浅析电镀上渗镀影响因素
电镀质量六大影响因素

电镀质量六大影响因素影响电镀质量的因素很多,包括镀液的各种成分以及各种电镀工艺参数,下面讨论其中的主要因素。
(l) pH值的影响镀液中的pH值影响氢的放电电位、碱性夹杂物的沉淀,还影响络合物或水化物的组成以及添加剂的吸附程度。
但是,对各种因素的影响程度一般不可预见。
最佳的pH值往往要通过试验决定。
在含有络合剂离子的镀液中,pH值可能影响存在的各种络合物的平衡,因而必须根据浓度来考虑。
电镀过程中,若pH值增大,则阴极效率比阳极效率高,pH值减小则反之。
通过加入适当的缓冲剂可以将pH值稳定在一定的范围。
(2)添加剂的影响镀液中的光亮剂、整平剂、润湿剂等添加剂能明显改善镀层组织。
这些添加剂有无机和有机之分,无机添加剂在电解液中形成高分散度的氢氧化物或硫化物胶体,吸附在阴极表面阻碍金属析出,提高阴极极化作用。
有机添加剂多为表面活性物质,它们会吸附在阴极表面形成一层吸附膜,阻碍金属析出,因而提高阴极极化作用。
另外,某些有机添加剂在电解液中形成胶体,会与金属离子络合形成胶体一金属离子型络合物,阻碍金属离子放电而提高阴极极化作用。
(3)电流密度的影响任何电镀液都必须有一个能产生正常镀层的电流密度范围。
当电流密度过低时,阴极极化作用较小,镀层结晶粗大,甚至没有镀层。
随着电流密度的增加,阴极极化作用也随着增加,镀层晶粒越来越细。
当电流密度过高,超过极限电流密度时,镀层质量开始恶化,甚至出现海绵体、枝晶状、“烧焦”及发黑等。
电流密度的上限和下限是由电镀液的本性、浓度、温度和搅拌等因素决定的。
一般情况下,主盐浓度增大,镀液温度升高,以及有搅拌的条件下,可以允许采用较大的电流密度。
(4)电流波形的影响电流波形的影响是通过阴极电位和电流密度的变化来影响阴极沉积过程的,它进而影响镀层的组织结构甚至成分,使镀层性能和外观发生变化。
实践证明,三相全波整流和稳压直流相当,对镀层组织几乎没有什么影响,而其他波形则影响较大。
例如,单相半波会使镀铬层产生无光泽的黑灰色;单相全波会使焦磷酸盐镀铜及铜锡合金镀层光亮。
pcb板镀铜锡渗镀原因

PCB板镀铜锡渗镀原因一、概述在电子制造中,PCB板(印刷电路板)的表面处理是至关重要的环节,它直接影响到产品的性能和可靠性。
其中,PCB板镀铜锡是一种常见的表面处理方法,旨在提高导电性、耐腐蚀性和连接可靠性。
然而,在镀铜锡过程中,渗镀是一个常见的问题,它可能导致电路短路、断路等质量问题。
因此,探究PCB 板镀铜锡渗镀的原因,对于提高产品质量和生产效率具有重要意义。
二、渗镀原因分析渗镀是指镀层在基材表面形成缺陷,导致镀层不连续或厚度不均匀。
在PCB 板镀铜锡过程中,渗镀的发生可能是由多种因素共同作用导致的。
下面将从几个方面详细分析渗镀的原因。
1.基材表面处理不当基材表面的清洁度和粗糙度对镀层的质量有着重要影响。
如果基材表面存在杂质、油污、氧化物等,就会导致镀层与基材之间的附着力减弱,从而引发渗镀。
此外,基材表面的粗糙度过大也会增加渗镀的风险。
2.电镀参数不适当电镀参数如电流密度、电镀时间、电镀液温度等对镀层的质量有显著影响。
如果这些参数设置不当,可能会导致镀层厚度不均匀、颗粒状结构等问题,从而引发渗镀。
3.电镀液成分不均一电镀液中的各种成分应保持适当的比例和浓度,以确保镀层的质量。
如果电镀液中的铜、锡离子浓度不均一或不足,就可能会导致渗镀的发生。
4.前处理和后处理不当在电镀之前对基材进行适当的预处理和在电镀之后进行适当的后处理,对于确保镀层质量是至关重要的。
例如,如果预处理的酸洗或浸渍步骤不足,就会导致基材表面残留杂质或氧化物,从而引发渗镀。
同样,如果后处理的清洗不彻底,也会增加渗镀的风险。
5.设备维护不当电镀设备和附属设施的维护也是影响镀层质量的重要因素。
例如,如果电极棒受损、阳极袋老化或过滤系统故障,就可能会导致电镀液的成分比例失衡,从而引发渗镀。
三、解决策略针对上述渗镀原因的分析,可以采取以下解决策略来降低渗镀的风险:1.加强基材表面处理在电镀前对基材进行严格的清洁和预处理,去除表面杂质、油污和氧化物,以提高基材表面的附着力和粗糙度。
【正天伟课堂】电镀上渗镀成因及解决对策

【正天伟课堂】电镀上渗镀成因及解决对策2015-11-07正天伟科技 欢迎来到正天伟课堂!本期要与大家分享的是通过缺陷模式将渗镀分为上渗镀和下渗镀,分别从图像转移和图形电镀制程详细描述了每一个环节对渗镀的影响,并通过案例阐述了上渗镀的解决对策。
愿共分享,共探讨。
一、前言 随着精细线路板和高频线路板的发展,对线路的精度提出了更高的要求,线路稍有偏差就会影响到信号传输,线路渗镀便是导致信号传输不良的重要因素之一。
线路渗镀是“正片线路+电镀铜锡”工艺之板常出的问题,俗称线路狗牙(或线路锯齿),有上渗镀和下渗镀之分,出现在线路底端称为下渗镀,出现在线路顶端称为上渗镀。
二、下渗镀 对于下渗镀业界同行已有比较深刻的认识,在此简单阐述一下:下渗镀主要是由干膜和铜面结合力差或显影后干膜的显影侧蚀过大导致。
解决对策a)改善磨板的粗糙度及板面的清洁度;b)调整贴膜压力、温度、速度及压辘的平整度;c)使用品质优良的干膜;d)控制合适的显影点及水洗效果;e)对显影后的存放环境及时间进行管控;f)评估电镀除油剂、光剂和干膜的兼容性;g)其他异常情况。
