全手工封装技术
SMT及焊接解析
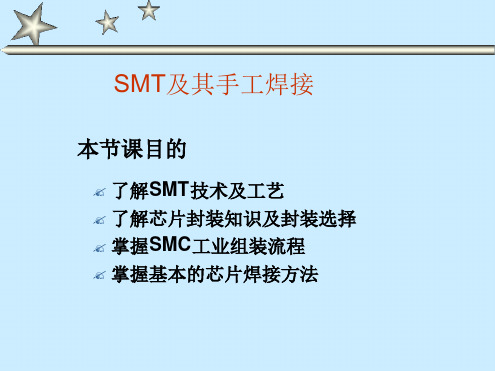
二、SOP 小外形封装
? SOP(Small Out-Line Package 小外形封装) 是一种很常见的元器件形式。引脚从封装两侧 引出呈海鸥翼状 (L字形)。材料有塑料和陶瓷两 种。始于 70年代末期。
3、封装的分类
三、QFP塑料方型扁平式封装和 PFP塑料扁平组件式封装
QFP(PlasticQuadFlatPackage)封装的 芯片引脚 之间距离很小,管脚很细, 一般大规模或超大型集成电路都采用
3、封装的分类
? 芯片的封装技术已经历了好几代 的变迁,从 DIP、QFP、PGA、 BGA到CSP,技术指标一代比一代先进。 – 芯片面积与封装面积之比越来越接近于 1, – 适用频率越来越高 – 耐温性能越来越好 – 引脚数增多,重量减小,可靠性提高,使用 更加方便等等。
3、封装的分类
? 一、DIP封装 70年代流行的是双列直插封装, 简称DIP(Dual In-line Package)。
1.什么是封装
? 封装技术其实就是一种将集成电路打 包(包装)的技术。
? 封装,就是指把硅片上的电路管脚, 用导线接引到外部接头处,以便与其它器件连接.
? 封装形式----指安装半导体集成电路芯片用的外壳。它不
仅起着安装、固定、密封、保护芯片和增强导热性能的作用,而且 还是沟通芯片内部世界和外部电路的桥梁——芯片上的接点用到线 连接到封装外壳的引脚上,这些引脚又通过印制电路板上的导线与 其它器件建立连接。
SMT及其手工焊接
本节课目的
? 了解SMT技术及工艺 ? 了解芯片封装知识及封装选择 ? 掌握ቤተ መጻሕፍቲ ባይዱMC工业组装流程 ? 掌握基本的芯片焊接方法
几个术语
? SMT----- Surface Mounted Technology ? SMD-----Surface Mounted Device ? SMC-----Surface Mounted Component
封装工艺介绍
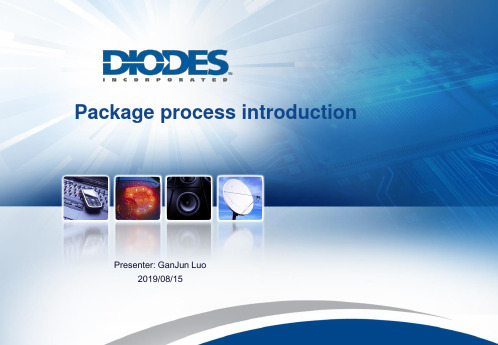
导热电性能好,但CTE失配严重, 在焊接中易产生热应力,芯片易开 裂,一般只用于小芯片装片
工艺通用性强,适用于导电热性要
导电胶(Epoxy)
环氧树脂(填充银)化 芯片不需要预处理,粘结后固 求不高的器件,因为其导热电性能
学结合
化出来或热压结合
比共晶、铅锡银装片差,吸潮易形
成空洞,开裂。
软焊料(Soft Solder) 铅锡银焊料合金反应
芯片背面镀银或金或镍,镀银 基岛更优,轨道气保护加热
导热电性能好,但工艺复杂,焊料 易氧化,一般用于大电流大功率器 件
玻璃胶(DAF)
绝缘玻璃胶物理结合 上胶加热至玻璃熔融温度
成本低,适用于超薄芯片叠封,焊 线前需要洗plasma去除有机成分
Die Attach
Page 12
粘着剂的工艺流程
Die Attach
Post Mold Cure Laser Marking
De-junk De-flash Plating Trim/Form
Test Packing
Page 4
Laser Marking
Before
After
Wafer Grinding
Purpose:
Make the wafer to suitable thickness for the package
Wafer Saw
Page 8
Wafer Saw Technology
Technology
Advantages or Characteristics
Range of applic ation
使用微细金刚石颗粒构成的磨轮刀片,以每分钟3万转到4万
BD(Blade Dicing)
ALLEGRO封装教程

一、手工制作封装1、打开“PAD Designer”如下界面按实际需求填好后保存,如保存为cd160X30注:阻焊层比助焊层大约1MM即可2,启动Allegro PCB Ediror 选择“File”-“New”弹出对话框3、点击OK进入编辑界面,选择“SETUP”-“Design Parameters”弹出窗口4、选择“SETUP”-“Grids”打开以下窗口设置5.选择“SETUP”-“User Preference”打开以下界面6,添加管脚焊盘。
选择“LAYOUT”---“PINS”或者图标,然后设置控制面板”options”标签页中的相关选项7,设置好后,在命令窗口中输入放置的坐标如( x 0 0)按回车键确定添加。
注意,输入坐标时x要用小字母加空格8焊盘放置完成后添加Place_Bound_Top(放置约束)。
选择”SETUP”—“Areas-“—“Package Boundary”选项。
设置控制面板的”Options”然后用坐标输入放置9、设置封装限制高度,选择”SETUP”—“Areas-“—“Package Height”选项。
然后选择该封装。
设置控制面板的”Options”10、添加丝印外框。
选择“Add”—“Line”选项,设置控制面板中“Options”然后按封装要求画出丝印框11.添加标签,选择“LAYOUT”--“LABELS”—“RefDes”选择。
