延长渣油加氢硫装置运行周期的技术
渣油加氢工艺的研究与应用
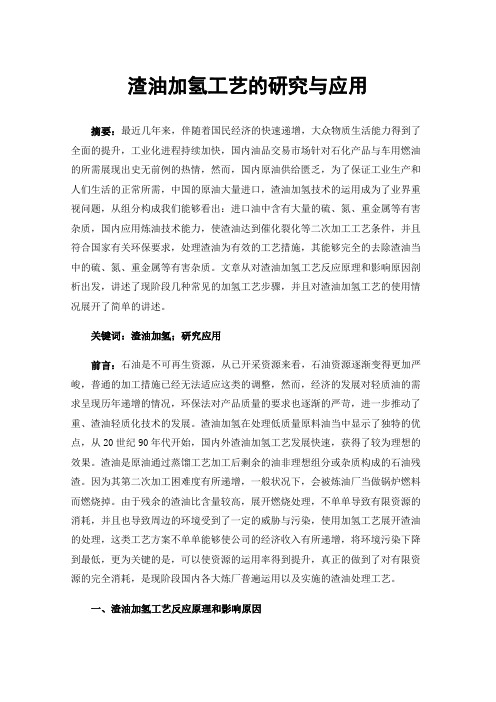
渣油加氢工艺的研究与应用摘要:最近几年来,伴随着国民经济的快速递增,大众物质生活能力得到了全面的提升,工业化进程持续加快,国内油品交易市场针对石化产品与车用燃油的所需展现出史无前例的热情,然而,国内原油供给匮乏,为了保证工业生产和人们生活的正常所需,中国的原油大量进口,渣油加氢技术的运用成为了业界重视问题,从组分构成我们能够看出:进口油中含有大量的硫、氮、重金属等有害杂质,国内应用炼油技术能力,使渣油达到催化裂化等二次加工工艺条件,并且符合国家有关环保要求,处理渣油为有效的工艺措施,其能够完全的去除渣油当中的硫、氮、重金属等有害杂质。
文章从对渣油加氢工艺反应原理和影响原因剖析出发,讲述了现阶段几种常见的加氢工艺步骤,并且对渣油加氢工艺的使用情况展开了简单的讲述。
关键词:渣油加氢;研究应用前言:石油是不可再生资源,从已开采资源来看,石油资源逐渐变得更加严峻,普通的加工措施已经无法适应这类的调整,然而,经济的发展对轻质油的需求呈现历年递增的情况,环保法对产品质量的要求也逐渐的严苛,进一步推动了重、渣油轻质化技术的发展。
渣油加氢在处理低质量原料油当中显示了独特的优点,从20世纪90年代开始,国内外渣油加氢工艺发展快速,获得了较为理想的效果。
渣油是原油通过蒸馏工艺加工后剩余的油非理想组分或杂质构成的石油残渣。
因为其第二次加工困难度有所递增,一般状况下,会被炼油厂当做锅炉燃料而燃烧掉。
由于残余的渣油比含量较高,展开燃烧处理,不单单导致有限资源的消耗,并且也导致周边的环境受到了一定的威胁与污染,使用加氢工艺展开渣油的处理,这类工艺方案不单单能够使公司的经济收入有所递增,将环境污染下降到最低,更为关键的是,可以使资源的运用率得到提升,真正的做到了对有限资源的完全消耗,是现阶段国内各大炼厂普遍运用以及实施的渣油处理工艺。
一、渣油加氢工艺反应原理和影响原因在渣油加氢的过程当中,时常会同时出现精制和裂化两种反应,其主要的反应方式有以下几个方面:1.脱硫反应渣油加氢处理工艺当中最为关键的化学反应则是脱硫反应,因为渣油硫化物的类别以及结构繁琐多样,因此,在实际的反应过程当中,所囊括的脱硫反应也较为繁琐。
VRDS渣油加氢装置概况

VRDS渣油加氢装置概况1.1 装置简介为适应原油逐年重质化、劣质化的趋势,提高轻油收率和减少环境污染,胜利炼油厂于1989年10月份从美国雪弗隆(Chevron)公司引进了设计能力为84×104t/a的固定床减压渣油加氢脱硫装置(简称VRDS)。
该装置由华鲁工程公司设计,中石化十化建承建,1992年5月21日建成投产。
1998年,根据中石化公司整体原油加工方案的安排,胜利炼油厂需要掺炼75%(6.0 Mt/a)的进口中东高硫原油,胜利炼油厂原有以加工胜利原油为主的加工流程难以适应劣质高硫原油的加工,为此,1999年10月份装置进行了扩能改造,增加了Chevron公司的最新专利—上流式反应器(Up Flow Reactor,简称UFR),因此,装置又简称为UFR/VRDS。
2000年1月7日完成并投产。
装置改造后的设计处理能力150×104t/a(其中包括120×104t/a减压渣油及30×104t/a减压蜡油),主要对中东减压渣油进行脱硫、脱氮、脱金属并部分裂解为石脑油、柴油和蜡油。
设计运转初期,349℃产品馏份的MCR为<8.5%,S<0.5%,末期MCR<9.2%、S<0.8%,生产的石脑油可作为乙烯原料,柴油是优质的低硫轻柴油产品,常压渣油是优质的催化裂化原料。
2005年,随着VRDS—FCC组合工艺的投用,常压和减压渣油混合做为催化原料,催化回炼油改进本装置处理,优化了FCC装置原料性质,提高了FCC装置轻油收率。
2006年10月份,利用第五周期停工检修时机,进行了装置节能改造,主要改造内容是停开减压塔,对原料/产品换热网络进行优化和流程动改,及对加热炉烟气余热回收系统进行改造。
2006年11月14日装置开工正常。
目前随着催化剂级配及操作的不断优化,装置运行周期已延长到480天。
图3-1 渣油加氢装置方块流程图1.2 工艺原理1.2.1 工艺过程渣油加氢作为重油加工的重要手段,在整个炼厂的加工工艺中有着十分重要的地位。
沿江炼油厂首套渣油加氢装置的运行分析
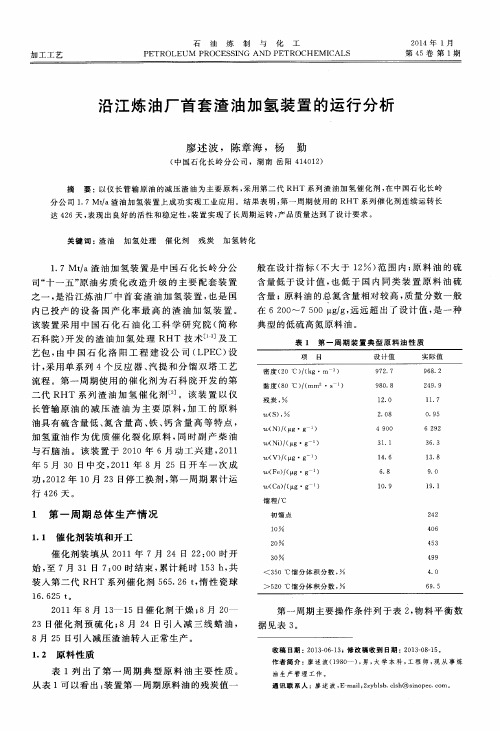
艺包 , 由 中 国石 化 洛 阳 工 程 建 设 公 司 ( L P E C) 设 计, 采 用单 系列 4个 反 应 器 、 汽 提 和 分 馏 双 塔工 艺
流程 。第 一周 期使 用 的催 化 剂 为 石 科 院 开 发 的第 二代 RHT系 列 渣 油 加 氢 催 化 剂 ] 。该 装 置 以仪
年 5月 3 0 E l 中交 , 2 0 1 1 年 8月 2 5 E l 开 车 一 次 成 功, 2 0 1 2年 1 O月 2 3日停 工换 剂 , 第 一周 期 累 计 运
行 4 2 6天 。
1 第 一周 期 总体 生产 情 况
1 . 1 催 化剂 装填 和开 工
催化 剂装 填 从 2 0 1 1年 7月 2 4日2 2 : 0 0时 开
始, 至 7月 3 1日 7 : O 0时 结束 , 累计 耗 时 1 5 3 h , 共 装 入第 二代 RHT系列 催 化剂 5 6 5 . 2 6 t , 惰 性 瓷 球
1 6. 6 2 5 t 。
2 0 1 1年 8月 1 3 l 5 日催 化 剂 干 燥 ; 8月 2 0
从表 1 可 以看 出 : 装置 第一 周期 原料 油 的残炭 值一
作者简介 : 廖 述 波( 1 9 8 O 一) , 男, 大学本科 , 工 程 师, 现 从 事 炼
油 生产 管 理 工 作 。 通讯联系人 : 廖述 波, E ma i l : 2 z y b l s b . c l s h @s i n o p e c . c o m。
6 0
石 表 2 第 一 周 期 装 置 主 要 操 作 条 件
油
渣油加氢装置运行中存在问题及解决措施

渣油加氢装置运行中存在问题及解决措施摘要:经济发展和时代的发展趋势进一步促进了炼油厂工业生产的发展趋势,而渣油加氢加工工艺以及机器设备做为当中的关键环节,对所有领域的进步有着至关重要的危害。
与此同时,在渣油的生产加工中,渣油加氢装置可以提升油品质量。
殊不知,因为多种缘故,渣油加氢装置在运转环节中常常出现异常,不能合理提升油品质量。
对渣油加氢装置运作中存在问题开展了剖析,并指出了相对的解决方案。
关键词:渣油加氢工艺;装置运行引言:伴随着社会经济的飞速发展,现阶段大家已经离不了石油。
在炼油厂工业生产的发展趋势中,必须借助渣油加氢加工工艺以及机器设备,对渣油开展生产加工和过滤,提升油品质量,为大家的日常生活给予协助。
但机器设备存在的不足会限定油品质量和加氢裂化机器设备的功效。
仅有不断完善和提升,才可以更好地发挥功效。
一、渣油加氢装置工艺重要性固定床渣油加氢加工工艺做为现阶段最成熟稳定的工艺,在渣油加氢加工工艺中占主导性。
因为原料油的复杂和劣质性及其固定床反应釜的特性,固定床渣油加氢装置的运行周期时间较短,通常仅有一年,有的装置运行2年,而做为冶炼厂关键生产制造装置的催化裂化装置的运行周期时间大多数在三年以上,造成渣油加氢装置和催化裂化装置的运行周期时间不配对。
