SMT撞件之模式分析
SMT不良定义及不良品判断 [兼容模式]
![SMT不良定义及不良品判断 [兼容模式]](https://img.taocdn.com/s3/m/46d07c4dcf84b9d528ea7aca.png)
脚变形
脚变形:来料或制程中引起的引脚变形而导致智短路一般出现于有引脚IC
深圳创维数字技术股份有限公司
AI/SMT生产部
PCB露铜
假性露铜,线路表面有线油复 蓋,未有祼露,多出现于线路拐 弯处
露铜,线路祼露,此不良如 遇锡珠等导体,则会造成短路。
OK
NG
深圳创维数字技术股份有限公司
AI/SMT生产部
深圳创维数字技术股份有限公司
AI/SMT生产部
空 焊
空焊:泛指一切引肢或电极与盘水有有效焊接及接触之不良,我们一般 将其分为无锡空焊,少锡空焊,浮高空焊三类
深圳创维数字技术股份有限公司
AI/SMT生产部
浮 高
浮高:由于贴装不当,而导致元件浮起,此类不良在CHIP元件上一般 不影响功能,在CONN上可能会影响整机的组装。
深圳创维数字技术股份有限公司
AI/SMT生产部
锡 珠
深圳创维数字技术股份有限公司
AI/SMT生产部
偏 移
偏移:由于贴装不当,而导致元件偏离PAD的正确贴装位置,严重者 可导致与其它元件短路或完全偏离PAD而致开路。
深圳创维数字技术股份有限公司
AI/SMT生产部
偏 移
深圳创维数字技术股份有限公司
AI/SMT生产部
连 锡
连锡:指焊锡导致之PIN间短路,因其连接于元件两PIN之间,故称之连锡, 导致因素一般认为与锡膏印刷,钢网开孔所造成之多锡或回焊有关,此外PCB 防焊层及印刷不良擦拭亦有一定影响。
深圳创维数字技术股份有限公司
AIБайду номын сангаасSMT生产部
连 锡
深圳创维数字技术股份有限公司
AI/SMT生产部
深圳创维数字技术股份有限公司
SMT失效模式分析PFMEA

O过
现行探测 过程控制
3
执行“先出先消耗”原则
探 风险 测数 度 D RPN
2 18
该区环境湿 度过大
PCB、IC等 返潮,影响
焊接品质
4 4
1、空调性能下降
5
2、空调性能下降,该区管 理员未及时点检
5
及时反馈空调维修员
将裸露MSD置于恒温恒湿的干燥箱 内;对环境温湿度定期点检/监控
4 80 2 40
要求
潜在
过程 功能
失效模式
物料包装带
折痕数过多
潜在 失效后果
贴片时: 物料抛损
少件
严 重分 度类 S
潜在失效 起因/机理
4 2、作业员点料时折出
烘烤时间 过长
烘烤时间 过短
PCB、IC等 受损,影响 4
产品外观/ 功能 4
PCB、IC等 湿度仍过
3
大,影响焊 接品质 3
烘烤温度 过高
PCB、IC等 4 湿度仍过 大,影响焊 4 接品质 4
锡膏存储温 度过高
缩短锡膏存 箱冷藏性能下降
3
2、锡膏管理员不清楚标准 3
3、锡膏管理员未及时监控 4
及时反馈冰箱维修员
3 36
培训标准:锡膏存储温度在0~10℃ 2 24
点检(1次/2小时)控制在0~10℃
2 32
锡膏存储温 锡膏活性 4
度过低
下降 4
1、锡膏管理员不清楚标准 3 2、锡膏管理员未及时监控 4
N
万用表/电 容表失真
误测,导致 用错料
3
物料测量不 发错料,导 完全 致用错料
5
5
BOM、ECN、 单据等文件
出错
撞件改善报告

4 PDF 檔案以 "PDF 製作工廠" 試用版建立 昳責Ì方昳方止板人人人题撞任此成止規任此方题,禁制
數據收集
目檢及數據收集站別
SMT罩板&目檢(A面)
投入數
不良率
SMT
SMT罩板&目檢(B面)
投入數
不良率
AIห้องสมุดไป่ตู้件前
投入數
不良率
爐后 取板
錫面 檢查
補焊
安裝 散熱片
包裝
錫面檢查 罩板
零件面 檢查
F/T
在線燒錄
ICT
7 PDF 檔案以 "PDF 製作工廠" 試用版建立 香責ÿ方香方止板人人人题撞任此成止規任此方题,禁制
原因分析及改善對策
一 . A面reflow(AOI)后罩板疊板作業 As-is
To-be
2PCS疊板作業
AI
投入數 AI插件后
不良率
DIP裂片前
投入數 不良率
修補段目檢
投入數 不良率
投入數 散熱片
不良率
DIP
ICT、燒錄站
投入數 不良率
F/T后罩板&目檢
投入數 不良率
1500 0
2630 0.42% 2400 0.17% 2600
0 2600 0.19% 2600 0.54% 2600 0.08% 2600 0.23% 2600 0.88%
面。 • 完成時間: 已完成
14 PDF 檔案以 "PDF 製作工廠" 試用版建立 耀
原因分析及改善對策
八.散熱片壓合治具行程修正及導入推垃式:
As-is
SMT过程失效模式分析范例(PFMEA)
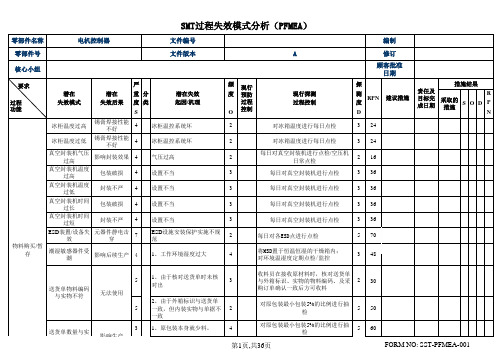
