连续铸造及其与轧制的衔接工艺-资料
连续铸轧技术
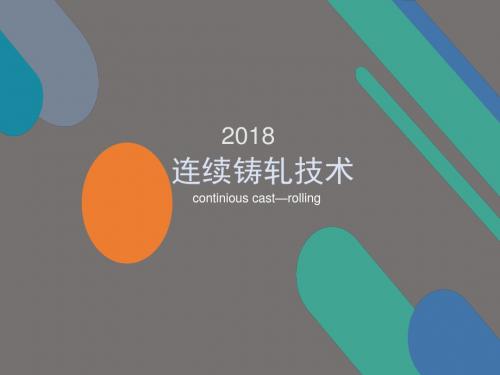
水冷速度 铸轧速度 辊套厚度
辊套材料
例
(3) 连续铸轧的设计参数
① 铸轧角
两辊铸轧中心连线和供料嘴顶 端到铸轧辊中心连线所形成的角 度,即为铸轧角,如右图所示, α一般在 5º~ 10º之间。h为铸轧 区的高度。
O h
R
铸轧角示意图
② 辊径的选择
铸轧辊径一般采取大些尺寸 为好,这样铸轧冷却得好,辊 径越大,在铸轧角一定的情况 下,铸轧区加长,有利于热交 换,辊径一般在 400~550mm 之 间
① 铸轧温度
一般比所铸轧的金属熔点高60~80℃。如果铸轧温度过低,金 属溶液冷凝在浇注系统中,如果过高,则不易成形,或板坯质 量变差。
② 铸轧速度
铸轧速度必须是无级调速。铸轧过程中冷却速度的调整主要是 靠铸轧速度,同时,水冷强度也起着配合作用。
③ 冷却强度
在铸轧过程中,单位时间,单位面积 影响冷却 速度的因 上导出热量的大小即为冷却强度。 素 液体金属 铸轧 向外导热 冷却强度 在铸轧时 速度慢 时间充分 增加 停留时间长
2018
连续铸轧技术
continious cast—rolling
连续铸轧:金属熔体在连续铸造凝固的同时进行轧 制变形的过程。 工艺特点:结晶器为两个带水冷系统的旋转铸轧辊 ,熔体在其辊缝间完成凝固和热轧两个过程,而且 是在很短时间内(2~3s)完成的。 与连铸连轧的区别:连铸连轧实质上是将薄锭坯铸 造与热轧连续进行,即金属熔体在连铸机结晶器中 凝固成厚度约 50~90mm 的坯后,再在后续的连轧 机上连续轧成板材,其铸造和轧制是两道独立的工 序。
③ 铸轧辊套的选择
a) 有足够的导热性能; b) 有较高的力学性能; c) 耐高温; d) 耐热交变应力的疲劳作用
连续铸造及其与轧制的衔接工艺
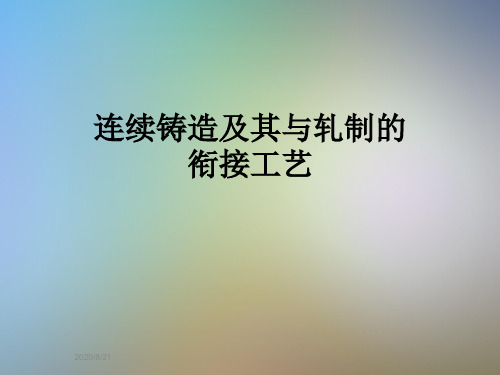
连铸机类型 连铸机可以按铸坯断面形状分为厚板坯 、薄板坯、大方坯、小方坯、圆坯、异型 钢坯及椭圆形钢坯连铸机等,也可按铸坯 运行的轨迹分为立式、立弯式、垂直-多点 弯曲形、垂直-弧形、多半径弧形(椭圆形 )、水平式及旋转式连铸机 。
2020/8/21
立式连铸机出现最早,其优点是钢中夹杂易于 上浮排除,凝壳冷却均匀对称,不受弯曲矫直 应力,适用于裂纹较敏感钢种的连铸,但缺点 是设备高度大,建设投资大,且钢水静压力大 易使钢坯产生鼓肚变形,铸坯断面和长度都不 能过大,拉速也不宜过高。立弯式连铸机为降 低设备高度,将完全凝固的铸坯顶弯成90°角 ,在水平方向出坯,消除了定尺长度的限制, 降低了设备的投资,但缺点是铸坯受弯曲矫直 应力,易产生裂纹。
2020/8/21
弧形连铸机大大降低了设备的高度,仅为立式的1/2-1/3 ,投资少,操作方便,利于拉速的提高,但缺点是存在 设备对弧较难,内外弧冷却欠均匀,弯曲矫直应力较大 及夹杂物在内弧侧聚集的缺点,故对钢水纯净度要求更 高。椭圆形连铸机为分段改变弯曲半径,故设备更低, 称为超低头铸机。垂直-弧形和垂直-多点弯曲形连铸机 采用直结晶器并在其下部保留2m左右的直线段,使铸机 的高度增加不多,而有利于克服内弧侧夹杂物富集的缺 点。水平式铸机设备高度更低,更轻便且投资少,但尚 不能制成大生产适用机型。目前世界各国弧形铸机占主 导地位,达60%以上。其次为垂直-多点弯曲形。板坯和 方坯多采构垂直弧形,而垂直-多点弯曲形则呈增加趋势 。
2020/8/21
二冷装置安装在紧接结晶器的出口处,其作用 是借助喷水或雾化冷却以加速铸坯凝固并控制 铸坯的温度,夹辊和导辊支撑着带液心的高温 铸坯,以防止鼓肚变形或造成内裂。要求二冷 装置水压、水量可调,以适应不同钢种和不同 拉速的需要。拉矫机的作用是提供拉坯动力及 对弯曲的铸坯进行矫直,并推动切割装置运动 。拉坯速度对连铸产量、质量皆有很大的影响 。引锭装置的作用是在连铸开始前,用引锭头 堵住结晶器下口,待钢水凝固后将铸坯引拉出 铸机,再脱开引锭头,将引锭杆收入存放装置 。铸坯切割设备则将连续运动中的铸坯切割成 定尺,常用的切割设备有火焰切割器或液压剪 与摆动剪。
连铸连轧工艺
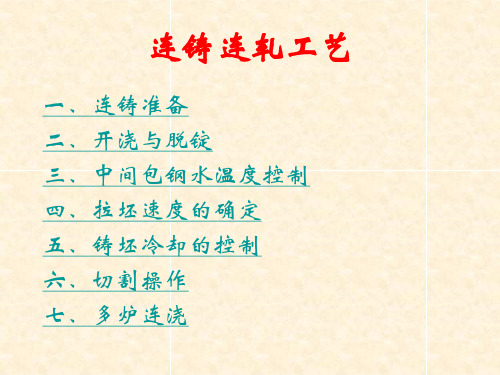
3.3 钢水在钢包中的温度控制