渣油加氢停产期内,必须对催化裂化原料开展更新以确保正常的运行,这对公司的石油选购和配制明确提出了很高的规定,对公司的经济收益造成了危害。
因而,消除影响渣油加氢装置平稳运行的多种要素,适度增加渣油加氢装置的运行时长具备关键实际意义。
在其中,渣油加氢装置应用的原料主要是常减压装置的常压渣油和减压渣油的混合物质。
最后产品是脱硫、脱氮、脱金属材料、脱残炭的加氢渣油,所占比例大,也会形成小量的石脑油和柴油。
生产制造的渣油可以为催化裂化装置的原料,降低焦炭的生成,大大提高催化裂化装置的产量,并对催化裂化装置生产制造的柴油和汽油的提质增效。
因而,渣油加氢装置的运转效果和质量对全部炼油厂工业生产至关重要。
应用上流式反应技术扩能改造渣油加氢脱硫装置

油。
应器前增加一 台上流式反应器 , 其技术特点为 : 由 于反应物流自下而上 流动, 使催化剂床层略呈现膨 胀, 因而初始压力 降小 , 从而解决 了常规 固定床反
的经 济效 益
技术 , 由于系统压降的增加将会使 改造 的投资增 大; 若采用 O R专利技术 , C 在经济上不合理 因此 决定该 装置 的 改造 采用 上 流 式 反 应 器 专 利 技 术 。 U R是 O R技术的一部分 , F C 即在常规 的固定床反
() 3 根据上流式反应器的技术要求 , 对上流式 反应 器进料 油品 粘度有一 定 限制 , 需要提供 一定 量
如果原设计不作改动, 处理这种劣质渣油预计其处 理量只能达到 60k a 0 t 。为满足加工流程 的安排 , / 该装 置 的处 理 能力 必须从 60k. 扩 能改造 到 15 0 ta / .
Mta / 。因此 , 在选 择 改造 方 案 时 , 论 是 工 艺 技 术 无 的选择 , 是工 程 设 计 方案 的确 定 , 改 造 的 技术 还 其
难度都很大。
裹 1 齐鲁 I ∞s装置改造前后 的原料油性质对 比
器( v ) u a 专利技术 , 由中国石化北京设计院完成工 程设计 , l 对 I DS装 置 进 行 扩 能 改 造 。l S装置 于 I D
19 99年 1 0月停工 改造 , 20 于 00年 1 7日投产 。 月 2 上流 式反应 器专 利技 术应 用的必 要性及 装 置改
工 的孤 岛减 压渣油 的硫 含 量 增加 3 ,%, N +v 52 ( i ) 总金属 含量 增加 2 以 上 , 炭 含量 增 加 1.% 倍 残 54
浆态床渣油加氢长周期运行问题及优化措施
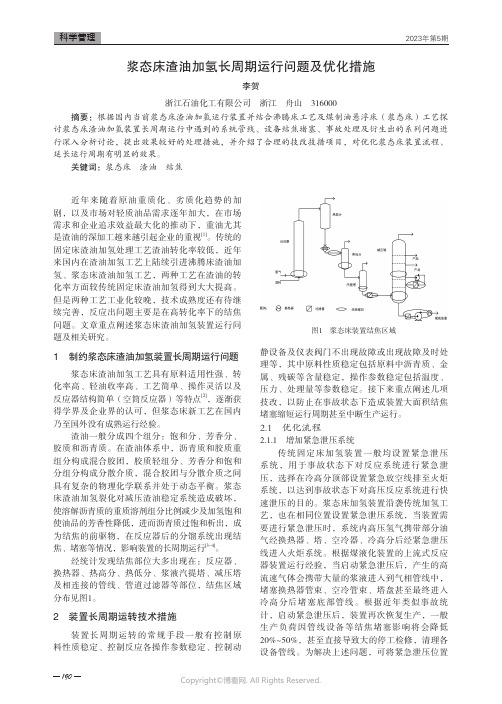
190近年来随着原油重质化、劣质化趋势的加剧,以及市场对轻质油品需求逐年加大,在市场需求和企业追求效益最大化的推动下,重油尤其是渣油的深加工越来越引起企业的重视[1]。
传统的固定床渣油加氢处理工艺渣油转化率较低,近年来国内在渣油加氢工艺上陆续引进沸腾床渣油加氢、浆态床渣油加氢工艺,两种工艺在渣油的转化率方面较传统固定床渣油加氢得到大大提高。
但是两种工艺工业化较晚,技术成熟度还有待继续完善,反应出问题主要是在高转化率下的结焦问题。
文章重点阐述浆态床渣油加氢装置运行问题及相关研究。
1 制约浆态床渣油加氢装置长周期运行问题浆态床渣油加氢工艺具有原料适用性强、转化率高、轻油收率高、工艺简单、操作灵活以及反应器结构简单(空筒反应器)等特点[2],逐渐获得学界及企业界的认可,但浆态床新工艺在国内乃至国外没有成熟运行经验。
渣油一般分成四个组分:饱和分、芳香分、胶质和沥青质。
在渣油体系中,沥青质和胶质重组分构成混合胶团,胶质轻组分、芳香分和饱和分组分构成分散介质,混合胶团与分散介质之间具有复杂的物理化学联系并处于动态平衡。
浆态床渣油加氢裂化对减压渣油稳定系统造成破坏,使溶解沥青质的重质溶剂组分比例减少及加氢饱和使油品的芳香性降低,进而沥青质过饱和析出,成为结焦的前驱物,在反应器后的分馏系统出现结焦、堵塞等情况,影响装置的长周期运行[3-4]。
经统计发现结焦部位大多出现在:反应器、换热器、热高分、热低分、浆液汽提塔、减压塔及相连接的管线、管道过滤器等部位,结焦区域分布见图1。
2 装置长周期运转技术措施装置长周期运转的常规手段一般有控制原料性质稳定、控制反应各操作参数稳定、控制动静设备及仪表阀门不出现故障或出现故障及时处理等,其中原料性质稳定包括原料中沥青质、金属、残碳等含量稳定,操作参数稳定包括温度、压力、处理量等参数稳定。
接下来重点阐述几项技改,以防止在事故状态下造成装置大面积结焦堵塞缩短运行周期甚至中断生产运行。
炼油厂延迟焦化装置生产运行优化措施

炼油厂延迟焦化装置生产运行优化措施摘要:随着延迟焦化原料的恶化,已经切实影响延迟焦化装置长周期运行,延迟焦化装置的加热炉,焦碳塔和分馏塔的良好运行是该装置长周期安全运行的关键。
以炼油厂90万吨/年延迟焦化装置为例,分析了影响该厂长期运营的相关因素后,在装置大修期间采取了优化和改造措施,以确保能够满足装置长周期安全生产及创效。
关键词:长周期;延迟焦化;瓶颈;优化措施延迟焦化作为炼油厂重要的二次加工技术,由于原料适应性范围广,加工成本低以及成熟可靠的技术而继续被广泛使用。
其运行的平稳与否直接影响着炼油厂其它装置的正常运行,焦化装置属于炼油二次加工装置。
随着炼油企业节能减排的要求以及技术的进步,炼油厂各装置直接供料成为主流,装置间的相互影响更显突出。
随着原油资源的消耗,原油性质的劣质化趋势明显。
受此影响,焦化装置原料劣质化趋势也明显加剧,不断给装置的长周期稳定运行工作带来新的问题与挑战。
因此,及时总结经验,为装置管理提供技术支持和指导,保证延迟焦化装置全面实现无故障、长周期运行打下坚实的基础,已经成为一项非常必要的工作。
天津分公司炼油部1#延迟焦化装置最初设计原料参照辽河渣油中石化北京设计院总承包,中石化第四建设公司承建,为两炉四塔的生产模式。
装置始建于1996年,初始设计为100万吨/年,加工原料为大港原油的减压渣油。
后在2005年进行扩能改造为120万吨/年,同时进行了部分材料升级,以适应加工含硫原油的减压渣油。
2008年装置改为加工高硫原油的减压渣油,加工规模按照90万吨/年设计。
延迟焦化装置规模90万吨/年,设计生焦周期为24小时,操作弹性为60%~120%。
年开工时数8400小时。
循环比为0.3,可在0.2~0.4的范围内调节。
1#延迟焦化的主要产品是石油焦。
中间产品有干气,液态烃,汽油,柴油,蜡油。
装置生产的焦化干气,去干气脱硫单元,脱硫后作燃料气或作制氢原料。
焦化液化气脱硫后最为产品或去气分再加工成丙烯等产品。
渣油加氢装置循环氢脱硫的优化
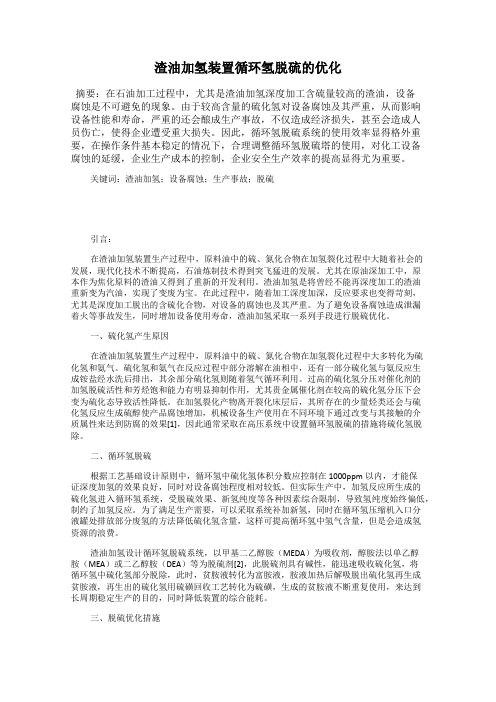
渣油加氢装置循环氢脱硫的优化摘要:在石油加工过程中,尤其是渣油加氢深度加工含硫量较高的渣油,设备腐蚀是不可避免的现象。
由于较高含量的硫化氢对设备腐蚀及其严重,从而影响设备性能和寿命,严重的还会酿成生产事故,不仅造成经济损失,甚至会造成人员伤亡,使得企业遭受重大损失。
因此,循环氢脱硫系统的使用效率显得格外重要,在操作条件基本稳定的情况下,合理调整循环氢脱硫塔的使用,对化工设备腐蚀的延缓,企业生产成本的控制,企业安全生产效率的提高显得尤为重要。
关键词:渣油加氢;设备腐蚀;生产事故;脱硫引言:在渣油加氢装置生产过程中,原料油中的硫、氮化合物在加氢裂化过程中大随着社会的发展,现代化技术不断提高,石油炼制技术得到突飞猛进的发展。
