计划管理-MRP计算流程
金蝶K3 MRP运算操作流程
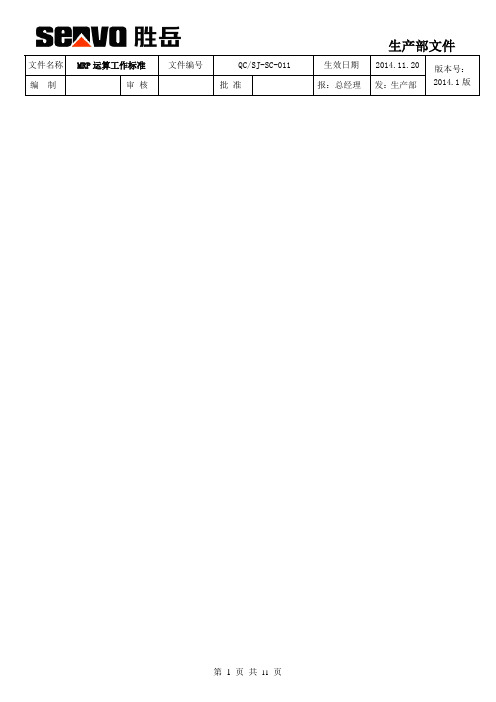
文件名称MRP运算工作标准文件编号QC/SJ-SC-011生效日期2014.11.20版本号:2014.1版编制审核批准报:总经理发:生产部1 目的:规范MRP 运算工作程序,保证MRP 运算物料采购计划的准确、及时。
2 适用范围:本制度适用于山东胜岳精密机械有限公司塑机事业部计划部物料下单工作。
3 权责:4 定义4.1 关于MRP 运算MRP 即物料需求计划(Material Requirement Planning),是指根据产品结构各层次物品的从属和数量关系(BOM ),以每个物品为计划对象,以完工时期为时间基准倒排计划,按提前期(生产、采购周期)长短区别各个物品下达计划时间的先后顺序,是一种工业制造企业内物资计划管理模式。
MRP 是根据市场需求预测和顾客订单制定产品的生产计划,然后基于产品生成进度计划,组成产品的材料结构表和库存状况,通过计算机计算所需物料的需求量和需求时间,从而确定材料的加工进度和订货日程的一种实用技术。
通过MRP ,系统对市场需求预测进行运算,即能得解决需要什么以及需求多少的问题。
4.2制订物料需求计划前就必须具备以下的基本数据:1)、第一项数据是生产计划,它指明在某一计划时间段内应生产出的各种产品和备件,它是物料需求计划制订的一个最重要的数据来源。
我们公司的生产计划一般分两种:《生产计划》和《采购计划》。
对两种计划的计算分别投放C 类和A/B 类的物料。
2)、第二项数据是物料清单(BOM),它指明了物料之间的结构关系,以及每种物料需求的数量,它是物料需求计划系统中最为基础的数据。
3)、第三项数据是库存记录,它把每个物料品目的现有库存量和计划接受量的实际状态反映出来。
4)、第四项数据是提前期,即物料的生产、采购周期。
它决定着每种物料何时开工、何时完工。
期间 项目提出 审核 审批 运算前 的准备 《主生产计划(预案)》计划部 市场部 总经理 《主生产计划》 计划部 市场部 总经理 《采购计划》 计划部 市场部 总经理 运算中 的使用 物料需求计划(MRP 运算)计划部计划部--运算完成 生成单据 《采购申请单》 计划员 计划主管 ---注:物料的提前期及A/B/C类物料的划分标准详见《物料采购周期表》。
金蝶K3MRP运算操作流程图
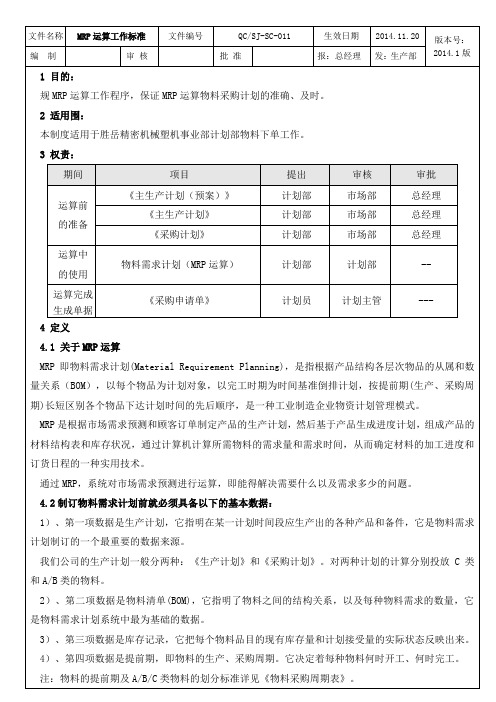
○2录入《产品预测单》:打开“产品预测单新增”后,光标放在在“物料代码”列按“F7”键,会出现机型选择界面。
按顺序选择所需要的机型,回车确认即可实现机型录入;○3确定日期: 定义:预测开始日期:指预测需求开始的日期。
预测结束日期:指预测需求结束的日期。
要求:1、“预测开始日期”即物料的要求到货日期(必须晚于运算的开始日期); 2、“预测截止日期”必须晚于“预测开始日期”,但不应超过一周。
○4将该批次的信息填入备注栏(XX 月生产计划)。
(三)、说明:通过MRP 运算《生产计划》时,《产品预测单》至少应录入两部分: a 、新增《生产计划》对应批次,是为满足下月计划需求: 产品预测单台数=《生产计划》需求台数;b 、录入在制的生产批次,是为了运算时系统抵消未完成批次的需求预测单数据来源计算方法1、抵消原有生产任务 ERP 系统《生产任务单》中“下达”状态的单据 计划生产台数-已入库台数 2、新生产计划需求 新签批的《生产计划》即《生产计划》需生产台数在制的批次的产品预测单台数=原计划生产台数-入库台数;(四)、注意,录入需求的《产品预测单》时,必须将无效的《产品预测单》关闭,防止混淆。
5.4、核实计算参数确定计算参数(位置:计划管理--物料需求计划--系统设置—MRP计算方案维护)。
具体如下:○1计算方案为MTS1(SYS);需求来源为来自产品预测单。
如下图所示:○2净需求数量=(净需求-现有库存+安全库存-预计入库量+已分配数量)。
如下图所示:○3投放参数按采购负责人分类。
如下图所示:○4仓库参数:原材料、标准件、零件、辅料仓。
如下图所示:○5启用锁单冲销算法。
如下图所示:5.5、开始运算运算步骤(一)、首先,打开“MRP计算”(位置:计划管理--物料需求计划--MRP计算--MRP计算)。
界面如下图,直接点击“下一步”;(二)、MRP运算预检查:包括“BOM单嵌套检查”、“BOM单完整性检查”、“低位码维护必须维护”。
MRP运算
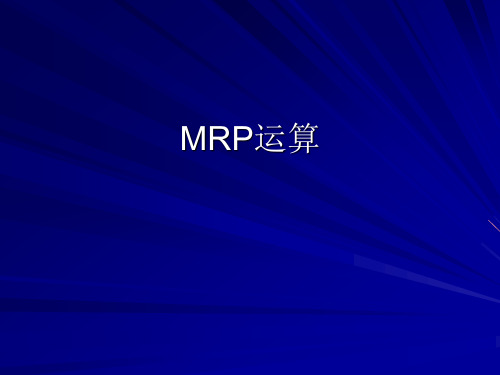
3 库存信息,物料可用量
4 还缺什么?何时定货? 4 建议的加工及采购计划
(量)
(期)
制造业的通用公式 (生产什么 用到什么) - 已有什么 = 还缺什么
快速运算
(逐级展开)
X A (1) C (2) O (1)
X
时段
MPS 计划产出量 计划投入量
A
时段
MRP 计划产出量
计划投入量
加
工C
计时段 划 计划接收量
– 根据计划产出量、提前期和合格率计算的投入数量 – 安排产品什么时候开始生产;
毛需求量
净需求量
