钻床的力学分析
毕设参考资料:半自动钻床及其运动分析

1 绪论1.1 课题选择的意义液压传动与其他类型的传动相比较具有许多突出的优点,液压传动技术在工程中,特别是在高效率的自动化和半自动化机械中,应用十分广泛。
本文主要利用钻床液压系统设计来实现钻床的半自动化控制是工业中经常用到的一种控制方式,它采用液压完成传递能量的过程。
因为液压传动控制方式的灵活性和便捷性,液压控制在工业上受到广泛的重视。
液压传动是研究以有压流体为能源介质,来实现各种机械和自动控制的学科。
液压传动利用这种元件来组成所需要的各种控制回路,再由若干回路有机组合成为完成一定控制功能的传动系统来完成能量的传递、转换和控制。
图1-1 液压传动能量传递过程Fig.1-1 hydraulic transmission energy transfer process从原理上来说,液压传动所基于的最基本的原理就是帕斯卡原理,就是说,液体各处的压强是一致的,这样,在平衡的系统中,比较小的活塞上面施加的压力比较小,而大的活塞上施加的压力也比较大,这样能够保持液体的静止。
所以通过液体的传递,可以得到不同端上的不同的压力,这样就可以达到一个变换的目的。
我们所常见到的液压千斤顶就是利用了这个原理来达到力的传递[2]。
图1-2 液压传动基本原理Fig.1-2 hydraulic transmission basic principleXXX半自动钻床设计和运动学分析液压作为一个广泛应用的技术,在未来更是有广阔的前景。
随着计算机的深入发展,液压控制系统可以和智能控制的技术、计算机控制的技术等技术结合起来,这样就能够更多的场合中发挥作用,也可以更加精巧的、更加灵活地完成预期的控制任务。
1.2 液压系统在工程中的应用液压传动相对于机械传动来说,是一门新技术。
自1795年制成第一台水压机起,液压技术就进入了工程领域,1906年开始应用于国防战备武器。
第二次世界大战期间,由于军事工业迫切需要反应快和精度高的自动控制系统,因而出现了液压伺服系统。
钻床使用总结

钻床使用总结引言钻床是一种主要用于钻孔的工具,在各种加工领域中广泛应用。
它具有稳定性高、操作简单等优点,被许多企业和个人所青睐。
本文将对钻床的使用进行总结,通过探讨钻床的结构和操作技巧,以及一些常见问题的解决方法,旨在提供给读者一些有用的建议和参考。
一、钻床的结构与工作原理钻床的基本结构包括床身、主轴箱、工作台、进给机构和操作系统等部分。
床身是整个钻床的基础,承受着钻孔过程中的各种力和转矩。
主轴箱则是驱动钻头旋转的重要部分。
工作台上有工件夹持装置,用于固定待加工的工件。
进给机构则负责控制工件相对于钻头的进给速度。
钻床的工作原理相对简单。
当钻床开始工作时,主轴箱带动钻头旋转。
操作人员将工件夹持在工作台上,通过盘旋装置和进给机构调整工件的位置和进给速度。
随着钻头的旋转,切削液不断冷却刀具并冲洗切屑,确保工件的质量和钻孔的效果。
二、钻床的使用技巧1. 选用合适的钻头钻床的钻头种类繁多,不同的工件需要选择不同的钻头。
一般来说,硬度较高的工件需要选择高速钢钻头或硬质合金钻头,而对于较软的工件则可以选择普通高速钢钻头。
此外,还需注意钻头的直径和长度,以确保能够满足加工要求。
2. 确保工件夹持牢固稳定在使用钻床进行工作时,需要保证工件夹持装置夹持工件牢固稳定,以防止在钻孔过程中工件发生位移或者晃动。