设置控制面板中“Options”单击屏幕区域出现文本输入框,输入标签如U* j* REF 右键单击选择“DONE ”12,选择“File”---“Save”选项,保存元件封装二、O RCAD和ALLEGRO交互式布局1,打开原理图,选中文件,然后选择“options”-----“Preferences”出现下界面三、更改坐标原点的方式1、打开文件,选择“SETUP”--“Design Parameter Editor”弹出以下界面2,第2种方式,选择“SETUP”—“Change Drawing Origin”然后单击需要设置成为坐标原点的地方四、O r CAD导出网络表打开原理图文件,选择设计文件,选择“Tloos”--“Create Netlst”弹出以下界面五、ALLEGRO导入网络表1,设置路径:选择“SETUP”-“User Preference”打开以下界面2、选择“File”--“Import”---“Logic”弹出以下界面。
成品半成品保护措施方案

成品半成品保护措施方案在制造和生产过程中,成品和半成品的保护是至关重要的。
无论是大规模生产的工业产品,还是小规模制作的手工艺品,保护措施的质量和有效性都直接关系到产品的质量和市场竞争力。
本文将探讨成品和半成品的保护措施,并提出几个可行方案。
一、防护包装成品半成品的防护包装是最常见的保护措施之一。
这种包装可以保护产品免受外界环境的影响,如湿气、光线和温度变化。
同时,防护包装还能够减少运输过程中的摩擦和碰撞,防止产品受损。
例如,在运输玻璃制品时,可以使用泡沫塑料或气囊充气包装来保护产品的完整性。
二、环境控制在生产过程中,温度、湿度和灰尘等因素对成品和半成品的质量和保护至关重要。
通过建立恰当的环境控制措施,可以降低产品受到这些因素影响的风险。
例如,在制造电子产品时,可以建立无尘室,以减少灰尘对电子元件的侵害。
另外,还可以通过控制温度和湿度来保持成品和半成品的稳定状态。
三、封装技术利用封装技术对成品和半成品进行保护是一种常见的方法。
封装技术能够将产品封装在一个安全的外壳中,以防止外部因素的侵害。
例如,在食品行业,将产品封装在真空袋或密封罐中,可以延长产品的保质期和营养价值。
在电子产品行业,将电路板封装在塑料外壳中,可以保护电路板免受灰尘和湿气的损坏。
四、监测和检测成品和半成品的保护不仅仅包括在生产和运输过程中的措施,还需要进行监测和检测。
通过实时监测,可以及时发现可能的问题,并采取措施进行修复。
例如,在电子产品制造中,可以使用温湿度传感器监测环境条件,及时发现温度过高或湿度过大的情况,以避免产品受损。
五、培训和教育成品半成品保护的成功不仅仅依靠技术手段,还需要培训和教育的支持。
在整个生产链条中,员工需要了解产品保护的重要性,并采取正确的操作和管理措施。
通过培训和教育,可以提高员工的认识和意识,避免人为因素对成品和半成品的损害。
六、应急措施即使在采取了所有必要的保护措施后,意外事故仍然可能发生。
因此,制定和执行应急措施也非常重要。
IC封装测试工艺流程

IC封装测试工艺流程1.芯片准备:在IC封装测试工艺流程开始之前,需要对待封装的芯片进行准备工作。
这包括将芯片切割成单个的小尺寸芯片,然后对其进行清洗、去除尘埃等净化处理。
2.焊接:在将芯片封装前,需要在芯片上焊接金线。
这些金线用于将芯片内部的各个功能单元与外界的引线相连。
这个过程需要使用特殊的焊接设备,确保焊接质量。
3.封装:接下来,将芯片放置在封装材料中。
封装材料可以是塑料、陶瓷等,不同的材料可以提供不同的保护性能。
芯片与封装材料之间还需要使用金线或焊膏进行连接。
封装过程可以是手工操作,也可以是自动化机器进行。
4.封装测试:在完成封装后,需要对封装好的芯片进行测试以确保其质量和性能。
这些测试可以包括外观检查、尺寸测量、电气性能测试等。
测试过程需要使用专业的测试设备和工艺流程。
5.校准:如果芯片测试结果不符合要求,可能需要对测试设备进行校准,以确保测试的准确性和一致性。
校准可以通过标准器件或其他校准设备进行。
6.封装精调:如果芯片测试结果仍然不达标,可能需要对封装工艺进行精细调整。
这意味着需要调整封装材料的配方、焊接参数、封装温度等。
精细调整可以通过试验和实验确定最佳的封装工艺参数。
7.标识与包装:在完成封装测试后,需要对封装好的芯片进行标识和包装。
标识可以包括芯片型号、生产日期、批次号等信息。
包装可以是常规的芯片包装方式,如管装、带装等。
包装后的芯片可以进行存储或运输。
8.品质管理:在整个封装测试工艺流程中,需要对每个步骤进行严格的品质管理。
这包括设立合理的工艺流程、制定工艺参数标准、对工艺设备和材料进行检验等。
品质管理可以通过ISO9001等质量管理体系认证。
总结:IC封装测试工艺流程是将芯片封装为成品集成电路的关键过程。
通过逐步进行焊接、封装、测试、校准、精细调整、标识和包装等步骤,可以确保封装好的芯片的品质和性能。
并且通过切合实际的品质管理措施,可以提高封装工艺的稳定性和一致性。
太阳能电池组件封装工艺

太阳能电池组件封装工艺太阳能电池组件的制造过程中主要有以下一些步骤:激光划片—光焊(将电池片焊接成串)—手工焊(焊接汇流条)—层叠(玻璃—EVA—电池—EVA—TPT)—中测—层压—固化—装边框、接线盒—终测。
1、激光划片:太阳能电池每片工作电压0.4-0.5V左右(开路电压约0.6V),将一片切成两片后,每片电压不变;太阳电池的功率与电池板的面积成正比(同样转化率下)。