客戶需B求rowser
销售预销测售部门订单
预计可用 库存量
计划投入量
计划员
工厂
生产
计划产出量
入库
发运
成品仓库
计划接收量
返回
结构层次 0
10000
方桌 销售X件
件 1.0
独立需求件 相关需求件
产品结构树
X[1]
Y[1]
MRP
MPS
B(1)
C
D(2)
B(1)
U
E(2)
MRP
B(3) F(3)
X
提前期=1 批量=1 现有量=0
时段 4 5 6 7 89
计划产出量
10
计划投入量
10
时段 毛需求
4 5 6 7 89 10
H(3) F(3)
Y
提前期=1 批量=1 现有量=0
时段 4 5 6 7 89
计划产出量
10
10
10
10
10
5
提前期=1
现有量=0
1 2 3 4 5 6 7 8 9 10 11 12
金蝶MRP计算及投放操作流程
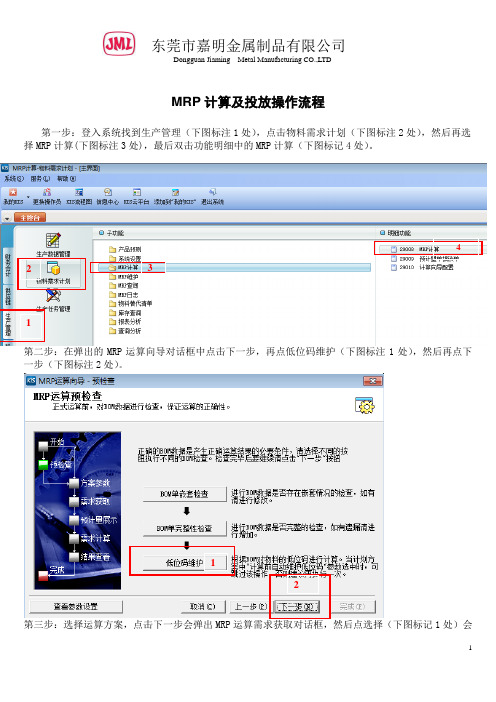
MRP计算及投放操作流程
第一步:登入系统找到生产管理(下图标注1处),点击物料需求计划(下图标注2处),然后再选择MRP计算(下图标注3处),最后双击功能明细中的MRP计算(下图标记4处)。
4
2 3
1
第二步:在弹出的MRP运算向导对话框中点击下一步,再点低位码维护(下图标注1处),然后再点下一步(下图标注2处)。
1
2
第三步:选择运算方案,点击下一步会弹出MRP 运算需求获取对话框,然后点选择(下图标记1处)会
弹出销售订单序时簿,可以根据模糊条件查询(下图标注2处),筛选自己需求订单,选好后点返回。
然后点下一步,最后点完成。
此订单MRP 运算完成。
第四步:<对MRP 计划订单进行投放生成采购申请单> 登入系统找到生产管理(下图标注1处),点击物料需求计划(下图标注2处),然后再选择MRP 维护(下图标注3处),最后双击功能明细中的MRP 计划订单-维护(下图标记4处),输入筛选条件进行筛选,然后对需外购的计划的进行审核投放。
1 2 1
3
4
5
2。
mrp物料需求计划步骤

mrp物料需求计划步骤一、概述MRP(Material Requirements Planning,物料需求计划)是一种计算工具,可以帮助企业进行物料需求的计划和控制。
它可以根据销售订单、生产计划等信息,自动计算出所需的原材料、零部件等物料,并提供采购、生产等决策支持。
二、步骤1. 建立物料清单(BOM)BOM是指产品的物料清单,包括所有需要用到的原材料、零部件等。
建立BOM是MRP计算的基础,必须准确无误。
BOM应该包括物料编号、名称、数量等信息。
2. 收集需求信息MRP需要收集销售订单、生产计划等信息来进行计算。
销售订单包括客户订购的产品数量和交货时间;生产计划包括要生产的产品数量和交货时间。
3. 计算净需求量净需求量是指需要采购或生产的物料数量。
它由销售订单和生产计划决定,通过减去已有库存量得出。
如果库存不足,则需要采购或生产。
4. 计算批量大小批量大小是指每次采购或生产所需的最小数量。
它由供应商提供的最小订购量、生产设备的最小生产数量等因素决定。
批量大小应该尽可能小,以减少库存和成本。
5. 计算采购或生产计划根据净需求量和批量大小,计算出采购或生产的计划。
如果需要采购,则需要考虑供应商的交货时间、运输时间等因素;如果需要生产,则需要考虑工艺流程、设备利用率等因素。
6. 更新库存信息采购或生产完成后,需要更新库存信息。
如果有多个仓库,则需要分别记录每个仓库的库存情况。
同时,还需要记录每个物料的最大和最小库存量,以便及时补充或清理过多的库存。
7. 监控和调整计划MRP是一个动态的过程,需求信息、供应商情况等都可能发生变化。
因此,需要不断监控和调整计划,以保证物料供应充足、成本最低。
三、注意事项1. MRP计算结果只是一种参考,不是绝对的规定。
实际操作中还需考虑人力资源、设备利用率等因素。
2. MRP计算涉及到大量数据,必须保证数据准确无误。
3. MRP计算应该根据企业实际情况进行调整,不能照搬别人的做法。
运营管理物料需求计划MRP

运营管理物料需求计划MRP运营管理物料需求计划(MRP)是一个重要的供应链管理工具,用于规划和控制物料的采购和生产,以确保企业按时、按量地满足客户的需求。
本文将详细介绍MRP的定义、目的、步骤以及如何有效执行MRP计划,以提高运营效率和客户满意度。
一、MRP的定义和目的MRP是基于主生产计划(MPS)和物料清单(BOM)的需求计划工具,用于计划所需的原材料、零部件和子装配件,以满足最终产品的生产需求。
其目的是最大程度地减少库存成本、提高生产和交付的效率,并确保生产计划的准确性和及时性。
二、MRP的步骤1.确定MPS: MPS是基于业务需求和销售预测的生产计划,包括产品类型、数量和交付时间等信息。
根据MPS,确定所需零部件和原材料的清单。
2.制定物料清单:物料清单列出了每个产品所需的零部件、原材料和子装配件。
清单中包括每个物料的名称、数量和所需交付时间。
3.确定库存水平:通过分析历史销售数据和预测需求,确定所需的库存水平。
这可以帮助企业避免过高或过低的库存。
