300T转炉课程设计说明书
300吨转炉炼钢工艺操作规程

300吨转炉炼钢工艺操作规程一、前期准备工作1.确认炼钢转炉的容量和炉内清洁度,准备好所需的原料和辅助材料。
2.对于炉缸砖、吹氧工艺和氧枪的检查、维护和更换工作要做到位。
3.确认好吹氧的工艺参数和流量。
4.对于所需取样检验的项目和方法进行确认和准备。
5.工作人员进行相关设备的检查、试车和操作培训。
6.开始生产前,进行安全会议,明确操作规程和安全措施。
二、炼钢工艺操作1.转炉预热a.打开转炉排放系统,排除转炉内部的杂质,确保转炉内部干净。
b.将预热氧气引入转炉,预热炉缸砖和炼钢转炉。
2.加入铁水a.逐步将铁水加入转炉,注意加入速度和均匀性。
b.记录加铁时间、数量和铁水成分,以备后续分析。
3.加入废钢和废铁a.根据炼钢配料列表,逐步加入所需的废钢和废铁。
b.注意废钢和废铁的化验报告,确保加入的质量合格。
4.吹氧炼钢a.在加入铁水和废钢后,开始吹氧炼钢。
b.根据设定的工艺参数和流程,控制氧气的流量和时间。
5.取样检验a.在炼钢过程中,定时取样并送至实验室检验。
b.检验项目包括成分、温度、气体成分等。
6.调整炼钢过程a.根据取样结果,及时调整工艺参数,确保炼钢质量。
b.与实验室和现场操作人员密切合作,保证炼钢过程的稳定性和质量。
7.出钢a.在炼钢完成后,开始出钢。
b.出钢的时间、温度和成分要做好记录。
8.清洁转炉a.在炼钢结束后,对转炉内部进行清洁和检查。
b.确保下一次炼钢的顺利进行。
三、结束工作1.整理资料a.对于生产过程和取样检验的数据进行整理和归档。
b.确保质量信息的完整和可追溯性。
2.设备维护a.对于炼钢设备进行维护和保养。
b.准备好下一次炼钢生产的准备工作。
3.安全检查a.进行安全设备和设施的检查和维护。
b.对生产过程中的安全事故和隐患进行总结和处理。
四、注意事项1.在炼钢过程中,操作人员要遵守相关操作规程,确保安全生产。
2.对于炼钢原料和辅助材料要进行认真的检查和保管。
3.炼钢过程中的各项工艺参数和生产数据要详细记录和保存。
300t转炉课程设计说明书

1 转炉物料平衡与热平衡计算炼钢过程的物料平衡与热平衡计算是建立在物质与能量守恒的基础上的。
其主要目的是比较整个冶炼过程中物料、能量的收入项和支出项,为改进操作工艺制度,确定合理的设计参数和提高炼钢技术经济指标提供定量依据。
物料平衡是计算转炉炼钢过程中加入炉内与参与炼钢的全部物料(如铁水、废钢、氧气、冷却剂、渣料、合金添加剂、被侵蚀的炉衬等)和炼钢过程的产物(如钢水、炉渣、炉气、烟尘等)之间的平衡关系。
热平衡是计算转炉炼钢过程的热量收入(如铁水物理热、化学热)和热量支出(如钢水、炉渣、炉气的物理热、冷却剂溶化和分解热)之间的平衡关系。
1.1 原始数据的选取1.1.1 原材料成分(表1-1~表1-5)表1-1 铁水、废钢成分(%)表1-3 各材料的热容(kJ/kg.K)表1-4 反应热效应(25℃)表1-5 铁合金成分(分子)及其回收率(分母)1.1.2假设条件根据各类转炉生产实际过程假设:(1)渣中铁珠量为渣量的8%;(2)喷溅损失为铁水量的1%;CO(3)熔池中碳的氧化生成90%CO,10%2Fe O (4)烟尘量为铁水量的1.6%,其中FeO为77%,23(5)炉衬侵蚀量为铁水量的0.5%;(6)炉气温度取1450℃,炉气中自由氧含量为总炉气量的0.5%;(7)氧气成分:98.5%氧气,1.5%氮气。
1.1.3冶炼钢种及规格成分要求冶炼低碳钢,以Q235钢为例,其规格成分为(%):C 0.14~0.22,Si 0.12~0.30,Mn 0.40~0.65,P≤0.045,S≤0.0501.2物料平衡计算物料平衡基本项目:(1)收入项:铁水、废钢、溶剂(石灰、萤石、白云石)、氧气、炉衬蚀损、铁合金。
(2)支出项:钢水、炉渣、烟尘、渣中铁珠、炉气、喷溅。
根据铁水、渣料质量及其冶炼钢种的要求,采用单渣法操作。
为了简化运算,以100 kg铁水为计算基础。
1.2.1渣量及其成分计算(1)铁水中元素氧化量(表1-6)氧化量=元素在铁水中的含量–元素在钢水中的含量表1-6 铁水中的元素氧化量由表1-6知:脱磷率= 0.135 / 0.15×100% =90%;脱硫率 =0.009 /0.025 ×100% =36%;钢中残锰量 =0.17 /0.5 ×100% =34%.(2)各元素耗氧量及氧化产物量(表1-7)表1-7 铁水中元素氧化量、氧化产物量*:假定炉内气化脱硫1/3;铁的氧化由表1-13得出。
300吨转炉炼钢车间设计
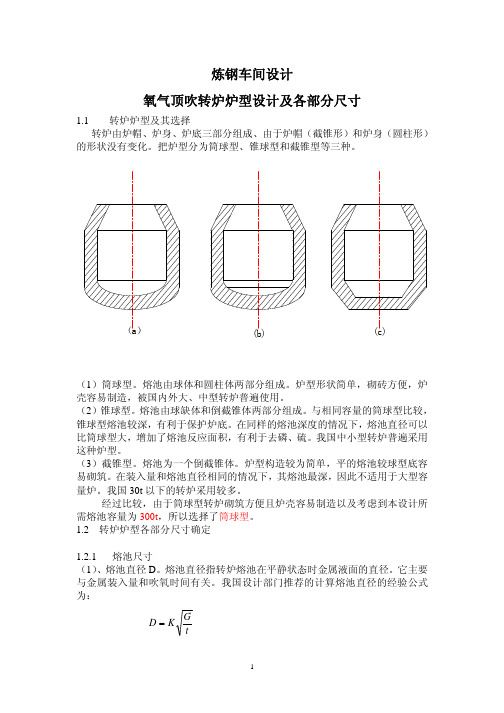
=8523-0.8358×(1600+273) =8523-1565 =6959 ㎏/m3 V 池=3×105÷6959=43.11 m3 因此 h
V池 0.046 D 3 0.79 D 2 43.11 0.046 6.213 0.79 6.212
表 3-1 氧气转炉平均冶炼时间 30 50 100-120 150 14~15 15~16 16~18 18~19 28~30 30~33 33~36 36~38
4