可以使用适当的夹具和夹具块来增加夹持力,并确保工件与夹具表面接触紧密。
3. 控制进给速度和切削液的使用钻孔时的进给速度需要根据工件的材料和直径来确定,一般情况下可以进行试钻来确定合适的进给速度。
进给速度过快会导致切削过度而产生毛刺,进给速度过慢则会影响工作效率。
此外,切削液的使用也很重要,可以有效延长钻头的使用寿命,并提高钻孔质量。
4. 定期检查和维护钻床作为一种常用的加工设备,需要经常进行检查和维护,以确保其正常运行和延长使用寿命。
定期检查各个部件的磨损情况,及时更换损坏的零件,并进行润滑和清洁工作。
三、常见问题及解决方法1. 钻孔产生毛刺如果钻孔产生毛刺,可能是因为进给速度过快或切削液不足。
钻机基本原理范文
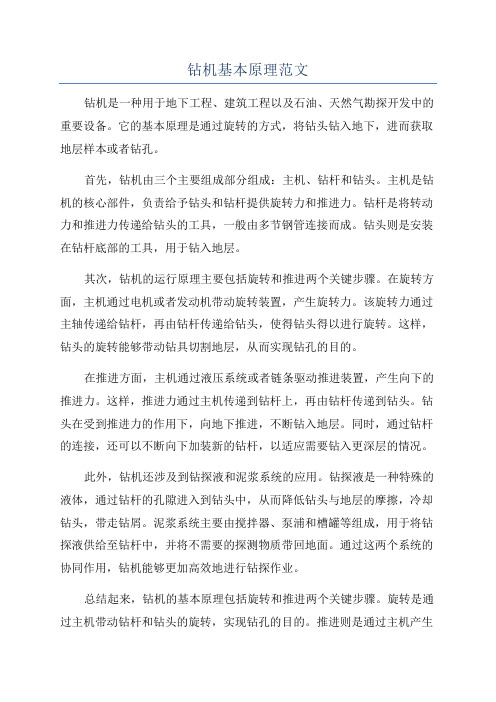
钻机基本原理范文钻机是一种用于地下工程、建筑工程以及石油、天然气勘探开发中的重要设备。
它的基本原理是通过旋转的方式,将钻头钻入地下,进而获取地层样本或者钻孔。
首先,钻机由三个主要组成部分组成:主机、钻杆和钻头。
主机是钻机的核心部件,负责给予钻头和钻杆提供旋转力和推进力。
钻杆是将转动力和推进力传递给钻头的工具,一般由多节钢管连接而成。
钻头则是安装在钻杆底部的工具,用于钻入地层。
其次,钻机的运行原理主要包括旋转和推进两个关键步骤。
在旋转方面,主机通过电机或者发动机带动旋转装置,产生旋转力。
该旋转力通过主轴传递给钻杆,再由钻杆传递给钻头,使得钻头得以进行旋转。
这样,钻头的旋转能够带动钻具切割地层,从而实现钻孔的目的。
在推进方面,主机通过液压系统或者链条驱动推进装置,产生向下的推进力。
这样,推进力通过主机传递到钻杆上,再由钻杆传递到钻头。
钻头在受到推进力的作用下,向地下推进,不断钻入地层。
同时,通过钻杆的连接,还可以不断向下加装新的钻杆,以适应需要钻入更深层的情况。
此外,钻机还涉及到钻探液和泥浆系统的应用。
钻探液是一种特殊的液体,通过钻杆的孔隙进入到钻头中,从而降低钻头与地层的摩擦,冷却钻头,带走钻屑。
泥浆系统主要由搅拌器、泵浦和槽罐等组成,用于将钻探液供给至钻杆中,并将不需要的探测物质带回地面。
通过这两个系统的协同作用,钻机能够更加高效地进行钻探作业。
总结起来,钻机的基本原理包括旋转和推进两个关键步骤。
旋转是通过主机带动钻杆和钻头的旋转,实现钻孔的目的。
推进则是通过主机产生推进力,使钻头不断向下钻进地下。
此外,钻探液和泥浆系统也是钻机运行中的关键组成部分,为钻机提供冷却、润滑以及钻探废物处理等功能。
这些原理的应用共同使得钻机成为一种高效、精确的地下钻探工具。
PCB钻床Z轴钻孔机构的动力学分析与结构改进

PCB钻床Z轴钻孔机构的动力学分析与结构改进刘顺;张冬冬【摘要】PCB钻床钻孔机构是钻孔设备的重要组成部分,它通过Z轴方向上下运动实现钻孔.首先,对钻床Z轴钻孔机构进行结构介绍;然后,对钻孔机构下钻时产生的钻孔偏差和孔径质量进行分析,简化钻孔机构的模型结构,应用罗伯森-维滕堡(R/W)方法对Z轴钻孔机构进行多刚体系统动力学分析,发现钻孔机构中连接件对钻孔机构的动态特性有着重要的影响;最后对原整体式连接件进行结构改进,改为调心机构,调心机构通过增加压簧以缩小机构传动间隙、增加预拉力、改善动力学特性,从而减少钻孔机构下钻时产生的偏差,提高钻孔质量.【期刊名称】《河南工程学院学报(自然科学版)》【年(卷),期】2019(031)001【总页数】5页(P58-62)【关键词】多刚体动力学;连接件;调心机构;压簧【作者】刘顺;张冬冬【作者单位】安徽机电职业技术学院数控工程系,安徽芜湖340202;南京林业大学工程培训中心,江苏南京210037【正文语种】中文【中图分类】TG527随着电子技术的蓬勃发展,PCB加工工艺越来越复杂,对PCB板的钻孔精度和质量也提出了更高的要求。
