线束技术要求及检测内容
QCT29106线束技术条件
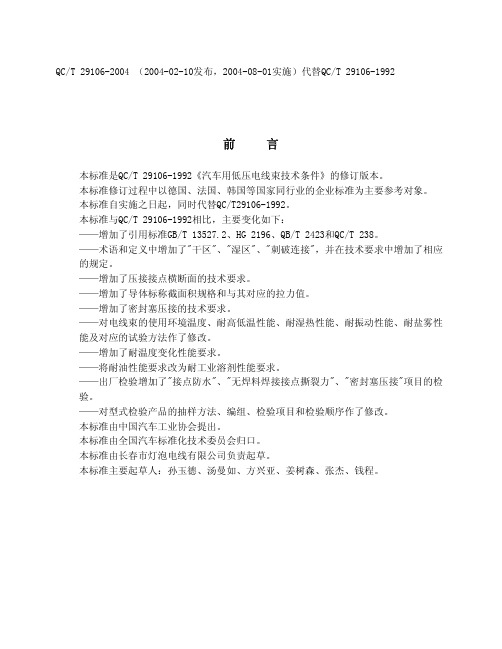
QC/T 29106-2004 (2004-02-10发布,2004-08-01实施)代替QC/T 29106-1992前 言本标准是QC/T 29106-1992《汽车用低压电线束技术条件》的修订版本。
本标准修订过程中以德国、法国、韩国等国家同行业的企业标准为主要参考对象。
本标准自实施之日起,同时代替QC/T29106-1992。
本标准与QC/T 29106-1992相比,主要变化如下:——增加了引用标准GB/T 13527.2、HG 2196、QB/T 2423和QC/T 238。
——术语和定义中增加了"干区"、"湿区"、"刺破连接",并在技术要求中增加了相应的规定。
——增加了压接接点横断面的技术要求。
——增加了导体标称截面积规格和与其对应的拉力值。
——增加了密封塞压接的技术要求。
——对电线束的使用环境温度、耐高低温性能、耐湿热性能、耐振动性能、耐盐雾性能及对应的试验方法作了修改。
——增加了耐温度变化性能要求。
——将耐油性能要求改为耐工业溶剂性能要求。
——出厂检验增加了"接点防水"、"无焊料焊接接点撕裂力"、"密封塞压接"项目的检验。
——对型式检验产品的抽样方法、编组、检验项目和检验顺序作了修改。
本标准由中国汽车工业协会提出。
本标准由全国汽车标准化技术委员会归口。
本标准由长春市灯泡电线有限公司负责起草。
本标准主要起草人:孙玉德、汤曼如、方兴亚、姜树森、张杰、钱程。
QC/T 29106-2004汽车低压电线束技术条件1 范围本标准规定了汽车用低压电线束(以下简称电线束)的要求、试验方法、检验规则、标志、包装、储存和保管。
本标准适用于标称电压低于50V的各种汽车用电线束(含单根线)。
2 规范性引用文件下列文件中的条款通过本标准的引用而成为本标准的条款。
凡是注日期的引用文件,其随后所有的修改单(不包括勘误的内容),或修订版均不适用于本标准。
线束技术要求及检测内容

技术要求一:测量线束的长度:1.主干线的长度,2.支线的长度,3.分支点的长度,4.保护套管与护套的距离(即裸露电源线的长度),以上线束的基本尺寸极限偏差应符合表一规定表一基本尺寸极限偏差mm二:压接处及牢固性检测:1.电线无损伤。
2.采用无特殊要求压接方法时,端子应分别压紧在导体和绝缘层上,导体不应压断,绝缘层不应压入导体压接部位,在图一所示的a区中可见电线导体,但不能妨碍插接。
3.绝缘层压接部位经不少于3个循环的弯折试验后,在图一所示的b 区中仍可见绝缘层。
30°图一4.端子与电线连接应牢固,在规定的拉力下不应损伤和脱开,其拉力值应不小于表二规定。
表二 拉力值三: 端子与电线压接处的电压降应不大于表三的规定。
表三 电压降值四:接点出要求:1.采用无焊料焊接方法时焊接处表面不允许出现氧化、断丝、缺损和绝缘层熔化现象。
2.采用无焊料焊接方法时撕裂力应不小于表四规定。
表四撕裂力值五:密封塞在压接时不应损伤。
电线与密封塞之间、密封塞与护套之间不应有目视可见的间隙。
电线和密封塞与端子压接后,在下图所示的 a区内应可见密封塞和电线绝缘层的端部。
六:电线束包扎时,应紧密、均匀,不应松散。
采用保护套管时,无位移和影响电线束弯曲现象。
七:电线束中电线与端子连接处的绝缘套管应紧密套在连接部位上,无位移、脱开现象。
八:电线束中电线及零部件应正确装配,不应有错位现象,端子在护套中不应脱出。
九:电线束中线路导通率为100%,无短路、错路现象。
十:标志1. 电线束应附有不易脱落的明显标志。
2. 产品标志的内容如下:a ) 产品名称b ) 型号或适用机组或空调成品检验内容1.线束经检验合格后,应附有证明产品质量合格的文件或标记,2. 线束经检验合格后方能使用。
附录A( 规范性附录)端子与电线导体压接处和压接接点处横断面的要求A1 端子与电线导体压接处和压接接点处横断面应符合下列要求A 1.1 如图A1所示,导体中所有单线的断面应呈不规则多边形,导体与端子相接部位、单线与单线之间应无明显缝隙,端子压接部位应包住全部导体。
国标线束标准
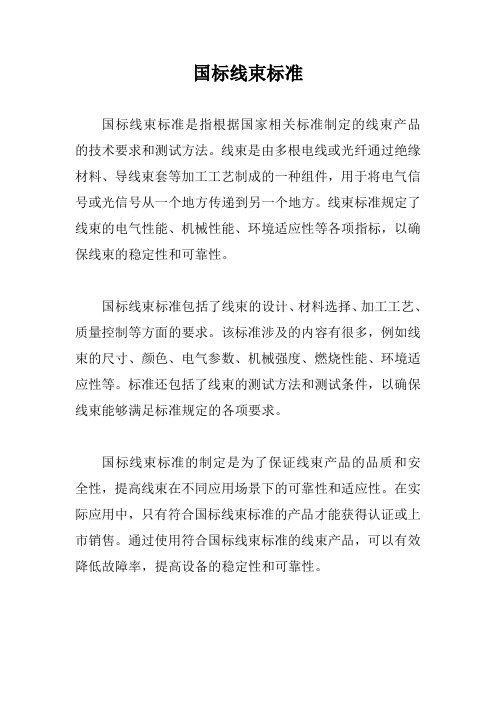
国标线束标准
国标线束标准是指根据国家相关标准制定的线束产品的技术要求和测试方法。
线束是由多根电线或光纤通过绝缘材料、导线束套等加工工艺制成的一种组件,用于将电气信号或光信号从一个地方传递到另一个地方。
线束标准规定了线束的电气性能、机械性能、环境适应性等各项指标,以确保线束的稳定性和可靠性。
国标线束标准包括了线束的设计、材料选择、加工工艺、质量控制等方面的要求。
该标准涉及的内容有很多,例如线束的尺寸、颜色、电气参数、机械强度、燃烧性能、环境适应性等。
标准还包括了线束的测试方法和测试条件,以确保线束能够满足标准规定的各项要求。
国标线束标准的制定是为了保证线束产品的品质和安全性,提高线束在不同应用场景下的可靠性和适应性。
在实际应用中,只有符合国标线束标准的产品才能获得认证或上市销售。
通过使用符合国标线束标准的线束产品,可以有效降低故障率,提高设备的稳定性和可靠性。
线束标准

