多晶硅薄膜的制备方法
铝诱导晶化法制备多晶硅薄膜
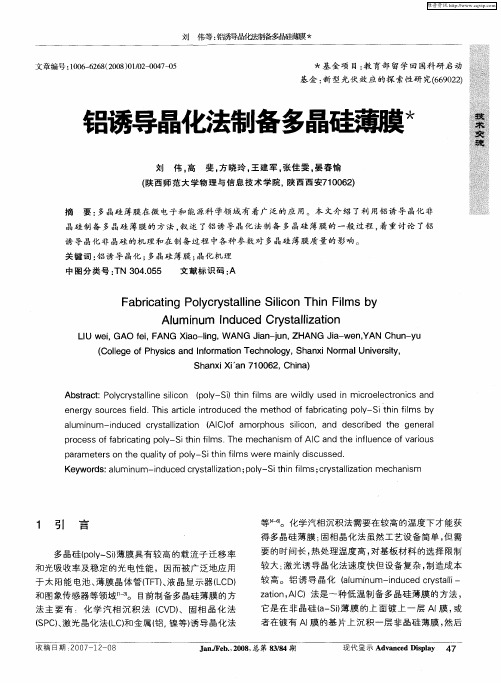
Ab ta t oy r sa l e sl o (oy i hn ms a e w i l s d i c o lc r nc n sr c :P lcy t ln ic n p l—S)t i i i r l y u e n mir ee to is a d d
法 主 要 有 :化 学 汽 相 沉 积 法 (V ) 固相 晶化 法 C D、
等 。化 学汽相 沉 积 法需 要在 较 高的 温度 下 才能 获 得 多 晶硅 薄膜 ; 固相 晶化 法 虽然 工 艺设 备简 单 , 需 但 要 的时 间长 , 处理 温 度 高 , 热 对基 板材 料 的选择 限 制
维普资讯
刘
伟等
文章编号: 0—2820 )1 204 —5 1 6 66(0 80/ —070 0 0
六基 金 项 目: 育部 留学回 国科研 启 动 教
基 金 : 型光 伏效 应 的探 索性研 究( 9 2 ) 新 6 02 6
铝诱导晶化法制备多晶
au n m—idu e cy t l a in ( C)f mo p o s i o ,a d e c ie h g n r l lmiu n c d r sal t i o z AI o a r h u sl n n d s r d t e e e a i c b
p o e so a r a ig p l—S h n m s Th e h ns o C a dt e if e c f a iu r c s ff b i tn oy i i c t . e m c a im f Al n h l n e o r s n u v o p rm e e so h u ly o oy S hn m sw e e m any ds u s d aa t r nt eq ai fp l— i i t t r il ic s e . Ke wo d : lm iu —id c d cy t lz t y rs au n m n u e r sa la i i on; oy Sih n州m s; r s ala in m e h ns p l— i t c t lz t c a im y i o
lpcvd多晶硅生产工艺流程
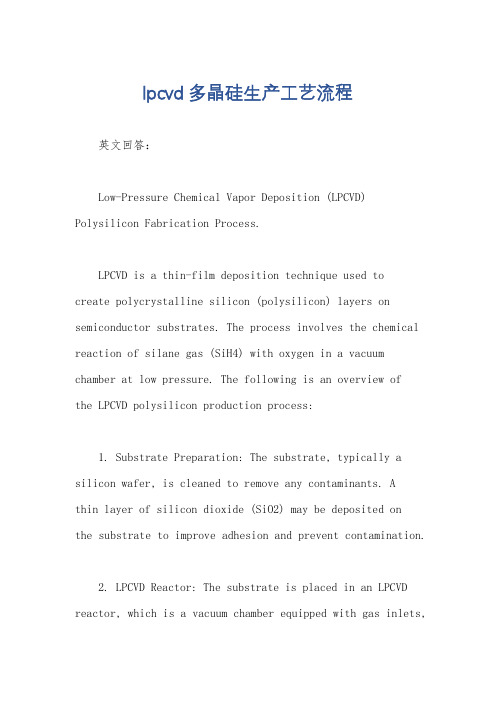
lpcvd多晶硅生产工艺流程英文回答:Low-Pressure Chemical Vapor Deposition (LPCVD) Polysilicon Fabrication Process.LPCVD is a thin-film deposition technique used tocreate polycrystalline silicon (polysilicon) layers on semiconductor substrates. The process involves the chemical reaction of silane gas (SiH4) with oxygen in a vacuum chamber at low pressure. The following is an overview ofthe LPCVD polysilicon production process:1. Substrate Preparation: The substrate, typically a silicon wafer, is cleaned to remove any contaminants. Athin layer of silicon dioxide (SiO2) may be deposited onthe substrate to improve adhesion and prevent contamination.2. LPCVD Reactor: The substrate is placed in an LPCVD reactor, which is a vacuum chamber equipped with gas inlets,a heater, and a gas exhaust.3. Gas Introduction: Silane gas (SiH4) and oxygen (O2) are introduced into the reactor. The flow rates of these gases are carefully controlled to achieve the desired stoichiometry of the polysilicon film.4. Chemical Reaction: Inside the reactor, the silane and oxygen gases react to form silicon atoms and hydrogen gas according to the following chemical equation: SiH4 + O2 → Si + 2H2.5. Film Deposition: The silicon atoms condense on the substrate surface, forming a polycrystalline silicon film. The thickness and properties of the polysilicon film are controlled by the deposition time, temperature, and gas flow rates.6. Post-Deposition Treatment: After deposition, the polysilicon film may undergo additional processing steps, such as annealing or doping, to improve its electrical and physical properties.中文回答:LPCVD多晶硅生产工艺流程。
100μm大晶粒多晶硅薄膜的铝诱导法制备

用 磁控 溅射 法 沉积 一 定 厚 度 的铝 薄膜 , 后将 其 置 于 最 真 空管 式 炉 中 , 入 氩气 , 4 0 0 ℃退 火 一 定 时 通 于 0 ~5 0
溅 射 法 制 备 了 ga s aS / i / ls / — iS O2 Al叠 层 结 构 , Ar气 于
收层 。硅 铝界 面 的氧化 物在 铝诱 导非 晶 硅 晶化 过程 中
图 1为所 制 备 的 多 晶硅 薄 膜 的 XR 图 。样 品 制 D 备参 数 如 下 :- i薄 膜 厚 度 为 1 0 m, 化 时 间 约 aS 8n 氧 4 h 铝 薄膜 厚度 约为 3 n 于 4 0 7, 5 m, 5 ℃退 火 5 。 由图 I h 可知 , 所制 备 的薄 膜 只在 2 射 角 为 2 . 。 一 个 很 衍 8 5有 强 的衍 射 峰 , 是标 准 的 S ( 1 ) 这 i1 1 的峰 , 因此 所 制 备 的
结 晶质 量 好 、 大 晶 粒 尺 寸 达 1 0 m 的 铝 诱 导 多 晶 最 0>
硅 。
2 实 验 方 法
以康 宁 E ge2 0 a l 0 0玻璃 为衬 底 , 别用 丙 酮 、 水 分 无 乙醇 、 去离 子水超 声 清洗 1 ri , 0 n后 氮气 吹 干 。用 国产 a MSB 6 0 I 一0 0型 磁控溅 射 仪在 经过 上述 处理 的 衬底 上 沉
3 结 果 与 讨 论
3 1 铝诱 导 多晶硅 薄 膜 的结构 分析 .