间夹有一层石棉板绝热层。 永久层贴紧炉壳(无绝热层时) ,维修时一般不予拆除。其主要作用是保护 炉壳。该层常用镁砖砌筑。 填充层介于永久层与工作层之间, 一般用焦油镁砂捣打而成, 厚度 80~100 ㎜。 其主要功能是减轻炉衬受热膨胀时对炉壳产生挤压和便于拆除工作层。 也有 的转炉不设填充层。本设计取用 100 ㎜。 工作层系指与金属、熔渣和炉气接触的内层炉衬,工作条件极其苛刻。目 前该层多用镁炭砖和焦油白云石砖综合砌筑。 炉帽可用二部煅烧镁砖,也可根据具体条件选用其他材质。 转炉各部位的炉衬厚度设计参考值如下表。 表 2-1 转炉炉衬厚度设计参考值 转炉容量 炉衬各部位名称 <100 100~200 >200 本设计选用 永久层厚度/㎜ 60~115 115~150 115~150 120 炉帽 工作层厚度/㎜ 400~600 500~600 550~650 500 永久层厚度/㎜ 115~150 115~200 115~200 120 炉身(加料侧) 工作层厚度/㎜ 550~700 700~800 750~850 700 永久层厚度/㎜ 115~150 115~200 115~200 120 炉身(出钢侧) 工作层厚度/㎜ 500~650 600~700 650~750 700 永久层厚度/㎜ 300~450 350~450 350~450 400 炉底 工作层厚度/㎜ 550~600 600~650 600~750 600
转炉氧枪课程设计
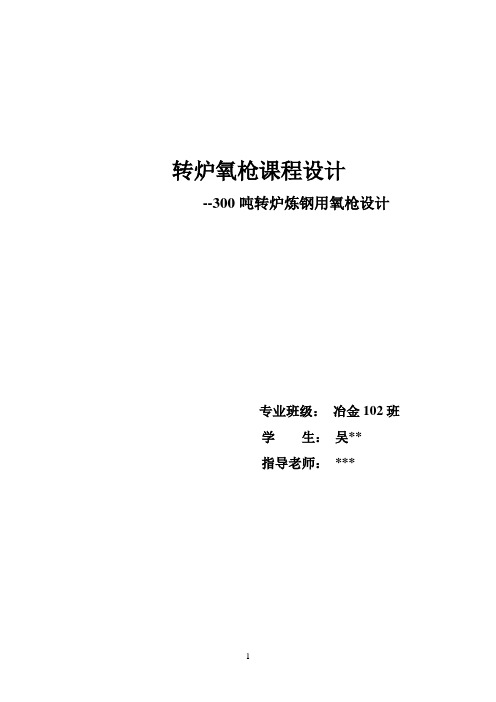
转炉氧枪课程设计--300吨转炉炼钢用氧枪设计专业班级:冶金102班学生:吴**指导老师:***一、课程设计题目金属装入量中铁水占90%,废钢占10%,吹炼钢种是Q235B,渣量是金属装入量的7.78%;吹炼过程中,金属料中93%的碳氧化生成CO,7%的碳氧化生成CO2。
二、吨钢氧消耗量的计算12g的C生成CO消耗16g氧气,生成CO2消耗32g氧气,设100kg金属料ω[C]=1%生成CO消耗氧气量为x t、生成CO2消耗氧气量为y t。
[C] + 1/2{O2} = {CO}12g 16g1%×100×93% kg x得到:x=1.240kg[C] + {O2} = {CO2}12g 32g1%×100× 7% kg y得到:y=0.187kg因此,100kg的金属料ω[C]=1%氧化消耗的氧气量为1.427kg同理可以计算出100kg金属料中ω[Si]=1%耗氧量为 3.429t、ω[Mn]=1%耗氧量为0.785t、ω[P]=1%耗氧量为3.484t、ω[S]=1%耗氧量为2.700t、ω[Fe]=1%的氧耗量为1.543t。
所以铁水的总耗氧量4.400+3.429+0.785+3.484+2.700+1.543=16.705t渣中ω(FeO)=9%、ω(Fe2O3)=3%,吹炼过程中被氧化进入炉渣的Fe元素数量,FeO中ω[Fe]= ,Fe2O3中ω[Fe]=100kg金属料各元素氧化量和氧耗量如下表所示。
100kg金属料各元素氧化量和氧耗量项目元素成分ω/%C Si Mn P S Fe铁水 4.30 0.50 0.30 0.04 0.04 废钢0.10 0.25 0.40 0.02 0.02 平均 3.88 0.475 0.31 0.038 0.038终点0.15 痕迹0.124 0.004 0.025 FeO Fe2O3烧损量/kg 3.73 0.475 0.186 0.034 0.013 0.544 0.163每1%元素消耗氧气量/kg这样每100kg金属料需氧量为:×△ω[C]+ ×△ω[Si]+ ×△ω[Mn]+ ×△ω[P]+ ×△ω[S]+ ×△ω[Fe]-(FeO)+ ×△ω[Fe]-(Fe2O3)其中,△ω[C]、△ω[Si]、△ω[Mn]、△ω[P]、△ω[S]、△ω[Fe]分别为钢中C、Si、Mn、P、S、Fe的氧化量。
300吨转炉炼钢工艺操作规程

300吨转炉炼钢工艺操作规程转炉炼钢是一种常用的钢铁生产方法,该工艺操作规程主要针对300吨转炉炼钢的工艺流程进行详细阐述,以确保生产过程的安全、高效和质量。
本规程应由炼钢厂技术人员、操作工和巡检人员等相关人员遵守,在工艺操作中严格执行,以确保钢铁质量合格。
一、工艺准备1.炉前设备和设施的检查及准备工作,包括水、气、电等设备的正常工作情况,并确保供应充足。
2.检查炼钢工艺参数的设定,如转炉倒炉量、炉温、吹氧量等,并确保各设定值正确。
3.检查炼钢原料的质量情况,确保合格原料的投入。
4.检查各种辅助设备的工作情况,如钢包、渣车、取样设备等,并确保其工作正常。
二、转炉进料1.安全操作转炉吊机,将炼钢原料按配料要求放入转炉。
2.严格按照炉前指导书的要求投入炉子中的原料种类、质量和投料速度。
三、炉前检查1.检查转炉电器元件的接线是否正常,确保电气系统稳定可靠。
2.检查转炉内外壁的情况,如有裂纹或严重损坏,及时通知相关人员进行修理。
3.检查吹氧及吹炼系统是否正常,确保吹氧过程中氧气供应畅通。
四、开炉操作1.按照指定的炉温要求进行预热,确保转炉内温度达到要求。
2.确保各种仪表设备正常,记录好包括温度、压力等相关数据。
五、转炉炼炉操作1.在炉内加入适量的生铁,控制好各种合金添加的量和添加时间。
2.使用合适的吹炼模式,并根据实际情况调整氧气供应量和吹炼时间,确保炼钢过程的稳定和高效。
3.监控炼钢过程中的温度、压力等关键参数,及时调整操作,以确保钢液质量。
六、出炉操作1.出炉前将转炉渣排出,并对转炉进行清理。
2.安全操作吊机,将转炉内钢水顺利倾倒入钢包。
3.在出钢过程中记录重要参数,如温度、出钢时间等,并做好相关记录。
七、事故处理1.若出现紧急情况,应迅速采取应急措施,并立即汇报。
2.发生设备故障或事故时,应立即停止相关操作,并进行现场处理。
八、安全操作1.严格按照相关安全操作规程进行操作,并确保操作人员具备必要的安全知识和技能。
300t转炉倾翻机构的设计【开题报告】
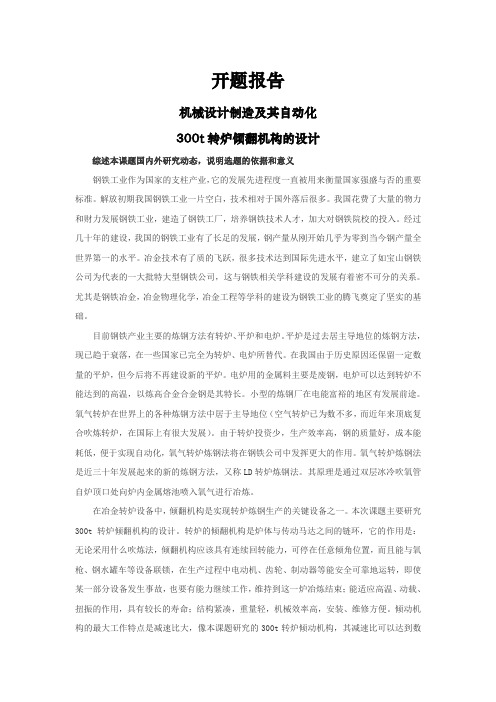
开题报告机械设计制造及其自动化300t转炉倾翻机构的设计综述本课题国内外研究动态,说明选题的依据和意义钢铁工业作为国家的支柱产业,它的发展先进程度一直被用来衡量国家强盛与否的重要标准。
