AI PCB. layout standard
AI插件PCB设计示范
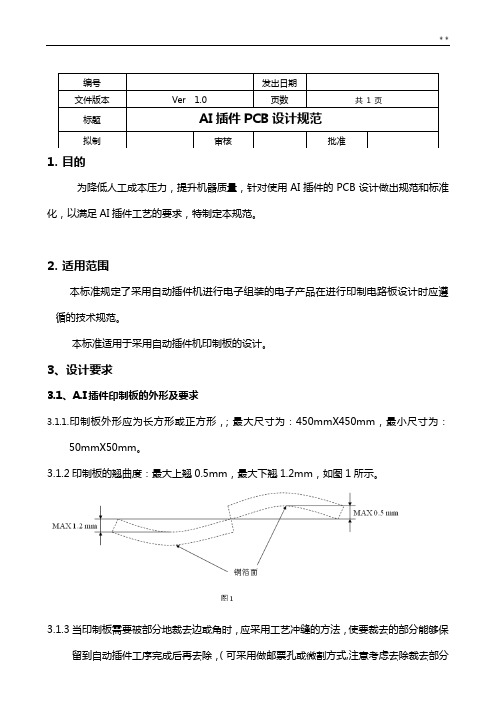
编号发出日期文件版本Ver 1.0 页数共1 页标题AI插件PCB设计规范拟制审核批准1.目的为降低人工成本压力,提升机器质量,针对使用AI插件的PCB设计做出规范和标准化,以满足AI插件工艺的要求,特制定本规范。
2.适用范围本标准规定了采用自动插件机进行电子组装的电子产品在进行印制电路板设计时应遵循的技术规范。
本标准适用于采用自动插件机印制板的设计。
3、设计要求3.1、A.I插件印制板的外形及要求3.1.1.印制板外形应为长方形或正方形,;最大尺寸为:450mmX450mm,最小尺寸为:50mmX50mm。
3.1.2印制板的翘曲度:最大上翘0.5mm,最大下翘1.2mm,如图1所示。
3.1.3当印制板需要被部分地裁去边或角时,应采用工艺冲缝的方法,使要裁去的部分能够保留到自动插件工序完成后再去除,(可采用做邮票孔或微割方式,注意考虑去除裁去部分的方便性)如图2所示。
3.1.4 边沿若要开口,其开口宽度不要超过3mm,深度不要超过30mm。
开口与附近角的距离要大于35mm;同一边上不要超过5个开口;尽量避免在长边上开口;如图3所示。
3.2 印制板的插机定位孔3.2.1.采用AI插件的印制板应在最长的一条边上设置主副两个电插定位孔。
如图4所示(元件面)。
其中左下角为主定位孔,孔径为Ø4.0mm;右下角为副定位孔,其孔径尺寸应为Ø4.0mm的鹅蛋形定位主定位孔副定位孔3.2.2两定位孔的中心轴连线平行于最长边,离最长边的距离为5.0±0.1mm,主定位孔与左边的距离为5.0±0.1mm,副定位孔孔边与右边的距离应不小于3.0mm,定位孔周围从孔边向外至少2mm范围内应覆铜箔以增加板的机械强度。
3.2.3主副两定位孔的中心距L的优选系列为:290mm、235mm、350mm,误差为±0.1。
3.2.4 AI插件PCB定位孔在元件面标记符号图中用方框标示。
AI插件PCB设计规范
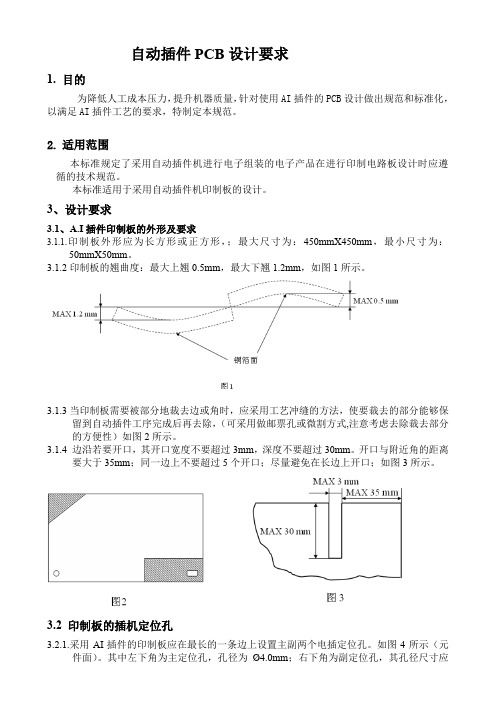
自动插件PCB设计要求1.目的为降低人工成本压力,提升机器质量,针对使用AI插件的PCB设计做出规范和标准化,以满足AI插件工艺的要求,特制定本规范。
2.适用范围本标准规定了采用自动插件机进行电子组装的电子产品在进行印制电路板设计时应遵循的技术规范。
本标准适用于采用自动插件机印制板的设计。
3、设计要求3.1、A.I插件印制板的外形及要求3.1.1.印制板外形应为长方形或正方形,;最大尺寸为:450mmX450mm,最小尺寸为:50mmX50mm。
3.1.2印制板的翘曲度:最大上翘0.5mm,最大下翘1.2mm,如图1所示。
3.1.3当印制板需要被部分地裁去边或角时,应采用工艺冲缝的方法,使要裁去的部分能够保留到自动插件工序完成后再去除,(可采用做邮票孔或微割方式,注意考虑去除裁去部分的方便性)如图2所示。
3.1.4 边沿若要开口,其开口宽度不要超过3mm,深度不要超过30mm。
开口与附近角的距离要大于35mm;同一边上不要超过5个开口;尽量避免在长边上开口;如图3所示。
3.2 印制板的插机定位孔3.2.1.采用AI插件的印制板应在最长的一条边上设置主副两个电插定位孔。
如图4所示(元件面)。
其中左下角为主定位孔,孔径为Ø4.0mm;右下角为副定位孔,其孔径尺寸应为Ø4.0mm 的鹅蛋形定位3.2.2两定位孔的中心轴连线平行于最长边,离最长边的距离为5.0±0.1mm ,主定位孔与左边的距离为5.0±0.1mm ,副定位孔孔边与右边的距离应不小于3.0mm ,定位孔周围从孔边向外至少 2mm 范围内应覆铜箔以增加板的机械强度。
3.2.3主副两定位孔的中心距L 的优选系列为:290mm 、235mm 、350mm ,误差为±0.1。
3.2.4 AI 插件PCB 定位孔在元件面标记符号图中用方框标示。
3.3 印制板的非AI 插件区3.3.1在非AI 插件区内布置的元件(其插孔在此区内)不适用于AI 插件,如该部分确需布件,就需采用手工插件。
AI插件PCB设计规范最新版本
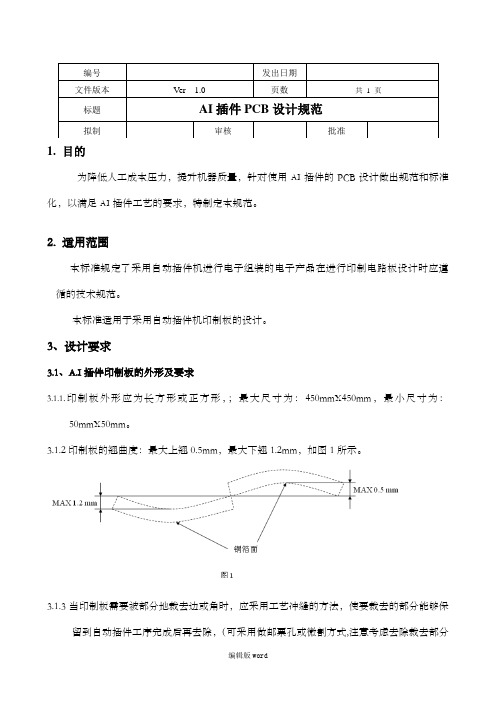
编号发出日期文件版本Ver 1.0 页数共1 页标题AI插件PCB设计规范拟制审核批准1.目的为降低人工成本压力,提升机器质量,针对使用AI插件的PCB设计做出规范和标准化,以满足AI插件工艺的要求,特制定本规范。
2.适用范围本标准规定了采用自动插件机进行电子组装的电子产品在进行印制电路板设计时应遵循的技术规范。
本标准适用于采用自动插件机印制板的设计。
3、设计要求3.1、A.I插件印制板的外形及要求3.1.1.印制板外形应为长方形或正方形,;最大尺寸为:450mmX450mm,最小尺寸为:50mmX50mm。
3.1.2印制板的翘曲度:最大上翘0.5mm,最大下翘1.2mm,如图1所示。
3.1.3当印制板需要被部分地裁去边或角时,应采用工艺冲缝的方法,使要裁去的部分能够保留到自动插件工序完成后再去除,(可采用做邮票孔或微割方式,注意考虑去除裁去部分的方便性)如图2所示。
3.1.4 边沿若要开口,其开口宽度不要超过3mm,深度不要超过30mm。
开口与附近角的距离要大于35mm;同一边上不要超过5个开口;尽量避免在长边上开口;如图3所示。
3.2 印制板的插机定位孔3.2.1.采用AI插件的印制板应在最长的一条边上设置主副两个电插定位孔。
如图4所示(元件面)。
其中左下角为主定位孔,孔径为Ø4.0mm;右下角为副定位孔,其孔径尺寸应为Ø4.0mm的鹅蛋形定位副定位孔主定位孔3.2.2两定位孔的中心轴连线平行于最长边,离最长边的距离为5.0±0.1mm,主定位孔与左边的距离为5.0±0.1mm,副定位孔孔边与右边的距离应不小于3.0mm,定位孔周围从孔边向外至少2mm范围内应覆铜箔以增加板的机械强度。