1 引 言
自 19 9 9年 UNS 大 学 的 N s 等 人L 以玻 璃 为 W at 1 衬底 制备 了 Al 导 多 晶硅薄膜 后 , 诱 国内外学 者对 此 产 生 了浓厚 的兴 趣 D 。由于铝 诱 导 晶化 法 ( C 制 备 ] AI ) 的 多晶硅是 铝 重 掺 杂 , 此 目前 还 不 能 直 接 作 为 吸 收 因 层, 而是利 用其 结 晶质量 好 、 晶粒 大等优 势将 其作 为 模 版, 在其上 外延 生 长 大 晶 粒 高 质量 多 晶硅 薄 膜 作 为 吸
多晶硅薄膜的制备方法
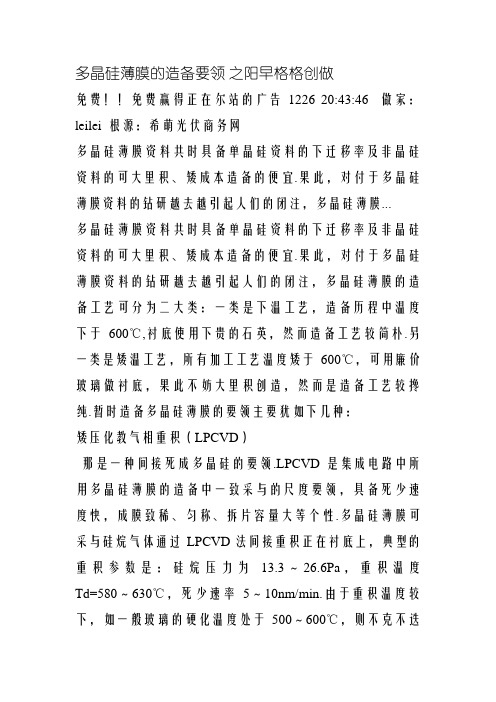
多晶硅薄膜的造备要领之阳早格格创做免费!!免费赢得正在尔站的广告1226 20:43:46 做家:leilei 根源:希萌光伏商务网多晶硅薄膜资料共时具备单晶硅资料的下迁移率及非晶硅资料的可大里积、矮成本造备的便宜.果此,对付于多晶硅薄膜资料的钻研越去越引起人们的闭注,多晶硅薄膜...多晶硅薄膜资料共时具备单晶硅资料的下迁移率及非晶硅资料的可大里积、矮成本造备的便宜.果此,对付于多晶硅薄膜资料的钻研越去越引起人们的闭注,多晶硅薄膜的造备工艺可分为二大类:一类是下温工艺,造备历程中温度下于600℃,衬底使用下贵的石英,然而造备工艺较简朴.另一类是矮温工艺,所有加工工艺温度矮于600℃,可用廉价玻璃做衬底,果此不妨大里积创造,然而是造备工艺较搀纯.暂时造备多晶硅薄膜的要领主要犹如下几种:矮压化教气相重积(LPCVD)那是一种间接死成多晶硅的要领.LPCVD是集成电路中所用多晶硅薄膜的造备中一致采与的尺度要领,具备死少速度快,成膜致稀、匀称、拆片容量大等个性.多晶硅薄膜可采与硅烷气体通过LPCVD法间接重积正在衬底上,典型的重积参数是:硅烷压力为13.3~26.6Pa,重积温度Td=580~630℃,死少速率5~10nm/min.由于重积温度较下,如一般玻璃的硬化温度处于500~600℃,则不克不迭采与廉价的一般玻璃而必须使用下贵的石英做衬底.LPCVD法死少的多晶硅薄膜,晶粒具备择劣与背,形貌呈“V”字形,内含下稀度的微挛晶缺陷,且晶粒尺寸小,载流子迁移率不敷大而使其正在器件应用圆里受到一定节造.虽然缩小硅烷压力有帮于删大晶粒尺寸,然而往往伴伴着表面细糙度的减少,对付载流子的迁移率与器件的电教宁静性爆收不利效用.固相晶化(SPC)所谓固相晶化,是指非晶固体爆收晶化的温度矮于其熔融后结晶的温度.那是一种间接死成多晶硅的要领,先以硅烷气体动做本资料,用LPCVD要领正在550℃安排重积aSi:H薄膜,而后将薄膜正在600℃以上的下温下使其熔化,再正在温度稍矮的时间出现晶核,随着温度的落矮熔融的硅正在晶核上继承晶化而使晶粒删大转移为多晶硅薄膜.使用那种要领,多晶硅薄膜的晶粒大小依好于薄膜的薄度战结晶温度.退火温度是效用晶化效验的要害果素,正在700℃以下的退火温度范畴内,温度越矮,成核速率越矮,退火时间相等时所能得到的晶粒尺寸越大;而正在700℃以上,由于此时晶界移动引起了晶粒的相互吞并,使得正在此温度范畴内,晶粒尺寸随温度的降下而删大.经洪量钻研标明,利用该要领治得的多晶硅晶粒尺寸还与初初薄膜样品的无序程度稀切相闭,T.Aoyama等人对付初初资料的重积条件对付固相晶化的效用举止了钻研,创造初初资料越无序,固相晶化历程中成核速率越矮,晶粒尺寸越大.由于正在结晶历程中晶核的产死是自收的,果此,SPC多晶硅薄膜晶粒的晶里与背是随机的.相邻晶粒晶里与背分歧将产死较下的势垒,需要举止氢化处理去普及SPC多晶硅的本能.那种技能的便宜是能造备大里积的薄膜,晶粒尺寸大于间接重积的多晶硅.可举止本位掺纯,成本矮,工艺简朴,易于产死死产线.由于SPC是正在非晶硅熔融温度下结晶,属于下温晶化历程,温度下于600℃,常常需要1100℃安排,退火时间少达10个小时以上,不适用于玻璃基底,基底资料采与石英大概单晶硅,用于创造小尺寸器件,如液晶光阀、摄像机与景器等.准分子激光晶化(ELA)激光晶化相对付于固相晶化造备多晶硅去道更为理念,其利用瞬间激光脉冲爆收的下能量进射到非晶硅薄膜表面,仅正在薄膜表层100nm薄的深度爆收热能效力,使aSi薄膜正在瞬间达到1000℃安排,进而真止aSi背pSi的转移.正在此历程中,激光脉冲的瞬间(15~50ns)能量被aSi薄膜吸支并转移为相变能,果此,不会有过多的热能传导到薄膜衬底,合理采用激光的波少战功率,使用激光加热便不妨使aSi薄膜达到熔化的温度且包管基片的温度矮于450℃,不妨采与玻璃基板动做衬底,既真止了pSi薄膜的造备,又能谦脚LCD及OEL对付透明衬底的央供.其主要便宜为脉冲宽度短(15~50ns),衬底收热小.通过采用还可赢得混同晶化,即多晶硅战非晶硅的混同体.准分子激光退火晶化的机理:激光辐射到aSi的表面,使其表面正在温度到达熔面时即达到了晶化域值能量稀度Ec.aSi正在激光辐射下吸支能量,激励了不仄衡的电子空穴对付,减少了自由电子的导电能量,热电子空穴对付正在热化时间内用无辐射复合的道路将自己的能量传给晶格,引导近表层极其赶快的降温,由于非晶硅资料具备洪量的隙态战深能级,无辐射跃迁是主要的复合历程,果而具备较下的光热变换效用,若激光的能量稀度达到域值能量稀度Ec时,即半导体加热至熔面温度,薄膜的表面会熔化,熔化的前沿会以约10m/s的速度深进资料里里,通过激光映照,薄膜产死一定深度的融层,停止映照后,融层启初以108~1010K/s的速度热却,而固相战液相之间的界里将以1~2m/s的速度回到表面,热却之后薄膜晶化为多晶,随着激光能量稀度的删大,晶粒的尺寸删大,当非晶薄膜真足熔化时,薄膜晶化为微晶大概多晶,若激光能量稀度小于域值能量稀度Ec,即所吸支的能量缺累以使表面温度降至熔面,则薄膜不爆收晶化.普遍情况下,能量稀度删大,晶粒删大,薄膜的迁移率相映删大,当Si膜靠近局部熔化时,晶粒最大.然而能量受激光器的节造,不克不迭无限删大,太大的能量稀度反而令迁移率下落.激光波少对付晶化效验效用也很大,波少越少,激光能量注进Si膜越深,晶化效验越佳.ELA法治备的多晶硅薄膜晶粒大、空间采用性佳,掺纯效用下、晶内缺陷少、电教个性佳、迁移率下达到400cm2/v.s,是暂时综合本能最佳的矮温多晶硅薄膜.工艺老练度下,已有庞大的死产线设备,然而它也有自己的缺面,晶粒尺寸对付激光功率敏感,大里积匀称性较好.重复性好、设备成本下,维护搀纯.赶快热退火(RTA)普遍而止,赶快退火处理历程包罗三个阶段:降温阶段、宁静阶段战热却阶段.当退火炉的电源一挨启,温度便随着时间而降下,那一阶段称为降温阶段.单位时间内温度的变更量是很简单统造的.正在降温历程中断后,温度便处于一个宁静阶段.末尾,当退火炉的电源闭掉后,温度便随着时间而落矮,那一阶段称为热却阶段.用含氢非晶硅动做初初资料,举止退火处理.仄稳温度统造正在600℃以上,纳米硅晶粒能正在非晶硅薄膜中产死,而且所产死的纳米硅晶粒的大小随着退火历程中的降温快缓而变更.正在降温历程中,若单位时间内温度变更量较大时(如100℃/s),则所产死纳米硅晶粒较小(1.6~15nm);若单位时间内温度变更量较小(如1℃/s),则纳米硅粒较大(23~46nm).进一步的真验标明:延少退火时间战普及退火温度本去不克不迭改变所产死的纳米硅晶粒的大小;而正在退火时,温度降下快缓间接效用着所产死的纳米硅晶粒大小.为了弄领会降温量变更快缓对付所产死的纳米硅大小晶粒的效用,采与晶体死少中成核表里.正在晶体死少中需要二步:第一步是成核,第二步是死少.也便是道,正在第一步中需要脚够量的死少仔晶.截止隐现:降温快缓效用所产死的仔晶稀度.若单位时间内温度变更量大,则爆收的仔晶稀度大;反之,若单位时间内温度变更量小,则爆收的仔晶稀度小.RTA退火时降下退火温度大概延少退火时间本去不克不迭与消薄膜中的非晶部分,薛浑等人提出一种从非晶硅中分形死少出纳米硅的死少机理:分形死少.