过程审核报告(评分表)-083
供应商过程审核打分表

3.1.11 交货期的控制
评论
指引
1.一个程序来控制FIFO 2.传入的部分日期的标签和完成好 3.料架的设计很容易控制 物质的储藏住址签署,架分类,走道告示适 当地且包含正确的数据。所有材料在被指定 的位置被储存。通道地面上是没有材料和部 件的,或在架下也一样。溢流材料位于被指 定的位置。 1.有物流管理人员通知顾客并立即回应任何情 况是否由组织或顾客发现在文件的程序,可 能产生负面影响的客户的业务。
3.2.2 快速响应会议实现
3.2客户的满 意度 3.2.3问题解决过程的识别和消除问题的根本原因
3.2.4 经验教训数据库创建
3.2.5客户调查
顾客满意度的总结
0
1.定期回顾客户投诉(质量,物流问题) 2.行动计划的创建和跟踪 1.日常运作会议,审查的内部和外部的质量问 题和控制行动的建立
8D或5什么原理解决问题
历史的经验教训,反映问题的新方案
记录和行动计划
维修服务 项目
仓库/物流/配送
区段
3.1.1短期生产计划及生产能力计划
3.1.2长期生产计划及生产能力计划
3.1.3 在FIFO系统及实现
3.1仓库 物流/
3.1.4 在仓库的可视化管理和组织。
送货
3.1.5 在发生紧急程序和通信
评分表 分数
3.1.6完成包装好顾客批准
3.1.7 供应商有溢价的出货量控制目标和根本原因分析
完成包装好顾客认可,子供应商零件批准供 应商的包装 保险货物数据采集,根本原因和作用在目标 项目,经验教训
行动计划创建时,库存的最大和最小库存
过程审核打分表
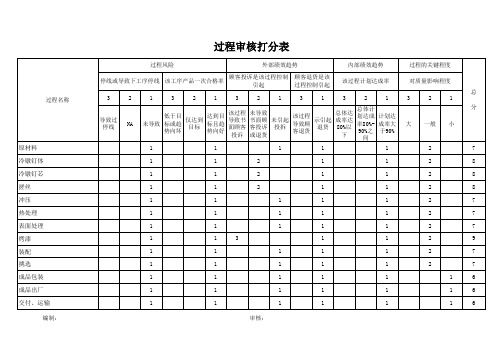
原材料 冷镦钉体 冷镦钉芯 搓丝 冲压 热处理 表面处理 烤漆 装配 挑选 成品包装 成品出厂 交付、运输
编制:
2 2 2 2 2 2 29 7 7 6 6 6
过程审核打分表
过程风险 停线或导致下工序停线 该工序产品一次合格率 过程名称 3 2 1 3 2 1 外部绩效趋势 顾客投诉是该过程控制 引起 3 2 1 顾客退货是该 过程控制引起 3 1 内部绩效趋势 该过程计划达成率 3 2 1 过程的关键程度 对质量影响程度 3 2 1 总 分 大 一般 小
导致过 停线
NA
该过程 低于目 达到目 仅达到 导致书 未导致 标或趋 标且趋 目标 面顾客 势向坏 势向好 投诉 1 1 1 1 1 1 1 1 1 1 1 1 1 1 1 1 1 1 1 1 1 1 1 1 1 1 3
总体计 未导致 总体达 该过程 划达成 计划达 书面顾 未引起 示引起 成率达 导致顾 率80%- 成率大 客投诉 投拆 退货 80%以 客退货 90%之 于90% 或退货 下 间 1 2 2 2 1 1 1 1 1 1 1 1 1 1 1 1 1 1 1 1 审核: 1 1 1 1 1 1 1 1 1 1 1 1 1 1 1 1 1 1
过程审核报告(评分表)

XXXX有限公司过程审核报告SJ/JL-083-B/0123456123456符合率(%)1.策划2.落实E DE1234561234561.策划2.