PCB板孔逐步向着微小化、高密度和高精度的方向发展,所以对钻孔设备加工能力的要求越来越高[1]。
目前最高技术水平的钻孔设备是瑞士生产的,孔径为0.10~6.35 mm,钻孔精度为±0.02 mm。
美国和德国也有较好的PCB数控钻床,孔径为0.20~6.35 mm,钻孔精度为±0.025 mm[2]。
国内的PCB钻孔技术与国外相比还有不小差距,尤其是在复杂多层PCB板的加工方面。
PCB数控钻床是钻孔的专用设备,而Z轴钻孔机构是PCB数控钻床的重要组成部分,是实现钻孔的直接机构,具有转速高、行程短、孔径小等特点,这使得钻孔时钻头会出现冲击、振动等现象,而且钻孔机构的动态特性较差,会影响钻孔的质量和精度。
为了提高PCB数控钻床的钻孔精度和质量,对Z轴钻孔机构进行研究具有重要的意义。
钻床知识点

钻床知识点钻床是一种常用的机床,常见于金属加工行业。
它通过将刀具固定在主轴上,然后以高速旋转并将刀具推入工件中,实现对工件进行钻孔的加工操作。
钻床广泛应用于各个领域,例如汽车制造、航空航天、电子设备等。
本文将介绍钻床的基本原理、操作步骤以及常见问题及解决方法。
一、钻床的基本原理钻床的基本原理是通过旋转刀具和推入刀具的方式,对工件进行钻孔加工。
刀具通常由硬质合金制成,具有良好的耐磨性和切削性能。
刀具的旋转由主轴驱动,主轴通常由电机提供动力。
刀具可以通过手动或自动方式进行进给,以便控制钻孔的深度和速度。
钻孔的直径可以通过更换不同尺寸的刀具来实现。
二、钻床的操作步骤1.准备工作:首先需要检查钻床的各个部件是否正常工作,例如主轴、进给装置等。
然后选择适当的刀具,并进行安装和固定。
最后,将工件固定在工作台上,并调整好工件的位置和角度。
2.开机:将电源接通,并打开钻床的电源开关。
等待主轴达到适当的转速后,即可开始操作。
3.定位:使用手动或自动进给装置,将刀具定位到工件上。
在定位过程中,需要注意保持刀具与工件之间的正确对位关系,并保持稳定的进给速度。
4.钻孔:当刀具定位到工件上后,开始旋转主轴,同时推入刀具。
根据需要,可以调整刀具的旋转速度和进给速度,以控制钻孔的直径和深度。
同时,需要注意保持刀具与工件之间的良好润滑,以提高钻孔的质量和切削效率。
5.停止和检查:当钻孔完成后,停止主轴的旋转和刀具的进给。
然后检查钻孔的质量和尺寸是否符合要求。
6.关机和清洁:关闭钻床的电源开关,并清洁工作台、刀具和机床。
三、常见问题及解决方法1.刀具磨损:长时间使用后,刀具可能会磨损,影响钻孔的质量和效率。
解决方法是定期检查和更换刀具,保持刀具的锋利度。
2.钻孔偏斜:钻孔可能会出现偏斜的情况,导致钻孔不符合要求。
解决方法是调整刀具的位置和进给角度,并保持刀具与工件之间的正确对位关系。
3.钻孔质量不佳:钻孔表面可能出现毛刺、破碎等问题,影响工件的使用。
钻柱力学分析
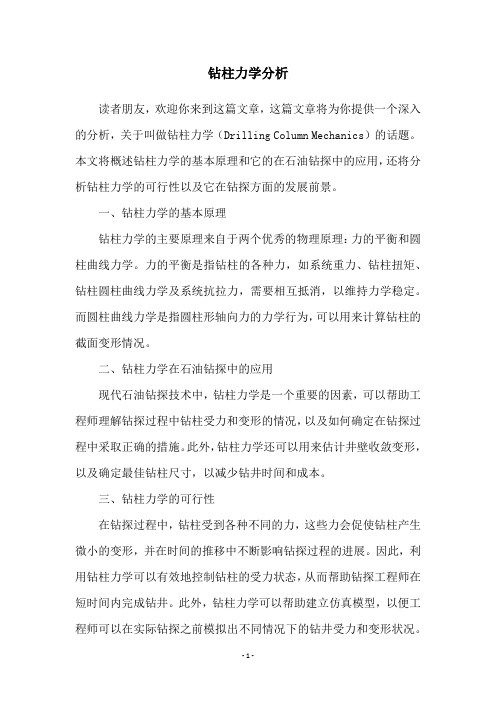