严频探潜在潜在重分潜在失效度现行探测测R 失效模式失效后果度类起因/机理过程控制度PSO DN冰柜温度过高锡膏焊接性能不好4冰柜温控系统坏2对冰箱温度进行每日点检324冰柜温度过低锡膏焊接性能不好4冰柜温控系统坏2对冰箱温度进行每日点检324真空封装机气压过高影响封装效果4气压过高2每日对真空封装机进行点检/空压机日常点检216真空封装机温度过高包装破损4设置不当3每日对真空封装机进行点检336真空封装机温度过低封装不严4设置不当3每日对真空封装机进行点检336真空封装机时间过长包装破损4设置不当3每日对真空封装机进行点检336真空封装机时间过短封装不严4设置不当3每日对真空封装机进行点检336ESD 装置/设备失效元器件静电击穿7ESD 设施安装保护实施不规范2每日对各ESD点进行点检570潮湿敏感器件受潮影响后续生产41、工作环境湿度过大4将MSD置于恒温恒湿的干燥箱内;对环境温湿度定期点检/监控34851、由于核对送货单时未核对出3收料员在接收原材料时,核对送货单与外箱标识、实物的物料编码、及采购订单确认一致后方可收料23052、由于外箱标识与送货单一致,但内装实物与单据不一致2对原包装最小包装5%的比例进行抽检55031、原包装本身就少料。
4对原包装最小包装5%的比例进行抽检560责任及目标完成日期建议措施措施结果DS O 现行预防过程控制无法使用影响生产送货单数量与实物不符物料购买/暂存送货单物料编码与实物不符文件版本A修订SMT过程失效模式分析(PFMEA)零部件名称电机控制器文件编号编制RPN 采取的措施核心小组顾客批准日期零部件号过程功能要求第1页,共36页FORM NO: SST-PFMEA-001等文件出错用错料第3页,共36页FORM NO: SST-PFMEA-00131、烘烤人员不清楚温度标准4培训《MSD管制办法》33632、MSD的标识不清晰2将《SMT MSD干燥记录表》记录清楚21233、未生产而长时间放置3长时间放置的MSD实行真空包装21831、烘烤人员不清楚厚度/间距标准4培训《PCB、IC烘烤作业指导书》33632、烘烤人员因“烤箱空间”不够而随意加厚、加密4严格执行《PCB、IC烘烤作业指导书》33631、烘烤人员不清楚裸露时间标准4培训《PCB、IC烘烤作业指导书》33632、烘烤人员未执行“先出先消耗”的原则3执行“先出先消耗”原则21841、空调性能下降5及时反馈空调维修员48042、空调性能下降,该区管理员未及时点检5将裸露MSD置于恒温恒湿的干燥箱内;对环境温湿度定期点检/监控24041、冰箱冷藏性能下降3及时反馈冰箱维修员33642、锡膏管理员不清楚标准3培训标准:锡膏存储温度在0~10℃22443、锡膏管理员未及时监控4点检(1次/2小时)控制在0~10℃23241、锡膏管理员不清楚标准3培训标准:锡膏存储温度在0~10℃22442、锡膏管理员未及时监控4点检(1次/2小时)控制在0~10℃23241、锡膏进料后的有效期短4检验出厂的瓶身标签:有效期≥6月34842、未执行“先进先出”3标识清晰,执行“先进先出”,严格控制锡膏存储期在6个月内22441、锡膏管理员不清楚标准4培训标准:室温下锡膏回温时间≥4H 23242、管理员控制的起止回温时间不清晰4利用《锡膏使用标识卡》严格记录/管控34843、因"急"而超前使用4“急”则须提前解冻34841、锡膏管理员不清楚标准4培训标准:室温下锡膏回温时间≥4H 23242、回温的起止时间标识不清楚4利用《锡膏使用标识卡》严格记录/管控34843、停产时,未将已解冻品及时回冻4《锡膏使用标识卡》标识清晰,工作环境中未开封放置不能超过24小时232烧录器电压不稳定程序拷贝时出错,影响功能5220V输入电压不稳定2每日对其进行点检44051、硬件、软件运行有误2每日对其画面显示状况进行确认33052、作业员违规操作3按照“PI-150”作业,禁止多余操作345拷贝电脑运行不正常程序拷贝时出错,影响功能锡膏活性下降,导致印刷性能下降锡膏回温解冻时间过长锡膏存储期限过长PCB、IC等返潮,影响焊接品质开封/烘烤后裸露时间过长PCB、IC等返潮,影响焊接品质该区环境湿度过大锡膏活性下降锡膏存储温度过低PCB、IC等湿度仍过大,影响焊接品质锡膏存储温度过高缩短锡膏存储周期,影响焊接品质摆放厚度过厚、间距过小PCB、IC等反潮,影响焊接品质MSD于干燥箱内的时间过长备/领出锡膏变质,影响焊接品质锡膏吸水引起锡珠\气泡\炸锡锡膏回温解冻时间过短第5页,共36页FORM NO: SST-PFMEA-00131、拷贝槽的拷贝脚弹性不够3每日对拷贝脚的完好性进行点检32732、IC的放置不到位3保证作业员将IC脚充分接触到拷贝槽的底部32733、IC脚氧化2发现时,及时反馈IQC63651、软件确认书或效验和或备录忘或ECN/BOM等文件出3对每个工单的首次软件拷贝的IC要求物料房拉长进行首件确认46052、用错软件5对每个工单的首次软件拷贝的IC要求物料房拉长进行首件确认37553、用错IC5对每个工单的首次软件拷贝的IC要求物料房拉长进行首件确认,并使用BOM/ECN核对所拷贝IC实物的正确性37551、作业员不能识别辅料型号/用途3对作业员培训《辅料型号、使用对照表》34552、作业员疏忽3领辅料时,实行两人确认345ESD设施失效静电敏感器件被击穿,功能丢失7ESD设施的安装或保护或实施不规范2每日对各ESD点进行点检57031、作业指导书未制作4及时制作33632、丢失/未悬挂4每日对各工位作业指导书进行点检33631、作业员不能识别Feeder类型2对作业员培训各类机器、Feeder类型的识别方法31832、作业员未掌握物料类型与Feeder类型的匹配方法2对作业员培训各Feeder类型与物料类型匹配的方法31833、作业员疏忽3上料/换料后,对所上Feeder与物料的匹配情况进行两人核对、确认32751、站位表的制作出错31、站位表制作后,实行两人确认2、站位表在上线使用之前,技术员必须用BOM核对站位表是否正确,交助工签名后方可使用34552、拿错站位表4拉长依据客户、机型、程序名领取站位表,与技术员实行两人确认36051、站位表出错3拉长依据客户、机型、程序名领取站位表,与技术员实行两人确认345拷贝槽与IC 的接触不良作业指导书不全不按标准/流程作业,流出不良程序不能拷入,影响功能生产辅料发错用错辅料拷错程序,影响功能/换错物料软件确认书,效验和,备录忘ECN,BOM未核对物料上线物料抛损、影响贴片质量Feeder(类型)使用出错错料站 位 表出错第6页,共36页FORM NO: SST-PFMEA-001清晰第8页,共36页FORM NO: SST-PFMEA-001出。