线束1 范围本标准规定了家用和类似一般设备所用的线束的分类、技术要求、试验方法、检验规则和标志、包装、运输、贮存等内容。
2 引用标准下列标准所包含的条文,通过本标准中引用而构成为本标准条文。
本标准出版时,所示版本均为有效。
所有标准都会被修订,使用本标准的各方应探讨,使用下列标准最新版本的可能性。
GB15934-1996 《电线组件》GB17196-1997 《连接器件连接铜导线用的扁形快速连接端头安全要求》GB2099.1-1996 《家用和类似用插头插座》GB/T 2828.1-2003《计数抽样检验程序第1部分:按接收质量限(AQL)检索的逐批检验抽样计划》3 技术要求3.1 外观要求3.1.1 线束表面应光滑、外皮均匀、无气孔、裂纹、压痕、凹凸、破损、花斑、污浊等。
3.1.2 线束与端子压接牢固、无松脱。
若与端子进行焊接,应焊接牢固,无散芯。
3.1.3 电线字体清晰,擦拭不掉色。
3.2 长度线束长度应符合图纸。
3.3 护套护套应紧密挤包在绞合的绝缘线芯或内护套上,且应容易剥离而不损伤绝缘体或内护套。
护套表面应平整,色泽均匀。
护套厚度的平均值应不小于规定的标称值,其最薄点的厚度应不小于标称值的85% (0.1mm)。
厚度测量结果应按GB1.1附录C(补充件)修约到小数一位。
3.4 压接强度。
压接部分应能经受得住正常使用时可能出现的机械应力。
是否合格,可能过如下抗拉强度试验检查。
施加表1、表2规定的拉力1min,施力时,不应使用爆发力。
此拉力亦可通过抗拉试验机来施加,试验机头部的移动速度应为25㎜(1.0in)/ min至50㎜(2.0in)/ min之间,应无脱落、无断裂现象。
表1表23.5 耐燃耐热 通过4.8试验。
3.6 绝缘电阻3.7 导线的抗电强度电压依次施加在每一导线对连接在一起的所有其它导体之间,然后电压再施加在所有连接 在一起的 导体和护套之间:a) 弱电线束:1500V 交流电压,持续1min ; b) 强电线束:2000V 交流电压,持续1min ; c) 护套:3750V 交流电压,持续1min ; 施加如上电压,不会出现击穿插或闪络现象。
整车线束技术要求

整车电线束技术要求1范围本标准规定了车低压电线束(以下简称电线束)的技术要求、试验方法、检验规则、标志、包装、运输及贮存。
本标准适用于标称电压低于50V的各种汽车用电线束(含单根线)。
2引用标准下列标准所包含的条文,通过在本标准中引用而构成为本标准的条文。
本标准出版时,所示版本均为有效。
下列所有标准都会被修订,本标准的进一步完善存在使用下列标准中最新版本的可能性。
GB 484 车用汽油GB 485 QB 汽油机润滑油GB 2828 逐批检查计数抽样表(适用于连续批的检查)GB 9328 公路车辆用低压电缆(电线)QC/T413 汽车电器设备基本技术条件QC/T417 汽车用片式插接件QCn 29009 汽车用电线接头技术条件JJG 4 钢卷尺QC/T 29106-92 汽车用低压电线束技术条件3术语3.1干线电线束中两根或两根以上电线包扌L在一起的部分。
3.2支线电线束中电线的末端没有包扎的部分或单根电线。
3.3分支点电线束中干线与干线或干线与支线中心线的交点。
3.4接点电线与电线的连接点。
3.5端子接插件和接头的统称。
4技术要求4.1电线束应符合本规范要求,并按经规定程序审批的图样及技术文件制造。
图纸上的要求优于本规范。
表1 电线束基本尺寸偏差接插件应符合图纸要求;电线应符合的规定。
4.4端子与电线连接采用压接方法,并符合下列要求:441端子应分别压紧在导体和绝缘层上,导体不应压断。
442端子与电线连接应牢固,在规定的拉力下不损伤和脱开,其拉力值应不小于表2规定。
表2 端子与电线拉力值4.4.3 端子与电线之间的电压降应不大于表3规定。
表端子与电线之间的电压降值444 采用压接方法的端子与导体压接处的横断面应符合QC/T 29106中附录A的要求。
4.5接头应符合下列要求:4.5.1接点表面绝缘应良好,导体不应压断。
4.5.2接点应牢固,在规定的拉力下不损伤和脱开,其拉力值应不小于表2规定。
4.6电线束采用绝缘物包扎时,应紧密、均匀、不松散;采用保护套管时,无移位和影响电线束弯曲现象。
电动车线束检验标准

