液工段压滤机生产一直存在压滤后滤渣中含锌量偏高,渣的含水量多等问题。
造成滤渣中硫酸锌等有价金属的流失,以及滤渣因含水多运输的不方便等问题。
(一)压滤机的基本状况厢式压滤机主要由固定板、滤板、压紧板、横梁和压紧装置等组成。
两根横梁把固定板和压紧装置连接在一起构成机架,机架上靠近压紧装置端放置活动压紧板。
压紧板和固定板之间依次交替排列着滤板,滤板间夹着滤布。
湿法炼锌锑盐除钴工艺的研究

湿法炼锌锑盐除钴工艺的研究
湿法炼锌锑盐除钴工艺是通过化学反应来提高原料异型锌的锑含量的一种炼制工艺.
湿法炼锌锑盐除钴工艺可以提高原料铁的损耗和锑利用率,降低对环境造成的污染.
这种工艺就是在铁-锑熔铸中用热源加热喷雾器熔化硫化锑矿,冷却成盐状,以提高原
料铁的耗损和锑利用率;然后将锑盐混合在受热的锌浆中,添加乳化剂和钴去除剂(这种
钴去除剂可以有效地抑制锌浆中的钴含量),再把该锌浆加到硫酸铁的溶液中,使液体溶
液的pH值维持在8~9范围内,并进行搅拌和搅拌。
湿法炼锌锑盐除钴工艺的优势在于它可以有效改善原材料铁的损耗和锑利用率,并降
低对环境造成的污染。
此外,它采用的乳化剂和钴去除剂可以有效地抑制锌浆中的钴含量,大大提高炼锌效率。
湿法炼锌锑盐除钴工艺也有不足之处,如:1、当温度过高时,锑盐可能会在腐蚀熔
料中溶解而损失活性物质。
2、乳化剂的添加量不当或存在泄漏的情况下,也会影响炼锌
效果及金属结构的稳定性。
为了解决上述技术问题,改进湿法炼锌锑盐除钴工艺的首要因素是合理选择乳化剂、
加入合适的温度,并严格控制喷雾器加热过程。
同时,应做好产品加工、质量控制和污染
控制工作,及时发现和处理各类问题,确保湿法炼锌锑盐除钴工艺能够有效运行,确保炼
锌过程对环境造成的污染尽可能的减小。
湿法炼锌净化镍钴渣全湿法回收新工艺

湿 法炼锌 净 化过程 中产生 的镍钴 渣是 一种 典 型
的多金 属渣 泥 , 锌 含量 4 0 ~5 O , 钴 含量 0 . 3 ~
1 . 9 8 ~2 . 3 0 g / c m。 , 主要 成分 ( 干基 , ) : Z n 4 6 . 8 2 、 C o 0 . 4 3 、 C d 1 . 8 7 、 P b 0 . 9 5 、 As 0 . 0 1 、 Ni 0 . 0 2 , 磨 矿 细度 一0 . 0 7 4 mm 占 8 5 以上 。 采 用“ 全 湿 法 酸浸 ( 二段 浸 出) 一 活 化 剂分 离 锌
p r o c e s s e s i n c l u d i n g l e a c h i n g t e mp e r a t u r e o f 7 0 ℃ ,l e a c h i n g t i me o f 1 . 5 h,r a t i o o f l i q u i d t o s o l i d o f 4 :1,
2 0 1 3年 第 1 2期
有色金属( 冶炼部分 ) ( h t t p : / / y s y 1 . b g r i mm. c n )
d o i :1 0 . 3 9 6 9 / j . i s s n . 1 0 0 7 — 7 5 4 5 . 2 0 1 3 . 1 2 . 0 0 4
Ne w Re c o v e r y Pr o c e s s f o r Zi nc Hy d r o me t a l l u r g y Ni - - Co - ・ Be a r i ng Pu r i f i c a t i o n S l a g
Li a n g,LU Xi ng — wu,YI Cha o M A J i n。H E GU O — c a i ,CHENG
湿法炼锌除杂技术研究现状
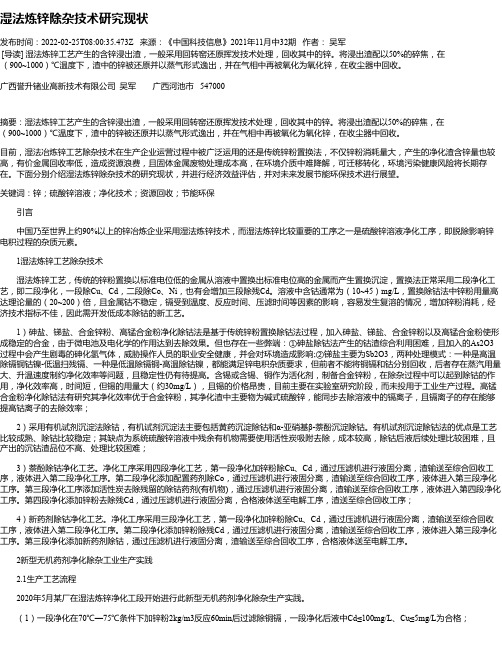
湿法炼锌除杂技术研究现状发布时间:2022-02-25T08:00:35.473Z 来源:《中国科技信息》2021年11月中32期作者:吴军[导读] 湿法炼锌工艺产生的含锌浸出渣,一般采用回转窑还原挥发技术处理,回收其中的锌。
将浸出渣配以50%的碎焦,在(900~1000)℃温度下,渣中的锌被还原并以蒸气形式逸出,并在气相中再被氧化为氧化锌,在收尘器中回收。
广西誉升锗业高新技术有限公司吴军广西河池市 547000摘要:湿法炼锌工艺产生的含锌浸出渣,一般采用回转窑还原挥发技术处理,回收其中的锌。
将浸出渣配以50%的碎焦,在(900~1000)℃温度下,渣中的锌被还原并以蒸气形式逸出,并在气相中再被氧化为氧化锌,在收尘器中回收。
目前,湿法冶炼锌工艺除杂技术在生产企业运营过程中被广泛运用的还是传统锌粉置换法,不仅锌粉消耗量大,产生的净化渣含锌量也较高,有价金属回收率低,造成资源浪费,且固体金属废物处理成本高,在环境介质中难降解,可迁移转化,环境污染健康风险将长期存在。
下面分别介绍湿法炼锌除杂技术的研究现状,并进行经济效益评估,并对未来发展节能环保技术进行展望。
关键词:锌;硫酸锌溶液;净化技术;资源回收;节能环保引言中国乃至世界上约90%以上的锌冶炼企业采用湿法炼锌技术,而湿法炼锌比较重要的工序之一是硫酸锌溶液净化工序,即脱除影响锌电积过程的杂质元素。