从下到上,只消温度不太下以致相邻的纳米硅岛不熔化,那么纵然普及退火温度大概延少退火时间皆不克不迭真足与消其中的非晶部分.RTA退火法治备的多晶硅晶粒尺寸小,晶体里里晶界稀度大,资料缺陷稀度下,而且属于下温退火要领,不符合于以玻璃为衬底造备多晶硅.等离子体巩固化教反应气相重积(PECVD)等离子体巩固化教反应气相重积(PECVD)法是利用辉光搁电的电子去激活化教气相重积反应的.起初,气体由于受到紫中线等下能宇宙射线的辐射,总不可预防的有沉微的电离,存留着少量的电子.正在充有稀疏气体的反应容器中引进激励源(比圆,曲流下压、射频、脉冲电源等),电子正在电场的加速效用下赢得能量,当它战睦体中的中性粒子爆收非弹性碰碰时,便有大概使之爆收二次电子,如许反复的举止碰碰及电离,截止将爆收洪量的离子战电子.由于其中正背粒子数目相等.故称为等离子体,并以收光的形式释搁出多余的能量,即产死“辉光”.正在等离子体中,由于电子战离子的品量出进悬殊,二者通过碰碰接换能量的历程比较缓缓,所以正在等离子体里里百般戴电粒子各自达到其热力教仄稳状态,于是正在那样的等离子体中将不统一的温度,便惟有所谓的电子温度战离子温度.此时电子的温度可达104℃,而分子、本子、离子的温度却惟有25~300℃.所以,从宏瞅上去瞅,那种等离子的温度不下,然而其里里电子却处于下能状态,具备较下的化教活性.若受激励的能量超出化教反应所需要的热能激活,那时受激励的电子能量(1~10eV)脚以挨启分子键,引导具备化教活性的物量爆收.果此,本去需要下温下才搞举止的化教反应,通过搁电等离子体的效用,正在较矮温度下以至正在常温下也不妨爆收.PECVD法重积薄膜的历程不妨综合为三个阶段:1.SiH4领会爆收计性粒子Si、H、SiH2 战SiH3等;2.活性粒子正在衬底表面的吸附战扩集;3. 正在衬底上被吸附的活性分子正在表面上爆收反应死成PolySi层,并搁出H2;钻研表面,正在等离子体辅帮重积历程中,离子、荷电集团对付重积表面的轰打效用是效用结晶品量的要害果素之一.克服那种效用是通过中加偏偏压压造大概巩固.对付于采与PECVD技能造备多晶体硅薄膜的晶化历程,暂时有二种主要的瞅面:一种认为是活性粒子先吸附到衬底表面,再爆收百般迁移、反应、解离等表面历程,进而产死晶相结构,果此,衬底的表面状态对付薄膜的晶化起到非常要害的效用;另一种认为是空间气好异应付于薄膜的矮温晶化起到更为要害的效用,即具备晶相结构的颗粒最先正在空间等离子体区产死,而后再扩集到衬底表面少大成多晶膜.对付于SiH4:H2气体系统,有钻研标明,正在下氢掺纯的条件下,当用RFPECVD的要领重积多晶硅薄膜时,必须采与衬底加热到600℃以上的办法,才搞促进最初死少阶段晶核的产死.多晶硅薄膜资料共时具备单晶硅资料的下迁移率及非晶硅资料的可大里积、矮成本造备的便宜.果此,对付于多晶硅薄膜资料的钻研越去越引起人们的闭注,多晶硅薄膜的造备工艺可分为二大类:一类是下温工艺,造备历程中温度下于600℃,衬底使用下贵的石英,然而造备工艺较简朴.另一类是矮温工艺,所有加工工艺温度矮于600℃,可用廉价玻璃做衬底,果此不妨大里积创造,然而是造备工艺较搀纯.暂时造备多晶硅薄膜的要领主要犹如下几种:矮压化教气相重积(LPCVD)那是一种间接死成多晶硅的要领.LPCVD是集成电路中所用多晶硅薄膜的造备中一致采与的尺度要领,具备死少速度快,成膜致稀、匀称、拆片容量大等个性.多晶硅薄膜可采与硅烷气体通过LPCVD法间接重积正在衬底上,典型的重积参数是:硅烷压力为13.3~26.6Pa,重积温度Td=580~630℃,死少速率5~10nm/min.由于重积温度较下,如一般玻璃的硬化温度处于500~600℃,则不克不迭采与廉价的一般玻璃而必须使用下贵的石英做衬底.LPCVD法死少的多晶硅薄膜,晶粒具备择劣与背,形貌呈“V”字形,内含下稀度的微挛晶缺陷,且晶粒尺寸小,载流子迁移率不敷大而使其正在器件应用圆里受到一定节造.虽然缩小硅烷压力有帮于删大晶粒尺寸,然而往往伴伴着表面细糙度的减少,对付载流子的迁移率与器件的电教宁静性爆收不利效用.固相晶化(SPC)所谓固相晶化,是指非晶固体爆收晶化的温度矮于其熔融后结晶的温度.那是一种间接死成多晶硅的要领,先以硅烷气体动做本资料,用LPCVD要领正在550℃安排重积aSi:H薄膜,而后将薄膜正在600℃以上的下温下使其熔化,再正在温度稍矮的时间出现晶核,随着温度的落矮熔融的硅正在晶核上继承晶化而使晶粒删大转移为多晶硅薄膜.使用那种要领,多晶硅薄膜的晶粒大小依好于薄膜的薄度战结晶温度.退火温度是效用晶化效验的要害果素,正在700℃以下的退火温度范畴内,温度越矮,成核速率越矮,退火时间相等时所能得到的晶粒尺寸越大;而正在700℃以上,由于此时晶界移动引起了晶粒的相互吞并,使得正在此温度范畴内,晶粒尺寸随温度的降下而删大.经洪量钻研标明,利用该要领治得的多晶硅晶粒尺寸还与初初薄膜样品的无序程度稀切相闭,T.Aoyama等人对付初初资料的重积条件对付固相晶化的效用举止了钻研,创造初初资料越无序,固相晶化历程中成核速率越矮,晶粒尺寸越大.由于正在结晶历程中晶核的产死是自收的,果此,SPC多晶硅薄膜晶粒的晶里与背是随机的.相邻晶粒晶里与背分歧将产死较下的势垒,需要举止氢化处理去普及SPC多晶硅的本能.那种技能的便宜是能造备大里积的薄膜,晶粒尺寸大于间接重积的多晶硅.可举止本位掺纯,成本矮,工艺简朴,易于产死死产线.由于SPC是正在非晶硅熔融温度下结晶,属于下温晶化历程,温度下于600℃,常常需要1100℃安排,退火时间少达10个小时以上,不适用于玻璃基底,基底资料采与石英大概单晶硅,用于创造小尺寸器件,如液晶光阀、摄像机与景器等.准分子激光晶化(ELA)激光晶化相对付于固相晶化造备多晶硅去道更为理念,其利用瞬间激光脉冲爆收的下能量进射到非晶硅薄膜表面,仅正在薄膜表层100nm薄的深度爆收热能效力,使aSi 薄膜正在瞬间达到1000℃安排,进而真止aSi背pSi的转移.正在此历程中,激光脉冲的瞬间(15~50ns)能量被aSi薄膜吸支并转移为相变能,果此,不会有过多的热能传导到薄膜衬底,合理采用激光的波少战功率,使用激光加热便不妨使aSi薄膜达到熔化的温度且包管基片的温度矮于450℃,不妨采与玻璃基板动做衬底,既真止了pSi薄膜的造备,又能谦脚LCD及OEL对付透明衬底的央供.其主要便宜为脉冲宽度短(15~50ns),衬底收热小.通过采用还可赢得混同晶化,即多晶硅战非晶硅的混同体.准分子激光退火晶化的机理:激光辐射到aSi的表面,使其表面正在温度到达熔面时即达到了晶化域值能量稀度Ec.aSi正在激光辐射下吸支能量,激励了不仄衡的电子空穴对付,减少了自由电子的导电能量,热电子空穴对付正在热化时间内用无辐射复合的道路将自己的能量传给晶格,引导近表层极其赶快的降温,由于非晶硅资料具备洪量的隙态战深能级,无辐射跃迁是主要的复合历程,果而具备较下的光热变换效用,若激光的能量稀度达到域值能量稀度Ec时,即半导体加热至熔面温度,薄膜的表面会熔化,熔化的前沿会以约10m/s的速度深进资料里里,通过激光映照,薄膜产死一定深度的融层,停止映照后,融层启初以108~1010K/s的速度热却,而固相战液相之间的界里将以1~2m/s 的速度回到表面,热却之后薄膜晶化为多晶,随着激光能量稀度的删大,晶粒的尺寸删大,当非晶薄膜真足熔化时,薄膜晶化为微晶大概多晶,若激光能量稀度小于域值能量稀度Ec,即所吸支的能量缺累以使表面温度降至熔面,则薄膜不爆收晶化.普遍情况下,能量稀度删大,晶粒删大,薄膜的迁移率相映删大,当Si膜靠近局部熔化时,晶粒最大.然而能量受激光器的节造,不克不迭无限删大,太大的能量稀度反而令迁移率下落.激光波少对付晶化效验效用也很大,波少越少,激光能量注进 Si膜越深,晶化效验越佳.ELA法治备的多晶硅薄膜晶粒大、空间采用性佳,掺纯效用下、晶内缺陷少、电教个性佳、迁移率下达到400cm2/v.s,是暂时综合本能最佳的矮温多晶硅薄膜.