钻柱力学分析读者朋友,欢迎你来到这篇文章,这篇文章将为你提供一个深入的分析,关于叫做钻柱力学(Drilling Column Mechanics)的话题。
本文将概述钻柱力学的基本原理和它的在石油钻探中的应用,还将分析钻柱力学的可行性以及它在钻探方面的发展前景。
一、钻柱力学的基本原理钻柱力学的主要原理来自于两个优秀的物理原理:力的平衡和圆柱曲线力学。
力的平衡是指钻柱的各种力,如系统重力、钻柱扭矩、钻柱圆柱曲线力学及系统抗拉力,需要相互抵消,以维持力学稳定。
而圆柱曲线力学是指圆柱形轴向力的力学行为,可以用来计算钻柱的截面变形情况。
二、钻柱力学在石油钻探中的应用现代石油钻探技术中,钻柱力学是一个重要的因素,可以帮助工程师理解钻探过程中钻柱受力和变形的情况,以及如何确定在钻探过程中采取正确的措施。
此外,钻柱力学还可以用来估计井壁收敛变形,以及确定最佳钻柱尺寸,以减少钻井时间和成本。
三、钻柱力学的可行性在钻探过程中,钻柱受到各种不同的力,这些力会促使钻柱产生微小的变形,并在时间的推移中不断影响钻探过程的进展。
因此,利用钻柱力学可以有效地控制钻柱的受力状态,从而帮助钻探工程师在短时间内完成钻井。
此外,钻柱力学可以帮助建立仿真模型,以便工程师可以在实际钻探之前模拟出不同情况下的钻井受力和变形状况。
四、钻柱力学的发展前景由于石油钻探技术不断进步,钻柱力学在钻井过程中也将变得越来越重要。
目前,钻柱力学已经被广泛应用于石油钻探,但未来仍有很多空间可以改进和优化,如研发新型工具和材料,以及提高力学分析技术。
此外,研究人员正在尝试用钻柱力学来优化钻探布线,以减少钻探过程中的受力和变形。
总结以上是关于钻柱力学的详细介绍。
从上面可以看出,钻柱力学是一个非常重要的概念,它可以帮助工程师在短时间内完成钻井,而且在未来也会越来越受重视。
因此,为了提高石油钻探的效率,应该加强对钻柱力学的研究,以提升钻探技术水平。
机床加工中的加工力学理论

机床加工中的加工力学理论机床加工是一种广泛应用于制造业的重要工艺,其加工质量和效率直接影响到产品的成型精度和产能。
而在机床加工过程中,加工力学理论的应用则成为了实现高精度加工的重要手段之一。
本文将对机床加工中的加工力学理论进行探讨和分析。
一、引言机床加工是通过机床设备对工件进行材料去除和形状加工的过程。
在机床加工过程中,加工力学理论的研究旨在深入探索并优化加工过程中的动力分析、切削力预测和切削稳定性控制等关键问题,以提高加工质量和效率。
二、动力分析在机床加工过程中,动力分析是研究切削力大小和方向的重要手段。
通过动力分析,可以清楚了解切削力在各个方向上的分布情况,从而有针对性地调整加工参数和工件材料。
动力分析的关键在于确定切削力的作用方向和大小。
因此,研究人员利用力学原理和实验数据建立了一系列的数学模型,并通过仿真和试验验证模型的准确性。
基于这些模型,可以预测并控制加工过程中的切削力,从而提高加工质量和效率。
三、切削力预测切削力预测是机床加工中的另一个重要研究方向。
通过对切削力的准确预测,可以帮助操作员选择合适的刀具和加工参数,从而避免加工过程中的过载和失稳现象。
切削力的预测主要基于材料的力学特性和切削过程中的热力学变化。
通过建立数学模型和仿真,可以预测切削过程中的切削力大小和方向,为操作员提供科学依据。
