梯形螺纹的车削浅析
浅谈车削梯形外螺纹的加工方法

浅谈车削梯形外螺纹的加工方法车削梯形外螺纹是机械加工中常用的加工工艺之一,在工业制造中具有重要的作用。
梯形外螺纹是一种具有斜面、楔形等特点的螺纹,其加工难度相对较大,必须采用合适的加工方法以保证加工质量。
本文将从车削梯形外螺纹的加工方法入手,详细介绍梯形外螺纹的加工技术和注意点。
1. 梯形外螺纹的特点梯形外螺纹是一种比普通的直径相同的圆形螺纹工艺难度更大的螺纹。
它具有一些特点:(1) 梯形外螺纹与粗细不同的斜面相交,有两组楔形刃;(2) 梯形外螺纹斜率小于普通螺纹,阻力大,摩擦力大;(3) 梯形外螺纹制作困难,加工技术含量高。
(1) 刀具选择加工梯形外螺纹时应选择防护切削较佳的刀具。
通常采用圆柱形精密前角铣刀钻头和精度高的蜗杆加工,如螺旋铣刀和螺旋丝锥。
(2) 加工顺序加工梯形外螺纹时,应先在工件上加工出圆弧或相应的圆弧平面,然后再切削极度。
调整车床的进给速度和速度比,确保梯形外螺纹的表面质量和精度。
(3) 切削参数加工梯形外螺纹时,应根据材料硬度、切削深度、进给速度等参数来确定切削参数,以确保加工效率和加工质量。
(4) 普通车床的加工方法普通车床加工梯形外螺纹时,首先要进行预扫径,即将车床压板的座面和刃口压下去,使它们分别与基准圆的外径和切削刃的底部相接触,并自动连接。
然后,确定刀位和进给速度,并开始切削。
在切削过程中,必须反复调整刀具,确保梯形外螺纹的表面质量和精度。
数控车床加工梯形外螺纹时,首先要根据工件的要求,编写数控程序,并将切削参数输入系统中。
然后,将刀具安装到工件上,并通过数控系统控制刀具移动轨迹和切削参数进行加工。
(1) 切削时应注意切削刃的过度磨损,及时更换切削刃,以保证加工质量;(2) 切削时应注意加工表面的清洁和平整,以保证加工质量;(4) 在加工前一定要进行充分的准备工作,如测量工件的尺寸、检查设备的工作状态和加工程序等。
总之,梯形外螺纹的加工方法比较复杂,需要选用合适的加工工具和根据工件材料的硬度和加工特点确定切削参数。
梯形螺纹的数控车削
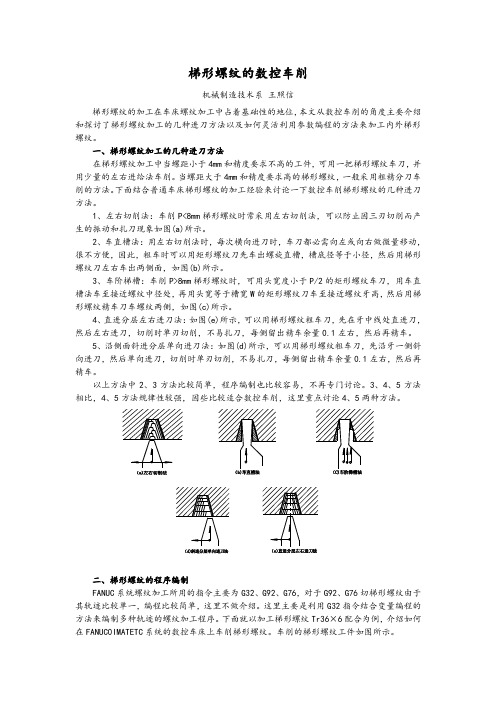
梯形螺纹的数控车削机械制造技术系王照信梯形螺纹的加工在车床螺纹加工中占着基础性的地位,本文从数控车削的角度主要介绍和探讨了梯形螺纹加工的几种进刀方法以及如何灵活利用参数编程的方法来加工内外梯形螺纹。
一、梯形螺纹加工的几种进刀方法在梯形螺纹加工中当螺距小于4mm和精度要求不高的工件,可用一把梯形螺纹车刀,并用少量的左右进给法车削。
当螺距大于4mm和精度要求高的梯形螺纹,一般采用粗精分刀车削的方法。
下面结合普通车床梯形螺纹的加工经验来讨论一下数控车削梯形螺纹的几种进刀方法。
1、左右切削法:车削P<8mm梯形螺纹时常采用左右切削法,可以防止因三刃切削而产生的振动和扎刀现象如图(a)所示。
2、车直槽法:用左右切削法时,每次横向进刀时,车刀都必需向左或向右做微量移动,很不方便,因此,粗车时可以用矩形螺纹刀先车出螺旋直槽,槽底径等于小径,然后用梯形螺纹刀左右车出两侧面,如图(b)所示。
3、车阶梯槽:车削P>8mm梯形螺纹时,可用头宽度小于P/2的矩形螺纹车刀,用车直槽法车至接近螺纹中径处,再用头宽等于槽宽W的矩形螺纹刀车至接近螺纹牙高,然后用梯形螺纹精车刀车螺纹两侧,如图(c)所示。
4、直进分层左右进刀法:如图(e)所示,可以用梯形螺纹粗车刀,先在牙中线处直进刀,然后左右进刀,切削时单刃切削,不易扎刀,每侧留出精车余量0.1左右,然后再精车。
5、沿侧面斜进分层单向进刀法:如图(d)所示,可以用梯形螺纹粗车刀,先沿牙一侧斜向进刀,然后单向进刀,切削时单刃切削,不易扎刀,每侧留出精车余量0.1左右,然后再精车。
4、5方法相比,4、5二、梯形螺纹的程序编制FANUC系统螺纹加工所用的指令主要为G32、G92、G76,对于G92、G76切梯形螺纹由于其轨迹比较单一,编程比较简单,这里不做介绍。
这里主要是利用G32指令结合变量编程的方法来编制多种轨迹的螺纹加工程序。
下面就以加工梯形螺纹Tr36×6配合为例,介绍如何在FANUC0IMATETC系统的数控车床上车削梯形螺纹。
浅谈车削梯形外螺纹的加工方法

浅谈车削梯形外螺纹的加工方法车削梯形外螺纹是工程中常见的一种加工方法,其主要用于连接矛盾物件或传动运动的机械元件上。
本文将从加工工艺、工具选择和操作技巧等方面对车削梯形外螺纹进行讨论。
一、加工工艺1. 工具选择:车削梯形螺纹通常采用刀具进行加工。
常用的刀具有螺纹车刀、手动车刀、切割车刀等。
2. 材料准备:在进行梯形外螺纹加工前,需要选择适当的材料。
通常情况下,选择硬度较高、耐磨性较好的材料进行加工,如不锈钢、碳钢等。
3. 加工精度:车削梯形外螺纹加工需要考虑螺纹的精度要求。
通常情况下,螺纹的直径和螺距都需要符合设计要求,误差控制在合理范围内。
4. 加工参数的选择:车削梯形外螺纹时,需要选择合适的加工参数,如进给速度、切削速度等。
不同材料和螺纹直径有不同的最佳加工参数。
二、工具选择车削梯形外螺纹时,使用不同的刀具可以得到不同的加工效果。
常见的刀具有以下几种:1. 螺纹车刀:这是车削梯形螺纹最常用的刀具之一。
螺纹车刀具有多个刀具尺寸,可以选择合适的螺纹刀片进行加工。
螺纹车刀适用于大批量生产外螺纹的需要。
2. 手动车刀:手动车刀主要用于小规模生产和修补工作。
它的刀片可以根据螺纹需求进行调整,对螺纹加工的灵活性较大。
3. 切割刀:切割刀是一种用于切削外螺纹的特殊刀具。
它的刀片上带有梯形切槽,可以直接切削螺纹。
切割刀通常用于螺纹长而细螺距的加工。
三、操作技巧在车削梯形外螺纹时,需要掌握一些操作技巧,以保证加工质量和效率。
1. 外径车削:外径车削是车削梯形外螺纹的第一步。
在进行外径车削时,需要将螺纹刀具的刀片正确安装,并根据螺纹直径选择合适的刀具尺寸。
要注意控制进给速度和切削深度,避免过大过小造成加工品质问题。
2. 锥度车削:锥度车削是车削梯形外螺纹的第二步。
在进行锥度车削时,需要将工件与车床的床面调至一定角度。
要控制车刀在车削时的进给速度和切削深度,使螺纹锥度达到设计要求。
3. 脱刀:在车削梯形外螺纹完成后,需要保持车刀与工件的一定距离,然后再慢慢将车刀从工件上移开。
浅析梯形螺纹的数控加工