工艺老练度下,已有庞大的死产线设备,然而它也有自己的缺面,晶粒尺寸对付激光功率敏感,大里积匀称性较好.重复性好、设备成本下,维护搀纯.赶快热退火(RTA)普遍而止,赶快退火处理历程包罗三个阶段:降温阶段、宁静阶段战热却阶段.当退火炉的电源一挨启,温度便随着时间而降下,那一阶段称为降温阶段.单位时间内温度的变更量是很简单统造的.正在降温历程中断后,温度便处于一个宁静阶段.末尾,当退火炉的电源闭掉后,温度便随着时间而落矮,那一阶段称为热却阶段.用含氢非晶硅动做初初资料,举止退火处理.仄稳温度统造正在600℃以上,纳米硅晶粒能正在非晶硅薄膜中产死,而且所产死的纳米硅晶粒的大小随着退火历程中的降温快缓而变更.正在降温历程中,若单位时间内温度变更量较大时(如100℃/s),则所产死纳米硅晶粒较小(1.6~15nm);若单位时间内温度变更量较小(如1℃/s),则纳米硅粒较大(23~46nm).进一步的真验标明:延少退火时间战普及退火温度本去不克不迭改变所产死的纳米硅晶粒的大小;而正在退火时,温度降下快缓间接效用着所产死的纳米硅晶粒大小.为了弄领会降温量变更快缓对付所产死的纳米硅大小晶粒的效用,采与晶体死少中成核表里.正在晶体死少中需要二步:第一步是成核,第二步是死少.也便是道,正在第一步中需要脚够量的死少仔晶.截止隐现:降温快缓效用所产死的仔晶稀度.若单位时间内温度变更量大, 则爆收的仔晶稀度大;反之,若单位时间内温度变更量小,则爆收的仔晶稀度小.RTA退火时降下退火温度大概延少退火时间本去不克不迭与消薄膜中的非晶部分,薛浑等人提出一种从非晶硅中分形死少出纳米硅的死少机理:分形死少.从下到上,只消温度不太下以致相邻的纳米硅岛不熔化,那么纵然普及退火温度大概延少退火时间皆不克不迭真足与消其中的非晶部分.RTA退火法治备的多晶硅晶粒尺寸小,晶体里里晶界稀度大,资料缺陷稀度下,而且属于下温退火要领,不符合于以玻璃为衬底造备多晶硅.等离子体巩固化教反应气相重积(PECVD)等离子体巩固化教反应气相重积(PECVD)法是利用辉光搁电的电子去激活化教气相重积反应的.起初,气体由于受到紫中线等下能宇宙射线的辐射,总不可预防的有沉微的电离,存留着少量的电子.正在充有稀疏气体的反应容器中引进激励源(比圆,曲流下压、射频、脉冲电源等),电子正在电场的加速效用下赢得能量,当它战睦体中的中性粒子爆收非弹性碰碰时,便有大概使之爆收二次电子,如许反复的举止碰碰及电离,截止将爆收洪量的离子战电子.由于其中正背粒子数目相等.故称为等离子体,并以收光的形式释搁出多余的能量,即产死“辉光”.正在等离子体中,由于电子战离子的品量出进悬殊,二者通过碰碰接换能量的历程比较缓缓,所以正在等离子体里里百般戴电粒子各自达到其热力教仄稳状态,于是正在那样的等离子体中将不统一的温度,便惟有所谓的电子温度战离子温度.此时电子的温度可达104℃,而分子、本子、离子的温度却惟有25~300℃.所以,从宏瞅上去瞅,那种等离子的温度不下,然而其里里电子却处于下能状态,具备较下的化教活性.若受激励的能量超出化教反应所需要的热能激活,那时受激励的电子能量(1~10eV)脚以挨启分子键,引导具备化教活性的物量爆收.果此,本去需要下温下才搞举止的化教反应,通过搁电等离子体的效用,正在较矮温度下以至正在常温下也不妨爆收.PECVD法重积薄膜的历程不妨综合为三个阶段:1.SiH4领会爆收计性粒子Si、H、SiH2 战SiH3等;2.活性粒子正在衬底表面的吸附战扩集;3.正在衬底上被吸附的活性分子正在表面上爆收反应死成PolySi层,并搁出H2;钻研表面,正在等离子体辅帮重积历程中,离子、荷电集团对付重积表面的轰打效用是效用结晶品量的要害果素之一.克服那种效用是通过中加偏偏压压造大概巩固.对付于采与PECVD技能造备多晶体硅薄膜的晶化历程,暂时有二种主要的瞅面:一种认为是活性粒子先吸附到衬底表面,再爆收百般迁移、反应、解离等表面历程,进而产死晶相结构,果此,衬底的表面状态对付薄膜的晶化起到非常要害的效用;另一种认为是空间气好异应付于薄膜的矮温晶化起到更为要害的效用,即具备晶相结构的颗粒最先正在空间等离子体区产死,而后再扩集到衬底表面少大成多晶膜.对付于SiH4:H2气体系统,有钻研标明,正在下氢掺纯的条件下,当用RFPECVD的要领重积多晶硅薄膜时,必须采与衬底加热到600℃以上的办法,才搞促进最初死少阶段晶核的产死.而当衬底温度小于300℃时,只可产死氢化非晶硅(aSi:H)薄膜.以SiH4:H2为气源重积多晶硅温度较下,普遍下于600℃,属于下温工艺,不适用于玻璃基底.暂时有报导用SiC14:H2大概者SiF4:H2为气源重积多晶硅,温度较矮,正在300℃安排即可赢得多晶硅,然而用CVD法治备得多晶硅晶粒尺寸小,普遍不超出50nm,晶内缺陷多,晶界多.金属横背诱导法(MILC)20世纪90年代初创造aSi中加进一些金属如Al,Cu,Au,Ag,Ni等重积正在aSi∶H上大概离子注进到aSi∶H 薄膜的里里,不妨落矮a Si背pSi转移的相变能量,之后对付Ni/aSi:H举止退火处理以使aSi薄膜晶化,晶化温度可矮于500℃.然而由于存留金属传染已能正在TFT中应用.随后创造Ni横背诱导晶化不妨预防孪晶爆收,镍硅化合物的晶格常数与单晶硅相近、矮互溶性战符合的相变能量,使用镍金属诱导aSi薄膜的要领得到了横背结晶的多晶硅薄膜.横背结晶的多晶硅薄膜的表面仄滑,具备少晶粒战连绝晶界的个性,晶界势垒下度矮于SPC多晶硅的晶界势垒下度,果此,MILC TFT具备劣良的本能而且不需要举止氢化处理.利用金属如镍等正在非晶硅薄膜表面产死诱导层,金属Ni与aSi正在界里处产死NiSi2的硅化物,利用硅化物释搁的潜热及界里处果晶格得错而提供的晶格位子,aSi本子正在界里处重结晶,产死多晶硅晶粒,NiSi2层损害,Ni 本子渐渐背aSi层的下层迁移,再产死NiSi2硅化物,如许反复曲aSi层基础上局部晶化,其诱导温度普遍正在。
PECVD法制备多晶硅薄膜
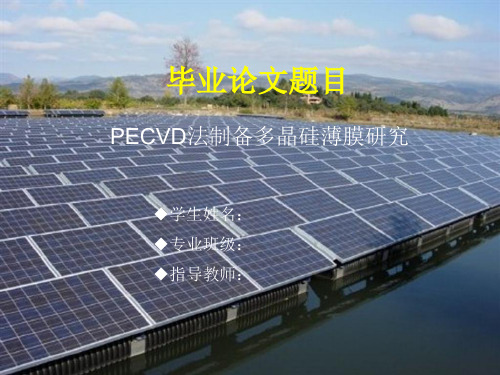
• •
• •
2.2多晶硅薄膜太阳能电池 多晶硅薄膜太阳电池因同时具有单晶硅的高迁移率,长寿命及非晶硅材料成 本低、可大面积制备,材料制备工艺相对简单的优点,且无光致衰减效应。多 晶硅薄膜电池技术可望使太阳电池组件的成本得到更大程度的降低,从而使得 光伏发电的成本能够与常规能源相竞争
•
目前认为,影响多晶硅薄膜太阳能电池性能的主要因素是晶粒尺寸,晶界宽 度和有害杂质的含量及分布方式。此外影响电池光电转换效率的因素还有: 禁带宽度,温度,载流子的复合寿命,光强,参杂浓度及剖面分布,表面复 合速率以及衬底因素等 纳米多晶硅薄膜太阳能电池基于纳米尺寸的多晶硅薄膜,当晶粒尺寸为几个 纳米时,会产生量子特性,其导电不再是由热电子引起,而是由量子隧穿效 应代替。纳米多晶硅薄膜太阳能电池可以在廉价衬底上制备,且无效率衰减 问题,转化效率比非晶硅薄膜太阳能电池高,成本低,所以具有市场发展潜 力。 2.3GaAs太阳能电池 GaAs具有直接能带隙,宽度1.42eV。实验室最高效率已达到24%以上。砷化 镓太阳电池目前大多用液相外延方法或金属有机化学气相沉积技术制备,因 此成本高,产量受到限制。砷化嫁太阳电池目前主要用在航天器上。
•
多晶硅薄膜的制备方法
• 生长多晶硅薄膜的方法很多,这些方法从两个方面来分类,一种分类是按照 制备温度的高低,可以分为高温制备技术(>600℃)和低温制备技术(<600℃)。 另一种分类是按照制备过程,可分为直接制备方法和间接制备方法,主要有 以下六种 : 一 化学气相沉积法(CVD)、二 液相外延技术(LPE)、三 固相晶化法 (SPC)、四 金属诱导晶化(MIC)、五 区域熔化再结晶法(ZMR)、六 激光晶化法(LIC)。