根据组件所需电压、功率,可以计算出所需电池片的面积及电池片片数,由于单体电池(未切割前)尺寸一定(有几种标准),面积通常不能满足组件需要,因此,在焊接前,一般有激光划片这套工序,切割前,应设计好切割路线,画好草图,要尽量利用切割剩余的电池片,提高电池片的利用率。
切片时的具体要求:1.1、切片时,切痕深度一般要控制在电池片厚度的1/2—2/3,这主要通过调节激光划片机的工作电流来控制。
如果工作电流太大,功率输出大,激光束强,可以将电池片直接划断,容易造成电池正负极短路。
反之,当工作电流太小,划痕深度不够,在沿着划痕用手将电池折断时,容易将电池片弄碎。
1.2、太阳电池片价格较贵,为减少电池片在切割中的损耗,在正式切割前,应先用与待切电池片型号相同的碎电池片做试验,测试出该类电池片切割时激光划片机合适的工作电流I0,这样正常样品的切割中划片机按照电流I0工作,可以减少由于工作电流太大或太小而造成损耗。
1.3、激光划片机激光束进行路线是通过计算机设置XY坐标来确定的,设置坐标时,一个小数点和坐标轴的差错会使激光束路线完会改变,因此,在电池片切割前,先用小工作电流(使激光能被看清光斑即可)让激光束沿庙宇的路线走一遍,确认路线正确后,再调大电流进行切片。
1.4、一般来说,激光划片机只能沿XY轴方向进行切割,切方形电池片较方便。
当电池片切成三角形等形状时,切割前一定要计算好角度,摆好电池方位,使需要切割的线路沿X或Y方向。
1.5、在切割不同电池片时,如果两次厚度差别较大,调整工作电流的同时,注意调整焦距。
PADS元件封装制作

库文件 名.pt4
可以通过 Import 与 Export 命令将 Part Type 导入和 导出。 使用的文件后缀名 称是.p。形式为: 名称.p
是 PowerLogic 中的逻辑封装 CAE Decal 库。 库文件
CAE 库
必须与 Part Type 建立对应关系。
名.ld4
可以通过 Import 与 Export 命令将 Part Type 导入和 导出。 使用的文件后缀名 称是.c。形式为: 名称.c
根据我们上一小节的介绍在其它操作之前首先应该选好目标元件库在下面的例子中我们选择的是系统自带的common打开元件库管理窗口除了对元件库进行整理操作外有时需要对照元件名称进行查询然后对查询到的元件进行编辑修改edit命令如果没有找到目标元件可能需要重新设计new命令在powerpcb下只能对decals与parts库进行edit操作和new操作
图 9-1 各元件库功能说明
例如我们新建了一个名为 FTL 的库后,在 Padspwr 的 Lib 目录下就会同时出现四个名称相同
但后缀名各异的元件库,如图 9-2 分别为: FTL.pt4:Part Type 元件类型库 FTL.pd4:Part Decal 元件封装库 FTL.ld4:CAE 逻辑封装库 FTL.ln4:Line 线库 这是 Padspwr 的 Lib 目录下的所有元件库的列表,在这里可以找到所有元件库,包括系
Decal 与 CAE Decal。 Part Type 名。或者说软件在上述两个系统下调用元件时
而且一个 Part Type 使用的都是 Part Type。
名下可以分配多个 注意:
Part Type
Part Decal(因为一
1.Part Type 既可以在 PowerLogic 下也可以在
LED封装技术及结构
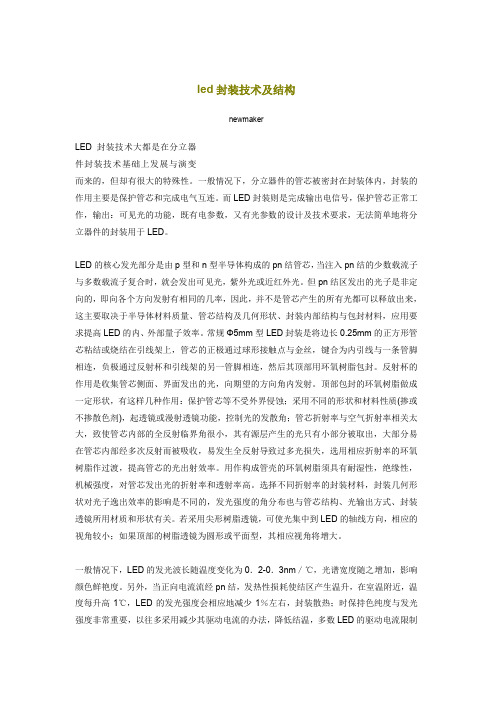
led封装技术及结构newmakerLED封装技术大都是在分立器件封装技术基础上发展与演变而来的,但却有很大的特殊性。
一般情况下,分立器件的管芯被密封在封装体内,封装的作用主要是保护管芯和完成电气互连。
而LED封装则是完成输出电信号,保护管芯正常工作,输出:可见光的功能,既有电参数,又有光参数的设计及技术要求,无法简单地将分立器件的封装用于LED。
LED的核心发光部分是由p型和n型半导体构成的pn结管芯,当注入pn结的少数载流子与多数载流子复合时,就会发出可见光,紫外光或近红外光。
但pn结区发出的光子是非定向的,即向各个方向发射有相同的几率,因此,并不是管芯产生的所有光都可以释放出来,这主要取决于半导体材料质量、管芯结构及几何形状、封装内部结构与包封材料,应用要求提高LED的内、外部量子效率。
常规Φ5mm型LED封装是将边长0.25mm的正方形管芯粘结或烧结在引线架上,管芯的正极通过球形接触点与金丝,键合为内引线与一条管脚相连,负极通过反射杯和引线架的另一管脚相连,然后其顶部用环氧树脂包封。
反射杯的作用是收集管芯侧面、界面发出的光,向期望的方向角内发射。
顶部包封的环氧树脂做成一定形状,有这样几种作用:保护管芯等不受外界侵蚀;采用不同的形状和材料性质(掺或不掺散色剂),起透镜或漫射透镜功能,控制光的发散角;管芯折射率与空气折射率相关太大,致使管芯内部的全反射临界角很小,其有源层产生的光只有小部分被取出,大部分易在管芯内部经多次反射而被吸收,易发生全反射导致过多光损失,选用相应折射率的环氧树脂作过渡,提高管芯的光出射效率。
用作构成管壳的环氧树脂须具有耐湿性,绝缘性,机械强度,对管芯发出光的折射率和透射率高。
选择不同折射率的封装材料,封装几何形状对光子逸出效率的影响是不同的,发光强度的角分布也与管芯结构、光输出方式、封装透镜所用材质和形状有关。
