2000td烧无烟煤水泥生产线若干问题分析
水泥窑煅烧工艺异常情况原因分析及处理措施
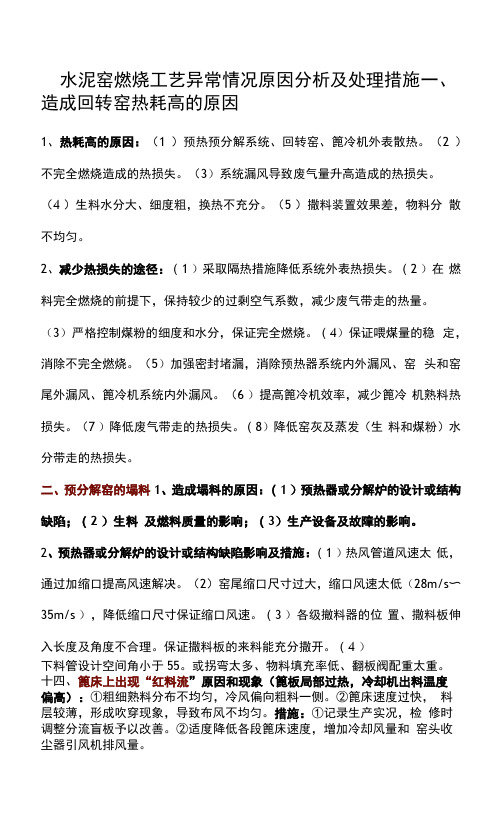
水泥窑燃烧工艺异常情况原因分析及处理措施一、造成回转窑热耗高的原因1、热耗高的原因:(1 )预热预分解系统、回转窑、篦冷机外表散热。
(2 )不完全燃烧造成的热损失。
(3)系统漏风导致废气量升高造成的热损失。
(4 )生料水分大、细度粗,换热不充分。
(5 )撒料装置效果差,物料分散不均匀。
2、减少热损失的途径:(1 )采取隔热措施降低系统外表热损失。
(2 )在燃料完全燃烧的前提下,保持较少的过剩空气系数,减少废气带走的热量。
(3)严格控制煤粉的细度和水分,保证完全燃烧。
(4)保证喂煤量的稳定,消除不完全燃烧。
(5)加强密封堵漏,消除预热器系统内外漏风、窑头和窑尾外漏风、篦冷机系统内外漏风。
(6 )提高篦冷机效率,减少篦冷机熟料热损失。
(7 )降低废气带走的热损失。
(8)降低窑灰及蒸发(生料和煤粉)水分带走的热损失。
二、预分解窑的塌料1、造成塌料的原因:(1 )预热器或分解炉的设计或结构缺陷;(2 )生料及燃料质量的影响;(3)生产设备及故障的影响。
2、预热器或分解炉的设计或结构缺陷影响及措施:(1 )热风管道风速太低,通过加缩口提高风速解决。
(2)窑尾缩口尺寸过大,缩口风速太低(28m/s〜35m/s ),降低缩口尺寸保证缩口风速。
(3 )各级撤料器的位置、撒料板伸入长度及角度不合理。
保证撒料板的来料能充分撒开。
(4 )下料管设计空间角小于55。
或拐弯太多、物料填充率低、翻板阀配重太重。
十四、篦床上出现“红料流”原因和现象(篦板局部过热,冷却机出料温度偏高):①粗细熟料分布不均匀,冷风偏向粗料一侧。
②篦床速度过快,料层较薄,形成吹穿现象,导致布风不均匀。
措施:①记录生产实况,检修时调整分流盲板予以改善。
②适度降低各段篦床速度,增加冷却风量和窑头收尘器引风机排风量。
十五、篦板温度偏高原因:①熟料粒度过细;②篦床上出现〃红料流〃;③ 风室冷却风量过大,或料层较薄,熟料层被吹穿;④风室冷却风量过小,缺乏以充分冷却熟料;⑤窑皮跨落,篦床上有大量熟料堆积,无法及时冷却所致;⑥篦床速度过快,料层过薄;⑦篦板脱落或篦绛较宽,漏料比拟严重。
2000t/d水泥熟料生产线掺无烟煤煅烧探讨

关 键 词 :无 烟 煤 ;煅 烧 ;水 泥 熟 料
1 概 述
11 煤 及 煤 的 分 类 .
挥发 分 的燃 烧及 周 围高 温 的作 用 ,固定 碳 被点 燃 , 反 过来 又进 一 步加快 了挥发 分 的析 出和燃 烧 。
一
煤 是 一 种 能 燃 烧 产 生 热 量 的 有 机 岩 类 一 化 石 燃 料 , 由植 物 残 骸 演 变 而 成 。 植 物 的 残 骸 受 地 壳 变 动 被 埋 于 地 下 ,经 历 亿 万 年 地 层 内 的 高 温 高 压 作 用 和 通 过 细 菌 的分 解 及 变 质 过 程 而 变 成 为 煤 。 由于 煤 的 变 质 程 度 不 同 ,矿 物 煤 的组 分 也 不 同 ,
12 煤 的 燃 烧 机 理 . 煤 在 隔绝 空 气 的条 件 下 加 热 时 ,有 机 质 分 释 放 出气 态 和蒸 汽状 物 质 所 占质 量 百 分 数 减 去 水 分
以 将 煤 粉 加 热 到 着 火 温 度 时 ,低 挥 发 分 煤 的 着 火
和 稳 定 就 更 加 困 难 。 另 #- 挥 发 分 对 煤 粉 的 燃 烬 1 , 也 有 直 接 的 影 响 ,一 般 挥 发 分 较 高 的 煤 形 成 的 焦
据 此 , 我 们 通 常 将 矿 物 煤 分 为 褐 煤 、 烟 煤 和 无 烟 煤 : 褐 煤 是 泥 煤 初 级 成 岩 阶 段 的 煤 种 , 因 呈 褐 色 而 得 名 ,褐 煤 煤 化 成 岩 , 离 地 表 不 深 、温 度 不 高 、
质 地 疏 松 、水 分 较 高 ; 烟 煤 是 在 褐 煤 的 基 础 上 经
炭 疏 松 多 孔 , 它 的 化 学 反 应 能 力 也 比 较 强 _。 I 1 13 通 常 水 泥 熟 料 生 产 用 煤 .