3.2.3主副两定位孔的中心距L的优选系列为:290mm、235mm、350mm,误差为±0.1。
3.2.4 AI插件PCB定位孔在元件面标记符号图中用方框标示。
AI PCB Layout 规范

Ø1.2±0.1
+0.1
VR規格 規格: 規格
Ø1.0 -0 2. 5
3.0 ±0.1
5.0 ±0.1
• E. 零件成垂直直線布置時 本體間距為 零件成垂直直線布置時,本體間距為 本體間距為1~1.5mm.
AI臥式零件與 臥式零件與PCB布置原則 臥式零件與 布置原則
A. 定位孔 定位孔:
+0.10 mm • 右則為圓孔 右則為圓孔:Ø4.0 -0
• 右則為橢圓孔:Ø4.0 右則為橢圓孔
+0.10 * 5 -0
mm
5mm 5mm 5mm 4.0 +0.10 -0
B. 二定位孔平行度與板邊平行 同時也平行 二定位孔平行度與板邊平行,同時也平行 兩位孔的孔心. 兩位孔的孔心 C. PCB的加尺寸 的加尺寸 最大 •AI臥式 臥式 •AI立式 立式 457*310 483*406 最小 100*80 100*80
•1.臥式零件本體與 臥式零件本體與 立式零件腳間距 最小為2mm. 最小為
2mm
• 2. 三腳晶體 / 半圓形晶體 下方不可布置AI零件 下方不可布置 零件. 零件
• 3. 立式零件本體下方不可布置 與之相垂直的臥式零件. 與之相垂直的臥式零件 (AI治具無法放置零件 治具無法放置零件) 治具無法放置零件
+0.1 mm -0.05 +0.12 -0.0 mm +0.1 mm -0.05
• AI自動插件所需的規格為 自動插件所需的規格為1.1 自動插件所需的規格為
B.
PCB LAYOUT 要求

PCB LAYOUT 要求1.穿孔元件要求:零件腳徑為 A mm Drill[A+0.2~0.4mm]●噴錫板:Drill [D] PAD [D+1.2mm] MASK [D+1.4mm]●無鉛板:Drill [D] ≦1.5mmPAD [D+1.2mm] Top MASK [D+0.4mm] Bot MASK [D+1.0mm]Drill [D] 1.6~2.0mmPAD [D+1.5mm] Top MASK [D+0.4mm] Bot MASK [D+1.3mm]Drill [D] 2.1~3.0mmPAD [D+2.0mm] Top MASK [D+0.4mm] Bot MASK [D+1.8mm]2.定位孔要求:●每片PCB頇要有2個以上定位孔,距板邊(5,5),基準孔在左下角,橢圓孔在右下角●定位孔周圍15ψ不能放零件,PCB四邊距離板邊≧5mm,也不要放零件●螺絲孔可做定位孔,孔徑≧2.8mm●螺絲孔PAD請設計成8片花瓣,避免過錫後吃錫過多或不均,影響鎖付●定位孔﹑螺絲孔﹑散熱孔,如孔邊有銅箔者請將孔邊銅箔去除1mm以防止孔塞錫3.SMT AI插件基準點(Fiducial mark):●Fiducial Mark之位置最好放在PCB四角落,邊緣距板邊≧5mm,必頇與SMT零件同一面,如為雙面板亦頇作Fiducial Mark●PCB板內最少要有2個基準點,左右斜對角,不要對稱● 零件包裝為BGA 或QFP 必頇要放置Fiducial Mark,請在零件四角落選兩點對角作為基準點4. PCB 尺寸:● PCB 尺寸限制:最大限制 : 440 x 350 mm最小限制 : 80 x 50 mm● PCB 的基本折斷邊:(a) PCB 兩長板邊需要預留8mm 以上之V-CUT 折邊,D-SUB 需要到10mm(b) PCB 四邊或短板邊需平整,如無平整請用(a)V-cut 折邊補齊或將(b)加PCB 缺口補齊若小於80x50mm 請以連板製作以多連板製作時,長板邊至少頇預留 8mm 以上之V-cut 折斷邊短板邊必頇平整,如無平整請用V-cut 折斷邊補齊或加PCB 將缺口補齊(c) 以過Reflow 後不變形,折除時不傷線路為準,郵票孔距離零件或trace 至少 ≧ 2mm 郵票孔之齒距定為≧15mil,孔徑≧25mil,郵票孔接合長度 5mm ~ 7mm,以增加支撐≧8mm5. 防銲漆(SOLDER MASK):● 防銲漆之顏色一般以綠色為主,但在connector 底部請用白漆● SMD PAD 之solder mask,由pad 外緣算起 3mil ± 1mil 作solder mask● SMD QFP 、PLCC 、BGA 等四邊皆有pin 腳之方形零件底下之所有via hole 必頇作solder mask,即該零件底下之via hole 要蓋上防銲漆● 相近零件之pad 必頇塗防銲漆隔開,或依零件外形隔開,至少要用0.13mm6. 文字面(SILK SCEEN):● 文字油墨採用不褪色、不導電性的白色油墨● 文字面與via hole 、 pad 、 測試點等不可重疊,避免文字殘缺不清● 文字面的標示,每個Location 必頇標示清楚,以目視可見清晰明確為主(a) 有極性(方向性)之零件應清楚標示腳位及極性(b) IC 四角腳位必頇標示各腳位,及第1 pin 方向性(c) Connector 、線圈應標示第1 pin 及方向性(d) BGA 應標示第1 pin 及各腳之陣列腳位及零件外框(e) 極性請不要被零件本體覆蓋● 文字距板邊最小距離為10mil如果過大易造成solder ball(a)不正確 (b)正確 塗防銲漆≧0.13mm(a)不正確 (b)正確 塗防銲漆≧0.13mm● 有極性及方向性零件範例圖示如下:電容(C) 二極體(D) IC(U)● 零件編號(REFERENCE):R:電阻 C:電容 L:電感U:IC D:二極體 W:ConnectorQ:電晶體 F:FUSE SW:SwitchJP:Jumper ZD:稽鈉二極體 RP:排阻CP:排容 Y:振盪器編號順序由1,2,……….,99,100● 每片PCB 板子必頇要標示PCB 料號、單片尺寸、連板尺寸、檔案名稱、日期,以便日後查詢7. 