油缸稳定性计算
油缸压力计算公式

油缸压力计算公式
油缸压力计算公式是机械制造业中的重要计算公式。
它的优点是不仅能够准确地计算出油缸的压力,而且可以作为油缸在设计过程中的重要参考。
本文将介绍油缸压力计算公式的原理和应用,并给出一些有用的技巧。
油缸压力计算公式的基本原理
油缸压力计算公式主要通过力学原理计算出油缸的压力:压力=
重力×面积。
在计算油缸压力时,需要根据油缸的长度和容积来确定油缸上的重力,并通过油缸的柱面积来计算出压力。
油缸压力计算公式的应用
油缸压力计算公式可用于柴油机车辆、汽车和液压系统等机械领域的油缸设计和制造过程中。
它可以用来计算出油缸设计要求的压力,以便将油缸按要求安装到设备中。
同时,油缸压力计算公式还可以用来检查和评估尚在使用的油缸是否仍符合制造要求,以确保其安全性。
油缸压力计算公式的技巧
在油缸压力计算公式的应用中,可以采取以下几种技巧来简化计算:
1.首先,根据油缸的长度和容积来确定油缸上的重力,并计算出油缸的柱面积;
2.其次,通过油缸容积的改变来改变油缸的压力,从而获得更准确的结果;
3.最后,通过调整油缸质量来调整油缸的压力。
结论
油缸压力计算公式是设计和制造机械设备中油缸的重要参考,通过它可以准确地计算出油缸的压力。
在使用油缸压力计算公式时,需要根据油缸的容积、重量和长度来确定油缸上的重力,并利用油缸的柱面积来计算出压力,从而更好地安装油缸和检查油缸的安全。
液压油缸设计计算公式.

液压油缸的主要设计技术参数一、液压油缸的主要技术参数:1.油缸直径;油缸缸径,内径尺寸。
2. 进出口直径及螺纹参数3.活塞杆直径;4.油缸压力;油缸工作压力,计算的时候经常是用试验压力,低于16MPa乘以1.5,高于16乘以1.255.油缸行程;6.是否有缓冲;根据工况情况定,活塞杆伸出收缩如果冲击大一般都要缓冲的。
7.油缸的安装方式;达到要求性能的油缸即为好,频繁出现故障的油缸即为坏。
应该说是合格与不合格吧?好和合格还是有区别的。
二、液压油缸结构性能参数包括:1.液压缸的直径;2.活塞杆的直径;3.速度及速比;4.工作压力等。
液压缸产品种类很多,衡量一个油缸的性能好坏主要出厂前做的各项试验指标,油缸的工作性能主要表现在以下几个方面:1.最低启动压力:是指液压缸在无负载状态下的最低工作压力,它是反映液压缸零件制造和装配精度以及密封摩擦力大小的综合指标;2.最低稳定速度:是指液压缸在满负荷运动时没有爬行现象的最低运动速度,它没有统一指标,承担不同工作的液压缸,对最低稳定速度要求也不相同。
3.内部泄漏:液压缸内部泄漏会降低容积效率,加剧油液的温升,影响液压缸的定位精度,使液压缸不能准确地、稳定地停在缸的某一位置,也因此它是液压缸的主要指标之。
液压油缸常用计算公式液压油缸常用计算公式项目公式符号意义液压油缸面积 (cm 2 A =πD 2/4D :液压缸有效活塞直径(cm液压油缸速度 (m/min V = Q / AQ :流量(l / min液压油缸需要的流量(l/minQ=V×A/10=A×S/10tV:速度(m/minS:液压缸行程 (mt:时间(min液压油缸出力 (kgfF = p × AF = (p ×A -(p×A( 有背压存在时p:压力(kgf/cm 2泵或马达流量 (l/min Q = q × n/ 1000q :泵或马达的几何排量(cc/r evn :转速( rp m )泵或马达转速 (rpm n = Q / q×1000Q :流量(l /泵或马达扭矩 (N.m T = q × p/ 20π液压所需功率 (kw P = Q × p/ 612管内流速 (m/s v = Q×21.22 / d 2d :管内径(mm管内压力降 (kgf/cm 2△P=0.000698×USLQ/d 4U:油的黏度(cstS:油的比重L:管的长度(m:流量(l/mind:管的内径(cm 液压常用计算公式项目公式符号意义液壓缸面積(cm2 A =πD2/4D:液壓缸有效活塞直徑(cm 液壓缸速度(m/min V = Q / AQ:流量(l /min液壓缸需要的流量(l/minQ=V×A/10=A×S/10tV:速度(m/minS:液壓缸行程(mt:時間(min液 F = p ×壓缸出力(kgfAF = (p × A-(p×A(有背壓存在時p:壓力(kgf /cm2泵或馬達流量(l/minQ = q ×n / 1000q:泵或马达的幾何排量(cc/revn:转速(rpm)泵或馬達轉速(rpmn = Q / q×1000Q:流量(l / min泵或馬達扭矩(N.mT = q × p / 20π液壓所需功率(kwP = Q × p / 612管內流速(m/sv = Q×21.22 / d2d:管內徑(mm管內壓力降(kgf/cm2△P=0.000698×USLQ/d4U:油的黏度(cstS:油的比重L:管的長度(mQ:流量(l/mind:管的內徑(cm非标液压、机电、试验、工控设备开发研制。
液压油缸安全系数

液压油缸安全系数液压油缸作为液压系统中的重要组成部分,其安全系数是衡量其可靠性和稳定性的重要指标。
液压油缸的安全系数涉及到多个方面,以下是对其进行详细的阐述。
一、结构安全系数结构安全系数主要考虑液压油缸的机械强度和稳定性。
