现场制程改善的基本方法
制程改善的技巧范文
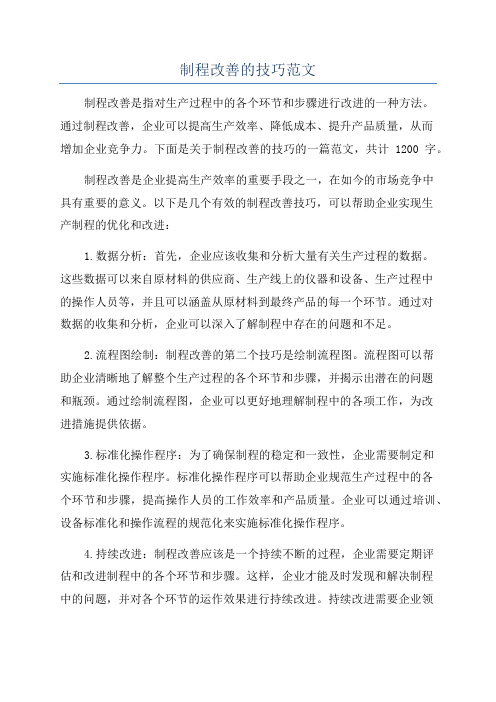
制程改善的技巧范文制程改善是指对生产过程中的各个环节和步骤进行改进的一种方法。
通过制程改善,企业可以提高生产效率、降低成本、提升产品质量,从而增加企业竞争力。
下面是关于制程改善的技巧的一篇范文,共计1200字。
制程改善是企业提高生产效率的重要手段之一,在如今的市场竞争中具有重要的意义。
以下是几个有效的制程改善技巧,可以帮助企业实现生产制程的优化和改进:1.数据分析:首先,企业应该收集和分析大量有关生产过程的数据。
这些数据可以来自原材料的供应商、生产线上的仪器和设备、生产过程中的操作人员等,并且可以涵盖从原材料到最终产品的每一个环节。
通过对数据的收集和分析,企业可以深入了解制程中存在的问题和不足。
2.流程图绘制:制程改善的第二个技巧是绘制流程图。
流程图可以帮助企业清晰地了解整个生产过程的各个环节和步骤,并揭示出潜在的问题和瓶颈。
通过绘制流程图,企业可以更好地理解制程中的各项工作,为改进措施提供依据。
3.标准化操作程序:为了确保制程的稳定和一致性,企业需要制定和实施标准化操作程序。
标准化操作程序可以帮助企业规范生产过程中的各个环节和步骤,提高操作人员的工作效率和产品质量。
企业可以通过培训、设备标准化和操作流程的规范化来实施标准化操作程序。
4.持续改进:制程改善应该是一个持续不断的过程,企业需要定期评估和改进制程中的各个环节和步骤。
这样,企业才能及时发现和解决制程中的问题,并对各个环节的运作效果进行持续改进。
持续改进需要企业领导层的支持和员工的积极参与,可以通过设立改善目标、开展改善活动和定期评估结果来实施。
5.跟踪和反馈:企业应该建立起跟踪和反馈机制,及时了解和掌握制程中的问题和改进措施的实施效果。
跟踪和反馈应该是全员参与的过程,企业可以通过会议、报告、绩效考核等方式进行。
通过跟踪和反馈,企业可以及时发现和解决制程中的问题,确保改进措施的有效实施。
综上所述,制程改善是企业提高生产效率的重要手段之一、通过数据分析、流程图绘制、标准化操作程序的制定、持续改进和跟踪和反馈等技巧,企业可以实现对制程的优化和改进。
产品制程工序的改善

(1) 节约材料费:提高利用率、降低不良等;(2)节约工时:线体平衡率、人员编制、能力负荷对策、内外作业区分、运输改善等;(2)节约制造费用:通过对工序及其他管理系统的改善,节约管理费、实现设备和工器具的合理化;☺ 提高生产力(1) 通过对瓶颈工序的人员增援或设备增设,提高能力; (2) 通过交班制,增加运转时间;(3) 采取提高运转率(人员及设备)或减少不良品的对策; (4) 增设新生产线并计算最佳生产线数量。
☺ 减少材料损伤并维持质量(1) 采取防止搬运工序上的振动、冲击、摔落、压缩引起的变质、破损的对策; (2) 探讨防止材料损伤或影响质量的包装形式或运输容器等;(3) 防止在管理时因取放不好产生的损伤,保管或储藏方式不当引起的劣化及变质; (4) 设备的选择或改善对产品质量的影响;(5) 确认质量、探讨质量检查工序方式和工序系列内检查位置。
☺ 减少在制品(日程、交货期)(1) 研讨整个工序系列的工序管理; (2) 研讨各工序间的同期化; (3) 生产工序和运输设备调整;(4) 设备平面布置图变更或搬运次数增加等的对策。
☺ 空间有效利用(1) 提高保管、储藏效率;(2) 排除设备等的布置变更引起的浪费或空间浪费; (3) 为实现灵活运用立体空间进行规划。
☺ 提高安全、环境条件(1) 安全、噪音、振动、粉尘、气体(1) 要考虑<此作业是为了什么而做?>;(2) 产品设计(形象、表面处理、涂装、标准化)的变更;(3) 材料规格(材质、形象、尺寸、材料截断、内外作业区分)的变更; (4) 包装规格(包装速度的标准化、尺寸、形象)的变更。
(1) 结合:考虑将分离的工序合在一起; (2) 分离:将结合的工序进行分解; (3) 交替:考虑交替前后工序的顺序;(4) 并行:考虑设备、作业内容的并行,构思最佳化。
(1)在各工序上选定最佳的加工条件;(2) 在各工序上考虑最佳(低费用、高性能、自动化)设备;(3) 简化(生手也容易做到)各工序的作业内容。
关于制程质量异常问题改善的几点建议

关于制程质量异常问题改善的几点建议进入公司将近一个月以来,我经过对工模、注塑、冲压、装配车间现场管理进行熟悉和对各工序质量异常情况处理及跟进,发现质量异常处理流程存在问题,如在首检或巡检确认产品不合格时,冲压车间未按异常处理流程停止生产,正确流程应该是质量部判定为不合格,由工模部改模或修模合格后再确认是否能继续生产,或者研发部和质量部同时确认可以特采,特采单现在有流程但没有实行。
对各车间存在的问题,我进行总结如下:五金注塑车间异常问题鱼骨图:1、五金模具问题从2月10日-3月8日的制程异常数据分析可知,冲压异常一个月共44起异常,从历史的数据来看,以前平均每个月冲压异常单有30张左右,冲压模具精度满足不了生产实际需求,主要集中在五金冲压模具:尺寸不良(压片、方块、引脚、衬套、压板、铜片),根据20/80法则,压片和引脚的尺寸不良占80%以上,需要重点改善压片和引脚的模具精准度。