若采用尖形树脂透镜,可使光集中到LED的轴线方向,相应的视角较小;如果顶部的树脂透镜为圆形或平面型,其相应视角将增大。
qfp封装手工焊接方法

qfp封装手工焊接方法
QFP(Quad Flat Package)封装是一种表面贴装技术,它是将
芯片引脚直接焊接在PCB板的表面上,而不需要通过孔穿插
连接。
下面是手工焊接QFP封装的步骤:
1. 准备工具和材料:手持式烙铁、钳子、吸锡器、酒精清洁剂、焊锡丝、焊通剂、PCB板和QFP封装芯片。
2. 将PCB板放在工作台上,将QFP封装芯片轻轻放在PCB板的相应位置上。
3. 使用吸锡器或烙铁加热来清除QFP封装芯片引脚和PCB板
的引脚焊锡,确保焊盘和引脚干净。
4. 使用酒精清洁剂擦拭PCB板和QFP封装芯片上的引脚,以
去除任何污垢和油脂。
5. 使用烙铁预热引脚焊盘和引脚,然后使用焊通剂涂抹在焊盘上,以促进焊料的流动。
6. 取一根适当长度的焊锡丝,将焊锡丝的一端与烙铁接触,等待焊锡熔化。
7. 将熔化的焊锡移动到焊盘和引脚接触的位置,稍微加压,以确保焊锡完全覆盖焊盘和引脚。
8. 等待焊锡冷却凝固,然后用钳子将多余的焊锡剪掉。
9. 重复上述步骤,一次焊接一个引脚,确保每个引脚都焊接牢固。
10. 等待所有引脚焊接完成后,使用酒精清洁剂清洁PCB板和QFP封装芯片,以去除焊通剂和焊锡残留物。
请注意,手工焊接QFP封装是一种复杂且需要经验的工艺,如果没有经验或技术能力,建议使用自动化设备或寻求专业焊接服务来保证焊接质量。
此外,工作环境要保持整洁,并使用适当的防静电措施,以避免损坏芯片。
电子封装、微机电与微系统第四章 封装工艺

1
4.2 厚 膜 技 术
厚膜材料是有机介质掺入微细金属粉、玻璃粉或陶瓷 粉末的混合物,通过丝网印刷工艺,印制到绝缘基板上。 无机相金属粉可确定厚膜成分:
● 金属或金属合金组成无机相导体; ● 金属合金或钌(Ruthenium)系化合物组成厚膜电阻; ● 玻璃或玻璃陶瓷无机相组成多层介质、密封剂或高介 电常数的电容层。
第四章 封 装 工 艺
1
图4-12 寄生电容
第四章 封 装 工 艺
1
4.8 倒装芯片技术
倒装芯片技术(Flip Chip Technology,FCT)是1960年首 先由IBM公司设计并开发研制出来的,但一直到近几年才 开 始应用于高速、单芯片微处理器或微电子集成芯片。倒装芯 片技术应用于少数功率器件,则是在最近的时间内。
第四章 封 装 工 艺
1
3. 孔内电连通 斜孔深度一般有几百微米,要在其侧壁上形成电通路, 通常可采用溅射、蒸发、电镀等方法。直孔电连通的常用 方法有低温化学淀积、熔融金属淀积、电镀等。
第四章 封 装 工 艺
1
4. 重布线 通孔内金属层制作完毕后,可以采用类似于集成电路
的再分布技术对键合好的圆片表面进行重新布线。
第四章 封 装 工 艺
1
2) 保温段 保温段是指温度从120℃~150℃升至焊膏熔点的区域, 其主要目的是使PCB上各元器件的温度趋于稳定,尽量减 少 温差。应保证足够的时间,使较大元器件的上升温度同 较 小元器件上升温度同步,保证焊膏中的助焊剂得到充分 挥 发。
第四章 封 装 工 艺
1
3) 回流段 在回流区域里,加热温度最高,元器件的温度快速上 升至峰值温度。在回流阶段,不同的焊膏,焊接峰值温度 不同,一般为焊膏的熔点温度加20℃~40℃。对于熔点为 183℃的Sn63Pb37焊膏和熔点为179℃的Sn62Pb36Ag2焊膏, 峰值温度一般为210℃~230℃。回流时间不要过长,以防 对PCB及元器件造成不良影响。理想的温度曲线是超过焊 锡熔点“尖端区”覆盖的面积最小。
射频模组封装工艺

射频模组封装工艺射频模组是指在射频电路中集成了各种功能模块的电子器件,广泛应用于无线通信、雷达、导航、遥感等领域。
封装工艺是射频模组制造过程中的关键环节,它直接影响到射频模组的性能和可靠性。
在射频模组封装工艺中,首先需要选择合适的封装材料。
射频模组中的封装材料需要具有良好的电气性能和机械性能,以确保信号的传输和模组的稳定性。
常用的封装材料有陶瓷、塑料和金属等,不同的材料具有不同的特点和应用范围。
接下来是封装工艺中的基板制备。
基板是射频模组的核心部件,承载着射频电路的结构和元器件。
制备高质量的基板对于射频模组的性能至关重要。
常见的基板制备工艺包括印刷电路板(PCB)制作、半导体工艺等,其中PCB制作是最常用的基板制备工艺。
然后是射频模组的封装方式。
射频模组的封装方式有多种,常见的有芯片封装、模块封装和集成封装等。
芯片封装是将射频芯片直接封装在基板上,适用于尺寸较小的射频模组。
模块封装是将射频芯片与其他元器件集成在一起形成模块,适用于功能较复杂的射频模组。
集成封装是将射频模组中的多个功能模块集成在一起,实现更高集成度和更小尺寸的射频模组。
封装工艺中的关键步骤之一是焊接。
焊接是将射频芯片或其他元器件与基板连接的过程。
常见的焊接方式有手工焊接、表面贴装技术(SMT)和无铅焊接等。
焊接质量的好坏直接影响到射频模组的可靠性和性能稳定性。
射频模组的封装工艺还包括封装结构设计和封装工艺优化等方面。
封装结构设计需要考虑射频信号的传输特性和电磁兼容性,以降低信号损耗和干扰。
封装工艺优化则是通过不断改进工艺流程和技术手段,提高射频模组的生产效率和质量稳定性。