1湿法炼锌工艺除杂技术湿法炼锌工艺,传统的锌粉置换以标准电位低的金属从溶液中置换出标准电位高的金属而产生置换沉淀,置换法正常采用二段净化工艺,即二段净化,一段除Cu、Cd,二段除Co、Ni,也有会增加三段除残Cd。
溶液中含钴通常为(10~45)mg/L,置换除钴法中锌粉用量高达理论量的(20~200)倍,且金属钴不稳定,镉受到温度、反应时间、压滤时间等因素的影响,容易发生复溶的情况,增加锌粉消耗,经济技术指标不佳,因此需开发低成本除钴的新工艺。
1)砷盐、锑盐、合金锌粉、高锰合金粉净化除钴法是基于传统锌粉置换除钴法过程,加入砷盐、锑盐、合金锌粉以及高锰合金粉使形成稳定的合金,由于微电池及电化学的作用达到去除效果。
锌冶炼渣综合回收有价金属工艺综述与展望

锌冶炼渣综合回收有价金属工艺综述与展望摘要:我国的锌冶炼企业每年均会产生数百万吨渣料,例如炼锌渣和铅烟灰,铅泥等。
该废料中铅、金、银、铟等金属含量较高,具有巨大的回收价值。
近年来有方法研究从锌冶炼渣料中回收铅、金、银、铟等金属。
本文通过对从锌冶炼渣料中回收贵金属工艺的综述,对未来的综合回收工艺进行展望。
关键词:锌冶炼;渣料;综合回收;冶炼工艺引言对国内主流的湿法锌冶炼锌浸出渣处理工艺技术进行简要阐述,并结合某锌冶炼公司具体应用实例对改造效果进行分析。
企业通过积极进行技术升级改造,冶炼渣料中的贵金属综合回收能力大幅提高,经济效益显著增加,市场竞争力得到进一步加强。
同时,企业的技术升级改造也在向更大的深度和广度上发展。
通过生产工艺技术改造实现综合回收,既是一种有效的创效方式,又是企业可持续发展的有效途径,已经得到企业的普遍认同。
文中将对锌冶炼渣料处理工艺技术在实际工程中的应用效果进行重点分析。
1锌冶炼渣料回收贵金属1.1锌冶炼渣料来源锌冶炼工艺分为火法工艺和湿法工艺,火法炼锌过程中,主要的渣料为冶炼炉的炉渣和收尘器中的烟尘,铅、金、银、铟等贵金属大部分分布在炉渣中。
湿法炼锌工艺中,主要的渣料为常规工艺中的浸出渣、硫酸锌溶液的净化渣、电解过程的阳极泥以及回转窑氧化锌浸出渣(铅泥)等;高温沸腾浸出工艺中产生的黄钾铁矾渣、针铁矿渣、赤铁矿渣等。
1.2火法渣料回收有价金属火法炼锌的炉渣,一般通过在浮选的方式回收有价金属,将炉渣通过筛分、球磨后,用水配成矿浆加浮选药剂采用精密浮选机进行浮选,回收渣料中的金、银、铜、锌等有价金属。
烟尘一般通过火法窑炉在处理或通过湿法工艺将贵金属及常规有价金属进行分离富集,再进一步提炼成成品。
1.3湿法渣料回收有价金属在常规湿法炼锌两段浸出过程中,产出的浸出渣一般通过回转窑焙烧后变为氧化锌焙砂,再通过三段浸出分离贵金属及锌。
一段中性浸出将大部分锌浸出至溶液中返回主系统;浸出渣采用低酸浸出,将金属铟浸出至溶液中通过中和置换进行富集,富集后的高铟渣再通过浸出、萃取、反萃、电解等工序产出成品铟锭;酸性浸出渣通过高温高酸浸出,将金、银等贵金属富集至高铅渣中,高铅渣再通过铅冶炼系统或火法窑炉进行处理,进一步分离回收金、银等贵金属。
湿法冶炼锌系统中金属镉的回收
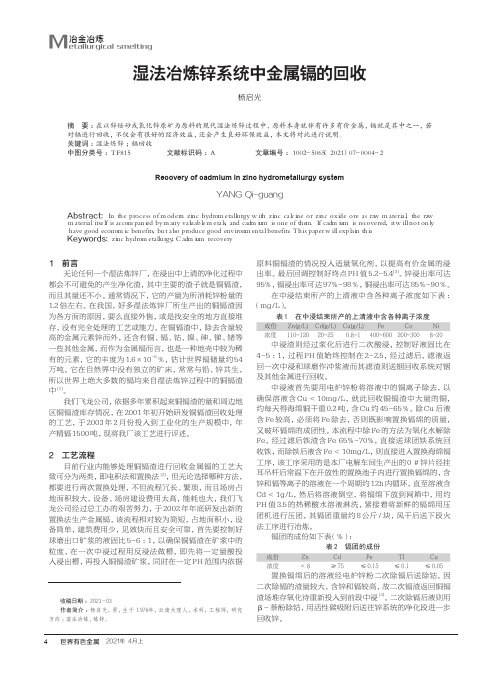
冶金冶炼M etallurgical smelting湿法冶炼锌系统中金属镉的回收杨启光(云南祥云飞龙有色金属股份有限公司,云南 祥云 672100)摘 要:在以锌焙砂或氧化锌原矿为原料的现代湿法炼锌过程中,原料本身就伴有许多有价金属,镉就是其中之一,若对镉进行回收,不仅会有很好的经济效益,还会产生良好环保效益,本文将对此进行说明。
关键词:湿法炼锌;镉回收中图分类号:TF815 文献标识码:A 文章编号:1002-5065(2021)07-0004-2Recovery of cadmium in zinc hydrometallurgy systemYANG Qi-guang(Yunnan Xiangyun Feilong Nonferrous Metals Co., Ltd,Xiangyun 672100,China)Abstract: In the process of modern zinc hydrometallurgy with zinc calcine or zinc oxide ore as raw material, the raw material itself is accompanied by many valuable metals, and cadmium is one of them. If cadmium is recovered, it will not only have good economic benefits, but also produce good environmental benefits. This paper will explain this.Keywords: zinc hydrometallurgy; Cadmium recovery1 前言无论任何一个湿法炼锌厂,在浸出中上清的净化过程中都会不可避免的产生净化渣,其中主要的渣子就是铜镉渣,而且其量还不小。
酸浸法处理湿法炼锌高钴锌渣回收锌和钴
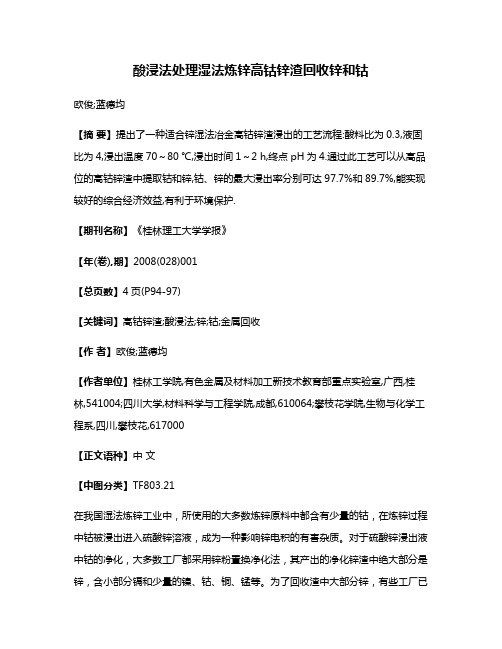