撞件分析
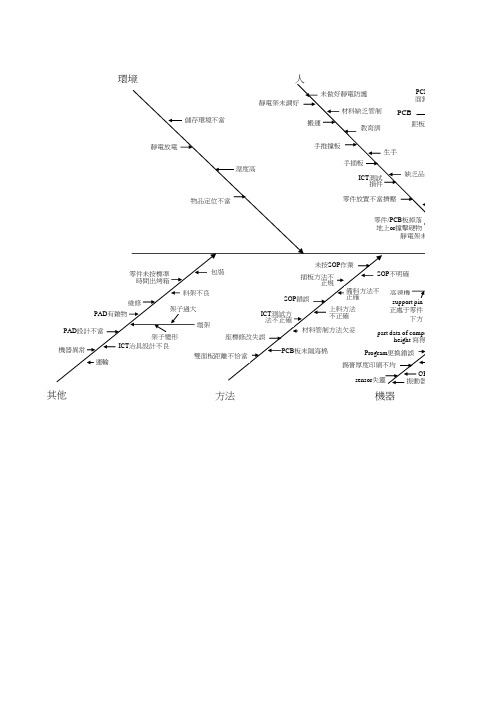
SOP不明確
support
維修
料架不良
SOP錯誤
備料方法不 高速機 正確
support pin
PAD有雜物 PAD設計不當
架子過大
架子變形
塌架
ICT測試方 法不正確
座標修改失誤
上料方法 不正確 材料管制方法欠妥
機器異常
ICT治具設計不良
雙面板距離不恰當
PCB板未隔海棉
正處于零件 下方
part data of component height 寫得太薄
回焊區時 升溫速 多件 間太長 度過快
寫得太薄
板邊壓
住零件 熱沖擊 載板系統調整不當
升溫區時 爐溫過高 間太短
回焊爐
QP242切換nozzle時壓坏 振動器不良
損件
環境
儲存環境不當
人
靜電架未調好
未做好靜電防護
搬運
材料缺乏管制 教育訓
PCB表 面錫珠
PCB 距板邊較近 之零件
靜電放電
溼度高
手推撞板 手插板
生手
設計
ICT測試 損件
缺乏品質意識
物品定位不當
零件放置不當擠壓
零件/PCB板掉落 地上or撞擊硬物
靜電架未調好
未按SOP作業
零件未按標準 時間出烤箱
包裝
插板方法不 正規
撞擊硬物
靜電架未調好
QC撿板 未依標準作業
兩邊開口大 鋼板
張力
support
支撐 支撐pin頂 軌道不平
pin 住反面零
太高 件
Nozzle抓偏
support pin 正處于零件
置件 高度 下壓
吸空料槃 ICT治具
撞件不良解析报告演示文稿

优选撞件不良解析报告
目录
1.工序排布描述 2. SMT撞件不良原因解析 3. AI撞件不良原因解析 4. DIP撞件不良原因解析 5.小结
一、易发生撞件的工序和流程
1. 易发生撞件不良的工序和流程如下:
上板
AI
印刷
板卡周转
转
回流炉后
板
分板
DIP 老化
SMT维修
插件
测 试
DIP补焊撞件不良案例分析:
预防措施: 4.存放或堆积板卡时需使用防静电泡棉板。 5.员工在堆板时,及时放入周转箱,避免堆集在台面上。 6.将流水线线体的护角用防表电皮包裹作防护。 7.用PVC防静电泡棉将流水线的铁边进行包裹。防止拿取板时撞件。 8.生产MS908.PB751F机型时,从炉后开始需要使用黑色周转泡棉进行周转,各工 位作业时,需将泡棉和PCB一起拿取。
DIP撞件形成原因: 1.员工在拿取板时,在流水线上拖板,导致板卡和流水线撞件。 2.在放板时扔板,导致靠近板边的排插或端子损件。
3.员工在堆板时,板卡和板卡之间碰撞导致撞件。
预防措施: 1.此工序撞件主要控制点为员工拿取板的作业方法。 2.对流水线易发生撞件的地方进行防护。
损件部位
七、DIP补焊工序撞件不良解析
增加流水线防护海 棉
板卡存放方式
流水线防护皮
七、DIP补焊工序撞件不良解析
DIP补焊撞件不良案例分析:
预防措施: 9.产线在炉后放板时,采用每格放一片板卡的方式作业。以便控制生产节拍。
流水线上用白色油漆笔画成节拍格, 每格只能放一片PCB,避免叠 板,造成撞件。
七、DIP补焊工序撞件不良解析
DIP补焊撞件不良案例分析:
SMT产品线撞件不良分析与改进措施

113
科技创新导报 2009 NO.16 Science and Technology Innovation Herald S M T 产品线撞件不良分析与改进措施
工 程 技 术
王海明 ( 哈 工 大 华 德 应 用 技 术 学 院 电 子 系 哈尔滨 1 5 0 0 2 5 )
摘 要:本文针对电脑主机板 SMT 生产线出现的撞件不良进行系统的分析和研究,从中发现不良出现的可能原因,针对不同的原因采取相 应的措施, 从而改善不良, 提高生产良率, 增加企业效益。 关键词: S M T 产品撞件 不良分析 改进措施 中图分类号:TP 文献标识码:A 文章编号:1674-098X(2009)06(a)-0112-02
处和 T/U 段之间,目检处因人员在从 AOI 轨 道 中 拿 取 机 板 时 动 作 不 规 范 ,在 放 取 机 板 时 未 能 做 到 轻 拿 轻 放 ,甚 至 有 在 刷 漏 刷 时 ,机 板 在 运 输 途 中 未 能 做 到 按 标 准 拿 取 机 板 ,主 要 为 一 个 托 盘 未 按 三 片 标 准 在 运 输 而 是 多 片 堆 叠 在 一 起 ,加 上 泡 棉 残 缺 很 容易撞件等;T/U 段的人员作业不规范,尤 其是当该站不良超标收箱时人员在装箱的 过程中 TAKE CPU 处的不良主要来源于 各 测 试 段 人 员 的 动 作 不 规 范 所 致 ,如 产 线 F/T 的测试机台主要集中于线体的两侧由 于线体中央有上方平台,F/T 人员在放取 机板的过程中目视不太方便容易导致撞 件;EBT 处的散热片在取放的过程中动作 不当.