三、上渗镀 上渗镀时常困扰着很多工艺技术人员,本文重点论述上渗镀成因及解决对策,以某公司处理线路上渗镀的案例来展开说明。
某公司长期被上渗镀困扰,时好时坏,从干膜到电镀制程,调整过多次参数及物料,均无法将上渗镀问题彻底解决。
首先对缺陷模式进行分析,检查蚀刻后的板发现线路边缘有突起和亮边现象(见图3);进一步做金相切片分析,并与正常线路(图4)对比,切片对比显示问题板线路顶端未能正常蚀刻(对比图5、6);因此,推断线路顶端有抗蚀物质。
抗蚀物质来源有两方面:一是退膜不净,二是有渗锡;试板过两次退膜未有改善,同时对异常板和正常板退膜前进行切片分析,发现正常板镀锡层和二铜层平齐(图7),而异常板镀锡层对二铜边缘有包裹现象,线路边缘顶端被锡层包裹(图8),即渗锡导致蚀刻时线路顶端未能正常蚀刻,出现线路上渗镀。
浅谈电镀锡线状渗镀——记马达板线状渗镀处理
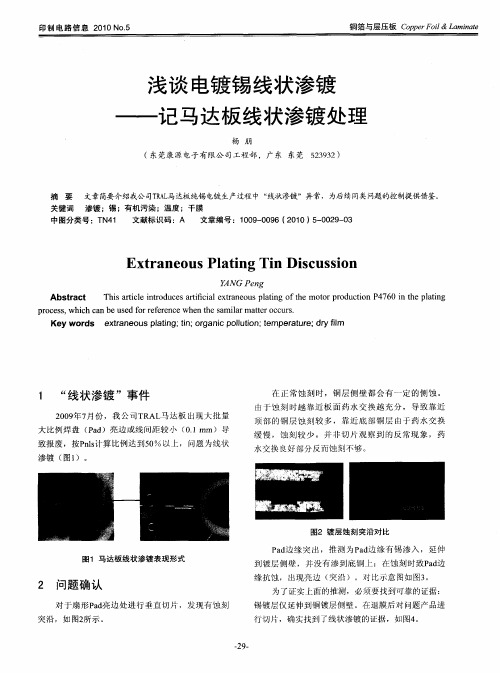
( )碳 过 滤3 ,每 次2h 5 次 ;
( )小 电流 进行拖 缸 ; 6
图 4 镀 铜侧 壁发 现 锡
通 过 以上 措 施 的 实 施 后 ,跟 进 生 产 和 HUL L
CE L 片 ,生产 板 电镀 锡逐 渐 可 以得 到均匀 、细致 L打
到镀 层侧 譬 ,并 没有 渗 到底 铜 上 ;在 蚀 刻 时致 P d a 边
缘 抗蚀 ,出现 亮边 ( 沿 ) 。对 比示意 图如 图3 突 。 为 了证实上 面 的推测 ,必 须要 找到 可靠 的证据 : 锡 镀层 仅 延伸 到铜镀 层侧 壁 。在 退膜 后对 问题产 品进 行 切片 ,确 实找 到了线 状渗镀 的证 据 ,如 图4 。
小 结:线状 渗镀 为镀层 侧壁 渗锡造 成 。
的半光 亮镀层 ;打 片 ( S 1 D,5 i)烧 片区域 也正 A n m
3 原 因查找及 改善
什 么 原 因 导 致 了此 种 渗 镀 , 该 如 何 处 理 和 预 防 ?通 过 查 看 《 制 程 全 书 》 中对 于 锡 渗镀 ( 状 湿 线 渗镀 )的分析 ,做 出特性 要 因图 ( )。 图5
图3 蚀 刻 对 比 图
( )极少进 行拖 缸 ,碳 芯过 滤等保 养 ; 3 根据 ( 3)的特 点 ,我 们 认 为 存 在 两 个 问题 :
① 锡 缸 光 剂 过 量 ( 于 马达 板 而 言 ,盲 孔 板 无 影 对 响 ) ; ② 存 在 有 机 污 染 。所 以需 要 对 锡 缸 进 行 保 养 ,遂进行 了以下改 善措施 :
一
一
图 5 渗 锡 的特 性 要 因图
3 1 锡 缸温度超温 .
采 用冰 块 降温 方 法对 锡 缸 降温 ,温 度 由2 6℃降 到 了2 0℃,试验 产 品按p l计算缺 陷 比例 由5 %降到 ns 0 了1 %,线状 渗镀依 然存 在 。 5
电镀溶液跑、冒、滴、漏的预防
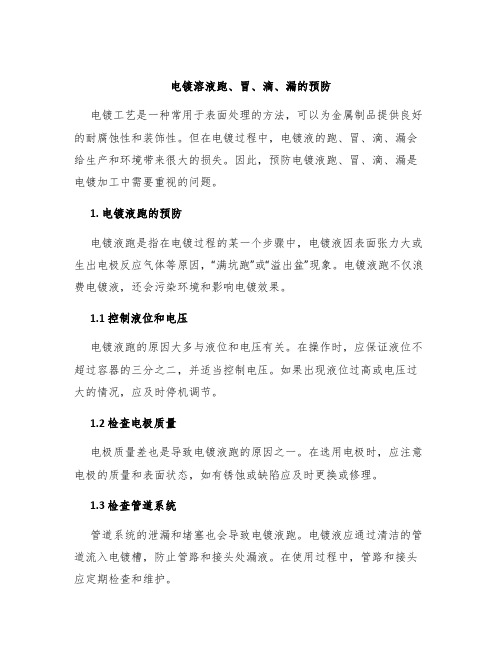
电镀溶液跑、冒、滴、漏的预防电镀工艺是一种常用于表面处理的方法,可以为金属制品提供良好的耐腐蚀性和装饰性。
但在电镀过程中,电镀液的跑、冒、滴、漏会给生产和环境带来很大的损失。
因此,预防电镀液跑、冒、滴、漏是电镀加工中需要重视的问题。
1. 电镀液跑的预防电镀液跑是指在电镀过程的某一个步骤中,电镀液因表面张力大或生出电极反应气体等原因,“满坑跑”或“溢出盆”现象。
电镀液跑不仅浪费电镀液,还会污染环境和影响电镀效果。
1.1 控制液位和电压电镀液跑的原因大多与液位和电压有关。
在操作时,应保证液位不超过容器的三分之二,并适当控制电压。
如果出现液位过高或电压过大的情况,应及时停机调节。
1.2 检查电极质量电极质量差也是导致电镀液跑的原因之一。
在选用电极时,应注意电极的质量和表面状态,如有锈蚀或缺陷应及时更换或修理。
1.3 检查管道系统管道系统的泄漏和堵塞也会导致电镀液跑。
电镀液应通过清洁的管道流入电镀槽,防止管路和接头处漏液。
在使用过程中,管路和接头应定期检查和维护。
2. 电镀液冒的预防电镀液冒是指电镀液在搅拌、振动、通气等作用下产生的气泡运动或喷射现象。
电镀液冒会导致电镀效果不均匀,影响产品质量。
2.1 控制液位和气体与电镀液跑相似,电镀液冒也与液位和气体的存在有关。
控制电镀槽的液位,及时清理污染物和杂质,减少气体的产生和存在,都可以减少或消除电镀液冒。
2.2 控制搅拌速度和温度搅拌速度和温度也会影响电镀液冒。
在操作时应保持适宜的搅拌速度和温度,以减少电镀液冒的发生。
同时,应使用适当的搅拌设备,使电镀液的搅拌均匀而不会产生气泡。
2.3 使用抗冒剂选用合适的抗冒剂,也可以减少或消除电镀液冒。
抗冒剂是通过减小电镀液的表面张力,抑制气泡的产生而发挥作用的。
3. 电镀液滴的预防电镀液滴是指电镀液在流动或运动过程中散落或“溅”出的现象,这些电镀液滴会沉积在设备表面,影响电镀质量。
3.1 保护设备表面保护设备表面可以减少电镀液滴的沉积。
电镀件常见不良原因分析
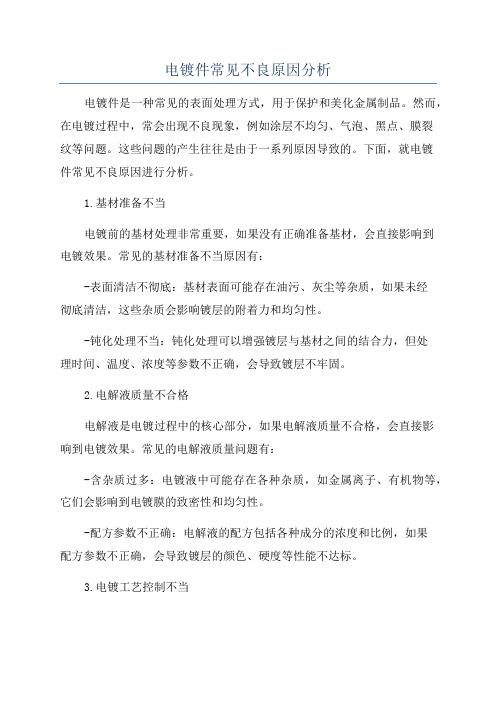
电镀件常见不良原因分析电镀件是一种常见的表面处理方式,用于保护和美化金属制品。