酸浸法处理湿法炼锌高钴锌渣回收锌和钴欧俊;蓝德均【摘要】提出了一种适合锌湿法冶金高钴锌渣浸出的工艺流程:酸料比为0.3,液固比为4,浸出温度70~80 ℃,浸出时间1~2 h,终点pH为4.通过此工艺可以从高品位的高钴锌渣中提取钴和锌,钴、锌的最大浸出率分别可达97.7%和89.7%,能实现较好的综合经济效益,有利于环境保护.【期刊名称】《桂林理工大学学报》【年(卷),期】2008(028)001【总页数】4页(P94-97)【关键词】高钴锌渣;酸浸法;锌;钴;金属回收【作者】欧俊;蓝德均【作者单位】桂林工学院,有色金属及材料加工新技术教育部重点实验室,广西,桂林,541004;四川大学,材料科学与工程学院,成都,610064;攀枝花学院,生物与化学工程系,四川,攀枝花,617000【正文语种】中文【中图分类】TF803.21在我国湿法炼锌工业中,所使用的大多数炼锌原料中都含有少量的钴,在炼锌过程中钴被浸出进入硫酸锌溶液,成为一种影响锌电积的有害杂质。
对于硫酸锌浸出液中钴的净化,大多数工厂都采用锌粉置换净化法,其产出的净化锌渣中绝大部分是锌,含小部分镉和少量的镍、钴、铜、锰等。
为了回收渣中大部分锌,有些工厂已采用选择性酸溶工艺[1,2],使产出的高钴锌渣中含锌量降到30%左右,渣中锌回收率超过90%,渣中钴、镉品位也相应地提高。
尽管如此,由于所产渣中的钴含量较高,给处理带来很大的困难,多数工厂只好堆置而不加处理,造成渣中尚存的大量锌不能回收利用,不但造成环境污染,也使渣中大部分资源浪费。
目前有研究者使用氨性体系处理锌渣[3],但该体系难于和现有体系相衔接,不甚理想。
有鉴于此,本文对锌渣进行了常规硫酸浸出研究,以能最好地溶出锌、钴、镉等金属进行综合回收,而对此浸出液中钴分离的热力学分析已有另文介绍[4]。
1.1 试验原理在锌浸出液锌粉置换净化钴过程中,所产渣中有相当一部分物料为金属态。
某些金属的可溶性硫酸盐如锌、镉、钴、镍等将直接溶于水中,这是由于氧化、洗涤不彻底;残酸等使渣中不可避免地夹杂;或由氧化物与硫酸反应形成硫酸盐。
湿法炼锌

湿法炼锌-中性浸出液的净化置换沉淀法除铜镉钴镍A 置换净化的热力学在水溶液中用一种金属取代另一种金属的过程为置换。
从热力学讲,只能用较负电性金属去置换溶液中的较正电性金属。
例如,用金属锌能将溶液中的铜置换出来:Zn+Cu2+ ==== Zn2++Cu↓因此,置换的次序决定于水溶液中金属的电位次序,而且置换趋势的大小决定于它们的电位差。
这一点可以通过热力学计算来说明。
从热力学分析可知,采用锌粉置换Cu,Cd,Co,Ni均可净化得很彻底,可使Cu,Cd,Co,Ni的离子活度分别为Zn离子活度的10-38,10-11.63,10-16.81,与10-17.69倍。
B 置换净化的动力学采用锌粉置换净化Cu,Cd比较容易,而净化除Co,Ni并不是很容易。
用理论量锌粉很容易沉淀除Cu,用几倍于理论量的锌粉也可以使Cd除去,但是用甚至几百倍理论量的锌粉也难以将Co除去至符合锌电积的要求。
Co难以除去的原因,国内外较多的文献都解释为Co2+还原析出时具有高的超电压的缘故,同时还有一个反应速率的问题。
置换反应的速率,可以理解为负电性金属在含有正电性金属离子的溶液中溶解速率,并可用下式表示:dc A- —— = k — cdt V式中 k——速率常数;A——与溶液的接触面积;V——溶液的体积;c——正电性金属离子的浓度;t——反应时间。
积分上式得到:V 1 c2k = - —·— ln —A t c1——为正电性金属离子反应前的浓度;式中 c1c——为正电性金属离子反应t时间后的浓度。
2置换过程速率可能是扩散控制,或者是化学反应控制。
研究证实,反应Zn+Cd2+ ==== Cd+Zn2+在50℃,当转速在250r/min以下时,置换反应速率常数k与转速n呈正比。
当转速在250r/min以上时,置换反应速率保持不变。
表明当低转速时,置换反应在扩散区进行,高转速时反应在动力学区进行。
置换反应速率与温度的关系式:(是在25~85℃范围内)1350lgk = 13.54 - ———T活化能 = 4.95 x 5650J/mol = 23.14kJ/mol,即反应没有纯扩散的特征。
十万吨常规湿法炼锌工艺流程简介及小金属回收

十万吨常规湿法炼锌工艺流程简介及小金属回收十万吨常规湿法炼锌工艺流程简介及小金属回收一、工艺流程锌精矿焙烧余热锅炉烟气焙砂烟尘球磨两段浸出收尘送制酸浓密机压滤液浸出液干燥回转窑挥发三段净化新液Cu 、Cd 渣Co 渣电解熔铸锌锭(出售)镉回收海绵镉铜渣酸洗沉钴钴精矿氧化锌烟尘多膛焙烧中性浸出浸出液浸出渣酸性浸出浸出液铅渣送铅厂氧化锌送氧化锌系统铟绵浸出萃取铟锭(出售)压团粗镉熔铸蒸馏精镉铸锭镉锭(出售)窑渣酸底流浮选银精矿磁选焦粉铁粉尾渣浮选Au 、Ag 、Cu 等电解熔铸蒸汽余热发电水解二、原料:一般锌矿石含锌量太低,不能直接还原处理,需要首先富集。
锌矿的富集或选矿通常在矿石像粗粒浸染状锌矿物或赋存在低密度脉石中锌-铅矿物容易处理。
它们首先需要破碎,通常在地下用颚式、旋回或圆锥破碎,然后用球磨或棒磨机麻到75~150μm (100 目~200目),再将破碎和筛分的矿石在重介质圆锥、跳汰机和摇床上处理。
在单锌矿石的情况下,通常用硫酸铜进行浮选,使疏水锌矿石颗粒粘附近到上升气泡。
浮选的锌精矿含锌50%~60%。
三、焙烧:焙烧系统由备料工段和焙烧工段两部分组成。