四、切削稳定性控制切削稳定性控制是机床加工中的关键问题之一。
在加工过程中,由于切削力的作用,刀具和工件之间会产生振动,影响加工质量和效率。
为了控制振动,研究人员开发了各种方法,如主动振动控制和被动振动控制等。
主动振动控制通常通过在刀具或加工系统中引入专门设计的振动阻尼器来实现,而被动振动控制则采用改进刀具结构或加工系统的方法。
五、结论机床加工中的加工力学理论是实现高精度加工的重要手段之一。
动力分析、切削力预测和切削稳定性控制等研究问题的深入探索和研究,将有助于优化加工过程,提高加工质量和效率。
通过对机床加工中的加工力学理论的了解和应用,可以更好地理解和控制加工过程中的力学现象,为提高制造业的竞争力和发展空间做出积极贡献。
实例分析二、钻床[1]
![实例分析二、钻床[1]](https://img.taocdn.com/s3/m/7faf4bfd910ef12d2af9e734.png)
实例分析二:钻床(减压阀)
问题描述:
钻床的钻头垂直进给运动和夹紧装置采用液压驱动,该液压控制系统含有两个液压缸(夹紧缸1A和进给缸2A)。
因工件不同,其所需夹紧力也不同,因此,在夹紧缸1A中,其夹紧压力应可调,且应以最大速度回缩。
钻头进给速度可调,不过,在可变负载情况下,其进给速度应保持恒定。
注意:安装在进给缸(2A)活塞杆上的钻床主轴为拉力负载。
进给缸(2A)也以最大速度回缩。
解决方案:
为使夹紧缸的夹紧力可调,可以使用减压阀,减压阀用于降低系统压力,以满足不同液压设备的压力需要。
如果对钻床考虑两级压力控制,而不是压力调节,则将会产生下列不良后果。
当换向阀1动作时,首先以系统压力夹紧工件。
如果换向阀2动作,则系统压力就降为进给缸的工作压力,对夹紧缸也一样。
如果对回路进行扩展,即增加减压阀,则可调节夹紧压力,不过,系统压力在进给缸伸出过程中不断降低。
为可靠保持溢流阀出口处夹紧压力,其进口压力应大于夹紧压力,这可通过在换向阀2出口安装流量阀来获得。
换向阀1动作,可使夹紧缸以最大速度回缩。
调速阀使进给缸伸出速度与负载无关,且使其伸出速度可调。
不过,由于钻床主轴为拉力负载,因此,在系统中安装溢流阀,以作为背压阀。
在夹紧缸和进给缸回缩过程中,单向阀为旁通阀,从而保证其回缩速度最大。
液压回路:
注意事项:
安装在进给缸(2A)活塞杆上的钻床主轴为拉力负载,即负值负载,因此在活塞伸出时必须安装背压阀,提高系统的平稳性。
除了此处用到的溢流阀,还有哪几种液压控制阀可用作背压阀?。
- 1、下载文档前请自行甄别文档内容的完整性,平台不提供额外的编辑、内容补充、找答案等附加服务。
- 2、"仅部分预览"的文档,不可在线预览部分如存在完整性等问题,可反馈申请退款(可完整预览的文档不适用该条件!)。
- 3、如文档侵犯您的权益,请联系客服反馈,我们会尽快为您处理(人工客服工作时间:9:00-18:30)。
摘要通常情况下,术语“高速钻床”就是指具有较高切削速率的钻床。
高速钻床(HSDM)也是指具有非常快的和正确的点到点运动的钻床。
新的HSDM是由带有两个直线电动机的平面并联机构组成。
本文主要就是对并联机器(PKM)的动力学分析。
运动合成是为了介绍一种新方法,它能够完善钻孔操作和点到点定位的准确性。
动态合成旨在减少因使用弹簧机械时PKM的输入功率。
关键词: 并联运动机床;高速钻床;动力学的合成1 介绍在最近的几年里,研究所和工业协会介绍了各式各样的PKM。
