石化旋转机械基于风险的维修决策研究
化工机械设备维修的常见问题及解决策略
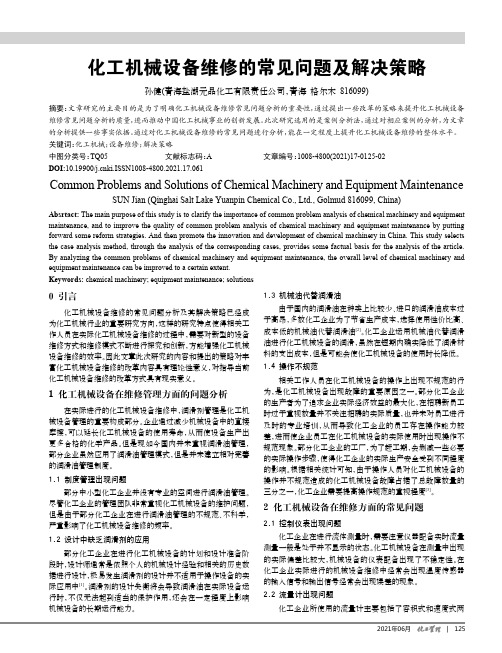
2.1 控制仪表出现问题
化工企业在进行流体测量时,需要注意仪器配备实时流量 测量一般是处于并不显示的状态。化工机械设备在测量中出现 的实际偏差比较大,机械设备的仪表配备出现了不稳定性。在 化工企业实际进行的机械设备维修中经常会出现温度传感器 的输入信号和输出信号经常会出现误差的现象。
3.4 提高机械密封泄漏故障的重视程度
为了提高企业对化工机械设备的机械密封泄漏故障的重视 程度,化工企业在将相关的化工机械设备采购进企业时,需要检 查机器和设备的实际质量是否符合行业规范和行业标准。事实 上,机械的密封处理需要结合化工机械设备的实际操作技能进 行设计,企业在机械密封中采用的材料尽量选择使用寿命较长、 耐磨性比较高的摩擦材料,可以提高设备的密封效果。为了确保 化工机械设备具有相对稳定性和相对可靠性,企业需要严格把 控化工机械设备的配套零部件的质量要求,企业需要确保在化 工机械设备的实际安装中,严格依照安装标准进行实际安装。
2.2 流量计出现问题
化工企业所使用的流量计主要包括了容积式和速度式两
2021年06月
| 125
设备运维
种方式。这两种方式都具有一定的优势和劣势,但当化工机械 设备出现故障时,设备上出现的数据一般会呈现出不稳定或者 失真的效果。因此,在化工机械设备在出现故障时,化工企业需 要安排专业人员进行电源的损坏、老化、接触不良的定期检查。 电路检查人员需要重点查看电源是否可以满足化工企业稳步 供电的实际需求,对设备插件是否处于稳定状态下都需要进行 定时检查。如果化工企业使用的化工机械设备的变压器处于比 较紧的状态,可能会导致变压器内部的损坏。因此化工企业需 要及时地进行检查、维修、更换,从而确保化工机械设备的稳步 运行,有助于提升化工企业的实际工作效率。
转动设备检修作业风险及安全措施

转动设备检修作业风险及安全措施1. 引言在工业生产中,许多设备都涉及到转动部件的运作,如发电机、电机、风机等。
这些设备在正常运转时能够提供高效的工作效率,但同时也存在一定的风险。
在进行转动设备的检修作业时,必须注意风险,采取相应的安全措施,以确保操作人员和设备的安全。
本文将对转动设备检修作业的风险进行分析,并提供一些常见的安全措施。
2. 转动设备检修作业的风险转动设备检修作业涉及到与旋转部件接触,因此存在一定的风险。
以下是一些常见的转动设备检修作业风险:2.1 电击风险由于转动设备通常与电源相关联,在检修作业中可能会遇到电击风险。
例如,接触到带电的部件或没有正确切断电源就进行检修作业,都可能导致电击伤害。
2.2 夹伤风险转动设备的旋转部件可能会夹住操作人员的手指、手臂等身体部位,造成夹伤伤害。
特别是在旋转部件没有完全停止的情况下进行检修作业,夹伤风险更高。
2.3 坠落风险在对转动设备进行检修作业时,操作人员可能需要爬上高处,如设备顶部或架子上。
这样的工作高度增加了坠落的风险。
如果没有采取适当的安全措施,操作人员摔倒或从高处坠落可能会造成严重的伤害。
2.4 疲劳和集中力不足风险转动设备检修作业往往需要长时间、高强度的操作,操作人员可能会因为过度疲劳而降低注意力和集中力,从而增加事故发生的风险。
3. 转动设备检修作业的安全措施为了避免转动设备检修作业过程中的风险,我们必须采取一系列的安全措施。
以下是一些常用的安全措施:3.1 切断电源并确保设备停止运转在进行转动设备的检修作业之前,必须切断相关的电源,并确保设备完全停止运转。
这样可以避免电击和夹伤的风险。
3.2 使用个人防护装备操作人员应该佩戴适当的个人防护装备,如安全帽、防护手套、防护眼镜等。
这些防护装备可以减轻操作人员在意外事故中受伤的程度。
3.3 设置有效的围栏和警示标志在进行转动设备检修作业时,应设立有效的围栏和警示标志,以限制未经授权的人员进入作业区域。
炼油化工装置风险及风险防范
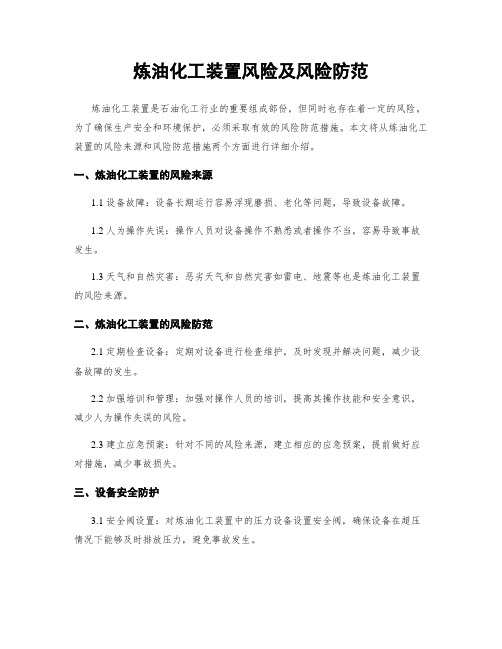
炼油化工装置风险及风险防范炼油化工装置是石油化工行业的重要组成部份,但同时也存在着一定的风险。
为了确保生产安全和环境保护,必须采取有效的风险防范措施。
本文将从炼油化工装置的风险来源和风险防范措施两个方面进行详细介绍。
一、炼油化工装置的风险来源1.1 设备故障:设备长期运行容易浮现磨损、老化等问题,导致设备故障。
1.2 人为操作失误:操作人员对设备操作不熟悉或者操作不当,容易导致事故发生。
1.3 天气和自然灾害:恶劣天气和自然灾害如雷电、地震等也是炼油化工装置的风险来源。
二、炼油化工装置的风险防范2.1 定期检查设备:定期对设备进行检查维护,及时发现并解决问题,减少设备故障的发生。
2.2 加强培训和管理:加强对操作人员的培训,提高其操作技能和安全意识,减少人为操作失误的风险。
2.3 建立应急预案:针对不同的风险来源,建立相应的应急预案,提前做好应对措施,减少事故损失。
三、设备安全防护3.1 安全阀设置:对炼油化工装置中的压力设备设置安全阀,确保设备在超压情况下能够及时排放压力,避免事故发生。
3.2 火灾防护:在炼油化工装置中设置火灾报警器、灭火器等设备,及时发现并扑灭火灾,防止火灾蔓延。
3.3 防爆措施:对易燃易爆的物质进行分类存储,并设置防爆设备,减少爆炸事故的发生。
四、环境保护措施4.1 废水处理:对炼油化工装置产生的废水进行处理,达到排放标准,保护周围环境。
4.2 废气处理:采用高效的废气处理设备,减少废气排放对空气质量的影响。
4.3 节能减排:采用节能技术和减排措施,减少能源消耗和污染排放,实现可持续发展。
五、安全文化建设5.1 安全教育:开展定期的安全培训和教育活动,提高员工的安全意识和应急处理能力。
5.2 安全奖惩制度:建立健全的安全奖惩制度,激励员工积极参预安全管理,减少事故发生。
5.3 安全监督:建立安全监督机制,定期开展安全检查和评估,及时发现问题并加以整改,确保炼油化工装置的安全生产。