广西鱼峰2000t/d无烟煤煅烧熟料生产线快速达标达产

广西鱼峰 2 0 t 0 0/ d无烟 煅烧 熟 料 生产线快 速达标 立 J
马祖 生 ( 中材 国际工程股份有限公司 , 南京 20 2 ) 109
0 前 言
广 西 鱼 峰 水 泥 股 份 公 司( 以下 简 称 鱼 峰 公 司 ) 位
为 充 分 利 用 原 有 设 备 和 节 省 投 资 , 设 计 中保 在 留 了 原 3条 湿 法 生 产 线 湿 法 制 浆 以 前 的 所 有 设 备 和 设 施 , 保 留 了 熟 料 储 存 及 以后 的 生 产 设 施 。该 并 技 改 工 程 的 主 要 系统 配 置 见 表 1 。
维普资讯
马 祖生 : 西鱼峰 20 t 广 00 d无烟 煤煅 烧熟料 生产 线 快速 达标 达产 /
[ 图 分类号 】Q 7. 中 T 12 6
[ 献 标识 码] 文 B
[ 章 编 号 ] 0 7 0 8 一( 0 2 0 — 0 9 0 文 10 —3 9 20 ) 40 5— 4
万 t 且 日产 稳 定 在 2 O t  ̄ 2 O/ 该 工 程 从 第 一 , 1O/ 2 O t d d。
次 投 料 开 始 , 个 月 内 实 现 燃 5 %无 烟 煤 的 达 标 生 1 0 产 ,. 15个 月 内 实 现 燃 1 0 无 烟 煤 的 达 标 生 产 , 0% 2
煤粉制 备
煤 达
风 量 4 5 0 m3h; 压 8 0 Pa 100 / 风 50
O 4 X5 m ; 0 0/ m 6 2 0 td F os Ba ; 0 0 /
风 扫 式 煤 磨
选粉 机
3 r x 65 25m ; 1  ̄ 9 th . 0 ( .+ . e ) ( 7 1 )/
湿磨干烧和燃无烟煤技术在2000t/d工程上的成功应用
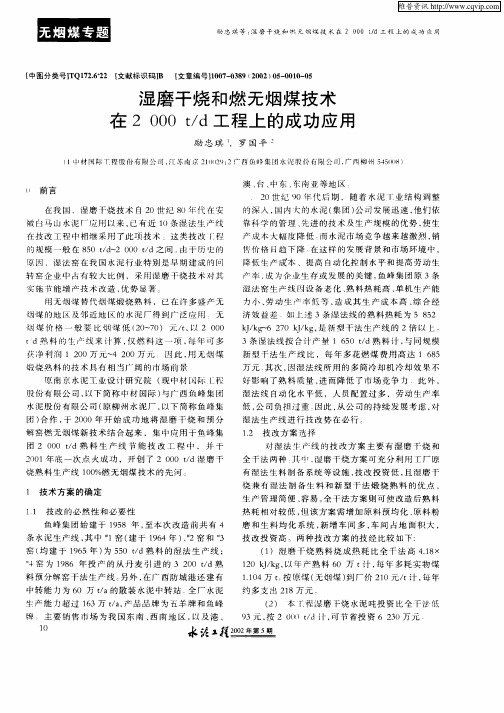
万元: 次, 其 因湿 法线 所 用 的多筒 冷 却机 冷却 效 果 不 好 影 响 了熟 料 质量 , 而降低 了市 场竞 争 力 :此 外 , 进
湿 法 线 自动 化水 平低 ,人员 配 置过 多 ,劳 动生 产率 低 , 司 负担 过重 。 公 因此 , 从公 司的持 续 发 展考 虑 , 对 湿 法 生产 线进 行 技改 势 在必 行 。 1 . 技改 方 案 选择 2 对 湿 法 生 产线 的技 改 方 案 主要 有 湿 磨 干烧 和 全 干 法两 种 : r . 磨 干烧 方案 可 充分 利 用工 厂原 其 {湿 f 有 湿法 生 料制 备 系统 等设 施 , 改投 资低 , 湿 磨干 技 且
【 前言 】
澳、 、 东、 台 中 东南亚 等 地 区 一 2 0世 纪 9 0年 代后 期 ,随着 水 泥 1 业结 构 调 整 一
在我 国 ,湿磨 干烧 技 术 自 2 0世 纪 8 O年 代 在 安 徽 白马 山水泥 厂 应用 以来 , 已有 近 1 O条湿 法生 产线 在 技改 工 程 中相继 采 用 了此 项技 术 :这 类 技改 r 程
原因 ,湿 法窑 在我 国水 泥行 业特 别 是早 期 建成 的 同
降低 生产 成 本 、提 高 自动 化控 制水 平 和提 高 劳动 生
产率 , 为 业生 存 或 发展 的关 键 。 峰集 团 原 3条 成 鱼
湿法 窑 生产 线 圈设 备老 化 、 料热 耗高 、 机生 产 能 熟 单 力 小 、 动生 产 率 低 等 , 成 其 生 产成 本 高 、 合 经 劳 造 综 济 效 益差 如 上述 3条湿法 线 的熟 料 热耗 为 5 8 2 5 k/ g 6 2 0 k/ g 是 新型 干 法 生产 线 的 2倍 以 上 Jk  ̄ 7 J k , 3条 湿 法线 按 合计 产量 1 6 0 td熟 料计 , 同规模 5 / 与 新 型 干 法生 产 线 比 ,每年 多 花燃 煤 费用 高 达 1 6 5 8
2000t-d水泥熟料生产线脱硝改造项目实施方案和施工计划

2000t/d水泥熟料生产线脱硝改造项目实施方案和施工计划建材有限责任公司2000t/d水泥熟料生产线脱硝改造项目实施方案和施工计划一、项目概况1、项目名称:2000t/d水泥熟料生产线脱硝改造项目2、项目改造依据:根据兵团环保局《关于对兵团水泥行业氮氧化物排放企业限期治理的通知》(兵环发[20xx]74号)精神,要求公司2000t/d水泥熟料生产线在20xx年8月底前完成脱硝改造,氮氧化物排浓度(以NO2计)满足水泥工业大气污染排放新标准(GB4915-20xx)。
3项目改造内容:采用选择性非催化还原(SNCR)技术,对水泥窑煅烧过程中氮氧化物进行还原反应生成氮气和水,反应温度在900-1050ºC之间进行,最佳反应温度950ºC。
因此,在水泥窑窑尾系统中只有分解炉出口处是此温度范围,所以此项目的所选位置和使用还原剂-氨水的量至关重要。
4、项目改造效果情况:根据相关资料介绍SNCR脱硝技术可以把NOx降低40-60%,这样我公司的NOx排放浓度可达到400mg/Nm3左右,基本上可满足国家新标准的要求, NOx排放量的减少,较好地改善空气质量,对我国"十二五"氮氧化物减排起到积极作用。
另外,该项目不产生企业经济效益,反而要增加公司的运行成本,吨产品成本要增加4-5元,每年公司新增成本200万元左右。
5、SNCR脱硝设施请设备生产专业单位帮助现场设计、指导安装、调试和试运行。
二、项目技术方案1、氮氧化物排放基本原理氮氧化物在水泥生产中由煤燃烧过程产生。
煤燃烧过程中,依据氮氧化物生成机理不同区分为三种类型号:(1)燃烧与空气中的N2在高温条件下氧化生成的热力NOx;(2)燃料中的有机氮化合物在燃烧过程中被氧化形成的燃料NOx;(3)在碳氢集团反应过程中形成的中间产物和N2反应形成的快速NOx。
水泥生产过程中,回转窑和分解炉是两个主要的热工设备。
分解炉主要完成生料的碳酸盐分解过程,分解后产物进入回转窑,进行高温煅烧,形成水泥熟1料。
无烟煤使用的难点及对策

无烟煤使用的难点及对策
发布: 2010-11-08 13:44 | 编辑: 小平 |