射频模组封装工艺是射频模组制造过程中至关重要的环节。
合理选择封装材料、精确制备基板、选择适合的封装方式、优化焊接工艺,都能够提高射频模组的性能和可靠性。
在封装工艺中需要注意封装结构设计和工艺优化,以确保射频模组的传输特性和电磁兼容性。
射频模组封装工艺的不断创新和优化将推动射频技术的发展,满足人们对无线通信和雷达导航等领域的需求。
集成电路封装技术及其应用

塑料封装
定义:塑料封装是一种以塑料为基材的集成电路封装形式 特点:重量轻、成本低、可塑性强、绝缘性能好 常见类型:DIP、SIP、SOP、QFP等 应用领域:消费电子、汽车电子、通信等领域
04
集成电路封装技术应用领域
通信领域
集成电路在通信领域的应 用
通信设备中的集成电路封 装技术
集成电路在通信网络中的 重要性
集成电路封装技术在消费 电子领域的发展趋势
汽车电子领域
集成电路在汽车电子中的应用: 如发动机控制、车身控制、安全 系统等
汽车电子领域对集成电路封装技 术的需求:高可靠性、高耐久性、 低功耗等
添加标题
添加标题
添加标题
添加标题
集成电路封装技术在汽车电子中 的优势:提高性能、降低成本、 增强可靠性
集成电路封装技术在汽车电子领 域的发展趋势:小型化、轻量化、 集成化等
封装类型与结构
封装类型:DIP、SOP、QFP、BGA等 封装结构:芯片、基板、引脚、外壳等 封装材料:塑料、金属等 封装工艺:焊接、压接、绕接等
03
集成电路封装技术分类
气密性封装
定义:气密性封装是一种通过严格控制封装体内 气体流动的封装方式,以确保封装体内部的气体 不会泄漏到外部环境中。
原理:通过在封装体上设置一定的密封结构,如 密封环、密封垫等,以阻止气体通过封装体与外 部环境之间的缝隙流动。
集成电路封装技术的作用
集成电路封装技术的分类
集成电路封装技术的发展历程
封装技术发展历程
早期封装技术:简单的芯片封装形式,主要采用手工操作,生产效率低 分立器件封装:将晶体管、电阻、电容等分立器件封装在一起,提高了性能和可靠性 集成电路封装:将多个器件集成在一个芯片上,然后进行封装,大大提高了集成度和可靠性 表面贴装技术:采用表面贴装技术,将芯片直接贴装在印制板上,提高了生产效率和可靠性 先进封装技术:采用先进封装技术,如倒装焊、晶圆级封装等,进一步提高了集成度和可靠性
【Altium专题】【原创】3D封装技术

【Altium专题】——3D封装技术AndyZhouAltium Designer的3D功能向来充满争议,曾经在与一些前辈交流的过程中,他们似乎对此功能不屑一顾,甚至取笑我“不务正业”,也许仁者见仁智者见智,当时心里觉得有落差,但是,面对质疑,我没有因此放弃对这一块的摸索,于是,才有了这一专题…要说3D功能有什么好处,最大的好处就是“所见即所得”,当时我Layout一块多路稳压电源的板子,发到工厂去打板,回来与3D预览一对照,几乎一模一样!(如上图)通常,我习惯Layout的时候检查元器件之间的干涉情况以及对照三维图手工焊接PCB,有些时候,还能根据元器件的空间分布调整PCB板的大小,节省成本。
以往,我都是先有PCB封装,再有3D Body,最近,我有幸看到了Altium的官方视频,进而学会了新的技能——从3D模型生成PCB FootPrint。
☺目录1. 为何使用3D封装 (2)2. “自力更生” (5)2.1准备二维封装 (5)2.1.1测量数据 (5)2.1.2绘制丝印 (5)2.2面动成体 (7)2.2.1使用3D Body管理器 (7)2.2.2使用Place 3D Body (14)3. 为我所用 (16)4. 总结 (26)1. 为何使用3D封装➢方便手工焊接使用3D视图,可以很方便我们手工焊接,尤其是有极性的元件摆放,都可以一目了然,下面的两幅图可以作为对比,上图为3D视图,其下为实物图。
➢方便布局和碰撞检查初学者绘制电路图都是在二维平面上进行的,但应该注意的是,元件并不是“平面”的,它们也有自己的形态,拥有自己的高度,它们有自己的性格,有的“实实在在”,有的则可以“海纳百川”,比如一个1602的液晶,它下面其实可以放很多东西,您一开始就注意到了吗?☺这是一片直插的单片机,40脚,位于1602正下方如上图,晶振、单片机均放置在1602的正下方,在保证电路功能的前提下,既美观有节省空间。
LCC封装器件的手工焊接

LCC 封装器件的手工焊接摘要:随着微电子组装技术的不断发展, LCC 封装器件广泛地应用到电子产品中,该类器件为可烧程序的多引脚器件,辉接部位在器件底部,且引脚四边引出辉接部位向里内抠呈 J 型,对手工焊接造成一定难度。
因此装焊质量直接影响到器件的应用前景,本文主要讲述 LCC 封装器件的手工焊接技术。
关键词: PROM 芯片引脚检查对位焊接清洁1.引言随着微电子组装技术的发展,型号中大量采用了 LCC 封装的J 型器件。
在生产中,手工焊接的质量好坏直接决定产品质量,影响产品可靠性。
2.LCC器件简介J 型器件( PROM 芯片)一般为黑色塑封或金色陶瓷封装,引脚四边引出,焊接部位向里内弯曲呈 J 型。
J 型器件是一种新型可烧程序的片子,它的手工焊接一般多出现于单板完成后修复环节中, PCB 板上其他器件已完成焊接。
焊接时既要保证 J 型器件焊接完好还要保证板上别的器件不受影响。