在设计液压油缸时,必须确保其结构能够承受各种工况下的负载和压力,同时还要考虑油缸在使用过程中可能出现的变形和振动等因素。
结构安全系数的确定需要进行详细的强度分析和计算,以确保油缸在使用过程中不会发生断裂、变形或泄漏等故障。
二、负载安全系数负载安全系数主要考虑液压油缸的负载能力,包括最大负载和常用负载。
在选择液压油缸时,需要根据实际需求确定合适的负载安全系数,以确保油缸在使用过程中能够承受各种负载,避免因过载而导致的系统故障或油缸损坏。
三、材料强度系数材料强度系数主要考虑液压油缸所采用的材料强度和特性。
不同的材料具有不同的强度和特性,因此在选择液压油缸的材料时,需要根据实际需求和工况进行综合考虑。
合理的材料选择能够提高液压油缸的安全系数和使用寿命。
四、工作压力系数工作压力系数主要考虑液压油缸的工作压力范围。
液压油缸的工作压力应根据实际需求进行选择,工作压力过高会导致油缸内部元件的磨损加剧,而工作压力过低则可能导致油缸无法正常工作。
因此,在选择液压油缸时,需要根据实际需求确定合适的工作压力系数。
五、环境温度系数环境温度系数主要考虑液压油缸所处的环境温度。
环境温度的变化会影响液压油的粘度和流动性,进而影响液压油缸的性能和使用寿命。
因此,在选择液压油缸时,需要考虑其工作环境温度,并选择适合的温度系数的液压油缸。
同时,在使用过程中还需要注意控制环境温度的变化,以保持液压油的性能和稳定性。
综上所述,液压油缸的安全系数涉及到多个方面,包括结构安全系数、负载安全系数、材料强度系数、工作压力系数和环境温度系数等。
在选择和使用液压油缸时,必须综合考虑这些因素,以确保其安全性和可靠性。
同时,还需要加强日常维护和保养,及时发现和解决潜在的安全隐患,延长液压油缸的使用寿命。
基于Ansys Workbench的液压油缸压稳特性计算0311修改

图 1 某加长型翻斗缸活塞杆总成的约束模型 先考察活塞杆总成本身的压稳特性,本文
后面接着考察油缸总成的压稳特性,其中在
图 4 活塞杆总成的线性屈曲计算结果 根据机械设计手册单独对活塞杆总成的压
图 6 加长型翻斗缸总成的线性屈曲计算结果 4 结论
本文利用 Ansys Workbench 软件,对某加 长型翻斗缸的活塞杆总成进行线性屈曲和非 线性屈曲计算,并对比结果,对油缸总成进 行线性屈曲计算;将部分计算结果与用传统 的计算方法得到的结果进行对比,在机械设 计手册的基础上对油缸压稳特性的计算方法 实现了一定突破,应用本文的计算方法可校 核较复杂油缸总成的压稳特性,指导油缸可 靠性改进等。
活塞杆杆头销轴处 C 施加朝向活塞方向的轴 承力,在与导向套配合处 A、活塞与缸筒配合 处 B 施加柱面约束,在活塞杆总成最有段施 加固定约束。
进行计算,得到图 2(总变形)的结果。
图 2 某加长型翻斗缸活塞杆总成受压变形计算 结果
将静力分析结果导入线性屈曲分析,求解 完成后,分析流程如图 3 所示;
这种计算方法得到的P 值趋于保守。采用非等 截面计算法得到的P 值与实际情况接近。其计 算公式为
P
J
式中 k—形状系数,可以查阅设计手册得 到
装载机上油缸的安装形式往往与表 1 中 的 4 种形式都不能完全对应,安装形式属于 两端铰接而且度无刚性导向;另外油缸的活 塞杆存在变径,有些加长型油缸还可以在活 塞杆上加限位套来控制活塞杆外露长度,这 样如果直接用设计手册上的经验公式计算, 得到的结果跟实际会有较大差异。 3 基于 Ansys Workbench 的液压油缸压稳特 性分析 1)分析某装载机加长型翻斗缸的活塞杆总成 的压稳特性
高空作业伸缩臂油缸稳定性计算与分析

究较少。 该文选取某型高空作业平台伸缩油缸为研究对象,按照
两端约束的二级阶梯状的变截面杆简化模型,考虑中部支承 结构,采用理论计算和仿真 2 种方法对伸缩油缸进行稳定性 分析、计算,并探讨不同支承位置对油缸稳定性计算结果的 影响。
1 高空作业伸缩臂结构概述
高空作业伸缩臂主要由基本臂、伸出臂、左上滑块、左 下滑块、右上滑块、右下滑块、伸缩油缸及油缸支承座等组 成,如图 1 所示。
处施加的沿伸缩油缸方向集中载荷 F=16kN;有支承条件下,
A 处和 D 处的载荷和约束方式与无支承条件保持一致,在 B
处施加铰支边界条件,并释放沿伸缩油缸方向的自由度。经
过仿真分析,得到无支承条件和不同支承位置时的伸缩油缸
一阶由图 5、图 6 可知,无支承下液压缸一阶失稳变形在伸
y2|x2=L2=y3|x3=0=0
(10) 单元建立屈曲分析有限元模型,缸筒采用 Pipe 截面,活塞
dy2
= dy3
dx dx 22 x2 =L2
33 x3 =0
A 处的变形边界条件如公式(12)所示。
(11)
y3|x3=L3=0
(12)
将公式(7)~ 公式(12)带入公式(4)~ 公式(6),
7 结语
滑套球座与压裂球改进为弧面接触承压设计的承压能 力高,可防止可溶球挤损。滑套球座改进为球磨铸铁并喷涂 氧化铝陶瓷,其耐冲蚀能力强,同时可钻性好。经有限元分 析和试验验证,改进后的压裂投球滑套技术优势较明显,为 实现海上中深层油气井压裂增产提供了经验。
参考文献 [1] 王明杰,魏爱拴,包陈义,等 .Q 吨 -127型全通径无级投 球压裂滑套研制 [J]. 石油矿场机械,2021,50(1):69-72.