浅析梯形螺纹的数控加工摘要 :主要介绍了利用左右切削法在数控车床上加工梯形螺纹的加工方法,梯形螺纹的加工是数控车削的一个难点,由于梯形螺纹加工工艺要求较高,在数控加工中往往会因为工艺不当而产生问题。
文章利用左右切削法解决了梯形螺纹在数控车床上加工编程困难的问题,在程序中巧妙地结合了普通车床车削梯形螺纹时应用的各种工艺技巧,采用左右进刀法车削、合理递减切削深度、螺纹切削粗精加工分段降低牙侧的粗糙度。
为数控车削梯形螺纹提供了一个实用合理的通用程序。
关键词:梯形螺纹工艺分析一、梯形螺纹零件图分析梯形螺纹常用于传动,精度要求较高。
在机床加工行业,三角形螺纹加工最为普遍,加工方法成熟易学。
梯形螺纹与三角形螺纹相比,螺距大、牙型高、切除余量大、切削抗力大,而且精度高,牙型角两侧表面粗糙度值较小,这就导致梯形螺纹加工时,吃刀深、走刀快,尤其是加工硬度较高的材料时,加工难度较大。
在数控车床上加工梯形螺纹,由于数控车床自动化程度高,加工过程由程序控制,这就要求车削梯形螺纹时,数控加工工艺设计要合理,程序编写要准确。
本文结合长期教学经历及生产实践,介绍用华中世纪星系统数控车床HNC-21/22T加工梯形螺纹的方法。
该零件是梯形螺纹轴,材料为中碳钢(45)。
零件最大外圆直径?64,总长80mm。
外圆及表面粗糙度为Ra1.6,零件的左端为Tr36单头螺纹,导程是6mm,螺纹两端倒角3x30°。
梯形螺纹根部退刀槽为?26x8,台阶圆柱直径?50,上偏差0,下偏差-0.1,台阶圆长12mm,台阶端面倒角1x45°。
零件右端直径?64,上偏差0,下偏差-0.1,长度20mm,上偏差0,下偏差-0.05,两端倒角0.5x45°。
根据要求分为两部分进行加工:(1)在该零件的加工中,为了便于装夹,选择先以毛坯材料左端定位,夹持毛坯外圆,用90°外圆车刀加工右端直径?64保证公差及粗糙度Ra1.6,倒角0.5x45°及右端面见光。
浅谈梯形螺纹的车削工艺

、
纹 可 崩 一 把 梯 形 螺 纹 车 刀 并 用 少 量 的 左 右 进给 法 车 削 。 2 . 螺距 4 — 8 m m 的 梯 形 螺 纹
一
或 钻 柄 直 径 尺 寸 , 最 大 不 能 放 入 螺 纹 槽 中 被 项 在 螺 纹 牙尖 上 ,最 小 不 能 在放 入 螺 旋 槽 时和 牙底 相碰 。
螺 距4 — 8 m m 或 精度 要 求 高的 梯形 螺 纹 , 般 采 用 左 右 切 削法 或 切 直 槽 法 车 削 _ 3 ] , 步 骤 如下 : ( 1 )粗车 、半精 度 螺纹 大 径 ,精 车余 量0 . 3 m m 左右 ,倒角 与端 面 成 1 5 。。 ( 2 )用左 右 切 削法 粗 、半 精 车螺 纹 , 底 槽 宽减 0 . 0 5 a r m 。 每 边 留精 车 余量 0 . 卜0 . 2 m m 。 螺 纹 小 径 精 车 ( 3 )纵 向前 角 :粗 车 刀一 般 为 1 5 。 左 至 尺 寸 或 选 用 刀 头 宽 度 稍 小 于 槽 底 的 切 槽 右 , 精 车 刀 为 了 保 证 牙 型 角 正 确 , 前 角 应 刀 , 用 直 进 法 粗 车 螺 纹 , 槽 底 直 径 等 于 螺 等 于 0。 , 但 实 际 上 , 生 产 时 取 5 。一 1 O 。。 纹小 径 。 ( 4 )纵 向后角 :一般 为6 O 一 8 O 。。 ( 3 )精车 螺纹 大 径至 图样 要 求 。 ( 5 ) 两 侧 刃 后 角 : 与 方 牙 螺 纹 车 刀 相 ( 4 ) 用 两 侧 切 削 刃 磨 有 卷 屑 槽 的 梯 形 同。 螺纹 精车 刀 精车 两侧 面 至 图样要 求 。 2 . 梯 形 螺 纹 车 刀 的 刃 磨 要 求 3 . 螺距 大 于8 m m的梯 形 螺 纹 ( 1 )用板 样校 对 螺纹 车 刀两 刃夹 角 。 螺 距大 于 8 m m 的 梯形 螺纹 ,一般 采 用切 ( 2) 径 向 前 角 不 为 0。 的 螺 纹 车 刀 , 阶梯槽 的方法 。步骤 如 下 : 两 刃 的 夹 角 应 修 正 (1 ) 粗 、 半 精 车 螺 纹 大 径 , 留 余 量 ( 3 ) 螺纹 车 刀 各 车 削刃 要 光滑 、 平 直 、 0 . 3 m m,倒 角 与 端 面 成 1 5 。。 无 裂 口 , 两 侧 切 削刃 对 称 , 刀 体 不 能 歪 斜 。 ( 2)用 刀 头 宽 度 小 于 p / 2 的 切槽 刀直 ( 4) 各 切 削 刃 应 用 油 石 研 去 毛 刺 。 进 法 粗 车 螺 纹 至 接 近 中 径 处 , 再 用 刀 头 宽 ( 5 )梯 形 内螺 纹车 刀 两侧 切 削 刃对 称 度 略 小 于槽 底 宽 的切 槽 直 进 法 粗 车 螺 纹 , 应 垂 直于 刀 柄 。 槽 底 直 径 等 于 螺 纹 小 径 , 从 而 形 成 阶 梯 状 3 . 梯 形 螺 纹 车 刀 的 选 择 和 装 夹 的螺 旋槽 。 ( 1 )车刀 的选 择 ( 3 ) 用 梯 形 螺 纹 粗 车 刀 , 采 用 左 右 切 通 常采用低速 车 削,一般选用 高速钢 。 削 法 半 精 车 螺 纹 两 侧 面 , 每 面 留 精 车 余 量 0.1 -0 . 2 m m。 ( 2 )车 刀装夹 ① 螺纹 车刀 的刀尖 应 与工件轴 线等 高 , ( 4 )精车 螺 纹大 径至 图样 要 求 。 弹 性螺纹 车刀应 高于工件轴 线0 . 2 - 0 . 5 m m 。 ( 5 ) 用 梯 形 螺 纹 精 车 刀 , 精 车 两 侧 ② 两 切 削 刃 夹 角 的 平 分 线 应 垂 直 于 工 面 , 控 制 中 径 完 成 螺 纹 加 工 。 件 轴 线 , 装 刀 时 用 对 刀 样 板 校 正 , 以 免 产 四 、梯 形 螺 纹 的 测 量 生 螺 纹半 角 误差 。 1 . 综合 测量 法 二 、工 件 的 装 夹 用 标准 螺纹 规 综合 测量 。 车 削 梯 形 螺 纹 时 , 切 削 力 较 大 , 工 2 . 三针 测量 法 件 一 般 采 用 一 夹 一 项 的 方 式 装 夹 , 粗 车 螺 此 种 方 法 是 测 量 外 螺 纹 中 经 的 一 种 比 距 较 大 的 梯 形 螺 纹 时 , 可 采 用 单 动 卡 盘 一 较 精 密 的 方 法 , 适 用 于 测 量 一 些 精 度 要 求 夹 一 顶 , 以保 证 装 夹 牢 固 ,此 外 , 轴 向 采 高 的螺 纹升 角 小于 4 。 的 螺 纹 工 件 , 测 量 时 用 限 位 台 阶 或 限 位 支 撑 固 定 工 件 的 轴 向 位 把 三 根 直 径 相 等 的 量 针 放 置 在 螺 纹 相 对 应 置 , 以 防 车 削 中 工 件 轴 向 窜 动 或 移 动 造 成 的 螺 旋 槽 中 ,用 千 分 尺 量 出两 边 量 针 顶 点 乱 牙撞 坏 车 刀 。 之 间的距 离 。如 图1 所示 。 三 、梯 形 螺 纹 的 车 削 方 法 三 针 测 量 法 采 用 的 量 针 一 般 是 专 门 制 1 . 螺距 小 于4 m m的 梯 形 螺 纹 造 的 。 实 际 应 用 中 , 有 时 也 用 优 质 钢 丝 或 螺 距 小于 4 m m 和 精 度 要 求 不 高 的 梯 形 螺 新 钻 头 的 柄 部 来 代 替 , 要 求 可 代 用 的 钢 丝
梯形螺纹加工新解