然而,在电镀过程中,常会出现不良现象,例如涂层不均匀、气泡、黑点、膜裂纹等问题。
这些问题的产生往往是由于一系列原因导致的。
下面,就电镀件常见不良原因进行分析。
1.基材准备不当电镀前的基材处理非常重要,如果没有正确准备基材,会直接影响到电镀效果。
常见的基材准备不当原因有:-表面清洁不彻底:基材表面可能存在油污、灰尘等杂质,如果未经彻底清洁,这些杂质会影响镀层的附着力和均匀性。
-钝化处理不当:钝化处理可以增强镀层与基材之间的结合力,但处理时间、温度、浓度等参数不正确,会导致镀层不牢固。
2.电解液质量不合格电解液是电镀过程中的核心部分,如果电解液质量不合格,会直接影响到电镀效果。
常见的电解液质量问题有:-含杂质过多:电镀液中可能存在各种杂质,如金属离子、有机物等,它们会影响到电镀膜的致密性和均匀性。
-配方参数不正确:电解液的配方包括各种成分的浓度和比例,如果配方参数不正确,会导致镀层的颜色、硬度等性能不达标。
3.电镀工艺控制不当电镀工艺过程中的各个环节都需要精确控制,否则会产生不良现象。
常见的电镀工艺控制不当原因有:-电流密度不均匀:电镀过程中,电流密度分布不均匀会导致镀层厚度不均匀,甚至出现孔洞等问题。
-温度控制不准确:电镀过程中的温度控制对于镀层的质量和均匀性非常重要,如果温度控制不准确,会影响到电解液的反应速率和镀层的结构。
4.设备维护不当电镀设备的维护工作也是保证电镀质量的关键。
常见的设备维护不当原因有:-阴极和阳极污染:设备内部的阴极和阳极可能会受到电解液的腐蚀,长期使用后会产生污染物,需要定期清洗和更换。
-设备参数不稳定:设备的电流、温度、电压等参数需保持稳定,如果设备参数不稳定,会导致镀层质量下降。
综上所述,电镀件常见的不良现象往往由基材准备不当、电解液质量不合格、电镀工艺控制不当和设备维护不当等原因导致。
为确保电镀质量,操作人员应遵循正确的工艺流程,提高工作细致性和耐心性,严格控制每个环节的参数和条件,以及定期维护设备,确保设备的正常运行。
选择性镀金渗镀影响分析

选择性镀金渗镀影响分析天津普林电路股份有限公司天津市 300160摘要:沉镍金因具有良好的平整性、可焊性、可打线、接触电阻小等优点,使其迅速成为PCB最终表面工艺的主流之一。
但沉镍金的金比较软,不具有良好的耐磨性,不适用于金手指,而电镀金硬度高具有良好的耐磨性,适用于金手指。
为了满足既具备可焊性,打线性又具备良好的耐磨性,所以很多产品选择性镀金工艺加工。
但在加工过程中干膜容易出现气泡,甚至干膜破裂导致电金盘发黑异常。
关键词:抗化金干膜;渗镀焊盘发黑;干膜附着力;选择性引言沉镍金因具有良好的平整性、可焊性、可打线、接触电阻小等优点,使其迅速成为PCB最终表面工艺的主流之一。
但沉镍金的金比较软,不具有良好的耐磨性,不适用于金手指,而电镀金硬度高具有良好的耐磨性,适用于金手指。
为了满足既具备可焊性,打线性又具备良好的耐磨性,所以很多产品选择性镀金工艺加工。
此表面处理工艺先电镀金再沉镍金时,需将电金位置用干膜(W250)或抗化金油墨覆盖保护,当用干膜保护电镀金PAD时,会出现干膜无法保护电金位置,沉镍金药水攻击电镀金PAD导致金面不良,产生品质异常。
通过报废缺陷的影响进行调查和分析,从中寻求解决的办法并总结经验和结果,从而得出更好的改善方法。
1.流程说明前流程→局部电镀金→退膜→外层图形(2)→图形电镀→外层蚀刻→外层AOI→丝印阻焊→外层图形(3)→沉金→退膜→后流程2.异常描述以上流程外层图形(3)时需使用抗化金干膜(W250)将电金位置覆盖,保证沉镍金时药水不会攻击电镀金PAD位置。
实际生产过程中沉镍金厚电镀金位置覆盖的干膜会出现气泡,部分干膜出现破裂问题,沉镍金药水渗入攻击电镀金位置,退膜后出现电镀金盘发黑异常。
3.原因分析4.试验跟进确认结轮:从以上试验跟进结果来看:1.导致沉镍金时药水渗入电镀金位置的主要影响因素是曝光能量不足,W250干膜底部光固化不足,导致干膜与电镀金位置结合力不足,沉金时出现药水渗入异常;2.提高曝光能量到10格满11格残(原有管控要求为8-10格)能够有效的解决气泡问题,但不能完全杜绝,仍有药水渗入导致电镀金位置发黑的隐患。
影响电镀层质量的内因与外因剖析

影响电镀层质量的内因与外因剖析电镀件质量的好坏直接影响着设备的整体质量。
影响电镀质量的因素包括内部因素和外部因素。
因此,不仅要对影响电镀质量的内部因素应有一个全面的认识,而且对影响电镀质量的外部因素也不容忽视,严格控制每一个环节,才能确保电镀质量。
影响电镀质量的因素包括内部因素和外部因素两个方面:一、内部因素电镀车间内部严格的质量管理是电镀零件质量的有力保障。
为了从根本上提高电镀质量,并获得优质镀层的目的,对影响电镀质量的每一个内部环节都应有一个全面的认识。
(一)前处理因素镀层与基体之间的结合力、防腐性能和外观质量的好坏,与零部件镀前表面处理的优劣有着直接关系。
附着于零件表面的油、锈、氧化皮等污物,就是妨碍电镀液与金属基体充分接触的中间障碍物,在这种表面上不可能形成合格的电镀层。
当镀件上附着极薄的甚至肉眼看不见的油膜和氧化膜时,虽然得到外观正常、结晶细致的镀层,但是结合强度大为降低。
因此,做好零件的前处理,是整个电镀工序获得良好结果的先决条件。
