甲醇合成铜基催化剂催化活性及失活研
甲醇合成催化剂失活分析
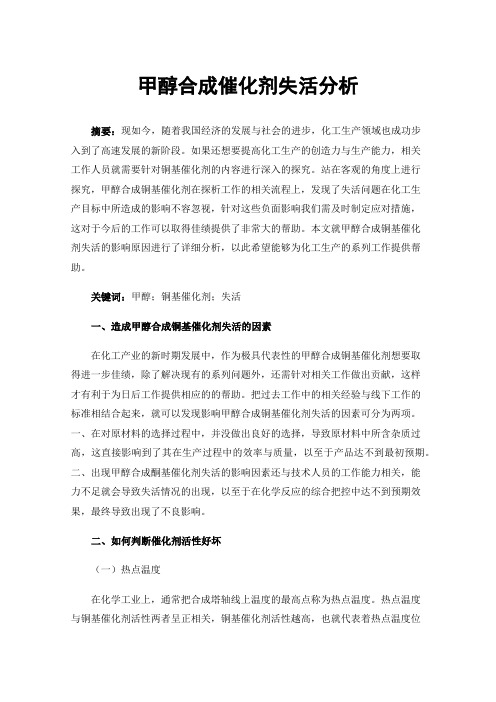
甲醇合成催化剂失活分析摘要:现如今,随着我国经济的发展与社会的进步,化工生产领域也成功步入到了高速发展的新阶段。
如果还想要提高化工生产的创造力与生产能力,相关工作人员就需要针对铜基催化剂的内容进行深入的探究。
站在客观的角度上进行探究,甲醇合成铜基催化剂在探析工作的相关流程上,发现了失活问题在化工生产目标中所造成的影响不容忽视,针对这些负面影响我们需及时制定应对措施,这对于今后的工作可以取得佳绩提供了非常大的帮助。
本文就甲醇合成铜基催化剂失活的影响原因进行了详细分析,以此希望能够为化工生产的系列工作提供帮助。
关键词:甲醇;铜基催化剂;失活一、造成甲醇合成铜基催化剂失活的因素在化工产业的新时期发展中,作为极具代表性的甲醇合成铜基催化剂想要取得进一步佳绩,除了解决现有的系列问题外,还需针对相关工作做出贡献,这样才有利于为日后工作提供相应的的帮助。
把过去工作中的相关经验与线下工作的标准相结合起来,就可以发现影响甲醇合成铜基催化剂失活的因素可分为两项。
一、在对原材料的选择过程中,并没做出良好的选择,导致原材料中所含杂质过高,这直接影响到了其在生产过程中的效率与质量,以至于产品达不到最初预期。
二、出现甲醇合成酮基催化剂失活的影响因素还与技术人员的工作能力相关,能力不足就会导致失活情况的出现,以至于在化学反应的综合把控中达不到预期效果,最终导致出现了不良影响。
二、如何判断催化剂活性好坏(一)热点温度在化学工业上,通常把合成塔轴线上温度的最高点称为热点温度。
热点温度与铜基催化剂活性两者呈正相关,铜基催化剂活性越高,也就代表着热点温度位置越高。
在其床层的上方位置反应物的浓度可以达到最高值,生成物的浓度相反确是最低点,这时所形成的运动反应是最剧烈的,铜基催化剂的温度也因此呈持续上升趋势。
当到达温度巅峰值后,生成物的浓度增加反应物的浓度降低,反应进程开始减慢。
反应的生成物热量被带走,床层的温度逐渐降低。
(二)铜基催化剂床层温差铜基催化剂的床层温度变化过大,就会造成部分床层温度达不到铜基催化剂活性温度的状况出现,这就会出现变化反应都集中在局部活性温度达标的地点,从而释放热量,因此化学反应越剧烈就会带动床层温度变化越大,铜基催化剂的活性温度也就因此变得更好了。
铜基催化剂的制备及其催化甲醇变换研究

铜基催化剂的制备及其催化甲醇变换研究近年来,铜基催化剂在催化领域中日益受到人们的关注。
铜作为一种廉价、易得、丰富的元素,具有很多种不同的氧化态,并能够形成不同的配位化合物,因此对于催化反应具有很好的应用前景。
本文将介绍铜基催化剂的制备及其在甲醇变换反应中的应用研究。
一、铜基催化剂的制备方法常用的制备铜基催化剂的方法有共沉淀法、沉淀还原法、浸渍法、脉冲喷雾法等。
其中,共沉淀法是一种常见的制备方法,其步骤简单,操作方便。
具体流程为:将金属铜盐和碱性沉淀剂(如氢氧化钠)按适当比例加入到有机溶剂中,并进行搅拌使其完全反应,然后过滤、洗涤、干燥即可得到催化剂。
沉淀还原法则是将金属铜盐与还原剂(如氢气)反应,使其还原为金属铜颗粒,可以得到高纯度、高催化活性的催化剂。
不过该方法操作性复杂,需要高温高压条件下进行。
浸渍法是将载体浸泡于预先配好的含有铜盐的溶液中,待溶液逐渐干燥后,再进行烧结,形成铜基催化剂。
该方法具有操作简便、催化活性较高等优点。
脉冲喷雾法则是一种新型的微粒制备技术。
利用电脉冲电压在短时间内将铜基溶液喷雾成微粒,并在空气中凝结,得到纳米级铜基催化剂,具有高比表面积、高分散度、可控制备等特点。
二、铜基催化剂在甲醇变换中的研究甲醇变换反应是将甲醇转化为一种更高级别、含碳量更高的化合物的过程,通常是甲醇制取甲烷、甲基氧化物或乙醇等。
铜基催化剂在该反应中具有重要应用价值。
铜基催化剂通常是将载体与合适的铜盐进行浸润或共沉淀,形成铜基催化剂。
同时,铜在反应中发挥的催化作用是氧化还原过程,其能够在反应中扮演氧化剂和/或还原剂的角色,控制反应中产物的选择性和活性。
由于甲醇转化反应的反应机理复杂,导致铜基催化剂的研究存在一定的困难,但是学术界已经取得了一系列的研究成果。
一项研究结果表明,以La2O3负载的Cu-Zn-Al催化剂对甲醇转化反应有较好的活性和选择性。
在该反应中,氧化铜被还原形成Cu0,并参与反应产生甲烷,较少生成二甲醇、甲醛等不必要的副产物。
甲醇合成铜基催化剂催化活性及失活研

甲醇合成铜基催化剂催化活性及失活研究1引言甲醇是一种极其重要的化工原料,主要用于生产一系列化工产品,还可用作潜在的车用醇醚燃料电池的燃料等。
随着甲醇制烯烃等技术进步及下游产品的开发,特别是甲醇燃料电池的开发和应用,合成甲醇的研究越来越受到广泛重视。
目前,甲醇的工业生产主要是采用CO/CO2催化加氢技术,所以甲醇合成催化剂的研发是甲醇合成工业的基石。
甲醇工业的发展很大程度上取决于催化剂的研制及其性能改进。
在甲醇生产中,很多工业指标和操作条件都是由催化剂的性质决定的。
随着甲醇工业的快速发展,对甲醇合成催化剂的研究开发提出了更高的要求。
2 甲醇合成催化剂在甲醇合成过程中,催化剂的重要性显而易见,目前工业上使用的甲醇合成催化剂一般可分为锌铬催化剂和铜基催化剂两类。
国外比较有名的研究和生产甲醇合成催化剂公司主要有英国ICI公司、德国BASF公司、德国SudChemie公司和丹麦TopsΦe公司等,国内研究铜基催化剂的院所主要有南化集团研究院、西南化工研究设计院,西北化工研究院及齐鲁石化研究院等[1]。
锌铬(ZnO/Cr2O3)催化剂由德国BASF公司于1923年首先开发研制成功。
操作温度必须在590 K~670 K,操作压力必须为25 MPa~35MPa,锌铬催化剂的特点是:耐热性能好、对硫不敏感,机械强度高,使用寿命长,使用范围宽,操作控制容易,但是其活性低、选择性低、产品中杂质复杂,精馏困难。
铜基催化剂由英国ICI公司和德国Lurgi公司先后研制成功,操作温度为210℃~300℃,压力为5MPa~10MPa,比传统的合成工艺温度低得多,对甲醇反应平衡有利。
其特点是:活性好,单程转化率为7%~8%;选择性高,大于99%,易得到高纯度的精甲醇;耐高温性差,对合成原料气中杂质比较敏感。
目前工业上甲醇的合成主要使用铜基催化剂。
近年来,新型催化剂的研制也在一直进行,新型催化剂的研制方向在于提高活性,改善热稳定性及延长催化剂使用寿命等,如钯系、钼系及低温液相催化剂,但这些催化剂因活性不理想或对甲醇的选择性较差,还只停留在研究阶段未实现工业化。
铜基甲醇合成催化剂的TPR研究

有最佳 c / n 即5 4 的铜基催化剂 , uZ ( / ) 其主还原温度最低。考察了在不同p H值时进行并流共沉淀 所制备的催化剂的Ⅱ), R 表明沉淀时的 p H值对催化剂的结构有很大影响, 并对其本质原 因 进行了深 入探讨。另外, 了铝含量对催化荆还原行为的影响以 考察 厦在不同升温速率下 催化荆 T R的差异。 P 关 键词 : 成 甲醇 ; 合 铜基催 化剂 ; 一步并 流共 沉 淀法
维普资讯
0 0 第20卷 第 3期 1 2年 5月
工 业 催 化
I DUS N TRI = 札 YS S AL CA r I
Ma 0 2 y2 0 v0. 0 No 3 11
铜 基 甲醇 合成 催 化剂 的 T R研 究 P
郭宪吉,叶长明,赵 蕾 , 向宇, 王 李利 民
GUO Xinj ,Y C an - i g,Z a -i E h g r n u HAO L i e ,WANG Xi gy an - u,LILi n - mi
( e at n f hmi r Z e gh uUnvr t H nnZ egh u4 0 5 , hn ) D pr me t e s y, h n o i s y, e a h n z o 5 0 2 C i oC t a ei a A src: r so p e—ae aa s t iee t u Z t ( oe weep p rdb n - bt t A s i f o p r sd ctl t wi df rn / nr i m l) r r ae yo e a ee c b ys h f C ao e