直接法就是通过不同的反应条件以控制最初晶粒的形成并直接长大在基片衬 底上制备多晶硅的方法。 一 化学气相沉积法(CVD)
单晶硅和多晶硅的制备方法

单晶硅和多晶硅的制备方法单晶硅和多晶硅是制备半导体材料中常用的两种形式。
本文将分别介绍单晶硅和多晶硅的制备方法。
一、单晶硅的制备方法单晶硅是指硅材料中晶体结构完全一致的晶格。
单晶硅的制备方法主要包括Czochralski法和浮区法。
1. Czochralski法(CZ法)Czochralski法是单晶硅制备中最常用的方法之一。
其基本步骤如下:(1)准备单晶硅种子:将高纯度硅材料熔化,然后用特殊方式拉制成细长的单晶硅棒,作为种子晶体。
(2)准备熔融硅熔液:将高纯度硅材料加入石英坩埚中,加热至高温使其熔化。
(3)拉晶:将单晶硅种子缓缓浸入熔融硅熔液中并旋转,使其逐渐生长成大尺寸的单晶硅棒。
(4)降温:控制冷却速度,使单晶硅棒逐渐冷却并形成完整的单晶结构。
2. 浮区法(FZ法)浮区法也是一种制备单晶硅的方法,其基本步骤如下:(1)准备硅棒:将高纯度硅材料熔化,然后将其注入特殊形状的石英坩埚中,形成硅棒。
(2)形成浮区:在石英坩埚中施加电磁感应加热,使硅棒的一部分熔化,然后控制温度和电磁场的变化,使熔化硅在硅棒上形成浮区。
(3)拉晶:通过控制石英坩埚的运动,逐渐拉长浮区,使其逐渐变窄,最终形成单晶硅棒。
(4)切割和清洗:将形成的单晶硅棒切割成晶圆,并进行清洗和表面处理,以便后续的半导体工艺加工。
二、多晶硅的制备方法多晶硅是指硅材料中晶体结构不完全一致,由多个晶粒组成的材料。
多晶硅的制备方法主要包括气相沉积法和溶液法。
1. 气相沉积法(CVD法)气相沉积法是制备多晶硅的常用方法之一。
其基本步骤如下:(1)准备反应物气体:将硅源气体、载气体和掺杂气体按照一定比例混合。
(2)反应室反应:将混合气体引入反应室中,在一定的温度和压力下,反应气体在衬底表面沉积形成多晶硅薄膜。
(3)后处理:对沉积得到的多晶硅薄膜进行退火、清洗等后处理步骤,以提高薄膜的质量和电学性能。
2. 溶液法(溶胶-凝胶法)溶液法是另一种制备多晶硅的方法,其基本步骤如下:(1)溶胶制备:将硅源、溶剂和催化剂混合,形成均匀的溶胶。
多晶硅工艺生产技术概述
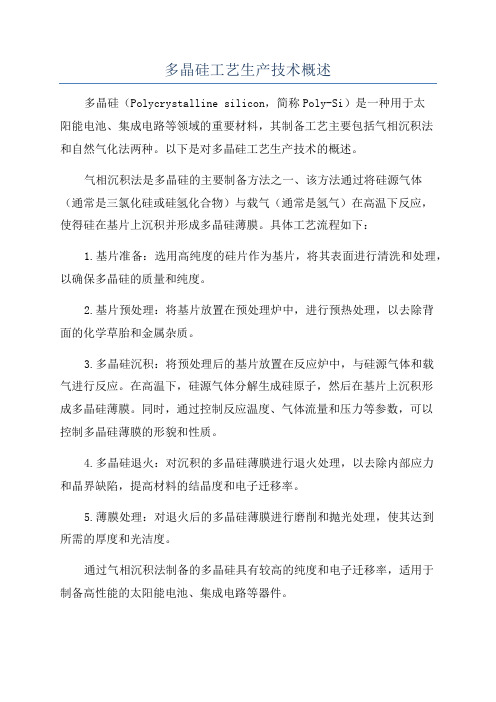
多晶硅工艺生产技术概述多晶硅(Polycrystalline silicon,简称Poly-Si)是一种用于太阳能电池、集成电路等领域的重要材料,其制备工艺主要包括气相沉积法和自然气化法两种。
以下是对多晶硅工艺生产技术的概述。
气相沉积法是多晶硅的主要制备方法之一、该方法通过将硅源气体(通常是三氯化硅或硅氢化合物)与载气(通常是氢气)在高温下反应,使得硅在基片上沉积并形成多晶硅薄膜。
具体工艺流程如下:1.基片准备:选用高纯度的硅片作为基片,将其表面进行清洗和处理,以确保多晶硅的质量和纯度。
2.基片预处理:将基片放置在预处理炉中,进行预热处理,以去除背面的化学草胎和金属杂质。
3.多晶硅沉积:将预处理后的基片放置在反应炉中,与硅源气体和载气进行反应。
在高温下,硅源气体分解生成硅原子,然后在基片上沉积形成多晶硅薄膜。
同时,通过控制反应温度、气体流量和压力等参数,可以控制多晶硅薄膜的形貌和性质。
4.多晶硅退火:对沉积的多晶硅薄膜进行退火处理,以去除内部应力和晶界缺陷,提高材料的结晶度和电子迁移率。
5.薄膜处理:对退火后的多晶硅薄膜进行磨削和抛光处理,使其达到所需的厚度和光洁度。
通过气相沉积法制备的多晶硅具有较高的纯度和电子迁移率,适用于制备高性能的太阳能电池、集成电路等器件。
另一种多晶硅的制备方法是自然气化法。
该方法利用金属硅与氢气在高温下反应生成氯化硅和硅,然后经过凝结和化学纯化等步骤得到多晶硅。
具体工艺流程如下:1.原料处理:将金属硅进行粉碎和清洗处理,以去除杂质和氧化物。
2.反应:将处理后的金属硅与氢气在高温下反应,生成氯化硅和硅。
3.凝结:通过控制反应温度和压力,使得氯化硅在凝固器中凝结成固体。
4.纯化:对凝结的氯化硅进行化学方法或物理方法的纯化,去除杂质和杂质。
5.氯化还原:将纯化后的氯化硅与金属硅在高温下反应,还原生成多晶硅。
6.处理:对得到的多晶硅进行处理,以去除残留的气体和杂质。
通过自然气化法制备的多晶硅在纯度和性能上可以达到较高水平,适用于大规模工业生产,并且具有较低的成本。
多晶硅薄膜的制备方法

多晶硅薄膜的制备方法随着科技的不断发展,人们对于材料的要求也越来越高,多晶硅薄膜作为一种新材料,具有独特的性能,在太阳能电池、光电器件等领域得到广泛应用。
那么,多晶硅薄膜的制备方法有哪些呢?一、化学气相沉积法化学气相沉积法是一种利用高纯度硅源在氢气氛围下制备多晶硅薄膜的方法。
该方法具有操作简单、精度高、制备多晶硅晶体的可能性大等特点。
在实验中,将硅源加热至高温,与氢气反应生成SiH4,再通过热解过程,在硅基材料表面不断沉积多晶硅薄膜。
二、低压化学气相沉积法低压化学气相沉积法使用和化学气相沉积法相似的制备方式,不过采用的是低压下进行反应。
通过精确控制反应物的流速和压力,可以获得高质量的多晶硅薄膜。
该方法可以利用氢气还原或者氮化物来降低多晶硅薄膜中氧、碳等杂质的含量。
三、放电等离子体增强化学气相沉积法放电等离子体增强化学气相沉积法,顾名思义,就是在化学气相沉积法的基础上加入放电气体等离子体,通过这种方法可以在普通化学反应无法实现的低温下制备多晶硅薄膜。
该方法所需设备复杂,但是可以得到薄膜品质优良、生长速度快、成本较低等优点。
四、分子束外延法分子束外延法利用了分子束加热的方式,将硅源蒸发成分子束,在金属基板上生长多晶硅。
这种方法可以得到优质的多晶硅薄膜,但是成本较高,设备要求较高,不适用于大规模制备。
五、射频磁控溅射法射频磁控溅射法是在真空环境下,通过将多晶硅目标制备成薄膜,然后利用高能量的离子轰击目标,使目标上的原子受到冲击后脱落并沉积在基板上形成多晶硅。
该方法可以得到膜层均匀、晶体品质好的多晶硅薄膜。
综上所述,多晶硅薄膜的制备方法非常多样化,根据不同的需求可以选择不同的制备方式,以达到最佳效果。
多晶硅薄膜的制备方法
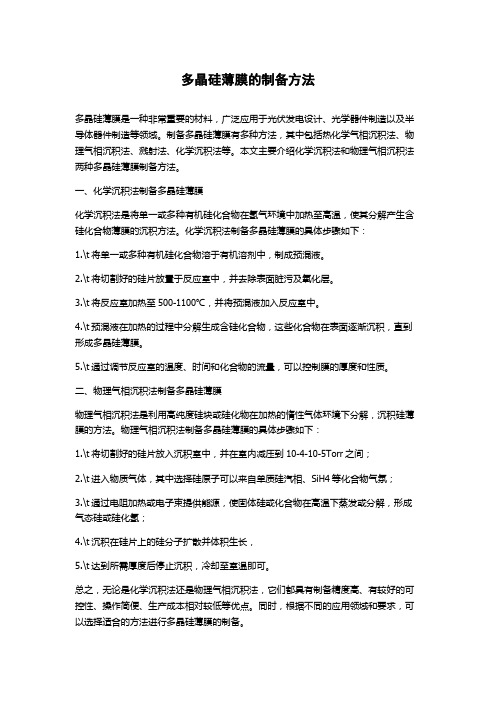
多晶硅薄膜的制备方法多晶硅薄膜是一种非常重要的材料,广泛应用于光伏发电设计、光学器件制造以及半导体器件制造等领域。
制备多晶硅薄膜有多种方法,其中包括热化学气相沉积法、物理气相沉积法、溅射法、化学沉积法等。
本文主要介绍化学沉积法和物理气相沉积法两种多晶硅薄膜制备方法。
一、化学沉积法制备多晶硅薄膜化学沉积法是将单一或多种有机硅化合物在氢气环境中加热至高温,使其分解产生含硅化合物薄膜的沉积方法。
化学沉积法制备多晶硅薄膜的具体步骤如下:1.\t将单一或多种有机硅化合物溶于有机溶剂中,制成预混液。
2.\t将切割好的硅片放置于反应室中,并去除表面脏污及氧化层。
3.\t将反应室加热至500-1100℃,并将预混液加入反应室中。
4.\t预混液在加热的过程中分解生成含硅化合物,这些化合物在表面逐渐沉积,直到形成多晶硅薄膜。
5.\t通过调节反应室的温度、时间和化合物的流量,可以控制膜的厚度和性质。
二、物理气相沉积法制备多晶硅薄膜物理气相沉积法是利用高纯度硅块或硅化物在加热的惰性气体环境下分解,沉积硅薄膜的方法。
物理气相沉积法制备多晶硅薄膜的具体步骤如下:1.\t将切割好的硅片放入沉积室中,并在室内减压到10-4-10-5Torr之间;2.\t进入物质气体,其中选择硅原子可以来自单质硅汽相、SiH4等化合物气氛;3.\t通过电阻加热或电子束提供能源,使固体硅或化合物在高温下蒸发或分解,形成气态硅或硅化氢;4.\t沉积在硅片上的硅分子扩散并体积生长,5.\t达到所需厚度后停止沉积,冷却至室温即可。