落实101010101010E PE12345678910101010E Z1.11.21.31.41.52.12.22.32.42.52.62.73.13.23.33.43.54.14.24.34.44.54.61010101010101010101010101010101010101010101010E 1E 2E 3E 4E 5E 6E 7E 8E 9E 10B2要素中对照质量体系的评分(工序1-n 的平均值)1.1 1.2 1.3 1.4 1.52.1 2.2 2.3 2.4 2.5 2.6 2.73.1 3.2 3.3 3.4 3.54.1 4.2 4.3 4.4 4.5 4.6101010101010101010101010101010101010101010101012345610110101010E KB2要素中按产品组的符合率E PG (%)(E X -E n 的平均值)按产品组计算的总符合率批量生产前批产开始时/以后注:未进行评分的提问用nb 填入过程审核评分表昆山博富新材料科技股份有限公司100100人员/素质生产设备/工装nb100100运输/搬运/贮存/包装A 产品诞生过程1 产品开发(设计)2 过程开发ES 1(%)B 批量生产2 生产(对各道工序评分)工序1:工序3:缺陷分析,纠正措施,持续改进(KVP)100工序2:#DIV/0!E PG (%)1 分供方/原材料#DIV/0!工序6:#DIV/0!工序7:#DIV/0!工序4:#DIV/0!工序5:ES 2(%)ES 3(%)ES 4(%)100#DIV/0!工序8:#DIV/0!工序9:产品组#DIV/0!工序10:#DIV/0!3 服务/顾客满意程度85100工序产品组符合率EP(%)已评要素数E P (%)=E DE +E PE +E Z +E PG +E K=保存期:三年。
过程审核的评分标准

0
--产品上有缺陷(不能满足功能性,产品的 --机器/设备/工装不适用,不完整或者完全没有 使用受到严重限制,顾客对其不能开展进一 到位 步的制造) --在接下来的过程/检验中不能发现缺陷,从 --涉及顾客的特性的制造不能满足过程可靠性 而也就不能加以筛选或者返工
--没有提供相关的检查,检验和测量工具,从而 对涉及顾客的特性开展监控 --零部件搬运过程中会引起涉及顾客的特性的受 --产品应用对接下来的用户而言构成一种风险 损 --企业内部或者发货过程中会导致零部件混淆, 从而影响到顾客那里的进一步制造
--没有为人员提供必要的资格培训 --于有关要求的落实情况不足,导致顾客那里 发生功能缺陷
--会出现投诉以及现场失效的情况
过程审核的评分风险评分表
评分 10 产品风险
--产品没有任何缺陷,满足技术要求 --产品上有缺陷(但不影响到功能,使用或者在 过程中的进一步制造),需要加以改进
过程风险
--满足了技术要求/产品和过程的技术规范要求 --生产流程中存在轻度的故障 --过程中存在薄弱环节,但被及时发现和排除
质量管理体系相关性
8
6
--产品上有缺陷(但不影响到功能,缺陷会导致 使用时或者在过程中的进一步制造时发生故障) --没有满足过程能力要求(特殊特性) --在接下来的过程中将对缺陷加以返工 --检验时发现缺陷,有缺要求,但特殊 特性仍满足技术规范要求 --对特殊特性没有开展系统的监控 --需要开展筛选行动 --需要开展返工 --零部件有受到损伤的风险 --整个材料流转过程中存在过程风险 --检验和测量工具不适用于发现缺陷 --员工的培训不够 --产品的生产不能满足过程可靠性的要求,特殊 特性部分超差 --对特殊特性没有开展系统的监控 --需要开展筛选行动 --需要开展返工 --零部件有受到损伤的风险 --零部件混合/错误的安装导致过程故障 --用于发现缺陷的检验和测量工具不适用 --员工一方面接受的培训不足,另一方面对故障 模式也不了解
过程审核打分表
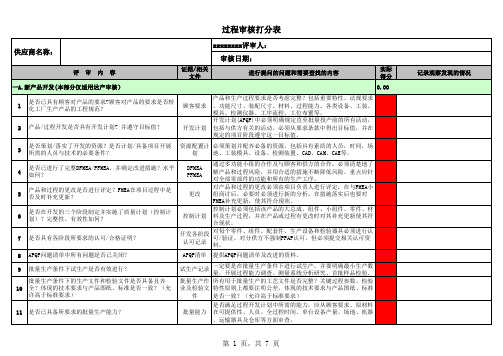
控制计划必须包括该产品的大总成、组件、小组件、零件、材 控制计划 料及生产过程,并在产品或过程有更改时对其补充更新使其符
合现状。
7 是否具有各阶段所要求的认可/合格证明?