金华莱德电动技术有限公司电动车线束检验标准线束是电动车电路的网络主体,没有线束也就不存在电动车电路。
在目前,不管是什么类型的电动车,线束编成的形式基本上是一样的,都是由电线、联插件和包裹胶带组成。
电动车电线都是铜质多蕊软线,几条乃至几十条软铜线包裹在塑料绝缘管(聚氯乙烯)内,柔软而不容易折断。
1:范围:本标准规定了本公司外购电动车线束的性能指标、技术要求、检验项目,作为本公司对外购电动车线束的检验标准。
2:引用标准:SAE J1127 车辆用低压电瓶线标准SAE J1128 车辆用低压主回路电缆标准UL 1581 电线电缆和软线基础标准3:检验方法及要求线束内的电线常用规格有标称截面积0.5、0.75、1.0、1.5、2.0、2.5、4.0、6.0等平方毫米的电线,它们各自都有允许负载电流值,配用于不同功率用电设备的导线。
以整车线束为例,0.5规格线适用于仪表灯、指示灯、门灯、顶灯等;0.75规格线适用于牌照灯,前后小灯、制动灯等;1.0规格线适用于转向灯、雾灯等;1.5规格线适用于前大灯、喇叭等;主电源线例如发电机电枢线、搭铁线等要求2.5至4平方毫米电线。
这只是指一般汽车而言,关键要看负载的最大电流值,例如蓄电池的搭铁线、正极电源线则是专门的汽车电线单独使用,它们的线径都比较大,起码有十几平方毫米以上,这些"巨无霸"电线就不会编入主线束内。
线束上各端头都会打上标志数字和字母,以标明导线的连接对象,操作者看到标志能正确连接到对应的电线和电气装置上,这在修理或更换线束时特别有用。
同时,电线的颜色分为单色线和双色线,颜色的用途也有规定,一般是车厂自订的标准。
我国行业标准只是规定主色,例如规定单黑色专用于搭铁线,红单色用于电源线,不可混淆。
线束用机织线或塑料粘带包裹,出于安全、加工和维修方便,机织线包裹已经淘汰,现在是用粘性塑料胶带包裹。
线束与线束之间、线束与电气件之间的连接,采用联插件或线耳。
汽车用低压电线束技术条件

汽车用低压电线束是指安装在汽车中,用于传输低压电信号和电力的线束系统。
以下是一些常见的汽车用低压电线束的技术条件:
1. 电线材料:
-电线应使用符合相关标准的高质量、耐久的绝缘材料,如聚氯乙烯(PVC)或交联聚乙烯(XLPE)等。
-绝缘材料应具有良好的绝缘性能、耐磨损性和抗化学腐蚀性。
2. 导体规格:
-导体应采用导电性能良好的铜材质,确保电流传输效率高。
-根据所需电流及负载要求,确定合适的导体截面积和线径。
3. 绝缘层厚度:
-绝缘层的厚度应根据电线的额定电压和环境条件来确定,以确保防止电线短路或绝缘击穿。
4. 温度等级:
-电线束应符合特定温度等级要求,以保证在不同工
作环境下的可靠性和安全性。
-常见的温度等级包括80℃、105℃和125℃等。
5. 阻燃性能:
-为确保在汽车发生火灾时电线束不会加剧火势,电线束应具有良好的阻燃性能。
-符合相关标准要求的低烟无卤(LSZH)材料可用于提高电线束的阻燃性能。
6. 抗振动和耐久性:
-由于汽车运行中存在振动和冲击,电线束应具备良好的抗振动和耐久性,以保持稳定的电信号传输和使用寿命。
7. 标识和色彩:
-电线束上应有清晰易读的标识,包括电线规格、颜色代码和制造商信息等。
-不同功能的电线可以使用不同的颜色代码,便于安装和维护。
请注意,以上是一些常见的技术条件,实际汽车用低压电线束的技术条件可能因所在地区、汽车制造商的
要求和特定应用而有所不同。
建议根据相关标准和规范进行详细的技术要求和测试,以确保电线束的质量和符合使用要求。
线束技术要求及检验报告

REV1
功率线束技术要求
一、 1、 2、 3、 4、 5、 6、 7、 定制 --- HUB至汇流盒空开功率电缆
BESS3.0-PWTR-0011
近端连接器型号为AC-HA002267,有正极符号的使用橙色连接器,有负极符号的使用黑色连接器; 电缆为35mm² 1500V硅胶高压电缆 橙色;电缆长度根据线束表要求; 近端连接器与电缆厂家一次压铸成型; 远端端头绝缘去皮18mm,压接片形端子铜鼻子,C45-35mm² 标签为A4缠绕式覆盖保护膜线缆标签,环绕线缆粘贴;标签58025 标签宽度:58mm 高度:25mm 标签与端头之间套热缩管300mm,POS+红色,POS-黄色,NEG+绿色,NEG-黑色; 制作完毕每根电缆整齐捆扎后,塑料袋包装。包装袋相应标识线束号。
电缆为35mm² 1500V硅胶高压电缆 橙色; 近端铜鼻子型号为SC35-8;绝缘去皮15mm,用液压钳将铜鼻子与电缆压接; 远端压接片形端子铜鼻子,C45-35mm²,绝缘去皮18mm,用液压钳将铜鼻子与电缆压接; 压接后套45mm热缩套管,POS+红色,POS-黄色,NEG+绿色,NEG-黑色; 标签为A4缠绕式覆盖保护膜线缆标签,环绕线缆粘贴;标签58025 标签宽度:58mm 高度:25mm; 制作完毕每根电缆整齐捆扎后,塑料袋包装。包装袋相应标识线束号。
AC-HA002267(+橙 -黑)
标签
35mm2 1500V硅胶线 橙色
C45-35 片型铜端子
二、 1、 2、 3、 4、 5、
定制 --- 面板间连接功率电缆 两端连接器型号为AC-HA002267,有正极符号的使用橙色连接器,有负极符号的使用黑色连接器; 电缆为35mm² 1500V硅胶高压电缆 橙色;电缆长度根据线束表要求; 近端连接器与电缆厂家一次压铸成型; 标签为A4缠绕式覆盖保护膜线缆标签,环绕线缆粘贴;标签58025 标签宽度:58mm 高度:25mm 制作完毕每根电缆整齐捆扎后,塑料袋包装。包装袋相应标识线束号。
线束质量控制标准