尤其在原油深加工中,原本作为焦化原料的渣油又得到了重新的开发利用。
渣油加氢是将曾经不能再深度加工的渣油重新变为汽油,实现了变废为宝。
在此过程中,随着加工深度加深,反应要求也变得苛刻,尤其是深度加工脱出的含硫化合物,对设备的腐蚀也及其严重。
为了避免设备腐蚀造成泄漏着火等事故发生,同时增加设备使用寿命,渣油加氢采取一系列手段进行脱硫优化。
一、硫化氢产生原因在渣油加氢装置生产过程中,原料油中的硫、氮化合物在加氢裂化过程中大多转化为硫化氢和氨气。
硫化氢和氨气在反应过程中部分溶解在油相中,还有一部分硫化氢与氨反应生成铵盐经水洗后排出,其余部分硫化氢则随着氢气循环利用。
过高的硫化氢分压对催化剂的加氢脱硫活性和芳烃饱和能力有明显抑制作用,尤其贵金属催化剂在较高的硫化氢分压下会变为硫化态导致活性降低。
在加氢裂化产物离开裂化床层后,其所存在的少量烃类还会与硫化氢反应生成硫醇使产品腐蚀增加,机械设备生产使用在不同环境下通过改变与其接触的介质属性来达到防腐的效果[1],因此通常采取在高压系统中设置循环氢脱硫的措施将硫化氢脱除。
二、循环氢脱硫根据工艺基础设计原则中,循环氢中硫化氢体积分数应控制在1000ppm以内,才能保证深度加氢的效果良好,同时对设备腐蚀程度相对较低。
渣油加氢装置长周期运行的影响因素及其对策

渣油加氢装置长周期运行的影响因素及其对策摘要:渣油加氢装置长周期运行受到多种因素的影响,因此,本文简要阐述了装置长周期运行的影响因素的基本内容,重点对渣油加氢装置长周期运行的三种措施进行探讨分析,主要是催化剂的研发、高效率设备的使用和加强原料管理的方式来稳定渣油加氢装置的正常使用。
关键词:渣油加氢;装置;周期引言:渣油是指原油经过减压蒸馏所得到的残余油,主要呈现为黑色粘稠半固体形状,而渣油加氢装置对渣油进行作用。
为降低该装置在使用过程中受催化剂、高压换热器和反应器物流、使用材料等方面的不良影响,要增加科学技术的运用,从而有效增加该装置的使用寿命,保证装置的稳定运行。
1装置长周期运行的影响因素1.1催化剂催化剂是通过化学反应产生一定的催化作用,以此改变物质反应速度。
在渣油加氢装置长周期运行中会产生很多金属类杂质,仅仅依靠单一的催化剂无法对杂质进行消除,无法保证装置运行需求,降低整体工作效率。
由于催化剂的顶部结盖,使反应床层的压降过大,产生升高影响。
1.2运行设备1.2.1高压换热器高压换热器的使用无法满足装置使用需求。
换热器温差变化大,设备长时间使用会造成整体温度数值下降。
装置运行速度变慢,换热效果较差,影响了生产效率,产生一定经济损失。
1.2.2反应器物流反应器在使用中,由于物流分配不均,在反应容器内的产品在制作时,所需温度达不到使用标准,产生温度不稳定现象。
由于设备设计负荷存在问题,使反应器最大负荷温度距离产品制作所需温度有些许差距,影响设备使用效率[1]。
若长时间出现这种情况,会使反应器设备停止运行,缩短设备使用时间和寿命。
1.2.3泡罩式分配盘根据其使用特征发现,泡罩式分配盘在渣油加氢装置使用中设备适应性低,使装置运行速度变慢,造成使用原料分配不均匀,会产生较为严重影响,对设备运行阻碍较大。
1.3使用原料在渣油加氢装置使用中,材料在运转状态下产生化学反应,影响其运行效率。
一方面是设备运行中金属离子产生的影响。
关于对渣油加氢脱硫技术的研究

关于对渣油加氢脱硫技术的研究【摘要】自七十年代以来,石油开采出来的原油质量开始变差,原油中的重质油含量尤其是渣油收率出现增加的趋势,而渣油和燃料油在燃烧过程中,渣油中所含的硫化物会与氧气结合形成二氧化硫、三氧化硫等气体排放到空气中,进而形成酸雨,影响人类正常的生活。
为了改善渣油的燃烧性能,降低有毒气体的排放,需要对渣油进行脱硫处理,来去除硫化物,并使渣油转化为易以加工处理的原料油。
对渣油进行脱硫处理的方式有加氢和不加氢两种,本文针对渣油的加氢脱硫处理技术,介绍了几种渣油脱硫装置,以及雪佛龙专利、ifp专利及联合油专利等三种固定床式渣油脱硫技术工艺。
【关键词】渣油加氢脱硫雪佛龙专利 ifp专利联合油专利1 几种渣油加氢脱硫装置的介绍为了进行渣油的脱硫处理,首先就要选择合适合理的加氢脱硫装置,本文主要介绍三套用于渣油加氢脱硫的装置:(1)中石化齐鲁分公司胜利炼油厂减压渣油加氢脱硫处理装置(简称vrds)是引进美国雪弗隆(chevron)公司的固定床渣油加氢专利技术,由华鲁工程公司设计,原设计规模为0.84 mt/a,用于处理孤岛减压渣油,并于1992年5月21日一次投料试车成功;1999年采用了chevron公司的最新专利—上流式反应器(up flowreactor,简称ufr)技术对装置进行扩能改造,以满足原料性质、处理量及产品质量等大幅度变化的要求。
ufr-vrds装置于2000年1月7日顺利投产,成为世界上首套采用ufr-vrds 联合技术的装置。
(2)西太平洋石油化工有限公司的200万t/a加氢脱硫装置,该装置以处理进口的沙特轻、重混合原油(50:50)的常压渣油为主,该装置是联合油公司的专利,并有该公司提供工艺包,由中国石油化工总公司北京设计院完成最初设计和最终设计;(3)茂名石油化工公司2.0mt/a渣油加氢脱硫装置,该装置以减压渣油和减压蜡油的混合油为原料,其主要产品加氢脱硫渣油能满足重油催化裂化进料的性质要求,而最终实现了渣油的完全催化转化。
渣油加氢装置运行中存在问题及措施

渣油加氢装置运行中存在问题及措施摘要:本文主要针对渣油加氢装置技术特性,对在运行周期内产生的床层径向温差大、脱硫化氢汽提塔腐蚀严重、物料反冲洗频率高等问题进行了分析。
结果表明:进料口“容垢”能力不够是导致床层径向温差较大的主要原因;碳氢化Cl沉淀和结晶是造成脱硫化氢汽提塔腐蚀的重要因合物中Cl-、NH4+所产生的NH4素,而反冲洗过滤器冲洗频繁主要是由加工的原料油性质所导致的。
通过对上述问题进行研究分析为渣油加氢装置的平稳长周期运行提供方向。
关键词:渣油加氢床层径向铵盐结晶反冲洗引言:渣油加氢技术是实现对重质渣油进行深处理的一项重要技术。
通过对重质渣油进行加氢处理去除大量的镍和钒等金属杂质,降低残碳的含量从而提高油品质量,达到更高的环保指标。
天津石化渣油加氢装置是炼油产品结构调整及油品质量升级项目的新建装置。
利用渣油加氢装置能够更好地提升油品的收率且对于整个炼油产业来说能够提升整个行业的运行效率,为石油类产品提供质量保障。
一、渣油加氢装置工艺特点渣油加氢采用的原料主要是常减压蒸馏装置常压渣油、减压渣油、过气化汽油以及焦化蜡油的混合原料,最终的产物占比最多的是经过加氢脱硫、脱氮、脱金属、脱残碳处理之后的加氢渣油,为催化裂化装置装置提供原料。
渣油加氢装置主要包括原料系统、反应系统、分馏系统、循环氢脱硫系统以及膜分离系统等。
渣油加氢装置体积空速度较高,床厚较低,氢分压较低,属高苛刻度操作的渣油加氢设备。
在运行周期内能够满足洁净环保的要求,但同时也存在着较大的床层径向温差大、脱硫化氢汽提塔顶腐蚀以及反冲洗清洗频率高等问题。
针对这些问题提出对应的解决措施从而为延长渣油加氢的高品质运行周期提供保障。