开发各阶段 认可记录
对每个零件、组件、配套件、生产设备和检验器具必须进行认 可/验证。对分供方不强制PPAP认可,但必须提交相关认可资 料。
批量生产作 所有用于批量生产的工艺文件是否完整?关键过程参数、检验
业及检验文 特性原则上都要注明公差。体现的技术要求与产品图纸、标准
件 是否一致?(允许高于标准要求)
是否满足过程开发计划中所需的能力,应从顾客要求、原材料 批量能力 在可提供性、人员、全过程时间、单台设备产量、场地、机器
、运输器具及仓库等方面审查。
(图纸上有技术条件的也认可)
对关键、安全、环保等产品和过程的特殊特性应完整识别(包
特殊特性 括顾客指定的特殊特性),并借助于FMEA来建立特性排序,并
在控制计划、各类作业指导书中加以注明。
作业、检验 指导书
查产品实现过程的所有工艺文件、检验指导书是否完整?体现 的技术要求与产品图纸、标准是否一致?(允许高于标准要 求)
过程审核打分表
供应商名称:
xxxxxxxx评审人: 审核日期:
评审内容
证据/相关 文件
进行提问的问题和需要查找的内容
实际 得分
一A.新产品开发(本部分仅适用达产审核)
0.00
1
是否已具有顾客对产品的要求?顾客对产品的要求是否转 化工厂生产产品的工程规范?
产品和生产过程要求是否考虑完整?包括重要特性、法规要求 顾客要求 、功能尺寸、装配尺寸、材料、过程能力、各类设备、工装、
行了陈述?
过程审核评分矩阵及结果一览表

6.1 .2
.3
.4
6.1.2 6.1.3 6.1.4 6.2.5 6.2.6 6.4.4 6.6.2 6.6.3
4
8
0
0 24
0
0
0
0
0
0 0
0
0 Eu3[%]
0 0
0
0
0
0 0
0
0
0
0 0
0
0
0
0 0
0
EPG
80
8
0
0
0
0
0
0 10
0
Eu1[%] P7
Eu2[%]
Eu4[%]
.7.3* .7.4 .7.5 .7.6
EPZP
80
EPP
80
EPP [%]=(EPDP+EPZP)/2
10
0
6
0
P4
产品开发及过程开发的落实 产品 .4.1 .4.2 .4.3 .4.4 .4.5* .4.6 .4.7 .4.8 .4.9 EPDR 过程 .4.1* .4.2 .4.3 .4.4 .4.5 .4.6 .4.7 .4.8 .4.9 8 4 10
3.过程支持
6.3.1 6.3.2* 6.3.3
4.物质资源
6.4.1 6.4.2* 6.4.3 6.4.4
5.满意度
6.5.1 6.5.2 6.5.3* 6.5.4*
6.过程成果
6.6.1* 6.6.2 6.6.3 6.6.4
7.零部件搬运的落实程度
6.1.2 6.1.3 6.1.4 6.2.5 6.2.6 6.4.4 6.6.2 6.6.3
G1 PR
G2 TO
G3 CO
过程审核评分一览表-03

NITL-QR19-003/A
过程审核评分一览表
年
顾客: 报告号: A、产品诞生过程 (a)产品开发(设计) 1)策划 (b)过程开发 1)策划 B、批量生产 1 3)供方/原材料 4)生产(对每一工序的评定) 5.1人员/素质 5.2设备/工装 1 2 3 4 5 1 2 3 4 工序1 工序2 2 3 产品诞生过程/批量生产 分厂/部门: 日期:
EU4(%) 1 2 3
4
5 EK
6、服务/顾客满意程度 B5要素中按产品组计算符合率EPG(%)(E1至En的均值) A B C 产品组 工序 EPG(%) EDE+EPE+EZ+EPG+EK 被评定要素的数量
D
某产品组过程审核的总符合率EP(%)=
(%)=
NO.:
