常减压装置腐蚀分析与防护措施
《2024年石油炼制常减压装置腐蚀与防腐》范文

《石油炼制常减压装置腐蚀与防腐》篇一一、引言石油炼制过程中,常减压装置是关键的工艺流程之一。
由于该装置长期在高温、高压以及腐蚀性环境中工作,导致设备受到严重的腐蚀。
这不仅影响装置的正常运行,还会对炼油厂的生产安全和经济效益造成重大影响。
因此,深入研究常减压装置的腐蚀问题及其防腐措施,对于保障石油炼制的安全和效率具有重要意义。
二、常减压装置的腐蚀原因及类型1. 腐蚀原因(1)化学腐蚀:在炼油过程中,常减压装置接触到的原油、气体和化学品等含有各种腐蚀性成分,如硫化物、氯化物等,这些物质与金属表面发生化学反应,导致设备腐蚀。
(2)电化学腐蚀:由于设备和管道中存在电位差,使得金属表面发生电化学反应,导致金属腐蚀。
(3)高温腐蚀:常减压装置在高温高压环境下运行,使得金属表面发生氧化、碳化等反应,加剧了设备的腐蚀。
2. 腐蚀类型(1)均匀腐蚀:指金属表面在化学或电化学作用下,发生全面均匀的腐蚀。
(2)局部腐蚀:指金属表面局部区域的腐蚀速度明显高于其他区域,如点蚀、缝隙腐蚀、应力腐蚀等。
三、常减压装置的防腐措施1. 材料选择:选用耐腐蚀性能好的材料,如不锈钢、合金钢等,以提高设备的耐腐蚀性能。
2. 表面处理:对设备表面进行喷涂、镀层等处理,以隔离介质与金属的接触,减缓腐蚀速度。
3. 工艺控制:通过优化工艺参数,如温度、压力、流速等,减少设备在腐蚀性环境中的暴露时间。
4. 添加缓蚀剂:在原油中添加缓蚀剂,减少硫化物、氯化物等对设备的腐蚀。
5. 定期检查与维护:定期对设备进行检查和维护,及时发现并处理腐蚀问题,防止事故发生。
四、实例分析以某炼油厂的常减压装置为例,该装置在运行过程中发现设备局部出现严重腐蚀现象。
经过分析,主要原因包括设备材料选择不当、工艺参数控制不严格以及介质中腐蚀性成分含量较高等。
针对这些问题,该炼油厂采取了以下措施:1. 更换耐腐蚀性能更好的材料,如不锈钢等;2. 对设备表面进行喷涂处理,以隔离介质与金属的接触;3. 优化工艺参数,如降低温度、压力和流速等;4. 在原油中添加缓蚀剂,减少介质中的腐蚀性成分含量;5. 定期对设备进行检查和维护,及时发现并处理腐蚀问题。
常减压装置常压塔顶腐蚀原因分析与防护

特#设备安全风险评估与安全分析常减压装置常压塔顶腐蚀原因分析与防护鞠舰波(中国特种设备检测研究院北京100029)主商要:本文以某炼油厂常减压塔顶冷凝冷却系统为研究对象,对该系统发生腐蚀泄漏进行原因分析。
通过分析其腐蚀原因,提出了控制腐蚀的措施和方法,从而达到设备长周期运转的目的。
关键词:常减压装置腐蚀分析泄漏Cause Analysis and Protection of Top Corrosion of Atmospheric Pressure Towerin an Atmospheric and Vacuum DeviceJu Jianbo(China Special Equipment Inspection&Research Institute Beijing100029) Abstract This paper takes the condensation and cooling system on the atmospheric and vacuum tower top of a refinery as the research object,and analyzes the corrosion cause of the corrosion leakage of the system.By analyzing the reason of corrosion,the measures and methods to control corrosion are put forward,so as to achieve the purpose of long cycle operation of equipment.Keywords Atmospheric and vacuum equipment Corrosion analysis Leakage中图分类号:X933.4 文献标志码:B文章编号:1673-257X(2022)(M-0070-03 DOI:10.3969/j.issn.1673-257X.2022.01.016随着国内各企业炼制劣质原油数量的增加,常减 压装置的腐蚀逐渐加重,由此带来的不利影响亦越来 越明显,因此开展劣质原油加工过程中的腐蚀特征 及防护技术研究成为-件刻不容缓的课题。
炼油厂常减压装置常见腐蚀与防护措施探析

炼油厂常减压装置常见腐蚀与防护措施探析摘要:炼油厂常减压装置是炼油工艺中关键的环节,负责对原油进行初步加工。
然而,由于原油成分复杂和加工过程中温度、压力等条件的变化,装置部件容易受到腐蚀的影响。
腐蚀会导致设备损坏、生产效率降低,甚至可能引发安全事故。
因此,了解常减压装置的常见腐蚀类型及防护措施具有重要意义。
关键词:炼油厂;常减压装置;常见腐蚀;防护措施引言常减压装置作为炼油厂的“龙头”装置,是原油加工的第一道工序。
原油劣质带来的问题首先反映在常减压装置上,使装置的生产、安全、设备受到严重威胁,对下游装置也会产生不良影响。
为解决这一问题,要加强对常减压装置腐蚀与防护措施的管理,从而有效缓解常减压装置的腐蚀,避免出现严重的生产安全事故,确保装置安全、平稳、长周期运行。
1炼油厂常减压装置腐蚀机理(1)化学腐蚀:化学腐蚀是由于金属与周围介质(如气体、液体或固态沉积物)直接发生化学反应而引起的。
在炼油厂常减压装置中,化学腐蚀主要发生在高温、高压的环境下。
常见的化学腐蚀介质有硫化氢、氢氧化物、有机酸、无机酸等。
化学腐蚀的速率受到温度、压力、金属材料、腐蚀介质成分等多方面因素的影响。
(2)电化学腐蚀:电化学腐蚀是金属在电化学作用下发生的腐蚀现象。
在炼油厂常减压装置中,电化学腐蚀主要发生在金属与电解质溶液接触的部位。
电化学腐蚀的类型包括析氢腐蚀、吸氧腐蚀等。
电化学腐蚀的严重程度受到电解质溶液的成分、金属材料的耐腐蚀性、环境温度和湿度等因素的影响。
(3)微生物腐蚀:微生物腐蚀是由于微生物生长活动引起的金属腐蚀。
在炼油厂常减压装置中,微生物腐蚀主要发生在含有微生物的介质中。
微生物腐蚀的类型包括厌氧腐蚀、好氧腐蚀等。
微生物腐蚀的严重程度受到微生物种类、生长环境、金属材料等因素的影响。
2炼油厂常减压装置腐蚀的主要原因2.1原油中的腐蚀性物质原油中含有的硫、酸、氯等腐蚀性物质在加工过程中会对设备产生腐蚀。
尤其是高硫、高酸原油,其腐蚀性更强,容易导致设备表面的金属材料脱落。
常减压装置存在的腐蚀及应对措施分析

95前言随着加工原油的劣质化,原油中硫、氯含量和酸值升高给常减压蒸馏装置带来的腐蚀问题已严重影响装置的安全平稳运行。
一、常减压装置存在的腐蚀1.低温部位腐蚀低温部位腐蚀主要集中在初馏塔、常压塔顶的挥发线上,主要有HCl腐蚀、湿H 2S腐蚀、NH 4Cl盐垢下腐蚀等。
(1)HCl腐蚀原油中的MgCl 2和CaCl 2在水中容易水解生成HCl,HCl在塔内高于水露点温度不会导致金属材料腐蚀问题,在等于或低于水露点的温度,HCl溶于水形成盐酸,对金属材料会发生强烈的腐蚀作用。
塔内初凝区是腐蚀性最强的环境,由于液态水刚刚生成,气态HCl溶于水滴生成浓度很高的盐酸,此处pH值可低至1~2,对塔壁或管线会造成强烈腐蚀。
常减压装置中塔顶挥发线注水点后和塔顶油气第一台换热器就属于上述初凝区,塔顶注水点通常注入温度不高的净化水,若注入水后水易液态的形式存在于塔顶,将可能造成塔顶露点腐蚀;而塔顶油气第一台换热器,如本装置初顶换热器(E-54)、常顶换热器(E-1),均给原油进行加热,将原油温度由45℃升高到78~82℃,而塔顶油气也由110~135℃冷却到80℃左右,回收了塔顶油气中的显热和相变热,但由于换热器管程中有相变的发生,易形成高浓度的盐酸小水滴,将对换热器管束造成点蚀或坑蚀。
(2)H 2S腐蚀H 2S腐蚀是减压塔顶和冷凝冷却部位的主要腐蚀,H 2S 主要来源是加工过程中的硫化物分解而形成。
低温段的H 2S腐蚀主要表现为均匀性腐蚀及湿H 2S应力性腐蚀开裂。
湿H 2S应力腐蚀开裂有氢鼓泡、氢至开裂、硫化物的应力腐蚀开裂及应力向导氢开裂。
一定温度时。
在硫化氢、水和氯化氢共同存在的相互作用下,会促进腐蚀加剧。
(3)NH 4Cl盐垢下腐蚀电脱盐后,原油、中和剂及注水(净化水)中氮化物部分转化为NH 3,原油中的无机氯(主要是CaCl 2、MgCl 2)和有机氯转化为HCl,在常压塔顶操作温度低于NH 4Cl盐结晶温度时,则NH 3和HCl从气相直接结晶生成NH 4Cl盐。
《石油炼制常减压装置腐蚀与防腐》

《石油炼制常减压装置腐蚀与防腐》篇一一、引言在石油炼制过程中,常减压装置作为关键的工艺流程之一,其稳定运行对于整个炼油厂的效益和安全至关重要。
然而,由于常减压装置在运行过程中会接触到各种腐蚀性物质,如硫化物、氯化物、水等,这些物质的存在往往会导致设备的腐蚀问题。
腐蚀不仅会降低设备的使用寿命,还可能引发安全事故,影响整个炼油厂的稳定运行。
因此,研究常减压装置的腐蚀与防腐问题具有重要的现实意义。
二、常减压装置的腐蚀问题1. 腐蚀类型及原因(1)电化学腐蚀:在常减压装置中,由于金属表面与介质之间存在电位差,容易发生电化学腐蚀。
这种腐蚀主要是由于介质中的电解质与金属发生反应,导致金属表面形成原电池效应。
(2)化学腐蚀:由于介质中的化学物质与金属直接发生化学反应,导致金属表面形成腐蚀产物。
例如,硫化物、氯化物等化学物质对金属的腐蚀作用较强。
(3)冲刷腐蚀:在常减压装置中,由于介质流动的冲击作用,金属表面会受到冲刷,从而加剧腐蚀程度。
2. 腐蚀对设备的影响设备受到腐蚀后,其强度和密封性能会降低,甚至可能导致设备泄漏、穿孔等严重后果。
此外,腐蚀还会导致设备的使用寿命缩短,增加维护成本和停机时间,影响炼油厂的稳定运行和经济效益。
三、防腐措施1. 材料选择:选用耐腐蚀性能好的材料是防止常减压装置腐蚀的有效措施。
如选用不锈钢、合金钢等耐腐蚀性较强的材料,可以有效地提高设备的耐腐蚀性能。
2. 工艺优化:通过优化工艺流程和操作条件,减少介质中的腐蚀性物质含量,降低设备的腐蚀程度。
例如,通过控制温度、压力、流速等参数,避免介质中的化学物质与金属直接接触。
3. 防腐涂层:在设备表面涂覆防腐涂层,可以有效隔离介质与金属的接触,从而减缓设备的腐蚀速度。
防腐涂层应具有良好的耐腐蚀性、耐磨性和附着力。
4. 阴极保护:通过在金属表面施加阴极电流,使金属成为阴极而避免电化学腐蚀。
这种方法需要专业的设备和技术支持,但可以有效保护设备免受电化学腐蚀的侵害。
常减压装置的腐蚀与防护分析!