二、运行周期中存在问题及措施2.1床层径向温差大原因及措施2.1.1反应器床层物料结焦原因稠环芳香族类在重油加氢厂的原材料中存在;胶质、沥青质和金属(Ni+ V)等,稠环芳烃、残炭、胶质、沥青质会在触媒的表层被吸收而形成炭,从而导致反应活性下降,从而导致反应器的压降升高;同时,由于在去除过程中,废油中的镍、钒、铁等金属元素会在催化剂的内壁和表层上沉积,从而导致催化剂的活化和提高。
1.50Mt/a渣油加氢装置周期运行分析
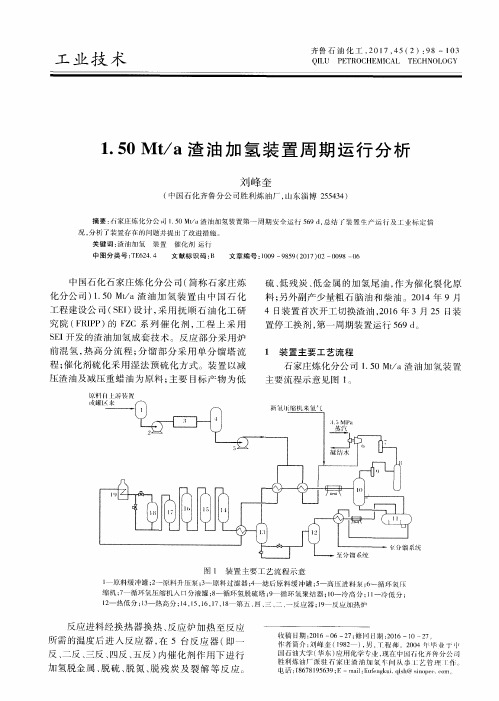
溶 解 的气体 闪蒸 出来 , 热 低 分油 经 分 馏 加 热 炉 加 热 后 直接 去 分馏 塔 。热 高分 气 相 先 后 与 混 氢 油 、 混氢 换热 后进 入 高 压 空 冷 器 , 经 高压 空冷 器 冷 却 至5 0℃后 进 入冷 高分 。冷 高分 气 相 经 循 环 氢 脱 硫 塔脱 硫后 作 为循 环氢 经循 环氢 压缩 机循 环 回反 应 系统 。冷高 分 油 减压 后 进 入 冷 低 分 , 冷 低 分 油 作 为分 馏塔 轻烃 进料 。
究院 ( F R I P P) 的 F Z C系列催 化 剂 , 工 程 上 采 用
硫、 低残炭 、 低 金 属 的加 氢尾 油 , 作 为催 化 裂化 原 料; 另 外 副产少 量 粗石 脑 油 和 柴 油 。2 0 1 4年 9月 4日装 置首次 开 工切换 渣 油 , 2 0 1 6年 3月 2 5 口装 置停 工换 剂 , 第 一 周期 装置 运行 5 6 9 d 。
收 稿 日期 : 2 0 1 6—0 6—2 7; 修 ㈨ 日期 : 2 0 1 6一J ( ) 一2 7 作 简 介 : 刘峰奎 ( 1 9 8 2 ) , 男, T 程 帅 。2 0 ( / 4年 毕 、 』 于 【 I I 国石油大学( 华东) 应用化学 专、 现 在 中 国石 化 齐鲁 分 公 司 胜利炼油厂派驻 石家 庄渣 油加 氢 1 问从 事 J 艺 管 f ‘ 作 电话 : t 8 6 7 8 1 9 5 6 3 9; E —m a i l : l i u f e n g k u i . q l s h @s i n o [ ・ . ( ! O l l q
出延 长装 置运 行 时间 。热高 分 液相经 液 力透平 降
压 回收能 量后 去 热 低 分 , 在 热 低 分 内进 一 步 将 其
固定床渣油加氢装置的运行难点与对策分析
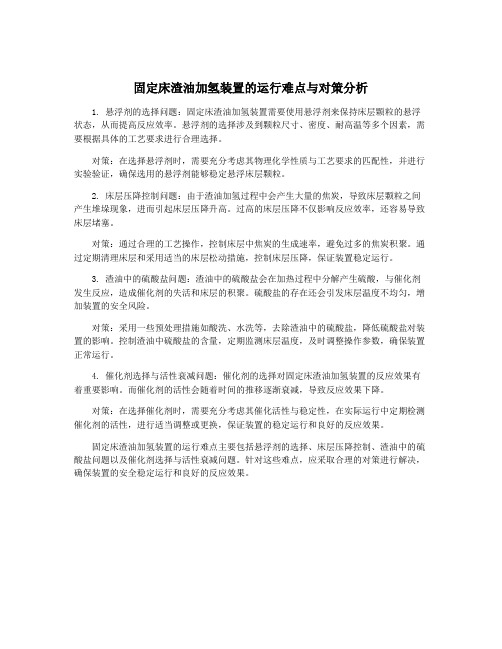
固定床渣油加氢装置的运行难点与对策分析1. 悬浮剂的选择问题:固定床渣油加氢装置需要使用悬浮剂来保持床层颗粒的悬浮状态,从而提高反应效率。
悬浮剂的选择涉及到颗粒尺寸、密度、耐高温等多个因素,需要根据具体的工艺要求进行合理选择。
对策:在选择悬浮剂时,需要充分考虑其物理化学性质与工艺要求的匹配性,并进行实验验证,确保选用的悬浮剂能够稳定悬浮床层颗粒。
2. 床层压降控制问题:由于渣油加氢过程中会产生大量的焦炭,导致床层颗粒之间产生堆垛现象,进而引起床层压降升高。
过高的床层压降不仅影响反应效率,还容易导致床层堵塞。
对策:通过合理的工艺操作,控制床层中焦炭的生成速率,避免过多的焦炭积聚。
通过定期清理床层和采用适当的床层松动措施,控制床层压降,保证装置稳定运行。
3. 渣油中的硫酸盐问题:渣油中的硫酸盐会在加热过程中分解产生硫酸,与催化剂发生反应,造成催化剂的失活和床层的积聚。
硫酸盐的存在还会引发床层温度不均匀,增加装置的安全风险。
对策:采用一些预处理措施如酸洗、水洗等,去除渣油中的硫酸盐,降低硫酸盐对装置的影响。
控制渣油中硫酸盐的含量,定期监测床层温度,及时调整操作参数,确保装置正常运行。
4. 催化剂选择与活性衰减问题:催化剂的选择对固定床渣油加氢装置的反应效果有着重要影响。
而催化剂的活性会随着时间的推移逐渐衰减,导致反应效果下降。
对策:在选择催化剂时,需要充分考虑其催化活性与稳定性,在实际运行中定期检测催化剂的活性,进行适当调整或更换,保证装置的稳定运行和良好的反应效果。
固定床渣油加氢装置的运行难点主要包括悬浮剂的选择、床层压降控制、渣油中的硫酸盐问题以及催化剂选择与活性衰减问题。
针对这些难点,应采取合理的对策进行解决,确保装置的安全稳定运行和良好的反应效果。
催化裂化装置加工常压渣油的长周期运行要点及对策

20 my • kg" 1,同时碱性氮高于1 000 my • kg" 1 ,对 催化剂性能造成不可逆的影响,严重时造成催化剂 中毒;高硫、高盐会加速设备及管线腐蚀,加重后续 产品精制与环保系统的调控压力[2] $
2装置运行
2.1反应系统
(1)原料油雾化效果$鉴于原料油性质较重,经 过操作摸索在原料预热温度220 V情况下,提升管原
(6) 油浆系统材质升级。油浆系统结焦及腐 蚀,除调控反应深度保证一定油浆外甩,且维持油浆 密度低于1 100 kg * m'3外,设备及管线材质升级是 维持长周期的有效方法。
4结论
通过河南某炼油厂催化装置以常渣为原料投产
以来的运行情况,总结常渣作为原料限制装置长周 期运行的要点,提出了防结焦、降尾燃和保油浆系统 等积极对策,有利于挖掘催化装置长周期运行的潜 能,提高经济效益,经过生产验证,这些方法行之有 效,为其他重油催化装置长周期运行提供参考。
表1原料油性质 Table 1>Propert nes of feedstock o nl
密度/kg • m- 3
938.6 四组分
盐含量/mg • L- 1
5. 24
胶质/%
13.77
残炭/% 点 jV
5.9
沥青质/%
203
饱和分/%
1.2 46.76
350 V憎出量/mL 15.5
芳香分/%
29.17
of catalytic cmckiny unit is adected by moy factors, such as tha characte/stics of feedstock oil which
渣油加氢脱硫装置试运行技术分析

渣油加氢脱硫装置试运行技术分析摘要:四川石化有限责任公司300万吨/年渣油加氢脱硫装置开工试运行6个月。
结果表明本套渣油加氢脱硫装置设计合理、设备选配适当、催化剂性能优良、活性稳定。
虽然在开工运行中出现个别小问题,但经过小技措改造,目前装置运行平稳。
关键词:渣油加氢脱硫运行技术分析中国石油天然气股份有限公司四川石化分公司300×104t/a渣油加氢脱硫装置采用CLG公司的固定床渣油加氢脱硫工艺技术,以哈萨克斯坦、南疆及北疆原油的减压重蜡油和减压渣油为原料,经过催化加氢反应,进行脱除硫、氮、金属等杂质,降低残碳含量,为催化裂化装置提供原料,同时生产部分柴油,并副产少量石脑油和燃料气。
一、装置概况本装置的原料主要有来自常减压装置的减压渣油、减压重蜡油,来自于渣油原料罐区的减压渣油、减压重蜡混合油,进料中减压渣油与减压重蜡油的混合比例为89.7:10.3。
渣油产品大部分送催化装置,少部分送催化裂化原料罐区;柴油送柴油加氢装置;石脑油送乙烯装置罐区;含硫燃料气送加氢裂化装置脱硫后并入工厂燃料气管网。
含硫富氢气体,送加氢裂化装置脱硫后去PSA 回收氢气。
该工艺技术满足操作周期8000小时,柴油产品硫含量不大于500PPm、加氢常渣产品硫含量不大于0.3w%、残炭不大于5.0w%、Ni+V不大于15PPmwt的指标要求。
装置由美国CLG公司提供工艺包,洛阳石化工程公司负责基础设计和详细设计,中油一建施工。
装置经历了单机试车、联动试车,从2013年1月16日正式引入物料,进入投料试车阶段。
