失效分析的思路与诊断
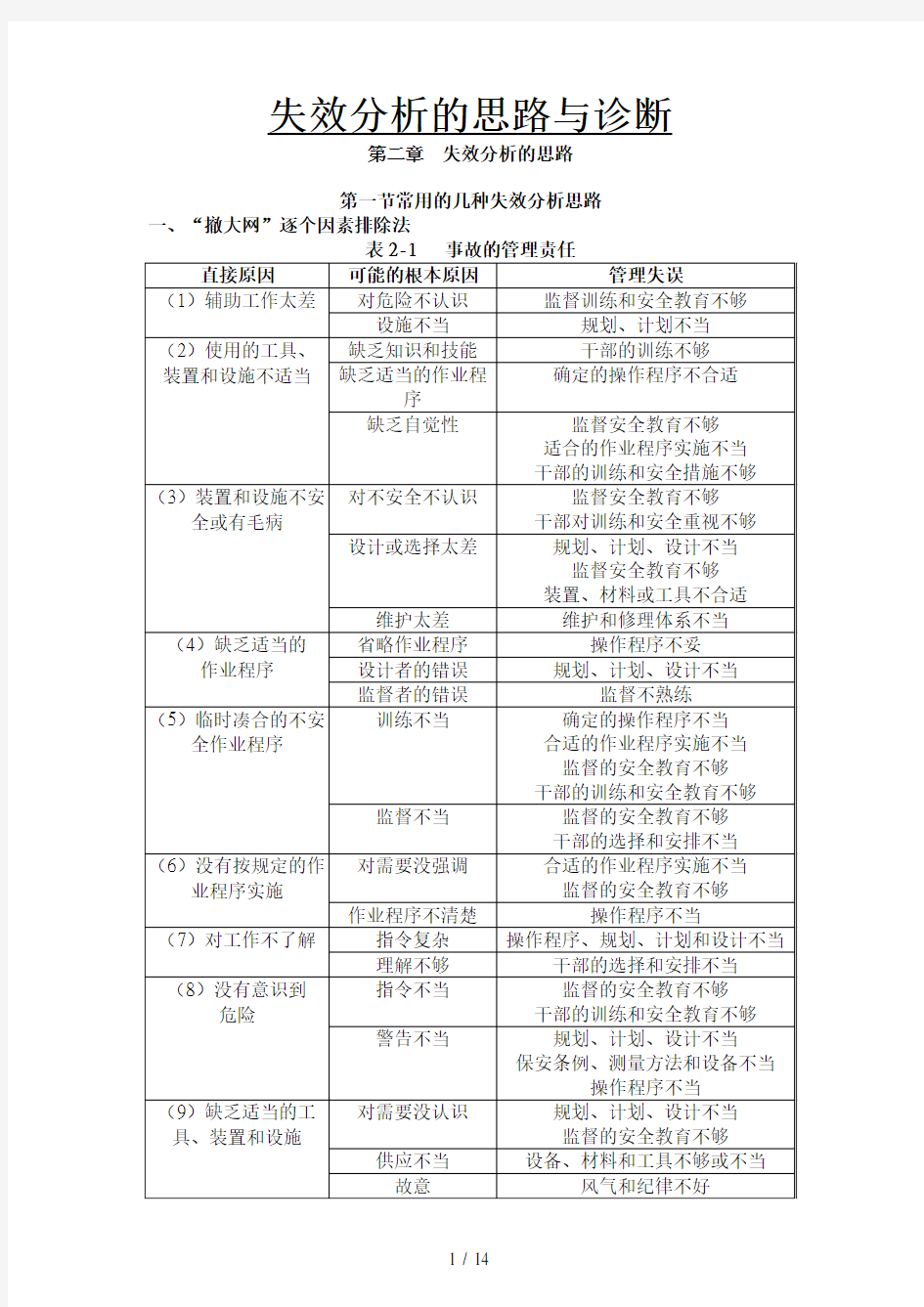

失效分析的思路与诊断
第二章失效分析的思路
第一节常用的几种失效分析思路
一、“撤大网”逐个因素排除法
二、以设备制造全过程为一系统进行分析
任何一个设备都要经历规划、设计、选材、机械加工(包括铸、锻、焊等工艺)、热处理、二次精加工(研磨、酸洗、电镀)和装配等制作工序,如果失效已确定纯属设备问题,还可对上述工序逐个进一步分析,包括以下内容:1.设计不当
(1)开孔位置不当造成应力集中;
(2)缺口或凹倒角半径过小;
(3)高应力区有缺口;
(4)横截面改变太陡;
(5)改变设计,没有相应地改变受力状况;
(6)设计判据不足;
(7)计算中出现过载荷;
(8)焊缝选择位置不当,以及配合不适当等;
(9)对使用条件的环境影响,未做适当考虑;
(10)提高使用材料的受力级别;
(11)刚性和韧性不适当;
(12)材料品种选择错误;
(13)选择标准不当;
(14)材料性能数据不全;
(15)材料韧脆转变温度过高;
(16)对现场调查不充分,认识不足就投入设计;
(17)与用户配合有差错。
2.材料、冶金缺陷
(1)成分不合格;
(2)夹杂物含量及成分不合格;
(3)织组不合格;
(4)各种性能不合格;
(5)各向异性不合格;
(6)断口不合格;
(7)冶金缺陷(缩孔、偏析等);
(8)恶化变质;
(9)混料。
3.锻造等热加工工艺缺陷
(1)折叠、夹砂、夹渣;
(2)裂缝;
(3)锻造鳞皮;
(4)流线分布突变或破坏;
(5)晶粒流变异常;
(6)沿晶氧化(过烧);
(7)氧化皮压入;
(8)分层、疏松;
(9)带状组织;
(10)过热、烧裂;
(11)外来金属夹杂物;
(12)缩孔;
(13)龟裂;
(14)打磨裂纹;
(15)皱纹。
4.机械加工缺陷
(1)未按图纸要求;
(2)表面粗糙度不合格;
(3)倒角尖锐;
(4)磨削裂纹或过烧;
(5)裂纹;
(6)划伤、刀痕;
(7)毛刺;
(8)局部过热;
(9)矫直不当。
5.铸造缺陷
(1)金属突出;
(2)孔穴;
(3)疏松;
(4)不连贯裂纹;
(5)表面缺陷;
(6)浇注不完全;
(7)尺寸和形状不正确;
(8)夹砂、夹渣;
(9)组织反常;
(10)型芯撑、内冷铁。
6.焊接缺陷
(1)错口超标;
(2)咬边超标;
(3)焊肉过凸或过凹;
(4)焊道深沟;
(5)焊趾、焊缝或根部有裂纹;
(6)熔化不全;
(7)打弧;
(8)焊接深度不够,未焊透;
(9)夹渣、夹杂或疏松;
(10)接头尺寸不合格;
(11)热输入不适当;
(12)焊前预热不足;
(13)焊后消除热应力不够或未消除;
(14)显微组织不合格;
(15)焊接裂纹。
7.热处理不当
(1)过热或过烧;
(2)显微组织不合格;
(3)淬火裂纹;
(4)淬火变形、翘曲;
(5)奥氏体化温度不当使晶粒粗大;
(6)脱碳或增碳;
(7)渗氮;
(8)回火脆化;
(9)淬火后未及时回火;
(10)热应力。
8.再加工缺陷
(1)酸洗后或电镀后未除氢或除氢不够;
(2)酸迹清洗未尽;
(3)镀前喷丸清洗不全;
(4)电镀电极打弧引起硬点;
(5)镀Cd、镀Zn的液态金属脆化;
(6)形成金属间化合物致脆;
(7)碰伤、标记压痕过深或位置不当;
(8)校直引起残余应力;
(9)镀铬碎屑划伤;
(10)化学热处理不当;
a.渗层组织反常;
b.力学性能不合格。
9.装配检验中的问题
(1)轴线对中不正;
(2)紧固件松动;
(3)敲打损伤;
(4)装配损伤;
(5)装配不正确;
(6)强迫装配;
(7)装配说明书说明不全或不清楚;
(8)装配马虎大意;
(9)磁粉检查电弧烧伤;
(10)磁化吸住钢屑造成磨损;
(11)漏检。
10.使用和维护不当
(1)超载、超温、超速;
(2)冲撞、热冲击;
(3)振动过大的断续载荷;
(4)操作错误、没按说明书要求做;
(5)每次开车或停车猛烈、突然;
(6)清洗剂不适合;
(7)润滑不当;
(8)疏忽,不按期维护;
(9)没定期检查;
(10)修理不当;
(11)灾害预防措施不完善;
(12)安全措施差;
(13)漏电;
(14)早期疲劳裂纹。
11.环境损伤
(1)腐蚀性气氛介质;
(2)高温或温度陡度过大;
(3)低温;
(4)海洋气氛;
(5)碱性溶液;
(6)氨气氛;
(7)润滑介质不适合;
(8)润滑剂变质或污染;
(9)流体介质中含有磨粒;
(10)控制的或规定的环境不适当。
上面列举了可能引起设备系统失效的一些主要因素,当然这并非全部因素。还应指出,在某一大方面(如热处理不当)的因素中,有的还可以往前追查原因,例如对于热处理不当的淬火裂纹,还可进一步分析其原因,如表2-2所列举的。
表2-2 导致形成淬火裂纹的因素
对于使用中承受交变载荷的部分出现的早期疲劳断裂,也可进一步分析其失效原因,如表2-3所示:
表2-3 金属部件疲劳失效的诱发因素
三、根据部件失效模式分析
机械产品一旦失效,一般表现为过量变形、表面损伤、破裂或断裂三种主要形式。这些类型还要进一步按失效模式再细分类。下面表2-4是按实际观察到的一些失效模型⑵所作的分类。
表2-4 金属零部件的各种失效模式
六、根据部件和设备类别分析
1.轴类零件的失效原因
轴类的失效模式,有以下12种:
(1)单向弯曲疲劳;
(2)双向弯曲疲劳;
(3)旋转弯曲疲劳;
(4)扭转疲劳;
(5)接触疲劳;
(6)微振疲劳;
(7)脆性疲劳;
(8)延性疲劳;
(9)塑性变形;
(10)磨损失效;
(11)蠕变断裂;
(12)腐蚀断裂。
常见的有弯曲疲劳损坏、扭转疲劳损坏、复合的(弯曲和扭转)疲劳损坏、和超载或撞击的延性断裂。
引起轴类失效的原因如表2-8和表2-9所示⑸。
表2-8 轴类失效的原因与诱发因素
表2-9 联邦德国阿利安茨技术中心1968—1975年间对传动轴和
支承轴失效案例统计⑸
a.包括制订产品规划和设计的失误(结构布局不合理、计算错误、几何形
状不合理、选材不当等)。制造工艺和处理工艺所造成的缺陷(如焊
接、铸造、热处理、机加工缺陷等),装配或安装造成的缺陷,以及混料、用错料等原因引起的失效。
b.如因振动造成的松动、安全保护装置失灵,伺服设施故障、磨损、腐
蚀、失效老化等引起的失效。
c.如自然灾害、异物侵袭、电网超高压等造成的失效。