原油之所以对装置具有一定的腐蚀性,主要是因为其中含有一定的盐、硫物质。
我国油田油品含有较高的硫,进口原油往往高酸高硫,所以原油生产中,常减压装置时刻处于腐蚀环境中。
另外石化工艺流程复杂,在高温高压环境中,腐蚀性介质可能会发生一系列化学反应,给设备带来更加严重的腐蚀环境。
实际化工生产中,常减压装置通常被作为第一加工装置,原油劣质化问题会首先反映到这类设备中,同时常减压设备会对原油进行脱盐脱硫处理,其工作效率也决定了原油是否会对后续设备带来腐蚀性影响。
可以说,加强对常减压装置腐蚀问题的分析,对于保持整套设备平稳运行具有积极的意义。
1、常减压装置中常见的腐蚀介质(1)化工腐蚀介质中,氯化物是非常常见的一种,原油经过初步的脱水处理后,依然会有少量的水残留下来,残留水分一般含有由氯化物构成的盐类成分,比如,氯化钠、氯化镁、氯化钙等,这些盐类成分受热后,会发生化学反应—水解反应,产生氯化氢,氯化氢具有强腐蚀性。
(2)硫化物也是一种常见的腐蚀性介质,一般来说,硫化物的腐蚀性的发挥往往受环境温度因素的影响。
原油中所含有的硫化物一般具有不稳定性,如果环境温度升高,这类硫化物就会分解生成分子量相对较小的硫化物。
原油生产中,元素硫与硫化氢之间可以相互转化,在转换过程中,硫化物分布在装置的不同部位,比如具有强腐蚀性的硫化氢一般聚集在装置低温部位,而硫元素则聚集在装置的高温部位。
(3)除了上述两种腐蚀性物质,有机酸、游离状态的氧、二氧化碳、水也会对常减压装置造成腐蚀性影响。
2、常减压装置腐蚀类型2.1 低温露点腐蚀引起这类腐蚀的主要原因是原油中含有盐类成分,主要发生在常减压蒸馏塔顶管部位以及初馏塔。
原油生产加工中,原油中的盐类物质发生水解反应,生成氯化氢,比如:在系统中,如果HCl以气体形式存在,其具有的腐蚀性几乎可以忽略,但是当氯化性进入到冷凝区后,遇到水,迅速溶于水形成稀盐酸,经测定,冷凝区域的稀盐酸浓度处于1%-2%,对于设备来说,系统内部就形成了强酸性腐蚀环境,继而给系统带来严重的腐蚀性影响。
常减压装置腐蚀与防护

氮,%
0.06~0.24 1.06
0.40~0.61 0.36~0.38
0.43 0.36 0.40~0.63 0.36 0.21 0.63 0.75 0.056 0.08
0.31~0.35 0.41 0.13 0.08
酸值,KOH/g
0.016 1.26 0.98~2.26 4.50~4.70
④ 炼制管输原油减压塔其腐蚀较高硫低酸值原油严重,塔体改用20g+ 00Cr18Ni12Mo2Ti复合板可以拟制腐蚀,但进料处塔壁的冲蚀不可避 免。
12
3 腐蚀形态、部位及原因
3.2高温(240~425℃)部位的高温硫的均匀腐蚀及环烷酸的沟槽状腐蚀
➢常减压加热炉炉管腐蚀
低硫高酸值原油和高硫低酸值原油及高硫高酸值原油炼油厂, 加热炉炉管腐蚀情况:
根据原油中含硫及酸值的高低,原油可分为
✓ 低硫低酸值原油(S0.1~0.5%.1~0.5%,酸值>0.5KOH/g),如辽
河原油,新疆原油
✓ 高硫低酸值原油( S>0.5%,酸值≤0.5KOH/g),如胜利原
油
✓ 高硫高酸值原油(S>0.1~0.5%,酸值>0.5KOH/g),如
10
3 腐蚀形态、部位及原因
3.2高温(240~425℃)部位的高温硫的均匀腐蚀及环烷酸的沟槽状腐蚀
➢ 常压塔的腐蚀
① 炼制大庆原油常压塔使用A3钢基本上无腐蚀和 腐蚀轻微
② 炼制辽河原油常压塔蒸发段塔壁及其上下各层 塔盘碳钢腐蚀率大于3mm,腐蚀形态为“沟槽 状”,其余部位腐蚀轻微
③ 炼制胜利原油和管输原油,常压塔及其内构件 腐蚀相对轻微,可用碳钢。为防止和减缓进料 段塔壁冲蚀和腐蚀,防冲板在原基础上长宽方 向各延长1倍,并改用0Cr13或0Cr18Ni9Ti
石油化工常减压装置腐蚀与防护

石油化工常减压装置腐蚀与防护摘要:为了更好地促进石化企业的发展,在企业发展的同时保护人民的财产、生命、健康和安全,需要有关人员采取有效措施保护常减压装置,减少设备应用中的腐蚀现象,并采取有效措施处理腐蚀问题,做好常减压设备的防腐工作。
本文对石油化工常减压装置腐蚀与防护进行了探讨。
关键词:石油化工;常减压装置;腐蚀;防护措施1化工常减压装置腐蚀介质在众多腐蚀介质中,氯化物对腐蚀的影响非常显著,是一种典型的化学腐蚀产物。
原油脱水后,往往会留下少量水。
在许多情况下,水中含有一些盐,它们是氯化钙、氯化镁和氯化钠。
氯化钙和氯化镁在加热环境中会发生水解,形成腐蚀性氯化氢。
此外,在许多腐蚀性介质中,含硫化合物也非常常见,需要引起重视。
硫化氢的腐蚀效果与生产环境温度直接相关。
硫化物与热的关系并不稳定。
温度升高后会出现各种分子硫化物。
硫化氢和单质硫相互转化,硫化氢在空气氧化作用下可以变成单质硫。
此时,元素硫与原油烃类反应后,会出现硫化氢。
一系列的过程使硫化氢在高温和低温下分布在不同的位置。
低温腐蚀主要是硫化氢腐蚀,高温腐蚀主要是元素硫腐蚀。
另外,有机酸的腐蚀性也很强。
有机酸由脂肪酸和环烷酸组成。
原油中的水、二氧化碳和氧气进入真空装置后会从真空装置逸出。
冷凝系统出现氢去极化腐蚀和氧去极化腐蚀。
2石油化工常减压装置腐蚀的原因2.1低温露点在石油化工生产中,常减压装置最常见的腐蚀是低温露点腐蚀。
这种腐蚀现象的出现与原油含盐量密切相关。
一般来说,这种盐是以水包裹体的形式存在的,主要包括氯化镁、氯化钙和氯化钠。
事实上,这些物质并不具有腐蚀性,但它们在高温下会分解,这使得许多腐蚀性物质如氯化氢出现。
原油中含有大量硫化物,在加热作用下会产生硫化氢气体。
硫化氢气体和氯化氢等气体进入水中后,会有强腐蚀性物质。
一般来说,常减压蒸馏装置的盐酸浓度不高,一般只有1%~2%。
但盐酸本身的浓度具有很强的腐蚀性,常减压蒸馏装置会受到硫化氢的严重影响。
炼油厂常减压装置常见腐蚀与防护措施探析

炼油厂常减压装置常见腐蚀与防护措施探析摘要:近年来,我国的炼油厂建设不断增加,但是在炼油厂中,由于原油成分各不相同,尤其是高硫原油对设备的腐蚀较为严重。
因此,本文首先分析加热炉及烟风换热系统腐蚀情况检查,其次对原油炼化生产中对常减压装置带来的腐蚀分析,最后就常减压装置的腐蚀防护措施进行研究,希望能够为相关研究提供一定的参考。
关键词:炼油厂;常减压装置;腐蚀;防护引言常减压装置是炼油厂生产的重要装置,该装置在生产运行时,很容易受到腐蚀影响,尤其是原油中的一些物质会在炼油生产条件下加剧对常减压装置的腐蚀,对炼油生产安全带来非常严重的影响。
为解决这一问题,有必要加强对常减压装置腐蚀与防护措施的探索分析,从而有效缓解腐蚀对常减压装置带来的负面影响,加强对装置的防护,避免出现严重的生产安全事故,推动炼油厂生产经营实现更好的发展。