C C n mb rT 2 : Q 1 D ere t o eA A t l l 10 —14 (0 2 0 —02 —0 L u e : Q4 6 T 2 4 ouna d : ri ei 0 8 1 3 2 0 )3 0 5 4 c c D:
合成甲醇铜基催化剂及制备工艺研究进展
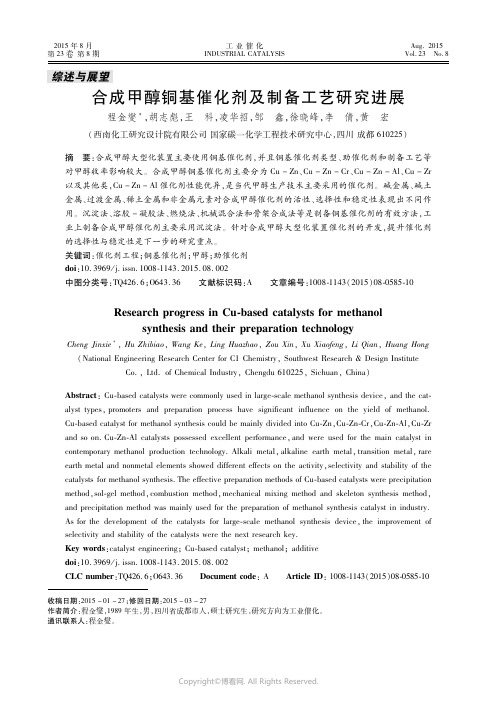
2015年8月第23卷第8期 工业催化INDUSTRIALCATALYSIS Aug.2015Vol.23 No.8综述与展望收稿日期:2015-01-27;修回日期:2015-03-27作者简介:程金燮,1989年生,男,四川省成都市人,硕士研究生,研究方向为工业催化。
通讯联系人:程金燮。
合成甲醇铜基催化剂及制备工艺研究进展程金燮 ,胡志彪,王 科,凌华招,邹 鑫,徐晓峰,李 倩,黄 宏(西南化工研究设计院有限公司国家碳一化学工程技术研究中心,四川成都610225)摘 要:合成甲醇大型化装置主要使用铜基催化剂,并且铜基催化剂类型、助催化剂和制备工艺等对甲醇收率影响较大。
合成甲醇铜基催化剂主要分为Cu-Zn、Cu-Zn-Cr、Cu-Zn-Al、Cu-Zr以及其他类,Cu-Zn-Al催化剂性能优异,是当代甲醇生产技术主要采用的催化剂。
碱金属、碱土金属、过渡金属、稀土金属和非金属元素对合成甲醇催化剂的活性、选择性和稳定性表现出不同作用。
沉淀法、溶胶-凝胶法、燃烧法、机械混合法和骨架合成法等是制备铜基催化剂的有效方法,工业上制备合成甲醇催化剂主要采用沉淀法。
针对合成甲醇大型化装置催化剂的开发,提升催化剂的选择性与稳定性是下一步的研究重点。
关键词:催化剂工程;铜基催化剂;甲醇;助催化剂doi:10.3969/j.issn.1008 1143.2015.08.002中图分类号:TQ426.6;O643.36 文献标识码:A 文章编号:1008 1143(2015)08 0585 10ResearchprogressinCu basedcatalystsformethanolsynthesisandtheirpreparationtechnologyChengJinxie,HuZhibiao,WangKe,LingHuazhao,ZouXin,XuXiaofeng,LiQian,HuangHong(NationalEngineeringResearchCenterforC1Chemistry,SouthwestResearch&DesignInstituteCo.,Ltd.ofChemicalIndustry,Chengdu610225,Sichuan,China)Abstract:Cu basedcatalystswerecommonlyusedinlarge scalemethanolsynthesisdevice,andthecat alysttypes,promotersandpreparationprocesshavesignificantinfluenceontheyieldofmethanol.Cu basedcatalystformethanolsynthesiscouldbemainlydividedintoCu Zn,Cu Zn Cr,Cu Zn Al,Cu Zrandsoon.Cu Zn Alcatalystspossessedexcellentperformance,andwereusedforthemaincatalystincontemporarymethanolproductiontechnology.Alkalimetal,alkalineearthmetal,transitionmetal,rareearthmetalandnonmetalelementsshoweddifferenteffectsontheactivity,selectivityandstabilityofthecatalystsformethanolsynthesis.TheeffectivepreparationmethodsofCu basedcatalystswereprecipitationmethod,sol gelmethod,combustionmethod,mechanicalmixingmethodandskeletonsynthesismethod,andprecipitationmethodwasmainlyusedforthepreparationofmethanolsynthesiscatalystinindustry.Asforthedevelopmentofthecatalystsforlarge scalemethanolsynthesisdevice,theimprovementofselectivityandstabilityofthecatalystswerethenextresearchkey.Keywords:catalystengineering;Cu basedcatalyst;methanol;additivedoi:10.3969/j.issn.1008 1143.2015.08.002CLCnumber:TQ426.6;O643.36 Documentcode:A ArticleID:1008 1143(2015)08 0585 10Copyright ©博看网. All Rights Reserved. 586 工业催化 2015年第8期 在世界能源快速消耗的情况下,C1化学发挥的作用日益重要[1],甲醇作为C1化学的基石倍受关注。
甲醇合成催化剂知识

甲醇合成催化剂知识d i4 X+ }1 z! j0 v1 铜基催化剂的催化原理 + W7 b1 C1 Y9 W4 M1 h)o9 F0 t8 j* c: D q, |6 O 目前,低压甲醇合成铜基催化剂主要组分是 CuO、ZnO和Al2O3,三组分在催化剂中的比例随着生产厂家的不同而不同。
一般来说, CuO的质量分数在40% ~80%, ZnO的质量分数在10% ~30%, Al2O3的质量分数在5% ~10%。
铜基催化剂在合成甲醇时, CuO、ZnO、Al2O3三组分的作用各不相同。
CO和H2在催化剂上的吸附性质与催化剂的活性有非常密切的关系。
在铜基催化剂表面对CO的吸附速率很高,而H2的吸附则比CO 慢得多。
ZnO是很好的氢化剂,可使H2被吸附和活化, 但对CO几乎没有化学吸附,因此可提高铜基催化剂的转化率。
纯铜对甲醇合成是没有活性的,H2和CO合成甲醇的反应是在一系列活性中心上进行的,而这种活性中心存在于被还原的Cu-CuO界面上。
在催化剂中加入少量 Al2O3的首要功能就是阻止一部分氧化铜还原。
当催化剂被还原后,开始进行反应时,合成气中的H2 和CO都是还原剂,有使氧化铜进一步还原的趋势。
这种过度的还原,使得活性中心存在的界面越来越小,催化剂活性也越来越低。
从合成的整个过程来看,随着还原表面向催化剂的内层深入,未还原的核心越来越小,作为被还原的Cu-CuO界面的核心表面积也越来越小,催化剂的活性降低,合成反应速率随之降低。
研究认为,Al2O3在催化剂中作为结构助剂起阻碍铜颗粒烧结的作用, CuO/ZnO/Al2O3催化剂的活性远高于双功能催化剂CuO/ZnO的活性。
q7 h- G8 n9 ]$ B5 m- Q: ?& ]/ D2 铜基催化剂助剂6 j8 } x5 L! ?0 V1 l1 K4 H$ Q! m% g\5 K8 e) C+ g5 A)E! ~ 铜基催化剂助剂的研究是甲醇合成催化剂研究的一个重要课题。
甲醇合成铜基催化剂制备工艺的研究
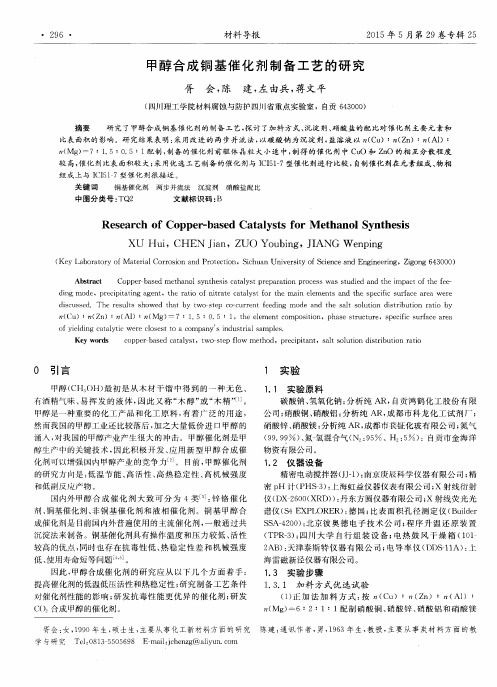
o f y i e l d i n g c a t a l y t i c we r e c l o s e s t t o a c o mp a n y S i n d u s t r i a l s a mp l e s .