2.滑动轴承的失效原因
滑动轴承失效的表现形式,常见的是轴瓦上有磨损沟槽、腐蚀斑块,剥落和麻点。其原因和诱发因素列于表2-10。
表2-10 滑动轴承失效的原因和诱发因素
3.滚动轴承的失效原因
不同的失效原因造成滚动轴承失效的形式也大不相同,说明于表2-11和表2-12。
4.弹簧的失效原因
弹簧失效的主要模式是疲劳断裂和脆性断裂。其次是腐蚀断裂、应力腐蚀断裂、氢脆、黑脆、松弛、变形和磨损。现将弹簧脆断和疲劳断裂的原因和影响因素列表于2-13。至于两种断裂的特征,横向平断口上无贝壳花样的为脆断;斜断口上有贝壳花样的为疲劳断。
表2-11 滚动轴承失效的原因及其对应的损坏形式
表2-12 滑动轴承和滚动轴承失效案例原因的统计分布⑸
表2-13 弹簧脆性断裂和疲劳断裂的原因
5. 齿轮的失效原因
齿轮损伤的模式,主要表现为断齿和齿面损伤。现将齿轮失效模式和失效原因列表如下。
表2-14 齿轮失效的模式、形貌和原因
注:1. 上述失效模式中,以疲劳断裂、麻点、磨损和咬接四种最常见。
2. 麻点、齿面剥落、磨损、咬接、塑性变形和裂纹都能促进疲劳断裂,其
中的后二种常导致疲劳断裂。
故障诊断方法与应用
课程名称:故障诊断方法与应用报告题目:内圈故障诊断实验报告学生班级;研152 学生姓名: 任课教师: 学位类别:
设备故障诊断技术是一种了解和掌握设备在使用过程中的状态,确定其整体或局部是正常或异常,早期发现故障及其原因,并能预报故障发展趋势的技术。安装合适的传感器可以获得故障的特征信号,通过信号反映故障产生原因。滚动轴承是机械中的易损元件,据统计旋转机械的故障有30%是由轴承引起的,它的好坏对机器的工作状态影响极大。轴承的缺陷会导致机器剧烈振动和产生噪声,甚至会引起设备的损坏。滚动轴承的振动可由于外部的振源引起,也可由于轴承本身的结构特点及缺陷引起。而随着科学技术不断发展和工业化程度的不断提高,机械设备精密程度、复杂程度及自动化程度不断提高,凭个人的感观经验对机械设备进行诊断己经远远不够,因此轴承的状态检测和故障诊断是十分必要的,已经成为机械设备故障诊断技术的重要内容。滚动轴承故障监测诊断方法有很多种,它们各具特点,其中振动信号法应用最广泛。本次实验就是采用振动信号法对滚动轴承故障实验平台的滚动轴承的故障信号进行分析。
1 绪论 (1) 2 轴承内圈故障特征频率 (2) 3 时域无量纲参数分析 (2) 3.1 时域波形 (2) 3.2 傅里叶变换运算分析故障 (3) 4通过自相关、互相关、功率谱运算分析故障 (4) 4.1 自相关分析 (4) 4.2 互相关运算分析故障 (5) 4.3功率谱密度 (6) 5 Haar小波分析 (7) 5.1小波分解 (7) 5.2 小波降噪 (9)
1 绪论 随着对滚动轴承的运动学、动力学的深入研究,对于轴承振动信号中的频率成分和轴承零件的几何尺寸及缺陷类型的关系有了比较清楚的了解,加之快速傅里叶变换技术的发展。开创了用频域分析方法来检测和诊断轴承故障的新领域。其中最具代表性的有对钢球共振频率的研究,对轴承圈自由共振频率的研究。本文主要着重于对滚动轴承内圈磨损的故障研究,主要研究方法为傅里叶变换,功率谱,自相关以及互相关,小波理论。 滚动轴承在运行过程中可能会因为各种原因出现故障,如安装不当、异物入侵、润滑不良、腐蚀和剥落等都会导致轴承出现故障。安装不当会导致轴承不对中,使得轴承在运行中,产生一种附加弯矩,给轴承增加附加载荷,形成附加激励,引起几组强烈振动,严重时会导致转子严重磨损、轴弯曲、联轴器和轴承断裂等严重后果。即使轴承安装正确,在长期的运行中,由于异物的入侵或则负荷的作用下,接触面会出现不同程度的金属剥落、裂痕等现象,进而导致旋转部件与故障区域接触时产生强烈振动。本次实验主要针对潜在危害很大的裂痕故障信号进行分析研究。滚动轴承在出现裂痕故障后,随着轴承的旋转,由于旋转部件与裂痕周期性的碰撞会产生周期性的冲击信号,且周期可以通过轴承结构计算得出。图1.1所示为滚动轴承基本结构。 图1.1 滚动轴承基本结构 d:滚动体直径 D:轴承节径(滚动体所在圆的直径) R:内圈直径 i R:外圈直径 o :接触角(滚动体受力方向与轴承径向平面的夹角) Z:滚动体个数
失效分析的思路和诊断
失效分析的思路与诊断 第二章失效分析的思路 第一节常用的几种失效分析思路 一、“撤大网”逐个因素排除法
二、以设备制造全过程为一系统进行分析 任何一个设备都要经历规划、设计、选材、机械加工(包括铸、锻、焊等工艺)、热处理、二次精加工(研磨、酸洗、电镀)和装配等制作工序,如果失效已确定纯属设备问题,还可对上述工序逐个进一步分析,包括以下容: 1.设计不当 (1)开孔位置不当造成应力集中; (2)缺口或凹倒角半径过小; (3)高应力区有缺口; (4)横截面改变太陡; (5)改变设计,没有相应地改变受力状况; (6)设计判据不足; (7)计算中出现过载荷; (8)焊缝选择位置不当,以及配合不适当等; (9)对使用条件的环境影响,未做适当考虑; (10)提高使用材料的受力级别; (11)刚性和韧性不适当; (12)材料品种选择错误; (13)选择标准不当; (14)材料性能数据不全; (15)材料韧脆转变温度过高; (16)对现场调查不充分,认识不足就投入设计; (17)与用户配合有差错。 2.材料、冶金缺陷 (1)成分不合格; (2)夹杂物含量及成分不合格; (3)织组不合格; (4)各种性能不合格; (5)各向异性不合格; (6)断口不合格; (7)冶金缺陷(缩孔、偏析等); (8)恶化变质; (9)混料。
3.锻造等热加工工艺缺陷 (1)折叠、夹砂、夹渣; (2)裂缝; (3)锻造鳞皮; (4)流线分布突变或破坏; (5)晶粒流变异常; (6)沿晶氧化(过烧); (7)氧化皮压入; (8)分层、疏松; (9)带状组织; (10)过热、烧裂; (11)外来金属夹杂物; (12)缩孔; (13)龟裂; (14)打磨裂纹; (15)皱纹。 4.机械加工缺陷 (1)未按图纸要求; (2)表面粗糙度不合格; (3)倒角尖锐; (4)磨削裂纹或过烧; (5)裂纹; (6)划伤、刀痕; (7)毛刺; (8)局部过热; (9)矫直不当。 5.铸造缺陷 (1)金属突出; (2)孔穴; (3)疏松; (4)不连贯裂纹; (5)表面缺陷; (6)浇注不完全; (7)尺寸和形状不正确; (8)夹砂、夹渣; (9)组织反常; (10)型芯撑、冷铁。