撞件分析与改善措施(勿删)
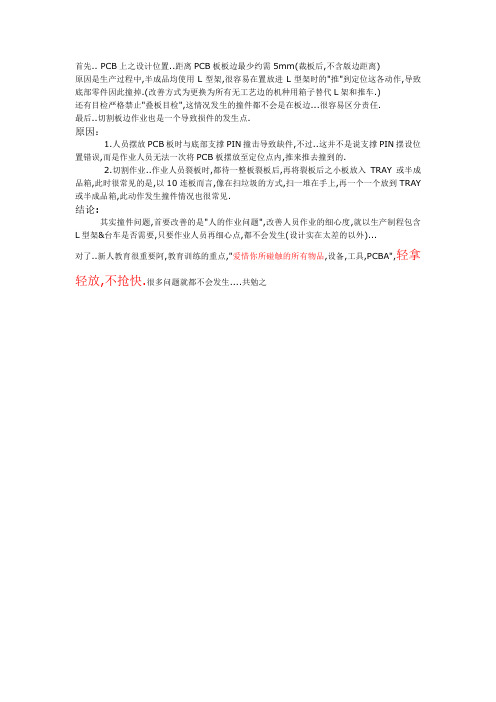
首先.. PCB上之设计位置..距离PCB板板边最少约需5mm(裁板后,不含版边距离)
原因是生产过程中,半成品均使用L型架,很容易在置放进L型架时的"推"到定位这各动作,导致底部零件因此撞掉.(改善方式为更换为所有无工艺边的机种用箱子替代L架和推车.)
还有目检严格禁止"叠板目检",这情况发生的撞件都不会是在板边...很容易区分责任.
最后..切割板边作业也是一个导致损件的发生点.
原因:
1.人员摆放PCB板时与底部支撑PIN撞击导致缺件,不过..这并不是说支撑PIN摆设位置错误,而是作业人员无法一次将PCB板摆放至定位点内,推来推去撞到的.
2.切割作业..作业人员裂板时,都待一整板裂板后,再将裂板后之小板放入TRAY或半成品箱,此时很常见的是,以10连板而言,像在扫垃圾的方式,扫一堆在手上,再一个一个放到TRAY 或半成品箱,此动作发生撞件情况也很常见.
结论:
其实撞件问题,首要改善的是"人的作业问题",改善人员作业的细心度,就以生产制程包含L型架&台车是否需要,只要作业人员再细心点,都不会发生(设计实在太差的以外)...
对了..新人教育很重要阿,教育训练的重点,"爱惜你所碰触的所有物品,设备,工具,PCBA",轻拿轻放,不抢快.很多问题就都不会发生....共勉之。
撞件改善报告

2 PDF 檔案以 "PDF 製作工廠" 試用版建立 题httpy://
專案組織架構
瑞中/樂軒專案組織架構圖:
3 PDF 檔案以 "PDF 製作工廠" 試用版建立 昳責Ì方昳方止板人人人题撞任此成止規任此方题,禁制
撞件執行計劃表:
開始日期:2月19日 撞件驗証選定機種:VP422 384201820150 Main Board
2月19日 0 4 0 0 0 0 0 0 0
PDF 檔案以 "PDF 製作工廠" 試用版建立 f
2月20日 ---0 0 0 0 4 2 1 4
不良數 2月21日
---2 2 0 2 3 0 2 8
2月22日 ---3 0 0 2 2 0 0 6
2月23日 ---2 2 0 1 5 0 3 5
爐后 取板
錫面 檢查
補焊
安裝 散熱片
包裝
錫面檢查 罩板
零件面 檢查
F/T
在線燒錄
ICT
7 PDF 檔案以 "PDF 製作工廠" 試用版建立 香責ÿ方香方止板人人人题撞任此成止規任此方题,禁制
原因分析及改善對策
一 . A面reflow(AOI)后罩板疊板作業 As-is
To-be
2PCS疊板作業
改善項目匯總
撞件改善list一:(舊)
撞件隱患
臨時改善對策
改善單 完成時
位
間
長期改善對策
改善單 位
完成時間
AI操機人員從AI 1.從AI投板入口投板 ,IE加入SOP 機器中間投板 2.生技開啟AI機台安全操作
制造 / 生技動供板
生技
撞件原因分析及对策
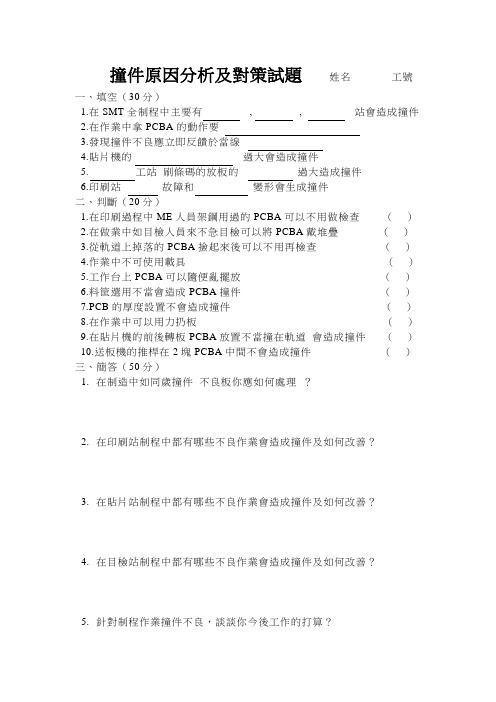
撞件原因分析及對策試題姓名工號
一、填空(30分)
1.在SMT全制程中主要有, , 站會造成撞件
2.在作業中拿PCBA的動作要
3.發現撞件不良應立即反饋於當線
4.貼片機的過大會造成撞件
5. 工站刷條碼的放板的過大造成撞件
6.印刷站故障和變形會生成撞件
二、判斷(20分)
1.在印刷過程中ME人員架鋼用過的PCBA可以不用做檢查()
2.在做業中如目檢人員來不急目檢可以將PCBA戴堆疊()
3.從軌道上掉落的PCBA撿起來後可以不用再檢查()
4.作業中不可使用載具()
5.工作台上PCBA可以隨便亂擺放()
6.料筐選用不當會造成PCBA撞件()
7.PCB的厚度設置不會造成撞件()
8.在作業中可以用力扔板()
9.在貼片機的前後轉板PCBA放置不當撞在軌道會造成撞件()
10.送板機的推桿在2塊PCBA中間不會造成撞件()
三、簡答(50分)
1.在制造中如同歲撞件不良板你應如何處理?
2.在印刷站制程中都有哪些不良作業會造成撞件及如何改善?
3.在貼片站制程中都有哪些不良作業會造成撞件及如何改善?
4.在目檢站制程中都有哪些不良作業會造成撞件及如何改善?
5.針對制程作業撞件不良,談談你今後工作的打算?。
撞件改善

改善对策
问题点:SMT印刷工 位单手拿板,在固定板 和取板时容易造成刮碰 撞件。
改善对策:SMT印刷 工位双手持板边,工艺 在印刷的作业指导书中 明确此要求。
改善对策
问题点:1.SMT外观检 查完成后,装周转架时 方向不统一,有的元件 靠近板边容易撞件。 2.未装入到位。
改善对策:SOP规定 装周转架的方向。
IPQC稽核是否有装入 不到位现象。
改善对策
问题点:SMT外观检 查完成后,装周转架未 间隔,拿取时容易造成 上下两片刮碰。
ቤተ መጻሕፍቲ ባይዱ
改善对策:SMT外观 检查完成后,装周转架 时需要间隔一层,AI的 间隔距离要更大。保证 拿取时上下两层不会刮 碰。
改善对策
取板要 从上到 下
放板要 从下往 上
问题点:取放板的顺序 不正确,容易刮碰撞件。
改善对策:SOP规定 每个工位不可以堆积超 过5PCS.