备料工段包括:锌精矿贮存、筛分、破碎(松散)等作业,为沸腾炉提供合格精矿。
焙烧工段包括:焙烧、烟气余热回收、焙砂冷却、焙砂磨细等工序。
锌精矿仓长120m,宽30m,采用半地下仓,内设3台5t抓斗桥式起重机、3台定量给料机。
精矿贮期30天。
锌精矿由汽车或火车运至仓内后,采用桥式抓斗起重机上矿,由定量给料机配料后,经胶带输送机送往转运站。
焙烧车间配置一台109m2鲁奇式沸腾焙烧炉。
焙烧温度控制在890℃左右。
焙烧炉沸腾层内设有冷却盘管,回收多余反应热,产生的蒸汽并入热力管网。
为了控制焙烧炉温度,炉内还设有自动喷水装置以便降低沸腾层温度。
主要技术经济指标年处理精矿量 198170t/a(干基)年工作日 330d沸腾焙烧炉床面积 109m2沸腾焙烧炉床能率5.5t/m2·d沸腾层高度 1m沸腾层线速度 0.56m/s锌可溶率 94.29%脱硫率 93.15%焙砂产量 84300t/a焙砂含锌 59.64%焙砂含硫 1.31%其中硫化物硫 0.38%烟尘产量: 88230t/a烟尘含锌 56.99%烟尘含硫 3.45%其中硫化物硫 1.23%焙烧温度890±20℃左右烧减率 87.06%鼓风量 48630m3/h焙烧炉出口烟气量 49300m3/h其中SO2浓度 9.551%锌焙烧回收率 99.5%四、浸出浸出工艺概述1备料焙砂用压缩空气输送到浸出厂房内的料仓,由料仓锥底排出经星型给料器、称量给料机、正反转螺旋给料机,将焙砂送入氧化槽和中性浸出槽内。
210979000_湿法冶炼锌锌粉净化工艺及净化渣处理工艺优化实践

2022年 12月下 世界有色金属5冶金冶炼M etallurgical smelting湿法冶炼锌锌粉净化工艺及净化渣处理工艺优化实践冶玉花(白银有色集团股份有限公司,甘肃 白银 730900)摘 要:本文针对于锌冶炼原料的日益紧缺及杂质成分越来越高等现象,为了提高净化系统对原料的适应性,通过对湿法炼锌常规的锌粉-锑盐净化工艺及净化渣处理工艺分析研究,提出了较为详尽的工艺完善及优化措施,在生产实践中取得了较好的效果,达到了增加效益和提高企业综合利用率水平的目的。
关键词:一段低温锌粉除铜镉;二段高温锌粉-锑盐除钴镍;净化渣;铜镉渣;镍钴渣中图分类号:TF813 文献标识码:A 文章编号:1002-5065(2022)24-0005-3Optimization of zinc powder purification process and slag treatment process in hydrometallurgical zinc smeltingYE Yu-hua(Baiyin Nonferrous Metals Group Co., Ltd., Gansu Baiyin 730900)Abstract: In view of the phenomenon of increasing shortage of zinc smelting raw materials and higher impurity composition, in order to improve the adaptability of the purification system to raw materials, through the analysis and study of the conventional zinc hydrometallurgy zinc powder - antimony salt purification process and purification slag treatment process, more detailed process perfection and optimization measures are put forward, and good results have been achieved in the production practice. It achieves the purpose of increasing efficiency and improving the level of comprehensive utilization of enterprises.Keywords: first-stage low-temperature zinc powder for removal of copper and cadmium; second-stage high-temperature zinc powder-antimony salt for removal of cobalt and nickel; copper-cadmium slag; nickel-cobalt slag收稿日期:2022-10作者简介:冶玉花(1978-),女,青海省民和县,大学本科,冶炼高级工程师,研究方向为锌湿法冶金、湿法炼锌综合回收利用。
锌湿法净化钴镍渣的综合回收

锌湿法净化钻镣渣的综合回收湿法炼锌的主要工序有焙烧、浸出、净化和电 积⑴。
关于浸出液的净化,世界各国的锌冶炼厂由 于不同的技术水平和原料的具体情况而釆用不同的 方法。
目前国内外釆用併盐净化的生产厂家有18 家,如美国大瀑布锌冶厂、中国会东铅锌矿、日本会 津锌冶厂、比利时埃思锌电积厂等;釆用碑盐净化的 生产厂家有13家,如日本秋田冶炼厂、日本饭岛锌 冶厂、西德打特思锌厂等〔2-5]。