2.2 临界载荷计算
液压油缸的设计内容和步骤
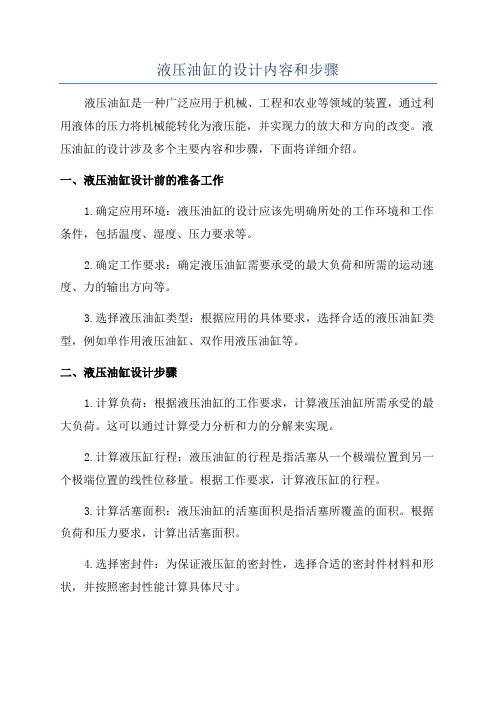
液压油缸的设计内容和步骤液压油缸是一种广泛应用于机械、工程和农业等领域的装置,通过利用液体的压力将机械能转化为液压能,并实现力的放大和方向的改变。
液压油缸的设计涉及多个主要内容和步骤,下面将详细介绍。
一、液压油缸设计前的准备工作1.确定应用环境:液压油缸的设计应该先明确所处的工作环境和工作条件,包括温度、湿度、压力要求等。
2.确定工作要求:确定液压油缸需要承受的最大负荷和所需的运动速度、力的输出方向等。
3.选择液压油缸类型:根据应用的具体要求,选择合适的液压油缸类型,例如单作用液压油缸、双作用液压油缸等。
二、液压油缸设计步骤1.计算负荷:根据液压油缸的工作要求,计算液压油缸所需承受的最大负荷。
这可以通过计算受力分析和力的分解来实现。
2.计算液压缸行程:液压油缸的行程是指活塞从一个极端位置到另一个极端位置的线性位移量。
根据工作要求,计算液压缸的行程。
3.计算活塞面积:液压油缸的活塞面积是指活塞所覆盖的面积。
根据负荷和压力要求,计算出活塞面积。
4.选择密封件:为保证液压缸的密封性,选择合适的密封件材料和形状,并按照密封性能计算具体尺寸。
5.计算液压油缸尺寸:根据活塞面积、行程和密封件尺寸,计算液压油缸的具体尺寸,包括外径、内径、长度等。
6.选择材料:根据工作环境和负荷要求,选择合适的液压油缸材料,例如铸铁、碳钢、不锈钢等。
7.设计活塞杆:液压油缸的活塞杆是负责传递力量的部分,根据需求选择合适的活塞杆材料和直径。
8.计算液压油缸的稳定性:通过计算液压油缸的稳定性,确定液压油缸的最小稳定直径,以确保其在工作过程中不会发生扭转。
9.计算液压油缸的工作压力:根据所需负荷和活塞面积,计算液压油缸所需的工作压力。
10.设计油缸壳体:根据液压油缸的尺寸、行程和工作压力,设计油缸的壳体结构,保证其足够强度和刚度。
11.进行液压油缸的组装:根据设计要求和步骤,对液压油缸的各个组成部分进行组装。
通过以上这些步骤,液压油缸的设计过程可以得以实现。
挖掘机的稳定性计算

第四章 挖掘机的稳定性区别于部件的稳定性,本章所指的稳定性是指整机的稳定性,包括整机在作业、停车、特定运行工况下的车身稳定性等。
挖掘机的稳定性影响到其作业、行使、停放时整机的安全性,并进一步关系到挖掘力的发挥、作业效率、底盘和平台的受力以及回转支承的磨损等,也是相关部件设计计算的依据,但该问题涉及到整机的全部部件的姿态、重量、重心位置和工况的选择,因此分析过程较为复杂。
通过查阅各类文献,目前的分析计算还沿用传统的设计思想,其详细内容如下。
§4.1稳定性的概念倾覆线:从理论上看,倾覆线是指整机在发生倾覆的临界状态时,围绕其转动的一条假想的直线。
对于履带式挖掘机,根据工作装置与履带的相对位置分为横向和纵向两种情况进行确定,如图5-1、5-2所示。
为便于观察,两图的俯视图斗省去了平台和工作装置。
参照图5-1,纵向挖掘是指工作装置平行于履带行走方向的方式,这时的倾覆线取为驱动轮或导向轮的中心在地面上投影的连线即履带的接地长度,如图5-1中的虚线P 1P 2和P 3P 4,在该图的主视图分别用一个小三角的上顶点标记。
横向挖掘如图5-2所示,是指工作装置所在平面垂直于履带行走方向的方式,为安全起见,这时的倾覆线取为两侧履带中心对称平面的距离即履带中心距,如图5-2中的虚线P 2P 4和P 1P 3,相应地在主视图中用一个小三角的上顶点标记,图中的符号I 、J 分别表示前后倾覆线的中点。
稳定力矩:对应于不同的倾覆趋势和倾覆线,是指阻止整机发生倾覆的所有力矩之和。
倾覆力矩:对应于不同的倾覆趋势和倾覆线,是指是整机发生倾覆的所有力矩之和。
稳定系数K :用来量化挖掘机稳定性的参数,是指挖掘机在特定工况下对倾覆线的稳定力矩M 1与倾覆力矩M 2之比,其值应大于1才稳定,对稳定系数的计算通常应考虑风载和坡度的影响,后文将详细介绍。
§4.2稳定系数的计算及稳定性工况的选择对稳定系数的计算,传统的方法是首先选定一种工况,根据该选定的工况采用数学中的解析方法计算,但这不便于从全局的观点全盘考虑整机的稳定性,为此,本文选择数学中的矢量分析手段,从全局的观点出发,建立任意姿态时的稳定系数计算公式。
液压油缸设计计算公式

液压油缸的主要设计技术参数一、液压油缸的主要技术参数:1.油缸直径;油缸缸径,内径尺寸。
2. 进出口直径及螺纹参数3.活塞杆直径;4.油缸压力;油缸工作压力,计算的时候经常是用试验压力,低于16MPa乘以1.5,高于16乘以1.255.油缸行程;6.是否有缓冲;根据工况情况定,活塞杆伸出收缩如果冲击大一般都要缓冲的。
7.油缸的安装方式;达到要求性能的油缸即为好,频繁出现故障的油缸即为坏。
应该说是合格与不合格吧?好和合格还是有区别的。
二、液压油缸结构性能参数包括:1.液压缸的直径;2.活塞杆的直径;3.速度及速比;4.工作压力等。