1加热炉及烟风换热系统腐蚀情况检查加热炉辐射室炉墙总体较好,只有两路进料顶部衬里有部分脱落,分别进行了补修、清理。
空气预热器系统低温露点腐蚀较为严重,换热管翅片上附着黄色黏稠物质较多,由于管束交错排列,比较紧凑很难清理。
另外,换热管积灰现象比较明显,位于空气预热器顶部的激波吹灰器套管有腐蚀漏洞,空气预热器出口至引风机入口内衬脱落,分别进行了清扫、更换及修补。
引风机本体腐蚀漏点较多,直接焊接整块钢板进行修补,涂有机硅高温漆对手动调节阀及引风机本体进行防腐。
2原油炼化生产中对常减压装置带来的腐蚀分析原油的存在,对常减压装置带来的腐蚀包括以下几点:(1)在常减压装置中,一般会存在很多焊接接头,这些接头必然会存在焊缝。
从炼油生产实践来看,原油对这些焊接接头的焊缝带来的腐蚀影响比较大。
因为在接头焊接时,带来的高温降低了焊接接头处的耐腐蚀性。
(2)常压塔腐蚀。
常压塔是常减压装置的关键组成部分,主要由碳钢与不锈钢衬里材料组成。
但在该装置低温运行时,很容易遭受低温腐蚀影响,出现裂纹,影响装置安全性。
常减压装置腐蚀分析与防护措施

・ 3 9・
常减压 装置腐蚀分析 与 防护措施
王 慧
ห้องสมุดไป่ตู้
( 中 国石 油哈 尔滨 石化 分公 司, 黑龙 江 哈 尔滨 1 5 0 0 5 6 )
摘 要: 低 压清油和高温重油是常减压装置 中设备 常常被 腐蚀 的两大对 象, 本文主要 对其 腐蚀原理进行 了分析 , 并提 出有针对性 的腐 蚀 防护 措 施 和 思考 。 关键词: 常减压装置; 腐蚀 分析; 防护措施; 硫 腐蚀; 露点腐蚀 H: S—HC I —H2 0 露 割箭虫 发生的主要部位, 其腐蚀现象主要是由于 1 主要腐 蚀部位 和腐蚀类型分析 所含的无机盐( 以 常减压装置是炼油 厂各个没备中最腐蚀程度最为严重的龙头装置, 原油中的含盐物质而引发的。原油的加工过程中 , 特别是现在的原油重质化和劣质化的程度逐渐加深 ,原油中含盐量和含 N a C 1 、螈 c f 2 、C a 三种成分为主 ) 以及原油开采过程中所添加的有机氯 生的 HC I 而造成的。而在对原油进行蒸馏 硫量的不断飙升都会加重常减压装置的腐蚀程度。就目前的事故统汁来 化物发生水解而产生具有腐蚀I 看, 由于常减压腐蚀而造 或的工业事故率直线 匕 升, 而这些事故的频繁发 操作时 , H C l 与原油中的硫化物加热分解而产生的 H: S一同存在于蒸馏 培珂 嘴 却系统当中。不管是 HC I还 H S, 该 勿 贡以气体_ 威 . 存在于 生, 也对炼油装置开工效率造成了很大的影响。 通常隋况下,常减压装置的高温重油部位组件和低温清油部位组件 珂 晓中时, 研 她 的腐蚀陛。而在露 位置 即冷凝 区出现液体冰 会立即溶于水中, 形成对设备腐蚀较为强烈的、 浓度在 1 %到 的稀 是腐蚀隋况较为集中的组件部分 ,高温重油组件部分的腐蚀贝 0 是 因为含 时, 这一现象便是造成常减压装置初馏塔、 常压塔 、 减压塔塔顶以及相 硫原油和高酸值反应产生 的S—H: S —R C OO H 腐蚀环境而造成的, 高 盐酸, 与此同时, H S 存在于该 温环烷酸腐蚀和高温硫腐蚀是主要腐蚀类型 , 而低温清油部位组件是因 对应的冷凝冷却系统设备病蚀现象的主要因素。 形成 — H C I ~ 0 的腐蚀环境, 形成循环腐蚀状态 , 这种循 为原油中硫化物和氯化物受热分解而产生的 Hz S—HC I —H 2 0形成的 环境中, 腐蚀环境而造成的。除此以外, S O: 、 D 3 一日 D 类型的腐蚀也较为常 环也l 是力 口 工含硫原油腐蚀加剧的主要因素。 反应产生的 F e C I : 易溶于水 , 会使得硫酸亚铁形成的保护膜被剥落, 形成了塔顶腐 见, 而 这两种腐 蚀物质 通常都 出现在 n Ⅱ 热 炉空气 预热器和 对流室炉 管 中。 当其被水流冲走时, 下面, 笔者就结合常减压装置的主要腐蚀部位进行总结归纳, 并通过引用 蚀最为 突出的露 点腐蚀现象 。 3 腐蚀 防护措施 建议 成因进行分析,就止 I = 圭 黾 出—些较为适用的 3 . 1 对‘ ‘ 一脱 三注 ” 工艺 进行有效调整 防护措施 。 脱三注’ 堤蒸馏装置中最为中心的工艺防腐措施 , 其 内容包括 : 原 2常减压装置腐 蚀分析 2 1 高温 S — H 2 S — R C O O H 腐 蚀分析 油物质脱盐脱水、 缓蚀剂注入、 中和剂注入和水注 ^。其中, 原油物质脱盐 ( 1 ) 电脱盐温度的提 2 l - 1 高温硫腐蚀分析。原_ 油 中部分有机硫化物在 2 、 4 0 以上的环境 效率的提高应该以电脱盐操作工艺的优化 为切人点 : 中, 转换为元素硫和 , 与硫醇、 活 陆硫和H: S在高温环境中形成腐 高 。环 境温度 的升高能 够降低 原油的粘度 , 进而减 少水滴运 动 的阻力 , 并 促进磁孑 L 水滴的聚结。 而温良过高则会引起水的 蚀环境, 其腐蚀程度由原油中的活陆疏( 包括单质硫、 硫化氢和硫醇 ) - #t ' i t 目降低油水界面的张力, 脱盐压力增加的同时油水的乳化也会变得十分容易 , 因此应该将温 的大小而决定, 活f 生 硫的含量较多则会加速腐蚀行为, 该行为在 2 4 0 ' : C ' 到 汽化, 4 3 0 ' t 2 之间时表现十分明显 , 而温度超过了 4 8 0 ' C ' : 时, 腐蚀行为逐渐减弱, 度控制在 1 2 0 到1 4 0  ̄ C 之J 司; ( 2 ) 破乳刺的合适选择。 市场中的破乳刺都具 每种原油都有与其对应的最佳破乳剂。混合原油由于其 由此可知 , 该环境的腐蚀程度当环境温度在 2 4 0  ̄ C 到4 8 0 " 1 2 司。而活 陛 有一定的选择 , 硫化物(  ̄ - r N0 是单质硫、 硫化氢和硫醇) 等成分与金属发生反应时, 会形成 性质较为复杂, 所以要对其进行专项正交实验, 并通过 自动注入系统来对 进而提升脱盐效率; ( 3 ) 注水量的 像硫化亚铁—类的腐蚀物质。 腐蚀刚开始时反应速率 陕, 当进行到—定时 破乳剂注入的成分和分量进行严格控制, 期时由于 F e S 形成的保护膜减缓了窗蚀速率而当高速流体中的环烷酸与 适当提高。 水量的适当增加能够 寸 原油乳化液的稳定跛 f 洧 所提升, 但 水的水质和 p h 值的影响。当下脱盐一、 二级注水都是用净 其发生反应时, F e S 保护膜会逐渐消失 , 并且与反应析出的 日: S 形成循环 是考虑到注 ^ 腐蚀, 这一现象是高温硫腐蚀的主要特征。