2、五金冲压设备问题:2月10日-3月8日冲压设备7,2,1,6,3五台设备引起的异常占80%以上(共44次),应该重点关注和改善设备的点检、维修、保养。
3、注塑问题从2月10日-2月29日注塑车间制程异常发生共19次,其中螺孔飞边、拼接松动、断针、结构NG、顶针高不良项目占80%以上,为重点改善项目。
4、装配问题2月9日-2月27日装配车间制程异常共8起,作业员未按作业指导书操作、螺钉问题、引脚问题占80%以上,对生产人员和IPQC人员的培训为重点改善项目。
对以上问题,改善建议如下:一、提高模具精确度(设计图纸与实物、样品),需要研发设计与工模车间在图纸上和实际制作模具,研发技术要求公差与生产实际操作误差匹配,改模时配合准确,及时更新,质量部参与监督并确认,缩短模具修改维护周期。
二、传递质量压力,对制程异常责任部门要求签字确认,组织召开专题改善项目会议,建立品质圈,形成质量责任追溯机制。
三、增加水口料按等级进行可靠性实验检测,对于检测不合格的水口料进行限级使用,控制水口料质量,加强封样管理和完善标准样品管理。
制程改善部工作规划
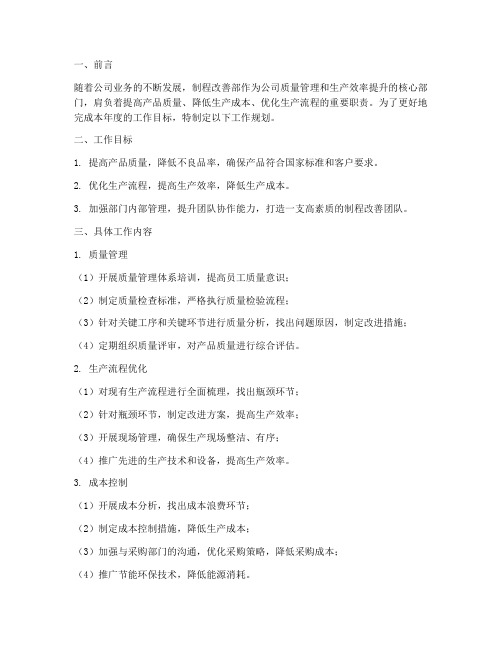
一、前言随着公司业务的不断发展,制程改善部作为公司质量管理和生产效率提升的核心部门,肩负着提高产品质量、降低生产成本、优化生产流程的重要职责。
为了更好地完成本年度的工作目标,特制定以下工作规划。
二、工作目标1. 提高产品质量,降低不良品率,确保产品符合国家标准和客户要求。
2. 优化生产流程,提高生产效率,降低生产成本。
3. 加强部门内部管理,提升团队协作能力,打造一支高素质的制程改善团队。
三、具体工作内容1. 质量管理(1)开展质量管理体系培训,提高员工质量意识;(2)制定质量检查标准,严格执行质量检验流程;(3)针对关键工序和关键环节进行质量分析,找出问题原因,制定改进措施;(4)定期组织质量评审,对产品质量进行综合评估。
2. 生产流程优化(1)对现有生产流程进行全面梳理,找出瓶颈环节;(2)针对瓶颈环节,制定改进方案,提高生产效率;(3)开展现场管理,确保生产现场整洁、有序;(4)推广先进的生产技术和设备,提高生产效率。
3. 成本控制(1)开展成本分析,找出成本浪费环节;(2)制定成本控制措施,降低生产成本;(3)加强与采购部门的沟通,优化采购策略,降低采购成本;(4)推广节能环保技术,降低能源消耗。
4. 团队建设(1)开展团队建设活动,提高团队凝聚力;(2)加强员工培训,提升员工技能水平;(3)建立绩效考核体系,激发员工工作积极性;(4)加强与各部门的沟通协作,共同推进公司发展。
四、实施计划1. 第一季度:开展质量管理体系培训,梳理现有生产流程,找出瓶颈环节;2. 第二季度:制定改进方案,实施生产流程优化,降低生产成本;3. 第三季度:开展成本分析,推广节能环保技术,提高能源利用率;4. 第四季度:总结全年工作,对部门工作进行评估,制定下一年度工作计划。
五、总结制程改善部作为公司的重要部门,肩负着提高产品质量、降低生产成本、优化生产流程的重要职责。
本年度工作规划旨在提高部门工作效率,为公司创造更多价值。
生产制程问题改善措施

生产制程问题改善措施引言在制造业中,生产制程问题是不可避免的。
这些问题可能会导致生产效率低下、产品质量下降和成本增加。
因此,对生产制程问题进行改善是非常重要的。
本文将讨论一些常见的生产制程问题,并提出改善措施。
问题一:生产效率低下低生产效率是制造业中经常面临的问题。
主要原因可能包括设备故障、工艺不合理和操作不当等。
下面是一些建议来改善生产效率:•定期维护和保养设备,以确保设备正常运行并减少故障的发生。
•优化生产工艺,通过分析数据和流程改进来减少生产时间。
•提供员工培训,确保操作规范和高效。
问题二:产品质量下降产品质量下降是另一个常见的生产制程问题。
有几个因素可能导致产品质量下降,如原材料质量不合格、错误的工艺参数和人为错误。
以下是改善产品质量的一些建议:•建立严格的原材料供应链管理,确保原材料质量符合要求。
•控制工艺参数,确保每一步工艺都按照规范执行。
•培训员工,提高操作技能和质量意识。
问题三:成本增加成本增加是制造业中一直受到关注的问题。
高成本可能是由于原材料价格的上涨、废品率的增加和设备维修费用的增加等问题引起的。
以下是降低成本的一些建议:•寻找替代的原材料来源,以降低原材料成本。
•优化工艺流程,减少废品率,并提高产品质量。
•定期维护设备,减少维修费用,并延长设备使用寿命。
结论生产制程问题对制造业的影响非常大,可以导致低生产效率、产品质量下降和成本增加。
然而,通过采取一系列改善措施,可以有效地解决这些问题。
定期维护设备、优化工艺流程和培训员工等措施可以提高生产效率和产品质量,并降低成本。