一.传统车削方法的弊端在教梯形螺纹和蜗杆的车削中,我们常用“直进法”和“左右切削法”,但这两种方法由于学生的接受能力有高低,因而产生了以下普遍的一系列问题:1.“直进法”在车削中,车刀的左右两侧刀刃都参与切削,排屑比较困难,同时车刀所受的总切削力比较大,因此,车刀的受力和散热条件比较差,车刀容易磨损,当进刀量过大时还能产生“扎刀”,把牙形表面镂去一块,甚至于折断车刀。
2.左右切削法相对直进法而言,只有一侧刀刃参与切削,但不如直进法简单,牙形也不易边不易车的清晰,同时车刀受单向轴向切削分力的影响,将会增加大螺纹牙形的误差。
3.学生在使用“直进法”与“左右切削法“车削梯形螺纹和蜗杆的过程中,由于技术不够成熟,加上在切削过程中,切削量掌握不好,时大时小,没有一个恒定的进刀量,很容易造成车刀“烧怀”退火,另外,掌握不好加工余量的多少,容易在粗车的过程中就把螺纹的中径车小,成为废品。
二.“分层切削法”的原理如图一,通过计算所要切削的槽宽,留光刀余量,在要所切削的槽宽行程内,通过一个合理的进刀比。
小拖板进刀量与中拖板进刀量的数量比,把需要切削掉的量,平均的分配到每一刀。
在小拖板与中拖板不断进刀,左右来回一层一层切削,最终形成一个30°或40°的梯形槽,从而切削出梯形螺纹或蜗杆。
(图一)在梯形螺纹和蜗杆的车削过程中,要切削掉的是一个梯形槽。
梯形螺纹与蜗杆只不过在角度上有所区别,一个是30°,一个是40°,为了保证车刀不三面同时参与切削,要保证在所要切削掉的梯形槽内进行左右分层切削。
槽宽的计算公式可根据梯形螺纹与蜗杆的计算公式分别求出:梯形螺纹槽宽= P – 0.366P蜗杆的槽宽= P -0.843mx梯形螺纹和蜗杆的轴向剖面形状是一个等腰梯形,而我们使用的车刀也是一个梯形成型刀。
如何使车刀沿这个等腰梯形的腰向下延伸,形成一个15°或20°的角呢?在这里就要运用三角函数算一个进刀比。
浅谈梯形螺纹的车削

浅谈梯形螺纹的车削【摘要】梯形螺纹是应用十分广泛的螺纹,有米制和英制两种。
英制螺纹在我国采用较少,我国主要采用米制梯形螺纹。
本文就梯形螺纹车刀的选用、车刀的安装、工件的安装、车床的调整、车削方法的选用及螺纹的检测加以阐述如何又快又好的车削梯形螺纹。
【关键词】车削;梯形螺纹;方法车床上长丝杠和中、小滑板的丝杠都是梯形螺纹,他们的工作长度较长,传动中精度要求高,同时梯形螺纹牙型两侧面表面粗糙度值较小,致使梯形螺纹车削时,难度较大。
在车削中如果采用较大的吃刀深度,较快的走刀速度,在一定程度上可以提高梯形螺纹的车削速度,但对于初学者较难掌握。
在实际操作中容易造成扎刀,甚至刀头折断,从而使得初学着产生畏惧心理,使得初学者再次车削时不敢进刀,甚至不敢再次车削。
针对上述情况,在长期的教学中通过不断的教学实践,总结了一套切实有效的车削梯形螺纹的方法,现加以阐述。
1.梯形螺纹车刀的选用1.1粗车刀的选用为了提高梯形螺纹的加工效率,采用硬质合金梯形螺纹粗车刀(以车Tr50×6-7h螺纹为例)。
车刀的刀尖角应小于牙型角30°,取29°为宜。
刀尖宽度小于牙槽底宽,刀头宽度可刃磨为1.6mm左右。
为了增强刀头的刚性、耐磨性,可将梯形螺纹车刀刀头刃磨成圆弧形,并可适当的刃磨出前角,前角10°以内为宜,使切削更加顺畅。
在粗车螺纹时,由于受到螺纹螺旋线的影响,螺纹升角Ψ较大,其影响不可忽略,因此在刃磨梯形螺纹车刀时,必须考虑。
车削右旋螺纹时,左侧后角应为(3°-5°)+Ψ,右侧后角应为(3°-5°)-Ψ。
1.2精车刀的选用为了提高螺纹两侧面以及底面的表面粗糙度,梯形螺纹精车刀可选用高速钢梯形螺纹车刀。
螺纹车刀的径向前角为0°,两侧切削刃之间的夹角等于牙型角,刃磨成30°,同时两侧切削刃沿着刀柄轴线方向对称分布。
为了保证车削加工的顺畅,也可在两侧磨出较大前角(10°~15°)的卷屑槽,在车削时,车刀的前端不能参与切削,只能用于精车牙型两侧面。
浅谈车削梯形外螺纹的加工方法

浅谈车削梯形外螺纹的加工方法车削梯形外螺纹是机械加工中常用的一种方法,广泛应用于汽车、机械制造等行业。
本文将从加工原理、加工方法以及工艺优化等方面对车削梯形外螺纹进行讨论。
梯形外螺纹的加工原理相对简单,即利用车床进行螺纹车削。
所谓梯形外螺纹是指螺纹牙的截面形状呈梯形,具体可以分为M型和MJ型两种。
梯形螺纹的主要参数有螺距、齿顶直径、齿根直径和螺纹锥度等,加工时需要根据给定的参数进行设置。
对于梯形外螺纹的加工,常用的方法有单刀片车削法、双刀片车削法和索引盘车削法。
下面将分别介绍这三种方法的特点和应用。
首先是单刀片车削法。
单刀片车削法适用于一些中等精度的螺纹加工,加工效率较高。
它的特点是只需要一把刀具即可完成整个螺纹的加工,节约了成本。
但是由于只有一把刀具,所以无法进行深孔加工,适用于螺纹长度较短的工件。
其次是双刀片车削法。
双刀片车削法适用于一些高精度和较长长度的梯形外螺纹加工。
它的特点是可以同时进行齿顶和齿根的车削,提高了加工精度。
双刀片车削法需要两把刀具同时进行切削,因此较单刀片车削法来说,加工效率相对较低。
最后是索引盘车削法。
索引盘车削法适用于批量生产的梯形外螺纹加工,加工效率较高。
它的特点是利用索引盘进行分度,每次轮转一个螺纹牙的角度,然后进行车削。
索引盘车削法适用于螺纹长度较长的工件,但是需要专门设计制作索引盘,成本较高。
对于车削梯形外螺纹的加工过程中,有几点需要特别注意。
首先是刀具的选用和磨削。
由于梯形外螺纹的牙形较复杂,所以刀具的要求较高,需要选择质量好、刚性强的刀具。
其次是加工过程中的刀具进给和主轴转速的选择。
进给过大会导致切削力过大,加工质量下降;主轴转速过高则会增加工件的热变形。
最后是加工润滑液的选择和使用,润滑液的作用是冷却刀具和工件,减少摩擦阻力。
车削梯形外螺纹是一种常用的机械加工方法。
通过合理选择加工方法和刀具,控制加工参数和加工工艺,可以获得高精度、高效率的梯形外螺纹加工。
浅谈车削梯形外螺纹的加工方法

