客车半成品加工工艺
半成品车间工艺知识学习

钢丝帘布常见的质量缺陷及产生原因
1.帘线稀密不均或缺线 产生原因: 1.1.整经辊磨损或磕碰伤; 1.2.压力辊与3#辊筒间隙不合适或间隙不一致; 1.3. 2#和3#辊筒间辊筒间积胶过多; 1.4.帘线张力不均; 1.5.胶料的粘度过大或过小; 1.6.压延辊温过高; 1.7.压延速度过快; 1.8. 覆贴的塑料垫布与冷却牵引辊打滑,造成压延张力不稳定等。 2.缺胶露线 产生原因: 2.1.供胶不均匀;; 2.2.压延辊温过低或供胶胶料温度过低; 2.3.胶料热炼不均; 2.4.压延胶片厚度达不到技术标准; 2.5. 2#,3#压延辊筒间无积胶
3.表面不光滑、粘性差 产生原因: 3.1.挤出机各部位温度不符合技术规定; 3.2.压延辊筒的温度不符合技术规定; 3.3.胶料混炼不均; 3.4.胶料的门尼粘度过低粘辊等。 4.喷霜或有自硫胶 产生原因: 4.1.胶料的存放时间过长; 4.2.胶料有自硫或混入其它胶料或混炼不均; 4.3.返回胶掺用过多或返回胶是多次返回的; 4.4..机头排胶温度过高等。 5.贴合的内衬层有气泡 产生原因: 5.1.过渡层存放时间过长或温度过低; 5.2.贴合时,过渡层、气密层的输送带速度匹配不合适; 5.3.贴合压力辊不合适等。
1.半成品表面不光滑、粗糙 产生原因: 1.1.机头、口型温度低(表面呈粗细不均的麻面状); 1.2.胶料焦烧自硫(表面呈麻面状焦烧); 1.3.胶料热炼不均或掺用返回胶料不均; 1.4.牵引运输带速度慢于压出速度(表面出现皱纹); 1.5.机头的压出口型处有杂物堵塞等。 2.压出部件焦烧自硫 产生原因: 2.1.胶料的焦烧时间短; 2.2.掺用多次返回的返回胶料; 2.3.机头、螺杆温度过高; 2.4.机头内有积胶或胶料回流等。
零度工艺规定
客车 车身 制造工艺
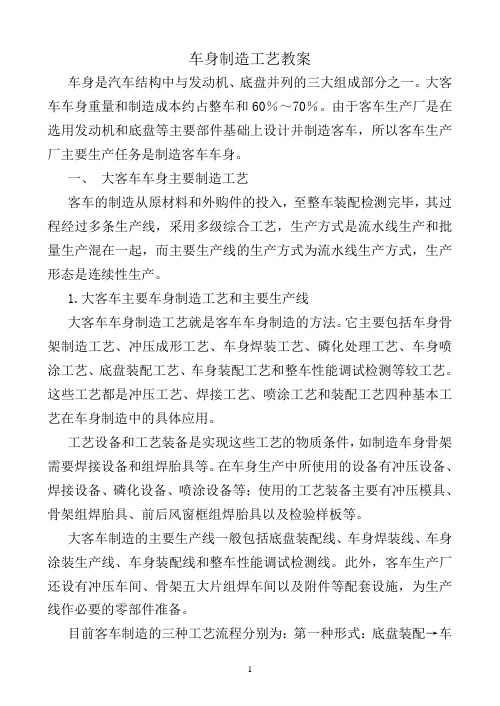
车身制造工艺教案车身是汽车结构中与发动机、底盘并列的三大组成部分之一。
大客车车身重量和制造成本约占整车和60%~70%。
由于客车生产厂是在选用发动机和底盘等主要部件基础上设计并制造客车,所以客车生产厂主要生产任务是制造客车车身。
一、大客车车身主要制造工艺客车的制造从原材料和外购件的投入,至整车装配检测完毕,其过程经过多条生产线,采用多级综合工艺,生产方式是流水线生产和批量生产混在一起,而主要生产线的生产方式为流水线生产方式,生产形态是连续性生产。
1.大客车主要车身制造工艺和主要生产线大客车车身制造工艺就是客车车身制造的方法。
它主要包括车身骨架制造工艺、冲压成形工艺、车身焊装工艺、磷化处理工艺、车身喷涂工艺、底盘装配工艺、车身装配工艺和整车性能调试检测等较工艺。
这些工艺都是冲压工艺、焊接工艺、喷涂工艺和装配工艺四种基本工艺在车身制造中的具体应用。
工艺设备和工艺装备是实现这些工艺的物质条件,如制造车身骨架需要焊接设备和组焊胎具等。
在车身生产中所使用的设备有冲压设备、焊接设备、磷化设备、喷涂设备等;使用的工艺装备主要有冲压模具、骨架组焊胎具、前后风窗框组焊胎具以及检验样板等。
大客车制造的主要生产线一般包括底盘装配线、车身焊装线、车身涂装生产线、车身装配线和整车性能调试检测线。
此外,客车生产厂还设有冲压车间、骨架五大片组焊车间以及附件等配套设施,为生产线作必要的零部件准备。
目前客车制造的三种工艺流程分别为:第一种形式:底盘装配→车身焊装→车身涂装→车身装配→整车性能调试检测;第二种形式:车身焊装→车身涂装→底盘装配和车身装配→整车性能调试检测;第三种形式:车身焊装→车身涂装→车身装配→整车性能调试检测。
底盘装配与三种工艺流程相对应的主要生产线编排顺序应与生产纲领、生产方式、工艺水平及车身结构形式等方面相适应。
2.产品工艺性和制造工艺工艺性分析产品的工艺性是指在确定的生产条件和规模下,能否最经济、最安全、最稳定地获得质量优良产品的可能性。
汽车制造业的原材料、半成品、产成品、生产设备等案例分析