【水泥人网】摘要:目前,在新型干法生产线中百分之百使用无烟煤早已成功,关键是掌握它与烟煤的区别及难点,并有针对性地解决,不但有利于企业因地制宜地选择煤源,更为无烟煤产区建设预分解窑生产线、逐步淘汰立窑提供可能。
1、窑内无烟煤燃烧的观点
1.1无烟煤燃点高、燃烬慢。
如果按煤的办法,火焰会很长,并使用窑尾温度偏高。
1.2无烟煤一旦着火,因其热值高,处理不当,高温区很集中,窑前温度很高,窑的烧成高温区即使是进口镁铬砖,安全期也仅3个月左右,窑头罩衬料的寿命也很短。
2、分解炉中无烟煤燃烧的难点
分解炉中无烟煤燃烧主要是设法延长燃料、生料在炉内的停留时间,并加快煤粉燃烧速度。
这两点在设计方面会予以充分考虑。
3、对策
3.1对此采取的措施除了提高燃料成份中心的稳定、提高入窑的二次风温外,关键是选择较高推力的喷煤管及与之相匹配的一次见机。
3.2由于一般无烟煤的磨蚀性较大,较少选用立磨。
而更多采用管磨机磨制煤粉。
为了加速煤粉在分解炉的燃烧速度,分解炉内需要更细的煤粉,80微米的筛余量仅为2%,窑头用煤粉则可以放宽,为此,煤粉的制备过程系统常常设置两级选粉,以同时生产两种不同细度的煤粉。
3.3在操作中应努力做到保持风、煤、料在质量上稳定,设计上考虑为适应煤的燃烧速度变化及分解率的变化,在分解炉及四级、五级预热器及上升烟道处置了调料、调煤的阀门,但操作中并不需要经常调整,只要煤、料成份稳定,在摸索出最佳工艺参数后,不应经常变动。
2500td+TSD分解炉燃烧极难烧无烟煤的实践

2009.NO.2杠渤倒刖T2500t/dTSD分解炉燃烧极难烧无烟煤的实践陈远胜1,王红霞2(1.福建省永定闽福建材有限公司,福建永定364120;2.天津水泥上业设计研究院有限公司,天津300400)中图分类号:TQl72.622.26文献标识码:B文章编号:1002—9877(2009)02—0025—02福建省永定闽福建材有限公一j2x2500t/d乍产线由天津水泥.亡业设计研究院设计,一线于2004年9月投产,二线于2007年10月投产。
两条生产线均100%采用当地无烟煤,煤的挥发分3%,燃点在750℃以上,90%燃尽时间为64.8s,属极难烧无烟煤。
目前,生产线运转良好,平均日产量达到2850t/d,熟料28d抗压强度平均在60MPa以上。
1烧成系统介绍采用天津院专为燃烧劣质煤开发的1’SD分解炉。
烧成系统主机设备配置见表1,分解炉的结构示意见图l。
表l烧成系统主机设备项目一线二线Cl:2x04700ram,C2:06600mm,项热器C3:06800ram.C4:qb6800ram,C,:中7000mm中5600mm.高31050ram,05600ram,高31050mm.分解炉预燃炉04900mm预燃炉05500ram篦冷机TC—1164TC—1268窑气图1分解炉结构示意TSD分解炉实际上是RSP型的预燃室加TDF炉的组合。
来自窑头的高温三次风切向进入旋流预燃室,煤粉采用特制的三通道燃烧器喷入预燃室并在纯空气的高温环境中稳定着火并快速燃烧,来自C4的热物料喂入预燃室三次风入口,出预燃室的未燃尽煤粉及物料经斜烟道进入主炉中继续边燃烧边分解,最一25一后出炉进入Cs进行气固分离后人窑。
2生产控制实践2.1原燃材料及配料方案原燃料的化学成分见表2,原料配比及熟料率值见表3,煤的工业分析见表4。
表2原燃料化学成分%巧!目LossSi02A1203Ca0F02('3MgOK20NazOSOjCl-“灰五39.956.261.5750.26O.72O.78O.23O.06O.14O.OOJ低硅粉5.6466.6417.301.044.34O.952.63O.350.09O.00l砂岩商硅粉3.1078.1610.310.494.150.742.27O.()60.02O.()(J2砂岩铁矿粉7.9737.9511.688.0130.042.60O.360.04O.12O.002煤灰48.3818.07“.929.962.502.020.286.98().000表3原料配比及熟料率值、矿物组成配比/%熟料率值熟料矿物组成/%低硅粉高硅粉石灰石铁矿粉KHsMfMCjsC参C3AC4AF砂岩砂岩87.73.25.93.2O.922.651.5558.29J9.157.859.77表4煤的工业分析I帆,%Md|%rA^I/%V_I/%FC_|%仉.。
2000t水泥线中控操作实例

2.2
2.5
2.7
3.0
一段篦床
3.8
4.3
6.6
7.5
8.5
9.4
10.3
11.2
12.7
二段篦床
3.5
4.0
5.3
6.0
6.8
7.5
8.2
9.0
10.0
1.3预分解窑系统的调节控制:
控制的关键:使系统均衡稳定的生产运转,它是生产状态良好的重要标志.
运转不能均衡稳定,调节控制频繁,甚至出现周期性的”恶性循环”,是窑系统生产效率低,工艺和操作参数混乱的明显迹象,因此,调节控制的目的就是要使窑系统经常保持最佳的热工制度,实现连续均衡运转.
(3)窑转动力矩
烧成带温度较高的熟料被窑壁带动的较高,因而
其转动力矩较大,故以此结合比色高温计, Nox浓度等参数,对烧成带物料的煅烧情况进行综合判断.但是,由于掉窑皮以及喂料量的变化等原因,也会影响转动力矩的测量.因此,当窑的转动力矩与高温计测量值以及Nox浓度值发生矛盾时,必须充分考虑掉窑皮,物料变化的影响,综合权衡,作出正确判断.
(4)窑尾废气温度
它連同燒成帶溫度一起表征窑内各带热力分布情
况.连同最上一级旋风筒出口气体温度(或连同分解炉出口气体温度)一起表征预热器(或含分解炉)系统的热力分布状况.同时,适当的窑尾温度对于窑系统物料的均匀加热及防止窑尾烟室,上升烟道及旋风筒因超温而发生结皮堵塞也十分重要,一般可根据需要控制在900-1050度.
脱落,窑衬侵蚀,掉转及窑内结圈状况,以便及时粘补窑皮,延长窑衬使用周期,避免红窑事故的发生,提高窑的运转率.
注:
在进行故障或不正常情况的判断时,要分清主要矛盾和次要矛盾,逐步进行判断,一般情况下首先要重点观擦一级旋风筒出风口,分解炉(最下一级旋风筒出风口),窑尾及窑头压力的变化;再次是窑尾及预热器后风管气体成分的变化;最后是其它参数的变化.