焊墊(PADS):● SMD PAD 的設計會直接影響到SMT 製程的品質,所以PAD 之大小的設計為其重點 ● PAD 不可與Via hole 、螺絲孔、測試點相連接● SMD 的PARTS,Fine-Pitch 、QFP 、TQFP 、SSOP 與TSOP 必頇確保零件放置在PAD上,零件腳的前端頇露出0.6~0.8mm,內側尾端至零件腳(heel)處露出0.5~0.8mm 之距離,0.4Pitch 之QFP 零件腳的前端頇露出0.8mm● 焊墊(PAD)與測試點(TEST POINT)(a) 焊墊與測試點不能相連,以避免錫被測試點分攤,而導致焊點 open零件位移 shift錫量不足 less solder(b) 焊點與測試點連接線路部分頇以綠漆覆蓋or 加白漆(c) 焊點與測試點間距距離≧1.0mmb-2d a+2c8.導通孔( VIA HOLE):● Via hole 距離Pad 至少≧0.127mm,且不可在 pad 旁或內部● Via hole 與 Via hole 之間距離至少>0.127mm● Via hole 在,兩面都要,以免造成短路9. 零件佈置(Placement notes):● 位置固定之零件,必頇依機構所標示,放在正確位置、方向及腳位● 相同零件方向(極性)應朝同一方向,一片板子上最多兩個方向,以利檢測● 較大之QFP 、PLCC 等零件,在layout 時應儘量避免集中於某區域,必頇分散平均佈置 ● 在DIP IC 、 Connector 方面,其零件之長邊必頇與PCB 長邊平行,避免錫橋之產生(此為理想狀況下,有時因機構or 電器特性而無法達到)過錫爐方向(佳) (不佳)● SMD 小零件電阻電容放在板邊或有折斷邊時,零件長邊頇與板邊垂直不佳●Dip 零件其周圍layout smd 零件時,頇預留1.5mm空間,以防止卡位現象,於bottom side時要有3mm以上之空間Top side Bottom side●SMD 擺放零件之間距:10.佈線:● 線路設計與SMT 生產品質有關,好的設計可提昇SMT 的品質減少open 和 less solder(a) SMD PAD:(1)(2)(3)正確不佳* 圖 (1)會因為線路吸熱而造成 open和 less solder* 圖 (2) 會使目視人員誤判為 short(b) SMD BGA PAD:(1) 不佳 (2) 正確(c) DIP & SMD PAD 與大銅箔之連接:● Layout 的線路距離板邊至少1.0mm 以上,距離郵票孔要2.0mm 以上,零件距離郵票孔要2.0mm 以上郵票孔11.ICT 測試點:●每片pcb 板都必頇要做ICT 測試,以確保產品之品質及功能,在PVT前請加入測試點●每條net至少要有一個測點,測試點應要平均分佈,避免局部密度過高●測試點最好放在同一面,若要雙面測試則top side 針點要少於bottom side●測點優先順序: (1).測試點(test pad) (2).零件腳(component lead) (3).貫穿孔(via hole)公司因密度關係加上可測率頇100%,是以via hole 當測點,針點植於bottom side●測點中心要>55mil(1.4mm),空間允許則最好>75mil(1.9mm),且儘量交錯,pad要>0.6mm●測試點與螺絲孔邊及板邊距離要>3.0mm●BGA、QFP 等零件本體下之via hole 皆要蓋綠漆,測點儘可能打在body外pad>0.6mm >3.0mm>>1.4mm12.Function test:●Function test 的測點要>0.8mm,若為此用途請另外拉出test pad ,兩點間距>1.5mm●LVDS connector 必頇要拉test pad 以便做Function test●若測試治具已開,有版本進階,則原有之測點(ICT&Function) 儘可能不變動13.出圖:●出圖格式請統一用RS274X●出圖前必頇要做DRC check ,以確保資料之正確性,請填寫DRC check list並與製作聯絡單同時歸檔●出圖後請務必將圖檔、gerber file及鋼板資料上傳歸檔,每個版本皆要存檔,以利日後查詢14.相關資料提供:●鋼板: 請提供連版之鋼板gerber file 及零件座標檔●ICT&Function : 請提供gerber file15.其他注意事項:●取消,孔改成npth,以避免錫絲造成short●為提高150x200mm●1mm以防塞孔,影響組裝>1.0mm●針對改善無鉛via hole吃錫狀況,根據板廠建議:(a). Via hole: Drill=0.4mm PAD=0.6mm Top Mask=0.7mm Bot Mask=0.85mm(b). 大片銅箔時via hole 請用Thermal方式連接以達到良好之品質。
PCB layout的一些原则

(2) 零件布置如下图时
则零件本体与孔距关系表如下图
(3) 当零件b高于零件a时,两零件相距1.47mm
(4) 零件布置如下图,则两零件本体距离2mm
(5) 零件布置如下图时,两零件相距0.5mm
八 SMD零件布置原则
1. 基板切割方式为V-CUT时,为避免手折板应力损坏SMD零 件,布置SMD零件时,本体与V-CUT边垂直时至少需保持 5mm距离,本体与V-CUT平行至少需保持3mm距离,否则板 边需SLOT,两种情况下,最小距离均为2mm,避免后续作业 时,零件受撞击。
备注栏 跳线,电阻,二极体 钽质电容,直脚电解电容,X电容,立 式电阻跳线,突波吸收器,热敏电阻, Y电容
卧式架高电阻,电解电容(D=10mm以上,特别是 厂商成型者)
立式 立式成型 (kink) 变压器,4pin(含)以上有 座线圈
4PIN以上为d+0.4 d+0.2是指只有两个PIN的线圈 d≤1.0 d>1.0 桥式固定于散热片上
三 立式零件布置卧式原则
零件名称 布置方式 备注橍
本体与弯脚距离为
半圆型晶体(92)