3.焊接过程问题分析LCC 器件在手工焊接时存在以下难点:>器件引脚不在同一水平面而使器件焊锡量不均匀;>烧完程序后的器件引脚发乌,直接焊接影响焊接质量:>四面引脚器件焊接时容易造成器件引脚与焊盘错位,导致器件整体偏移;> J 型器件一般为待调器件,局部修复操作时注意器件防护,以免多余物造成器件短路,影响整板性能:>引脚在底部焊接难度大,镀金引脚焊接时焊锡容易爬到引脚外侧;>修复中由于邻近机壳壁或紧贴无法拆卸器件时无法检查,焊接引脚;>助焊剂流入器件底部无法清洁留下隐患。
4.问题解决为解决以上焊接难点,保证焊接质量,经过理论分析及试验验证,给出如下的焊接方法4.1焊前准备器件在焊接前要检查外观是否有损伤,引脚有无变形,引脚焊接面是否在同一半面,校完引脚检查在同一平面上后才可焊接,以免焊接完成后发现锡量多少不均匀的情况。
对烧完程序的器件引脚进行手工搪锡,对引脚发乌程度严重及镀金引脚搪两次,待自殃冷却后用吸锡绳将多余焊锡吸掉,以保证器件平面度,从而有效保证焊接质量。
微组装工艺
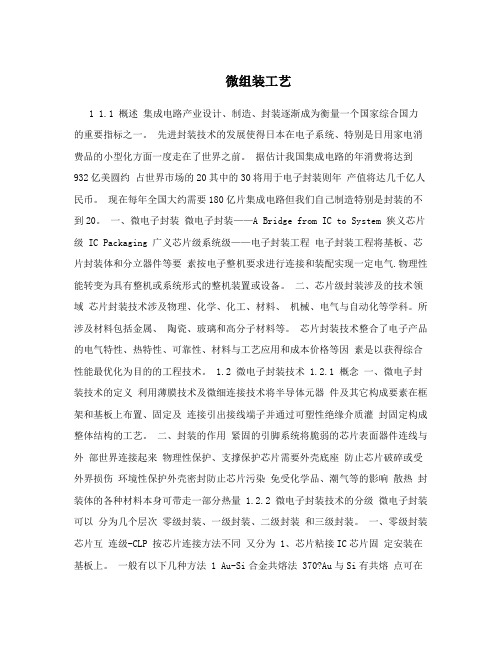
微组装工艺1 1.1 概述集成电路产业设计、制造、封装逐渐成为衡量一个国家综合国力的重要指标之一。
先进封装技术的发展使得日本在电子系统、特别是日用家电消费品的小型化方面一度走在了世界之前。
据估计我国集成电路的年消费将达到932亿美圆约占世界市场的20其中的30将用于电子封装则年产值将达几千亿人民币。
现在每年全国大约需要180亿片集成电路但我们自己制造特别是封装的不到20。
一、微电子封装微电子封装——A Bridge from IC to System 狭义芯片级 IC Packaging 广义芯片级系统级——电子封装工程电子封装工程将基板、芯片封装体和分立器件等要素按电子整机要求进行连接和装配实现一定电气.物理性能转变为具有整机或系统形式的整机装置或设备。
二、芯片级封装涉及的技术领域芯片封装技术涉及物理、化学、化工、材料、机械、电气与自动化等学科。
所涉及材料包括金属、陶瓷、玻璃和高分子材料等。
芯片封装技术整合了电子产品的电气特性、热特性、可靠性、材料与工艺应用和成本价格等因素是以获得综合性能最优化为目的的工程技术。
1.2 微电子封装技术 1.2.1 概念一、微电子封装技术的定义利用薄膜技术及微细连接技术将半导体元器件及其它构成要素在框架和基板上布置、固定及连接引出接线端子并通过可塑性绝缘介质灌封固定构成整体结构的工艺。
二、封装的作用紧固的引脚系统将脆弱的芯片表面器件连线与外部世界连接起来物理性保护、支撑保护芯片需要外壳底座防止芯片破碎或受外界损伤环境性保护外壳密封防止芯片污染免受化学品、潮气等的影响散热封装体的各种材料本身可带走一部分热量 1.2.2 微电子封装技术的分级微电子封装可以分为几个层次零级封装、一级封装、二级封装和三级封装。
一、零级封装芯片互连级-CLP 按芯片连接方法不同又分为 1、芯片粘接IC芯片固定安装在基板上。
一般有以下几种方法 1 Au-Si合金共熔法 370?Au与Si有共熔点可在多个IC芯片装好后在氮气保护下烧结也可用超声熔焊法逐个熔焊。
详解LED封装全步骤

详解LED封装全步骤一、生产工艺1.生产:a) 清洗:采用超声波清洗PCB或LED支架,并烘干。
b) 装架:在led管芯(大圆片)底部电极备上银胶后进行扩张,将扩张后的管芯(大圆片)安置在刺晶台上,在显微镜下用刺晶笔将管芯一个一个安装在PCB或LED支架相应的焊盘上,随后进行烧结使银胶固化。
c)压焊:用铝丝或金丝焊机将电极连接到LED管芯上,以作电流注入的引线。
LED 直接安装在PCB上的,一般采用铝丝焊机。
(制作白光TOP-LED需要金线焊机)d)封装:通过点胶,用环氧将LED管芯和焊线保护起来。
在PCB板上点胶,对固化后胶体形状有严格要求,这直接关系到背光源成品的出光亮度。
这道工序还将承担点荧光粉(白光LED)的任务。
e)焊接:如果背光源是采用SMD-LED或其它已封装的LED,则在装配工艺之前,需要将LED焊接到PCB板上。
f)切膜:用冲床模切背光源所需的各种扩散膜、反光膜等。
g)装配:根据图纸要求,将背光源的各种材料手工安装正确的位置。
h)测试:检查背光源光电参数及出光均匀性是否良好。
2.包装:将成品按要求包装、入库。
二、封装工艺1. LED的封装的任务是将外引线连接到LED芯片的电极上,同时保护好led芯片,并且起到提高光取出效率的作用。
关键工序有装架、压焊、封装。
2. LED封装形式LED封装形式可以说是五花八门,主要根据不同的应用场合采用相应的外形尺寸,散热对策和出光效果。
led按封装形式分类有Lamp-LED、TOP-LED、Side-LED、SMD-LED、High-Power-LED等。
3. LED封装工艺流程a)芯片检验镜检:1、材料表面是否有机械损伤及麻点麻坑(lockhill);2、芯片尺寸及电极大小是否符合工艺要求;3、电极图案是否完整。
b)扩片由于LED芯片在划片后依然排列紧密间距很小(约0.1mm),不利于后工序的操作。
我们采用扩片机对黏结芯片的膜进行扩张,是LED芯片的间距拉伸到约0.6mm。
手 工 插 件
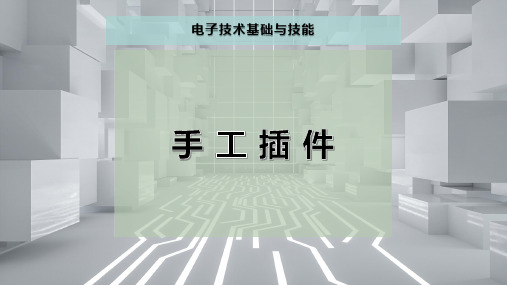
1. 简要说明手工手件的工艺流程。 2. 元器件的装插有哪些具有要求?