Байду номын сангаас
2)落实 2)落实 4 5 6 7 8 9
EDE EPE
EZ 5.3运输/搬运/贮存 1 2 3 4 5 5.4缺陷分析/纠正措施/持续改进 1 2 3 4 5 6 E1 E2
5
6
7
工序3 E3 工序4 E4 工序5 E5 工序6 E6 工序7 E7 工序8 E8 工序9 E9 工序10 B5中各分要素与质量管理体系对照表的评分(工序1至工序n的均值) 1 2 3 4 5 1 2 3 4 5 6 7 1 2 3 4 EU1(%) EU2(%) EU3(%) E10 5 1 2 3 4 5 6
IATF16949 过程审核评分表 (机加工序)
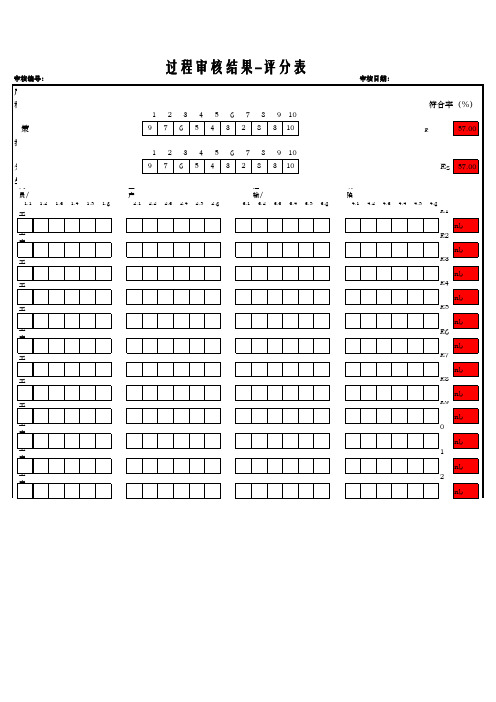
E1 nb 2
nb
对 照 体 系 的 评 分 要 素 ( 工 序 E
1
n 符 合 率 , 平 均 值 )
1.1 1.2 1.3 1.4 1.5 1.6
nb nb nb nb nb nb
ES1(%)
nb
3 为 顾 客 服 务 / 令 顾 客 满 意 按 产 品 组 要 素 计 算 的 总 符 合 率
EPG (%)
2.1 2.2 2.3 2.4 2.5 2.6 nb nb nb nb nb nb
3.1 3.2 3.3 3.4 3.5 3.6 nb nb nb nb nb nb
ES2(%)
nb
ES3(%)
nb
1 2 3 4 5 6 7 8 9 10
9 7 6 5 4 3 2 8 3 10
nb
4.1 4.2 4.3 4.4 4.5 4.6 nb nb nb nb nb nb
生 产
2.1 2.2 2.3 2.4 2.5 2.6
运 输/
3.1 3.2 3.3 3.4 3.5 3.6审核日期:符率(%)EPE
57.00
EZ 57.00
缺 陷
4.1 4.2 4.3 4.4 4.5 4.6
E1
nb E2
nb E3
nb E4
nb E5
nb E6
nb E7
nb E8
nb E9
E1 nb 0
审A 核编号: 产过 程
1 B策 批 1 分2 生
人 员/
1.1 1.2 1.3 1.4 1.5 1.6
工
工 序
工
工
工
工 序
工
工
工
工 序
工 序
过程审核评分表

必须定义和规范质量数据和过程参数(设定值),这些数据对于证明产品一致性来说是必要的。
记录实际数据(实际值),用于展示对目标要求的符合性。
这些数据必须确保可用以评价。
对异常情况进行记录(班次日志/设备日志)。
收集的数据要与产品和过程相关,数据来源是实际的、易获取的、可查的、可存档的。
要考虑追溯性要求。
对收集的数据进行分析,并启动相应的改进措施。
潜在的改进必须根据质量、成本、服务的先前问题来持续开展。
导致过程或产品发生偏离的事件,及其相关措施,被体现在相应的风险分析(例如FMEA)当中。
●缺陷收集卡
●控制图
●特殊特性
●过程参数(温度,时间,压力...)
●生产数据采集
●故障信号(例如停线,断电,程序故障报警)●参数变化
●失效类型/失效频率
●失效成本(不符合)
●报废/返工
●隔离通知/拣选行动
●节拍时间,周期时间
●SPC●柏拉图分析
●因果图
●风险分析(FMEA、FTA…)。
过程审核检查表_2
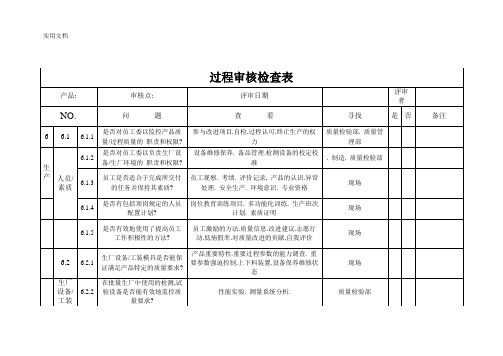
生产部
D2.3
是否根据评定的结果(实物质量问题或质量能力不足)与供方一起制定提高措施并落实?
与问题供方领导的会谈.改进计划的落实.改进的服务过程.审核结果
生产部
D2.4
是否与供方协商确定改进过程和外委服务的目标/措施并加以落实?