故障诊断分析方法-结课论文
故障诊断分析方法比较 摘要:小波变换作为信号处理的手段,逐渐被越来越多领域的理论工作者和工 程技术人员重视和应用。在机械系统和电气系统中,故障时常发生,为了诊断 系统是否故障,小波分析是很好的方法。小波分析的方法很多,小波的选择也 很多类,为了研究哪种小波分析方法更加适合于故障检测。论文将通过一个例 子来分别采用功率谱、多分辨小波分析和小波包三种方法进行突发性故障诊断,来研究各自的分析特点。并总结在故障发生时,一个更加好的分析方法。 关键词:故障功率谱多分辨分析小波包分析 正文: 在对机械设备进行故障检测时,通常采用对振动信号进行频谱分析找出奇 异点的方法来实现设备监测。傅里叶变换是频谱分析的主要工具,其方法是研 究函数在傅里叶变换后的衰减以推断函数是否具有奇异性及奇异性的大小,但 傅里叶分析只能确定一个函数奇异性的整体性质而难以确定奇异点空间的位置 分布情况,这一局限性导致了频谱分析不能精确的确定信号的奇异性特点,给 进一步分析信号的规律带来了一定的障碍。 而在傅里叶基础上发展而来的功率谱可以识别不同信号的故障信号。将正 常信号的功率谱与运行过程中不断连续收集的信号功率谱进行对比,功率谱异 常就表示机械系统有故障,不同类型的故障会有不同类型的频谱特征,从故障 信号的功率谱中可以识别故障的类型。 然而利用传统的频谱分析方法只能从频谱图上了解故障信号的所包含的频 率成分,而无法确定具体的频率成分的震动形式。无法对具体的频率成分进行 分析,难以直接描述机械的状态。小波分析是近十年发展起来的一门适用于时 变信号分析的新兴工具,它可以把时域信号变换到时间—尺度域中,在不同尺 度下观察不同的局部化特性。在信号突变时,其小波变换后的系数具有模量极 大值,可通过对模的极大值点的检测来确定故障发生的时间点。在从小波基础 上发展的小波包,对各个子小波空间做出更加细致的分解,其对应的频带被进 一步分解,这使得时—频分析能聚焦于任意的细节,在故障诊断时,可从细节 上分析故障。 很多工作系统正常工作时,工作输出点的采样信号是蠕变信号,当由于多 种原因系统系统故障时,输出信号将产生一突变信号(主要表现在幅度和频率 的变化),信号的突变时刻被称为信号的奇异点。这些奇异点数值包含有重要 的故障信息,因此,对突变信号进行检测和处理,是故障诊断的关键。 因此,本文从功率谱、多分辨分析分析和小波包三种方法进行蠕变信号突发性 故障诊断,并比较总结它们的特点。 实例:由于日常机械中很多振动信号都是由不通频率的正弦余弦波组成的,于 是这里选择的原始信号采用的是单一频率正弦波的形式。为了研究上述三种分 析方法,并且由于还未在先研究阶段中未得到研究机械的信号,为了简化分析
常用简易的设备故障诊断方法
常用简易的设备故障诊 断方法 Document number:PBGCG-0857-BTDO-0089-PTT1998
常用简易的设备故障诊断方法 常用的简易状态监测方法主要有听诊法、触测法和观察法等。 1、听诊法 设备正常运转时,伴随发生的声响总是具有一定的音律和节奏。只要熟悉和掌握这些正常的音律和节奏,通过人的听觉功能就能对比出设备是否出现了重、杂、怪、乱的异常噪声,判断设备内部出现的松动、撞击、不平衡等隐患。用手锤敲打零件,听其是否发生破裂杂声,可判断有无裂纹产生,用听诊法对滚动轴承工作状态进行监测的常用工具是木柄螺丝刀,也可以使用外径为φ20mm左右的硬塑料管。 (1)滚动轴承正常工作状态的声响特点 滚动轴承处于正常工作状态时,运转平稳、轻快、无停滞现象,发出的声响和谐而无杂音,可听到均匀而连续的“哗哗”声,或者较低的“轰轰”声。噪声的强度不大。异常声响所反映的轴承故障锥入度大一点的新润滑脂。 (2)轴承在连续的“哗哗”声中发出均匀的周期性的“嗬罗”声。这种声音是由于滚动体和内外圈滚道出现伤痕、沟槽、锈蚀斑而引起的。声响的周期与轴承的转速成正比。应对轴承进行更换。 (3)轴承发出不连续的“梗梗”声。这种声音是由于保持架或者内外圈破裂而引起的。必须立即停机更换轴承。 (4)轴承发出不规律、不均匀“嚓嚓”声。这种声音是由于轴承内落入铁屑、砂粒等杂质而引起的。声响强度较小,与转速没有联系。应对轴承进行清洗,重新加脂或换油。
(5)轴承发出连续而不规则的“沙沙”声。这种声音一般与轴承的内圈与轴配合过松或者外圈与轴承孔配合过松有关系,声响强度较大。应对轴承的配合关系进行检查,发现问题及时修理。 (6)轴承发出连续刺耳啸叫声。这种声音是由于轴承润滑不良,缺油造成了干摩擦,或者滚动体局部接触过紧,如内外圈滚道偏斜,轴承内外圈配合过紧等情况而引起的。应及时对轴承进行检查找出问题,对症处理。 电子听诊器是一种振动加速度传感器。它将设备振动状况转换成电信号并进行放大,工人用耳机监听运行设备的振动声响,以实现对声音的定性测量。通过测量同一测点、不同时期、相同转速、相同工况下的信号,并进行对比,来判断设备是否存在故障。当耳机出现清脆尖细的噪声时,说明振动频率较高,一般是尺寸相对较小的、强度相对较高的零件发生局部缺陷或微小裂纹。当耳机传出混浊低沉的噪声时,说明振动频率较低,一般是尺寸相对较大的、强度相对较低的零件发生较大的裂纹或缺陷。当耳机传出的噪声比平时增强时,说明故障正在发展,声音越大,故障越严重。当耳机传出的噪声是杂乱无规律地间歇出现时,说明有零件或部件发生了松动。 2、触测法 用人手的触觉可以监测设备的温度、振动及间隙的变化情况。人手上的神经纤维对温度比较敏感,可以比较准确地分辨出80℃以内的温度。当机件温度在0℃左右时,手感冰凉,若触摸时间较长会产生刺骨痛感。10℃左右时,手感较凉,但一般能忍受。20℃左右时,手感稍凉,随着接触时间延长,手感渐温。30℃左右时,手感微温,有舒适感。40℃左右时,手感较热,有微烫感觉。50℃左右时,手感较烫,若用掌心按的时间较长,会有汗感。60℃左右
故障诊断理论方法综述