3mm
本体与弯脚距离为 2.5mm
电解电容
Y电容陶瓷电 容突波吸收器
(1) 线脚直径为0.6,本体 与弯脚距离为4.0mm (2) 线脚直径为0.8,本体 与弯脚距离为5.5mm
零件名称
布置方式
备注橍
本体与弯脚距离为 3mm
(3) 方向如果无法统一,每一SMD均需增加直径0.9的气孔 (4) 因零件本身为金属,故电解电容不可布置于背面
5. SMD 1210以上(含)尺寸之电容,3216以上(含)尺寸之钽质 电容及2512尺寸低阻值5m欧(含)以下之电阻,不可布置于锡炉 作业面 因为零件本体耐温不够.
AI PCB设计参考标准

自动插件PCB 设计参考及检查标准一. PCB 尺寸要求:PCB 的外形最小尺寸 50mm*50mm,最大尺寸450mm*450mm二.PCB 定位孔要求:根据PCB 长度L 的范围,插件机对于鹅蛋形定位孔距PCB 边缘的距离 S2 的要求也不同。
注意:圆形定位孔为固定的标准位置,鹅蛋形定位孔应根据PWB 长度L 的不同而其 S2 也有所改变,有关数据请参照下表:另外,当PCB 定位孔过多,生产时容易造成PCB 取放板方向混淆。
故设计PCB 时,只须在该PCB 长边上设计一组定位孔(左边圆形定位孔+右边 鹅蛋形定位孔)。
三. 自动插件机元件引脚直径范围为: 0.38mm -0.71mm因此,自动插件机可插以下元件:1. 1/16W 、1/8W 、1/4W 电阻2. 色环电容3. 0.6mm 跳线4. 二极管5. 色环电感四. 元件跨度C 的范围: 5.0mm -17.0mm设计元件跨度必须同时考虑到元件体长度L ,如果L 过长,插件机容易打伤 元件体或打断元件引脚,损坏插件机刀具,同时对排料机要求非常严格。
如果跨度C 过大,插件机速度会降低,插件时易掉件(插件机刀具夹不牢)、元件易浮脚。
目前AI 部插件最多的是5.0mm 跨度,5.0mm 跨度的元件在插件时比较容易出现拱起、损伤元件等坏机;故建议将AI插件元件的最小跨度定为6.0mm ,以求大幅度降低坏件率。
最小跨度的推算: 一般元件=MAX L +1.3mm二极管、色环电感=MAX L +2.8mm、五. 元件孔径要求:现时PCB 供应商工艺质量控制不是很好,如果再加上元件孔径过小,就不 符合插件机的插件要求,那将会极大的增加AI 插件的坏件率,需要增加大量人手去弥补(检查员检查和补件)。
但是,如果元件孔径过大,又将会导致元件过松容易脱落(过波峰焊前),且会产生锡 点不良等质量问题。
自插机要求:MIN D = MAX d + 0.45考虑以上情况,我们确定如下数据:注意:以上孔径对于手插元件可能过大,故请参考第三、第四、第六、第九、第十点, 分清哪些元件是手插件,以便单独对手插件的孔径采用不同的标准。
最全的PCB Layout规范

PCB Layout规范PCB Layout规范一、安全间距1. LN之间3mm以上,空间距离1.8mm以上,不足时开1mm以上的槽增加沿面距离。
2. 初次级间6.4mm以上,空间距离5mm以上,不足时开1mm以上的槽增加沿面距离。
3. 初级与外壳地4.5mm以上,空间距离3mm以上,不足时开1mm以上的槽增加沿面距离。
4.高压与地之间铜箔距离1mm以上,其它无要求铜箔间距离0.5mm以上。
二、走线、铜箔、焊盘、过孔1. 电源PCB最小走线0.3mm以上;2. 铜箔、走线与板边、挖槽处距离0.5mm以上;3.焊盘孔边与孔边距1mm以上,与板边距离1mm以上;4.SMD元件焊点与直立插件焊点间距需≥0.4mm;4.焊盘孔大小=元件引脚大小+(0.2~0.4 mm),变压器多引脚元件、自动插件元件应加0.4mm;5.焊盘孔径最小为0.8mm,同一块PCB孔径大小的类型越少越好,减少PCB加工成本;6.焊盘大小通常为孔径大小的2.0~2.3倍;7.后焊零件需开流锡槽,这样过波峰焊时内孔才不会被封住;8.过孔的大小由它的载流量决定,需要的载流量越大,所需的过孔尺寸越大,如电源层和地层与其它层联接所用的过孔就要大一些;9.Chip元件焊盘设计应掌握以下关键要素:三、自动插件技术1、零件方向以水平或垂直为主;2、零件与零件本体距离需1.0mm以上,零件本体与板边距离0.5mm以上;3、焊点与焊点间距离需0.5mm以上;4.自动插件元件焊盘孔径需≥1mm,一般为元件引脚大小+0.4mm;4、电阻、二极管等元件以卧式放置才可自动插件;7.自动插件电阻、二极管、跳线等卧式元件,脚距应为2.5mm的整数倍四、表面贴着技术1.零件方向以水平或垂直为主;2.SMD 贴片零件最小间距要求0.3mm;3.SMD零件摆设时需考虑过锡炉的方向,以防止阴影效应;波峰焊SMD元件的排布方向:4.SMD零件两端焊点铺铜应平均分布,以防止墓碑效应。
AI插件PCB设计规范
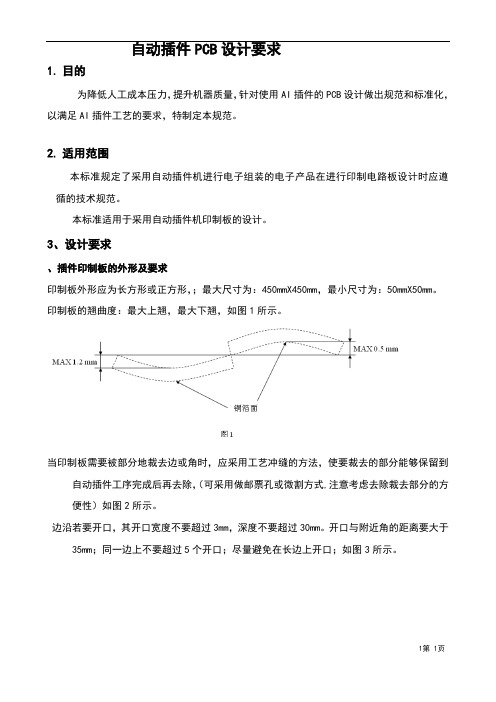
v1.0 可编辑可修改自动插件PCB设计要求1.目的为降低人工成本压力,提升机器质量,针对使用AI插件的PCB设计做出规范和标准化,以满足AI插件工艺的要求,特制定本规范。
2.适用范围本标准规定了采用自动插件机进行电子组装的电子产品在进行印制电路板设计时应遵循的技术规范。
本标准适用于采用自动插件机印制板的设计。