石油修井机设备维修及保养刍议

石油修井机设备维修及保养刍议摘要:油井设备的维修保养工作也是油田开发中不可避免的重点工作。
对石油的巨大需求对我国石油生产的质量、效率和安全产生了重大影响,需要确保稳定可靠的运作。
一套综合仪器,主要用于石油钻井、气体、水下排水或中小型修理和大修。
全套盖板主要由八个主要系统组成:拖动系统、旋转系统、循环系统、电源、驱动系统、控制器、机器架、其他辅助设备等。
使用竖井时,可能会出现不同的磨损、疲劳、变形或磨损或性能下降。
本文对石油修井机设备维修及保养进行分析,以供参考。
关键词:石油修井机;设备维修;保养引言石油修井机设备是修井和井下作业施工中最基本、最主要的动力来源,一般来说主要包括井架、钻台、转盘及动力传动系统、游动系统、液压系统等。
定期做好修井设备的维护工作,提高设备的整体性能和维护特性,延长设备的使用寿命,保障石油生产安全、高效的有序进行,对油田及企业来说都是具有长远经济效益的良好生产习惯。
随着科技和时代的发展,石油修井机故障维修更多的被事前预防性维护取代,为油气开发保驾护航。
1石油修井机故障检修的重要性石油和天然气勘探机械的维修和检查是油田开发的必然组成部分。
对石油的需求很高,机器影响着石油的质量、效率和安全性,必须保证机器的平稳运行。
竖井设备主要用于中小型维修,以及井下钻油、气动和竖井控制,或用于一套控制井底深度的集成设备。
整套工作设备主要由八个系统组成:拖动系统、旋转系统、循环系统、电源、动力系统、控制系统、维护会话和其他辅助工具。
使用加工设备时,可能会出现各种磨损、疲劳、变形或磨损,或者性能降低。
我国油气加工机械的分类和维修仍然存在问题,需要进一步研究。
石油生产相对具体,设备通常在恶劣条件下运行,因此设备的耐久性或长期运行期间零件损坏对设备的运行产生不利影响。
在这方面,需要定期审查并及时查明和解决问题。
维护包括所有设备,并采取有针对性的措施来解决现有故障,以确保设备平稳运行。
同时,通过定期维护降低生产成本,提高企业利润,同时创建安全的工作环境,避免人身安全问题。
石油修井机械设备故障类别与检修探讨
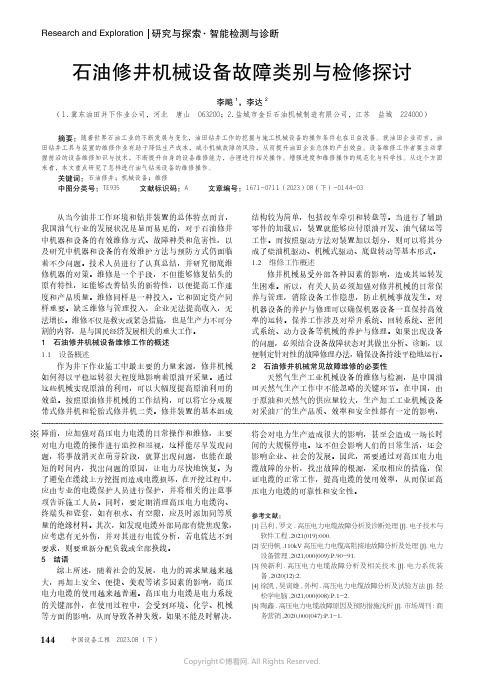
石油修井机械设备故障类别与检修探讨
李飚 1,李达 2 (1. 冀东油田井下作业公司,河北 唐山 063200;2. 盐城市金巨石油机械制造有限公司,江苏 盐城 224000)
摘要:随着世界石油工业的不断发展与变化,油田钻井工作的挖掘与施工机械设备的操作条件也在日益改善。就油田企业而言,油 田钻井工具与装置的维修作业有助于降低生产成本,减小机械故障的风险,从而提升油田企业总体的产出效益。设备维修工作者要主动掌 握前沿的设备维修知识与技术,不断提升自身的设备维修能力,合理进行相关操作。增强进度和维修操作的规范化与科学性。从这个方面 来看,本文重点研究了怎样进行油气钻采设备的维修操作。
在修井机械设备出现问题的第一时刻,要求检修人 员进行事故检测、调查和准备等。要研究事故出现的施 工环节、事故形成的因素等,对事故情况、出现问题的 现场情况进行拍照,录入机械设备事故的有关资料。另 外,收集整理修井机械设备有关的设计说明书、检修记 录、事故信息资料等信息,通过设备的有关信息对事故 状况作出简单的评估。通过专业检验仪器对石油修井机 械进行内部检验,通过无损检验手段判断设备内零部件 的状态,并通过有关信息推断出事故的具体成因。针对 事故状态、问题的根源采取相应的补救措施,就可以提 高机械设备的工作质量。 5.2 选择合适的设备检修方式
石油修井机械设备的维护方法主要包括以下几类: (1)预防性维护方法。在旧设备没有出现问题以前对 设备实施维护,方法包括通过及时替换陈旧设备、受 损伤零件消除设备的质量安全隐患,从而防止旧设备 在正常工作过程中出现问题。在对修井机械设备实施 预防性维护之前,就必须制订好具体的工作时间,包 括规定维修作业时长、规定维修间隔时长等。(2)预 测性养护方法。通过观察连续测量的资料对设备情况 作出预报后,再按照数据情况对设备实施维修保养作 业,可以减少对修井机械设备的维护成本等。(3)修 理性维修方法。当设备出现运行问题时,由维护人员 依据问题对设备实施针对性的修理,并采用调换零部 件、恢复设备正常工作系统等的方法,使设备迅速恢 复到安全状态。在日常运行中,维护人员也应灵活运 用这三类的检修方法。 5.3 提高维护人员的专业技能
石油化工转动设备的振动故障分析及处理

石油化工转动设备的振动故障分析及处理摘要:石油化工行业引进了大量机械和设备,促进了工业发展,特别是引进了旋转设备,大大提高了生产力。
在实践中,由于各种原因,设备振动造成的故障是不可避免的,设备振动幅度与设备间隙有关,间隙越大,设备损坏越大,设备故障的可能性越大,影响设备正常运行的可能性越大,因此需要对这应该是解决办法。
关键词:转动设备;振动;处理引言在石油化工中,大量设备特别是旋转设备的应用促进了石油工业的发展。
如果在实际操作过程中存在各种因素,则在操作过程中会发生装置的位置偏移,从而导致振动。
设备的振动幅度和控制间隙相互联系,间隙越大,振动越大,声音越大,导致设备正常运行。
因此,要做好石化旋转设备的振动故障分析,并提出故障处理对策。
1、石油化工中主要的转动设备运行问题在石油化工设备、烟机、风扇、气压计、燃气能源、合成器等方面是主要的旋转装置和振动源。
这些地基通常由离心式或轴向压缩机组成,具有高功率转速特性,其中大多数是主要生产设备,一旦出现故障,可能会造成生产损失,直接影响企业的经济效益。
随着石油化工的不断发展,生产设备的规模和重量都有所增加,对自动检测、缺陷检测等提出了新的要求尤其是旋转设备振动一直是设备故障的主要原因之一,设备振动造成的损坏,额外的能量损失,维修停机是生产成本上升的主要原因,对生产安全和员工健康构成了更大的威胁。
2、石油化工转动设备振动故障类型2.1转子失衡与弯曲石油化学旋转设备被广泛用作主要设备。