浅谈车削梯形外螺纹的加工方法【摘要】本文旨在探讨车削梯形外螺纹的加工方法,首先介绍了车削梯形外螺纹加工方法的重要性和研究背景。
接着从梯形外螺纹加工方法的选择、车削工艺参数的确定、车削刀具的选择与磨削等方面展开讨论,详细介绍车削梯形外螺纹的具体加工步骤以及需要注意的问题。
在结论部分总结了车削梯形外螺纹加工方法的关键步骤,并展望了其未来的发展方向。
通过本文的阐述,读者可以更加全面地了解车削梯形外螺纹加工方法,为实际工程应用提供参考和指导。
【关键词】车削梯形外螺纹、加工方法、工艺参数、刀具选择、加工步骤、注意事项、发展方向、关键步骤、磨削、车削。
1. 引言1.1 介绍车削梯形外螺纹加工方法的重要性车削梯形外螺纹是一种常见的加工方法,广泛应用于各种机械设备中。
梯形外螺纹在工程中具有重要的作用,常用于连接零件或传递动力。
掌握车削梯形外螺纹的加工方法是非常必要的。
通过车削梯形外螺纹,可以实现产品的精准加工,提高产品的质量和精度。
梯形外螺纹的加工方法有助于提高生产效率,减少加工成本,提高企业的竞争力。
车削梯形外螺纹的加工方法也是机械加工行业的重要技术之一,掌握了这一技术,不仅可以提高个人技能水平,还可以为企业的发展提供技术支持。
介绍车削梯形外螺纹加工方法的重要性不言而喻,它对于推动机械加工技术的发展和提升产品质量具有积极的意义。
1.2 概述车削梯形外螺纹加工方法的研究背景梢裡20世紀60年代以來,工業的發展呈現出快速增長的趨勢,尤其是機械加工行業。
隨著產品數量的增加和質量的要求不斷提高,與此同時對於零部件加工精度和效率的要求也日益加大。
螺紋是機械零件中常見的連接方式,而梯形外螺紋作為一種特殊形狀的螺紋,在許多機械裝配中得到廣泛應用。
研究梯形外螺紋的加工方法對於提高零部件加工的精度和效率具有重要意義。
在過去的研究中,對於梯形外螺紋的加工方法進行了一定程度的探討,主要集中在工藝參數的選擇、刀具的選擇和加工步驟等方面。
浅析数控车梯形螺纹
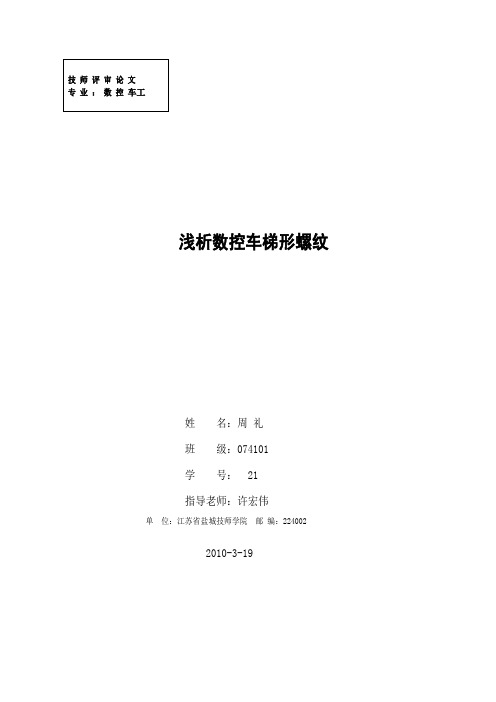
浅析数控车梯形螺纹姓名:周礼班级:074101学号: 21指导老师:许宏伟单位:江苏省盐城技师学院邮编:2240022010-3-19浅析数控车梯形螺纹【摘要】:数控车床从成型原理上讲与卧式车床基本相同,但由于增加了数字控制能力,与卧式车床相比,具有通用性好,加工效率和加工精度高,以及加工过程自动控制的特因此数控车削加工已成为国内目前使用最多的数控加工方法之一。
【关键词】:数控车削数控编程表面粗糙度残余应力一、机械加工表面质量对机器使用性能的影响1.表面质量对耐磨性的影响(1)表面粗糙度对耐磨性的影响一个刚加工好的摩擦副的两个接触表面之间,最初阶段只在表面粗糙的的峰部接触,实际接触面积远小于理论接触面积,在相互接触的峰部有非常大的单位应力,使实际接触面积处产生塑性变形、弹性变形和峰部之间的剪切破坏,引起严重磨损.零件磨损一般可分为三个阶段,初期磨损阶段、正常磨损阶段和剧烈磨损阶段.表面粗糙度对零件表面磨损的影响很大.一般说表面粗糙度值愈小,其磨损性愈好.但表面粗糙度值太小,润滑油不易储存,接触面之间容易发生分子粘接,磨损反而增加.因此.接触面的粗糙度有一个最佳值,其值与零件的工作情况有关,工作载荷加大时,初期磨损量增大,表面粗糙度最佳值也加大.(2)表面冷作硬化对耐磨性的影响加工表面的冷作硬化使摩擦副表面层金属的显微硬度提高,故一般可使耐磨性提高.但也不是冷作硬化程度愈高,耐磨性就愈高,这是因为过分的冷作硬化将引起金属组织过度疏松,甚至出现裂纹和表层金属的剥落,使耐磨性下降.2.表面质量对疲劳强度的影响金属受交变载荷作用后产生的疲劳破坏往往发生在零件表面和表面冷硬层下面,因此零件的表面质量对疲劳强度影响很大.(1)表面粗糙度对疲劳强度的影响在交变载荷作用下,表面粗糙度的凹谷部位容易引起应力集中,产生疲劳裂纹.表面粗糙度值愈大,表面的纹痕愈深,纹底半径愈小,抗疲劳破坏底能力就愈差。
(2)残余应力、冷作硬化对疲劳强度的影响残余应力对零件疲劳强度的影响很大.残余拉应力将使疲劳裂纹扩大,加速疲劳破坏;而表面层残余应力能够阻止疲劳裂纹的扩展,延缓疲劳破坏的产生表面冷作硬化,一般伴有残余应力的产生,可以防止裂纹产生并阻止已有裂纹的扩展,对提高疲劳强度有利.3.表面质量对耐腐蚀性的影响零件的耐腐蚀性在很大程度上取决于表面粗糙度,表面粗糙度值愈大,则凹谷中聚积腐蚀性物质就愈多,抗蚀性就愈差。
浅谈梯形螺纹车削