制造业应该重视生产制程问题,并积极寻找解决方案,以提高竞争力和可持续发展。
生产线的改善方法及改善思路

生产线的改善方法及改善思路一、生产线改善分析中,企业活动可分为3类:1、能创造价值的步骤,如产品的加工过程。
2、不创造价值,但在现有技术下是不可避免的活动,如搬运、装卸等、不创造价值,可以立即取消的步骤。
3、消除第三类活动、减少第二类活动、增加与扩大第一类活动、达到改善生产线的目的。
根据以对企业活动的分析,可以结合对这些功能的实现投入的成本,然后利用价值分析规则对其进行价值的提升和改善。
采用精益生产的方式,能生产出高品质、低成本和交货快速且稳定的产品,且生产方法富有弹性和创新。
二、生产现场的改善指导原则在精益生产中实现均衡生产的关键技术就是一个流生产方式,是按产品类别布置的多制程生产方式,可让产品在生产过程中实现单件流动,一个流生产是指从原材料投入到成品产出的整个制造加工过程,零件始终处于不停滞、不堆积、不超越的流动状态,按生产节拍逐个流动的生产方法。
需要做到低成本、高品质、高服务、高产出、消除各个环节的浪费:改善工作环境。
提高工作效率,达到生产线平衡,力争做到4个满惫(业主满意、客户满意、雇员满意、社会满意)。
精益生产方式的一个重要特征是实践性高于理论性,它源于生产现场,践行于生产现场,是边实践、边思考、边完善的产物。
在生产现场改善前,天行健管理公司建议应该对生产现场进行评估和作业测量,只有对生产现场进行实事求是的评估和测定,全面掌握和认识现况,对不合理的动作要素进行优化,减少作业时间,消除瓶颈,可采取的措施主要有:1、瓶颈工序进行工作改善,如增加或改善工装、改善设备性能等2、进行操作分析和动作研究,剔除不必要的操作,提高瓶颈工序工作人员效率或机能3、增加瓶颈工序工作人员4、将瓶颈工序的工作内容分担给其他工序5、合并相关工序,重新进行工序排序6、拆分工作时间较短的工序并入其他工序二、生产线上的改善方法,须遵循以下原则:1、有利于实现少人化2、有利于操作者的作业3、有利于物流与信息传递的控制4、有利于质量保证5、有利于全员生产维修(TPM, Total ProductiveMaintenance(全面生产性维修; 总生产维修制)开展6、有利于实现标准作业7、有利于保障安全三、生产线的四种改善思路1、平衡生产线生产线平衡是对生产线上的全部工位进行平均化、调整作业负荷,以使各作业时间尽可能使用相近的技术手段与方法。
质量改善的三现五原则方法

制程变异应从制程面去改善
2017/11/10
28
伍、变化点分析不清楚
疑 问 点:以前为何不会发生不良,现在才发生? 一定是哪里有变更,变化点在哪里?
思 考:不良隐藏於变化点中。
分析方法:4M1D里寻找真因 人[Man]:人员有否更换,有否依标准作业、人员之 工作情绪等。 机[Machine]:机器设备、镆、治、检、工具有否调 整、变更等。 材[Material]:材料有否改变、前工程流入件不良 等。 方法[Method]: 标准有否规定?标准是否明确? 设计[Design]: 是否设计变更等。
1、发生场所:汽缸压铸NO.2生产线。 2、 发生状况:请参照右手腕受伤素描图
(由于汽缸倒下来,作业人员在准备将其扶起时, 手腕被支架给夹住了)。
3、 发生月日:SEP-21-1988 4、 发生件数:1 件。 5、 处置内容:在事故发生1 小时内,伤者被送到市内的医院急救,
4.重要之标准类:作业标准、图面、零件检验标准、
QC工程表、试验规范、规章、标
准样品。
5.保证不会再发: 真因 对策 回馈标准
2017/11/10
30
柒:再现试验证明
疑 问 点:你如何知道解析不良原因是正确的吗?
思 考:科学的实验是最好的证明→再现试验。
分析方法:正向再现与反向再现。 1.正向:将不良要因排除(不良条件修正)后会制造 出良品。 2.反向:以不良条件生产会制造出不良品。 若上述二向再现结果与假设违背,则肯定 所解析出之不良原因必定有偏差。 3.不良品再现。
何时 – 记入问题发生的日期。
2017/11/10
11
把握现况 - 5W1H
现场生产力提升与工作效率改善
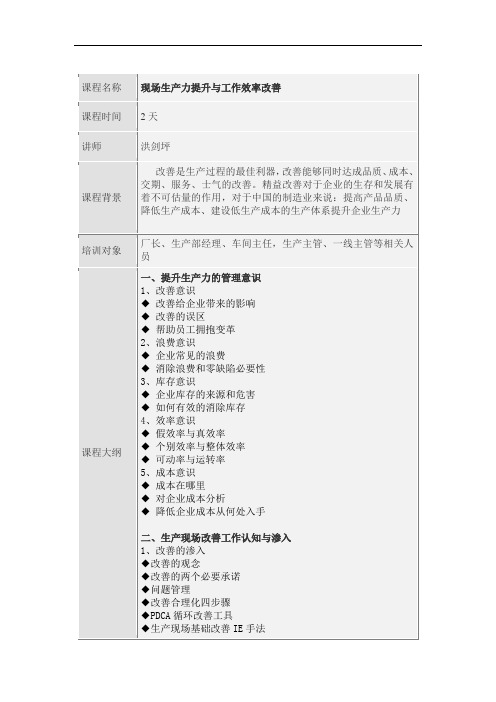
◆流程优化的内容
◆流程优化的步骤
◆流程改善四个原则
◆向工艺流程要效益
◆向平面流程要效益
◆向移动方式要效益
◆向均衡生产要效益
2、精益化柔性生产单元与U型布局
◆单件流动
◆按工艺流程布置设备
◆生产速度同步化
◆设备小型化
◆生产线U形化
◆多工序操作
◆走动作业
◆员工多能化
◆一个流生产的推行步骤
◆生产线平衡分析与改善
◆生产线平衡改善方法要领
◆平衡线对降低成本和减少浪费的作用
※案例研讨分析
5、精益均衡化生产
◆准时化的前提条件——均衡化
◆均衡化的生产工序
◆消除了不平均现象的均衡化
◆批量生产和均衡化生产
◆产品总量均衡化
◆种类的均衡化
◆生产均衡化之混合生产
◆如何实现混合生产
◆品种及生产数的排列
※案例研讨分析
3、准时化拉动生产与看板管理
◆快速响应客户的拉动系统