到1月28日正式生产的产品分析合格。
截止5月30日,装置运行平稳,各项产品指标合格。
1.本装置的主要工艺技术特点有:1.1采用上流式反应器。
反应部分设置两个系列,每个系列可以单开单停(单开单停是指装置内二个系列分别进行正常生产和停工更换催化剂)。
由于渣油加氢脱硫装置的设计操作周期与其它主要生产装置不一致,从全厂生产安排的角度,单开单停可以有效解决原料储存、催化裂化装置进料量等问题,并使全厂油品调配更灵活。
延迟焦化装置工艺过程简述及工艺流程简图

延迟焦化装置工艺过程简述及工艺流程简图2.1 工艺流程简述原料渣油(包括催化油浆及常Ⅲ洗涤油等)从装置外来,进入原料缓冲罐(V1101),经原料油泵(P1101/1、2)抽出升压后,先与柴油换热至181℃(E1101/1、2),接着与中段油换热至227℃(E1102/1、2),最后与蜡油换热至289℃ (E1103/1~4)后分两路进入分馏塔,一路进入分馏塔(T1102) 下段换热区与来自焦炭塔(T1101/1、2)的高温油气接触换热,高温油气中的循环油馏分被冷凝,原料油与冷凝的循环油一起进入分馏塔底,另一路直接进入分馏塔底部。
分馏塔底油经辐射进料泵入口过滤器FI1102/1、2过滤后由辐射进料泵(P1102/1~2)升压后进入加热炉(炉1101),经对流室和辐射室加热至490~505℃出加热炉,经过四通阀进入焦炭塔(T1101/1、2)底部。
在焦炭塔内经过高温和长时间停留,原料油和循环油在焦炭塔内发生一系列复杂的裂解、缩合等反应,最后生成焦炭和油气。
生成的高温油气自焦炭塔顶逸出去分馏塔下段换热区,焦炭在塔内沉积生焦并储存在塔内。
当焦炭塔生焦到一定高度后停止进料,切换到另一个焦炭塔内进行生焦。
切换后,老塔用蒸汽进行小吹汽,将塔内残留油气吹至分馏塔回收,小吹汽结束后改大吹汽、给水进行冷焦,焦炭塔大吹汽、给水冷焦时产生的大量高温蒸汽及少量油气进入接触冷却塔(T1103),接触冷却塔底的污油由接触冷却塔底泵(P1112/1、2)抽出,经水箱冷却器(WC1105)冷却后,部分作为T1103顶回流,部分送入本装置污油罐经脱水后做急冷油回炼。
塔顶蒸汽及轻质油气经塔顶空冷器、水冷器后入接触冷却塔顶油气分离器(V1106)分离,分离出的污油送入本装置污油罐,污水经接触冷却塔顶污水泵(P1113/1、2)升压后送入冷焦水热水灌(V1401),不凝气进入低压瓦斯管网。
进入分馏塔(T1102)下段换热区的高温油气与原料油直接接触换热后,冷凝下来的循环油进入分馏塔底,大量油气经过5块洗涤板后进入蜡油集油箱以上进行分馏,从下往上分别切割出蜡油、柴油、汽油和富气等馏分。
渣油加氢工艺说明

第一节工艺技术路线及特点一、工艺技术路线300×104t/a渣油加氢脱硫装置采用CLG公司的固定床渣油加氢脱硫工艺技术,该工艺技术满足操作周期8000h、柴油产品硫含量不大于500ppm、加氢常渣产品硫含量不大于0.35w%、残炭不大于5.5w%、Ni+V不大于15ppm的要求;二、工艺技术特点1、反应部分设置两个系列,每个系列可以单开单停单开单停是指装置内二个系列分别进行正常生产和停工更换催化剂;由于渣油加氢脱硫装置的设计操作周期与其它主要生产装置不一致,从全厂生产安排的角度,单开单停可以有效解决原料储存、催化裂化装置进料量等问题,并使全厂油品调配更灵活;2、反应部分采用热高分工艺流程,减少反应流出物冷却负荷;优化换热流程,充分回收热量,降低能耗;3、反应部分高压换热器采用双壳、双弓型式,强化传热效果,提高传热效率;4、反应器为单床层设置,易于催化剂装卸,尤其是便于卸催化剂;5、采用原料油自动反冲洗过滤器系统,滤除大于25μm以上杂质,减缓反应器压降增大速度,延长装置操作周期;6、原料油换热系统设置注阻垢剂设施,延长操作周期,降低能耗,而且在停工换剂期间可减少换热器和其它设备的检修工作;7、原料油缓冲罐采用氮气覆盖措施,以防止原料油与空气接触从而减轻高温部位的结焦程度;8、采用炉前混氢流程,避免进料加热炉炉管结焦;9、第一台反应器入口温度通过调节加热炉燃料和高压换热器旁路量来控制,其他反应器入口温度通过调节急冷氢量来控制;10、在热高分气空冷器入口处设注水设施,避免铵盐在低温部位的沉积;11、循环氢脱硫塔前设高压离心式分离器除去携带的液体烃类,减少循环氢脱硫塔的起泡倾向,有利于循环氢脱硫的正常操作;12、设置高压膜分离系统,保证反应氢分压;13、冷低压闪蒸罐的富氢气体去加氢裂化装置脱硫后去PSA回收氢气;14、新氢压缩机采用二开一备,每台50%负荷,单机负荷较小,方便制造,且装置有备机;15、分馏部分采用主汽提塔+分馏塔流程,在汽提塔除去轻烃和硫化氢,降低分馏塔材质要求;分馏塔设侧线柴油汽提塔及中段回流加热原料油,降低塔顶冷却负荷,提高能量利用率,减小分馏塔塔径;16、利用常渣产品发生部分低压蒸汽;通过对装置换热流程的优化,把富裕热量集中在温位较高的常渣产品,发生低压蒸汽;17、考虑到全厂能量综合利用,正常生产时常渣在150℃送至催化裂化装置;在催化裂化装置事故状态下,将常渣冷却至90℃送至工厂罐区;18、催化剂预硫化按液相预硫化方式设置;三、工艺流程说明一工艺流程简述1、反应部分原料油自进装置后至冷低压分离器V-1812前的流程分为两个系列,以下是一个系列的流程叙述:原料油在液位和流量的串级控制下进入滤前原料油缓冲罐V-1801;原料从V-1801底部出来由原料油增压泵P1801/S升压,经中段回流油/原料油换热器E-1801AB、常渣/原料油换热器E-1802AB、E-1803AB分别与中段回流油和常渣换热,然后进入原料油过滤器S-1801以除去原料油中大于25μm的杂质;过滤后的原料油进入滤后原料油缓冲罐V-1802,原料油从V-1802底部出来后由加氢进料泵P1802/S升压,升压后的原料油在流量控制下进入反应系统;原料油和经热高分气/混合氢换热器E-1805AB预热后的混合氢混合,混合进料经反应流出物/反应进料换热器E-1804预热后进入反应进料加热炉F-1801加热至反应所需温度进入第一台加氢反应器R-1801,R-1801的入口温度通过调节F-1801的燃料量和E-1804的副线量来控制,R-1801底部物流依次通过其它三台反应器R-1802、R-1803、R-1804,各反应器的入口温度通过调节反应器入口管线上注入的冷氢量来控制;从R-1804出来的反应产物经过E-1804换热后进入热高压分离器V-1803进行气液分离,V-1803底部出来的热高分液分别在液位控制下减压后,进入热低压分离器V-1804进行气液分离,V-1803顶部出来的热高分气分别经热高分气/混合氢换热器、热高分气蒸汽发生器E-1806换热后进入热高分气空冷器E-1807,冷却到52℃进入冷高压分离器V-1806进行气、油、水三相分离;为了防止铵盐在低温位析出堵塞管路,在热高分气空冷器前注入经注水泵P-1803/S升压后的脱硫净化水等以溶解铵盐;从V-1806顶部出来的冷高分气体循环氢进入高压离心分离器V-1807除去携带的液体烃类,减少循环氢脱硫塔C-1801的起泡倾向;自V-1807顶部出来的气体进入C-1801底部,与贫胺液在塔内逆向接触,脱除H2S,脱硫溶剂采用甲基二乙醇胺MDEA,贫胺液从贫胺液缓冲罐V-1809抽出经贫溶剂泵P-1804/S升压后进入C-1801顶部,从塔底部出来的富胺液降压后进入富胺液闪蒸罐V-1810脱气;富液脱气后