改善对策
问题点:工位下方放置 工具,容易造成撞件。
改善对策:工具必须放 置于工具盒内不可以随 意摆放。
改善对策
问题点:PCB板随意放 置。
改善对策:对人员进行 宣导,板不可以侧放, 不可以随意放置, IPQC稽核。
改善对策
问题点:流水线上金属 边刮碰。
SMT印刷工位顶PIN设置不合理
方法
机器
SMT DIP 研发
撞件原因汇总
1.印刷工位拿板方式不正确(法) 2.周转工具使用不正确(法) 3.周转架装板方式不正确(法) 4.取放板的顺序不正确(法) 5.SMT周转工具宽度调整不正确(机器) 6.SMT印刷工位顶PIN设置不合理(机器) 1.DIP分板方式不正确 2.DIP投板工位流水拉堆板 3.拉线上使用架桥,有推板现象 4.使用过炉载具的板,在流水拉上装载具 5.取放板的顺序不正确 6.分板后放置层数太多 7.隔板上放置数量太多超边 8.流水线工序间隔条堆板 9.流水线工位堆积 10.工位下方放置工具 11.产品随意摆放 12.流水线金属边刮碰 13.测试治具行程小刮碰 设计不合理
XXX电感撞件调查分析报告

不良品处理过程 中B面电感受力
置件
顶Pin
炉后目检与贴 贴条码过程中B面
条码
电感受力
没有撞件风险 撞件风险1 撞件风险3
现顶Pin设置OK 撞件风险4
装板数量未定义 作业过程中B面没有防
护措施治具
作业过过程中B面没有 防护措施治具
“风险点
与现况数
据统计发
生段”吻 合
维修站
维修过程中B面电 感受力
三、问题查找与风险排除
5. 炉后目检与贴条码:
6. 维修
电感受力被顶
电感受力被顶
员工贴条码过程中 1. 若将板子拿在左手中,同 时右手撕条码贴在板子上, 这样操作较不方便。 2. 若将板子放在轨道旁操作 台上作业,则B面电感正受 力被顶住,易造成零件裂碎。
A面生产过程中,若AOI出现 的不良在维修工位的过程中, 目前是放在一硬静电板上, 在维修过程中易造成零件裂 碎。
XXX PCB撞件起铜皮调查 分析报告
目录
➢ 不良问题描述 ➢ 在线现况数据统计 ➢ 问题调查与风险排除 ➢ 调查分析结论 ➢ 改善措施 ➢ 标准化
一、不良问题描述
✓ 不良现象:测试段在目检站发现不良品过多,不良为主板撞件, 目检650PCS,不良有13PCS,参考如下不良图片 ✓ 不良率:2.0% ✓ 不良位置:电源插座处PCB板边
不良图片1
不良图片2
二、在线现况数据统计
根据生产后段反馈的现象及不良板的确认,针对现SMT正在 生产现场按四个管制点( B面炉后、 B面装周转车后、 A面炉后、 A面装周转车后)进行不良统计收集,具体数据参考如下表:
二、问题查找与风险排除
• 根据生产后段反馈的现象及不良板的确认,针对现SMT正在生 产现场对生产工艺流程中存在的作业风险点进行确认与排除
SMT撞件之模式分析
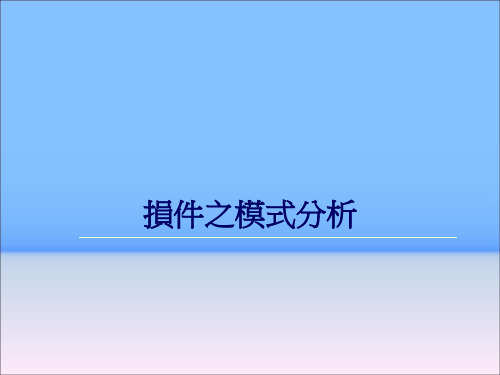
Reflow軌道抖 動,板邊零件受 損 鏈條損壞 頂PIN圖 設計錯誤
頂PIN頂到零 件 頂PIN沒有按照
頂PIN圖放置 吸嘴選用 不合理 置件高度 值過小
人
轉板過程中產 生撞擊跌落 新人上線
Clamp 厚度 使用錯誤 軌道過寬, 吸嘴磨損
DEK CP QP
Reflow
升溫過快造 成零件破損
造成掉板 置件損傷 治具所對應的有 治具壓力不 零件位置無開孔 穩定 : 5-7kg
Wave Solder
T/U
放置NG板時,作業員作業不規範,導致放板時,手中的板撞擊 框中已有的板或者撞擊箱中的隔離板而造成板上零件脫落 或歪曲, 制程改善: 放板時平行放板,避免撞到箱子和其它板子
NG
OK
刷錫珠放板到治具上時,治具頂pin設置與頂pin圖不符造 成撞到正面零件 制程改善: 要求作業員在開線前確認頂pin 圖與治具設定相符.
損件之分類及其典型模式
損件主要分為兩大類:材料問題和作業問題, 具體分類如下: 一.材料問題: 1.元件制程損傷:缺角、畸形、裂痕…
a.元件製程中折條或折粒時,因刀具不良(電容)、或預刻痕不 平均或折斷應力不當(電阻)所造成之缺陷; b.元件製程中各式夾具固定不良損傷(蒸鍍、槽鍍、電極沾錫 夾損); c.測試漏出不良;
電極端剝離
電極端剝離
3.包裝、運輸及儲存:缺角、裂痕、層剝離(濕氣)… a.包裝: 原因:大量零件於封帶機內碰撞擠壓造成磨損、缺角。 特徵:通常在8個角落處較易發生,其破裂通常不會超 過邊 長的1/2,且已具有尖銳粗糙面之特徵。 b.運輸: 原因:因搬運震動或掉落、擠壓而形成(發生機率較小)。 特徵:通常為斷裂式之破裂,發生機率較小且置件機大多可以 篩除。 c.儲存: 原因:濕氣滲入。 特徵:當濕氣滲入層間(電容),如遇熱衝擊時將會導致層分離, 且於其表面或許可見一較深色之水紋狀裂痕。
SMT不良现象要因分析图

MT 不良现象偏移要因分析图
环境因素
人 员
人为碰掉零件
PAD 上有异物
上料
零件不良
预检碰掉零件
顶Pin 孔未清理干净
电极氧化
电极损伤
PCB 不良 PCB 板弯
HMT 漏件
印刷锡膏被擦伤
人为疏忽漏贴
未预告停电
顶Pin 摆放不均衡 顶Pin 高度不良
着装顶Pin 不良
Nozzle 赃污 真空管破损
Nozzle 真空不良 真空电磁阀不良 过滤棉赃污
PCB 推杆碰到零件
轨边不良
轨边不顺畅
装着零件速度太快
吸嘴型号选用不当
Mounting gap 设置不当
装贴偏移
零件坐标不良
材料不良 设备因素
印刷时PAD 上无锡或少锡
工法不良
SMT 缺件不良特性要因分析图
缺 件
SMT 材料不良要因分析图。
电子厂撞件防患控制点集合

Thank you !