◆拉动系统图示
◆拉动式生产之信息传递工具---看板
◆生产看板管理--符合JIT ,压缩库存量
◆看板运行的种类和工作原理
◆看板方式的六个原则
◆决定看板的数目
◆领取看板的运行过程
※精益企业看板案例分析
4、实现生产线平衡效率最大化
◆何为生产线平衡
◆平衡线计算
◆降低企业成本从何处入手
二、生产现场改善工作认知与渗入
1、改善的渗入
◆改善的观念
◆改善的两个必要承诺
◆问题管理
◆改善合理化四步骤
◆PDCA循环改善工具
◆生产现场基础改善IE手法
◆识别并改善企业瓶颈
LINE改善基本知识

定量领取
生产线
24/24
纳入时间管理板 所谓时间管理板是: 纳入部品协力厂商(协 力公司)时,根据协力 厂商时间进行纳入的话 ,受入方的工作会发生 混乱。 所以,根据规定时间 段,撑握下一个要纳 入的厂商的时间管理 板。 看板用不同颜色区分 纳入前和纳入后的厂 商,纳入方到 达时把牌子放反,有了 这样的管理,谁看了都 能知道纳入的状况。
一人多工程: 编工程时从生产效率开 始考虑,机械要根据加工的顺序放置, 然后沿着流程让一人担任几台机械
一人?台
单能工和多能工 多能工: 名符其实的可进行多工程作业的 单能工:只具备加工一工程的能力的作业 员,所以,说我是旋床工,所以只能做旋床 作业,其它和旋床类似的工作也做不到 的人. 为了调整生产量,或其它外介条件,要变换 生产人员时,单能工的话无法移动工程间 而伤脑筋. 作业员,可根据加工顺序摆放机台,把多工
3.作业面积不妨碍 作业就可以,材料 工具等尽量放在 作业的近处
Ⅲ 各动作的 距离最短 化
Ⅳ 动作 轻松化
1. 实现没有限制的 基础动作 2. 动作转向、变换时 要轻松自然 3. 利用惯性、重力、 自然力
3. 作业点的高度 要适当
5.利用治具、指引 线等统一运转的 路线, 6.尽量利用动力 工具
9/24
所说的浪费有时会是在库,有时是搬运,也有时是作业其本身。 这些事物在现场互相纠缠,浪费导致再浪费而影响企业经营。 所以,在制物方法中彻底废除各种各样的浪费,以求低减成本是生产方式的 基本的想法。
把需要的东西,在需要的时候,只拿需要的量
何谓原价
企业一边在社会全体中提供谐调,一 边在生成发展.
贡献于人间社会,谋求社会的使命,在结 果中赚得利润,必须永久性地发展下去.
现场改善计划和行动计划

现场改善计划和行动计划
目的:
通过分析工厂现场的风险点和不足,制定改善计划和具体行动,以提高工厂整体安全管理水平。
一、现场识别和评估
1. 通过工厂现场视察,识别存在的风险点,包括:
- 機器操作区域无安全障壁
- 操作人员无个人防护装备
- 操作程序缺少详细說明
2. 使用风险评估表对每個风险点进行风险等級分析
二、改善目标和措施
根据风险分析结果,制定以下改善目标和措施:
1. 目标:消除存在高风险可能的地方
措施:为所有机器设置安全罩及隔离区
2. 目标:降低中风险可能性
措施:为所有操作人员提供安全装备,并制定详细操作规程
3. 目标:杜絕低风险事件的發生
措施:开展安全培训及作业管制
三、实施计划
1. 责任单位:安全管理部门
2. 实施日期:2021年6月1日-2021年8月31日
3. 具体任务安排:参照附件
4. 资源保障:根据实施计划安排所需人力、物力支持
四、效果评估
实施完工后使用相同的评估表对现场进行再评估,调查员工意见,检查达成情况,并写出评估报告。
以上为一份简单的"现场改善计划和行动计划"样本,实际应根据企业的实际情况进行修改完善。
品质现场改善方案
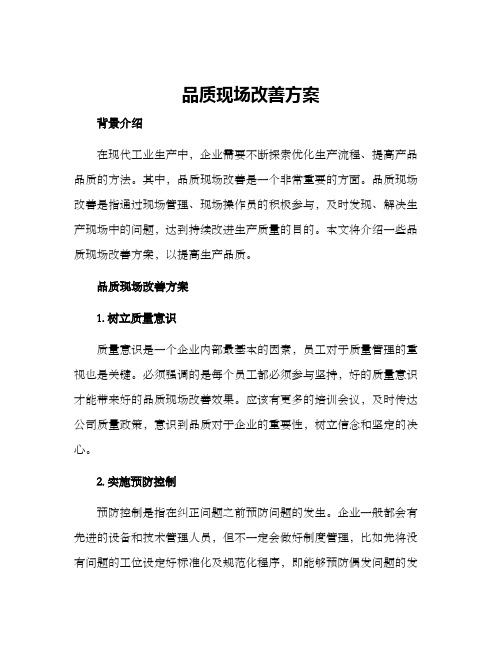
品质现场改善方案背景介绍在现代工业生产中,企业需要不断探索优化生产流程、提高产品品质的方法。
其中,品质现场改善是一个非常重要的方面。
品质现场改善是指通过现场管理、现场操作员的积极参与,及时发现、解决生产现场中的问题,达到持续改进生产质量的目的。
本文将介绍一些品质现场改善方案,以提高生产品质。
品质现场改善方案1. 树立质量意识质量意识是一个企业内部最基本的因素,员工对于质量管理的重视也是关键。
必须强调的是每个员工都必须参与坚持,好的质量意识才能带来好的品质现场改善效果。
应该有更多的培训会议,及时传达公司质量政策,意识到品质对于企业的重要性,树立信念和坚定的决心。
2. 实施预防控制预防控制是指在纠正问题之前预防问题的发生。
企业一般都会有先进的设备和技术管理人员,但不一定会做好制度管理,比如先将没有问题的工位设定好标准化及规范化程序,即能够预防偶发问题的发生。
可以通过设定“5S”管理、标准操作规程、设定标准的物料清单等来达到“预防控制”的目的。
3. 引入QC工具QC工具包括Pareto图、散点图、直方图等等。
从方案角度来说,这些图表非常有用,并且可以在制程控制和分析中帮助员工快速判断问题出在哪里。
例如,大问题常常是因为少数问题源不明导致,Pareto 图可以让员工快速识别主要问题源,集中攻克。
4. 合理分工质量管理企业内部的分工越来越明晰,那么相应的品质管理责任也应该分轻重缓急。