解放初期我国钢铁工业一片空白,技术相对于国外落后很多。
我国花费了大量的物力和财力发展钢铁工业,建造了钢铁工厂,培养钢铁技术人才,加大对钢铁院校的投入。
经过几十年的建设,我国的钢铁工业有了长足的发展,钢产量从刚开始几乎为零到当今钢产量全世界第一的水平。
冶金技术有了质的飞跃,很多技术达到国际先进水平,建立了如宝山钢铁公司为代表的一大批特大型钢铁公司,这与钢铁相关学科建设的发展有着密不可分的关系。
尤其是钢铁冶金,冶金物理化学,冶金工程等学科的建设为钢铁工业的腾飞奠定了坚实的基础。
目前钢铁产业主要的炼钢方法有转炉、平炉和电炉。
平炉是过去居主导地位的炼钢方法,现已趋于衰落,在一些国家已完全为转炉、电炉所替代。
在我国由于历史原因还保留一定数量的平炉,但今后将不再建设新的平炉。
电炉用的金属料主要是废钢,电炉可以达到转炉不能达到的高温,以炼高合金合金钢是其特长。
小型的炼钢厂在电能富裕的地区有发展前途。
氧气转炉在世界上的各种炼钢方法中居于主导地位(空气转炉已为数不多,而近年来顶底复合吹炼转炉,在国际上有很大发展)。
由于转炉投资少,生产效率高,钢的质量好,成本能耗低,便于实现自动化,氧气转炉炼钢法将在钢铁公司中发挥更大的作用。
氧气转炉炼钢法是近三十年发展起来的新的炼钢方法,又称LD转炉炼钢法。
其原理是通过双层冰冷吹氧管自炉顶口处向炉内金属熔池喷入氧气进行冶炼。
在冶金转炉设备中,倾翻机构是实现转炉炼钢生产的关键设备之一。
本次课题主要研究300t转炉倾翻机构的设计。
转炉的倾翻机构是炉体与传动马达之间的链环,它的作用是:无论采用什么吹炼法,倾翻机构应该具有连续回转能力,可停在任意倾角位置,而且能与氧枪、钢水罐车等设备联锁,在生产过程中电动机、齿轮、制动器等能安全可靠地运转,即使某一部分设备发生事故,也要有能力继续工作,维持到这一炉冶炼结束;能适应高温、动载、扭振的作用,具有较长的寿命;结构紧凑,重量轻,机械效率高,安装、维修方便。
300吨转炉设计0000
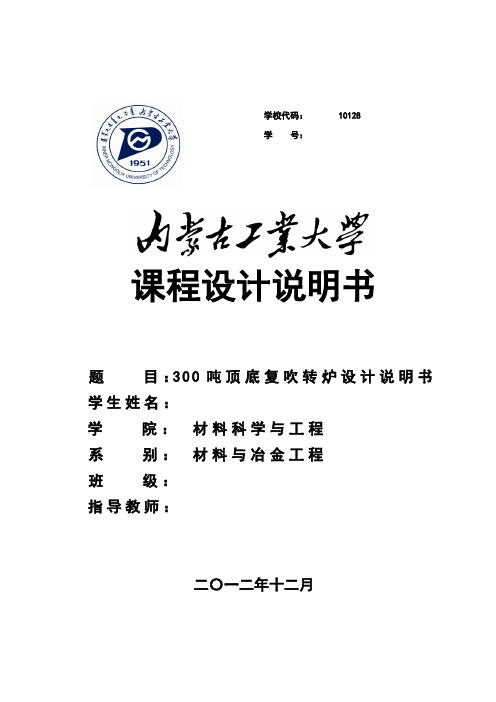
课程设计说明书题 目:300吨顶底复吹转炉设计说明书 学生姓名:学 院: 材料科学与工程 系 别: 材料与冶金工程 班 级: 指导教师:二〇一二年十二月300t 顶底复吹转炉炉型设计转炉的设计包括炉型设计、转炉中心及倾动力矩的计算、转炉机构的设计计算。
炉型设计包括确定所设计炉子的公称容量、选择炉型、确定炉型主要设计参数、计算熔池尺寸、整个炉型尺寸。
1 炉型选择结合中国已建成的转炉的设计经验,在选择炉型时,250-300t 的转炉,采用筒球形炉型,所以本设计采用筒球形[1]。
2转炉主要尺寸参数的确定及计算2.1 熔池形状及尺寸计算① 熔池直径:D=K 式中:G — 新炉子金属装入量t — 吹氧时间(取18min )K — 比例系数(取1.5) 确定初期装入量G :取B=10﹪ 08.1=η ==ηη1金0.925B —老炉比新炉多产钢系数η—金属消耗系数η金—金属收得率t 57.308G B2T2=⨯=+ηD = 1.5×1857.308 =6.211 m② 熔池深度h :23D79.0D046.0+=金V h取37m kg =金ρ 3m 08.44757.308G===金金ρVm h 816.1= 校核:29.0=D h 符合要求[2]。
2.2 炉帽尺寸的计算① 炉口直径0d取m6.30=d [3]② 帽锥角θ取 ︒=60θ③ 炉帽高度 帽H400~300H =口mm (本设计取400mm ) ()m261.2t a n d D21H 0=-=θ锥m 661.2469.24.0H H H =+=+=锥口帽 ④ 炉帽容积帽V炉帽体积约为炉熔体积的30%[4]。
m 90%30300V =⨯=帽2.3 炉身尺寸的确定① 炉膛直径 D =膛D (炉衬无加厚段的转炉) ② 选取炉容比为 t m /13炉膛体积 3300m V = ③ 炉身高度m D V V V D H 479.5/)(4/V 422=--==ππ池帽身身④ 炉型内高m 688.10H h =++=身帽内H H2.4 出钢口尺寸的确定① 出钢口中心线与水平倾角取 018=β ② 出钢口直径 mT d T 242.030075.16375.163=⨯+=+=③ 出钢口衬砖外径 m d d T st 455.1243.066=⨯== ④ 出钢口长度 md L T T 819.1243.05.75.7=⨯==[5]3 炉衬的组成、材质选择及厚度确定炉衬一般由永久层和工作层组成。
300吨转炉炼钢工艺操作规程

300吨转炉炼钢工艺操作规程第一章:总则第一条:本规程适用于300吨转炉炼钢工艺操作。
第二条:炼钢工艺操作必须严格按照本规程的要求进行,确保炼钢的安全、稳定和质量。
第二章:工艺流程第三条:炉前设备操作1.确保炉前设备的正常运行,如氧气、天然气等供应设备;2.检查转炉冷却水系统的压力和流量,确保正常运行。
第四条:炉前准备1.确定炉液成分和炉温要求;2.检查转炉内外表面的清洁度和设备的完好性,确保炉内无异物;3.检查炉底是否有积杂物,如有需要清理。
第五条:原料装入1.原料装入顺序为:底吹剂-生铁-废钢-矿石-废钢-矿石;2.原料装入前要检查原料的质量和含水率,并记录;3.原料装入时,要保证装入均匀并尽量避免飞溅。
第六条:加料结束后1.检查转炉口的密封情况,必要时进行修补;2.完成装料记录。
第七条:转炉预热1.开启转炉风门,通风10分钟,进行预热;2.检查转炉风门的开度和风量,确保正常运行;3.检查转炉烟道温度和压力,以确保正常预热。
第八条:吹氧阶段1.转炉预热结束后,开启底吹氧气,氧气流量要逐渐增大;2.检查转炉底吹氧气压力和流量;3.监测转炉底部温度,确保吹氧的效果;4.检查底吹氧气消耗情况,进行记录。