Ke y wo r d s
( Ke y L a b o r a t o r y o f Ma t e r i a l Co r r o s i o n a n d Pr o t e c t i o n,S i c hu a n Un i v e r s i t y o f S c i e n c e a n d En g i n e e r i n g ,Z i g o n g 6 4 3 0 0 0 ) Ab s t r a c t Co p p e r b a s e d me t h a n o l s y n t h e s i s c a t a l y s t p r e p a r a t i o n p r o c e s s wa s s t u d i e d a n d t h e i mp a c t o f t h e f e e -
甲醇 是一 种重 要 的化 工 产 品 和 化工 原 料 , 有 着 广 泛 的用 途 , 然 而我 国的 甲醇工业 还 比较落 后 , 加 之 大量 低价 进 口 甲醇 的 涌人 , 对 我 国的 甲醇产 业产 生很 大 的 冲击 。 甲醇 催 化 剂 是 甲 醇生 产 中的关 键技 术 , 因 此 积极 开 发 、 应 用新 型 甲醇 合 成 催 化刺 可 以增强 国 内甲醇 产业 的竞 争 力 l 2。 目前 , 甲醇催 化 剂 的研 究方 向是 : 低温节能、 高 活性 、 高热稳定性、 高 机械 强 度
文献标识码 : B
甲醇合成催化反应机理及催化剂失活因素分析

甲醇合成催化反应机理及催化剂失活因素分析摘要:在甲醇生产过程中,甲醇合成催化剂常会发生中毒、高温烧结、失活等现象,大大影响了甲醇产量,也降低了催化剂的寿命,使生产成本进一步提高。
本文主要对甲醇合成催化反应机理及催化剂失活因素进行分析。
关键词:甲醇合成催化反应机理失活一、反应机理甲醇合成催化反应机理一直是研究人员关注和争议的焦点,不同的反应原料(CO/H2,或CO2/H2)、不同的催化剂、甚至相同的催化体系,催化剂结构不同,也可能导致反应机理不同。
有关反应机理的研究,主要集中在甲醇合成反应的直接碳源、反应的中间物种、反应的控速步骤以及CO在反应中的作用等问题。
早期研究者多数以动力学和H2、CO吸附等问接的实验结果为基础进行反应机理的研究;而现在多数基于同位素标记、光谱测定以及动力学模拟计算等比较直接的证据,但仍不能得出统一明确的结论。
本文按合成甲醇直接碳源的不同,将机理划分为以下3种:CO与CO2共同作为直接碳源机理、CO作为直接碳源机理以及CO2作为直接碳源机理。
(一)一氧化碳和二氧化碳作为直接碳源在CO和CO2加氢合成甲醇反应机理研究中,人们普遍认为甲酰基和甲酸基是反应过程的重要中间物种,CO吸附活化后直接生成甲酰基,而CO2吸附活化后生成甲酸基,并且CO和CO2可以通过表面氧或甲酸基等物种相互转化。
也有不同的观点认为CO吸附活化后与表面羟基结合生成甲酸盐,而CO则与表面氧结合生成碳酸根离子。
(二)一氧化碳作为直接碳源CO加氢合成甲醇的机理,可分为以下两种观点。
一种观点认为,CO首先在活性位上吸附活化,然后与吸附态的氢原子发生分步加氢反应,最终生成甲醇;而原料气中的CO2仅为补充碳源。
这种机理不能解释原料中少量CO2的存在能够明显促进甲醇合成反应的现象。
第二种观点认为,活化态的CO在加氢过程中同时与羟基、表面氧等物种发生反应,生成甲酸盐、甲氧基以及碳酸盐等中间物种,中间物种再通过脱氧及水解等反应生成甲醇。
甲醇合成铜基催化剂末期运行优化分析
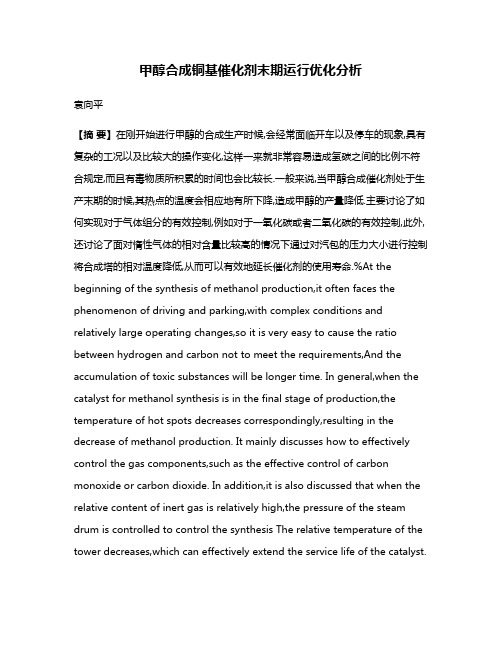
甲醇合成铜基催化剂末期运行优化分析袁向平【摘要】在刚开始进行甲醇的合成生产时候,会经常面临开车以及停车的现象,具有复杂的工况以及比较大的操作变化,这样一来就非常容易造成氢碳之间的比例不符合规定,而且有毒物质所积累的时间也会比较长.一般来说,当甲醇合成催化剂处于生产末期的时候,其热点的温度会相应地有所下降,造成甲醇的产量降低.主要讨论了如何实现对于气体组分的有效控制,例如对于一氧化碳或者二氧化碳的有效控制,此外,还讨论了面对惰性气体的相对含量比较高的情况下通过对汽包的压力大小进行控制将合成塔的相对温度降低,从而可以有效地延长催化剂的使用寿命.%At the beginning of the synthesis of methanol production,it often faces the phenomenon of driving and parking,with complex conditions and relatively large operating changes,so it is very easy to cause the ratio between hydrogen and carbon not to meet the requirements,And the accumulation of toxic substances will be longer time. In general,when the catalyst for methanol synthesis is in the final stage of production,the temperature of hot spots decreases correspondingly,resulting in the decrease of methanol production. It mainly discusses how to effectively control the gas components,such as the effective control of carbon monoxide or carbon dioxide. In addition,it is also discussed that when the relative content of inert gas is relatively high,the pressure of the steam drum is controlled to control the synthesis The relative temperature of the tower decreases,which can effectively extend the service life of the catalyst.【期刊名称】《化工设计通讯》【年(卷),期】2018(044)002【总页数】2页(P14,82)【关键词】甲醇合成;铜基催化剂;催化剂末期;工艺优化【作者】袁向平【作者单位】陕西神木化学工业有限公司,陕西榆林 719319【正文语种】中文【中图分类】TQ223.1211 概述从目前来看,对于甲醇的合成所采取的方法主要就是鲁奇工艺,通过将气冷合成塔与水冷合成塔相互串联来实现对于甲醇的有效合成。
甲醇合成催化剂知识-推荐下载
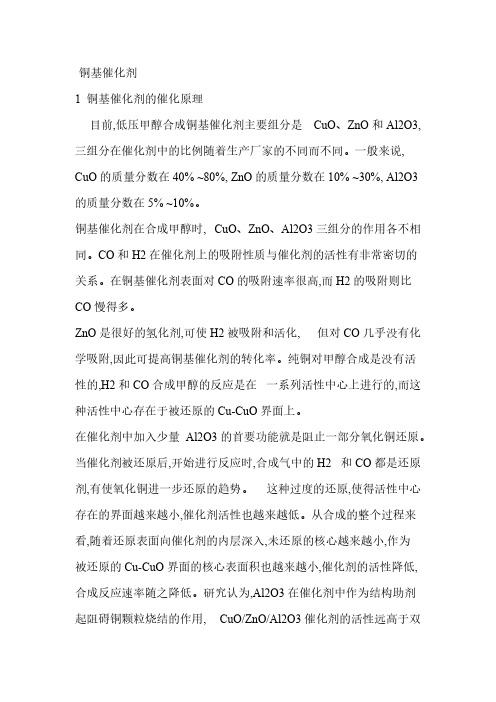
铜基催化剂1 铜基催化剂的催化原理目前,低压甲醇合成铜基催化剂主要组分是CuO、ZnO和Al2O3,三组分在催化剂中的比例随着生产厂家的不同而不同。
一般来说, CuO的质量分数在40% ~80%, ZnO的质量分数在10% ~30%, Al2O3的质量分数在5% ~10%。
铜基催化剂在合成甲醇时, CuO、ZnO、Al2O3三组分的作用各不相同。
CO和H2在催化剂上的吸附性质与催化剂的活性有非常密切的关系。
在铜基催化剂表面对CO的吸附速率很高,而H2的吸附则比CO慢得多。
ZnO是很好的氢化剂,可使H2被吸附和活化, 但对CO几乎没有化学吸附,因此可提高铜基催化剂的转化率。