4.计算净需求:通过比较MPS和物料清单,计算出每个零部件和原材料的净需求量。
净需求量等于所需数量减去库存量。
5.制定采购计划:根据净需求量,制定采购计划,包括采购数量、采购日期和供应商信息。
采购计划应与供应商进行沟通,并确保及时供货。
6.制定生产计划:根据净需求量,制定生产计划,包括生产数量、生产日期和生产线信息。
生产计划应与生产部门进行沟通,并确保生产线的协调运作。
7.监控执行情况:定期监控采购和生产的执行情况,确保按计划进行,并及时调整计划,以应对突发情况和变化的需求。
三、执行MRP计划的注意事项1.有效的信息共享:确保MPS、物料清单和库存数据的准确性和及时性。
各部门之间应进行有效的沟通和协作,以便及时了解所需物料的变化。
2.建立稳定的供应链合作关系:与供应商建立长期合作关系,以确保稳定的供货和优惠的价格。
同时,与生产部门建立良好的合作关系,以确保生产计划的顺利执行。
【ERPMRP管理】MRP运算
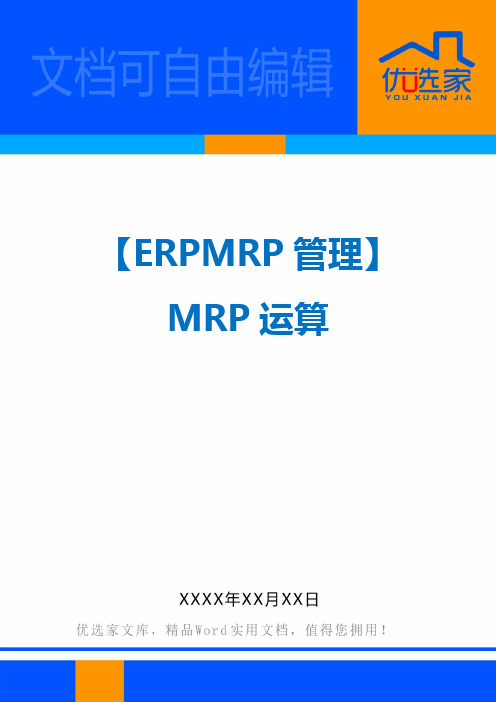
【ERPMRP管理】MRP运算MRP在软件中的概念是物料需求计划(Material Requirement Planning),它的作用是将指定的订单中所需要的原材料的用量做统计,以使生产部门、仓库了解当前生产这些产品需要多少的原材料,这是因为在一般的工业企业里,产成品它是有很多的原材料组成的(即在ERP里称之为BOM),但是在下订单时,一般只会选择某一个产成品,而不会列出它是由哪些原材料组成的,不过到生产部门时,他们所要关心的是生产产品时所需的原材料数量,而并非单单的产品数量,所以此时MRP 运算的作用可以体现出来了。
一、基本逻辑净需求=毛需求+预计出-预计入-期初库存+安全库存可按自由项匹配相应的BOM分解,如找不到相应的BOM,系统按默认版本BOM分解虚项及生成子订单物料不生成计划订单,按净需求分解下级物料二、MRP的基本任务1.从最终产品的生产计划(独立需求)导出相关物料(原材料、零部件等)的需求量和需求时间(相关需求);2.根据物料的需求时间和生产(订货)周期来确定其开始生产(订货)的时间。
三、主生产计划主生产计划是确定每一具体的最终产品在每一具体时间段内生产数量的计划。
这里的最终产品是指对于企业来说最终完成、要出厂的完成品。
通常包括如下内容:1、要生产什么东西?2、什么时候需要?3、要生产多少?主生产计划是独立需求,主要是根据客户合同或者对市场的预测,把在一定时期内需要生产的产品一一预测,使之成为展开物料需求计划的主要依据。
主生产计划是MRP的源头,所以,其的重要性是不言而喻的。
若其包含的以上三个主要参数有错误,则下面的计算肯定是错误的。
所以,主生产计划编制时,一定要准确,否则,不但不能给企业带来效益,反而会给企业带来损失。
NC对主生产计划的说明:包括主需求计划和主生产计划,可满足工业企业生产计划制定与管理的要求,并提供主生产计划的生成模拟与能力分析。
主需求计划是主生产计划的驱动数据,其主要来源是销售订单与销售预测,并可在不同的时区设定不同的需求合并策略。
金蝶K3-MRP运算操作流程

文件名称MRP运算工作标准文件编号QC/SJ-SC-011生效日期2014.11.20版本号:2014.1版编制审核批准报:总经理发:生产部1 目的:规范MRP 运算工作程序,保证MRP 运算物料采购计划的准确、及时。
2 适用范围:本制度适用于山东胜岳精密机械有限公司塑机事业部计划部物料下单工作。
3 权责:4 定义4.1 关于MRP 运算MRP 即物料需求计划(Material Requirement Planning),是指根据产品结构各层次物品的从属和数量关系(BOM ),以每个物品为计划对象,以完工时期为时间基准倒排计划,按提前期(生产、采购周期)长短区别各个物品下达计划时间的先后顺序,是一种工业制造企业内物资计划管理模式。
MRP 是根据市场需求预测和顾客订单制定产品的生产计划,然后基于产品生成进度计划,组成产品的材料结构表和库存状况,通过计算机计算所需物料的需求量和需求时间,从而确定材料的加工进度和订货日程的一种实用技术。
通过MRP ,系统对市场需求预测进行运算,即能得解决需要什么以及需求多少的问题。
4.2制订物料需求计划前就必须具备以下的基本数据:1)、第一项数据是生产计划,它指明在某一计划时间段内应生产出的各种产品和备件,它是物料需求计划制订的一个最重要的数据来源。
我们公司的生产计划一般分两种:《生产计划》和《采购计划》。
对两种计划的计算分别投放C 类和A/B 类的物料。
2)、第二项数据是物料清单(BOM),它指明了物料之间的结构关系,以及每种物料需求的数量,它是物料需求计划系统中最为基础的数据。
3)、第三项数据是库存记录,它把每个物料品目的现有库存量和计划接受量的实际状态反映出来。
4)、第四项数据是提前期,即物料的生产、采购周期。
它决定着每种物料何时开工、何时完工。