设计和安装轴时,容易出现偏心或质量差等问题,导致转子不平衡、相互力和设备振动。
同时,转子转动的过程中,会产生离心力或离心炬,当离心力发生变化时,设备发生振动,包括大小和方向。
此外,转子在弯曲时也会受到设备振动的影响,主要是横截面几何中心和转子旋转轴之间的不一致,导致质量偏差和不平衡。
2.2支承松动支承松动是指系统连接刚度不足或不牢固,导致机器阻力降低和设备振动过大。
在松动的情况下,极易引发系统不连续位移,发生碰磨现象,产生不稳定的振动,如果情况更严重,会对设备造成很大的冲击,并产生很大的振动声。
智能诊断在旋转机械故障研究中的应用
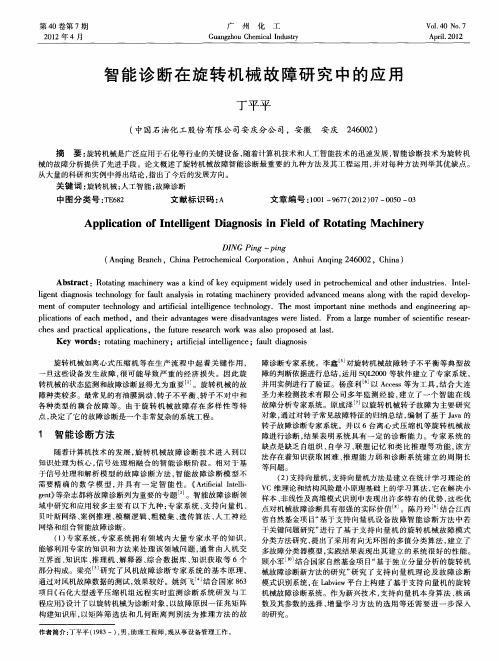
障诊断专家系统 。李鑫 对旋转机械 故障转子 不平衡 等典 型故 障的判断依据进行总结 , 运用 S L 0 0等 软件建立 了专家 系统 , Q 20 并用实例进行 了验 证。杨彦 利 以 A cs ces等为 工具 , 结合 大连
圣力来检测技术有 限公 司多 年监测 经验 , 立 了一个智 能 在线 建 故障分析专家 系统 。原成泽 以旋转 机械转子 故障为 主要 研究 对象 , 过对 转子常见故障特征的归纳总结 , 通 编制 了基于 Jv aa的 转子故障诊断专家 系统 。并 以 6台离 心式压 缩机等 旋转机 械故 障进行诊断 , 结果表 明 系统 具有 一定 的诊 断能 力。专 家系 统 的 缺点是缺乏 自组 织 、 自学 习 、 想记忆 和类 比推理 等功 能 , 联 该方 法存在着知识获取 困难 、 推理 能力 弱 和诊断 系统建 立 的周期 长 等问题 。 () 2 支持 向量机 , 支持 向量机方法是建立在 统计学 习理论 的 v c维 理 论 和结 构 风 险 最 小 原 理 基 础 上 的学 习 算 法 , 在 解 决 小 它 样本 、 非线性及高维模式识别 中表现 出许多特 有 的优 势 , 这些优 点对机械故障诊断具有很强 的实 际价 值 J 。陈丹玲 结 合江西
一
模型存在着 案例维 护 困难 、 案 例生成 需要 额外 知识 等不 足之 处 。结合 方式主要有 : 新 各种诊断理论 与神经 网络 的结合 、 信号处 处。 理 与神经网络的集 成 、 于知识 的专 家系统 与神经 网络诊 断 系 基
第4 0卷第 7期 21 0 2年 4月
广
州
化
工
Vo . 0 No 7 14 . A r . 01 pi 2 2 l
Gu n z o h mia n u t a g h u C e c lI d s ̄
《2024年旋转机械故障诊断与预测方法及其应用研究》范文

《旋转机械故障诊断与预测方法及其应用研究》篇一一、引言旋转机械作为工业生产中不可或缺的重要设备,其稳定运行对生产效率和产品质量具有重大影响。
然而,由于操作环境复杂、维护不当或设备老化等因素,旋转机械常会出现各种故障。
这些故障如不及时发现和处理,可能会对生产造成巨大损失。
因此,对旋转机械的故障诊断与预测显得尤为重要。
本文将重点研究旋转机械的故障诊断与预测方法,以及其在工程实践中的应用。
二、旋转机械故障诊断与预测方法(一)基于信号处理的诊断与预测方法1. 信号采集:通过传感器技术,实时采集旋转机械的振动、声音、温度等信号。
2. 信号处理:利用信号处理技术,如频谱分析、小波变换等,对采集的信号进行预处理和特征提取。
3. 故障诊断与预测:根据处理后的信号特征,结合专家系统或模式识别技术,实现故障的诊断与预测。
(二)基于机器学习的诊断与预测方法1. 数据预处理:对历史故障数据进行清洗、标注和整理,构建故障数据集。
2. 模型训练:采用机器学习算法,如支持向量机、神经网络等,对故障数据集进行训练,建立故障诊断与预测模型。
3. 模型应用:将训练好的模型应用于实际场景中,实现旋转机械的故障诊断与预测。
(三)基于深度学习的诊断与预测方法深度学习通过模拟人脑神经网络的工作方式,可以自动提取数据的深层特征。
在旋转机械的故障诊断与预测中,深度学习模型可以更好地处理复杂、非线性的故障数据。
常见的深度学习模型包括卷积神经网络、循环神经网络等。
三、旋转机械故障诊断与预测方法的应用研究(一)在设备维护中的应用通过实时监测和诊断旋转机械的故障,可以及时发现潜在的问题并采取相应的维护措施,从而避免设备停机或损坏。
这不仅可以提高设备的运行效率,还可以延长设备的使用寿命。
(二)在生产管理中的应用通过对旋转机械的故障进行预测和预警,可以提前制定生产计划和调整生产安排,避免因设备故障而导致的生产延误和资源浪费。
这有助于提高生产效率和产品质量。
机械维修风险分析及防范措施
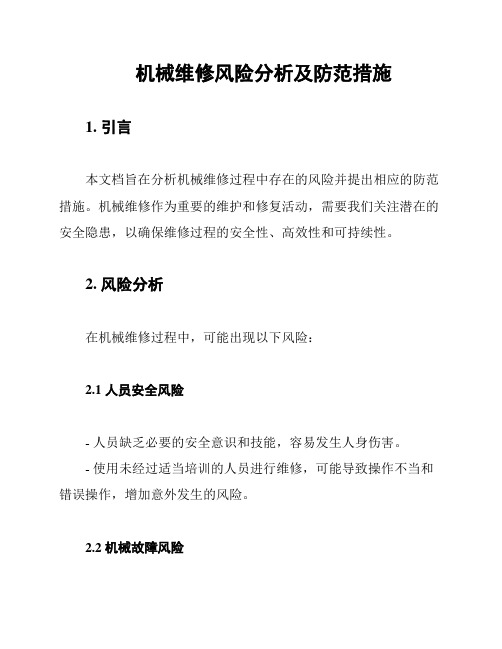
机械维修风险分析及防范措施1. 引言本文档旨在分析机械维修过程中存在的风险并提出相应的防范措施。
机械维修作为重要的维护和修复活动,需要我们关注潜在的安全隐患,以确保维修过程的安全性、高效性和可持续性。
2. 风险分析在机械维修过程中,可能出现以下风险:2.1 人员安全风险- 人员缺乏必要的安全意识和技能,容易发生人身伤害。
- 使用未经过适当培训的人员进行维修,可能导致操作不当和错误操作,增加意外发生的风险。
2.2 机械故障风险- 维修使用的机械设备可能存在故障,导致维修过程无法进行或造成进一步损坏。
- 维修中使用的工具、设备可能存在缺陷,增加维修过程中发生意外的风险。
2.3 设备损坏风险- 由于维修过程中操作不当或使用错误的工具,可能导致设备损坏,进一步增加维修成本和时间。
3. 防范措施为了降低机械维修过程中的风险,我们可以采取以下防范措施:3.1 培训和安全意识提升- 定期组织安全培训,提高人员的安全意识和技能水平,确保他们能够正确操作维修设备。
- 强化维修人员的技术培训,确保他们熟练掌握维修操作的技能,减少错误操作的可能性。
3.2 使用可靠的机械设备和工具- 定期检查维修所使用的机械设备,确保其正常运行,减少因设备故障造成的维修延误。