持续改进.确定可度量的目标值.成本优化
顾客满意度调查
质量管理部
服务
D3.2.2
是否对纠正措施的落实情况及其有效性进行审查?
顾客.内部抱怨.再发防止措施报告.结果验证.内审,管审
质量检验部
D3.2.3
是否能保证满足对过程的特殊质量要求?
设备维护.照明,人机工程学
生产部.
D3.2.4
是否对服务过程的有效性进行监控?
顾客满意度调查
质量管理部
D3.2.5
原始记录.控制图.数据收集.过程参数的记录装置(时间.温度等).停机.参数更改
项目公司.质量检验部
缺陷分析/纠正措施/持续改进(KVP)
6.4.2
是否用统计技术分析质量数据/过程数据,并由此制定改进措施?
过程能力.缺陷.过程参数.废品.返修件.隔离通知返修.生产节拍.可靠性失效特征(SPC.排列图.因果图)
项目公司.质量检验部.
D3.1.3
在服务过程中使用的员工是否有能力完成所交给的任务?是否对其素质进行定期的监控?
安全环保.质量意识.员工满意度.培训措施
生产部
D3.1.4
是否调查并能保证满足人员需求?是否有足够的顶岗人员?
人员需求调查.费用核算.重要岗位代理制度
生产部
D3.2
D3.2.1
是否对服务进行认可?是否调查并记录其与要求之间的偏差?
过程审核检查表--示例

2.3.5工装模具、设备和检测设备是否合适地存放?
考虑要点:防损伤的存放;有序清洁;定置存放区;有管理的发放;环境影响;标识;明确的认可状态和更改状态;
此工序配置的所有工装、设备及量具要求操作者保持其清洁状态,确保其使用,并执行
考虑要点:足够的、合适的运输器具;定置库位;最小的/无中间库存;看板(KANBAN);JIT;先进先出(FIFO);仓库管理;更改状态;向下道工序只供给合格件;产量记录分析;信息流;
在生产过程中,规定由下工序的作业人员向本工序进行适时领用,一次性领用量不超过XX箱,保证各工序间的物流均衡流动。
2.3.2产品/零件是否按要求存放,运输器具/包装设备是否与产品/零件的特点相适应?
过程审核检查表
审核日期:年月日~年月日审核员:
检查项目
检查要点
客观论据记录
评分
10
8
6
4
0
3顾客关怀/顾客满意度(服务)
3.1是否满足顾客对质量管理体系、产品和过程的要求?
考虑要点:质量管理体系按照ISO/TS16949:2002标准;质量协议;针对零缺陷要求的目标协议;交付审核;耐久试验(调查失效模式);功能检验;
公司建立了相应的程序文件及应急计划程序,对于突出事件能及时做出反映,特殊是当顾客出现抱怨时的及时处理。
8
3.4与质量要求有偏差时,是否进行了缺陷分析并实施了改进措施?
考虑要点:分析的可能性(实验室、检验和试验设施、人员);;实验室符合ISO/IEC17025的要求;针对缺陷特性进行排列图-分析(内部/外部)各有关部门的介入(内部/外部);运用解决问题的方法(如8D-报告);
过程审核报告(评分表)

### ### ### ### ###
### ### ### ### ### ### ###
### ### ### ### ###
### ### ### ### ### ###
ES1(% #DIV/0!
ES2(%)
3 服务/顾客满意程度 B2 要
产品组
工序
#DIV/0!
ES3(% #DIV/0!
ES4(%)
123
#DIV/0! 456
E #DIV/0!
按 EPG(%) 产
批 量
批
注
产
:
EP(%)=
EDE+EPE+EZ+EPG+EK 已评要素数
=
产品组
符合率EP(%)
保存期:三年
XXXX有限公司
过程审核报告
SJ/JL-083-B/0
保存期:三年
符E
nb DE
EP
#DIV/0!