生产过程
1.铸造 2.锻造 3.冷冲压
• 校车20人、20-30人、30-40人、40人-;团 体15-20人、21-30人、31-40人、41-50人、 51人-;旅游同团体车号;客运6-7米、7-8米、 8-9米、9-10米、10-11米、11-12米、1213米、13-;公交6-7米、7-8米、8-9米、910米、10-11米、11-12米、12-13米、13-; 专用车指挥车、房车、商务车、楼盘车、 体检车、采血车、救护车、教练车、军警 车、工程车、机场摆渡车、运兵宿营车、 全铝公交车、商品展示车、其他
主要原料
轮胎材料主要原料:天然橡胶或合成橡胶、炭黑、顺丁、 丁苯、钢丝;汽车制动器原料:铸铁;钢、铸铁、铸钢、 有色金属及合金、滑动轴承合金、其他有色金属,粉末 冶金材料,高分子材料如塑料、热固性塑料,橡胶如天 然橡胶、合成橡胶,胶黏剂,陶瓷,玻璃,纤维增强复 合材料,层复合材料,耐高温到点原子灰、铜棒、铝合 金板、不锈钢制管、不锈钢带、不锈钢液位变送器、耐 磨钢球、窄带钢板钢卷、弹簧钢、贴片电感器、黄铜线。 半成品:发动机、传送装置、方向盘、车架、轮胎
生产设备
• 铸造设备:包括压块机、混砂机、落砂机、抛丸机、造芯 机、造型机、浇注机。 • 锻造设备:包括成形用的锻锤、机械压力机、液压机、螺 旋压力机和平锻机,以及锻造操作机、开卷机、矫正机、 剪切机、等辅助设备。 • 冷冲压设备:包括曲柄压力机、双动拉伸压力机、高速压 力机。 • 焊接 • 金属切削加工设备:车床、铣床、磨床、钻床。 • 热处理加热设备(如各类加热炉),冷却设备(如各种冷 却介质槽)。校直设备(压力机、淬火压床等),以及辅 助设备(比如吊车,检验设备等)。 • 装配设备主要包括:汽车装配线所用输送设备、各种油液 加注设备、出厂检测设备、专用汽车装配线设备。
客车制造工艺技术

客车制造工艺技术客车制造工艺技术是指在客车制造过程中所需要运用的一系列技术和工艺方法。
客车作为一种大型交通工具,不仅要求具备良好的外观和性能,更需要在制造过程中保证车辆的质量、安全和耐久性。
本文将从车体制造、焊接工艺和喷漆工艺等方面介绍客车制造的工艺技术。
首先,车体制造是客车制造过程中一项重要的工艺环节。
传统的车体制造通常采用钢板冲压、焊接和组装的方式完成。
现代客车制造中,为了降低车体重量、提高车辆性能,常常使用轻量化材料如铝合金和复合材料。
钢板冲压是将平板钢料通过模具冲压成所需形状,然后再进行折弯和弯曲等工艺,最后通过焊接方法将各零部件连接成一体。
钢板冲压工艺技术的精准性和效率对于车体制造至关重要。
其次,焊接工艺是客车制造过程中的核心技术之一。
焊接是将金属材料通过热的方式进行熔合,实现零部件的连接。
在客车制造中,常用的焊接方法包括手工电弧焊、气体保护焊、激光焊等。
这些焊接方法各有优缺点,选用合适的焊接方法需要根据材料的种类、厚度和组合结构等因素进行综合考虑。
焊接工艺对车体质量和结构强度具有重要影响,必须严格按照规范和标准进行操作。
最后,喷漆工艺是客车制造过程中的一项重要环节。
喷漆不仅是美观的体现,更是对车身进行保护的一道屏障。
客车的喷漆工艺要求颜色均匀、光亮度高、抵抗腐蚀和耐久性好。
喷漆工艺包括表面处理、底漆涂装和面漆涂装等环节。
表面处理是保证涂层附着力和外观质量的关键,底漆涂装是为面漆提供承载和保护作用,而面漆涂装则是最终的外观效果呈现。
喷漆工艺需要严格控制温度、湿度和喷漆厚度等参数,以及遵循环保要求和安全操作规程。
综上所述,客车制造工艺技术是一个综合性强、环节众多的过程。
车体制造、焊接工艺和喷漆工艺都是客车制造中的重要环节,对车辆的外观和性能都有重要影响。
在客车制造过程中,必须严格按照相关规范和标准进行操作,以保证客车质量和安全性。
未来随着技术的不断创新和发展,客车制造工艺技术也将迎来新的突破和进步。
客车制造流程

