机床夹具制造中精度控制的几种加工方法探讨
机械加工中工件尺寸精度测量的5大方法

机械加工中工件尺寸精度测量的5大方法(1)试切法即先试切出很小部分加工表面,测量试切所得的尺寸,按照加工要求适当调刀具切削刃相对工件的位置,再试切,再测量,如此经过两三次试切和测量,当被加工尺寸达到要求后,再切削整个待加工表面。
试切法通过“试切-测量-调整-再试切”,反复进行直到达到要求的尺寸精度为止。
例如,箱体孔系的试镗加工。
试切法达到的精度可能很高,它不需要复杂的装置,但这种方法费时(需作多次调整、试切、测量、计算),效率低,依赖工人的技术水平和计量器具的精度,质量不稳定,所以只用于单件小批生产。
作为试切法的一种类型——配作,它是以已加工件为基准,加工与其相配的另—工件,或将两个(或两个以上)工件组合在一起进行加工的方法。
配作中最终被加工尺寸达到的要求是以与已加工件的配合要求为准的。
(2)调整法预先用样件或标准件调整好机床、夹具、刀具和工件的准确相对位置,用以保证工件的尺寸精度。
因为尺寸事先调整到位,所以加工时,不用再试切,尺寸自动获得,并在一批零件加工过程中保持不变,这就是调整法。
例如,采用铣床夹具时,刀具的位置靠对刀块确定。
调整法的实质是利用机床上的定程装置或对刀装置或预先整好的刀架,使刀具相对于机床或夹具达到一定的位置精度,然后加工一批工件。
在机床上按照刻度盘进刀然后切削,也是调整法的一种。
这种方法需要先按试切法决定刻度盘上的刻度。
大批量生产中,多用定程挡块、样件、样板等对刀装置进行调整。
调整法比试切法的加工精度稳定性好,有较高的生产率,对机床操作工的要求不高,但对机床调整工的要求高,常用于成批生产和大量生产。
(3)定尺寸法用刀具的相应尺寸来保证工件被加工部位尺寸的方法称为定尺寸法。
它是利用标准尺寸的刀具加工,加工面的尺寸由刀具尺寸决定。
即用具有一定的尺寸精度的刀具(如铰刀、扩孔钻、钻头等)来保证工件被加工部位(如孔)的精度。
定尺寸法操作方便,生产率较高,加工精度比较稳定,几乎与工人的技术水平无关,生产率较高,在各种类型的生产中广泛应用。
机械制造工艺与机床夹具 第2版 教学课件 吴年美 吴拓 第二章 机械加工精度
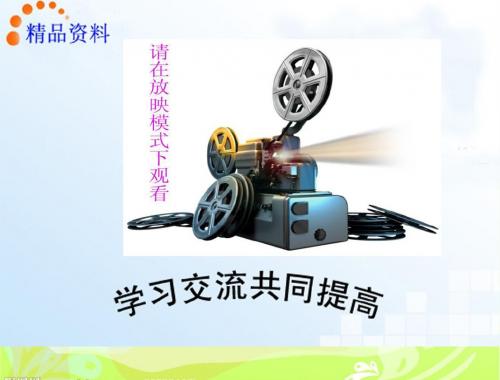
而且毛坯结构越复杂、壁厚越不均,散热的条件差别越大,毛坯内
部产生的残余应力也越大。
第二节 影响加工精度的因素及其分析
(2)冷校直带来的残余应力 直工艺进行校直。 某些刚度低的零件,如细长轴、曲轴和
丝杠等,由于机加工产生弯曲变形不能满足精度要求,常采用冷校
第二节 影响加工精度的因素及其分析
图2-12 冷校直引起的残余应力 a)冷校直方法 b)加载时残余应力的分布 c)卸载后残余应力的分布
教材其余课件及动画素材请查阅在线教务辅导网 在线教务辅导网:
QQ:349134187 或者直接输入下面地址:
第二章
机械加工精度
第二章 机械加工精度 第一节 概 述
第二节 影响加工精度的因素及其分析 第三节 加工误差的综合分析 第四节 保证和提高加工精度的主要途径
证工件位置精度的安装方法。
第二节 影响加工精度的因素及其分析
图2-1 原始误差
一、加工原理误差
第二节 影响加工精度的因素及其分析
加工原理误差是指采用了近似的成形运动或近似的切削刃轮廓进行 加工而产生的误差。 二、工艺系统的几何误差 1.机床几何误差 (1)机床主轴误差。 1)主轴回转误差。
图2-2 主轴回转轴线的运动误差
一、加工误差的性质 根据一批工件加工误差出现的规律,可将影响加工精度的误差因素 按其性质分为两类: (1)系统误差 (2)随机误差 在顺序加工的一批工件中,若加工误差的大小和方向 在顺序加工的一批工件中,其加工误差的大小和方向 都保持不变或按一定规律变化,这类误差统称为系统误差。 的变化是无规律的,称为随机误差,例如,毛坯误差的复映、残余 应力引起的变形误差和定位、夹紧误差等都属于随机误差。 二、加工误差的数理统计方法
数控机床加工精度的影响因素及提高方法

数控机床加工精度的影响因素及提高方法数控机床加工精度是指机床在进行加工过程中所能达到的准确度和稳定性。
影响机床加工精度的因素非常多,下面将对影响因素和提高方法进行一些阐述。
1. 机床自身的优劣:机床的设计、制造和装配技术对加工精度有直接影响。
优质的机床在设计和制造过程中会注重减小传动误差、提高定位精度和重复定位精度等。
2. 机床的刚性和稳定性:机床的刚性和稳定性对加工精度起着决定性的作用。
刚性不足会导致机床在加工过程中出现振动和变形,从而影响加工精度。
3. 传动装置的精度和可靠性:传动装置的传动误差、反向间隙等都会影响加工精度。
传动装置的精度和可靠性越高,加工精度也越高。
4. 控制系统的精度:数控机床的控制系统对加工精度有直接影响。
控制系统的精度主要包括伺服系统的控制精度、编码器的精度以及数控系统的实时性等。
5. 刀具和夹具的精度:刀具和夹具的精度直接影响加工质量。
刀具和夹具的选择和安装都需要考虑其精度和稳定性。
1. 选用优质的机床:选择优质的机床是提高加工精度的基础。
优质的机床具有高精度、高刚性和高稳定性,能够更好地满足加工要求。
2. 优化加工工艺:通过优化加工工艺,合理设置切削参数和进给速度等,可以减小加工误差,提高加工精度。
4. 优化编程和加工过程:合理优化数控程序和加工过程,减小加工误差。
尽量避免急停和急转等情况,保证加工过程的平稳性和稳定性。
5. 定期进行机床维护和保养:定期进行机床的维护和保养,保证机床的正常运行和精度稳定性。
包括清洁、润滑和紧固等工作。
数控机床加工精度的提高需要从机床自身的优劣、刚性和稳定性、传动装置的精度和可靠性、控制系统的精度以及刀具和夹具的精度等方面进行综合考虑。