第九条:加矿石阶段1.底吹氧气达到要求后,加入矿石;2.检查矿石的质量和含水率,并记录;3.加入矿石的过程中要注意控制转炉底部温度的上升速度。
第十条:吹气到出钢水的阶段1.确保底吹氧气达到要求,停止加矿石;2.开始顶吹氧气,保持适当的风速;3.监测转炉底部温度,确保达到出钢水的要求。
第十一条:出钢水阶段1.当转炉达到出钢水温度要求时,开始出钢水;2.检查出钢水质量和温度,确保符合要求;3.出钢水的流量要逐渐增大,直到达到设定值。
第十二条:工艺结束后1.停止吹氧和出钢水,关闭风门;2.检查转炉内外表面的清洁度,清除杂物;3.记录相关工艺参数和操作情况。
第十三条:应急处理1.发生突发情况时,及时报告上级,并按照应急预案进行处理;2.停止吹氧和出钢水,关闭风门,并切断相应设备的电源。
宝钢300吨转炉生产工艺介绍
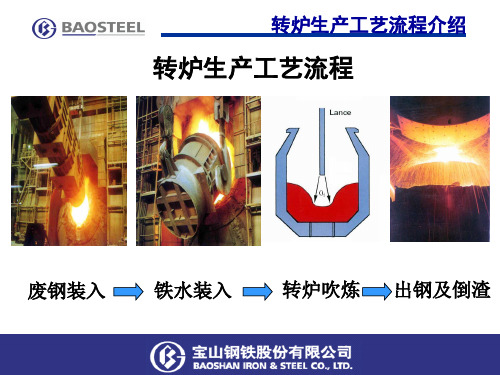
H=氧枪间隙 N=孔数 D=孔径 K=1.0
生产工艺流程介绍—造渣制度
控制炼钢过程的重要手段就是掌握造渣制度,所谓造渣制 度就是通过加入造渣材料及掌握氧气喷枪等操作及时调整炉渣 的化学成份和物理状态,做到早化渣、化好渣、控制住渣的氧 化性等,使炉渣在吹炼过程中,真正起到脱磷、脱硫、保护炉 衬、减少喷溅的作用。
尺寸及单重 块度要求:<50~70×170×800mm,单重0.03~0.04吨 块度要求:<300×500×2000mm,单重<1.0吨
块状
块度要求:<300×500×2000mm,单重<2.5吨
块条及异 型状
机械打包
块度要求:<300×800×1800mm,单重<1.0吨 尺寸:<800×500×400mm,比重>2.5吨/米3
注:各修正参数可参考技术规程。
二、300t转炉过程温度的控制计算方法 根据炉内反应理论以及炉内O2平衡、热平衡 ,引入冷却能的概念, 计算出每炉钢所需冷却剂量或发热剂量和吹氧量,进而对转炉过程 温度进行控制。具体计算方法可参见技术规程。
生产工艺流程介绍—复吹工艺
宝钢300t氧气顶吹转炉于1990年6月进行了复吹改造,底部喷吹惰性气体的弱搅拌 型复吹工艺,以改善钢水纯净度,提高经济效益,充分发挥大型氧气转炉炼钢的优势。 宝钢转炉的复吹方式采用新日铁的LD-CB顶底复吹技术,主要底吹N2和Ar气,供气强度 0.022~0.11Nm3/min.t,N2总管压力1.5~1.7MPa,Ar气总管压力2.4~2.6MPa。目前底 部供气风口有6孔、6孔、10孔等方式,其中1#炉、3#炉均为二路控制,2#炉经2002年 10月份进行BRP脱磷改造以后变为五路单独可调控制。风口的透气砖有2种型式,一种 是日本黑崎窑业圆形Φ4×39,即由39根精制的细不锈钢管组成,每根管内径4mm;另 一种是奥镁方形Φ2.5×96,即由96根内径2.5mm的不锈钢管组成。风口的透气砖长度 为900mm,但2#炉因BRP改造现采用1200mm长度的透气砖。 复吹工艺的优点:
设计300t的转炉

辽宁科技学院课程设计说明书课程设计名称:设计一座公称容量300吨的转炉指导教师:班级:姓名:2010年7月20日绪论 (2)1 转炉炉型设计 (3)1.1 炉型设计 (3)1.2 主要参数的确定 (3)1.3底部供气构件的设计 (5)2转炉炉衬设计 (6)2.1材质的选择 (6)2.2炉衬的组成和厚度的确定 (6)3转炉炉体金属构件设计 (7)3.1炉壳 (7)3.2、支承装置 (7)3.3转炉重心计算 (8)3.3.1空炉重心计算 (8)3.3.2铁水重心计算 (12)3.4倾动装置 (12)4转炉氧枪设计及相关参数计算 (13)4.1氧流量计算 (13)4.2喷头孔数 (13)4.3理论计算氧压及喷头出口马赫数M (13)4.4 300t转炉氧枪喷头尺寸计算 (13)4.5 300t转炉氧枪枪身尺寸计算 (15)结论 (17)参考文献 (19)致谢 (20)氧气转炉炼钢是当前国内外主要的炼钢方法。
氧气转炉炼钢至20世纪40年代初问世以来,在世界各国得到了广泛的应用,技术不断进步,设备不断改进,工艺不断完善。
在短短的五十几年里,从顶吹发展到底吹、侧吹和复合吹炼。
氧气转炉炼钢的飞速发展,使炼钢生产进入了一个崭新的阶段,炼钢产量不断的增加成本不断下降。
从目前看来,转炉炼钢可以说是最佳的炼钢方法。
20世纪50年代,在顶吹转炉发展的同时,欧洲就提出过从炉底吹入底吹气体的方法以改善脱磷反应。
并称之为复合吹炼法,但是在实际中未能得到应用。
底吹转炉的成熟以及70年代后期的有关顶吹和底吹的一些重要研究成果,推动了复合吹炼的的工业应用。
1978年,卢森堡阿尔贝德公司在贝尔瓦厂180t转炉上采用了顶底复合吹炼法,即LBE法。
这是工业生产中使用复合吹炼法的开始。
从顶吹或底吹的比较中可以看出,混合吹炼系统具有一些既不同于顶吹,也不同于底吹的特点。
与顶吹相比复合吹炼的目的在于:(1)减少熔池的浓度和温度梯度,以改善吹炼的可控性,从而减少喷溅和提高供氧强度;(2)减少渣和金属过氧化,从而提高钢水和铁合金的收得率;使吹炼进行得更接近平稳,从而改善脱磷和脱硫率,使炉子更适用于生产低碳钢。
转炉课程设计第二章、第三章
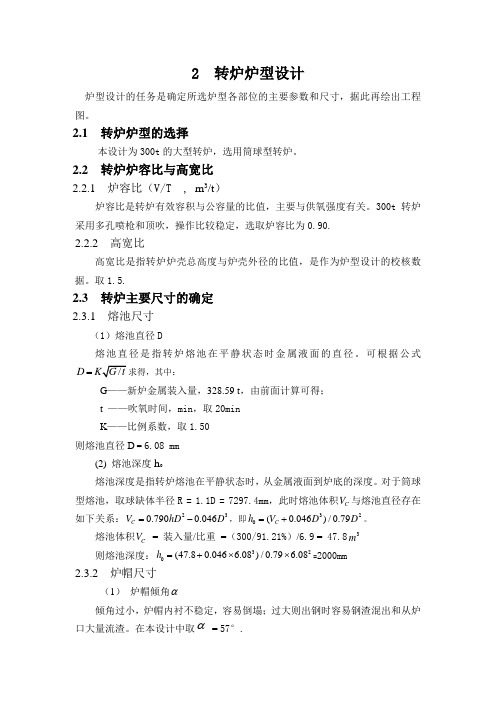
2 转炉炉型设计炉型设计的任务是确定所选炉型各部位的主要参数和尺寸,据此再绘出工程图。
2.1 转炉炉型的选择本设计为300t 的大型转炉,选用筒球型转炉。
2.2 转炉炉容比与高宽比2.2.1 炉容比(V/T , m 3/t )炉容比是转炉有效容积与公容量的比值,主要与供氧强度有关。
300t 转炉采用多孔喷枪和顶吹,操作比较稳定,选取炉容比为0.90.2.2.2 高宽比高宽比是指转炉炉壳总高度与炉壳外径的比值,是作为炉型设计的校核数据。