篮筐装板时的品质隐患
D I P 要 点
4. 装箱时PCB需垂直放下,不可歪斜。距离较远时需拉近箱 体或调转方向,不可投掷,半空松手。取放板时一只手只能拿 取一块PCBA。
歪斜放入不良
PCB未放入格内松手
单手抓取多块PCB
D I P 要 点
6. 工位堆积大于五块时应装箱处理,堆积过多,推动时易掉板及堆叠碰撞 ,PCB应放于桌面中间位置不可放于拉线金属面上。
SMT撞件控制点
SMT管制要点
板子上车后放置不规范
SMT管制要点
板子装车时要用相应的车子
SMT管制要点
板子装车时的规范要求,不叠板,板子不超出
SMT管制要点
拿取板时是否板边的零件是否被轨道卡到
SMT管制要点
AOI测试的时候要注意卡钩和卡槽是否干涉到板子
SMT管制要点
AOI测试的时卡钩干涉到板子
拉线叠板
D I P 要 点
2.炉后捡板要及时,不可出现两夹具堆叠,过炉夹具 无压扣,下到拉线时有可能PCB与夹具分离造成碰撞 。
D I P 要 点
3. 炉后堆积装箱时需避免,一格放两块及以上 的PCB,底部有元件的板不可平放于箱上。
一格多板
双面板平放
D I P 要 点
炉后板放过密或叠板现象
D I P 要 点
2. 产品放置时要一次到位,不可先入一半,再推动校准。 放板时注意不可下压托板,以致测试针外露,刮到板底, 产品对位需准确无误方可下压,
放置时,未放到位
放置时,下压托板
测试撞件控制点
测 试 站 要 点
5.临时放置及周转箱放置时,需摆放工整,做好标识,不可堆叠。 双面板时不可直接平入于刀卡上,以免造成刮碰。
撞件分析报告

撞件分析报告引言撞件是指两个物体之间发生碰撞时产生的磨损、损坏或形变等现象。
撞件分析报告用于分析撞件事件的原因、影响和解决办法,从而提供有效的决策依据。
本报告将对撞件的影响因素、分析方法以及解决方案进行探讨。
影响因素撞件事件的发生受多种因素的影响,主要包括以下几个方面:车辆速度车辆速度是影响撞件严重程度的重要因素之一。
速度越高,撞击力越大,撞件造成的损坏程度也会更严重。
材料强度撞件的材料强度决定了它对撞击的抵抗能力。
相对脆弱的材料容易在撞击过程中发生破碎或形变,从而导致更严重的损害。
撞击角度撞件的撞击角度会影响撞击后力的传递方式。
撞角越大,撞击力对目标物体造成的影响会更大。
相对速度相对速度是指两个物体在撞击前的相对运动速度。
相对速度越高,撞击力也会增加,从而导致更严重的撞击效果。
分析方法撞件事件的分析通常需要进行实验、数据收集和模拟分析等步骤。
实验通过实验可以获取撞件事件发生时的相关数据,如车辆速度、撞击角度等。
可以通过使用高速摄像机、测力仪等设备来记录实验过程中的数据。
数据收集通过收集现实世界中发生的撞件事件的数据,可以更好地理解撞击过程和后果。
例如,可以收集事故报告、保险索赔数据等。
模拟分析利用现代计算机仿真软件,可以对撞件事件进行模拟分析。
可以通过建立物理模型、设定撞击条件等来模拟真实场景下的撞击情况,从而得出相关的结论。
解决方案针对撞件事件的发生,可以采取以下措施来解决问题:设计改进在产品设计阶段,可以采用更坚固耐用的材料,增加抗撞击能力,降低撞击后的损坏程度。
安全防护装置可以在撞件的关键位置安装安全防护装置,如安全气囊、防撞托盘等,以减轻撞击力和减少损伤。
提高驾驶员素质通过加强驾驶员培训,提高驾驶技术和安全意识,减少交通事故的发生。
总结撞件分析报告对于了解撞件事件的影响因素、分析方法和解决方案具有重要意义。
在未来的撞件预防和安全设计中,应该综合考虑车辆速度、材料强度、撞击角度和相对速度等因素,并采取相应的措施,以减少撞件事件的发生和减轻损伤程度。
分析引起撞件过程的流程图
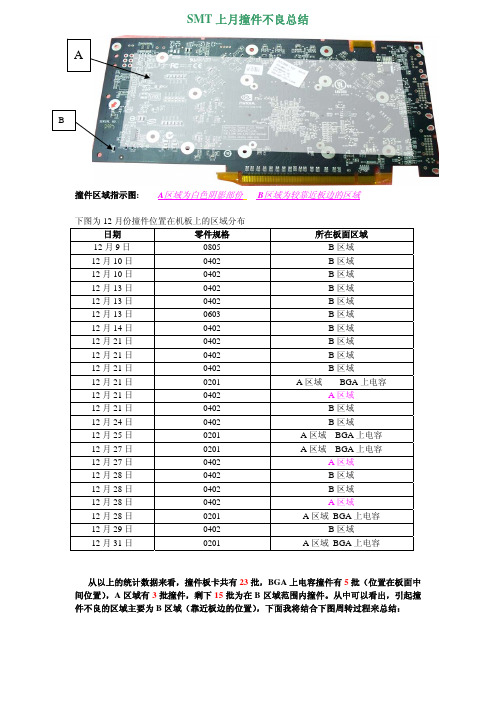
SMT上月撞件不良总结撞件区域指示图:A区域为白色阴影部份 B区域为较靠近板边的区域下图为12月份撞件位置在机板上的区域分布日期零件规格所在板面区域12月9日 0805 B区域12月10日 0402 B区域12月10日 0402 B区域12月13日 0402 B区域12月13日 0402 B区域12月13日 0603 B区域12月14日 0402 B区域12月21日 0402 B区域12月21日 0402 B区域12月21日 0402 B区域12月21日 0201 A区域BGA上电容12月21日 0402 A区域12月21日 0402 B区域12月24日 0402 B区域12月25日 0201 A区域BGA上电容12月27日 0201 A区域BGA上电容12月27日 0402 A区域12月28日 0402 B区域12月28日 0402 B区域12月28日 0402 A区域12月28日 0201 A区域 BGA上电容12月29日 0402 B区域12月31日 0201 A区域 BGA上电容从以上的统计数据来看,撞件板卡共有23批,BGA上电容撞件有5批(位置在板面中间位置),A区域有3批撞件,剩下15批为在B区域范围内撞件。
从中可以看出,引起撞件不良的区域主要为B区域(靠近板边的位置),下面我将结合下图周转过程来总结:下图为SMT过炉后板卡到FQA检验的周转过程:据统计初步认为以下各方面存在撞件的因素项目撞件隐患建议1、炉后捡板a、炉后接板人员接板不及时,造成炉后叠板导致板边撞件。