通过优化加工工艺、合理选择刀具和夹具、加强编程和加工过程的管理以及定期进行机床维护和保养等措施,可以有效提高数控机床的加工精度。
CNC机床加工中的夹具设计与应用

CNC机床加工中的夹具设计与应用CNC机床加工在现代制造业中扮演着重要的角色,它能够以高精度、高效率完成各种复杂零部件的加工任务。
而夹具作为CNC机床加工过程中不可或缺的辅助工具,对于确保工件的位置、固定和刚性等方面起着至关重要的作用。
本文将探讨CNC机床加工中夹具设计与应用的相关问题。
一、夹具的定义与分类夹具是指在加工过程中将工件固定在CNC机床上的一种装置。
它的主要作用是保证工件的准确定位、稳定固定,从而确保加工质量和效率。
根据不同的应用需求,夹具可以分为以下几类:1. 机床夹具:用于将工件固定在机床上进行加工。
常见的机床夹具包括平口夹具、机床铣削用刀具夹具、分度头夹具等。
2. 刀具夹具:主要用于固定和夹持刀具,保证刀具在加工过程中的稳定性和刚性。
刀具夹具的设计应考虑到刀具的类型、尺寸以及加工要求。
3. 工件夹具:将工件固定在机床上进行加工的夹具,能够确保工件的稳定固定和准确定位。
根据工件的形状和尺寸不同,工件夹具可分为平口夹具、螺纹夹具、气动夹具等。
二、夹具设计的重要性在CNC机床加工中,夹具设计的合理与否直接影响到加工效果和质量。
一方面,夹具设计需要根据具体工件的特点和加工要求进行合理选择,以确保工件在加工过程中的稳定性和精度;另一方面,夹具设计还需要考虑材料的选择、结构的合理优化,以提高夹具的刚性和耐用性。
三、夹具设计的基本原则夹具设计应遵循一定的原则,以保证夹具的可靠性和稳定性:1. 合理选择夹具类型:根据工件的形状、尺寸和加工要求,选择适当的夹具类型,并确保夹具能够提供足够的固定力和刚性。
2. 准确定位和定位:夹具设计中需要确保工件在加工过程中的准确定位和定位,避免加工误差和产生不良影响。
3. 确保夹具刚性:夹具的刚性直接影响加工过程中的稳定性和加工精度。
因此,在夹具的设计中,需要合理选择夹具材料和结构,提高夹具的整体刚性。
4. 简化夹具结构:夹具的结构应简洁、紧凑,减少不必要的部件和连接点。
浅淡自动化加工中机床夹具设计

浅淡自动化加工中机床夹具设计【摘要】现代制造业中,自动化加工技术已经成为提高生产效率和产品质量的重要手段。
而机床夹具作为自动化加工中不可缺少的一环,其设计质量直接影响了加工效率和成品质量。
本文首先介绍了机床夹具设计的基本原则,包括稳固性、精度和易用性等方面。
随后分析了自动化加工对机床夹具设计的需求,探讨了如何在自动化加工中更好地应用机床夹具。
然后提出了一些机床夹具设计的方法,并通过实际案例进行了分析。
展望了机床夹具设计的智能化发展趋势,强调了智能化技术在未来机床夹具设计中的重要性。
通过本文,读者可以更全面地了解机床夹具设计在自动化加工中的重要性,以及未来的发展方向。
【关键词】机床夹具设计,自动化加工,原则,需求,方法,案例分析,智能化,发展趋势,总结,展望未来1. 引言1.1 研究背景机床夹具设计在自动化加工中起着至关重要的作用。
随着制造业的发展和智能化水平的提高,对机床夹具设计的要求也越来越高。
传统的机床夹具设计往往存在着效率低下、精度不高、适应性差等问题,难以满足现代制造业的需求。
对机床夹具设计进行深入研究和改进,成为当前研究的热点之一。
通过科学的机床夹具设计,可以提高加工效率,提高加工精度,降低成本,提高生产质量等。
目前对机床夹具设计的研究仍存在一些局限性,如对自动化加工需求的不完全理解、机床夹具设计方法的不够系统和规范、案例分析的不够充分等。
有必要对机床夹具设计进行进一步的探讨和完善,以更好地适应自动化加工的发展趋势。
1.2 问题提出在自动化加工生产中,机床夹具设计是至关重要的环节。
在实际生产中,往往会出现一些问题,如何更好地应对这些问题是当前亟需解决的难题。
现有的机床夹具设计存在着不够灵活、适应性差的问题,无法满足不同工件的加工需求。
传统的机床夹具设计缺乏智能化和自适应性,无法适应现代自动化生产的要求,使生产效率和质量无法有效提升。
机床夹具设计过程中常常会出现误差和不稳定性,给生产过程带来一定的风险和不确定性。
CNC机床加工中的精度控制与误差分析

CNC机床加工中的精度控制与误差分析在现代制造业中,CNC机床已经成为一种关键设备,广泛应用于各个领域。
CNC机床的加工精度对于保证产品质量至关重要,因此精度控制与误差分析在CNC机床加工过程中起到了至关重要的作用。
一、精度控制CNC机床的精度控制主要包括几个方面,即机床本身的精度、夹具的精度、工具的精度以及工艺参数的控制。
1. 机床本身的精度机床本身的精度是指机床在设计和制造过程中所允许的误差范围。
在机床的设计和制造过程中,需要考虑到各个零部件的加工精度、装配精度以及机床结构的刚性等因素。
通过精密的设计和制造工艺,可以尽量减小机床本身的误差,并且通过校正和调整等方式进一步提高机床的精度。
2. 夹具的精度夹具是用于固定和定位工件的装置,夹具的精度直接影响到工件在CNC机床上加工的精度。
夹具的设计和制造需要考虑到工件的形状和尺寸、固定方式、定位方式以及夹持力等因素。
通过使用高精度的夹具,并采取合适的夹紧力,可以有效提高工件的加工精度。
3. 工具的精度工具的精度包括刀具的直径、长度、刃角和轴线的偏差等方面。
在CNC机床上,切削工具是直接参与加工的关键部件,其精度对于加工结果有很大的影响。
因此,在选择和安装刀具时,需要考虑到刀具的精度要求,并采取相应的措施来保证刀具的精度。
4. 工艺参数的控制在CNC机床加工过程中,工艺参数的控制对于加工精度至关重要。
包括切削速度、进给速度、切削深度、切削力等参数的选择和调整。
通过合理地选择和控制工艺参数,可以有效地减小加工误差,提高加工精度。
二、误差分析在CNC机床加工过程中,误差是不可避免的。