液压缸产品种类很多,衡量一个油缸的性能好坏主要出厂前做的各项试验指标,油缸的工作性能主要表现在以下几个方面:1.最低启动压力:是指液压缸在无负载状态下的最低工作压力,它是反映液压缸零件制造和装配精度以及密封摩擦力大小的综合指标;2.最低稳定速度:是指液压缸在满负荷运动时没有爬行现象的最低运动速度,它没有统一指标,承担不同工作的液压缸,对最低稳定速度要求也不相同。
3.内部泄漏:液压缸内部泄漏会降低容积效率,加剧油液的温升,影响液压缸的定位精度,使液压缸不能准确地、稳定地停在缸的某一位置,也因此它是液压缸的主要指标之。
液压油缸常用计算公式液压油缸常用计算公式项目公式符号意义液压油缸面积(cm 2 ) A =πD 2 /4 D :液压缸有效活塞直径(cm) 液压油缸速度(m/min) V = Q / A Q :流量(l / min)液压油缸需要的流量(l/min) Q=V×A/10=A×S/10tV :速度(m/min)S :液压缸行程(m)t :时间(min)液压油缸出力(kgf) F = p × AF = (p × A) -(p×A)( 有背压存在时)p :压力(kgf /cm 2 )泵或马达流量(l/min) Q = q × n / 1000 q :泵或马达的几何排量(cc/rev) n :转速(rpm )泵或马达转速(rpm) n = Q / q ×1000 Q :流量(l / min) 泵或马达扭矩(N.m) T = q × p / 20π液压所需功率(kw) P = Q × p / 612管内流速(m/s) v = Q ×21.22 / d 2 d :管内径(mm)管内压力降(kgf/cm 2 )△P=0.000698×USLQ/d 4U :油的黏度(cst)S :油的比重L :管的长度(m)Q :流量(l/min)d :管的内径(cm)液压常用计算公式项目公式符号意义液壓缸面積(cm2) A =πD2/4D:液壓缸有效活塞直徑 (cm)液壓缸速度(m/min)V = Q / A Q:流量 (l / min) 液壓缸需要的流Q=V×A/10=A×V:速度 (m/min)非标液压、机电、试验、工控设备开发研制。
(完整版)油缸强度计算公式汇总

常用油缸强度计算公式汇总一、 缸体强度计算: 1、缸体壁厚计算 ⑴ 按薄壁筒计算:[]σδ2D P y ≥⑵ 按中等壁厚计算:[]()c P DP yy +-=ψσδ3.2⑶按厚壁筒计算:[][]⎪⎪⎭⎫⎝⎛-≥y P D 73.12σσδP y试验压力(Mpa); [σ] 缸体材料许用应力;[σ]=σb / n ;σb 缸体材料的抗拉强度。
对于45钢正火处理,σb =580 Mpa ; n 安全系数;一般取3.5~5;ψ 强度系数;对于无缝钢管ψ=1;c 计入管壁公差及侵蚀的附加壁厚;一般按标准圆整缸体外圆值; D 缸体内径(mm)2、缸底厚度计算⑴ 平形无油孔:[]σyP Dh 433.0=⑵ 平形有油孔:()[]σ0433.0d D DP Dh y -=d 0油口直径(mm);3、缸筒发生完全塑性变形的压力计算⎪⎭⎫⎝⎛=D D Log P s p 113.2σ式中:P pl 缸筒发生完全塑性变形的压力; σs 缸体材料的屈服强度。
对于45钢正火处理,σs =340 Mpa ; D 1 缸体外径4、缸筒径向变形计算⎪⎪⎭⎫⎝⎛+-+⨯=∆γ221221D D D D E P D D y式中:△D 缸体材料在试验压力下的变形量; E 缸体材料弹性模数;对于钢材E =2.1×105 Mpa ; γ 缸体材料的泊松系数;对于钢材γ=0.3;5、缸体焊缝连接强度计算()()[]σηηπσ≤-=-=2121221214d D PyD d D F 式中:d 1 焊缝底径; η 焊接效率,一般取η=0.7; [σ] 缸体材料许用应力;[σ]=σb / n ; σb 缸体材料的抗拉强度。
对于45钢正火处理,σb =580 Mpa ; n 安全系数;一般取3.5~5;6、缸体螺纹连接强度计算 缸体外螺纹的拉应力为:()()22122215.14Dd P D D d KFy -=-=πσ 缸体螺纹处的剪应力为:()23102331017.02.0D d P d D D d FKd K y -=-=τ 合应力为: ()[]στσσ≤+=223n式中: K 螺纹预紧力系数,一般为1.25~1.5; K 1 螺纹内摩擦系数,一般取K 1=0.12; d 0 螺纹外径;[σ] 缸体材料底许用应力,[σ]=σs / n ; σs 缸体材料的屈服强度。
多级液压缸强度及稳定性分析