线束质量控制标准一、引言线束是指由一组或者多组电线、电缆或者光纤组成的电气连接装置,广泛应用于汽车、航空航天、电子设备等领域。
线束质量控制是确保线束产品符合质量要求的关键环节。
本文旨在制定一套线束质量控制标准,以确保线束产品的可靠性、安全性和一致性。
二、线束质量控制标准内容1. 产品规范- 线束结构:包括线束的长度、宽度、高度、弯曲半径、束径等要求。
- 线材规格:包括导体材料、截面积、绝缘材料、绝缘厚度、耐温等要求。
- 连接器规格:包括连接器型号、引线长度、引线颜色、连接方式等要求。
- 标识要求:包括产品型号、批次号、生产日期、质量标识等要求。
2. 材料采购- 供应商选择:选择具备良好信誉和质量管理体系的供应商。
- 材料检验:对进货的线材、连接器等材料进行外观检查和性能测试,确保符合规格要求。
3. 生产过程控制- 工艺流程:明确线束生产的工艺流程,包括导线剥皮、绝缘处理、连接器安装、终端压接等环节。
- 工艺参数:制定合理的工艺参数,确保每一个环节的操作符合标准。
- 工艺记录:记录每一个工艺环节的操作过程和结果,以便追溯和分析。
4. 检验与测试- 外观检查:对线束外观进行检查,包括线材损伤、连接器安装质量等。
- 电气性能测试:对线束进行电阻、绝缘电阻、耐压等测试,确保符合技术要求。
- 功能测试:对线束进行功能性测试,如连通性测试、信号传输测试等。
5. 抽样检验- 抽样方案:制定合理的抽样方案,确保抽样结果能够代表整个批次的质量水平。
- 抽样标准:制定合理的抽样标准,包括接受质量水平、拒绝质量水平等。
6. 不良品处理- 不良品判定:对不合格线束进行判定,明确判定标准。
- 不良品分类:将不良品按照不同类型进行分类,如外观缺陷、电气性能不合格等。
- 不良品处理:对不良品进行返修、报废或者重新生产等处理。
7. 记录与追溯- 质量记录:记录每一个环节的质量数据,包括原材料检验报告、生产记录、检验报告等。
- 追溯能力:确保每一个线束产品都能够追溯到原材料供应商、生产工艺、检验结果等信息。
线束技术要求及检验报告

PRODUCT SPECIFICATION REV1通信线束致命重轻1包装整齐捆扎后,塑
料袋包装。
目视2标识线束号码打印清
晰,配套合适,位
置正确。
目视3
外观线束绝缘层无破损变形,颜色正确;端子接插件型号正确,连接头外无飞丝外露。
目视4端头处理连接方式正确,压接牢固,拉拔不脱落,绝缘恢
复措施得当。
目视拉拔5线束导通性万用表导通档量测,线束两端正常导通。
万用表6尺寸按照技术要求,
长度偏差在±2mm
内。
卷尺7
8
9
检验员
确认
承认正常导通长度偏差最大为2mm,符合要求
判定:
备注:
检测结果缺陷数结论符合技术要求符合技术要求
符合技术要求检验依据
允收水准致命: 重: 轻:符合技术要求序号检测项目检测标准
设备/方式抽样数 通信线束检验报告 -CWIR-002产品名称
型号/规格检验日期提检数
抽检数。
汽车低压线束要求和测试技术条件

汽车低压线束要求和测试技术条件
汽车低压线束是指车辆中用于传输低电压信号与电力的线束系统。
其要求和测试技术条件主要包括以下几个方面:
1. 电气性能要求:低压线束的电气性能要符合标准规定的要求,包括电阻、电容、电压、电流等参数的要求。
测试技术条件包括使用合适的测试设备进行电阻、电容、电压、电流等参数的测量,并与标准规定的要求进行对比。
2. 机械性能要求:低压线束的机械性能要能够满足车辆运行中的振动、温度变化等环境要求。
测试技术条件包括使用合适的设备进行振动测试、温度变化测试等,以评估线束的机械性能。
3. 绝缘性能要求:低压线束的绝缘性能要达到标准规定的要求,以确保线束在车辆使用过程中不发生电气短路等问题。
测试技术条件包括使用绝缘测试仪进行绝缘电阻测试、介电强度测试等。
4. 环境适应性要求:低压线束要能够适应不同的环境条件,如高温、低温、潮湿等。
测试技术条件包括使用温度箱等设备进行高温、低温、潮湿等环境适应性测试。
5. 可靠性要求:低压线束在车辆使用寿命内应具有良好的可靠性,不应发生断裂、接触不良等问题。
测试技术条件包括使用拉力测试机进行线束的拉力测试,使用接触电阻测试仪进行接触电阻测试等。
通过以上测试,可以确保低压线束的质量和性能达到标准规定的要求,保证车辆的安全和可靠性。
线束质量控制标准
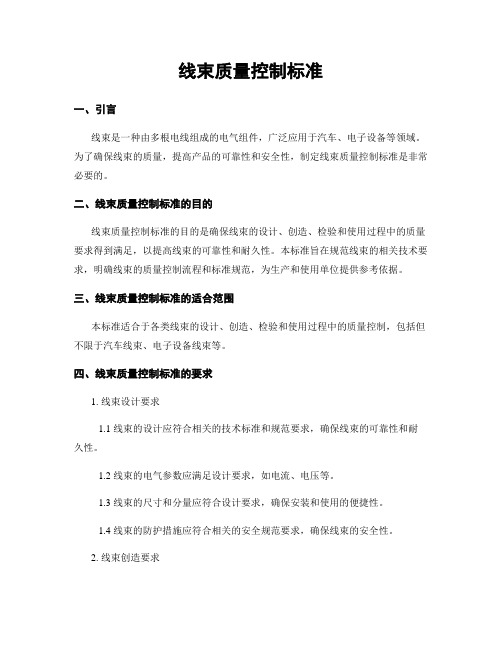
线束质量控制标准一、引言线束是一种由多根电线组成的电气组件,广泛应用于汽车、电子设备等领域。
为了确保线束的质量,提高产品的可靠性和安全性,制定线束质量控制标准是非常必要的。
二、线束质量控制标准的目的线束质量控制标准的目的是确保线束的设计、创造、检验和使用过程中的质量要求得到满足,以提高线束的可靠性和耐久性。
本标准旨在规范线束的相关技术要求,明确线束的质量控制流程和标准规范,为生产和使用单位提供参考依据。
三、线束质量控制标准的适合范围本标准适合于各类线束的设计、创造、检验和使用过程中的质量控制,包括但不限于汽车线束、电子设备线束等。
四、线束质量控制标准的要求1. 线束设计要求1.1 线束的设计应符合相关的技术标准和规范要求,确保线束的可靠性和耐久性。
1.2 线束的电气参数应满足设计要求,如电流、电压等。
1.3 线束的尺寸和分量应符合设计要求,确保安装和使用的便捷性。
1.4 线束的防护措施应符合相关的安全规范要求,确保线束的安全性。
2. 线束创造要求2.1 线束的创造过程应符合相关的工艺标准和规范要求,确保线束的质量稳定。
2.2 线束的材料应符合相关的材料标准和规范要求,确保线束的质量可控。
2.3 线束的创造设备应符合相关的设备标准和规范要求,确保线束的创造过程稳定可靠。
2.4 线束的创造人员应经过专业培训,具备相关的技能和知识,确保线束的创造质量。
3. 线束检验要求3.1 线束的检验应符合相关的检验标准和规范要求,确保线束的质量合格。
3.2 线束的检验设备应符合相关的设备标准和规范要求,确保线束的检验结果准确可靠。
3.3 线束的检验人员应经过专业培训,具备相关的技能和知识,确保线束的检验质量。
4. 线束使用要求4.1 线束的安装应符合相关的安装标准和规范要求,确保线束的安装质量可靠。
4.2 线束的使用环境应符合相关的使用标准和规范要求,确保线束的使用寿命和性能稳定。
4.3 线束的维护和保养应符合相关的维护标准和规范要求,确保线束的正常运行和延长使用寿命。
汽车用低压电线束通用技术条件