故障诊断理论方法综述 故障诊断的主要任务有:故障检测、故障类型判断、故障定位及故障恢复等。其中:故障检测是指与系统建立连接后,周期性地向下位机发送检测信号,通过接收的响应数据帧,判断系统是否产生故障;故障类型判断就是系统在检测出故障之后,通过分析原因,判断出系统故障的类型;故障定位是在前两部的基础之上,细化故障种类,诊断出系统具体故障部位和故障原因,为故障恢复做准备;故障恢复是整个故障诊断过程中最后也是最重要的一个环节,需要根据故障原因,采取不同的措施,对系统故障进行恢复一、基于解析模型的方法 基于解析模型的故障诊断方法主要是通过构造观测器估计系统输出,然后将它与输出的测量值作比较从中取得故障信息。它还可进一步分为基于状态估计的方法和基于参数估计的方法,前者从真实系统的输出与状态观测器或者卡尔曼滤波器的输出比较形成残差,然后从残差中提取故障特征进而实行故障诊断;后者由机理分析确定系统的模型参数和物理元器件之间的关系方程,由实时辨识求得系统的实际模型参数,然后求解实际的物理元器件参数,与标称值比较而确定系统是否发生故障及故障的程度。基于解析模型的故障诊断方法都要求建立系统精确的数学模型,但随着现代设备的不断大型化、复杂化和非线性化,往往很难或者无法建立系统精确的数学模型,从而大大限制了基于解析模型的故障诊断方法的推广和应用。 二、基于信号处理的方法 当可以得到被控测对象的输入输出信号,但很难建立被控对象的解析数学模型时,可采用基于信号处理的方法。基于信号处理的方法是一种传统的故障诊断技术,通常利用信号模型,如相关函数、频谱、自回归滑动平均、小波变换等,直接分析可测信号,提取诸如方差、幅值、频率等特征值,识别和评价机械设备所处的状态。基于信号处理的方法又分为基于可测值或其变化趋势值检查的方法和基于可测信号处理的故障诊断方法等。基于可测值或其变化趋势值检查的方法根据系统的直接可测的输入输出信号及其变化趋势来进行故障诊断,当系统的输入输出信号或者变化超出允许的范围时,即认为系统发生了故障,根据异常的信号来判定故障的性质和发生的部位。基于可测信号处理的故障诊断方法利用系统的输出信号状态与一定故障源之间的相关性来判定和定位故障,具体有频谱分析方法等。 三、基于知识的方法 在解决实际的故障诊断问题时,经验丰富的专家进行故障诊断并不都是采用严格的数学算法从一串串计算结果中来查找问题。对于一个结构复杂的系统,当其运行过程发生故障时,人们容易获得的往往是一些涉及故障征兆的描述性知识以及各故障源与故障征兆之间关联性的知识。尽管这些知识大多是定性的而非定量的,但对准确分析故障能起到重要的作用。经验丰富的专家就是使用长期积累起来的这类经验知识,快速直接实现对系统故障的诊断。利用知识,通过符号推理的方法进行故障诊断,这是故障诊断技术的又一个分支——基于知识的故障诊断。基于知识的故障诊断是目前研究和应用的热点,国内外学者提出了很多方法。由于领域专家在基于知识的故障诊断中扮演重要角色,因此基于知识的故障诊断系统又称为故障诊断专家系统。如图1.1
各类材料失效分析方法
各类材料失效分析方法 Via 常州精密钢管博客 失效分析是一门发展中的新兴学科,近年开始从军工向普通企业普及,它一般根据失效模式和现象,通过分析和验证,模拟重现失效的现象,找出失效的原因,挖掘出失效的机理的活动。在提高产品质量,技术开发、改进,产品修复及仲裁失效事故等方面具有很强的实际意义。 失效分析流程 图1 失效分析流程 各种材料失效分析检测方法 1 PCB/PCBA失效分析 PCB作为各种元器件的载体与电路信号传输的枢纽已经成为电子信息产品的最为重要而关键的部分,其质量的好坏与可靠性水平决定了整机设备的质量与可靠性。
图2 PCB/PCBA 失效模爆板、分层、短路、起泡,焊接不良,腐蚀迁移等。 常用手段· 无损检测: 外观检查,X射线透视检测,三维CT检测,C-SAM检测,红外热成像表面元素分析: 扫描电镜及能谱分析(SEM/EDS) 显微红外分析(FTIR) 俄歇电子能谱分析(AES) X射线光电子能谱分析(X PS) 二次离子质谱分析(TOF-SIMS)· 热分析:· 差示扫描量热法(DSC) 热机械分析(TMA) 热重分析(TGA) 动态热机械分析(DMA) 导热系数(稳态热流法、激光散射法) 电性能测试: · 击穿电压、耐电压、介电常数、电迁移· 破坏性能测试: 染色及渗透检测
2 电子元器件失效分析 电子元器件技术的快速发展和可靠性的提高奠定了现代电子装备的基础,元器件可靠性工作的根本任务是提高元器件的可靠性。 图3 电子元器件 失效模式 开路,短路,漏电,功能失效,电参数漂移,非稳定失效等 常用手段· 电测:连接性测试电参数测试功能测试 无损检测: 开封技术(机械开封、化学开封、激光开封) 去钝化层技术(化学腐蚀去钝化层、等离子腐蚀去钝化层、机械研磨去钝化层) 微区分析技术(FIB、CP) 制样技术: 开封技术(机械开封、化学开封、激光开封) 去钝化层技术(化学腐蚀去钝化层、等离子腐蚀去钝化层、机械研磨去钝化层) 微区分析技术(FIB、CP) 显微形貌分析: 光学显微分析技术 扫描电子显微镜二次电子像技术 表面元素分析: 扫描电镜及能谱分析(SEM/EDS) 俄歇电子能谱分析(AES)
服务器维修故障诊断思路大全
前言: 相对PC机而言服务器出故障的机率是小多了,但是它的故障给企业也带来了一些影响。作为服务器工程师除要有服务器基础知识以外,还需要具备服务器故障的诊断思路,这样才能最快速的解决问题也可以减少故障停机时间。 本文并不是针对某个厂家服务器故障完全手册,而是根据个人经验总结出来的一些经验思路还有一些总结案例。按照下面思路和方法基本上能够解决目前服务器更换式维修的大多数问题。而且里面的一些操作风险性也不是很大,因为服务器本身就是坏的,最坏的情况下就是它一点都不能工作了呗,(主要确认是否有数据,数据无价啊)而且现在很多厂商都有自己的客服电话关于产品问题打个电话也很方便,所以安心做啦 当然如果服务器在保修期内就打电话让售后工程师上门服务,毕竟顾客就是上帝嘛,但是如果上帝比较着急使用,一般小故障自己解决一下就好了,因为一般报修最快都是第二天(大客户如银行等除外,一般当天还得是晚上才能停机解决) 目录: 一、服务器常见故障分类 二、服务器常见故障现象及其对应排错方法 三、服务器排错基本原则 四、服务器故障需要收集哪些信息 五、服务器硬件故障排错实例 六、服务器软件故障排错实例 七、服务器常见内存故障现象 一、服务器常见故障类型分类: A. 开机无显示 B. 加电BIOS自检阶段故障 C. 系统和软件安装阶段故障和现象 D. 操作系统启动失败 E. 系统运行阶段故障 二、服务器常见故障现象及其对应的排除方法