b、如为铝架过炉,从铝架取板不慎造成撞件a、炉后捡板要及时,避免叠板b、取板要轻拿轻放2、把机板插入静电框的动作从上图可以看出从机板过炉后至FQA检验,插入周转框的次数频繁,如不慎,很容易造成撞到板边零件。
插入机板时要轻且避免碰到别的机板用静电框边3、静电框的搬运从上图看出,静电框的搬运也较频繁,主要分为两种情况:a、人员拿静电框时数量过多,(有时2-3框),容易造成机板倾倒导致撞件.每一次最好是拿一个静电框,用双手拿住框的两边较稳。
- 1、下载文档前请自行甄别文档内容的完整性,平台不提供额外的编辑、内容补充、找答案等附加服务。
- 2、"仅部分预览"的文档,不可在线预览部分如存在完整性等问题,可反馈申请退款(可完整预览的文档不适用该条件!)。
- 3、如文档侵犯您的权益,请联系客服反馈,我们会尽快为您处理(人工客服工作时间:9:00-18:30)。
2.元件製程不良:電極端消失、剝離…
電極端消失
原因:電極處理部分之銀、鎳及錫鉛鍍 層厚度不良,鎳層有缺陷造成銀 浸蝕於錫鉛中形成電極部份或完 全消失(電阻較常見)。(PS.無鉛製 程之電阻改採端電極蒸鍍錫之方 式製成,已無這種現象發現)
原因:同上,但電容材質或多加一層 銅或其他金屬,故多僅有包覆末端之翹 起(剝離)。 原因:應力破壞造成電極端上緣裂痕剝 離。
機
Reflow軌道抖 動,板邊零件受 損 鏈條損壞 頂PIN圖 設計錯誤
頂PIN頂到零 件 頂PIN沒有按照
頂PIN圖放置 吸嘴選用 不合理 置件高度 值過小
人
轉板過程中產 生撞擊跌落 新人上線
Clamp 厚度 使用錯誤 軌道過寬, 吸嘴磨損
DEK CP QP
Reflow
升溫過快造 成零件破損
造成掉板 置件損傷 治具所對應的有 治具壓力不 零件位置無開孔 穩定 : 5-7kg
制程流程 設定錯誤 作業規范 指導不合理
倉庫存儲 環境沒有 達到規定 標准
損 件 分 析
元件 損傷
刀具 不良
不光滑 夾具 不固 定
程不良 印刷不良 值缺 陷 搬運震動或 掉落、擠壓 包裝,運輸,储存
畸形裂痕
料
封帶機內 碰撞擠壓
PCB Layout 輿 板邊距離過近 距板邊至少 3mm
濕度過高 Spec:35%60% 溫度過低 spec 23℃+/-2
3.零件之位移
a.僅裂痕無分離位移:若當零件已有縱 向之裂痕或迴焊受熱但未斷裂之情形 時,極有可能僅見裂痕但並無分離造 成檢驗困擾。
b.斷裂分離:於迴焊前即已造成之裂痕 因銲錫熔解之拉力將造成如此之拉開 現象,甚至當背面製程時亦會有斷裂 部立碑情形。其導致原因多為第一製 程置件損傷、彎折應力或第二製程之 頂針不當致損;當然,元件製程中之 切割、包裝等所造成之裂痕於迴焊後 受熱斷裂亦有可能。
特徵典型: 1.在電極終端完成前之損傷通常 端電極形狀仍會依破裂處形狀 完成。 2.在折粒缺陷方面,電阻缺角、 畸形部分通常發現其位於側面 之部份或全部,且未超過1/3之 總面積。如有超過及位於電極 端側之缺陷通常會於測試階段 即被篩除。 3.電容之缺角、畸形製程不良漏 出部分(包裝運送致損除外)通常 在其破裂處會因Baking製程而
電極端剝離
電極端剝離
3.包裝、運輸及儲存:缺角、裂痕、層剝離(濕氣)… a.包裝: 原因:大量零件於封帶機內碰撞擠壓造成磨損、缺角。 特徵:通常在8個角落處較易發生,其破裂通常不會超 過邊 長的1/2,且已具有尖銳粗糙面之特徵。 b.運輸: 原因:因搬運震動或掉落、擠壓而形成(發生機率較小)。 特徵:通常為斷裂式之破裂,發生機率較小且置件機大多可以 篩除。 c.儲存: 原因:濕氣滲入。 特徵:當濕氣滲入層間(電容),如遇熱衝擊時將會導致層分離,
鎖支架
作業員在打螺絲時電批不 垂直,造成打滑,撞到周 邊元件
制程改善:
打螺絲時垂直電批.
F/T
測試時,因測試工具變形造成機構零件的接口變形或 損壞
制程改善:
1.當工具有變形時要及時更換
2. 作業時動作要合理,用力適當
目檢
目檢NG板放置時,作業 員作業不規範,導致放 板時,手中的板撞擊框 中已有的板或者撞擊 箱中的隔離板而造成 板上零件脫落或歪曲,
垂直撞擊
水平撞擊
層剝離
層剝離:焊接修補不當… 特徵典型:零件附近有焦黑FLUX、表面粗 糙變色、層剝離(電容)、文字面脫落…
分析模式著眼點及分析方法介紹
一.分析模式著眼點 二.分析方法介紹
一.分析模式著眼點 根據撞件後的具體狀況,分析模式可以確定為以下 四個: 1.助焊劑殘餘結晶之破壞: a.過reflow前; b.過reflow後; 2.撞擊點及方向、程度: a.有無撞擊點; b.是橫向撞擊還是縱向撞擊; c. 具體零件及位置(電阻、電容); d.撞擊力之程度
制程改善:
目前廠內Loader 的 Pitch值NG品框設為40,OK品框設為 20
AOI
SMT ICT
作業員轉板,操作不規 範,導致撞板,
制程改善:
作業員必須將板子平 行放入Magazine.放板 入棧板時,確保板子 整齊、穩當、有足夠 的間距。
SMT ICT
在放板時板邊的零件有 可能撞擊到L筐上發生撞 件。該現象也會發生在 AOI維修工位和DIP轉 板工位 制程改善: 1.放置時以一定的角度 傾斜放置,改角度的方 向要偏離周邊可能撞擊 的物體。如有圖所示 2.放置的板子置件要有 間隔距離,避免板子與 板子之間產生碰撞。如 有圖所示,間隔距離一 般為一個間隔。
進板
裝板時要平行裝板,避免pcb與Magazine產生撞擊 (圖1) 在機台內頂Pin設置錯誤,導致撞掉背焊.