首先,必须保证除油和酸洗溶液的浓度和纯度,溶液中漂浮的油污要及时清理干净;其次,除锈液杂质达到一定量时,将会影响镀层质量,所以要定期更换。
(二)电镀药液因素在电镀生产中,由于各种原因,导致各种有害杂质进入电镀液。
杂质的种类繁多,大致有金属杂质、金属氧化物、非金属杂质和种种不溶性悬浮物、有机杂质等。
各种镀液所含杂质的种类不尽相同,对同一种杂质的容忍程度也不相同。
当一种或几种有害杂质积累到一定程度时,就会影响镀液性能和镀层质量,因此,不能等到杂质积累到造成危害时,才处理电镀液。
另外,电镀药液各成分含量有一个最佳工艺范围,应对槽子药液定期进行化验分析,保证各成份在工艺范围内;同时,根据生产任务量、实际经验和化验结果,在杂质积累到有可能影响电镀层质量之前,净化处理电镀液,以保证电镀药液的稳定性。
(三)工艺条件控制因素工艺条件的控制直接影响着电镀层的质量。
只有掌握和控制好每个镀种的各工艺条件,才能获得优质镀层。
影响电镀锌的因素

影响电镀锌的因素
电镀锌的质量和效果受到多个因素的影响,以下是其中一些主要因素:
1. 金属表面的准备:在进行电镀锌之前,金属表面必须进行充分的准备,以确保表面清洁、光滑且不受污染。
通常会使用化学物质或机械方法来清洁金属表面。
2. 电镀过程中的电流密度:电流密度是指单位面积内通过电流的电量,电流密度越大,电镀速度越快,但如果电流密度过大,则可能会导致电镀层质量下降。
3. 电镀液的成分:电镀液中的化学成分可以影响电镀层的质量和效果。
例如,添加剂可以改善电镀层的质量和均匀性。
4. 电镀时间和温度:电镀时间和温度也会影响电镀层的质量和效果。
通常来说,电镀时间越长,电镀层越厚,但也可能导致电镀层不均匀。
温度过高也会影响电镀层的质量。
5. 金属基材的质量:金属基材的质量也会影响电镀层的质量和效果。
如果金属表面存在缺陷或污染,可能会导致电镀层质量下降。
这些因素是影响电镀锌的主要因素,但并不是所有因素。
在进行电镀锌之前,需要仔细评估所有相关的因素,并采取适当的措施来确保电镀层的质量和效果。
【正天伟课堂】电镀上渗镀成因及解决对策

【正天伟课堂】电镀上渗镀成因及解决对策2015-11-07正天伟科技 欢迎来到正天伟课堂!本期要与大家分享的是通过缺陷模式将渗镀分为上渗镀和下渗镀,分别从图像转移和图形电镀制程详细描述了每一个环节对渗镀的影响,并通过案例阐述了上渗镀的解决对策。
愿共分享,共探讨。
一、前言 随着精细线路板和高频线路板的发展,对线路的精度提出了更高的要求,线路稍有偏差就会影响到信号传输,线路渗镀便是导致信号传输不良的重要因素之一。
线路渗镀是“正片线路+电镀铜锡”工艺之板常出的问题,俗称线路狗牙(或线路锯齿),有上渗镀和下渗镀之分,出现在线路底端称为下渗镀,出现在线路顶端称为上渗镀。
二、下渗镀 对于下渗镀业界同行已有比较深刻的认识,在此简单阐述一下:下渗镀主要是由干膜和铜面结合力差或显影后干膜的显影侧蚀过大导致。
解决对策a)改善磨板的粗糙度及板面的清洁度;b)调整贴膜压力、温度、速度及压辘的平整度;c)使用品质优良的干膜;d)控制合适的显影点及水洗效果;e)对显影后的存放环境及时间进行管控;f)评估电镀除油剂、光剂和干膜的兼容性;g)其他异常情况。
三、上渗镀 上渗镀时常困扰着很多工艺技术人员,本文重点论述上渗镀成因及解决对策,以某公司处理线路上渗镀的案例来展开说明。
某公司长期被上渗镀困扰,时好时坏,从干膜到电镀制程,调整过多次参数及物料,均无法将上渗镀问题彻底解决。
首先对缺陷模式进行分析,检查蚀刻后的板发现线路边缘有突起和亮边现象(见图3);进一步做金相切片分析,并与正常线路(图4)对比,切片对比显示问题板线路顶端未能正常蚀刻(对比图5、6);因此,推断线路顶端有抗蚀物质。
抗蚀物质来源有两方面:一是退膜不净,二是有渗锡;试板过两次退膜未有改善,同时对异常板和正常板退膜前进行切片分析,发现正常板镀锡层和二铜层平齐(图7),而异常板镀锡层对二铜边缘有包裹现象,线路边缘顶端被锡层包裹(图8),即渗锡导致蚀刻时线路顶端未能正常蚀刻,出现线路上渗镀。
常见电镀缺陷和原因分析

常见电镀缺陷和原因分析电镀缺陷是指在电镀过程中(包括准备工作和电镀工艺)出现的不良现象或问题。
下面我将介绍一些常见的电镀缺陷以及可能的原因分析。
1. 镀层不均匀:电镀层在部分区域厚度不均匀或出现斑点、斑纹等现象。
可能的原因包括:- 温度控制不准确:电镀液的温度不稳定、过高或过低,导致镀液在镀件表面的分布不均匀。
- 电镀液流动不均匀:电镀液在镀件上的流动速度不同,导致电流分布不均,进而影响镀层的均匀性。
- 镀液成分不稳定:电镀液中的添加剂、盐类等成分浓度不稳定,导致镀层的形成不均匀。
2. 黑斑或黄斑:镀层表面出现黑色或黄色的斑点。
可能的原因包括:- 杂质污染:电镀液中的杂质(如氧化物、铁离子等)进入镀液中,被还原到镀层表面形成斑点。
- 温度控制不当:电镀液的温度过高,导致镀层表面出现黄色或黑色反应物。
- 电流密度不均匀:镀件表面的电流密度不均匀,导致镀层表面出现黑斑或黄斑。
3. 镀层剥落:镀层与基材之间出现脱落现象。
可能的原因包括:- 镀液准备不当:电镀液的配方和浓度不正确,导致镀液附着力不足。
- 清洗不彻底:镀件在电镀前未进行彻底的清洗,导致表面存在杂质或脱脂剂,影响镀液与基材的结合。