A.服务器开机无显示(加电无显示和不加电无显示) 1. 检查供电环境 2. 检查电源和故障指示灯(故障指示灯状态,目前很多厂商的服务器都有故障指示灯,或故障诊断卡等。) 3. 按下电源开关时,键盘指示灯是否亮、风扇是否全部转动 4. 是否更换过显示器,尝试更换另外一台显示器 5. 插拔内存,用橡皮擦擦拭一下金手指,如果在故障之前有增加内存,去掉增加的内存尝试 6. 是否添加了CPU,如果有增加CPU尝试去掉 7. 去掉增加的第三方I/O卡包括Raid卡等 8. ClearCMOS (记得使用跳线来清除,尽量不要直接拔电池,每款服务器清除跳线位置不一致,具体找不到电话联系一下厂商客服) 9. 尝试更换主板、内存等主要部件 10.清除静电,将电源线等外插在服务器上的线缆全部拔掉,然后轻按开机键几下 B.加电BIOS自检报错 1. 根据BIOS自检报错信息提示 2. 查看是否外插了第三方的卡或者添加部件,如果有还原基本配置重启 3. 做最小化测试 4. 尝试清除CMOS 5. 看能否正常进入BIOS C. 系统安装阶段故障和现象 1.查看服务器支持操作系统的兼容版本(从厂商能查到兼容性列表) 2.系统安装蓝屏(对蓝屏故障代码诊断) 3.安装在分区格式化的时候找不到硬盘 (阵列驱动没有安装或者没有配置阵列,可以尝试适应引导光盘安装) 4.大于2T的硬盘式应该如何分区(必须使用阵列卡才能实现或者有外插识别卡) (使用阵列卡配置阵列分成一个小于2T的空间,一个大于2T的空间,然后将系统安装在小于2T的上面,安装好系统后在使用GPT方式分区即可) 5.安装过程是死机 (检查兼容性列表---查看硬盘接口选择是否正确---阵列驱动安装是否正确---尝试最小化配置安装检查是否为内存和CPU等问题) 6.引导光盘安装失败
失效分析
失效分析 第三章失效分析的基本方法 1.按照失效件制造的全过程及使用条件的分析方法:(1)审查设计(2)材料分析(3)加工制 造缺陷分析(4)使用及维护情况分析 2.系统工程的分析思路方法:(1)失效系统工程分析法的类型(2)故障树分析法(3)模糊故 障树分析及应用 3.失效分析的程序:调查失效时间的现场;收集背景材料,深入研究分析,综合归纳所有信息 并提出初步结论;重现性试验或证明试验,确定失效原因并提出建议措施;最后写出分析报告等内容。 4.失效分析的步骤:(1)现场调查①保护现场②查明事故发生的时间、地点及失效过程③收集 残骸碎片,标出相对位置,保护好断口④选取进一步分析的试样,并注明位置及取样方法⑤询问目击者及相关有关人员,了解有关情况⑥写出现场调查报告(2)收集背景材料①设备的自然情况,包括设备名称,出厂及使用日期,设计参数及功能要求等②设备的运行记录,要特别注意载荷及其波动,温度变化,腐蚀介质等③设备的维修历史情况④设备的失效历史情况⑤设计图样及说明书、装配程序说明书、使用维护说明书等⑥材料选择及其依据⑦设备主要零部件的生产流程⑧设备服役前的经历,包括装配、包装、运输、储存、安装和调试等阶段⑨质量检验报告及有关的规范和标准。(3)技术参量复验①材料的化学成分②材料的金相组织和硬度及其分布③常规力学性能④主要零部件的几何参量及装配间隙(4)深入分析研究(5)综合分析归纳,推理判断提出初步结论(6)重现性试验或证明试验 5.断口的处理:①在干燥大气中断裂的新鲜断口,应立即放到干燥器内或真空室内保存,以防 止锈蚀,并应注意防止手指污染断口及损伤断口表面;对于在现场一时不能取样的零件尤其是断口,应采取有效的保护,防止零件或断口的二次污染或锈蚀,尽可能地将断裂件移到安全的地方,必要时可采取油脂封涂的办法保护断口。②对于断后被油污染的断口,要进行仔细清洗。③在潮湿大气中锈蚀的断口,可先用稀盐酸水溶液去除锈蚀氧化物,然后用清水冲洗,再用无水酒精冲洗并吹干。④在腐蚀环境中断裂的断口,在断口表面通常覆盖一层腐蚀产物,这层腐蚀产物对分析致断原因往往是非常重要的,因而不能轻易地将其去掉。 6.断口分析的具体任务:①确定断裂的宏观性质,是延性断裂还是脆性断裂或疲劳断裂等。② 确定断口的宏观形貌,是纤维状断口还是结晶状断口,有无放射线花样及有无剪切唇等。③查找裂纹源区的位置及数量,裂纹源的所在位置是在表面、次表面还是在内部,裂纹源是单个还是多个,在存在多个裂纹源区的情况下,它们产生的先后顺序是怎样的等。④确定断口的形成过程,裂纹是从何处产生的,裂纹向何处扩展,扩展的速度如何等。⑤确定断裂的微观机理,是解理型、准解理型还是微孔型,是沿晶型还是穿晶型等。⑥确定断口表面产物的性质,断口上有无腐蚀产物,何种产物,该产物是否参与了断裂过程等。 7.断口的宏观分析(1)最初断裂件的宏观判断①整机残骸的失效分析;②多个同类零件损坏的 失效分析;③同一个零件上相同部位的多处发生破断时的分析。(2)主断面(主裂纹)的宏观判断①利用碎片拼凑法确定主断面;②按照“T”形汇合法确定主断面或主裂纹;③按照裂纹
失效分析思路_张峥
理化检验-物理分册PTCA(PART:A PH YS.T EST.)2005年第41卷3专题讲座 失效分析思路 FAILURE ANA LYSIS M ETH ODOLOGY 张峥 (北京航空航天大学材料学院,北京100083) 中图分类号:T B303文献标识码:E文章编号:1001-4012(2005)03-0158-04 失效分析在生产建设中极其重要,失效分析的限期往往要求很短,分析结论要正确无误,改进措施要切实可行。导致零部件或系统失效的因素往往很多,加之零部件相互间的受力情况很复杂,如果再考虑外界条件的影响,这就使失效分析的任务更加繁重。此外,大多数失效分析的关键性试样十分有限,只容许一次取样、一次观察和测量。在分析程序上走错一步,可能导致整个分析的失败。由此可见,如果分析之前没有一条正确的分析思路,要能如期得出正确的结论几乎是不可能的。 有了正确的分析思路,才能制定正确的分析程序。大的事故需要很多分析人员按照分工同时进行,做到有条不紊,不走弯路,不浪费测试费用。所以从经济角度也要求有正确的分析思路。 1失效分析思路的内涵 世界上任何事物都是可以被认识的,没有不可以认识的东西,只存在尚未能够认识的东西,机械失效也不例外。实际上失效总有一个或长或短的变化发展过程,机械的失效过程实质上是材料的累积损伤过程,即材料发生物理的和化学的变化。