- 购买并使用经过品质审查的工具和设备,确保其质量可靠,减少因工具损坏导致的维修延误和设备损坏的风险。
3.3 严格的操作规范和程序- 制定明确的操作规范和程序,确保维修人员按照规范进行操作,减少不当操作造成的风险。
- 强制使用正确的工具和设备,防止因使用错误工具导致的设备损坏。
4. 结论机械维修过程中存在一定的风险,但通过培训和安全意识的提升、使用可靠的机械设备和工具,以及严格的操作规范和程序,可以有效减少风险发生的概率,确保机械维修过程的安全性和可靠性。
注意:以上内容仅供参考,具体风险分析和防范措施需根据实际情况进行针对性制定。
石油石化行业针对旋转设备的预测性维护解决方案简述

3
PMQ与企业资产管理系统整合
从Maximo系统中导入资产主数据以加速实现
描述, 位置, 材料类型, 流程, 产品, 供应商... Maximo 资产 管理系统 PMQ 当Maximo系统 中的资产数据 发生变更, PMQ系统中会 自动更新
4
自动初始化Maximo系统工单及推荐行动
Nidal Cruz
业务范围及价值
针对石油石化、矿山、运输、水电 等广泛且严重依赖旋转生产设备的 制造型企业 典型的旋转设备包括:泵(电潜泵 )、发动机、涡轮增压设备、传送 设备以及相关附属设备等 主要价值:降低成本、降低风险、 增加产量、提升质量 主要关注对象: – 负责生产的管理层团队 – 生产运维团队 – 设备维护团队
A. Withers
When removing the PM rotating assembly from the motor care must be taken to overcome the inherent magnetic forces that will try to hold the rotating assembly (rotor and shaft) in the stator winding. It is recommended that the motor be disassembled and reassembled in a vertical drive end shaft up position using a hoist to remove the rotating assembly. In the horizontal position first remove any accessory items (fans, blower, feedback devices, etc.) Also remove the bearing inner cap bolts (if provided). Mount the motor in a vertical drive end shaft up position and remove the drive end bracket. The opposite drive end bracket can remain installed. The thread in the end of the shaft can be used with an eye bolt to lift the rotating assembly with the hoist out of the frame/winding stator.
2023年石化转动设备预防性工作策略
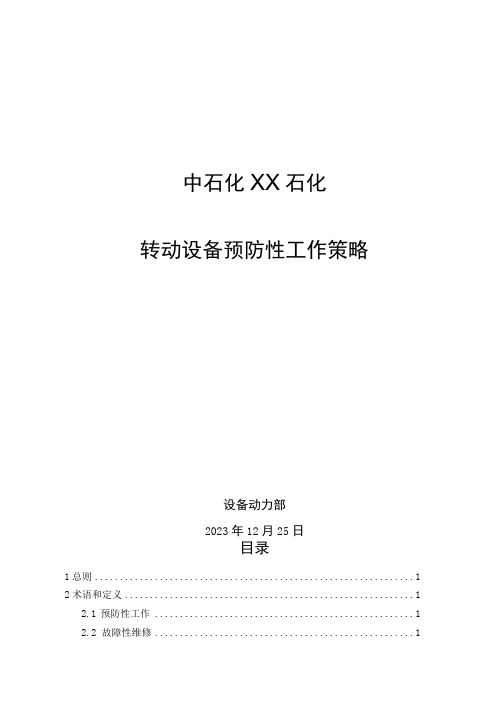
中石化XX石化转动设备预防性工作策略设备动力部2023年12月25日目录1总则 (1)2术语和定义 (1)2.1预防性工作 (1)2.2故障性维修 (1)2.3预防性维修 (1)2.4预知性维修 (1)2.5预测性维修 (1)2.6以可靠性为中心的维修(RCM) (1)2.7故障模式与影响分析(FMEA) (1)2.8DRBPM (1)2.9设备分级分类 (2)3职责 (2)3.1设备管理部门(运行、维护方面) (2)3.2设备技术支持中心(或可靠性团队) (2)3.3基层单位 (2)3.4维保单位 (2)4支持 (2)4.1培训 (3)4.2文件和记录 (3)5实施 (3)5.1总则 (3)5.2预防性工作策略原则 (3)5.3前期管理 (4)5.4运行维护策略 (4)6预防性维修策略要求 (5)6.1透平及透平式压缩机组 (5)6.2容积式压缩机 (6)6.3泵和风机 (10)6.4专有专用设备 (10)6.5特殊阀门 (10)7预防性工作计划 (11)8检查与改进 (11)9附录 (12)9.1规范性引用文件 (12)9.2标准规范 (12)XX石化转动设备预防性工作策略1总则为提高炼化企业转动设备管理水平,以中国石化炼化企业设备完整性管理体系为基础,落实转动设备预防性工作,及时管控风险、消除缺陷,保证设备安全平稳运行,特制定公司转动设备预防性维修策略。
2术语和定义2.1预防性工作在设备发生故障前,按照预定计划或相关要求进行的检验检测、维护保养、维修、改造等工作,其目的是防止设备损坏、提高设备运行可靠性、保证设备安全运行。
维修方式包含预测性维修、预防性维修和预知性维修等。
2.2故障性维修指设备达到故障判定标准而进行的维修作业。
2.3预防性维修按预定的时间间隔和规定的准则实施的设备维修作业。
2.4预知性维修通过对设备运行状态进行监视、测量,识别设备中可能存在缺陷的零件并确定维修时间,从而开展的维修作业。
旋转机械故障机理与故障特征提取技术研究
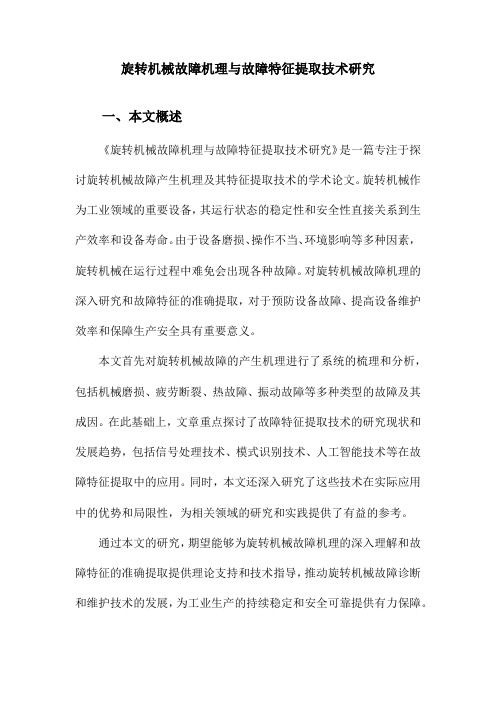
旋转机械故障机理与故障特征提取技术研究一、本文概述《旋转机械故障机理与故障特征提取技术研究》是一篇专注于探讨旋转机械故障产生机理及其特征提取技术的学术论文。
旋转机械作为工业领域的重要设备,其运行状态的稳定性和安全性直接关系到生产效率和设备寿命。
由于设备磨损、操作不当、环境影响等多种因素,旋转机械在运行过程中难免会出现各种故障。
对旋转机械故障机理的深入研究和故障特征的准确提取,对于预防设备故障、提高设备维护效率和保障生产安全具有重要意义。