客车制造流程客车制造是一个复杂而精密的过程,它涉及到多个环节和多个专业领域的知识。
客车制造的流程一般包括设计、原材料采购、生产制造、质量检验和售后服务等环节。
下面将对客车制造的流程进行详细介绍。
首先,客车制造的第一步是设计阶段。
在这个阶段,设计师们根据客户的需求和市场的需求,进行车辆的外观设计和内部结构设计。
他们需要考虑到客车的安全性、舒适性、节能性等方面的要求,同时还要兼顾到生产的可行性和成本控制。
设计师们需要运用CAD、CAE等软件进行设计和仿真,以确保客车的设计方案是合理可行的。
接下来是原材料采购阶段。
客车制造需要大量的原材料,如钢材、塑料、橡胶、电子元器件等。
制造商需要与多家供应商进行合作,确保原材料的质量和供应的及时性。
同时,制造商还需要对原材料进行严格的质量检验,以确保原材料符合客车制造的要求。
生产制造是客车制造的核心环节。
在这个阶段,制造商需要根据设计方案,进行车身焊接、内饰安装、动力系统组装、电气系统安装等工序。
在生产过程中,制造商需要严格控制每个环节的质量,确保客车的各项指标符合标准要求。
同时,制造商还需要确保生产线的高效运转,以提高生产效率和降低成本。
质量检验是客车制造的关键环节。
在生产完成后,客车需要经过严格的质量检验,包括外观检查、内部结构检查、性能测试等。
只有通过了质量检验的客车,才能够出厂销售。
质量检验是保证客车质量的重要手段,制造商需要建立完善的质量管理体系,确保每一辆客车都是合格的。
最后是售后服务阶段。
客车制造商需要为客户提供完善的售后服务,包括保修、维护、配件供应等。
客车在使用过程中可能会出现各种问题,制造商需要及时响应客户的需求,解决问题,提升客户满意度。
综上所述,客车制造是一个复杂而精密的过程,它涉及到设计、原材料采购、生产制造、质量检验和售后服务等多个环节。
制造商需要在每个环节严格把控,确保客车的质量和性能达到标准要求,以满足客户的需求和市场的需求。
客车生产工艺流程简介

客车生产工艺流程简介随着城市化进程的不断加快,客车作为城市交通的重要组成部分,需求量逐年增加。
客车生产工艺流程是指客车从设计到生产的一系列工作环节,包括设计、原料采购、生产装配、测试等多个环节。
下面将对客车生产工艺流程进行简要介绍。
1.设计阶段:在设计阶段,首先需要确定客车的用途、载客量、外观造型等基本要求。
设计师根据市场需求和用户要求,进行3D建模、结构设计和风洞试验等工作,确保客车的设计符合各项标准和规范。
2.原料采购:在客车生产过程中,需要大量的原材料,包括钢材、铝材、塑料、玻璃等。
生产工厂需要与供应商建立合作关系,并根据生产计划及时采购所需原材料。
3.钣金加工:钣金加工是客车生产的重要环节之一、在这个阶段,钢材和铝材等原材料会经过切割、冲孔、折弯等工序,形成车身骨架和外壳等部件。
4.涂装:涂装是客车生产中的关键环节。
在涂装车间,经过除锈、喷砂、底漆涂装、面漆涂装等工序,给车身进行保护和美观处理。
5.装配:装配是客车生产的核心环节。
在装配线上,将各个部件进行精确配合和组装。
包括底盘组装、车身组装、电器设备安装等。
同时,还需要对车辆进行电气连接和管路连接等工作。
6.内饰装饰:内饰装饰是客车生产的重要环节。
在这个阶段,对车内进行座椅安装、地板铺设、内部电器设备连接等工作。
同时,进行内饰装饰的工作,如顶棚、车门内饰板等。
7.车辆测试:在客车生产完成后,需要进行各项测试工作确保其性能和品质。
包括底盘性能测试、车身安全测试、综合试验等。
只有通过所有测试并符合规定标准,才能交付给客户使用。
8.成品检验:成品检验是客车生产的最后一道关卡。
对生产完成的客车进行全面的检查和测试,确保各项功能正常运作。
只有通过检验,客车才能出厂并交付给客户。
以上介绍了客车生产工艺流程的几个主要环节,每个环节都非常重要,缺一不可。
客车生产工艺的优化和提升,将有助于提高客车的品质和性能,满足用户需求,推动城市交通向更高水平发展。
典型的汽车零件的加工工艺流程

典型的汽车零件的加工工艺流程汽车零件的加工工艺流程在不同的零件类型和加工方法下会有所不同,下面是一个典型的汽车零件加工工艺流程的示例。
首先,根据汽车零件的设计图纸和要求,进行工艺规划和工序安排。
确定所需的原材料和加工设备,并准备好所需的加工工具。
1.原料准备根据设计要求,选择适合的原材料并进行准备。
原材料可以是金属(如铝、钢、铸铁等)或非金属(如塑料)。
2.切削加工对于金属零件,通常需要进行切削加工以获得所需的形状和尺寸。
切削加工可以通过铣床、车床、钻床等加工设备进行。
根据设计图纸,将原材料装夹在加工设备上,并使用适当的刀具对其进行切削、车削、钻孔等操作,直至获得所需的形状和尺寸。
3.焊接和焊接组装对于一些复杂的零件,可能需要通过焊接来将不同的部件组装在一起。
焊接可以通过电弧焊、气焊、激光焊等方式进行。
4.表面处理为了提高零件的表面质量和耐腐蚀性,常常需要进行表面处理。
这可以包括喷涂、镀层、电镀、阳极氧化等方法。
表面处理还可以改变零件的颜色、光泽和纹理。
5.组装和调试将经过切削加工、焊接和表面处理的零件进行组装。
这可以包括螺栓连接、机械连接、粘合等方式。
组装后,需要进行调试和检查,确保零件的性能和质量符合要求。
6.检测和质量控制完成零件的加工和组装后,对其进行检测和质量控制。
这可以包括尺寸检测、力学性能测试、材料成分分析、外观检查等。
如果零件不符合要求,可能需要进行修复或重新加工。
7.包装和出货当零件通过检测,并满足要求后,进行包装和出货。
根据零件的特性和客户的要求,可以选择合适的包装方法,以确保零件在运输和储存过程中不受损坏。
总结,这是一个简要的汽车零件加工工艺流程示例,具体的加工工艺流程可能因零件类型、加工方法以及生产厂家的不同而有所差异。
但无论是哪种零件,都需要经过原料准备、切削加工、焊接和焊接组装、表面处理、组装和调试、检测和质量控制、包装和出货等流程。
这些环节的成功完成,对于确保汽车零件的质量和性能至关重要。
客车生产工艺流程简介