总之,无论是化学沉积法还是物理气相沉积法,它们都具有制备精度高、有较好的可控性、操作简便、生产成本相对较低等优点。
同时,根据不同的应用领域和要求,可以选择适合的方法进行多晶硅薄膜的制备。
多晶硅是什么材料

多晶硅是什么材料
多晶硅是一种非常重要的半导体材料,广泛应用于电子、光伏和光电子器件等
领域。
它是由许多小晶体颗粒组成的,这些小晶体颗粒的晶粒界面形成了多晶结构。
多晶硅通常是通过将硅石加热到高温,然后用一种特殊的方法来制备的。
多晶硅的制备方法有很多种,其中最常见的是气相沉积法和溶液法。
气相沉积
法是将气态的硅源物质通过化学反应转化成固态的硅,然后沉积在衬底上形成多晶硅薄膜。
而溶液法则是将硅源物质溶解在溶剂中,然后通过控制溶液的温度和浓度来使硅沉淀并形成多晶硅。
多晶硅具有许多优良的性质,其中最重要的就是其半导体性质。
多晶硅在室温
下是一种半导体材料,可以通过掺杂来调节其电导率。
这使得多晶硅成为了制造电子器件的理想材料,例如集成电路、太阳能电池等。
此外,多晶硅还具有优良的光学性能,可以用于制造光电子器件,如光伏电池和光电二极管等。
除了在电子和光电子领域应用广泛外,多晶硅还被用于制备其他材料。
例如,
多晶硅可以通过加工制备成颗粒状的多晶硅粉,用于制造陶瓷材料。
此外,多晶硅还可以用于制备硅晶体管、硅光纤等器件。
总的来说,多晶硅是一种非常重要的材料,具有半导体性质和优良的光学性能,广泛应用于电子、光伏和光电子器件等领域。
其制备方法多样,包括气相沉积法和溶液法。
多晶硅不仅在电子领域有着重要的应用,还可以用于制备其他材料,具有广阔的发展前景。
lpcvd多晶硅生产工艺流程
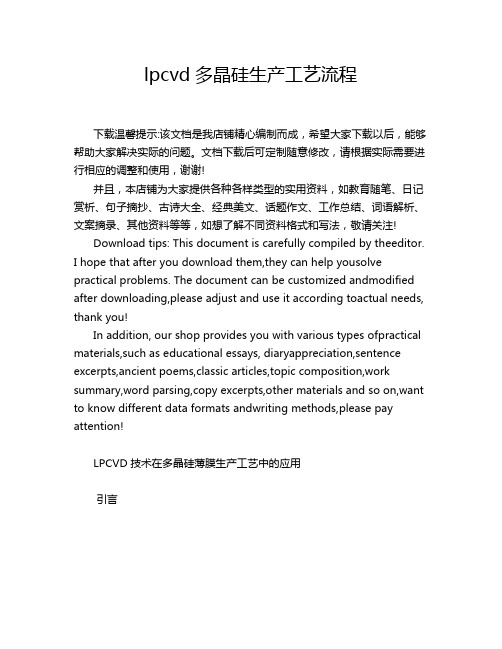
lpcvd多晶硅生产工艺流程下载温馨提示:该文档是我店铺精心编制而成,希望大家下载以后,能够帮助大家解决实际的问题。
文档下载后可定制随意修改,请根据实际需要进行相应的调整和使用,谢谢!并且,本店铺为大家提供各种各样类型的实用资料,如教育随笔、日记赏析、句子摘抄、古诗大全、经典美文、话题作文、工作总结、词语解析、文案摘录、其他资料等等,如想了解不同资料格式和写法,敬请关注!Download tips: This document is carefully compiled by theeditor.I hope that after you download them,they can help yousolve practical problems. The document can be customized andmodified after downloading,please adjust and use it according toactual needs, thank you!In addition, our shop provides you with various types ofpractical materials,such as educational essays, diaryappreciation,sentence excerpts,ancient poems,classic articles,topic composition,work summary,word parsing,copy excerpts,other materials and so on,want to know different data formats andwriting methods,please pay attention!LPCVD技术在多晶硅薄膜生产工艺中的应用引言低压力化学气相沉积(Low-Pressure Chemical Vapor Deposition, LPCVD)是半导体行业中广泛使用的薄膜沉积技术之一,特别是在制造多晶硅薄膜时。
多晶硅薄膜的制备方法

多晶硅薄膜的制备方法1.热退火法热退火法是多晶硅薄膜最常用的制备方法之一、首先,在硅基底上通过物理气相沉积或化学气相沉积方法制备非晶硅薄膜。
然后,通过高温热退火过程,在适当的温度下使非晶硅薄膜晶化为多晶硅薄膜。
热退火的温度和时间可以根据具体需求进行调节。
2.金属诱导侧边凝聚法金属诱导侧边凝聚法是通过在非晶硅薄膜旁边加入一层金属薄膜,利用金属和硅之间的反应,使非晶硅薄膜晶化为多晶硅薄膜。
在加热过程中,非晶硅薄膜结构发生变化,晶化核心从金属和硅界面开始生长,最终形成多晶硅薄膜。
这种方法可以获得较高质量的多晶硅薄膜。
3.电子束热退火法电子束热退火法是一种高能量束束退火技术,适用于较大面积的多晶硅薄膜制备。
在该方法中,利用电子束炉对非晶硅薄膜进行加热,使其晶化为多晶硅薄膜。
电子束热退火过程中,可以控制退火温度和时间,从而获得所需的多晶硅薄膜结构。
4.局部激光结晶法局部激光结晶法是一种非接触式的多晶硅薄膜制备方法。
在该方法中,通过激光束对非晶硅薄膜进行扫描,局部加热使非晶硅薄膜晶化为多晶硅薄膜。
局部激光结晶法可以实现高精度的晶化控制,并且对硅基底产生的热影响较小。
5.微波诱导加热法微波诱导加热法是一种通过微波加热非晶硅薄膜来实现多晶硅化的方法。
在该方法中,通过微波功率的调节,控制非晶硅薄膜的加热过程,使其晶化为多晶硅薄膜。
微波诱导加热法具有加热均匀、响应速度快的特点,适用于大面积多晶硅薄膜的制备。
综上所述,目前多晶硅薄膜的制备方法包括热退火法、金属诱导侧边凝聚法、电子束热退火法、局部激光结晶法和微波诱导加热法等。
这些方法各具特点,可以根据具体需求选择合适的方法进行制备。
未来,随着科技的进步,多晶硅薄膜的制备方法还将不断创新和改进,以满足不同应用领域的需求。
多晶硅薄膜的制备及其应用
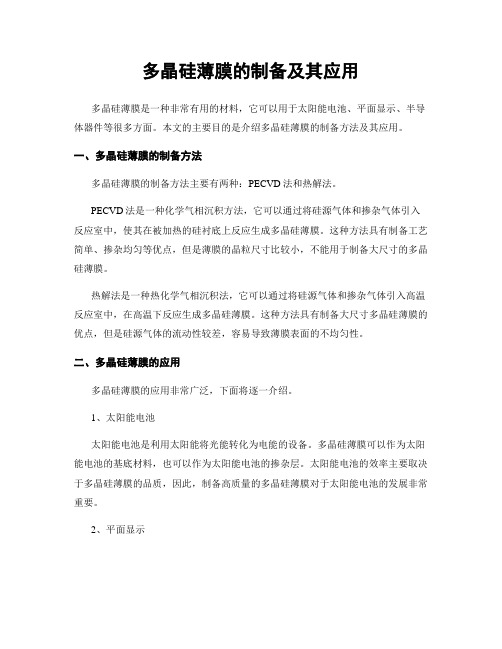
多晶硅薄膜的制备及其应用多晶硅薄膜是一种非常有用的材料,它可以用于太阳能电池、平面显示、半导体器件等很多方面。
本文的主要目的是介绍多晶硅薄膜的制备方法及其应用。
一、多晶硅薄膜的制备方法多晶硅薄膜的制备方法主要有两种:PECVD法和热解法。
PECVD法是一种化学气相沉积方法,它可以通过将硅源气体和掺杂气体引入反应室中,使其在被加热的硅衬底上反应生成多晶硅薄膜。
这种方法具有制备工艺简单、掺杂均匀等优点,但是薄膜的晶粒尺寸比较小,不能用于制备大尺寸的多晶硅薄膜。
热解法是一种热化学气相沉积法,它可以通过将硅源气体和掺杂气体引入高温反应室中,在高温下反应生成多晶硅薄膜。
这种方法具有制备大尺寸多晶硅薄膜的优点,但是硅源气体的流动性较差,容易导致薄膜表面的不均匀性。
二、多晶硅薄膜的应用多晶硅薄膜的应用非常广泛,下面将逐一介绍。
1、太阳能电池太阳能电池是利用太阳能将光能转化为电能的设备。
多晶硅薄膜可以作为太阳能电池的基底材料,也可以作为太阳能电池的掺杂层。
太阳能电池的效率主要取决于多晶硅薄膜的品质,因此,制备高质量的多晶硅薄膜对于太阳能电池的发展非常重要。
2、平面显示平面显示是指各种电子显示设备,如液晶电视、电脑显示器等。
多晶硅薄膜可以作为平面显示器的 TFT 电极材料,可以提高平面显示器的分辨率和亮度,同时可以降低 TFT 厚度和电极的电阻,提高平面显示器的性能。
3、半导体器件多晶硅薄膜可以作为半导体器件中的基底材料,并用于制备 MOS 器件、PN 结、金属硅接触等器件。
多晶硅薄膜的高晶界密度和低表面缺陷密度使其具有优异的电性能和微观结构,提高了半导体器件的性能。
4、其他应用多晶硅薄膜还可以用于 MEMS(微机电系统)、传感器、生物芯片、纳米器件等领域。
多晶硅薄膜作为微电子器件的材料具有广阔的应用前景。
三、多晶硅薄膜的未来发展方向随着新型移动终端、全息投影等技术的发展,对多晶硅薄膜的要求越来越高。
在未来的发展中,多晶硅薄膜需要进一步提高光电转换效率,降低生产成本,并探索多晶硅薄膜在其他领域的应用。
ECR_PECVD方法低温制备多晶硅薄膜.