3、设计要求、插件印制板的外形及要求印制板外形应为长方形或正方形,;最大尺寸为:450mmX450mm,最小尺寸为:50mmX50mm。
印制板的翘曲度:最大上翘,最大下翘,如图1所示。
当印制板需要被部分地裁去边或角时,应采用工艺冲缝的方法,使要裁去的部分能够保留到自动插件工序完成后再去除,(可采用做邮票孔或微割方式,注意考虑去除裁去部分的方便性)如图2所示。
边沿若要开口,其开口宽度不要超过3mm,深度不要超过30mm。
开口与附近角的距离要大于35mm;同一边上不要超过5个开口;尽量避免在长边上开口;如图3所示。
印制板的插机定位孔采用AI 插件的印制板应在最长的一条边上设置主副两个电插定位孔。
如图4所示(元件面)。
其中左下角为主定位孔,孔径为Ø;右下角为副定位孔,其孔径尺寸应为Ø的鹅蛋形定位两定位孔的中心轴连线平行于最长边,离最长边的距离为±,主定位孔与左边的距离为±,副定位孔孔边与右边的距离应不小于,定位孔周围从孔边向外至少 2mm 范围内应覆铜箔以增加板的机械强度。
主副两定位孔的中心距L 的优选系列为:290mm 、235mm 、350mm ,误差为±。
主定位孔副定位孔AI插件PCB定位孔在元件面标记符号图中用方框标示。
印制板的非AI插件区在非AI插件区内布置的元件(其插孔在此区内)不适用于AI插件,如该部分确需布件,就需采用手工插件。
对于卧插元件,其非AI插件区(定位盲区和边缘盲区)为图5所示画有斜线的区域,如该部分有元件,需采用手插。
AI插件机PCB设计规范要求
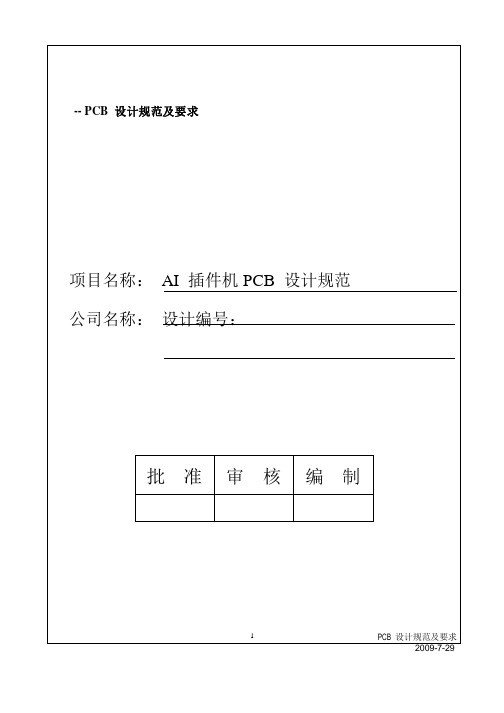
项目名称:AI插件机PCB设计规范
公司名称:设计编号:
批准
审核
编制
1PCB设计规范及要求
2009-7-29
1:印刷线路板设计标准:
2.1印刷线路板规格。
机器正面
2PCB设计规范及要求
2009-7-29
2.2插入限制:
3PCB设计规范及要求
2009-7-29
元件长度:
编带精度(I):最大Lb=插入跨距(P)-1.6编带精度(Ⅱ):最大Lb=插入跨距(P)-2.O编带精度(Ⅲ):最大Lb=插入跨距(P)-2.7
印刷线路板公差:
6PCB设计规范及要求
2009-7-29
★插入跨距为5mm时,最大Lb为3.4mm29
计算相邻元件之间需留的间隙:对以下计算所得的数值应再加O.2mm的余量。跳线直径:d,先前插入元件的引脚直径:d1先前插入元件的直径:D1,正要插入元件的直径:D2
5PCB设计规范及要求
2009-7-29
PCB设计软件Layout使用方法简介

PCB设计软件Layout使用方法简介当我们把原理图设计完毕,准备做实际电路的测试或者要制成最终的产品,就要用到PCB(印刷电路板)的设计工具。
OrCAD是一套完整的电路板设计工具,他的PCB设计工具是Layout和Layout Plus(比Layout功能强,下面的讲述主要以Layout Plus为主,为了方便,我们也称之为Layout),本章的内容将指导大家学习这套软件的使用。
要熟悉PCB设计软件的使用,就必须要对印刷电路板有很比较深刻的理解。
随处可见的电路板都可以作为很好的例子,平时多观察就会对电路板设计有很好的帮助。
实际的电路板可能有单层、双层、四层或者更多层。
最常见的电路板是双层和四层板,每一层上的“铜线”(track)和“铜膜”(copper pour)都是电气上相连的,不同层之间通过“过孔(via)”相连。
与原理图设计比较,PCB中的铜线、铜膜和过孔都是原理图中连线的实际表现。
一般来说,在制作PCB之前都要先完成原理图的设计,只有PCB和原理图完全一一对应,才可以保证制作出来的电路板符合设计的要求。
PCB的设计流程一般分为:网表(Netlist)输入、规则设置、元器件布局、布线、检查、复查、输出六个步骤,下面就分别对这几个步骤进行介绍。
一、 网表输入我们作为例子的电路原理图如下所示。
完成原理图的设计是PCB制作的开端。
图D-1 示例电路原理图PCB图和原理图的联系是一个被称作“网表”的文件,这个文件由Capture根据原理图生成,然后被Layout软件引入。
网表文件包含了电路图中包括的所有器件的封装(footprint,可以理解为元器件的外形)信息和器件各个引脚的连接信息。
器件的外形信息,也就是封装,在PCB设计中是最重要的,也是最容易出问题的地方。
因为同样的器件可能会有不同的封装类型,例如常见的74系列器件就有双列直插(DIP)和表面贴装(SMT)的区别。
一般来说,在设计PCB之前需要把器件拿到手再决定所选用的封装类型,否则即使你选择的封装没有错,也有可能发生买不到这种封装的情况。
AIPCBLayout规范
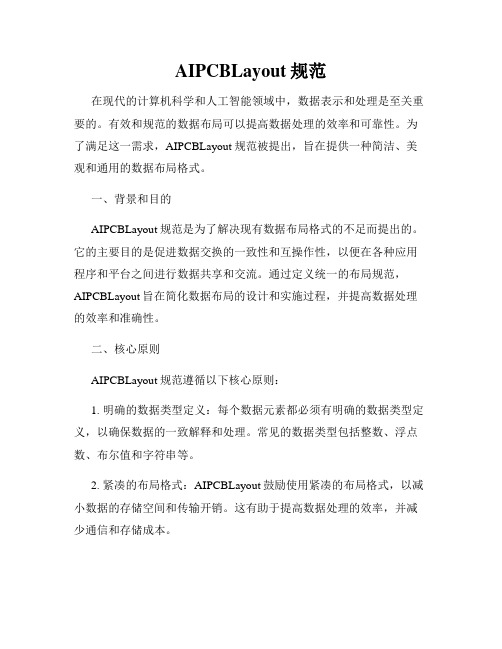
AIPCBLayout规范在现代的计算机科学和人工智能领域中,数据表示和处理是至关重要的。
有效和规范的数据布局可以提高数据处理的效率和可靠性。
为了满足这一需求,AIPCBLayout规范被提出,旨在提供一种简洁、美观和通用的数据布局格式。
一、背景和目的AIPCBLayout规范是为了解决现有数据布局格式的不足而提出的。
它的主要目的是促进数据交换的一致性和互操作性,以便在各种应用程序和平台之间进行数据共享和交流。
通过定义统一的布局规范,AIPCBLayout旨在简化数据布局的设计和实施过程,并提高数据处理的效率和准确性。