这两种方法都能满 足溶液深度净化的要求,是目前世界上硫酸锌溶液 净化的主要方法与发展趋势。
钻镣渣是湿法炼锌净化渣之一。
根据净化方法 的不同,其渣的成分也有所不同,但无论是使用哪种 添加剂净化所产出的渣,都有可回收利用的价值。
所以,对工业废渣进行行之有效的处理,不但可以降 低环境的污染,而且能综合回收利用渣中的有价金 属。
1 试验原料和方法试验所釆用的原料是云南某湿法炼锌厂的逆镣 净化渣。
其化学成分为(%):Zn 38.32、Cd 11.30、 Co 0.41、Ni 0.29、Fe 0.14、Mn 0.18、Cu 0.11、S 6.20^Mg 0.40o试验拟将渣中镉、钻和镣分别开路处理,锌留在 净化液中返回湿法炼锌系统,工艺流程如下(图1)。
在置换除镉和镣过程中所用的还原剂为合金锌粉, 在除镣过程中添加Sb 2O 3,CuSO 4各50 mg/L,氧化 沉钻所用的氧化剂是过硫酸钠。
2 试验结果与讨论2.1硫酸浸出2.1.1硫酸量的影响80C,液固比2.5-1,浸出时间1 h,考察不同的 硫酸浓度对Zn.Co.Ni 浸出率的影响。
结果表明, 随着硫酸用量的增加,Zn 、Co 、Ni 的浸出率逐渐增 加,但当硫酸用量为理论量的 1.2倍时,Zn 、Co 、Ni 的浸出率分别为97%.96.8%和95.8%,再增加硫 酸用量,Zn 、Co 、Ni 的浸出率变化不大。
因此,硫酸 用量以理论量的1.4倍为宜。
钻镣渣 捋酸还原剂1硫酸浸出~1置换除镉11—1过滤1Fig. 1 Principle flow chart of dealing withCo-Ni residue2.1.2温度的影响液固比2.5:1,浸出时间1 h,硫酸用量为理论 量1.4倍,改变温度进行试验,考察温度对Zn 、Co 、 Ni 的浸出率影响。
湿法炼锌净化除钴技术探讨
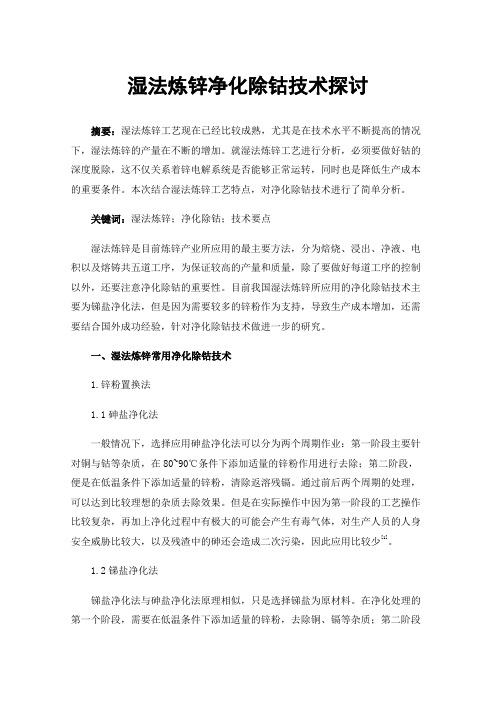
湿法炼锌净化除钴技术探讨摘要:湿法炼锌工艺现在已经比较成熟,尤其是在技术水平不断提高的情况下,湿法炼锌的产量在不断的增加。
就湿法炼锌工艺进行分析,必须要做好钴的深度脱除,这不仅关系着锌电解系统是否能够正常运转,同时也是降低生产成本的重要条件。
本次结合湿法炼锌工艺特点,对净化除钴技术进行了简单分析。
关键词:湿法炼锌;净化除钴;技术要点湿法炼锌是目前炼锌产业所应用的最主要方法,分为焙烧、浸出、净液、电积以及熔铸共五道工序,为保证较高的产量和质量,除了要做好每道工序的控制以外,还要注意净化除钴的重要性。
目前我国湿法炼锌所应用的净化除钴技术主要为锑盐净化法,但是因为需要较多的锌粉作为支持,导致生产成本增加,还需要结合国外成功经验,针对净化除钴技术做进一步的研究。
一、湿法炼锌常用净化除钴技术1.锌粉置换法1.1砷盐净化法一般情况下,选择应用砷盐净化法可以分为两个周期作业:第一阶段主要针对铜与钴等杂质,在80~90℃条件下添加适量的锌粉作用进行去除;第二阶段,便是在低温条件下添加适量的锌粉,清除返溶残镉。
通过前后两个周期的处理,可以达到比较理想的杂质去除效果。
但是在实际操作中因为第一阶段的工艺操作比较复杂,再加上净化过程中有极大的可能会产生有毒气体,对生产人员的人身安全威胁比较大,以及残渣中的砷还会造成二次污染,因此应用比较少[1]。
1.2锑盐净化法锑盐净化法与砷盐净化法原理相似,只是选择锑盐为原材料。
在净化处理的第一个阶段,需要在低温条件下添加适量的锌粉,去除铜、镉等杂质;第二阶段则是在高温条件下,添加适量的锌粉与锑盐,去除钴与镍等杂志。
在实际操作中,受湿法炼锌工艺条件影响,所需要的锑盐数量不同,可进行灵活调节。
相比砷盐净化法,锑盐净化法操作流程更加简单,具有较高的安全性,且不会对环境造成污染,是目前国内应用最为广泛的一种净化去钴的方法。
2.β-萘酚净化除钴法β-萘酚净化除钴法属于有机试剂除钴法,处理时是将适量的β-萘酚溶液添加到去除铜与镉的溶液内,进行大约10min的搅拌后,继续向内加入废电积液,待溶液温度达到65~75℃时,继续添加酸度为0.5g/L的硫酸,继续搅拌60min,观察发现溶液内有蓬松状红褐色络合物沉淀析出。
探讨提高湿法炼锌中铜镉的回收率的方法
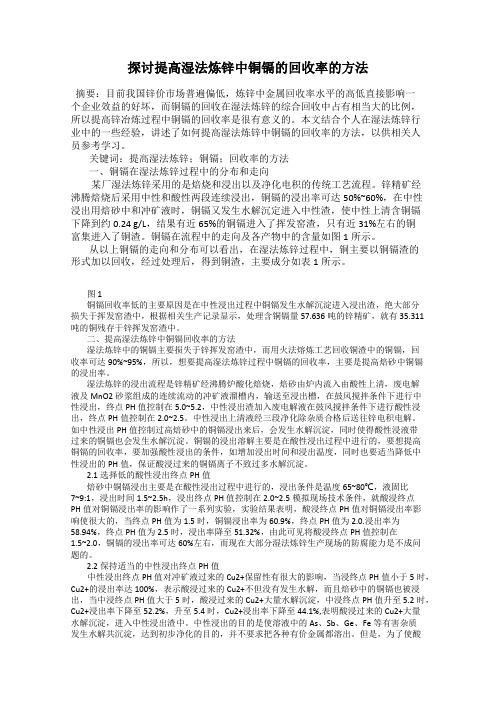
探讨提高湿法炼锌中铜镉的回收率的方法摘要:目前我国锌价市场普遍偏低,炼锌中金属回收率水平的高低直接影响一个企业效益的好坏,而铜镉的回收在湿法炼锌的综合回收中占有相当大的比例,所以提高锌冶炼过程中铜镉的回收率是很有意义的。
本文结合个人在湿法炼锌行业中的一些经验,讲述了如何提高湿法炼锌中铜镉的回收率的方法,以供相关人员参考学习。
关键词:提高湿法炼锌;铜镉;回收率的方法一、铜镉在湿法炼锌过程中的分布和走向某厂湿法炼锌采用的是焙烧和浸出以及净化电积的传统工艺流程。
锌精矿经沸腾焙烧后采用中性和酸性两段连续浸出,铜镉的浸出率可达50%~60%,在中性浸出用焙砂中和冲矿液时,铜镉又发生水解沉定进入中性渣,使中性上清含铜镉下降到约0.24 g/L,结果有近65%的铜镉进入了挥发窑渣,只有近31%左右的铜富集进入了铜渣。
铜镉在流程中的走向及各产物中的含量如图1所示。