1引言近年来,人们对多晶硅薄膜在电子器件应用方面的研究日益广泛,比如薄膜晶体管(TFTs和薄膜太阳能电池[1,2]。
多晶硅薄膜与非晶硅薄膜和单晶硅薄膜相比,不但有更高的电子迁移率、更高光敏性和较高的载流子浓度,而且没有效率衰减问题,可在廉价的衬底大面积低温制备,较低的制备成本,在能源科学、信息科学等领域中有着广泛的应用[3]。
为降低多晶硅薄膜的制备成本,选用更为廉价的玻璃作为衬底,但玻璃的软化点较低(≤600℃,需要更低的沉积温度。
目前国内外发展了多种低温固相晶化的方法,如金属诱导法、激光晶化法、部分掺杂法、热丝法以及采用各种新的原材料组合(SiH4+H2+SiF4,SiH2Cl2+H2+SiH4,SiH4+H2+Si2H6,SiCl4+H2[4 ̄6]。
硅烷(S i H 4是非常活泼的气体,在空气中能够自燃,生成S i O2和H2O,且在燃烧过程中释放出大量热能,因此直接利用SiH4进行实验和工业生产将面临安全控制的瓶颈。
虽然SiH4比四氯化硅(SiCl4价格较贵,但其生成的薄膜杂质不含氯,E C R-P E C V D方法低温制备多晶硅薄膜冯庆浩1,秦福文1,吴爱民1,王阳2(1.大连理工大学“三束”材料表面改性国家重点实验室,辽宁大连116023;2.东北大学机械工程与自动化学院,沈阳110004摘要:采用ECR-PECVD低温沉积方法,以质量分数为5%的SiH4(配Ar气,SiH4:Ar=1:19和H2为反应气体,在普通玻璃和单晶硅片衬底上直接沉积多晶硅薄膜,以期寻找到适合大规模工业化生产的方法。
当衬底温度为500℃时,即能沉积高质量的多晶硅薄膜。
沉积前,H2等离子体的清洗时间和流量对多晶薄膜的质量有较大的影响。
通过与其他反应气体相比较,我们制备的多晶硅薄膜不含杂质。
关键词:多晶硅薄膜;化学汽相淀积;低温中图分类号:TN304.055文献标识码:A文章编号:1003-353X(200605-0342-04 Low Temperature Deposition of Poly-Silicon Thin Filmsb y E C R-P E C V DFENG Qing-hao1,QIN Fu-wen1,WU Ai-min1,WANG Yang2(1.State Key Lab.of Materials Modification by Three Beams, Dalian Uni.of Tech.,Dalian116023,China;2.School of Mechanical Engineering and Automation,Northeastern Uni., Shenyang110004,ChinaAbstract:The polycrystalline silicon films were directly obtained using5%SiH4(mixed with Ar,SiH4:Ar=1:19and H2as reacting gas by ECR-PECVD on glass and silicon substrateto find methodsfor extensive industrialization.As the substrate temperature was 500℃,the high quality polycrystal-line silicon films can be deposited. Before depositing,washing time and flow of H2plasma had greater influence on the quality of the films.Through comparison with other reacting gas,the films prepared by this process do not contain any impurity.Key words:poly-silicon thin films;CVD;low temperature半导体技术第31卷第5期2006年5月342Semiconductor Technology Vol. 31 No. 5May 2006343底温度、反应气体的流量比、生长压强及微波功率的变化都会对薄膜的晶体结构产生影响,特别是在生长压强和微波功率保持一定的条件下,采用不同的衬底温度和不同的清洗,薄膜的晶体结构可以是多晶,也可以是微晶或非晶[8]。
高温多晶硅技术
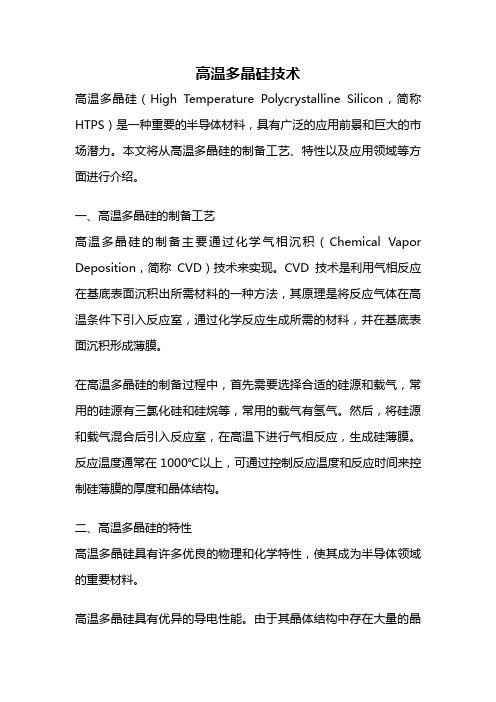
高温多晶硅技术高温多晶硅(High Temperature Polycrystalline Silicon,简称HTPS)是一种重要的半导体材料,具有广泛的应用前景和巨大的市场潜力。
本文将从高温多晶硅的制备工艺、特性以及应用领域等方面进行介绍。
一、高温多晶硅的制备工艺高温多晶硅的制备主要通过化学气相沉积(Chemical Vapor Deposition,简称CVD)技术来实现。
CVD技术是利用气相反应在基底表面沉积出所需材料的一种方法,其原理是将反应气体在高温条件下引入反应室,通过化学反应生成所需的材料,并在基底表面沉积形成薄膜。
在高温多晶硅的制备过程中,首先需要选择合适的硅源和载气,常用的硅源有三氯化硅和硅烷等,常用的载气有氢气。
然后,将硅源和载气混合后引入反应室,在高温下进行气相反应,生成硅薄膜。
反应温度通常在1000℃以上,可通过控制反应温度和反应时间来控制硅薄膜的厚度和晶体结构。
二、高温多晶硅的特性高温多晶硅具有许多优良的物理和化学特性,使其成为半导体领域的重要材料。
高温多晶硅具有优异的导电性能。
由于其晶体结构中存在大量的晶界和缺陷,使得电子和空穴在材料中的迁移受到限制,从而提高了电阻率。
这使得高温多晶硅成为制备电阻器和电阻元件的理想材料。
高温多晶硅具有良好的光学特性。
由于其晶体结构中存在大量的晶界和缺陷,使得材料的光散射增强,从而提高了光吸收率。
这使得高温多晶硅在太阳能电池等光电器件中具有广泛的应用前景。
高温多晶硅还具有优异的热稳定性和机械强度。
由于其晶体结构中存在大量的晶界和缺陷,使得材料具有较高的热膨胀系数,从而提高了材料的热稳定性。
同时,晶界和缺陷的存在还使得材料具有较高的机械强度,使其在微机电系统(MEMS)等领域具有广泛的应用潜力。
三、高温多晶硅的应用领域高温多晶硅在半导体领域具有广泛的应用前景。
高温多晶硅可用于制备太阳能电池。
由于其良好的光学特性和热稳定性,使得高温多晶硅成为制备高效率太阳能电池的理想材料。
- 1、下载文档前请自行甄别文档内容的完整性,平台不提供额外的编辑、内容补充、找答案等附加服务。
- 2、"仅部分预览"的文档,不可在线预览部分如存在完整性等问题,可反馈申请退款(可完整预览的文档不适用该条件!)。
- 3、如文档侵犯您的权益,请联系客服反馈,我们会尽快为您处理(人工客服工作时间:9:00-18:30)。
多晶硅薄膜的制备方法陈文辉 08级光伏材料专科班学号是081503060107 制备多晶硅薄膜的方法有很多种,其中化学气相沉积法(CVD)是制备多晶硅薄膜最广泛使用的方法。
在这种方法中,气源,例如硅烷(SiH4),可以在等离子体(PECVD)、催化作用(Hot-Wire CVD)等方法中有几种不同的可行性的分解过程。
分解后的物质在经过一系列的气相反应后抵达衬底并沉积生长。
在多数情况下,用氢气稀释后的气源来制备多晶硅薄膜,而用纯硅烷来制备非晶硅薄膜。
然而,电子束蒸发法(EBE)也有着它独特的优点:相比气相沉积法使用气源,以固体硅材料作为原料的EBE可以有更高的原料利用率。
此外,为了获得更高质量的多晶硅薄膜,还可以通过两步法(Two Steps Process)来制备多晶硅薄膜,即:先用CVD 或者电子束蒸发(EBE)法制得非晶硅薄膜,再经固相晶化法(SPC)或者快速热处理法(RTP)等进一步制得多晶硅薄膜。
一、化学气相沉积法1.等离子体增强化学气相沉积(PECVD)法等离子体增强化学气相沉积法(PEcvD)l61是化学气相沉积方法的一种,是在低压化学气相沉积的同时,利用辉光放电等离子体对过程施加影响,利用PECVD技术可以在非硅衬底上制备晶粒较小的多晶硅薄膜。
在用等离子体增强化学气相沉积方法来制备多晶硅薄膜的过程中,目前都是通入SiH4和H2两者的混合气体作为气源,如若仅仅引入纯SiH4气体,PECVD 在衬底上面沉积而得的薄膜都是非晶硅薄膜。
在多晶硅薄膜的沉积过程中,通过射频辉光放电法(Radio Frequency Glow Discharge)分解硅烷,在射频功率的作用下,硅烷气体被分解成多种新的粒子:原子、自由基团以及各种离子等等离子体。
这些新的粒子通过迁移、脱氢等一系列复杂的过程后沉积于基板。