根据冶炼钢种严格控制出钢温度, 根据冶炼钢种严格控制出钢温度,使其在较窄的范围 内变化;其次,要最大限度地减少从出钢、钢包中、 内变化;其次,要最大限度地减少从出钢、钢包中、钢包 运送途中及进入中间包的整个过程中的温降。 运送途中及进入中间包的整个过程中的温降。 实际生产中需采取在钢包内调整钢水温度的措施: 实际生产中需采取在钢包内调整钢水温度的措施: ①钢包吹氩调温。 钢包吹氩调温。 ②加废钢调温。 加废钢调温。 ③在钢包中加热钢水技术。 在钢包中加热钢水技术。 ④钢水包的保温。 钢水包的保温。
• △T4:钢包精炼结束钢水在静置和运往连铸
平台的温降
分析: 分析: 热量损失形式:钢水上表面通过渣层的热损失、 热量损失形式:钢水上表面通过渣层的热损失、 钢包包衬吸热。 钢包包衬吸热。 热量损失大小:钢包内衬吸热降低, 热量损失大小:钢包内衬吸热降低,加了保温 温降减小低。 剂,温降减小低。
• △T5:钢水从钢包注入中间包过程中产生的温降 分析: 分析: 热量损失形式:辐射热损失、对流热损失、钢包吸热。 热量损失形式:辐射热损失、对流热损失、钢包吸热。 影响因素:钢流保护状况;中间包的容量、材质、 影响因素:钢流保护状况;中间包的容量、材质、 烘烤温度及保温措施 降低热量损失的措施: 降低热量损失的措施: 钢流需保护,采用长水口; ①钢流需保护,采用长水口; 减少浇铸时间; ②减少浇铸时间; 充分预热中间包内衬; ③充分预热中间包内衬; 中间包钢液面添加保温剂; ④中间包钢液面添加保温剂; 速的确定和控制
4.1、拉速定义: 4.1、拉速定义:拉坯速度是以每分钟从结晶器拉出的铸坯 长度来表示。拉坯速度应和钢液的浇注速度相一致。 长度来表示。拉坯速度应和钢液的浇注速度相一致。 4.2、拉速控制的意义:拉速控制合理, 4.2、拉速控制的意义:拉速控制合理,不但可以保证连铸 生产的顺利进行,而且可以提高连铸生产能力, 生产的顺利进行,而且可以提高连铸生产能力,改善铸坯的 质量。现代连铸追求高拉速。 质量。现代连铸追求高拉速。 4.3、拉速确定: 4.3、拉速确定: 确定原则: 1)确定原则: 确保铸坯出结晶器时的厚度能承受钢水的静 压力而不破裂,对于参数一定的结晶器,拉速高时, 压力而不破裂,对于参数一定的结晶器,拉速高时,坯壳 反之拉速低时则形成的坯壳厚。 薄;反之拉速低时则形成的坯壳厚。 一般认为,拉速应确保出结晶器的坯壳厚度为12 14mm。 12一般认为,拉速应确保出结晶器的坯壳厚度为12-14mm。
连铸连轧知识点
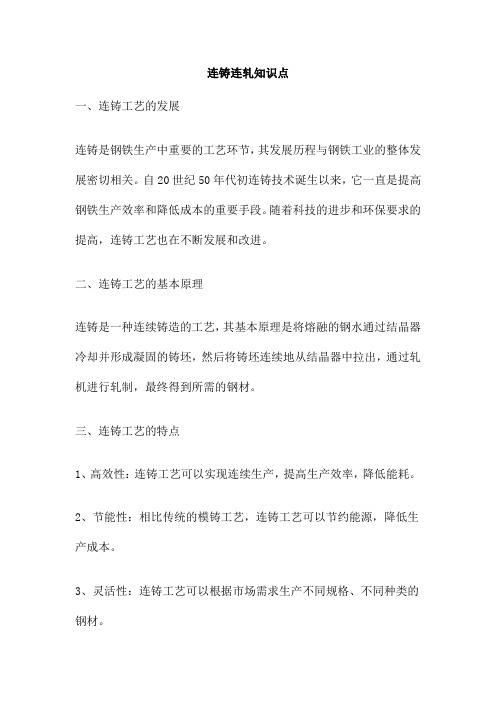
连铸连轧知识点一、连铸工艺的发展连铸是钢铁生产中重要的工艺环节,其发展历程与钢铁工业的整体发展密切相关。
自20世纪50年代初连铸技术诞生以来,它一直是提高钢铁生产效率和降低成本的重要手段。
随着科技的进步和环保要求的提高,连铸工艺也在不断发展和改进。
二、连铸工艺的基本原理连铸是一种连续铸造的工艺,其基本原理是将熔融的钢水通过结晶器冷却并形成凝固的铸坯,然后将铸坯连续地从结晶器中拉出,通过轧机进行轧制,最终得到所需的钢材。
三、连铸工艺的特点1、高效性:连铸工艺可以实现连续生产,提高生产效率,降低能耗。
2、节能性:相比传统的模铸工艺,连铸工艺可以节约能源,降低生产成本。
3、灵活性:连铸工艺可以根据市场需求生产不同规格、不同种类的钢材。
4、环保性:连铸工艺可以减少废弃物的产生,降低环境污染。
四、连铸工艺的应用范围连铸工艺广泛应用于各种钢铁产品的生产,包括板材、带材、型材、管材等。
随着技术的发展,连铸工艺也逐渐应用于有色金属、稀有金属等领域。
五、连铸工艺的未来发展方向随着科技的不断发展,连铸工艺的未来发展方向主要集中在以下几个方面:1、智能化:利用先进的自动化技术和智能化设备,提高生产过程的自动化水平和生产效率。
2、绿色化:进一步降低能耗和废弃物排放,实现生产过程的环保和可持续发展。
3、高效化:研发更高效的连铸技术,提高生产速度和产品质量。
薄板坯连铸连轧轧制区组织模拟薄板坯连铸连轧是一种高效、节能的钢材生产工艺,具有较高的生产效率和产品质量。
在轧制过程中,钢材的组织形态和性能特点对产品的质量和使用性能具有重要影响。
因此,薄板坯连铸连轧轧制区组织模拟成为了一个备受的研究领域。
通过组织模拟,可以深入了解轧制过程中材料的组织变化和性能特点,为工艺优化和产品性能提升提供理论支持和实践指导。
薄板坯连铸连轧轧制区背景及基础概念薄板坯连铸连轧是指将液态钢水倒入薄板坯连铸机中进行连续铸造,然后将连铸坯送入轧机进行连续轧制。