从以上铜镉的走向和分布可以看出,在湿法炼锌过程中,铜主要以铜镉渣的形式加以回收,经过处理后,得到铜渣,主要成分如表1所示。
图1铜镉回收率低的主要原因是在中性浸出过程中铜镉发生水解沉淀进入浸出渣,绝大部分损失于挥发窑渣中,根据相关生产记录显示,处理含铜镉量57.636吨的锌精矿,就有35.311吨的铜残存于锌挥发窑渣中。
二、提高湿法炼锌中铜镉回收率的方法湿法炼锌中的铜镉主要损失于锌挥发窑渣中,而用火法熔炼工艺回收铜渣中的铜镉,回收率可达90%~95%,所以,想要提高湿法炼锌过程中铜镉的回收率,主要是提高焙砂中铜镉的浸出率。
湿法炼锌的浸出流程是锌精矿经沸腾炉酸化焙烧,焙砂由炉内流入由酸性上清,废电解液及MnO2砂浆组成的连续流动的冲矿液溜槽内,输送至浸出槽,在鼓风搅拌条件下进行中性浸出,终点PH值控制在5.0~5.2,中性浸出渣加入废电解液在鼓风搅拌条件下进行酸性浸出,终点PH值控制在2.0~2.5。
中性浸出上清液经三段净化除杂质合格后送往锌电积电解。
如中性浸出PH值控制过高焙砂中的铜镉浸出来后,会发生水解沉淀,同时使得酸性浸液带过来的铜镉也会发生水解沉淀。
湿法炼锌渣的无害化处理及资源综合回收pdf
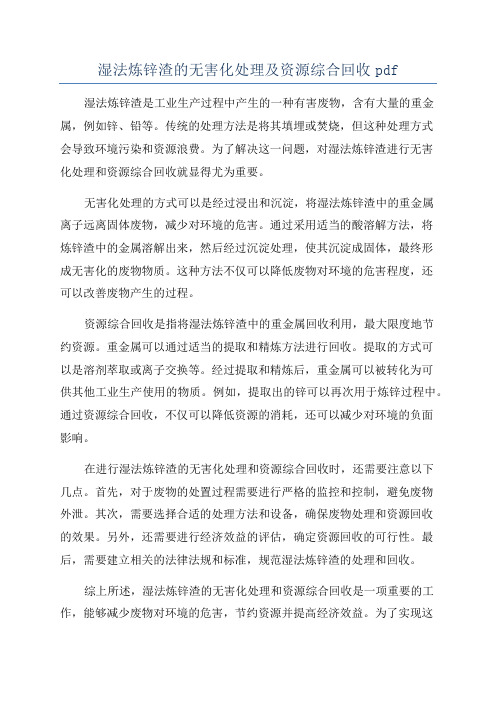
湿法炼锌渣的无害化处理及资源综合回收pdf 湿法炼锌渣是工业生产过程中产生的一种有害废物,含有大量的重金属,例如锌、铅等。
传统的处理方法是将其填埋或焚烧,但这种处理方式会导致环境污染和资源浪费。
为了解决这一问题,对湿法炼锌渣进行无害化处理和资源综合回收就显得尤为重要。
无害化处理的方式可以是经过浸出和沉淀,将湿法炼锌渣中的重金属离子远离固体废物,减少对环境的危害。
通过采用适当的酸溶解方法,将炼锌渣中的金属溶解出来,然后经过沉淀处理,使其沉淀成固体,最终形成无害化的废物物质。
这种方法不仅可以降低废物对环境的危害程度,还可以改善废物产生的过程。
资源综合回收是指将湿法炼锌渣中的重金属回收利用,最大限度地节约资源。
重金属可以通过适当的提取和精炼方法进行回收。
提取的方式可以是溶剂萃取或离子交换等。
经过提取和精炼后,重金属可以被转化为可供其他工业生产使用的物质。
例如,提取出的锌可以再次用于炼锌过程中。
通过资源综合回收,不仅可以降低资源的消耗,还可以减少对环境的负面影响。
在进行湿法炼锌渣的无害化处理和资源综合回收时,还需要注意以下几点。
首先,对于废物的处置过程需要进行严格的监控和控制,避免废物外泄。
其次,需要选择合适的处理方法和设备,确保废物处理和资源回收的效果。
另外,还需要进行经济效益的评估,确定资源回收的可行性。
最后,需要建立相关的法律法规和标准,规范湿法炼锌渣的处理和回收。
综上所述,湿法炼锌渣的无害化处理和资源综合回收是一项重要的工作,能够减少废物对环境的危害,节约资源并提高经济效益。
为了实现这一目标,需要采取适当的处理方法和设备,并建立相关法律法规和标准,确保废物处理和资源回收的有效性和可行性。
这样才能保护环境,促进可持续发展。
湿法炼锌的钴渣处理研究
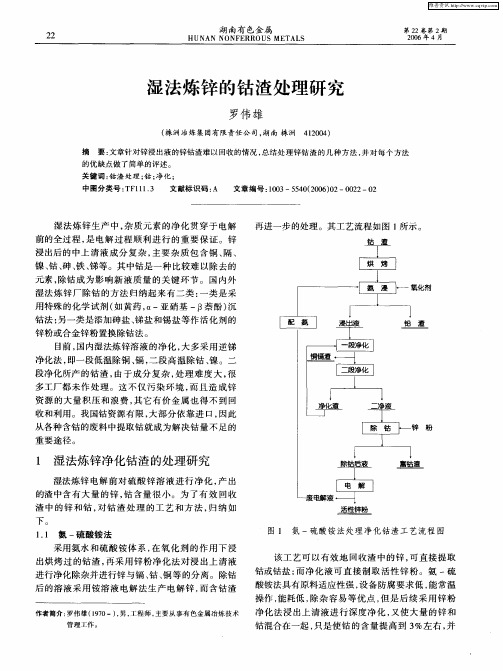
方法进行 了综合试验 , 富集含 量可 以达 到 4 ~ 钴 %
1% , 于进 一步 回收 。 2 便
但是 研究 表 明 , 用锑 盐 除钴 渣 进 行净 液 除 钴 , 采
选择性 , 果证 明 C ae3 2的效 果 较好 。 山西大 学 结 ynx0
化学系 王 靖 芳 等 人 采 用 P0 化 煤 油 在 硫 酸 体 系 57磺 下 , 以有效 地萃 取分 离锌 和其 它杂 质离子 。加拿 大 可
重 要途径
l 湿法炼锌净化钴渣 的处理研究
湿法 炼锌 电解 前 对 硫 酸 锌 溶 液 进行 净 化 , 出 产
的渣 中含 有 大 量 的锌 , 含 量 很 小 。 为 了有 效 回 收 钴 渣 中 的锌 和钴 , 对钴 渣 处 理 的 工 艺 和 方 法 , 纳 如 归
下。
壁 图 1 氨 一硫 酸铵 法处 理 净化 钴渣工 艺 流程 图 该 工 艺 可 以有 效 地 回收渣 中 的锌 , 可直 接 提 取
维普资讯
2 2
湖南 有 色金 属
H U NA N 0N FER ROU S M ETALS N
第2 2卷 第 2 期 20 0 6年 4月
湿法炼锌 的钴渣处理研究
罗伟 雄
( 株洲冶炼集 团有 限责任公 司, 湖南 株洲 摘 4 20 ) 104
作者简介 : 罗伟 雄 (9 0一)男 , 17 , 工程 师 , 主要从事 有色金属冶炼 技术 管理工作。
钴或 钴盐 ; 而净 化 液可 直 接 制 取 活性 锌 粉 。氨 一硫 酸 铵法 具有 原料 适应性 强 , 备 防腐 要 求低 , 常温 设 能 操作 , 能耗低 , 杂 容 易 等优 点 , 是 后 续 采 用 锌 粉 除 但 净 化 法 浸 出上 清 液 进 行 深 度净 化 , 使大 量 的锌 和 又
- 1、下载文档前请自行甄别文档内容的完整性,平台不提供额外的编辑、内容补充、找答案等附加服务。
- 2、"仅部分预览"的文档,不可在线预览部分如存在完整性等问题,可反馈申请退款(可完整预览的文档不适用该条件!)。
- 3、如文档侵犯您的权益,请联系客服反馈,我们会尽快为您处理(人工客服工作时间:9:00-18:30)。