水泥厂燃爆工艺事故原因分析及防范对策

水泥厂燃爆工艺事故原因分析及防范对策水泥厂燃爆工艺事故是指由于水泥生产过程中发生的燃烧爆炸,造成人员伤亡和财产损失的事故。
其原因可能涉及到多个方面,包括设备故障、操作不当、管理不严格等。
以下是对水泥厂燃爆工艺事故原因分析及防范对策的探讨。
一、原因分析1.设备故障:水泥生产过程需要使用大量的设备设施,如窑炉、破碎机、磨粉机等。
这些设备设施如果存在设计、制造、使用等方面的问题,如密封不严、防爆措施不完善等,就有可能引发火源。
同时,长期使用过程中设备的老化和磨损也可能导致设备故障,从而引发燃爆事故。
2.操作不当:水泥生产是一个复杂的工艺过程,需要经验丰富的操作人员进行控制。
操作人员如果缺乏专业知识和合理操作经验,可能会在操作过程中产生火源或误操作,导致事故发生。
另外,操作人员也应该严格遵守操作规程和安全操作手册,如不得将火源带入作业现场、不得在易燃物品附近吸烟等。
3.管理不严格:水泥厂的管理人员应制定并严格执行相应的安全管理制度和操作规程,加强对生产过程的监督与管理。
如果管理制度不完善,如未进行定期设备维护保养、安全检查不到位等,就可能导致潜在的安全隐患。
此外,应提供必要的安全培训和教育,不断提高员工的安全意识和应急处理能力。
二、防范对策1.设备安全:水泥厂应对设备进行定期维护保养,确保设备的正常运转。
同时,应加强设备设计和制造的质量检查和监管工作,确保设备的安全性能。
对于存在安全隐患的设备,应及时进行更换或修复。
2.操作规程:制定系统化的操作规程和安全操作手册,并严格执行。
对操作人员进行必要的安全培训和教育,提高他们的安全意识和技能。
禁止操作人员在工作现场吸烟、携带易燃物品等,确保操作过程的安全性。
3.安全管理:建立健全的安全管理制度,对生产过程进行全面的监督与管理。
加大对设备的巡检频率,及时发现和解决潜在的安全隐患。
在重要位置设置监控设备,加强现场视频监控和报警系统,及时发现异常情况。
4.应急预案:制定完善的应急预案,明确各岗位员工在事故发生时的应急处理措施。
西藏2000t_d生产线的热工检测与分析

西藏高争2000t/d生产线的检测与分析章诚、余学飞、谢萌、万畅达、王祖润、夏俊雅(合肥水泥研究设计院,安徽合肥230051)摘要:基于西藏高争2000t/d生产线的热工标定结果,结合生产实际,并与其他不同地区的生产线进行了比较,对生产线主机设备运行现状及熟料烧成热主要支出项进行了分析,并提出了改进措施。
关键词:热工标定;设备运行;热耗西藏高争建材股份有限公司成立于2001年1月20日,始建于1960年的原拉萨水泥厂经改制而设立的股份有限公司,是西藏自治区建厂最早,现今规模最大,最具有实力的区内水泥生产国有骨干企业,同时也是自治区建材行业的龙头企业。
公司现有两条2000t/d新型干法水泥生产线,年产水泥120万吨。
这两条生产线位于西藏自治区拉萨市堆龙德庆县,海拔约3700m,为世界上海拔最高的水泥生产线。
为了全面系统地考察和评价公司2000t/d水泥生产线,充分了解生产线的实际运作情况,为今后的节能增产提供科学依据,国家建筑材料工业水泥能效环保评价检验测试中心应邀对该生产线进行测试。
1.主机配置及测试方法该线主机配置见表1,标定期间现场生产情况稳定,原材料成分及系统参数变化较小。
测试期间该线的气象环境见表2,测试及数据整理计算依据GB16780-2007《水泥单位产品能源消耗限额》、GB/T3485-1998《评价企业合理用电技术导则》、JC/T733-2007《水泥回转窑热平衡测试方法》、JC/T730-2007《水泥回转窑热平衡、热效率、综合能耗计算方法》GB4915-2004《水泥工业大气污染物排放标准》的要求进行。
表1 主机配置受地球重力作用,大气的分子密度随海拔高度而变化,高度愈高,空气密度愈低,大气压力就愈小。
该生产线海拔约为3700m,对应的基本环境参数如表2所述,由于空气比热及密度等以容积为单位来表示时将有较大变化,修正后的标况空气比热及密度略有降低。
表2 测试期间天气情况2.原燃材料及熟料成分分析标定期间入窑生料、出篦冷机熟料的化学成分及入窑煤粉的工业分析分别见表3和表4。
水泥工业中燃烧问题的分析及改进

水泥工业中燃烧问题的分析及改进水泥工业是很重要的建筑材料生产行业。
在生产水泥的过程中,燃烧问题一直是生产过程中的关键问题。
因为水泥生产过程中需要大量的能源,而这种能源主要来源于燃烧化石燃料。
燃烧后产生的废气中含有多种有毒有害的物质,对环境和人体健康带来了很大的影响。
因此,在水泥工业中,怎么解决燃烧问题已成为了行业发展的重点。
一、水泥工业中燃烧问题主要表现在哪些方面?1.废气的产生水泥生产过程中必须要进行能源的燃烧,这就会产生很多废气。
这些废气中呈现出多种有毒有害的物质,如二氧化硫、氮氧化物、碳氧化物和氢氧化物等。
这些废气在大气中聚集,会引起不良反应,导致严重的大气污染。
2.能源的浪费在水泥生产过程中,能源的消耗十分巨大。
一方面,这种能源是不可再生的,另一方面,质量上的不合理使用容易导致能源的浪费,带来生产成本的增加。
3.工人的健康水泥工业中的燃烧问题不仅会产生废气和浪费能源,还会对工人的健康产生影响。
在生产过程中,化学物质和粉尘会通过工人的皮肤或呼吸道进入人体,造成一定的伤害。
二、如何解决水泥工业中的燃烧问题?1. 建立完善的监管机制应建立严密的规章制度,确保工艺的合理性和环保性,对产生的污染物进行严密监管和排放,防止环境的进一步污染。
2. 设备升级目前,水泥工业中大部分炉窑使用的煤粉精炼炉是一种老式的燃烧设备,它的燃烧效率低,容易造成污染。
因此,在生产过程中,应加强炉窑的升级工作,采用高效率、低能耗的炉窑。