二、核心原则AIPCBLayout规范遵循以下核心原则:1. 明确的数据类型定义:每个数据元素都必须有明确的数据类型定义,以确保数据的一致解释和处理。
常见的数据类型包括整数、浮点数、布尔值和字符串等。
2. 紧凑的布局格式:AIPCBLayout鼓励使用紧凑的布局格式,以减小数据的存储空间和传输开销。
这有助于提高数据处理的效率,并减少通信和存储成本。
3. 可扩展性和可兼容性:AIPCBLayout支持数据布局的可扩展性和可兼容性。
它允许向现有布局中添加新的数据元素,同时保持对旧布局的向后兼容性。
4. 结构化的数据布局:AIPCBLayout规范鼓励使用结构化的数据布局,以提高数据的可读性和可维护性。
结构化布局可以通过使用层次结构、组合和嵌套来组织数据元素。
三、AIPCBLayout格式示例下面是一个示例,展示了使用AIPCBLayout规范定义的数据布局格式:```{"type": "object","properties": {"name": {"type": "string"},"age": {"type": "integer"},"address": {"type": "object","properties": {"street": {"type": "string"},"city": {"type": "string"},"country": {"type": "string"}}}}}```在这个示例中,我们定义了一个包含姓名、年龄和地址的数据布局。
AI插件机PCB设计规范要求

AI插件机PCB设计规范要求随着科技的不断发展和普及,人工智能已经越来越被广泛应用在各个行业中。
在电子工业中,AI插件机PCB已经成为不可或缺的一个重要部分。
然而,为了保证其可靠性和稳定性,在设计中需要遵守一系列规范要求。
本文将详细介绍AI插件机PCB设计规范要求。
一、布局原则1.信号线与电源线分离布局。
这是因为信号线和电源线的电性质不同,如果两者混在一起,会产生互相干扰和噪声。
2.在布局时,要注意信号线的长度和走向。
信号线的长度应该尽量短,走向应该尽量避免过于复杂的弯曲。
这样可以减小信号的衰减和传输错误的概率。
3.电源线的布局也需要考虑好。
一般来说,电源线应该尽量接近负载,且需要规划好电源的限流电阻,以防止过流电流对电路的损坏。
4.信号和电源线的布局应该与功能模块的位置相对应,以最大程度地减少线路长度。
二、元件组合原则1.要求元件品种合理、组合适宜、电路结构合理。
元件的选用应符合可靠性、稳定性和性能的要求。
2.对于信号放大器、滤波器、数据转换器等关键部件,需要选择高质量的元件。
3.元件之间的接口和连接方式应符合标准化和规范化的要求。
在连接中需要注意防止电磁干扰和信号干扰。
三、电源系统设计原则1.对于电源系统的设计,需要考虑到稳定性和可靠性。
为了避免纹波过大,需要选择高质量、低纹波的电源。
2.电源系统需要加入保护电路,以避免超过规定电压范围的电压对电路的损坏。
3.在电源系统的设计中,需要考虑到电池系统、变压器、整流器等元件的选用和位置布置。
四、接口设计原则1.在设计接口时,需要考虑到接口的标准化和匹配性。
尽量使用标准接口,并需要定义接口标准。
2.接口的位置和设计需要易于扩展和升级,以适应未来的使用需求。
3.需规定接口的工作范围和工作温度范围,并对接口线路进行可靠性测试,以确保接口的稳定性和可靠性。
五、测试设计原则1.在测试设计中,需要定义测试结果的准确性和精度,并考虑如何对测试结果进行合理的分析和处理。
AI制程PCB设计规范
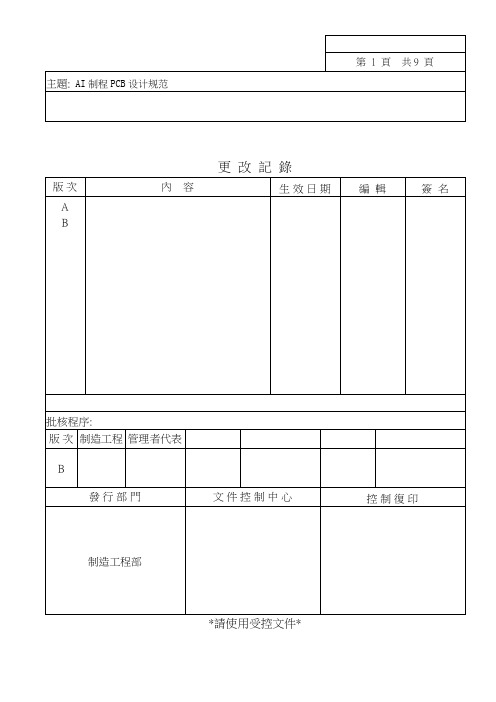
图 14
第8 頁 共9頁
文件編號:WII-259 版次:B
Radial 元件与 SMT 元件间的密度: Bottom Side SMT 元件与 Radial 元件的密度 由于 Radial 插件机的元件剪断弯脚部件在进行 Radial 插件时会与 PCB 的 Bottom Side 有较近的 距离,为此对 Bottom Side 的 SMT 元件与 Radial 元件孔的距离有要求。
5~15
2.5±0.1
图 4.2
2.5±0.1
S2=5~15
2.5±0.1
S1=5~15
图 4.1
第3 頁 共9頁 文件編號:WII-259 版次:B
图5
5
元件的插孔 3.4.1 元件插孔中心连线的平行度或垂直度如图 7 所示。 3.4.2 元件插孔的中心距 CS:
卧插元件 CS=5.5~20mm,如图 7 示 立插元件 CS=2.5/5.0/7.5±0.1mm,如图 8 所示。 3.4.3 元件插孔直径 Ø 卧插元件: Ø=1.3±0.1mm(塑封整流二极管等 0.8mm 引线的元件)
3.3印制板的非电插区 3.3.1 在非电插区内布置的元件(其插孔在此区内)不适用于自动插机。 3.3.2 对于自动插机元件,其非电插区(定位盲区和边缘盲区)为图 5 所示画有剖线的区域。 3.3.3 为防止工装、夹具等损伤印制板边沿的印制线,应避免在印制板边沿 3mm 范围内布宽度 1mm
以下的电路走线。
自动插件工序完成后再去除,如图 2 所示。 3.1.4 边沿若要开口,其开口宽度不要超过 3mm,深度不要超过 3.0mm。开口与附近角的距离要大