出装置去溶剂再生,气体去硫磺回收;自C-1801顶不出来的循环氢进入循环氢压缩机入口分液罐V-1808除去携带的胺液,V-1808顶部出来的循环氢分成两路,一路去氢提浓ME-1801部分,提浓后的氢气经提浓氢压缩机K-1804升压后与新氢压缩机K-1802A.B.C出口新氢汇合,释放气去轻烃回收装置;另一路进入循环氢压缩机K-1801升压,升压后的循环氢分为三部分,第一部分与新氢压缩机来的新氢混合,混合氢去反应部分;第二部分作为急冷氢去控制反应器入口温度;第三部分至E-1807前作为备用冷氢和K-1801反飞动用;循环氢压缩机选用背压蒸汽透平驱动的离心式压缩机;从两个反应系列的冷高压分离器底部出来的冷高分液分别在液位控制下减压混合后,进入冷低压分离器V-1812进行气液分离,冷低分液体在液位控制下从罐底排出并进入热低分气/冷低分液换热器E-1809、柴油/冷低分油换热器E-1811、常渣/冷低分油换热器E-1812换热后进入汽提塔C-1803;V-1812顶部出来的冷低分气去轻烃回收装置脱硫;冷高压分离器底部的含H2S、NH3的酸性水进入酸性水脱气罐V-1823集中脱气后送出装置;两个反应系列的热低分油在液位控制下从V-1803底部排出去分馏部分;热低分气体经E-1809换热后进入热低分气空冷器E-1810冷却到54℃,然后进入冷低压闪蒸罐V-1811进行气液分离,为了防止在低温位的地方有铵盐析出堵塞管路,在E-1810前注水以溶解铵盐;V-1811顶部出来的富氢气体直接送至加氢裂化装置进行脱硫,然后去PSA装置回收氢气;从下部出来的冷低压闪蒸液进入到冷低压分离器;新氢从全厂氢网送入,进入新氢压缩机经三段压缩升压后分两路分别与两个系列循环氢压缩机出口的循环氢混合,混合氢气分别返回到各自的反应部分;新氢压缩机设三台,二开一备,每一台均为三级压缩,每台的一级入口设入口分液罐,级间设冷却器和分液罐;2、分馏部分来自反应部分的热低分油与经加热后的冷低分液一起进入汽提塔C-1803;塔底采用水蒸汽汽提;塔顶部气相经汽提塔顶空冷器E-1814冷凝冷却后进入汽提塔顶回流罐V-1814进行气液分离,V-1814气体与冷低分气一起出装置送至轻烃回收统一脱硫;V-1814底部出来的液体经汽提塔顶回流泵P-1805/S升压后分成两部分,一部分作为回流返回到塔顶部,另一部分去石脑油加氢;V-1814底部分水包排出的酸性水进入V-1823脱气后出装置;为减轻塔顶管道和设备的腐蚀,在汽提塔的顶部管道注入缓蚀剂;汽提塔底油经分馏塔进料加热炉F-1802加热至合适温度进入分馏塔C-1804,分馏塔设一个柴油抽出侧线和一个中段回流,塔底采用水蒸汽汽提,塔顶气相经分馏塔顶空冷器E-1815冷凝冷却后进入分馏塔顶回流罐V-1815进行气液分离;V-1815底部出来的液体经分馏塔顶回流泵P-1806/S 升压后分成两部分,一部分作为塔顶回流返回到塔顶部,另一部分在V-1815液位控制下与C-1803塔顶油一道送出装置;V-1815底部分水包排出的含油污水经含油污水泵P-1807/S升压后送注水罐回用;未汽提柴油从分馏塔抽出进入柴油汽提塔C-1805,柴油汽提塔底设重沸器,以分馏塔底油为热源,C-1805顶气体返回到分馏塔;柴油从塔底部抽出经柴油泵P-1811/S升压后再经柴油/低分油换热器、柴油空冷器E-1816冷却到50℃出装置;中段回流油从分馏塔集油箱用分馏塔中段回流泵P-1809/S抽出,进入E-1801A.B换热后返回分馏塔;分馏塔底油加氢常渣经分馏塔底泵P-1810/S加压后依次经柴油汽提塔重沸器E-1818、常渣/原料油换热器、常渣蒸汽发生器E-1817等换热至168℃作为热供料去催化裂化装置,或再经常渣空冷器E-1819冷却至90℃出装置至罐区;3、催化剂预硫化为了使催化剂具有活性,新鲜的或再生后的催化剂在使用前均必须进行预硫化,设计采用液相硫化法,硫化剂为二甲基二硫化物DMDS;两个系列催化剂可以分别独立进行预硫化,以下是一个系列硫化的流程叙述:硫化时,系统内氢气经循环氢压缩机按正常操作路线进行循环,冷高压分离器压力为正常操作压力;DMDS自硫化剂罐V-1831来,至加氢进料泵入口管线,硫化油采用蜡油;自R-1804来的流出物经E-1804、V-1803、E-1805A.B、E-1806、E-1807冷却后进入冷高压分离器V1806进行分离,冷高分气体经循环氢压缩机K-1801循环,催化剂预硫化过程中产生的水从V4004底部间断排出;二主要操作条件如下:1反应部分反应器液时空速,h-10.20总气油比,SOR/EOR1132/1232反应器入口压力,SOR/EORMPag19.45/19.88平均反应温度,SOR/EOR℃391/402 2热高压分离器温度℃SOR/EOR371/374压力MPaG17.8 3冷高压分离器温度℃52压力MPaG17.5 4反应进料加热炉入口/出口温度℃337/365SOR350/378EOR压力MPaG20.6 5循环氢压缩机入口温度℃61入口/出口压力MPaG17.46/21.43循环氢压缩机设计能力m3n/h224315单台6新氢压缩机入口温度℃40入口/出口压力MPaG 2.4/21.2新氢压缩机设计能力m3n/h51400单台7提浓氢压缩机入口温度℃60入口/出口压力MPaG 4.18/21.37提浓氢压缩机设计能力m3n/h31800 8循环氢脱硫塔塔顶温度℃61塔顶压力MPaG17.59汽提塔进料温度℃364/366SOR/EOR塔顶温度℃189/172SOR/EOR塔顶压力MPaG 1.1塔底温度℃350/344SOR/EOR10分馏塔进料温度℃371塔顶温度℃124/129SOR/EOR塔顶压力MPaG0.14塔底温度℃354/322SOR/EOR10柴油汽提塔进料温度℃226/231塔顶温度℃227/247塔顶压力MPaG0.17塔底温度℃293第二节副产品的回收、利用及“三废”处理方案一、副产品的回收和利用该装置副产品富氢气体和含硫燃料气;富氢气体约为2422Kg/hEOR,其中H2含量为83.02%V,H2S含量为2.99%V,C1含量为7.13%V,C2含量为3.34%V,富氢气体送至加氢裂化装置进行脱硫,然后去PSA装置回收氢气;含硫燃料气由低分气、汽提塔顶气、氢提浓单元尾气、酸性水罐闪蒸气及富胺液闪蒸气总量约为7969Kg/hEOR,其中H2含量为32.67%V,H2S含量为10.32%V,C1含量为6.63%V,C2含量为11.94%V,含硫燃料气送轻烃回收装置脱硫;二、“三废”处理方案一废水处理废水按其性质主要可分为四类含硫污水:主要由冷高压分离器、冷低压分离器、汽提塔顶回流罐等排出,含有较高浓度的H2S和NH3,送酸性水处理装置进行处理;含油污水:分馏塔顶回流罐产生的含油污水经含油污水升压后送注水罐作为装置注水回收利用;机泵和地面冲洗等产生的含油污水,送至污水处理场;装置界区内的初期雨水并入含油污水,后期雨水排入清净废水系统,以减轻工厂污水处理的负荷;生活污水:装置间断排出职工生活污水,排入生活污水系统;废水见表2-1;表2-1废水排放量和污染物浓度一览表二废气处理1 