采用新型的预计算型燃烧设备,以提高燃料的使用效率,减少废气的排放。
3. 强化工人的健康保护工人是企业的核心资本,企业应注重员工健康保护,加强安全教育和培训,提高员工自我保护能力。
同事也要为有害化学气体、颗粒物质等构成关键性危险的岗位上的工人,配备有效的个人保护装备。
4. 加强环保理念的建设改善企业管理理念,增强企业责任感和环保意识。
识别改变所有涉及到的流程。
引入新的、零排放的冶炼工艺,探讨使用可再生能源燃料,把燃烧带来的污染降到最低限度。
2000td水泥熟料生产线SNCR技术烟气脱硝工程环境影响报告表
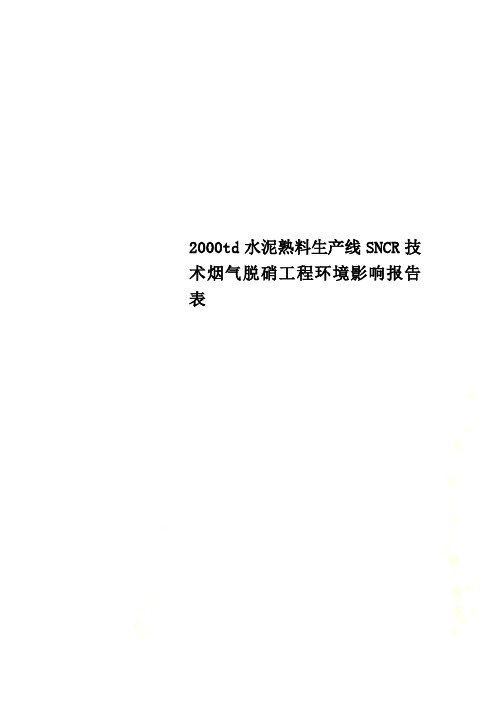
2000td水泥熟料生产线SNCR技术烟气脱硝工程环境影响报告表
二、建设项目所在地自然环境社会环境简况
三、环境质量状况
图5-3 SNCR系统实施位置图
2、SNCR技术系统组成
SNCR系统主要包括:还原剂原料的接受及制备系统、还原剂的供应系统、喷射系统、电气、控制系统以及配套土建。
3、还原剂
SNCR技术还原剂选择是整个系统中很重要的一个环节。
在SNCR系统中,还原剂是最大的消耗品。
其消耗成本直接影响到脱硝系统的整体经济评估。
该项目SNCR系统使用的还原剂为氨水和尿素。
(2)氨水的特性:氨水与无水氨都属于危险化学品。
氨溶液:含氨>50%的氨溶液,。
2000td烧无烟煤水泥生产线情况分析
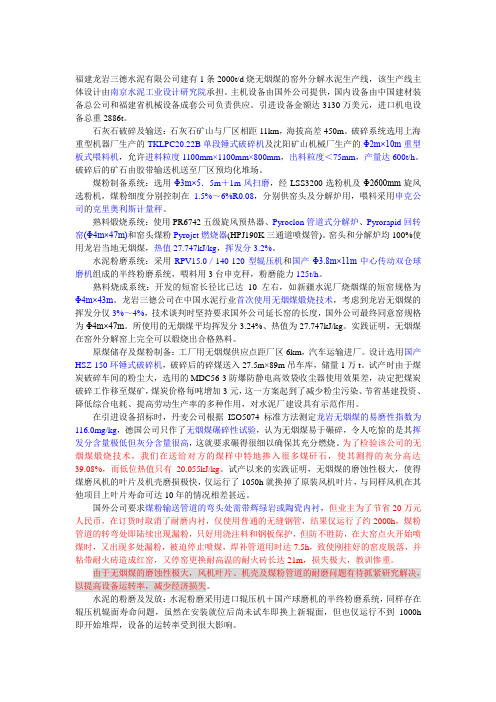
福建龙岩三德水泥有限公司建有1条2000t/d烧无烟煤的窑外分解水泥生产线,该生产线主体设计由南京水泥工业设计研究院承担。
主机设备由国外公司提供,国内设备由中国建材装备总公司和福建省机械设备成套公司负责供应。
引进设备金额达3130万美元,进口机电设备总重2886t。
石灰石破碎及输送:石灰石矿山与厂区相距11km,海拔高差450m。
破碎系统选用上海重型机器厂生产的TKLPC20.22B单段锤式破碎机及沈阳矿山机械厂生产的Φ2m×10m重型板式喂料机,允许进料粒度1100mm×1100mm×800mm,出料粒度<75mm,产量达600t/h。
破碎后的矿石由胶带输送机送至厂区预均化堆场。
煤粉制备系统:选用Φ3m×5.5m+1m风扫磨,经LSS3200选粉机及Φ2600mm旋风选粉机,煤粉细度分别控制在 1.5%~6%R0.08,分别供窑头及分解炉用,喂料采用申克公司的克里奥利斯计量秤。
熟料煅烧系统:使用PR6742五级旋风预热器、Pyroclon管道式分解炉、Pyrorapid回转窑(Φ4m×47m)和窑头煤粉Pyrojet燃烧器(HPJ190K三通道喷煤管)。
窑头和分解炉均100%使用龙岩当地无烟煤,热值27.747kJ/kg,挥发分3.2%。
水泥粉磨系统:采用RPV15.0/140-120型辊压机和国产Φ3.8m×11m中心传动双仓球磨机组成的半终粉磨系统,喂料用3台申克秤,粉磨能力125t/h。
熟料烧成系统:开发的短窑长径比已达10左右,如新疆水泥厂烧烟煤的短窑规格为Φ4m×43m。
龙岩三德公司在中国水泥行业首次使用无烟煤煅烧技术,考虑到龙岩无烟煤的挥发分仅3%~4%,技术谈判时坚持要求国外公司延长窑的长度,国外公司最终同意窑规格为Φ4m×47m。
所使用的无烟煤平均挥发分3.24%、热值为27.747kJ/kg。
实践证明,无烟煤在窑外分解窑上完全可以煅烧出合格熟料。
水泥烧失量试验常见问题分析及处理

水泥烧失量试验常见问题分析及处理摘要:随着铁路工程的发展,铁路桥梁建设规模的不断扩大,大体积混凝土施工技术的应用也愈加广泛,其对提升桥梁结构承载能力、耐久性以及稳定性有着十分重要的影响,对提升行车安全性和舒适度有十分重要的现实意义和社会意义。
因此做好原材料的检测工作是质量的保证,在铁路工程建设中所使用的原材料必须要经过严格的检测之后才能够进入现场进行使用,将质量控制在一定的规范和标准之中,加强对铁路工程整个施工过程的质量保证作用,本文针对桥梁大体积混凝土施工中水泥的烧失量试验方面存在问题进行简单的分析与处理。
关键词:混凝土原材;烧失量试验;方法控制引言随着国内经济的不断提升,以及城市化进程的不断加快,桥梁作为交通运输中的重要组成部分,对社会经济发展有极为重要的影响。
大体积混凝土作为桥梁工程中的重要施工内容,直接关系到桥梁基础的稳定性、耐久性以及承载能力,因此在实际施工过程中对混凝土胶凝材料水泥的技术要求,尤其是胶凝材料水泥烧失量技术指标的控制及烧失量试验操作方法的制定,直接影响了大体积混凝土的耐久性指标,因此严格要求烧失量试验操作流程,保证大体积混凝土使用胶凝材料水泥的质量,为提升混凝土桥梁工程质量和寿命奠定坚实的基础。
1水泥烧失量试验检测目前,建筑行业普遍采用高温炉来测定混凝土胶凝材料水泥烧失量。
1.1 所用仪器设备高温炉;分析天平(称量200g、感量0.0001g);干燥器。
1.2 分析步骤该方法原理是将混凝土胶凝材料称取约1g试样,精度至0.0001g,放入已灼烧恒量的瓷坩埚中,将盖斜置于坩埚上,放在高温炉内,从低温开始逐渐升高温度,在(950±25)℃下灼烧(15~20)min,取出坩埚置于干燥器中,冷却至室温,称量;反复灼烧,直至恒量。
从而算出混凝土胶凝材料灼烧后试样的质量即烧失量。
4.4 烧失量的质量百分数按式1-6计算,结果精确至0.01%。
式中:XLOI——烧失量的质量百分数(%)m1——试样的质量(g)m2——灼烧后试样的质量(g)2 烧失量试验中存在问题目前试验室使用干燥器均包括干燥器主体和盖体,在冷干燥样品过程中,由于干燥器内温度(950±25)℃及压力急速升高,干燥器内空气高温及高压下热膨胀,导致干燥器的盖体被顶出从而与干燥器错位,为此,试验人员需要手扶干燥器的盖体,才能解决由于高温高压产生而对试验结果造成影响或无法继续进行试验的问题。