于 3.5mm;同一边上不要超过 5 个开口;尽量避免在长边上开口;如图 3 所示。
AI工艺设计规范
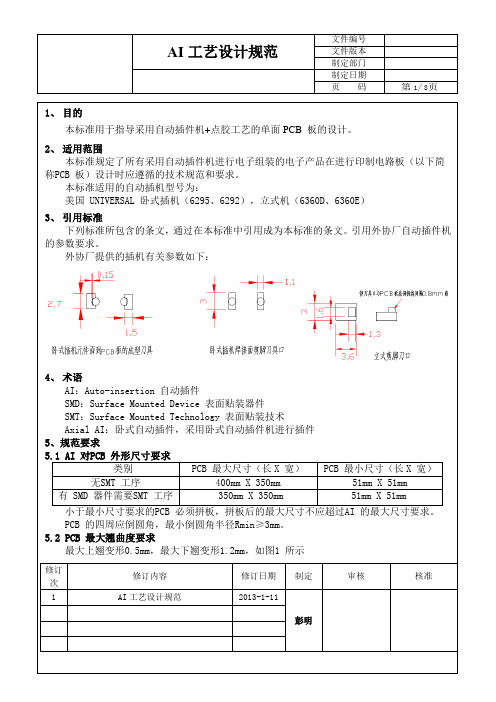
AI 工艺设计规范
文件编号 文件版本 制定部门 制定日期 页码
第 8/ 8 页
6、 参考文件: UNIVERSAL《GS-403-04》 IPC-A-610D
7、附件: 无
AI 工艺设计规范
文件编号 文件版本 制定部门 制定日期 页码
第 7/ 8 页
5.7.4 卧式和立式混插的AI 器件布局距离要求 混合做AI 的产品一般先做卧式AI,再做立式RH.其布局之间的距离除满足上述4.7.2
和 4.7.3 要求外,还需要满足下列图示要求
基本要求:本体之间应≥1.0mm,焊盘的距离应≥1.0mm 保证波峰焊接不连锡。 5.7.5 AI 器件和SMD 器件的布局距离要求
二个引脚的元件,P=2.5mm 或 5.0mm
三个引脚的元件,P=2.5mm 5.4.5 跳线设计要求
跳线尺寸:Φ 0.6±0.02mm 的镀锡引线。 跳线孔之间的距离为:最小5mm,最大20 mm。可选取在此范围内的自然整数。 5.5 PCB 定位孔 板的长边方向必须设置二个直径4mm(优选),次选直径3.8mm 或3.5mm 的定位孔,位置 参见下图。拼板后整个 PANANL 的要求同上。
同时需要满足: 6mm ≤ P ≤ 20mm
例如,一个长L为6mm,引脚直径0.7mm的卧式电阻,其焊孔间距P P = 6-(√2*0.7-1.131)+ 2*0.81 + 0.25 = 8.0112 mm 实际取 P=9mm
5.4.3 立式 AI 的器件要求
项目
要求
圆柱型元件本体直径 D
D ≤ 10mm
小于最小尺寸要求的PCB 必须拼板,拼板后的最大尺寸不应超过AI 的最大尺寸要求。 PCB 的四周应倒圆角,最小倒圆角半径Rmin≥3mm。 5.2 PCB 最大翘曲度要求 最大上翘变形0.5mm,最大下翘变形1.2mm,如图1 所示
- 1、下载文档前请自行甄别文档内容的完整性,平台不提供额外的编辑、内容补充、找答案等附加服务。
- 2、"仅部分预览"的文档,不可在线预览部分如存在完整性等问题,可反馈申请退款(可完整预览的文档不适用该条件!)。
- 3、如文档侵犯您的权益,请联系客服反馈,我们会尽快为您处理(人工客服工作时间:9:00-18:30)。
自动插件PCB 板工艺标准(A0版)
(FOR UNIVERSAL)
现AI 部拥有环球卧式、松下立式插件机,由于机器的特性,对于PCB 板有它的工艺标准,为了使现时自动插件机发挥最大效率,提高产品质量,特整理和制定了这份工艺标准供设计PCB 板和检验PCB 板来料作参考。
一、PCB 板尺寸要求(参考图1)
在不考虑SMT 贴片机情况下:最大尺寸:457.2mm(长) 300mm(宽) 需AI/SMT 混合工艺生产时:最大尺寸:330mm (长) 250mm (宽)
(注:如PCB 板小可考虑拼板以便提高插件效率)
图1
二、PCB 板定位孔要求(参考图1)
A 、定位孔形状因考虑放板的方便及定位的准确性,要求左边圆形定位孔为标准 位置,右边为椭圆形定位孔(元件面朝上)
B 、定位孔大小标准:左边圆形标准定位孔直径Φ=4.0mm
右边椭圆形定位孔长度A=6.0mm ,宽度B=4.0mm 但定位孔直径Φ必须等于椭圆形定位孔宽度B(Φ=B)。
C、定位孔误差:(参考图1)
L1-L2 ≤0.05mm L1=5.0±0.05MM L2=5.0±0.5mm S1=5.0±0.5mm
D、定位孔跨距S2
板长度(mm) 跨距(mm) L ≤35.5
S2=L-10 355≤L≤457.2
330≤S2≤345
E 、当PCB 定位孔过多,生产时容易造成PCB 板取向方向混淆,故设计PCB 板时,则只需在该PCB 板长边设计一组定位孔。
当PCB 板元件面朝上时,左边为圆形定位孔,右边为椭圆形定位孔。
三、DYNA-PERT &UNIVERSAL 自动插件机可插以下元件:
椭圆形定位孔宽度b=4.0±0.05mm
长度a=60±005mm
1、 1/16W 1/18W 1/4W(为了自动插件机刀具的使用
寿命,建议1/2W 电阻不在自动插件机AI 生产)
D 2、 色环电容
3、二极管
4、色环电感
四、元件跨度C 的范围:
L,如果L 过长,插件容易打伤元件体或
打断元件引脚,损坏插件刀具,同时对排料机要求非常严格,如果过大,插件机速度会降低,插件时容易掉料元件容易损坏,因此,根据不同元件定出适合的跨度。
推算方式:一般小元件(C=MAXL+1.3mm)
1/4W 电阻 1/2W 电阻、二极管、电感(C=MAXL+2.8mm) 参考标准:
元件
最佳跨度 最小跨度 最大跨度
1/16W 1/18W 6.0mm-9.0mm 5.4mm
17.0mm
色环电容 6.0mm-9.0mm 5.4mm 17.0mm 跳线
6.0mm-9.0mm 5.4mm 1
7.0mm 1/4W 电阻 大二极管
10.0mm-12.0mm 9.8mm 17.0mm 小二极管
7.0mm-9.0mm 6.5mm 17.0mm 1/2W 电阻 电感
14.3mm-15.0mm 13.8mm
17.0mm
五、现时PCB 板供应商工艺质量控制得不是很好,如果再加上元件孔径过小,就不符合插件机的插件要求,那将会极大的增加插件坏机率,并且需要增加大量人手去弥补(检查员检查和补件)。