2021/8/7
14
电子技术基础与技能
2021/8/7
安装元件的标志方向
12
主、副板插件工序的质量控制要求
2021/8/7
1)操作工应具备元件的识别能力,严格执行工艺操作规范,保证所 对应的位号、极性、型号、准确、装插集成块时必须佩带防静电腕带 ,保证插件质量。
2)对生产所需的原材料,元器件、零部件和重要辅助材料等物质在 领用时必须与工艺文件规范一致;
电子技术基础与技能
手工插件
电子整机机芯板中的元器件可以用自动插件机来完成 大多数元器件的插装,但大型元器件或不规则元器件 ,如:大功率电阻、大容量电容、各种接插件,集成 块及晶振、声表面滤波器,行输出变压器、遥控接收 等无法用机器自动装插,因而需采用手工插件。
1. 手工插件的工艺流程
手工插件是在机插机芯板检验合格后,波峰焊前检查的一道关 键工序。
手工插件工艺流程
2021/8/7
2
2. 常用元器件的插装 轴向引线型元器件有电阻、二极管等。常见的径向引线型器件有各种电容、发
光二极管、光电二极管以及各种三极管等。元器件的安装有立式、卧式(水平 式),倒式以及横式装等几种方法。
一般三极管,电解电容、晶振和单列直插集成电路多采用立式插装法、而电阻 、二极管、双列直插及扁平封装集成电路多采用水平插装方式。
2021/8/7
3
3、元器件装插的具体要求
(1)每个工位的操作人员将已检验元器件按不同的品种、规格装入 元件盒或纸盒内,并整齐有序地放置在工作台内的滑槽里,然后严格 按照工位前上方悬挂的工艺卡片操作。
(2)按电路流向分区块装插各种规格的元器件。
dip生产工艺流程

dip生产工艺流程DIP生产工艺流程DIP(Dual In-line Package)是一种基于电子组件封装技术的一种生产工艺。
它是一种通过将电子元件安装在两排引线上,使其能够与电路板上的其他元件连接的方法。
下面将对DIP生产工艺流程进行详细介绍。
首先,在DIP生产工艺流程中的第一步是准备基板。
基板是DIP封装的载体,可以是金属或塑料材料。
首先,需要选择适当的材料,并根据设计要求制作出基板。
第二步是将元件装配到基板上。
这一步需要使用SMT (Surface Mount Technology)技术。
它是一种将元件焊接到表面上的封装技术。
利用SMT技术,可以将电子元件直接安装到基板表面上,使得封装更加紧凑和可靠。
第三步是进行元件焊接。
焊接是将元件与基板之间进行连接的关键步骤。
在DIP生产工艺中,有两种常用的焊接方法:手工焊接和机器焊接。
手工焊接需要熟练的操作人员,并且比较费时费力,但是可以适应各种复杂的封装要求。
机器焊接则是使用自动化设备进行焊接,效率更高,但是适应性较差。
第四步是进行元件测试。
在DIP生产工艺中,对封装后的元件进行测试是必不可少的。
常用的测试方法包括ICT(In-circuit Test)和FCT(Functionality Check Test)。
ICT主要用于检测封装后电路的连通性和电气性能,而FCT则用于检测整个封装电路的功能性。
最后一步是封装。
在DIP封装过程中,需要将元件与基板之间进行固定和封装。
通常使用胶水或焊锡来进行封装。
这一步需要仔细操作,确保元件和基板之间的牢固连接。
总结起来,DIP生产工艺流程主要包括基板准备、元件装配、元件焊接、元件测试和封装。
通过这些步骤,可以生产出具有良好电气性能和可靠性的DIP封装元件。
这种生产工艺在电子制造业中得到了广泛应用,为各种电子设备的制造提供了基础。
- 1、下载文档前请自行甄别文档内容的完整性,平台不提供额外的编辑、内容补充、找答案等附加服务。
- 2、"仅部分预览"的文档,不可在线预览部分如存在完整性等问题,可反馈申请退款(可完整预览的文档不适用该条件!)。
- 3、如文档侵犯您的权益,请联系客服反馈,我们会尽快为您处理(人工客服工作时间:9:00-18:30)。
全手工封装技术转深度以S&R&S为例,谈一下封装及封装工具一个不经处理的Windows系统直接恢复到另一台机器上,最有可能出现的情况就是蓝屏,或者反复重新启动。
那么,造成蓝屏、重启等的原因是什么呢?事实上,这就是通用克隆系统所要解决的最基本的技术问题。
我们这里以封装XP系统为例,2003及2K的方法都是大同小异的首先我们来了解一下封装的步骤:一.安装操作系统装系统、打补丁,至于集成驱动及软件、优化或美化等由需要而定。
Dllcache备份的步骤可选,这里就不单独列为一项了。
Dllcache备份的原理不是备份文件,而是备份文件名,在系统恢复后从I386的CAB包中提取相应文件。
Deepin XP lite是没有这些文件的,300多兆的Dllcache并不是必需的。
二.删除、更改系统硬件驱动1.更改HAL电源模式的方法其实有很几种,目前主流的就是使用Longhorn的ntldr自动判断。
longhorn的ntldr有一个新参数,即/detecthal(在boot.ini的启动项中设置),通过这个参数,可以实现自动判断并选择计算机类型,而且这种技术由于源出于微软,所以其结果是百分百准确的。
基本上,使用Longhorn技术来判断正确的hal就是目前最完美的解决办法。
死改不改的S&R&S 9.x版本基本上都使用这种方式。
2.更改存储控制器类型硬盘控制器包括PATA(传统的硬盘控制器)、SATA、RAID、SCSI等,实际上,死性不改的S&R&S就是SATA&RAID&SCSI的意思。
在通用克隆发展的早期,SATA硬盘还不是很流行,这个问题还不是很严重,因为所有的PATA(IDE)控制器都兼容于标准双通道IDE 控制器,所以人们制做克隆时只需要将源机器的IDE控制器修改为标准双通道即可。
但很显然,SATA并不兼容于标准双通道,所以当时制做的克隆系统在SATA硬盘上恢复后重启时会出现蓝屏。
3.删除其他硬件驱动三.封装依照作者选用的封装方式,封装的步骤也就不尽相同。
如果选用SRS的话,这里就可以直接封装了,它会调用sysprep完成封装过程。
手工替换NTLDR的就需要自己细心一点,替换文件、删除相关注册表等。
注:S&R&S9.7集成了更改电源及IDE模式的功能,所以第二步里面的1和2也可不做。
下面我们研究一下封装工具都做了些什么:一.电源检测S&R&S9.X采用了基于MCC硬件抽象层电源识别技术,即替换LONGHORN版本的NTL DR,依靠/DETECTHAL来完成对电源模式的检测。
早期是需要用户手工选择的,这里就不说了。
二.更改IDE模式通过mshdc.inf文件来更新IDE模式为双通道runwait("devcon update "&@windowsdir&"\inf\mshdc.inf E_ISA_UP","",@SW_HIDE)三.驱动集成很显然,以我们个人的能力是不可能搜集到所有的MassStorage设备的驱动的,同时存储技术在不断发展,新硬件也层出不穷,这是通用克隆不可能实现万能的原因之一。
S&R&S9.X采用了DPS驱动包,所以大家在N多使用不改的封装工具的GHOST作品里都可以看到“含大多数驱动,支持SATA。
支持64位”。
这话是怎么来的呢?This one supports almost all (none are reported missing) MassStorage controllers (PATA, SATA, SCSI, RAID and al their combinations).大家可以到这个地址下载相关驱动:/DriverPacks/除了存储设备的驱动,新型的CPU以及USB键盘、鼠标等设备驱动也要集成到系统里,例如AMD K8 CPU等。