- 电镀时间过短:电镀时间不足,镀层与基材之间的结合力不强,易剥离。
4. 镀层起泡:镀层表面出现气泡现象。
可能的原因包括:- 水分污染:电镀液中存在水分,经电解反应后生成氢气,导致镀液中产生气泡。
- 剧烈搅拌:电镀液在搅拌过程中引入大量气体,导致镀液中产生气泡。
- 电流密度不均匀:镀件表面的电流密度分布不均匀,导致一些区域出现过高的电流密度,进而引发气泡。
5. 镀层色差:镀层表面出现色差现象,包括颜色不均匀、色泽深浅不一等。
可能的原因包括:- 镀液浓度不均:电镀液中添加剂或盐类的浓度不均匀,导致镀层颜色不均匀。
- 电镀液PH值不稳定:电镀液中PH值变化较大,会影响镀层的色泽。
- 镀液渗染:电镀液渗透到基材中,与基材反应产生色差。
电镀溶液泄漏的原因分析和可采取的措施正式样本
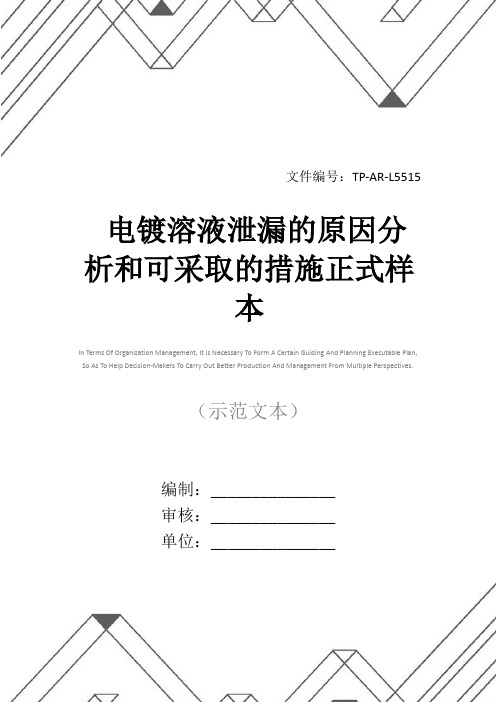
文件编号:TP-AR-L5515In Terms Of Organization Management, It Is Necessary To Form A Certain Guiding And Planning Executable Plan, So As To Help Decision-Makers To Carry Out Better Production And Management From Multiple Perspectives.(示范文本)编制:_______________审核:_______________单位:_______________电镀溶液泄漏的原因分析和可采取的措施正式样本电镀溶液泄漏的原因分析和可采取的措施正式样本使用注意:该解决方案资料可用在组织/机构/单位管理上,形成一定的具有指导性,规划性的可执行计划,从而实现多角度地帮助决策人员进行更好的生产与管理。
材料内容可根据实际情况作相应修改,请在使用时认真阅读。
原因分析(1)严防镀液加温过高。
当镀液加温过高时,镀液会加速蒸发和分解,气雾中含有高浓度的溶质成分。
这时会严重污染环境,尤其是酸、碱气雾,氰化物和铬雾对环境的影响和人体危害会更大。
(2)严格防止镀液被排风机吸走。
当排风机配备不当(规格过大),镀液液位过高(离槽沿过近),这时镀液容易被吸走,在槽盖未启开之前尤为严重,既引起环境污染,又会造成镀液损耗,出现这种情况时要及时采取措施予以解决,如降低镀液液位,调整吸风口宽度,在室外的排风机之前的管道下方设一个集液器,以便收集吸入的镀液或冷凝水。
(3)减轻镀液大处理时的损耗。
镀液大处理过程中若不加以注意,则镀液的损耗量是相当大的,通常的损耗量达2%~3%,即1000L镀液经处理之后往往需补充20~30L纯净水,及相应的化工材料,才能恢复到原来的液位和原来的浓度,操作时若能细心一点,机械过滤与手工过滤相配合,让镀液尽可能由槽底的沉淀物中滤出来,则可大大减轻镀液的损耗,从而既节省材料的损耗,又能大大改善对环境的污染程度。
电镀溶液跑、冒、滴、漏的原因及预防
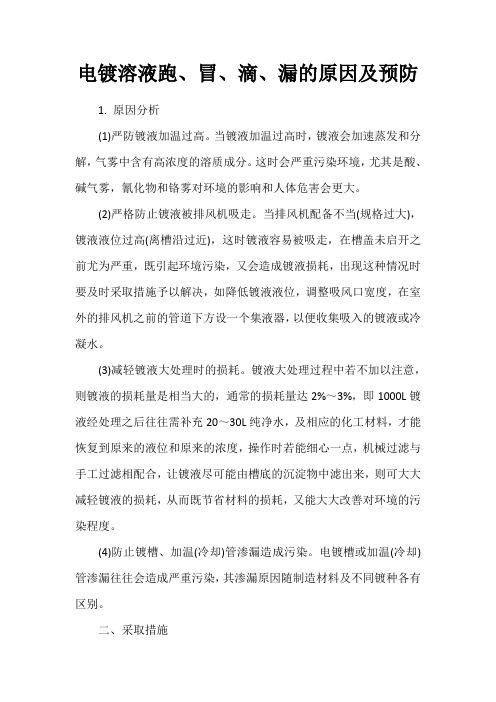
电镀溶液跑、冒、滴、漏的原因及预防1. 原因分析(1)严防镀液加温过高。
当镀液加温过高时,镀液会加速蒸发和分解,气雾中含有高浓度的溶质成分。
这时会严重污染环境,尤其是酸、碱气雾,氰化物和铬雾对环境的影响和人体危害会更大。
(2)严格防止镀液被排风机吸走。
当排风机配备不当(规格过大),镀液液位过高(离槽沿过近),这时镀液容易被吸走,在槽盖未启开之前尤为严重,既引起环境污染,又会造成镀液损耗,出现这种情况时要及时采取措施予以解决,如降低镀液液位,调整吸风口宽度,在室外的排风机之前的管道下方设一个集液器,以便收集吸入的镀液或冷凝水。
(3)减轻镀液大处理时的损耗。
镀液大处理过程中若不加以注意,则镀液的损耗量是相当大的,通常的损耗量达2%~3%,即1000L镀液经处理之后往往需补充20~30L纯净水,及相应的化工材料,才能恢复到原来的液位和原来的浓度,操作时若能细心一点,机械过滤与手工过滤相配合,让镀液尽可能由槽底的沉淀物中滤出来,则可大大减轻镀液的损耗,从而既节省材料的损耗,又能大大改善对环境的污染程度。
(4)防止镀槽、加温(冷却)管渗漏造成污染。
电镀槽或加温(冷却)管渗漏往往会造成严重污染,其渗漏原因随制造材料及不同镀种各有区别。
二、采取措施1.预防方法:在靠近阳极的槽壁竖块耐温玻璃或塑料板,起到隔断阳极板与槽衬的接触,减轻腐蚀机会。
补救方法:在铁质外壳槽的液位以下3~5cm处钻个声l~1.5mm的小孔,当内衬铅槽(也包括内衬塑料槽)损坏时,镀铬溶液即会由此射出,通过这一信号即可知道内衬槽已损坏,可当即进行修复,从而可以避免更大事故的发生。
2.铅质加温(降温)管的渗漏原因及预防方法。
铅质加温(降温)管的渗漏原因与铅质衬槽渗漏有某些相似,但它还有因承受压力引起膨胀而造成损裂的可能,铅管渗漏对环境的危害同样很厉害,一旦渗漏即有可能使槽内溶液随蒸汽或水射出槽外,若回汽回人锅炉,则危害性更大,有可能为此而毁坏锅炉而发生更大事故。
渗镀导致的原因
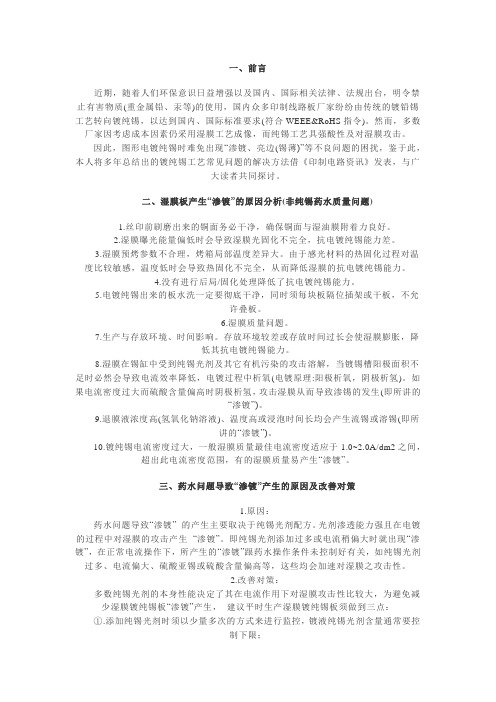