6
一. 五金冲压材料介绍
什么是冲压材料? 冲压材料是指适合冲压成型工艺的材
料,涉及到材料性能包括材料硬度,抗拉强度,抗 剪切强度等。成型的工艺包括冲切,折弯,拉伸 等。
常见的冲压材料
(1). SPCC (2). SECC (3). SGCC (4).不锈 钢(5). SPTE马口铁 (6).洋白铜片(镍铜合金) (7). 磷青铜片(8). 硬铝合金 (9).碳素工具钢
2021/7/5
7
2. 工位布置特点:客车生产线的工位面积大、工位数 少、工位作业量大、作业内容繁杂、作业时间不均 衡。所以对作业量大的瓶颈工位设置了必要的辅助 工位,并通过设置辅助生产线,适当分组装配,减 少生产线上的总装配量,提高生产线对多品种混合 生产的适应性,以稳定流水线生产。
2021/7/5
料,涉及到材料性能包括材料硬度,抗拉强度,抗 剪切强度等。成型的工艺包括冲切,折弯,拉伸 等。
常见的冲压材料
(1). SPCC (2). SECC (3). SGCC (4).不锈 钢(5). SPTE马口铁 (6).洋白铜片(镍铜合金) (7). 磷青铜片(8). 硬铝合金 (9).碳素工具钢
2021/7/5
2021/7/5
17
• 客车制造的主要生产线采用流水线作业方式。各客车制造 厂因其生产规模、生产条件和生产车型的不同,所采取的 工艺流程亦有所不同,常见的工艺流程可归纳为三类。
1、脱壳式
底盘总成装配
车身骨架组焊
车身蒙皮焊装及 门体安装
车身总成涂装
车身总成-底盘总 成合装
2021/7/5
交付
整车测试调整
2021/7/5
14
• 车身焊装工艺:是在车身焊装线上进行的多种作业方法的总 称。对于小型车车身,冲压成型的构件和覆盖件通过焊装而 形成车身总成(又称之白皮车身),焊装是车身成型的关键。 车身焊装工艺将车身零部件焊装为合件,再将若干合件和零 部件焊装为分总成,最后将分总成、合件、零件装焊成白车 身。在车身焊装过程中,通常使用专用的装焊胎具将其零件 进行定位、夹紧,装焊胎具和焊接设备是焊装的主要工装设 备。对于大型客车,在车身焊装线上的各工位依次完成车身 骨架联装组焊、侧围蒙皮张拉、前后围蒙皮组焊、各种门体 以及前后保险杠的安装等作业。车身焊装质量不但影响车的 外观质量,也影响车身装配件的装配质量。
客车生产工艺流程简介

客车制造工艺的特点
➢ 客车的特点:多品种、小批量、大尺寸、装配工作量大。 ➢ 我公司客车产品覆盖从6米到14米,以及18米铰接车,目
前在用约1700多个车型代码
➢ 小型客车工艺形式及方法:车身壳体主要由车身覆盖件和 构件等冲压件构成,其制造工艺与乘用车相近。
BenQ Confidential (yyyy/mm/dd) 2005, BenQ Corporation
客车制造工艺流程
• 客车制造的主要生产线采用流水线作业方式。各客车制造 厂因其生产规模、生产条件和生产车型的不同,所采取的 工艺流程亦有所不同,常见的工艺流程可归纳为三类。
1、脱壳式
底盘总成装配
我公司生产线、工艺流程概况
• 一、部件准备车间,主要完成车身及底盘零部件自 制件的加工。按工作内容主要可分为:剪折工位、 钳工工位、焊接工位、等离子工位、备料工位、浸 漆工位。
• 矩形管下料,重点控制的是下料尺寸、角度。其下 料的准确程度关系到小总成乃至车身总成的尺寸准 确程度。下料设备一般采用带式锯床、盘式锯床、 弓式锯床、冲床等。
钢(5). SPTE马口铁 (6).洋白铜片(镍铜合金) (7). 磷青铜片(8). 硬铝合金 (9).碳素工具钢
BenQ Confidential (yyyy/mm/dd) 2005, BenQ Corporation
一. 五金冲压材料介绍
什么是冲压材料? 冲压材料是指适合冲压成型工艺的材
料,涉及到材料性能包括材料硬度,抗拉强度,抗 剪切强度等。成型的工艺包括冲切,折弯,拉伸 等。
客车制造工艺的特点
3. 一些生产规模较大的客车企业为了提高生产能力,适应 客车品种多、批量小的生产特点,多采用设置两条并行 的车身焊装线和两条并行的车身装配线与一条车身涂装 线相衔接的方式,焊装线、装配线的工位采用串联式布 置,整体浸渍磷化和浸漆、电泳底漆生产线工位采用串 联式布置;涂装线其他工位采用并列式布置。由于主要 生产线位于不同的厂房内,能更好地满足环境保护和安 全性要求。
客车生产制造工艺ppt课件