连铸连轧知识点

连铸连轧知识点连铸和连轧是金属工业中常见的两个工艺过程。
连铸是指将液态金属连续铸造成坯料的过程,而连轧是指将坯料经过一系列压制和变形操作,连续地轧制成所需尺寸的金属板、带材或线材的过程。
本文将介绍连铸和连轧的基本概念、工艺流程和主要应用。
一、连铸连铸是一种高效的金属铸造技术,具有生产速度快、坯料质量好等优点。
连铸主要应用于钢铁、铜、铝等金属的生产中。
1. 连铸的基本原理连铸的基本原理是将熔融的金属通过连续浇注的方式,直接铸造成连续的坯料。
具体原理如下:首先,将金属熔融至液态,并通过加热设备保持在一定温度范围内;然后,通过连续浇注系统,将熔融金属均匀地注入到连铸结晶器中;在连铸结晶器中,通过冷却剂的作用,使金属迅速凝固,并形成坯料;最后,通过一系列传动装置,将连续产生的坯料送往下游的轧制设备或其他后续处理过程中。
2. 连铸的工艺流程连铸的工艺流程一般包括以下几个关键步骤:(1)冶炼:将矿石等原料经过熔炼处理,得到液态的金属合金;(2)调温:通过加热设备将金属保持在一定的液态温度;(3)连续浇注:通过连续浇注系统,将熔融金属注入到连铸结晶器中;(4)结晶与凝固:在连铸结晶器中,通过冷却剂的作用,使金属迅速凝固,并形成坯料;(5)切割和输送:将连续产生的坯料切割成合适的长度,并送往下游的加工设备。
3. 连铸的应用连铸广泛应用于钢铁、铜、铝等金属的生产中。
在钢铁工业中,连铸可以直接将炼钢铁水铸造成连续坯料,用于后续轧制成钢板和钢材。
在有色金属工业中,连铸可以将液态金属铸造成连续的板材、带材和线材,用于制造电线电缆、汽车零部件等产品。
二、连轧连轧是一种将金属坯料经过多道次的压制和变形操作,连续地轧制成所需尺寸的金属板、带材或线材的工艺过程。
连轧具有高效快速、坯料成形完整等特点,广泛应用于钢铁、有色金属等工业领域。
1. 连轧的基本原理连轧的基本原理是通过一系列的压制和变形操作,使金属坯料逐渐减小厚度、增大长度,并达到所需的尺寸要求。
连铸连轧生产工艺
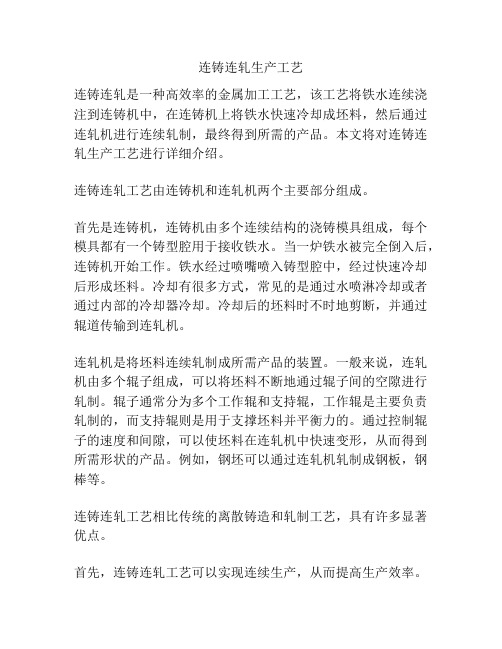
连铸连轧生产工艺连铸连轧是一种高效率的金属加工工艺,该工艺将铁水连续浇注到连铸机中,在连铸机上将铁水快速冷却成坯料,然后通过连轧机进行连续轧制,最终得到所需的产品。
本文将对连铸连轧生产工艺进行详细介绍。
连铸连轧工艺由连铸机和连轧机两个主要部分组成。
首先是连铸机,连铸机由多个连续结构的浇铸模具组成,每个模具都有一个铸型腔用于接收铁水。
当一炉铁水被完全倒入后,连铸机开始工作。
铁水经过喷嘴喷入铸型腔中,经过快速冷却后形成坯料。
冷却有很多方式,常见的是通过水喷淋冷却或者通过内部的冷却器冷却。
冷却后的坯料时不时地剪断,并通过辊道传输到连轧机。
连轧机是将坯料连续轧制成所需产品的装置。
一般来说,连轧机由多个辊子组成,可以将坯料不断地通过辊子间的空隙进行轧制。
辊子通常分为多个工作辊和支持辊,工作辊是主要负责轧制的,而支持辊则是用于支撑坯料并平衡力的。
通过控制辊子的速度和间隙,可以使坯料在连轧机中快速变形,从而得到所需形状的产品。
例如,钢坯可以通过连轧机轧制成钢板,钢棒等。
连铸连轧工艺相比传统的离散铸造和轧制工艺,具有许多显著优点。
首先,连铸连轧工艺可以实现连续生产,从而提高生产效率。
相比离散铸造和轧制工艺,连铸连轧工艺减少了产品在生产过程中的停留时间,有效减少生产周期,提高了生产效率。
其次,连铸连轧工艺可以减少产品的变形和出现缺陷的可能性。
在连铸连轧过程中,坯料的变形是在连续产生的,产品形状相对稳定,因此可以减少变形和出现缺陷的可能性。
同时,由于坯料在连轧过程中受到很大压力的作用,使其内部结构更加紧密,提高了产品的强度和硬度。
最后,连铸连轧工艺还可以减少能耗并降低生产成本。
连续生产可以减少能耗浪费,同时由于工艺参数的控制更加精准,可以减少废品率,降低了生产成本。
总之,连铸连轧是一种高效率的金属加工工艺,通过连续的铸造和轧制过程,可以快速地生产出所需的产品。
其优点包括高生产效率,减少变形和缺陷的可能性,降低能耗和生产成本等。
连铸连轧工艺
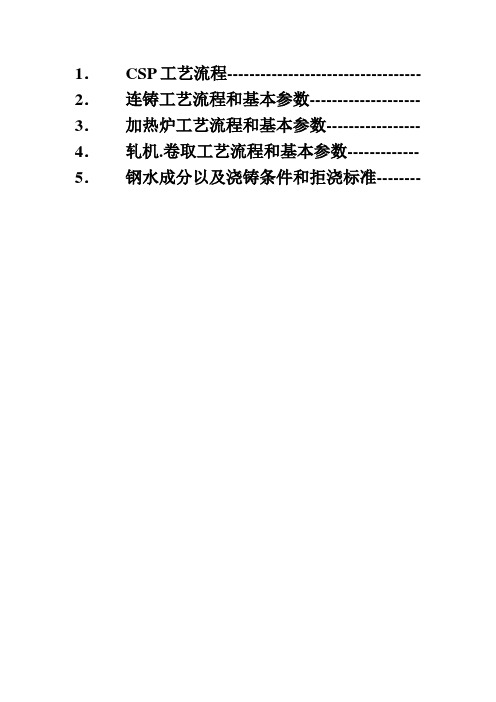