误差主要分为机床本身的误差、工件本身的误差和外部环境的误差等几个方面。
1. 机床本身的误差机床本身的误差是由于机床结构的限制、加工质量和装配精度等因素引起的。
机床本身的误差包括定位误差、运动误差和刚度误差等。
定位误差是由于机床定位系统的精度限制引起的,运动误差是由于机床的传动系统、运动系统和测量系统等因素引起的,刚度误差是由于机床结构的刚度不足引起的。
机床夹具设计方案的分析与研究

1、国内研究成果:中国学者在机床夹具设计方面进行了大量研究,提出了 多种新型的夹具结构,如高速气动夹具、自适应夹具等。这些新型夹具均取得了 良好的应用效果。
2、国外研究成果:外国学者也对机床夹具设计进行了深入研究,如德国的 专家研发了一种智能夹具系统,该系统能够自动识别工件类型并调整夹具的定位 和加紧参数,极大地提高了生产效率。
4、设计夹紧机构:设计师应根据工件的形状和尺寸,确定合适的夹紧机构, 以保证工件在加工过程中不发生移动或旋转。
5、选择材料和表面处理:设计师应根据夹具的使用要求和使用环境,选择 合适的材料和表面处理方式,以提高夹具的使用寿命和抗腐蚀能力。
6、结构设计:在确定定位方案和夹紧机构后,设计师应进行夹具的结构设 计,考虑安装方便、刚性要求、可靠性高等因素,同时应优化结构,减少加工难 度和提高生产效率。
参考内容
机床夹具是机械加工中的重要辅助设备,主要用于固定工件,使其在加工过 程中保持稳定,以便准确、高效地完成各种机械加工操作。本次演示将深入探讨 机床夹具设计的方法和步骤,旨在帮助设计师更好地进行夹具设计工作,提高生 产效率和质量。
一、机床夹具的作用和重要性
机床夹具在机械加工中起着非常重要的作用。首先,夹具能够有效地固定工 件,避免其在加工过程中产生移动或振动,从而提高加工精度和稳定性。其次, 夹具的设计可以简化加工操作,提高生产效率,减少工人劳动强度。此外,好的 夹具设计能够减少废品和不良品的产生,提高产品质量和生产效益。因此,机床 夹具的设计是机械加工过程中不可或缺的一环。
3、其他领域:除了工业和医疗领域,机床夹具在其他领域中也具有广泛的 应用前景。例如,在建筑领域中可以用于对钢筋进行定位和固定;在电子行业中 可以用于对电子元件进行定位和加工。
机床夹具重复定位精度控制
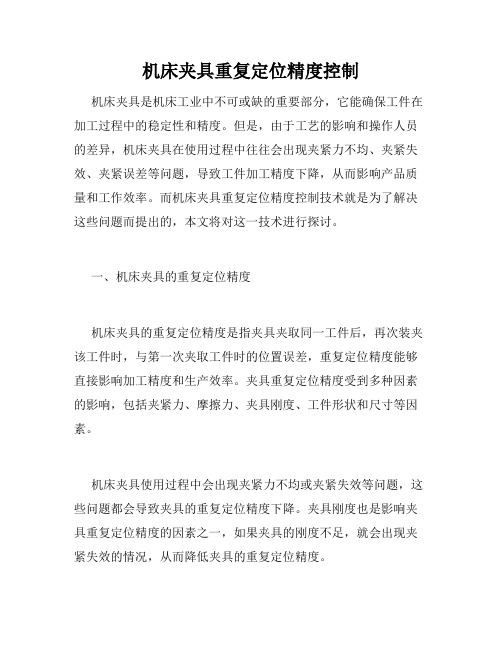
机床夹具重复定位精度控制机床夹具是机床工业中不可或缺的重要部分,它能确保工件在加工过程中的稳定性和精度。
但是,由于工艺的影响和操作人员的差异,机床夹具在使用过程中往往会出现夹紧力不均、夹紧失效、夹紧误差等问题,导致工件加工精度下降,从而影响产品质量和工作效率。
而机床夹具重复定位精度控制技术就是为了解决这些问题而提出的,本文将对这一技术进行探讨。
一、机床夹具的重复定位精度机床夹具的重复定位精度是指夹具夹取同一工件后,再次装夹该工件时,与第一次夹取工件时的位置误差,重复定位精度能够直接影响加工精度和生产效率。
夹具重复定位精度受到多种因素的影响,包括夹紧力、摩擦力、夹具刚度、工件形状和尺寸等因素。
机床夹具使用过程中会出现夹紧力不均或夹紧失效等问题,这些问题都会导致夹具的重复定位精度下降。
夹具刚度也是影响夹具重复定位精度的因素之一,如果夹具的刚度不足,就会出现夹紧失效的情况,从而降低夹具的重复定位精度。
摩擦力是机床夹具定位精度问题中不可忽视的因素。
摩擦力不足会导致工件的移动,而过大的摩擦力则会降低夹具的重复定位精度。
此外,工件的形状和尺寸也会影响夹具的重复定位精度,如工件的表面粗糙度、工件出现凹凸不平或工件弯曲等情况,都会影响夹具的夹紧力和重复定位精度。
二、机床夹具的重复定位精度控制技术为了提高机床夹具的重复定位精度,控制机床夹具的重复定位精度成为机床工业中的一个重要研究方向。
目前常用的控制机床夹具重复定位精度的技术有以下几种:1、使用精度较高的夹具通过选择精度比较高的夹具,能够降低夹具的重复定位精度误差,从而提高工件加工精度。
但是这种方法代价较高,且难以达到完美的效果。
2、夹具调整技术夹具调整技术是通过夹具面的调整,来提高夹具的重复定位精度。
这种方法通常使用的是夹口调整器和夹口保持器等工具对夹具进行调整。
3、夹具状态监测技术夹具状态监测技术是一种实时监测夹具工作状态的技术。
该技术使用夹具状态传感器实时监测夹具的夹紧力、夹紧误差以及夹具变形等数据,并根据数据对夹具进行调整,从而提高机床夹具的重复定位精度。
机床夹具设计中的定位误差计算探讨

机床夹具设计中的定位误差计算探讨
机床夹具设计中的定位误差计算是一个非常重要的问题,其正确的计算方法可以保证机床夹具的定位精度,并且可以提高生产效率和产品质量。
本文将探讨机床夹具设计中的定位误差计算方法。
首先,需要明确的是,机床夹具的定位误差是指实际定位点和理论定位点之间的距离差。
它是由多个因素造成的,如夹具本身的精度、工件形状的偏差、夹紧力的大小等。
在机床夹具设计中,定位误差可以通过以下四个步骤进行计算:
第一步是夹具的设计。
在机床夹具设计中,夹具的定位面应该与工件的轮廓一致,并且要考虑工件的形状、大小和重量等因素。
同时,还要注意夹具的材料选择,以使其具有足够的强度和刚性。
第二步是夹具的加工制造。
机床夹具的加工制造过程需要严格控制夹具的精度和表面质量,以降低定位误差的大小。
加工过程中还需要使用高精度的测量工具对夹具的尺寸进行检测,以确保其符合设计要求。
第三步是工件的夹紧。
在机床夹具夹紧工件之前,需要对工件的表面进行清洁,并且要使用合适的夹紧力。
夹紧力过大或者过小都会导致定位误差的增加。
第四步是测量和调整。
在夹具夹紧工件之后,需要进行精确的测量和调整,以确保工件的定位精度满足要求。
如果存在定位误差,可以通过重新调整夹具、重新夹紧工件或者调整加工程序等方式进行纠正。