期间 项目提出 审核 审批 运算前 的准备 《主生产计划(预案)》计划部 市场部 总经理 《主生产计划》 计划部 市场部 总经理 《采购计划》 计划部 市场部 总经理 运算中 的使用 物料需求计划(MRP 运算)计划部计划部--运算完成 生成单据 《采购申请单》 计划员 计划主管 ---注:物料的提前期及A/B/C类物料的划分标准详见《物料采购周期表》。
计划管理-MPS MRP计算流程

主生产计划报表(周计划)料号:01.01.01料名:主板计划员:张三计划日期:维度/规格:计量单位:PCS可用库存:10安全库存:提前期:7提前期单位:天批量:10批量规则:需求时届:3计划时届:7一.名词解释1.批量规则(Lot sizing rules)1).最大批量:当计划下达量大于此批量时,取此批量作为计划下达量。
2).最小批量:当计划下达量小于此批量时,取此批量作为计划下达量。
3).固定批量:订货计划数量,按照固定值下达。
4).直接批量:按照计划或实际的需求决定订货量。
5).固定周期批量:间隔周期相同,按照周期内计划或实际的需求决定订货量。
6).周期批量:根据经济订货批量(EOQ)计算间隔期,按照间隔内的计划或实际的需求决定订货量。
7).批量倍数:如果需求量小于批量,则按批量计算。
如果需求量大于批量,则按照批量倍数计算。
2.批量:按照批量订货时的订货数。
3.批量周期:按照周期批量订货时,订货的周期。
4.毛需求量(Gross requirements):指初步的需求数量。
5.计划接收量(Schedule receipts):已经下达的订单,在将来某段时间产出的数量。
6.预计可用库存量(Projected available balance-PAB):某段时间的期末库存量,要扣除用于需求的预计可用库存量=前段时间预计可用库存+本时段计划接收量-本时段毛需求量+本时段计7.净需求量(Net requirements):净需求量=本阶段毛需求量-前一阶段末可用库存量(计划产出量-净需求)-本阶段的计划接收量+安全库8.计划产出量(Plan order receipts):当需求不能满足时,根据批量规则计算出来的供应数量。
它9.计划投入量(Plan order releases):根据计划产出量,提前期以及合格率等计算出来的投入数量10.可供销售量(Available to promise - ATP):某段时间物品的产出量可能大于订单或合同的数量,可供销售量=某时段的计划产出量(包括计划接收量)-这段时间的订单或合同量之和二.计算过程1.计算毛需求1,2,3时段处于时区1,毛需求等于订单数量;4,5,6,7时段处于时区2,毛需求等于订单与预测数量的最2.计算(读取)计划接收量和过去库存量(预计库存)3.计算预计可用库存量 预计可用库存量=前段时间预计可用库存+本时段计划接收量-本时段毛需求量4.计算净需求量和计划产出量净需求量=本阶段毛需求量-前一阶段末可用库存量-本阶段的计划接收量+安全库存量对第一个零或负的计划可用库存量的时段计算出净需求(考虑安全库存),然后考虑批量计算出计划产5.根据提前期和成品率计算计划投入量和可供销售量可供销售量=某时段的计划产出量(包括计划接收量)-这段时间的订单或合同量之和表(周计划)2013-8-315固定批量678910 10月5日10月12日10月19日10月26日11月2日303225302016352028253035253020116111111242924241430303030203030302014-5102划或实际的需求决定订货量。
MRP的几种公式

MRP的几种公式1.净需求量=订单量*BOM(或叫毛需求量)-库存量-己分配量+在途量+安全库存量或:净需求量=(毛需求量-库存量-己分配量+在途量+安全库存量)*(1+损耗率)如不考虑安全库存,则该项为零。
还要考虑不可用量 ......2.毛需求量-库存量-己分配量+计划交付量,如果当前库存量包括了安全库存量的话可以不考虑(看企业物料管理的实际情况而定)3.MRP 通用计算公式:净需求=毛需求+已分配量+安全库存-计划在途-实际在途-可用库存毛需求量: 不考虑库存、制造、采购的需求量,相对于净需求而言。
如果是独立需求,那么毛需求= 主生产计划需求量/(1 –料品不良率)。
如果是相关需求,那么毛需求= 上层料品的下达量。
其中独立需求是指某一存货项目的需求与其他项目需求没有关联4.我的理解为:物料需求数量=(所有销售订单欠货量-产品库存) X 相关BOM表物料用量- 物料库存- 采购订单欠料量如果分析所有销售订单的话这个公式计算出来的物料需求数量是正确的,但是如果只要分析其中一张销售订单,就不知要怎样计算物料需求数量了要考虑计划采购量更有一个物料可用量物料可用量=现库存中的物料可以分配的数量(不是现库存数量)在任何一个订单来时,按BOM算出物料需求数量,与物料可用量相比即可关键是算物料可用量物料可用量=库存量+(计划采购量+已采购量-计划生产量*BOM-已生产量*BOM)MRP 通用计算公式MRP 通用计算公式:净需求=毛需求+已分配量+安全库存-计划在途-实际在途-可用库存毛需求量: 不考虑库存、制造、采购的需求量,相对于净需求而言。
如果是独立需求,那么毛需求= 主生产计划需求量/(1 –料品不良率)。