1.CSP工艺流程----------------------------------- 2.连铸工艺流程和基本参数-------------------- 3.加热炉工艺流程和基本参数----------------- 4.轧机.卷取工艺流程和基本参数------------- 5.钢水成分以及浇铸条件和拒浇标准--------连铸工艺流程和基本参数1.工艺流程2.主要工艺参数♦浇铸断面:宽度900-1680mm厚度68-52mm(70mm结晶器)♦浇铸速度:C<0.08% max 5.5m/minC>0.15% max 4.5m/min上引锭杆速度: 4.0m/min♦铸坯导向段长度:8065mm♦顶弯半径:3250mm♦中间包公称容量:36t 液面深度1100mm 溢流容量:38t 液面深度1150mm ♦铸坯定尺:10m-38m大包容量 120t承载能力:2×200t回转半径:5500mm♦中间包车承载能力:62.5 t运行速度: 1.5/15 m/min中间包车升降行程:600mm中间包车升降速度:60mm/s12结晶器振动振幅:±10mm(max)选择振幅±3mm 振频 400次/分(max)±5mm 振频250次/分(max)3.浇钢操作3.1钢水的温度测定液态钢水的温度测定采用人工浸入型一次性热电偶来进行。
用测量方式采用测量,测温系统精度为±3℃。
如果中间包测温T中间包<T液相线+15℃或T中间包>T液相线+48℃,则须补测。
3.23.6浇注周期与拉速匹配关系5. 中间包工艺参数5.1中间包耐火材料的组成及各部分的功能1 2 3 4 5 67 8910115.2中间包相关技术参数中间包几何尺寸基本参数中间包底面距结晶器上口距离 398mm浸入式水口底面距结晶器上口距离 422mm浸入式水口的对中偏差≯±2mm浸入式水口距塞棒的距离 3510mm冲击板中心距挡墙距离 500mm注流保护套管浸入深度 400 mm挡墙距中包底面距离 200 mm挡墙距第一堤坝的距离 150 mm第二堤坝距塞棒距离 660 mm包衬总厚度 210 mm包衬保温层厚度 30 mm包衬永久层厚度 150 mm包衬工作层厚度 30 ~ 50mm水口高出工作层 10 mm水口伸出中包底面 825±5 mm加热炉工艺流程和基本参数一.加热原理1、钢加热的目的a.提高钢的塑性,以降低钢在热加工时的变形抗力,从而减少轧制中轧辊的磨损和断辊等机械设备事故。
连铸工艺与设备之连铸连轧的匹配
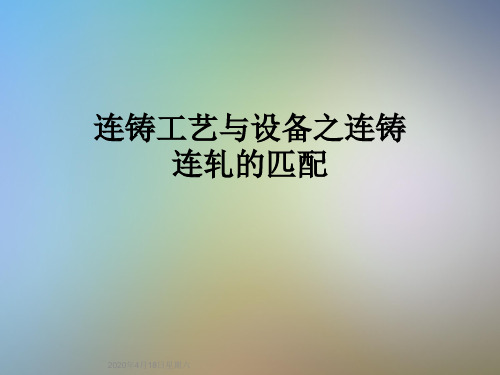
组织性能有更大的提高。
11.3连铸坯热装及直接轧制技术发展概况
连铸连轧技术的起源
•传统轧 钢工序 能源消 耗情况
•加热炉-57.5% •电能-38.6% •其他-3.9%。
•节能的潜 力
20世纪50年代初期,开始实验研究工作,先后 建立了一些连铸连轧试验性机组进行探讨。
连铸-在线同步轧制 •含义
连铸与轧制在同一作业线上,铸坯出连铸机后, 不经切断即直接进行与铸速同步的轧制。
•特点 先轧制后切断,铸与轧同步,铸坯一般要进行在 线加热均温或绝热保温,每流连铸需配置专用轧机( 行星轧机或摆锻机和连锻机),轧机数目1~13架。
可使成材率提高0.5%~1.5%。 3. 简化生产工艺流程 • 减少厂房面积和运输设备,节约基建投资和生产费
用。
•11.2 连铸与连轧衔接工艺类型
4. 生产周期缩短 ➢ 从投料炼钢到轧制出成品仅需几个小时; ➢ 直接轧制时从钢水浇注到轧出成品只需十几分钟
。 5. 产品的质量提高 ➢ 加热时间短,氧化铁皮少,钢材表面质量好; ➢ 无加热炉滑道痕迹,使产品厚度精度也得到提高
•类型3、4为铸坯冷至A3甚至A1线以下温度装炉,称 为低温热装轧制工艺,简称HCR(Hot Charge
Rolling)
•特点:装炉温度一 般在400~700℃之 间。而低温热装工
艺,则常在加热炉
之前还有保温坑或
保温箱等,即采用
双重缓冲工序,以
解决铸、轧节奏匹
配与计划管理问题
。
•类型5为传统的连铸坯冷装炉轧制工艺,简称CCR(Cold Charge Rolling)
•特点:连铸坯 冷至常温后, 再装炉加热后 轧制,一般连 铸坯装炉的温 度在400℃以下 。
连铸连轧工艺及设备
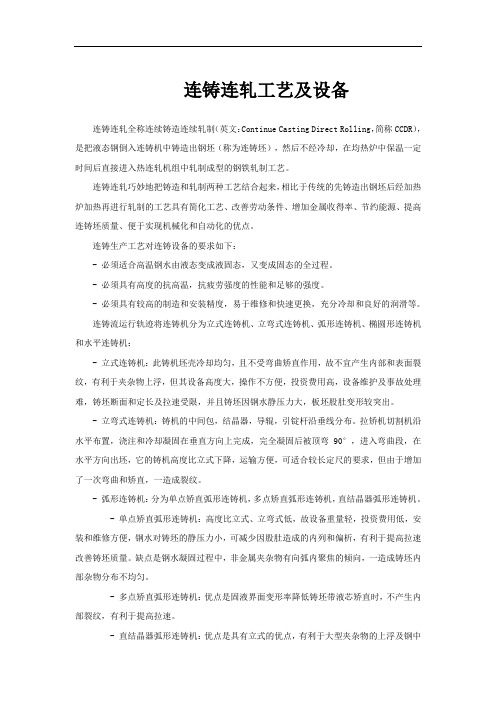
连铸连轧工艺及设备连铸连轧全称连续铸造连续轧制(英文:Continue Casting Direct Rolling,简称CCDR),是把液态钢倒入连铸机中铸造出钢坯(称为连铸坯),然后不经冷却,在均热炉中保温一定时间后直接进入热连轧机组中轧制成型的钢铁轧制工艺。