梯 形 螺 纹 是 应 用 广 泛 的传 动 螺 纹 , 因 此 技 工 学 校 教 学
五 、梯 形 螺 纹 车 削 方 法
车 削 梯 形 螺 纹 加 工 难 度 大 。 除与 车三 角 螺 纹 类 似 地 按
中车 削 梯 形 螺 纹 的教 学非 常 重 要 。 车 削梯 形螺 纹 时 走 刀 快 , 吃 刀 深 ,车 削 余 量 大 , 车 削 时 易 扎 车 , 难 度 较 大 , 因此 , 在 车 削梯 形 螺 纹 教 学 过 程 中 ,教 师 要注 意 使 学 生 掌 握 车 削
A P P L I C A T I O N l 技术与应用
浅谈梯形螺纹车削
文/ 梁 云 摘来自要 :梯 形螺 纹 是 应 用 广 泛 的传 动 螺 纹 , 用 以传 递 准确 的 运 动 和动 力 。 因此 ,技 工 学校 实 习教 学 中车 削梯 形 螺纹 的
教 学 ,在 生产 实践 和技 能训 练 上 都非 常重要 。
台阶车 好 。 车刀 移 向左 侧 面 台阶 车好 ,再用 直 进 法车 削牙 型
三 、梯 形 螺 纹 车 刀 的 装 夹
第 一 , 车 刀 主 切 削刃 与 工 件 轴 线 略 高 0 . 1 am, 同 时 应 r 和 工件 轴 线 平 行 。 第 二 , 刀 头 的 角 平 分 线 要 垂 直 于 工 件 轴 线 , 用 样 板 找 正 装 夹 , 以免 产 生 螺纹 半 角 误差 。
第 三 , 刃 磨 两 侧 后 角 时 要 注 意 的左 右 旋 向 ,然 后 根 据
螺 纹 升角 的大 小 来 决定 两 侧 后角 的数 值 。 第 四 ,修 正 刀 尖 后 角 时 ,应 注 意刀 尖 横 刃 宽 度 应 小 于 槽 宽度 。 第 五 ,用 油石 研 去 各 刀 刃 的毛 刺 。
数控车床车削梯形螺纹

数控车床车削梯形螺纹梯形螺纹有低速切削和高速切削两种方法。
(1)低速切削梯形螺纹对精度要求较高的梯形螺纹,以及在修配或单件生产时,常采用低速切削的方法。
当车削螺距较大的梯形螺纹时,为避免三个切削刃同时参与切削而产生振动,应先用粗车刀,采用左右赶刀法的进给方式进行租车。
数控车床厂在保证牙型高度后,再采用精车刀采用直进法进行精加工成形;当螺距很大时,则用径向前角为零、两侧磨有卷屑槽的精车刀,采用左右赶刀的方法精车梯形螺纹。
(2)高速切削梯形螺纹在车削刚度、精度要求不高的梯形螺纹时,可用硬质合金螺纹车刀进行高速切削。
采用这种车刀切削时,由于三个切削刃同时参与切削,会产生带状切屑流出,操作很不安全。
为此,可采用数控车床厂螺纹车刀。
这种螺纹车刀在前面磨出对称的两个圆弧,使径向前角y。
增大。
数控车床厂两圆弧还使前刀面呈3。
~5。
的屋脊状结构。
这种车刀可减小切削力,增加了车刀的强度,从而减轻了切削振动。
数控车床厂同时形成球状切屑,使排屑顺畅。
可以用G76或G92编程,螺距大的螺纹采取左右进刀法车削比较好。
先用G76车,G76 P0100**(**为梯形螺纹牙型角)Q150 R0.03;G76 X Z P Q R F ;(第一行可以套用,Q是每次吃刀量,单位微米。
R是精车余量,半径值)(第二行:X、Z是目标点坐标,P是牙型高,Q是第一刀的吃刀量,R是锥螺纹编程的螺纹起点与终点的半径差(直螺纹不用),F是螺距。
)大螺距螺纹用G76粗车过之后,留点余量用G92车效果好点,车削起点不要变化。
先走一刀G92 X Z F ;,然后起点分别往左边和右边偏0.01或0.02毫米再走第二刀和第三刀。
如M100X4的螺纹长度50T0101M3S500M8G0X105.Z2.G92X99.Z-50.F2.X98.5X98.X97.5X97.X96.5X96.1X96.也就是车床的左右借刀法程序没什么特殊的,主要就是你的起刀点的位置变化,比如开粗的起点为X60 Z3 先车到底径或留点精光一刀(刀要小于30度要么用槽刀)那么第二把刀(30度但刀头是比标准的小的好像是0.366*螺距)。
浅谈车削梯形外螺纹的加工方法

浅谈车削梯形外螺纹的加工方法车削梯形外螺纹是机械制造中常见的一种加工方法,其具有许多特点和应用场景。
本文以梯形外螺纹的加工方法为主题,进行详细论述。
一、梯形外螺纹的基本概念和特点梯形外螺纹是一种具有梯形截面的螺纹,其形状类似于房子的楼梯,因此称为梯形螺纹。
梯形外螺纹具有以下几个基本特点:1. 梯形外螺纹的螺距是固定的,即单位长度上的螺纹齿数是固定的。
2. 梯形外螺纹的截面形状为梯形,其螺纹角度相对于齿距较小,通常为30度或45度。
3. 梯形外螺纹具有较高的强度和刚性,适用于承受较大的力矩和挤压力的场合。
4. 梯形外螺纹的加工精度要求较高,通常需要进行高精度的车削和螺纹度量。
二、梯形外螺纹的加工方法梯形外螺纹的加工主要有以下几种方法:1. 传统车削法:传统车削法是最常用的梯形外螺纹加工方法之一。
该方法使用梯形车刀进行车削,根据预定的工艺参数进行加工,如进给速度、车刀刀具角度等。
这种方法适用于小批量和单件生产,但加工效率较低。
2. 插刀车削法:插刀车削法是一种高效的梯形外螺纹加工方法。
该方法使用高速车刀进行插刀车削,具有较高的生产效率和加工精度。
插刀车削法适用于大批量生产,且要求加工精度较高的情况。
3. 加工中心车削法:加工中心车削法是一种在加工中心上进行梯形外螺纹加工的方法。
该方法使用加工中心的刀具库进行车削,可以实现多轴同时加工和自动换刀,大大提高了生产效率。
加工中心车削法适用于大批量生产和要求高精度的情况。
4. 车铣结合法:车铣结合法是一种综合利用车床和铣床进行梯形外螺纹加工的方法。
该方法先进行车削,然后通过铣床进行梯形外螺纹的修整和后续加工。
车铣结合法适用于单件和小批量生产,同时具有较高的加工精度和效率。
三、梯形外螺纹加工的工艺要点在梯形外螺纹的加工过程中,需要注意以下几个工艺要点:1. 选择合适的车刀和切削参数:根据加工材料和尺寸要求选择合适的车刀,并设置合理的切削参数,如切削速度、进给速度和切削深度等。
浅谈普通车床低速车削梯形螺纹方法的改进
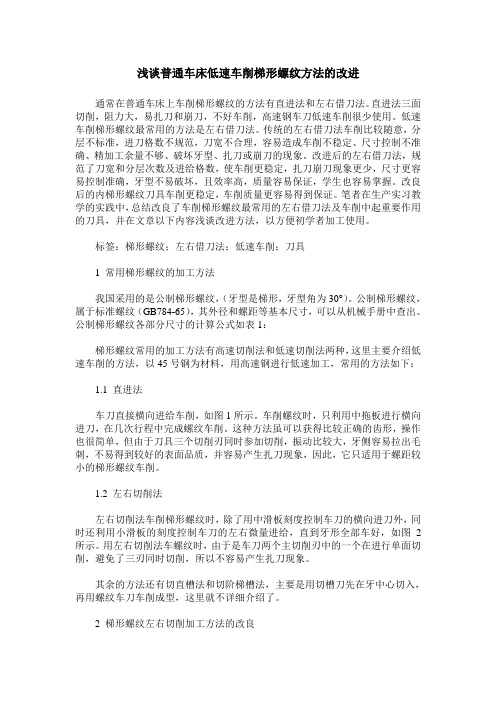
浅谈普通车床低速车削梯形螺纹方法的改进通常在普通车床上车削梯形螺纹的方法有直进法和左右借刀法。
直进法三面切削,阻力大,易扎刀和崩刀,不好车削,高速钢车刀低速车削很少使用。
低速车削梯形螺纹最常用的方法是左右借刀法。
传统的左右借刀法车削比较随意,分层不标准,进刀格数不规范,刀宽不合理,容易造成车削不稳定、尺寸控制不准确、精加工余量不够、破坏牙型、扎刀或崩刀的现象。
改进后的左右借刀法,规范了刀宽和分层次数及进给格数,使车削更稳定,扎刀崩刀现象更少,尺寸更容易控制准确,牙型不易破坏,且效率高,质量容易保证,学生也容易掌握。
改良后的内梯形螺纹刀具车削更稳定,车削质量更容易得到保证。
笔者在生产实习教学的实践中,总结改良了车削梯形螺纹最常用的左右借刀法及车削中起重要作用的刀具,并在文章以下内容浅谈改进方法,以方便初学者加工使用。
标签:梯形螺纹;左右借刀法;低速车削;刀具1 常用梯形螺纹的加工方法我国采用的是公制梯形螺纹,(牙型是梯形,牙型角为30°)。
公制梯形螺纹,属于标准螺纹(GB784-65),其外径和螺距等基本尺寸,可以从机械手册中查出。
公制梯形螺纹各部分尺寸的计算公式如表1:梯形螺纹常用的加工方法有高速切削法和低速切削法两种,这里主要介绍低速车削的方法,以45号钢为材料,用高速钢进行低速加工,常用的方法如下:1.1 直进法车刀直接横向进给车削,如图1所示。
车削螺纹时,只利用中拖板进行横向进刀,在几次行程中完成螺纹车削。
这种方法虽可以获得比较正确的齿形,操作也很简单,但由于刀具三个切削刃同时参加切削,振动比较大,牙侧容易拉出毛刺,不易得到较好的表面品质,并容易产生扎刀现象,因此,它只适用于螺距较小的梯形螺纹车削。
1.2 左右切削法左右切削法车削梯形螺纹时,除了用中滑板刻度控制车刀的横向进刀外,同时还利用小滑板的刻度控制车刀的左右微量进给,直到牙形全部车好,如图2所示。
用左右切削法车螺纹时,由于是车刀两个主切削刃中的一个在进行单面切削,避免了三刃同时切削,所以不容易产生扎刀现象。
浅谈左右车削法车梯形螺纹的一些技法