此时,合理的由设计、制造、品质控制等人员来负责品质管理,有一套完整的质量控制流程品质现场改善才能实现。
5. 总结改善成果无论是品质改善还是生产管理,总结每一步改进的成果是非常有必要的,它是品质现场改善方案实际成效的重要组成部分。
通过清晰的总结可以了解改善前后的提高度,并且对于后续的再次改进也会起到积极的推动作用。
结论品质现场改善是一个不断提高企业生产效率的过程,每一步都必须要依靠整个企业的员工参与,思路的引导和技术的推广和实现。
生产车间现场改善方案
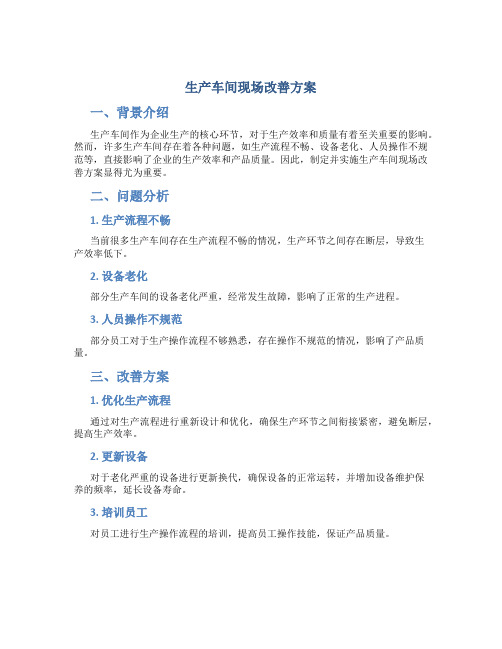
生产车间现场改善方案一、背景介绍生产车间作为企业生产的核心环节,对于生产效率和质量有着至关重要的影响。
然而,许多生产车间存在着各种问题,如生产流程不畅、设备老化、人员操作不规范等,直接影响了企业的生产效率和产品质量。
因此,制定并实施生产车间现场改善方案显得尤为重要。
二、问题分析1. 生产流程不畅当前很多生产车间存在生产流程不畅的情况,生产环节之间存在断层,导致生产效率低下。
2. 设备老化部分生产车间的设备老化严重,经常发生故障,影响了正常的生产进程。
3. 人员操作不规范部分员工对于生产操作流程不够熟悉,存在操作不规范的情况,影响了产品质量。
三、改善方案1. 优化生产流程通过对生产流程进行重新设计和优化,确保生产环节之间衔接紧密,避免断层,提高生产效率。
2. 更新设备对于老化严重的设备进行更新换代,确保设备的正常运转,并增加设备维护保养的频率,延长设备寿命。
3. 培训员工对员工进行生产操作流程的培训,提高员工操作技能,保证产品质量。
四、实施步骤1. 制定改善计划根据问题分析,制定具体的改善方案和实施计划。
2. 落实责任人明确改善方案的责任人,确保改善工作有序进行。
3. 实施改善方案按照制定的改善方案,逐步实施生产车间现场改善工作。
4. 监督检查定期对改善工作进行监督检查,及时发现问题并采取措施纠正。
五、改善效果评估1. 生产效率提升优化生产流程和更新设备,生产效率得到提升,产能得到增加。
2. 产品质量提高员工操作水平提升和设备更新,产品质量得到提高,消除了质量问题带来的损失。
3. 员工满意度提升通过培训员工,提高了员工的工作技能和工作积极性,增加了员工的满意度。
六、结语生产车间现场改善是企业提高生产效率和产品质量的一个重要举措,通过优化生产流程、更新设备和培训员工,可以实现生产车间的现场改善,对于企业的发展具有重要意义。
希望以上改善方案能够为企业的生产车间改善工作提供一定的参考和指导。
制程异常分析改善汇总

防焊前五项制程问题分析:一、防焊空泡:造成原因:1、前处理不良。
(H2SO4浓度、水质、吹干段角度及风量,吸水海棉清洁度、烘干温度)。
2、磨刷后放置时间过长,室内湿度偏低。
3、印刷台面沾有油墨及其它有机溶剂,反沾板面,油墨搅拌不均。
4、预烤不足。
5、曝光能量太低或太高。
6、显影侧蚀太多。
7、HAL浸助焊剂时间太长,锡槽温度太高,浸锡时间太长。
预防措施:1、前处理作业必须按SOP要求生产。
2、磨刷后放置时间不得超过2H ,室内湿度控制在50-60%之间。
3、印刷台面保持清洁,印第一面时台面上垫一张白纸,以保证板面清洁度。
4、预烤温度保持70±2℃,烤后之板保证不粘棕片。
5、曝光能量保持在9-13格。
6、显影点控制在50-60%,避免过多侧蚀。
7、后烤通风保持良好,塞孔板必须分段烘烤。
8、HAL作业须完全按照SOP操作,不可有违规作为。
二、L/Q内圈阴影:原因分析:1、油墨过期。
2、预烤时间过长,温度过高。
3、挡点印刷时,孔环处积墨过多,印刷房湿度不够。
4、曝光前,静置时间过长。
5、显影速度过快,压力过小。
6、棕片遮光度不够。
7、曝光时吸真空压力未能达到要求。
改善对策:1、油墨按照先进先出的方式使用,保证在油墨保质期内使用。
2、预烤时间和温度按SOP要求作业,且烤好后及时取出防止冷烤。
3、印刷房湿度保持在50-60%之间,挡点印刷保持连贯,且印一PNL刮一次网版。
4、预烤后板静置时间不能眼过12H,最连贯4H以内对位完。
5、显影点保持在50-60%之间。
6、选用遮光度及质量较好之棕片生产。
7、吸真空不得低于600㎜Hg,且须保持导气良好。
三、卡锡珠:原因分析:1、印刷塞孔不满(量产板)。
2、退洗板导通孔内油墨未剥除干净。
3、油墨本身质量问题。
4、HAL贴胶未贴好,某些孔呈半覆盖状态。
5、HAL浸助焊剂及浸锡时间过短。
改善对策:1、从印刷各条件去改善塞孔程度。
(刮刀压力、角度、确度、速度、网目T数量)2、选用适合的退洗液,尽可能洗净导通孔内油墨,保证塞孔效果。
制程改善方案范文

制程改善方案范文制程改善是企业持续改进的重要环节,通过优化和改进制程,可以提高效率、降低成本、提高产品质量,并增加生产能力。
下面是一个针对制程改善的方案,包括制程分析、问题识别、改进策略和实施措施等。