产品开发设计简介
客车生产制造工艺
0
工艺工作的主要内容
工艺工作是技术转变为生产力的实践过程。工艺是使产品设计变为成品的整 个制造过程中的基础,它是保证产品质量以及企业经济技术效益的重要条件之一。 工艺是人类在生产中积累起来并经过总结的操作技术经验。
对于制造业来讲工艺就是在企业的产品的设计、生产准备、制造和经营管理 活动中,贯穿产品全生命周期的技术过程。包括(产品设计、工厂布置设计、设 备配置、工艺规划、工艺装备设计制造、工艺定额编制、生产计划、现场加工、 售后服务等)的各个环节。工艺既来源于产品设计、企业现实条件,又来源于工 艺情报、科学试验、制造和售后服务等的总结,以及有关人员的专业工艺知识。
这种局部调整设计在工厂设计中是见得最多的一种,主要是添加设备等, 原则是充分利用现有条件和资源。
2
客车的生产特点和组成
一、客车的生产特点: 在进行工厂设计和确定生产工艺时,首先应考虑客车的结构特征、品种以
及生产规模,从而合理选择客车生产的工艺方法、生产形式以及工艺流程。 1、外形尺寸大。 2、客车的生产规模相对较小。 3、客车生产更加专业化和生产协作化。(相应的配套厂家及模块化) 4、客车厂属于技术密集型和劳动密集型企业。(技能型、手工作业) 5、产品自制率较低。客车工业的发展依赖于汽车行业、机械制造、电子
证产品质量、投资少收效快、长期综合效益好的目的。 ➢ 尽量采用流水线生产方式,采用直线式工艺流程。简化搬运作业。车间之间具
有最短的流程。 ➢ 尽量工序集中,压缩劳动量,减少工作面积和流水线长度。 ➢ 广泛采用风动液压快速装置及工具,实现单个工序机械化自动化,减少工人劳
动强度和提高生产效率。 ➢ 对设备选型和生产线设计要有柔性,尽量采用柔性可变流水线,以适应产品品
客车生产制造工艺

客车生产制造工艺
答案由网络收集
一、简介
大巴车是一种重型汽车,因它的大型结构而受到广泛关注。
大巴车是城市交通出行的重要手段,为乘客提供安全、舒适、经济的出行环境。
大巴车由汽车车身、车架、电气系统和发动机等部件组成,主要用于客运、货运、旅游等运输任务。
合理可靠的工艺是大巴车制造的关键环节,需要从设计、制造、安装等方面进行全面考虑。
1、设计工艺:在大巴车生产制造过程中,设计是第一步,也是关键步骤。
设计要考虑客车的性能参数,要求动力、结构等方面满足客车的要求。
2、制造工艺:在客车制造过程中,需要按照设计图纸进行工艺流程的设计与实施,并在生产现场统筹安排把控车辆的制造工艺,确保车辆的成品质量。
而且在生产过程中,要完善车辆的检测、验收工艺,以确保产品可靠、安全。
3、安装工艺:大巴车的安装工艺也是大巴车生产制造过程中的一个重要环节。
安装工艺分为内装工艺和外装工艺,内装工艺包括电气系统、电子设备等安装,外装工艺包括涂装、底盘等安装。
而在安装过程中,要求装配安装精度、成品外观质量等满足客车生产质量标准。
客车制件车间工艺流程

客车制件车间工艺流程英文回答:The process flow of the coach parts workshop involves several steps to ensure the efficient production of high-quality components. Let me walk you through the process.First, we receive the design specifications anddrawings for the coach parts. These specifications outline the dimensions, materials, and tolerances required for each component. I work closely with the design team to understand the requirements and ensure that our production process aligns with them.Next, we move on to material preparation. This involves sourcing the necessary materials, such as steel or aluminum, and preparing them for the manufacturing process. For example, if we need to create a metal bracket, we wouldstart by cutting the appropriate size and shape from asheet of metal.Once the materials are ready, we proceed to the machining stage. This is where we use various machines,such as lathes, milling machines, and CNC machines, toshape the components according to the design specifications. For instance, if we need to create a wheel hub, we woulduse a lathe to turn the raw material into the desired shape and size.After machining, the components undergo a quality inspection. This step is crucial to ensure that the parts meet the required standards. We use various measuring tools, such as calipers and micrometers, to check the dimensions and tolerances. If any defects or deviations are found, we make the necessary adjustments or reject the part if it doesn't meet the specifications.Once the components pass the inspection, they move onto the assembly stage. Here, we put together the different parts to create the final product, such as a brake assembly or a suspension system. This may involve using specialized tools, such as torque wrenches or pneumatic tools, toensure proper assembly and tightness of the components.Finally, we conduct a final inspection to ensure the assembled parts function correctly and meet all quality requirements. For example, if we assembled a door mechanism, we would test its opening and closing functionality, check for any abnormal noises, and verify that all components are securely fastened.中文回答:客车制件车间的工艺流程涉及多个步骤,以确保高质量零部件的高效生产。
简述客车制造工艺流程及内容