连铸连轧巧妙地把铸造和轧制两种工艺结合起来,相比于传统的先铸造出钢坯后经加热炉加热再进行轧制的工艺具有简化工艺、改善劳动条件、增加金属收得率、节约能源、提高连铸坯质量、便于实现机械化和自动化的优点。
连铸生产工艺对连铸设备的要求如下:- 必须适合高温钢水由液态变成液固态,又变成固态的全过程。
- 必须具有高度的抗高温,抗疲劳强度的性能和足够的强度。
- 必须具有较高的制造和安装精度,易于维修和快速更换,充分冷却和良好的润滑等。
连铸流运行轨迹将连铸机分为立式连铸机、立弯式连铸机、弧形连铸机、椭圆形连铸机和水平连铸机:- 立式连铸机:此铸机坯壳冷却均匀,且不受弯曲矫直作用,故不宜产生内部和表面裂纹,有利于夹杂物上浮,但其设备高度大,操作不方便,投资费用高,设备维护及事故处理难,铸坯断面和定长及拉速受限,并且铸坯因钢水静压力大,板坯股肚变形较突出。
- 立弯式连铸机:铸机的中间包,结晶器,导辊,引锭杆沿垂线分布。
拉矫机切割机沿水平布置,浇注和冷却凝固在垂直方向上完成,完全凝固后被顶弯90°,进入弯曲段,在水平方向出坯,它的铸机高度比立式下降,运输方便,可适合较长定尺的要求,但由于增加了一次弯曲和矫直,一造成裂纹。
- 弧形连铸机:分为单点矫直弧形连铸机,多点矫直弧形连铸机,直结晶器弧形连铸机。
- 单点矫直弧形连铸机:高度比立式、立弯式低,故设备重量轻,投资费用低,安装和维修方便,钢水对铸坯的静压力小,可减少因股肚造成的内列和偏析,有利于提高拉速改善铸坯质量。
缺点是钢水凝固过程中,非金属夹杂物有向弧内聚焦的倾向,一造成铸坯内部杂物分布不均匀。
- 多点矫直弧形连铸机:优点是固液界面变形率降低铸坯带液芯矫直时,不产生内部裂纹,有利于提高拉速。
连续铸造及其与轧制的衔接工艺

连续铸造及其与轧制的衔接工艺1. 引言连续铸造是一种现代化的铸造工艺,它与传统的间歇铸造相比具有更高的生产效率和质量控制能力。
随着工业技术的发展,连续铸造在轧制过程中的应用也越来越广泛。
本文将介绍连续铸造的基本原理和与轧制的衔接工艺。
2. 连续铸造的原理连续铸造是通过在连铸机上连续铸造金属坯料,将熔融金属倒入预先制备好的连续浇注铸模中,经过一系列冷却和凝固过程,最终形成所需的连续坯料。
连续铸造具有以下几个主要特点:•产量高:连续铸造可以实现连续、自动化生产,生产效率高于传统的间歇铸造。
•质量可控:由于冷却和凝固过程的控制,连续铸造可以获得均匀的结晶组织,从而提高材料的力学性能和物理性能。
•节省能源:连续铸造的过程中可以充分利用余热和余能,提高能源利用效率。
3. 轧制与连续铸造的衔接工艺在连续铸造生产的金属坯料经过冷却和凝固后,需要进行进一步的加工,其中轧制是最常用的一种加工方式。
轧制是利用辊轧机将金属坯料进行塑性变形,最终得到所需的板材、型材或管材。
轧制与连续铸造的衔接工艺主要包括以下几个步骤:3.1 金属坯料的预热在连续铸造后的金属坯料中,由于冷却和凝固过程的影响,金属坯料温度较低,不利于轧制操作。
因此,需要对金属坯料进行预热处理,将其温度提高到适合轧制的范围。
3.2 理化性能测试在进行轧制前,需要对金属坯料进行理化性能测试,以确保其符合轧制要求。
测试项目包括金属材料的化学成分、力学性能和物理性能等。
3.3 轧制机的调试轧制机是进行轧制操作的关键设备,调试工作包括辊轧机的调整和辊轧力的设定,以保证轧制过程中金属坯料的塑性变形符合要求。
3.4 轧制过程的控制轧制过程中,需要对金属坯料的温度、厚度、宽度等进行实时监控和控制。
一般采用自动控制系统,通过传感器和控制算法,对轧制参数进行调整,以实现所需的轧制结果。
3.5 轧制后的检验和修整轧制后的金属板材、型材或管材需要进行质量检验,包括外观质量、尺寸精度和力学性能等。
连续铸造及其及轧制和衔接工艺25页PPT
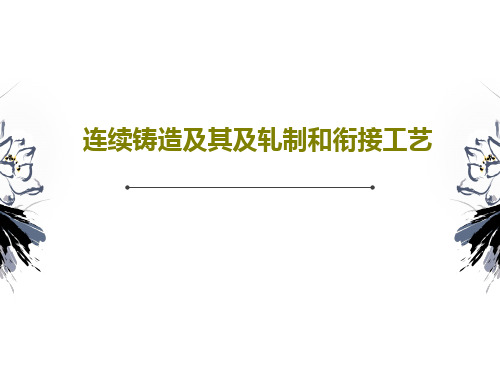
36、“不可能”这个字(法语是一个字 ),只 在愚人 的字典 中找得 到。--拿 破仑。 37、不要生气要争气,不要看破要突 破,不 要嫉妒 要欣赏 ,不要 托延要 积极, 不要心 动要行 动。 38、勤奋,机会,乐观是成功的三要 素。(注 意:传 统观念 认为勤 奋和机 会是成 功的要 素,但 是经过 统计学 和成功 人士的 分析得 出,乐 观是成 功的第 三要素 。
39、没有不老的誓言,没有不变的承 诺,踏 上旅途 ,义无 反顾。 40、对时间的价值没有没有深切认识 的人, 决不会 坚韧勤 勉。
谢谢!