取1.5.2.3 转炉主要尺寸的确定 2.3.1 熔池尺寸(1)熔池直径D熔池直径是指转炉熔池在平静状态时金属液面的直径。
可根据公式/D K G t =求得,其中:G ——新炉金属装入量,328.59 t ,由前面计算可得; t ——吹氧时间,min ,取20min K ——比例系数,取1.50 则熔池直径D = 6.08 mm(2) 熔池深度h 0熔池深度是指转炉熔池在平静状态时,从金属液面到炉底的深度。
对于筒球型熔池,取球缺体半径R = 1.1D = 7297.4mm ,此时熔池体积C V 与熔池直径存在如下关系:230.7900.046C V hD D =-,即320(0.046)/0.79C h V D D =+。
熔池体积C V = 装入量/比重 =(300/91.21%)/6.9 = 47.83m 则熔池深度:320(47.80.046 6.08)/0.79 6.08h =+⨯⨯=2000mm2.3.2 炉帽尺寸(1) 炉帽倾角α倾角过小,炉帽内衬不稳定,容易倒塌;过大则出钢时容易钢渣混出和从炉口大量流渣。
在本设计中取α = 57°.(2) 炉口直径d 0本设计中取取炉口直径为熔池直径的50%,即d 0 = 6.08×50% = 3.04m = 3040mm(3) 炉帽高度H帽取炉口上部直线段高度H口 = 400 mm ,则炉帽高度为:H 帽 =1/200()tan D d H α-+= 1/2(6.08 — 3.04)tan57°+ 0.4 = 2.74m 2.3.3 炉身尺寸(1) 炉身直径转炉炉帽以下,熔池面以上的圆柱体部分称为炉身。
转炉炼钢课程设计
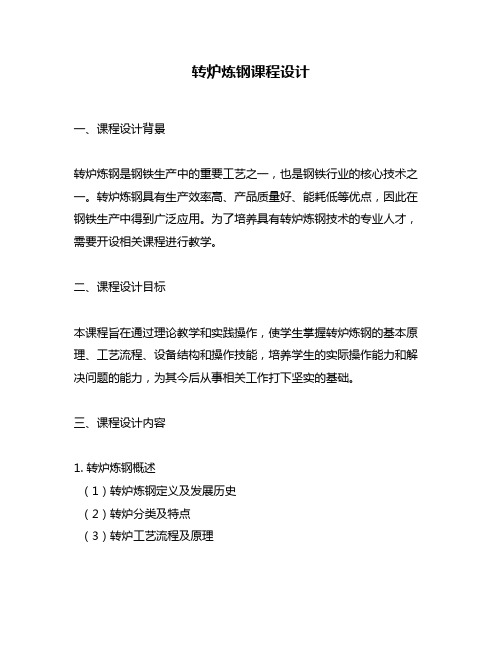
转炉炼钢课程设计一、课程设计背景转炉炼钢是钢铁生产中的重要工艺之一,也是钢铁行业的核心技术之一。
转炉炼钢具有生产效率高、产品质量好、能耗低等优点,因此在钢铁生产中得到广泛应用。
为了培养具有转炉炼钢技术的专业人才,需要开设相关课程进行教学。
二、课程设计目标本课程旨在通过理论教学和实践操作,使学生掌握转炉炼钢的基本原理、工艺流程、设备结构和操作技能,培养学生的实际操作能力和解决问题的能力,为其今后从事相关工作打下坚实的基础。
三、课程设计内容1. 转炉炼钢概述(1)转炉炼钢定义及发展历史(2)转炉分类及特点(3)转炉工艺流程及原理2. 转炉结构与设备(1)转炉结构及组成部分(2)各部位功能及作用介绍(3)常见故障及处理方法3. 转炉操作技能(1)转炉操作前准备工作(2)转炉开炉及加料操作(3)钢水出钢及出渣操作(4)转炉关炉及清理工作4. 转炉生产管理(1)生产计划编制及执行(2)设备维护保养及安全管理(3)质量控制及环境保护5. 实践操作(1)模拟实验:转炉开、关炉操作演练(2)现场实习:参观钢厂,观摩现场生产过程四、教学方法本课程采用多种教学方法,包括理论讲解、案例分析、模拟实验和现场实习等。
其中,模拟实验是本课程的重要组成部分,通过对转炉开、关炉等操作的演练,使学生能够真正掌握相关技能。
五、考核方式本课程考核方式包括平时成绩和期末考试两部分。
平时成绩占总成绩的30%,主要评估学生的出勤情况、课堂表现和模拟实验成绩;期末考试占总成绩的70%,主要考核学生对转炉炼钢原理、设备结构和操作技能的掌握程度。
六、教学资源本课程需要的教学资源包括课件、实验器材、教材和参考书籍等。
其中,教材应选用权威性强、内容全面、易于理解的转炉炼钢专业书籍;参考书籍应包括转炉炼钢技术及相关领域的最新进展。
七、教学团队本课程需要一支专业素质高、经验丰富的教师团队。
其中,主讲教师应具备扎实的专业知识和丰富的实践经验,能够灵活运用多种教学方法,激发学生学习兴趣和积极性;助教应能够协助主讲教师进行模拟实验和现场实习等工作,提供必要的技术支持。
转炉炼钢课程设计
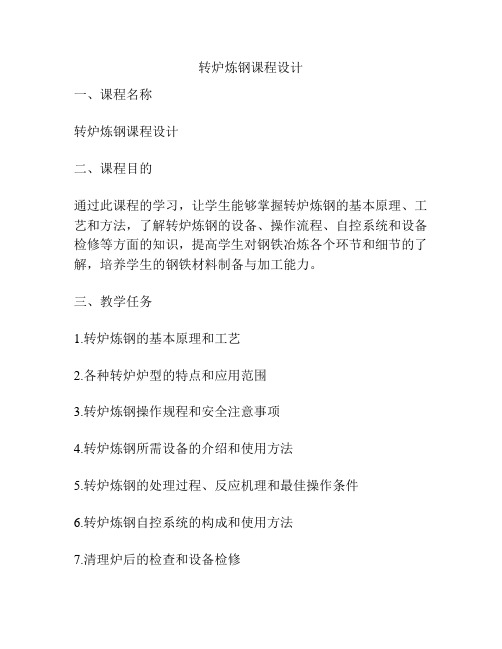
转炉炼钢课程设计一、课程名称转炉炼钢课程设计二、课程目的通过此课程的学习,让学生能够掌握转炉炼钢的基本原理、工艺和方法,了解转炉炼钢的设备、操作流程、自控系统和设备检修等方面的知识,提高学生对钢铁冶炼各个环节和细节的了解,培养学生的钢铁材料制备与加工能力。
三、教学任务1.转炉炼钢的基本原理和工艺2.各种转炉炉型的特点和应用范围3.转炉炼钢操作规程和安全注意事项4.转炉炼钢所需设备的介绍和使用方法5.转炉炼钢的处理过程、反应机理和最佳操作条件6.转炉炼钢自控系统的构成和使用方法7.清理炉后的检查和设备检修四、教学内容1.转炉炼钢的基本原理和工艺(1)转炉炼钢钢种和质量要求(2)在转炉炼钢中应用的基本原理(3)转炉炼钢工艺的基本流程2.各种转炉炉型的特点和应用范围(1)各种转炉炉型的特点(2)各种转炉炉型的应用范围3.转炉炼钢操作规程和安全注意事项(1)操作规程的概述(2)操作指导(3)操作注意安全事项4.转炉炼钢所需设备的介绍和使用方法(1)转炉炼钢所需主要设备的特点和作用(2)如何操作转炉所需设备5.转炉炼钢的处理过程、反应机理和最佳操作条件(1)转炉炼钢的主要处理过程(2)转炉炼钢的反应机理(3)转炉炼钢的最佳操作条件6.转炉炼钢自控系统的构成和使用方法(1)转炉炼钢的自控系统构成(2)使用方法7.清理炉后的检查和设备检修(1)清理炉后的检查(2)设备检修五、教学方法1.教学以理论课为主,结合实际案例进行分析2.采用讲述和互动交流相结合的方法,让学生能够更好的理解和掌握内容3.采取课堂讨论和研究报告相结合的方式,让学生主动参与和发言六、教材及参考书目教材:《钢铁原理》,邹国华、徐福坦参考书目:1.《钢铁冶炼技术手册》,吕永卫、沈友智2.《钢铁冶炼学》,邵益民3.《钢铁大全》,付继红4.《现代钢铁工程》,陈洛南、彭元锋七、考核评价考核方式:1.平时成绩(作业、课堂表现、实验)2.期末考试3.论文报告评价标准:1.学生是否能够掌握理论和实践知识2.学生是否能够独立思考问题并做出自己的解决方案3.学生是否能够有效地表达自己的观点和意见4.学生是否能够遵守学习纪律和考试要求5.学生是否能够积极参加课程的讨论和研究活动八、课程总结通过这门课程的学习,学生将深入了解和掌握转炉炼钢的基本知识和技能,能够熟练掌握钢铁冶炼中的各个环节和要素,为未来的学习和工作奠定坚实的基础。