不过,这些驱动之间有可能存在不兼容问题,驱动的不兼容会导致同时加载时直接死机,例如intelide与viaide的不兼容问题,这是导致克隆不能万能的原因之二,也是最主要的同时也很难解决的问题。
至于更改及恢复启动菜单、调用sysprep进行静默封装等非技术步骤,这里不做讨论。
了解了封装工具的工作原理以后,我们会想:封装工具是必需的吗?答案是:不!在预封装问题上,为了让系统能正确识别MassStorage设备,目前可以采取集成驱动到sy stem32\driver或使用txtsetup引导(深度的V2及老毛桃的PE都是这样做的)的办法。
通过手工替换相关文件,可以做到完美的电源检测,在深度白金3in1中已经做到了100%准确。
虽然SRS采用的也这个技术,但是在实际应用中,效果仍不是绝对满意的,出现了部分用户无法正常关机的情况,也就是电源检测上出了问题。
尽管我们可以通过手工替换NTLDR及HAL、修改注册表、更改电源及IDE模式,最后运行SYSPREP进行封装,但是在一些驱动问题上,我还没有做到面面俱到,在3in1中就已经体现了对一些SATA等设备的识别问题。
Windows NT不再依赖于BIOS提供的方式访问硬盘,而是通过底层的驱动程序,如果没有加载对应的驱动程序,那么Windows就会找不到硬盘,找不到硬盘当然就不可能将Windo ws启动起来。
而DOS则是通过BIOS来访问硬盘的,所以这也是为什么DOS能够访问S ATA、RAID、SCSI硬盘而Windows却不能访问的主要原因。
目前,死性不改正在探索在DOS下运行的S&R&S软件,目的就是解决这个问题,其实现原理就是根据目标机器的硬件情况在DOS下只加载适合目标机器的对应的驱动,这样就可以有效避免驱动程序的不兼容问题。
实际上我们深度已经有了自己的封装工具,但是我们必须看到这条路的发展方向,我个人认为,封装工具不是必需的,而辅助工具却是急需的。
Ghost系统封装教程及封装工具原理本教程基于MCC硬件抽象HAL(电源模式)原理,系统以XP为例。
这里将系统封装分为3步:做系统、封装、部署================================一、做系统================================平台不限,但不建议在虚拟机上制作。
CPU及主板芯片没有限制,关于intelide和intelpp m的不兼容问题,深度白金3in1并没有删除这些注册表,没有反馈因此在AMD机器上蓝屏的现象。
1、选用免激活的版本安装盘,正常安装系统,打补丁,优化服务这里选用深度XP精简版5.7,安装大约需要15-20分钟。
建议关闭系统还原及自定义通知,关闭远程,关闭共享,关闭休眠注意声卡要驱动上,否则封装后的系统都不在任务栏显示音量。
运行一次windows meida player,避免以后出现向导安装输入法,并在“区域和语言选项”的“高级”中,应用于默认用户账户。
我的文档,如果有需要也可以移动到D盘。
outlook不能保存密码及SQL安装挂起的问题,也可以在这里清理一下相关注册表。
2、安装需要的软件OFFICE安装时要将“第一次使用时安装”的项目完全安装上,否则会以后提示插入光盘。
不建议安装杀毒软件,特别是卡巴斯基,该软件会与某封装工具冲突。
不建议安装虚拟光驱及刻录软件,已知部分软件在封装后失效。
不建议删除windows\Installer下的安装文件,可能会造成部分程序无法卸载。
3、封装准备运行“gpedit.msc"打开组策略“计算机配置\管理模板\系统”启用“关闭Windows Update 设备驱动程序搜索”“管理模板/系统/Internet 通信管理/Internet 通信设置”启用“关闭Windows Update 设备驱动程序搜索”“用户配置\管理模板\系统”启用“配置驱动程序搜索位置” (不搜索软盘,光驱,Windows Update)“用户配置\管理模板\系统”忽略“设备驱动程序的代码签名”检查系统属性中的驱动签名是否为忽略,update是否为从不搜索。
清理Documents and Settings目录,可以清理到10M以下。
当前账户\收藏夹,安装软件后经常有链接,清之~当前账户\SendTo,邮件接收,建议删除当前账户\Recent,历史记录,现在删了以后还得删当前账户\Local Settings\Temp,临时文件,能删的全删当前账户\Local Settings\Application Data下的图标缓存IconCache.db,约5-10M 当前账户\桌面,建议将所有图标移动到All Users\桌面看下控制面板里的添加删除程序,有没有流氓软件,有就干掉,当然,除非你有特殊目的。
================================二、封装================================1、更改IDE 控制器及电源在设备管理器中更新驱动从列表或指定位置安装不要搜索,我要自己选择要安装的驱动程序IDE更改为“标准双通道PCI IDE 控制器”,电源更改为“Standard PC”2、提取检测电源需要的相关文件WIN2000在SP4.CAB/WINDOWS XP SP2在SP2.CAB/WINDOWS 2003在SP1. CAB中halacpi.dllhalapic.dllhalmps.dllhalaacpi.dllhalmacpi.dllhal.dll→并更名为halstnd.dllntkrnlmp.exentkrnlpa.exentkrpamp.exentoskrnl.exe→并更名为ntkrnlup.exe将上述文件拷贝到系统SYSTEM32目录3、添加inf文件将以下代码保存为dtecthal.inf并拷贝到\WINDOWS\INF\,2000为\WINNT\INF\[Version]signature="$Windows NT$"DriverVer=07/01/2001[hal]MPS_MP = halmps.dllMPS_UP = halapic.dllE_ISA_UP = halstnd.dllACPIPIC_UP = halacpi.dllACPIAPIC_UP = halaacpi.dllACPIAPIC_MP = halmacpi.dll[ACPIOptions]ACPIEnable = 2ACPIBiosDate = 01,01,19994、引导修改boot.ini,加上/DETECTHAL参数,使系统启动时检测电源注意将原boot.ini备份,并在部署后还原[boot loader]timeout=3default=multi(0)disk(0)rdisk(0)partition(1)\WINDOWS[operating systems]multi(0)disk(0)rdisk(0)partition(1)\WINDOWS="Microsoft Windows XP Professional" /no execute=optin /fastdetect /detecthalC:\GHLDR=一键GHOST v11.0 Build 0707075、NTLDR引导文件,将LONGHORN版本的NTLDR放到C盘下注意将原NTLDR备份,并在部署后还原6、封装将sysprep.exe,setupcl.exe,及配置好的sysprep.inf放到c:\sysprep运行sysprep,“使用最小化安装”、关机模式“退出”,点击“重新封装”等待大约5-10秒,完成。