燃无烟煤窑电流低的原因分析及解决措施

燃无烟煤窑电流低的原因分析及解决措施我公司现拥有两条日产5000t/d生产线,目前运行比较稳定,该生产线由中材国际南京水泥工业设计院设计,100%燃无烟煤。
近段时间出现窑电流一直偏低,且波动较大,最低时甚至到90A,熟料还原料多、质量差、强度低、窑产量低等状况。
为此,公司组织人员分析问题原因,并针对性的进行解决,取得了明显的效果,同时总结了一些经验供大家参考。
1 烧成系统主要设备配置回转窑规格:Φ4.8×74m 斜度:4°预热器为NC高效低阻型,并配NST型分解炉篦冷机采用NC-Ⅲ型控制流推动篦式冷却机,篦床有效面积:133.2㎡2 窑电流低的原因分析通过综合判断引起窑电流低的主要原因是窑系统通风能力差,窑内还原气氛严重导致。
具体从以下几个方面进行分析:(1)原材料波动大,分解炉温度控制不当。
由于近段时间石灰石供应不足,矿石成分比较复杂,当中甚至含有CaF2,MgO的含量偏高(3.0%-4.0%)生料易烧性好,加上这种无烟煤很容易形成局部高温(见表1),物料在分解炉内提前形成熔相,严重时形成颗粒状。
Mad(%)Vad(%)Aad(%)Sbad(%)Qnetad(kJ∕kg)1.54.026.01.123800表1 煤的工业分析分解炉锥部、缩口、三次风进风口结料严重(见图1),分解炉出口负压从正常时的-1000Pa 升至-1500Pa,严重影响了窑内通风。
图1 分解炉结料示意图(2)系统漏风严重。
其中包括窑尾密封圈漏风、烟室清料口变形漏风、分解炉与烟室连接处膨胀节漏风等,相对减小了窑内通风量,漏风处也容易形成结皮。
(3)喂煤量不稳定。
由于长时间运行,窑头转子称间隙偏大,实际喂煤量比中控给定的偏多,窑头、窑尾用煤量成倒挂现象,窑内煤粉燃烧不完全。
(4)篦冷机急冷效果差。
篦冷机一段篦板篦缝堵塞,出窑熟料急冷差,三次风中O2含量不足,促使系统产生还原气氛,窑电流低。
3采取的措施和效果针对我公司窑电流低的问题,通过分析原因,采取了以下几个方面的措施:(1)加强原材料的管控,合理均化,杜绝使用含CaF2的矿石。
水泥厂燃爆工艺事故原因分析及防范对策

水泥厂燃爆工艺事故原因分析及防范对策随着水泥生产技术的不断进步,新型干法窑以节能环保、熟料质量好、生产大型化、投资成本低、运转率高和运行稳定等优点越来越被水泥业界普遍认同和推广。
近年来,新型干法窑每年以较快的速度增长,由于技术和管理人员增长不能与新型干法窑发展同步,时常出现新型干法窑燃爆工艺事故,造成停产和设备损坏,甚至出现人员伤亡事故,给企业造成较大的经济损失,尤其是冬季,是新型干法窑燃爆工艺事故的多发期。
本文针对新型干法窑生产中的几起燃爆工艺事故进行分析,制定防范措施,以防止类似事故的再发生。
1煤磨电除尘器的燃烧事故2006年冬季,连续的雨雪天气造成A厂露天堆场的原煤等物料潮湿。
因原煤潮湿,不仅使煤磨台产大幅下降,煤粉供应紧张,而且致使入煤磨除尘器的烟气湿度增大,造成煤磨电除尘器结露,灰斗堵塞。
事故发生前,中控操作员发现煤磨电除尘器第二电场电压较低,随即安排停机检查,打开煤磨电除尘器检查门,发现电场内煤粉已经燃烧,电场内出现大量的烟雾,灰斗内表层煤粉有火星,且温度较高。
随后组织人员进行事故善后处理工作,并做好停窑准备工作。
该起事故不仅造成停窑31 h,损失煤粉20多吨,而且造成严重的环境污染。
1.1事故善后处理(1)事故发生后,立即对煤磨系统停机,停煤磨电除尘器风机,关闭煤磨电除尘器检查门。
由于着火面积较小,不需要开启CO2灭火系统,开通排灰通道,将电除尘器灰斗下的螺旋输送机反转,使得电除尘器灰斗内的煤粉从排灰通道排放到磨房外,同时用消防水袋对排出着火煤粉及时进行喷水灭火,防止二次燃烧,直到灰斗内的煤粉排完。
(2)与此同时,检查煤粉仓情况。
由于煤粉仓没有着火,要求尽快将煤粉仓内用完,并做好停窑的准备工作。
(3)对于排出的煤粉除现场喷水灭火外,还派人值班看护,防止死灰复燃。
在生产正常后,组织人员清理煤粉,打扫现场环境。
1.2原因分析(1)煤磨电除尘器是煤磨系统的主要工艺设备之一,其职能是收集煤粉成品。
水泥厂2000td回转窑预热器塌料安全事故应急救援演练总结

2000t/d回转窑预热器塌料安全事故应急救援演练总结为了积累员工的安全知识和在突发事故中,确保员工在紧急状态下安全、有序地逃离事故现场的的应急经验,根据中材水泥公司关于应急救援演练的相关文件精神,我公司领导高度重视,责成主管安全生产的副总经理王生平和总经理助理田建科牵头主抓此项工作,安环部具体安排布置,一车间组织人员实施应急行动。
根据应急救援演练的相关程序,安全环保部首先组织一车间相关人员学习中材水泥公司的相关文件,明确开展本次应急演练的目的、任务和背景。
为保证演练效果能真正达到提高员工应急能力的目的,安环部又与一车间领导多次在回转窑窑头篦冷机现场具体调研和协商沟通,充分征求技术人员和现场岗位意见,在公司领导的指导下,于2008年7月16日制定了《2000t/d回转窑预热器塌料安全事故应急救援预案演练方案》。
演练方案制定后,安全环保部又组织相关人员对方案进行了讨论,根据讨论结果和实际情况,安全环保部对方案做了部分调整,同时按照水泥公司的要求,将最后修订的《2000t/d回转窑预热器塌料安全事故应急救援预案演练方案》上报水泥公司,下发具体实施部门生产部一车间。
接到最后修订的应急演练方案后,一车间专门召开了会议布置落实此项方案,再次明确了应急救援演练的必要性。
根据生产进度情况,公司最后确定2008年7月29日上午对《2000t/d回转窑预热器塌料安全事故应急救援预案演练方案》进行了全面演练。