39技术从湿法炼锌锑盐净化钴渣中回收钴、锌、镉、铜□文/刘庆杰贾玲李广海中冶葫芦岛有色金属集团公司技术中心摘要:在湿法炼锌工艺中,采用锑盐除钴法产出的净化钴渣经过酸性浸出后,锌、镉、钴等有价金属进入溶液,铜进入浸出渣。
浸出液经过双氧水氧化除铁、低温锌粉置换除铜后,用α-亚硝基-β-萘酚的碱性溶液进行沉钴,沉钴渣经过酸洗除杂后,进行氧化焙烧而得粗Co 3O 4。
该工艺,经济效益明显。
Puri fi cation of Salt from the Hydrometallurgy of C obalt Antimony Slag Recovery of Cobalt, Zinc, cadmium, Copper湿法炼锌的除钴方法有砷盐除钴法、黄药除钴法、β-萘酚除钴法和锑盐除钴法。
砷盐除钴法有剧毒的砷化氢气体产生,同时铜镉渣被砷污染而使回收流程复杂化;黄药除钴法由于在生产的过程中有恶臭气体产生,作业环境恶劣;β-萘酚除钴法在国外应用较多,如日本的彦岛、安中等冶炼厂,国内的紫金矿业在处理高钴锌精矿采用β-萘酚除钴法;锑盐除钴法除杂能力强,作业环境好,其应用越来越广泛。
目前,国内采用锑盐除钴法的湿法炼锌企业中,净化钴渣的处理通常采用稀酸进行选择性的浸出,即将净化钴渣中的锌浸出进入溶液而将钴留在渣中。
稀酸选择性浸出工艺的不足之处在于:选择性比较差,锌钴分离不彻底;浸出渣中含锌、镉高,其中浸出渣中含锌高达20%以上,需采用回转窑处理回收这部分锌、镉;经过回转窑处理,铜、钴进入窑渣中,不能有效回收。
研究如何从净化钴渣中综合回收锌、镉、铜、钴等有价金属,是一项紧迫的任务。
一、基本原理β-萘酚除钴工艺的反应机理是β-萘酚与NaNO 2在弱酸性溶液中生成α-亚硝基-β-萘酚,α-亚硝基-β-萘酚同钴反应生成蓬松的红褐色内络盐沉淀(通常叫螯合物沉淀。
α-亚硝基-β-萘酚不稳定,生产中只能边使用边制备。
反应前,β-萘酚同按比例在NaOH溶液中混合配制。
在碱性溶液中配制的原因一是β-萘酚溶于碱液而难溶于水,二是NaNO 2在碱性溶液中稳定。
主要化学反应方程式如下:NaNO 2 + H + = Na + + HNO 2 C 10H 7ONa + H + = C 10H 8O + Na +C 10H 8O + HNO 2 = C 10H 6ONOH + H 2O 4Co 2+ + C 10H 6ONOH+ 4H + = 4Co 3+ + C 10H 6NH 2OH + H 2O C o3++3C10H6O N O H =Co(C 10H 6ONO3↓ + 3H +二、工艺过程从湿法炼锌锑盐净化钴渣中回收钴的工艺流程为:净化钴渣经过酸性浸出后,锌、镉、钴等有价金属进入溶液,铜进入浸出渣。
浸出液经过双氧水氧化除铁、低温锌粉置换除铜后,用α-亚硝基-β-萘酚的碱性溶液进行沉钴,沉钴渣经过酸洗除杂后,进行氧化焙烧而得粗Co 3O 4。
从湿法炼锌净化钴渣中回收钴工艺流程见图1。
1. 酸浸根据加料量,计算加水量和加酸量。
先将水加入浸出罐中,然后打开加酸阀门加酸。
打开蒸汽阀门加热,当溶液温度达到50℃~60℃时,开始加料,进行浸出。
浸出结束,停止搅拌,进行压滤。
滤渣洗涤数次,洗液返回酸浸配液或打入除铁槽中,酸浸渣脱水后运到渣场存放。
浸出控制要点:(1加料的速度。
加料的速度不宜过快,避免物料沉底或反应过快造成冒槽事故。
加料时,仔细观察反应情况,当反应过快时,适当减少加料量或停止加料,待反应平稳后继续加料或增加加料量。
(2浸出的温度。
温度低,作业的时间长,金属的浸出率低;温度过高,反应过于激烈,易发生冒槽事故。
(4浸出时间。
40资源再生 2010/9T技术echnology图1 从电解锌净化钴渣中回收钴工艺流程图(5浸出终点pH值控制(当pH值>1.5时,加酸调整;pH值<1.0时加钴渣调整。
湿法炼锌净化钴渣见表1,废电解液成份见表2,浸出液成份见表3。
2. 除铁根据浸出液中铁元素的含量计算出铁的量,按照铁和双氧水的一定质量比计算出双氧水的用量。
除铁时,先将双氧水慢慢加入到浸出液中,然后加入氢氧化钠,调整pH 值,将p H 值控制在4~5之间,搅拌0.5~1小时。
取样分析除铁后液含Fe合格后,进行压滤。
除铁渣洗涤数次。
洗液返回酸浸配液或打入沉钴槽,除铁渣运到渣场存放。
除铁控制要点:(1作业温度;(2双氧水的用量;(3终点的p H 值。
除铁后液成份见表4。
3. 除铜根据除铁后液中铜的含量计算出铜的重量,按照铜和锌粉的一定的质量比计算出锌粉的用量。
将锌粉慢慢加入到除铁后液中,搅拌30分钟,取样分析,除铜后液含Cu合格后,进行压滤。
滤渣用少量水冲洗,洗液和除铜后液打入除钴槽。
除铜控制要点:(1作业温度;(2锌粉用量。
除铜后液成份见表5。
4. 沉钴根据除铁液中钴的含量计算出Co的重量,按照Co:β-萘酚:亚硝酸钠:烧碱:水,计算出β-萘酚、亚硝酸钠、烧碱、水的用量,进行配制α-亚硝基-β-萘酚溶液。
配制时,先加烧碱,然后加入水,加热至温度50℃~60℃,同时进行适当搅拌。
烧碱全部溶化后将β-萘酚加入到烧碱溶液中,然后将亚硝酸钠加入到β-萘酚烧碱溶液中,进行搅拌直至溶解完全。
α-亚硝基-β-萘酚溶液放置时间不能超过2小时,要现用现配。