而整个过程的演变是有条件的、有规律的,也就是说有原因的。因此,机械失效的客观规律性是整个失效分析的理论基础,也是失效分析思路的理论依据。 失效分析思路是指导失效分析全过程的思维路线,是在思想中以机械失效的规律(即宏观表象特征和微观过程机理)为理论依据,把通过调查、观察和实验获得的失效信息(失效对象、失效现象、失效环 收稿日期:2005-02-07 作者简介:张峥(1965-),男,教授,博士生导师。境统称为失效信息)分别加以考察,然后有机结合起来作为一个统一整体综合考察,以获取的客观事实为证据,全面应用推理的方法,来判断失效事件的失效模式,并推断失效原因。因此,失效分析思路在整个失效分析过程中一脉相承、前后呼应,自成思考体系,把失效分析的指导思路、推理方法、程序、步骤、技巧有机地融为一体,从而达到失效分析的根本目的。 在科学的分析思路指导下,才能制定出正确的分析程序;机械的失效往往是多种原因造成的,即一果多因,常常需要正确的失效分析思路的指导;对于复杂的机械失效,涉及面广,任务艰巨,更需要正确的失效分析思路,以最小代价来获取较科学合理的分析结论。总之,掌握并运用正确的分析思路,才可能对失效事件有本质的认识,减少失效分析工作中的盲目性、片面性和主观随意性,大大提高工作的效率和质量。因此,失效分析思路不仅是失效分析学科的重要组成部分,而且是失效分析的灵魂。 失效分析是从结果求原因的逆向认识失效本质的过程,结果和原因具有双重性,因此,失效分析可以从原因入手,也可以从结果入手,也可以从失效的某个过程入手,如/顺藤摸瓜0,即以失效过程中间状态的现象为原因,推断过程进一步发展的结果,直至过程的终点结果;/顺藤找根0,即以失效过程中间状态的现象为结果,推断该过程退一步的原因,直至过程起始状态的直接原因;/顺瓜摸藤0,即从过程中的终点结果出发,不断由过程的结果推断其原因;/顺根摸藤0,即从过程起始状态的原因出发,不断由过程的原因推断其结果。再如/顺瓜摸藤+顺藤找根0 /顺根摸藤+顺藤摸瓜0/顺藤摸瓜+顺藤找根0等。 # 158 #
失效分析常见思路
失效分析在生产建设中极其重要,失效分析的限期往往要求很短,分析结论要正确无误,改进措施要切实可行。导致零部件或系统失效的因素往往很多,加之零部件相互间的受力情况很复杂,如果再考虑外界条件的影响,这就使失效分析的任务更加繁重。此外,大多数失效分析的关键性试样十分有限,只容许一次取样、一次观察和测量。在分析程序上走错一步,可能导致整个分析的失败。由此可见,如果分析之前没有一条正确的分析思路,要能如期得出正确的结论几乎是不可能的。 有了正确的分析思路,才能制定正确的分析程序。大的事故需要很多分析人员按照分工同时进行,做到有条不紊,不走弯路,不浪费测试费用。所以从经济角度也要求有正确的分析思路。 1 失效分析思路的内涵 世界上任何事物都是可以被认识的,没有不可以认识的东西,只存在尚未能够认识的东西,机械失效也不例外。实际上失效总有一个或长或短的变化发展过程,机械的失效过程实质上是材料的累积损伤过程,即材料发生物理的和化学的变化。而整个过程的演变是有条件的、有规律的,也就是说有原因的。因此,机械失效的客观规律性是整个失效分析的理论基础,也是失效分析思路的理论依据。 失效分析思路是指导失效分析全过程的思维路线,是在思想中以机械失效的规律(即宏观表 象特征和微观过程机理)为理论依据,把通过调查、观察和实验获得的失效信息(失效对象、失效现象、失效环境统称为失效信息)分别加以考察,然后有机结合起来作为一个统一整体综合考察,以获取的客观事实为证据,全面应用推理的方法,来判断失效事件的失效模式,并推断失效原因。因此,失效分析思路在整个失效分析过程中一脉相承、前后呼应,自成思考体系,把失效分析的指导思路、推理方法、程序、步骤、技巧有机地融为一体,从而达到失效分析的根本目的。 在科学的分析思路指导下,才能制定出正确的分析程序;机械的失效往往是多种原因造成的,即一果多因,常常需要正确的失效分析思路的指导;对于复杂的机械失效,涉及面广,任务艰巨,更需要正确的失效分析思路,以最小代价来获取较科学合理的分析结论。总之,掌握并运用正确的分析思路,才可能对失效事件有本质的认识,减少失效分析工作中的盲目性、片面性和主观随意性,大大提高工作的效率和质量。因此,失效分析思路不仅是失效分析学科的重要组成部分,而且是失效分析的灵魂。 失效分析是从结果求原因的逆向认识失效本质的过程,结果和原因具有双重性,因此,失效分析可以从原因入手,也可以从结果入手,也可以从失效的某个过程入手,如“顺藤摸瓜”,即以失
基于噪声分析的机械故障诊断方法研究
基于噪声分析的机械故障诊断方法研究 摘要 基于噪声分析的机械故障诊断方法可以非接触地获得机械信号,适用于众多不便于使用振动传感器的场合,如某些高温、高腐蚀环境,是一种常用而有效地故障诊断方法。但在实际应用中,由于不相干噪声和环境噪声的影响,我们需要的待测信号往往被淹没在这些混合噪声中,信号的信噪比较低。 盲源分离作为数字信号处理领域的新兴技术,能利用观测信号恢复或提取独立的各个机械信号,在通讯、雷达信号处理、图像处理等众多领域具有重要的实用价值及发展前景,已经成为神经网络学界和信号处理学界的热点研究课题之一。 本文分析总结了盲源分离技术的相关研究现状,对盲源分离的原理、算法、相关应用作了探讨和研究。并就汽轮机噪声问题运用了盲源分离技术进行机械故障诊断,试验表明,该方法能将我们需要的故障信号从混合信号中分离出来,成功实现汽轮机部件的故障诊断。 