为例 ) 。下图为高速钢右旋梯形螺纹精车刀 。为保证 牙型角正 确 ,两侧切削刃之间的夹角略大 于牙 型角 ,刀头宽度仍可略 小于牙槽底宽 ,以利于两侧 面的加工 ,并保证两侧面 的表面 表糙度达到要求 ,三处后角均可略取 大 OO 8 、 OO > 。 r : 。 r 5 . .
中外表 t研 宄
◇20年l月 第l期 ◇ 08 1 1
浅谈左 右车削法车梯形螺纹的一些技法
马 利 湖南省 长沙县职业 中专学校
【 要】 摘 梯形螺纹的车削不管是在生产实践 中,还是在技 能训练模块 中,是非常重要 的。本文就梯形螺纹 车削过程 中车 刀的刃磨 要求 、 工件 的装夹以及车 削时如何利用梯形螺纹 的计算公式从 数学方面来保证粗加工余量的快速 去除和精加工余量 的
有效预 留,从 而达到高效、稳定地车 削梯形螺纹 。 【 关键词 】左右车 削法 车梯形螺纹 技法
梯形螺纹一般作传动用 ,用 以传递准确的运动和动力 , 所以精度要求 比较高 ,例如车床上的长丝杠和 中、小滑板的 丝杆 等 ,而且 其精度直接影响传动精度和被加工零件的尺寸 精度。梯形 螺纹 的工件不仅广泛 的被用在各种机床上 ,而且
在每年毕业生应会考试 中多有梯形螺纹车削这一 内容 , 因此 , 梯形 螺纹 的车削已成为职业 中专学校车工专业学生必须掌握 的一个非常重要的模块 。很多操作者都是 因为无法快速的去 除粗加工余量和将精加工余量 留得过多或过少 ,导致加工速 度太慢或将工件报废 。笔者结合多年实习教学经验 ,在此谈 谈左右车削法车削梯形 螺纹 时的几点心得体会 。
进行 比较 。现 以车 T 3 6— h螺纹来介绍我是如何指导学 r2 7 X
对梯形螺纹车削的心理感悟

对梯形螺纹车削的心理感悟车工专业有许多基础课题,但对我们来说,不学螺纹就等于没学车工,可见螺纹这一章节在整个车工实习教学中的重要性。
而螺纹车削中的梯形螺纹车削无疑又是一个重要课题。
三角形螺纹车削是基础,但要达到熟练程度以及对整个车削的掌握,还在于是否掌握好梯形螺纹的车削。
车刀的刃磨摆在首位。
当然仍然采用高速钢车刀,但就其角度的变化程度较三角螺纹明显了许多。
因为从螺距的区别上就是一个明证。
角度的变化主要体现在两个工作后角上。
如双头梯牙,其变化则更大,但这种变化要体现其原则:在保证后角正确的基础上,尽量增大其刚性。
否则在车削过程中,如刚性不足,则会影响其正常车削,甚至导致断裂。
因此,授课时要讲清,事实上总的刀头面积不会变多少。
学生对于确认两个工作后角的大小要有一个明确的概念。
螺纹车得好坏与熟练程度,就看是你在车削过程中对左右切削法的运用了。
不错,车削过程的顺利与否,就在于对其的自如运用。
应该说,在三角螺纹的车削过程中,左右切削法运用不是很明显,很多学生未必掌握。
但是,随着梯形螺纹是车削,螺距的加大,切削面积增大,此时必须交代学生,要运用左右切削法了,否则螺纹肯定车不下去。
如何运用呢?有什么条件吗?如车刀承受力较大,加注冷切液直冒蓝烟,产生积屑瘤,切屑较难排出等等,以上只是一系列的危险信号,但我们何必要等到这一刻呢?也许当你等到这一刻时,车刀就有断裂的危险或产生扎刀了。
文无定法,虽然是机械,但螺纹车削是一个过程,在这一过程中,你却可以随意自如。
我们明白:左右借刀,其宗旨是避免两个主刀刃同时切削,达到省力与车削顺利,以及粗糙的要求等。
事实我们告诉学生可以说,当一开始车削,左右借刀也就可以开始了。
但不管如何借刀,运用哪种方法,始终要注意牙顶宽的变化。
如6mm螺距的梯形螺纹,即在精车之前,要有大于2.2mm的余量。
方法是辅助,达到车削的精度是最终目的。
刚才说,达到车削的精度是最终目的,梯形螺纹较规范,精密检测螺纹中径应该是运用三针测量法。
浅谈车削梯形外螺纹的加工方法

浅谈车削梯形外螺纹的加工方法车削梯形外螺纹是机械制造中比较常见的加工形式,其主要用途在于连接螺纹配合部件,以满足机械传动和固定定位的需求。
下面将着重介绍梯形外螺纹的加工方法及其注意事项。
1. 数控车床加工数控车床相对于传统车床具有更高的精度和效率,因此在梯形外螺纹的加工中,数控车床得到了广泛的应用。
数控车床的加工方式分为两种:一种是精确砂轮修整法,另一种是通用切削法。
精确砂轮修整法需要通过数控机床的轴向和径向来进行,其主要作用是通过旋转和修整砂轮,使其精确地削除工件表面材料,以达到研磨和研磨的要求。
通用切削法主要用于梯形外螺纹的初步加工,它是通过刀具的旋转和移动来进行的。
在进行加工时,刀具必须保持在完全垂直于工件表面的位置,以减少误差和提高加工效率。
此外,应该注意的是,切削时要注意切削深度,如不当调整,会影响加工速率和质量。
2. 其他加工方式除了数控车床外,还可以采用滚压加工和模具切削加工。
滚压加工的原理是使用特殊的滚轮,并将其沿着螺纹轴线滚动,使工件表面上的金属流动进入螺纹凸起部分,从而达到加工的目的。
模具切削加工是通过将模具固定在车床上,然后拉动工件,以梯形螺纹的方式加工。
3. 加工注意事项(1) 螺纹公差要求高,所以在加工前必须仔细检查车床的各项参数,确保其能够满足加工的精度。
在进行加工时,要注意刀具的清洁和切削速度的控制,以减少误差和提高加工效率。
(2) 在加工过程中,应该注意每次加工深度的大小,以避免压力过大而导致空隙,同时,还要注意切削润滑剂的使用,以减少磨损和延长刀具使用寿命。
(3) 在加工中如果发现车床或切削工具有移动或在切削前有松动等情况,应及时停车排查并调整,以保证加工质量和效率。
总之,梯形外螺纹的加工方法因加工对象的不同而各有不同,但是无论采用哪种方式,准确的加工技术和仔细的操作都是保证加工成品质量的关键。
梯形螺纹的加工工艺与分析