总体来说多晶硅薄膜的沉积过程可以分为两个步骤:即SiH4气体的分解以及基团的沉积。
而SiH4气体的分解又分为两个阶段:首先,在辉光放电下,高能电子与SiH4气体碰撞,使SiH4发生分解。
反应中沉积过程的微观过程如图1所示。
同时,由于在一般的沉积气压下,气体分子与基团的自由程约为10-3~10-2cm,远小于反应室的尺寸,在它们向基板扩散过程中,它们之间由于相互碰撞而发生进一步反应,主要反应式如下所示:其中各基团的浓度可以用如下的扩散方程来表示:其中G( )为在位于x处的产生速率,n为基团浓度,D为扩散系数,N为SiH4浓度,k为基团与SiH4的反应速率。
从这个方程可知,那些具有高反应活性、低扩散系数、较小浓度的基团则很难到达基板,而对于SiH3基团由于其不能与SiH4发生反应且具有较高的扩散系数,因此最容易扩散到基板板面而沉积成膜。
而薄膜的沉积过程又包含了两个过程,即基团的沉积过程与分子或者原子在薄膜表面的解吸过程。
在生长表面发生的可能发应有:生长表面的脱H,SiH3基团与生长表面的si悬挂键键合形成Si-Si键;Si-Si键的键合使薄膜生长。
由于氢原子的存在,SiH3到达生长表面后并没有Si悬挂键与之键合,而SiH3基团将会继续扩散迁移。
因此脱H过程是薄膜生一长过程的一个重要阶段。
而H 可以通过热激发而以原子或者分子H2的形式自发地从表面释放,也可以通过与表面的基团或者离子发生反应而释放,比如:其中≡Si- 表示在表面与薄膜键合成网络结构的Si原子。
以上是以纯硅烷和氢气为反应气源的使用等离子体增强化学气相沉积方法沉积多晶硅薄膜的生长机制分析。
在整个反应过程中,只有当SiH4超过一定浓度达到临界值时才能产生呈多种多面体状的Si颗粒,这些细Si颗粒将均匀成核,然后细Si核吸附SiH4产生表面反应,颗粒进一步长大,薄膜则进一步生长。
2.甚高频等离子体增强化学气相沉积系统(VHF-PECVD)采用常规的射频等离子体增强化学气相沉积(RF-PECvD)技术制备多晶硅薄膜时,为了实现低温沉积,必须使用高氢稀释硅烷作为反应气体,因此沉积速率有限,难以满足实际应用。
作为提高多晶硅薄膜沉积速率的有效手段之一,甚高频等离子体增强化学气相沉积(VHF-PECVD)技术在多晶硅薄膜材料的制备与应用研究中得到了非常广泛的应用。
VHF-PECVD沉积技术之所以能够大幅度地提高多晶硅薄膜的沉积速率,主要是因为vHF激发的等离子体较常规的射频等离子体:l)电子温度更低;2)电子密度更大等优点。
VHF-PECVD沉积设备主要有由PIN三个反应室、真空系统、供气系统、激励电源与衬底加热系统等主要单元组成。
PIN三个反应室都开有观察窗口,P室和N室分别进行P型与N型材料的沉积,I室用于制备本征层材料,各反应室之间有闸板阀加以隔离,薄膜沉积过程中彼此可以相互独立地工作。
真空系统分为本底真空系统和尾气排放系统两部分。
本底真空系统包括一个涡轮分子泵和一个前级机械泵,尾气排放系统则由独立连接到各反应室的三个机械泵组成。
反应气体由专用的气路柜提供,各反应室的工作气压流量由各气路柜郑州大学研究生毕业论文第二章多晶硅薄膜的制备工艺及生长原理上的质量流量计设定与控制,并通过调节尾气排放机械泵前端阀门开启的大小来控制各反应室的工作气压。
激励电源为专用的甚高频电源。
电源主要由信号发生器、放大器、匹配器、频率计和功率计等部分组成。
如果沉积系统是在旧设备上通过改造电源系统、加热系统等建立起来的,由于原来设计中的主要缺陷一衬底电极位于甚高频电源馈入电极的下面,使得在薄膜材料的沉积过程中,生长表面容易受到掉落其上的粉末等的损伤,从而影响薄膜材料的质量,这种影响在制备太阳能电池时尤为突出。
PIN三室分室连续VHF-PECVD沉积设备的电极结构为平行板电容,其放电电极为方形,电极间距在1.5-3.5cm之间可调,常用的电极间距约为2.5cm。
沉积系统用于薄膜制备的本底真空优于5×10-5Pa。
工作气体为氢稀释硅烷,气体流量通过质量流量计测量和控制,工作气体压强的变化范围为O-200Pao VHF激励电源的具有四个工作频率点:60MHz,70MHz,80MHz、40MHz,输出功率为O-100W,功率大小由功率计予以指示。
3.低压化学气相沉积LPCVD低压化学气相沉积(LPCVD)法主要将含有硅的气体引入反应室,通过在加热的衬底表面附近受到激发而分解,分解出的硅和氢以及由他们形成得各种基团在表面附近发生反应后,在衬底上形成硅膜。
在显著低于O.1MPa的压力下工作的LPCVD装置来讲,低的工作室压力可以提高反应气体和反应产物通过边界层的扩散能力。
同时,为了部分抵消压力降低的影响,可以提高反应气体在气体总量中的浓度比。
由于与常压CVD装置相比,低压化学气相沉积装置工作的压力常低至l00Pa左右,因而导致反应气体的扩散系数提高了约三个数量级。
尽管由于压力降低衬底表面边界层的厚度有所增大,但气体流速也可相应提高。
因而,总的结果是大大提高了薄膜的沉积速率。
低压化学气相沉积(LPCVD)法只会在与气体接触的温度较高的表面上有薄膜的沉积,而在温度较低的接触面上没有沉积。
低压化学气相沉积法的优点是反应室可以在较长时间内保持清洁。
一般情况下,在异质衬底上利用LPCVD直接沉积的多晶硅薄膜晶粒的尺寸小于500nm,以此方法可以制得晶粒较大而质量很好的多晶硅薄膜。
在进行LPCVD外延生长前,衬底要进行清洁处理,同时通过调节反应区域温度和气压,以改变薄膜材料的沉积速率和性能。
低压化学气相沉积装置与一般的常压热壁式装置的主要区别在于它需要一套真空泵系统维持整个系统的工作气压。
4.快速热化学气相沉积(RTCVD)RTCVD(Rapid Thermal Chemical Vapour Deposition)是常压CVD(APCVD)的一种,它靠光加热或射频感应加热衬底和衬底支持物,使温度中央快速达到反应温度。
实验室用的RTCVD是石墨舟射频(RF)加热方式。
RTCVD的反应室内壁的温度较低,没有足够的能量发生淀积反应,因此RTCVD属于冷壁反应器。
与高温沉积多晶硅薄膜的其它常用工艺:如低压CVD(LPCVD)与液相外延(LPE)相比,TRCVD的主要优点是设备相对简单,沉积速率高,升降温速度快(因而能耗较少),反应简单,有多种气源组合可供选择。
有的沉积方法在生长速率上存在强烈的各向异性(如LPE),这种效应在CVD过程中小得多,这一点对于在多晶或异质衬底上的外延生长薄膜很重要。
CVD沉积晶体硅薄膜是从气相生长晶体的复相物理一化学过程。
生长过程可以分为以下步骤:1)反应气体输运到沉积区并扩散到衬底的表面;2)反应物分子吸附在衬底表面;3)反应物分子间的化学反应。
生成的硅原子在表面迁移、聚集、沉积;4)反应的副产物脱吸附并离开沉积区。
以上步骤接连发生,总的沉积速率由最慢的步骤决定,所以,薄膜沉积的速度主要由上述步骤1、3决定。
一般,温度较低时,反应物分子间的化学反应决定了薄膜的生长速度(这种情况称反应速度控制),温度较高时,沉积速度将不再受化学反应速度的控制。
这时,到达衬底表面的反应物分子的数量将决定沉积速度的大小(这种情况称质量传输控制)。
二、固相晶化非晶硅薄膜法(SPC)固相晶化技术(SPC)是指通过使固态下的非晶硅薄膜的硅原子被激活,重组,从而使非晶硅薄膜转化为多晶硅薄膜的晶化技术。
它的特点是非晶固体发生晶化的温度低于其熔融后结晶的温度。
低造价太阳电池多晶硅薄膜,一般用廉价的玻璃作为衬底,硅烷气体作为原料,用PECVD方法生长a-Si:H薄膜,然后用热处理的方法转化为多晶硅薄膜。
这种技术的优点是能制备大面积的薄膜,可进行远原位掺杂,成本低,工艺简单,易于形成生产线。
常规高温炉退火、快速热退火、金属诱导晶化、微波诱导晶化等都属于固相晶化的范畴。
1.常规高温炉退火该方法是在真空或者高纯氮气保护下把非晶硅薄膜放入炉子内退火,使其由非晶态转变为多晶态。
它是利用非晶硅薄膜再结晶制备多晶硅薄膜的一种最直接、最简单的方法,也是人们最早采取的一种晶化技术。
多晶硅薄膜的晶粒尺寸除了受温度的影响外,与初始的非晶硅膜的结构状况也有密切的关系。
制备非晶硅薄膜的方法很多,如磁控溅射法、CVD沉积法等。
一般情况下,利用CVD方法所制备的a-Si:H薄膜材料经过固相晶化后,能够得到质量较好而晶粒尺寸较大的多晶硅薄膜。
这是因为该方法所沉积的非晶硅薄膜当中含有大量氢。
事实上,沉积条件对所制备的a-Si:H薄膜中H的含量及其与Si的结合方式对后续的固相晶化过程和多晶硅薄膜材料的性质起着关键的影响。
a-Si:H薄膜的沉积温度越低,固相晶化后所得的多晶硅薄膜材料的晶粒就越大。
这是因为较低的沉积温度导致了非晶硅材料中较高的无序状态,使得成核固相晶化法(SPC)制备多晶硅薄膜的研究密度较低,从而晶粒尺寸较大。