纯铜对甲醇合成是没有活性的,H2和CO合成甲醇的反应是在一系列活性中心上进行的,而这种活性中心存在于被还原的Cu-CuO界面上。
在催化剂中加入少量Al2O3的首要功能就是阻止一部分氧化铜还原。
当催化剂被还原后,开始进行反应时,合成气中的H2 和CO都是还原剂,有使氧化铜进一步还原的趋势。
这种过度的还原,使得活性中心存在的界面越来越小,催化剂活性也越来越低。
从合成的整个过程来看,随着还原表面向催化剂的内层深入,未还原的核心越来越小,作为被还原的Cu-CuO界面的核心表面积也越来越小,催化剂的活性降低,合成反应速率随之降低。
研究认为,Al2O3在催化剂中作为结构助剂起阻碍铜颗粒烧结的作用, CuO/ZnO/Al2O3催化剂的活性远高于双功能催化剂CuO/ZnO的活性。
2 铜基催化剂助剂铜基催化剂助剂的研究是甲醇合成催化剂研究的一个重要课题。
铜基催化剂耐热强度较低,使用时间过长或操作温度过高都会造成铜的晶体长大使催化剂失去活性。
其热稳定性差,很容易发生硫、氯中毒,使用寿命短等缺点,一般通过加入其他助剂得以改善,由此形成具有工业价值的新一代铜基催化剂。
锌就是铜基催化剂的最好助剂,很少量的锌就能使铜基催化剂的活性提高。
加入Al2O3,可以使催化剂铜晶体尺寸减小,活性提高。
甲醇合成催化剂失活及影响因素分析

甲醇合成催化剂失活及影响因素分析摘要:甲醇 (CHOH) 是一种结构最简单的一元醇,也被称为木醇,因为它最3初存在于干燥的蒸馏木材中。
甲醇是一种无色挥发性液体,有酒精气味。
它是一种重要的化工原料,广泛用于化学实验和化学领域。
用途广泛,不仅可作为萃取剂,还可作为化工原料及其加工产品,如甲醛、醋酸、农药等。
随着科学技术的发展,甲醇转化为烯烃生产技术不断发展,甲醇转化为高附加值产品的力度不断加大对甲醇的需求不断增长,甲醇合成领域的研究越来越受到研究关注。
催化剂是一类能够在化学反应过程中改变化学反应速率而不被自身消耗的物质,广泛应用于许多化学反应中。
催化剂作为甲醇合成中的一个非常重要的环节,与甲醇生产中的许多条件和性能指标密切相关,其种类、性能和活性对甲醇的合成起着重要的作用。
因此,有必要对催化剂活性进行系统的分析和研究。
关键词:甲醇合成;催化剂失活;影响因素引言甲醇制烯烃是以甲醇为原料,在催化剂的作用下,在流化床反应器中进行脱水和碳链重整的过程,实现MTO工艺优化的核心和关键是MTO催化剂,具有极高的比表面积、良好的水热稳定性、丰富的质子酸性和离子交换位,独特的八元环三维孔道体系更使得它拥有了极好的小分子择形催化性能。
甲醇制烯烃SAPO-34分子筛工业化应用过程中因反应物、反应过程及传质等问题,引起催化剂失活和磨损,导致催化剂需要再生和补充新的催化剂,增加了生产成本,必须进行再利用。
本文综述甲醇合成催化剂失活的影响因素,并对提高甲醇合成催化剂活性的措施进行总结,提出甲醇催化剂今后的发展方向。
1甲醇合成催化剂失活的影响因素1.1结蜡问题( 1) 在催化剂装填过程中,如果铁锈或油脂等杂质带入合成塔内,会降低催化剂的活性和选择性,促进石蜡的生成。
( 2) 铜基催化剂在使用过程中,随着使用时间的增加,特别是催化剂使用中后期,受催化剂选择性的限制,会生成一定量的石蜡。
同时,甲醇生产时难免会伴有少量甲酸及其他有机酸生成,这些酸类物质在 CO 的作用下腐蚀合成塔生成Fe( CO)5与 Ni( CO)4,加速石蜡的生成。
铜基甲醇催化剂失活因素及解决措施研究进展
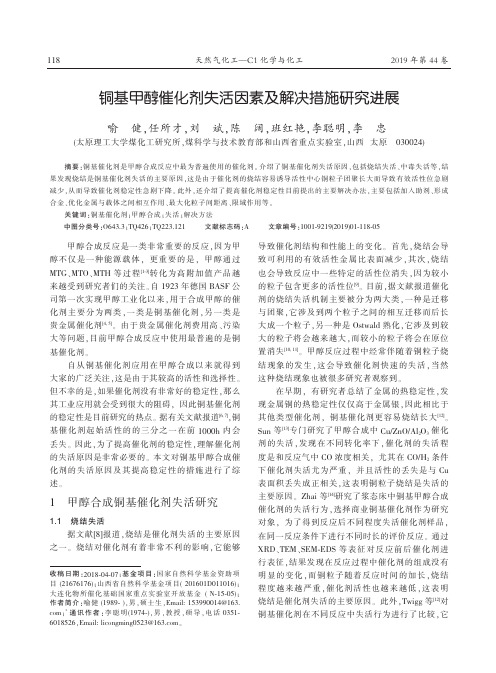
甲醇合成反应是一类非常重要的反应,因为甲醇不仅是一种能源载体,更重要的是,甲醇通过MTG、MTO、MTH等过程[1鄄3]转化为高附加值产品越来越受到研究者们的关注。
自1923年德国BASF公司第一次实现甲醇工业化以来,用于合成甲醇的催化剂主要分为两类,一类是铜基催化剂,另一类是贵金属催化剂[4,5]。
由于贵金属催化剂费用高、污染大等问题,目前甲醇合成反应中使用最普遍的是铜基催化剂。
自从铜基催化剂应用在甲醇合成以来就得到大家的广泛关注,这是由于其较高的活性和选择性。
但不幸的是,如果催化剂没有非常好的稳定性,那么其工业应用就会受到很大的阻碍,因此铜基催化剂的稳定性是目前研究的热点。
据有关文献报道[6,7],铜基催化剂起始活性的的三分之一在前1000h内会丢失。
因此,为了提高催化剂的稳定性,理解催化剂的失活原因是非常必要的。
本文对铜基甲醇合成催化剂的失活原因及其提高稳定性的措施进行了综述。
1甲醇合成铜基催化剂失活研究1.1烧结失活据文献[8]报道,烧结是催化剂失活的主要原因之一。
烧结对催化剂有着非常不利的影响,它能够导致催化剂结构和性能上的变化。
首先,烧结会导致可利用的有效活性金属比表面减少,其次,烧结也会导致反应中一些特定的活性位消失,因为较小的粒子包含更多的活性位[9]。
目前,据文献报道催化剂的烧结失活机制主要被分为两大类,一种是迁移与团聚,它涉及到两个粒子之间的相互迁移而后长大成一个粒子,另一种是Ostwald熟化,它涉及到较大的粒子将会越来越大,而较小的粒子将会在原位置消失[10,11]。
甲醇反应过程中经常伴随着铜粒子烧结现象的发生,这会导致催化剂快速的失活,当然这种烧结现象也被很多研究者观察到。
在早期,有研究者总结了金属的热稳定性,发现金属铜的热稳定性仅仅高于金属银,因此相比于其他类型催化剂,铜基催化剂更容易烧结长大[12]。
Sun等[13]专门研究了甲醇合成中Cu/ZnO/Al2O3催化剂的失活,发现在不同转化率下,催化剂的失活程度是和反应气中CO浓度相关,尤其在CO/H2条件下催化剂失活尤为严重,并且活性的丢失是与Cu 表面积丢失成正相关,这表明铜粒子烧结是失活的主要原因。
铜基催化剂的制备及其催化性研究
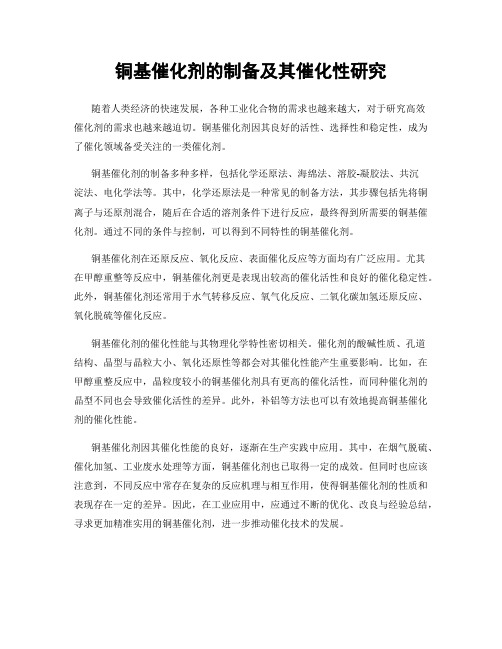
铜基催化剂的制备及其催化性研究随着人类经济的快速发展,各种工业化合物的需求也越来越大,对于研究高效催化剂的需求也越来越迫切。
铜基催化剂因其良好的活性、选择性和稳定性,成为了催化领域备受关注的一类催化剂。
铜基催化剂的制备多种多样,包括化学还原法、海绵法、溶胶-凝胶法、共沉淀法、电化学法等。
其中,化学还原法是一种常见的制备方法,其步骤包括先将铜离子与还原剂混合,随后在合适的溶剂条件下进行反应,最终得到所需要的铜基催化剂。
通过不同的条件与控制,可以得到不同特性的铜基催化剂。
铜基催化剂在还原反应、氧化反应、表面催化反应等方面均有广泛应用。
尤其在甲醇重整等反应中,铜基催化剂更是表现出较高的催化活性和良好的催化稳定性。
此外,铜基催化剂还常用于水气转移反应、氧气化反应、二氧化碳加氢还原反应、氧化脱硫等催化反应。
铜基催化剂的催化性能与其物理化学特性密切相关。
催化剂的酸碱性质、孔道结构、晶型与晶粒大小、氧化还原性等都会对其催化性能产生重要影响。
比如,在甲醇重整反应中,晶粒度较小的铜基催化剂具有更高的催化活性,而同种催化剂的晶型不同也会导致催化活性的差异。
此外,补铝等方法也可以有效地提高铜基催化剂的催化性能。
铜基催化剂因其催化性能的良好,逐渐在生产实践中应用。
其中,在烟气脱硫、催化加氢、工业废水处理等方面,铜基催化剂也已取得一定的成效。
但同时也应该注意到,不同反应中常存在复杂的反应机理与相互作用,使得铜基催化剂的性质和表现存在一定的差异。
因此,在工业应用中,应通过不断的优化、改良与经验总结,寻求更加精准实用的铜基催化剂,进一步推动催化技术的发展。
总之,铜基催化剂的制备及其催化性研究是一个十分重要的课题。
通过对其制备、性质、催化机理等方面的研究,可以为其在各个领域中的应用提供更为准确的理论指导,推进工业技术的发展。
甲醇合成催化剂失活原因分析及延长使用寿命的方法
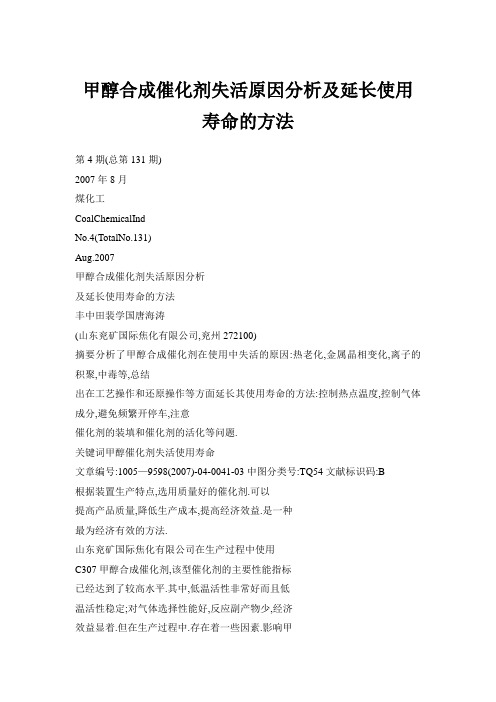