对此现象稍加研究可知, 高温 化 水进行 注入 , 水 质和 p h 值 都控 制在 规定 范 围内 , 注水 量则 按照 工艺指 硫腐蚀的影响因素有介贡流速、温度、环烷酸含量大小以及组件材贡等 标 的 3 %到 5 %进行控 制。 3 . 2 腐 蚀在 线监 测系统 的安装 等, 常减压装置中出现此类腐蚀的部件有: 转油线、 炉管、 塔进料组件的上 系统, 其系统主要由监测探针、 7 1 - :  ̄ 下堵盘 、 边料 殴塔壁 及内部构. f 牛 以及其他 癖 温管线组僻翻 等。 2 . 1 . 2 高温环烷酸腐铤 H 分析。 1 7 7 ℃到 3 4 3 ' : 1 2 之间是环烷酸的沸腾 范 器和数据转换模块等组件构成 , 对设备和管道 的壁厚 、 局部 p h 值等腐蚀 滥控 , 并通过局域网上传至腐i 虫 葡苴 决策服务器 , 为其 围, 其相对分子量的变化范围较大, 3 0 0 到4 0 0 是较为常见的数值。 该成分 状态进行动态实拍 在原油中的酸 『 生 物质中的总含量达到 9 O %( 质量分数 占比) 左右, 因此环 调整配备提供在线动态 息, 常三线 、 减二线、 减三线 、 减四线等重要部位 从而监控常减压装置的高温硫和环烷酸腐蚀 , 保证了 烷酸也成为了石油酸的代名词。 一 旦原油中的总酸值大于了0 . 5 m g K O H / g 安装高温电感探针, 时, 就会引起管线腐蚀, 因此炼油行业中将总酸值大于 0 . 5 m g K O H / g 的原 防腐锚} } 昔 施的及时l 生 和有效陛。 参 考文献 油成为高酸原油。事实研究证明, 环烷酸对管线造成腐蚀较小时的环境温 1 ] 李志平. 常减压装置的腐蚀与应对措璇 . 安全、 健康和环境, 2 0 0 7 ( 9 ) . 度在 2 2 0 。 c 以下 , 一旦温度达到 2 2 0 " C 或更高时, 环烷酸的腐蚀速率会随 【 着环境温度的升高而逐渐变 决; 环境温度在 2 7 0 ℃到 2 8 0 ℃之间时, 腐蚀 冈卫四凤. 加工高酸原油的常减压装置的防腐研究 石油化工技 术与经 达到第— 峰值, 环境温度高于 2 8 0 q C 后, 环烷酸的腐蚀速率有所减缓, 在 济, 2 0 1 1 3 ] 韩巍, 孙文君袁 军, 郭雷. 炼油常减压装置常顶 系统腐蚀分析及防护口 l 全 环境温度达到 3 5 0 ℃时, 腐蚀达到第 二个峰值; 环境温度超过 4 0 0 " C 时, 环 『 2 0 1 1 烷酸会被分解 , 腐蚀现象也随之消失 , 其腐蚀类型属于高温化学腐蚀。在 面腐蚀控制 , 此高温环境中, 环烷酸除了与铁质金属直接反应发生腐蚀现象以外, 还会 与腐蚀产物硫化亚铁发生反应, 形成能溶于油质的环烷酸铁。 该反应不仅 使 得 有_定保护 作用 的硫化亚铁 膜 捌 破 坏 ,同时 其成分 中游 离 出来 的硫化氢又会对金属表面进行更深层的腐蚀。对环烷酸腐蚀现象有关的 因素有: 原油温度、 流速以及油质的酸值和硫质量浓度等等。此类腐蚀现 象发生的主要部位则在塔内填料和塔盘、 转油线 、 加热炉炉管、 控制阀下
常减压装置腐蚀分析与防护措施
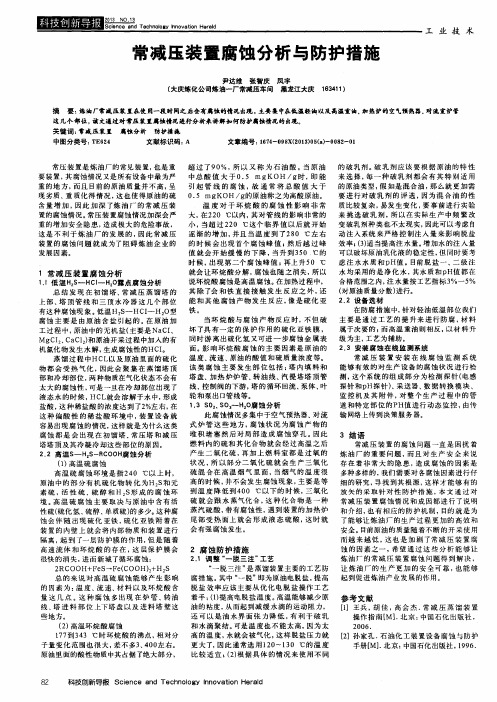
大, 在2 2 0 ℃以 内, 其 对 管 线 的 影响 非 常 的 小, 当超 过 2 2 0 ℃这 个 临 界 值 以后 就 开 始
这 是 不 利 于 炼 油 厂 的发 展 的 , 因此 常 减 压 逐 渐 的 增 加 , 并且 当温 度 到 了2 8 0 ℃左 右 装 置的 腐 蚀 问题 就 成 为了 阻碍 炼 油 企 业 的 的 时 候 会 出现 首 个 腐 蚀 峰 值 ; 然后 越 过 峰 发 展因 素。 值 就 会开 始缓 慢 的 下 降 , 当升 到3 5 0 ℃的 时候, 出 现 第 二个 腐 蚀 峰 值 ; 再上 升5 0℃ 就 会 让 环烷 酸分 解 , 腐 蚀 也 随 之 消失 , 所 以 水 均 采 用的 是 净 化 水 , 其水 质 和 p H值 都 在 1 常 减 压 装置 腐 蚀 分析 注 水 量按 工艺 指 标 3 %一 5 % 说 环烷 酸 腐 蚀是 高温 腐蚀 。 在 加 热 过程 中, 合 格范 围之 内, 1 . I低 温 H s —H c I —H O 露 点 腐蚀 分析 还 ( 对原 油质量 分 数) 进行。 总结 发现在 初馏塔、 常 减 压 蒸 馏 塔 的 其 除 了会 和 铁 直 接 接 触 发 生 反 应 之 外 , 像 是硫 化 亚 2 . 2 设 备选 材 上部、 塔 顶 管 线 和 三 顶水 冷 器 这 几 个 部 位 能 和 其 他 腐 蚀 产物 发 生 反 应 , 在 防腐 措 施 中, 针对 轻油 低 温部 位我 们 有 这种 腐 蚀 现 象 。 低温 H 2 S — HC I —H 2 0 型 铁 。 当 环 烷 酸 与 腐 蚀 产 物 反 应 时 , 不 但 破 主 要 是 通 过 工 艺 的 提 升 来进 行 防 腐 , 材 料 腐 蚀 主 要 是 由原 油 含盐 引起 的 。 在 原 油 加 属于 次 要的 ; 而 高 温 重 油则 相 反 , 以材 料 升 工过 程 中 , 原油 中 的无 机 盐 ( 主 要 是 Na C I 、 坏 了具 有 一 定 的 保 护 作 用 的硫 化 亚 铁 膜 , 工艺 为辅 助 。 Mg C I 2 、 C a C 1 2 ) 和 原 油开 采过 程中加 入 的有 同时 游 离 出硫 化 氢 又 可进 一 步 腐蚀 金 属 表 级 为主 , 面。 影 响 环 烷 酸 腐 蚀 的 主 要 因 素是 原 油 的 2 . 3 安装 腐蚀 在 线监 测 系统 机氯化 物 发 生水 解 , 生 成 腐蚀 性 的HC I 。 常 减 压 装 置 安 装 在 线 腐 蚀 监 测 系 统 流速、 原油 的 酸 值 和 硫 质量 浓 度 等。 蒸 馏 过 程 中HC L 以 及 原 油 里 面 的硫 化 温 度 、 塔 内填 料 和 能 够 有 效 的 对 生产 设 备 的 腐蚀 状 况 进行 检 物 都 会 受 热 气化 , 因此 会 聚 集 在 蒸 馏 塔 顶 该 类 腐 蚀 主 要 发 生 部 位 包括 : 加 热炉炉管、 转油线、 汽 提 塔 塔 顶 管 测 , 这 个 系统 的 组 成 部 分 为 检 测 探 针 ( 电感 部和 冷 却部 位 , 两 种 物 质在气化 状 态 不会 有 塔 盘 、 控制 阀 的下 游 , 塔 的 循环 回 流、 泵体 、 叶 探 针 和 p H探 针 ) 、 采 送 器、 数据转换模块 、 太大 的 腐 蚀 性 , 可 是 一旦在 冷 却 部位 出 现 了 线、 监 控 机 及其 附 件 , 对 整 个 生 产 过 程 中的 管 轮 和 泵 出口管 线 等。 