51、 天 下 之 事 常成 于困约 ,而败 于奢靡 。——陆 游 52、 生 命 不 等 于是呼 吸,生命是活 动。——卢 梭
53、 伟 大 的 事 业,需 要决心 ,能力 ,组织 和责任 感。 ——易 卜 生 54、 唯 书 籍 不 朽。——乔 特
55、 为 中 华 之 崛起而 读书。 ——周 恩来
《连续铸造及其与轧制的衔接工艺》课件

1)连铸坯内部绝热技术和烧嘴加热技术相结合。 2)火焰切割机附近采用板坯边部加热装置。可采用电磁感应 加热或煤气烧嘴加热。
连续铸造及其与轧制的衔接工艺
1.3 连铸生产工艺 注意防止各种缺陷的产生,严格控制浇注温度,化学成分要求严格。控制
Mn/Si和Mn/S。 拉坯速度-重要的工艺参数。 根据钢种不同,控制二次冷却区的冷却强度,控制各种缺陷的产生。
连续铸造及其与轧制的衔接工艺
2连铸与轧制的衔接工艺 2.1钢坯断面规格及产量的匹配衔接
连续铸造及其与轧制的衔接工艺
1.1连续机类型 按铸坯断面形状分:厚板坯、薄板坯、大方坯、小方坯、
圆坯、异型坯、椭圆坯连铸机。 按铸坯运行轨迹分:立式、立弯式、垂直-多点弯曲式、
垂直-弧形、多半径弧形(椭圆形)、水平式、旋转式连 铸机。 1.2连铸机组成 钢水运转装置(钢水包、回转台)、中间包及更换装置、 结晶器及其振动装置、二冷区夹持辊及冷却水系统、拉引 矫直机、切断设备、引锭装置。
《连续铸造及其与轧制的衔 接工艺》
连续铸造及其与轧制的衔接工艺
1连续铸钢技术 将钢水连续注入结晶器,待钢水凝成硬壳后从结晶器出口
连续拉出或送出,经喷水冷却,全部凝固后切成坯料或直送 轧制工序。
(1)钢水在结晶器内得到迅速而均匀的冷却凝固,细晶 区较厚,柱状晶不发达。
2+连续铸钢与轧制的衔接工艺
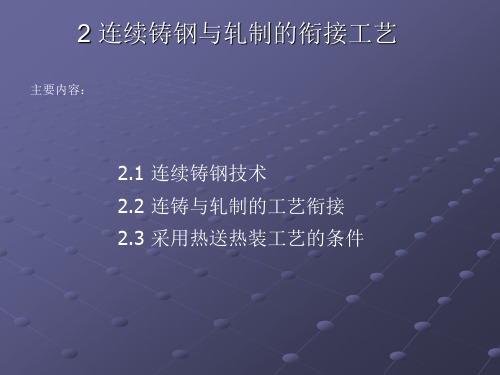
高温热装 低温热装 ( 400℃ 低温界限)
5、常规冷装炉轧制工艺
2.2.2薄板坯连轧连轧CSP工艺(连铸坯直接轧制工艺 )
2.2.3 2.2.3线、棒材车间典型的热装工艺布置(高、低温热装工艺)
采用热装热送工艺的优点:
(1)减少能源消耗、提高加热炉产量。(燃料消耗降低40%~67%,加热炉产 量提高20%~30%) (2)减少金属消耗(加热时间,金属损耗降0.3%) (3)降低建设投资、生产成本(厂房面积、起重设备、钢坯存量、人员) (4)缩短生产周期 (6)轧钢车间生产管理概念的革新、生产更灵活(按规格组织生产——》按钢 种组织生产)
2 连续铸钢与轧制的衔接工艺
主要内容:
2.1 连续铸钢技术 2.2 连铸与轧制的工艺衔接 2.3 采用热送热装工艺的条件
ห้องสมุดไป่ตู้
2.1 连续铸钢技术 什么是连续铸钢?
连铸是把液态钢用 连铸机浇注、冷凝、 连铸机浇注、冷凝、 切割而直接得到铸坯 的工艺, 的工艺,它是连接炼 钢和轧钢的中间环节。 钢和轧钢的中间环节。
5、电磁搅拌 :均匀成分、细化晶粒,加速铸坯凝固,使气体和夹杂 上浮 。 6、多点矫直和压缩浇注 :防止内外裂纹
2.2 连铸与轧制的工艺衔接
2.2.1 连铸-连轧衔接模式
1‘、连续铸轧 1、连铸坯直接轧制工艺 2、连铸坯A3线以上温度装炉 (热送直接轧制) 3、A3线A1线之间温度装炉 (直接热装轧制工艺) 4、A1线以下到400℃温度装 炉(热装轧制)
弧形连铸机工艺示意图
6、引锭装置 7、铸坯切割设备:定尺、火焰切割、液 压或摆动剪
铸坯鼓肚变形示意图
2.1.3 连铸生产工艺
连铸工艺必须保证铸坯的质量和产量, 连铸坯常见的缺陷有: 表面缺陷 内部缺陷 形状缺陷
连续铸钢工艺教程
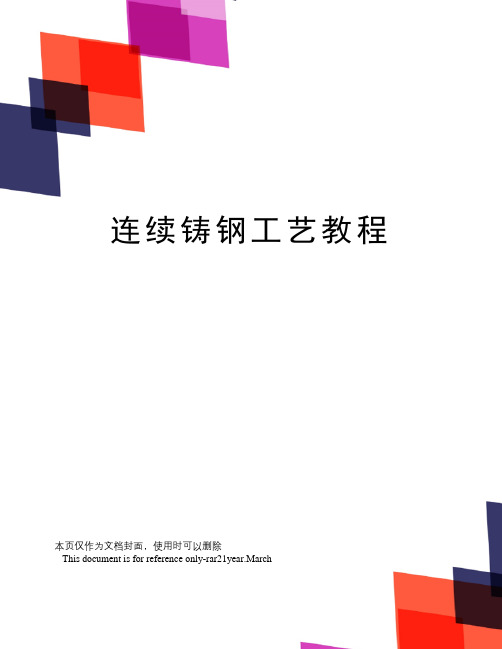
连续铸钢工艺教程本页仅作为文档封面,使用时可以删除This document is for reference only-rar21year.March连续铸钢工艺教程1.连铸工艺1.1连铸工艺介绍连铸全称连续铸钢,与模铸不同,它不是将高温钢水浇铸到一个个的钢锭模内,而是将高温钢水浇注到一个或几个用强制水冷、带有“活底”(叫引锭头)的铜模内(叫结晶器),钢水很快与“活底”凝结在一起,待钢水凝固成一定厚度的坯壳后,就从铜模的下端拉出“活底”,这样已凝固成一定厚度的铸坯就会连续不断地从水冷结晶器内被拉出来,,在二次冷却区继续喷水冷却,带有液芯的铸坯一边走一边凝固,直到完全凝固,待铸坯完全凝固后,用氧气切割或剪切机把铸坯切成一定尺寸的钢坯。
连铸是连接炼钢和轧钢的中间环节,是炼钢生产的重要组成部分,连铸生产的正常与否,不但会影响到炼钢生产任务的完成,还会影响到轧材的质量和成材率。
一台连铸机主要由大包回转台、中间包、中间包车、结晶器、结晶器振动装置、二次冷却装置、拉坯矫直装置、切割装置和出坯辊道等部分组成。
在连铸生产时通常用天车将钢包吊至大包回转台,然后大包转台将钢包旋至浇注位,经大包底部水口把钢水注入到中间包内,打开中间包塞棒后,钢水流入到下口用引锭杆堵塞并能上下振动的结晶器中,钢水沿结晶器周边冷凝成坯壳,当结晶器下端出口处坯壳有一定厚度时,带有液芯并和引锭杆连在一起的铸坯在拉矫装置的作用下,离开结晶器,沿着二冷段的支撑结构下移,与此同时铸坯被二次冷却装置进一步冷却并继续凝固,当引锭装置进入拉矫机后脱去引锭装置,铸坯在全部凝固或带有液芯的状态下被矫直,随后在水平位置被切割成定尺长度,经出坯辊道运送到规定地点,上述整个过程在实际生产中是连续进行的。
1.2我厂连铸机的基本技术参数1.3连铸的主要设备1.3.1钢包回转台钢包回转台设置在电炉、精炼同一跨,它的本体是一个具有两个钢包支撑架的转臂,绕回转台中心回转,钢包回转台工作时,出钢跨一侧的天车将盛满钢水的钢包吊放到支撑架上,然后回转台旋转180o,将钢包转到连铸跨中间包上方的浇注位进行浇注,浇注完毕,再把空包转出的同时,又把另一个盛满钢水的钢包旋转到浇注位置,这样就可以快速更换钢包,实现多炉连浇。