关键词:声信号,机械故障诊断,独立分量分析 Investigation of Mechanical Fault Diagnosis Based on Noise Analysis Abstract You can obtain a non-contact method of mechanical fault diagnosis based on noise analysis of mechanical signals , not suitable for many occasions to facilitate the use of vibration sensors , such as certain high temperature , highly corrosive environment , is a common and effective fault diagnosis method . However, in practice , the effects of noise and extraneous ambient noise , the signal under test often need to be submerged in the mixed noise , lower signal to noise ratio . Blind source separation as an emerging field of digital signal processing technology to take advantage of the observed signal recovery or extraction of various mechanical signals independently in many communications, radar signal processing , image processing has important practical value and development prospects , has become a neural network one of the hot research topic in academic circles and signal processing . In this paper summarizes the research status of blind source separation techniques , the principles of blind source separation algorithms, related applications and research were discussed . Turbine noise problems and to use the blind source separation techniques for mechanical fault diagnosis, tests showed that the method we need fault signal can be separated from the mixed signal , fault diagnosis of steam turbine components successfully . Key Words:Mechanical Fault Diagnosis,Independent Component Analysis
失效分析的思路与诊断
失效分析的思路与诊断 Prepared on 22 November 2020
失效分析的思路与诊断 第二章失效分析的思路 第一节常用的几种失效分析思路 一、“撤大网”逐个因素排除法
任何一个设备都要经历规划、设计、选材、机械加工(包括铸、锻、焊等工艺)、热处理、二次精加工(研磨、酸洗、电镀)和装配等制作工序,如果失效已确定纯属设备问题,还可对上述工序逐个进一步分析,包括以下内容: 1.设计不当 (1)开孔位置不当造成应力集中;
(2)缺口或凹倒角半径过小; (3)高应力区有缺口; (4)横截面改变太陡; (5)改变设计,没有相应地改变受力状况; (6)设计判据不足; (7)计算中出现过载荷; (8)焊缝选择位置不当,以及配合不适当等; (9)对使用条件的环境影响,未做适当考虑; (10)提高使用材料的受力级别; (11)刚性和韧性不适当; (12)材料品种选择错误; (13)选择标准不当; (14)材料性能数据不全; (15)材料韧脆转变温度过高; (16)对现场调查不充分,认识不足就投入设计; (17)与用户配合有差错。 2.材料、冶金缺陷 (1)成分不合格; (2)夹杂物含量及成分不合格; (3)织组不合格; (4)各种性能不合格; (5)各向异性不合格; (6)断口不合格; (7)冶金缺陷(缩孔、偏析等); (8)恶化变质; (9)混料。 3.锻造等热加工工艺缺陷 (1)折叠、夹砂、夹渣; (2)裂缝; (3)锻造鳞皮; (4)流线分布突变或破坏; (5)晶粒流变异常; (6)沿晶氧化(过烧); (7)氧化皮压入; (8)分层、疏松; (9)带状组织; (10)过热、烧裂; (11)外来金属夹杂物; (12)缩孔; (13)龟裂; (14)打磨裂纹; (15)皱纹。 4.机械加工缺陷 (1)未按图纸要求; (2)表面粗糙度不合格;
失效分析的思路与诊断
失效分析的思路与诊断失效分析思路 第一节常用几种失效分析思路 一、“撤大网”逐个因素排除法 表2-1 事故管理责任
二、以设备制造全过程为一系统进行分析 任何一个设备都要经历规划、设计、选材、机械加工(包括铸、锻、焊等工艺)、热处理、二次精加工(研磨、酸洗、电镀)和装配等制作工序,如果失效已确定纯属设备问题,还可对上述工序逐个进一步分析,包括以下内容: 设计不当 开孔位置不当造成应力集中; 缺口或凹倒角半径过小; 高应力区有缺口; 横截面改变太陡; 改变设计,没有相应地改变受力状况; 设计判据不足; 计算中出现过载荷; 焊缝选择位置不当,以及配合不适当等; 对使用条件环境影响,未做适当考虑; 提高使用材料受力级别; 刚性和韧性不适当; 材料品种选择错误; 选择标准不当; 材料性能数据不全; 材料韧脆转变温度过高; 对现场调查不充分,认识不足就投入设计; 与用户配合有差错。 材料、冶金缺陷 成分不合格; 夹杂物含量及成分不合格; 织组不合格;
各种性能不合格; 各向异性不合格; 断口不合格; 冶金缺陷(缩孔、偏析等);恶化变质; 混料。
锻造等热加工工艺缺陷折叠、夹砂、夹渣;裂缝; 锻造鳞皮; 流线分布突变或破坏;晶粒流变异常; 沿晶氧化(过烧);氧化皮压入; 分层、疏松; 带状组织; 过热、烧裂; 外来金属夹杂物; 缩孔; 龟裂; 打磨裂纹; 皱纹。 机械加工缺陷 未按图纸要求; 表面粗糙度不合格;倒角尖锐; 磨削裂纹或过烧; 裂纹; 划伤、刀痕; 毛刺; 局部过热; 矫直不当。