液 态水 的 时 候 , HC L 就会 溶 解 于水 中, 形 成 道和 特 定 部 位 的P H值 进 行 动 态 监控 , 由传 . 3 S O 2 、 S O 3 一H 2 0 腐蚀 分 析 盐酸, 这 种 稀盐 酸 的浓 度 达 到 了2 % 左右, 在 1 此 腐 蚀 情况 多集 中于 空 气预 热器 对 流 这 种 偏 酸 性 的 稀 盐 酸 环 境 中, 装 置 设 备 就 腐 蚀 状 况 为 腐蚀 产 物 的 容 易出现 腐 蚀 的 情况 , 这 样 就 是为 什么这 类 式 炉 管 这 些 地 方 , 腐 蚀 都 是 会 出现 在 初 馏 塔 、 常 压 塔 和 减 压 堆 积 堵 塞 然 后 对 局 部 造 成 腐 蚀 穿 孔 。因此 燃 料 内的 硫 和 其 化 合 物 就 会 经 过高 温 之 后 塔 塔顶 及 其 冷凝 冷 却 这些 部 位 的原 因 。 产生 二氧化硫 , 再加 上 燃 料 室 都 是 过 氧 的 2 . 2 高温 s —H 2 S - R C O O H 腐 蚀 分析 状况 , 所 以部 分二 氧 化 硫 就 会 生 产 三 氧 化 ( 1 ) 高 温硫 腐 蚀 硫 混 合在 高温 烟 气 里 面 , 当 烟 气 的 温 度很 高 温 硫 腐 蚀 环 境 是指 2 4 0 ℃以 上 时 , 高 的 时候 , 并不 会发 生 腐蚀 现象, 主 要是 等 原油 中 的 部 分 有 机 硫 化 物 转 化 为 H: s 和 元 0 0 ℃以 下 的 时 候 , 三 氧化 素硫 , 活 性硫 、 硫 醇 和 H, s 形 成 的 腐 蚀 环 到 温 度 降 低 到4 这 种 化 合 物 是 一 种 境。 高 温 硫 腐 蚀 主 要 取 决 与 原 油 中 含 有活 硫 就 会 跟 水 蒸气 化 合 , 带有 腐 蚀性 , 遇 到 装 置的加 热 炉 性硫 ( 硫化氢、 硫醇、 单 质硫 ) 的 多少。 这 种 腐 蒸 汽 硫 酸 , 尾 部 受 热 面 上 就会 形 成 液态硫 酸, 这 时 就 蚀 会 伴 随 出现 硫 化 亚 铁 , 硫 化 亚 铁 附 着 在 装 置 的 内壁 上 就 会 将 内部 物 质和 装 置 进 行 会 有 强腐蚀 发生 。
常减压装置腐蚀及防护分析
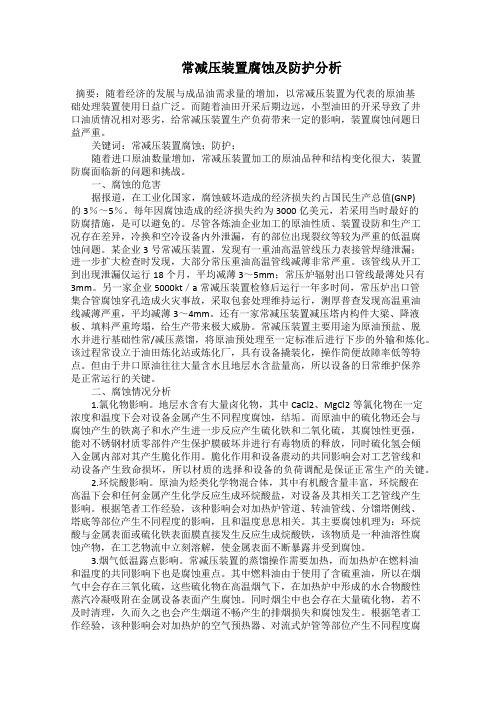
常减压装置腐蚀及防护分析摘要:随着经济的发展与成品油需求量的增加,以常减压装置为代表的原油基础处理装置使用日益广泛。
而随着油田开采后期边远,小型油田的开采导致了井口油质情况相对恶劣,给常减压装置生产负荷带来一定的影响,装置腐蚀问题日益严重。
关键词:常减压装置腐蚀;防护;随着进口原油数量增加,常减压装置加工的原油品种和结构变化很大,装置防腐面临新的问题和挑战。
一、腐蚀的危害据报道,在工业化国家,腐蚀破坏造成的经济损失约占国民生产总值(GNP)的3%~5%。
每年因腐蚀造成的经济损失约为3000亿美元,若采用当时最好的防腐措施,是可以避免的。
尽管各炼油企业加工的原油性质、装置设防和生产工况存在差异,冷换和空冷设备内外泄漏,有的部位出现裂纹等较为严重的低温腐蚀问题。
某企业3号常减压装置,发现有一重油高温管线压力表接管焊缝泄漏;进一步扩大检查时发现,大部分常压重油高温管线减薄非常严重。
该管线从开工到出现泄漏仅运行18个月,平均减薄3~5mm;常压炉辐射出口管线最薄处只有3mm。
另一家企业5000kt/a常减压装置检修后运行一年多时间,常压炉出口管集合管腐蚀穿孔造成火灾事故,采取包套处理维持运行,测厚普查发现高温重油线减薄严重,平均减薄3~4mm。
还有一家常减压装置减压塔内构件大梁、降液板、填料严重垮塌,给生产带来极大威胁。
常减压装置主要用途为原油预盐、脱水并进行基础性常/减压蒸馏,将原油预处理至一定标准后进行下步的外输和炼化。
该过程常设立于油田炼化站或炼化厂,具有设备撬装化,操作简便故障率低等特点。
但由于井口原油往往大量含水且地层水含盐量高,所以设备的日常维护保养是正常运行的关键。
二、腐蚀情况分析1.氯化物影响。
地层水含有大量卤化物,其中CaCl2、MgCl2等氯化物在一定浓度和温度下会对设备金属产生不同程度腐蚀,结垢。
而原油中的硫化物还会与腐蚀产生的铁离子和水产生进一步反应产生硫化铁和二氧化硫,其腐蚀性更强,能对不锈钢材质零部件产生保护膜破坏并进行有毒物质的释放,同时硫化氢会倾入金属内部对其产生脆化作用。
《石油炼制常减压装置腐蚀与防腐》范文

《石油炼制常减压装置腐蚀与防腐》篇一一、引言石油炼制过程中,常减压装置是关键的工艺流程之一。
该装置的主要功能是利用物理过程,如蒸馏和减压蒸馏,将原油分离成不同的石油产品。
然而,由于原油中含有的各种化学成分和操作环境的影响,常减压装置面临着严重的腐蚀问题。
腐蚀不仅影响装置的正常运行,还可能导致设备损坏、生产事故和环境污染。
因此,防腐措施的采取对于保障常减压装置的安全、稳定和长期运行具有重要意义。
本文将详细探讨石油炼制常减压装置的腐蚀问题及防腐措施。
二、常减压装置的腐蚀问题1. 腐蚀类型及原因常减压装置的腐蚀主要分为化学腐蚀、电化学腐蚀和物理腐蚀等类型。
化学腐蚀主要由酸性物质、硫化物等化学成分引起的;电化学腐蚀则是由于金属与介质之间的电位差导致的;物理腐蚀则是由机械磨损、冲刷等物理因素引起的。
这些腐蚀问题不仅影响设备的性能和寿命,还可能引发安全事故。
2. 腐蚀对设备的影响常减压装置的腐蚀会导致设备壁厚减薄、穿孔甚至破裂,严重影响设备的正常运行。
此外,腐蚀还会导致设备密封性能下降,泄漏问题频发,对生产环境和人员安全构成威胁。
同时,腐蚀还会增加维护成本,缩短设备的使用寿命,影响企业的经济效益。
三、防腐措施1. 材料选择选用具有良好耐腐蚀性能的材料是防止常减压装置腐蚀的关键措施。
在选择材料时,应充分考虑原油的性质、操作条件以及设备的用途等因素。
常用的耐腐蚀材料包括不锈钢、合金钢、钛及钛合金等。
此外,对设备进行表面涂层处理,如喷涂防腐涂料、镀层等,也可提高设备的耐腐蚀性能。
2. 工艺控制通过优化工艺参数和控制操作条件,可以降低常减压装置的腐蚀程度。
例如,控制原料的含硫量、含盐量等有害成分的含量,调整加热温度和压力等操作参数,以减轻化学腐蚀和电化学腐蚀的程度。
此外,加强设备的冲洗和排水,避免介质在设备内长时间停留,以减轻物理腐蚀的影响。
3. 防腐技术采用阴极保护、阳极保护等电化学防腐技术,可以有效地减缓金属设备的电化学腐蚀。