一、制程分析对当前制程进行全面的分析,了解其流程、环节、时间、资源、成本等方面的情况。
可以采用价值流图、时间流程图等工具,对制程进行详细的描述,以便更好地识别问题和改进方向。
二、问题识别在制程分析的基础上,识别出影响制程效率、成本和质量的问题,可能的问题包括:1.流程繁琐,存在重复和浪费的环节;2.设备老化,存在故障率高、维修频繁等问题;3.人力资源不足,缺乏技能和培训;4.质检不合格率高,存在质量管理问题。
三、改进策略根据问题识别的结果,制定相应的改进策略。
可以综合考虑多个方面进行改进,包括:1.流程简化和优化:通过消除重复环节、简化操作流程,提高制程效率;2.设备升级和维护:投入资金更新设备,并加强设备维护,降低故障率和维修频次;3.人员培训和技能提升:加强员工培训,提高技术水平和操作能力;4.质量管控和监测:建立完善的质量管理体系,加强质检和过程监测,及时发现和解决问题。
四、实施措施制定改进方案后,需要具体实施措施,包括:1.建立改进团队:由专业团队负责制程改进工作,明确责任和任务分工;2.制定详细实施计划:制定改进实施的具体时间表和目标,明确需要投入的资源和预期效果;3.测试和验证:在实施前,进行小规模的试点和验证,验证改进方案的可行性和效果;4.逐步推广和落地:根据试点结果,逐步推广实施,最终实现全面改进;5.监测和评估:实施改进后,持续监测和评估效果,及时调整和改进。
五、持续改进制程改进是一个持续性的过程,需要不断地进行监测和改进。
建立持续改进机制,包括:1.定期检查和评估制程:定期进行制程分析和问题识别,及时调整和改进;2.建立反馈机制:鼓励员工提供改进建议和意见,建立沟通渠道,及时反馈问题和解决方案;3.绩效考核和激励机制:将制程改进的效果纳入绩效考核体系,给予相关人员合理的激励和回报。
现场改善方案及几点建议

Luzhou Detian Ceramics Co., Ltd
何志 2016.6.27
尊敬的刘总、李总并各位领导:
本人加入得天陶瓷已一个多月的时间。期间耗时半个月对公司所有车间的生产流
程有了一个初步的熟悉,对于公司的工艺流程及生产管理现状已经有了一个初步的认识。后 定职于整个公司最重要也是最关键的成型车间,在此期间发现了一系列急需改善的问题点。 根据本人以前的工作经验,拟定了部分的改善思路与几点建议。由于本人以前未接触过陶瓷 行业,肯定存在诸多认识不到位之处,还望各位领导指教。 以上 何志 2016.6.27
排拉方式:
通过现场实测数据分析,此排拉的瓶颈岗位在于精坯外观全检。 瓶颈岗位时间:N/T=6.46S 标准工时:3600S/6.5S=553个; 若每日上班8H,其中,作业时间7.5H,则全天产能为7.5H*553个=4153个; 若按现阶段产能,共需6组人完成每日25000的产能; 目前仅有4人,实行抽检的方式,若导入全检,则总人力需求为6组*2人=12人,需求8人; 增加的人力成本: 全检人员采用计时的方式,若每人每月2000元工资,则月增加人力成本2000*8=16000元; 若采取全检的方式,其他不看,仅瓶底泥渣一项就提升大约2%的成瓷良率水平。减 少报废的件数:25000*0.02=500件;每月节省500件*30天=15000件; 假设成瓷的报废成本为2元/个,则减少报废15000件*2元=30000元,相比人力成本支出可节约 公司成本30000元-16000元=14000元。 故根据以上数据得出结论,必须在精坯检导入全检的方式,以提升成瓷的良率水平。 若成型的制程改善比较明显,能大大提升直通率,才可考虑由全检变更为抽检。这样才 能最大限度的为公司节省成本。若导入流水线,则可将全检集成在流水线,这样成型车间的 精坯可直接到达烧成车间,进入窑炉烧制,提高坯架车周转效率。
现场制程管制和改善方式

QFD:Quality Function Development 即品質質機能展 開 PDCA又稱戴明管理循環圖(Deming Circle)
P------------Plan計劃 D------------DO執行
C------------Check檢核
A------------Action改善 PDCA是一種沒有起點,沒有終點的循環步驟也不一定 要從P開始
UCL UCL
檢 定 規 則 4 : (8 缺 C ) 有 8 點 在 中 心 線 之 兩 側 , 但 C 區 並 無 點 子 者 。
A B
A B
X
C C B
X
C C B
LCL
A
LCL
A
管 制 圖 之 判 讀 (二)
檢 定 規 則 5 : (9 單 側 ) 連續 9 點在 C 區或 C 區以外者。
拒收標簽: 任何不合格之產品標示
特采標簽: 不影響品質機能經品保部主管 以上特采認可之產品標示 初物標簽:針對第一次上線之產品標示 以上均需立即明顯,隔區放置依需求分 別記錄
不合格物品如何處理? 是指不符合規格標準的 物品、半成品、零件、材料等、其處置 方法如下: 掛標簽識別; 隔離放置(利用不良品、箱、 架放置于固定的區域; 盡快由專業人員對其作檢查、 對策、追蹤到改善解決為止.