梯形螺纹的加工工艺与分析梯形螺纹是一种常见的螺纹形式,广泛应用于各个工业领域。
梯形螺纹的加工工艺与分析对于保证螺纹质量和提高加工效率至关重要。
本文将从梯形螺纹的特点、加工工艺和分析等方面进行详细阐述。
首先,梯形螺纹的特点是螺纹高度大于或等于螺距,螺纹侧面倾斜角度一般为30度。
梯形螺纹的形状复杂,加工难度相对较大。
梯形螺纹一般分为外螺纹和内螺纹两种形式,加工工艺略有不同。
外螺纹的加工通常包括车削和磨削两个过程。
车削是主要的加工方法,适用于粗加工和半精加工。
在车削过程中,应注意刀具的选择和切削参数的合理设置,以保证螺纹的精度和表面质量。
对于一些较高要求的外螺纹加工,还可以采用磨削方法。
磨削可以提高螺纹的精度和表面质量,但是工艺过程复杂,成本较高。
内螺纹的加工通常使用攻丝刀进行。
攻丝刀一般由带有螺纹刀齿的刀片和攻丝杆组成。
加工内螺纹时,首先选择合适的攻丝刀,根据螺纹参数和材料性质确定切削速度和进给量。
攻丝刀通过旋转和推进的方式加工内螺纹,具有加工效率高和精度好的优点。
然而,攻丝刀的刀具寿命有限,需定期更换或修磨。
在梯形螺纹的加工过程中,应注意以下几个方面的问题。
首先,切削力对加工过程和刀具寿命有重要影响。
切削力的大小与材料的性质、切削方式和切削参数等因素密切相关。
合理控制切削力可以提高加工效率和保证产品质量。
其次,表面质量和精度是评价螺纹加工是否合格的重要指标。
加工过程中要注意刀具的选择和切削参数的合理设置,以提高表面质量和精度。
最后,加工过程中的冷却润滑剂的选择和使用是关键。
适当的冷却润滑可以减小切削热对刀具和工件的损伤,同时也有助于提高切削效率。
总结起来,梯形螺纹的加工工艺与分析对于保证产品质量和提高加工效率具有重要意义。
需要根据不同的螺纹形式和加工要求,选择合适的加工方法和切削参数,以确保螺纹的精度和表面质量。
此外,还需要注意切削力和冷却润滑剂的影响,以保证加工过程的稳定性和刀具的寿命。
通过科学合理的加工工艺和分析,可以提高梯形螺纹的加工质量和效率,满足不同应用领域的需求。
浅谈梯形螺纹的切削