废气燃烧废气:反应进料加热炉、分馏塔进料加热炉排出的燃烧烟气,充分回收能量后,经烟囱高空排放;放空气体:安全阀及放空系统包括紧急放空排放的含烃气体排入密闭的火炬系统;废气排放情况见表2-2表2-2主要废气污染源表三固液体废物正常生产时无固液体废物排放,仅在停工检修时,排出废保护剂、废催化剂和废碱液等;废保护剂、催化剂:由加氢反应器排出,约1年一次,送废催化剂回收工厂或桶装深埋;废碱液:反应部分中和清洗排放的废碱液由工厂系统统一处理;固体废弃物列于表2-3;表2-3固体废物分类汇总表四噪声源及处理1空冷器选用低转速、低噪声风机,单台噪声控制在85分贝以下;2机泵选用低噪声增安型电机;3蒸汽放空装有消音器;4加热炉采用低噪声燃烧器,风道部分采用保温隔音材料;5凡易产生噪声的排放点均设置消音器;6加氢进料泵、新氢压缩机配用的大型电机设置消音罩;采用上述措施后,噪声指标符合石油化工企业职业安全卫生设计规范SH3047-93;表2-4噪声特征表第三节安全卫生一、装置危险、危害性分析1 火灾、爆炸危害因素分析所用原料、中间产品、产品的火灾理化特性见表3-1;表3-1生产中主要原料、中间产品、产品火灾危险性分类表2 危害因素较大设备及场所主要危险设备包括:加氢反应器、循环氢脱硫塔、新氢压缩机、循环氢压缩机、高压换热器等;主要危险岗位见表3-2:表3-2主要危险岗位表3 生产中使用、产生的部分物料为有毒物质,对人体有一定程度的危害作用,其危害及危害程度见表3-3;表3-3主要有毒、有害物质及其特性表4 危险等级所用原料、中间产品、产品各物料在加工过程中处于高温、高压、含氢环境中,当环境温度超过其自燃点时,发生泄漏就可能引发火灾;火灾危险性属于甲类;二安全卫生措施1 安全卫生设施依托情况该装置所需的劳动安全卫生措施,按现行有关劳动安全卫生标准、规范的要求,在依托现有系统劳动安全卫生设施的基础上补充完善,以确保该装置的劳动安全卫生达到标准和规范的要求;2 主要安全卫生防范措施⑴工艺设计①采用先进可靠的工艺技术和合理的工艺流程,设计考虑必要的裕度及操作弹性,以适应加工负荷上下波动的需要;②装置内设有1.05/2.1MPa/min紧急泄压系统;当出现反应器床层温度过高或发生严重火灾时,使用紧急泄压系统手动启动,使反应系统迅速降压,以避免催化剂和设备严重损坏;③为确保安全操作,保障设备、人身安全,设置下述自动联锁保护系统;当1.05/2.1MPa/min放空系统启动时,反应进料加热炉将自动停运;当燃料气压力过低,反应器入口温度过高,反应进料加热炉流率过低时,反应进料加热炉停炉;当燃料油压力过低,加热炉出口温度过高,加热炉流率过低时,分馏塔进料加热炉停运;当循环氢压缩机入口分液罐高高液位时,循环氢压缩机停机;④所有带压设备及管道均设安全阀,所有安全阀均设备阀;⑤各部分设置的安全阀泄压时,其排放物分别由火炬线或液体放空线排至密闭的放空罐,然后气体去工厂火炬,液体去工厂污油罐;⑥关健转动设备,均设有备机,以确保安全生产;⑵平面布置设计①平面布置在满足有关防火、防爆及安全卫生标准和规范要求的前提下,尽量采用露天化、集中化和流程式布置,并考虑同类设备相对集中,以达到减少占地、节约投资、降低能耗、便于安全生产操作和检修管理,实现本质安全的目的;②四周设绿化带和环形消防通道,并确保与周围装置的防火间距满足有关规范的要求;设置检修及消防通道,保证消防车和急救车能顺利通往可能出现事故的地方;③加热炉布置在全年最小风频的下风向;④所有框架、管架均按GB50160-921999版的有关规定设有防火层;界区内设有消火栓、水炮、蒸汽灭火设施、软管站及灭火器等消防设施用于火灾扑救;⑤对于表面温度高于60℃管线,在操作人员可触摸到的部位均采用隔热层防烫保护;在管带区、框架区、塔区等地方均设蒸汽灭火系统;⑥设计中选用优质垫片,加强管道、设备密封,防止介质泄漏;⑦设置移动式小型灭火设备;包括推车式泡沫灭火器,手提式干粉灭火器以及手提式泡沫灭火器;⑶自控设计①装置的仪表自动控制采用DCS,由控制室进行统一管理,并根据工艺特点和安全要求,对关键部位,设置必要的报警、自动控制及自动联锁等控制措施;②为保证装置停电时仪表用电,设置UPS不间断电源;③对有可能泄露可燃气体和H2S等有毒气体的地方,设置固定式的可燃气体报警仪和H2S气体报警仪;可能有H2S气体泄漏和聚积岗位上的操作人员配备便携式H2S气体报警器;④为了保护设备和生产安全,在设计中选用风开、风关调节阀,以便停风时,调节阀能处于安全位置;同时为防止仪表管道的冻凝和阻塞,在必要部位设置仪表蒸汽伴热系统和冲洗油系统;⑤监测、控制仪表除按工艺生产要求选型时,还考虑了仪表安装地点的防爆等级,并按爆炸和火灾危险环境电力装置设计规范GB50058-92进行选型;⑥生产仪表及其它电气设备按所处区域的防爆等级选用防爆型号;在中控室、变配电室内设置可燃气体报警仪、火灾检测报警器;并设置事故通风设施;⑷电气设计①装置内爆炸危险区域内的电力设备设置严格按照爆炸和火灾危险环境电力装置设计规范GB50058-92的要求进行设计;②在爆炸危险场所的电器设备均选用相应等级的防爆电器,如防爆电钮、防爆照明灯、防爆电机等;③电力配电电缆均选用阻燃铠装电缆;④设防爆检修动力箱,供停工时检修用电;⑤平台、过道及其它需要的地方均设置照明设施,照明亮度符合规范要求;为了便于事故抢救,局部重要的操作通道及操作点配备事故照明设施;⑥为确保人身安全,在有关建构筑物、工艺设备及管道上均设置防雷防静电的可靠接地装置,并依照工业与民用电力装置接地设计规范GBJ65-83的要求,接地电阻<4Ω,接地线均采用镀锌扁钢;⑦设防爆对讲电话以及火灾报警装置,以便发生火灾时及时报警;⑸工艺配管工程设计①各部分均设有固定的消防蒸汽管线和足够的软管站,使可能出现的泄漏点均在消防蒸汽软管范围之内;②按标准、规范规定选用管道、管件、法兰、垫片、阀门;③对安装管道采取必要的保温、保冷措施:a 工艺过程的需要;b 减少散热或冷量散失的需要c 保证操作人员安全、改善劳动条件的需要;④工艺管道安全的措施a 热补偿安全b 适应高温、高压及腐蚀介质的管道材质;c 防泄漏措施;⑹土建设计①各建筑物、构筑物的抗震性能均按建筑抗震设计规范GB50011-2001的规定进行设计;建筑物的耐火性能满足2级耐火等级的要求;②钢结构框架、管带及其它梁柱均满足设计规范所要求的强度、耐火、防爆等性能,并加设厚型无机外防火层,以防止火灾伤害及火势蔓延;③抗震、防雷措施:建构筑物及大型框架设备采取相应的抗震、防雷措施;⑺设备机械工业炉设计①根据有关规定,设备设计中充分考虑当地的风压、地震烈度及场地等因素,对反应器等主要设备基础按7度近震地震烈度设计;②主要设备的裙座均设置防火层,对高温设备和管道均进行隔热保温;③根据设备内介质操作温度、压力和腐蚀情况,分别选用相适应的材质,以减少腐蚀,延长设备寿命;加热炉设置长明灯,以防瞬间熄火而引起炉内瓦斯爆炸,同时在炉体安装防爆门,并设置灭火蒸汽管;④对必须在高空操作的设备,根据规范要求在必要的位置均设置平台、梯子、扶手、围栏等,以保证操作人员的人身安全;⑤加热炉的燃料气管线上设置阻火器,防止回火发生事故;三防毒与职业病防治1、生产过程中会产生有毒气体硫化氢,在操作和检修过程中少量的硫化氢气体可能从密闭系统中泄漏到大气中;因此,装置中除设置硫化氢报警仪外,还配备防毒面具和空气呼吸器,以便在事故时进行自救、抢救,防止硫化氢中毒;2、据国内外炼油厂调查资料表明,在同类装置工作的操作人员及管理人员至今尚未发现患有国家规定的职业病及其他特殊病症;但为确保操作人员的身体健康,对该装置的操作人员应定期进行体检,以防患于未然;四设置安全色、安全标志1、按GB2894规定,凡容易发生事故的场所和设备设置安全警示标志,并在生产场所、作业场所的紧急通道和出入口,设置醒目的标志和指示箭头;2、按GB2893规定,对需要迅速发现并引起注意,以防发生事故的场所、部位涂有安全色;对阀门布置比较集中,易因误操作而引发事故的地方,在阀门的附近设标明输送介质的名称、符号等标志;五消防措施的设置1 