如果是相关需求,那么毛需求= 上层料品的下达量。
其中独立需求是指某一存货项目的需求与其他项目需求没有关联MRP 概念MRP 通用计算公式:净需求=毛需求+已分配量+安全库存-计划在途-实际在途-可用库存毛需求量: 不考虑库存、制造、采购的需求量,相对于净需求而言。
mrp运算操作流程

mrp运算操作流程English Answer:MRP (Material Requirements Planning) is a production planning and inventory control system used to manage the manufacturing process. It helps manufacturers determine the materials and components needed to produce a finished product, and the timing of those needs. MRP systems are typically used in conjunction with ERP (Enterprise Resource Planning) systems, which provide a broader view of the entire manufacturing process.The MRP process typically involves the following steps:1. Develop a master production schedule (MPS). The MPS is a detailed plan of the production quantities and timing for each finished product.2. Create a bill of materials (BOM). The BOM is a list of all the materials and components required to produceeach finished product.3. Calculate gross requirements. Gross requirements are the total amount of each material or component needed to produce the MPS.4. Calculate net requirements. Net requirements are the gross requirements minus any existing inventory or on-order inventory.5. Schedule receipts. Receipts are scheduled to ensure that materials and components are available when needed.6. Monitor and adjust. The MRP process is monitored and adjusted on a regular basis to ensure that it is meeting the needs of the production process.MRP systems can be complex, but they can provide a number of benefits, including:Improved inventory management.Reduced lead times.Increased productivity.Improved customer service.Chinese Answer:物料需求计划(MRP)是一种生产计划和库存控制系统,用于管理制造过程。
MRP运算规则
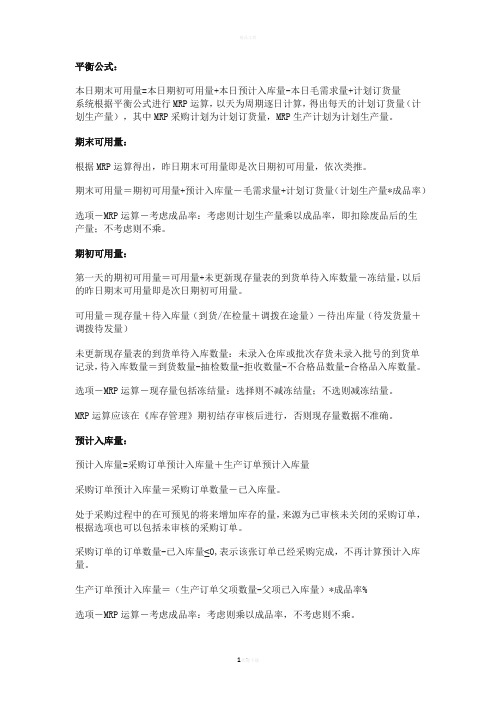
平衡公式:本日期末可用量=本日期初可用量+本日预计入库量-本日毛需求量+计划订货量系统根据平衡公式进行MRP运算,以天为周期逐日计算,得出每天的计划订货量(计划生产量),其中MRP采购计划为计划订货量,MRP生产计划为计划生产量。
期末可用量:根据MRP运算得出,昨日期末可用量即是次日期初可用量,依次类推。
期末可用量=期初可用量+预计入库量-毛需求量+计划订货量(计划生产量*成品率)选项-MRP运算-考虑成品率:考虑则计划生产量乘以成品率,即扣除废品后的生产量;不考虑则不乘。
期初可用量:第一天的期初可用量=可用量+未更新现存量表的到货单待入库数量-冻结量,以后的昨日期末可用量即是次日期初可用量。
可用量=现存量+待入库量(到货/在检量+调拨在途量)-待出库量(待发货量+调拨待发量)未更新现存量表的到货单待入库数量:未录入仓库或批次存货未录入批号的到货单记录,待入库数量=到货数量-抽检数量-拒收数量-不合格品数量-合格品入库数量。
选项-MRP运算-现存量包括冻结量:选择则不减冻结量;不选则减冻结量。