E
E
#DIV/0! Z
人员/素质
生产设备/工装
运输/搬运/贮存/包装
缺陷分析,纠正措施,持续改进(KVP)
1.1 1.2 1.3 1.4 1.5
工序1: 工序2: 工序3: 工序4: 工序5: 工序6: 工序7: 工序8: 工序9: 工序10:
B2 要
1.1 1.2 1.3 1.4 1.5
2.1 2.2 2.3 2.4 2.5 2.6 2.7 2.1 2.2 2.3 2.4 2.5 2.6 2.7
3.1 3.2 3.3 3.4 3.5 3.1 3.2 3.3 3.4 3.5
4.1 4.2 4.3 4.4 4.5 4.6
最新过程审核产品组评分表
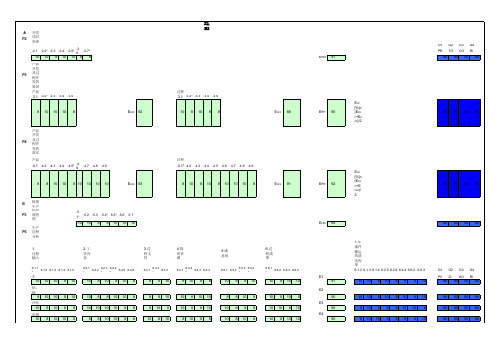
10
9
9
9 90
9
9
8
9 85
8
10
9
10 98
10
EPG
91
9.4
10
9.1
9.1
8.9
9.1 9.14 9.71 93
Eu1[%] P7
Eu2[%]
Eu4[%]
.7.3* .7.4 .7.5 .7.6
Eu5[%]
Eu6[%]
Eu7[%]
客户关怀、客户满意度、服务
.7.1* .7.2
10 产品组的满足度: EPGN[%], 选择P6[%](E1--En 平均值) 1 产品组 过程步骤 EPGN[%] 91
G1 PV
G2 ZI
G3 KO
G4 RI
90 90 90 90 90 90 90 0 0 0
90 90 90 90 90 90 90 0 0 0
90 90 90 90 90 90 90 0 0 0
90 90 90 90 90 90 90 0 0 0
钻、铣 8 10 冲压 10 电焊 10
表面电泳 8 10 装配 10 包装 10 工序8 工序9 工序10
EPDR
.5.7
93
EPZR
91
EPR
92
EPR [%]=(EPDR+EPZR)/2
90
90
90
90
B P5 P6
批量生产 供应商管理 生产过程分析 1. 过程输入
6.1.1* 6.1.2 6.1.3 6.1.4 6.1.5
.5.1*.5.2
.5.3
.5.4* .5.5* .5.6
10
10
8
过程审核评分方法

过程审核评分方法附件一:过程审核评分方法1 提问和过程要素的单项评分:审核员根据对提问的要求以及在产品诞生过程(产品质量先期策划过程/服务诞生过程)和批量生产(实施服务)中满足过程审核要求的实际情况对提问的项目进行评定。
每个提问的得分以0、4、6、8、或10分进行评分,满足项目要求的程度是打分的根据。
评分不满10分时则须制订纠正/改进措施并确定落实其改进期限。
分数对符合要求程度的评定10 完全符合8 绝大部分符合,只有微小的偏差(*)6 部分符合,有较大的偏差4 少部分符合,有严重的偏差0 完全不符合备注(*)“绝大部分符合”指的是证明已满足了约3/4以上的规定要求。
没有特别的风险。
过程要素符合率Ee计算公式如下:各相关问题实际得分的总和Ee(%)= ─────────────× 100%各相关问题满分的总和2 审核员于每次过程审核结束时,将上述相关表单/记录整理后,将各项评分结果填入“表单-03过程审核提问的评分/符合率表”中,并计算其各项符合率,计算完成后提交给审核组长。
3 审核结果的综合评分(符合率计算方法):a.审核员首先须对下列各要素分别进行评定:产品服务—产品开发 Ede—策划 Ede—过程开发Epe—原材料/外购件Epg—外委服务或/和外购产品Ez—各道工序的平均值Ez —各道工序的平均值Epg—售后服务/用户满意Ek —用户服务/用户满意Ek备注1.在对服务进行审核时,请把下列描述中的生产换为服务,生产过程换为服务过程。
由于在要素“生产”中的产品组不同,其工序也不同,所以必须把产品组各生产工序的得分汇总起来(平均值Epg),然后计算总符合率。
这对于保证各要素进行均衡的评定也是必要的。
这样,产品组不同,所选的生产工序不同,“生产”要素计算出的符合率也可能不同。
b.每个产品组工序平均值Epg的计算公式如下:(E1+E2+E3+……En)Epg(%)= ──────────× 100%被评定工序数量c.整个过程的总符合率计算如下:(Ede+Epe+Ez+Epg+Ek)Ep(%)=───────────× 100%被评定过程要素的数量①.此外,作为对整个过程的评定的补充,也可以另外对“生产”要素中的各分要素进行评定,来反映质量管理体系的情况。