其中大部分(但不是所有),以众所周知的斯图尔特月台[1]为基础结构。
这一做法的好处是高公称的负载重量比,良好的位置精度和结构刚性[2]。
斯图尔特式PKM的主要缺点是相对小的工作空间和相对慢的操作速度[3,4]。
机床刀具的工作空间是指刀尖能够移动和切削材料所需要的容积。
平面的斯图尔特月台的设计在[5]中被提到,像是对无CNC机器作翻新改进的方法需要塑料的铸模机制一样。
PKM[5]的设计允许可以调整几何学已经被规定了的最佳的再配置的任何路径。
一般的,改变一根或较多连杆的长度是以PKM受约束的顺序来做几何学的调整。
在机床设计中,“定长度连杆”的PKM应用比“不定长度连杆”的共同点要少的多。
一个优秀“定长度连杆”型的机器例子被显示在[6]。
Renault-Automation Comau 已经建造叫做“Urane SX”的机器。
在此HSDM被描述成是一个采用“定长度连杆”组成的并联机械装置。
钻床操作在文学[7]中被很好的介绍了。
汽车工业中,一项关于高速钻孔的操作的广泛的实验研究在[8]中被报告。
数据从数百个钻床控制实验上收集起来,是为了具体指定钻床质量所必须的参数。
理想的钻床运动和制造高质量钻床的指导方针通过理论和实验的研究被呈现在[9]中。
在被建议的PKM综合中,我们遵循[9]中的结论。
新推出的PKM的详细机械结构在[10,11]被介绍,机器的大致结构显示在图1中;它有很大的工作空间,点到点的高速运动和非常高的钻速。
并联的机械装置提供给了Y和Z轴的动作,X轴动作是由工作台提供的。
为了达成高速的运转,用了两个线性马达来驱驶机械装置和用一个高速的主轴来钻孔。
这篇文章的目的就是描述新的运动学的和动力学合成的方法的发展,为了改良机器的运转。
通过输入运动,规划钻井和点对点定位,机器的误差将会被减少,而且完成孔的质量能被极大的提高。
通过增加一个弹簧机械要素到PKM,输入动力就能被最小,以便机器的尺寸和能量损耗降低。
数字模拟的正确查证和热交换率的方法呈现在这篇文章中。
图1-1 HSDM 模块的示意图2 PKM 模型的运动学和动力学的运动方程式PKM 模型的概要线图在图2中被显示。
由于机床刀具库的一致,Z 轴是沿着工具运动的方向的。
PKM 模型有部分1和部分6二个输入指示(二个线性电机),和一个刀具的输出动作。
在PKM 模型应用中,定位和钻孔运动分别通过 61yy =( y 轴动作相对点到点的定位)和61yy -= (z 轴动作相对钻孔)表示。
刚体和柔性体的PKM 模型运动方程式都被发展了。
刚体方程式被用于合成输入钻床的动作计划和输入力量还原。
柔性体方程式被用来在刀具点到点定位之后的剩余振动控制。
图2-1 PKM 模块的示意图2.1 刚性连杆的PKM 模型的运动方程式机械装置[12]的特点是使用了数字集成,刀具设备(含工作台,主轴和刀具3部份)。
它的运动学方程式的发展依下列各项。
刀具的变位是βsin 2/)(y 3613r z y y =+= 式(2-1)且)2/()cos(ar 16r b y y c --=β 式(2-2)其中b 是点B 和点C 之间的距离,r 是连杆AB 的长度(连杆AB 、CD 和CE 的长度是相等的)。