总之,机床夹具设计中的定位误差计算是一个较为复杂的过程,需要综合考虑多个因素。
通过严格的设计、制造、夹紧和调整操作,可以控制定位误差的大小,并提高机床夹具的定位精度和生产效率。
机床夹具设计中的定位误差计算探讨
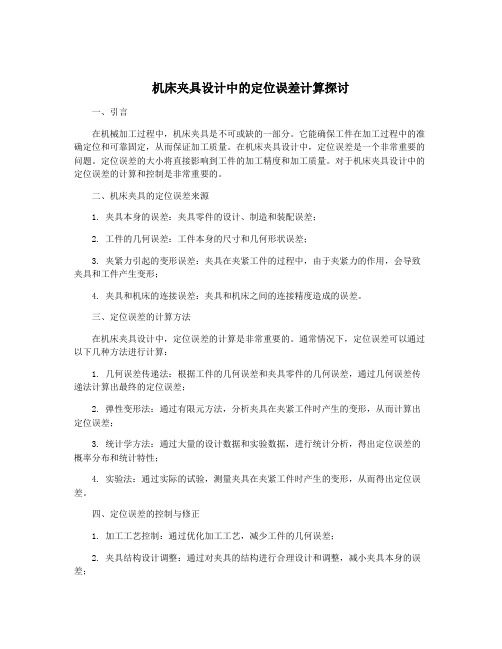
机床夹具设计中的定位误差计算探讨一、引言在机械加工过程中,机床夹具是不可或缺的一部分。
它能确保工件在加工过程中的准确定位和可靠固定,从而保证加工质量。
在机床夹具设计中,定位误差是一个非常重要的问题。
定位误差的大小将直接影响到工件的加工精度和加工质量。
对于机床夹具设计中的定位误差的计算和控制是非常重要的。
二、机床夹具的定位误差来源1. 夹具本身的误差:夹具零件的设计、制造和装配误差;2. 工件的几何误差:工件本身的尺寸和几何形状误差;3. 夹紧力引起的变形误差:夹具在夹紧工件的过程中,由于夹紧力的作用,会导致夹具和工件产生变形;4. 夹具和机床的连接误差:夹具和机床之间的连接精度造成的误差。
三、定位误差的计算方法在机床夹具设计中,定位误差的计算是非常重要的。
通常情况下,定位误差可以通过以下几种方法进行计算:1. 几何误差传递法:根据工件的几何误差和夹具零件的几何误差,通过几何误差传递法计算出最终的定位误差;2. 弹性变形法:通过有限元方法,分析夹具在夹紧工件时产生的变形,从而计算出定位误差;3. 统计学方法:通过大量的设计数据和实验数据,进行统计分析,得出定位误差的概率分布和统计特性;4. 实验法:通过实际的试验,测量夹具在夹紧工件时产生的变形,从而得出定位误差。
四、定位误差的控制与修正1. 加工工艺控制:通过优化加工工艺,减少工件的几何误差;2. 夹具结构设计调整:通过对夹具的结构进行合理设计和调整,减小夹具本身的误差;3. 弹性补偿设计:在夹具设计中,通过弹性补偿设计,降低夹具变形误差;4. 检测与修正:在机床夹具使用过程中,定期进行检测与修正,及时发现和修正定位误差。
保证和提高机床加工精度的方法有哪些
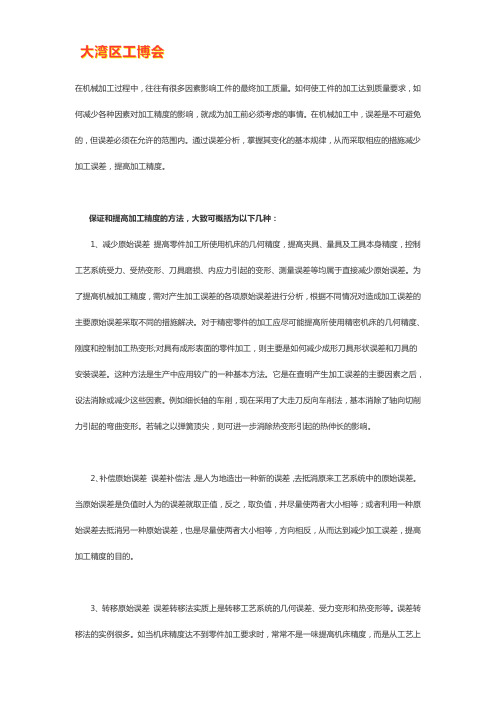
在机械加工过程中,往往有很多因素影响工件的最终加工质量。
如何使工件的加工达到质量要求,如何减少各种因素对加工精度的影响,就成为加工前必须考虑的事情。
在机械加工中,误差是不可避免的,但误差必须在允许的范围内。
通过误差分析,掌握其变化的基本规律,从而采取相应的措施减少加工误差,提高加工精度。
保证和提高加工精度的方法,大致可概括为以下几种:1、减少原始误差提高零件加工所使用机床的几何精度,提高夹具、量具及工具本身精度,控制工艺系统受力、受热变形、刀具磨损、内应力引起的变形、测量误差等均属于直接减少原始误差。
为了提高机械加工精度,需对产生加工误差的各项原始误差进行分析,根据不同情况对造成加工误差的主要原始误差采取不同的措施解决。
对于精密零件的加工应尽可能提高所使用精密机床的几何精度、刚度和控制加工热变形;对具有成形表面的零件加工,则主要是如何减少成形刀具形状误差和刀具的安装误差。
这种方法是生产中应用较广的一种基本方法。
它是在查明产生加工误差的主要因素之后,设法消除或减少这些因素。
例如细长轴的车削,现在采用了大走刀反向车削法,基本消除了轴向切削力引起的弯曲变形。
若辅之以弹簧顶尖,则可进一步消除热变形引起的热伸长的影响。
2、补偿原始误差误差补偿法,是人为地造出一种新的误差,去抵消原来工艺系统中的原始误差。
当原始误差是负值时人为的误差就取正值,反之,取负值,并尽量使两者大小相等;或者利用一种原始误差去抵消另一种原始误差,也是尽量使两者大小相等,方向相反,从而达到减少加工误差,提高加工精度的目的。
3、转移原始误差误差转移法实质上是转移工艺系统的几何误差、受力变形和热变形等。
误差转移法的实例很多。
如当机床精度达不到零件加工要求时,常常不是一味提高机床精度,而是从工艺上或夹具上想办法,创造条件,使机床的几何误差转移到不影响加工精度的方面去。
如磨削主轴锥孔保证其和轴颈的同轴度,不是靠机床主轴的回转精度来保证,而是靠夹具保证。
保证夹具装配精度的加工方法
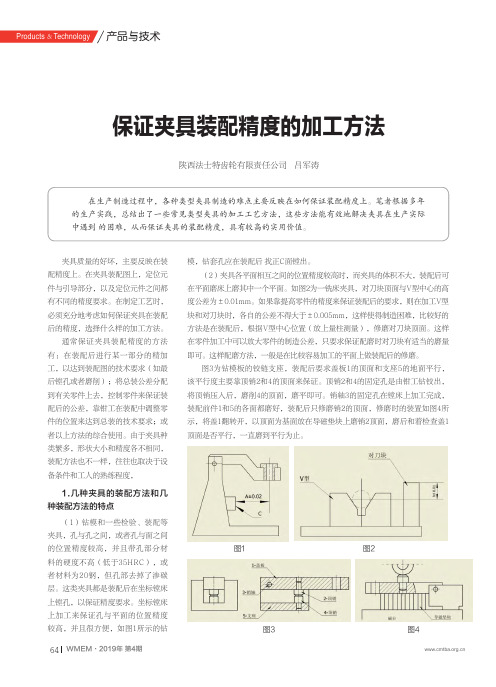
64WMEM·2019年 第4期Products & Technology产品与技术保证夹具装配精度的加工方法陕西法士特齿轮有限责任公司 吕军涛在生产制造过程中,各种类型夹具制造的难点主要反映在如何保证装配精度上。
笔者根据多年的生产实践,总结出了一些常见类型夹具的加工工艺方法,这些方法能有效地解决夹具在生产实际中遇到 的困难,从而保证夹具的装配精度,具有较高的实用价值。
夹具质量的好坏,主要反映在装配精度上。
在夹具装配图上,定位元件与引导部分,以及定位元件之间都有不同的精度要求。
在制定工艺时,必须充分地考虑如何保证夹具在装配后的精度,选择什么样的加工方法。
通常保证夹具装配精度的方法有:在装配后进行某一部分的精加工,以达到装配图的技术要求(如最后镗孔或者磨削);将总装公差分配到有关零件上去,控制零件来保证装配后的公差,靠钳工在装配中调整零件的位置来达到总装的技术要求;或者以上方法的综合使用。
由于夹具种类繁多,形状大小和精度各不相同,装配方法也不一样,往往也取决于设备条件和工人的熟练程度,1.几种夹具的装配方法和几种装配方法的特点(1)钻模和一些检验、装配等夹具,孔与孔之间,或者孔与面之间的位置精度较高,并且带孔部分材料的硬度不高(低于35HRC),或者材料为20钢,但孔部去掉了渗碳层。
这类夹具都是装配后在坐标镗床上镗孔,以保证精度要求。
坐标镗床上加工来保证孔与平面的位置精度较高,并且很方便,如图1所示的钻模,钻套孔应在装配后 找正C面镗出。