汽车用低压电线束通用技术条件汽车用低压电线束是汽车电气系统中的重要组成部分,承载着电力传输、信号传递和控制功能。
为了确保汽车电气系统的正常运行和安全性,制定了汽车用低压电线束的通用技术条件。
一、导线材料要求汽车用低压电线束的导线材料应采用优质的铜材料,以确保电流传输的稳定性和可靠性。
导线应符合国家相关标准,具有良好的导电性能和耐腐蚀性能,以应对恶劣的工作环境。
二、绝缘材料要求低压电线束的绝缘材料应具有良好的绝缘性能,能够有效防止电流泄漏和短路。
常用的绝缘材料有聚氯乙烯(PVC)、交联聚乙烯(XLPE)等,选择合适的绝缘材料要考虑到工作温度、耐候性和耐磨性等因素。
三、外皮材料要求汽车用低压电线束的外皮材料应具有良好的耐磨性和耐油性,能够抵御外界环境的侵蚀和物理损坏。
常用的外皮材料有聚氯乙烯(PVC)、聚氨酯(PU)等,选择合适的外皮材料要考虑到工作环境的特殊要求。
四、线束结构要求低压电线束应具备良好的线束结构,能够方便安装和维修。
线束内的导线应按照电气系统的布局进行合理的排列和分组,避免导线之间的交叉干扰和短路现象。
同时,线束的长度和形状也要根据汽车的布置和空间要求进行合理设计。
五、标识要求为了方便安装和维修,低压电线束上应标注清晰的标识,包括导线编号、颜色、功能等信息。
标识应符合国家相关标准,以确保用户能够准确识别和操作。
六、测试要求低压电线束应经过严格的测试和检测,以确保质量和性能符合技术要求。
测试内容包括导线的电阻、绝缘电阻、耐压等,同时还要进行可靠性测试,模拟各种工作环境和负载条件下的使用情况。
七、环境要求汽车用低压电线束要能够适应各种恶劣的工作环境,包括高温、低温、潮湿、震动等。
因此,在设计和选择材料时要考虑到这些因素,并采取相应的防护措施,以确保电线束的稳定性和可靠性。
汽车用低压电线束通用技术条件的制定,旨在确保汽车电气系统的正常运行和安全性。
通过对导线材料、绝缘材料、外皮材料、线束结构、标识要求、测试要求和环境要求等方面的规定,可以提高汽车用低压电线束的质量和性能,满足汽车行驶过程中的各种需求和要求。
线束质量控制标准

线束质量控制标准一、引言线束是电气设备中的重要组成部分,其质量直接影响着设备的可靠性和安全性。
为了确保线束的质量符合要求,本文将制定线束质量控制标准,以便在生产过程中进行质量控制和检验。
二、适用范围本标准适用于所有线束的生产过程,包括设计、材料采购、制造、装配和测试等环节。
三、术语和定义1. 线束:由多根导线、电缆或光纤等组成的电气连接装置。
2. 组件:线束中的各个部件,包括导线、绝缘材料、连接器等。
3. 质量控制:通过一系列措施和活动,确保产品质量符合要求的过程。
四、质量控制要求1. 设计阶段:a. 确定线束的功能和性能要求。
b. 选择合适的材料和组件,确保其质量可靠。
c. 设计合理的线束结构,减少连接点和接头数量,降低故障率。
2. 材料采购:a. 选择供应商时,要评估其质量管理体系和产品质量。
b. 对采购的材料进行检验,确保其符合规定的技术要求。
3. 制造过程:a. 制定详细的制造工艺流程,确保每个环节都得到控制。
b. 建立质量记录,记录每个工序的检验结果和质量问题。
c. 对每个制造环节进行自检和互检,确保质量的可追溯性。
4. 装配过程:a. 严格按照装配要求进行线束的组装。
b. 对组装的线束进行外观检查,确保没有损伤和松动。
5. 测试过程:a. 制定线束的测试方案,包括功能测试、电气测试和可靠性测试等。
b. 对线束进行全面的测试,确保各项指标符合规定的要求。
c. 对测试结果进行记录和分析,及时处理发现的质量问题。
6. 质量控制文件:a. 建立质量控制文件,包括设计文件、制造工艺文件、检验记录等。
b. 对质量控制文件进行管理和归档,确保其可追溯性和完整性。
五、质量控制措施1. 建立质量管理体系,包括质量目标、质量责任和质量管理程序等。
2. 培训员工,提高其质量意识和技能水平。
3. 定期进行内部审核,发现问题并及时纠正。
4. 进行供应商评估和监督,确保供应的材料符合要求。
5. 进行设备维护和校准,确保测试和检验设备的准确性和可靠性。
最新版线束标准