刀具的速度是ββcos 2/)(y 3613r z y y =+= 式(2-3) 其中)sin 2/(y 61ββr y )( -= 式(2-4) 刀具的加速度是ββββsin cos 2/)(y 23613 r r zyy -=+= 式(2-5) 其中ββββsin )2/()(cos 162--+=r y y 式(2-6) PKM 模型的动力学方程式的发展如方程(7)所示,使用了拉格朗日的第二个类型的方程式[13]。
j j jtQ qT q T =∂∂-⎪⎪⎭⎫ ⎝⎛∂∂ d d )(k ,2,1j = 式(2-7) 其中t 是系统的总动能;j q 和j q 是总坐标值和速度值;j Q 是总力对应到j q 的的值。
k 是坐标系中总的独立数目。
在这里,k=2,11q y =和62q y =,引出之后,公式(2-7)可被表达成{}j j i i gi j gi gi j gi gi ni i Q q I q z z q y y m =∂∂+⎪⎪⎭⎫ ⎝⎛∂∂+∂∂∑= θθ1 ),2,1(j k = 式(2-8)其中n 是移动连杆的数目;)(gi i I ,m 是连杆i 的大量惯性矩;)(gi gi z ,y 是连杆i 的质量中心坐标;i θ是PKM 模型中连杆i 的旋转角。
总力j Q 的值通过式(2-9)决定ji ni i j q r F q VQ ∂∂+∂∂-=∑=1'j 式(2-9)其中V 是势能,'i F 是没有势能的力。
为了对PKM 模型的钻孔操作,我们有⎪⎪⎭⎪⎪⎬⎫⎪⎪⎩⎪⎪⎨⎧+∂∂-∂∂-+∂∂-∂∂-=⎭⎬⎫⎩⎨⎧∑∑==52663611315221z g i g cut gi i g cut gi i i F y F y z m g F y z F y z m Q Q 式(2-10) 其中cut F 是切削力, 1F 和6F 是线性马达在PKM 上输入的力。
公式(2-1)到公式(2-10)构成了刚性连杆PKM 模型的运动学和动力学方程式。
2.2 柔性连杆的PKM 模型的动作方程式顺从的机械装置的动微分方程式能用有限的机械要素方法和以下的公式得到[]{}[]{}[]{}{}1111n n ⨯⨯⨯⨯⨯⨯⨯=++n n n n n n n n R D K D C D M 式(2-11) 其中[M]、[C]和[K]分别是系统质量,阻尼和刚性母体;{D}是在全球同等坐标系中的每个机械要素平移和旋转变形表现的总坐标值;{R}是总外力值,与{D}保持一致;n 是坐标的总数目值(机械装置的柔性自由度)。
在我们的FEA 模型中,我们使用在图3中被显示的机械要素结构,其中e EI 是弯曲刚性(E 是材料的柔性系数,e I 是惯性矩),ρ是物质的密度,e I 是图2-2 平面框架元素机械要素的最初长度。
)6,,2,1(i =i δ是(x,y)坐标系统中表现的结点变位。
机械要素的大众基地和刚性基地将会是66个对称的矩阵,能从动能和应变能中得到,表达在公式(2-12)和式(2-13)中[]{}δδδ e t m T T d =⎭⎬⎫⎩⎨⎧∂∂-⎪⎭⎫ ⎝⎛∂∂d 式(2-12) []{}δδe K U =⎭⎬⎫⎩⎨⎧∂∂ 式(2-13) 其中t 是动能,U 是机械要素的应变能;{}[]T 654321δδδδδδδ=是机械要素基本坐标系中线性的123456和角变形节。
详细的推论能在[14]被发现。
典型地,在有限的机械要素分析中,一个顺从的机械装置是被离散成许多个机械要素的。
每个机械要素与一个质量和一个刚性母体有关。