MRP运算应该在《库存管理》期初结存审核后进行,否则现存量数据不准确。
预计入库量:预计入库量=采购订单预计入库量+生产订单预计入库量采购订单预计入库量=采购订单数量-已入库量。
处于采购过程中的在可预见的将来增加库存的量,来源为已审核未关闭的采购订单,根据选项也可以包括未审核的采购订单。
采购订单的订单数量-已入库量≤0,表示该张订单已经采购完成,不再计算预计入库量。
生产订单预计入库量=(生产订单父项数量-父项已入库量)*成品率%选项-MRP运算-考虑成品率:考虑则乘以成品率,不考虑则不乘。
处于生产过程中的在可预见的将来增加库存的量,来源为已审核未关闭的生产订单,根据选项也可以包括未审核的生产订单。
生产订单的订单数量-已入库量≤0,表示该张订单已经生产完成,不再计算预计入库量。
毛需求量:毛需求量=订单/预测单毛需求量+BOM展开子项毛需求量+生产订单子项毛需求量销售订单、预测单,即当天的销售订单量、市场预测量,根据选项取值。
【ERPMRP管理】MRP运算逻辑
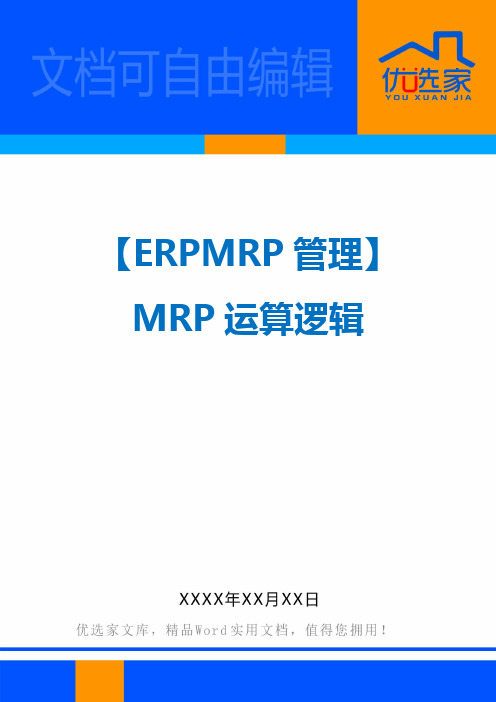
【ERPMRP管理】MRP运算逻辑基本MRP的运算逻辑基本MRP的运算逻辑图如图所示:图1 MRP运算逻辑图下面结合实例说明MRP的运算逻辑步骤。
如图2是产品A的结构图。
图2 A产品结构图于是,现在我们就可以计算各个产品及相应部件的需求量。
要注意的是,由于提前期的存在,使得物料的计划交付时间和净需求的时间有时会产生不一致。
另外,我们为了简化计算,也暂时没有将安全库存量考虑在内。
表1 产品A的需求量计算(产品A,提前期=2,批量=10)以上计算过程表明虽然1,2,4,6周均需要A,但实际A只要3及4周交付10个即可以了。
这个计划下达时间和数量就是部件B和C的毛需求的时间和数量。
表2 部件B的需求量计算(部件B,提前期=1,批量=20,1A=2B=2´10=20)表3 部件C的需求量计算(部件C,提前期=3,批量=60,1A=3C=3´10=30)从这一层的分解可以看出,对于部件B,它还在需要在第3周交付个10个,为此我们还要按照产品结构展开下一层的分解。
分解方法和步骤如前,这里我们就不一一展开了。
经过了以上的展开计算后,我们就可以得出产品A的零部件的各项相关需求量。
然而,现实中企业的情况远没有这样简单,在许多加工制造性的企业中,由于产品种类繁多,并不只是产品A要用到部件B、部件C以及零件D和E,可能还有其他产品也需要用到它们,也可能零件D、E还有一定的独立需求(如作为服务件用的零件等)。
所以,MRP要做的工作是要先把企业在一定时段内对同一零部件的毛需求汇总,然后再据此算出它们在各个时段内的净需求量和计划交付量,并据以安排生产计划和采购计划。
这里为了解释它的原理,我们可以假设,企业还有产品X要用到零件D,此外,零件D还有一定的独立需求。
则对零件D的总需求计算如图3所示。
求得了零件D的总需求量,我们就可以根据前面介绍的原理,进一步计算出该零件总的净需求量和计划交付量,由此,有关的生产计划和采购计划就能够在适当的时间给予安排。
MRP、SRP、生产订单流程图

ERP-MO03
业务流程名称
生产订单(制令)流程图
责任部门
岗位
流程图
流程描述
表单
权限
手动自动下单
改制产品
商务
生产
信息中心
生产
商务
生管
信息中心
生管
1.手动录入生产订单,确认存货,和数量,订单类别,开工日期,完工日期,生产部门,审核确认后,并进行MRP计划;
2.根据己审核的销售订单进行MRP计划或SRP计划自动生成生产订单;
3.手动录入预测的生产订单,
4.需求规划的运算定在每周五下班之前运算,请相关部门务必确认相关数据的准确,出入库单据要审核完毕,单据需要关闭务必关闭;
5.MRP计划前稽核作业,
6.MRP运算,MRP计划生成,按执行即可,系统自动计算,计算成功,会报信息“MRP运算成功”,如报“错误信息”,请查看“自动规划错误信息表”中错误信息,并通知相关部门修正,且MRP计划整批删除,重新进行MRP计划。
MRP计划维护
生产订单自动生成
业务流程编号
ERP-MO01
业务流程名称
MRP运算流程图
责任部门
岗位
流程图
流程描述
表单
权限
商务
生产部
档案室
信息中心
生产部
商务
生管
档案室
信息中心
生管
1.商务的销售订单务必在MRP运算前录入并审核完毕完成销售订单相应的产品BOM表,
5.在生产订单处理中审核生产订单,可以批量审核。
改制的产品:将仓储的现有存货改制成其他产品。
1.手动录入生产订单,类型选择非标准,确认存货,和数量,订单类别,开工日期,完工日期,生产部门;子件(也就是用料)可以随便选择包括要生产东西的本身。
(ERPMRP管理)MRP运算

一、MRP在软件中的概念是物料需求计划(Material Requirement Planning),它的作用是将指定的订单中所需要的原材料的用量做统计,以使生产部门、仓库了解当前生产这些产品需要多少的原材料,这是因为在一般的工业企业里,产成品它是有很多的原材料组成的(即在ERP里称之为BOM),但是在下订单时,一般只会选择某一个产成品,而不会列出它是由哪些原材料组成的,不过到生产部门时,他们所要关心的是生产产品时所需的原材料数量,而并非单单的产品数量,所以此时MRP运算的作用可以体现出来了。