但是,如果元件孔径过大,又将会导致元件过松容易脱落,并且会产生锡点不良等质量问题。
自插机要求: MIND=MAX d=0.45mm
元件
最小孔径 最大孔径
1/16W 1/8W 电阻 0.95mm 1.05mm 色环电阻
0.95mm 1.05mm 1/4W 色环电感
0.95mm 1.05mm 0.6mm 跳线
0.95mm 1.05mm 二极管
0.95mm 1.05mm
PCB
注意:元件孔不能歪斜,不能有毛刺,不可以成喇叭状,否则,孔径符合要求也会使自动插件不良率高,效率低。
六、元件密度要求:
PCB ①板元件密度越大,自插机走位越小,因此效率越高。
但是元件密度过大,插件时会打伤打断邻近的元件,损坏刀具,下图是插件机能够接受的最大密度:
平行方向:MIN A=3.0mm 向:MIN B=3.0mm
(A 与B 均为孔中心到孔中心的距离)
PCB ②板的元件不能太靠近板边缘(元件孔中心到板边ΔX ≥5.0mm)太靠
近PCB 板边缘,机器不能接受,周转笼(已开始箱改为笼)也会把PCB 板边缘
如果PCB 板铜皮面线路较密,自动插件时容易造成元件与相邻铜皮短路,
因此在设计PCB 板时应在元件焊盘边加白油保护。
(如下图)
≥3.0mm ≥1.2mm
MAX W1 MAX W2
1.2mm 0.8mm
九、元件孔偏差:
十、同一型号
PCB 板元件孔座(相对于孔中心)的偏差不大于0.05mm.
要求:X Y 的偏差
不大于0.05mm
十一、PCB 板之间的连接位的要求:
板与板之间的连接位如为针孔连接方式,则需要连接强度可靠,如为 "∨"槽连接,"∨"形槽的尺寸参照下图:
D D1
D1=D2=1/4D
十二、拼板必須同向。
以上工艺标准为AIS 部所制定,从生效日期起,我部将按以上标准检 验 PCB 板,凡不符合以上工艺标准的PCB 板将被判为不良,望相关部门合作。
多谢!
自动插件立式元件设计参考及PCB来料检查标准
一、立式元件插件机可插元件:
立式元件插件机可插两脚和三脚元件,如LED,微调电位器、微调电
容、小型开关、轴向元件、三极管、电容、电感、晶振、SDP包装
等。
电阻片状电容三极管晶振二极管电解电容SIP包装
开关微调电位器LED
二、立式元件要求
1、元件来料必须有编带
两脚元件编带
三脚元件编带
2 、元件外形尺寸要求:
鉴于我厂插件机使用的刀具,以上立式元件的外形尺寸要求如下:
A 两脚元件
序号说明最小最大
A 元件体高度0.36mm21.5mm
B 元件体真直径0.71mm10.5mm
C 矩形元件体宽度0.71mm26.16mm
D 元件脚脚径0.36mm0.71mm
D1 D2 矩形元件脚尺寸0.36mm0.71mm
E 元件脚间距 4.90mm 5.10mm
B 三脚元件
序号说明最小最大
A 元件体高度0.36mm 21.5mm
B 元件体真直径0.71mm 10.5mm
C 矩形元件体宽度0.71mm 26.16mm
D 元件脚脚径0.36mm 0.71mm
D1 D2 矩形元件脚尺寸0.36mm 0.71mm
E 元件脚间距 4.90mm 5.10mm
E1 E2 元件脚间距 2.45mm 2.55mm
三、元件密度要求:
在进行插件时,如果元件间的密度过大,会令已插入的元件被正要插入的元件碰松(掉)或正要插入的元件被已插入的元件碰飞,这样会造成过多的插件不良,因此元件的密度在情况允许下应尽量设计小一些。
元件俯视图
要求:D1≥1.0mm
D2≥5.0-MIN(r1 r2)
min D2=1.0mm
注:MIN(r1 ,r2)表示取r1和r2中最小的值,例r1=3.0 则MIN(r1,r2)=3.0
四、我部立工插件機(6380B)可以生產任何角度的立式元件,但元件孔這間距離須符工芑
標准(5.0或2.5mm),不須平行或垂直。
五、元件极向要求
对于有极性的立式元件,如三极管、二极管、电解电容、LED等,要求极性方向一
致,(通常规定X方向元件负极向左,Y 方向元件负极向上),否则自动插件机生产效
率降低,编制插件机程序困难,浪费插件机站位(如果方向不一致,同一种元件要占用
2个站位,若方向一致,只需一个站位),而且人工手补时较难辩认极性,容易插反。
*此点对于人手插件PCB设计同样适用
X方向元件负极全部向左极性不统一负极
向左向右向上向下均有
Y方向元件负极全部向上
GOOD NO GOOD
六、PCB元件孔跨度C(C1)的要求
七、PCB元件孔径的要求
D1:元件脚直径D2:元件孔直径
自插机要求:|
MinD2=Max D1+0.45mm
Max D2=Max D1+0.55mm
现鉴于我公司用材料,定出一个标准为:
0.95mm<D2<1.05mm
请注意:此孔比较大,如果用人手插件,会产生浮脚、锡点不良等质量问题。
因此在设计时应明确该元件是手插还是机插。
八、PCB板允许变元形范围(参考卧式工艺标准)。
九、元件孔座偏差(参考卧式工艺标准)
X Y偏差≤0.05mm
十、连接位(参考卧式工艺标准)
D1=D2=1/4D
十一、元件铜皮白油保护尺寸
由于直插元件剪脚方式与卧式不同,元件脚反向45度(下图所示)因些设计焊盘时后考虑相邻元件脚是否相碰短路。
白油的位置也是反向45度
(下图所示)。