甲醇合成催化剂失活原因分析及延长使用寿命的方法第4期(总第131期)2007年8月煤化工CoalChemicalIndNo.4(TotalNo.131)Aug.2007甲醇合成催化剂失活原因分析及延长使用寿命的方法丰中田裴学国唐海涛(山东兖矿国际焦化有限公司,兖州272100)摘要分析了甲醇合成催化剂在使用中失活的原因:热老化,金属晶相变化,离子的积聚,中毒等,总结出在工艺操作和还原操作等方面延长其使用寿命的方法:控制热点温度,控制气体成分,避免频繁开停车,注意催化剂的装填和催化剂的活化等问题.关键词甲醇催化剂失活使用寿命文章编号:1005—9598(2007)-04-0041-03中图分类号:TQ54文献标识码:B根据装置生产特点,选用质量好的催化剂.可以提高产品质量,降低生产成本,提高经济效益.是一种最为经济有效的方法.山东兖矿国际焦化有限公司在生产过程中使用C307甲醇合成催化剂,该型催化剂的主要性能指标已经达到了较高水平.其中,低温活性非常好而且低温活性稳定;对气体选择性能好,反应副产物少,经济效益显着.但在生产过程中.存在着一些因素.影响甲醇合成催化剂的活性.即使用寿命.1甲醇合成催化剂失活原因分析1.1热老化导致失活铜基催化剂对反应热比较敏感.甲醇合成反应为放热反应,其钝化和还原过程也均为放热反应.因此.在升温与还原或生产控制过程中,如果反应控制不当.导致反应热不能移出,就很容易发生床层温度"飞温",致使活性下降.热老化会使载体的表面积减少.使金属微粒发生迁移,金属晶相发生变化,致使活性位减少,并增加床层阻力.热老化发生的主要原因就是反应余热不能迅速移出反应器,或者反应过于剧烈,反应热突然增加(如系统新鲜气组成突然发生变化,C0配比发生变化或中断).有时为了追求高产,气体氢碳比降低,表现为收稿日期:2007—05-13作者简介:丰中田(1965一),男,1992年毕业于青岛化工学院,高级工程师,长期从事甲醇生产技术工作.人塔合成气体C0组分达到16%18%.氢碳比4.24.6,副产蒸汽增加,选择了C0过多参与反应.而忽略了C0对稳定催化剂床层的有利影响,最终造成催化剂使用寿命的缩短.以某厂为例:在装置运行过程中,由于精制气净化系统脱碳塔设备问题的影响,使C0暂时无法配入,中断2h后恢复(此时入塔气体中C0体积分数<0.5%). 结果在恢复C0正常配比后,发现甲醇产量相对降低,表明催化剂活性在C0中断过程中,C0加剧了催化剂的热老化,甚至有可能出现催化剂深度还原.1.2积碳失活在甲醇合成反应中,存在2种析碳反应:C0+H2=C+H20(还原析碳)(1)2CO=C+CO,(歧化析碳)(2)在系统运行过程中.长期处于较低的氢碳比状态(尤其是在催化剂使用后期),入塔气体中C0含量较高,而C0含量较低,导致大量的氢气剩余.主要表现为系统放空量大,合成气体单程转化率较低.在微观的瞬间反应中,存在这2种析碳反应发生的可能.析碳反应发生后,产生的积碳能够覆盖催化剂的活性表面,使部分活性位丧失,会造成床层阻力增大. 但由于合成系统的空速较大,积碳造成的影响一般不是很明显.某厂在更换催化剂时.在卸出的废旧催化剂表面,发现一些黑色石墨粉尘,表明催化剂在使用过程中.有析碳反应发生.1.3金属晶相变化导致失活A10.作为载体的主要部分为晶相较好的—A10.,一42一煤化工2007年第4期在升温和还原以及工艺运行中,受非操作因素的影响,可能会发生金属晶相的变化,尤其是铜金属晶粒的生长影响,或在高温下转变为其他形态B—A10.或一Al0..在较高含水量下,会生成含水Al0.化合物,Cu-ZnO中心的移动.而降低活性.水蒸气的吸附可导致ZnO吸附氢气能力变弱,活性晶格氧空位被其他离子占用,从而丧失活性.1.4Fe2+的聚积导致对气体选择性发生变化输送新鲜气体的管道有些采用普通碳钢,造成新鲜气体中C0对碳钢管道的晶相腐蚀,产生羟基铁几乎不可避免,并通过气体携带进入合成塔.在合成塔的温度和压力下,以挥发,分解和吸附的方式沉积在催化剂表面上.有可能会转变为氧化亚铁,使合成甲醇活性下降,促进烷烃的生成.甚至出现明显的结蜡现象.这样使催化方向发生变化,造成对反应气体选择性的竞争加剧,不利于甲醇合成反应的进行.具体表现为:在甲醇合成催化剂使用后期,甲烷含量增加,副反应产物增多,合成反应热加大,有石蜡产生.1.S中毒失活催化剂中夹带少量的杂质,或在生产过程中积聚的杂质.以及开停车过程中气体成分的影响.都可能促进副反应的进行,引起反应竞争.这些杂质有的很难在工艺上完全脱除,有的在催化剂制作过程中就已经存在,且无法去除.常见的杂质或毒物对催化剂的影响对比见表1.表1杂质或毒物对催化剂的影响对比杂质或毒物可能的来源对催化剂的影响SiO,等酸性氧化物自蒸汽或原料气带人生成蜡及其他副产物B—A103催化剂制造生成二甲醚碱金属,盐催化剂制造降低活性生成高级醇铁以Fe(CO)带人生成甲烷,链烷烃,石蜡镍以Ni(CO)带人降低选择性钴催化剂制造生成甲烷氯化物自原料气带人永久性降低活性硫化物自原料气带人永久性降低活性1.5.1硫中毒硫是甲醇合成催化剂的主要毒物之一,也是引起催化剂活性衰退的主要因素.在甲醇合成原料气体中,硫主要以HS和COS形式存在,根据造气工艺的不同,原料气体中还存有微量大分子有机硫,如硫醇, 硫醚,噻吩等,由于受低温水解弱的影响.这部分有机硫在低温水解中是无法脱除干净的.但在高温加氢条件下,有机硫发生转化反应,可以完全转化成无机硫. 通常认为:HS,COS和活性组分Cu发生反应,生成稳定的无活性的金属硫化物,在甲醇合成反应条件下(220℃~260℃),硫醇或硫醚会发生加氢转化反应而生成无机硫.反应方程式如下:RSH+H2=RH+H2S(3)RlSR2+2H2=RjH+R2H+H2S(4)在变换反应中,由于水气比限制了有机硫的加氢转化,所以,在高浓度C0合成条件下,微量的硫醇,硫醚基本不会造成较大影响,只有在催化剂使用后期,反应温度较高的情况下,才有可能发生;或者在催化剂使用过程中,高浓度CO引发各类副反应的竞争,使析出的硫迅速被CuO吸收,生成稳定无活性的CuS.1.5.2氢中毒原料气(合成气)氢碳比例对甲醇合成催化剂有重要影响,但在一般情况下不会发生氢中毒.如果在开停车过程中(主要是在停车过程中),工艺处理不当造成氢气含量过高,而CO+CO含量长时间较低,会对催化剂进行深度还原,生成无活性的单质Cu,使催化剂活性丧失所以,在开车过程中,要适当进行新鲜气和循环气的交替加量,短时间内调整至正常的氢碳比例:在停车过程中,一旦分析合成气中C0+C0的体积分数<0.5%,就必须进行氮气置换,用氮气进行保温,保压.1.5.3氯,砷离子中毒氯,砷也是甲醇合成催化剂毒物,氯,砷离子主要存在于蒸汽中,所以在造气或气化过程中,需要特别注意蒸汽中氯,砷离子的含量,确保锅炉水质量.2延长催化剂使用寿命的方法2.1控制热点温度某厂对更换后C307型甲醇合成催化剂的操作数据进行整理,得出催化剂的使用天数与平均热点温度有以下关系:Y=5×10×0.959X其中,y为催化剂使用天数,为平均热点温度.因此,降低催化剂热点温度,是延缓催化剂热老化程度并增加使用寿命的好方法.防止催化剂热老化的主要措施有:(1)在还原,开停车过程中,按照预定的指标进行操作,防止超温.(2)在保证产量的前提下,稳定操作,尽可能降低床层热点温度,每次提升热点温度应慎重.提升幅度不宜过大,一般为5℃左右.(3)适当提高新鲜气(合成气)中的C0的含量.2007年8月丰中田等:甲醇合成催化剂失活原因分析及延长使用寿命的方法一43—2.2控制气体成分控制好气体成分,首先是控制好C0和C0,的比例,根据催化剂的不同使用时期进行调整;其次是控制好惰性气体的含量,掌握并分析放空气体量.作为优化指标的依据:第三是控制好循环气体中的含醇量,人塔气体中含醇量越低,越有利于合成甲醇反应的进行,也可以避免高级醇等副产物的生成.所以要尽可能降低出甲醇水冷器的气体温度,及时将冷凝下来的甲醇分离出来.2.3避免频繁开停车有很多厂家因设备或系统原因.