(2)夹具各平面相互之间的位置精度较高时,而夹具的体积不大,装配后可在平面磨床上磨其中一个平面。
如图2为一铣床夹具,对刀块顶面与V型中心的高度公差为±0.01mm。
如果靠提高零件的精度来保证装配后的要求,则在加工V型块和对刀块时,各自的公差不得大于±0.005mm,这样使得制造困难,比较好的方法是在装配后,根据V型中心位置(放上量柱测量),修磨对刀块顶面。
项目六:夹具精度校核

教学组织设计
一般工作台中间T型槽精度较高,为H8、H9,常与键配合,靠同侧接触,且两键尽量相互远离。
键与T型槽:型槽名义宽度 h6或h8。
通过过渡盘与车床主轴连接:用于较大夹具。
用“止口”定心,用螺钉固定。
(3)夹具的过程误差(△GC)——因机床精度、
三基面体系控制法:
工件安装于夹具中,将工件与夹具视为一个整体对象,将控制夹具精度的所有测量项目直接对三基面体系提出。
夹具的安装基准:
第一基面:夹具的安装基面;
第二基面:夹具定向键侧面;
七、获得夹具精度的工艺方法
装配后加工法:是保证钻套或镗套轴线和夹具安装基面垂直或平行的最可靠、简便的方法。
(2)找正固定法:先找正位置,然后用螺钉固定,再合件配钻、配绞销钉孔,并压入有过盈量的定位销。
(3)就地加工法——在工件定位加工前首先使用该机床就地精加工夹具定位元件的工作平面。
(5)组成零件精度保证法:尽量减少影响位置精度的零件数目。
浅析数控车床的加工精度

浅析数控车床的加工精度摘要:数控车床作为一种重要的加工设备,其加工精度直接影响到工件的质量和精度要求。
本文通过对数控车床的加工精度进行浅析,探讨了影响加工精度的因素,并提出了提高加工精度的方法与措施。
旨在为数控车床的加工精度提升提供一定的理论支持和实践指导。
关键词:数控车床;加工精度随着制造业的发展,数控车床作为一种高效、精确的加工设备,被广泛应用于各个领域。
而加工精度作为衡量数控车床性能的重要指标,对于满足工件的精度要求具有关键意义。
一、数控车床的加工精度概述数控车床加工精度是指在数控车床上进行加工过程中,工件达到的尺寸、形状和位置的精确程度。
它是衡量数控车床加工质量的重要指标之一。
随着工业技术的不断发展,数控车床在各个领域得到了广泛应用,而加工精度的提高也成为了人们关注的焦点。
首先,尺寸精度是数控车床加工中的一个重要方面。
在工件加工过程中,尺寸精度的高低直接影响着工件能否符合设计要求。
要提高尺寸精度,可以通过控制切削量、刀具和刀具夹持方式、工件夹紧方式等来实现。
只有确保这些因素的合理选择和控制,才能保证工件加工后的尺寸与设计要求之间的偏差尽可能小。
其次,形状精度也是数控车床加工中不可忽视的一点。
在实际应用中,工件的形状往往要求具备一定的几何精度,例如平面度、圆度、圆柱度等。
为了提高形状精度,可以采取优化工艺参数、选择合适的刀具和夹具、控制加工温度等措施。
通过这些方式,能够有效减小工件加工后形状与设计要求之间的偏差,确保工件的几何形状达到精确的要求。
此外,位置精度也是影响数控车床加工精度的重要因素之一。
位置精度主要指工件上各个特定点之间的相对位置精度,例如平行度、垂直度、同轴度等。
要提高位置精度,可以通过优化工艺参数、提高机床刚性、加强夹紧与定位等来实现。
只有确保工件在加工过程中的稳定性和精度,才能保证位置精度的提升。
最后,表面粗糙度也是数控车床加工精度的重要方面之一。
工件表面的光洁程度对于某些特定工件的功能和装配要求有着重要影响。
数控机床加工尺寸控制的方法与技巧
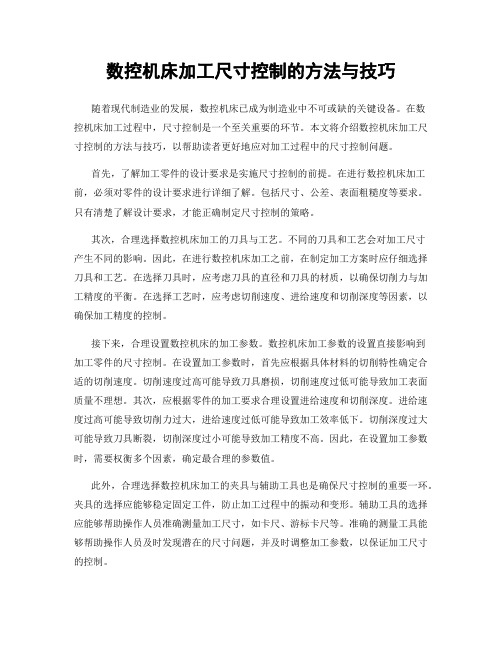
数控机床加工尺寸控制的方法与技巧随着现代制造业的发展,数控机床已成为制造业中不可或缺的关键设备。
在数控机床加工过程中,尺寸控制是一个至关重要的环节。
本文将介绍数控机床加工尺寸控制的方法与技巧,以帮助读者更好地应对加工过程中的尺寸控制问题。
首先,了解加工零件的设计要求是实施尺寸控制的前提。
在进行数控机床加工前,必须对零件的设计要求进行详细了解。
包括尺寸、公差、表面粗糙度等要求。
只有清楚了解设计要求,才能正确制定尺寸控制的策略。
其次,合理选择数控机床加工的刀具与工艺。
不同的刀具和工艺会对加工尺寸产生不同的影响。
因此,在进行数控机床加工之前,在制定加工方案时应仔细选择刀具和工艺。
在选择刀具时,应考虑刀具的直径和刀具的材质,以确保切削力与加工精度的平衡。
在选择工艺时,应考虑切削速度、进给速度和切削深度等因素,以确保加工精度的控制。
接下来,合理设置数控机床的加工参数。
数控机床加工参数的设置直接影响到加工零件的尺寸控制。
在设置加工参数时,首先应根据具体材料的切削特性确定合适的切削速度。
切削速度过高可能导致刀具磨损,切削速度过低可能导致加工表面质量不理想。
其次,应根据零件的加工要求合理设置进给速度和切削深度。
进给速度过高可能导致切削力过大,进给速度过低可能导致加工效率低下。
切削深度过大可能导致刀具断裂,切削深度过小可能导致加工精度不高。
因此,在设置加工参数时,需要权衡多个因素,确定最合理的参数值。
此外,合理选择数控机床加工的夹具与辅助工具也是确保尺寸控制的重要一环。
夹具的选择应能够稳定固定工件,防止加工过程中的振动和变形。
辅助工具的选择应能够帮助操作人员准确测量加工尺寸,如卡尺、游标卡尺等。
准确的测量工具能够帮助操作人员及时发现潜在的尺寸问题,并及时调整加工参数,以保证加工尺寸的控制。
最后,加强质量控制和质量检验是确保尺寸控制的重要手段。
在数控机床加工过程中,质量控制和质量检验是不可或缺的环节。
在加工过程中,应加强对刀具的定期检修和更换,以确保刀具的几何精度。
数控机床技术中的工件夹紧方式与调整方法

数控机床技术中的工件夹紧方式与调整方法数控机床是一种高精度、高效率的加工设备,在现代制造业中具有重要的地位。