二、基本逻辑净需求=毛需求+预计出-预计入-期初库存+安全库存可按自由项匹配相应的BOM分解,如找不到相应的BOM,系统按默认版本BOM分解虚项及生成子订单物料不生成计划订单,按净需求分解下级物料三、MRP的基本任务1.从最终产品的生产计划(独立需求)导出相关物料(原材料、零部件等)的需求量和需求时间(相关需求);2.根据物料的需求时间和生产(订货)周期来确定其开始生产(订货)的时间。
四、主生产计划主生产计划是确定每一具体的最终产品在每一具体时间段内生产数量的计划。
这里的最终产品是指对于企业来说最终完成、要出厂的完成品。
通常包括如下内容:1、要生产什么东西?2、什么时候需要?3、要生产多少?主生产计划是独立需求,主要是根据客户合同或者对市场的预测,把在一定时期内需要生产的产品一一预测,使之成为展开物料需求计划的主要依据。
主生产计划是MRP的源头,所以,其的重要性是不言而喻的。
若其包含的以上三个主要参数有错误,则下面的计算肯定是错误的。
所以,主生产计划编制时,一定要准确,否则,不但不能给企业带来效益,反而会给企业带来损失。
NC对主生产计划的说明:包括主需求计划和主生产计划,可满足工业企业生产计划制定与管理的要求,并提供主生产计划的生成模拟与能力分析。
主需求计划是主生产计划的驱动数据,其主要来源是销售订单与销售预测,并可在不同的时区设定不同的需求合并策略。
金蝶-K3-MRP-操作流程
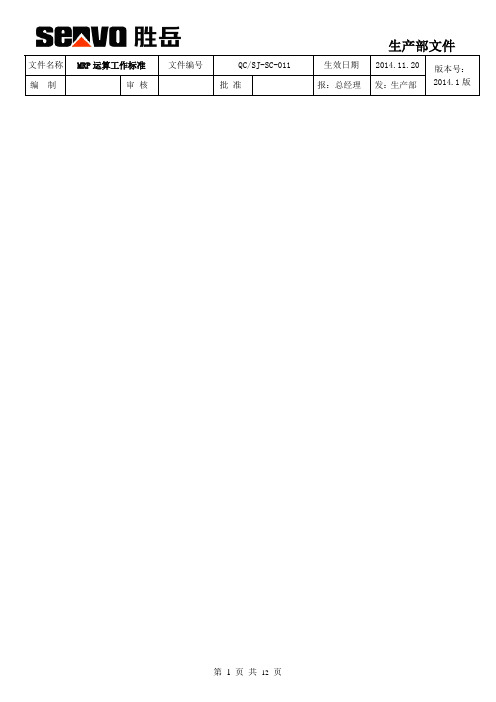
文件名称MRP运算工作标准文件编号QC/SJ-SC-011生效日期2014.11.20版本号:2014.1版编制审核批准报:总经理发:生产部1 目的:规范MRP 运算工作程序,保证MRP 运算物料采购计划的准确、及时。
2 适用范围:本制度适用于山东胜岳精密机械有限公司塑机事业部计划部物料下单工作。
3 权责:4 定义4.1 关于MRP 运算MRP 即物料需求计划(Material Requirement Planning),是指根据产品结构各层次物品的从属和数量关系(BOM ),以每个物品为计划对象,以完工时期为时间基准倒排计划,按提前期(生产、采购周期)长短区别各个物品下达计划时间的先后顺序,是一种工业制造企业内物资计划管理模式。
MRP 是根据市场需求预测和顾客订单制定产品的生产计划,然后基于产品生成进度计划,组成产品的材料结构表和库存状况,通过计算机计算所需物料的需求量和需求时间,从而确定材料的加工进度和订货日程的一种实用技术。
通过MRP ,系统对市场需求预测进行运算,即能得解决需要什么以及需求多少的问题。
4.2制订物料需求计划前就必须具备以下的基本数据:1)、第一项数据是生产计划,它指明在某一计划时间段内应生产出的各种产品和备件,它是物料需求计划制订的一个最重要的数据来源。
我们公司的生产计划一般分两种:《生产计划》和《采购计划》。
对两种计划的计算分别投放C 类和A/B 类的物料。
2)、第二项数据是物料清单(BOM),它指明了物料之间的结构关系,以及每种物料需求的数量,它是物料需求计划系统中最为基础的数据。
3)、第三项数据是库存记录,它把每个物料品目的现有库存量和计划接受量的实际状态反映出来。
4)、第四项数据是提前期,即物料的生产、采购周期。
它决定着每种物料何时开工、何时完工。
期间 项目提出 审核 审批 运算前 的准备 《主生产计划(预案)》计划部 市场部 总经理 《主生产计划》 计划部 市场部 总经理 《采购计划》 计划部 市场部 总经理 运算中 的使用 物料需求计划(MRP 运算)计划部计划部--运算完成 生成单据 《采购申请单》 计划员 计划主管 ---注:物料的提前期及A/B/C类物料的划分标准详见《物料采购周期表》。
mrp处理逻辑或计算方法

mrp处理逻辑或计算方法一、MRP处理逻辑概述。
1.1 MRP的基本概念。
MRP啊,就是物料需求计划。
这可是企业生产管理里相当重要的一个东西呢。
简单来讲,它就像是企业生产的一个大管家,把生产过程中需要的物料都安排得明明白白的。
企业要生产产品,就需要各种各样的原材料、零部件啥的,MRP就是负责计算到底需要多少这些东西,什么时候需要。
这就好比咱们居家过日子,要做一顿大餐,得提前想好需要买多少肉、多少菜,啥时候去买,MRP在企业里干的就是这事儿。
1.2 为啥要有MRP。
你想啊,要是企业没有这么个东西,那生产可就乱套了。
可能会出现原材料买多了,积压在仓库里,占用资金不说,还可能会因为存放时间长而损坏。
或者是原材料买少了,生产到一半没料了,那生产线就得停工,这就好比做饭做一半发现没盐了,多闹心啊。
所以说,MRP就是为了让企业的生产能够有条不紊地进行,做到“心中有数”。
二、MRP的计算方法。
2.1 需求计算。
首先呢,得确定产品的生产数量。
这是基础,就像盖房子得先知道要盖多大的房子一样。
根据这个生产数量,再去分析产品的物料清单(BOM)。