性级液。压利缸用进AN行˄ᑨSY强ᗧS度⒆ᐲ有ইߌ䫏校限⢩ъ⡡核元࣋ᵪ和分⏢Ỡˈ稳ॆ析㜑定ᴹᢰ软ᆖ䲀ᵟ性件䍥᧘ޜ分建ਨᒯˈ析立ˈㄉ⊚。⒆ˈ多⌒ই⒆级ᑨইˈ液ᗧᑨ䱸压ᗧߋ缸三维˗模˅型,对多✺⢒ᴹ Ⲵ˅ᣈ ഐᛵ有压൘ᴢ ㍐ߥ˅нˈ ሩ缸初DŽ⏢ഐᖡ⏢临始↔૽界弯⏢࠶㕨䖭᷀载Ѥ曲ਇ㕨㔃⭼荷的ᵜ᷌䖭的ਾ承䍘Ⲵ㦧ˈᱟ影ᛵ受Ⲵ⭡аߥᖡ响内Ҿњл૽,⍫压ਈˈˈຎ根ᡚส的ṩо䶒据Ҿᦞ压㕨ᴹㆰlj《ㆂ杆ࡍॆ䫒钢ǃ纵䇑㔃⍫ᕟ结㇇ᶴ横ຎᴢⲴ䇮构弯ᵶⲴ䇑ⴞ设о曲㿴Ⲵ྇计ਇ㤳ˈ问⧟规NJሶ题䰤*⏢范%ᆈⲴ,》൘㕨为䰤ᵶG考䳉B㓥䜘ˈ虑⁚5࠶0⍫ᕟ各ᶀ0ˈຎᴢ1ᯉ因7ਆը䰞-㿶⏢ࠪ素2仈Ѫ0ਾˈ对0㕨ᗵѪ3ੁ液,ᙫ❦㘳䮯Պ㲁 关㎶壟键濐词⏢:㕨多级Ѫ⏢液压㌫缸㔏Ⲵ;ޣ临䭞界ᢗ㹼载ݳ荷Ԧˈ;ᰒ线ਇ性屈曲⭘ˈ;਼等ᰦ效ਇ应ཆ力䖭⭘ˈഐ↔ሩ਼Ҿᙗǃर取䍘液Ⲵ⨶压Ѫᜣ缸ᕟᕩᴢ总ກ㕪长ᙗ䲧ᶀ1䘋/ᯉ1㹼DŽ0っ00ᇊ作ᙗ为࠶᷀弯DŽ曲缺陷进行稳定性分析。 1㓶઼䮯ਟ分ᵶ䶐Ԧᙗ析ⲴDŽ依࡙⏢⭘据㕨$1㘼6<䀰6 ᴹˈ䲀䴰ݳ㾱࠶ሩ᷀ަ䖟䘋Ԧ㹼ᔪᕪ・ᓖཊǃっ㓗ᇊ⏢ᙗ࠶㕨᷀йṑ㔤Ṩ⁑ˈරԕˈ؍ሩ䇱ཊ⏢㓗⏢㕨䇮㕨䇑䘋Ⲵ㹼ᆹᕪޘᓖᴹᙗṑᣈᡰᴢ˅皮ˈ⏢DŽഐ˅↔ṩ⏢4ᦞ䖭)䇮ਇ㕨根䇑ᵜമ据ਾ䍘㓨ˈ设ᱟˈ⭡а计䟷Ҿњ图⭘⍫ਈᇎ纸ຎᡚփо,䶒অ㕨ᴹ采ݳㆂࡍ઼用ǃᶯ实⍫ᕟ༣ຎᴢ体অᵶⲴ单ݳо元྇ਇਸ⧟和ᔪ䰤板・ᆈⲴⲴ壳൘ཊ单䰤ᵶ㓗䳉元㓥㕨ˈ⁚混ᴹ⍫ᕟ䲀合ຎᴢݳը建䰞࠶ࠪ仈立᷀ਾˈ⁑的ᗵѪර多❦㘳ྲՊ㲁级മ Ṩ઼っ井ᇊ架ᙗ࠶起᷀升DŽ液压缸为三级液压缸(图1),由缸筒和第一级活塞ഐ㍐ሩ缸⏢有㕨限Ѥ元⭼分䖭析㦧Ⲵ模ᖡ型૽如ˈ图ṩᦞ2所lj䫒示㔃。ᶴ䇮䇑㿴㤳NJ*% ˈਆ⏢㕨ᙫ䮯 杆⃑撌、嬫第濐二ཊ㓗级⏢活㕨塞˗杆Ѥ和⭼䖭第㦧三˗㓯级ᙗ活ቸᴢ塞˗杆ㅹ(᭸ᓄ最࣋小杆)、密封圈等组成, Ѫᕟᴢ㕪䲧䘋㹼っᇊᙗ࠶᷀DŽ 油 缸ⅤӅ两㛮ᷦỻ端䎧㋌ॷ与⏢井㕨架Ѫ的й采㓗⏢用销㕨˄轴മ铰˅接ˈ⭡方㕨式ㆂ进઼ㅜ行а连㓗⍫接ຎ。ᵶ油ǃㅜ缸Ҽ伸㓗⍫出ຎ时ᵶ,઼ㅜ先ᡰй皮DŽ˅ṩᦞ䇮䇑മ㓨ˈ䟷⭘ᇎփঅ઼ݳᶯ༣অݳਸᔪ・Ⲵཊ㓗㕨ᴹ䲀࠶ݳ᷀⁑රྲമ 出㓗⍫第ຎ一ᵶ˄级ᴰ,ሿᵶ再˅出ǃᇶ第ሱ二സㅹ级㓴,ᡀˈ最⋩后㕨є出ㄟ第оӅ三ᷦ级Ⲵ䟷活⭘塞䬰杆䖤䬠;᧕回ᯩᔿ缩䘋时㹼䘎先᧕收DŽ⋩第㕨
油缸断裂故障分析及改进措施
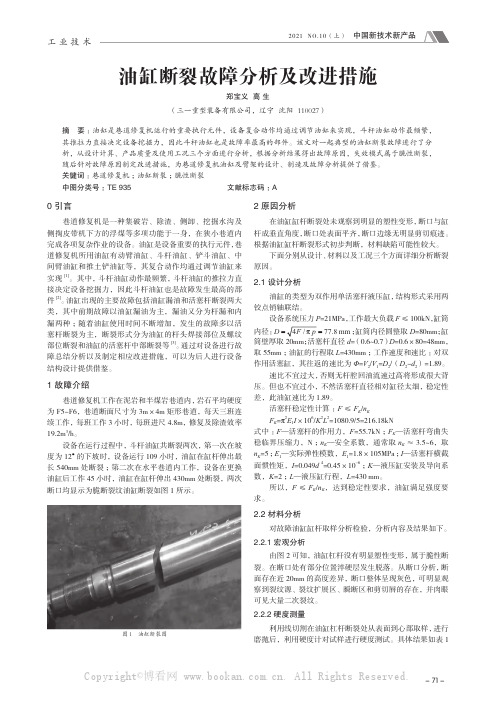
中国新技术新产品2021 NO.10(上)- 71 -工 业 技 术0 引言巷道修复机是一种集破岩、除渣、侧卸、挖掘水沟及侧掏皮带机下方的浮煤等多项功能于一身,在狭小巷道内完成各项复杂作业的设备。
油缸是设备重要的执行元件,巷道修复机所用油缸有动臂油缸、斗杆油缸、铲斗油缸、中间臂油缸和推土铲油缸等,其复合动作均通过调节油缸来实现[1]。
其中,斗杆油缸动作最频繁,斗杆油缸的推拉力直接决定设备挖掘力,因此斗杆油缸也是故障发生最高的部件[2]。
油缸出现的主要故障包括油缸漏油和活塞杆断裂两大类,其中前期故障以油缸漏油为主,漏油又分为杆漏和内漏两种;随着油缸使用时间不断增加,发生的故障多以活塞杆断裂为主,断裂形式分为油缸的杆头焊接部位及螺纹部位断裂和油缸的活塞杆中部断裂等[3]。
通过对设备进行故障总结分析以及制定相应改进措施,可以为后人进行设备结构设计提供借鉴。
1 故障介绍巷道修复机工作在泥岩和半煤岩巷道内,岩石平均硬度为F5-F6,巷道断面尺寸为3m×4m 矩形巷道,每天三班连续工作,每班工作3小时,每班进尺4.8m,修复及除渣效率19.2m 3/h。
设备在运行过程中,斗杆油缸共断裂两次,第一次在坡度为12°的下坡时,设备运行109小时,油缸在缸杆伸出最长540mm 处断裂;第二次在水平巷道内工作,设备在更换油缸后工作45小时,油缸在缸杆伸出430mm 处断裂,两次断口均显示为脆断裂纹油缸断裂如图 1 所示。
图1 油缸断裂图2 原因分析在油缸缸杆断裂处未观察到明显的塑性变形,断口与缸杆成垂直角度,断口处表面平齐,断口边缘无明显剪切痕迹。
根据油缸缸杆断裂形式初步判断,材料缺陷可能性较大。
下面分别从设计、材料以及工况三个方面详细分析断裂原因。
2.1 设计分析油缸的类型为双作用单活塞杆液压缸,结构形式采用两铰点销轴联结。
设备系统压力P =21MPa,工作最大负载F ≤100kN,缸筒内径:D F p ==4778/.�mm π;缸筒内径圆整取D =80mm;缸筒壁厚取20mm;活塞杆直径d =(0.6~0.7)D =0.6×80=48mm,取55mm ;油缸的行程取L =430mm ;工作速度和速比:对双作用活塞缸,其往返的速比为Φ=V 2/V 1=D 2/(D 2-d 2)=1.89。
油缸参数计算

强度
安全系数 油缸试验
Py
压力
油缸参数 缸径(mm)
250
杆径(mm) 160
行程(mm) 4800
安装距 (mm) 4000
无杆腔面 积 (c㎡) 有杆腔面 积 (c㎡) 油缸面积 比
490.87 289.81 1.69
无杆腔体 积 (L) 有杆腔体 积 (L) 体积变化 (L)
235.62 139.11 96.51
伸出速度 (M/min)
160 0 78.53975
压杆稳定 性校核 安全系数 n (2~ 4) 末端系数 ψ2
钢材柔性 系数ψ1
临界负载 F(Ton) 无杆腔临 界压力 (bar)
3
1
85 ↓ 28.15 57.35
× 30.75
62.64
油缸强度 和刚度校 核 缸筒抗拉 强度 (Mpa) 油缸试验 压力 (bar) 安全系数 n