本文首先对旋转机械故障的产生机理进行了系统的梳理和分析,包括机械磨损、疲劳断裂、热故障、振动故障等多种类型的故障及其成因。
在此基础上,文章重点探讨了故障特征提取技术的研究现状和发展趋势,包括信号处理技术、模式识别技术、人工智能技术等在故障特征提取中的应用。
同时,本文还深入研究了这些技术在实际应用中的优势和局限性,为相关领域的研究和实践提供了有益的参考。
通过本文的研究,期望能够为旋转机械故障机理的深入理解和故障特征的准确提取提供理论支持和技术指导,推动旋转机械故障诊断和维护技术的发展,为工业生产的持续稳定和安全可靠提供有力保障。
二、旋转机械故障机理分析旋转机械故障机理分析是旋转机械故障诊断中的重要环节,它有助于理解故障发生的原因和机制,从而为故障特征的提取和诊断提供依据。
本节将主要讨论旋转机械中的常见故障机理。
大型旋转机械在运转过程中,由于质量分布不均或外部因素的影响,可能导致转子产生不平衡。
这种不平衡会导致周期性的离心力,进而引发机器的振动。
不平衡故障是旋转机械中较为常见的故障类型,它可能由多种因素引起,如转子制造过程中的误差、材料质量问题、零部件磨损等。
不对中是指旋转机械的轴心线与轴承中心线不重合,这种不对中可能是由于安装误差、热变形、基础沉降等原因引起的。
不对中会导致轴系的径向力和弯矩增加,从而引起振动和轴承的异常磨损。
轴承是旋转机械中的关键部件,其性能直接影响到机械的运转状态。
转动设备检修作业风险及安全措施
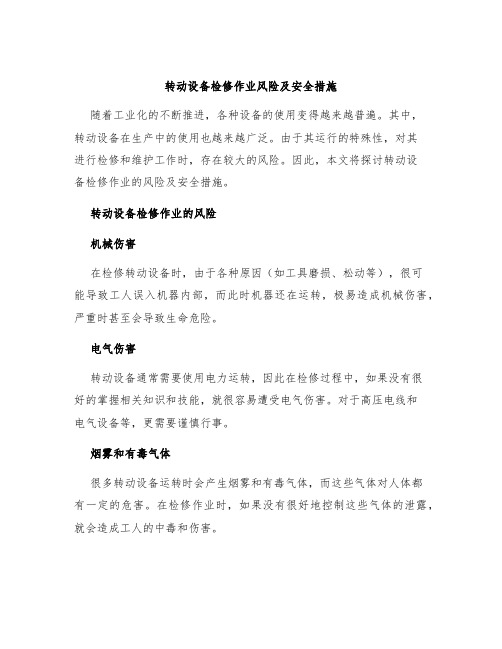
转动设备检修作业风险及安全措施随着工业化的不断推进,各种设备的使用变得越来越普遍。
其中,转动设备在生产中的使用也越来越广泛。
由于其运行的特殊性,对其进行检修和维护工作时,存在较大的风险。
因此,本文将探讨转动设备检修作业的风险及安全措施。
转动设备检修作业的风险机械伤害在检修转动设备时,由于各种原因(如工具磨损、松动等),很可能导致工人误入机器内部,而此时机器还在运转,极易造成机械伤害,严重时甚至会导致生命危险。
电气伤害转动设备通常需要使用电力运转,因此在检修过程中,如果没有很好的掌握相关知识和技能,就很容易遭受电气伤害。
对于高压电线和电气设备等,更需要谨慎行事。
烟雾和有毒气体很多转动设备运转时会产生烟雾和有毒气体,而这些气体对人体都有一定的危害。
在检修作业时,如果没有很好地控制这些气体的泄露,就会造成工人的中毒和伤害。
火灾和爆炸一些转动设备运转时产生的高温和压力,很容易导致火灾和爆炸的发生。
在检修作业时,如不注意火源和爆炸源控制,可能引发火灾和爆炸事故。
转动设备检修作业的安全措施安全帽和防护鞋安全帽和防护鞋是非常基本的保护措施。
由于转动设备作业时很可能遭受机械伤害,因此戴上安全帽是非常必要的。
同样,穿上防护鞋也能有效地减少脚部伤害的风险。
正确使用工具检修转动设备需要使用各种工具,如果使用不当,会给工人带来很大的危险。
因此,在进行检修作业时,必须保证使用的工具都是符合标准的,并且使用方法正确无误。
检修时停止设备运转在进行检修作业时,一定要将设备停止运转。
如果设备还在运转,很容易导致机械伤害和其他安全事故的发生。
因此,在检修作业之前,必须认真审核设备状态,并进行必要的安全控制。
通风和消防为了避免检修作业时产生烟雾和有毒气体,需要做好通风工作。
同样,在火灾和爆炸的情况下,也需要做好消防工作,及时控制火源和爆炸源。
这些做法可以有效地减少安全事故的发生。
预防泄漏在转动设备检修作业过程中,还需要注意控制液体和气体的泄漏。
旋转机械系统动力学及故障诊断

旋转机械系统动力学及故障诊断引言旋转机械在现代工业生产中扮演着重要的角色,涵盖了许多领域,包括能源、交通、制造等。
然而,由于长期运行和频繁的工作条件,旋转机械系统可能会面临动力学问题和潜在的故障。
因此,理解旋转机械系统的动力学行为以及如何进行故障诊断变得至关重要。
旋转机械系统动力学旋转机械系统的动力学研究是理解其运行行为的基础。
动力学主要研究系统在给定载荷和运行条件下的运动和行为。
旋转机械系统的动力学包括自由振动和受迫振动两种类型。
自由振动是指旋转机械系统在没有外部激励的情况下的振动行为。
自由振动的频率和振幅由系统的质量、刚度和阻尼特性决定。
在自由振动中,系统会以特定的固有频率进行振动,这可以通过数学模型进行预测和计算。
受迫振动则是指旋转机械系统受到外部激励而发生的振动。
外部激励可以来自多个方面,包括不平衡质量、轴向力、径向力等。
受迫振动的频率由外部激励频率决定,并且可能会引起系统共振,导致严重的机械故障。
旋转机械系统的故障诊断故障诊断是指通过对旋转机械系统动力学行为的分析和监测,来判断是否存在故障并识别其类型和位置。
故障诊断可以通过多种方法来实现,包括振动分析、声音分析、温度监测等。
振动分析是最常用的故障诊断方法之一。
通过对旋转机械系统振动信号的采集和分析,可以识别出许多常见的故障类型,如不平衡、轴承故障、齿轮故障等。
振动分析可以通过频谱分析、包络分析等技术来获得故障特征,并与预先建立的故障数据库进行比对,从而确定故障位置和类型。
声音分析是另一种有效的故障诊断方法。
通过对旋转机械系统产生的声音信号进行采集和分析,可以判断是否存在异常噪音,并确定其来源。
例如,轴承故障通常会伴随着明显的噪音变化,这可以通过声音分析来检测和诊断。
除了振动和声音分析外,温度监测也是一种常用的故障诊断方法。
旋转机械系统在工作时会产生热量,因此监测系统不同部位的温度变化可以帮助发现故障。
例如,轴承过热可能是轴承故障的指示,而传动系统异常温度升高可能与齿轮故障有关。
旋转机械故障诊断研究方法综述

运用推广 ]。本文作 者对 国 内外学 者在故 障诊断方 法 的研究方 面进行分析 总结 。 1 旋 转机 械故 障诊 断 方法概 述