Tpm:Total Produtie Maintenance 即全員生產保養包 涵四重點: 預防保養--------指日常保養與定期保養 事後保養--------故障維修 改良保養--------設備改造使之易養易護 保養設計--------設計不易故障之生產設備
8-DS Disciplines Team Quotiented Problem Solving是 利用團隊以事實導向以解決問題的方式 D1--------成立團隊,面對問題(Team組成) D2-------- 敘述問題(現況調查,目標明確化 D3--------實施並確認暫時行動(緊急對策) D4--------界定及確認(要因分析)
制程改善的技巧范文

制程改善的技巧范文制程改善是指通过不断优化和改进生产流程,提高产品质量、降低生产成本、提高生产效率和缩短生产周期的方法和技巧。
下面是一些常用的制程改善技巧:1.流程分析和价值流映射:通过绘制流程图和价值流图,详细了解和分析整个生产过程中的工序、流程和资源利用情况。
通过找出流程中的瓶颈和浪费,可以有针对性地改善和优化流程。
2.5S整理:通过整理、整顿、清扫、清洁、标准化,实现现场管理的优化和规范化。
通过清除现场杂物,保持现场整洁,提高操作员工作效率和品质。
3. Kaizen:即改善的概念。
通过小步骤的持续改进,不断优化工作流程和生产过程。
通过员工参与和团队合作,发现和解决问题,提高产品和流程的质量。
4.容器管理:通过调整物料的容器大小、形状和数量,提高物料和信息流的可视化和管控能力。
通过建立和优化物料供应链,避免物料短缺和过剩。
5.持续改进:通过对关键指标的监控和分析,持续改进业绩和流程。
使用PDCA循环反馈机制,通过计划、执行、检验和调整,不断优化制程。
6.标准作业程序(SOP):通过标准化和规范化操作流程,减少变异性,提高生产过程的稳定性和可控性。
确保员工在操作中遵循规定流程,减少错误和浪费。
7.设备保养和维护:通过定期检查和保养设备,延长设备寿命和稳定性,减少因设备故障和停机而导致的生产中断和产品质量问题。
8.质量管理:通过建立可追溯性和检验点,确保产品质量符合标准和要求。
实施质量检验和控制,及时发现和纠正质量问题,提高产品的质量稳定性。
9.员工培训和参与:通过培训和教育,提高员工的专业知识和技能,增强员工的责任心和合作精神。
鼓励员工参与制程改善活动,共同推动生产过程的优化。
10.制程自动化:通过引入先进的自动化设备和信息系统,提高操作的一致性和效率,减少人为因素对制程的影响。
自动化可以提高生产过程的可控性和准确性,减少错误和浪费。
以上是一些常用的制程改善技巧,企业可以结合自身的情况和需求,选择合适的技巧来优化和改进生产过程,提高产品质量和工作效率。
生产现场改善及流水线线改造提案
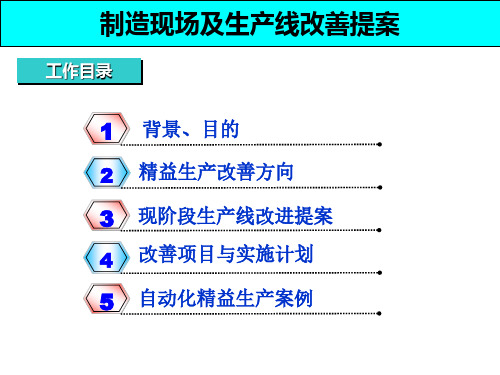
4月
5月
12341234 W W W W W W W W 参与实施人员 备注
*****
王任远 陆红 平 谢志锋
***
王任远 侯亿
设备日常保养项目,管理规范,稽 核小组形成
责任区域的划分、区域内摆放规范& 使用规范、稽核小组的形成,库内 物料盘点及物料出入库软件系统的 推广。
** ****
王任远
陆红平 莫敬 芝
400
单价(元) 总价(元)
12
4800
备注(含4 个装配小车)
扣件连接件
套
300
16
地杯与轮件.防护 个
60
8
件
导轨材料
米
40
50
4800 480
2000
脚轮 工装板
个
16
块
30
50
900
200
6000
丝印台
个
1
2000
2000
工作台面板
米
备注:生产线长7米,宽1.5米,单轨宽0.6米,中间工作台宽 0.3米,采用U型设计。
王任远 盛洁
10
11
制造现场改善提案
精益生产案例
丰田试制车间
车辆焊装工位
汽车座垫生产线
制造现场改善提案
THE END
合计:20980
使用原有台面 制作
制造现场改善提案
改善项目与实施计划
序
号
改善主题
1 生产线改善设计及实施
2 作业人员培训
日常保养制度形成工治具 的保养与管理规范制定 3
5S及现场与环境改善 4 5 6 7 8 9
规划
具体项目
完成现场规划,方案及预算评审, 物料申购与实施制作完成。
- 1、下载文档前请自行甄别文档内容的完整性,平台不提供额外的编辑、内容补充、找答案等附加服务。
- 2、"仅部分预览"的文档,不可在线预览部分如存在完整性等问题,可反馈申请退款(可完整预览的文档不适用该条件!)。
- 3、如文档侵犯您的权益,请联系客服反馈,我们会尽快为您处理(人工客服工作时间:9:00-18:30)。
5W2H
5W2H====why/what/where/when/who/ how to do/how much(many).
5.Who(何人) -----責任擔當是誰. -----誰來協助他. -----誰來指導他. -----有哪些人可以候補/替換.
5W2H
5W2H====why/what/where/when/who/ how to do/how much(many).
---流水線優點:減少搬運和空間占用.降低人員疲勞
工廠布置
生
短距離原則----工段間傳遞
產
流暢原則------單流向
固定循環原則--依流程
線
分工原則------專精熟練
布
經濟產量原則--大量
平衡原則------行云流水
置
設備零故障----保養
原
舒適原則------照明.通風.粉塵 空間應用原則--不囤積
5W2H
5W2H====why/what/where/when/who/ how to do/how much(many).
2.What(何事) -----應該做什麼事. -----哪件事最重要.
5W2H
5W2H====why/what/where/when/who/ how to do/how much(many).
研 工廠布置物料移動
究
作業區域配置
分
工廠內部與部門之間及人與物 流程圖分析
料之活動
模型配置分析
作業者位置及周圍物品的放置 方法,作業者物品移動的方法
動作研究 動作經濟原則 作業簡化原則
析
連合工程分析
組合作業或自動機作業
以組合進行的共同作業或以自 動機器作業的人機配合
工作抽樣
技
作業簡化原理
巧 作業中的作業
則
彈性原則------易換線
IE與現場改善
對 Industrial Engineering工業工程
協助以最小的投入(Input)得到最大的產出
IE
(Output),以致獲得最大的效益.
的 IE是藉著設計,改善或設定人.機.料.法的工作
認
系統,以求得到更高生產力的專門技術.