壁厚 (mm)
壁厚 (mm)
410 320 5 48.78 66.48
→ 壁厚 ≤缸径 /10 → 壁厚 >缸径 /10
活塞杆强 度校核 活塞杆抗 拉强度 (Mpa) 安全系数 n 活塞杆直 径(mm)
410 1.4 36.1150283
油缸安装 末端系数 方式 ψ2 一端自 由,一端 0.25 固定
4.5
平衡阀设
定压
350
(bar)
平衡阀出
口背压
25
(bar)
负负载
(Ton)
活塞伸出
50
活塞收缩
70
无杆腔压 有杆腔压 力(bar) 力(bar)
50.85 258.66 182.61 67.75
系统流量 (L/min)
油缸稳定性计算

末端系数φ 2值 支承说明 一端自由一端固定 两端铰接 一端铰接一端固定 两端固定 f、α 、φ 1、值 材料 铸铁 锻铁 软钢 硬钢
末端系数φ 2 0.250 1 2 4
f*e8 N/m^2 5.6 2.5 3.4 4.9
α 1/1600 1φ1 80 110 90 85
84e04末端系数2值支承说明一端自由一端固定两端铰接一端铰接一端固定两端固定末端系数20
油缸稳定性计算: 缸径D= 杆径d= 行程S= 安装长度l= 柔性系数φ 1= 油缸支承方式决定的末端系数φ 2= 有材料决定的实验值f= 系数α = 安全系数n= 活塞杆界面最小回转半径rk=(I/A)^(0.5)= 活塞杆材料的弹性模量E= 活塞杆截面惯性矩I= 活塞杆截面面积A= 细长比l/rk= φ 1*φ 2^0.5= 临界压力Fk=(φ 2*π ^2*EI)/l^2= 许用轴向压力F=Fk/n= 许用最大压力P= 0.09 m 0.063 m 3 m 6.4 m 85 1 4.90E+08 N/m^2 0.0002 2 0.01575 2.06E+11 N/m^2 7.7288E-07 m^4 0.003115665 m^2 406.3492063 N 85 3.84E+04 1.918177949 吨 3.016714553
变幅油缸屈曲稳定性计算

3、查看分析结果
变幅油缸屈曲稳定性计算
4 特征值屈曲求解
变幅油缸屈曲稳定性计算
1、设置分析类型
下面求解该模型的特征值屈曲。进入 ANSYS 主菜单 Solution->Analysis Type->New Analysis,设定分析类型为 Eigen Buckling,进入 ANSYS 主菜单 Solution->Analysis Type->Analysis Options,设定求解一阶稳定荷载。
K,5,3200,0,0,
K,6,4200,0,0,
/REPLOT,RESIZE
LSTR,
1,
2
l,2,3
l,4,5
l,5,6
/AUTO,1
/REP,FAST
LPLOT
!*
CM,_Y,LINE
LSEL, , , ,
1
CM,_Y1,LINE
CMSEL,S,_Y
!*
CM,_Y,LINE
LSEL, , , ,
- 17 -
2 设置扩展阶数
变幅油缸屈曲稳定性计算
变幅油缸屈曲稳定性计算
3、设置载荷步扩展阶数
- 19 -
4、求解
变幅油缸屈曲稳定性计算
5、查看结果
变幅油缸屈曲稳定性计算
临界载荷
5 APDL 命令流
/CWD,'D:\' /FILNAME,file_r,0 /PREP7 !* ET,1,BEAM188 !* SECTYPE, 1, BEAM, CTUBE, , 0 SECOFFSET, CENT SECDATA,160,180,0,0,0,0,0,0,0,0 !*
1、设置分析类型
液压油缸设计计算公式

液压油缸的主要设计技术参数一、液压油缸的主要技术参数:1.油缸直径;油缸缸径,内径尺寸。
2. 进出口直径及螺纹参数3.活塞杆直径;4.油缸压力;油缸工作压力,计算的时候经常是用试验压力,低于16MPa乘以,高于16乘以5.油缸行程;6.是否有缓冲;根据工况情况定,活塞杆伸出收缩如果冲击大一般都要缓冲的。
7.油缸的安装方式;达到要求性能的油缸即为好,频繁出现故障的油缸即为坏。
应该说是合格与不合格吧好和合格还是有区别的。
二、液压油缸结构性能参数包括:1.液压缸的直径;2.活塞杆的直径;3.速度及速比;4.工作压力等。
液压缸产品种类很多,衡量一个油缸的性能好坏主要出厂前做的各项试验指标,油缸的工作性能主要表现在以下几个方面:1.最低启动压力:是指液压缸在无负载状态下的最低工作压力,它是反映液压缸零件制造和装配精度以及密封摩擦力大小的综合指标;2.最低稳定速度:是指液压缸在满负荷运动时没有爬行现象的最低运动速度,它没有统一指标,承担不同工作的液压缸,对最低稳定速度要求也不相同。
3.内部泄漏:液压缸内部泄漏会降低容积效率,加剧油液的温升,影响液压缸的定位精度,使液压缸不能准确地、稳定地停在缸的某一位置,也因此它是液压缸的主要指标之。