复杂机械 系统是 由各种小 的系统组 成 ,如 在 自然 条件下 的大生态 系统 ,其是 由许 多个不 同种群 、不 同 生物组成 。复杂 机械 设 备 中旋转 机 械故 障产 生 的特 点 :其产生故 障原 因很多 ,并且相互之 间存在着耦合 的作用 。故 障与征兆之 间没有存在着 明显 的联 系 ,故 障特征之 间相互交织 ,使得很多故 障诊 断方法在某种 程度上对故 障诊断存在一定 的局 限性 [5]。早期 的量纲
关键词 :旋转机械 ;有量纲指标 ;量纲一指标 ;故 障诊 断 中图分类号 :TH165+.3 文献标志码 :A 文章编号 :1001-3881 (2018)07-133-7
Research M ethods of the Rotating M achinery Fault Diagnosis SU Naiquan ’ ,XIONG Jianbin ,ZHANG Qinghua ,HUANG Chonglin (1.School of Electromechanica l Engineering,Guangdong University of Technology,Guangzhou Guangdong 5 10006, China;2.Guangdong Provincial Key Lab of Fault Diagnosis of Petrochemical Equipment,
2018年 4月 第 46卷 第L & HYDRAULICS
Apr.2018 Vo1.46 No.7
DOI:10.3969/j.issn.1001—3881.2018.07.030
基于危险与可操作性分析在生产运行安全中的实践
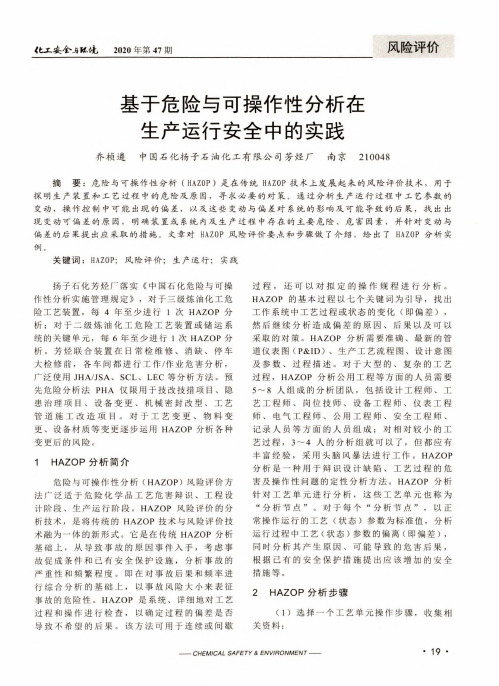
〈匕匚娈舍为穗疏2020年第47期风险评价基于危险与可操作性分析在生产运行安全中的实践乔桢遴中国石化扬子石油化工有限公司芳怪厂南京210048摘要:危险与可操作性分析(HAZ0P)是在传统HAZ0P技术上发展起来的风险评价技术,用于探明生产装置和工艺过程中的危险及原因,寻求必要的对策。
通过分析生产运行过程中工艺参数的变动,操作控制中可能出现的偏差,以及这些变动与偏差对系统的影响及可能导致的后果,找出出现变动可偏差的原因,明确装置或系统内及生产过程中存在的主要危险、危害因素,并针对变动与偏差的后果提出应采取的措施。
文章对HAZ0P风险评价要点和步骤做了介绍,给出了HAZ0P分析实例。
关键词:HAZ0P;风险评价;生产运行;实践扬子石化芳绘厂落实《中国石化危险与可操作性分析实施管理规定》,对于三级炼油化工危险工艺装置,每4年至少进行1次HAZOP分析;对于二级炼油化工危险工艺装置或储运系统的关键单元,每6年至少进行1次HAZOP分析。
芳炷联合装置在日常检维修、消缺、停车大检修前,各车间都进行工作/作业危害分析,广泛使用JHA/JSA,SCL、LEC等分析方法。
预先危险分析法PHA仅限用于技改技措项目、隐患治理项目、设备变更、机械密封改型、工艺管道施工改造项目。
对于工艺变更、物料变更、设备材质等变更逐步运用HAZOP分析各种变更后的风险。
1HAZOP分析简介危险与可操作性分析(HAZOP)风险评价方法广泛适于危险化学品工艺危害辩识、工程设计阶段、生产运行阶段。
HAZOP风险评价的分析技术,是将传统的HAZOP技术与风险评价技术融为一体的新形式。
它是在传统HAZOP分析基础上,从导致事故的原因事件入手,考虑事故促成条件和已有安全保护设施,分析事故的严重性和频繁程度。
即在对事故后果和频率进行综合分析的基础上,以事故风险大小来表征事故的危险性。
HAZOP是系统、详细地对工艺过程和操作进行检查,以确定过程的偏差是否导致不希望的后果。
转动机械危险点分析及控制措施
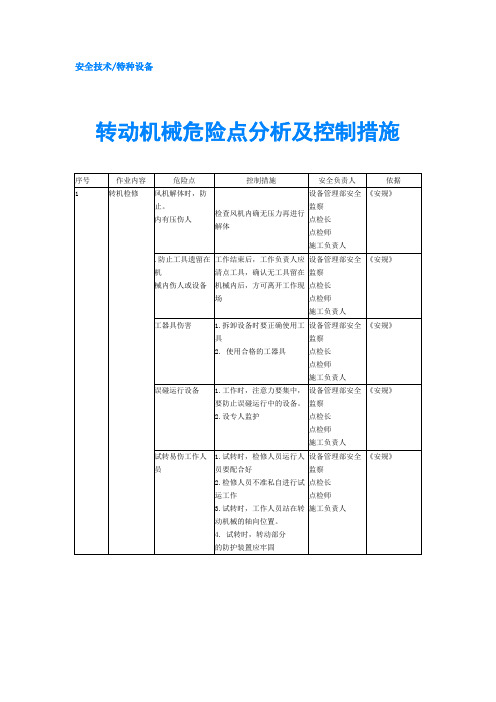
3.试转时,工作人员站在转动机械的轴向位置。
4.试转时,转动部分
的防护装置应牢固
设备管理部安全监察
点检长
点检师
施工负责人
《安规》
设备管理部安全监察
点检长
点检师
施工负责人
《安规》
工器具伤害
1.拆卸设备时要正确使用工具
2.使用合格的工器具
设备管理部安全监察
点检长
点检师
施工负责人
《安规》
误碰运行设备
1.工作时,注意力要集中,要防止误碰运行中的设备。
2.设专人监护
设备管理部安全监察
点检长
点检师
施工负责人
《安规》
试转易伤工作人
员
1.试转时,检修人员运行人员要配合好
安全技术/特种设备
转动机械危险点分制措施
安全负责人
依据
1
转机检修
风机解体时,防止。
内有压伤人
检查风机内确无压力再进行解体
设备管理部安全监察
点检长
点检师
施工负责人
《安规》
.防止工具遗留在机
械内伤人或设备
工作结束后,工作负责人应清点工具,确认无工具留在机械内后,方可离开工作现场
转动设备检修作业风险及安全措施

转动设备检修作业风险及安全措施转动设备在工业生产中广泛应用,例如离心机、风扇、泵等,这些设备通常在高速运转时产生巨大的动能,因此转动设备的检修作业具有高风险性。
在进行检修作业前,需要对风险进行评估,并采取相应的安全措施来保障检修人员的安全。
常见的检修风险1.机器启动和运行风险在进行设备检修作业时,检修人员需要对设备进行停机操作,但是如果操作不当,设备可能存在重新启动的风险。
此外,在停机前未能对设备的所有部件进行检查也可能导致设备在检修时无法稳定停止,造成安全事故的风险。
2.碎片飞溅风险设备在运转时会不可避免地产生震动和摩擦,因此设备的部件可能会发生损坏或破裂,产生碎片飞溅的风险。
这些碎片可能会造成切割、穿刺、撞击等危害,严重时甚至可能伤及生命安全。
3.摔倒和滑倒风险在进行设备检修作业时,检修人员可能需要站在设备的高处或踩在设备上,这会增加检修人员的摔倒和滑倒的风险。
同样,地面上可能存在杂物、油污等危险物品,增加了检修人员走动的风险。
4.电击风险在进行设备检修时,将设备并入电源时,检修人员可能面临电击的风险。
如果检修人员没有接地或没有正确地使用绝缘工具,可能会导致电击事故的发生。
安全措施1.安全培训和教育在进行设备检修作业前,必须对检修人员进行必要的安全培训和教育,使他们了解设备的危险性并掌握相应的安全知识和操作技能。