转炉炼钢课程设计
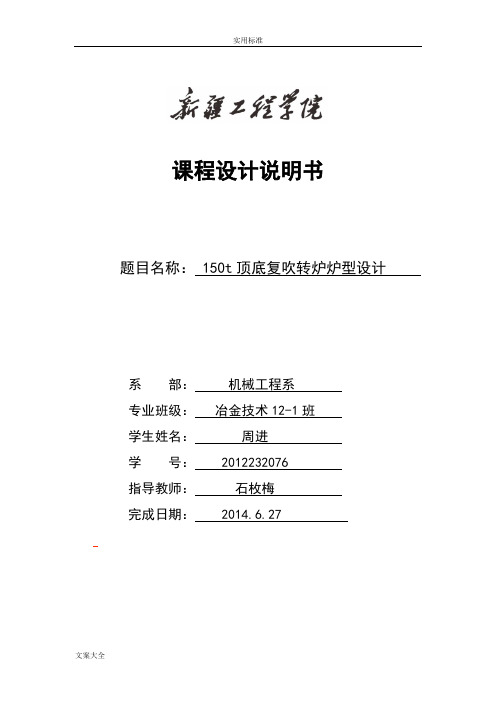
课程设计说明书题目名称: 150t顶底复吹转炉炉型设计系部:机械工程系专业班级:冶金技术12-1班学生姓名:周进学号: 2012232076指导教师:石枚梅完成日期: 2014.6.27新疆工程学院课程设计评定意见设计题目 150t顶底复吹转炉炉型设计系部 ___机械工程系__ 专业班级冶金技术12-1班学生姓名 ____周进_______ 学生学号 2012232076 评定意见:评定成绩:指导教师(签名): 2014年 6月 27日新疆工程学院机械工程系(部)课程设计任务书2013-2014 学年第2学期 2014 年 6月27日教研室主任(签名)系(部)主任(签名)目录1.摘要 (1)2 转炉物料平衡与热平衡计算 (1)2.1 原始数据的选取 (2)2.1.1 原材料成分 (2)铁水、废钢成分见表1.1 (2)2.1.2 假设条件 (3)2.1.3 冶炼钢种及规格成分 (3)2.2.1 渣量及其成分计算 (3)2.2.3 氧气消耗量计算 (7)2.2.4 炉气量及成分计算 (8)2.2.5 未加废钢和合金时的物料平衡表 (8)2.3.1 热收入 (9)2.3.2 热支出 (9)2.3.3 热平衡表 (11)2.4 吨钢物料平衡 (11)3 转炉炉型设计 (12)3.1 转炉炉型的选择 (12)3.2 转炉炉容比与高宽比 (12)3.2.1 炉容比(V/T , m3/t) (12)3.2.2 高宽比 (13)3.3 转炉主要尺寸的确定 (13)3.3.1熔池尺寸 (13)3.3.2 炉帽尺寸 (13)3.3.4 出钢口尺寸 (14)3.3.5 炉衬 (15)3.3.6 炉壳 (15)结束语 (17)参考文献 (18)1.摘要转炉炼钢(converter steelmaking)是以铁水、废钢、铁合金为主要原料,不借助外加能源,靠铁液本身的物理热和铁液组分间化学反应产生热量而在转炉中完成炼钢过程。
t转炉课程设计

转炉的设备选型与配置
转炉类型:选择合适的转炉类型,如顶吹转炉、底吹转炉等 设备选型:根据生产需求选择合适的设备,如炉体、炉盖、炉底等 设备配置:确定设备的配置,如加热方式、冷却方式、控制系统等 设备维护:制定设备的维护计划,确保设备的正常运行和寿命延长
转炉的控制系统设计
控制系统类型:PLC控制 系统
增强团队协作:培养学生的团队 协作能力和领导能力
添加标题
添加标题
添加标题
添加标题
提升创新能力:培养学生的创新 思维和解决问题的能力
促进就业:提高学生的就业竞争 力和适应社会的能力
感谢观看
汇报人:
02
转炉课程设计的内容
转炉的工艺流程设计
原料准备:选择合适的原料,如铁矿石、焦炭等
熔炼过程:将原料放入转炉中,加热至熔化状态
脱碳过程:通过吹氧等方法,去除铁水中的碳元素
合金化过程:添加合金元素,如硅、锰等,以提高钢的质 量
精炼过程:进一步去除杂质,提高钢的纯净度
浇铸过程:将钢水浇铸成钢锭或钢坯,进行后续加工
控制功能:温度控制、压 力控制、流量控制等
控制策略:PID控制、模 糊控制、自适应控制等
安全保护:过热保护、过 压保护、漏电保护等
通信接口:RS485、以 太网、无线通信等
软件平台:WinCC、 LabVIEW、Matlab等
转炉的安全与环保措施
安全措施:设置安全防护装置,如安全门、安全护栏等 环保措施:采用环保型材料,如无毒无害的耐火材料 节能措施:采用节能型设备,如高效节能的转炉设备 环保处理:对废气、废水、废渣进行环保处理,如废气净化、废水处理、废渣回收利用等
评估与反馈:对教学效果进行评估,收集 学生反馈,进行改进和优化
设计作业 300t顶底复吹转炉炉型计算

转炉炉型设计计算1.1原始数据(1)、转炉的公称容量为300t 。
(2)、采用顶底复吹冶炼工艺1.2 转炉的炉型选择图为常见转炉炉型(a)筒球型; (b)锥球型; (c)截锥型根据原始条件及采用顶底复吹工艺的要求,为便于安装底部供气元件,要求转炉底部为平的,所以本设计将采用截锥型炉型作为设计炉型。
1.3炉容比炉容比系指转炉有效容积与公称容量之比值。
转炉炉容比主要与供氧强度有关,与炉容量关系不大。
从目前实际情况来看,顶底复吹转炉炉容比一般取0.85~0.95m 3/t 。
本设计为300t ,取V/T=0.92 1.4熔池尺寸的计算 熔池直径的计算公式tGkD 式中 D ——熔池直径,m ;G ——新炉金属装入量,t ,可取公称容量; K ——系数,参见表1-1;t ——平均每炉钢纯吹氧时间,min表1-1 系数K 的推荐值b.确定吹氧时间表1.2 推荐的转炉纯吹氧时间本设计的转炉公称容量为300t ,又根据国家关于新建转炉的要求,吹氧时间在16min , 所以选择的吹氧时间为16min 。