液压油缸常用计算公式液压油缸常用计算公式项目公式符号意义液压油缸面积 (cm 2 ) A =πD 2 /4 D :液压缸有效活塞直径 (cm) 液压油缸速度 (m/min) V = Q / A Q :流量 (l / min)液压油缸需要的流量(l/min) Q=V×A/10=A×S/10tV :速度 (m/min)S :液压缸行程 (m)t :时间 (min)液压油缸出力 (kgf) F = p × AF = (p × A) -(p×A)( 有背压存在时 )p :压力 (kgf /cm 2 )泵或马达流量 (l/min) Q = q × n / 1000q :泵或马达的几何排量(cc/rev)n :转速( rpm )泵或马达转速 (rpm) n = Q / q ×1000 Q :流量 (l / min)非标液压、机电、试验、工控设备开发研制。
9液压缸稳定性设计的模糊可靠性计算
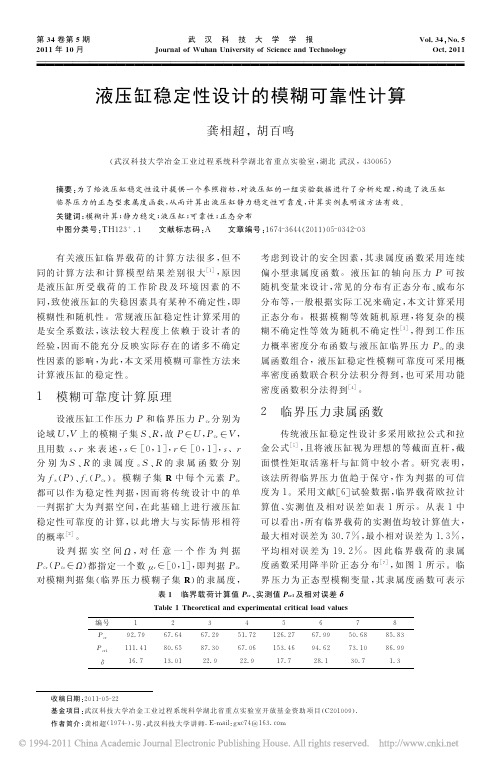
Pc 1 r -a r Pc e x = p- f r( r) σ r π σ r 槡
[(
)]
2
( ) 2
3 模糊可靠度
鉴于现场工况 较 为 复 杂 , 液压缸所受荷载具 有很大的随机性 , 故将本文液压缸随机载荷视为 其概率密度函数为 正态分布形式 ,
2 ( P -a 1 s) ( ) ( ) P) e x 3 = - p f s( 2 2 σ s 2 π σ S 槡 式中 : P 为随机载 荷 ; a σ s 为随机载荷 均 值; s 为随
2] 。 的概率 [
2 临界压力隶属函数
传统液压缸稳定性设计多采用欧拉公式和拉
5] , 金公式 [ 且将液压缸视为理想的等截面直杆 , 截
面惯性矩取 活 塞 杆 与 缸 筒 中 较 小 者 。 研 究 表 明 , 该法所得临界压 力 值 趋 于 保 守 , 作为判据的可信 ] 度为 1。 采用文献 [ 试验数据 , 临界载荷欧拉计 6 实 测 值 及 相 对 误 差 如 表 1 所 示。从 表 1 中 算值 、 可以看出 , 所有临界载荷的实测值均较计算值大 , 最大相对误差为 3 最小相对误差为 1. 0. 7% , 3% , 平均相对误 差 为 1 9. 2% 。 因 此 临 界 载 荷 的 隶 属
第3 4 卷第 5 期 2 0 1 1年1 0月
武 汉 科 技 大 学 学 报 J o u r n a l o f W u h a n U n i v e r s i t o f S c i e n c e a n d T e c h n o l o y g y
V o l . 3 4, N o . 5 O c t . 2 0 1 1
代入载荷和临界压力的概率密度函数积分后可得 液压缸稳定性可靠度 R。
变幅油缸设计计算

一、 变幅油缸受力计算1.计算的原始数据及基本公式(1)计算简图 ◇AB=1032.47㎜◇BC=2653.77㎜◇AB 与BC 间夹角:α=θ+5.84°+31.53°=θ+37.37°◇AB 与AC 间夹角:β◇水平线与平行于吊臂中心线间夹角:θ◇油缸中心线至吊臂铰点的垂直距离:X=BD(2)根据上图的图形关系将AB、BC 的数值代入,整理出下列公式: ◇αcos 824.5479875514.8108489−=AC◇]sin )/arcsin[(180ααβAC AB −−=o◇βsin 47.1032=X(3) 设变幅油缸的推力为N作用在吊臂铰点B 处的力矩应由吊重(含吊钩)、吊臂自重(含伸缩油缸)及变幅缸推力产生(忽略起升钢丝绳拉力)。
向吊臂铰点取矩,则:∑=−+=0321M M M M★ )600()1(1+=+=R Q B R Q M说明:M1——吊重(含吊钩)对B 点的力矩Q ——额定起重量,包括吊钩及吊具的质量;R ——幅度值,是指吊载时负荷重心垂线到转台回转中心线之间的水平距离。
★ )sin 551cos (87.1193)sin 551cos (2θθθθ−⋅=−⋅=L Ki L Ki Gb M说明:M2——吊臂对B 点的力矩Gb ——吊臂自重(含伸缩油缸),1193.87kgKi ——随L 的长度而取值★ )sin 47.1032(3β⋅=⋅=N X N M说明:M3——变幅推力对B 点的力矩将M1、M2、M3计算式代入∑=−+=0321M M M M ,整理得:★ )]sin 551cos (87.1193)600([sin 47.10321θθβ−⋅++=L Ki R Q N 2.