2.停电、断电、能见度控制在进行设备检修作业时,应将设备停电或断电,确保设备处于不运转的状态。
此外,检修作业现场应保持良好的能见度,防止操作出错和事故的发生。
3.设备维护和保养定期维护和保养设备,增加设备的可靠性和使用寿命。
同时,还可以及时发现设备故障和缺陷,提前采取维修和更换措施,降低设备检修作业的风险。
4.使用安全防护装备在进行设备检修作业时,必须配备必要的安全防护装备,例如头盔、安全鞋、手套、眼镜、耳塞等,进行必要的保护。
5.建立检修作业标准和流程建立合适的检修作业标准和流程,确保检修作业的规范化和安全性。
转动设备检修作业风险及安全措施

转动设备检测、修理作业风险及安全措施
转动设备检测、修理时,误操作电、汽源产生误转动,会危及检测、修理作业人员的生命和财产安全;设备(或备件)较大(重)时,安全措施不当,可发生机械伤害,应该做好下述方面的安全措施:(1)检测、修理作业前,必须联系工艺人员将系统进行有效隔离,把检测、修理设备、管道内的易燃易爆、有毒有害介质排净、冲洗、置换,分析合格,办理《作业许可证》。
(2)在修理带电(汽)设备时,要同有关人员和班组联系,切
断电(汽)源,并在开关箱上挂“禁止合闸、有人工作”的标示牌等。
(3)作业项目负责人应落实该项作业的各项安全措施和办理作
业许可证及审批;对于危险性特大的作业,应与作业区域安全负责人
一起进行安全评估,制定安全作业方案。
(4)作业人员应按要求穿戴劳保用品;熟知工作内容,尤其是
相关部门签署的意见,在作业前和作业中均要认真严格执行。
(5)拆卸的零、部件要分区摆放,善加保护,重要部位或部件
要派专人值班看守。
(6)在使用风动、电动、液压等工具作业时,要按《安全操作
使用说明书》规范操作,安全施工。
(7)设备(或备件)较大(重),需要多工种协同作业时,必
须统一指挥,令行禁止。
(8)加强油品类物质管理,所有废油应倒入回收桶内。
(9)作业完成后,工完料净场地清,做好现场的清洁卫生工作。
- 1、下载文档前请自行甄别文档内容的完整性,平台不提供额外的编辑、内容补充、找答案等附加服务。
- 2、"仅部分预览"的文档,不可在线预览部分如存在完整性等问题,可反馈申请退款(可完整预览的文档不适用该条件!)。
- 3、如文档侵犯您的权益,请联系客服反馈,我们会尽快为您处理(人工客服工作时间:9:00-18:30)。
( C2)
Ⅰ 基本无影响 基本无影响
装置生产降量
Ⅱ
较轻的影响
12 h 之内
环境后果 ( C3)
基本无影响
维修成本 ( C4)
015 万元以下
车间内可处理 015~1 万元
装置停产 Ⅲ
12~24 h
人员受到较重
大伤害
公司内可处理 1~2 万元
装置停产 Ⅳ
24~48 h 装置停产 Ⅴ 48 h 以上
人员永久性伤 由地方政府来
图 5 维修逻辑决断框图 Fig. 5 Flow diagram of the maintenance logical decision2making
(1) 根据故障模式风险值确定维修方式 。本文 的目地是把主要的人力 、物力和财力花费在重要的 故障模式的预防性维修工作中 ,因而故障模式的风 险等级越高 ,所应选择的维修方式和监/ 检测级别越 高 。对高风险故障模式 ,以实时在线状态监测与故 障专家诊断相结合为主 ,采取主动控制措施降低风 险 ,以尽量避免非计划停车带来的重大损失 。中风 险故障模式以视情维修为主 。低风险故障模式以事 后维修和日常点检为主 。
(1) 轴承磨损 ; (2) 气
蚀或气缚 。
D
Ⅱ Ⅰ Ⅰ ⅣM
流量或 (扬程 、(1) 口环磨损或间隙 排压) 异常 过大 ; (2) 滤网堵塞 。 E
ⅡⅠⅠⅣH
机封泄漏
(1) 机械密封件损坏 ; (2) 含焦粒过量损坏 D 机封 。
ⅡⅢⅡⅢH
异常停机 (除 电机故障
泵以外)
C Ⅱ Ⅰ Ⅰ ⅣM
轴承温度高 轴承磨损 电机超载 抱轴
故障模式
常见故障原因
原因
根本原因
预防维修建议
状态监/ 检测建议
润滑不良 按操作法正确开停泵 ,加强润滑保养 ; (1) 对泵前后轴承进行振动监测 ;
(2) 根据故障模式的技术特性确定维修方式 。 故障模式有 2 个技术特性 。一是指故障发生的历 程 ,可分为突发性故障和渐进性故障 。突发性故障 发生前无明显的征兆 ,通常状态监测不能有效地探
1 —急冷器 ;2 —急冷油/ 稀释蒸汽换热器 ;3 —急冷油循环泵 ;4 — 汽油分馏塔 ;5 —过滤器 ;6 —裂解柴油汔提塔 ;7 —裂解燃料油泵 ; 8 —减粘塔
引 言
以可靠性为中心的维修 ( RC维修制度的 一种系统工程方法[123 ] 。从广义上说 ,以可靠性为 中心的维修是为确保设备在运行环境下实现并保持 其设计功能所必须的工作方法[425 ] 。
RCM 在我国石化行业应用刚刚起步 ,即使在发 达国家石化行业也没有大量应用 。石化装置一般为 高危连续生产流程 ,其中旋转机械数量 、种类很多 , 故障率较高 ,对于有限的维修资源 ,必须根据设备的 重要度等级进行资源分配 ,而风险是设备重要度的 一个综合量度 ,不同的设备风险等级意味着故障造 成的影响不同 ,因此风险评价结果可作为维修决策 的依据 。但在传统的 RCM 逻辑分析中 ,没有采用 重要度评价 , 只根据对故障后果评价得到“是”或 “否”的结果来确定维修方式 。对于石化企业来说 , 应用传统的 RCM 进行维修决策 ,维修资源不能得 到真正合理分配 。同时 ,RCM 逻辑决断分析过程繁 杂冗长[6 ] ,因而分析效率很低 ,应用传统的 RCM 分 析将耗费大量的人力和时间 。
表 1 故障发生可能性 ( P) 评价准则 Table 1 Evaluation criteria of failure occurrence possibility ( P)
水平 发生程度
定义
E
易于发生 在一个大修周期内经常发生
D
有时发生 在一个大修周期内有时可能发生
C
偶尔发生 在寿命期内偶尔发生