不可避免地出现多次开停车,如果在停车过程中处理不当,将会使催化剂活性受到损害.试验证明:短期停车后,如果催化剂封存在原料气中(合成塔死气,且无法用氮气置换),在重新开车后,其催化剂活性出现明显下降.因此短期或紧急停车后,应作以下处理:(1)应立即用氮气进行置换.如不能置换,可让循环机照常运行.使循环气中的碳氢混合物得到完全反应,直至系统中只有惰性气体和氢气(或者CO,+CO体积分数<0.5%).(2)当床层温度下降时,应适当开大开工蒸汽,并减少循环量,使床层温度维持在210℃,并将系统压力缓慢降低到0.2MPa.(3)如果出现长期停车,在进行氮气置换合格后,应使系统保持微正压,防止在检修时混入空气.2.4催化剂的装填在催化剂装填时,应注意的问题是:(1)催化剂强度较差,在运输过程中严禁摔,碰.(2)装填前,催化剂应轻轻过筛,除去粉尘和碎片.(3)最好采用撒布法装填,尽可能降低催化剂自由下落高度,防止出现架桥现象,应对列管压差进行抽检,压差应在许可范围内.(4)装填时应选择较好天气,以免催化剂吸潮而降低活性,催化剂一旦开始装填应连续进行,避免间断. 装填后应立即封口,充人氮气或进行升温还原.2.5催化剂的活化催化剂的活化在一定程度上决定了催化剂的活性,直接影响其使用寿命,依此在催化剂活化(还原) 时,应特别注意的问题是:(1)氢含量控制还原反应为强放热反应,当氢气含量较低时.催化剂床层的温升和氢气浓度成正比,一般每提高1% 的氢气,将引起床层温度升高28℃,因此控制好加氢速度是还原操作的关键.在还原时,掌握提温不提氢, 提氢不提温的原则,防止还原过于剧烈,床层温度猛涨,使催化剂活性受影响.所以,在还原操作中一般采用低氢,高空速控制还原速度.(2)出水量控制还原终点判断催化剂活性影响较大,在还原时.既要防止还原操作不彻底,又要防止出现深度还原, 很多厂家采用精制气还原,出水量尽可能控制均匀. 在还原操作中,理论出水量与实际出水量应基本接近,并分析进出合成塔氢气含量稳定,这时基本可以判断还原结束.(3)惰性气体放空量控制惰性气体一般为还原气体(氢气)的载气.一般采用氮气为稀释气体,在还原操作中,惰性气体能够有效控制还原速度,床层温度便于控制,有利于提高催化剂活性,保护催化剂强度.此外,由于采用精制气还原,惰性气体中的C0,含量也影响还原进度的判断,根据放空气体中的C0, 含量,判断C0参与还原反应程度,所以出水量有可能要比理论出水量低.3结论甲醇合成催化剂的使用寿命受到催化剂本身构造影响和还原操作的影响,以及在工艺运行中操作条件的限制.所以,在一般情况下,为追求单炉催化剂产量,是以牺牲催化剂使用寿命来换取高产量的,同时,造成了催化剂频繁更换,应从经济效益上来衡量. CausesofDeactivationofCatalystforMethanolSynthesisandMethodtOProlongItsLifetim eFengZhongtian,PeiXueguoandTangHaitao (ShandongYankuangInternationalCokingCo.,Ltd.,Yanzhou272100) AbstractBasedoncompositionandstructureofmethanolsynthesiscatalyst,itsdeactivationc auseswerefoundandanalyzed:thermalaging,metalcrystallinephasechange,ionaccumulation,poisoning,etc.S omemethodstoprolongthelifetimeofcatalystweresuggested,i.e.controllinggascompositionandtemperatureofthehot spot,avoidingfrequentstart—upandshutdown,payingattentiontothechargeandactivationofcatalyst,etc. KeyWOrdsmethanol,catalyst,deactivation,lifetime。
甲醇合成操作问答
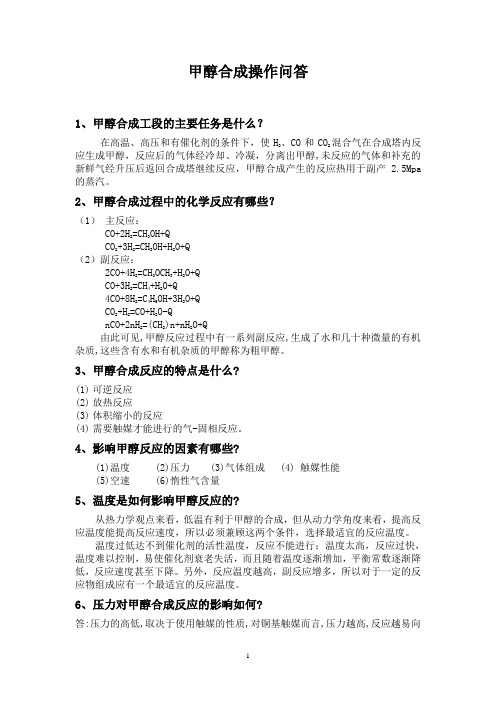
甲醇合成操作问答1、甲醇合成工段的主要任务是什么?在高温、高压和有催化剂的条件下,使H2、CO和CO2混合气在合成塔内反应生成甲醇,反应后的气体经冷却、冷凝,分离出甲醇,未反应的气体和补充的新鲜气经升压后返回合成塔继续反应,甲醇合成产生的反应热用于副产 2.5Mpa 的蒸汽。
2、甲醇合成过程中的化学反应有哪些?(1)主反应:CO+2H2=CH3OH+QCO2+3H2=CH3OH+H2O+Q(2)副反应:2CO+4H2=CH3OCH3+H2O+QCO+3H2=CH4+H2O+Q4CO+8H2=C4H9OH+3H2O+QCO2+H2=CO+H2O-QnCO+2nH2=(CH2)n+nH2O+Q由此可见,甲醇反应过程中有一系列副反应,生成了水和几十种微量的有机杂质,这些含有水和有机杂质的甲醇称为粗甲醇。
3、甲醇合成反应的特点是什么?(1)可逆反应(2)放热反应(3)体积缩小的反应(4)需要触媒才能进行的气-固相反应。
4、影响甲醇反应的因素有哪些?(1)温度 (2)压力 (3)气体组成 (4) 触媒性能(5)空速 (6)惰性气含量5、温度是如何影响甲醇反应的?从热力学观点来看,低温有利于甲醇的合成,但从动力学角度来看,提高反应温度能提高反应速度,所以必须兼顾这两个条件,选择最适宜的反应温度。
温度过低达不到催化剂的活性温度,反应不能进行;温度太高,反应过快,温度难以控制,易使催化剂衰老失活,而且随着温度逐渐增加,平衡常数逐渐降低,反应速度甚至下降。
另外,反应温度越高,副反应增多,所以对于一定的反应物组成应有一个最适宜的反应温度。
6、压力对甲醇合成反应的影响如何?答:压力的高低,取决于使用触媒的性质,对铜基触媒而言,压力越高,反应越易向生成甲醇的方向进行,平衡甲醇含量越高,甲醇越易冷凝及分离,生产强度越高。
7、甲醇催化反应过程有几个步骤?答:甲醇合成反应是一个气固相催化反应的过程,共分五步:(1) CO和H2扩散到催化剂表面;(2) CO和H2被催化剂表面吸附;(3)CO和H2在催化剂表面进行化学反应;(4) CH3OH在催化剂表面脱附;(5)CH3OH扩散到气相中去。
甲醇合成工艺常出现的问题及解决办法
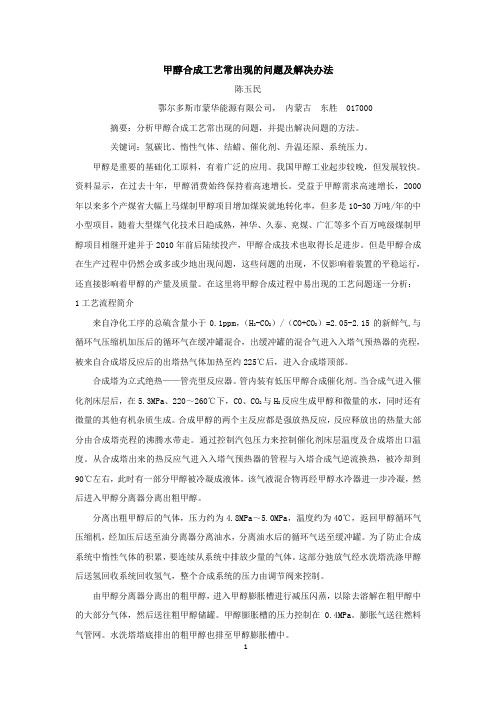
甲醇合成工艺常出现的问题及解决办法陈玉民鄂尔多斯市蒙华能源有限公司,内蒙古东胜 017000 摘要:分析甲醇合成工艺常出现的问题,并提出解决问题的方法。
关键词:氢碳比、惰性气体、结蜡、催化剂、升温还原、系统压力。
甲醇是重要的基础化工原料,有着广泛的应用。
我国甲醇工业起步较晚,但发展较快。
资料显示,在过去十年,甲醇消费始终保持着高速增长。
受益于甲醇需求高速增长,2000年以来多个产煤省大幅上马煤制甲醇项目增加煤炭就地转化率,但多是10-30万吨/年的中小型项目,随着大型煤气化技术日趋成熟,神华、久泰、兖煤、广汇等多个百万吨级煤制甲醇项目相继开建并于2010年前后陆续投产,甲醇合成技术也取得长足进步。
但是甲醇合成在生产过程中仍然会或多或少地出现问题,这些问题的出现,不仅影响着装置的平稳运行,还直接影响着甲醇的产量及质量。
在这里将甲醇合成过程中易出现的工艺问题逐一分析:1工艺流程简介来自净化工序的总硫含量小于0.1ppm,(H2-CO2)/(CO+CO2)=2.05-2.15的新鲜气,与循环气压缩机加压后的循环气在缓冲罐混合,出缓冲罐的混合气进入入塔气预热器的壳程,被来自合成塔反应后的出塔热气体加热至约225℃后,进入合成塔顶部。
合成塔为立式绝热——管壳型反应器。