一、前言近期,随着人们环保意识日益增强以及国内、国际相关法律、法规出台,明令禁止有害物质(重金属铅、汞等)的使用,国内众多印制线路板厂家纷纷由传统的镀铅锡工艺转向镀纯锡,以达到国内、国际标准要求(符合WEEE&RoHS指令)。
然而,多数厂家因考虑成本因素仍采用湿膜工艺成像,而纯锡工艺具强酸性及对湿膜攻击。
因此,图形电镀纯锡时难免出现“渗镀、亮边(锡薄)”等不良问题的困扰,鉴于此,本人将多年总结出的镀纯锡工艺常见问题的解决方法借《印制电路资讯》发表,与广大读者共同探讨。
二、湿膜板产生“渗镀”的原因分析(非纯锡药水质量问题)1.丝印前刷磨出来的铜面务必干净,确保铜面与湿油膜附着力良好。
2.湿膜曝光能量偏低时会导致湿膜光固化不完全,抗电镀纯锡能力差。
3.湿膜预烤参数不合理,烤箱局部温度差异大。
由于感光材料的热固化过程对温度比较敏感,温度低时会导致热固化不完全,从而降低湿膜的抗电镀纯锡能力。
4.没有进行后局/固化处理降低了抗电镀纯锡能力。
5.电镀纯锡出来的板水洗一定要彻底干净,同时须每块板隔位插架或干板,不允许叠板。
6.湿膜质量问题。
7.生产与存放环境、时间影响。
存放环境较差或存放时间过长会使湿膜膨胀,降低其抗电镀纯锡能力。
8.湿膜在锡缸中受到纯锡光剂及其它有机污染的攻击溶解,当镀锡槽阳极面积不足时必然会导致电流效率降低,电镀过程中析氧(电镀原理:阳极析氧,阴极析氢)。
如果电流密度过大而硫酸含量偏高时阴极析氢,攻击湿膜从而导致渗锡的发生(即所讲的“渗镀”)。
9.退膜液浓度高(氢氧化钠溶液)、温度高或浸泡时间长均会产生流锡或溶锡(即所讲的“渗镀”)。
10.镀纯锡电流密度过大,一般湿膜质量最佳电流密度适应于1.0~2.0A/dm2之间,超出此电流密度范围,有的湿膜质量易产生“渗镀”。
三、药水问题导致“渗镀”产生的原因及改善对策1.原因:药水问题导致“渗镀” 的产生主要取决于纯锡光剂配方。
光剂渗透能力强且在电镀的过程中对湿膜的攻击产生“渗镀”。
漏镀分析报告

漏镀分析报告背景介绍漏镀是指在金属镀膜过程中,部分或整个镀层没有完全覆盖被镀物表面的现象。
漏镀不仅会影响镀层的质量,还会降低镀层的保护功能和装饰效果,因此对漏镀现象进行分析和排查十分重要。
本文档旨在对漏镀进行分析,并提出相应的解决方案。
漏镀分析漏镀现象可能由多种原因引起,需要进行仔细的分析才能找出根本原因。
下面列举了一些常见的漏镀原因:1.表面污染:如果被镀物的表面有污物、油脂或氧化物,会阻碍电镀液与金属表面的接触,从而导致漏镀。
2.镀液质量问题:如果电镀液中发生变质、污染或者化学成分不正确,也会导致漏镀出现。
3.电流密度不均匀:如果电极之间的电流密度不均匀,会引起一部分区域镀层过厚,另一部分区域漏镀。
4.电镀时间不足:如果电镀时间不足,没有完成整个镀层的形成过程,也会造成漏镀。
漏镀解决方案根据分析结果,我们可以针对不同的漏镀原因提出相应的解决方案:表面污染解决方案:1.在电镀前,对被镀物进行彻底的表面清洁,去除污物、油脂和氧化物。
2.使用适当的清洗剂和工艺流程,确保被镀物表面没有残留的污染物。
镀液质量问题解决方案:1.定期检查和更换电镀液,避免电镀液的变质和污染。
2.控制电镀液的化学成分,确保其符合镀层要求。
3.使用高质量的电镀液,以提高稳定性和镀层质量。
电流密度不均匀解决方案:1.优化电镀槽的设计和电极布置,确保电流能够均匀分布到被镀物的各个部分。
2.使用电流均匀分布器等设备,调节电流密度,避免过高或过低的区域出现。
电镀时间不足解决方案:1.根据镀层要求,确保电镀时间足够长,以完成整个镀层的形成过程。
2.定期检查电镀时间的准确性,避免由于电镀时间不足导致的漏镀问题。
结论通过对漏镀原因的分析和解决方案的提出,可以有效地避免漏镀现象的发生。
关键是加强镀前的表面清洁和质量控制,优化电镀液的质量和电流密度的均匀分布,以及确保电镀时间足够长。
只有这样,才能获得具有良好质量和装饰效果的镀层。
本文档提供了一些基本的漏镀分析和解决方案,但具体应根据实际情况进行调整和补充。
影响电镀加工的因素
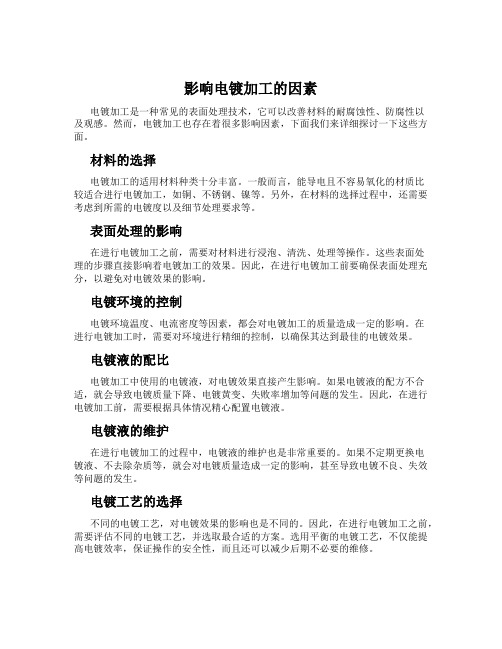
影响电镀加工的因素电镀加工是一种常见的表面处理技术,它可以改善材料的耐腐蚀性、防腐性以及观感。
然而,电镀加工也存在着很多影响因素,下面我们来详细探讨一下这些方面。
材料的选择电镀加工的适用材料种类十分丰富。
一般而言,能导电且不容易氧化的材质比较适合进行电镀加工,如铜、不锈钢、镍等。
另外,在材料的选择过程中,还需要考虑到所需的电镀度以及细节处理要求等。
表面处理的影响在进行电镀加工之前,需要对材料进行浸泡、清洗、处理等操作。
这些表面处理的步骤直接影响着电镀加工的效果。
因此,在进行电镀加工前要确保表面处理充分,以避免对电镀效果的影响。
电镀环境的控制电镀环境温度、电流密度等因素,都会对电镀加工的质量造成一定的影响。
在进行电镀加工时,需要对环境进行精细的控制,以确保其达到最佳的电镀效果。
电镀液的配比电镀加工中使用的电镀液,对电镀效果直接产生影响。
如果电镀液的配方不合适,就会导致电镀质量下降、电镀黄变、失败率增加等问题的发生。
因此,在进行电镀加工前,需要根据具体情况精心配置电镀液。
电镀液的维护在进行电镀加工的过程中,电镀液的维护也是非常重要的。