《石油炼制常减压装置腐蚀与防腐》
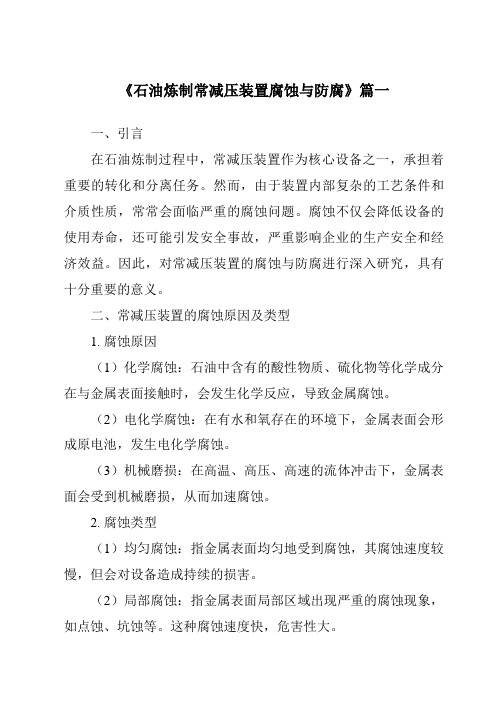
《石油炼制常减压装置腐蚀与防腐》篇一一、引言在石油炼制过程中,常减压装置作为核心设备之一,承担着重要的转化和分离任务。
然而,由于装置内部复杂的工艺条件和介质性质,常常会面临严重的腐蚀问题。
腐蚀不仅会降低设备的使用寿命,还可能引发安全事故,严重影响企业的生产安全和经济效益。
因此,对常减压装置的腐蚀与防腐进行深入研究,具有十分重要的意义。
二、常减压装置的腐蚀原因及类型1. 腐蚀原因(1)化学腐蚀:石油中含有的酸性物质、硫化物等化学成分在与金属表面接触时,会发生化学反应,导致金属腐蚀。
(2)电化学腐蚀:在有水和氧存在的环境下,金属表面会形成原电池,发生电化学腐蚀。
(3)机械磨损:在高温、高压、高速的流体冲击下,金属表面会受到机械磨损,从而加速腐蚀。
2. 腐蚀类型(1)均匀腐蚀:指金属表面均匀地受到腐蚀,其腐蚀速度较慢,但会对设备造成持续的损害。
(2)局部腐蚀:指金属表面局部区域出现严重的腐蚀现象,如点蚀、坑蚀等。
这种腐蚀速度快,危害性大。
三、常减压装置的防腐措施1. 材料选择:选用耐腐蚀、耐高温、耐高压的金属材料,如不锈钢、合金钢等,以降低设备的腐蚀速度。
2. 表面处理:对金属表面进行喷涂、镀层等处理,形成一层保护膜,隔绝介质与金属的接触,从而达到防腐的目的。
3. 工艺控制:通过优化工艺参数,如温度、压力、流速等,减少设备内部介质的腐蚀性。
同时,定期对设备进行清洗和检查,及时发现并处理腐蚀问题。
4. 添加缓蚀剂:在石油中添加缓蚀剂,可以降低介质的腐蚀性,减缓设备的腐蚀速度。
5. 阴极保护:通过使金属设备成为阴极,减少或避免电化学腐蚀的发生。
这种方法常用于大型设备和管道的防腐。
四、实例分析以某石油炼厂为例,该厂常减压装置采用不锈钢材料和合金钢材料制作,同时对设备进行了喷涂和镀层处理。
此外,还通过优化工艺参数、定期清洗和检查设备、添加缓蚀剂等方法来降低设备的腐蚀速度。
经过一系列防腐措施的实施,该厂常减压装置的使用寿命得到了显著提高,减少了维修和更换设备的成本和时间。
常减压装置主要腐蚀机理分析与防护措施
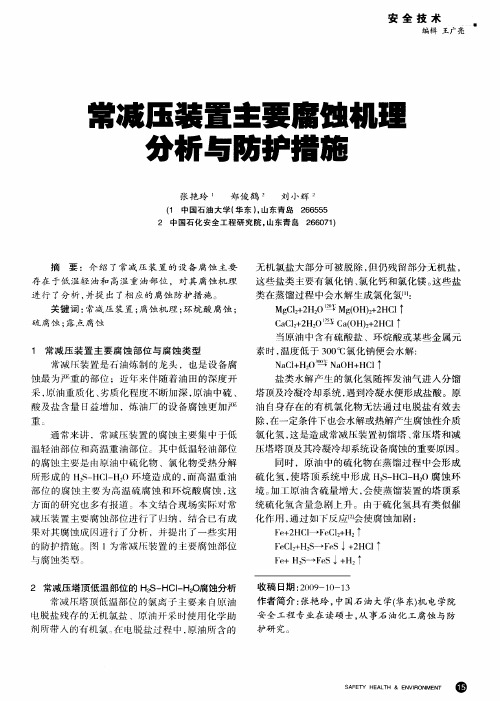
腐蚀、 坑蚀 ,r3为点 蚀 ,8 8不锈钢 为应 力腐蚀 。 Cl 1— 此 类腐 蚀易 发部 位如 图 1 所示 , 包括 : 减压 常
装 置塔 顶冷 凝 系统 的塔顶 部 、 冷凝 冷却 器 、 冷器 空
作 用 ,但 氨 的 中 和效 果 差 ,加 注 量 大 ,易 形 成
N 4l 物 , 而 引起 空 冷器 和 热交 换 器 的堵 塞 , HC 垢 从
安 全 技 术
F S HC— F C2 2 T e +2 l }e H 1H 0环 境 的腐蚀 形貌为 : 钢为均 匀 — C一 碳
这 种循环 促进 作 用 ,是加 工含 硫 原油 时腐 蚀 加 剧 的重要 因素 。 另外 ,工 艺 防腐 中常用 的 注氨 虽 能起 到 中和
及 塔顶 管线 的低 温部 位 。
图 1 常减压装置主要腐蚀部位与腐蚀类型
3 高温 部位 的腐 蚀分 析
3 1 高温硫 腐蚀 . 3 0 0 %两个 温度 区间最严 重 ,属 于 高温 化学 2 ~4 0
腐 蚀 。 高温 系统 中 , 在 环烷 酸 除了 与铁直 接作 用产 生 腐蚀 外 , 还能 与腐 蚀 产物 如硫化 亚铁 反应 , 成 生
溶 于油 的环 烷酸 铁I: 4 _
高温 硫腐蚀 主 要是硫 化 氢 、硫醇 和 单质 硫腐 蚀 ,而这些 物 质大 多都 是其 他硫 化合 物分 解 的产
方 面 的研 究也 多 有报 道 。本 文 结合 现 场 实 际对 常
压塔塔 顶及其 冷凝 冷却 系统设 备腐蚀 的重要 原因 。
同 时 ,原油 中的硫 化 物 在蒸 馏 过 程 中会形 成 硫 化 氢 , 塔 顶 系统 中 形成 H S HC一 蚀 环 使 — 1H 0腐 境 。 工 原油 含硫 量 增 大 , 使 蒸馏 装 置 的塔 顶 系 加 会 统 硫 化 氢 含量 急剧 上 升 。 由于硫 化 氢具 有 类似 催
一套常减压装置减压塔顶空冷腐蚀原因分析及对策
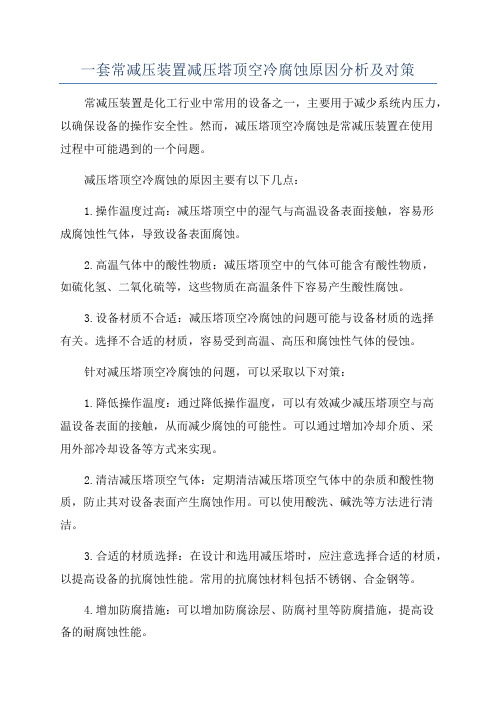
一套常减压装置减压塔顶空冷腐蚀原因分析及对策常减压装置是化工行业中常用的设备之一,主要用于减少系统内压力,以确保设备的操作安全性。
然而,减压塔顶空冷腐蚀是常减压装置在使用过程中可能遇到的一个问题。
减压塔顶空冷腐蚀的原因主要有以下几点:1.操作温度过高:减压塔顶空中的湿气与高温设备表面接触,容易形成腐蚀性气体,导致设备表面腐蚀。
2.高温气体中的酸性物质:减压塔顶空中的气体可能含有酸性物质,如硫化氢、二氧化硫等,这些物质在高温条件下容易产生酸性腐蚀。
3.设备材质不合适:减压塔顶空冷腐蚀的问题可能与设备材质的选择有关。
选择不合适的材质,容易受到高温、高压和腐蚀性气体的侵蚀。
针对减压塔顶空冷腐蚀的问题,可以采取以下对策:1.降低操作温度:通过降低操作温度,可以有效减少减压塔顶空与高温设备表面的接触,从而减少腐蚀的可能性。
可以通过增加冷却介质、采用外部冷却设备等方式来实现。
2.清洁减压塔顶空气体:定期清洁减压塔顶空气体中的杂质和酸性物质,防止其对设备表面产生腐蚀作用。
可以使用酸洗、碱洗等方法进行清洁。
3.合适的材质选择:在设计和选用减压塔时,应注意选择合适的材质,以提高设备的抗腐蚀性能。
常用的抗腐蚀材料包括不锈钢、合金钢等。
4.增加防腐措施:可以增加防腐涂层、防腐衬里等防腐措施,提高设备的耐腐蚀性能。
5.定期检测和维护:定期进行减压塔顶空冷腐蚀的检测,发现问题及时进行维护和修复,以避免进一步的腐蚀损坏。
总之,减压塔顶空冷腐蚀是常减压装置在使用过程中需要面对的一个问题。
通过降低操作温度、清洁空气、合适的材质选择、增加防腐措施以及定期检测和维护等措施,可以有效减少减压塔顶空冷腐蚀问题的出现,提高设备的寿命和安全性。
常减压装置的腐蚀与防护
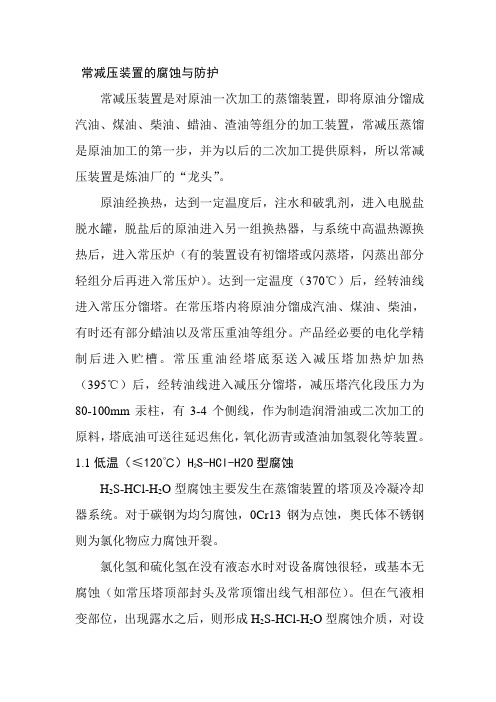
常减压装置的腐蚀与防护常减压装置是对原油一次加工的蒸馏装置,即将原油分馏成汽油、煤油、柴油、蜡油、渣油等组分的加工装置,常减压蒸馏是原油加工的第一步,并为以后的二次加工提供原料,所以常减压装置是炼油厂的“龙头”。
原油经换热,达到一定温度后,注水和破乳剂,进入电脱盐脱水罐,脱盐后的原油进入另一组换热器,与系统中高温热源换热后,进入常压炉(有的装置设有初馏塔或闪蒸塔,闪蒸出部分轻组分后再进入常压炉)。