管内装有低压甲醇合成催化剂。
当合成气进入催化剂床层后,在5.3MPa、220~260℃下,CO、CO2与H2反应生成甲醇和微量的水,同时还有微量的其他有机杂质生成。
合成甲醇的两个主反应都是强放热反应,反应释放出的热量大部分由合成塔壳程的沸腾水带走。
通过控制汽包压力来控制催化剂床层温度及合成塔出口温度。
从合成塔出来的热反应气进入入塔气预热器的管程与入塔合成气逆流换热,被冷却到90℃左右,此时有一部分甲醇被冷凝成液体。
该气液混合物再经甲醇水冷器进一步冷凝,然后进入甲醇分离器分离出粗甲醇。
分离出粗甲醇后的气体,压力约为4.8MPa~5.0MPa,温度约为40℃,返回甲醇循环气压缩机,经加压后送至油分离器分离油水,分离油水后的循环气送至缓冲罐。
甲醇合成铜基催化剂概述

催化剂的制备方法
制备 方法 沉淀法 球磨法 复频超声法 火焰燃烧法 碳纳米管促 进法
优点
纳米级颗粒混合 均匀,活性高
CuO/ZnO 间作用强, 比表面积大
分散均匀, 粒径小,协 同作用强
易形成良好 结构,如高 比面积
CNTs对H2 吸附活化力 强,活性高
缺点
耐热性与抗毒性 较差
需要高强度 的机械混合
耐热性能好、对硫不敏感,机械强度高,使用寿 命长,使用范围宽,操作控制容易,但是其活性 低、选择性低、产品中杂质复杂,精馏困难。
铜基 催化剂
210℃ 300℃ 之间
5MPa 10MPa 之间
活性好,单程转化率为7%~8%;选择性高,大于 99%,易得到高纯度的精甲醇;耐高温性差,对 合成原料气中杂质比较敏感。目前工业上甲醇的 合成主要使用铜基催化剂。
热失活源自热失活则是由于在使用过程中催化剂中的氧化 铜晶粒长大造成的,它与催化剂的结构稳定性 有关,可通过催速老化实验检验催化剂的活性 稳定性。 为了延长催化剂的使用寿命、提高甲醇生产效 率,需要严格控制操作温度,做到平稳操作, 防止反应温度骤升骤降,加减负荷也要逐步平 稳进行。甲醇催化剂传热效果差,如果不能控 制还原反应速度,及时移走反应放出的热量, 很易使催化剂过热或烧坏,发生整炉催化剂烧 毁的严重后果。
甲醇合成铜基催化剂概述
调度三班 2016年2月25日
主要内容
1. 2. 3. 4. 5.
合成催化剂的特点 合成机理概述 催化剂制备概述 反应条件对催化剂的影响 催化剂的失活研究
不同催化剂的特点
催化剂 系列 操作温 度 操作压 力 25Mpa 35MPa 之间 催化剂特点
锌铬 317℃ (ZnO/Cr 397℃ 2O3)催化 之间 剂
探究甲醇合成催化剂失活的影响因素

探究甲醇合成催化剂失活的影响因素甲醇合成催化剂的失活问题,是制约生产质量、效率和安全的重要因素。
在实际生产中,需要采用综合手段治理甲醇合成催化剂的失活问题,既要应用技术手段,更要注重管理手段。
应该运用科学方法从多元化的角度着手,确保为安全生产,增加甲醇产量和催化剂效率,降低生产成本,增強企业经济效益提供良好的保障。
标签:甲醇合成;催化剂失活;影响因素1 稳定甲醇合成催化剂的重要性1.1 提升经济效益良好的经济效益是促进化工企业平稳发展的重要力量。
在生产过程中,甲醇合成催化剂的活性将直接影响甲醇的产率,同时决定产品的生产效果。
在整个生产过程中,其他环节出现问题的概率较小,所以催化剂失活就成为了一个生产短板,必须予以解决。
1.2 稳定生产在常规甲醇合成生产过程中,甲醇合成催化剂的使用情况往往是最为主要的生产技术标准,其体现了工艺的特征以及装置的特点。
如果甲醇合成催化剂经常失活,那么说明工艺存在严重缺陷,需要更换工艺甚至是设备。
如果能够通过其他方式来稳定生产,就可以确保技术应用水平,稳定生产各个环节。
1.3 提升甲醇产品质量甲醇产品质量将决定化工企业的市场综合竞争力与市场信誉。
通过稳定的催化剂可以获得更好的产品质量,从而获得良好的行业口碑,这对于企业的健康平稳快速发展具有重要意义。
2 影响甲醇合成催化剂失活的主要因素2.1 毒害物对甲醇合成催化剂失活造成的影响2.1.1 毒害物的种类及可能来源通常无论是原材料,设备中存在的杂质以及催化剂制作的过程中都可能产生一定的毒害物,而这些毒害物极有可能对催化剂的生产效率和应用效果造成严重的影响,常见的毒害物可以分为硫与氨等多种物质。
2.1.2 硫对甲醇合成催化剂失活的影响现阶段,我们所使用的甲醇合成催化剂其主要是铜基催化剂,硫与其化合物是造成甲醇合成催化剂失活的主要因素之一,通常硫与硫化合物会对甲醇合成催化剂的使用期限与活性的关系极为紧密。
原料气中的硫多会以COS与H2S的形式出现,而COS与H2S和活性组分铜会产生一定的反应,最后会产生硫化亚铜,由此便会对甲醇合成催化剂表面以及堵塞孔道造成部分影响,不仅导致了催化剂失活的问题出现,还会造成永久性的中毒现象。
- 1、下载文档前请自行甄别文档内容的完整性,平台不提供额外的编辑、内容补充、找答案等附加服务。
- 2、"仅部分预览"的文档,不可在线预览部分如存在完整性等问题,可反馈申请退款(可完整预览的文档不适用该条件!)。
- 3、如文档侵犯您的权益,请联系客服反馈,我们会尽快为您处理(人工客服工作时间:9:00-18:30)。
甲醇合成铜基催化剂催化活性及失活研究1引言甲醇是一种极其重要的化工原料,主要用于生产一系列化工产品,还可用作潜在的车用醇醚燃料电池的燃料等。
随着甲醇制烯烃等技术进步及下游产品的开发,特别是甲醇燃料电池的开发和应用,合成甲醇的研究越来越受到广泛重视。
目前,甲醇的工业生产主要是采用CO/CO2催化加氢技术,所以甲醇合成催化剂的研发是甲醇合成工业的基石。
甲醇工业的发展很大程度上取决于催化剂的研制及其性能改进。
在甲醇生产中,很多工业指标和操作条件都是由催化剂的性质决定的。
随着甲醇工业的快速发展,对甲醇合成催化剂的研究开发提出了更高的要求。
2 甲醇合成催化剂在甲醇合成过程中,催化剂的重要性显而易见,目前工业上使用的甲醇合成催化剂一般可分为锌铬催化剂和铜基催化剂两类。
国外比较有名的研究和生产甲醇合成催化剂公司主要有英国ICI公司、德国BASF公司、德国SudChemie公司和丹麦TopsΦe公司等,国内研究铜基催化剂的院所主要有南化集团研究院、西南化工研究设计院,西北化工研究院及齐鲁石化研究院等[1]。
锌铬(ZnO/Cr2O3)催化剂由德国BASF公司于1923年首先开发研制成功。
操作温度必须在590 K~670 K,操作压力必须为25 MPa~35MPa,锌铬催化剂的特点是:耐热性能好、对硫不敏感,机械强度高,使用寿命长,使用范围宽,操作控制容易,但是其活性低、选择性低、产品中杂质复杂,精馏困难。
铜基催化剂由英国ICI公司和德国Lurgi公司先后研制成功,操作温度为210℃~300℃,压力为5MPa~10MPa,比传统的合成工艺温度低得多,对甲醇反应平衡有利。
其特点是:活性好,单程转化率为7%~8%;选择性高,大于99%,易得到高纯度的精甲醇;耐高温性差,对合成原料气中杂质比较敏感。
目前工业上甲醇的合成主要使用铜基催化剂。
近年来,新型催化剂的研制也在一直进行,新型催化剂的研制方向在于提高活性,改善热稳定性及延长催化剂使用寿命等,如钯系、钼系及低温液相催化剂,但这些催化剂因活性不理想或对甲醇的选择性较差,还只停留在研究阶段未实现工业化。
对铜基催化剂的改进研究主要集中在两个方面[2],一是添加除铜锌铝以外的其他组分,另一方面是改进催化剂的制备方法和工艺。
3 铜基催化剂的催化原理目前,低压甲醇合成铜基催化剂系列品种较多,有铜锌铬系(CuO/ZnO/Cr2O3)、铜锌铝系(CuO/ZnO/Al2O3)、铜锌硅系(CuO/ZnO/Si2O3)、铜锌锆系(CuO/ZnO/ZrO)等,其中铜锌铝系(CuO/ZnO/Al2O3)应用较为广泛,下面就该系列讨论铜基催化剂催化原理。
铜锌铝系主要组分是CuO、ZnO和Al2O3,三组分在催化剂中的比例随着生产厂家的不同而不同,具体表1所示。