电池ccs工艺

电池ccs工艺
电池CCS工艺是一种关键的制造工艺,它在电池领域发挥着重要作用。
CCS,即连续铸轧工艺 (Continuous Casting and Rolling) ,是指通过连续铸造和连续轧制的方式,生产出具有均匀结构和优异性能的电池材料。
在电池制造过程中,CCS工艺的应用具有诸多优势。
首先,它能够大幅提高生产效率。
传统的电池制造方法需要多道工序,而CCS工艺则将连续铸造和连续轧制有机地结合在一起,实现了工艺流程的高度集成,大大节省了时间和资源。
CCS工艺还能够显著提升电池材料的品质。
通过连续铸造和连续轧制,电池材料的晶粒结构更加均匀,内部缺陷更少,从而提高了电池的导电性能和耐久性。
此外,CCS工艺还能够对电池材料进行精确的尺寸控制,使得电池的尺寸更加一致,提高了电池组件的装配质量。
在CCS工艺中,连续铸造起着关键的作用。
通过将熔融的电池材料注入连续铸造机中,经过冷却和凝固,形成连续的电池片。
这些电池片具有均匀的厚度和宽度,并且内部结构紧密有序。
接下来,这些电池片会经过连续轧制机的处理,进一步改善材料的性能。
CCS工艺的实施需要高度的自动化控制和精密的设备。
通过采用先进的传感技术和自动控制算法,可以实现对连续铸造和连续轧制过
程的精确控制。
这样不仅可以提高生产效率,还可以减少人为操作错误的发生,确保电池材料的质量稳定可靠。
总的来说,电池CCS工艺是一项重要的技术创新,它革新了传统的电池制造方法,提高了生产效率和产品质量。
随着科技的不断进步,CCS工艺将会在电池领域发挥越来越重要的作用,为电池技术的发展带来更多的可能性。
连续铸造工艺

图1 立式离心铸造示意图
1-浇包 2-铸型 3连-液续体金铸属造4-,皮带由轮于和皮金带属5-旋被转迅轴 6速-铸冷件 却7-电(动机30秒以内),导致合金结晶致密,组织均 也3)调有整在扇旋匀形转,段轮辊槽机子中械间成距形性的能线材较连好续铸;造而。离心铸造时,由于合金中不同金属的原子量不同,离心力 连续铸造使和得普通原铸子造比量较大有下的述金优点属:分部靠近外表面(距离轴心远),这样就使得合金的分部不 也连有续在 铸旋造均转使匀轮用槽的;中设砂成备形和铸的工的线艺材过冷连程却续都铸很非造简常。单,慢生,产效导率致和金其属冷利用却率过高,程用中以和很轧多机组金成属生产原线子时, 出还现可大抱量团节省的能现源。象,导 3)调整扇致形金段辊属子密间距度分部不再均匀。 1连、续由铸于造金使属用被连的迅设续速备冷铸和却工造,艺结时过晶程,致都密铸很,简件组单织上,均生没匀产,有效机率浇械和性注金能属系较利好统用;率的高冒,用口以,和轧故机连组成续生铸产线锭时在,还轧可制大量时节不省能用源切。 头去 如果用两尾个,圆辊节组约成结了晶金器则属可,用于提薄高板连了续收铸造得。率; 图 3、2为简铁 化简管 了化连 工续 序了铸 ,工造 免。 除序造,型及免其除它工造序型,因及而其减轻它了工劳动序强,度;因而减轻了劳动强度;所需生产面积也大为 离心铸造减的少生产;长度受到了限制,其直径决定了产品铸造长度。 连图续2 卧铸式造离在心国铸连内造外续示已意铸经图被造广生泛采产用易,如于连实续铸现锭机(钢械或化有色和金属自锭动),化连,续铸铸管锭等。时还能实现连铸连轧,大大提 1-浇包高2-浇了注生槽 3产-铸效型 4率-液,体金在属大5-端规差模6-生铸件产的情况下,其成本较低; 3图)调2为整铁扇管形连段续辊离铸子心造间。距铸造的生产长度受到了限制,其直径决定了产品铸造长度。连续铸造非 从机械强但度不方面会说受,由到于铸铜合造金长从连度续的铸造限结制晶器,中而流出且,可在一以定短程度期上内,结进晶行器起大到规了挤模压生作用产,;所以同其时强度,也离会比心离铸心铸造造高出 11、0%由到于生2金0%产属之被过间迅程速冷中却,,结表晶面致密氧,化组织层均较匀,厚机,械性从能而较好使;得铸造尺寸和终端毛坯尺寸差距较大,离 在连续铸心造铸生产造过;程中也极易出现各种各样的质量问题,如:漏钢、裂纹、偏析、针孔、机械性能不合格等,从钢水冶炼、铸造工艺参 数图确2 卧定式、离连心铸铸复设造备杂示等意断,图从面以生下几产个能方面力阐:述了离如心何在铸整造个生并产不过程能中根进行据质客量控户制的以得要到求优质生铸产坯。具有复杂断面结构 1-浇包的2-浇产注品槽 3,-铸而型 4高-液端体金连属续5-端铸差造6-可铸件以,并且可以将成本控制得很低 3简)采化用了气工水序冷,却从免方除机法造,械型选及强用其合度它理工方气序水面,比因说而,减轻由了于劳动铜强合度;金从连续铸造结晶器中流出,在一定程度上, 2、主要结工晶艺参器数起的制到定了挤压作用,所以其强度也会比离心铸造高出10%到20%之间
- 1、下载文档前请自行甄别文档内容的完整性,平台不提供额外的编辑、内容补充、找答案等附加服务。
- 2、"仅部分预览"的文档,不可在线预览部分如存在完整性等问题,可反馈申请退款(可完整预览的文档不适用该条件!)。
- 3、如文档侵犯您的权益,请联系客服反馈,我们会尽快为您处理(人工客服工作时间:9:00-18:30)。
3.1 连续铸钢技术 连续铸钢是将钢水连续注入水冷结晶器,
待钢水凝成硬壳后从结晶器出口连续拉出或 送比,经喷水冷却,全部凝固后切成坯料或 直送轧制工序的铸造坯料,称为连续铸坯。
2020/5/31
1
连续铸坯在冶金学方面的特点是:
(1)钢水在结晶器内得到迅速而均匀的冷却凝
(1)钢坯生产的主要方法 1)轧制法—在初轧(或开坯)机上将钢锭轧 成各种断面形状的钢坯的方法。
2)锻造法—用锺锤(或水压机)将钢锭锻成 各种断面形状的钢坯的方法。