铸造缺陷 金属突出; 孔穴; 疏松; 不连贯裂纹; 表面缺陷; 浇注不完全; 尺寸和形状不正确;夹砂、夹渣; 组织反常; 型芯撑、内冷铁。
机械零部件失效分析的方法和步骤
第一章机械零部件失效分析的方法和步骤 1、失效分析与机械设计的关系 机械产品丧失其规定功能的事件称为机械产品的失效。失效常发生在产品使用过程中,也发生在试运转过程中,甚至可能发生在使用前的存放过程中。以同类产品使用寿命期内失效事件总数为基数的统计数据表明,寿命早期失效率较高,晚期的失效率也较高,而中期较长时间的失效率很低,典型的失效率曲线呈浴盘状曲线。机械产品的早期失效案例尤其值得重视。它们常常暴露出设计和制造工艺中各种的欠缺和不当,及时的失效分析有利于改进和提高产品的质量。晚期失效分析反应出机械产品耗损期的诸多病端失效分析有利于提高产品的使用寿命。 针对机械产品失效案例进行的技术和管理活动称为失效分析。失效分析的主要内容是查明失效的具体原因(失效诊断)和提出预防和补救措施(失效对策)。失效分析的主要目标是防止同类失效事件的再次发生和提高产品质量。 机械产品的恶性失效事故造成重大经济损失,甚至人员伤亡,例如飞机坠落,大型机组毁坏,大型压力容器爆炸,这种特大事故发生后,通常开展大规模的调查活动。如果确认或怀疑事故是由机械零部件失效而造成,就会进行一系列失效分析活动,包括各种试验和研究工作。由于领导部门重视,投入较大,研究工作深入,常能达到预期目标。 中、小型失效事件或事故,也应该进行相应的失效分析活动。而各单位和厂家对于所发生失效事件的重视程度有很大的差异。有一些厂家极重视其产品的失效案例,买回典型的失效零部件,进行认真分析研究。许多设计师经常调查所设计机械设备使用中失效情况,作为改善设计的重要依据。“失败乃成功之母”,概略地说明了失效分析与机械设计间的关系。2、机械产品失效分类 机械产品失效分类有两种主要系统:按照失效类型分类;按照失效原因分类。 机械产品失效类型有五大类:变形、断裂、腐蚀、磨损和老化。还可以进一步细分为更多的类型,断裂失效可分为塑性断裂、脆性断裂、环境促进断裂和高温断裂。还有一些复合的失效类型,例如微动腐蚀疲劳是磨损、化学腐蚀和疲劳断裂的综合。 机械产品失效原因分为四大类:设计不当、制造工艺不当、材料冶金缺陷和使用操作失误。每一类中都有其具体原因,例如制造工艺不当可能涉及切削加工、热处理、电镀或装配的具体工艺。确定失效原因是一项复杂的工作,涉及的学科门类宽广;当机械设备毁坏严重时,查找证据困难;失效原因认定涉及到事故责任单位和责任,经常发生争议和互相推诿。失效分析是依据试验结果和证据作出结论,失效分析工作者必须坚持客观性和公正性。 上述四类失效原因也可分为两类。前三类原因都与机械产品品质有关,由机械设计和制造单位负责,简称为机械失效。操作原因造成的失效,一般与产品品质无直接因果关系,由产品的使用单位负责。 对于各类机械产品的失效原因,有关领导部门或研究单位会发布一定时期内各类失效原因的统计数据,可供参考。例如:美国空军发布的一项3824次飞机失效事件统计时,操作原因占41%,机械失效约占43%,气象原因占3%,不明原因占13%。 3、失效分析的步骤 失效分析的实施步骤旨在保证这项活动顺利的进行和完成。下面推荐通用的失效分析实施步骤,可供参考。由于每个失效事件的重要程度和规模大小不同,对失效分析的要求和步骤也会有所不同。 3.1 收集背景资料和侦查失效现场 失效现场必须注意保护,等待有关人员进行侦查。失效现场的一切证据应该维持原状,完整无缺和真实不伪,这是保证失效分析顺利进行的先决条件。对于公路和铁路事件,由于要保持交通顺畅需要采取一定措施,但是保护失效现场的原则仍需执行。
概括分析和故障诊断方法的过程监控
概括分析和故障诊断方法的过程监控 Carlos F. Alcala, S. Joe Qin? 化学工程、材料科学的Mork Family部门,电气工程的Ming Hsieh 部门,南加州大学,美国,洛杉矶,CA90089 文章信息 文章历史: 2011年二月24日网上可用 故障诊断 摘要 在过程监控,一些诊断方法已用于故障诊断。这些方法从不同的背景和考虑演变而来。在本文中,五个现有诊断方法被总结和分析。结果表明,它们能被统一成三种一般方法,使得原有的诊断方法成为普遍问题的特殊情况。同时,一种新形式的相对分配被提出。一项诊断能力的分析表明,一些诊断方法不保证正确的诊断,即使是简单的传感器故障和大的量级。对于故障的故障等级,蒙特卡罗模拟被应用与比较诊断方法的性能。 1、介绍 过程监控是工业用的检测和诊断的反常行为的过程。多元统计方法和基于模型方法用于过程的监控。在统计方法是一种很常见的用于工业的方法是主成分分析(PCA)【11、18、19】。利用主成分分析法(PCA)隔开测量空间分为主成分子空间(PCS)和残子空间(RS)。故障检测利
用故障检测指标。当故障检测指标之一超出它的控制限度,故障就被发现。断层被发现后,有必要对其诊断原因。有几种方法进行故障诊断。其中的一些方法检查一个故障检测指标变量的分配,利用的是这样一个观点:作分配的变量会有高值。被提出的分析分配方法包括了彻底分解的分配(CDC)、部分分解的分配(PDC)、斜交的分配(DC)、基于重建的分配(RBC),和基于角度的方法(ABC)。表1显示了诊断方法,提出他们的作者和他们被用于的评价指标。由此可见,一些诊断方法并没有被提出用于所有的故障检测的指标。此外, Dunia et al. [6]建议对于关系到RBC的故障诊断,用一种重建索引。但是,尚不清楚,是否这些诊断方法是独立的,哪一种方法会优于某一特定的检测指标。 对故障诊断的必然要求是尽可能多地避免误诊。虽然分配计划作为故障诊断方法被广泛地应用, 但直到最近才给出了诊断能力的不严谨分析[1,2]。分配平面图主要在故障情况下计算变量分配,挑选出一番大分配变量作为故障的可能原因。因为这个想法,一个定义明确的分配分析需要有以下可取的性能。 1、当没有缺点的存在时,所有可变分配应该有显著的相同的意思。 当故障存在时,这将建立一个水平基准用来比较分配; 2、如果错误主要归功于一个变量,那个变量的分配应该是最大的。本文的目的是揭示哪一个的故障诊断方法具有上述特性。为了去做诊断方法的分析,他们被表达为一般形式,以便他们可以与任何故障检测指标[3]一起使用。然后,结果表明该诊断方法可以统一为一般的诊