表1 铜基催化剂各组分所占比例组分CuO ZnO Al2O3质量分数40%~80% 10%~30% 5%~10%铜基催化剂在合成甲醇时,CuO、ZnO、Al2O3三组分的作用各不相同。
CO和H 在催化剂上的吸附性质与催化剂的活性有非常密切的关系。
在铜基催化剂表面对CO的吸附速率很高,而对H2的吸附则比CO慢得多。
ZnO是很好的氢化剂,可使H2被吸附和活化,但对CO几乎没有化学吸附,因此可提高铜基催化剂的转化率。
实验证实,纯铜对甲醇合成是没有活性的。
催化理论认为,氢和一氧化碳合成甲醇的反应是在一系列活性中心上进行的,这种活性中心存在于被还原的Cu—CuO 界面上。
在催化剂中加人少量Al2O3的首要功能就是阻止一部分氧化铜还原。
Fujitani T等[3]认为,在由共沉淀法制备的催化剂中,ZnO对增进Cu分散和增强催化剂活性具有重要的作用。
当催化剂被还原后,开始进行反应时,合成气中的H和CO都是还原剂,有使氧化铜进一步还原的趋势。
这种过度的还原,使得活性中心存在的界面越来越小,催化剂活性也越来越低。
从合成的整个过程来看,随着还原表面向催化剂的内层深入,未还原的核心越来越小,作为被还原的Cu-CuO界面的核心表面积也越来越小,催化剂的活性降低[4],合成反应速率随之降低。
Kurtz M等[5]人研究认为,Al2O3在催化剂中作为结构助剂能够阻碍铜颗粒烧结。
4 制备条件对催化剂活性的影响目前,铜基甲醇合成催化剂主要制备方法有沉淀法、球磨法、复频超声法、火焰燃烧法、碳纳米管促进法等。
由于沉淀法操作过程简单、制得的催化剂性能优越,因此铜基甲醇催化剂的工业生产均采用沉淀法。
对沉淀法制备铜基甲醇合成催化剂的影响因素及研究进展进行了探讨。
表2 铜基合成催化剂制备方法优缺点一览表制备沉淀法球磨法[6]复频超声法[7]火焰燃烧法[8]碳纳米管促进法[9]方法优点纳米级颗粒混合均匀,活性高CuO/ZnO间作用强,比表面积大分散均匀,粒径小,协同作用强易形成良好结构,如高比面积CNTs对H2吸附活化力强,活性高缺点耐热性与抗毒性较差需要高强度的机械混合操作较为复杂,且产物纯度不高仪器相当复杂,不能普遍使用要制备符合特定条件的碳纳米管共沉淀过程包括沉淀、陈化、洗涤、干燥、煅烧、压片成型等,还包括最终的还原活化,每一步对催化剂的性能都有一定的影响,特别是沉淀、陈化、煅烧、还原步骤更关键。
沉淀是催化剂制备的关键因素,沉淀条件的微小变化都会对活性产生巨大影响。
4.1沉淀过程对催化剂性能的影响沉淀过程包括晶核的生成和晶核的长大两个过程。
如果晶核生成速率远超过晶核长大速率,则离子很快聚集为大量的晶核,溶液的过饱和度迅速下降,溶液中没有更多的离子聚集到晶核上,于是晶核迅速聚集成细小的无定形颗粒,得到非晶型沉淀,甚至是胶体;如果晶核长大速率远超过晶核生成速率,溶液中最初形成的晶核不是很多,有较多的离子以晶核为中心,依次排列长大而成为颗粒较大的晶型沉淀。
相同反应物经过不同条件产生不同前驱体,分解得到的催化剂活性也就大不相同。
魏蓉等[10]认为最佳Cu/Zn为1和2,铜锌间具有较强的协同作用;铝含量不超过10%;沉淀温度不低于70℃;沉淀pH值在7-9之间。
4.2 煅烧过程对催化剂性能的影响煅烧是使催化剂具有活性的重要步骤,可能发生如下变化:①热分解,使其转化成所需的化学形态;②固态反应、互溶和再结晶获得一定晶型、比表面积等;③烧结,提高催化剂的机械强度,获得较大孔隙率。
煅烧温度与催化剂活性的关系煅烧过程一般为吸热过程,故升高温度有利于分解反应,但温度过高会烧结,使催化剂活性下降,而煅烧温度降低则达不到活化的目的。
因此研究者对合适的煅烧条件一直在不断的探索。
许勇等[11]发现煅烧温度能改变催化剂表面积、催化活性、晶相组成等,Al2O3的加入有利于提高催化剂的热稳定性,阻止CuO晶粒长大,提高催化剂活性。
煅烧温度为350-650℃为宜,当温度高于650℃,催化活性显著下降,这是由于煅烧温度太高使氧化物烧结颗粒长大所致。
洪中山等[12]提出合适煅烧条件为:富氧气氛、较低的升温速率和350℃煅烧。
该煅烧条件获得的催化剂比表面积高、铜粒径小,选择性高。
甲醇收率随煅烧温度的升高先增加后降低,煅烧温度为350℃时达到最高。
4.3 添加助剂还有一些特殊助剂,作用就是有助分散铜晶体,阻止高温下铜晶体生长,特别是在超温时,减小对催化剂的伤害,延长使用时间,提高效益,刘艳霞等[13]研究发现γ-A12O3的添加量为催化剂量的3%时,催化剂的初活性和耐热后的活性明显高于其他催化剂。
杨意泉等[14]在Cu-Zn-Al甲醇合成催化剂中添加适量的氧化锆助剂制得Cu-Zn-Al-Zr催化剂,它对CO的吸附量大于Cu-Zn-Al催化剂对CO的吸附量。
随着当代催化工业迅速发展和新型催化技术开发和应用,沉淀法制备铜基甲醇催化剂技术也应不断吸收新兴技术的优点。
比如微乳液技术[15]、溶胶凝胶技术[16-17]分别与沉淀法相结合,这些技术各有特点且各种技术常可相互关联运用并取得令人满意的结果,因而受到人们广泛关注。
5反应条件对催化剂活性的影响5.1 反应温度的影响合成甲醇反应:2H2+CO=CH3OH,其△r G m= –114.17+0.244 KJ/mol,因此,从热力学上来说,升高温度对合成甲醇是不利的。
但升高温度使得反应速率加快,即在动力学上升温是有利的。
所以,甲醇合成必有一个合适的反应温度。
在实验操作中发现催化剂活性先随反应温度升高而升高,后又随反应温度升高而下降。
温度过高,会使催化剂发生热烧结而降低活性甚至丧失活性。
但是反应温度在280℃以下,铜基甲醇催化剂的热烧结因素几乎可以忽略。
因为我们无论在测试催化剂耐热前的活性还是耐热后的活性时,在120℃~280℃的温度范围内,都通过反复的升温、降温,进行过多次测试,活性结果的重现性均很好。
这也就是说,两种催化剂的活性(无论是耐热实验前还是耐热实验后的活性)在210℃~280℃的反应温度范围内的变化趋势,都主要是反应热力学和动力学这两种效应的综合体现。
5.2 合成气空速的影响空速增加,合成气在反应器内的停留时间减少,与催化剂的接触时间减少,从而不利于副反应的发生,这样甲醇的选择性就会有所提高,进而使催化剂的生产能力提高,甲醇收率提高,所以我们说增加空速可以提高了催化剂的活性。
如果采用高空速,催化剂的生产强度虽然可以提高,但增大了预热所需的面积,出塔气热能利用价值较低,系统阻力增大,压缩循环气功耗增加,同时增加了分离反应产物的费用,当空速增大到一定程度后,催化剂的床温度难以控制。
适宜的空速与催化剂活性,反应温度及进塔气体组成有关,在铜基催化剂上为10000-20000h-1。
5.3合成气组成的影响由合成气合成甲醇的反应相当复杂,除主反应外,还有低碳醇合成反应,F-T合成反应和水煤气变换反应。
反应进行的方向、程度及其产物组成取决于催化体系及相应反应条件。
水煤气变换反应是甲醇、低碳醇及烃类合成反应的副反应。
此外合成甲醇反应中氢与CO的理论分子比为2:1,但反应气体受催化剂表面吸附的影响,CO在催化剂表面上的吸附速率远大于H2,存在吸附竞争。
因此,要求反应气体中的H,含量要大于理论量,以提高反应速度,增加甲醇产率,所以一般入塔气中的H/C之比要大于4。
5.4 反应压力的影响合成甲醇反应CO+2H2=CH3OH是一个气体分子数减少的反应,故增加压力可使反应平衡向右移动,即升高压力在热力学上对合成甲醇是有利的。
从动力学上来说,由于多相催化反应动力学的复杂性,表面反应过程,反应物在催化剂表面上的吸附以及产物在催化剂表面上的脱附均有可能成为多相催化反应的控制步骤。
而无论那个是控制步骤,反应压力均有可能影响反应速率。
在实验操作过程中发现,增加压力,甲醇收率(mol/g·h)随反应总压的增加而增高。
压力增加10%,甲醇产率增加10%,达到8MPa以上开始下降[18]。