简述客车制造工艺流程及内容英文回答:The manufacturing process of a coach involves several steps and encompasses various aspects. Here is a brief overview of the coach manufacturing process and its content:1. Design and Engineering:The process begins with the design and engineering phase, where the coach's specifications, features, andlayout are determined. This includes designing the exterior and interior, selecting the materials, and ensuring compliance with safety regulations and industry standards.2. Body Fabrication:The next step is body fabrication, where the coach's frame and structure are built. This involves cutting and shaping the metal sheets, welding them together, andreinforcing the structure for strength and durability. The body fabrication process also includes creating openingsfor doors, windows, and other components.3. Painting and Coating:Once the body structure is complete, it undergoes surface preparation, including cleaning, sanding, and priming. After that, the coach is painted with the desired color and finish. The painting process not only enhancesthe coach's aesthetics but also protects it from corrosion and other environmental factors.4. Interior Installation:After the body is painted, the interior installation begins. This involves fitting the coach with various components such as seats, flooring, lighting, air conditioning, electrical systems, and entertainment systems. The interior installation is crucial for providing comfort, convenience, and safety to the passengers.5. Final Assembly and Testing:In this phase, all the components and systems are integrated into the coach. This includes installing the engine, transmission, suspension, brakes, and other mechanical parts. Once the assembly is complete, the coach undergoes rigorous testing to ensure that all systems are functioning correctly and meet the required standards.6. Quality Control and Inspection:Before the coach is ready for delivery, it goes through a series of quality control checks and inspections. This involves checking for any manufacturing defects, ensuring proper functioning of all components, and conducting safety tests. Any issues or discrepancies found during this stage are rectified and retested.7. Final Finishing and Detailing:After passing the quality control checks, the coach undergoes final finishing and detailing. This includescleaning, polishing, and adding finishing touches to enhance its appearance. The coach is then thoroughly inspected to ensure it meets the desired quality standards.8. Delivery and After-sales Service:Once the coach is deemed ready, it is prepared for delivery to the customer. This involves packaging, transportation, and logistics arrangements. Additionally, manufacturers often provide after-sales service, including warranty, maintenance, and repair support, to ensure customer satisfaction.中文回答:客车制造工艺流程包括以下几个步骤及内容:1. 设计与工程:制造过程始于设计与工程阶段,确定客车的规格、特点和布局。
大客车制造工艺

大客车制造工艺一、客车是指在设计和技术特性上用于载运乘客及随身行李的商用车包括驾驶员在内其座位数超过9座。
二、客车的分类1 按用途分为城市客车、公路客车、旅游客车和专用客车2 按结构形式分为非承载、半承载和承载车身。
车身主要生产线包括磷化处理生产线、车身焊装生产线、车身涂装生产线、总装配线及整车调试检测线。
三、生产方式是流水线生产和批量生产混合在一起而主要生产线的生产方式为流水线生产方式生产形态是连续性生产。
四、车身制造工艺的特点1 由客车主要生产线构成的工艺路线多采用回转布置工艺线路便捷工艺传递方便主要生产线之间产品流动畅通有利于生产进度控制和管理。
2 客车生产线的恭维面积大工位数少工位作业量大作业内容复杂作业时间不均衡。
3 为了适应客车品种多、批量小的生产特点同时为了提高生产能力是主要生产线的生产能力相适应采用设置两条并行的车身焊装线和两条并行车身装配线与一条车身涂装线相衔接的方式。
4 为了保证车身涂装的清洁的要求将车身表面预处理工位集中布置在涂装厂房的一侧与中涂、面涂及其烘干工位保持一定距离。
5 采用的工装设备具有一定的通用性。
6 客车因其车身尺寸大形成了一些特点显著的工艺形式。
7 所选的工艺方法和工装设备呈现多样性。
五、车身制造主要工艺冲压、焊接、喷涂和装配工艺车身蒙皮制造工艺包括侧位蒙皮张拉工艺拉伸形式和加热形式、顶盖两侧蒙皮的滚压成形工艺、薄板张拉弯曲成型工艺、车身蒙皮冲压工艺、顶盖蒙皮低工位作业组焊工艺和前后围蒙皮组焊工艺。
白皮车身冲压成形的构件和覆盖件通过焊装而形成的车身总成。
冲压生产的三大要素板材、模具和冲压设备金属表面的磷化处理喷射法指磷化液借助喷嘴以一定压力射向构件表面来实现磷化处理的方法。
适用于大型连续生产构件2 浸渍法六、产品工艺分析和制造工艺工艺性分析产品的工艺性是指在确定的生产条件和规模下能否最经济最安全、最稳定地获得质量优良的产品的可能性。
产品工艺性分析主要包括1 产品方面产品性能、生产效率和产品成本2 工艺方面加工工序、加工方法、加工基准、尺寸精度、材料及检验方法3 作业性方法设备及产品流程的人员配备、作业方法、作业量、作业环境、安全性4 生产方式方面与设备及平面布置有关的装置、材料准备、产品流程、废料处理方法、辅助材料的选择七、车身制造主要工艺流程1 客车制造工艺流程其最大的特点是车身和底盘分别制作涂装完工的车身总成再与底盘总成口和连接进入内外饰装配用于非承载式和半承载式客车。
汽车半轴加工工艺分析与方案