压缩机、反应器、加热炉等需要重点保护的设备附近,设置箱式消火栓,其保护半径为30m;2 反应器附近设置固定式消防水炮保护;3 按照石油化工企业设计防火规范GB50160—921999年局部修订的要求在装置危险设备区设置蒸汽灭火软管;4 框架、平台上每层设置半固定式蒸汽接头;5 在高于15米的框架处,沿梯子平台敷设半固定式消防竖管;6 装置内设置的固定式露天消防设施如箱式消火栓、消防水炮等采取防冻措施;7 装置内按照石油化工企业设计防火规范GB50160—921999年版设置手提式灭火器;8 装置内报警采用电话报警,报警报至厂消防站;六劳动保护措施1、设置密闭式采样器,以减少可燃有害介质的扩散;2、有毒有害物质的装卸人员应配戴防毒面具;采取以上防范措施后,该装置的职业安全卫生设计可以满足有关标准规范的要求;。
- 1、下载文档前请自行甄别文档内容的完整性,平台不提供额外的编辑、内容补充、找答案等附加服务。
- 2、"仅部分预览"的文档,不可在线预览部分如存在完整性等问题,可反馈申请退款(可完整预览的文档不适用该条件!)。
- 3、如文档侵犯您的权益,请联系客服反馈,我们会尽快为您处理(人工客服工作时间:9:00-18:30)。
等 国 内外 的 l 2个 油 种 , 加 工 渣 油 25 0 8 6t蜡 质 堵 塞 造 成 压 力 降 上 升 较 快 、 置 运 行 周 期 缩 短 共 7 8 , 装 A L公 司 的 自动 反 冲 20 00年 和 20 年 茂 名 分 公 司 分 别 加 工 高 含 行 综 合 考 察 评 价 后 选 定 了 P L 01
层热点 问题 , 确保 装置安 全平 稳地 运 行 到检修 , 为 在 操 作 上 采 取 了 一 些 措 施 , 如 限 制 一 反 入 口温 例 度 不 得 超 过 35 , 抑 制 床 层 热 点 温 度 上 升 , 6℃ 以 因 而 使 整 个 反 应 部 分 温 度 也 偏 低 , 成 l 份 的 产 造 1月
采 用 的延 长 运 行 周 期 的 措 施 也 起 到 了很 好 效 果 。
合 格 产 品 , 20 年 l 到 01 2月 3 1日的 第 一 周 期 里 运
行 了 60天 , 1 0 , 设 计 运 行 周 期 800h l 改 造 原 料 过 滤 器 降 低 原 料粘 度 8 计 630h 是 0
硫 原 油 达 5. 5 和 5 9 , 别 占 总 加 工 量 洗 过 滤 器 , 在 开 工 前 根 据 现 场 实 际 情 况 对 该 系 3 . 2 Mt 分 并
5 .6 和 5 .4 。 38% 56%
统 进 行 了一 系 列 改 造 。 例 如 增 加 了 顶 部 排 气 管 和
主 题 词 : 压 渣 油 加 氢 脱 硫 装 置 减
催 化 剂 运 转 周 期 原 料
操 作条 件
技术 措施
中 国 石 化 股 份 有 限 公 司 茂 名 分 公 司 2 0 Mta 装 置 的进 料 要 求 。 装 置 安 全 平 稳 运 行 到 20 . / 0 1年
2月 1 3日按 计 划 停 工 检 修 。 渣 油 加 氢 脱 硫 ( — H ) 置 是 我 国 首 套 采 用 国 内 l SR T 装 固定 床 渣 油 加 氢 技 术 及 国 产 催 化 剂 , 要 设 备 由 主
从 19 9 9年 l 2月 3 0日进 油 开 工 ,2月 3 l 1日生 产 出
装 置 有 如 此 长 的 运 行 周 期 , 明 除 了 采 用 的 说
国 内 自 行 设 计 、 造 和 安 装 的 国 产 化 装 置 j 国 产 F C系 列 催 化 剂 有 较 好 的 活 性 和 稳 定 性 外 , 制 。 Z
差 便 逐 渐 拉 大 并 且 在 装 置 提 降 温 时 部 分 热 电偶 温 进 行 柴 油 冲洗 浸 泡 。此 外 根 据 原 料 的 粘 度 合 理 调
度 指 示 出 现 了滞 后 的 现 象 , 后 几 个 月 这 一 现 象 整冷 渣 油 、 渣 油 及 蜡 油 比例 和 换 热 温 度 使 混 合 随 热
维普资讯
20 0 2年 6月
炼 油 设 计 PTR L U R nN R N I E R G E O E M E E Y E G N E j
第 3 2卷第 6期
延 长 渣 油 加 氢 脱 硫 装 置 运 行 周 期 的 技 术
王 祝 平
中 国石 油 化 工股 份 有限 公 司茂 名分 公 司 ( 东 省茂 名市 5 5 1 ) 广 20 1
摘 要 : 国石化 股 份有 限公 司茂 名 分公 司 2 0Mta 油加 氢脱 硫装 置通 过搞 好 原料 过 滤 、 化 原料 结 构 、 中 . / 渣 优 优化 操作 条 件 、 平衡 好 不 同功能 的催 化剂 负 荷 以及采 用新技 术 等措 施 , 延长 了运行 周 期 , 降低 了运行 成本 。
越 来 越 明 显 。 20 0 1年 l O月 1日在 一 反 中 部 床 层 进 料 10C粘 度 始 终 低 于 10姗 2s 远 低 于 设 计 0 ̄ 0 /,
温 度 开 始 出 现 温 度 波 动 现 象 , 层 热 点 温 度 最 高 值 (0 l s , 证 了整 个 周 期 内过 滤 系 统 正 常 床 20I 1 )保 T / H 达 49 ;1 l 2 ℃ l 月 1日第 Ⅱ系 列 一 反 中 部 床 层 温 度 床 层 热 点 最 高 温 度 曾 升 至 4 4 C。 8 ̄
的两 倍 多 。在 此 期 间 , 加 工 了 中 国 大 庆 、 塔 尔 共 卡
油 l 5 0 , 油 : 油 为 7 9 :9 0 。 39 8t渣 0 蜡 O.2 2 .8
针 对 固定 床 反 应 器 催 化 剂 床 层 容 易 被 机 械 杂
的难 题 , 装 置 筹 建 之 初 对 各 种 过 滤 器 及 滤 芯 进 在
S R T装 置 经 过 1 0 —H 50 0 h运 行 进 入 第 一 周 期 反 冲 洗 油 抽 出泵 , 改 完 善 了 自动 运 行 程 序 , 得 修 使 末 期 后 , 响 生 产 的 主 要 是 床 层 热 点 问 题 。 从 过 滤 器 日后 能 长 时 间 正 常 运 行 。 在 实 际 运 行 当 影 20 0 1年 7月 份 开 始 , 1系 列 一 反 床 层 的径 向 温 中 , 据 过 滤 器 运 行 周 期 情 况 , 时 对 过 滤 器 滤 芯 第 根 适
自动 运 行 。 由 于 装 置 进 料 得 到 有 效 过 滤 , 以一 所 也 仅 为 0 5 a 低 于 设 计 值 ( . a , 为 S .1MP , O 7MP ) 这 —
也 开 始 出 现 温 度 波 动 现 象 并 一 度 造 成 轻 微 飞 温 , 反 床 层 压 力 降 即 使 在 运 行 末 期 满 负 荷 生 产 时 最 高 在装 置运 行 末 期 , 由于 两 系 列 一 反 出 现 了 床 R- I I 置长周期运 行创造 了先决条件 。 T装