7月29日,总经理助理田建科的亲自指导,安环部全体人员、一车间的主任、副主任、相关工程师、预热器巡检工、窑头篦冷机巡检查工共25人参加了此次演练。
上午10点,全体人员专门召开了演练前的安排布置会议,对演练的目的、演练的程序及演练时的注意事项再次进行了强调。
预备会议结束后,按照演练要求,车间领导在车间办公室待命,其它窑头篦冷机巡检工及相关人员到地坑的现场进行落实,随着烟雾弹的点燃,现场指挥人员的一声令下,演练正式开始了,篦冷机巡检工分组从煤磨入坑口鱼贯而下,在穿过烟雾绕过设备,沿着设备通道紧急迅速从篦冷机东、北两个出口撤出。
- 1、下载文档前请自行甄别文档内容的完整性,平台不提供额外的编辑、内容补充、找答案等附加服务。
- 2、"仅部分预览"的文档,不可在线预览部分如存在完整性等问题,可反馈申请退款(可完整预览的文档不适用该条件!)。
- 3、如文档侵犯您的权益,请联系客服反馈,我们会尽快为您处理(人工客服工作时间:9:00-18:30)。
2000t/d烧无烟煤水泥生产线若干问题分析2009-3-21 作者:1概况福建龙岩三德水泥建材工业有限公司是由龙岩市新罗区建材工业有限公司与香港兴三德有限公司、新加坡三德兴工业有限公司兴建的中外合资企业。
建有一条2 000 t/d全烧无烟煤的窑外分解水泥生产线,留有扩建一条同规模生产线的余地。
1995年8月破土动工,1997年5月2日一次点火成功进入试生产阶段,1997年9月实现达标。
工程包括年产84万t石灰石矿山、17万t粉砂岩矿山、70万t水泥生产线。
项目主体设计由南京水泥工业设计研究院承担。
主机设备由国外公司提供,国内设备由中国建材装备总公司和福建省机械设备成套公司负责供应。
引进设备金额达3 130万美元,进口机电设备总重2 886 t。
2主机设备2.1石灰石破碎及输送石灰石矿山与厂区直距11 km,海拔高差450 m。
破碎系统选用上海重型机器厂生产的TKLPC20.22B单段锤式破碎机及沈阳矿山机械厂生产的2 m×10 m重型板式喂料机,允许进料粒度1 100×1 100×800 mm,出料粒度<75 mm,产量达600 t/h。
破碎后的矿石由B800×10 079.059 m胶带输送机(分五段)送至厂区预均化堆场,中途设有两个Φ12 m库容为3 000 t的中转圆库,控制系统采用S曲线软起动技术,起(制)动加减速度≤0.05 m/s2。
2.2生产制备系统喂料用4台申克秤,生料粉磨采用RP15.0/140-160型辊压机终粉磨系统,入料综合水份≤7%,设计产量为180 t/h,生料经Φ1 500 mm×6 500 mm气力提升机泵送入Φ17 m×42 m 的依堡多料流式生料均化库。
2.3煤粉制备系统选用Φ3 m×5.5 m+1 m风扫磨,经LSS3 200选粉机及Φ2 600 mm旋风选粉机后煤粉细度分别控制在5%~6%R0.08和1.5%R0.08,分别供窑头及分解炉用,喂料采用申克公司的克里奥利斯计量秤。
2.4熟料煅烧系统设有PR6742五级旋风预热器、Pyroclon管道式分解炉、Pyrorapid回转窑(Φ4 m×47 m)和窑头煤粉Pyrojet燃烧器(HPJ190K三通道喷煤管)。
窑头和分解炉均100%使用龙岩本地无烟煤,热值27 747 kJ/kg,挥发份3.2%。
熟料冷却采用PSC2-042.07T倾斜篦冷机。
2.5水泥粉磨系统采用RPV15.0/140-120型辊压机和国产Φ3.8 m×11 m中心传动双仓球磨机组成的半终粉磨系统,喂料用三台申克秤,粉磨能力125 t/h。
2.6其他设备水泥包装设有两台湖北水泥机械厂生产的哈佛技术6嘴包装机;窑头BE110-4B型电收尘器、窑尾BE140/2-3电收尘器和煤磨BEA23-2电收尘器均为龙岩龙净集团公司生产;石灰石和粉砂岩的堆取料机由沈阳矿山机械厂提供。
3若干问题分析3.1石灰石破碎及输送破碎机选用TKLPC20.22B单段锤式破碎机,设计能力为600 t/h,锤头是5排×10个=50个。
试生产时台时产量一度达不到300 t/h,出料粒度>75 mm的大块很多,但其中<2.5 mm的粉状物料又占了35%,而且Mn13Cr2锤头寿命仅13 000 t,破碎费用高、运转率低、劳动强度大。
经分析:产量达不到设计能力的原因是料仓底部的进料口太小、边侧钢轨挡料引进板喂机物料填充不满,加上板喂机宽度为2 000 mm(应为2 200 mm),且最高转速仅870r/min。
将板喂机传动电机YCT355-6B(45 kW)改为YCT355-4A(55 kW)、最大转速由870 r/min改为1 320 r/min,并将破碎机篦缝由40 mm改为55 mm、在下工作腔后部的安全门与给料辊间加焊43 kg钢轨后,产量达到了600 t/h,出料粒度也达到了要求,详见表1石灰石破碎粒度筛分对比。
通过试用Mn13Cr2、Mn13Cr2NiTiMoRe、30CrMoV9等多种锤头,并采用郑州机械研究所的TDL-65耐磨焊条后,堆焊后锤头寿命达到10万t,虽有大幅度提高,但与国内其他厂家使用同类破碎机的锤头寿命相比,仍不理想。
影响锤头寿命的因素有岩石硬度及进出料粒度、锤头材质、岩石含水量及含泥量、转子转速及传动方式、锤头排列方式等等,根据近两年的实践比较及试验证明,在不改变转子转速及传动方式的情况下,影响锤头寿命的最主要因素是锤头材质及排列方式、矿石的爆破方式。
采用毫秒微差爆破的矿石因应力作用内部会产生微裂纹,易碎性大大提高;6排×7个的锤头排列比5排×10个排列的效果好得多,同样材质的一套新锤头,在采用新锤头与磨损过的锤头交错排列后,寿命可比使用全套新锤头提高一倍,详见表2锤头使用情况对比。