每个机械要素有它自己的基本坐标系。
我们结合机械要素质量和所有机械要素的刚性矩阵运行坐标转换时,必须把机械要素的基本坐标系转换成世界坐标系,这就提供了系统质量[M]和刚性[K]矩阵。
在一个顺从的系统中捕获阻尼特性不是这么顺利的。
即使, 在许多应用中,阻尼可能很小,但是它能作用在系统安全性和动力的频率响应中,尤其在共振区域中,可能是重要的。
阻尼基地[C]能被写做一种质量和刚性矩阵[15]的线性结合,构成比例阻尼[C]如下式表达所示[][][]K M C βα+= 式(2-14)其中α和β是二个通常由实验决定的正系数。
一个表现阻尼基地的交互方法[16] 表达成[C]如下[][][]'C M C = 式(2-15)机械要素[C']被定义为21')/)((2ij ij ij ijM K signK C ζ=,其中)(ij ij ij K K signK =,ij K 和ij M 是[K]和[M]的机械要素, ζ是材料的阻尼比。
机械要素结构中的总力被定义为∑=∂∂+∂∂+∂∂=mj ij j i iyjij xje iM y F x F R 1)(δθδδθ )6,,2,1( =i 式(2-16) 其中j F 和j M 是jth 的外力和力矩,包括在)(j i y x ,上动作的机械要素的惯性力和力矩,m 是在机械要素上动作的外力数目。
机械要素的总力{}[]T e e e e e e e R R R R R R R 654321=-组合构成了系统总力{R}。
系统动作的第二次序普通微分方程式,如公式(11), 用一个数字能直接被整合的方法,就像是Runge- Kutta 的方法那样。
对于我们研究的PKM,每个连杆被分离成15个机械要素结构。
Matlab和ADAMS 软件都被用来规划和解决这些方程式。
3 为钻床输入动作计划假如我们知道钻床理想的动作功能。
高质量钻床的关键是如何决定输入电动机动作以便刀具的理想动作能被了解。
创建明白的输入动作功能时也为机器控制提供了必需的数据。
依照研究在[9]中所做的,钻孔的过程能分为三个时期: 入口期,中间期和出口期。
为了增加生产能力和钻孔的质量,许多操作限制,例如最小刀具的寿命限制,孔位置误差限制,退出毛边限制,钻头扭转破坏限制等等,一定要考虑而且要满意。
在这些条件之下,刀具的补给速度在入口期应该是慢的,以减少孔位置的误差。
刀具的速度在出口期也应该是慢的,以减少出口毛边。
在中央期,刀具的钻速应该很快速并且保持持续。
刀具在完成钻孔之后的退回应该被做的尽可能的快,以增加生产能力。
基于这些考虑, 我们采取了公式(17)中得到的理想钻床和刀具的退回速度。
⎪⎪⎪⎪⎪⎪⎪⎩⎪⎪⎪⎪⎪⎪⎪⎨⎧≤≤+-+≤≤≤≤----++≤≤+--++≤≤≤≤-=∑∑∑∑∑=====)()cos 1(2)()()cos 1(2)()cos 1(2)()0()cos 1(25166251412314143212321213211211111c i i c r i i i i r i i i i r r r r T T t T T T T t v T t T v T t T T T T T t v T T T t T T T T T t v T T t T v T t T t v v ππππ 式(3-1)其中1T v 是最大的钻孔速度,1T 、2T 和3T 是分别对应入口期,中间期和出口期的时间。