如果不定期更换电镀液、不去除杂质等,就会对电镀质量造成一定的影响,甚至导致电镀不良、失效等问题的发生。
电镀工艺的选择不同的电镀工艺,对电镀效果的影响也是不同的。
因此,在进行电镀加工之前,需要评估不同的电镀工艺,并选取最合适的方案。
选用平衡的电镀工艺,不仅能提高电镀效率,保证操作的安全性,而且还可以减少后期不必要的维修。
良好的操作技能良好的电镀加工操作技能,也是保证电镀效果的重要因素。
电镀加工是一种精细的工艺,在操作时需要严格遵守操作规程,注意安全防护措施,保证操作的规范性和质量。
以上就是影响电镀加工的因素的介绍。
在实际的生产操作中,需要全面考虑这些因素,以保证电镀加工的效果达到预期。
电镀不良现象及产生原因

雾锡镀件不良现象及产生原因不良现象原因说明低电流密度区镀层不均匀,或有漏铜现象1,金属含量太高2,电流密度太小3,硫酸浓度不足4,添加剂过量5,阳极面积不足6,前处理不充分高电流密度区发灰、发黑或烧焦1,电流密度太高2,金属含量太低3,添加剂不足表面粗糙1,电流密度过大2,电解液组成不均衡4,电解液受到杂质金属污染5,滚轮转速慢锡层易变色1,2,黄铜底材发生置换现象2,电镀后水洗不充分3,产品存储不佳,受潮或碰到腐蚀性液体4,添加剂过量锡层不均匀1,添加剂不足2,锡浓度过高 3.电流密度太小4,硫酸浓度低锡层耐腐蚀性不佳1,前处理不足2,有杂质空隙3,镀件不良针孔多镀层泛黄1,锡层厚度不足2,光泽剂添加不足3,存储场所不佳有酸碱气体,空气潮湿4,电镀后中和不佳线管发黑1,多发于S型端子,卡在滚桶壁上电击伤,黑斑1,电流密度过大,阴极放电将端子烧焦亮锡镀件不良现象及产生原因不良现象原因说明表面有白雾1,含量太高2,电流密度太小3,硫酸浓度不足4,光泽剂不足5,阳极面积不足6,浴温太高7,阳极钝化8,前处理不充分锡层容易剥落1,锡层厚度不足2,锡层氧化3,光泽剂过量4,电解液受到金属杂质污染表面粗糙1,电流密度过大2,电解液组成不均衡4,电解液受到杂志金属污染5,光泽剂不足1锡层不均匀1,添加剂不足2,锡浓度过高 3.电流密度太小4,硫酸浓度低镀层泛黄1,锡层厚度不足2,光泽剂添加不足3,存储场所不佳有酸碱气体,空气潮湿4,电镀后中和不佳镀层泛蓝1,添加剂比例不均衡,光泽剂过量前处理的重要性前处理的目的前处理的目的是保持产品表面清洁,由于镀件在制造、加工搬运、保存期间会有油脂、氧化物锈皮、氢氧化物、灰尘等污物附著于镀件表面,若不去除这些污物进行电镀,产品品质将无法得到保证,所以前处理在电镀制程中占有很重要的地位。
前处理不良会造成的电镀不良现象前处理不良会产生的不良现象,有下列几项:(1)锡层脱落(2)镀层有气泡(3)表面有黑点(4)色泽不均匀(5)表面有锡点(7)表面粗糙(8)产品耐腐蚀性降低(9)脆化。
- 1、下载文档前请自行甄别文档内容的完整性,平台不提供额外的编辑、内容补充、找答案等附加服务。
- 2、"仅部分预览"的文档,不可在线预览部分如存在完整性等问题,可反馈申请退款(可完整预览的文档不适用该条件!)。
- 3、如文档侵犯您的权益,请联系客服反馈,我们会尽快为您处理(人工客服工作时间:9:00-18:30)。
104均无法将上渗镀问题彻底解决,通过数据统计,出现上渗镀问题的板件全部表现在线距小于0.1mm的板件,同时经市场调查,行业内使用高感干膜做电镀铜锡流程的公司都发现有不同程度的上渗镀问题,无法得到100%有效的解决。
首先将上渗镀板件进行分析,检查上渗镀外观发现线路边缘有突出像锯齿一样的亮边现象(见图1),进一步金相显微镜切片分析(图2),并与正常线路做对比(图3、图4),切片问题板件显示线路的顶端有突延,没有正常蚀刻,分析线路顶端有抗蚀刻的物质保护,抗蚀刻物质的制程中来源有渗锡和褪膜不净,试板过2次褪膜,上渗镀问题没有改善,对异常板件和正常板件在褪膜前进行金相切片分析,发现正常板件镀锡层与二铜层平齐(图5),异常板件镀锡层对二铜有包裹现象(图6),可以锁定上渗镀原因为渗锡造成不能正常蚀刻,导致最终出现上渗镀现象,为此,需进一步查找渗锡原因。
为了从根源上有效改善上渗镀,上渗镀问题从人、
浅析电镀上渗镀影响因素
文/深圳市强达电路有限公司 江清兵
高精密线路板和通讯领域高频线路板的高速发展,
对线路的精度提出了更大的挑战,线路质量稍有偏差
就会影响阻抗和信号传输,传统曝光机制作方式已不
能满足此类高精度线路的要求,为应对高精度线路板
线路质量的挑战,近几年LDI激光直接成像与高感光
干膜搭配的新兴技术应运而生。
高精密线路板和通讯领域高频线路板在加工过程
中受线宽线距、铜厚等因素影响,无法全部使用负片
流程,但此类板件在LDI激光直接成像与高感光干膜
的搭配方式在正片制作流程中,无法全部避免上渗镀
问题,给线路板加工造成困扰,本文主要针对上渗镀
进行分析、探讨和改善。
因公司被上渗镀问题困扰,时好时坏,从干膜工
序到图电工序,多次调整参数、物料和对比实验分析,
【摘 要】高精密线路板和通讯领域高频线路板的高速发展,对线路的精度提出了更大的挑战,线
路质量稍有偏差就会影响阻抗和信号传输。
近几年LDI激光直接成像与高感光干膜搭配的新兴技
术应运而生,但此类板件在LDI激光直接成像与高感光干膜搭配方式的电镀铜锡制作过程中,无
法全部避免上渗镀问题,给线路板加工造成困扰,本文主要针对上渗镀进行分析、探讨和改善。