而在数控机床的加工过程中,工件的夹紧是一个至关重要的环节。
本文将对数控机床技术中常见的工件夹紧方式以及夹紧调整方法进行介绍和分析。
工件夹紧是指将工件固定在机床上,使其能够在加工过程中保持稳定的姿态,从而确保加工质量和加工效率。
在数控机床中,常见的工件夹紧方式主要有机械夹紧、气动夹紧和液压夹紧。
机械夹紧是一种常见且简单的夹紧方式,通过夹紧螺杆、夹具等机械装置来固定工件。
机械夹紧具有结构简单、成本低等优点,适用于一些简单的工件夹紧。
然而,机械夹紧也存在一些缺点,例如夹紧力不容易控制,夹紧面积小等,限制了其在一些复杂工件上的应用。
气动夹紧是通过气体压缩来产生夹紧力的一种夹紧方式。
气动夹紧具有夹紧力可调、夹具换位快等优点,使其在一些对夹紧力要求较高的工件加工中得到广泛应用。
然而,气动夹紧也存在一些缺点,例如夹具结构复杂、容易受环境温度变化影响等。
液压夹紧是使用压缩液体来产生夹紧力的一种夹紧方式。
液压夹紧具有夹紧力可调、夹紧面积大等优点,特别适用于对夹紧力要求较高的工件加工。
液压夹紧的主要缺点是液压系统的复杂性和维护成本较高。
在数控机床加工中,调整工件夹紧是确保加工质量的重要环节。
常见的夹紧调整方法主要有手动调整和自动调整。
手动调整是指在加工过程中,操作工人通过调整夹具、螺旋杆等手动装置来实现工件夹紧力的调整。
手动调整的优点是操作简单、灵活性强,适用于一些加工要求不高的工件。
然而,手动调整也存在人为差异大、调整难以精确等缺点,限制了工件加工的精度和稳定性。
自动调整是通过数控系统控制夹具、液压系统等自动装置来实现工件夹紧力的调整。
自动调整的优点是可精确控制夹紧力、提高加工精度和稳定性,适用于对加工质量要求较高的工件。
然而,自动调整也存在系统复杂、投资成本高等缺点。
为了实现工件的稳定夹紧和高精度加工,常常采用多种夹紧方式的组合。
机床夹具平行度控制

机床夹具平行度控制随着科技不断发展,机械加工行业也在迅速发展。
在机械加工过程中,夹具扮演着非常重要的角色。
夹具是机床上固定和夹持工件以使之稳定加工的装置。
然而,夹具本身的制造和组装质量也会影响到零件的质量和精度。
因此,为了提高加工精度,夹具的平行度控制是非常必要的。
一、什么是夹具平行度控制?夹具平行度控制是指对夹具加工时的平行度进行调整,使得夹紧工件的时候,工件在夹具中处于平行状态,这样可以保证工件在切削过程中的平衡性、稳定性和精度。
二、为什么要进行夹具平行度控制?我们知道,如果夹具的平行度不够好,工件在夹具中的位置就会不稳定,也就是说,会产生摆动和变形。
而摆动和变形是很难被观察到的,因此容易被忽略。
这样一来,在加工的时候会导致零件的精度下降,从而影响到加工的质量,最终导致不良的产品。
因此,为了保证加工的质量,夹具的平行度控制是非常必要的。
三、夹具平行度控制的方法1. 直角规检测法直角规也叫方角尺,它是一种可以量测直角的量具。
在夹具平行度检测中,我们可以使用直角规检测夹具的平行度。
具体操作方法如下:(1)将直角规对准夹具的面板,使之与面板接触。
(2)移动直角规到夹具另外一块面板上,观察是否还能继续保持平行。
如果保持平行,则夹具平行度就合格。
2. 电子投影仪检测法电子投影仪是一种主要用于测量的高精度光学仪器。
在夹具平行度检测中,可以使用电子投影仪来检查夹具的平行度。
具体操作方法如下:(1)将电子投影仪校准至零,让其光源对准夹具面板。
(2)移动电子投影仪至夹具的另外一块面板上,观察光线是否能够保持平行。
如果光线能够保持平行,则夹具平行度合格。
3. 光栅尺检测法光栅尺也叫光电码尺,是一种测量位移的高精度量测装置。
在夹具平行度检测中,我们可以使用光栅尺来检查夹具的平行度。
具体操作方法如下:(1)在夹具的面板上放置一根平整的均匀粗细的杆状物。
(2)在杆状物上粘贴光栅尺,并将其与夹具面板上的光栅尺靠近。
(3)对杆状物作水平移动,观察光栅尺的显示值变化情况。
CNC机床加工中的加工精度控制方法

CNC机床加工中的加工精度控制方法在CNC机床加工中,加工精度的控制是至关重要的。
精确的加工能够确保零件尺寸的准确性和质量的稳定性。
本文将介绍几种常用的加工精度控制方法,帮助读者更好地理解和应用于实际生产中。
一、选用高精度CNC机床及工具在选择CNC机床时,应注重其加工精度和重复定位精度。
高精度的机床能够提供更好的工件精度和表面质量。
同时,使用质量优良的刀具、夹具以及其他加工工具也能够提高加工精度。
二、合理规划工艺参数在加工过程中,合理规划和控制工艺参数对于实现加工精度的控制至关重要。
例如,合理选择切削速度、进给速度和切削深度等参数,能够有效地控制切削力和温度,确保加工过程的稳定性和一致性。
三、控制机床刚度和热变形机床的刚度和热变形是影响加工精度的重要因素。
通过提高机床刚度,可以降低振动和变形,提高加工精度。
此外,控制机床的温度分布,采取散热和稳定温度的措施也能够减小热变形,提高加工精度。
四、准确测量和调整工件在CNC机床加工过程中,及时准确地测量工件尺寸是保证加工精度的重要环节。
通过使用高精度测量工具,如三坐标测量仪等,可以对加工过程进行实时监控和调整,确保工件尺寸的准确性。
五、合理选择刀具与切削液选择合适的刀具和切削液对于加工精度的控制同样至关重要。
高性能的刀具能够提供更好的切削质量和稳定性,而适当的切削液能够降低切削温度和摩擦,减少刀具磨损,提高加工精度。
六、制定严格的工艺控制和操作规程制定严格的工艺控制和操作规程对于实现加工精度的一致性和可控性非常重要。
在制定过程中,应明确各个环节的要求和标准,并加强对操作人员的培训和管理,确保每个环节的工艺参数得到准确执行,从而实现加工精度的控制。
七、不断改进和优化加工精度的控制是一个不断探索和改进的过程。
企业应当注重科研创新,引进新的加工技术和设备,改进工艺和工具,提升加工精度。