取K=1.50 则)(495.61630050.1m t G K D =⋅=⋅= ② 截锥型熔池深度的计算公式为:)(822.1495.6574.0119.44574.0574.0222m D V D V h =⨯=⨯==)(金池 V 池=G/Y=44.119m 3 其中Y=6.8t/ m 3 ③熔池其他尺寸确定.)(546.4495.67.07.01m D D =⨯== 1.5炉帽尺寸的确定 ①炉口直径d 0.取)(2475.3495.65.00m d =⨯= ②炉帽倾角: 取︒60 ③炉帽高度H 帽: 取H 口=400mm ,)(76.260tan )2475.3495.6(21tan )(2100m d D H =⨯-=⋅-=θ锥 则整个炉帽高度为:)(06.33.076.2m H H H =+=+=锥口帽 在炉口处设置水箱试水冷炉口。
- 1、下载文档前请自行甄别文档内容的完整性,平台不提供额外的编辑、内容补充、找答案等附加服务。
- 2、"仅部分预览"的文档,不可在线预览部分如存在完整性等问题,可反馈申请退款(可完整预览的文档不适用该条件!)。
- 3、如文档侵犯您的权益,请联系客服反馈,我们会尽快为您处理(人工客服工作时间:9:00-18:30)。
西安建筑科技大学冶金工程课程设计说明书240t氧气转炉设计学生姓名班级学号指导老师冶金工程学院年月日目录1转炉物料平衡与热平衡计算---------------------------------------------------------11.1原始数据选取---------------------------------------------------------------------11.2未加废钢和合金的物料平衡计算---------------------------------------------31.3热平衡计算-----------------------------------------------------------------------91.4加废钢和合金的物料平计算--------------------------------------------------12 2转炉炉型设计----------------------------------------------------------------------------152.1转炉炉型选择--------------------------------------------------------------------152.2转炉炉容比与高宽比-----------------------------------------------------------152.3转炉主要尺寸确定--------------------------------------------------------------152.4转炉炉体结构图-----------------------------------------------------------------18 参考文献-------------------------------------------------------------------------------------211 转炉物料平衡与热平衡计算物料平衡是计算转炉炼钢过程中加入炉内与参与炼钢的全部物料(如铁水、废钢、氧气、冷却剂、渣料、合金添加剂、被侵蚀的炉衬等)和炼钢过程的产物(如钢水、炉渣、炉气、烟尘等)之间的平衡关系。
热平衡是计算转炉炼钢过程的热量收入(如铁水物理热、化学热)和热量支出(如钢水、炉渣、炉气的物理热、冷却剂溶化和分解热)之间的平衡关系。
1.1 原始数据的选取1.1.1 原材料成分(表1-1~表1-5)表1-1 铁水、废钢成分(%)表1-2 渣料和炉衬材料成分(%)表1-3 各材料的热容(kJ/kg.K)表1-4 反应热效应(25℃)表1-5 铁合金成分(分子)及其回收率(分母)1.1.2假设条件1.1.3冶炼钢种及规格成分要求冶炼低碳钢,以Q235钢为例,其规格成分为(%):C 0.14~0.22,Si 0.12~0.30,Mn 0.40~0.65,P≤0.045,S≤0.0501.2 未加废钢和合金的物料平衡计算物料平衡基本项目:(1)收入项:铁水、废钢、溶剂(石灰、萤石、白云石)、氧气、炉衬蚀损、铁合金。
(2)支出项:钢水、炉渣、烟尘、渣中铁珠、炉气、喷溅。
根据铁水、渣料质量及其冶炼钢种的要求,采用单渣法操作。
为了简化运算,以100 kg铁水为计算基础。
1.2.1渣量及其成分计算(1)铁水中元素氧化量(表1-6)氧化量=元素在铁水中的含量–元素在钢水中的含量表1-6 铁水中的元素氧化量由表1-6知:脱磷率= 0.135 / 0.15×100% =90%;脱硫率 =0.009 /0.025 ×100% =36%;钢中残锰量 =0.17 /0.5 ×100% =34%.(2) 各元素耗氧量及氧化产物量(表1-7)表1-7 铁水中元素氧化量、氧化产物量*:假定炉内气化脱硫1/3;铁的氧化由表1-13得出。
(3) 渣料的加入量1) 萤石加入量:根据冶金局(部)转炉操作规程,并参考《炼钢工艺学》,取萤石加入量4 kg/t,在本设计中,即为:0.1×4=0.4 kg,其成分质量计算见表1-9. (质量计算中各成分质量百分数见表1-2)表1-9 萤石加入量及成分其中: 2[P]+5/2O 2=P 2O 5(P 2O 5)生成量 = 0.002×142/62 = 0.005 kg3) 白云石加入量 :为了提高转炉寿命,采用白云石造渣,控制渣中(MgO )含量在6% ~ 8%范围内。
根据已投产转炉的经验,取生白云石30 kg/t ,在本设计中即为:30×0.1 = 3 kg ,其成分质量计算见表1-10。
(质量计算中各成分质量百分数见表1-2)表1-10 生白云石加入量及成分其中:烧减是白云石中33CaCO MgCO 分解产生的2CO 气体。