通蒸汽将除铜后液加热60℃~70℃,将配好的α-亚硝基-β-萘酚溶液缓慢地加入到除铜后液中,然后慢慢地加入浓硫酸调溶液的pH值,搅拌2个小时。
取沉钴后液分析,分析元素Co,沉钴后液合格后,进行压滤。
沉钴后液经过活性炭吸附后,返到浸出工序。
沉钴控制要点:(1β-萘酚、亚硝酸钠、烧碱与钴的比例;(2调酸的速度;(3终点的pH值。
沉钴后液的成份见表6。
5. 钴渣煅烧称量要煅烧的物料,将物料放入炉内,散开铺平。
调整布袋入口插板,保持炉内微负压,然后点燃煤气升温,升温的速度不宜过快,将温度控制一定的温度范围,恒温,直到没有烟气逸出时,停止加热。
待氧化钴完全冷却后,将氧化钴取出、分析、称重。
氧化焙烧控制要点:(1作业温度;(2空气的量。
粗Co 3O 4的成份见表7。
编号Co Zn Cd Mn Cu Fe #1净化钴渣0.60590.880.130.350.19#2净化钴渣0.3761.273.720.170.290.11编号Zn H2SO4Mn Fe #1电解废液49.32172.48 2.300.005#2电解废液50.35168.562.60表1湿法炼锌净化钴渣化学成分单位:%表2湿法炼锌废电解液化学成分单位:g/l试样编号Co Zn Cd Mn Cu Fe #1浸出液0.21111.318.00 2.500.050.026#2浸出液0.24134.090.510.740.080.015 #3浸出液0.50110.97 5.64 1.340.100.032#4浸出液0.52115.08 5.32 2.210.200.032#5浸出液0.64144.881.161.300.200.031表3湿法炼锌净化钴渣浸出液成份单位:g/l试样编号Co Zn Cd Mn Cu Fe #1除铁后液0.20109.167.50 2.460.040.001#2除铁后液0.22122.890.500.700.060.001#3除铁后液0.49105.76 5.46 1.290.090.001#4除铁后液0.50108.69 5.30 2.200.160.001#5除铁后液0.60135.651.081.270.200.001表4 除铁后液成份单位:g/l41技术表8挥发窑处理钴渣工艺与β-萘酚除钴工艺成本分析三、主要技术经济指标及经济效益对比1. 主要技术经济指标(1浸出渣含钴≤1%,浸出渣率≤2%,浸出率≥95%(2除铁后液含铁≤0.005g/L (3除铜后液含铜≤ 0.005g/L (4沉钴后液含钴≤0.001g/L,沉钴率≥99%(5粗氧化钴含钴≥40%(6废电解液消耗量800m 3/吨.钴(7双氧水消耗量0.5吨/吨.钴(8氢氧化钠消耗量5吨/吨.钴(9亚硝酸钠消耗量7.5吨/吨.钴(10β-萘酚10~12吨/吨.钴2. 挥发窑处理钴渣工艺与β-萘酚除钴工艺成本分析挥发窑处理钴渣工艺与β-萘酚除钴工艺成本分析见表8。
四、结论采用β-萘酚法从湿法炼锌锑盐净化钴渣回收钴、锌、镉、铜等有价金属,工艺成熟可靠,产品中钴的含量达到了50%,沉钴后液钴的含量达到了1mg/l以下。
在回收钴的同时,锌、镉、铜也得到了回收,其中锌、镉以硫酸盐溶液的形式返到浸出工序,铜富集到浸出渣中,含铜量达到了40%。
按照某公司13万t/a电解锌计算,采用β-萘酚法从湿法炼锌锑盐净化钴渣回收钴、锌、镉、铜等有价金属工艺与选择性浸出分离钴、锌、镉、铜—挥发窑回收锌、镉工艺相比,不仅减少了废渣对环境的污染,而且每年新增经济效益500万元,经济效益十分明显。
参考文献略试样编号CoZnCdMnCuFe#1除铜后液0.20109.20 3.76 2.400.0010.001#2除铜后液0.22122.870.300.700.0010.001#3除铜后液0.49105.52 1.89 1.300.0010.001#4除铜后液0.50108.60 4.26 2.200.0010.001#5除铜后液0.60135.380.35 1.250.0010.001表5除铜后液成份单位:g/l试样编号CoZnCdMnCuFe#1沉钴后液0.001102.66 2.80 2.320.0010.001#2沉钴后液0.001122.870.280.540.0010.001#3沉钴后液0.001105.52 1.80 1.150.0010.001#4沉钴后液0.001108.60 4.17 1.960.0010.001#5沉钴后液0.001135.380.27 1.060.0010.001表6沉钴后液的成份单位:g/l试样编号Co Zn Cd Mn Cu Fe #1氧化钴58.800.520.0010.0010.200.35#2氧化钴56.11 1.970.0130.0180.200.53#3氧化钴56.83 1.850.160.0160.0700.70#4氧化钴50.99 1.690.0700.0360.790.87#5氧化钴50.341.530.380.00150.601.99表7粗Co 3O 4的成份单位:% 项目β-萘酚除钴挥发窑处理钴渣差价(元单耗(吨价格(元单耗(吨/吨价格(元一、产品(钴 1.0240000 240000二、原料70700三、减返回品20000 硫酸锌m m 0铜渣0.5 4000020000四、加工费185152 12850956643经济效益(元/吨.钴203357。