达到一定温度(370℃)后,经转油线进入常压分馏塔。
在常压塔内将原油分馏成汽油、煤油、柴油,有时还有部分蜡油以及常压重油等组分。
产品经必要的电化学精制后进入贮槽。
常压重油经塔底泵送入减压塔加热炉加热(395℃)后,经转油线进入减压分馏塔,减压塔汽化段压力为80-100mm汞柱,有3-4个侧线,作为制造润滑油或二次加工的原料,塔底油可送往延迟焦化,氧化沥青或渣油加氢裂化等装置。
1.1低温(≤120℃)H2S-HCl-H2O型腐蚀H2S-HCl-H2O型腐蚀主要发生在蒸馏装置的塔顶及冷凝冷却器系统。
对于碳钢为均匀腐蚀,0Cr13钢为点蚀,奥氏体不锈钢则为氯化物应力腐蚀开裂。
氯化氢和硫化氢在没有液态水时对设备腐蚀很轻,或基本无腐蚀(如常压塔顶部封头及常顶馏出线气相部位)。
但在气液相变部位,出现露水之后,则形成H2S-HCl-H2O型腐蚀介质,对设备造成严重腐蚀。
H2S-HCl-H2O型腐蚀环境主要影响因素为:Cl-、pH值。
Cl-浓度:在H2S-HCl-H2O型腐蚀环境中,HCl的腐蚀是主要的。
HCl来源于原油中的氯盐水解。
另外,由于原油的深度开采,一些油田添加剂也成为HCl的主要来源之一。
pH值:由于氯化物的水解以及原油中硫化氢的逸出,在蒸馏装置塔顶低温露点部位形成强酸性腐蚀环境,pH值为2-3。
如某厂第一套常减压装置投产时,加工原油的含盐量达80mg/l,此状况下常顶空冷开工仅二个月就出现穿孔泄漏,入口弯头处的腐蚀率达15.5mm/a,直管段的腐蚀率达1.54mm/a。
第五章 常减压装置的腐蚀与防护
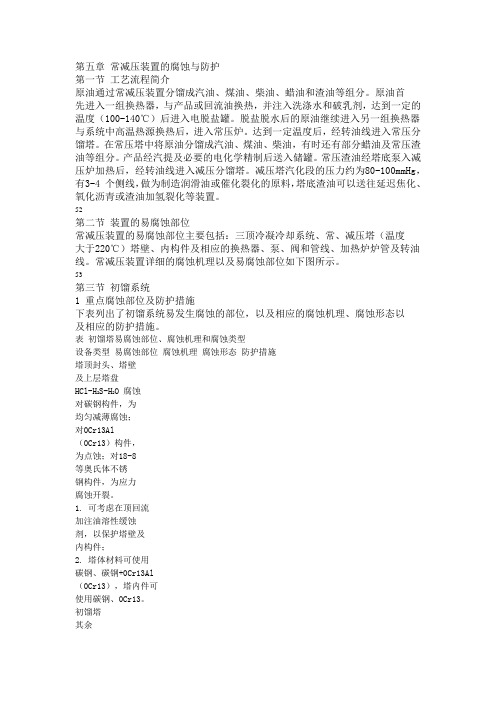
第五章常减压装置的腐蚀与防护第一节工艺流程简介原油通过常减压装置分馏成汽油、煤油、柴油、蜡油和渣油等组分。
原油首先进入一组换热器,与产品或回流油换热,并注入洗涤水和破乳剂,达到一定的温度(100-140℃)后进入电脱盐罐。
脱盐脱水后的原油继续进入另一组换热器与系统中高温热源换热后,进入常压炉。
达到一定温度后,经转油线进入常压分馏塔。
在常压塔中将原油分馏成汽油、煤油、柴油,有时还有部分蜡油及常压渣油等组分。
产品经汽提及必要的电化学精制后送入储罐。
常压渣油经塔底泵入减压炉加热后,经转油线进入减压分馏塔。
减压塔汽化段的压力约为80-100mmHg,有3-4 个侧线,做为制造润滑油或催化裂化的原料,塔底渣油可以送往延迟焦化、氧化沥青或渣油加氢裂化等装置。
52第二节装置的易腐蚀部位常减压装置的易腐蚀部位主要包括:三顶冷凝冷却系统、常、减压塔(温度大于220℃)塔壁、内构件及相应的换热器、泵、阀和管线、加热炉炉管及转油线。
常减压装置详细的腐蚀机理以及易腐蚀部位如下图所示。
53第三节初馏系统1 重点腐蚀部位及防护措施下表列出了初馏系统易发生腐蚀的部位,以及相应的腐蚀机理、腐蚀形态以及相应的防护措施。
表初馏塔易腐蚀部位、腐蚀机理和腐蚀类型设备类型易腐蚀部位腐蚀机理腐蚀形态防护措施塔顶封头、塔壁及上层塔盘HCl-H2S-H2O 腐蚀对碳钢构件,为均匀减薄腐蚀;对0Cr13Al(0Cr13)构件,为点蚀;对18-8等奥氏体不锈钢构件,为应力腐蚀开裂。
1. 可考虑在顶回流加注油溶性缓蚀剂,以保护塔壁及内构件;2. 塔体材料可使用碳钢、碳钢+0Cr13Al(0Cr13),塔内件可使用碳钢、0Cr13。
初馏塔其余S-H2S-RSH-RCOOH腐蚀高温硫腐蚀的均匀腐蚀减薄以及高温环烷酸腐蚀的沟槽状冲刷腐蚀。
塔壁材质可使用碳钢、碳钢+0Cr13Al(0Cr13),塔盘可使用碳钢、0Cr13。
塔顶冷凝冷却系统气液两相及液相区(大于70℃)HCl-H2S-H2O 腐蚀对碳钢构件,为酸露点腐蚀;对18-8 等奥氏体不锈钢构件,为应力腐蚀开裂。
常减压蒸馏装置腐蚀分析及防护措施优化

常减压蒸馏装置腐蚀分析及防护措施优化【摘要】因长周期运行,常减压装置设备的老化和腐蚀问题逐渐显现,给正常生产带来隐患。
因此,为加深对腐蚀介质以及腐蚀机理的进一步研究,文章在原防腐工艺措施的基础上,参考国内先进的生产工艺,对常减压工艺流程的一些环节和设备进行了优化和生产工艺的改进,切实为防腐工作以及保障常态化作业、长周期运行提供一些参考建议。
【关键词】常减压装置腐蚀防护措施优化长周期运行1、常减压蒸馏装置的基本原理常压蒸馏和减压蒸馏都属物理过程,经脱盐、脱水的混合原料油加热后在蒸馏塔里,根据其沸点的不同,从塔顶到塔底分成沸点不同的油品,即为馏分,这些馏分油有的经调和、加添加剂后以产品形式出厂,绝大多是作为二次加工装置的原料,因此,常减压蒸馏又称为原油的一次加工。
2、常减压蒸馏装置的主要设备常减压蒸馏装置的主要设备为常减压装置及电脱盐罐,其主要部件为原油分配器与电级板。
原油分配器的作用是使从底部进入的原油通过分配器后能够均匀地垂直向上流动,目的一般采用低速槽型分配器。
电极板一般有水平和垂直两种形式。
交流电脱盐罐常采用水平电极板,交直流脱盐罐则采用垂直电极板。
水平电极板往往为两至三层。
3、常减压装置中易发生腐蚀部位及腐蚀机理3.1低温部位腐蚀机理低溫部位的腐蚀主要属于HCl-H2O型和HCl-H2S-H2O型腐蚀。
腐蚀主要发生在初馏塔、常压塔和减压塔顶部,以及塔顶冷凝冷却系统的空冷器、水冷器等有液态水存在的低温部位。
腐蚀因素主要取决于pH值、Cl-以及H2S的含量。
其中Cl-是初馏塔、常压塔顶部腐蚀最主要的因素,主要来源于原油中的氯盐。
H2S是减压塔顶部和冷凝冷却系统腐蚀的主要因素。
在该腐蚀环境中,HCl溶于水生成盐酸。
若水量少,盐酸浓度可达1%~2%,形成十分强烈的稀盐酸腐蚀环境。
H2S的存在会使腐蚀加速,二者构成相互促进的循环腐蚀。
低温H2S 腐蚀表现为均匀腐蚀和湿H2S应力腐蚀开裂。
湿H2S应力腐蚀开裂包括氢鼓泡、氢致开裂、硫化物应力腐蚀开裂和应力导向氢致开裂。
- 1、下载文档前请自行甄别文档内容的完整性,平台不提供额外的编辑、内容补充、找答案等附加服务。
- 2、"仅部分预览"的文档,不可在线预览部分如存在完整性等问题,可反馈申请退款(可完整预览的文档不适用该条件!)。
- 3、如文档侵犯您的权益,请联系客服反馈,我们会尽快为您处理(人工客服工作时间:9:00-18:30)。
常减压装置腐蚀分析与防护措施
摘要原油的重质化和高含硫特性对炼油装置的腐蚀日趋严重,影响了常减压装置的长周期运行。
通过分析常减压蒸馏装置的腐蚀原因,并针对低温和高温2种腐蚀环境,提出了设备、管道材质选用和相关的防护措施。
关键词:常减压,腐蚀,选材,防护措施
1 常减压装置腐蚀原因分析 [1]