个人资料整理仅限学习使用汽车半轴加工工艺分析与设计目录中文摘要英文摘要1.前言1.1国外汽车半轴的加工工艺1.2国内后桥半轴先进的机械加工工艺技术2.材料的选择3.汽车半轴加工工艺流程及主要加工工序3.1剪料3.2摔杆3.3摆帽3.4喷丸3.5杆部校直3.6钻小端中心孔A3/7.53.7粗车大外圆3.8粗车小端3.9车大孔3.10钻中心孔B4/12.53.11粗车大端、精车大端3.12精车小端3.13冷滚轧花键3.13.1冷滚轧花键的优点3.13.2冷滚轧花键的加工方法3.13.3冷滚轧花键的工艺要求3.13.4典型的冷滚轧机技术参数3.13.5冷滚轧花键加工实例3.14半轴的热处理3.14.1热处理的具体工序3.15磁力探伤检验4.夹具设计4.1原夹具存在的问题4.2可微调新型夹具摘要汽车自19世纪末诞生至今100余年期间,汽车工业从无到有,以惊人的速度发展,写下了人类近代文明的重要篇章。
汽车是数量最多、最普及、活动范围最广泛、运输量最大的现代化交通工具。
没有哪种机械产品像汽车这样对社会产生如此广泛而深远的影响。
半轴是汽车传动系统的一个重要组成部分,半轴是用来将差速器半轴齿轮输出的动力传给驱动轮或轮边减速器,对于采用非独立式悬架的驱动桥,根据其半轴内端与外端的受力状况,一般又分为全浮式半轴、四分之三浮式半轴与半浮式半轴三种。
半轴内端以花键连接着半轴齿轮,半轴齿轮在工作时只将扭矩传给半轴,几个行星齿轮对半轴齿轮施加的径向力是互相平衡的,因而并不传给半轴内.个人资料整理仅限学习使用端。
主减速器从动齿轮所受径向力则由差速器壳的两轴承直接传给主减速器壳。
因而,半轴内端只受扭矩而不受弯曲力矩。
半轴是汽车的轴类零件中承受扭矩最大的零件,为了满足半轴的强度要求.多年来,世界备国除了用各种各样的计算方法外,还在材料选择、毛坯成型、机械加工和热处理等方面进行着不懈的努力。
本文主要是对半轴在锻造车间、机加车间、热处理车间的各步工艺进行分析和改进以及半轴的热处理和半轴齿轮的夹具改进。
客车工位工序生产工艺流程