同时,加强与供应商和客户的沟通与合作,不断改进产品质量和精度要求,以满足市场需求。
数控机床刀柄夹具的调整与固定方法
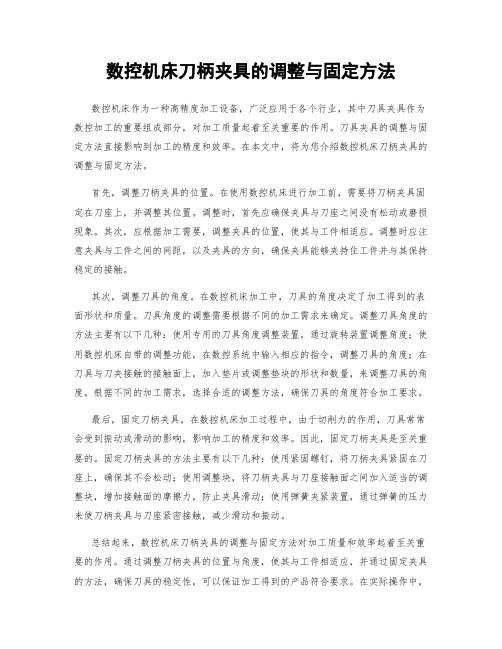
数控机床刀柄夹具的调整与固定方法数控机床作为一种高精度加工设备,广泛应用于各个行业,其中刀具夹具作为数控加工的重要组成部分,对加工质量起着至关重要的作用。
刀具夹具的调整与固定方法直接影响到加工的精度和效率。
在本文中,将为您介绍数控机床刀柄夹具的调整与固定方法。
首先,调整刀柄夹具的位置。
在使用数控机床进行加工前,需要将刀柄夹具固定在刀座上,并调整其位置。
调整时,首先应确保夹具与刀座之间没有松动或磨损现象。
其次,应根据加工需要,调整夹具的位置,使其与工件相适应。
调整时应注意夹具与工件之间的间距,以及夹具的方向,确保夹具能够夹持住工件并与其保持稳定的接触。
其次,调整刀具的角度。
在数控机床加工中,刀具的角度决定了加工得到的表面形状和质量。
刀具角度的调整需要根据不同的加工需求来确定。
调整刀具角度的方法主要有以下几种:使用专用的刀具角度调整装置,通过旋转装置调整角度;使用数控机床自带的调整功能,在数控系统中输入相应的指令,调整刀具的角度;在刀具与刀夹接触的接触面上,加入垫片或调整垫块的形状和数量,来调整刀具的角度。
根据不同的加工需求,选择合适的调整方法,确保刀具的角度符合加工要求。
最后,固定刀柄夹具。
在数控机床加工过程中,由于切削力的作用,刀具常常会受到振动或滑动的影响,影响加工的精度和效率。
因此,固定刀柄夹具是至关重要的。
固定刀柄夹具的方法主要有以下几种:使用紧固螺钉,将刀柄夹具紧固在刀座上,确保其不会松动;使用调整块,将刀柄夹具与刀座接触面之间加入适当的调整块,增加接触面的摩擦力,防止夹具滑动;使用弹簧夹紧装置,通过弹簧的压力来使刀柄夹具与刀座紧密接触,减少滑动和振动。
总结起来,数控机床刀柄夹具的调整与固定方法对加工质量和效率起着至关重要的作用。
通过调整刀柄夹具的位置与角度,使其与工件相适应,并通过固定夹具的方法,确保刀具的稳定性,可以保证加工得到的产品符合要求。
在实际操作中,需要根据不同的加工需求选择合适的调整和固定方法,不断提高加工技术和加工质量。
- 1、下载文档前请自行甄别文档内容的完整性,平台不提供额外的编辑、内容补充、找答案等附加服务。
- 2、"仅部分预览"的文档,不可在线预览部分如存在完整性等问题,可反馈申请退款(可完整预览的文档不适用该条件!)。
- 3、如文档侵犯您的权益,请联系客服反馈,我们会尽快为您处理(人工客服工作时间:9:00-18:30)。
-■ l
机床夹 具制造 中精 度控制 的几种 加工方重 型装 备有 限公 司 沈 阳 1 0 2 ) 三 0 7 1
[ 摘 要] 针对 机床 夹 具 的制造 、装 配 、定位 等 重要 环节 , 据 实践经 验 总 结出 三种 保证 夹 具精 度 的工 艺方 法, 根 并给 出 了具体 应用 实 例 : 这些 方法 能有 效 地提 高机床 夹 具 的精度 , 而保 证产 品质 量, 从 具有 相 当 的实用 价值 。 [ 关键 词] 夹具 制造 精度 工艺 方法 中图分类号 :M 2 .7 T 9 30 文献 标识码 : A 文章编 号 :0 99 4 (0 03 —3 30 10 — 1X2 1 )1 05 — 1
称度 精度 要求 很 高。V型块传 统制 造方 法, 般是 整体 制造 , 一 两斜 面的最 终精 加工 , 在平 面磨 床 利用 精密 正弦 夹 具和 V型 导磁铁 完 成 。然 这种 加工 方法 常 很 难保 证 v型对 称 度 达到 理 想状 态 。 用 镜像加 工法 时, 先将 V 型块先 制成 半成 品单体, 沿对称 面截 断后, NI 出 螺孔 , 定 向键和 联接 螺栓 组装 成组合 式 V 用 型块 。 这种 加工 方法 无需 高度精 度 机床 , 只需 借助 普通机 床, 型块 的对称 度就 能可 以达到 很 高精度, 而 V 因而 具有 相 当的实 用价值 。 实践证 明, 成组 加工 法对 具有对 称性 结构 或多件 重 复的夹 具 元 件 的 制造 十分 奏 效 。 3 临床加 工 法 所 谓临床 加工 法, 就是使 用 该夹具 的机床 切削 功能去 切削 另一个 部件, 以 消除彼 此 之间 的位置 误差 , 证各 部件 占据理 想 的位置, 保 从而 提高 夹具制 造精 度方法 。这 种方 法不仅 在夹 具 的定位 元件加 工过 程和 实 际使用过 程 中得 到广 泛应 用, 且还 常 在机 床 组装 中用 来 保证 机床 最 终精 度 。 而 车床 常用 附件三爪 卡盘长 时间使用 后, 出现卡爪 支承面 的中心与车床 主 会 轴中心 轴 线产生 不 同轴 的现 象, 时三爪 卡盘 夹持 的加工 工件 表面, 这 与定位 基 准面也 将产 生不 同轴 , 从而造 成工 件的 2i误 差超 差 。解 决此类 问题 , 采用 h 可 I 临床加 工法 来加 以修 正 。 利用 车床本 身主 轴 中心 轴 线的 回转精 度, 去校正 三爪 卡盘 中心对 主轴 轴线 的偏心 , 可大 大提 高零件 的加 工质量 。 内圆 、 圆磨 床精 外 度 要求 很高 的磨轴 类和 磨 内表面 夹具 、 床的芯 轴类 夹具 、 车 铣床 的工 作 台面、 平 面磨 床 的 电磁 吸盘 , 可采用 临床 2 i法 , 均 h 来提 高 定位元 件 工作表 面精 度 。 这 种方 法可 以消 除夹具 的制 造 、 装配 、 安装 各环 节的误 差, 终获得 极高 的精 最 度 。当然 , 临床 加工法 , 只有 具备 临床加 工条 件 的机床才 能使 用 。