1)Q/SQR前言本标准参考QC/T29106标准,在满足奇瑞汽车的产品性能的实际情况下制定的。
本标准作为产品质量抽查检验的依据。
同时在格式和内容的编排上均符合GB/T1.1-2000和GB/T1.2-2002的规定。
本标准与上一版本的标准主要区别如下:1.规范性引用文件的更改如下:增加(新的引用标准):Q/SQR.04.228 汽车用熔断器Q/SQR.04.295 线束波纹管Q/SQR.04.421 电线束绝缘胶带标准Q/SQR.04.572 线束紧固件标准(试用)Q/SQR.04.923 轿车、轻型汽车温度场底盘测功机法替换:将QC/T 417.1~QC/T417.5改为引用Q/SQR.04.935标准。
2.术语和定义的更改更改端子、护套的定义,删除插接件的定义。
新增插接器、插头、插座的定义。
3.要求中做的更改如下:在4.2.4中增加绝缘套管与孔中心的距离。
在4.2.5中对紧固件、主干、分支的公差进行分类规定。
在4.4.5、4.4.7、4.6.2中更改为采用Q/SQR.04.935标准的检测方法。
在4.12中对电线束的工作温度及贮存温度等级进行更改。
新增4.2.6 护套末端与保护材料之间的尺寸要求。
新增4.2.7 线束双绞线要求。
新增4.3.9、4.3.10、4.3.11、4.3.12对电线束的附件材料要求。
4.试验方法中更改如下:在5.5中将测试速度由25mm/min~l00mm/min改为50±10mm/min。
在5.7中更改为采用Q/SQR.04.935标准的测试方法。
在5.16中更改为采用Q/SQR.04.923标准的测试方法。
5.检验规则中更改如下:在6.3中增加对4.2.6、4.2.7的检验。
6.标志、包装、储存和保管更改如下在7.12中a)产品名称要求为中英文,b)改为产品图号,增加f)项图纸版本号。
本标准由奇瑞汽车有限公司乘用车工程研究一院提出。
本标准由奇瑞汽车有限公司汽车工程研究院标准管理科归口。
汽车线束技术条件和试验方法-整合_图文(精)

ICSJ021-005汽车线束技术条件和试验方法Test Methods and Performance Requirements for Automotive Wire Harness (草案稿中国·合兴集团有限公司发布Q/HXQ/HX 104— 2006 目次前言 (III)1 范围 (1)2 规范性引用文件 (1)3 术语和定义 (1)4 一般要求 ............................................................................ 3 4.1 默认试验公差 . ...................................................................... 3 4.2 默认试验条件 . ...................................................................... 3 4.3 试验设备 . (2)4.4 测量精度要求 . (2)5 技术要求和试验方法 .................................................................. 2 5.1 总则 . .............................................................................. 2 5.1.1 尺寸特性 [1、 2、3]................................................................. 2 5.1.2 物料特性 ......................................................................... 3 5.1.3 环境温度范围(分级 ............................................................. 3 5.1.4 线束的工作电压范围 ............................................................... 3 5.1.5 接触件样品准备 ................................................................... 4 5.1.6 预处理—连接器和 /或接触件插拔循环 ................................................. 4 5.1.7 外观[3]........................................................................... 4 5.1.8 线路检测 [1](QC/T29106 ......................................................... 5 5.1.9 电连续性监测(瞬断监测 ......................................................... 5 5.2 接触件—机械性能试验 . .............................................................. 6 5.2.1 接触件—接触件插入力 /拔出力[1] .................................................... 6 5.2.2 接触件抗弯性[2]................................................................... 7 5.2.3 绝缘层压接部位的弯折试验[2](QC/T 29106 ......................................... 8 5.2.4 导线—接触件拉脱力[1](USCAR21 ................................................ 8 5.3 接触件—电性能试验 . ................................................................ 9 5.3.1 接触电阻(干电路电阻(总连接电阻[2]........................................... 9 5.3.2 电压降[2]........................................................................ 10 5.3.3 最大电流能力[2].................................................................. 11 5.3.4 1008h电流循环[2]................................................................. 13 5.4 线束—机械性能试验 . ............................................................... 14 5.4.1 接触件—连接器插入力 /拔出力[1] ................................................... 14 5.4.2 连接器—连接器插入力 /拔出力(无机械辅助的连接器 [1].............................. 16 5.4.3 连接器—连接器插入力 /拔出力(带机械辅助的连接器 [1].............................. 18 5.4.4 线束极性防错能力[1].............................................................. 18 5.4.5 连接器其它零件如 CPA 、 PLR 、locator clip的插入力 /拔出力 [1].......................... 19 5.4.6 振动 /机械冲击[2] ................................................................. 20 5.4.7 连接器—连接器装配时的喀哒声[2].................................................. 22 5.4.8 线束跌落试验[2] (22)IQ/HX 104— 20065.4.9 连接器塑件(塑件(塑件(塑件(护套孔的易受损伤性 [2]...................... 22 5.5 线束—电性能试验 . ................................................................. 23 5.5.1 绝缘电阻[2]...................................................................... 23 5.5.2 耐压 [2](ISO16750-2 ............................................................ 24 5.6 线束—环境试验 . ................................................................... 24 5.6.1 可焊性 [2](QC/T29106 .......................................................... 24 5.6.2 耐焊接热 [2](QC/T29106 ........................................................ 24 5.6.3 热冲击(温度循环[2]............................................................ 25 5.6.4 温度 /湿度循环[2] ................................................................. 25 5.6.5 高温试验[2]...................................................................... 27 5.6.6 低温试验 [2](QC/T29106 ........................................................ 28 5.6.7 耐工业溶剂[3].................................................................... 29 5.6.8 浸渍试验[2]...................................................................... 29 5.6.9 压力 /真空泄露[2] ................................................................. 30 5.6.10 盐雾 [2](QC/T29106 ........................................................... 32 5.7 特殊试验 . ......................................................................... 32 5.7.1 连接器安装结构的机械强度[2]...................................................... 32 5.8 严酷环境试验 . ..................................................................... 33 5.8.1 高压水喷射 ...................................................................... 33 5.8.2 严酷振动 ........................................................................ 34 5.9 试验顺序 . ......................................................................... 36 5.9.1 说明 ............................................................................ 36 5.10 推荐的试验项目 . ................................................................... 3 5.10.1 新工具设计、工具更改或材料更改后推荐进行的试验 . (3)5.10.2 新 /现有接触件或连接器设计后推荐进行的试验 (5)6 质量评定程序 ........................................................................7 6.1 鉴定检验 . .......................................................................... 7 6.1.1 抽样 ............................................................................. 7 6.1.2 程序 ............................................................................. 7 6.1.3 合格 ............................................................................. 7 6.1.4 样品处理 ......................................................................... 7 6.2 质量一致性检验 . .................................................................... 7 6.2.1 逐批检验 (7)6.2.2 周期检验 (9)7 标志、包装、运输和贮存 ............................................................. 12 7.1 标志 . ............................................................................. 12 7.2 包装 . ............................................................................. 12 7.2.1 检验:.......................................................................... 12 7.3 运输 . ............................................................................. 12 7.4 储存 . ............................................................................. 12附录 A (规范性附录加速老化试验 ................................................... 13附录 B (资料性附录恒定湿热[2]...................................................... 14附录 C (资料性附录温升[2].......................................................... 15附录 D (资料性附录表 D1 导线—接触件拉脱力 (16)IIQ/HX 104— 2006 前言本规范是修改采用 SAE/USCAR02 Performance Specification for Automotive Electrical Connector Systems 标准。
低压线束技术规范