識 IE的基礎是“工作研究”
定 達到最大的工作效果的經濟法則. 義 基本原則:
---動作能量活用原則 ---動作量節約原則 ---動作改善原則
IE與現場改善
動
作 即在人的身體各部位,凡是能具有進行動作能力 能 的部分,不管任何部位,都希望能全面用到.腳部 量 或左手能操作的事,不使用右手.盡量雙手同時作
活
用 業,同時結束.雙手不要同時靜止,空閑時想下一 原 動作.
動作工改作善簡四化原則
動 四原則=====剔除/合並/重排/簡化 作 2.合並(Combination) 改 -----几項作業可否同時進行. 善 -----几項作業可否合並進行. 四 -----工程分割是否適當. 原 -----工程之間負荷平衡度如何. 則 -----檢驗工作能否合並
動作工改作善簡四化原則
法 ---生產對象<物>
研
A.從原料到成品的過程,做經濟性的探討
B.產品工程分析表/生產流程圖
究 ---生產主體<人>
A.作業規範.工作抽樣,基本動作
B.人.機配合合理性,稼動狀況分析
IE與現場改善
方 探討項目
內容
分析手法
法 制造整個工程系統
制造流程圖分析 從原料→生產→成品→出貨止
操作標準書分析
3.Where(何處) -----在哪裡做. -----由哪個班做.
5W2H
5W2H====why/what/where/when/who/ how to do/how much(many).
4.When(何時) -----什麼時候開始做. -----什麼時候完成. -----分几個階段. -----每一個階段要完成哪些事情. -----每一個階段要達成什麼目的.
4>穩定品質,改善作業秩序
的
生產線平衡法
不 1>不平衡檢討與改善
平
減少耗時最長的工序(瓶頸)(圖示說明)
衡
---作業分割
的
---利用或改良工具.機器
研
---提高機械效率
究
---提高作業技能/換人/加人
與 2>作業方法改善
改
---剔除/合并/重排/簡化
善
---布置與環境改善
作
作
業
業
時
時
間
間
工 程 A B C D EF
核定:黃淵勇 講師:鐘 傑
制作日期:2006年11月16日
課程目錄
一.改善的十種基本精神 二.改善的十大抵抗 三.常用改善手法 四.工廠布置Layout
五.IE與現場改善 六.動作經濟原則 七.工作簡化 八.生產線平衡法
一改善的十种基本精神
1.舍去原有的觀念,凡事求新求變. 2.不要找理由,而是找方法. 3.不能滿足現狀. 4.改善對策愈多愈好.,要因分析至少50點. 5.錯誤立即改正. 6.改善就是賺錢. 7.問題末改善之前不休息. 8.保持懷疑態度,連續追問5次為什麼這樣. 9.一個人的創意可供十個人共分享. 10.改善永無止境.
簡
3>看起來不合理的工作
4>布置不當或搬運不便的工作
化
(二)現狀分析及檢討
的
使用IE手法 ---工程流程圖
方
---產品/作業者工程分析
---工廠布置與搬運
法
---動作分析
工作簡化
工 (三)運用5W2H法發問
作
WHY WHAT WHERE
簡
WHEN WHO HOW TO DO
化
HOW MUCH(成本)
6.How to do(如何做) -----方法. -----工具/設備. -----步驟/要領. -----可能遇到的困難或障礙.
5W2H
5W2H====why/what/where/when/who/ how to do/how much(many).
7.How much/many(資源消耗多少) -----需要多少資源. -----需要多少資金. -----有多少事情/困難/問題.
C分割給B和D
工 程 A B C D EF
C改善縮短時間 (工具.方法.人)
生產線平衡法
作
作
業
業
時
時
間
間
工 程 A B C D EF
C增加人員
工 程 A B C D EF
B合并于A.C
生產線平衡法
作
作
業
業
時
時
間
間
工 程 A B C D EF
B分割給C E分割給D
工 程 A B C D EF
C經改善縮短時間 剩下的工作合并于B
改善的十大抵抗
1.那種東西沒有用. 2.確實是這樣,但我們公司則不同. 3.雖然是個好的方案,但. . . . . . . 4.成本無法再降低. 5.我們也一直這樣努力著. 6.不喜歡接受別人的建議而做. 7.要降低成本,品質也會降低. 8.目前不是很理想嗎?為何要改變. 9.這種方法行不通,早在20年前我們就試過. 10.我們對這件事情已清楚了.
類
9>適當姿勢原則
IE與現場改善
動
作 (二)工具設備方面
經
1>利用工具原則
濟
2>萬能工具原則----多用途
原
3>易于操作原則
則
分
4>適當位置原則
類
IE與現場改善
(三)場所布置方面 動
1>定點放置原則
作
2>雙手可及原則---(弧形)
經
3>按工排序原則---(手術工具)
濟
4>使用容器原則
原
5>用墜送法原則---(重力)
則
IE與現場改善
動
作 多余的運動量,不但浪費時間及空間,更會 量 浪費體力.動作盡量小材料及器具靠近手邊 節 盡量減少小單元的動作次數(鋰電池)
工具簡單易用材料及零件應使用易拿取之容器
約
(壓尺)
原
則
IE與現場改善
動
1>動作規律化
作
2>雙手可反向運動,不可同向運動.
改
3>利用慣性.重力.自然力等,尤其盡量
常用改善方法
一般性 ---5W2H法 ---腦力激蕩法 ---愚巧法----防呆 ---比較法
IE 7大手法
5W2H
5W2H====why/what/where/when/who/ how to do/how much(many).
1.Why(何故) -----原因是什麼. -----目的是什麼. -----目標要達到何種程度.
動 四原則=====剔除/合並/重排/簡化 作 3.重排(Rearrange) 改 -----作業順序可否重排. 善 -----工作流程可否重排. 四 -----工廠佈置可否重排. 原 -----物流線路可否改變. 則
動作工改作善簡四化原則
動 四原則=====剔除/合並/重排/簡化
作 4.簡化(Predigestion)
的 (四)動作改善四原則:
方
剔除/合并/重排/簡化
法 (五),制訂新標準/效果跟催
工作簡化
動 四原則=====剔除/合並/重排/簡化 作 1.剔除(Elimination) 改 -----此頂作業(動作)可否剔除. 善 -----此項作業經努力是否可消除掉. 四 -----可否減少工作環節或時間. 原 -----是否可以不必搬運. 則 -----是否可以減少作業人數.