【关键词】LDI;高感光干膜;电镀铜锡;上渗镀
作者简介:江清兵,强达电路工艺部主管,主要从事PCB工艺技术
工作。
0 前言
1 背景及市场调查
2 上渗镀不良现象
3 上渗镀原因分析因果图
2019年3月第2期
105
PCB Information
MAR 2019 NO.2统计不良板的共性特征及实际表现形态,针对上
4 实验验证
图1外观线路锯齿图片图3上渗镀板件切片图图5异常有锡包裹二铜切片图图7 上渗镀原因分析因果图
图8
图9
图2正常蚀刻板件外观图片
图4正常板件切片图
图6正常图电后板件切片图
机、物、法、环方面因果图分析,如下图7。
渗镀问题做实验方案进行验证影响因素,对可能产生上渗镀原因进行排查。
4.1 实验方案及结果4.1.1 实验方案一
使用不同厂家的高感干膜A、高感干膜B、普通干膜C 和普通干膜D 正常制作外层线路图形,图形最小线宽线都小于0.1mm,使用图电极限参数制作(镀铜参数:8ASF *120min,镀锡:11ASF *12.5min),蚀刻后AOI 扫描检查,观察线路上渗镀外观良率,验证不同厂家的干膜对上渗镀影响,统计数据如下图8。
小结:通过实验表明,对比不同厂家、不同型号的干膜在同一条件下生产,高感干膜上渗镀不良率明显比普通干膜上渗镀不良率更高。
4.1.2 实验方案二
使用不同厂家的高感干膜A、高感干膜B、普通干膜C 和普通干膜D 提升曝光能量到8格满(21级曝
光尺),曝光后静止30min,其余参数按照实验方案一制作,验证曝光能量对上渗镀影响,统计数据如下图
9。
小结:通过实验表明,不同厂家,不同型号的干膜在提升曝光能量后,上渗镀不良比率有明显下降趋势,但无法完全杜绝上渗镀问题。
2019年3月第2期
106
4.1.3 实验方案三
在出现不良板件的情况下,实测显影点测试结果为50%,显影后的板件做SEM 分析,排查是否有显影后干膜侧壁不平整或显影过度现象,SEM 实测4种干膜显影后侧壁均无明显不平整、显影过度现象,相关图片如下图10、图11、图12、图13。
小结:通过SEM 分析确认,是有干膜显影后侧壁均无明显不平整、显影过度现象,排除显影影响因素。
4.1.4 实验方案四
将板件使用12ASF *75min 的图电参数生产,其余参数均正常生产的条件下,将板件图电成夹膜状态,切片确认验证干膜是否是否出现变形、不抗镀,切片图片如图14、图15、图16、图17。
图10 高感干膜A图14 高感干膜A
图16 普通干膜C
图12 普通干膜C
图11 高感干膜B
图15 高感干膜B
图17 普通干膜D
图13 普通干膜
D
小结:通过实验发现,在同等条件下,两种高感干膜切片都发现明显的形变、不抗镀现象,普通干膜C 电镀后未发现干膜形变现象,普通干膜D 出现轻微的干膜形、不抗镀变现象,说明干膜本身和电镀药水
存在不兼容现象会影响上渗镀。
107
PCB Information
MAR 2019 NO.24.1.5实验方案五
将图电除油温度由设定30度调整为设定28度,其余参数均正常生产的条件下,验证除油温度对上渗镀的影响,统计数据如下图18。
小结:通过实验发现,不同厂家,不同型号的干膜在降低除油温度对上渗镀有明显改善趋势,但仍有较大比例板件上渗镀。
4.1.6实验方案六
将图电锡缸震动马达功率由35W 改为30W(图电线飞巴宽度3.2米),同时锡缸光剂浓度按下限控制,其余参数均正常生产的条件,验证图电锡缸震动马达震动功率和锡缸光剂对上渗镀的影响,统计数据如图19所示。
小结:通过实验发现,不同厂家、不同型号的干膜,在降低图电锡缸震动马达震动功率和锡缸光剂浓度对上渗镀的除油温度对上渗镀有极大的改善,但仍无法100%避免上渗镀。
4.2 上渗镀问题原因
经过多次实验排查对比分析,线路上渗镀问题原因主要有:
(1)使用的干膜性能不足;(2)干膜曝光能量不足;(3)除油温度过高;
(4)锡缸震动马达功率过高,锡缸光剂含量过高。
(1)选择性能好的干膜,同时需考虑与电镀药水的匹配性,避免出现因干膜与电镀药水不匹配导致的上渗镀问题。
(2)对不同的干膜选择合适的曝光能量,同时监控好
曝光设备的曝光能量和均匀性,避免因曝光能量低和均匀性差导致干膜曝光不足,导致渗锡造成上渗镀问题。
(3)图电除油药水的参数控制要求与除油药水的选择,都是重要的影响因素,必须要和干膜匹配,降低因除油对干膜造成的攻击。
(4)因干膜本身就是有机高分子聚合物,锡缸光剂是有机物,有机物含量越高对干膜的攻击越大,同时锡缸震动过大的条件下会加速干膜攻击,所以锡缸的控制就成了影响上渗镀最大的因素,将锡光剂含量控
制在下限,同时需定期做碳芯过滤,降低药水中的有机物含量,在不影响图电镀锡质量的条件下尽量的降低锡缸震动马达功率,以达到避免上渗镀的目的。
实验说明,目前市面上的高感光干膜做电镀铜锡流程,需要确保不出现上渗镀的条件下,实际生产参数会非常窄,同时上渗镀产生的原因非常广,涉及到物料本身和多个工序流程参数的控制问题,在出现上渗镀的问题后,需针对流程参数、物料进行逐一的排查,设计相应的实验,对于突发的问题,需考虑是否物料和流程中是否出现变更,寻找差异点,如长期存在的问题,需从物料的选择和参数设定是否合理方面入手。
技术指导人员:宋世祥、杨亚兵、郭先锋
图18
图
19
5 上渗镀改善对策
6 结论。