13.6
13.7
a) 接线点表面绝缘应良好,导体不应被压伤或压断。
a)接线点应牢固,在规定的拉力下不损伤和脱开,其拉力值应不小于表3的规定。
13.8
13.9
13.10
13.10.1
a)一端固定的定位扣
1. 若固定于1条电线束上,则保持力30N以上。
2. 若固定于2条电线束上,则保持力50N以上。
15.6
a) 抽样方案:一次正常检查抽样方案;
b) 检查水平:一般检查水平Ⅱ;
c) 合格及质量水平:AQL 5.5。
16
16.1
16.1.1
16.1.2
a)金客公司标识
b) 产品零件号
c) 产品名称;
d) 型号或适用车型;
e) 制造厂名或商标;
f) 制造日期。
16.2
16.2.1
16.2.2
16.2.3
全检
导通
3.9
4.7
全检
端子与电线间拉脱力
3.3
4.3
在工序中检验
(首末件)
15.4
a) 新产品或老产品转厂生产的试制定型鉴定;
b) 正式生产后,如结构、材料、工艺有较大改变而可能影响产品性能时;
c) 成批或大量生产的产品每10000套不少于一次;
d) 产品停产一年以上,恢复生产时;
e) 出厂检验结果与上次型式检验结果有较大差异时;
检验顺序和检验项目组别检验顺序检验项目技术要求条款试验方法条款耐振动31648314475防水性311471端子与导体压接横断面35344耐低温311472耐高温311472热冲击312473耐湿热313474耐油性311476固定扣橡胶圈与电线束间的保持力31049电压降3645端子与电线间拉脱力3544355产品的型式检验必须全部合格如有一项不合格时允许重新抽加倍数量的产品就该不合格项目进行复验
线束测量方法

线束测量方法线束测量方法是指通过使用各种测试仪器和设备对线束进行检测和测量的技术方法。
线束是一种将多根导线或电缆捆绑在一起的组件,常用于电气系统、电子设备和汽车等领域。
线束测量的主要目的是确保线束的质量和性能符合设计要求,以便在正常工作条件下可靠地传输电力、信号和数据。
在线束测量方法中,通常需要进行以下几个方面的测量和检测:1. 电阻测量:通过测量线束中导线之间的电阻,可以判断导线是否短路、开路或接触不良。
常用的电阻测量仪器包括万用表和电阻测量仪。
2. 绝缘电阻测量:通过测量线束与外部环境之间的绝缘电阻,可以判断线束是否存在绝缘损坏的情况。
常用的绝缘电阻测量仪器包括绝缘电阻测试仪。
3. 电容测量:通过测量线束之间或线束与地之间的电容,可以评估线束的电磁兼容性和信号传输性能。
常用的电容测量仪器包括LCR表和电容测试仪。
4. 电压测量:通过测量线束中的电压,可以评估线束的工作电压范围和电压稳定性。
常用的电压测量仪器包括数字万用表和示波器。
5. 高温测试:通过将线束暴露在高温环境下,可以评估线束的耐热性能和可靠性。
常用的高温测试设备包括高温箱和热电偶温度计。
6. 弯曲测试:通过将线束进行多次弯曲,可以评估线束的柔性和耐久性。
常用的弯曲测试设备包括弯曲试验机和弯曲强度测试仪。
7. 拉伸测试:通过对线束施加拉伸力,可以评估线束的拉伸强度和可靠性。
常用的拉伸测试设备包括拉力试验机和拉伸强度测试仪。
以上是线束测量方法的一些常见内容和参考设备。
实际应用中,具体的线束测量方法和设备选择会根据实际需求和测量要求进行确定。
此外,还需要注意测量环境的选择和标准的遵守,以确保线束测量结果的准确性和可靠性。
整车线束技术要求

整车线束技术要求整车线束技术要求意味着制造车辆时对线束的要求。
整车线束是指连接车辆主要电气系统的一组电线、接插件和保护装置。
它起着车辆各种电气部件之间传输电能和信号的作用。
整车线束的设计和制造质量对于车辆整体性能和安全性具有重要影响,因此整车线束有一系列的技术要求。
首先,整车线束的设计要符合车辆的功能需求。
设计者需要根据车辆的电气布局和功能要求,确定线束的布线方案、线束的长度、截面面积、导线材料等。
线束布线应该尽量简洁,避免环路和干扰。
同时,线束的长度和截面面积应根据电流负载计算得出,以确保线束能够承受预期的电流负载。
其次,整车线束要求具有良好的电气性能。
线束的导线材料应该具有较低的电阻和较高的绝缘性能,以最大限度地减少能量损耗和电路干扰。
线束的接插件应该具有良好的导电性能和稳定的连接性能,以确保电能和信号能够在各个部件之间有效传输。
同时,整车线束还要求具有良好的机械性能和耐久性。
线束应能够承受车辆运行中的振动、冲击和温度变化,不会松动、断裂或导致短路。
线束的保护装置应提供足够的保护,以防止线束被外部物体划伤或损坏。
此外,整车线束还需要满足可维护性和易于安装的要求。
线束的布线应尽量合理,易于维修和更换。
线束应具有一定的标识,以便于识别和诊断故障。
线束应具有标准化的接口和连接方式,以方便安装和拆卸。
最后,整车线束还需要符合相关的法规和标准要求。
不同国家和地区对于整车线束有一系列的安全和性能要求,如欧洲的ECE标准和美国的SAE标准等。
制造商需要确保线束符合当地的法规和标准,以确保车辆的合规性和安全性。
总而言之,整车线束技术要求包括设计合理、电气性能优良、机械性能耐久、易于维护和符合相关法规等方面。
只有满足这些要求,才能保证整车线束在车辆运行中的可靠性和安全性。
线束组件技术要求