设 计人 员要 求 使用 这种工 艺方 法来 设计 夹具 时, 在 夹具总 图上 注 明“ 图样尺 寸 留精 加 应 按 工 余 量 到使 用 机床 上 最 终 加 工 ” 。 结语 机床 夹具主 要元件 的精 度和 夹具 的装配精 度, 比被 加工 的工件 要高, 而且 又 是单件 生产 , 以夹 具精度 大 都在部 件装 配或 总装 过程 中采用 装配加 工法 、 所 临床 修 正法和 成组 加工法 来保 证 。 在夹 具设 计时 , 须熟 悉夹具 制造 工艺方 面 必 这一 特 点, 并在 结构 设计 、 尺寸 和形 位公 差标注 、 具元件 加工 和技 术条件 制 夹 定等 各方 面适 应这 一要 求 。 参 考 文 献 [] 贾 镜如 . 削加工 中 的液压夹 紧装 置 [] 组合 机床 与 自动化 加工技 1 切 J. 术, 92 (1. 18, 1) [ ] 张广乐 . 压夹 紧技术 [ ] 现代 制造, 0 4 ( 8 . 2 液 J. 2 0, 1 ) []B rhr u ta . 3 en adK tk t高效夹具系 统缩短加工 时间 [] 现代制造,20 , J. 07
夹具 是机床 切 削加工 的 重要工 艺 装备 。使用 夹具 的首要 目的, 是保 证机 械 零件尺 寸 ( 形状 ) 精度及 位置精 度, 而机械 零件 的制 造精度 , 很大程 度上取 决 于加工 该零件 的机床 夹具 能否 到达设 计精度 的 要求 。 具属单 件加 工, 夹 又加 之 有 较高 的精度要 求, 决定 了夹具 制造不 能像 一般机 械制 造那 样, 这 先按零 件 图 制造 出所有 零件然后 组装, 这样 难 以满 足装配 图提 出的各种 尺寸及 形位 公差 要 求 。要保 证夹具 制造精 度, 须采取 特殊 的工 艺方法 。 文 以V 块设 计制造 必 本 型 相 关 的实例 为例 , 有关保 证 机床 夹 具精 度 的 3种 实用 工 艺方 法 介绍如 下 。 将 1装配加 工 法 这是 一种 常用 的工艺 方法 , 在钻 夹 具 、车 夹 具及磨 夹 具设计 制 造 中得 到 了非常广 泛的应 用 。 夹具制 造 中, 在钻 为了到达 钻 套中心 轴线 对安 装基 面的垂 直度 要求 , 唯一 的工艺方 法就 是采 用装配 后精 镗导 向孔 。这 种装 配后精 镗 , 对 铰链 式 连接 的活动 钻模 板上 的钻 套底 孔 以及翻 转式 钻模 制造 上 , 作用 尤 为 明 显 。它能 消除组 成零件 累计 的尺 寸和 形状误 差, 钻套 孔 d 的 中心轴 线对 安装 1 基准 面 A的垂 直度 , 和对 v型定位 块 中心平 面 的位 置度 精度 要求 , 都是在 夹具 装配 后拧 紧蝶形 螺母 。在坐 标镗床 上, 正 V型定 位块 的 中心 平 面, 找 在钻模 板 上镗 衬套底 孔而 得到 的。这种 工艺 方法 , 本上 是靠坐 标镗床 的精度, 接保 基 直 证夹 具所 要求 的位 置精度 因此, 它是 保证钻 套 中心 轴线 和夹具 安装 基准面 垂直 度最有 效 的方法, 所 用钻 镗类 夹具 的导 向套底 孔, 是采 用这 种工 艺方 法加 工 的。 都 夹 具上 的定位元 件, 也可采 用装 配加 工法, 来保 证元件 在夹 具上 的准确 位 置尺 寸 。两 个 v型块 的位置 由高度尺 寸 H 、水 平尺 寸 L 来决 定, 夹具 设计要 求 两v 型块 的定位面 必须 与工件 保持 完全接 触, 同时又要 保证 两平 行度 要求 。 这 两个平 行度 用一个 双 点划线所 表示 的标 准芯棒 来检 验 要 保证 H 和两平 行 、L 度, 夹具 制造 时, 先把 两 v型 块做 成斜 面, 在 可 并留足 够 的磨加 工余 量 的半成 品 。把 V型块拼 装到 夹具 体, 圆锥销 将 V型 块和夹 具体 两者 固定 , 用 在工具 磨 床或 导轨磨床 上 以A B 定位基 准, v 、 为 对 型块 9 。斜 面进 行磨 削加 工, O 以满 足 H、L和 两 平行 度公 差 要 求 。 此外 , 装配后 磨削 的精加 工方 法, 常用 来获 得车床 、磨 床夹 具的 回转定 位 元件 表面 与 安装 基 准 面之 间的位 置 精度 。 2成组 加工 法 在夹 具制造 时, 巧妙地 应用成 组加工 , 可起 到 其他加 工方法 无可 替代 的作 用。所谓成 组加 工法, 指在加 工夹 具元件 时 , 次 同时加 工 出多个元 件上 相 是 一 同的结 构要素 , 些结构 要素通 常 是几何 尺寸 或截面 形状 、 此之 间 的相对位 这 彼 置。相 同加 工条件 , 使夹 具元件 的质 量和 互换性 容易 得到 保证, 而可 提高夹 从 具整体 的制造精 度 。根据制 造方 法不 同, 可将 成组加 工可 分为 “ 合对 加工 ” 和 “ 镜像 加工 ”两种 具体 工艺 方法 。 “ 对 加 工 ”法 , 是 指 夹 具 中 凡 成对 的元 件 均 采 用 “ 磨 ” 合 合 合 、“ 镗” “ 、 合钻 ” “ 、 合绞 ”等方 式进 行成 对加工 , 以消 除工件 问 的尺寸误 差和 位置 偏 差。夹 具制造 实践 中, 常见 的定位 销 的配制 、导 向孔 的镗 削、等 高块 的磨 削 等, 就是 具体 的应用 实例 。 “ 镜像 加工 ”法 , 是指 对一 些具 有对 称结 构 的夹具 元件 , 以 以其 对称 面 可 为 界, 先加工 出双倍 长度, 并加 适 当余 量 的工件, 然后 沿对 称面 切断, 再经 适 当 加 工后, 利用镜 像 原理将 两对称 件组 合成 形, 以消除对称 度误 差 。夹 具元 件制 造 中常见 的 V型定位 块, 设计 上需 要其 具有 自动对 中功 能, 二个 工作斜 面 的对