1 “体系”产生的背景由于客车生产具有多品种、小批量、劳动密集和产量低的特点,致使国内大部分客车生产企业在粗放式的生产管理方式上一直未取得明显突破。
这种管理方式的特点:一是主要通过对班组人员管理来实现对生产计划和作业内容的管理;二是通过增加作业人员或延长劳动时间来满足市场对生产能力的需求。
其缺点主要体现在以下几个方面:(1)生产工位不确定,常出现流动作业、工位作业人员相互影响和干扰的现象。
(2)工人的完工时间不一致,怠、等、闲等无效工作时间较多,常出现全员加班现象,全员劳动生产率低。
(3)工人的有效工作时间差异较大,不利于工人报酬的分配。
(4)因客车属劳动密集型产品,而且产品的差异性越大,复杂程度越高,就越容易出现漏装、错装现象,不易控制产品质量。
(5)生产现场秩序及物料管理较乱。
随着客车产量和复杂程度的提高,以及客户差异性需求的日趋明显,传统的生产模式已不能适应客车市场的迅猛增长与竞争需求。
面对新形式、新要求,传统的客车生产管理方式必须融入精益生产的管理思想,必须构建“客车定位节拍生产工艺流程体系“。
2 “体系”的构建与实施我们在吸收欧洲先进客车生产管理方式的基础上,结合自身产品特点,对传统的生产管理方式进行了突破性变革,其核心体现在“客车定位节拍生产工艺流程体系“的构建。
2.1以实测时间为基础的工时体系(1)原工时工艺定额主要依据历年经验工时制定,仅仅用于劳动报酬的分配。
此工时存在如下不足:①不能反映工人的实际:[作时间与劳动效率;②不能用于分析生产、作为人员配置和生产能力分析的依据;③在用于报酬分配时,其基准受人为主观因素影响较大,不能准确反映劳动环境、工艺条件和技术含量等影响因素。
(2)解决方案。
对原有的工时体系进行改革,构建以实际操作时间为基础、综合考虑各项因素的新工时体系。
所有工艺人员按明确分工,用秒表测定各制造工序的实际操作时间,历经四个月时间,测定汇总出在线投产车型的实际操作时间。
- 1、下载文档前请自行甄别文档内容的完整性,平台不提供额外的编辑、内容补充、找答案等附加服务。
- 2、"仅部分预览"的文档,不可在线预览部分如存在完整性等问题,可反馈申请退款(可完整预览的文档不适用该条件!)。
- 3、如文档侵犯您的权益,请联系客服反馈,我们会尽快为您处理(人工客服工作时间:9:00-18:30)。
摘 要: 简要介绍宇通公 司部分先进的半成品加 工工艺及其对客车耐用可靠性能的重要性。 关键词: 车耐用性 ; 客 半成品 ; 加工工艺
中图分类号 : 6 TH1 U4 ; 6 文献标识码 : B 文章编号 :0 63 3 (0 7 0 —0 40 1 0 —3 1 2 0 ) 10 4— 1
半成 品加工工艺 。
1 钢板拼焊模 具冲压技术
客车产品 日 新月异 , 就宇通公司来说 , 平均每三 个月就有一种全新造型的产品诞生。新产品由于造 型需要 , 使前后围的曲线复杂 , 型困难 , 成 很多厂家
整车骨架 的耐用性提供 了有力 的支持 , 同时为张拉
蒙皮及侧窗玻璃粘接的表面平整度提供了可靠的保
维普资讯
第1 期
2 0 年 07
客
车
技
术
与 研
究
・
材料 ・工艺’ 设备 ・ ・
客事半成 品加工工 艺
余少玲 李照杰。 吉凌燕。 , ,
(. 1番禺职 业技术学 院 , 广东 番 禺 518 ; . 143 2郑州 宇通 客车股份有 限公 司 , 河南 郑州 401 ) 506
客
车
技
术
与
研
究
・
市场 ・ 经营 ・ 管理 ・
向铁路 , 豪华大巴开始失去市场主导位置。到 20 07
年, 随着遂渝高速公路的全面通车, 以及成遂段铁路 的改造完成 , 铁路与公路 客运 的运行 时间都将控制 在 3h内, 即将凸显一场客源争夺大战 ! 各种交通方式具有不同的技术经济特征, 高速
起到焊接坡 口的作用 , 加强 了焊接强度 , 减少 了焊缝 打磨量。对于减少骨架洞 口变形和吊装变形起到了 很好的防范作用 , 极大地提高了骨架的整体强度 , 骨
架的耐用性能不言而喻。
2 数控滚弧焊 工艺
在当今 的客车设计 当中, 了追求车身造型的 为 流线形 , 骨架的弧线设计 日益增多。如在大顶、 前后 围及左右侧围骨架总成 中, 相当一部分零件局部 有
证。
为了满足新产品的开发速度 , 在前后围蒙皮上使用 的是玻璃钢制品或手工成形的铁制品。玻璃钢模具
制造周期短 , 但是璃 钢制品相对铁制件 , 重量 大,
型钢 扳 台或 打磨 坡 口工艺
为了保证客车骨架的焊接强度, 提高其耐用性 能, 宇通公司在生产左右侧 围骨架 、 大顶骨架、 前后 围骨架半成品时, 对于型钢壁厚在 2m 以下 的零 m
结构改为整体成形结构 , 大大提高了零件的强度 , 为
大延长客车的使用寿命 , 降低运营成本 , 提升客车的 运营能力 。“ 耐用性” 已经成为用户最关注的性能指
标之一。宇通产品的“ 耐用品质” 除了有先进的装配
工艺提供技术保证之外 , 还有 高质量 的半成 品提供 产品保证 。下面简单介绍一下宇通公司部分先进的
20 年 , 0 5 字通公司率先在行业提 出了客车产 品 的新理念 :耐用可靠” “ 。据一项公路运输市场上 的
调查显示 , 在客车的各项功能指标 中,耐用可靠” “ 成 为与整体功能表现最相关的指标 。耐用可靠能够大
影响车身外蒙皮和 内饰 的装配质量和精度 , 强度直
接决定整车的骨架强度 , 半成品的加工难度非常大 。 为此 , 宇通公司购买 了吉林工业大学新设备开发公
件实施扳台工艺 , 对于型钢壁厚 在 3mm 以上 的零 件实行打磨坡 口工艺 。型钢扳 台或打磨坡 口实际上
强度低 ; 铁质手工成形件表面质量不高 , 靠钣金腻子 刮平表面 , 腻子过厚使铁质品表面强度减弱 , 在行驶
过程中表面腻子开裂。为 了解决此问题 , 公司采用 钢板拼焊模具技术 , 使原来六个月才能完成的前后 围大型拉延模在短 短的两个半月 的时间 内就 能完 成, 大大缩短了模具 的制造周期 , 为快速制造出高质 量的外蒙皮提供了技术保证。
司生产的二维数控液压弯管机和三维数控液压弯管
机 。弯管机采用无金属靠模方式弯制管件 , 只需将 弯曲工件 的有关数据输入计算机 , 生成数字靠模 曲 线, 便可随心所欲地 弯曲任意形状 的二维曲线和三 维曲线 。尤其是对于钢材材质不 同而造成 的回弹量 不同影响弯曲成形 时, 利用计算机可 以很方便地进 行修改 。在客车大顶 、 左右侧围、 前后围骨架半成品 的制作过程中推广滚弧焊工艺 , 将原来 的对缝焊接
新车为 11 , .6 随折旧年限调整至 1 O 不等, .7 几乎 没 有差别 。
滚动发班模式在许多地方违背经济规律 , 并形
成一种新 的垄断性经 营, 客买票不能选择乘坐 车 乘
Abta tThsatces o t n rd c sp r n fcu etc n liso e —iih d po u t n Yuo g B sCo sr c : i ril h rl ito u e a tma u a t r e h o ye fs mif s e r d csi t n u m y n
4 激光切 割加工工艺
20 年宇通公司购买 了德 国进 口的激光切割 04 机, 在半成品加工过程中推广 了激光切割加工工艺 。 ( 下转 第 5 2页)
或全部采用弧线结构 。此类零件 的表面质量将直接
・4 4 ・
维普资讯
第1 期
2 0 年 07
p n ,a d sae t p ra c ob sa d c a hd r bl ya d rl bl y a y n ttsisi o tn et u n o c u a i t n ei i t. m i a i Ke r s b sa d c a hd rbl y;s mi iih d p o u t ma ua tr e h oo ywo d : u n o c u a it i e — ns e rd c f n fcu etc n lgy