线束组件技术要求
1 范围
本标准适用于本公司线束组件采购、入厂检验的依据。
2 引用文件
GB/T 2828.1-2003《计数抽样检验程序第一部分:按接受质量限(AQL)检索的逐批检验抽样计划》
GB 4706.1《家用和类似用途电器的安全第一部分:通用要求》
GB 5023.3-1997《额定电压450/750V及以下聚氯乙烯绝缘电缆》
GB 17196《连接器件连接铜导线用的扁形快速连接端头安全要求》
GB 15092.1《器具开关第一部分:通用要求》
3 技术要求
3.1 线规、尺寸:线束组件的导线技术参数、配合尺寸,按产品图纸;
3.2 外观:
a.导线表面光滑、色均,无明显油污、毛刺、砂粒、擦伤、裂纹等现象;
b.导线与连接端头压接部分,线芯无外露,护套完整无损坏;
c.导线的剥头对线芯的损伤(如线芯断、割伤等)不得大于8%;
3.3 导线:线束组件的导线应符合GB 5023.3要求;
3.4端接件:连接铜导线用的各规格快速连接端头尺寸,其尺寸规格应符合:GB 17196第6.1条;
3.5压接成型状态:导线在端子压合点的位置应正确并保持一致;
3.7抗拉强度:导线与连接端头压接部分的抗拉强度应符合GB 17196第9.6条;
其它项目,需方视产品质量情况,可不定期下厂检验。
4.3验收规则
产品按批次检验按GB/T 2828.1特殊检查水平S-3进行。
4.4型式检验
由需方按需要提出,由供方提供相应的试验报告。
5.供货状态
5.1供货产品必须附出厂检验报告(质保书)、合格证。
5.2包装数量、方式由供货方自定。
- 1、下载文档前请自行甄别文档内容的完整性,平台不提供额外的编辑、内容补充、找答案等附加服务。
- 2、"仅部分预览"的文档,不可在线预览部分如存在完整性等问题,可反馈申请退款(可完整预览的文档不适用该条件!)。
- 3、如文档侵犯您的权益,请联系客服反馈,我们会尽快为您处理(人工客服工作时间:9:00-18:30)。
技术要求
一:测量线束的长度:
1•主干线的长度,
2•支线的长度,
3•分支点的长度,
4•保护套管与护套的距离(即裸露电源线的长度)
以上线束的基本尺寸极限偏差应符合表一规定
表一基本尺寸极限偏差mm
二:压接处及牢固性检测:
1. 电线无损伤。
2. 采用无特殊要求压接方法时,端子应分别压紧在导体和绝缘层
上,导体不应压断,绝缘层不应压入导体压接部位,在图一所
示的a区中可见电线导体,但不能妨碍插接。
3. 绝缘层压接部位经不少于3个循环的弯折试验后,在图一所
示的b 区中仍可见绝缘层
图一
4. 端子与电线连接应牢固,在规定的拉力下不应损伤和脱开, 其
拉力值应不小于表二规定。
表二 拉力值
导体公称截面积mm2
拉力N
导体公称截面积mm2
拉力N
0.5 50
6.0 450 0.75
:80
10.0
500 1.0 100 16.0 1500
1.5 150 25.0 1900
2.5 200 35.0 2200
4.0 270 > 50-200 2700
注:接点或一个端子同时连接两根及两根以上电线时, 选择截面较大的电线测量 拉力。
三:端子与电线压接处的电压降应不大于表三的规定
表三
电压降值
导体公称截面积
试验电流
电压降 导体公称截面积
试验电流
电压降 mm2
A mV
mm2
A
mV
0.50
5 3 10.00 50 25 0.75 10 5 16.00 60 15 1.00 15 8 25.00 70
18 1.50 20 11 35.00 80 20 2.50 30 16 50.00 —
90 23 4.00
35
18
70.00
100 25
a
b
端子
电线
四:接点出要求:
1.采用无焊料焊接方法时焊接处表面不允许出现氧化、断丝、
缺损和绝缘层熔化现象。
2.采用无焊料焊接方法时撕裂力应不小于表四规定
表四撕裂力值
五:密封塞在压接时不应损伤。
电线与密封塞之间、密封塞与护套之间不应有目视可见的间隙。
电线和密封塞与端子压接后,在下图所示的a区内应可见密封塞和电线绝缘层的端部。
六:电线束包扎时,应紧密、均匀,不应松散。
采用保护套管时,无位移和影响电线束弯曲现象。
七:电线束中电线与端子连接处的绝缘套管应紧密套在连接部位上,无位移、脱开现象。
八:电线束中电线及零部件应正确装配,不应有错位现象,端子在护套中不应脱出。
九:电线束中线路导通率为100%无短路、错路现象。
十:标志
1.电线束应附有不易脱落的明显标志。
2. 产品标志的内容如下:
a ) 产品名称
成品检验内容
1•线束经检验合格后,应附有证明产品质量合格的文件或标记, 2.线束经检验合格后方能使用。
附录A
(规范性附录)
端子与电线导体压接处和压接接点处横断面的要求
A1端子与电线导体压接处和压接接点处横断面应符合下列要求
A 1.1如图A1所示,导体中所有单线的断面应呈不规则多边形,导体与端子相接部位、单线与单线之间应无明显缝隙,端子压接部位应包住全部导体。
端子压接的卷曲部分a、b必须相接,且对称。
图A1
A1.2如图A2所示,端子压接卷曲部分a、b端部距底部c的距离d不小于单标称直径的1/2 。
图A2
A1.3如图A3所示,横断面底部两侧的毛刺高e应不超过端子压接后的厚度g , 毛刺宽度f应不超过g的1/2。
图A3
A2端子与电线导体压接处和压接接点处横断面不允许存在下列任何一种缺陷
A2.1如图A4所示,端子卷曲部分a b之间有缝隙。
A2.2如图A5所示,端子卷曲a或b的端部与端子其他部位相接
L
A2.3如图A6所示,横断面上端子压接部位出现裂纹h
图A6。