Dek印刷
制程改善:
1.作業員制作頂Pin圖以後要ME確認以後才可以使用 2.開線前IPQA檢查頂Pin是否與頂Pin圖相附和(圖2)
圖1 圖2 在機台內頂Pin設置錯誤,導致撞掉背焊,
CP 置件
損件之模式分析
目錄 一.損件之分類及其典型模式 二.分析模式著眼點及分析方法介紹 三. 損件風險評估及制程改善 四.附錄損件不良圖片集
損件之分類及其典型模式
損件主要分為兩大類:材料問題和作業問題, 具體分類如下: 一.材料問題: 1.元件制程損傷:缺角、畸形、裂痕…
a.元件製程中折條或折粒時,因刀具不良(電容)、或預刻痕不 平均或折斷應力不當(電阻)所造成之缺陷; b.元件製程中各式夾具固定不良損傷(蒸鍍、槽鍍、電極沾錫 夾損); c.測試漏出不良;
b.重直撞擊力之破壞通常會 導致PCB之損傷,於元件部 分亦可看見明顯之損壞缺陷。 c.平行撞擊力會直接讓零件 產生破裂缺角之傷害,但因 力矩方向不大故多數時候並
2.裂痕形狀:
分層
斜向裂痕
放射狀裂痕
a.分層裂痕:分層之原因多由於熱衝擊所造成,但 亦有部份為元件製程不良所造成,因為層與層間 之壓合Baking製程缺陷造成迴焊後分層。 b.斜向裂痕:由於彎折之應力於零件下部形成支點, 固定之焊點於電極端側產生斷裂之斜面現象,尤 以與應力方向垂直之較大電容元件最為嚴重 c.放射狀裂痕:放射狀裂痕多有撞擊點可循,原因 多為點狀壓力所造成,如頂針、吸嘴、測試治具 等... d.完全破裂:完全破裂為最大之破壞模式,甚至常 伴隨著PCB之損壞。通常為橫向撞擊或電容裂痕 所造成之元件燒毀等情形造成。
損件風險評估及制程改善
根據不良類型及其典型模式和分析方法結合產 線實際生產流程狀況分析撞件主要表現為:零件受 外力撞擊造成本體破裂U01。 一. NG圖范例
二.人幾料法環要因分析圖 三.生產中風險評估及制程改善
一. NG圖范例
劑鉤零件損壞
PCB破裂
PCB板線路斷開
QPF零件腳變形 斷裂
二.人幾料法環要因分析圖
二.作業問題: 1.作業製程中損傷─撞擊破裂、應力損傷…
頂針設置不當:緊鄰區域內支撐,於置 件或測試實施加彎折應力破壞。 特徵典型:通常於電阻為斷裂或電極剝 離;電容則為斜面裂痕模式,如為第一 製程零件則或許於迴焊後會見到斷裂部 立碑現象。 應力損傷:進板不良造成夾板(卡板)變 形或人工彎折板子造成。 置件損傷:吸嘴不良及高度設定不當。 特徵典型:如為正面破裂斷裂通常於爐 後均會分離,而若為側邊損傷則多為缺 角狀斜面削落,且其特徵均可分辨出明 顯撞擊點存在。
NG
OK
DIP ICT/ATE
1.放板測試時,撞到 ICT 或ATE 治具, 2.治具安裝不到位,壓壞板或 零件
制程改善:
1.作業時要求雙手拿板放板, 放到位後才開始測試 2.要求ICT技術員測試前檢查 安裝是否到位
測電流/壓及 安裝散熱片
壓散熱片時,支架未頂住散熱片,導致壓住零件
制程改善:
操作前按氣壓治具check list 檢查頂針 是否松 動或歪斜
在料架加入防護欄桿
2.變更包裝方式時因動作方式不正確損傷零件 3. 濕敏零件真空包裝破壞.漏氣等. 烘烤後上線或烘烤後再真空包裝等 1.從備料室轉料過程中可能會發生跌落撞擊等導致零件損傷 在料架加入防護欄桿等
產線領料
2.在接料或CUT料過程中造成零件損傷. 使用正確的方法及工具.
PCB入Magazine時非平行進入時PCB板彎曲變形.
法
環
三.生產中風險評估及制程改善
1.來料本體不良,來料包裝方式不合理: 受外力導致.
倉庫存儲
要求供應商改善包裝方式. 2.倉庫溫濕度不達標: 倉庫管理員定時檢查溫濕度計查看是否在規格范圍內. 3.存儲包裝方式不合理:巖格專業的存儲堆碼方式防止包裝方式 變形,蠕變以至損傷零件
備料室發料
1.從倉庫轉料過程中可能會發生跌落撞擊等導致零件損傷.
3.裂痕之模式:.
a.分層裂痕; b. 斜向裂痕; c.放射狀裂痕 ; d. 完全破裂;
4.零件之位移:
a.僅裂痕但無分離位移; b.有分離位移之破裂;
二.分析方法介紹 分析方法 1.撞擊點: a.撞擊點之有無並非絕對之 分析判斷因子,但通常撞擊 點之位置、方向及破壞程度 將可提供分析相當之訊息。
當AOI前的LOADER已滿,或軌道緊急開關按下, 或軌道感應器失效,出回焊爐後前板未流下,而過回 焊爐的板繼續流下,導致後面的板撞擊前板
圖 3
Reflow
制程改善:
1.提高AOI的檢測速度, 2.產線安排此工位附近的人員注意蜂鳴器的報警, 確保在撞件前取出板子
Buffer
Buffer Pitch 設置錯誤氣壓推板竿碰到上面或下面的板
軌道卡板, 溫度過高, 造成零件爆 裂
治具下壓時下 壓力過大,造 成零件破損, 錫裂
流線過程中 PCB相撞,重 治具&載 疊 流線過程中 具問題 PCB跌落 機臺軌道上有