以风险矩阵表示的故障模式重要度评价方法 ,提出 了针对常见故障原因的维修策略逻辑决断方法 ,以 期在保证设备安全性和可靠性的前提下 ,为维修决 策提供科学的依据 。
1 石化旋转机械基于风险的维修决策
111 决策过程 根据石化行业的特点 ,以 RCM 理论为指导 ,对
石化旋转机械维修决策方法进行了研究 ,分析步骤 如下 :
R = max{ RL , R S , R E , R M} 113 维修决策
依据每一故障模式的风险分析结果和故障技术 特性 ,针对每一常见故障原因的根本原因 ,采用下面 的逻辑决断过程提出维修和监/ 检测建议 。维修逻 辑决断过程如图 5 所示 。
测到 。而渐进性故障发生前有明显征兆 ,可以通过 检查监测到逐渐趋于恶化的故障发生历程[728 ] ,状 态监测对于预防此类故障是非常有效的手段 。因此 正确判断故障有无明显征兆是确定是否可以采取状 态监测的重要依据之一 。技术特性之二指故障率是 否与时间相关 ,如果故障率随时间的增加而增大或 者减小 ,则适合采用定期更换维修 ;如果为随机发生 的故障 ,则适合采用状态监测或事后维修等 。
(1) 成立研究小组 ,确定研究对象 小组由各专业专家及车间工艺 、设备人员和操 作 、维修人员组成 。研究对象被确定之后 ,首先收集 相关的设备 、工艺 、维修等方面的资料 ,并做出详细 的记录 ,为维修决策提供必要的依据 。 (2) 系统划分 为了方便分析和提高效率 ,把分析对象按照工 艺功能或地理位置分成若干个子系统 。 (3) 故障模式 、原因分析和风险评价 根据设备功能 ,进行故障模式分析 ,并找出导致 故障的原因 。建立适合于石化旋转机械重要度评价 的风险评价准则 ,依据准则 ,采用系统的观点进行故 障模式风险评价 。 (4) 维修决策 根据故障模式的风险评价结果进行逻辑决断分 析 ,选择预防性维修工作类型 。 112 风险评价 根据石化生产的特点 ,风险评价包括 :生产损失 风险 ( RL) 、安全影响风险 ( R S) 、环境影响风险 ( R E)
B
不太可能发生 在寿命期内不易发生 , 但有可能发生 (同行业发生过)
A
极少发生
极不易发生 ( 理论上可能 ,但实际极不 可能发生)
表 2 故障后果等级评价准则 Table 2 Evaluation criteria of failure consequences
对生产的影响 安全后果
后果
( C1)
(1) 轴对中超标 ; (2) 轴弯曲 ,转子跳动量大 ,转子不平衡 ; (3) 轴承磨损 ; (4) 转子窜量过大 ; (5) 膜片联轴器损坏 ; (6) 动静零部件异常碰磨 ; (7) 气蚀或气缚 ; (8) 飞粘 、含焦粒过量冲蚀叶轮/ 泵壳 ; (9) 工艺参数异常变化 。 从上述 9 种故障原因中选出常见故障原因 ,为 (3) 和 (7) 。表 3 为急冷油泵的故障模式风险评价结 果 ,其中仅列出了故障模式的常见故障原因 。根据 图 5 的逻辑决策框图 ,针对 6 种故障模式的共 9 种
图 2 安全风险矩阵 Fig. 2 Safety effect risk matrix
图 3 环境风险矩阵 Fig. 3 Environment effect risk matrix
图 4 维修成本风险矩阵 Fig. 4 Maintenance cost risk matrix
初步确定故障发生的频率范围 , 然后把设备运行状 态趋势作为修正因子以预测故障发生可能性 。故障 后果评价采用系统的观点 , 同时考虑设备故障对设 备本身 、上一级子系统和整个装置的影响 。故障发 生可能性和故障后果评判准则分别如表 1~2 所示 。
第 36 卷 第 2 期 2009 年
北京化工大学学报 (自然科学版) Journal of Beijing University of Chemical Technology (Natural Science)
Vol. 36 , No. 2 2009
石化旋转机械基于风险的维修决策研究
郭丽杰 高金吉 杨剑锋 王世达 李大成
残
解决
2~5 万元
必须通过中央
1 人或 1 上死亡
人以
和国际组织协
5
万元以上
助处理
第 2 期 郭丽杰等 : 石化旋转机械基于风险的维修决策研究
·89 ·
风险值分为 3 个等级 :高 ( H) 、中 ( M) 和低 (L ) 。应 用最大危险原则 , 每一故障模式风险值 ( R ) 取 4 个 风险中的最大值 ,即
2 维修决策分析实例
为了验证基于风险的维修决策方法的有效性 , 以中石化某乙烯装置的急冷油循环泵作为分析实 例。
在进行维修决策分析之前 ,必须了解设备的功 能 。急冷油循环泵为单级卧式离心泵 ,介质为急冷 油 ,温度 197 ℃,泵入口压力 0108 MPa ,泵出口压力 11099 M Pa ,流量为 2110 m3/ h ,其工艺流程如图 6 所 示 。在汽油分馏塔中 ,来自裂解炉的裂解气被急冷 油迅速冷却 ,同时分离出裂解燃料油 。汽油分馏塔 塔底的急冷油经过急冷油循环泵之后 ,主要分为 3 股 ,第 1 股急冷油经急冷油/ 稀释蒸汽换热器冷却以 后作为汽油分馏塔的中部进料 ,第 2 股在急冷器与 来自裂解炉的裂解气换热以后 ,共同作为汽油分馏 塔底部的进料 ,第 3 股进入裂解柴油汽提塔 。装置 中设两台急冷油循环泵 ,分为主泵和备用泵 ,但备用 泵的流量小于主泵 ,所以如果主泵出现故障 ,虽然会 启用备用泵 ,但会造成整个装置的减产 。急冷油循
图 6 急冷油循环工艺流程简图 Fig. 6 The process flow diagram of t he quench oil
circulating pump
·90 ·
北京化工大学学报 (自然科学版) 2009 年
环泵共有 6 种常见的故障模式 :振动或异响 、流量或 (扬程 、排压) 异常 、机封泄漏 、异常停机 、轴承温度高 和电机超载 。对每种故障模式分析其所有可能的故 障原因 ,例如对振动或异响 ,有以下 9 种故障原因 :