浅谈梯形螺纹的切削梯形螺纹的加工是技工学校车工专业实习课的重要课题之一。
在教学中我们常用的加工方法有两种,一是先用刀头宽度稍小于槽底宽的切槽刀以直进法车到槽底,再用成形刀加工成型,这种方法多用于加工螺距较大的螺纹;一是左右切削法,即左右交替斜向进给,这种方法适用于车削螺距小于8mm的梯形螺纹。
根据教学大纲的要求,我们经常要练习的是车削螺距为6mm的梯形螺纹,螺纹的槽底宽度仅为1.93mm,也就是说梯形螺纹车刀的刀头宽度必须小于1.93mm。
采用整体车刀低速左右切削的加工方法,在实际的教学中容易产生以下一些问题:(1)用左右切削法加工,小拖板需左右频繁地交替移动,很不方便,而且,对于初学的学生来说,由于小拖板间隙的存在,小拖板左右的移动量也不易控制。
(2)采用这种方法时,小拖板的移动量不能过大,如果稍大一点,就易将牙顶带起一块,形成烂牙。
(3)随着螺纹切削深度的逐渐增强,刀刃与工件的接触长度也不断增加,小拖板的移动量稍大一点,就易产生扎刀现象,甚至打刀。
如果能在粗车时采用较大的切削用量而不产生烂牙或扎刀现象,学生又能够容易接受,那么车削梯形螺纹的速度就会得到提高,教学效果就会更好,尤其是现在对中级车工的要求是能够车削多头螺纹,因而提高车削螺纹的速度也就显得很有必要。
本着这种思路,我在实际的教学中采取了以下方法:一是用成型刀(刀头宽度小于螺纹槽底宽度约0.4 mm左右)先在槽的两端(亦即在牙顶两侧)车出约0.5mm的浅槽,将槽宽划出(亦即将牙顶划出)并留余量。
这样,解决了小拖板的移动量不能过大的问题,解决了烂牙现象。
二是采用对刀、分层切削的方法。
既将槽宽划出后,将车刀对在槽的中间(由于“对刀”在车削三角螺纹课题时已经学过,所以学生比较容易掌握),进给中拖板车第一刀(中拖板的进给量可达1mm到1.5mm);然后,中拖板不动,小拖板向前进给,进给量可达到螺纹的左侧面,车第二刀;之后,小拖板向后对刀、向后进给,进给量可达到螺纹的右侧面,车第三刀。
梯形螺纹的加工及问题处理
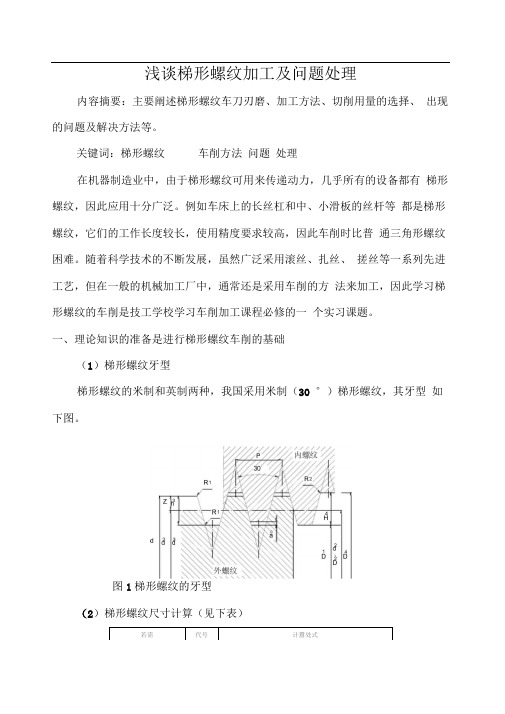
浅谈梯形螺纹加工及问题处理内容摘要:主要阐述梯形螺纹车刀刃磨、加工方法、切削用量的选择、出现的问题及解决方法等。
关键词:梯形螺纹车削方法问题处理在机器制造业中,由于梯形螺纹可用来传递动力,几乎所有的设备都有梯形螺纹,因此应用十分广泛。
例如车床上的长丝杠和中、小滑板的丝杆等都是梯形螺纹,它们的工作长度较长,使用精度要求较高,因此车削时比普通三角形螺纹困难。
随着科学技术的不断发展,虽然广泛采用滚丝、扎丝、搓丝等一系列先进工艺,但在一般的机械加工厂中,通常还是采用车削的方法来加工,因此学习梯形螺纹的车削是技工学校学习车削加工课程必修的一个实习课题。
一、理论知识的准备是进行梯形螺纹车削的基础(1)梯形螺纹牙型梯形螺纹的米制和英制两种,我国采用米制(30 °)梯形螺纹,其牙型如下图。
图1梯形螺纹的牙型(2)梯形螺纹尺寸计算(见下表)(3)梯形螺纹标记梯形螺纹标记由梯形螺纹代号,公差带代号和旋合长度代号组成。
梯形螺纹代号为Tr,单线螺纹用“公称直径x螺距”,多线螺纹用“公称直径x导程(螺距)”表示,左旋时加注LH。
公差带代号只标注中径公差带代号。
当旋长度为N组时,不标注旋合长度代号;当旋合长度为L组时,标注L,并用“-”隔开。
例如:Tr40x7-7H表示公称直径为40mm螺距为7mm中径公差为7H中等旋合长度的右旋梯形内螺纹。
又如:Tr40x14(p7) LH-7e-L表示公称直径为40mm导程为14 mm螺距为7mm中径公差为7e、长旋合长度的左旋梯形外螺纹。
再如:Tr40x7-7e-140表示公称直径为40mm螺距为7mm中径公差为7e、旋合长度为140mm的右旋梯形外螺纹。
二、梯形螺纹车刀的准备是进行梯形螺纹车削的前提梯形螺纹车刀的材料的工作一般包括车刀材料的选择和刀具刃磨等几个 方面的内容,在进行车刀准备时我们应注意以下几个方面的问题:(一)梯形螺纹车刀的材料的选择。
车刀材料的选择是否合理,对车削效率和加工质量有较大的影响。
- 1、下载文档前请自行甄别文档内容的完整性,平台不提供额外的编辑、内容补充、找答案等附加服务。
- 2、"仅部分预览"的文档,不可在线预览部分如存在完整性等问题,可反馈申请退款(可完整预览的文档不适用该条件!)。
- 3、如文档侵犯您的权益,请联系客服反馈,我们会尽快为您处理(人工客服工作时间:9:00-18:30)。
梯形螺纹的车削浅析
作者:袁成照
来源:《信息技术时代·下旬刊》2018年第03期
摘要:梯形螺纹牙型为等腰梯形,牙型角为30度,内外螺纹以锥面贴紧不易松动,工艺较好,牙根强度高,对中性好,主要用于传动螺纹。
在生产实践中梯形螺纹的车削是相当复杂的,车削过程中不可仅仅应用一种方法去车削,而应融会贯通,因此学生只有掌握和熟练了各种车削方法,才能在车削过程中灵活运用,高效率、高精度、高品质地完成梯形螺纹车削。
关键词:“直进法”;“左右进刀切削法”;三针测量
梯形螺纹的工件不仅广泛的被用在各种机床上,其螺距和牙型都大,而且精度高,牙型两侧面表面粗糙度值较小,致使梯形螺纹车削时,吃刀深,走刀快,切削余量大,切削抗力大。
这就导致了梯形螺纹的车削加工难度较大,学生在车工技能培训中难于掌握,容易产生扎刀现象,进而使学生对此产生紧张和畏惧的心理,很多操作者都是因为无法快速的去除粗加工余量和将精加工余量留得过多或过少,导致加工速度太慢或将工件报废。
在多年的车工实习教学中,通过不断的摸索、总结、完善,对于梯形螺纹的车削也有了一定的认知,,在此谈谈车削梯形螺纹时的几点心得体会。
我们在车削梯形螺纹时,常用的是“直进法”“斜进法”和“左右进刀切削法”,“直进法”一般适用于螺距小于4mm或精度要求不高的工件,“斜进法” 和“左右进刀切削法”一般适用于螺距大于4mm或精度要求高的梯形螺纹。
学生练习时,先练习车P=2.5的三角螺纹,采用的是直进法车削,最后练习车P=6的梯形螺纹,采用的是左右车削法,方便学生进行比较。
现以车Tr42×6-7h螺纹来介绍我是如何指导学生用左右车削法车削梯形螺纹的。
1.将螺纹大径(略小0.15左右)和两端倒角(2X15°)车好,然后将梯形螺纹粗车刀对到工件外圆上,将中滑板调至零位,同时小滑板朝前进方向消除间隙后对零。
此举目的是方便学生记住刻度,不易出错。
2.以直进法车螺纹。
由于粗车刀刃磨得锋利又耐用,可加大切削深度。
如Tr42×6的螺纹,螺纹牙型高度h3=0.5P+ac ,Ac为间隙量取0.5mm,牙高h3=0.5P+ac=0.5x6+0.5=
3.5mm;直径方向为7mm,可第一刀进1.5mm,第二刀1mm,第三刀0.5mm,共计3mm(此时因刀具三刃受力,难以继续采用大切削深度的直进法车削,如继续切削则会产生卡刀现象,开始使用左右借刀法)。
如图所示:
3.用游标卡尺测量此时牙顶宽,将测量牙顶宽减去理论牙顶宽(W=2.196≈2.2),再减去所留两侧精车余量(0.2~0.4左右,精车余量以两侧面表面粗糙情况而定,表面光洁时取
0.2mm,表面粗糙时取0.4mm),这就是借刀的余量,将这个余量除以2,就是每侧借刀的量。
例如:我现测得牙顶宽为4.4mm,则我应向左边借刀的量是[(4.4-2.2)-0.3]/2=0.95mm。
当我仍以进刀深度为3mm,向左借刀量为0.95mm车时,梯形螺纹刀只有左侧刃在切削,这个时候只有2条切削刃在受力,切削力不會太大。
车完左边借刀的一刀,将小滑板先退后进(消除空行程)对应地在零线右边借刀0.95mm车一刀(也可分两至三刀将借刀量0.95车完),如下图a。
车完后将小滑板再次对零。
此时刀具就落在车宽了的槽中间,如下图b。
4.再以直进法车螺纹,由于刀头宽度1.5
5.最后又以直进法车螺纹。
第一刀进刀深度为0.5mm,第二刀0.3mm,第三刀0.2mm,第四刀0.1mm。
经过2、3、4、5步的车削螺纹共车深7mm,然后如4步将左侧面借刀至整个侧面车起,同样再将右侧面减刀车起,至此粗车完成。
6.换上螺纹精车刀,将它在螺纹大径上对刀,并将中滑板刻度盘对零。
由于精车刀刀头宽度仍小于牙槽底宽,故精车刀可落到槽底,目测使精车刀处于槽中间,看此时刻度盘值,然后以每次进刀0.1~0.2mm,将总进刀深度车至7~
7.4mm(因应车深度为牙高3.5mm,大径小径偏差0~0.419mm,二者之和7+(0~0.419)=(7-7.4)mm),而粗车时已车切削深度
7.0mm,,故实际只需进刀0.1~0.2mm。
当牙底车起车平后,又向左侧赶刀,每次0.1~
0.05mm,至将左侧面全部车起、车平,然后以低速进0.02mm或走空刀(中、小滑板均不进刀),将左侧车至光洁度达到要求,再将螺纹刀直接退至右边车右侧面,每车一刀就用游标卡尺量一量牙顶宽,当牙顶宽接近2.2mm时,再用三针测量其M值。
当M值合格时,螺纹中径即合格。
7.至此梯形螺纹加工完毕。
在整个加工过程中,粗加工大约用16~24刀,约需时间15分钟左右,精加工8~12刀左右。
同样约需15分钟(包含测量的时间),而且由于每次车削参加切削的刃不太长,所受的切削力不太大,故切削过程平稳,不会出现扎刀的现象,更不会打刀。
从而保证车梯形螺纹的快速和稳定。
总之,在实践教学中,“左右切削法”这种易懂、易掌握的车削梯形螺纹方法,得到了充分地肯定和好评。
教师能够较形象、较直观地把车削方法讲解和传授给学生,学生普遍也能够较快、较容易地理解和掌握这种车削方法,大大降低了梯形螺纹车削这一课题的教学难度和强度。
但在生产实践中梯形螺纹的车削是相当复杂的,车削过程中不可仅仅应用一种方法去车削,而应融会贯通,因此学生只有掌握和熟练了各种车削方法,才能在车削过程中灵活运用,高效率、高精度、高品质地完成梯形螺纹车削。