这个BOM就像是产品的“族谱”,清楚地列出了生产这个产品需要哪些零部件、原材料,以及它们之间的层级关系。
比如说生产一辆汽车,BOM里就会有发动机、轮胎、车身这些大部件,发动机又由各种小零件组成,这都得在BOM里体现出来。
然后根据BOM和生产数量,就能算出生产这些产品总共需要多少各种物料了。
这一步可不能马虎,要是算错了,那后面可就全乱套了,就像搭积木,要是第一步基础的积木数量都没算对,那这个积木肯定搭不成想要的样子。
2.2 时间计算。
算出需要多少物料还不够,还得知道啥时候需要这些物料。
这就涉及到生产周期、采购周期这些时间因素了。
比如说生产一个零件需要3天,采购原材料需要5天,那就要提前安排好时间,确保在生产开始前,原材料和零件都能到位。
这就像赶火车,你得提前知道火车啥时候开,然后计算好从家到车站需要多长时间,这样才能顺利坐上火车。
计划管理-MPS_MRP计算流程 - 副本

9月8日 9月15日 150 140来自计划起始日需求时界
135 150 25 150
125 150 35 120
95 120 35 150
140 150 20 150
140 150 20 180
25 150
计划时区)
7 10月12日 32
时区3(预测时区)
8 25 9 30 28 30 10 X A(2) C(2) D(1) B(2) 20
时区3(预测时区)
8 9 10
10月19日 10月26日 11月2日 60 40 0
计划截止日
计划时界
60 60 10 60
60 60 10 40
40 40 10 0
0 0 10 0
计划时区)
7 10月12日 120
时区3(预测时区)
8 9 10
计划截止日
计划时界
10月19日 10月26日 11月2日 80 0 0
类型
计算公式
计算 编号 步骤
(=母件需求数量*用量) (=毛需求C-前一段末可用库存量E-本时段计划 接收量D+安全库存J (=本时段净需求量,考虑批量) (=前一时段末可用量E+本时段计划接收量D+本 时段产出量G-本时段毛需求C (=时段的计划产出量+计划接收量-下一次出现 计划产出量(接收量)时段前全部的订单量之
40 60 30 0
-20 0 30 0
计划时区) 计划时界
7 10月12日 45
时区3(预测时区)
8 9 10
计划截止日
10月19日 10月26日 11月2日 15 60 0
计划时区)
7 10月12日 165
时区3(预测时区)
- 1、下载文档前请自行甄别文档内容的完整性,平台不提供额外的编辑、内容补充、找答案等附加服务。
- 2、"仅部分预览"的文档,不可在线预览部分如存在完整性等问题,可反馈申请退款(可完整预览的文档不适用该条件!)。
- 3、如文档侵犯您的权益,请联系客服反馈,我们会尽快为您处理(人工客服工作时间:9:00-18:30)。
MRP计算流程
一. MRP的基本原理
1. 由最终产品的主生产计划导出有关物料的需求量和需求时间;
2. 根据物料的提前期确定投产和订货时间;
二.数据来源
1.MPS结果数据;
2.不包含在MPS中的独立需求数据;
三.依据的关键信息
1.MPS结果;
2.BOM;
3.库存;
四.计算模型
1. 低层码
1)概念:最上层为0层,下一层为1层,如此类推。
当一个物品在多个产品中所处的产品结构层次不同或在同一产取处在最低层的层级码作为该物品的低层码(取数字最大的层级码),低层码在MRP中是唯一的。
如
2)作用:MRP计算时,是从0层开始,按照物品低层码的数字从小到大的物料顺序进行计算。
如果计算时所在的层暂时存储起来,总的需求量可以进行汇总存储,但是不进行MRP需求计算(计算毛需求量、预计可用
才进行MRP计算和库存分配。
这样的机制保证了可用库存优先分配给最底层的物料,避免了晚需求的物品提前下达2. 计算模型
MPS物品:Y1 提前期:1周
周份123456
需求数量1008070
MRP:物品B 提前期:1周
周份期初123456
粗需求数量1008070
计划接受量120
预计可用存量153********
计划产出量120
计划投入量120
3.确认MRP:通过能力需求计划校验其可执行性。
在订单下达之前,计划人员应该检查:
1)物料需求日期是否发生变化;
2)工作中心的能力是否有效;
3)机器设备是否备好;
4)其它;
五.MRP报表:与MPS报表类似
料号:01.01.01料名:主板计划员:张三计划日期:2013-8-31维度/规格:计量单位:PCS可用库存:10安全库存:5
提前期:7天批量:10批量规则:固定批量批量周期:
需求时届:3计划时届:7
备注:毛需求来自MPS或独立销售需求
产品结构层次不同或在同一产品中但是处于不同产品结构层次时,
的。
如:根据上图所示D物品的低层码是2.
行计算。
如果计算时所在的层级码小于该物品的层级码,那么先把此物品的需求量
计可用库存量等)和原材料的库存分配。
只有当MRP计算层级码大于等于该物品的低层码时,
避免了晚需求的物品提前下达计划占用了库存,当然是否分配库存物料的需求日期。
低层码是MRP的计算顺序。
顺序。