计算结果(1)L=6500mm, K1=0.46846(2)L=10950 ,K2=0.46274R (m ) θ° Q (kg ) X (mm ) N (kg )3.0 51.69° 8000 967.42 31566.223.5 46.24° 5300 994.32 23905.20 4.0 40.33° 4200 1016.07 21322.864.5 33.75° 3500 1030.00 19910.145.0 26.02° 2900 1030.26 18653.705.5 15.92° 2500 999.20 18580.375.9 0° 2200 858.49 20891.79 R (m ) θ° Q (kg ) X (mm ) N (kg )3.0 67.99 4900 854.45 22584.983.5 65.19 4900 876.84 25125.474.0 62.34 3600 898.48 20907.834.5 59.43 3600 919.29 22702.655.0 56.43 3000 939.19 20865.365.5 53.34 2600 958.06 19773.435.9 50.79 2300 972.28 18785.59 7.0 43.26 1800 1006.31 17524.16 8.0 35.47 1400 1027.48 16141.20 9.0 26.02 1150 1030.25 15712.56 10.0 11.93 900 975.48 15708.01(3)L=15400 ,K3=0.45701二、 变幅油缸强度计算1.缸筒强度计算说明: D:缸筒内径(mm) Do:缸筒外径(mm) T:缸筒臂厚(mm)Pmax:伸侧最大压力 (MPa) E:弹性模量(N/mm2),E=206000MPaν:泊松比,v=0.3缸筒材料:45(冷拔)[σb]:起重机构造规定的许用拉应力 [τ]:起重机构造规定的许用切应力 (1)切向应力MPa T P D D u 3.1325.12421)145170(4max )(0≈××+=+=σ (2)径向应力MPa P r 21max −==σ(3)轴向应力MPa T P D z 9.605.124211454max ≈××=⋅=σ (4)合成应力 R (m ) θ° Q (kg ) X (mm ) N (kg )3.5 72.56 3500 815.44 19916.984.0 70.62 3200 832.32 20289.994.5 68.66 3000 848.88 20904.125.0 66.68 2700 865.09 20625.315.5 64.66 2500 880.94 20717.535.9 63.03 2200 893.35 19615.88 7.0 58.43 1800 926.10 18916.48 8.0 54.05 1450 953.86 17685.78 9.0 49.44 1200 979.24 16833.07 10.0 44.51 1020 1001.51 16317.99 11.0 39.14 850 1019.44 15657.36 12.0 33.12 700 1030.70 15036.47 13.0 26.01 600 1030.24 14969.98 14.0 16.62 500 1002.65 15123.29 14.8 0 400 858.49 16962.87MPa u r r z z u n 87.132)3.13221()219.60()9.603.132(21)()()(21222222≈−−+++−×=−+−+−=σσσσσσσ MPa n n 63.6287.1323232≈×==στ (5)内压引起半径增加量mm D T E P r 04.0)23.01()2145(5.1220600021)21()2(max 22=−×××=−⋅⋅⋅=Δν (6)安全率 47.287.13278.327][1≈==n b Sf σσ 97.1][*8.02≈=nb Sf σσ 03.3][3≈=n Sf ττ43.2][*8.04≈=n Sf ττ(7)结论安全 2.活塞杆强度计算说明 d1:活塞杆内径(mm) d:活塞杆外径(mm) L:屈服长度(mm),L=1643mmn:末端条件系数,n=1.5 w:屈服系数,w=1.71 σca:起重机构造规定的许用压应力 ◇ 断面回转半径: mm d d k 45.3416831101612222=+=+= ◇ 细长比:69.4745.341643≈==k L λ◇ 有效细长比:94.3869.475.111'≈×=∗=λλn ◇ 活塞杆的截面积:2222271.4092)83110(4)1(4mm d d A ≈−×=−=ππ◇ 作用于活塞杆的轴向力(定载总负荷时)N D P Fe 92.3467721454214max 22=××=⋅⋅=ππ(1) 根据起重机构造规格计算 ◇ 屈服应力:MPa ca k 14.1661.28471.111≈×=∗=σωσ ◇ 压缩应力:MPa A Fe 73.8471.409292.346772≈==σ ◇ 安全率:96.173.8414.166≈==σσk Sf (2) 稳定性计算 ◇ 临界载荷:N L I E n Pk 33.5487520164363.777164652060005.12222≈×××=∗∗∗=ππ 其中:4444463.77716465)83110(64)1(64mm d d I =−×=−=ππ ◇ 安全率: 82.1592.34677233.5487520≈==Fe Pk Sf (3)结论安全。