4)炉衬侵蚀量:转炉炉衬在炉渣作用下,将被侵蚀和冲刷进入渣中,本设计中取铁水量的0.5%,即100×0.5% = 0.5 kg ,其成分质量计算见表1-11. (质量计算中各成分质量百分数见表1-2)表1-11 炉衬侵蚀量及成分其中:炉衬中碳的氧化与金属中氧化生成的CO 和CO 2比例相同。
即: [C]+1/2O 2=CO :氧化产物CO 量为:0.025×90%×28/12 = 0.053 kg 耗氧量为:0.025×90%×16/12 = 0.03 kg [C]+O 2=CO 2:氧化产物CO 2量为:0.025×10%×44/12 = 0.009 kg 耗氧量为:0.009×32/44 = 0.007 kg共消耗氧量=0.03+0.007 = 0.037 kg5) 石灰加入量:根据铁水成分,取终渣碱度R=3.5,石灰加入量计算如下: ∑(SiO 2)=铁水[Si]生成(SiO 2)+ 炉衬、矿石、白云石、萤石带入的(SiO 2)=1.071 + 0.01 + 0.0561 + 0.09 + 0.024 =1.251 kg∑(CaO)=白云石、矿石、炉衬带入(CaO)—铁水、矿石中S消耗CaO量=1.65 + 0.01 + 0.27 —0.006×56/32 –0.001×56/32 = 1.918 kg 石灰加入量 = {∑(SiO2)×R - ∑(CaO)}/%CaO有效×100%= (1.251×3.5 – 1.918)/(91 – 3.5×2) ×100%= 2.93 kg 其成分质量计算见表1-12. (质量计算中各成分质量百分数见表1-2)表1-12 石灰加入量及成分其中:[S]+(CaO)=(CaS)+[O]生成的(CaS) = 0.0015×72/32 = 0.003 kg6) 渣中的铁氧化物:对于冶炼Q235钢,根据已投产转炉渣中含∑(FeO)量,取(FeO)= 10%,(Fe2O3)= 7%。
7)终渣总量及成分:根据表1-7~表1-12中的数据,确定终渣总量及成分,见表1-13,若不计(FeO)、(Fe2O3),由表1-13中可得:CaO+MgO+SiO2+P2O5+MgO+Al2O3+CaF2+CaS= 4.60 + 1.247 + 1.311 + 0.314 + 0.426 + 0.162 + 0.356 + 0.019 = 8.435 kg已知(FeO)= 10% ,(Fe2O3)= 7% ,则其余渣应占渣量总数的83%。
故总渣量为8.435/83% = 10.163 kg由此可知:(FeO)= 10.163 × 10% = 1.016 kg,(Fe2O3)= 10.163 × 7% = 0.711 kg。
由于矿石和白云石中带入部分(FeO)和(Fe2O3),其含量参见表1-8和1-10,实际铁氧化物为:(FeO)= 1.016 — 0.294 = 0.722 kg ;其值列入表1-7.(Fe2O3)= 0.711 — 0.618 — 0.03 = 0.063 kg .其值列入表1-7表1-13 终渣总量及成分1.2.2冶炼中的吹损计算根据假设条件,渣中铁珠量为渣量的8%,喷溅损失为铁水量的1%,烟尘损失为铁水量的1.6%。
故可得到:渣中铁珠量 = 10.163 × 8% = 0.813 kg喷溅损失量 = 100 × 1% = 1.0 kg烟尘铁损失量 = 100 × 1.6%×(77%×56/72 + 20%×112/160)= 1.182 kg 元素氧化损失 = 5.858 kg (见表1-7)吹损总量 = 0.813 + 1.0 + 1.182 + 5.858 = 8.853 kg钢水量 = 100 —8.853 = 91.147 kg .1.2.3 氧气消耗量计算1)元素氧化耗氧 =7.026 kg(见表1-7);2)烟尘铁氧化耗氧 =100×1.6%(77%×16/72 + 20%×48/160)= 0.37 kg;3) 炉衬中碳氧化耗氧 = 0.037 kg(见表1-10下)。
故总耗氧量 = 7.026 + 0.37 + 0.037 = 7.433 kg.换算为标准体积为:7.433×22.4/32 = 5.20 m3即冶炼100 kg 铁水需要5.203m氧气。
取氧气利用率为80%,则冶炼1 t 铁水的实际供氧量为:5.2 /80%×10 = 65 m3 /t由于氧气不纯,含有1.5%的氮气,故供氧时带入的氮气为:7.433 × 1.5% = 0.111 kg其体积量为:0.111 ×22.4/28 = 0.089 m3,则冶炼 1 t 铁水将会带入0.89 m3的氮气。
1.2.4炉气量及成分计算炉内产生的炉气由CO、CO2、SO2、H2O、N2和自由 O2组成。
其中:CO来源于铁水和炉衬中的碳氧化;CO2来源于铁水、炉衬中碳氧化,以及白云石和石灰石中的烧减量;SO2来源于铁水中硫氧化;H2O来源于矿石和萤石中;N2来源于供氧时被带入。
自由O2约占炉气总量的0.5%,即以上气体占炉气总量的99.5%,则炉气总量为:(6.846 + 0.893 + 0.002 + 0.016 + 0.089)/99.5% = 7.885 m3自由O2量为7.885 ×0.5% = 0.039 m3,其质量为0.039×32/22.4 = 0.056 kg表1-14 炉气量及成分1.2.5未加废钢和合金时的物料平衡表把以上各种物质的总收入和总支出汇总起来,得到未加合金时的物料平衡表1-15.表1-15 未加废钢和合金时的物料平衡表计算误差 = (收入项—支出项)/收入项×100%= (115.374 — 115.221)/115.374×100% = 0.133%.1.3热平衡计算为了简化运算,取加入炉内的炉料温度均为25℃。