3)连铸法—在连铸机上采用连续铸造直接将 钢水浇注成各种断面形状的钢坯的方法。
4)压铸法—在连铸机上将钢水压铸成各种断 面形状的钢坯的方法。
拉坯速度对连铸产量、质量皆有很大的影响。
引锭装置的作用是在连铸开始前,用引锭头堵
住结晶器下口,待钢水凝固后将铸坯引拉出铸
机,再脱开引锭头,将引锭杆收入存放装置。
铸坯切割设备则将连续运动中的铸坯切割成定
尺,常用的切割设备有火焰切割器或液压剪与
摆动剪。 2020/5/31
8
3.2 钢坯生产及连铸与轧制生产的连续化
2020/5/31
5
连铸机的组成 —般连铸机由钢水运载装置(钢水包、回转 台)、中间包及其更换装置、结晶器及其振动装 置、二冷区夹持辊及冷却水系统、拉引矫直机、
。 切断设备、引锭装置等组成
2020/5/31
6
中间包起缓冲与净化钢液的作用,容量一般为 钢水包容量的20%~40%,铸机流数越多,其 容量愈大。结晶器是连铸机的心脏,要求有良 好的导热性、结构刚性、耐磨性及便于制造和 维护等特点,一般由锻造紫铜或铸造黄铜制成。 其外壁通水强制均匀冷却。结晶器振动装置的 作用是使结晶器作周期性振动,以防止初生坯 壳与结晶器壁产生粘结而被拉破。振动曲线一 般按正弦规律变化,以减少冲击。其振幅和频 率应与拉速紧密配合,以保证铸坯的质量和产 量。
2020/5/31
14
• 连铸坯直接轧制(CC-DR),钢坯温度一般在1150℃ 以上,连铸机生产的高温连铸坯切割后直接输送到轧机 中进行直接轧制,一般情况下,在连铸和轧机间设有 均热炉,一方面对输送过程中的连铸坯进行边角补热 或均热,另一方面作为缓冲以便轧机出现事故时储存 热钢坯。这种模式要求连铸与轧机的小时能力高度匹 配,轧机能力应大于连铸机的能力。(板带生产基本 属于该模式)
• 连铸坯热装轧制(CC—-HCR),这种模式 的热装温度一般300℃—600℃,这种模式比较 适合连铸车间与轧钢车间距离较远,且连铸能 力与轧机能力不能很好匹配的情况。
• 连铸坯两相区热装轧制(CC—(+)-HCR), 连 铸 坯 直 接 热 装 轧 制 ( CC—DHCR ) , 这 两 种模式的热装温度一般在600℃~1150℃,比 较适合连铸车间与轧钢车间距离很近,且连铸 机与轧机小时能力基本匹配的情况。(棒、线、 型钢生产基本属于该模式)
各种方法生产的钢坯之比较见表下:
2020/5/31
9
2020/5/31
10
连铸法生产的优点:
1)不用初轧机简化了生产工序和设备、 节省投资和劳动力;
2)比初轧坯形状好,成分均匀、坯长 (重量)易调节;
3)成材率提高6~13%,可达94%以上。
4)能耗低、可降低成本10%
5)易热装、热送、直接轧制和实现自动 化。
固,形成较厚的细晶表面凝固层,无充分时
间生成柱状晶区;(2)连续浇铸可避免形成缩
孔或空洞,无铸锭之头尾剪切损失,使金属
收得率大为提高;(3)整灌钢水的连铸自始至
终的冷却凝固时间接近,连铸坯纵向成分偏
差可控制在10%以内,远比模铸钢锭为好,
(4)在塑性加工时为消除铸态组织所需的压缩
比也可以相对减小,铸坯的组织致密,有良
2020/5/31
7
二冷装置安装在紧接结晶器的出口处,其作用
是借助喷水或雾化冷却以加速铸坯凝固并控制
铸坯的温度,夹辊和导辊支撑着带液心的高温
铸坯,以防止鼓肚变形或造成内裂。要求二冷
装置水压、水量可调,以适应不同钢种和不同
拉速的需要。拉矫机的作用是提供拉坯动力及
对弯曲的铸坯进行矫直,并推动切割装置运动。
2020/5/31
11
连铸法不足:
1)钢种受一定限制,目前仅限于镇静钢、 半镇静钢;
2)压缩比受限制,不宜生产特厚板。 3)规格少,连铸工艺较复杂。
由于连铸法的上述优点,80年代以来获 得迅速发展,连铸法已成为钢坯生产的 主要生产方式和发展方向。
2020/5/31
12
3.3 连铸与轧制的衔接模式
2020/5/31
4
弧形连铸机大大降低了设备的高度,仅为立式的1/2-1/3, 投资少,操作方便,利于拉速的提高,但缺点是存在设 备对弧较难,内外弧冷却欠均匀,弯曲矫直应力较大及 夹杂物在内弧侧聚集的缺点,故对钢水纯净度要求更高。 椭圆形连铸机为分段改变弯曲半径,故设备更低,称为 超低头铸机。垂直-弧形和垂直-多点弯曲形连铸机采用 直结晶器并在其下部保留2m左右的直线段,使铸机的高 度增加不多,而有利于克服内弧侧夹杂物富集的缺点。 水平式铸机设备高度更低,更轻便且投资少,但尚不能 制成大生产适用机型。目前世界各国弧形铸机占主导地 位,达60%以上。其次为垂直-多点弯曲形。板坯和方坯 多采构垂直弧形,而垂直-多点弯曲形则呈增加趋势。
好的机械性能。
2020/5/31
2
连铸机类型 连铸机可以按铸坯断面形状分为厚板坯、
薄板坯、大方坯、小方坯、圆坯、异型钢 坯及椭圆形钢坯连铸机等,也可按铸坯运 行的轨迹分为立式、立弯式、垂直-多点弯 曲形、垂直-弧形、多半径弧形(椭圆形)、 水平式及旋转式连铸机 。
2020/5/31
3
立式连铸机出现最早,其优点是钢中夹杂易于 上浮排除,凝壳冷却均匀对称,不受弯曲矫直 应力,适用于裂纹较敏感钢种的连铸,但缺点 是设备高度大,建设投资大,且钢水静压力大 易使钢坯产生鼓肚变形,铸坯断面和长度都不 能过大,拉速也不宜过高。立弯式连铸机为降 低设备高度,将完全凝固的铸坯顶弯成90°角, 在水平方向出坯,消除了定尺长度的限制,降 低了设备的投资,但缺点是铸坯受弯曲矫直应 力,易产生裂纹。
1)连铸坯冷装炉轧制(CCR)-连铸坯与轧 机距离远或不能匹配,不能热装热送。
2)连铸坯冷至A1线以下状态热装轧制 (-HCR)。
3)连铸坯冷至两相(+)区,热装轧制 (+-HCR)。
4)连铸坯直接热装轧制(CC - DHCR) 。
5)连铸坯直接轧制 (CC- DR) 。
2020/5/31
13
不同衔接模式适应范围