1.1腐蚀原因分析
常减压装置的设备和管道腐蚀主要表现为化学腐蚀和电化学腐蚀。
化学腐蚀主要发生在高温部位(240℃~450℃),电化学腐蚀主要发生在低温部分(150℃),每类腐蚀由于HCl 和HCN等介质的作用存在多种腐蚀情况。
1.1.1低温部位的腐蚀
低温下的HCl-H2S-H2O腐蚀。
原油中含有一定的无机盐、氯化物、硫化物。
无机盐在常压炉出口360℃的温度下,MgCl2、CaCl2和NaCl水解,产生盐酸。
由于水的存在而形成“稀盐酸腐蚀”,原油中硫化物分解产生H2S,会盐酸的腐蚀速度H2S和HCl会上升到常压塔、减压塔和初馏塔的塔顶,与塔顶金属设备表面进行反应,对塔顶的塔体、塔盘等进行腐蚀。
当H2S和HCl经过冷换设备后温度下降到露点以下,冷凝区出现液体水时,HCl会溶于水中成为盐酸,在冷换设备壳层形成HCl-H2S-H2O腐蚀。
这类循环腐蚀对于碳钢为均匀腐蚀,对于0Cr13钢为点蚀,对于奥氏体不锈钢为氯化物应力腐蚀开裂。
1.1.2 高温部位的腐蚀
高温腐蚀主要包括高温硫腐蚀和高温环烷酸腐蚀。
(1)高温硫腐蚀。
原油中的硫主要是非活性硫,它与金属一般不会直接发生反应造成腐蚀,非活性形成的硫化亚铁在金属表面会形成半保护性膜。
在340℃~400℃时,硫化氢可分解产生H2和活性很高的单质硫,促进腐蚀发生。
当在420℃~480℃时,高温硫对设备腐蚀最快。
(2)高温环烷酸腐蚀。
环烷酸是有机酸的总称,包括环烷酸、脂肪酸、芳香酸以及酚类,以环烷酸含量最多,故一般称石油中的酸为环烷酸,其沸点约在177℃~343℃。
高温环烷酸腐蚀特点:发生在酸值>0.5 mg KOH/g、温度在220℃~400℃之间的高流速介质中。
腐蚀发生于液相,汽相无腐蚀,但在汽液相交变部位、有流速冲刷区及涡流区腐蚀最为严重。
腐蚀率随酸值的增加而升高。
235℃时,酸值提高1倍,碳钢腐蚀率增加2.5倍。
在270℃~280 ℃腐蚀性最强,温度继续升高,环烷酸部分气化未冷凝,液相中的环烷酸浓度降低,腐蚀性下降。
350℃时,气化速度加快,气相速度增加,腐蚀加剧。
350℃~400℃腐蚀性最强。
425℃时,环烷酸基本气化,对设备高温部位不再产生腐蚀。
当环烷酸存在时,环烷酸与硫化亚铁膜直接反应,生成环烷酸铁和H2S,H2S和Fe又可以反应,从而促使腐蚀加剧。
2 防护措施
为了能够有效防止设备腐蚀,在选用设备的材质时,应该根据所处的不同腐蚀部位来选择不同的材质。
对于那些容易遭受腐蚀的部位,应该尽量选取抗腐蚀性强的材质。
碳含量大的材质容易遭受腐蚀,而Cr、Ni、Mo等对于增加材质的抗腐蚀性比较有利。
除了采用耐蚀材质外,有时还要进行表面处理,如碳钢表面渗铝处理和金属镀膜等。
也可以在冲蚀比较严重的部位改用大管径管道或者安装缓冲板,以此来降低冲蚀的影响。
2.1 低温腐蚀部位的材质选型
低温部位的腐蚀发生在初馏塔和常压塔顶部、塔顶冷凝系统、减压塔部分挥发线和冷凝系统。
这类循环腐蚀对于碳钢为均匀腐蚀,对于0Cr13钢为点蚀,对于奥氏体不锈钢为氯化物应力腐蚀开裂。
在塔顶上部低温腐蚀部位和上部封头材质选用20R+00Cr17Ni14Mo。
塔体下部高温腐蚀部分和塔体下部封头材质选用20R+0Cr13,冷凝器的管束和空冷器管束内壁采用镍磷化学镀层,钛纳米聚合物涂料防腐涂层。
塔顶冷凝系统重点腐蚀部位可选用耐H2S腐蚀的材质,空冷管束入口段插入L=400 mm钛管,塔顶换热器选用钛材或316L,冷凝器的管束和空冷器管束内壁可采用镍磷化学镀层,钛纳米聚合物涂料防腐涂层。
而常压塔塔顶换热器材质选用双相不锈钢时,双相不锈钢的固溶组织中铁素体相和奥氏体相约各占一半,双相不锈钢兼有铁素体不锈钢和奥氏体不锈钢的优点,将奥氏体不锈钢具有的优良韧性和焊接性与铁素体不锈钢具有的较高强度和耐氯化物应力腐蚀性能结合在一起,达到最佳的防腐蚀效果。
双相钢选用3RE60和SAF2205。
2.2 高温腐蚀部位的材质选型
用耐高温硫腐蚀、高温环烷酸腐蚀的材质,是解决高温系统腐蚀最有效的方法。
分别对2种高温腐蚀提出材质选用:
(1)高温硫腐蚀中,腐蚀发生在加热炉炉管内壁,分馏塔进料层以下,减压塔底的渣油和原油换热器、渣油泵叶轮和重油泵的出口管线等。
主要选材如Cr5Mo、Cr9Mo、0Cr13、1Cr18Ni9Ti等、防止高温酸和硫腐蚀除了采用耐蚀材质外,有的还要进行表面处理,如碳钢表面渗铝处理和金属镀膜等。
渗铝碳钢表面经氧化后生成一层致密的Al2O3保护膜,具有良好的耐环烷酸腐蚀、抗硫化和冲蚀性能,而且成本较低;
(2)高温环烷酸的腐蚀中,腐蚀发生在常压蒸馏和高真空减压蒸馏的设备、高温油泵、塔进料层、回流线、换热器等。
主要选材如Cr5Mo、0Cr13、0Cr18Ni9、1Cr18Ni9、1Cr18Ni12Mo2 等防止常减压蒸馏装置设备和管道的腐蚀。
设备、管道的材质选用外,还应采用工艺防护措施“一脱三注”原油电脱盐,注中和剂、注水、缓蚀剂和利用在线监测系统进行腐蚀监测掌握腐蚀速率、分析原因。
常减压蒸馏装置的低温部分需要结合工艺防腐蚀进行,而高温部位的防腐蚀主要是以材质升级为主,再辅以定点测厚、在线腐蚀监测和氢铜监测等腐蚀监测手段。
3 常减压减压塔填料运行故障原因分析及对策[2]
3.1 某公司常减压装置简况
某公司常减压装置减压塔采用高效规整填料,全塔分5段,分别为减一线、减二线、减三线、减四线和洗涤油段,与武汉分公司减压塔填料结构形式基本相同。
填料及内件材质为316L,填料钢带厚度O.15mm。
自2003年初以来,在减压塔侧线泵入口处发现有大量填料残片,表明规整填料腐蚀损失加剧,因减压塔内使用的规整填料厚度只有0.15mm,厚度偏薄,经生产运行检测,该规整填料的设计寿命为3年,判断该规整填料使用寿命已到期。
2004年6月装置进行了检修,发现减三线填料、减四线填料及重洗涤油填料(减四线集油箱下填料)完全腐蚀,填料呈脆性,一触即碎,减二线填料部分腐蚀,减一线填料基本完好;为保证安全运行3~4年,故对第一、二、三、四、五等五段规整填料拆卸更换。
此次大修后,减三中、减四中填料材质采用317L,其他为316L-T(OOCrl7Nil4Mo2.5),其中Mo含量大于2.5%,填料钢带厚度也增加到
0.2mm~0.25mm。
另一公司减压塔填料构造、材质与某公司常减压装置减压塔填料结构、材质相同,在减压二中回流部位加注了高温缓蚀剂,注入量为20×10-6,一中回流已安装了高温缓蚀剂注入设施,准备加注。
据该车间介绍,上次减压塔检修过程中,加注高温缓蚀剂的三线填料无腐蚀,未加注缓蚀剂的减二线和四线填料出现中部坍塌,部分填料脆裂,其他段填料状况较好,故只对受。