当然,矿石的金属磨耗指数、转子转速及传动方式也是重要因素。
表2锤头使用情况对比破碎后的碎石需经E点—D点—C圆库—B点—A圆库—0点五段胶带输送机及两台短胶带和堆料机后才进入预均化堆场,而且长胶带的输送能力600 t/h,短胶带仅为300 t/h(设计上考虑在0点分成两部分同时供应两条生产线)。
实际生产中矿山破碎机到厂区预均化堆料机的诸多环节常因设备故障造成破碎、输送、堆料三个环节不协调,经常使破碎及输送不得不夜间加班才能满足厂区生产要求。
若将C库和A库的容量提高到10 000 t则可避免这一问题。
今后上第二条生产线时,应将0点至堆料机的输送能力改成与长胶带能力一致。
现在长胶带系统中仅遂道内有照明,而其余部分没有照明,并且除各转运站外各段长胶带区内没设维修电源,也在不同程度上影响了正常生产,今后必须补充完善。
3.2原料均化及生料制备石灰石及粉砂岩和预均化堆场为矩形,采用国产天桥皮带堆科机和桥式刮板取料机。
设计堆放石灰石2×20 000 t,粉砂岩2×8 700 t。
因工艺设计失误,只能堆放石灰石2×17 000 t。
设计布料400层,均化效果为8,但石灰石堆场实际均化效果只有2.5,主要是因为进料成分较均匀(标差1.231)、采用瞬间取样方式、取样频次小等原因所致。
设计在石灰石破碎机下短胶带输送机、粉砂岩破碎机下板喂机及石灰石堆场前的胶带机上分别装一台核子秤,国产核子秤的计量精度差,通过一年的实践,只好在两个矿山破碎机前设置电子地中衡取代核子秤作为矿山生产的计量设备。
由于石灰石堆场位于海拔390 m、而年降雨量1 700 mm的亚热带海洋性气候地区,通过多次争论,改变了初步设计中提出的石灰石采用户外型预均化堆场的方案,改用户内型,生产实践证明这一决策是正确的,既保证了进辊压机的物料综合水分≤7%,又避免了堆料时的粉尘飞扬,同时也方便了设备检修。
生料辊压机终粉磨系统在中国水泥行业是首次使用,其产量已达180 t/h(细度R0.08为11.74%)。
计算电耗的设备包括辊压机、打散机和选粉机,保证电耗为12 kWh/t,焊接辊面的寿命为200万t生料产量。
这种用陶瓷套堆焊成的圆柱型辊面实际生产中只粉磨了10万t 生料就需堆焊,在设备安装时,国外公司主动另外发来一套辊面,将原装辊面换下,但换上的辊面一般磨制15万t生料即要局部堆焊。
这种结构的辊面是否合理还需经过长时间的实践检验。
辊面寿命将是影响系统运转率的关键问题。
3.3熟料烧成系统开发的短窑长径比已达10左右,如新疆水泥厂烧烟煤的短窑规格为Φ4 m×43 m。
三德公司在中国水泥行业首次使用无烟煤煅烧技术,考虑到龙岩无烟煤的挥发份仅3%~4%,技术谈判时我们坚持要求国外公司延长窑的长度,国外公司最终同意窑规格为Φ4 m×47 m。
至1998年11月底共生产熟料26万t,平均标号达到66.4 MPa,fCaO为0.872%。
所使用的无烟煤平均挥发份3.24%、热值为27 747 kJ/kg。
实践证明,无烟煤在窑外分解窑上完全可以煅烧出合格熟料,窑系统的主要操作参数及技术经济指标见表3。
表3窑系统主要操作参数及技术经济指标但是,窑系统的窑尾风机的电机功率太小,仅730 kW,与国内同规模厂的1 250 kW相差520 kW,在生料喂料量达到125 t/h情况下运行较长时间,则经常出现跳停,不得不限制喂料量,使窑产量保持在1 900 t/d左右。
在技术谈判时我们要求窑产量要达到2 200 t/d,多次提出窑尾风机功率太小,但国外公司专家坚持认为730 kW已经足够,实践证明不能保证产量,今后必须改造。
受水泥销售市场影响,窑系统无法连续生产,试产初期煤粉细度太粗引起预热器多次堵塞,开窑停窑频繁,加上操作经验及熟练程度等原因的影响,至1998年11月高温带的耐火砖换了三次,窑头护铁换了一次,而喷煤管的浇注料一般20天需要更换一次。
因此,窑外分解窑全部使用无烟煤作燃料的操作和维护需要较长时间的摸索和总结。
3.4原煤储存及煤粉制备工厂用无烟煤供应点距厂区6 km,汽车运输进厂。
设计选用国产HSZ-150环锤式破碎机,破碎后的碎煤送入27.5 m×89 m吊车库,储量10 000 t。
试产时由于煤炭破碎车间的粉尘大,选用的MDC56-3防爆防静电高效袋收尘器使用效果差,决定把煤炭破碎工作移至煤矿,煤炭价格每吨增加3元,这一方案起到了减少粉尘污染、节省基建投资、降低综合电耗、提高劳动生产率的多种作用,对水泥工厂建设起到了示范作用,值得推广。
鉴于可研阶段对原煤质量的调查,附近立窑厂使用同一煤矿的无烟煤的年平均灰分14.69%,标差1.252,热值24 895 kJ/kg、标差609.2,认为煤质稳定,不设预均化堆场,经过一年多的生产证明,所供无烟煤的平均灰分13.70%、标准偏差1.156,热值27 747 kJ/kg,标差531.1,与预计的情况相符。
但是随着当地工业用煤量不断增加,供应趋于紧张,今后很难由一个煤矿供应,需要多点进煤,将给生产带来不便,因此原煤不设预均化堆场是不可取的,扩建二线时必须考虑。
在引进设备招标时,丹麦公司根据ISO5074标准方法测定龙岩无烟煤的易磨性指数为116.0 mg/kg,德国公司只作了无烟煤碾碎性试验,认为“无烟煤易于碾碎,令人吃惊的是其挥发份含量极低但灰份含量很高,这就要求碾得很细以确保其充分燃烧”。
为了检验该公司的无烟煤煅烧技术,我们在送给对方的煤样中特地掺入很多煤矸石,使其测得的灰分高达39.08%,而低位热值只有20 055 kJ/kg。
试产以来的实践证明,无烟煤的磨蚀性极大,使得煤磨风机的叶片及机壳磨损极快,仅运行了1 050 h就换掉了原装风机叶片,与同样风机在其他项目上叶片寿命可达10年的情况相差甚远,这是该公司和业主均没有事先引起重视的重大问题。